advertisement
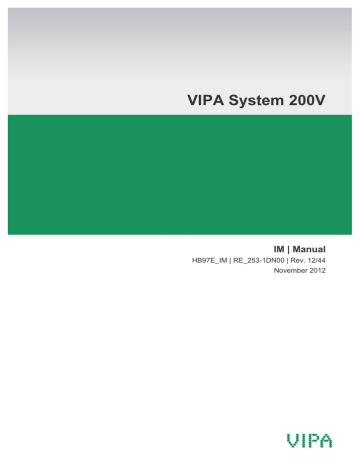
VIPA System 200V
IM | Manual
HB97E_IM | RE_253-1DN00 | Rev. 12/44
November 2012
Copyright © VIPA GmbH. All Rights Reserved.
This document contains proprietary information of VIPA and is not to be disclosed or used except in accordance with applicable agreements.
This material is protected by the copyright laws. It may not be reproduced, distributed, or altered in any fashion by any entity (either internal or external to VIPA), except in accordance with applicable agreements, contracts or licensing, without the express written consent of VIPA and the business management owner of the material.
For permission to reproduce or distribute, please contact:
VIPA, Gesellschaft für Visualisierung und Prozessautomatisierung mbH
Ohmstraße 4, D-91074 Herzogenaurach, Germany
Tel.: +49 (91 32) 744 -0
Fax.: +49 9132 744 1864
EMail: [email protected] http://www.vipa.com
Note
Every effort has been made to ensure that the information contained in this document was complete and accurate at the time of publishing. Nevertheless, the authors retain the right to modify the information. This customer document describes all the hardware units and functions known at the present time. Descriptions may be included for units which are not present at the customer site. The exact scope of delivery is described in the respective purchase contract.
CE Conformity Declaration
Hereby, VIPA GmbH declares that the products and systems are in compliance with the essential requirements and other relevant provisions.
Conformity is indicated by the CE marking affixed to the product.
Conformity Information
For more information regarding CE marking and Declaration of Conformity (DoC), please contact your local VIPA customer service organization.
Trademarks
VIPA, SLIO, System 100V, System 200V, System 300V, System 300S, System 400V, System 500S and Commander Compact are registered trademarks of VIPA Gesellschaft für Visualisierung und Prozessautomatisierung mbH.
SPEED7 is a registered trademark of profichip GmbH.
SIMATIC, STEP, SINEC, TIA Portal, S7-300 and S7-400 are registered trademarks of Siemens AG.
Microsoft und Windows are registered trademarks of Microsoft Inc., USA.
Portable Document Format (PDF) and Postscript are registered trademarks of Adobe Systems, Inc.
All other trademarks, logos and service or product marks specified herein are owned by their respective companies.
Information product support
Contact your local VIPA Customer Service Organization representative if you wish to report errors or questions regarding the contents of this document. If you are unable to locate a customer service center, contact VIPA as follows:
VIPA GmbH, Ohmstraße 4, 91074 Herzogenaurach, Germany
Telefax:+49 9132 744 1204
EMail: [email protected]
Technical support
Contact your local VIPA Customer Service Organization representative if you encounter problems with the product or have questions regarding the product. If you are unable to locate a customer service center, contact VIPA as follows:
VIPA GmbH, Ohmstraße 4, 91074 Herzogenaurach, Germany
Telephone: +49 9132 744 1150 (Hotline)
EMail: [email protected]
Manual VIPA System 200V
Contents
Contents
Chapter 1 Basics and Assembly ..................................................... 1-1
Safety Information for Users................................................................. 1-2
Demounting and module exchange .................................................... 1-11
Chapter 2 Hardware description ..................................................... 2-1
Chapter 3 Deployment ..................................................................... 3-1
Configuration by means of the DeviceNet-Manager ............................. 3-4
Specifying baudrate and DeviceNet address........................................ 3-5
Test in conjunction with the DeviceNet ................................................. 3-6
Module configuration in the DeviceNet-Manager .................................. 3-7
I/O addressing of the DeviceNet scanner ........................................... 3-12
HB97E - IM - RE_253-1DN00 - Rev. 12/44 i
Contents Manual VIPA System 200V ii HB97E - IM - RE_253-1DN00 - Rev. 12/44
Manual VIPA System 200V About this manual
About this manual
This manual describes the System 200V DeviceNet slave module IM 253-
1DN00 from VIPA. Here you may find every information for commissioning and operation.
