advertisement
▼
Scroll to page 2
of
20
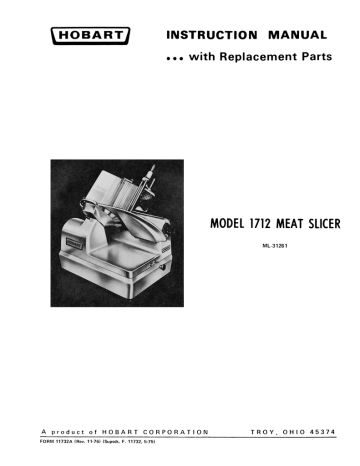
¡HOBART INSTRUCTION MANUAL eee With Replacement Parts MODEL 1712 MEAT SLICER ML-31261 A product of HOBART CORPORATION TROY, OHIO 45374 FORM 11732A (Rev. 11-76) (Supsds. F. 11732, 5-75) 1712 INSTRUCTIONS NN Instructions For Operation and Care of HOBART MODEL 1712 SLICING MACHINE 1. INSTALLATION: When the machine is packed for shipment, the four rubber feet (1, Fig. 1) are taken off to permit bolting the base to the shipping skid. The feet are shipped in a cloth bag and can be quickly installed. It is not necessary to fasten the slicer down in ordinary service, as the cup-shaped rubber feet will keep it from slipping on the table. The oil for the transmission case is drained for ship- ping purposes and MUST be replaced before the machine is placed in operation. Tilt machine on side (panel side up), dis-assemble panel and remove oil level screw (5, Fig. 2). Next, use a medium sized funnel and pour entire contents of oil from can labeled “OIL FOR GEAR CASE.” With the machine on its feet, the oil should then be at the proper level at the oil level screw (5, Fig. 2). INSTRUCTIONS 1712 PL-8825 If cord and plug is not used with this machine, electrical connections should be made by qualified workmen who will observe all applicable Safety Codes and the National Electrical Code. Before making electrical connections, CHECK THE SPECIFICATIONS ON THE NAME PLATE (5, Fig. 1), TOMAKE SURE THEY AGREE WITH THOSE OF YOUR ELECTRICAL SERVICE. 2. THICKNESS OF SLICE: The knob or dial (3, Fig. 1) adjusts the thickness of the slices cut. The numbers on the dial do not indicate actual measurements, but are helpful in duplicating past performances. To obtain the maxi- mum slice thickness, it is necessary to turn the knob beyond one complete revolution. 3. SAFETY PRECAUTIONS: When not actually slicing, turn the slice adjust- ing knob clockwise as far as it will go. The gauge plate will then be in line with the edge of the cut- ting knife and guard it. 4. POWER CARRIAGE OPERATION: The model 1712 slicing machine is equipped with a dual (fast or slow) speed, power driven carriage, but when desired the carriage may be hand- Fig. 2 operated. The carriage driving arm operates when- ever the slicer motor is running. To connect the driving arm to the carriage, the operator should first pull the carriage toward the front (dial end) of the slicer. Next, lift the actuating mechanism lever (1, Fig. 2) to a point where it is locked by the lock- ing clip (2, Fig. 2). The lever drops the yoke (3, Fig. 2) to a position where it can be picked up by the engaging roller (4, Fig. 2). Push the carriage for- ward toward the knife approximately 2", where it will then be picked up automatically and operated by power. NOTE: Always pull the carriage to the front at end of its travel before engaging the carriage power drive. 4.1 Stopping the Carriage: To stop the carriage, either turn off the switch of the machine or release the carriage power drive by lightly tapping the locking clip (2, Fig. 2). If the locking clip is tapped when the carriage is at the end of its stroke closest to the oper- ator, the carriage will stop instantly. This eliminates carriage coasting which might give an uncertain stopping position. 1712 INSTRUCTIONS 4.2 Changing Carriage Speed: The carriage speed shift may be changed with machine running or not running and also with the carriage engaged or not engaged. Speeds are easily changed (when the carriage is moving or stopped) if there is no load on the diving key. The “no-load” condition on the diving key occurs at each end of the carriage stroke while machine is running or can be produced when the machine is stopped by moving the carriage slightly back and forth by hand. To shift from low speed to high speed, pull the knob (2, Fig. 1) of the shifter rod out- ward and upward. In order to shift from high speed to low speed push the shifter rod knob (2, Fig. 1) down, a spring then automatically ~ returns the shifter to its low speed position. 