Vipa FM 250-1BS00 Owner's Manual
Add to My manuals40 Pages
VIPA FM 250-1BS00 is a high-performance SSI module designed for use with the VIPA System 200V programmable logic controller (PLC). It provides a simple and efficient way to connect SSI devices to the PLC, enabling the exchange of data between the two systems. The FM 250-1BS00 supports a wide range of SSI devices, including encoders, position sensors, and temperature sensors. It is also compatible with a variety of PLC models, making it a versatile solution for a variety of applications. With its high-speed data transfer rates and advanced features, the FM 250-1BS00 is an ideal choice for applications that require precise and reliable data communication between SSI devices and PLCs.
advertisement
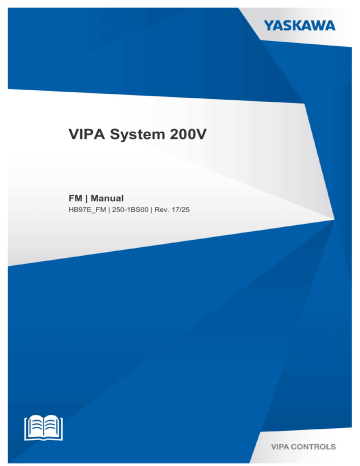
VIPA System 200V
FM | Manual
HB97E_FM | 250-1BS00 | Rev. 17/25
Copyright © VIPA GmbH. All Rights Reserved.
This document contains proprietary information of VIPA and is not to be disclosed or used except in accordance with applicable agreements.
This material is protected by the copyright laws. It may not be reproduced, distributed, or altered in any fashion by any entity (either internal or external to VIPA), except in accordance with applicable agreements, contracts or licensing, without the express written consent of VIPA and the business management owner of the material.
For permission to reproduce or distribute, please contact:
VIPA, Gesellschaft für Visualisierung und Prozessautomatisierung mbH
Ohmstraße 4, D-91074 Herzogenaurach, Germany
Tel.: +49 (91 32) 744 -0
Fax.: +49 9132 744 1864
EMail: [email protected] http://www.vipa.com
Note
Every effort has been made to ensure that the information contained in this document was complete and accurate at the time of publishing. Nevertheless, the authors retain the right to modify the information. This customer document describes all the hardware units and functions known at the present time. Descriptions may be included for units which are not present at the customer site. The exact scope of delivery is described in the respective purchase contract.
CE Conformity Declaration
Hereby, VIPA GmbH declares that the products and systems are in compliance with the essential requirements and other relevant provisions.
Conformity is indicated by the CE marking affixed to the product.
Conformity Information
For more information regarding CE marking and Declaration of Conformity (DoC), please contact your local VIPA customer service organization.
Trademarks
VIPA, SLIO, System 100V, System 200V, System 300V, System 300S, System 400V, System 500S and Commander Compact are registered trademarks of VIPA Gesellschaft für Visualisierung und Prozessautomatisierung mbH.
SPEED7 is a registered trademark of profichip GmbH.
SIMATIC, STEP, SINEC, TIA Portal, S7-300 and S7-400 are registered trademarks of Siemens AG.
Microsoft und Windows are registered trademarks of Microsoft Inc., USA.
Portable Document Format (PDF) and Postscript are registered trademarks of Adobe Systems, Inc.
All other trademarks, logos and service or product marks specified herein are owned by their respective companies.
Information product support
Contact your local VIPA Customer Service Organization representative if you wish to report errors or questions regarding the contents of this document. If you are unable to locate a customer service center, contact VIPA as follows:
VIPA GmbH, Ohmstraße 4, 91074 Herzogenaurach, Germany
Telefax:+49 9132 744 1204
EMail: [email protected]
Technical support
Contact your local VIPA Customer Service Organization representative if you encounter problems with the product or have questions regarding the product. If you are unable to locate a customer service center, contact VIPA as follows:
VIPA GmbH, Ohmstraße 4, 91074 Herzogenaurach, Germany
Telephone: +49 9132 744 1150 (Hotline)
EMail: [email protected]
Manual VIPA System 200V
Contents
Contents
Chapter 1 Basics and Assembly ..................................................... 1-1
Safety Information for Users................................................................. 1-2
Demounting and module exchange .................................................... 1-11
Chapter 2 Hardware description ..................................................... 2-1
Chapter 3 Deployment ..................................................................... 3-1
HB97E - FM - 250-1BS00 - Rev. 17/25 i
Contents Manual VIPA System 200V ii HB97E - FM - 250-1BS00 - Rev. 17/25
Manual VIPA System 200V About this manual
About this manual
Overview
This manual describes the System 200V SSI module FM 250S from VIPA.
Here you may find every information for commissioning and operation.
Chapter 1: Basics and Assembly
The focus of this chapter is on the introduction of the VIPA System 200V.
Here you will find the information required to assemble and wire a controller system consisting of System 200V components.
Besides the dimensions the general technical data of System 200V will be found.
Chapter 2: Hardware description
Here the hardware components of the FM 250-1BS00 are described.
The technical data are at the end of the chapter.
Chapter 3: Deployment
This chapter contains every information on the deployment and the configuration of the SSI module FM 250S.
HB97E - FM - 250-1BS00 - Rev. 17/25 1
About this manual Manual VIPA System 200V
Objective and contents
Target audience
Structure of the manual
Guide to the document
Availability
Icons
Headings
This manual describes the System 200V SSI module FM 250S from VIPA.
It contains a description of the construction, project implementation and usage.
