advertisement
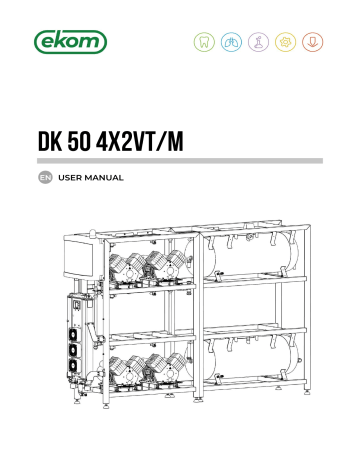
EN
USER MANUAL
DK50 4x2VT/M
DK50 6x2VT/M
COMPRESSOR DK50 4x2VT/M
EKOM spol. s r. o.
Priemyselná 5031/18
SK-
921 01 Piešťany
Slovak Republic tel.: +421 33 7967255 fax: +421 33 7967223 www.ekom.sk email: [email protected]
DATE OF LAST REVISION 10/2022
NP-DK50-Nx2VTM-ADM-
EN-3_10-2022
112000595-0001
CONTENTS
CONTENTS
IMPORTANT INFORMATION ....................................................................................................... 5
1.
CONFORMITY WITH THE REQUIREMENTS OF EUROPEAN UNION DIRECTIVES .... 5
2.
INTENDED USE .............................................................................................................. 5
3.
CONTRAINDICATIONS AND SIDE-EFFECTS ............................................................... 5
4.
SYMBOLS ....................................................................................................................... 5
5.
WARNINGS .................................................................................................................... 6
6.
STORAGE AND TRANSPORT CINDITIONS .................................................................. 8
PRODUCT DESCRIPTION ........................................................................................................... 9
7.
VARIANTS ...................................................................................................................... 9
8.
ACCESSORIES .............................................................................................................10
9.
PRODUCT FUNCTION ..................................................................................................11
TECHNICAL DATA ......................................................................................................................15
INSTALLATION ...........................................................................................................................22
10.
INSTALLATION CONDITIONS .......................................................................................22
11.
COMPRESSOR ASSEMBLY .........................................................................................23
12.
PNEUMATIC CONNECTION .........................................................................................26
13.
ELECTRICAL CONNECTION ........................................................................................28
14.
COMMISSIONING .........................................................................................................29
15.
PNEUMATC DIAGRAMS ...............................................................................................31
OPERATION ................................................................................................................................33
16.
SWITCHING THE COMPRESSOR ................................................................................33
17.
SWITCHING OFF THE COMPRESSOR ........................................................................36
AD DRYER ...................................................................................................................................37
18.
PRINCIPLE OF OPERATION .........................................................................................37
19.
USER INTERFACE / SETTINGS ....................................................................................38
20.
MAIN SCREENS ............................................................................................................40
21.
INDICATION OF MAINTENANCE AND ALARM STATES ..............................................42
PRODUCT MAINTENANCE ........................................................................................................44
22.
PRODUCT MAINTENANCE ...........................................................................................44
23.
LONG-TERM SHUTDOWN ............................................................................................51
24.
DISPOSAL OF DEVICE .................................................................................................51
TROUBLESHOOTING .................................................................................................................52
25.
REPAIR SERVICE .........................................................................................................54
ANNEX .........................................................................................................................................55
25.
INSTALLATION RECORD..............................................................................................55
NP-DK50-Nx2VTM-ADM-EN-3_10-2022 4 10/2022
IMPORTANT INFORMATION
IMPORTANT INFORMATION
1. CONFORMITY WITH THE REQUIREMENTS OF EUROPEAN UNION DIRECTIVES
This product conforms to the requirements of the Regulation (EU) on medical devices (MDR
2017/745) and is safe for the intended use if all safety instructions are followed.
2. INTENDED USE
The compressor is used as a source of clean, oil-free compressed air to power active medical devices where the parameters and properties of the compressed air are suitable for the specific application.
Compressed air supplied by the compressor is unsuitable for use with artificial lung ventilation devices without further filtration
3. CONTRAINDICATIONS AND SIDE-EFFECTS
There are no contraindications or side-effects known.
Any other use of the product beyond its intended use is considered an incorrect use.
The manufacturer is not liable for any damages or injuries resulting from the incorrect use.
4. SYMBOLS
The following symbols and marks are used in the User manual, on the device and its packaging:
General warning
Warning - risk of electric shock
Warning - compressor is controlled automatically
Warning - hot surface
General caution
Read the operating instructions
Refer to instruction manual
CE – marking
Medical device
Serial number
10/2022 5 NP-DK50-Nx2VTM-ADM-EN-3_10-2022
IMPORTANT INFORMATION
Protecting earthing
Terminal for ground connection
Alternating current
Package handling label – fragile
Package handling label – this side up
Package handling label – keep dry
Package handling label – temperature limits
Package handling label – limited stacking
Package label – recyclable material
Manufacturer
5. WARNINGS
The product is designed and manufactured to be safe for the user and the surrounding environment when used in the defined manner. Keep the following warnings in mind.
5.1. General warnings
READ THE USER MANUAL CAREFULLY
BEFORE USING THE DEVICE AND KEEP IT
FOR FUTURE USE!
The user manual supports the correct installation, operation and maintenance of the product. Careful review of this manual will provide the information necessary for the correct operation of the product for its intended use.
Original packaging should be retained for the return of the device. Only the original packaging ensures protection of the device during transport. If it is necessary to return the product during the warranty period, the manufacturer is not liable for damages caused by improper packaging.
NP-DK50-Nx2VTM-ADM-EN-3_10-2022 6
This warranty does not cover damages originating from the use of accessories other than those specified or recommended by the manufacturer.
The manufacturer only guarantees the safety, reliability and function of the device if:
- installation, new settings, changes, expansion, and repairs are performed by the manufacturer or an organisation authorised by the manufacturer
- the product is used pursuant to the user manual
The user manual corresponds to the configuration of the product and its compliance with the applicable safety and technical standards at the time of printing. The manufacturer reserves all rights for the protection of its configuration, methods and names.
Translation of the user manual is performed in accordance with the best available knowledge. The Slovak
10/2022
IMPORTANT INFORMATION version is to be used in the event of any uncertainties.
This user manual is the original instructions. Translation is performed in accordance with the best available knowledge.
5.2. General safety warnings
The manufacturer designed and manufactured the product to minimise all risks when used correctly for the intended use. The manufacturer considers it its obligation to lay down the following general safety precautions.
Use and operation of the product must comply with all laws and local regulations valid in the place of use.
The operator and user are responsible for following all the appropriate regulations in the interests of performing work safely.
Only the use of original parts guarantees the safety of operating personnel and the flawless operation of the product itself. Only the accessories and parts mentioned in the technical documentation or expressly approved by the manufacturer should be used.
The operator must ensure that the device is functioning correctly and safely before every use.
The user must be familiar with the operation of the device.
Do not use the product in environments with a risk of explosion.
The user must inform the supplier immediately if any problem directly related to the operation of the device occurs.
Any serious incident that has occurred in relation to the device should be reported to the manufacturer and the competent authority of the Member
State in which the user and / or patient is established.
5.3. Safety warnings on protection from electric current
The device must only be connected to a properly installed, earthed socket.
Before the product is plugged in, ensure that the mains voltage and frequency stated on the product are in compliance with the values of the mains.
Prior to putting the device into operation check for any damage to the connected pneumatic lines and electrical wiring. Replace damaged pneumatic lines and electrical wirings immediately.
Immediately disconnect the product from the mains (remove power cord from the socket) in hazardous situations or in the case of a technical malfunction.
During all repairs and maintenance, ensure that:
- the mains plug is removed from the power socket
- pressure is vented from the air tank and pipes
The product shall only be installed by a qualified technician.
10/2022 7 NP-DK50-Nx2VTM-ADM-EN-3_10-2022
IMPORTANT INFORMATION
6. STORAGE AND TRANSPORT CONDITIONS
The compressor is shipped from the manufacturer in transport packaging. This protects the product from damage during transport.
