advertisement
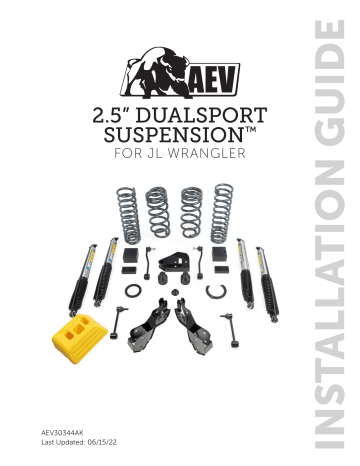
2.5” DUALSPORT
SUSPENSION
™
FOR JL WRANGLER
AEV30344AK
Last Updated: 06/15/22
PLEASE READ BEFORE YOU START
To guarantee a quality installation, we recommend reading these instructions thoroughly before beginning any work. These instructions assume a certain amount of mechanical ability and are not written nor intended for someone not familiar with auto repair.
INCLUDED PARTS
Springs
Shocks
Front Sway Bar End Links
Rear Sway Bar End Links
Front Upper Bumpstop Spacer
Rear Lower Bumpstop Spacer
Rear Sway Bar Spacer
Front Spring Shim
Rear Spring Shim
Rear Track Bar Tower Bracket
Track Bar Tower Alignment Puck
Geometry Correction Bracket Kit
Hardware Pack
AEV Jack Base
QTY
2
2
2
4
4
2
2
1
1
1
1
1
1
1
REQUIRED TOOLS
Basic Standard and Metric
Hand Tools
Torque Wrench
Jack and Jack Stands
Vehicle Applications: 2018-Current Jeep JL Wrangler and Unlimited
Vehicle Assumptions: Stock JL frame and axles with all stock brackets intact Stock Front and Rear Driveshafts
NOTE : Aftermarket units with double-Cardan joints will require a rear axle pinion angle adjustment that is NOT provided in these systems.
NOTE: 32–35 PSI is AEV’s recommended tire pressure with our DualSport Suspension TM Systems.
Aftermarket Wheels: These are recommended both for adequate width to mount large tires and decreased backspacing for chassis and steering clearance. AEV JL wheels are optimized to work with this suspension system for maximum clearance to chassis components and vehicle body/flares.
NOTE : Wheels with extremely negative offset may negatively affect ESP.
Install Time: Approximately 5 hours.
iii
REAR SUSPENSION
1. Raise Jeep and support the frame using jack stands or a hoist, such that the rear axle can be lowered enough to remove the springs. Support the axle by placing the floor jack under the center of the axle.
Remove the wheels. (Fig. 1)
2. Remove the shocks and save hardware (Fig. 2).
Figure 1
*Refer to Appendix for proper torque specs
Figure 2
1
3. Loosen but DO NOT remove all 8 control arm bolts and both track bar bolts (Fig. 3).
Figure 3A: Control Arm Bolts (Left Side Shown)
Figure 3B: Track Bar: Axle Side (left) Frame Side (right)
*Refer to Appendix for proper torque specs
2
4. Remove the sway bar end links and save mounting hardware. 392 vehicles will re-use end links .
Note the orientation of the end links, the new end links will be installed in the same way (see Fig. 2).
Gas engine vehicles only: Remove the sway bar from the frame and discard hardware (see note below for 392 Hemi models). Reinstall in same orientation using supplied M10 bolts and spacer blocks between sway bar mounting brackets and frame. Torque to 50 ft-lb. (Fig 4)
392 Hemi vehicles only: In addition to sway bar spacers noted above, sway bar also needs to be flipped in vehicle. The saddle block brackets and bushings do not need to be removed. Flip the bar along the vehicle axis(driver side of bar will become passenger side of bar and vice versa), then rotate bushings and brackets onto bar so it can be mounted in this new orientation. Flipping the bar will lower the arms that attach to the endlinks and prevent contact with wheel/tire at full suspension rebound.
EcoDiesel vehicles only: Mark hole 1” above existing endlink holes on axle brackets and drill new 1/2” hole in that location on both sides of vehicle. This is required because the DEF tank does not allow the sway bar to be lowered like the gas engine vehicles (fig. 5).
Figure 4: Gas Engine Vehicles Only
3
*Refer to Appendix for proper torque specs
Figure 5: EcoDiesel Vehicles Only
5. Carefully lower the axle using the floor jack enough to remove the springs. DO NOT overextend the wheel speed sensor, locker wiring, or e-brake cables. We recommend detaching the plastic fir tree cable ties from the axle and frame to allow sufficient movement. This pertains to wheel speed wiring and locker wiring if equipped. RH e-brake cable will be tight but does not need to be disconnected to remove/install springs.