Product
FM 250S
Order number
250-1BS00 as of state:
HW
02
The manual is targeted at users who have a background in automation technology.
The manual consists of chapters. Every chapter provides a self-contained description of a specific topic.
The following guides are available in the manual:
• an overall table of contents at the beginning of the manual
• an overview of the topics for every chapter
The manual is available in:
• printed form, on paper
• in electronic form as PDF-file (Adobe Acrobat Reader)
Important passages in the text are highlighted by following icons and headings:
Danger!
Immediate or likely danger.
Personal injury is possible.
Attention!
Damages to property is likely if these warnings are not heeded.
Note!
Supplementary information and useful tips.
2 HB97E - FM - 250-1BS00 - Rev. 17/25
Manual VIPA System 200V Safety information
Safety information
Applications conforming with specifications
Documentation
Disposal
The FM 250S is constructed and produced for:
• all VIPA System 200V components
• communication and process control
• general control and automation applications
• industrial applications
• operation within the environmental conditions specified in the technical data
• installation into a cubicle
Danger!
This device is not certified for applications in
• in explosive environments (EX-zone)
The manual must be available to all personnel in the
• project design department
• installation department
• commissioning
• operation
The following conditions must be met before using or commissioning the components described in this manual:
•
Hardware modifications to the process control system should only be carried out when the system has been disconnected from power!
•
Installation and hardware modification only by properly trained personnel.
•
The national rules and regulations of the respective country must be satisfied (installation, safety, EMC ...)
National rules and regulations apply to the disposal of the unit!
HB97E - FM - 250-1BS00 - Rev. 17/25 3
Safety information Manual VIPA System 200V
4 HB97E - FM - 250-1BS00 - Rev. 17/25
Manual VIPA System 200V
Chapter 1
Overview
Contents
Chapter 1 Basics and Assembly
Basics and Assembly
The focus of this chapter is on the introduction of the VIPA System 200V.
Here you will find the information required to assemble and wire a controller system consisting of System 200V components.
Besides the dimensions the general technical data of System 200V will be found.
Topic Page
Chapter 1 Basics and Assembly ..................................................... 1-1
Safety Information for Users ................................................................. 1-2
Demounting and module exchange .................................................... 1-11
HB97E - FM - 250-1BS00 - Rev. 17/25 1-1
Chapter 1 Basics and Assembly Manual VIPA System 200V
Safety Information for Users
Handling of electrostatic sensitive modules
VIPA modules make use of highly integrated components in MOS-
Technology. These components are extremely sensitive to over-voltages that can occur during electrostatic discharges.
The following symbol is attached to modules that can be destroyed by electrostatic discharges.
The Symbol is located on the module, the module rack or on packing material and it indicates the presence of electrostatic sensitive equipment.
It is possible that electrostatic sensitive equipment is destroyed by energies and voltages that are far less than the human threshold of perception.
These voltages can occur where persons do not discharge themselves before handling electrostatic sensitive modules and they can damage components thereby, causing the module to become inoperable or unusable.
Modules that have been damaged by electrostatic discharges can fail after a temperature change, mechanical shock or changes in the electrical load.
Only the consequent implementation of protection devices and meticulous attention to the applicable rules and regulations for handling the respective equipment can prevent failures of electrostatic sensitive modules.
Shipping of electrostatic sensitive modules
Modules must be shipped in the original packing material.
Measurements and alterations on electrostatic sensitive modules
When you are conducting measurements on electrostatic sensitive modules you should take the following precautions:
•
Floating instruments must be discharged before use.
•
Instruments must be grounded.
Modifying electrostatic sensitive modules you should only use soldering irons with grounded tips.
Attention!
Personnel and instruments should be grounded when working on electrostatic sensitive modules.
1-2 HB97E - FM - 250-1BS00 - Rev. 17/25
Manual VIPA System 200V Chapter 1 Basics and Assembly
System conception
Overview
Components
The System 200V is a modular automation system for assembly on a
35mm profile rail. By means of the peripheral modules with 4, 8 and 16 channels this system may properly be adapted matching to your automation tasks.
CPU 215 SM 221
DI 8xDC24V
SM 221
DI 8xDC24V
SM 221
DI 8xDC24V
SM 221
DI 8xDC24V
R RN
ST
MR
1 1
S .0
2 .0
2
MMC
.1
3
.1
3
PW .2
4
.2
4
SF .3
5
.3
5
FC
MC
M
P
2
I
.4
.5
6
7
.4
.5
6
7
.6
8
X1
DC
24V
+ 1
X 2
3 4
2
VIPA 215-1BA03
.7
9
I0
X 2
3 4
VIPA 221-1BF00
.6
.7
8
9
I0
X 2
3 4
VIPA 221-1BF00
.0
.1
.2
.3
.4
.5
.6
.7
1
2
3
4
7
8
9
I0
X 2
3 4
VIPA 221-1BF00
5
6
.0
.1
.2
.3
.4
.5
.6
.7
1
2
3
4
5
6
7
8
9
I0
X 2
3 4
VIPA 221-1BF00
The System 200V consists of the following components:
•
Head modules like CPU and bus coupler
•
Periphery modules like I/O, function und communication modules
•
Power supplies
•
Extension modules
Head modules
Periphery modules
PW
SF
FC
MC
CPU 214
R
S
MMC
RN
ST
MR
M
P
2
I
DC
24V
X 2
-
+
3 4
X1
1
2
VIPA 214-1BC03
SM 221
DI 8xAC/..48V
N
1
10
X 2
3 4
VIPA 221-1FF30
5
6
7
1
2
3
4
8
9
I0
IM 253DP
9 9
PW
ER
RD
DE
ADR.