Overview Chapter 1: Basics and Assembly
The focus of this chapter is on the introduction of the VIPA System 200V.
Here you will find the information required to assemble and wire a controller system consisting of System 200V components.
Besides the dimensions the general technical data of System 200V will be found.
Chapter 2: Hardware description
Here the hardware components of the IM 253-1DN00 are described.
The technical data are at the end of the chapter.
Chapter 3: Deployment
This chapter contains the description of the VIPA DeviceNet slave.
Another section of this chapter concerns the configuration by means of the
DeviceNet-Manager of Allen - Bradley. This section describes the configuration of the DeviceNet coupler and the System 200V modules.
A summary of the diagnostic messages conclude the chapter.
HB97E - IM - RE_253-1DN00 - Rev. 12/44 1
About this manual Manual VIPA System 200V
Objective and contents
Target audience
Structure of the manual
Guide to the document
Availability
Icons
Headings
This manual describes the System 200V DeviceNet slave module IM 253-
1DN00 from VIPA. It contains a description of the construction, project implementation and usage.
This manual is part of the documentation package with order number
HB97E_IM and relevant for:
Product
IM 253DN
Order number
VIPA 253-1DN00 as of state:
HW
03
The manual is targeted at users who have a background in automation technology.
The manual consists of chapters. Every chapter provides a self-contained description of a specific topic.
The following guides are available in the manual:
• an overall table of contents at the beginning of the manual
• an overview of the topics for every chapter
The manual is available in:
• printed form, on paper
• in electronic form as PDF-file (Adobe Acrobat Reader)
Important passages in the text are highlighted by following icons and headings:
Danger!
Immediate or likely danger.
Personal injury is possible.
Attention!
Damages to property is likely if these warnings are not heeded.
Note!
Supplementary information and useful tips.
2 HB97E - IM - RE_253-1DN00 - Rev. 12/44
Manual VIPA System 200V Safety information
Safety information
Applications conforming with specifications
Documentation
Disposal
The IM 253DN is constructed and produced for:
• all VIPA System 200V components
• communication and process control
• general control and automation applications
• industrial applications
• operation within the environmental conditions specified in the technical data
• installation into a cubicle
Danger!
This device is not certified for applications in
• in explosive environments (EX-zone)
The manual must be available to all personnel in the
• project design department
• installation department
• commissioning
• operation
The following conditions must be met before using or commissioning
the components described in this manual:
•
Hardware modifications to the process control system should only be carried out when the system has been disconnected from power!
•
Installation and hardware modification only by properly trained personnel.
•
The national rules and regulations of the respective country must be satisfied (installation, safety, EMC ...)
National rules and regulations apply to the disposal of the unit!
HB97E - IM - RE_253-1DN00 - Rev. 12/44 3
Safety information Manual VIPA System 200V
4 HB97E - IM - RE_253-1DN00 - Rev. 12/44
Manual VIPA System 200V
Chapter 1
Overview
Contents
Chapter 1 Basics and Assembly
Basics and Assembly
The focus of this chapter is on the introduction of the VIPA System 200V.
Here you will find the information required to assemble and wire a controller system consisting of System 200V components.
Besides the dimensions the general technical data of System 200V will be found.
Topic Page
Chapter 1 Basics and Assembly ..................................................... 1-1
Safety Information for Users ................................................................. 1-2
Demounting and module exchange .................................................... 1-11
HB97E - IM - RE_253-1DN00 - Rev. 12/44 1-1
Chapter 1 Basics and Assembly Manual VIPA System 200V
Safety Information for Users
Handling of electrostatic sensitive modules
VIPA modules make use of highly integrated components in MOS-
Technology. These components are extremely sensitive to over-voltages that can occur during electrostatic discharges.