6. Remove the factory springs.
7. Install rear track bar tower. NOTE: Not used on 392 Hemi models due to raised factory mount. Skip to step 8.
A. Disconnect axle end of track bar and save hardware NOTE: Not used on Ecodiesel, proceed to step 8-B.
B. Install the track bar tower in the orientation shown (Fig 6).
B
C
Figure 6
C. Place supplied tube spacer between AEV bracket and factory axle bracket in original track bar location.
Reuse factory bolt in this location (Fig 6-B).
4
*Refer to Appendix for proper torque specs
D. Install alignment puck into back side of factory axle bracket(side facing toward front of vehicle) and through the lower tube on track bar tower. Some resistance is normal to fully seat the alignment puck.
Install M12x90mm bolt and washer from outer side of bracket, through alignment puck, and install flange nut (Fig 6-C). Nut may need to be tightened to fully seat alignment puck.
E. Reinstall track bar to top hole using supplied M14 hardware (Fig 7).
F. Tighten bottom M14* and M12*. Do not tighten track bar bolts yet.
NOTE : There’s an extra hole on the outboard side of the track bar tower. Testing has shown this is not necessary, but if desired you can drill through the factory bracket and add an additional bolt here. Hardware is not provided for this location (Fig 7).
NOTE
Figure 7
8. Install springs.
A. Install rear spring shim to passenger side axle spring seat (Fig 7). JL has more weight on right side of vehicle than left, so this helps it sit level. Shim sits on top of isolator on axle.
*Refer to Appendix for proper torque specs
Figure 7
5
B. Install rear AEV springs making sure to properly index them on the upper isolators. If the isolators fall out during assembly or disassembly, reinstall them by making sure the top locating post passes through the hole in the frame pad.
9. Install new rear shocks at upper mount using factory hardware (5100 PN 33-310480). NOTE: Refer to separate XP8100 big bore shock instructions if using those. Shock body sits at the top with AEV graphic facing outward at vehicle (Fig 9).
Figure 9
10. Raise axle slowly and guide springs into position.
11. Re-install lower shock nut and bolt and tighten* (Fig 10). Install AEV sway bar end links (the longer of the 2 versions supplied in the kit) using factory hardware and tighten* (see Fig 2).
Figure 10
12. Rear bump stop spacers will not be installed until after control arms are torqued at ride height.
13. Reinstall wheels and tighten lug nuts, working in a star pattern.*
It is time to install the front suspension, however DO NOT tighten track bar or control arms at this time.
These will be torqued AFTER the front suspension is complete.
6
*Refer to Appendix for proper torque specs
FRONT SUSPENSION
1. Raise Jeep and support the frame using jack stands or a hoist, such that the front axle can be lowered enough to remove the springs. Support the axle by placing the floor jack under the center of the axle.
Remove the wheels.
2. Loosen but DO NOT remove all 8 control arm bolts (Fig 11).
Figure 11: Frame-side (left) Axle-side (right)
3. Loosen but DO NOT remove both track bar bolts (Fig 12).
Figure 12: Axle-side (left) Frame-side (right)
4. Disconnect brake line brackets at frame, electrical connector for axle disconnect, and push fastener for axle disconnect to allow extra droop (Fig 13).
Figure 13: Brake Line Bracket (left) Axle Disconnect (right)
*Refer to Appendix for proper torque specs
7
5. Remove both sway bar links and hardware, save hardware. Note orientation, new links will be installed in the same way (Fig 14).
Figure 14
6. Remove shocks and save all shock mounting hardware.
7. IMPORTANT STEP PLEASE FOLLOW CLOSELY . Bend brake line brackets on lower control arms flat/up to allow extra travel relative to frame (Fig 15). Be sure to check brake line to control arm clearance again at ride height. Bracket can be adjusted further to ensure proper clearance; see page 11 step 17. On vehicles that will be rock crawling, AEV suggests trimming off the bottom tab of these brackets below the mounting hole to eliminate a snag point.
Figure 15: Before (left) After (right)
8. Lower axle and remove springs. DO NOT remove factory isolator.
TRIM (OPTIONAL)
8
*Refer to Appendix for proper torque specs
TRIM (OPTIONAL)
9. Install upper bumpstop extensions. NOTE: 392 vehicles DO NOT receive bumpstop extensions.
A. Remove urethane bumpstops from inside spring towers. These simply press into place, so remove them by wiggling them downward and sideways, or carefully prying with large channel locks (Fig 16).
B. Reinstall urethane bumpstops into new aluminum extensions (Fig 17). Lube them with glass cleaner or detergent to make install easier.