D
P
X1
DC
24V
+
X 8
9 10
-
1
2
VIPA 253-1DP00 n
DI 16xDC24V
.3
.4
.5
.6
.0
.1
.2
.7
.0
.1
.2
.3
.4
.5
.6
.7
n+1
VIPA 221-1BH10
17
18
X 2
3 4
12
13
14
15
16
8
9
10
11
5
6
3
4
7
1
2
With a head module CPU respectively bus interface and DC 24V power supply are integrated to one casing.
Via the integrated power supply the CPU respectively bus interface is power supplied as well as the electronic of the connected periphery modules.
The modules are direct installed on a
35mm profile rail and connected to the head module by a bus connector, which was mounted on the profile rail before.
Most of the periphery modules are equipped with a 10pin respectively 18pin connector. This connector provides the electrical interface for the signaling and supplies lines of the modules.
HB97E - FM - 250-1BS00 - Rev. 17/25 1-3
Chapter 1 Basics and Assembly
Power supplies
PS 207/2
L
OH N
G
100-240V AC
550-230mA
50-60Hz
P
E
OL
OK
OUT DC 24V /
∑
X1
Ι: 2A
4A (peak)
+
DC 24V
-
1
2
+
DC 24V
-
X 2
3 4
VIPA 207-1BA00
3
4
Expansion modules
CM 201
X1.
X2.
Manual VIPA System 200V
With the System 200V the DC 24V power supply can take place either externally or via a particularly for this developed power supply.
The power supply may be mounted on the profile rail together with the System 200V modules. It has no connector to the backplane bus.
The expansion modules are complementary modules providing 2- or 3wire connection facilities.
The modules are not connected to the backplane bus.
Structure/ dimensions
Installation
X 2
3 4
VIPA 201-1AA00
•
Profile rail 35mm
•
Dimensions of the basic enclosure:
1tier width: (HxWxD) in mm: 76x25.4x74 in inches: 3x1x3
2tier width: (HxWxD) in mm: 76x50.8x74 in inches: 3x2x3
1
4
2
Please note that you can only install head modules, like the CPU, the PC and couplers at slot 1 or 1 and 2 (for double width modules).
3
(double width)
[2] Head module
(single width)
D
P
0 1
Note
Information about the max. number of pluggable modules and the max. current at the backplane bus can be found in the "Technical Data" of the according head module.
Please install modules with a high current consumption directly beside the head module.
Clack
1-4 HB97E - FM - 250-1BS00 - Rev. 17/25
Manual VIPA System 200V Chapter 1 Basics and Assembly
Dimensions
Dimensions
Basic enclosure
1tier width (HxWxD) in mm: 76 x 25.4 x 74
2tier width (HxWxD) in mm: 76 x 50.8 x 74
Installation dimensions
Installed and wired dimensions
In- / Output modules
74 mm
88 mm ca. 110 mm
HB97E - FM - 250-1BS00 - Rev. 17/25 1-5
Chapter 1 Basics and Assembly
Function modules/
Extension modules
Manual VIPA System 200V
CPUs (here with
EasyConn from
VIPA)
85 mm
1-6 HB97E - FM - 250-1BS00 - Rev. 17/25
Manual VIPA System 200V Chapter 1 Basics and Assembly
Installation
General
Profile rail
The modules are each installed on a 35mm profile rail and connected via a bus connector. Before installing the module the bus connector is to be placed on the profile rail before.
For installation the following 35mm profile rails may be used:
35 mm
35 mm
Bus connector
27 mm
Order number
290-1AF00
290-1AF30
Label
27 mm
35mm profile rail
35mm profile rail
Description
Length 2000mm, height 15mm
Length 530mm, height 15mm
System 200V modules communicate via a backplane bus connector. The backplane bus connector is isolated and available from VIPA in of 1-, 2-, 4- or 8tier width.
The following figure shows a 1tier connector and a 4tier connector bus:
The bus connector is to be placed on the profile rail until it clips in its place and the bus connections look out from the profile rail.
Order number Label Description
HB97E - FM - 250-1BS00 - Rev. 17/25 1-7
Chapter 1 Basics and Assembly Manual VIPA System 200V
Installation on a profile rail
1
The following figure shows the installation of a 4tier width bus connector in a profile rail and the slots for the modules.
2
The different slots are defined by guide rails.
3 [1] Head module
(double width)
[2] Head module
(single width)
4
PW
ER
RD
BA
ADR.
0 1
+
DC24V
-
1
2
R
S
PW
SF
FC
MC
MMC
Assembly regarding the current consumption
•
Use bus connectors as long as possible.
•
Sort the modules with a high current consumption right beside the head module. In the service area of www.vipa.com a list of current consumption of every System 200V module can be found.
1-8 HB97E - FM - 250-1BS00 - Rev. 17/25
Manual VIPA System 200V Chapter 1 Basics and Assembly
Assembly possibilities hoizontal assembly
0 1 lying assembly vertical assembly
Please regard the allowed environmental temperatures:
• horizontal assembly:
• vertical assembly:
• lying assembly: from 0 to 60°C from 0 to 40°C from 0 to 40°C
The horizontal assembly always starts at the left side with a head module, then you install the peripheral modules beside to the right.
You may install up to 32 peripheral modules.
Please follow these rules during the assembly!