Potential for damage to pneumatic components.
The compressor must be transported only when all air has been vented. Before moving or transporting the compressor, release all the air pressure from the tank and pressure hoses and drain condensate from the tank and from the condensate separator on the dryer.
Keep the original factory packaging in case the device needs to be returned Use the original factory packaging during transport as it provides optimum protection for the product. . If it is necessary to return the product during the warranty period, the manufacturer is not liable for damages caused by improper packaging.
The compressor is shipped in a vertical position and must be secured using transport straps.
Protect the compressor from humid and dirty extreme near any substances. environments temperatures transport and storage. Do not store volatile
If not, please dispose of the original packaging material in an environmentally-friendly way. The packaging cardboard can be recycled with old paper.
Storing or shipping the equipment in any conditions other than those specified below is prohibited. and during chemical
6.1. Ambient conditions
Products may only be stored and transported in vehicles that are free of any traces of volatile chemicals under the following climactic conditions:
Temperature
Relative humidity
–25°C to +55°C, do 24h at up to +70°C max. 90% (non-condensing)
NP-DK50-Nx2VTM-ADM-EN-3_10-2022 8 10/2022
PRODUCT DESCRIPTION
PRODUCT DESCRIPTION
7. VARIANTS
The compressor is manufactured according to its intended application in the following variants:
DK50 4x2VT/M Composed of modules:
1 compressor module with adsorption dyer - 4x2V air pumps
2 air tank module – 2x110 l
10/2022
DK50 4x2VT/M
9 NP-DK50-Nx2VTM-ADM-EN-3_10-2022
PRODUCT DESCRIPTION
8. ACCESSORIES
Accessories that are not included in the standard order must be ordered separately.
Set of compressed air outlet filters
The compressor may be equipped with a set of filters if specified. The filter set may be equipped with an air pressure regulator.
Where a different level of air filtration is required, this requirement must be agreed upon with the supplier and specified in the order.
Type Use
Leve of filtration
(
µm)
1
Bypass function*
Article number
FS 40F
FS 40M
FS 40S
DK50 4x2VT/M
1+0,1
1+0,01 no
604014119-000
604014119-004
604014119-024
FS 40AH 1+AC+HC(0,01) 604014119-005
*) These FS do not contain a filter bypass, which will ensure a continuous flow of air when replacing the filter element. Such a set must be ordered separately.
Set of filters
Filter set regulator assembly
The compressor may be equipped with a pressure regulator of the compressed air
Type
Regulator complete outlet if specified. The regulator must be selected according to the application to the filter set, or separately The regulator shall ensure constant pressure at the outlet.
Use
DK50 4x2VT/M
Article number
604014125-000
Filter set brackets
A suitable bracket must be ordered for every filter set.
Type
Compressor-mounted bracket
Wall-mounted bracket
Use
DK50 4x2VT/M
NP-DK50-Nx2VTM-ADM-EN-3_10-2022 10
Article number
603014137-000
603014120-000
10/2022
PRODUCT DESCRIPTION
9. PRODUCT FUNCTION
9.1. Compressor with adsorption dryer
The compressor air pumps (1) draw in air through the inlet filter and compress it through a non-return valve and into a manifold, from which it is routed to the adsorption dryer (3) through a connecting hose. From the inlet to the dryer module, the air is first cooled in the integrated cooler (16) and then moves through the condensate separator (24), entering the active chamber with adsorbent (15), where the
Description for figures 1-3:
1. Air pump
2. Air tank
3. Adsorption dryer
4. Electrical box / switchboard
5. Frame
6. Pressure switch
7. Compressed air outlet
8. Pressure gauge
9. Safety valve
10. Magnetic holder
11. Condensate collection vessel
12. Outlet module
13. Electrical panel
14. Bushing
15. Dryer chamber
16. Cooling module air is then dried. A portion of the dry air is routed into the second, regenerating chamber, where the air removes moisture from the adsorbent and is released together with the trapped condensate into the surroundings. Chamber operation (desiccant regeneration) is cyclically switched. Dry and filtered air then passes through the non-return valve into the air tank (2).
17. Inlet valve module
18. Regeneration solenoid valve
19. Outlet from condensate separator and regeneration valves
20. Compressed air inlet
21. Air outlet
22. Dryer display
23. Dryer fan
24. Condensate separator
25. Condensate drain solenoid valve
26. Three-pole circuit breaker
27. Single-pole circuit breaker
28. LOGO control electronics
29. Indicator
30. Contactor
31. Thermal overcurrent relays
10/2022 11 NP-DK50-Nx2VTM-ADM-EN-3_10-2022
Fig. 1: Compressor with adsorption dryer
PRODUCT DESCRIPTION
NP-DK50-Nx2VTM-ADM-EN-3_10-2022 12 10/2022
PRODUCT DESCRIPTION
Fig. 2: Adsorption dryer
10/2022 13 NP-DK50-Nx2VTM-ADM-EN-3_10-2022
Fig. 3: Electrical box/ switchboard
PRODUCT DESCRIPTION
The range of the pressure switch on the configured assemblies may only be adjusted after prior consultation manufacturer. with the
Adjusting the pressure setting of the safety valve is expressly prohibited.
The pressure relief valve automatically begins to vent air from the system if the pressure in the compressed air circuit exceeds its pre-set value. The pressure relief valve then closes as the pressure drops.
Pressure in the compressed air circuit can only increase because of an increase in flow resistance in the compressed air lines or as a result of a dryer malfunction (e.g. solenoid valve malfunction, an increase in flow resistance through the drying media, etc.), and therefore the repeated opening of the relief valve requires a dryer function check and repairs if necessary.
Consultation with the manufacturer is required before any adjustment is made to the relief valve!
The outlet openings on the relief valve must not be blocked and the flow of compressed air through them may not be restricted.
NP-DK50-Nx2VTM-ADM-EN-3_10-2022 14 10/2022
TECHNICAL DATA
TECHNICAL DATA
Compressors are designed for operation in dry, ventilated and dust-free indoor rooms
Temperature
Relative humidity
Working pressure 6 – 8 bar
Nominal voltage, Frequency a)
Capacity at 6 bar (FAD) PDP 20°C
40°C
Working pressure b) under the following climactic conditions:
V, Hz l/min
Rated current
Main circuit protection device rating
Mail electrical feeder
Enclosure
Motor power
Air tank volume
Air quality - filtration
Maximum operating pressure of safety valve
Noise level at 5 bar (L pA
)
Operating mode
PDP drying performance at 7 bar d)
Time to fill air tank from 0 to 7 bar
Net weight c)
Dimensions (net) w x d x h
Required cooling air changes in space
Classification under EN 60601-1 mm m 3 /h a) Specify the compressor version when ordering b) Consult any other range of pressure with the supplier c) d)
Weight is indicative and only applies to the product without accessories
Applies to ambient temperatures of <30°C PDP – pressure dew point bar
A
A mm 2 kW l
m bar dB
%
°C s kg
+5°C to +40°C max. 70%
DK50 4x2VT/M
3x400, 50
470
11.0
-
-20
190
6.0 – 8.0
25
4
IP10
1.2
220
12,0
≤72
S1-100
341
1000
Class I.