The following symbol is attached to modules that can be destroyed by electrostatic discharges.
The Symbol is located on the module, the module rack or on packing material and it indicates the presence of electrostatic sensitive equipment.
It is possible that electrostatic sensitive equipment is destroyed by energies and voltages that are far less than the human threshold of perception.
These voltages can occur where persons do not discharge themselves before handling electrostatic sensitive modules and they can damage components thereby, causing the module to become inoperable or unusable.
Modules that have been damaged by electrostatic discharges can fail after a temperature change, mechanical shock or changes in the electrical load.
Only the consequent implementation of protection devices and meticulous attention to the applicable rules and regulations for handling the respective equipment can prevent failures of electrostatic sensitive modules.
Shipping of electrostatic sensitive modules
Modules must be shipped in the original packing material.
Measurements and alterations on electrostatic sensitive modules
When you are conducting measurements on electrostatic sensitive modules you should take the following precautions:
•
Floating instruments must be discharged before use.
•
Instruments must be grounded.
Modifying electrostatic sensitive modules you should only use soldering irons with grounded tips.
Attention!
Personnel and instruments should be grounded when working on electrostatic sensitive modules.
1-2 HB97E - IM - RE_253-1DN00 - Rev. 12/44
Manual VIPA System 200V
Chapter 1 Basics and Assembly
System conception
Overview
Components
The System 200V is a modular automation system for assembly on a
35mm profile rail. By means of the peripheral modules with 4, 8 and 16 channels this system may properly be adapted matching to your automation tasks.
CPU 215
SM 221
DI 8xDC24V
SM 221
DI 8xDC24V
SM 221
DI 8xDC24V
SM 221
DI 8xDC24V
R
RN
ST
MR
1 1
S
.0
2
.0
2
MMC
.1
3
.1
3
PW
.2
4
.2
4
SF .3
5
.3
5
FC
MC
M
P
2
I
.4
.5
6
7
.4
.5
6
7
.6
8
X1
DC
24V
+
1
X 2
3 4
-
2
VIPA 215-1BA03
.7
9
I0
X 2
3 4
VIPA 221-1BF00
.6
.7
8
9
I0
X 2
3 4
VIPA 221-1BF00
.0
.1
.2
.3
.4
.5
.6
.7
1
2
3
4
7
8
9
I0
X 2
3 4
VIPA 221-1BF00
5
6
.0
.1
.2
.3
.4
.5
.6
.7
1
2
3
4
5
6
7
8
9
I0
X 2
3 4
VIPA 221-1BF00
The System 200V consists of the following components:
•
Head modules like CPU and bus coupler
•
Periphery modules like I/O, function und communication modules
•
Power supplies
•
Extension modules
Head modules
Periphery modules
PW
SF
FC
MC
CPU 214
R
S
MMC
RN
ST
MR
M
P
2
I
DC
24V
X 2
-
+
3 4
X1
1
2
VIPA 214-1BC03
SM 221
DI 8xAC/..48V
N
1
10
X 2
3 4
VIPA 221-1FF30
5
6
7
1
2
3
4
8
9
I0
IM 253DP
9 9
PW
ER
RD
DE
ADR.
D
P
X1
DC
24V
+
X 8
9 10
-
1
2
VIPA 253-1DP00 n
DI 16xDC24V
.3
.4
.5
.6
.0
.1
.2
.7
.0
.1
.2
.3
.4
.5
.6
.7
n+1
VIPA 221-1BH10
17
18
X 2
3 4
12
13
14
15
16
8
9
10
11
5
6
3
4
7
1
2
With a head module CPU respectively bus interface and DC 24V power supply are integrated to one casing.
Via the integrated power supply the CPU respectively bus interface is power supplied as well as the electronic of the connected periphery modules.
The modules are direct installed on a
35mm profile rail and connected to the head module by a bus connector, which was mounted on the profile rail before.