•
Turn off the power supply before you install or remove any modules!
•
Make sure that a clearance of at least 60mm exists above and 80mm below the middle of the profile rail.
1
4
2 3 •
Every row must be completed from left to right and it has to start with a head module.
[1] Head module (double width)
[2] Head module (single width)
•
Modules are to be installed side by side. Gaps are not permitted between the modules since this would interrupt the backplane bus.
•
A module is only installed properly and connected electrically when it has clicked into place with an audible click.
•
Slots after the last module may remain unoccupied.
Note!
Information about the max. number of pluggable modules and the max. current at the backplane bus can be found in the "Technical Data" of the according head module.
Please install modules with a high current consumption directly beside the head module.
HB97E - FM - 250-1BS00 - Rev. 17/25 1-9
Chapter 1 Basics and Assembly
Assembly procedure
Manual VIPA System 200V
•
Install the profile rail. Make sure that a clearance of at least 60mm exists above and 80mm below the middle of the profile rail.
•
Press the bus connector into the profile rail until it clips securely into place and the bus-connectors look out from the profile rail. This provides the basis for the installation of your modules.
•
Start at the outer left location with the installation of your head module and install the peripheral modules to the right of this.
1 2 3
[1] Head module
(double width)
(single width)
4
•
Insert the module that you are installing into the profile rail at an angle of 45 degrees from the top and rotate the module into place until it clicks into the profile rail with an audible click. The proper connection to the backplane bus can only be guaranteed when the module has properly clicked into place.
Attention!
Power must be turned off before modules are installed or removed!
1-10
Clack
HB97E - FM - 250-1BS00 - Rev. 17/25
Manual VIPA System 200V Chapter 1 Basics and Assembly
Demounting and module exchange
1
2
3
4
5
•
Remove if exists the wiring to the module, by pressing both locking lever on the connector and pulling the connector.
•
The casing of the module has a spring loaded clip at the bottom by which the module can be removed.
•
The clip is unlocked by pressing the screwdriver in an upward direction.
•
Withdraw the module with a slight rotation to the top.
Attention!
Power must be turned off before modules are installed or removed!
Please regard that the backplane bus is interrupted at the point where the module was removed!
HB97E - FM - 250-1BS00 - Rev. 17/25 1-11
Chapter 1 Basics and Assembly
Wiring
Overview
Manual VIPA System 200V
Most peripheral modules are equipped with a 10pole or a 18pole connector.
This connector provides the electrical interface for the signaling and supply lines of the modules.
The modules carry spring-clip connectors for interconnections and wiring.
The spring-clip connector technology simplifies the wiring requirements for signaling and power cables.
In contrast to screw terminal connections, spring-clip wiring is vibration proof. The assignment of the terminals is contained in the description of the respective modules.
You may connect conductors with a diameter from 0.08mm
2
up to 2.5mm
2
(max. 1.5mm
2
for 18pole connectors).
The following figure shows a module with a 10pole connector.
1
1
6
7
8
9
10
4
5
2
3
9
10
7
8
5
6
3
4
1
2
2
1
2
3
3 4 5
[1]
[2]
[3]
[4]
[5]
Locking lever
Pin no. at the module
Pin no. at the connector
Wiring port
Opening for screwdriver
1
Note!
The spring-clip is destroyed if you push the screwdriver into the wire port!
Make sure that you only insert the screwdriver into the square hole of the connector!
1-12 HB97E - FM - 250-1BS00 - Rev. 17/25
Manual VIPA System 200V Chapter 1 Basics and Assembly
Wiring procedure
•
Install the connector on the module until it locks with an audible click.
For this purpose you press the two clips together as shown.
The connector is now in a permanent position and can easily be wired.
The following section shows the wiring procedure from top view.
•
Insert a screwdriver at an angel into the square opening as shown.
•
Press and hold the screwdriver in the opposite direction to open the contact spring.
•
Insert the stripped end of the wire into the round opening. You can use wires with a diameter of 0.08mm
2
to 2.5mm
2
(1.5mm
2
for 18pole connectors).
•
By removing the screwdriver the wire is connected safely with the plug connector via a spring.
Note!
Wire the power supply connections first followed by the signal cables
(inputs and outputs).
HB97E - FM - 250-1BS00 - Rev. 17/25 1-13
Chapter 1 Basics and Assembly Manual VIPA System 200V
Installation guidelines
General
What means EMC? Electromagnetic digestibility (EMC) means the ability of an electrical device, to function error free in an electromagnetic environment without being interferenced res. without interferencing the environment.
All System 200V components are developed for the deployment in hard industrial environments and fulfill high demands on the EMC. Nevertheless you should project an EMC planning before installing the components and take conceivable interference causes into account.
Possible interference causes
The installation guidelines contain information about the interference free deployment of System 200V systems. There is the description of the ways, interference may occur in your control, how you can make sure the electromagnetic digestibility (EMC), and how you manage the isolation.
Electromagnetic interferences may interfere your control via different ways:
•
Fields
•
I/O signal conductors
•
Bus system
•
Current supply
•
Protected earth conductor
Depending on the spreading medium (lead bound or lead free) and the distance to the interference cause, interferences to your control occur by means of different coupling mechanisms.
One differs:
• galvanic coupling
• capacitive coupling
• inductive coupling
• radiant coupling
1-14 HB97E - FM - 250-1BS00 - Rev. 17/25
Manual VIPA System 200V
Basic rules for
EMC
Chapter 1 Basics and Assembly
In the most times it is enough to take care of some elementary rules to guarantee the EMC. Please regard the following basic rules when installing your PLC.