450
11.0
-40
200
2360x510x1730
-
10/2022 15 NP-DK50-Nx2VTM-ADM-EN-3_10-2022
Dependence of compressor output on working pressure
TECHNICAL DATA
NP-DK50-Nx2VTM-ADM-EN-3_10-2022 16 10/2022
TECHNICAL DATA
Working pressure 8 – 10 bar
Nominal voltage, Frequency a)
Capacity at 8 bar (FAD) PDP 20°C
40°C
Working pressure b)
Rated current
Main circuit protection device rating
Main electrical feeder
Enclosure
Motor power
Air tank volume
Air quality - filtration
Maximum operating pressure of safety valve
Noise level at 5 bar (L pA
)
Operating mode
PDP drying performance at 7 bar d)
Time to fill air tank from 0 to 7 bar
Net weight c)
Dimensions (net) w x d x h
Required cooling air changes in space
V, Hz l/min mm m 3 /h
Classification under EN 60601-1 a) Specify the compressor version when ordering b) Consult any other range of pressure with the supplier c) Weight is indicative and only applies to the product without accessories d)
Applies to ambient temperatures of <30°C PDP – pressure dew point bar dB
%
°C s kg bar
A
A mm 2 kW l
m
DK50 4x2VT/M
3x400, 50
380 370
8.0 – 10.0
14.0 14.0
25
4
IP10
1.2
220
- -
12.0
≤72
S1-100
-20
235
341
2360x510x1730
-40
240
1000
Class I.
10/2022 17 NP-DK50-Nx2VTM-ADM-EN-3_10-2022
Dependence of compressor output on working pressure
TECHNICAL DATA
FAD correction of capacity for altitude
Capacity given in the form of FAD („Free Air Delivery“) applies to the following conditions:
Altitude 0 m.n.m.
Atmospheric pressure 101325 Pa
Temperature
Relative humidity
20°C
0%
To calculate FAD compressor capacity in dependence on altitude, it is necessary to apply correction factor according to the following table:
Altitude [m.n.m.]
FAD correction factor
0 -1500
1
1501 - 2500
0,8
2501 - 3500
0,71
3501 - 4500
0,60
NP-DK50-Nx2VTM-ADM-EN-3_10-2022 18 10/2022
TECHNICAL DATA
Electromagnetic compatibility declaration
Medical equipment needs special precautions regarding electromagnetic compatibility
(EMC) and needs to be installed and put into service according to the EMC information provided below.
Guidance and manufacturer's declaration - electromagnetic emissions
Pursuant to IEC 60601-1-2:2014/AMD1:2020 - Medical electrical equipment - Part 1-2: General requirements for basic safety and essential performance - Collateral Standard: Electromagnetic disturbances
The equipment is intended for use in the electromagnetic environment specified below. The customer or the user of the equipment should assure that it is used in such an environment.
Emissions test Compliance Electromagnetic environment - guidance
RF emissions CISPR 11 Group 1
The equipment uses RF energy only for its internal functions. Therefore, the RF emissions are very low and are not likely to cause any interference in nearby electronic equipment.
RF emissions CISPR 11 Class B
Harmonic emissions IEC
61000-3-2
Voltage fluctuations/ flicker emissions IEC
61000-3-3
Class A
The equipment is not likely to cause any flicker, as the current flow is approx. constant after the start up.
The equipment is suitable for use in all establishments, including domestic establishments and those directly connected to the public low voltage power supply network that supplies buildings used for domestic purposes.
10/2022 19 NP-DK50-Nx2VTM-ADM-EN-3_10-2022
TECHNICAL DATA
Guidance and manufacturer's declaration - electromagnetic immunity
Pursuant to IEC 60601-1-2:2014/AMD1:2020 - Medical electrical equipment - Part 1-2: General requirements for basic safety and essential performance - Collateral Standard: Electromagnetic disturbances
The equipment is intended for use in the electromagnetic environment specified below. The customer or the user of the equipment should assure that it is used in such an environment.
Immunity test
IEC 60601-1-2 test level
Compliance level
Electromagnetic environment - guidance
Electrostatic discharge (ESD)
IEC 61000-4-2
±8 kV contact
±15 kV air
±8 kV contact
±15 kV air
Floors should be wood, concrete or ceramic tile. If floors are covered with synthetic material, the relative humidity should be at least 30%.
Electrical fast transient/burst
IEC 61000-4-4
Surge
IEC 61000-4-5
Voltage dips, short interruption, and voltage variations on power supply input lines IEC
60601-4-11
±2 kV for power supply lines
±1 kV for input/output lines
±1 kV differential mode
±2 kV common mode
U
T
=0%, 0,5 cycle
(at 0, 45, 90, 135,
180, 225, 270 and 315°)
U
T
=0%, 1 cycle
U
T
=70% 25/30 cycles (at 0°)
U
T
=0%, 250/300 cycles
±2 kV
100 kHz repetition frequency
Applied to mains connection
±1 kV L-N
±2 kV L-PE; N-PE
Applied to mains connection
U
T
=>95%, 0,5 cycle
(at 0, 45, 90, 135, 180,
225, 270 and 315°)
U
T
=>95%, 1 cycle
U
T
=70% (30% dipp
U
T
),
25(50Hz)/30(60Hz) cycles (at 0°)
U
T
=>95%,
250(50Hz)/300(60Hz) cycle
Mains power quality should be that of a typical commercial or hospital environment.
Mains power quality should be that of a typical commercial or hospital environment.
Mains power quality should be that of a typical commercial or hospital environment.
The device stops and restarts automatically at each dip. In this case does not occur unacceptable pressure drop.
Power frequency
(50/60 Hz)
IEC 61000-4-8
N/A N/A
The equipment does not contain magnetically sensitive components or circuits.
Radiated fields in close proximity per IEC 61000-4-
39
N/A N/A
The equipment does not contain magnetically sensitive components or circuits.
NOTE: U
T
is the A.C. mains voltage prior to application of the test level.
NP-DK50-Nx2VTM-ADM-EN-3_10-2022 20 10/2022
TECHNICAL DATA
Guidance and manufacturer's declaration - electromagnetic immunity
Pursuant to IEC 60601-1-2:2014/AMD1:2020 - Medical electrical equipment - Part 1-2: General requirements for basic safety and essential performance - Collateral Standard: Electromagnetic disturbances
The equipment is intended for use in the electromagnetic environment specified below. The customer or the user of the equipment should assure that it is used in such an environment.
Immunity test
IEC 60601-1-2 test level
Compliance level
Electromagnetic environment - guidance
Conducted RF
IEC 61000-4-6
Radiated RF
IEC 61000-4-3
Proximity fields from RF wireless communications equipment
IEC 61000-4-3
3 Vrms
150 kHz to 80MHz
3 V/m
80 MHz to 2,7
GHz
9 to 28 V/m
15 specific frequencies
(380 to 5800
MHz)
3 Vrms
3 V/m
9 to 28 V/m
15 specific frequencies
(380 to 5800
MHz)
Portable and mobile RF communications equipment should be used no closer to any part of the equipment, including cables, than the recommended separation distance calculated from the equation applicable to the frequency of the transmitter.
Recommended separation distance d=
1,2√
P d=
1,2√
P , 80 MHz to 800 MHz d= 2,3√ P , 800 MHz to 2,7 GHz where P is the maximum output power rating of the transmitter in watts (W) according to the transmitter manufacturer and d is the recommended separation distance in metres (m).
Field strengths from fixed RF transmitters, as determined by an electromagnetic site survey a , should be less than the compliance level in each frequency range b . Interference may occur in the vicinity of equipment marked with the following symbol:
NOTE 1 At 80 MHz and 800 MHz, the higher frequency range applies.
NOTE 2 These guidelines may not apply in all situations. Electromagnetic propagation is affected by absorption and reflection from structures, objects and people. a Field strengths from fixed transmitters, such as base stations for radio (cellular/cordless) telephones and land mobile radios, amateur radio, AM and FM radio broadcast and TV broadcast cannot be predicted theoretically with accuracy. To assess the electromagnetic environment due to fixed RF transmitters, an electromagnetic site survey should be considered. If the measured field strength in the location in which the equipment is used exceeds the applicable RF compliance level above, the equipment should be observed to verify normal operation. If abnormal performance is observed, additional measures may be necessary, such as re-orienting or relocating the equipment. b Over the frequency range 150 kHz to 80 kHz, field strengths should be less than 3 V/m.
10/2022 21 NP-DK50-Nx2VTM-ADM-EN-3_10-2022
INSTALLATION
INSTALLATION
Risk of incorrect installation.