Most of the periphery modules are equipped with a 10pin respectively 18pin connector. This connector provides the electrical interface for the signaling and supplies lines of the modules.
HB97E - IM - RE_253-1DN00 - Rev. 12/44 1-3
Chapter 1 Basics and Assembly
Power supplies
PS 207/2
L
OH
N
G
100-240V AC
550-230mA
50-60Hz
P
E
OL
OK
OUT DC 24V /
∑
X1
Ι:
2A
4A (peak)
+
DC 24V
-
1
2
+
DC 24V
-
X 2
3 4
VIPA 207-1BA00
3
4
Expansion modules
CM 201
X1.
X2.
Manual VIPA System 200V
With the System 200V the DC 24V power supply can take place either externally or via a particularly for this developed power supply.
The power supply may be mounted on the profile rail together with the System 200V modules. It has no connector to the backplane bus.
The expansion modules are complementary modules providing 2- or 3wire connection facilities.
The modules are not connected to the backplane bus.
Structure/ dimensions
Installation
X 2
3 4
VIPA 201-1AA00
•
Profile rail 35mm
•
Dimensions of the basic enclosure:
1tier width: (HxWxD) in mm: 76x25.4x74 in inches: 3x1x3
2tier width: (HxWxD) in mm: 76x50.8x74 in inches: 3x2x3
1
4
2
Please note that you can only install head modules, like the CPU, the PC and couplers at slot 1 or 1 and 2 (for double width modules).
3
(double width)
[2] Head module
(single width)
D
P
0 1
Note
Information about the max. number of pluggable modules and the max. current at the backplane bus can be found in the "Technical Data" of the according head module.
Please install modules with a high current consumption directly beside the head module.
Clack
1-4 HB97E - IM - RE_253-1DN00 - Rev. 12/44
Manual VIPA System 200V
Chapter 1 Basics and Assembly
Dimensions
Dimensions
Basic enclosure
1tier width (HxWxD) in mm: 76 x 25.4 x 74
2tier width (HxWxD) in mm: 76 x 50.8 x 74
Installation dimensions
Installed and wired dimensions
In- / Output modules
74 mm
88 mm ca. 110 mm
HB97E - IM - RE_253-1DN00 - Rev. 12/44 1-5
Chapter 1 Basics and Assembly
Function modules/
Extension modules
Manual VIPA System 200V
CPUs (here with
EasyConn from
VIPA)
85 mm
1-6 HB97E - IM - RE_253-1DN00 - Rev. 12/44
Manual VIPA System 200V
Chapter 1 Basics and Assembly
Installation
General
Profile rail
The modules are each installed on a 35mm profile rail and connected via a bus connector. Before installing the module the bus connector is to be placed on the profile rail before.
For installation the following 35mm profile rails may be used:
35 mm
35 mm
Bus connector
27 mm
Order number
290-1AF00
290-1AF30
Label
27 mm
35mm profile rail
35mm profile rail
Description
Length 2000mm, height 15mm
Length 530mm, height 15mm
System 200V modules communicate via a backplane bus connector. The backplane bus connector is isolated and available from VIPA in of 1-, 2-, 4- or 8tier width.
The following figure shows a 1tier connector and a 4tier connector bus:
The bus connector is to be placed on the profile rail until it clips in its place and the bus connections look out from the profile rail.
Order number Label Description
HB97E - IM - RE_253-1DN00 - Rev. 12/44 1-7
Chapter 1 Basics and Assembly Manual VIPA System 200V
Installation on a profile rail
1
The following figure shows the installation of a 4tier width bus connector in a profile rail and the slots for the modules.
2
The different slots are defined by guide rails.
3
[1] Head module
(double width)
[2] Head module
(single width)
4
PW
ER
RD
BA
ADR.
0 1
+
DC24V
-
1
2
R
S
PW
SF
FC
MC
MMC
Assembly regarding the current consumption
•
Use bus connectors as long as possible.
•
Sort the modules with a high current consumption right beside the head module. In the service area of www.vipa.com a list of current consumption of every System 200V module can be found.
