advertisement
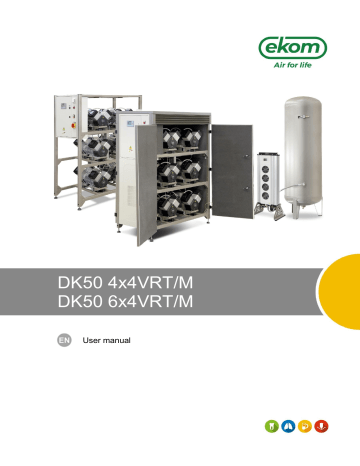
DK50 4x4VRT/M
DK50 6x4VRT/M
User manual
COMPRESSOR
DK50 4x4VRT/M
DK50 6x4VRT/M
EKOM spol. s r. o.
Priemyselná 5031/18
SK-
921 01 Piešťany
Slovak Republic tel.: +421 33 7967255 fax: +421 33 7967223 www.ekom.sk email: [email protected]
DATE OF LAST REVISION 04/2022
NP-DK50-Nx4VRTM-AD-A-
EN-5_04-2022
112000555-0001
CONTENTS
CONTENTS
GENERAL INFORMATION ........................................................................................................... 5
1.
CONFORMITY WITH THE REQUIREMENTS OF THE EUROPEAN UNION .................. 5
2.
SYMBOLS ....................................................................................................................... 5
3.
DEVICE USE................................................................................................................... 6
4.
GENERAL SAFETY INSTRUCTIONS ............................................................................. 7
5.
STORAGE AND TRANSPORT CONDITIONS ................................................................ 8
PRODUCT DESCRIPTION ........................................................................................................... 9
6.
VARIANTS ...................................................................................................................... 9
7.
ACCESSORIES .............................................................................................................11
8.
PRODUCT FUNCTION ..................................................................................................13
TECHNICAL DATA ......................................................................................................................16
INSTALLATION ...........................................................................................................................20
9.
INSTALLATION CONDITIONS .......................................................................................20
10.
COMPRESSOR ASSEMBLY .........................................................................................21
11.
PNEUMATIC CONNECTION .........................................................................................25
12.
ELECTRICAL CONNECTION ........................................................................................28
13.
COMMISSIONING .........................................................................................................34
14.
PNEUMATIC DIAGRAMS ..............................................................................................35
OPERATION ................................................................................................................................38
15.
SWITCHING ON THE COMPRESSOR ..........................................................................39
16.
SWITCHING OFF THE COMPRESSOR ........................................................................47
PRODUCT MAINTENANCE ........................................................................................................48
17.
PRODUCT MAINTENANCE ...........................................................................................48
18.
LONG-TERM SHUTDOWN ............................................................................................63
19.
DISPOSAL OF DEVICE .................................................................................................64
TROUBLESHOOTING .................................................................................................................64
20.
REPAIR SERVICE .........................................................................................................66
ANNEX .........................................................................................................................................67
21.
MAPPING PARAMETERS .............................................................................................67
22.
INSTALLATION RECORD..............................................................................................69
NP-DK50-Nx4VRTM-AD-A-EN-5_04-2022 4 04/2022
GENERAL INFORMATION
GENERAL INFORMATION
Carefully read this user manual before using the product and carefully store it for future reference. The user manual aids in the proper use, including installation, operation and maintenance, of the product.
The user manual corresponds to the configuration of the product and its compliance with applicable safety and technical standards at the time of its printing.
The manufacturer reserves all rights for the protection of its configuration, processes and names.
The Slovak version represents the original version of the user manual. The translation of the user manual is performed in accordance with the best available knowledge. The Slovak version is to be used in the event of any uncertainties.
The user manual is original and the translation is performed with the best available knowledge.
1. CONFORMITY WITH THE REQUIREMENTS OF THE EUROPEAN UNION
This product conforms to the requirements of the European Union 2006/42/EC,
2014/29/EU, 2014/35/EU, 2014/30/EU,
2011/65/EU and is safe if used in compliance with the intended use and if all safety instructions are followed.
User manual is in compliance with requirements of Directive 2006/42/EC.
2. SYMBOLS
The following symbols and marks are used in the User manual, on the device and its packaging:
General warning
Warning - risk of electric shock
Warning - compressor is controlled automatically
Warning - hot surface
General caution
Read the operating instructions
Refer to instruction manual
CE – marking
Serial number
Protecting earthing
Terminal for ground connection
04/2022 5 NP-DK50-Nx4VRTM-AD-A-EN-5_04-2022
GENERAL INFORMATION
Fuse
Compressed air inlet
Compressed air outlet
Control wire input
Package handling label – fragile
Package handling label – this side up
Package handling label – keep dry
Package handling label – temperature limits
Package handling label – limited stacking
Package label – recyclable material
Manufacturer
3. DEVICE USE
3.1. Intended use
The compressor is used as source of clean oilfree compressed air intended to be used in industry and laboratories, where parameters and properties of the compressed air are suitable.
The compressor is exclusively intended to compress air without content of explosive or chemically unstable substances.
The compressor is intended for operation in clean and dry rooms
3.2. Incorrect use
Contamination risk.
Air from the compressor is without additional treatment not suitable for breathing and direct contact with food
Explosion risk.
The product is not intended for operation in rooms with explosion risk.
The compressor must not be used to compress aggressive gases.
The compressor must not be operated in premises with occurrence of flammable vapors.
The compressor must not be operated in other conditions as mentioned in Technical data.
Any other use of the product beyond the intended use is considered as incorrect use.
The manufacturer is not responsible for any damages or injuries as a result of incorrect use or disobedience to instructions stated in this User manual. All risks shall be solely borne by the user/operator.
NP-DK50-Nx4VRTM-AD-A-EN-5_04-2022 6 04/2022
GENERAL INFORMATION
4. GENERAL SAFETY INSTRUCTIONS
The product is designed and manufactured so that any risks connected with its use are minimized and the product is safe for the user and surrounding when used according to the intended use and the instructions stated below are followed.
4.1. Required qualification of the personnel
Each user must be trained by the manufacturer or an organization authorized by the manufacturer or instructed on the device operation by other trained user.
Installation, new settings, changes, extensions and repairs of the product may be performed by the manufacturer or an organization authorized by the manufacturer
(hereinafter qualified technician).
- Otherwise the manufacturer is not responsible for safety, reliability and correct functioning of the product.
4.2. General instructions
When operating the compressor, all acts and local regulations valid in the place of use must be observed. The operator and user are responsible for following the applicable regulations.
Before every use, the user must check, if the device is functioning correctly and safely. Before building the compressor in other devices, the supplier must assess, if the supplied air and construction of the device comply with the requirements of the specified intended use. Taking this into account, follow the product technical data. Assessment of conformity shall be performed by the manufacturer – supplier of the final product.
4.3. Protection from dangerous voltage and pressure
The equipment may only be connected to a properly installed socket connected to earth (grounded).
Before the product is plugged in, make sure that the mains voltage and frequency stated on the product are the same as the power mains.
Check for any damage to the connected compressed air system and electrical circuits before use. Replace damaged pneumatic and electrical conductors immediately.
Immediately disconnect the product from the mains (remove the power cord from the socket) in hazardous situations or when a technical malfunction occurs.
Never adjust or use the safety valve to release the air pressure in the air tank.
Never adjust or use pressure relief valves to release air pressure from the device.
4.4. Original spare parts and accessories
Only the use of original parts guarantees the safety of operating personnel and flawless operation of the product itself. Only accessories and replacement parts specified in the technical documentation or expressly approved by the manufacturer may be used.
The warranty does not cover damage resulting from the use of other accessories and replacement parts as specified or recommended by the manufacturer and the manufacturer has no related liability.
04/2022 7 NP-DK50-Nx4VRTM-AD-A-EN-5_04-2022
GENERAL INFORMATION
5. STORAGE AND TRANSPORT CONDITIONS
The compressor is shipped from the manufacturer in transport packaging. This protects the product from damage during transport.
Potential for damage to pneumatic components.
The compressor must be transported only when all air has been vented. Before moving or transporting the compressor, release all the air pressure from the tank and pressure hoses, from dryer chambers and drain condensate from the tank and from the condensate separator on the dryer.
Keep the original factory packaging in case the device needs to be returned Use the original factory packaging during transport as it provides optimum protection for the product. . If it is necessary to return the product during the warranty period, the manufacturer is not liable for damages caused by improper packaging.
The compressor is shipped in a vertical position and must be secured using transport straps.
Protect the compressor from humid and dirty extreme near any substances.
environments temperatures transport and storage. Do not store volatile
If not, please dispose of the original packaging material in an environmentally-friendly way. The packaging cardboard can be recycled with old paper.