Only a qualified technician may install the compressor and place it into operation for the first time. Their duty is to train operating personnel on the use and maintenance of the equipment. An entry is made in the equipment installation record to certify installation and operator training. (see the
Annex chapter)
10. INSTALLATION CONDITIONS
The compressor may only be installed and operating in dry, well-ventilated and clean environments under the conditions specified in the Technical
Data chapter.
Risk of damage to the device.
The equipment may not be operated outdoors or in otherwise wet or damp environments.
The compressor must be installed so that it is accessible at all times for operating and maintenance. Please ensure that the nameplate on the device is readily accessible.
The compressor must stand on a flat, sufficiently stable base (be aware of the weight of the compressor, see the
Technical Data chapter).
The compressor on the operator’s side must be at least 70 cm from the wall to allow air flow for cooling purposes and to ensure the safety of the operator and maintenance personnel.
Approximately 70% of the electrical energy used by the compressor aggregates is converted to heat, and therefore the rooms in which the compressor is installed must have additional ventilation to provide sufficient air exchange for cooling purposes (see the Technical Data chapter).
NP-DK50-Nx2VTM-ADM-EN-3_10-2022 22
Burn or fire hazard! Caution!
Hot surface!
Portions of the compressor, dryer and connecting hoses between the dryer and compressor may be hot and reach hazardous temperatures during compressor operation that may harm materials or operating staff.
High temperature hazard
Placing air flow impediments upstream or downstream of the cooler is prohibited. The temperature of internal and external parts of the equipment may rise to hazardous levels.
Ensure the power cords and air hoses are not damaged. The power cord must not show signs of stress and must be kept without tension (placing any objects on it is prohibited), and subjecting the cord to external heat in any form is prohibited.
10/2022
INSTALLATION
Fig. 4: Equipment installation
Air outlet
Space condition:
-
Temperature +5°C ÷ +40°C
- Relative humidity 70%
11. COMPRESSOR ASSEMBLY
11.1. Handling and releasing the compressor
Unpack the compressor (compressor modules, dryer and air tank) from the packaging and remove the transport anchors from the pallet. All modules
Recommended flow of cooling air:
DK50 4x2VT/M –
1000m 3 /h
Applies for continuous operation and cooling air temperature of 20°C
Cooling air inlet are secured to pallets.
Use a fork lift or similar hoisting equipment to handle and position the product.
Position the compressor module at the
site of installation (Fig. 5).
10/2022 23 NP-DK50-Nx2VTM-ADM-EN-3_10-2022
Fig. 5: Handling the compressor module
INSTALLATION
NP-DK50-Nx2VTM-ADM-EN-3_10-2022 24 10/2022
INSTALLATION
Fig. 6: Levelling the compressor
Fig. 7: Frame installation
10/2022 25 NP-DK50-Nx2VTM-ADM-EN-3_10-2022
INSTALLATION
Prior to installation, ensure that the compressor is free of all transport packaging and stabilizers to avoid any risk of damage to the product.
Remove all devices used to secure the aggregates once the compressor is installed and levelled at the site of final installation.
Fig. 8: Releasing the air pumps
Remove the transport stabilisers from
the air pumps (X, Y, Z) (Fig. 8).
12. PNEUMATIC CONNECTION
Connect the compressed air lines at (C) and connect the equipment to the compressed air
DK50 4x2VT/M – 8x mounts.
system from the G3/4” threaded outlet ball valve.
Fig. 9: Pneumatic connection
NP-DK50-Nx2VTM-ADM-EN-3_10-2022 26 10/2022
INSTALLATION
Condensate outlet from dryer
Injury hazard.
Do not connect the condensate drain directly to a waste drain!
Passers-by may be injured!
Connect a hose to the outlet
(1) from the automatic condensate drain (2) to the provided collection vessel.
Fig. 10: Condensate drain
A G3/4” (F) ball valve is installed on the compressed air outlet from the air tank.
Fig. 11: Air outlet from the air tank
10/2022 27 NP-DK50-Nx2VTM-ADM-EN-3_10-2022
INSTALLATION
Potential for damage to pneumatic components.
Ensure the air hoses are not kinked.
13. ELECTRICAL CONNECTION
Unauthorised hazard interference
Only a qualified electrician may install electrical components!
Risk of damage to the device.
The operator is obliged to provide circuit protection devices for the equipment per the specifications in valid technical standards.
The product is delivered without a power cord.
Cord type (minimum requirements) H05 VV-
F_ 5G10
Risk of electric shock.
Ensure full compliance with all local electrical codes. The mains voltage and frequency must comply with the data stated on the nameplate on the equipment.
Fig. 12: Connecting the protective PE conductors
Connect the disconnected PE protective conductors and then the grounding wire after connecting (D).
Fig. 13: Connecting the electrical cables
Connect the disconnected electrical cables (E) to the terminal strips in the electric motor boxes. Insert the cables into the electrical installation trays and enclose with a cover.
NP-DK50-Nx2VTM-ADM-EN-3_10-2022 28 10/2022
INSTALLATION
Fig. 14: Connecting the power cord
Connect the TN-S mains to the power supply terminal in the equipment’s junction box (F). Connect the electrical components to the mains in accordance with the valid electrical standards and regional regulations.
Fig. 15: Connecting the cable to the pressure switch
Connect the loose cord to the pressure
switch per the schematic, or Fig. 15,
tighten the screws and secure with paint.
Fire hazard and risk of electric shock.
Ensure the electrical cable does not touch hot parts of the device or connecting hoses.
14. COMMISSIONING
Make sure all transport stabilizers were removed.
Check that all compressed air hose connections are correct.
Ensure the power cord is properly
10/2022 29 connected to the mains and the power cable is connected to the dryer.
Check to ensure the outlet valve is in the OFF position.
Check to ensure the hose from the
NP-DK50-Nx2VTM-ADM-EN-3_10-2022
automatic condensate drain is connected to the collection vessel.
Check the date and time settings on
the LOGO! controller (see chap. 16.1)
Configuring the language on the dryer
Configuring the date and time on the
INSTALLATION
dryer display (see chap. 19.3)
Check the drying mode settings (see
The compressor is not equipped with a backup power supply.
NP-DK50-Nx2VTM-ADM-EN-3_10-2022 30 10/2022
INSTALLATION
15. PNEUMATC DIAGRAMS
DK50 4x2VT/M
10/2022 31 NP-DK50-Nx2VTM-ADM-EN-3_10-2022
Description to pneumatic diagrams:
1. Inlet filter
2. Air pump
3. Compressor fan
4. Ball valve
5. Safety valve
6. Non-return valve
7. Condensate drain solenoid valve
8. Condensate separator
9. Dryer
10. Pressure switch
INSTALLATION
11. Pressure gauge
12. Cooler
13. Cooler fan
14. Air tank
15. Condensate drain valve
16. Outlet valve
17. Dryer solenoid valve - outlet
18. -
19. Condensate collection vessel
NP-DK50-Nx2VTM-ADM-EN-3_10-2022 32 10/2022
OPERATION
OPERATION
ONLY TRAINED PERSONNEL
MAY OPERATE
EQUIPMENT!
THE
Risk of electric shock.
In case of emergency, disconnect the compressor from the mains (pull out the mains plug).
Burn or fire hazard.
When the compressor is running, the connecting hose between the compressor and dryer and parts of the dryer and aggregate may be hot enough to burn people or other material.
Warning - compressor is controlled automatically.
Automatic compressor start. The automatically switches on when the pressure in the air tank drops to the pressure switch’s lower limit level. The compressor automatically switches off once the pressure in the tank reaches the shut-off pressure.
Potential for damage pneumatic components. to
The working pressure settings for the pressure switch set by the manufacturer cannot be changed. Compressor operation at a working pressure below the switching pressure indicates high air usage (see the
Troubleshooting chapter).
Risk of damage to the dryer.
The dryer may be damaged if operated at ambient temperatures that are higher than the maximum working temperature (ambient temperature >30°C or inlet air temperature of >100°C)
Required drying performance can only be achieved when following the defined operating conditions.