•
Take care of a correct area-wide grounding of the inactive metal parts when installing your components.
- Install a central connection between the ground and the protected earth conductor system.
- Connect all inactive metal extensive and impedance-low.
- Please try not to use aluminum parts. Aluminum is easily oxidizing and is therefore less suitable for grounding.
•
When cabling, take care of the correct line routing.
- Organize your cabling in line groups (high voltage, current supply, signal and data lines).
- Always lay your high voltage lines and signal res. data lines in separate channels or bundles.
- Route the signal and data lines as near as possible beside ground areas (e.g. suspension bars, metal rails, tin cabinet).
•
Proof the correct fixing of the lead isolation.
- Data lines must be laid isolated.
- Analog lines must be laid isolated. When transmitting signals with small amplitudes the one sided laying of the isolation may be favorable.
- Lay the line isolation extensively on an isolation/protected earth conductor rail directly after the cabinet entry and fix the isolation with cable clamps.
- Make sure that the isolation/protected earth conductor rail is connected impedance-low with the cabinet.
- Use metallic or metalized plug cases for isolated data lines.
•
In special use cases you should appoint special EMC actions.
- Wire all inductivities with erase links.
- Please consider luminescent lamps can influence signal lines.
•
Create a homogeneous reference potential and ground all electrical operating supplies when possible.
- Please take care for the targeted employment of the grounding actions. The grounding of the PLC is a protection and functionality activity.
- Connect installation parts and cabinets with the System 200V in star topology with the isolation/protected earth conductor system. So you avoid ground loops.
- If potential differences between installation parts and cabinets occur, lay sufficiently dimensioned potential compensation lines.
HB97E - FM - 250-1BS00 - Rev. 17/25 1-15
Chapter 1 Basics and Assembly
Isolation of conductors
Manual VIPA System 200V
Electrical, magnetically and electromagnetic interference fields are weakened by means of an isolation, one talks of absorption.
Via the isolation rail, that is connected conductive with the rack, interference currents are shunt via cable isolation to the ground. Hereby you have to make sure, that the connection to the protected earth conductor is impedance-low, because otherwise the interference currents may appear as interference cause.
When isolating cables you have to regard the following:
•
If possible, use only cables with isolation tangle.
•
The hiding power of the isolation should be higher than 80%.
•
Normally you should always lay the isolation of cables on both sides.
Only by means of the both-sided connection of the isolation you achieve high quality interference suppression in the higher frequency area.
Only as exception you may also lay the isolation one-sided. Then you only achieve the absorption of the lower frequencies. A one-sided isolation connection may be convenient, if:
- the conduction of a potential compensating line is not possible
- analog signals (some mV res. µA) are transferred
- foil isolations (static isolations) are used.
•
With data lines always use metallic or metalized plugs for serial couplings. Fix the isolation of the data line at the plug rack. Do not lay the isolation on the PIN 1 of the plug bar!
•
At stationary operation it is convenient to strip the insulated cable interruption free and lay it on the isolation/protected earth conductor line.
•
To fix the isolation tangles use cable clamps out of metal. The clamps must clasp the isolation extensively and have well contact.
•
Lay the isolation on an isolation rail directly after the entry of the cable in the cabinet. Lead the isolation further on to the System 200V module and don't lay it on there again!
Please regard at installation!
At potential differences between the grounding points, there may be a compensation current via the isolation connected at both sides.
Remedy: Potential compensation line.
1-16 HB97E - FM - 250-1BS00 - Rev. 17/25
Manual VIPA System 200V Chapter 1 Basics and Assembly
General data
Structure/ dimensions
•
Profile rail 35mm
•
Peripheral modules with recessed labelling
•
Dimensions of the basic enclosure:
1tier width: (HxWxD) in mm: 76x25.4x74 in inches: 3x1x3
2tier width: (HxWxD) in mm: 76x50.8x74 in inches: 3x2x3
Reliability •
Wiring by means of spring pressure connections (CageClamps) at the front-facing connector, core cross-section 0.08 ... 2.5mm
2
or 1.5mm
2
(18pole plug)
•
Complete isolation of the wiring when modules are exchanged
•
Every module is isolated from the backplane bus
HB97E - FM - 250-1BS00 - Rev. 17/25 1-17
Chapter 1 Basics and Assembly Manual VIPA System 200V
General data
Conformity and approval
Conformity
Approval
UL others
RoHS
UL 508 Approval for USA and Canada
2011/65/EU
Protection of persons and device protection
Type of protection -
Electrical isolation to the field bus to the process level
Insulation resistance
-
-
EN 61131-2
Insulation voltage to reference earth
Inputs / outputs
Protective measures
-
-
IP20 electrically isolated electrically isolated
-
AC / DC 50V, test voltage AC 500V against short circuit
Environmental conditions to EN 61131-2
Climatic
Storage / transport
Operation
EN 60068-2-14 -25…+70°C
Horizontal installation
Vertical installation
Air humidity
Pollution
EN 61131-2
EN 61131-2
EN 60068-2-30
EN 61131-2
0…+60°C
0…+60°C
RH1 (without condensation, rel. humidity 10…95%)
Degree of pollution 2
Mechanical
Oscillation
Shock
EN 60068-2-6
EN 60068-2-27
1g, 9Hz ... 150Hz
15g, 11ms
Mounting conditions
Mounting place
Mounting position
-
-
In the control cabinet
Horizontal and vertical
EMC
Emitted interference
Noise immunity zone B
Standard
EN 61000-6-4
EN 61000-6-2
Comment
Class A (Industrial area)
Industrial area
EN 61000-4-2 ESD
8kV at air discharge (degree of severity 3),
4kV at contact discharge (degree of severity 2)
EN 61000-4-3 HF field immunity (casing)
80MHz … 1000MHz, 10V/m, 80% AM (1kHz)
1.4GHz ... 2.0GHz, 3V/m, 80% AM (1kHz)
2GHz ... 2.7GHz, 1V/m, 80% AM (1kHz)
EN 61000-4-6 HF conducted
150kHz … 80MHz, 10V, 80% AM (1kHz)
EN 61000-4-4 Burst, degree of severity 3
EN 61000-4-5 Surge, installation class 3 *
)
*
)
Due to the high-energetic single pulses with Surge an appropriate external protective circuit with lightning protection elements like conductors for lightning and overvoltage is necessary.