Storing or shipping the equipment in any conditions other than those specified below is prohibited.
and during chemical
5.1. Ambient conditions
Products may only be stored and transported in vehicles that are free of any traces of volatile chemicals under the following climactic conditions:
Temperature
Relative humidity
–25°C to +55°C, 24 h at up to +70°C max. 90% (non-condensing)
NP-DK50-Nx4VRTM-AD-A-EN-5_04-2022 8 04/2022
PRODUCT DESCRIPTION
PRODUCT DESCRIPTION
6. VARIANTS
The compressor is manufactured according to its intended application in the following variants:
DK50 4x4VRT/M
DK50 6x4VRT/M
Composed of modules:
1 compressor module with 4 or 6 aggregates and controls for the assembled unit
2 adsorption dryer with connecting hoses
3 air tank module
DK50 4x4VRTS/M Composed of modules:
DK50 6x4VRTS/M
1 compressor module together with a noise reducing enclosure and comprised of 4 or 6 aggregates and controls for the assembled unit
2 adsorption dryer with connecting hoses
3 air tank module
04/2022
DK 50 4x4VRT/M
9 NP-DK50-Nx4VRTM-AD-A-EN-5_04-2022
PRODUCT DESCRIPTION
DK 50 6x4VRT/M
NP-DK50-Nx4VRTM-AD-A-EN-5_04-2022
DK50 4x4VRTS/M
10 04/2022
PRODUCT DESCRIPTION
DK50 6x4VRTS/M
7. ACCESSORIES
Accessories that are not included in the standard order must be ordered separately.
DK50 4x4VRT/M performance upgrade kit
If DK50 4x4VRT compressor performance is not keeping up with demand, a simple solution is to contact the manufacturer about the DK50
Use
Central intake
Existing type of dryer
DK50 4x4VRT/M no AD 1000E
DK50 4x4VRTS/M
DK50 4x4VRT/M
DK50 4x4VRTS/M yes AD 1000E
6x4VRT/M performance upgrade kit.
The DK50 4x4 VRT/M conversion kit converts the existing compressor into a fully functional
DK50 6x4VRT/M compressor with the required parameters in an efficient manner at optimal cost.
New type of dryer
AD
1500E
AD
1500E
Rated voltage / working pressure
3x400 V / 50 Hz
(6-8 bar)
3x400 V / 50 Hz
(8-10 bar)
3x400 V / 50 Hz
(6-8 bar)
3x400 V / 50 Hz
(8-10 bar)
Article number
447000009-171
447000009-172
447000009-173
447000009-174
Central air pump intake kit
This kit provides a properly sized central intake filter located on the compressor module used to supply the intakes of the individual air pumps. This extends the central filter
04/2022 11 replacement interval (to every 2000 hours) compared to the interval for changing the filters on individual compressors, and ensures simpler and faster central filter replacement.
NP-DK50-Nx4VRTM-AD-A-EN-5_04-2022
Use
DK50 4x4VRT/M
DK50 4x4VRTS/M
DK50 6x4VRT/M
DK50 6x4VRTS/M
Set of compressed air outlet filters
The compressor may be equipped with a set of filters if specified. The filter set may be equipped with an air pressure regulator.
PRODUCT DESCRIPTION
Article number
447000001-021
447000001-020
447000001-019
447000001-018
Where a different level of air filtration is required, this requirement must be agreed upon with the supplier and specified in the order.
Type
FS 40F
FS 40M
FS 40S
FS 40AH
Type
FS 41F
FS 41M
FS 41S
FS 41AH
Use
DK50
4x4VRT/M
Use
DK50
6x4VRT/M
Level of filtration
( µm)
1
1+0.1
1+0.01
1+AC+HC (0.01)
Level of filtration
( µm)
1
1+0.1
1+0.01
1+AC+HC (0.01)
Bypass function * no
Bypass function * no
Article number
604014119-000
604014119-004
604014119-024
604014119-005
Article number
604014119-006
604014119-010
604014119-025
604014119-011
*) These FS do not contain a filter bypass, which will ensure a continuous flow of air when replacing the filter element. Such a set must be ordered separately. pressure regulator of the compressed air outlet if specified. The regulator must be selected according to the application to the filter set, or separately the regulator shall ensure constant pressure at the outlet.
Filter set regulator assembly
The compressor may be equipped with a
Type
Regulator complete
Use
DK50 4x4VRT/M
DK50 6x4VRT/M
Article number
604014125-000
Filter set brackets
A suitable bracket must be ordered for every filter set.
Type
Compressor-mounted bracket
Wall-mounted bracket
NP-DK50-Nx4VRTM-AD-A-EN-5_04-2022
Use
DK50 4x4VRT/M
DK50 6x4VRT/M
12
Article number
603014139-000
603014120-000
04/2022
PRODUCT DESCRIPTION
Compressor module enclosure (noise reducing)
Enclosing the compressor module reduces the noise generated by the compressor by up to 11 dB(a) compared to the compressor module without the enclosure while ensuring sufficient cooling for the air pumps themselves for S1 class continuous operation.
With central intake Article number Use
DK50 4x4VRT/M
DK50 6x4VRT/M
DK50 4x4VRT/M
DK50 6x4VRT/M yes no
447000001-022
447000001-023
8. PRODUCT FUNCTION
8.1. Compressor with adsorption dryer
Fig. 1: Compressor aggregates (12) draw in
atmospheric air through the intake filters and compress it through check valves into the compressed air system. A connecting hose
(13) connects this system to the external adsorption dryer (8). From the inlet to the dryer module, the air is first cooled in the integrated cooler (9) and then through the condensate separator (10), entering the active chamber with adsorbent (11), where the air is dried. A portion of the air is fed into the second, regeneration chamber, where this air is used to remove moisture from the adsorbent, after which it is released through the silencer (21). The active chamber switches on a cyclical basis. Dry and filtered air then passes through the check valve into the air tank (2). The treated compressed air is ready for additional use in the air tank.
04/2022 13 NP-DK50-Nx4VRTM-AD-A-EN-5_04-2022
Fig. 1 - Compressor with dryer
PRODUCT DESCRIPTION
NP-DK50-Nx4VRTM-AD-A-EN-5_04-2022 14 04/2022
PRODUCT DESCRIPTION
Fig. 2
– Electrical box / switchboard
Descriptions for figures 1-2:
1. Compressor module
2. Air tank
3. Electrical box / switchboard
4. Safety valve
5. Pressure sensor
6. Pressure gauge
7. Outlet valve
8. Adsorption dryer
9. Integrated cooler
10. Condensate separator
11. Dryer chamber
12. Air pump
13. Connecting hoses
14. Electrical cables
15. Drain valve
16. Display
17. Indicator - alarm
18. Start/stop button
19. Main switch
20. Temperature sensor
21. Noise silencer
22. Condensate drain solenoid valve
23. Non-return valve
24. Connector
04/2022 15 NP-DK50-Nx4VRTM-AD-A-EN-5_04-2022
TECHNICAL DATA
TECHNICAL DATA
Compressors are designed for operation in dry, ventilated and dust-free indoor rooms under the following climactic conditions:
Temperature
Relative humidity
+5°C to +40°C max. 70%
DK50
4x4VRT/M
DK50
4x4VRTS/M
DK50
6x4VRT/M
DK50
6x4VRTS/M
Working pressure 6 – 8 bar
Rated voltage
Frequency a)
Output at 6 bar (FAD) at
PDP20°C
Output at 6 bar (FAD) at
PDP40°C
Working pressure b)
V, Hz l/min. l/min. bar
A Rated current
Main circuit protection device rating
Main electrical feeder
A mm 2
Enclosure
Motor output
Air tank capacity
Air quality – filtration
Maximum operating pressure of safety valve
Noise at 5 bar (L pA
)
Operating mode
PDP drying performance at 7 bar d)
Time to fill air tank from
0 to 7 bar
Net weight c)
Weight - compressor module
Weight - dryer module
Weight of air tank
Net dimensions
W x L x H
Dimensions - compressor module
(W x L x H)
Dimensions – dryer module
Air tank dimensions
(W x L x H)
Required cooling air changes in space kW
l m bar dB
%
°C s kg kg kg kg mm mm mm mm m 3 /h
3x400, 50
910
870
6.0 – 8.0
22
25
4
IP10
2.2
500
-
10.0
≤80
S1-100
-20
-40
150
439
268
44
127
2875 x 2090 x
705
1235 x 1720 x
630
530 x 965 x
350
730 x 2090 x
705
2250
3x400, 50
910
870
6.0 – 8.0
22
25
4
IP30
2.2
500
-
10.0
≤70
S1-100
-20
-40
150
572
401
44
127
2875 x 2090 x
705
1235 x 1755 x
705
530 x 965 x
350
730 x 2090 x
705
2250
3x400, 50
1370
1300
6.0 – 8.0
29
32
6
IP10
2.2
500
-
10.0
≤83
S1-100
-20
-40
115
531
350
54
127
2875 x 2090 x 705
1235 x 1720 x 630
530 x 1310 x
350
730 x 2090 x
705
3000
3x400, 50
1370
1300
6.0 – 8.0
29
32
6
IP30
2.2