Drying performance will decline and the achieved dew point will drop if the dryer is operated at any pressure below minimum working pressure.
the
16. SWITCHING THE COMPRESSOR
After the pressure switch (6) is activated and circuit breakers FA13 (26) and FA14 (27) are turned to position I, the compressor air pumps sequentially come online (the air pumps in the second column or shelf react with a 2 s delay).
Circuit breaker FA13 (26) functions as the main switch.
The air pumps switch on (at ≤6 bar) and off (at
≥8 bar) automatically and are controlled by the
LOGO! (28) controller and the pressure switch
(6) based on compressed air usage.
If the motor surface temperature exceeds
40oC, the temperature switches automatically turn on the compressor cooling fans, switching
10/2022 33 them off once the temperature decreases to approximately 32 o C.
16.1. Controller LOGO!
This controller controls the compressors monitors and signals alarms (as described below) and displays the number of operating hours. It is composed of a base module and an expansion module. The base module includes a display and the cursor (control) buttons ▲, ▼, ►, ◄, OK and ESC. The expansion module has LED indicators for
RUN and STOP.
NP-DK50-Nx2VTM-ADM-EN-3_10-2022
OPERATION
The parameters of this unit do not require configuration or set up under normal circumstances.
The LED indicator on the expansion module should be green once the equipment is connected to its power source and the display should show the current operating hours.
The displayed hours are only illustrative.
Proceed in accordance with Chapter 22 if the
indicator is not green.
If the operating hours are not shown, the compressor may have been disconnected from the power for an extended period of time and it must be restarted.
The display shows the main menu.
press▲ or ▼ to move the “>” cursor on the display to Setup..
and press
OK to confirm
A menu appears.
press▲ or ▼ to move the “>” cursor on the display to Clock..
and press
OK to confirm
A menu appears.
press▲ or ▼ to move the “>” cursor on the display to Set Clock..
and press OK to confirm
A menu appears.
press ▲ or ▼ to select the day of the week
press ► or ◄ to move the cursor to the next position
press ▲ or ▼ to set the desired value
repeat the previous two steps to set the date and time
confirm by pressing OK
NP-DK50-Nx2VTM-ADM-EN-3_10-2022 34
The controller is unable to archive time and data if it is disconnected from the power for more than 80 hours. This data must be configured when the equipment is first placed into service or after an extended period in which it has been placed out of service.
10/2022
OPERATION
The following appears:
Press ESC on the controller repeatedly until the main menu appears.
Start the controller program as follows:
press▲ or ▼ to move the “>” cursor on the display to Start and press OK to confirm
Never press OK if the cursor “>” is at Program! This menu provides access to windows with software functional blocks.
Changes to the parameters in these blocks have a direct effect on the functionality of the equipment!
Alarms and alarm signalling
The equipment automatically checks the functionality of specific parts of the equipment and indicates when maintenance service is needed. The controller determines an alarm as any situation in which the equipment functionality does not match the standard conditions.
The individual alarms are indicated by an alarm signal indicated by an activated HA beacon (29), with one or more alarm messages on the controller's display.
Alarms are classified based on their severity into:
low priority alarms – signal a maintenance interval I = n x 2000 hours (n = 1, 2, 3, ..) and the equipment supplies air to the central compressed air system using all air pumps; this status is indicated by an activated HA beacon and a message on the display.
medium priority alarm
– triggered by a malfunction in one or more air pumps and the equipment supplies air to the central compressed air system using only functional air pumps; this status is indicated by a flashing HA beacon and message on the display.
The equipment has an intelligent alarm system that generates an alarm signal based on its priority (medium priority alarms have a higher priority than low priority alarms)
Low priority alarm conditions
The equipment is equipped to monitor and signal maintenance intervals. Maintenance intervals are whole number multiples of 2000 operating hours I = n x 2000 hours (n = 1, 2,
3, etc.). The maintenance of specific components pursuant to the attached Table 2 must be performed once a maintenance interval is passed. This condition is indicated by an activated yellow HA beacon and an information message on the display:
10/2022
Maintenance intervals are counted from the moment the equipment is first started up.
35
This table must be inserted into the compressor maintenance log along with Table
3 in which maintenance work, inspections of
NP-DK50-Nx2VTM-ADM-EN-3_10-2022
the equipment during each maintenance interval and other records regarding the equipment will be recorded.
This signal from the controller must be cancelled once the maintenance work related to a service interval signal is completed by pressing and holding ESC and ▼ for 3 seconds. Cancelling this signal also resets the maintenance interval to a value of 2000.
OPERATION
Medium priority alarm conditions
The equipment is equipped to monitor and signal compressor malfunctions. Such a situation may occur for mechanical or electrical reasons in any of the compressors.
This is frequently accompanied by an increase in the current draw. This trips the thermal over current protection in the FA device for the respective air pump or air pumps (the blue button is in position M and the yellow off indicator is not pressed).
Such alarm is signalled by a flashing HA beacon –P1 and an the following message appears on the display:
The beacon will continue to flash after the air pump malfunction is remedied. Turn off the alarm by pressing and holding ESC and
▲together for 3 seconds.
The flashing beacon function and alarm may be turned off during maintenance work by pressing and holding ESC and ▲together for
3 seconds. Malfunctions are temporarily indicated by a flashing display on the controller and the subsequent message:
This message automatically disappears once the malfunction on the air pump is remedied and it is placed back into service.
Alarm signals have priority over maintenance interval signals.
As such, the light will indicate an alarm from any of the air pumps.
One the alarm is over, the service interval is indicated by the activated HA beacon.
17. SWITCHING OFF THE COMPRESSOR
Use circuit breakers FA13 and FA14 to switch off the equipment for service or other reasons.
Vent the air tanks by disconnecting from the
NP-DK50-Nx2VTM-ADM-EN-3_10-2022 36 central compressed air circuit and opening the outlet valve or the drain valves.
10/2022
AD DRYER
AD DRYER
18. PRINCIPLE OF OPERATION
The dryer is controlled by a signal from the compressor pressure switch.
When the compressor is running, compressed air enters the cooler where it is cooled, and a portion of the condensed moisture is separated in the integrated cyclical separator.
Solenoid valve V3 is located in the bottom of the separator, and it drains off the condensate from the separator at regular intervals.
Air then passes to the chamber of logic valve
OR1 which senses the pressure. If the pressure in the valve chamber does not reach
P1 = 3 bar, regeneration solenoid valves V1 and V2 (normally closed type) remain closed and regeneration is not initiated. If the pressure in the chamber of the logic valve reaches minimum3 bar, chamber switching is initiated using the logic described in point
When the signal from the compressor pressure switch deactivates, regeneration valves V1 and V2 open for a short time to vent the compressor aggregate and to vent the dryer chamber.
Dryer venting and regeneration is completed via the hose shared with the condensate separator drain and for this reason the condensate outlet cannot be connected directly to a drain
18.1. Dryer regeneration
Dryer regeneration is initiated when working pressure P1 = 3. During regeneration, valves
V1 and V2 switch cyclically, whereby there is a short delay (dT) to equalise the pressures in the chambers and during which both valves are closed before each switching cycle.
Working pressure is in chamber 1 and the chamber is in the drying phase, while there is atmospheric pressure in chamber 2 and this chamber is in the regeneration phase. The chamber is regenerated by air passing through the dryer nozzle.
18.2. Waring system
Every warning is indicated by a corresponding
visual signal (see Chapter 21) and the visual
signal flashes. Call an authorised service provider to conduct repairs required in the event of a failure.
Warning states indicate a potential failure of the device. Therefore, warning signals may not be deactivated.
All warning signals are intermittent
– when the cause of the warning no longer exists, the warning signals are deactivated.
Operator’s position. No specific operator’s position is required. The operator may remain within range of a visual warning signal depending on actual operating conditions.
Low pressure . This signal is active when the dryer pressure sensor reads low pressure in the dryer under the defined limit of 3 bar. An air leak from the compressor/dryer, malfunction of the control solenoid valves on the dryer or a software error may activate this alarm during operation.