Figure 16
C. Install extensions into factory bumpstop mounts. Using magnet or socket extension, install M12x25 flange bolt from top of spring tower (Fig 17). Torque bolts to 40 ft-lb
*Refer to Appendix for proper torque specs
Figure 17
9
10. Install springs
A. Remove passenger lower spring isolator by carefully prying it upward away from axle. Install front spring shim to bottom of isolator, passing molded stud through hole in shim. Reinstall assembly onto axle spring seat (Fig 18). JL has more weight on right side of vehicle than left, so this helps it sit level.
Shim sits underneath isolator on axle. NOTE: Not used on Ecodiesel. Proceed to step 10-B.
Figure 18
B. Install Front AEV springs making sure to properly index them on the lower isolators. Be careful the springs don’t snag the thin outer lip of the isolators. If the upper isolators fall out during assembly or disassembly, reinstall them by making sure the top locating posts pass through the holes in the spring tower. Raise axle to retain springs in place.
11. Install new front shocks at upper and lower mounts using factory hardware (PN 33-310473). Shock body sits at the top with AEV graphic facing outward from vehicle.
12. Install sway bar end links
A. For each side attach the upper end stud to the sway bar in the same manner as the original front links had been (nut on frame side of bar). NOTE: The upper stud has a different thread than the rest of the
M12 fasteners in the suspension—it is a “standard” pitch versus a “fine pitch.” Tighten to 40 ft-lbs. (Fig. 19).
B. The lower ends of the links will attach in the factory location using the original hardware, with AEVprovided washer added to the inboard side of driver side link only (Fig 19). Washer is not needed on passenger side because it has brackets on both sides of bushing. Torque to 40 ft-lbs.
M12 Washer
M12 Washer
Figure 19
10
*Refer to Appendix for proper torque specs
13. Reinstall wheels and tighten lug nuts, working in a “star pattern.”
14. Install Stamped Geometry Correction Brackets (refer to the Instructions for this product, pn:AEV30413)
NOTE: If the Jeep has an aftermarket front driveshaft and/or is going to be used for significant rock-crawling, it is recommended to swap the upper control arms side-to-side. They are normally bent down and inboard to clear the frame, but once lifted this bend gets closer to the front axle pinion/yoke on the driver’s side.
Swapping is possible once lifted and will improve clearance to the pinion yoke area. The control arms are switched between sides and flipped. THIS STEP IS REQUIRED ON 392 Hemi models to clear the vibration damper on the pinion.
15. Install rear lower bumpstop spacers onto axle pads. Feed countersunk M10 bolts through spacers and existing holes in axle pads. Install flange nuts to bottom side of axle pads. Torque until there’s only slight deformation of material at top of holes in spacer blocks (Fig 20).
Figure 20
16. You may now tighten all fasteners to factory specifications.* Too tight is NOT just right.
17. IMPORTANT STEP PLEASE FOLLOW CLOSELY . With vehicle sitting at ride height, check clearance between brake hose and upper control arm. Minimum 3/4” gap should be maintained, too little clearance could allow rubbing of brake hose and eventual leak. If gap is too small, use a crescent wrench to twist rear edge of brake hose bracket on lower control arm and bracket mounted to the frame outward until desired clearance is met (fig. 21).
*Refer to Appendix for proper torque specs
3/4” MINIMUM GAP
Figure 21
11
TIP: It is good practice to mark each major bolted suspension connection such as these with a paint pen.
Draw a line that runs from bolt head or nut to the adjacent bracket material. This will allow a visual inspection to easily catch bolts that work loose. After approximately 100 miles, you should perform a complete visual inspection and re-torque any suspect bolts as well as your wheel lug nuts.
AEV recommends having a professional alignment done at this point.
AEV recommends the use of the provided ProCal SNAP to calibrate for the new tire size. Please follow the instructions that come with your ProCal SNAP.
AEV recommends 32–35 PSI tire pressure with our Suspension Systems.
*Refer to Appendix for proper torque specs
12
APPENDIX
JL FACTORY TORQUE SPECIFICATIONS
JOINT
Front UCA to Axle
Front UCA to Frame and AEV Brackets
Front LCA to Axle
Front LCA to Frame and AEV Brackets
Front Brake Hose to LCA
Front Track Bar to Axle
Front Track Bar to Frame
Front Sway Bar Link to Axle
Front Sway Bar Link to Sway Bar
Front Lower Shock to Axle
Front Upper Shock to Frame
Rear UCA to Axle
Rear UCA to Frame
Rear LCA to Axle
Rear LCA to Frame
Rear Track Bar to Axle and AEV Brackets
Rear Track Bar to Frame
Rear Sway Bar Link to Axle
Rear Sway Bar Link to Sway Bar
Rear Lower Shock to Axle
Rear Upper Shock to Frame
TORQUE (FT-LB)
80
80
190
190
60
75
80
95
15
110
110
60
90
60
50
75
120
90
90
90
80
13
advertisement
Related manuals
advertisement