500
-
10.0
≤72
S1-00
-20
-40
115
664
483
54
127
2875 x 2090 x
705
1235 x 1760 x
705
530 x 1310 x
350
730 x 2090 x
705
3000
NP-DK50-Nx4VRTM-AD-A-EN-5_04-2022 16 04/2022
TECHNICAL DATA a) Specify the compressor version when ordering b) Consult any other range of pressure with the supplier c) d)
Weight is indicative and only applies to the product without accessories
Applies to ambient temperatures of <30°C PDP – pressure dew point
Dependence of compressor output on working pressure
04/2022 17 NP-DK50-Nx4VRTM-AD-A-EN-5_04-2022
TECHNICAL DATA
Working pressure 8 – 10 bar
Rated voltage
Frequency a)
Output at 8 bar (FAD) at
PDP20°C
Output at 8 bar (FAD) at
PDP40°C
Working pressure b)
V, Hz l/min. l/min. bar
A Rated current
Main circuit protection device rating
Main electrical feeder
A mm 2
Enclosure
Motor output kW l
m
Air tank capacity
Air quality – filtration
Maximum operating pressure of safety valve
Noise at 5 bar (L pA
)
Operating mode
PDP drying performance at 7 bar d)
Time to fill air tank from
0 to 7 bar
Net weight c)
Weight - compressor module
Weight - dryer module bar dB
%
°C s kg kg kg
DK50
4x4VRT/M
3x400, 50
700
660
8.0 – 10.0
23
25
4
IP10
2.2
500
-
11.0
≤80
S1-100
-20
-40
150
439
268
DK50
4x4VRTS/M
3x400, 50
700
660
8.0 – 10.0
23
25
4
IP30
2.2
500
-
11.0
≤70
S1-100
-20
-40
150
572
401
44 44
Weight of air tank
Net dimensions
W x L x H
Dimensions - compressor module
(W x L x H)
Dimensions – dryer module
Air tank dimensions
(W x L x H)
Required cooling air changes in space kg mm mm mm mm m 3 /h
127
2875 x 2090 x
705
1235 x 1720 x
630
530 x 965 x
350
730 x 2090 x
705
2250
127
2875 x 2090 x
705
1235 x 1755 x
705
530 x 965 x
350
730 x 2090 x
705
2250 a) Specify the compressor version when ordering b) Consult any other range of pressure with the supplier c) Weight is indicative and only applies to the product without accessories d) Applies to ambient temperatures of <30°C PDP – pressure dew point
DK50
6x4VRT/M
3x400, 50
1050
DK50
6x4VRTS/M
3x400, 50
1050
1000
8.0 – 10.0
30
32
6
IP10
2.2
500
-
11.0
≤83
S1-100
-20
-40
115
531
350
664
483
54
127
2875 x 2090 x 705
1235 x 1720 x 630
530 x 1310 x
350
730 x 2090 x
705
3000
54
127
2875 x 2090 x
705
1235 x 1760 x
705
530 x 1310 x
350
730 x 2090 x
705
3000
1000
8.0 – 10.0
30
32
6
IP30
2.2
500
-
11.0
≤82
S1-00
-20
-40
115
NP-DK50-Nx4VRTM-AD-A-EN-5_04-2022 18 04/2022
TECHNICAL DATA
Dependence of compressor output on working pressure
FAD correction of capacity for altitude
Capacity given in the form of FAD („Free Air Delivery“) applies to the following conditions:
Altitude 0 m.n.m.
Atmospheric pressure 101325 Pa
Temperature
Relative humidity
20°C
0%
To calculate FAD compressor capacity in dependence on altitude, it is necessary to apply correction factor according to the following table:
Altitude [m.n.m.]
FAD correction factor
0 -1500
1
1501 - 2500
0.80
2501 - 3500
0.71
3501 - 4500
0.60
04/2022 19 NP-DK50-Nx4VRTM-AD-A-EN-5_04-2022
INSTALLATION
INSTALLATION
Risk of incorrect installation.
Only a qualified technician may install the compressor and place it into operation for the first time. Their duty is to train operating personnel on the use and maintenance of the equipment. An entry is made in the equipment installation record to certify installation and operator training. (see the
Annex chapter)
9. INSTALLATION CONDITIONS
The compressor may only be installed and operating in dry, well-ventilated and clean environments under the conditions specified in the Technical
Data chapter.
Risk of damage to the device.
The equipment may not be operated outdoors or in otherwise wet or damp environments.
Risk of explosion.
Do not use the equipment in the presence of explosive gases, dust or combustible liquids.
The compressor must be installed so that it is accessible at all times for operating and maintenance. Please ensure that the nameplate on the device is readily accessible.
The compressor must stand on a flat, sufficiently stable base (be aware of the weight of the compressor, see the
Technical Data chapter).
The compressor on the operator’s side must be at least 70 cm from the wall to allow air flow for cooling purposes and to ensure the safety of the operator and maintenance personnel.
Approximately 70% of the electrical energy used by the compressor aggregates is converted to heat, and
NP-DK50-Nx4VRTM-AD-A-EN-5_04-2022 20 therefore the rooms in which the compressor is installed must have additional ventilation to provide sufficient air exchange for cooling purposes (see the Technical Data chapter).
Burn or fire hazard! Caution!
Hot surface!
Portions of the compressor, dryer and connecting hoses between the dryer and compressor may be hot and reach hazardous temperatures during compressor operation that may harm materials or operating staff.
High temperature hazard
Placing air flow impediments upstream or downstream of the cooler is prohibited. The temperature of internal and external parts of the equipment may rise to hazardous levels.
You may notice a “new product” odour when you first place the product into service
(for a short period of time). This odour is temporary and does not impede the normal use of the product. Ensure the space is properly ventilated after installation.
04/2022
INSTALLATION
Fig. 3: Equipment installation
Air outlet
Space conditions
-
Temperature +5°C ÷ +40°C
- Relative humidity 70%
10. COMPRESSOR ASSEMBLY
10.1. Handling and releasing the compressor
Unpack the compressor (compressor modules, dryer and air tank) from the packaging and remove the transport anchors from the pallet. All modules
Fig. 4: Handling the compressor module
Recommended flow of cooling air:
DK50 6x4VRT/M - 3000 m 3 /h.
DK50 4x4VRT/M – 2250 m 3 /h.
Applies for continuous operation and cooling air temperature of20°C
Cooling air inlet are secured to pallets.
Use a fork lift or similar hoisting equipment to handle and position the product.
Position the compressor module at the
site of installation (Fig. 4 A).
04/2022
A
21
B
NP-DK50-Nx4VRTM-AD-A-EN-5_04-2022
Fig. 5: Levelling the compressor
INSTALLATION
Prior to installation, ensure that the compressor is free of all transport packaging and stabilizers to avoid any risk of damage to the product.
Remove all devices used to secure the aggregates once the compressor is installed and levelled at the site of final installation.
NP-DK50-Nx4VRTM-AD-A-EN-5_04-2022 22 04/2022
INSTALLATION
Fig. 6: Releasing the air pumps
Remove the transport stabilisers from the air
DK50 4x4VRT/M – 8 mounts.
DK50 6x4VRT/M – 12 mounts
04/2022 23 NP-DK50-Nx4VRTM-AD-A-EN-5_04-2022
INSTALLATION
Air tank assembly
Fig. 7:Handling the air tank
Position the air tank at the site of installation and anchor it to the floor.
Assembly of the AD dryer
Remove the dryer from the packaging.
Install the dryer in its operating
At least two persons are needed to handle the equipment.
Integrated handles are installed on the lower brackets on the product. Each person must grasp the equipment with one hand on a handle and the other behind the dryer chamber when moving the equipment.
NP-DK50-Nx4VRTM-AD-A-EN-5_04-2022 24 04/2022
INSTALLATION
Fig. 8: Handling the dryer
11. PNEUMATIC CONNECTION
Connect compressor module, dryer module, and the air tank with the provided hoses. (Fig. 9)
Fig. 9: Connecting the compressor module, dryer and air tank
04/2022 25 NP-DK50-Nx4VRTM-AD-A-EN-5_04-2022
INSTALLATION
Fig. 10: Connecting the enclosed compressor module, dryer and air tank hose length 1 [mm] hose length 2 [mm]
DK50 4x4VRT/M 1000 600
DK50 4x4VRTS/M 600
DK50 6x4VRT/M 1300
DK50 6x4VRTS/M 600
600
1000
1000
AD dryer compressed air inlet
Connect to the compressor outlet
A G 3/4” connection is installed
NP-DK50-Nx4VRTM-AD-A-EN-5_04-2022 26
Fig. 11: Compressed air inlet
04/2022
INSTALLATION
Burn or fire hazard! Caution!
Hot surface!