Product is lead-free; Restriction of the use of certain hazardous substances in electrical and electronic equipment
1-18 HB97E - FM - 250-1BS00 - Rev. 17/25
Manual VIPA System 200V Chapter 2 Hardware description
Chapter 2 Hardware description
Overview
Contents
Here the hardware components of the FM 250-1BS00 are described.
The technical data are at the end of the chapter.
Topic Page
Chapter 2 Hardware description...................................................... 2-1
HB97E - FM - 250-1BS00 - Rev. 17/25 2-1
Chapter 2 Hardware description Manual VIPA System 200V
Properties
FM 250S
250-1BS00
•
Wiring does not depend on the length of the data word. The interface always uses 4 wires.
•
Maximum security due to the use of symmetrical clock and data signals.
•
Secure data acquisition die to the use of single-step gray code
(configurable).
•
Galvanic isolation of receiver and encoder by means of optocouplers
•
1 SSI channel
•
Direct power supply to the SSI transducer via front-facing connector
•
DC 24V power supply
•
Baud rate selection 100kBaud / 300kBaud
•
2 configurable digital outputs, one may be used as hold input to freeze the current SSI transducer value
•
Measured value available in gray or in binary code
•
6Byte of parameter data
•
4Byte of input data
•
4Byte of output data
•
Configuration by means of control byte
Order data
FM 250S
SSI-Interface
D+
D-
Us
L+
Cl+
Cl-
M
.0
.1
F
X 2
3 4
VIPA 250-1BS00
6
7
8
9
I0
3
4
1
2
5
Type
FM 250S
Order number Description
VIPA 250-1BS00 SSI module
2-2 HB97E - FM - 250-1BS00 - Rev. 17/25
Manual VIPA System 200V Chapter 2 Hardware description
Structure
Functionality
Configurable outputs
LED
L+
Ci+
D+
.0
.1
F
Status indicator pin assignment
Description
LED (yellow)
Supply voltage available
LED (green)
Clock output
LED (green)
Transducer data input
LED (green)
Input/Output 0
LED (green)
Output 1
LED (red)
Error /overload
SSI is the abbreviation for S ynchronous S erial I nterface. The SSI module provides the connection for transducers with absolute coding and a SSI module.
The module converts the serial information of the transducer into parallel information for the controller. Data can be transferred in gray or in binary code.
The interface has connections for the SSI signals clock, data and the transducer supply voltage as well as two additional outputs that may be set or reset when a limit value is exceeded.
Output 0 can also be programmed as hold input. This causes the SSI transducer value to be frozen when a 24V high level is applied to output 0.
A low level will cause the transducer to transmit the actual SSI values.
You can also configure the outputs that they will remain set if the BASP signal is active.
FM 250S
SSI-Interface
D-
Us
M
.0
L+
Cl+
Cl-
D+
.1
F
X 2
3 4
VIPA 250-1BS00
3
4
5
6
1
2
7
8
9
I0
8
9
10
4
5
6
7
Pin
1
2
3
Assignment
Supply voltage DC +24V
CLK+ (Output)
CLK- (Output)
Data+ (Input)
Data- (Input)
DC 24V SSI transducer supply voltage
Common SSI transducer supply
Input/Output .0 and hold input
Output .1
Common of supply voltage
HB97E - FM - 250-1BS00 - Rev. 17/25 2-3
Chapter 2 Hardware description Manual VIPA System 200V
LEDs
Name
L+
C+
D+
.0
.1
F
The SSI module has a number of LEDs.
The following table explains the significance of these LEDs:
Color Description yellow Indicates that 24V power is available green ON when clock pulses are transmitted
OFF when hold function has been activated and 24V at I/O .0 green ON when data is received from the transducer (wiring test) green ON when 24V power is available at I/O .0 green ON when 24V power is available at Output .1 red ON when short circuit or overload is detected on one of the I/O .0 / O .1
Line distances The baudrate depends on the length of the communication line and on the
SSI transducer. Wiring has to consist of screened twisted pair cables. The specifications below are only intended as a guideline.
< 400m:
< 100m:
→
100kBaud
→
300kBaud
8
9
10
1
2
3
4
5
6
7
Wiring diagram schematic diagramm
L+
Clock +
Clock -
Direction +
Direction -
DC24V SSI
M SSI
DC 24V
The SSI module has an internal power supply. This power supply requires a voltage of DC 24V via L+ and M.
The supply voltage provides power to the interface electronics as well as the SSI transducer connected with DC 24V to pin 6 and 7.