1-8 HB97E - IM - RE_253-1DN00 - Rev. 12/44
Manual VIPA System 200V
Chapter 1 Basics and Assembly
Assembly possibilities
hoizontal assembly
0 1 lying assembly vertical assembly
Please regard the allowed environmental temperatures:
• horizontal assembly:
• vertical assembly:
• lying assembly: from 0 to 60°C from 0 to 40°C from 0 to 40°C
The horizontal assembly always starts at the left side with a head module, then you install the peripheral modules beside to the right.
You may install up to 32 peripheral modules.
Please follow these rules during the assembly!
•
Turn off the power supply before you install or remove any modules!
•
Make sure that a clearance of at least 60mm exists above and 80mm below the middle of the profile rail.
1
4
2 3
•
Every row must be completed from left to right and it has to start with a head module.
[1] Head module (double width)
[2] Head module (single width)
•
Modules are to be installed side by side. Gaps are not permitted between the modules since this would interrupt the backplane bus.
•
A module is only installed properly and connected electrically when it has clicked into place with an audible click.
•
Slots after the last module may remain unoccupied.
Note!
Information about the max. number of pluggable modules and the max. current at the backplane bus can be found in the "Technical Data" of the according head module.
Please install modules with a high current consumption directly beside the head module.
HB97E - IM - RE_253-1DN00 - Rev. 12/44 1-9
Chapter 1 Basics and Assembly
Assembly procedure
Manual VIPA System 200V
•
Install the profile rail. Make sure that a clearance of at least 60mm exists above and 80mm below the middle of the profile rail.
•
Press the bus connector into the profile rail until it clips securely into place and the bus-connectors look out from the profile rail. This provides the basis for the installation of your modules.
•
Start at the outer left location with the installation of your head module and install the peripheral modules to the right of this.
1 2 3
[1] Head module
(double width)
(single width)
4
•
Insert the module that you are installing into the profile rail at an angle of 45 degrees from the top and rotate the module into place until it clicks into the profile rail with an audible click. The proper connection to the backplane bus can only be guaranteed when the module has properly clicked into place.
Attention!
Power must be turned off before modules are installed or removed!
1-10
Clack
HB97E - IM - RE_253-1DN00 - Rev. 12/44
Manual VIPA System 200V
Chapter 1 Basics and Assembly
Demounting and module exchange
1
2
3
4
5
•
Remove if exists the wiring to the module, by pressing both locking lever on the connector and pulling the connector.
•
The casing of the module has a spring loaded clip at the bottom by which the module can be removed.
•
The clip is unlocked by pressing the screwdriver in an upward direction.
•
Withdraw the module with a slight rotation to the top.
Attention!
Power must be turned off before modules are installed or removed!
Please regard that the backplane bus is interrupted at the point where the module was removed!
HB97E - IM - RE_253-1DN00 - Rev. 12/44 1-11
Chapter 1 Basics and Assembly
Wiring
Overview
Manual VIPA System 200V
Most peripheral modules are equipped with a 10pole or a 18pole connector.
This connector provides the electrical interface for the signaling and supply lines of the modules.
The modules carry spring-clip connectors for interconnections and wiring.
The spring-clip connector technology simplifies the wiring requirements for signaling and power cables.
In contrast to screw terminal connections, spring-clip wiring is vibration proof. The assignment of the terminals is contained in the description of the respective modules.
You may connect conductors with a diameter from 0.08mm
2
up to 2.5mm
2
(max. 1.5mm
2
for 18pole connectors).
The following figure shows a module with a 10pole connector.
1
1
6
7
8
9
10
4
5
2
3
9
10
7
8
5
6
3
4
1
2
2
1
2
3
3 4 5
[1]
[2]
[3]
[4]
[5]
Locking lever
Pin no. at the module
Pin no. at the connector
Wiring port
Opening for screwdriver
1
Note!
The spring-clip is destroyed if you push the screwdriver into the wire port!
Make sure that you only insert the screwdriver into the square hole of the connector!