When installing the connecting hoses at the inlet to the air dryer, ensure that the temperature is not hazardous if it was to come into contact with an operator or other material.
AD dryer compressed air outlet
Connect the outlet from the dryer (1) to the air inlet on the air tank.
A G 3/4” connection is installed.
Condensate outlet from dryer
Connect a hose to the outlet (1) from the automatic condensate drain (2) to drain piping or to the provided
Fig. 12: Compressed air outlet collection vessel.
A noise silencer is recommended when connecting directly to drain piping.
Fig. 13: Condensate drain
04/2022 27 NP-DK50-Nx4VRTM-AD-A-EN-5_04-2022
INSTALLATION
A G3/4” ball valve is installed on the compressed air outlet from the air tank.
Fig. 14: Air outlet from the air tank
Potential for damage to pneumatic components.
Ensure the air hoses are not kinked.
12. ELECTRICAL CONNECTION
Unauthorised hazard interference
Only a qualified electrician may install electrical components!
Risk of damage to the device.
The operator is obliged to provide circuit protection devices for the equipment per the specifications in valid technical standards.
The product is delivered without a power cord.
Connect the compressor module to the
dryer module using cable W22 (Fig.
Connect the compressor module to pressure sensor B1 located on the air tank using cable W23, which is terminated with a valve connector.
The manufacturer recommends protecting cabling loose on the floor (W22 and W23) with a cable bridge.
Connect the individual power cord conductors to the power terminals L1,
L2, L3, N(BU), PE(GNYE). (Fig. 19)
Recommended configuration of phase conductors: L1-BN, L2-BK, L3-GY.
Cord type (minimum requirements)
H05 VV-F_ 5G6
Route the power cord out of the enclosure as
NP-DK50-Nx4VRTM-AD-A-EN-5_04-2022 28 04/2022
INSTALLATION
Fig. 15: Connecting the compressor to the dryer
Fig. 16: Connecting the control signal
1. Harting connector
04/2022
Proper routing of the electrical cable to the dryer
29 NP-DK50-Nx4VRTM-AD-A-EN-5_04-2022
Fire hazard and risk of electric shock.
Ensure the electrical cable does not touch hot parts of the device or connecting hoses.
Fig. 17: Connecting the compressor to the pressure sensor
INSTALLATION
Cable bridge
NP-DK50-Nx4VRTM-AD-A-EN-5_04-2022 30 04/2022
INSTALLATION
Fig. 18: Electrical cord
Fig. 19: Connecting the power cord
Description of air pump controls
The air pumps are controlled in trios based on real demand. One trio is always set as the
MASTER (e.g. M1-3) and the others as
SLAVE (e.g. M4-6). The set of three Slave air pumps operate under the following conditions
- A waiting period (pressurising to the upper limit) of 1 minute under strong demand and 2 minutes under weak demand
- Pressure drops below 6.2 bar (SLAVE)
- Motor failure in the MASTER section
The lower limit settings ROTATE every 50 hours to ensure all the air pumps are evenly loaded.
04/2022 31 NP-DK50-Nx4VRTM-AD-A-EN-5_04-2022
INSTALLATION
Fig. 20: Air pump controls
A – motors M1-M3
B – motors M4-M6
UL – upper limit
BL – bottoms limit → Master = 6.2, SLAVE = 6.0
Description of adsorption dryer solenoid valve control
The inlet valves (Inlet A and B) switch every
120 seconds.
Fig. 21: Solenoid valve diagram
The regeneration valves open variably based on the real load, e.g. if all motors are running, flushing is set to 110 seconds, while if one trio set is running, flushing is set to 55 seconds.
NP-DK50-Nx4VRTM-AD-A-EN-5_04-2022 32 04/2022
INSTALLATION
Ethernet connection
The compressor may be connected to an
Ethernet 10/100 M network via the controller as follows:
1 Use the RJ-45 connector on the switchboard door to connect a cable to the Ethernet network.
2 The user shall then request IT staff to connect the compressor to the customer’s Ethernet network. The equipment’s default IP addresses are:
BM=192.168.0.3, TDE=192.168.0.2, sub-mask =255.255.255.0.
3 The user shall request the configuration of IP addresses (specific or requested) from the manufacturer
Open the web browser on a PC, smartphone or tablet and enter the IP address of the controller (in this case
192.168.0.3). before the compressor is shipped.
4 The user then configures the IP addresses (specific, requested) based on the manual (see the service manual) or uses the compressor manufacturer’s technical support for such purposes.
Web server
The controller has an integrated Web Server function that facilitates compressor monitoring via a PC, smartphone or tablet using a conventional web browser (Mozilla, Opera,
Safari, Google Chrome, etc.)
The process for logging into the Web Server function once the compressor is connected to an Ethernet network is as follows:
Enter the password “LOGO” and click on the “LOG on” button.
After logging in, the browser displays the first screen showing the system information for the controller itself: module generation, type, firmware
(FW), IP address and activity status.
Click on the “LOGO! BM” function in the browser to display the current virtual status of the display screen. Navigate through the screen using the ESC and cursor keys the same as on the real display.
04/2022 33 NP-DK50-Nx4VRTM-AD-A-EN-5_04-2022
Monitoring memory variables
The “LOGO! Variable” function is the other option for monitoring compressor parameters using selected memory variables. Click the
“LOGO! Variable” button on the display to bring up a screen and then use the “Add
Variable” button to select specific memory variables for monitoring based on the mapping provided by the compressor manufacturer.
INSTALLATION
Variables assigned based on addresses and models may be viewed in the MAPPING
PARAMETERS table (see the Annex chapter).
Select the variable parameters (per the annex) sequentially in the Range, Address,
Type and Display Format columns. Variable values are shown in the Value column. The monitoring table may then appear as follows:
Note:
Time values are displayed in minutes.
For instance, address 10 displays
120000 in minutes, which is 2,000
Logging out from the Web server:
Click on the button in the upper left corner.
13. COMMISSIONING
Make sure all transport stabilizers were removed.
Check that all compressed air hose connections are correct.
Ensure the power cord is properly connected to the mains and other cables are connected (compressorhours.
Analogue values (pressure and temperature) are displayed without decimal places. dryer and compressor-air tank).
Check to ensure the outlet valve is in the OFF position.
The compressor is not equipped with a backup power supply.
NP-DK50-Nx4VRTM-AD-A-EN-5_04-2022 34 04/2022
INSTALLATION
14. PNEUMATIC DIAGRAMS
DK50 4x4VRT/M, DK50 4x4VRTS/M
04/2022 35 NP-DK50-Nx4VRTM-AD-A-EN-5_04-2022
DK50 6x4VRT/M, DK50 6x4VRTS/M
INSTALLATION
NP-DK50-Nx4VRTM-AD-A-EN-5_04-2022 36 04/2022
INSTALLATION
Description to pneumatic diagrams:
1. Inlet filter
2. Air pump
3. Compressor fan
4. Solenoid valve
5. Safety valve
6. Non-return valve
7. Pressure relief valve
8. Condensate separator
9. Jet
10. Pressure sensor
11. Pressure gauge
12. Cooler
13. Cooler fan
14. Air tank
15. Drain valve
16. Outlet valve
17. Dryer solenoid valve
18. Central fan
19. Condensate collection vessel
20. Noise silencer
21. Coarse inlet filter
22. Adsorption filtration
23. Coarse outlet filter
24. OR logic valve
25. Dryer chamber 1
26. Dryer chamber 2
04/2022 37 NP-DK50-Nx4VRTM-AD-A-EN-5_04-2022
OPERATION
OPERATION
ONLY TRAINED PERSONNEL
MAY OPERATE
EQUIPMENT!
THE
Risk of electric shock.
In case of emergency, disconnect the compressor from the mains (pull out the mains plug).
Burn or fire hazard.
When the compressor is running, the connecting hose between the compressor and dryer and parts of the dryer and aggregate may be hot enough to burn people or other material.
Warning - compressor is controlled automatically.
Automatic compressor start. The automatically switches on when the pressure in the air tank drops to the pressure switch’s lower limit level. The compressor automatically switches off once the pressure in the tank reaches the shut-off pressure .
Potential for damage to pneumatic components.
The working pressure settings for the pressure switch set by the manufacturer cannot be changed. Compressor operation at a working pressure below the switching pressure indicates high air usage (see the
Troubleshooting chapter).
Risk of damage to the dryer.
The dryer may suffer damage if operated at ambient temperatures above its maximum working pressure as specified in the Technical Data chapter .
Required drying performance can only be achieved when following the defined operating conditions.
Drying performance will decline and the achieved dew point will drop if the dryer is operated at any pressure below the minimum working pressure.
During prolonged operation of the compressor, the temperature inside the enclosed model may increase to over 40°C. At this point the cooling fan in the enclosure and the compressor fan automatically switch on. The fans switch off automatically once the space is cooled to below 32°C.