Hold enable
SPS
Input .0
Hold
Shift clock Mode selection
Baudrate Param
BASP
Mode
:
Transducer
Shift register
24 Bit Gray/Binary Data In
I/O .0
O .1
M
MSB is transferred first, LSB is truncated
Output .0
Output .1
Data Out
2-4 HB97E - FM - 250-1BS00 - Rev. 17/25
Manual VIPA System 200V Chapter 2 Hardware description
Technical data
Order no. 250-1BS00
Current consumption/power loss
Current consumption from backplane bus 120 mA
Power loss
Technical data digital inputs
1 W
Number of inputs
Cable length, shielded
Cable length, unshielded
Rated load voltage
Reverse polarity protection of rated load voltage
Current consumption from load voltage L+
(without load)
Rated value
1
1000 m
600 m
DC 24 V
9
5 mA
Input voltage for signal "0"
Input voltage for signal "1"
Input voltage hysteresis
Frequency range
Input resistance
DC 20.4...28.8 V
-
-
DC 0...5 V
DC 15...28.8 V
-
Input current for signal "1" 7 mA
Connection of Two-Wire-BEROs possible -
Max. permissible BERO quiescent current -
Input delay of "0" to "1"
Input delay of "1" to "0"
Number of simultaneously utilizable inputs horizontal configuration
Number of simultaneously utilizable inputs vertical configuration
3 ms
3 ms
1
1
Input characteristic curve
Initial data size
Technical data digital outputs
Number of outputs
Cable length, shielded
Cable length, unshielded
Rated load voltage
Reverse polarity protection of rated load voltage
Current consumption from load voltage L+
(without load)
Total current per group, horizontal configuration, 40°C
Total current per group, horizontal configuration, 60°C
IEC 61131-2, type 1
4 Byte
2
1000 m
600 m
DC 24 V
9
5 mA
2 A
2 A
Total current per group, vertical configuration
Output voltage signal "1" at min. current
2 A
L+ (-0.8 V)
Output voltage signal "1" at max. current L+ (-125 mV)
Output current at signal "1", rated value 1 A
Output current, permitted range to 40°C
Output current, permitted range to 60°C
Output current at signal "0" max. (residual current)
Output delay of "0" to "1"
-
-
- max. 100 µs
HB97E - FM - 250-1BS00 - Rev. 17/25 2-5
Chapter 2 Hardware description
2-6
Manual VIPA System 200V
Order no.
Output delay of "1" to "0"
Minimum load current
Lamp load
Parallel switching of outputs for redundant control of a load
Parallel switching of outputs for increased power
Actuation of digital input
Switching frequency with resistive load
Switching frequency with inductive load
Switching frequency on lamp load
Internal limitation of inductive shut-off voltage
250-1BS00 max. 350 µs
-
5 W not possible not possible
- max. 1000 Hz max. 0.5 Hz max. 10 Hz
L+ (-52 V)
Short-circuit protection of output
Trigger level yes, electronic
1.8 A
Number of operating cycle of relay outputs -
Switching capacity of contacts
Output data size
Status information, alarms, diagnostics
-
4 Byte
Status display yes
Interrupts no
Process alarm
Diagnostic interrupt
Diagnostic functions
Diagnostics information read-out
Supply voltage display
Group error display
Channel error display
Isolation no no no none yes yes
Between channels
Between channels of groups to
Between channels and backplane bus
Between channels and power supply -
Max. potential difference between circuits -
- Max. potential difference between inputs
(Ucm)
Max. potential difference between Mana and Mintern (Uiso)
-
- Max. potential difference between inputs and Mana (Ucm)
Max. potential difference between inputs and Mintern (Uiso)
Max. potential difference between Mintern and outputs
Insulation tested with
Technical data SSI
Interfaces type none
-
-
9
-
-
DC 500 V
RS422
Encoder frequency / baud rate
SSI pause time parameterizable (100k, 300kHz)
35µs
Normalization -
Bit length encoder data
Mode master
24 Bit
9
Mode monitoring operation
Shift direction MSB first
Shift direction LSB first
Binary code
Gray code
9
9
9
HB97E - FM - 250-1BS00 - Rev. 17/25
Manual VIPA System 200V
Order no.
Datasizes
Input bytes
Output bytes
Parameter bytes
Diagnostic bytes
Housing
Material
Mounting
Mechanical data
Dimensions (WxHxD)
Net weight
Weight including accessories
Gross weight
Environmental conditions
Operating temperature
Storage temperature
Certifications
UL certification
KC certification
Chapter 2 Hardware description
250-1BS00
4
4
6
0
PPE / PA 6.6
Profile rail 35 mm
25.4 x 76 x 78 mm
100 g
-
-
0 °C to 60 °C
-25 °C to 70 °C yes
-
HB97E - FM - 250-1BS00 - Rev. 17/25 2-7
Chapter 2 Hardware description Manual VIPA System 200V
2-8 HB97E - FM - 250-1BS00 - Rev. 17/25
Manual VIPA System 200V Chapter 3 Deployment
Chapter 3 Deployment
Overview
Contents
This chapter contains every information on the deployment and the configuration of the SSI module FM 250S.
Topic Page
Chapter 3 Deployment ..................................................................... 3-1
HB97E - FM - 250-1BS00 - Rev. 17/25 3-1
Chapter 3 Deployment Manual VIPA System 200V
Functionality
Overview SSI is the abbreviation for S ynchronous S erial I nterface. The SSI module provides the connection for transducers with absolute coding and a SSI module.