1-12 HB97E - IM - RE_253-1DN00 - Rev. 12/44
Manual VIPA System 200V
Chapter 1 Basics and Assembly
Wiring procedure
•
Install the connector on the module until it locks with an audible click.
For this purpose you press the two clips together as shown.
The connector is now in a permanent position and can easily be wired.
The following section shows the wiring procedure from top view.
•
Insert a screwdriver at an angel into the square opening as shown.
•
Press and hold the screwdriver in the opposite direction to open the contact spring.
•
Insert the stripped end of the wire into the round opening. You can use wires with a diameter of 0.08mm
2
to 2.5mm
2
(1.5mm
2
for 18pole connectors).
•
By removing the screwdriver the wire is connected safely with the plug connector via a spring.
Note!
Wire the power supply connections first followed by the signal cables
(inputs and outputs).
HB97E - IM - RE_253-1DN00 - Rev. 12/44 1-13
Chapter 1 Basics and Assembly Manual VIPA System 200V
Installation guidelines
General
What means EMC?
Electromagnetic digestibility (EMC) means the ability of an electrical device, to function error free in an electromagnetic environment without being interferenced res. without interferencing the environment.
All System 200V components are developed for the deployment in hard industrial environments and fulfill high demands on the EMC. Nevertheless you should project an EMC planning before installing the components and take conceivable interference causes into account.
Possible interference causes
The installation guidelines contain information about the interference free deployment of System 200V systems. There is the description of the ways, interference may occur in your control, how you can make sure the electromagnetic digestibility (EMC), and how you manage the isolation.
Electromagnetic interferences may interfere your control via different ways:
•
Fields
•
I/O signal conductors
•
Bus system
•
Current supply
•
Protected earth conductor
Depending on the spreading medium (lead bound or lead free) and the distance to the interference cause, interferences to your control occur by means of different coupling mechanisms.
One differs:
• galvanic coupling
• capacitive coupling
• inductive coupling
• radiant coupling
1-14 HB97E - IM - RE_253-1DN00 - Rev. 12/44
Manual VIPA System 200V
Basic rules for
EMC
Chapter 1 Basics and Assembly
In the most times it is enough to take care of some elementary rules to guarantee the EMC. Please regard the following basic rules when installing your PLC.
•
Take care of a correct area-wide grounding of the inactive metal parts when installing your components.
- Install a central connection between the ground and the protected earth conductor system.
- Connect all inactive metal extensive and impedance-low.
- Please try not to use aluminum parts. Aluminum is easily oxidizing and is therefore less suitable for grounding.
•
When cabling, take care of the correct line routing.
- Organize your cabling in line groups (high voltage, current supply, signal and data lines).
- Always lay your high voltage lines and signal res. data lines in separate channels or bundles.
- Route the signal and data lines as near as possible beside ground areas (e.g. suspension bars, metal rails, tin cabinet).
•
Proof the correct fixing of the lead isolation.
- Data lines must be laid isolated.
- Analog lines must be laid isolated. When transmitting signals with small amplitudes the one sided laying of the isolation may be favorable.
- Lay the line isolation extensively on an isolation/protected earth conductor rail directly after the cabinet entry and fix the isolation with cable clamps.
- Make sure that the isolation/protected earth conductor rail is connected impedance-low with the cabinet.
- Use metallic or metalized plug cases for isolated data lines.
•
In special use cases you should appoint special EMC actions.
- Wire all inductivities with erase links.
- Please consider luminescent lamps can influence signal lines.
•
Create a homogeneous reference potential and ground all electrical operating supplies when possible.
- Please take care for the targeted employment of the grounding actions. The grounding of the PLC is a protection and functionality activity.
- Connect installation parts and cabinets with the System 200V in star topology with the isolation/protected earth conductor system. So you avoid ground loops.
- If potential differences between installation parts and cabinets occur, lay sufficiently dimensioned potential compensation lines.
HB97E - IM - RE_253-1DN00 - Rev. 12/44 1-15
Chapter 1 Basics and Assembly
Isolation of conductors
Manual VIPA System 200V
Electrical, magnetically and electromagnetic interference fields are weakened by means of an isolation, one talks of absorption.