NP-DK50-Nx4VRTM-AD-A-EN-5_04-2022 38 04/2022
OPERATION
15. SWITCHING ON THE COMPRESSOR
Turn the main switch (19) into the “I” position on the compressor switchboard. The white indicator P1
(17) lights up and the display (16) on the switchboard door shows the following message:
RUN HOURS: operating hours
PRESSURE: current pressure
TEMP_IN: internal temperature (only for enclosed version)
TEMPˇOUT: outdoor temperature
Press the "START” button (18) on the switchboard.
The display shows:
RUN HOURS: operating hours
STAND BY MODE or RUN MODE
Time-To-Go MTN: shows the time remaining until compressor maintenance is required
Note: TEMP_IN reads “N/A” for compressor models with no cover
TEMP_OUT: ambient temperature around the compressor
Press the START button to turn on all the compressor aggregates. The pressure sensor monitors the pressure in the air tank.
The aggregates operate in automatic mode, and are switched on and off (see the section on working pressures in the Technical Data chapter) by the controller depending on the compressed air usage. The compressors sequentially turn off once the switching pressure is reached.
The motors may be shut down by pressing the
STOP button (18), after which the display returns to the start screen.
Note: The START button is pre-set to
"RETENTIVITY=ON", which means that if the compressor has been activated once using the START button, the system remembers this action and there is no need to press the
START button to start up the compressor in the event of a power loss or if the compressor has been turned off.
Normal operation
Aggregates operate in automatic mode and are switched on and off based on the demand for compressed air. When the pressure in the air tank drops to the switching pressure, the compressors automatically switch on in a sequence. This ensures that the required pressure is delivered to the air tank in the shortest possible time.
Two screens are shown on the display during the normal operation of the equipment:
04/2022 39 NP-DK50-Nx4VRTM-AD-A-EN-5_04-2022
OPERATION
Motors are on
RUN MODE – all aggregates are switched on
RUN HOURS: operating hours
TIME-TO-GO MN - time to the next maintenance / service work (in hours).
Motors are switched off
PRESSURE: current working pressure
STANDBY MODE – all aggregates are switched off
RUN HOURS: operating hours
TIME-TO-GO MN - time to the next maintenance / service work (in hours).
The pressure sensor monitors the pressure in the air tank. The pressure is shown on the display.
Check all air line connections and check for compressed air leaks. Remedy all leaks that are identified.
Slowly open the outlet valve to the ON position. The compressor starts and runs until the pressure in the entire compressed air system stabilises. The aggregates then gradually turn off at the switching pressure.
Complete a record for the installation of the compressor assembly and commissioning
(see the Annex chapter).
Shutting down the compressor
Press the STOP button (18) to shut down the compressors.
NP-DK50-Nx4VRTM-AD-A-EN-5_04-2022 40
15.1. Controller – operation and alarms
The controller controls the aggregates, monitors their operation, analyses faults, reports alarms and indicates when maintenance is required after defined intervals are met.
The controller assesses the ambient and internal temperature of the compressor, working pressure and operating hours.
These values, alarms and service interval information are shown on the display.
Temperatures above the critical values are shown as alarms.
The control panel on the controller has four cursor buttons ▲, ▼, ►, ◄, ESC and OK buttons, and four function buttons F1-F4, which trigger the following:
F1 - in alarm display mode, press to switch back to normal operating mode for
60 seconds. Backlit screen.
04/2022
OPERATION
F2 – information on operating hours and maintenance intervals.
F3 – scrolls through:
- Motor malfunctions
- Number of motor starts
- Maximum temperatures
04/2022 41 NP-DK50-Nx4VRTM-AD-A-EN-5_04-2022
OPERATION
F4 - SERVICE TECHNICIAN BUTTON
(after completing service or maintenance work
- hold for 5 seconds to reset the 2,000 hour maintenance interval.)
Note: Pressing F1-3 on the control panel turns on the display back light for 30 seconds.
HOURS METER - aggregate operating hours
TIME –TO –GO MN - time to next maintenance/service
TOTAL HOURS: - total compressor operating hours
NUMBER of MN – number of completed maintenance (service) checks confirmed using the F4 button
The screen automatically returns to the home screen after 10 seconds.
Equipment operation
Normal operating mode is shown when the equipment is operating and the functional and control buttons are used to browse through the following:
Pressing F2:
NP-DK50-Nx4VRTM-AD-A-EN-5_04-2022 42 04/2022
OPERATION
Pressing F3:
This permits browsing through different auxiliary screens. E.g. displays the number of overload faults for motors M1 to M6 (motor circuit breaker disconnects the motor from power). The circuit breakers must be manually turned to the
ON position to remedy the malfunction.
The screen automatically returns to the home screen after 10 seconds.
04/2022 43 NP-DK50-Nx4VRTM-AD-A-EN-5_04-2022
OPERATION
Pressing F4:
F4 is only active if the maintenance screen appears once 2000 hours of operation have been passed (see the maintenance alarm).
Press and hold F4 for at least 5 seconds to set a new interval. The screen switches back to normal operating mode once the new interval is set.
Note: Only service personnel are authorised to configure a new service interval using the F4 button.
Alarms
The equipment has an intelligent monitoring system that generates an alarm signal based on priority (medium priority alarms have higher priority than low priority alarms).
Alarm signals have a higher priority than maintenance/service interval signals.
The maintenance/service interval is measured from the first time the equipment is energised.
All alarms are accompanied by a blinking red
P2 (Alarm) indicator.
Low priority alarm conditions
Expiry of defined maintenance / service interval
This alarm activates once the 2,000 hour maintenance/service interval expires. The display shows the following details:
SERVICE ACCORDING
INSTRUCTIONS FOR USE
TO
TOTAL HOURS - total time the equipment has been connected to power
RUN HOURS – equipment operating hours
The display flashes orange.
Note: Press F1 to switch to the normal operating mode screen for 60 seconds.
The compressor supplies air to the compressed air system as needed and without restriction.
Call in service personnel to perform the required service.
Note: Only service personnel are authorised to configure a new service interval.
Press F4 and hold for at least 5 seconds to confirm the completion of maintenance/service.
NP-DK50-Nx4VRTM-AD-A-EN-5_04-2022 44
The display then changes to the normal operating mode screen.
This indicates the new maintenance interval has been set on the controller from this time forward.
Any maintenance or service work must be recorded in the compressor’s service log.
Compressor module ambient temperature exceeds the limit.
04/2022
OPERATION
WARNING - high ambient temperature alarm.
The display flashes orange.
This alarm appears if the ambient temperature exceeds the 40°C limit for at least 30 seconds. The aggregates operate normally.
The display otherwise shows the current ambient air temperature.
The alarm clears when the temperature drops below the limit.
The compressor supplies air to the compressed air system as needed and without restriction.
Compressor module internal temperature exceeds the limit.
WARNING - high temperature alarm inside an enclosed compressor. The display flashes orange.
This alarm appears if the temperature inside the enclosed compressor module exceeds the 70°C limit for at least 30 seconds. The aggregates operate normally.
Note: The internal temperature monitoring function is not included on unenclosed compressors.
The display shows the current temperature inside the enclosed compressor module.
The alarm clears when the temperature drops below the limit.
The compressor supplies air to the compressed air system as needed and without restriction.
04/2022 45 NP-DK50-Nx4VRTM-AD-A-EN-5_04-2022
Low pressure alarm during compressor start-up.
SIGNALING - Low pressure alarm during compressor start-up. The display is backlit and the P2 alarm indicator flashes.
LOW PRESSURE MODE - low pressure signalling in the system with the aggregates switched on.
DRYER - REGENERATION NOT
CYCLING - no purging of the dryer chambers.
PRESSURE - current pressure in the system.
The information on the display automatically disappears once the air pressure is above 3 bar.
The compressor supplies air to the compressed air system as needed and without restriction.
Low pressure alarm at elevated compressed air demand.
SIGNALING – low pressure alarm at elevated compressed air demand. The display flashes orange.
PRESSURE - current pressure in the system
The display automatically disappears once the air pressure is above 3 bar.
The compressor supplies air to the compressed air system as needed and without restriction.
OPERATION
NP-DK50-Nx4VRTM-AD-A-EN-5_04-2022 46 04/2022
OPERATION
Medium priority alarm conditions
Air pump malfunction
The message on the display (FAULT) and indicator P2-ALARM (17) indicate that the aggregate is not running (a motor circuit breaker (Q1 - Q6) is tripped due to current overload). The display flashes red.
The other aggregates are working normally.
The screen disappears once the malfunction is remedied and the motor circuit breaker is manually placed back in the “ON” position.
The display for normal operation is shown.
The compressor only supplies compressed air to the central line through the functional aggregates.
All alarms are automatically recorded on an
SD card.
Alarm signals have priority over maintenance interval signals.
As such, the light will indicate an alarm from any of the aggregates.
All error signals are connected to controller output K3:Q3.2 and to terminals X1:44 and
X1:45 (in the control panel) as
NON VOLT ALARM SIGNAL.