5. SLICING FOOD: 5.1 Use of the fence: The use of the fence (9, Fig. 1) can greatly improve the automatic operation of the slicer. It should be adjusted so that it comes close to the material being sliced without touching it. When thus adjusted, it keeps the material in proper position in the carriage tray on the return stroke, thereby insuring a straight, un- iform cut, even at high speeds. One or more fences can be used to provide chutes for slicing a multiple number of smaller objects (for example, the cutting of onion rings). 5.2 Meat Grip: The meat grip is made with an especially long travel so that it can back-up the largest pieces of material being cut. It can be rotated for use in any one of three positions, depending upon the space available as determined by the position of the fence. A detachable, double pronged meat holder may be used with the meat grip for holding material from the top to suit special con- ditions. The hub of the meat grip arm (6, Fig. 1) has a shape which prevents swinging the grip (8, Fig. 1) out of the carriage tray to a position where it could mar the finish of machine. Do not try to force this arm. The grip moves freely at the proper positions, and it must be at the top of the slide rod (7, Fig. 1) to swing clear of the tray. When the grip is not needed, move it out of the way by the follow- ing procedure: (ON \ “д \! | \ \; \ Cu ae у ` x # | Fig. 3 5.2.1 Lift the grip to the top of the slide rod (7, Fig. 1). 5.2.2 Swing the grip around as shown by arrow and broken line (A, Fig. 3). 5.2.3 Rotate the grip into a position that allows it to nest in the grip retaining clip (1, Fig. 3). 6. CLEANING & SANITIZING: Unplug electrical power cord and clean the surface of the machine daily. Make sure the knife guards are in place and the slice adjusting knob is turned clockwise as far as it will go when performing this operation. A lift lever (8, Fig. 2) with a pivoting foot (7, Fig. 2) is used to support the 1712 slicer while cleaning. Raise the lift lever past center to its forward position. With the lift lever in this raised locked position the foot will rest on the table or other slicer resting surface. Simply pull lift lever back to its retracted position after cleaning. CAUTION: Never operate slicer in the raised position. WARNING: Observe the same care while working around the knife that you would use with any sharp- edged tool. PROCEDURE: 6.1 Materials required: 6.1.1 Small plastic two compartment pail. 6.1.2 Clean cloths. 6.1.3 Cleaner (“Soilax” All Purpose Cleaner). 6.1.4 Sanitizer (‘Mikro-Klene” iodophor sant tizer). 6.2 Cleaning (using “Soilax” and “Mikro- Klene”): 6.2.1 Add two ounces of “Soilax” Al Purpose Cleaner to a gallon of hot water in wash side of two compartment pail. 6.2.2 Mix rinse solution by adding two teaspoons of ‘“Mikro-Klene” in one gallon of cool water in rinse side of pail. 6.2.3 Wipe off large scraps of meat soil 6.2.4 Dip cloth into cleaning solution, then wring out cloth. Wipe the entire outside of slicer with cloth. Be sure to CAREFULLY wipe the gauge plate. 6.2.5 Loosen the two retaining knobs (2 & 3, Fig. 4), rotate the front knife guard (1, Fig. 4) clockwise to clear slots at the screw heads and unhook from the stud (4, Fig. 4). Lift off guard. 6.2.6 After front guard is removed, the back guard (5, Fig. 4) can then be disassembled by unscrewing the knob (6, Fig. 4). 