High pressure . This signal is active when the dryer pressure sensor reads an increase in pressure over the high limit. The aggregate will then shut down and remain shut-down until the pressure decreases. If the aggregate does not shut down, excess pressure is vented by the safety valve on the compressor’s air tank.
High dew point . This signal is active when the dew point sensor reads a high dew point value.
Expiration of service interval . This signal is activated until service is performed and the interval reset, or a new service interval is entered.
10/2022 37 NP-DK50-Nx2VTM-ADM-EN-3_10-2022
AD DRYER
19. USER INTERFACE / SETTINGS
19.1. Meaning of symbols on the display
Symbol representing the user manual, or to read the user manual.
Symbol expressing the ambient temperature (from 25oC) related to the selected mode.
The program adjusts the chamber pre-filling in the given mode.
Symbol expressing the ambient temperature (from 25°C to 30°C) related to the selected mode.
The program adjusts the chamber pre-filling in the given mode.
Symbol expressing the ambient temperature (over 30°C) related to the selected mode.
The program adjusts the chamber pre-filling in the given mode.
Back to the main menu on the 4 main screens.
Go back.
Symbol for the service interval.
Symbol for when the dryer chamber is currently in regeneration.
Symbol for when the dryer chamber is currently drying.
0
Symbol for chamber pre-filling – equalisation of pressure in chambers.
NP-DK50-Nx2VTM-ADM-EN-3_10-2022
Indication the device is operating
Indication of an alarm state
(on until the alarm state no longer exists)
38 10/2022
AD DRYER
19.2. Initial language settings for the user interface
The option to select a language appears when the program is first launched. The service technician selects the given language during installation based on the geographic location of the dryer installation. The program saves and remembers this setting. The option does not appear when the program is restarted.
LANGUAGE SETUP
ADSORPTION DRYER
IS ON
LANGUAGE SETUP
CZ SK
GER UK
RUS HUN
FR
RUN
CONFIRM THE
LANGUAGE:
CZECH
E N T E R
19.3. Setting the date and time during commissioning
It is recommended to set the date and time during commissioning. These settings are changed in the service menu in the SETUP section. Access to the service menu is protected by a code (1992).In SETUP you have to tap down arrow to set date and time.
In the same way, it is possible to reset the user interface language via LANGUAGE SETUP..
19.4. Setting the drying mode during commissioning
It is recommended to set the air-drying mode during commissioning. These settings are changed in the service menu in the SERVICE
SETUP section. Access to the service menu is protected by a code.
10/2022 39 NP-DK50-Nx2VTM-ADM-EN-3_10-2022
AD DRYER
Reset and adjustment of service intervals, reviewing service and alarm messages
Adjustment of the dryer pressure version
Adjustment of the dryer mode
The drying mode is set based on the expected pressure range in which the device will operate and the version of the compressor
(with or without a cabinet).
compressor without a cabinet t
O
< 25 ̊C
- set to ECONOMY mode
compressor without a cabinet t
O
= 25 ̊C
20. MAIN SCREENS
The home screen opens once the user interface language and drying mode are set.
There are 4 main screens accessed from the home screen.
20.1. Home screen
Hour counter
Dryer operating
- 30 ̊C - set to STANDARD mode
compressor without a cabinet t
O
> 30 ̊C
- set to ENHANCED mode
compressor in cabinet - set to
ENHANCED mode t
O
- ambient temperature
The arrows at the bottom of the screen are used to navigate between the individual screens.
Current dew point *
Current pressure in
Time to next service
Toggle to display dryer operation
Switch to language selection
(*this information is only shown if the compressor is equipped with a dew point sensor)
- Basic information and measured parameters are shown on the dryer
NP-DK50-Nx2VTM-ADM-EN-3_10-2022 40 10/2022
AD DRYER home screen. The dryer operating hours indicator is located at the top of the screen. The home screen has 4 main tiles that display the following information:
-
Dryer operating mode (see chap. 19.1)
- Current pressure in the dryer (min. working pressure to activate dryer
20.2. Dryer operation screen
Operating hours indicator
Hour counter regeneration is 3 bar)
- Current pressure dew point value (only for compressors equipped with dew point sensors)
- Remaining time to the next service
interval (see chap. 21.1, 21.2
– service intervals).
Chamber designation
Symbol for chamber pressure equalisation phase
Status icon for the left chamber
The dryer operating hours indicator is located at the top of the screen. The dryer operation screen is also divided into 4 tiles, which
Status icon for the right chamber
Arrow to navigate back to the home screen describe the dryer chamber working cycles using a graphical depiction of the operating states of each chamber.
Symbol for when the dryer chamber is currently in regeneration.
Symbol for when the dryer chamber is currently drying.
0
Symbol for chamber pre-filling – equalisation of pressure in chambers.
20.3. Language settings screen
The language settings screen is one of the main screens.
10/2022 41 NP-DK50-Nx2VTM-ADM-EN-3_10-2022
AD DRYER
20.4. Service menu screen
The service menu is intended exclusively for service personnel. Access to individual menu items is password (1992) protected.
21. INDICATION OF MAINTENANCE AND ALARM STATES
The adsorption dryer controller is capable of measuring selected parameters (pressure and pressure dew point in versions with a dew point sensor) and for assessing the basic dryer operating states. information on faults using the following notifications and warnings.
The compressor beacon does not light up in the event of a fault in the adsorption dryer!
Based on the measured parameters and service details, the controller displays
21.1. Notification – Upcoming service interval
100 operating hours prior to the next service interval a yellow notification appears (“Notice!”). The service tile also lights up orange.
The remaining hours to the next service interval are also displayed.
The warning is shown until service is completed and the service interval is reset.
21.2. Warning – Service interval exceeded
A red warning is shown (“Warning!”) once the service interval has lapsed. The service tile also lights up red.
The warning is shown until service is completed and the service interval is reset.
The hours to the next service interval are also displayed.
A list of warnings is saved in the “Warning log”
The dryer continues operating normally
NP-DK50-Nx2VTM-ADM-EN-3_10-2022 42 10/2022
AD DRYER
21.3. Alarm conditions
Low / high pressure
A red warning is shown (“Warning!”) if low pressure (<3 bar) or high pressure (> 8.5 bar, or > 10.5 bar depending on the pressure version) is detected. At the same time, the current pressure tile lights up red.
The warning is displayed as long as the alarm condition endures.
A list of warnings is saved in the “Warning log”
The dryer is not operating normally, regeneration is not initiated, the compressor must be shut down
A high dew point alarm may appear when the unit is first placed into service. The alarm will persist until the dryer regenerates. The regeneration time of the dryer depends on many parameters of use of the device. Dryer regeneration should take no more than 24 dryer working hours. If the dryer cannot meet the dew point set-point during the first
24 hours, please contact service personnel.
21.4. „Call Service“ screen
The “Call Service” screen alternates with the main screen if a notification or warning occurs.
10/2022 43 NP-DK50-Nx2VTM-ADM-EN-3_10-2022
PRODUCT MAINTENANCE
22. PRODUCT MAINTENANCE
The operator should carry out device checks regularly in the intervals defined by applicable regulations. Test results must be recorded.
The equipment has been designed and manufactured to keep maintenance to a minimum. The following work must be performed to preserve the proper and reliable operation of the compressor.
Unauthorised hazard. interference
Repair work outside the framework of standard
maintenance (see Chapter 22.1)
may only be performed by a qualified technician (an organisation authorized by the manufacturer) manufacturer’s service. or the customer
Standard maintenance work
(see Chapter 22.1) may only be
performed by the operator’s trained personnel.
Only use manufacturerapproved replacement parts and accessories.
PRODUCT MAINTENANCE
Danger of injury or equipment damage.
Prior to commencing compressor maintenance, it is necessary to:
- check if it is possible to disconnect the compressor from the appliance in order to avoid any risk of injury to the person using the appliance or other material damage;
- turn off the compressor;
- disconnect it from the mains (pulling the cord out of the mains socket);
- vent the compressed air from the air tank.