Data collection
Data is recorded on a micro SD card in a slot in the base module. Malfunction and operating event data is recorded on this card.
Information is saved in “.csv” formatted files.
The system sequentially saves data into 50 files, each of which may have up to 20,000 lines.
To copy data from the SD card, manually remove the card and load the data using
Excel onto a PC or remotely via the Ethernet network.
Fig. 22: Data collection
16. SWITCHING OFF THE COMPRESSOR
Use the main switch, Q10, to switch off the compressor for maintenance or other reasons; the switch also functions as a central stop button. The compressor is disconnected from the mains with the exception of the mains terminal block X0.
Vent the air tank by disconnecting from the
04/2022 47 central compressed air circuit and opening the
outlet valve (Fig. 14) or the drain valve.
Power terminals X0 remain energised even when main switch Q10 is in the “O” (off) position.
NP-DK50-Nx4VRTM-AD-A-EN-5_04-2022
PRODUCT MAINTENANCE
17. PRODUCT MAINTENANCE
The operator shall secure the completion of repeated testing of the equipment at least once every 24 months (EN 62353) or at the intervals defined by the applicable national regulations.
A record of the test results must be made (e.g.: as per EN 62353,
Annex G), along with the measurement methods.
The equipment has been designed and manufactured to keep maintenance to a minimum. The following work must be performed to preserve the proper and reliable operation of the compressor.
Unauthorised hazard. interference
Repair work outside the framework of standard
may only be performed by a qualified technician (an organisation authorized by the manufacturer) manufacturer’s service. or the customer
Standard maintenance work
(see Chapter 17.1) may only be
performed by the operator’s trained personnel.
Only use manufacturerapproved replacement parts and accessories.
PRODUCT MAINTENANCE
Danger of injury or equipment damage.
Prior to commencing compressor maintenance, it is necessary to:
- check if it is possible to disconnect the compressor from the appliance in order to avoid any risk of injury to the person using the appliance or other material damage;
- turn off the compressor;
- disconnect it from the mains (pulling the cord out of the mains socket);
- vent the compressed air from the air tank .
Prior to commencing dryer maintenance work, first:
- shut off the compressed air supply to the dryer
- turn the main switch on the side of the switchboard to the “0” position;
- check the pressure indicator on the dryer and if there is still pressure, it must first be vented from the dryer chamber.
Venting compressed air poses an injury hazard.
Wear eye protection, i.e. goggles, when venting compressed air from the compressed air circuit (air tank) and from the dryer chamber.
NP-DK50-Nx4VRTM-AD-A-EN-5_04-2022 48 04/2022
PRODUCT MAINTENANCE
Burn hazard.
When the compressor is running or shortly thereafter, certain portions of the air pump, the compressor’s compressed air system, parts of the dryer and connecting hoses between the compressor and dryer may be hot - do not touch these components.
Allow the equipment to cool down before maintenance, service or connecting/disconnecting the compressed air supply!
The work below may only be performed by trained personnel as follows:
Before beginning any of the following maintenance work, first switch the main switch on the side of the switchboard to the “0” position.
Please follow the recommended service intervals for the equipment to ensure proper and safe operation.
04/2022 49 NP-DK50-Nx4VRTM-AD-A-EN-5_04-2022
17.1. Maintenance intervals operator qualified technician
PRODUCT MAINTENANCE
NP-DK50-Nx4VRTM-AD-A-EN-5_04-2022 50 04/2022
PRODUCT MAINTENANCE qualified technician
04/2022 51 NP-DK50-Nx4VRTM-AD-A-EN-5_04-2022
qualified technician
PRODUCT MAINTENANCE
NP-DK50-Nx4VRTM-AD-A-EN-5_04-2022 52 04/2022
PRODUCT MAINTENANCE
17.2. Check of product operation
Check aggregate condition – the aggregates should be operating normally without excessive vibration or noise. Troubleshoot any problem or call in service personnel if trouble is detected.
Visually inspect fan operation – the fans must be operating when the aggregates are running. Troubleshoot any problem or call in service personnel if trouble is detected.
Check to ensure the power cord, the cable for the pressure sensor on the air tank and the connecting compressed air hoses are undamaged. Replace damaged components or call in service personnel.
Check the ambient temperature at the display – the ambient temperature must be below the temperature limit
(40°C). Cool the space if the temperature is high.
Check for alarm conditions on the display – troubleshoot and remedy all alarms.
17.3. Check the compressed air connections for leaks and inspect the equipment
Leak testing
Check the compressor's compressed air lines for leaks during operation – pressure supplied by the compressor.
Use a leak analyser or soapy water to check all joints and connections for leaks. Tighten or reseal the connection where leaks are found
Inspecting the equipment
Check the condition of the compressor aggregate for normal operation and noise levels.
Fan operation check – the fans must be running during the defined compressor work cycles.
Check the filter condition – clean dirty
04/2022 53 filters or replace with new filters.
Check the solenoid valves in the valve module.
Check the operation of the automatic condensate drain.
Call in service personnel if a malfunction is suspected.
17.4. Inspection of electrical connections
Risk of electric shock.
Inspect the product’s electrical connections when the mains are disconnected.
Check the mechanical function of the main switch Q10 and the START-
STOP buttons, S1 and S2.
Check the power cord, conductors connected to the X1 terminal strip and the main switch to ensure they are undamaged. Inspect to ensure the connection terminals are properly supported to relieve tension.
Check to ensure all threaded conductor terminals are tight (on motor circuit breakers Q1-6, circuit protection devices F1-3, contactors Q11-16 and
Q20-21, etc.). Tighten all loose terminals with a screwdriver.
Visually inspect the connection of individual cables to the terminal strip
X1 (spring clips) and the LOGO!
Control system (screw terminals).
Inspect all screw terminals for the protective green and yellow PE grounding conductors in the switchboard, the motor section, the cooling unit and the pressure vessel.
Tighten any loose terminals.
Inspect the connector X50 (dryer and cooler) and the pressure sensor (B1)
(in the pressure vessel).
17.5. Condensate drain
A wet floor resulting from overflow from the vessel poses a slip hazard.
NP-DK50-Nx4VRTM-AD-A-EN-5_04-2022
PRODUCT MAINTENANCE
Condensate from compressors with air dryers is automatically drained into a vessel to collect condensate.
Monitor the level in the vessel using the markings (depending on the volume of the vessel), and empty at least once a day.
Fig. 23: Check of the condensate collection vessel
17.6. Inlet filter replacement
The filters located in the compressor aggregate enclosure cover must be replaced at defined intervals.
Intake filter replacement:
Pull out the rubber plug by hand
(2).
Remove the dirty intake filter (1).
Insert a new filter and replace the rubber plug.
Pre-filter replacement:
Pull out the pre-filter by hand (3).
Replace with a new one and insert it back.
17.7. Check of safety valve
Damage to the safety valve could cause pressure to rise to hazardous levels.
Never use the safety valve to release the air pressure in the air tank. This could damage the safety valve. The valve is set to the maximum permitted pressure by the manufacturer.
Never adjust a safety valve.
NP-DK50-Nx4VRTM-AD-A-EN-5_04-2022 54
Fig. 24: Inlet filter replacement
Venting compressed air poses an injury hazard.
Wear safety glasses when inspecting a safety valve.
04/2022
PRODUCT MAINTENANCE
Turn the screw on the safety valve several rotations to the left until the safety valve releases air.
Let the safety valve vent for only a few seconds.
Turn the screw to the right until it seats, closing the valve.
17.8. Compressor intake filter cleaning/replacement
Only applicable to enclosed products.
Clean or replace the intake filters are defined intervals:
Remove the nuts (1) and covers (4) on the lower part of the enclosure beneath the aggregates two times and remove the filters (5).
Fig. 25: Check of safety valve
Remove the nuts (1) and covers (2) inside the enclosure three times and remove the filters (3).
Clean or wash the filters, if heavily contaminated, in a solution of soapy water and allow to dry completely.
Reinstall the filters once dry (reverse the procedure to reassemble).
Fig. 26: Compressor inlet filter cleaning/replacement
At Point A, remove the foam, remove the 4 screws (5), washers (6) and remove the suction filter cover (7).
Remove the 2 nuts (8) on the filter bracket (9) and remove the filter (10).
At Point B (on the sides (11), remove the 2 nuts (12), washers (13), release the filter bracket (14) and remove the filter (15).
Clean or wash the filters, if heavily contaminated, in a solution of soapy water and allow to dry completely.
Reinstall the filters once dry (reverse the procedure to reassemble).
04/2022 55 NP-DK50-Nx4VRTM-AD-A-EN-5_04-2022
PRODUCT MAINTENANCE
Fig. 27: Compressor inlet filter cleaning/replacement
17.9. Compressor performance check
Turn off the compressor using the
STOP button.
Vent the air pressure in the air tank to zero.