6.2.7 Carefully wash the front and rear of the knife with cloth that has been dipped in the cleaning solution. 6.2.8 Wash the front and back guards. 6.2.9 Rinsing and sanitizing can be done by going over all cleaned surfaces with a cloth 1 О 2 A Fig. 4 INSTRUCTIONS 1712 PT 3 iL + US > O © © < WS S № © <> «222777 Fig. 5 that has been soaked in “Mikro-Klene” rinse solution and wrung out enough so that the solution does not run over the machine but still leaves it wet. 6.2.10 Reassemble the back knife guard, then the front knife guard. In replacing the front knife guard, first hook the bottom clip over the necked diameter of the stud (4, Fig. 4) then drop the guard over the two round- nosed securing screws. This guard has been so designed, that if this procedure is follow- ed, the knife will not be damaged. 6.2.11 Allow all surfaces to dry. Do not wipe. Cover slicer until next use. 6.2.12 Cloth used for rinsing should be sent to laundry, or discarded. Wash out pails. CAUTION: Do NOT wash polished alumi- num parts in dish or pan washer. 7. SHARPENING: This machine is furnished with a Hobart “Stay- Sharp” stainless steel knife. It should be sharpened only when necessary. When not in use, hang the sharpening unit in the notch (5, Fig. 5) of the side panel. Use the thumb screw to secure the sharpener in position on the inside of the machine. The following sharpening procedure is recommended: 7.1 With the slice adjusting dial set at zero and the guards in place, wash all the grease from the exposed portion of the knife. 1712 INSTRUCTIONS Fig. 6 7.2 Remove the carriage (section 9) and set the slice adjusting dial at 50. 7.3 Remove the sharpener from its storage place. 7.4 Unscrew the thumb screw on the sharp- ener until the sharpener slips upward into the slot (4, Fig. 1) at the bottom of the gauge plate. Push the sharpener firmly upward with Fig. 7 the right hand, to remove any rocking tend- ency. Tighten the thumb screw with the left hand. 7.5 Start the motor. 7.6 Turn the slice adjusting knob (2, Fig. 7) slowly to the right. This will bring the grind- ing wheel into contact with the beveled side of the knife. 7.7 Stop knife and check to see if burr has started to develop on opposite face of knife. 7.8 As soon as burr appears depress truing wheel by pressing on plunger (1, Fig. 7) with right hand as shown. Grind and true simul- taneously for approximately 3 seconds. 7.9 Release truing wheel and back away grinder at the same time. 1 7 J 2 3 N N NM Fig. 8 7.10 Check to make sure that the characteristic grind marks (1, Fig. 6) are plainly visible on the ground surface, if not the grinding wheel is not cutting. (Many operators try to sharpen a knife with a grease-loaded stone which will not cut). 7.11 Stop the motor, remove the sharpener, turn the slice adjusting dial back to zero, and return the sharpener to its place on the inside of the side plate. 7.12 After sharpening; the slicer should be cleaned again to remove any dust, or dirt as a direct result of sharpening. NOTE: The adjustments on the sharpening unit are factory-set for best operation on the machine. 8. CARRIAGE BEARING ADJUSTMENT: 8.1 Turning the adjusting screw (7, Fig. 5) will regulate the amount of looseness (or play) in the carriage. This set screw changes the clearance between the “Rulon” plugs and the upper slide rod. NOTE: Excessive tighten- ing will cause needless friction on the upper slide rod. 8.2 To adjust the eccentric stud & brg. sub- assy. on the lower slide rod, loosen the locking nut (4, Fig. 5), then turn the ec- centric stud (3, Fig. 5) to suit. A proper setting may be reached by turning the ec- centric to a tight (or drag) position, then loosening so that outer race of ball bearing (2, Fig. 5) still turns on the lower slide rod, but with