The module converts the serial information of the transducer into parallel information for the controller. Data can be transferred in gray or in binary code.
Configurable outputs
Access to the
SSI module
The interface has connections for the SSI signals clock, data and the transducer supply voltage as well as two additional outputs that may be set or reset when a limit value is exceeded.
Output 0 can also be programmed as hold input. This causes the SSI transducer value to be frozen when a 24V high level is applied to output 0.
A low level will cause the transducer to transmit the actual SSI values.
You can also configure the outputs that they will remain set if the BASP signal is active.
Input data (Data In)
The input data from the SSI transducer has a length of 4Byte. Byte 0 can be used as an Input/Output status indicator for the. Data is supplied in binary or in gray code, depending on the selected mode.
Byte Data In
0 Bit 0: Status Input/Output .0
Bit 1: Status Output .1
Bit 7 ... 2: reserved
1
2
3
SSI transducer value: HB
SSI transducer value: MB
SSI transducer value: LB
3-2 HB97E - FM - 250-1BS00 - Rev. 17/25
Manual VIPA System 200V Chapter 3 Deployment
Output data (Data Out)
Data Out provides the option of controlling the 2 Output ports on the SSI module depending on the value of a transducer input. Output data consists of 4Byte.
The SSI transducer stores 8Byte of output data, i.e. you may define two comparative values along with the respective control byte.
In the control byte you are able to specify how the reference value should affect which output. The status of the I/Os is signaled via the input bytes.
The following table shows the assignment of these output bytes.
Byte Data Out
0 Bit 1 ... 0: set point value
00: no set point value
01: for Output 0
10: for Output 1
11: for both Outputs
1
Bit 2: reserved
Bit 3: set conditions for Output
0: when actual value exceeds comparison value
1: when actual value is less than comparison value
Bit 7 ... 4: reserved
Comparison value: HB
2
3
Comparison value: MB
Comparison value: LB
HB97E - FM - 250-1BS00 - Rev. 17/25 3-3
Chapter 3 Deployment Manual VIPA System 200V
Configuration
Configuration data
4Byte of configuration data are transferred. In these bytes you define the baud rate, the coding and the analysis of the combined I/O .0 as well as the
BASP signal.
The structure of the configuration data is as follows:
Byte Bit 7 ... 0
0 Bit 7 ... 0: reserved
1 Bit 7 ... 0: reserved
0: 300kBaud (default)
3
3 ... 255: reserved
Bit 0: Coding
0: Binary code (default)
1: Gray code
Bit 2: SSI format
0: Multi turn (24 bit)
Bit 4: Hold function
Bit 7: BASP signal
Baud rate The transducer connected to the SSI channel transmits serial data. It requires a clock pulse from the SSI module. The baud rate defines this clock. You may choose a value of 100 or 300kBaud.
The default setting is 300kBaud.
3-4 HB97E - FM - 250-1BS00 - Rev. 17/25
Manual VIPA System 200V
Coding
Hold function
BASP signal
Chapter 3 Deployment
The gray code is a different form of binary code. The principle of the gray code is that two neighboring gray numbers will differ in exactly one single bit.
When the gray code is used, transmission errors can be detected easily as neighboring characters may only be different in a single location.
Table of rules for the gray code:
Decimal
0
Gray Code
0 0 0 0
5
6
7
8
1
2
3
4
0 0 0 1
0 0 1 1
0 0 1 0
0 1 1 0
0 1 1 1
0 1 0 1
0 1 0 0
1 1 0 0
9
10
11
12
13
14
15
1 1 0 1
1 1 1 1
1 1 1 0
1 0 1 0
1 0 1 1
1 0 0 1
1 0 0 0
I.e. the last digit of the number results from the vertical repetition of the sequence "0 11 0", the penultimate digit results from the repetition "00 1111
00", the third-last number from the repetition of 4x"0", 8x"1" and again
4x"0", etc. (see columns in the table!).
Here you define that I/O .0 should be used as hold input. When you have activated this function, the current transducer value will be stored when
I/O .0 is connected to 24V. The transducer value is only updated when the
24V level is removed from I/O .0.
In this case you have to be aware that I/O .0 operates only in input mode.
BASP is a German abbreviation for command output inhibited, i.e. all outputs are reset and inhibited as long as the BASP signal is applied via the backplane bus. You may disable the evaluation of the BASP signals by setting this bit. This means that the outputs will remain set.
HB97E - FM - 250-1BS00 - Rev. 17/25 3-5
Chapter 3 Deployment Manual VIPA System 200V
3-6 HB97E - FM - 250-1BS00 - Rev. 17/25
advertisement
Key Features
- Supports a wide range of SSI devices, including encoders, position sensors, and temperature sensors.
- Compatible with a variety of PLC models.
- High-speed data transfer rates.
- Advanced features for enhanced performance and reliability.
Related manuals
Frequently Answers and Questions
What is the purpose of the FM 250-1BS00?
What types of SSI devices can be connected to the FM 250-1BS00?
Is the FM 250-1BS00 compatible with all PLC models?
What are the benefits of using the FM 250-1BS00?
advertisement
Table of contents
- 3 Contents
- 5 About this manual
- 7 Safety information
- 10 Safety Information for Users
- 11 System conception
- 13 Dimensions
- 15 Installation
- 19 Demounting and module exchange
- 20 Wiring
- 22 Installation guidelines
- 25 General data
- 28 Properties
- 29 Structure
- 31 Technical data
- 36 Functionality
- 38 Configuration