Prior to commencing dryer maintenance work, first:
- shut off the compressed air supply to the dryer
- turn the main switch on the side of the switchboard to the “0” position;
- check the pressure indicator on the dryer and if there is still pressure, it must first be vented from the dryer chamber.
Venting compressed air poses an injury hazard.
Wear eye protection, i.e. goggles, when venting compressed air from the compressed air circuit (air tank).
NP-DK50-Nx2VTM-ADM-EN-3_10-2022 44 10/2022
PRODUCT MAINTENANCE
Burn hazard.
When the compressor is running or shortly thereafter, certain portions of the air pump, the compressor’s compressed air system, parts of the dryer and connecting hoses between the compressor and dryer may be hot - do not touch these components.
Allow the equipment to cool down before maintenance, service or connecting/disconnecting the compressed air supply!
The work below may only be performed by trained personnel as follows:
Turn off the circuit breakers at the switchboard before starting any subsequent maintenance work.
10/2022 45 NP-DK50-Nx2VTM-ADM-EN-3_10-2022
22.1. Maintenance intervals operator qualified technician
PRODUCT MAINTENANCE
NP-DK50-Nx2VTM-ADM-EN-3_10-2022 46 10/2022
PRODUCT MAINTENANCE qualified technician
10/2022 47 NP-DK50-Nx2VTM-ADM-EN-3_10-2022
22.2. Check of product operation
Check air pump condition – the aggregates should be operating normally without excessive vibration or noise. Troubleshoot any problem or call in service personnel if trouble is detected.
Visually inspect fan operation – the fans must be operating when the aggregates are running. Troubleshoot any problem or call in service personnel if trouble is detected.
Check to ensure the power cord, the cable for the pressure sensor on the air tank and the connecting compressed air hoses are undamaged. Replace damaged components or call in service personnel.
Check the ambient temperature at the display – the ambient temperature must be below the temperature limit
(40°C). Cool the space if the temperature is high.
Check for alarm conditions on the display – troubleshoot and remedy all alarms.
22.3. Check the compressed air connections for leaks and inspect the equipment
Leak testing
Check the compressor's compressed air lines for leaks during operation – pressure supplied by the compressor.
Use a leak analyser or soapy water to check all joints and connections for leaks. Tighten or reseal the connection where leaks are found.
Inspecting the equipment
Check the condition of the compressor air pump for normal operation and noise levels.
Fan operation check – the fans must be running during the defined compressor work cycles.
Check the filter condition – clean dirty
NP-DK50-Nx2VTM-ADM-EN-3_10-2022 48
PRODUCT MAINTENANCE filters or replace with new filters.
Check the solenoid valves in the valve module.
Check the operation of the automatic condensate drain.
Call in service personnel if a malfunction is suspected.
22.4. Inspection of electrical connections
Risk of electric shock.
Inspect the product’s electrical connections when the mains are disconnected.
Check the mechanical operation of main circuit breaker FA13.
Check the power cord, conductors connected to the X1 terminal strip and the main circuit breaker FA13 to ensure they are undamaged. Inspect to ensure the connection terminals are properly supported to relieve tension.
Check to ensure all threaded conductor terminals are tight (on motor circuit breakers FA1-6, contactors
KM1-6, etc.). Tighten all loose terminals with a screwdriver.
Visually inspect the connection of individual cables to the terminal strip
X1 (spring clips) and the LOGO! control system (screw terminals).
Inspect all screw terminals for the protective green and yellow PE grounding conductors in the switchboard, the motor section, the cooling unit and the pressure vessel.
Tighten any loose terminals.
22.5. Condenste drain
A wet floor resulting from overflow from the vessel poses a slip hazard.
Regularly empty the condensate collection vessel.
Switch off the compressor every time before emptying the vessel!
10/2022
PRODUCT MAINTENANCE
Condensate from compressors with air dryers is automatically drained into a vessel to collect condensate.
Monitor the level in the vessel using the markings (depending on the volume of the vessel), and empty at least once a day.
Fig. 16: Check of the condensate collection vessel
22.6. Inlet filter replacement
The filters located in the compressor air pump enclosure cover must be replaced at defined intervals.
Intake filter replacement:
Pull out the rubber plug by hand
(2).
Remove the dirty intake filter (1).
Insert a new filter and replace the rubber plug.
Pre-filter replacement:
Pull out the pre-filter by hand (3).
Replace with a new one and insert it back.
10/2022 49
Fig. 17: Inlet filter replacement
NP-DK50-Nx2VTM-ADM-EN-3_10-2022
22.7. Check of safety valve
Damage to the safety valve could cause pressure to rise to hazardous levels.
Never use the safety valve to release the air pressure in the air tank. This could damage the safety valve. The valve is set to the maximum permitted pressure by the manufacturer.
Never adjust a safety valve.
PRODUCT MAINTENANCE
Venting compressed air poses an injury hazard.
Wear safety glasses when inspecting a safety valve.
Turn the screw on the safety valve several rotations to the left until the safety valve releases air.
Let the safety valve vent for only a few seconds.
Turn the screw to the right until it seats, closing the valve.
22.8. Compressor performance check
Turn off the compressor using the
STOP button.
Vent the air pressure in the air tank to zero.
Turn on the compressor using the
START button.
Measure the time to fill the air tank from 0 to 7 bar.
The measured value must be less than the data provided in the “Technical
Data” table.
22.9. Check of non-return valve operation
Compressed air line:
Check for the proper operation of all nonreturn valves in the compressed air line and
Fig. 18: Check of safety valve the disconnection of pressure hoses from air pumps.
One air pump must be running at all times, while the others may be shut off using the current protection device in the switchboard. No compressed air may leak from the non-return valves.
Air tank:
Check for proper operation of the non-return valve on the air tank by disconnecting the pressure hose from the valve.
Check the non-return valve operation once the air tank has come up to pressure and with the compressor off. No compressed air may leak.
NP-DK50-Nx2VTM-ADM-EN-3_10-2022 50 10/2022
PRODUCT MAINTENANCE
22.10. Check of solenoid valve operation
Check their operation using the
“Magnetic indicator” fixture as follows:
Attach the fixture to the valve coil and if the motors are active at the valve coil, the indicator must rotate and if they are out of inactive, the indicator must not rotate.
22.11. Check the function of the pressure switch
Every pressure switch has a defined hysteresis of ~2 bar. Functionality is checked visually. If the air pumps reach the upper limit, the pressure switch must disconnect the motors from the power. The process is reversed and the motors started at the low pressure limit.
22.12. Dew point sensor calibration
It is recommended to calibrate the dew point sensor every 2 years on compressors equipped with this sensor. Calibration is performed by the manufacturer (Vaisala) and must be ordered online.
Sensor calibration ordering process:
Visit the website www.vaisala.com
,
23. LONG-TERM SHUTDOWN
If the compressor will not be used for a prolonged time period, it is recommended to drain all condensate from the air tank and the condensate separator. Then turn on the compressor for 10 minutes, keeping the drain
24. DISPOSAL OF DEVICE
Disconnect the equipment from the mains.
Release the air pressure in the pressure tank by opening the drain valve.
Dispose of the equipment following all
10/2022 51
Fig. 19: Check of solenoid valve operation and then navigate to the Services section and select Calibration and repair services .
Then enter the type of sensor (sensor type: DMT143 ) and select a calibration type, then follow the provided instructions.
22.13. Cleaning and disinfection of the exterior surfaces of the product
Clean and disinfect the exterior surfaces with neutral cleaning products.
Use of aggressive detergents and disinfectants containing alcohol and chlorides can lead to surface damage and discolouration. valve on the air tank open. Switch off the compressor using the main switch, close the condensate drain valve and disconnect the equipment from the mains. applicable regulations.
Entrust a specialised company to sort and dispose of waste.
Worn out components have no negative environmental impact.