a minimum of bearing pressure. Excessive drag will be noted at the carriage if the bearing is overly tightened. When proper- ly adjusted, the carriage is free to glide on slide rods. Over a period of time it may be necessary to re-adjust bearing and/or rotate the slide rod to eliminate the effect of any flat on the rod. NOTE: The sleeve bearings are for alignment only. 9. CARRIAGE REMOVAL & ADJUSTMENT: The carriage tray assembly can be taken off as a unit by loosening the thumb screw (9, Fig. 5) and sliding the assembly out of the “V” support. Care should be used in order to prevent the tray from striking and damaging the knife edge. The carriage tray knife clearance may be changed by adjusting the self-locking set screw (1, Fig. 5) to suit. 10. WEAR ADJUSTMENT: After long service and many sharpenings of the knife, it may be necessary to adjust the gauge plate closer to the knife. Also the bevel on the worn knife may be changed. This work should be done by a Hobart Service Technician. Align gauge plate in plane with knife. Straight edge must lie flat across knife and gauge plate. 11. FRONT PLATE THRUST PLUG ADJUSTMENT: The front plate thrust plug (1, Fig. 8) is as- sembled in the center of the knife retaining screw. INSTRUCTIONS 1712 The end of this “Rulon” plug supports the front plate when a heavy load slides across it. To adjust the height of this plug, first dis-assemble the front plate (guard), then remove the hex head knife re- taining screw (2, Fig. 8). From the rear of this knife screw, adjust the set screw (3, Fig. 8), until the plug projects approximately 7/64" from the knife screw. If properly adjusted the thrust plug just clears or lightly touches (but must not raise) the front plate under normal operating conditions. If the plug (which is pressed into place) is adjusted too far forward, back up the set screw and press the plug back. 12. LUBRICATION: Very little lubrication is needed. Both the upper (8, Fig. 5) and lower (6, Fig. 5) slide rods are to be lubricated. Use a few drops of oil (Texas “Havoline” or equiv.) weekly on these slide rods. Add two drops of oil weekly to the top of the actuating block shaft. Keep the two gauge plate slide rods lubricated with a drop or two of tasteless oil (furnished) when re- quired. Keep the meat grip slide rod (7, Fig. 1) clean but do NOT lubricate it. The slicer power transmission, including the knife shaft drive and the speed change gears, are lubri- cated by a medium weight transmission oil circu- lated by a gear pump. The transmission was filled level at the oil level screw (5, Fig. 2) at the time of installation. To drain the oil, tilt the machine on its side (panel side up) and remove the drain screw (6, Fig. 2). Return machine to level position and oil will drain out. The motor bearings are grease-packed and sealed, making additional lubrication unnecessary. Bearings at the connecting points of the crank arm, connecting rod and engaging arm are self-lubricating porous bronze. However, it may be desirable to re-lubricate these bearings annually in order to replenish the lubricant. 13. MOTOR: No periodic service is required for the motor. 1712 REPLACEMENT PARTS 37 | 4 Turu 9 | | 33-31-35 12 a 30 - 31-32 pp L-1415 BASE UNIT REPLACEMENT PARTS 1712 ILLUS. PL-14152 PART NO. P-70238 SD-24-19 B-117579-1 B-117579-2 B-117578-1 SC-27-29 WL-10-1 FE-6-29 M-70021 WL-3-8 SC-9-70 M-88812-1 SC-37-85 WL-3-44 M-83681 B-117632 BF-2-1 B-105598 SC-9-49 NS-31-10 SC-7-82 M-86163-1 A-103912 M-88812-2 SC-9-82 P-87711-99-1 B-103914 5С-9-61 M-88733-1 M-88733-2 B-114767 B-87711-145-1 B-120857 A-105599 S-84067 SC-10-32 A-117718 A-106503 D-106504 SD-24-15 B-106501 PG-740 A-108001 A-106502 A-106505 BASE UNIT NAME OF PART Motor (See separate Motor