Turn on the compressor using the
START button.
Measure the time to fill the air tank from 0 to 7 bar.
The measured value must be less than the d ata provided in the “Technical
Data” table.
17.10. Check of non-return valve operation
Compressed air line:
Check for the proper operation of all nonreturn valves in the compressed air line and the disconnection of pressure hoses from air pumps.
One aggregate must be running at all times, while the others may be shut off using the current protection device in the switchboard. No compressed air may leak from the check valves.
Air tank:
Check for proper operation of the non-return valve on the air tank by disconnecting the pressure hose from the valve.
Check the check valve operation once the air tank has come up to pressure and with the compressor off. No compressed air may leak.
NP-DK50-Nx4VRTM-AD-A-EN-5_04-2022 56 04/2022
PRODUCT MAINTENANCE
17.11. Check of solenoid valve operation
Check their operation using the
“Magnetic indicator” fixture as follows:
Attach the fixture to the valve coil and if the motors are active at the valve coil, the indicator must rotate and if they are out of inactive, the indicator must not rotate.
Fig. 28: Check of solenoid valve operation
17.12. Check of temperature sensor switching
Checking the functionality of temperature
This check is conducted using the LOGO! TDE display where the instantaneous temperature values are shown on the starting screen in STOP mode.
The check is based on a slight change in temperature around the sensor, i.e. caused by heating, or the temperature shown on the display must also change. The B4 sensor is not connected on uncovered versions and the display shows
N/A. sensor B3 (external) and B4 (internal).
The B4 sensor is only used on covered models.
Fig. 29: Check of temperature switch switching
17.13. Check the function of the pressure sensor
This check is performed visually using the
TDE screen, which shows the compressed air value. The pressure level shown on the display must change with changes in air demand.
17.14. Cleaning and disinfection of the exterior surfaces of the product
Clean and disinfect the exterior surfaces with neutral cleaning products.
Use of aggressive detergents and disinfectants containing alcohol and chlorides can lead to surface damage and discolouration.
AD dryer maintenance
17.15. Venting pressure from the dryer
The equipment is designed to permit the safe venting of pressure within 10 seconds after the compressor is shut off.
If pressure is not automatically vented from the dryer, then the pressure may be vented
04/2022 57 NP-DK50-Nx4VRTM-AD-A-EN-5_04-2022
manually.
Venting compressed air poses an injury hazard
Wearing hearing protection is recommended given the noise generated by the venting process.
Shut off the compressed air source before venting pressure from the equipment
Venting pressure using the display screen
Press ESC+▼ in the display screen to vent pressure from the equipment.
PRODUCT MAINTENANCE
First, shut off the compressed air source.
Then press and hold ESC+▼, which will open all the solenoid valves (inlet and regeneration) for 10 seconds and then vent the pressure from the equipment and connected pneumatic circuits and elements that are not separated from the equipment by the check valve
Manual venting of pressure
Turn off the compressor.
Open the vent plugs on the outlet
module on the equipment (Fig. 30).
Fig. 30: Venting pressure from the dryer chambers
Disconnect the hose (2) from the lower part of the condensate separator (3) (Fig. 31).
Fig. 31: Venting pressure from the cooler and condensate separator
The process of manually venting pressure from the equipment is complete after approximately 2 minutes.
NP-DK50-Nx4VRTM-AD-A-EN-5_04-2022 58 04/2022
PRODUCT MAINTENANCE
17.16.
Replacement of the dryer’s internal filters
Working with pressurised pneumatic components poses a risk of injury.
Prior to any work, disconnect the equipment from the mains, shut off the compressor and vent all pressure in the equipment to zero.
In normal operation, filter replacement must be performed in the upper part of the dryer at the defined interval.
Turn off the compressor.
Check the pressure in the dryer.
If the dryer chambers are under pressure, proceed in accordance with Chapter
17.15.
Unscrew the 8 screws (1).
Disassemble the outlet panel (2) on which the filters (3) are mounted.
Unscrew the dirty filters (3) and replace with new filters.
Check the seal (4) on the bottom of the outlet module and replace if necessary.
Reverse the procedure to reassemble.
Switch on the compressor.
Check for any dryer leaks.
17.17. Replacement of cassettes with adsorbent media
In normal operation, the replacement of the
Fig. 32: Replacement of internal filters cassettes with adsorbent media must be performed at the defined interval.
04/2022 59 NP-DK50-Nx4VRTM-AD-A-EN-5_04-2022
PRODUCT MAINTENANCE
Turn off the compressor.
Check the pressure in the dryer.
If the dryer chambers are under pressure, proceed in accordance with Chapter 17.15.
Unscrew the 8 screws (1).
Remove the outlet panel (2).
Pull out and replace the cassettes (3) with new parts.
Check the seal (4) on the bottom of the outlet module and replace if necessary.
Reverse the procedure to reassemble.
Switch on the compressor.
Check for any dryer leaks.
Fig. 33: Replacement of cassettes with adsorbent media
17.18. Replacement of the logic valve ball
Turn off the compressor.
Check the pressure in the dryer.
If the dryer chambers are under pressure, proceed in accordance with
Chapter 17.15.
Unscrew the 4 screws (1) and remove the cover (2).
Remove the ball cover (3).
Replace the ball (4).
Check the nozzles (5) and clean as necessary.
Reverse the procedure to reassemble.
Check for leaks and the operation of the logic valve and nozzles – check for the cyclical switching of the chambers.
Fig. 34: Replacement of the logic valve ball
17.19. Replacement of the dryer’s silencer
Working with pressurised pneumatic components poses a risk of injury.
Operating the equipment without silencers generates high levels of noise. Only replace silencers when the equipment is shut down.
NP-DK50-Nx4VRTM-AD-A-EN-5_04-2022 60 04/2022
PRODUCT MAINTENANCE
Unscrew the silencer (1).
Install a new silencer.
17.20. Inspecting the cooler and fan
The equipment, in particular the compressor fan, cooler fan, and the cooler, must be kept clean to ensure efficient drying. Remove dust from the surface of the cooling fins and fans by vacuuming or blowing down with compressed air.
17.21. Replacement of solenoid valves
Risk of electric shock.
Shut off the compressed air source, turn off the equipment and disconnect it from the mains before working on the equipment.
Working with pressurised pneumatic components poses a risk of injury.
Disconnect the equipment from the mains and vent the pressure in the equipment and the pneumatic system to zero before working on the equipment.
In normal operation, the solenoid valves in the bottom of the dryer must be replaced at the defined interval.
Turn off the compressor.
Fig. 35: Replacement of the silencer
Check the pressure in the dryer.
If the dryer chambers are under pressure, proceed in accordance with
Chapter 17.15.
Unscrew the 1 screw from the valve connector (1).
Disconnect the valve connector (2).
Unscrew the 4 screws (3).
Remove the solenoid valve (4).
Remove the valve seal (4-1) from the body.
Physically clean the valve seat surface to remove any impurities.
Physically clean the 16 screws to remove the thread locking adhesive.
Install the solenoid valve (Fig. 37).
Install the new valve seal (4-1).
Install the new solenoid valve using the 4 screws (3) and use a thread locking adhesive on the threads of the screws (such as Loctite 243).
Reattach the solenoid valve connector and attach with a screw (1).
Switch on the compressor.
Check for any dryer leaks.
04/2022 61 NP-DK50-Nx4VRTM-AD-A-EN-5_04-2022
PRODUCT MAINTENANCE
Fig. 36: Solenoid valve replacement
Solenoid valve assembly
Replacement solenoid valves are delivered as disassembled replacement parts. The new valve must be assembled before a solenoid valve is replaced.
Mount the valve coil (4-5) onto the valve body (4-4) and secure with the nut (4-6).
Insert the valve membrane spring (4-
3) into the membrane (4-2) and the insert into the assembled valve coil and body assembly.
Then mount the valve seal (4-1) onto the dryer body.
Fig. 37: Solenoid valve assembly
17.22. Pressure relief valve
The pressure relief valve automatically begins
NP-DK50-Nx4VRTM-AD-A-EN-5_04-2022 62 to vent air from the system if the pressure in the compressed air circuit exceeds its pre-set value. The pressure relief valve closes as the
04/2022
PRODUCT MAINTENANCE pressure drops.
The pressure in the compressed air circuit can only increase because of an increase in flow resistance in the compressed air lines or as a result of a dryer malfunction
(e.g. solenoid valve malfunction), and therefore the repeated opening of the relief valve requires a dryer function check and repairs if necessary!
Consultation with the manufacturer is required before any adjustment is made to the relief valve!
The outlet openings on the relief valve may not be blocked and the egress of compressed air through them may not be restricted.