NP-DK50-Nx2VTM-ADM-EN-3_10-2022
TROUBLESHOOTING
TROUBLESHOOTING
Risk of electric shock.
Before interfering with the equipment, first disconnect it from the mains (remove the power socket).
Working with pressurised pneumatic components poses a risk of injury.
Before interfering with the equipment, vent the air tank and the compressed air system to zero pressure.
Malfunction Possible cause
Problem with electrical power source
Troubleshooting may only be performed by a qualified service technician.
Damage to the safety valve could cause pressure to rise to hazardous levels.
Never adjust a safety valve.
Compressor does not start
Power loss
Pressure switch failed
Loss of power to motor
Any of the air pumps does not start up
(indicator is on)
Motor winding shorted, damaged /open thermal protection/ high ambient temperature
Seized up piston or other moving component (mechanical damage to a moving part)
Solution
Main breaker is off
Check mains voltage
Loose terminal in switchboard – tighten
Check the primary power connection - replace if damaged
Check terminals and operation of the pressure switch - replace if damaged
Check mains voltage
Check the function of the contactor, and thermal relays - replace if damaged
Loose terminals at the motor terminal strip - tighten or replace if damaged or broken
Replace the motor / decrease the ambient temperature
Replace damaged parts
Controller malfunction
Loss of connection between controller and expansion module
RUN/STOP indicator is not green
Power loss
Air pumps switch often, even without demand for air
Problem with electrical power source
Controller or expansion module malfunction
Air leak in compressed air distribution system
Leaky check valves
Check controller operation, check to ensure software is present - replace if damaged or upload the correct program
Check connection – replace if damaged
Check mains voltage
Loose terminal in switchboard – tighten
Check the primary power connection - replace if damaged
Main breaker is off
Replace failed controller or expansion module
Check compressed air distribution system – seal loose joints
Test check vales and clean, or replace if damaged
NP-DK50-Nx2VTM-ADM-EN-3_10-2022 52 10/2022
TROUBLESHOOTING
Output of certain air pumps is reduced, extended run cycle
Output of certain air pumps is reduced, extended run cycle
Leak through solenoid valves once regeneration is complete
Leak at pressure sensor and safety valve
Air pump leaking
Worn piston rings
Gasket between cylinder head and valve plate damaged
Clean the check valve - replace if damaged
Test their function and clean, or replace if damaged
Check connections on the air pump for leaks – tighten leaking connections
Replace worn piston
Replace gasket, tighten
Air pump leaking
Damaged motor bearing
Check connections on the air pump for leaks – tighten leaking connections
Replace damaged bearing
One of the air pumps is noisy (knocking, metal noises)
Damaged piston bearing, piston rod Replace damaged piston
Failed (cracked) rubber mount spring
Replace damaged spring with new spring
Lack of ventilation in compressor room Secure suitable ambient conditions
High ambient temperature causes compressors to switch off in vertical stacks (overheating)
Cooling fans for aggregates, cooler and enclosure do not work
Defective fans - replace
Defective temperature switch - replace
Low operating pressure
Reduce the demand for air, check the output from the compressed air source, fix any leaks in the distribution system
Degraded drying performance – highpressure dew point
(condensed water in the air)
Regeneration solenoid valve not working
Air regeneration nozzle plugged
Cooling fan not working
Dirty cooler
Check coil operation, replace if damaged
Dryer emitting high levels of noise
Air leaking through relief valve at dryer inlet
Silencer plugged regeneration valve
Damaged fan
Damaged silencer
Air leaking through relief valve at dryer inlet
Compressor running at high working pressure
Dryer inlet solenoid valve not working
High pressure in equipment resulting from plugged filters at outlet from
Clean or replace the nozzle
(see product maintenance)
Check the power source to the fan
Replace damaged fan
Inspect the cooler and clean as necessary
Inspect the silencers. Clean or replace the silencer if flow resistance is too high or if heavily soiled.
Replace damaged fan
Replace the silencer
Check the dryer connection to the mains and dryer connections, check dryer operation, check the dryer’s working pressure, and replace defective components.
Check the compressor’s working pressure setting
Check coil operation, replace if damaged
Inspect the condition of the valve - clean the valve or replace if problems persist
Check the internal filters and accessory filter assemblies.
Clean or replace dirty filters.
Once a fault is cleared and after reassembling the dryer, the condensate must be drained from the air tank, then dry the air tank, and the dryer must be regenerated, best when using
10/2022 53 continuous compressor operation at a pressure of around 7.0 bar for a period of at least 1 hour.
NP-DK50-Nx2VTM-ADM-EN-3_10-2022
TROUBLESHOOTING
Check the moisture content of the air exiting the air tank (see the Technical data chapter) to prevent damage to connected downstream equipment.
25. REPAIR SERVICE
Warranty and post-warranty repairs must be done by the manufacturer, its authorized representative, or service personnel approved by the supplier.
Attention.
The manufacturer reserves the right to make changes to the equipment without notice. Any changes made will not affect the functional properties of the equipment.
NP-DK50-Nx2VTM-ADM-EN-3_10-2022 54 10/2022
ANNEX
ANNEX
26. INSTALLATION RECORD
1. Product: (model)
DK50 4x2VT/M
3.1. User’s name:
2. Serial number:
3.2. Address of installation:
4. Equipment connected to the compressor:
5. Installation / Commissioning:
Product completeness check **
6. Contents of operator training:
Y Description of the product and functions**
Documentation completeness check **
Installation/connection to equipment **
Functional test **
Y
N N
Y Product operation: turning on/off, controls, control procedures, data on the display panel,
N alarms, operation in alarm conditions**
Y
N
Y Product maintenance: maintenance intervals, maintenance procedure, service intervals,
N operating activities**
Y
N
Y Safety measures, warnings – their meaning and compliance **
N
Y
N
Notes:
7. Operator instructed on safety measures, operations and maintenance:
Name: Signature:
Signature: Name:
Name:
8. Installation and instruction performed by:
Signature:
Signature:
First name/Last name
Company: Address:
Phone:
Email: Date:
9. Distributor:
Company:
Contact person:
Phone:
Address:
Email:
** mark with an “X” in points 5 and 6 (Y - yes /N - no). Enter any observations from points 5 and 6 into the
“Notes” section
10/2022 55 NP-DK50-Nx2VTM-ADM-EN-3_10-2022
NP-DK50-Nx2VTM-ADM-EN-3_10-2022
112000595-0001
advertisement
Related manuals
advertisement
Table of contents
- 5 IMPORTANT INFORMATION
- 5 CONFORMITY WITH THE REQUIREMENTS OF EUROPEAN UNION DIRECTIVES
- 5 INTENDED USE
- 5 CONTRAINDICATIONS AND SIDE-EFFECTS
- 5 SYMBOLS
- 6 WARNINGS
- 8 STORAGE AND TRANSPORT CINDITIONS
- 9 PRODUCT DESCRIPTION
- 9 VARIANTS
- 10 ACCESSORIES
- 11 PRODUCT FUNCTION
- 15 TECHNICAL DATA
- 22 INSTALLATION
- 22 INSTALLATION CONDITIONS
- 23 COMPRESSOR ASSEMBLY
- 26 PNEUMATIC CONNECTION
- 28 ELECTRICAL CONNECTION
- 29 COMMISSIONING
- 31 PNEUMATC DIAGRAMS
- 33 OPERATION
- 33 SWITCHING THE COMPRESSOR
- 36 SWITCHING OFF THE COMPRESSOR
- 37 AD DRYER
- 37 PRINCIPLE OF OPERATION
- 38 USER INTERFACE / SETTINGS
- 40 MAIN SCREENS
- 42 INDICATION OF MAINTENANCE AND ALARM STATES
- 44 PRODUCT MAINTENANCE
- 51 LONG-TERM SHUTDOWN
- 51 DISPOSAL OF DEVICE
- 52 TROUBLESHOOTING
- 54 REPAIR SERVICE
- 55 ANNEX
- 55 INSTALLATION RECORD