Parts Sheet) Cover - Bearing Bracket Self-Tapping Screw - #8-32 x 3/8" Truss Hd. “Taptite” Cord & Plug Assy. (3 Cond. under 150 V.) (Ground) Cord & Plug Assy. (3 Cond. 200-250 V.) (Ground) Cord Assy. (I.E.C.) Mach. Screw - #8-32 x 3/8" Rd. Hd. Lock Washer - #8 Ext. Shakeproof Nut - Wire Cover - Junction Box -——+—+ on oo Lock Washer - #6 x .047" x .031” Mach. Screw - #6-32 x 1/4” Rd. Hd. Sub-Base & Bushing Sub-Assy. Fin. Bolt - §/16"-18 x 1” Hex Hd. Lock Washer - 5/16" x .125" x .078" Foot Tubing Bushing - 3/8" Anti-Short Cover - Switch Box Mach. Screw - #6-32 x 3/8" Rd. Hd. (cover to switch) Stop Nut - #10-24 “Elastic” Mach. Screw - #10-24 x 3/4" Rd. Hd. Knob - Switch Rod Rod - Switch Sub-Base & Bushing Sub-Assy. Mach. Screw - #8-32 x 5/16” Rd. Hd. (switch to base) Switch - Tumbler Cover - Switch Box Mach. Screw - #8-32 x 1/2" Rd. Hd. (cover to base) Pilot Light & Terminal Assy. (with nut) (115 V.) —=-———————— Pilot Light & Terminal Assy. (with nut) (230 М.) ———— Pilot Light & Terminal Assy. (with nut) (230 V.) —-=————————— Switch (with nuts) ————— —— Insulator - Switch Plug - 3/4" Dia. Panel - Side —————————— aaa Mach. Screw - #8-32 x 3/8" Truss Hd. Base & Name Plate Sub-Assy. Knob - Lifting Lever Lever - Lifting Self-Tapping Screw - 1/4"-20 x 3/4" Hex Washer Hd. “Taptite” Retainer - Lifting Lever Groov-Pin - Type #5, 1/16” x 9/16" Foot - Lifting Lever Push Nut Lever & Foot Sub-Assy. (Incls. items #39, 40, 43, 44 & 45) *1 Phase ONLY. **3 Phase ONLY. 1712 REPLACEMENT PARTS J N —— ~——— 34 33 32 3130 29 [PL-12599] KNIFE UNIT — 10 — REPLACEMENT PARTS 1712 KNIFE UNIT ILLUS. PART PL-12599 NO. NAME OF PART AMT. 1 R-12430-3 Key - ---\0-——- ts 1 2 M-70406 Worm (ST) -=-------"""—e 1 3 M-73348 Key - Special Woodruff —— ee moo ooo = 1 4 NS-32-29 Stop Nut - 1/27-20 “Flexloc” —-— AAA = ее 1 5 WS-8-9 Washer ———————— еее AA 1 6 M-70302 Gear - Knife Shaft Worm (24T) ———————————— —— 1 7 V-104001 Washer - Thrust —————— еее ————————— 1 8 BB-18-43 Ball Bearing - Hoover #9204 —-——-—-——————————— = 1 9 Р-70435 Knife Shaft & Dowel Sub-Assy. oe неее 1 10 P-118484 Screw - Back Knife Guard Retaining —-—----ee moo oo] 11 RR-10-18 Retaining Ring ———————— eo ooo 1 12 S-82952 Back - Knife Guard —-————-—— === неее 1 13 P-70196 Stud - Upper Knife Guard —=——- mmo — 1 14 R-83023 Knife Guard & Knob Assy, ———— nim ooo a a ООН 1 15 E-70231 Knife --—— moe ee == 1 16 BB-16-22 Ball Bearing - Fafnir #205kL +++ = 1 17 М-73355 Screw - Knife --\——-—--—— ovo] 18 M-73265 Plug - Plate Thrust —--—--——+-—--“+-+--—+ = еее ое — — 1 19 SC-644 Set Screw - 1/4"-28 x 3/8" Hdls., Flat Pt. “Nylok” ————- ~~~ ~~ 1 20 B-111154 Ring - Knife Shaft ———————— o AA нон 1 21 SC-12-34 Mach. Screw - 1/4"-20 x 1-3/8” Fil. Hd. ——---—-————- = — === = — 4 22 Р-88726 Knife Shaft Hub & Insert Assy. ——— ] 23 P-70348 Knife Shaft & Hub Assy. (Incls. items #3, 4, 5, 6, 7, 8, 9, 16, 20 & 22) —————— 1 24 M-70241 Stud - Center Knife Guard ~—————-—---- vo mm 1 25 P-70198 Lock Nut - Center Stud ——— + —— oo — — = e Q 26 M-83021 Stud - Lower Retaining Clip ———------------ no] 27 WL-7-15 Lock Washer - 1/4" Ext. Shakeproof ————————————-——--—-=-—--=------- | 28 NS-17-1 Jam Nut - 1/4-20 Hex Fin. ——--—--------=-=-=-===== | 29 NS-32-23 Stop Nut - 7/16"-20 “Flexlo¢” — ~~~ ooo ooo] 30 WS-7-50 Washer —-——- 1 31 V-17778-3 Washer - Shock (29/64" ID) mo] 32 V-17778-2 Washer - Shock (41/64 I.D.) —-------—--—----===--===== 1 33 V-17771-2 Retainer - Shock Washer (41/64 I.D.) —--—--—--—---==-=== m] 34 P-70239 Conveyor - Oil ——-—-————————-—-- AAA ео 1 1 M-73356 Knife Screw Assy. (Incls, items #17, 18 & 19) ————————— A „11 - 1712 REPLACEMENT PARTS PL-14153 CARRIAGE UNIT ~ 12 — REPLACEMENT PARTS 1712 CARRIAGE UNIT ILLUS. PART PL-14153 NO. NAME OF PART AMT. *1 P-70194 Handle - Carriage Tray —-—- oo 1 *2 R-75930 Plate - Pusher —-———-————-—------=-=- === неее 1 *3 M-75945 Pusher Plate 8 Handle Assy. (Incls. items +1 & 23) -—--———————————-———————— 1 *4 D-118332-1 Tube & Angled Seat Assy. — —\————— oe —— 1 *5 А-107364 Washer ————————-—-——-—-—------- ss 2 *6 C-108197-13 Thumb Screw —————— oo 1 7 B-111038-1 Carriage Fence & Thumb Screw Assy. (Incls. item #9) — —— 1 8 B-111038-2 High Fence & Thumb Screw Assy. (Horizontal Carriage Tray) (Incls. item #9) —————— 2 9 M-70448 Thumb Screw - Fence -—-—————-—o ooo неее l 10 R-77534 Meat Grip Sub-Assy. === o —— - 1 11 P-70341 Meat Holder - Meat Grip @---—----—--"+""ooo oo 2 12 M-70386 Washer --—\—-————— IA es 1 13 M-70387 washer - Handle @~N -1»—--——-— oi 1 14 P-70202 Handle - Meat Grip —--—-—-——-—-——-—----------=- 1 15 M-70344 Washer - Handle Tension oo —— 1 16 M-70345 Washer - Handle Retaining --——-——----veev 1 17 М-68042 Screw - Truss Hd. “Nylok” ———————— in == 1 18 SC-16-5 Mach. Screw - 1/4"-20 x 5/8 Oval Hd. —————— —— —— (— === —-——— l 19 M-70305 Washer - Meat Grip Retaining —— vo 1 20 WL-6-16 Lock Washer - 1/4" x .107" x 047" —— —— —— — — 1 21 M-75138 Meat Grip Arm € Brg. Sub-Assy. (Incls. item #22) —— ————— 1 22 M-75135 Bearing - Meat Grip Arm ——-————-— o —— 2 23 M-72579 Clip - Meat Grip Retaining oe 1 24 M-68042 Screw - Truss Hd. “NylokK” ————————-——————-—- 2 25 M-72758 Carriage Tray & Slide Rod Sub-Assy. ———— ove in i e oo 1 26 M-74027 Horizontal Carriage Tray & Slide Rod Sub-Assy. ovo __ 1 27 SC-64-15 Set Screw - 1/4"-20 х 1/2” На№., Оха! Р!. “Му1юК” ————————-——————-—-—----_— 1 28 A-107364 Washer - Belleville —— es 2 29 C-108197-5 Thumb Screw ooo IA 1 30 P-70194 Handle - Carriage Tray ——-——----"---ooo неее 1 31 R-88749 Carriage Support & Plug Assy. (Incls. items #27 & 30) —\——— 1 32 М-86260 Adjusting Screw - “Nylok” + cero 1 33 SC-37-21 Fin. Bolt - 1/2"-13 x 1-1/2" Hex Hd. ++ 1 34 WL+4-35 Lock Washer - 1/2" x .170" x 099" —\——— —— ss 1 35 V-10928-2 Nut ———— 1 неее неее 1 36 ВВ -4-11 Ball Bearing - Hoover #77036 —— 1 37 M-20622 Spring - Bumper -————————— 2 38 V-21046-1 Washer - Bumper i ooo css 2 39 V-12734 Spring - Slide Rod End --—-—-—-—-—-—------------—- = 2 40 RR-9-15 Retaining Ring —— ee see —— 1 41 B-109870 Stud - Eccentric === o_o 1 42 R-114022 Carriage Bearing Sub-Assy. (Incls. item 432) : =-—-—-—-—-—-------------------- 1 43 M-75052 Slide Rod & Cap Assy. (Incls. item #44) nn 1 44 M-74908 Cap - Slide Rod — io 2 45 V-24094 Ке!аиипр Кр —— on oo —— Q 46 M-75052 Slide Rod & Cap Assy. (Incls. item #44) — + + oo 1] 47 M-83416 Png -———---—-----—-ao A 2 M-86262 Eccentric Stud, Brg. & Nut Sub-Assy. (Incls. items #35, 36, 40 € 41) -—-—--————— 1 *B-118337 Food Chute Attachment Assy. (Incls. items #3, 4, 5 & 6) —————-———--- ———— ] B-103732-1 Carriage Tray, Meat Grip & Arm Sub-Assy. (Incls. items #10, 11, 12, 13, 14, 15, 16, 17, 18, 19, 20, 21, 23, 24, 25, 28 € 29) m 1 B-103733 Horizontal Carriage Tray, Meat Grip & Arm Sub-Assy. (Incls. items #10, u 12, ‚13, 14, 15, 16, 17, 18, 19, 20, 21, 23, 24, 26, 28 € 29) —-—-—-————————-———- = 1 *Attachment Chute (Special, used in place of Carriage) 1712 REPLACEMENT PARTS og 71-72-73 74 GEAR CASE UNIT ILLUS. PART PL-8835 NO. NAME OF PART 1 RR4-17 Retaining Ring -- ---- -- - - - --»-»- oi ie еее 2 WS-7-21 Washer Az ——— 3 R-70259 Engaging Arm Assy. —————————————— II 4 M-70283 Washer - Pivot Shaft Thrust -——————— or oo oo ooo 5 RR4-3 Retaining Ring —-————————-—-—-—-—-—-—-————- те 6 М-70303 Roller - Engaging Mech, zz 7 M-70295 Shaft - Engaging Mech, -——+————-— ve еее 8 M-70396 Ring - Stop Retaining s: —-———-—-—-——--->->-->->------------sssssss— 9 M-70324 Stop - Engaging Mech. Shaft —--------—+"o---—-—-——+—+°- еее 10 M-70307 Spring - Engaging Mech, -=-—-———--—----------=--------------sssssss 