1 Compressor pressure relief valve
2 Dryer pressure relief valve
Fig. 38: Pressure relief valve
18. LONG-TERM SHUTDOWN
If the compressor will not be used for a prolonged time period, it is recommended to drain all condensate from the air tank and the condensate separator. Then turn on the compressor for 10 minutes, keeping the drain
valve on the air tank open (15) (Fig. 1). Switch
off the compressor using the main switch (19)
(Fig. 2), close the condensate drain valve and
disconnect the equipment from the mains.
04/2022 63 NP-DK50-Nx4VRTM-AD-A-EN-5_04-2022
TROUBLESHOOTING
19. DISPOSAL OF DEVICE
Disconnect the equipment from the mains.
Release the air pressure in the pressure tank by opening the drain
Dispose of the equipment following all
TROUBLESHOOTING applicable regulations.
Entrust a specialised company to sort
and dispose of waste.
Worn out components have no negative environmental impact.
Risk of electric shock.
Before interfering with the equipment, first disconnect it from the mains (remove the power socket).
Working with pressurised pneumatic components poses a risk of injury.
Before interfering with the equipment, vent the air tank and the compressed air system to zero pressure.
Malfunction Possible cause
Problem with electrical power source
Troubleshooting may only be performed by a qualified service technician.
Damage to the safety valve could cause pressure to rise to hazardous levels.
Never adjust a safety valve.
Compressor does not start
Power loss
Pressure switch failed
Loss of power to motor
Any of the air pumps does not start up
(indicator is on)
Motor winding shorted, damaged /open thermal protection/ high ambient temperature
Seized up piston or other moving component (mechanical damage to a moving part)
Solution
Main breaker is off
Check mains voltage
Loose terminal in switchboard – tighten
Check the primary power connection - replace if damaged
Check terminals and operation of the pressure switch - replace if damaged
Check mains voltage
Check the function of the contactor, and thermal relays - replace if damaged
Loose terminals at the motor terminal strip - tighten or replace if damaged or broken
Replace the motor / decrease the ambient temperature
Replace damaged parts
Controller malfunction
RUN/STOP indicator is not green
Loss of connection between controller and expansion module
Power loss
Check controller operation, check to ensure software is present - replace if damaged or upload the correct program
Check connection – replace if damaged
Check mains voltage
NP-DK50-Nx4VRTM-AD-A-EN-5_04-2022 64 04/2022
TROUBLESHOOTING
Air pumps switch often, even without demand for air
Problem with electrical power source
Controller or expansion module malfunction
Air leak in compressed air distribution system
Leaky check valves
Leak through solenoid valves once regeneration is complete
Leak at pressure sensor and safety valve
Air pump leaking
Loose terminal in switchboard – tighten
Check the primary power connection - replace if damaged
Main breaker is off
Replace failed controller or expansion module
Check compressed air distribution system – seal loose joints
Test check vales and clean, or replace if damaged
Clean the check valve - replace if damaged
Test their function and clean, or replace if damaged
Check connections on the air pump for leaks – tighten leaking connections
Replace worn piston
Output of certain air pumps is reduced, extended run cycle
Worn piston rings
Gasket between cylinder head and valve plate damaged
Intake filter is plugged
Replace gasket, tighten
Damaged motor bearing
Replace old filter with a new filter
Replace damaged bearing
One of the air pumps is noisy (knocking, metal noises)
Damaged piston bearing, piston rod Replace damaged piston
Failed (cracked) rubber mount spring
Replace damaged spring with new spring
Lack of ventilation in compressor room Secure suitable ambient conditions
High ambient temperature causes compressors to switch off in vertical stacks (overheating)
Cooling fans for aggregates, cooler and enclosure do not work
Defective fans - replace
Defective temperature switch - replace
Low operating pressure
Reduce the demand for air, check the output from the compressed air source, fix any leaks in the distribution system
Degraded drying performance – highpressure dew point
(condensed water in the air)
Regeneration solenoid valve not working
Air regeneration nozzle plugged
Cooling fan not working
Dirty cooler
Check coil operation, replace if damaged
Dryer emitting high levels of noise
Air leaking through relief valve at dryer inlet
Silencer plugged regeneration valve
Damaged fan
Damaged silencer at outlet from
Air leaking through relief valve at dryer inlet
Compressor running at high working pressure
Dryer inlet solenoid valve not working
Clean or replace the nozzle
(see product maintenance)
Check the power source to the fan
Replace damaged fan
Inspect the cooler and clean as necessary
Inspect the silencers. Clean or replace the silencer if flow resistance is too high or if heavily soiled.
Replace damaged fan
Replace the silencer
Check the dryer connection to the mains and dryer connections, check dryer operation, check the dryer’s working pressure, and replace defective components.
Check the compressor’s working pressure setting
Check coil operation, replace if damaged
Inspect the condition of the valve - clean
04/2022 65 NP-DK50-Nx4VRTM-AD-A-EN-5_04-2022
TROUBLESHOOTING
High pressure in equipment resulting from plugged filters the valve or replace if problems persist
Check the internal filters and accessory filter assemblies.
Clean or replace dirty filters.
Once a fault is cleared and after reassembling the dryer, the condensate must be drained from the air tank, then dry the air tank, and the dryer must be regenerated, best when using continuous compressor operation at a pressure of around 7.0 bar for a period of at least 1 hour.
Check the moisture content of the air exiting the air tank (see the Technical data chapter) to prevent damage to connected downstream equipment.
20. REPAIR SERVICE
Warranty and post-warranty repairs must be done by the manufacturer, its authorized representative, or service personnel approved by the supplier.
Attention.
The manufacturer reserves the right to make changes to the equipment without notice. Any changes made will not affect the functional properties of the equipment.
NP-DK50-Nx4VRTM-AD-A-EN-5_04-2022 66 04/2022
ANNEX
ANNEX
21. MAPPING PARAMETERS
04/2022 67 NP-DK50-Nx4VRTM-AD-A-EN-5_04-2022
ANNEX
NP-DK50-Nx4VRTM-AD-A-EN-5_04-2022 68 04/2022
ANNEX
22. INSTALLATION RECORD
1. Product: (model)
DK50 4X4VRT/M
DK50 6x4VRT/M
3.1. User’s name:
DK50 4x4VRTS/M
DK50 6x4VRTS/M
2. Serial number:
3.2. Address of installation:
4. Equipment connected to the compressor:
5. Installation / Commissioning:
Product completeness check **
Y
N
Documentation completeness check **
Y
N
Installation/connection to equipment **
Y
Functional test **
N
Y
N
6. Contents of operator training:
Description of the product and functions**
Y
N
Product operation: turning on/off, controls, control procedures, data on the display panel, alarms, operation in alarm conditions**
Y
N
Product maintenance: maintenance intervals, maintenance procedure, service intervals, operating activities**
Y
N
Safety measures, warnings – their meaning and compliance **
Y
N
Notes:
7. Operator instructed on safety measures, operations and maintenance:
Name: Signature:
Name: Signature:
Name:
8. Installation and instruction performed by:
First name/Last name
Signature:
Signature:
Company: Address:
Phone:
Date: Email:
9. Distributor:
Company: Address:
Contact person:
Phone: Email:
** mark with an “X” in points 5 and 6 (Y - yes /N - no). Enter any observations from points 5 and 6 into the “Notes” section.
04/2022 69 NP-DK50-Nx4VRTM-AD-A-EN-5_04-2022
DK50 4x4VRT/M
DK50 6x4VRT/M
EKOM spol. s r.o.,
Priemyselná 5031/18, 921 01 PIEŠŤANY, Slovak Republic tel.: +421 33 7967255, fax: +421 33 7967223 e-mail: [email protected], www.ekom.sk
NP-DK50-Nx4VRTM-AD-A-EN-5_04-2022
112000555-0001
advertisement
Related manuals
advertisement
Table of contents
- 5 GENERAL INFORMATION
- 5 CONFORMITY WITH THE REQUIREMENTS OF THE EUROPEAN UNION
- 5 SYMBOLS
- 6 DEVICE USE
- 7 GENERAL SAFETY INSTRUCTIONS
- 8 STORAGE AND TRANSPORT CONDITIONS
- 9 PRODUCT DESCRIPTION
- 9 VARIANTS
- 11 ACCESSORIES
- 13 PRODUCT FUNCTION
- 16 TECHNICAL DATA
- 20 INSTALLATION
- 20 INSTALLATION CONDITIONS
- 21 COMPRESSOR ASSEMBLY
- 25 PNEUMATIC CONNECTION
- 28 ELECTRICAL CONNECTION
- 34 COMMISSIONING
- 35 PNEUMATIC DIAGRAMS
- 38 OPERATION
- 39 SWITCHING ON THE COMPRESSOR
- 47 SWITCHING OFF THE COMPRESSOR
- 48 PRODUCT MAINTENANCE
- 63 LONG-TERM SHUTDOWN
- 64 DISPOSAL OF DEVICE
- 64 TROUBLESHOOTING
- 66 REPAIR SERVICE
- 67 ANNEX
- 67 MAPPING PARAMETERS
- 69 INSTALLATION RECORD