11 SC-9-28 Mach. Screw - #10-24 x 3/8” Rd. Hd. -=-—-——-—-—-—-—-------—--------------- 12 B-103915 Cover Plate - Connecting Rod —-—-—-—-—-—-—-—-—-—-—-—----—------—— = 13 Р-70268 Connecting Rod Assy. ——— неее = > = A REPLACEMENT PARTS 1712 ILLUS. PL-8835 PART NO. WS-8-9 WS-8-8 WS-7-21 RR4-17 RP-2-46 M-70293 M-70290 M-70442 SC-14-76 P-70234 M-70244 C-70243 C-70242 D-11800-200 BN-2-13 SC-62-68 WS-21-21 M-64465-3 WS-21-20 SC-63-14 NS-32-1 M-70285 M-70446 M-70286 NS-9-30 M-70296 RP-2-28 D-675 00-2 R-12430-3 M-61654 M-61655 P-70267 BN-2-15 M-70281 M-70274 R-72715 R-70170 C-106936 C-114356 M-70308 M-61656 BN-2-14 WL-3-37 SC-36-6 R-70156 BB-15-37 B-116714 RP-3-8 C-70159 SC-11-17 WL-3-21 D-72716 M-70248 M-70275 RP-3-12 M-70283 WL-344 SC-37-85 SC-11-96 SC-62-35 M-72138 R-72714 A-106933 GEAR CASE UNIT (Cont.) NAME OF PART Washer Washer Washer Retaining Ring — + —— — отно Rollpin - 1/4” Dia. x 1-1/4" Lg. ————— еее mm Arm - Crank Washer - Crank Arm Thrust -——————————— = еее Seal - Drive Shaft ----- еее ноет о ——— Mach. Screw - #10-24 x 3/8” Flat Hd. Cover - Gear Pump Bottom ~--- -- - - - -\ - - - - - - -\ - --\ -\ +: :.\ oo oo Gasket - Bottom Cover Gear - Oil Pump Driven 277) zz Gear - Oil Pump Idler (271) Dowel Needle Bearing - Torrington #B-86 Fin. Bolt - 1/27-20 x 3/4” Hex Hd. Washer Plug - Oil Fill Washer Set Screw - #8-32 x 1/4" Hdls., Flat Pt. Stop Nut - 4+10-24 “Flexloc” Spring - Shifter Mech. Shift Rod, Selector & Knob Assy. Knuckle - Shifter Mach. Nut - #10-32 Hex Bracket - Shifter Rollpin - 3/16" Dia. x 3/4" Lg. “O” Ring keys =-—-------- Yoke - Shifter Shoe - Shifter Shaft - shifter —-——————-—--—------------------------------ Needle Bearing - Torrington #B-126 Washer - Gear Thrust -————------------------------------- Collar - Diving Key Сеаг - ОЭпуеп (119Т) ———————————— ——— —-— —— Gear - Driven (12047) ———————————— im — ———— Shaft - Crank Arm Drive Key - Diving Spring - Diving Key Sleeve - Clutch Shifter Needle Bearing - Torrington #M-881 Lock Washer - 1/4” x 109" x 062" —————— —— roi i i => Fin. Bolt - 1/4”-20 x 1” Hex Hd. Carrier - Pinion Shaft Bearing Ball Bearing - N.D. #3103 Retainer - Bearing Rollpin - 3/16" Dja. x 1-1/8" Lg, ———————— ooo Gear - Worm (297) Mach. Screw - #10-24 x 1/2” Fil. Hd. Lock Washer - #10 x .047" х .047" ooo Shaft - Pinion (19T & 14T) Fitting & Oil Tube Assy. Collar - Pivot Shaft Thrust Rollpin - 1/8" Dia. x 1-1/4" Lg. Washer - Thrust Lock Washer - 5/16" x .125” x .078” Fin. Bolt - 5/16"-18 x 1” Hex Hd. Mach. Screw - 5/16"-18 x 1” Fil. Hd. Fin. Bolt - 5/167-18 x 3” Hex Hd. Gear Case, Bearing & Dowel Sub-Assy. (Incls, item #21) Brg. Carrier, Pinion Shaft & Gear Assy. (Incls. items #58, 59, 60, 61, 62, 63, 64 & 65) ———-- Drive Shaft Sub-Assy. (Incls. items #51, 52, 53 & 54) — —— — A —— _—]_—— —_— —_—]— ———— — — —] _] ——] —— — —— —— 00 pm — et — — 0 ——oo—]_—_——]———] ———_—_——— —— — ен —— —— —— о —— — —]—] ][—Ú—— — — —— ен о ен не a ое Не не о он ен = — — оне —]]—— — ее не ее = еее ео не ое еее ее ен ееен не ео = ое ее == === = = еее —— an — — — — ——— —— === === == = ——] ———][— — = м неее ее еее ее ее нею еее еее = еее = == === еее ое — — = = —— — —— — — 15 — TS 2% uu ik 2 7 al le Ny el e 7 a Ala a o e > EE “ e 6 dis 4 — — vw a e e A 3 y UL ÿ — 7 er 7 e TT A ий A de 4 tel ” и il 7 e iL ll e e ori 7 20 LA GE TE AND INDEXI NG H JE EN > x REPLACEMENT PARTS 1712 ILLUS. PL-14154 PART NO. NS-32-12 M-70425 V-20610 SC-8-14 M-70343 5С-63-28 NS-17-1 M-87495 RP-2-22 M-88298 M-87494 V-10928-2 V-10928-2 M-70405 V-10928-2 S-70205 SC-16-22 B-112913 P-88740 E-109656 M-87493 GAUGE PLATE AND INDEXING MECH. NAME OF PART Stop Nut - 5/16"-18 “Flexloc” —~——————————— Indexing Plate, Roller, Collar € Stud Assy. —————— Spring - Indexing Plate —————————______ Mach. Screw - #10-32 x 3/16” Rd. Hd. —-—-—-—-—-——— Roller - Indexing Plate (Straight) ———————————— Set Screw - 1/4"-20 x 1” Hdis., Flat Pt. Jam Nut - 1/4"-20 Hex Fin. Worm - Indexing ----—-———————-—————————— Rollpin - 5/32" Dia. x 3/4" Lg. ———————————— Washer - Bellevile —— Shaft - Indexing ———---—-cee Nut - Special + Nut - Special o-oo Disc - Indexing Drive —————— oo Nut - Special @——————o— Knob - Indexing —-—————-————————-——-——————— Mach. Screw - #10-24 x 7/8” Oval Hd. ———————— Self-Tapping Screw - 3/8"-16 x 2” Hex Washer Hd. “Taptite” Gauge Plate Support & Slide Rod Assy. (Incls. Rods & Groov-Pins) ———————— Plate - Gauge —\———— —— —— — — — Indexing Shaft & Worm Assy. (Incls. items #8, 9 & 11) — 17 — 1712 REPLACEMENT PARTS ACTUATING MECH. UNIT ILLUS. PART PL-14312 NO. NAME OF PART 1 D-11800-137 Powers =-----—-—-"—-"—— SC-37-75 Fin. Bolt - 5/16"-18 x 3/4" Hex Hd. —+——-——-——-—-—-—-—---—----—-=---——------—- 3 WL-344 Lock Washer - 5/16" x .125" x 078 : -—-—-—-—-—-—-—-—-—"—-—-----——_—— 4 P-83424 Base and Brg. Sub-Assy. -——————-—+—— oo — 5 WS-2-43 Washer —————————-——-——--------=-- II 6 P-70240 Clip - Locking —-———-——-------------------------------eesssss 7 M-70351 Screw - Special =-—-———-—-------------------------------s--s--s-- 8 R-70233 Lever - Actuating Mech, —-—-— oon oo 9 M-70245 Clip - Lever Wear ——— ~~ oo 10 M-70297 Pin - Hinge -----------——--- ~~ 11 PC-3-23 Cotter Pin - 1/16" x 1/2" vii i 12 SC-60-21 Mach. Screw - #10-24 х 1/4" Ва. На. —————— i —_— 13 М-70399 Spring - Actuating Mech, ——---—--—+-+"éie 0 — нон 14 B-118161 Dowel - Yoke & Shaft Locating ----—————-——-—v — —— 15 SC-60-20 Mach. Screw - #10-24 x 1” Rd. Hd. —— oo ————— 16 P-70266 Yoke & Shaft Assy, ———-——————-—--—-—-------==- === ———— — 18 — REPLACEMENT PARTS 1712 KNIFE SHARPENER UNIT ILLUS. PART PL-8838 NO. NAME OF PART AMT. 1 M-74833 Screw - Retaining -———————————+—-——- — ——. 1 2 M-73851 Wheel - Grinding ——-—-——--—-iov i; 1 3 M-74900 Shaft - Grinding Wheel -—\-—-———-—+-—+—"ooio veo 1 4 P-22670 Carrier - Grinding Wheel] ~—————+-——c oe ie ——— 1 5 WS-2-18 washer -————--—-oii i III 2 6 SC-8-10 Mach. Screw - #10-24 x 1/2” Rd. Hd, ————-—-o 2 7 WS-3-40 washer -—-———-———r—-—ri—— i III 1 8 BA-2-1 Ball - 1/8” Dia, ori iii i iii 9 9 V-13199 Collar - Thrust ———————————— II 1 10 РС-3-7 Groov-Pin - Type #1, 3/32" x 7/16" — +" 1 11 M-72801 Sharpener Support & Slice Indicator Plate Sub-Assy, ———————— ooo _ 1 12 M-69585-1 Plug Button III 1 13 M-83089 Retaining Ring ————————-————— ------------------------- 1 14 M-73974 Cap - Truing Wheel ————--oe oo 1 15 WS-2-18 Washer ————————————-- —— 2 16 BA-2-1 Ball - 1/8” Dia, — —————-——-—-—---=----=---= 7 17 WS-4-39 Washer ————————-——-——---- eL III 1 18 M-70313 Spring - Truing Wheel Load ———————————————- === ss esse 1 19 SC-8-10 Mach. Screw - #10-24 x 1/2” Rd, Hd. ———————— ee 2 20 WS-2-18 Washer AI 2 21 M-73975 Carrier - Truing Wheel --——-—1+—+—+ oo 1 22 M-83092 Shaft - Truing Wheel ——~———— «ooo === 1 23 M-13201 Wheel - Trying ———————-————— oo 1 24 M-3404-7 Screw - Retaining —————————————-— ee 1 25 B-109702 Thumb Screw - Sharpener Attaching -————————-—oee 1 R-74023-2 Knife Sharpener Assy. (Incls. items 41 thru 25) ———-—— vo —— 1 M-73979 Truing Wheel Sub-Assy. (Incls, items #12, 13, 14, 15, 16, 17, 18, 21, 22, 23 & 24) —————— 1 M-74007 Grinding Wheel Sub-Assy. (Incls. items #1, 2, 3, 4, 7, 8, 9 & 10) —————————— 1 — 19 — 1712 INSTALLATION 0960.-S [2686-14] ai y el n£ 1333 401 8 | I, 3SV8 ans JO Y3NHOO HOV3 | A 57 iv SONT HOIHL ,2/1 NYHL \ ; 08-471 G3ddvi STIOH Uñ03 | 4 у / H / | / » | / - £2 5 ve 7 Ш — 9¢ 8 =2 — he — oi fe 8 \ | Ë Ai <2 — o] | ail С << TEC \ ~~ 5NOT 135 0805 o! ОЙ \ =62 \ | € Na | \ 7 | N / | ~~ NU _ él | " ~ > INSTALLATION DIAGRAM NOV. 1976 PRINTED IN U.S.A. FORM 11732A
advertisement