Via the isolation rail, that is connected conductive with the rack, interference currents are shunt via cable isolation to the ground. Hereby you have to make sure, that the connection to the protected earth conductor is impedance-low, because otherwise the interference currents may appear as interference cause.
When isolating cables you have to regard the following:
•
If possible, use only cables with isolation tangle.
•
The hiding power of the isolation should be higher than 80%.
•
Normally you should always lay the isolation of cables on both sides.
Only by means of the both-sided connection of the isolation you achieve high quality interference suppression in the higher frequency area.
Only as exception you may also lay the isolation one-sided. Then you only achieve the absorption of the lower frequencies. A one-sided isolation connection may be convenient, if:
- the conduction of a potential compensating line is not possible
- analog signals (some mV res. µA) are transferred
- foil isolations (static isolations) are used.
•
With data lines always use metallic or metalized plugs for serial couplings. Fix the isolation of the data line at the plug rack. Do not lay the isolation on the PIN 1 of the plug bar!
•
At stationary operation it is convenient to strip the insulated cable interruption free and lay it on the isolation/protected earth conductor line.
•
To fix the isolation tangles use cable clamps out of metal. The clamps must clasp the isolation extensively and have well contact.
•
Lay the isolation on an isolation rail directly after the entry of the cable in the cabinet. Lead the isolation further on to the System 200V module and don't lay it on there again!
Please regard at installation!
At potential differences between the grounding points, there may be a compensation current via the isolation connected at both sides.
Remedy: Potential compensation line.
1-16 HB97E - IM - RE_253-1DN00 - Rev. 12/44
Manual VIPA System 200V
Chapter 1 Basics and Assembly
General data
Structure/ dimensions
•
Profile rail 35mm
•
Peripheral modules with recessed labelling
•
Dimensions of the basic enclosure:
1tier width: (HxWxD) in mm: 76x25.4x74 in inches: 3x1x3
2tier width: (HxWxD) in mm: 76x50.8x74 in inches: 3x2x3
Reliability
Environmental conditions
•
Wiring by means of spring pressure connections (CageClamps) at the front-facing connector, core cross-section 0.08 ... 2.5mm
2
or 1.5 mm
2
(18pole plug)
•
Complete isolation of the wiring when modules are exchanged
•
Every module is isolated from the backplane bus
•
ESD/Burst acc. IEC 61000-4-2 / IEC 61000-4-4 (to level 3)
•
Shock resistance acc. IEC 60068-2-6 / IEC 60068-2-27 (1G/12G)
•
Class of protection IP20
•
Operating temperature: 0 ... +60°C
•
Storage temperature: -25 ... +70°C
•
Relative humidity: 5 ... 95% without condensation
•
Ventilation by means of a fan is not required
HB97E - IM - RE_253-1DN00 - Rev. 12/44 1-17
Chapter 1 Basics and Assembly Manual VIPA System 200V
1-18 HB97E - IM - RE_253-1DN00 - Rev. 12/44
Manual VIPA System 200V
Chapter 2 Hardware description
Chapter 2 Hardware description
Overview
Contents
Here the hardware components of the IM 253-1DN00 are described.
The technical data are at the end of the chapter.
Topic Page
Chapter 2 Hardware description...................................................... 2-1
HB97E - IM - RE_253-1DN00 - Rev. 12/44 2-1
Chapter 2 Hardware description Manual VIPA System 200V
Properties
IM 253DN
253-1DN00
The DeviceNet coupler IM 253DN provides a simple method of interfacing any decentral peripheral modules by means of the DeviceNet protocol.
•
Group 2 only Device
- employs the predefined connection set
•
Poll only Device
- no BIT STROBE mode support
- no CHANGE OF STATE support
• supports all baudrates: 125, 250 and 500kBaud
• address selection by means of switches
• definition of the data rate by means of a special
PowerON procedure (start from address 90 ... 92)
•
LED status indicators
• a max. of 32 peripheral modules can be installed
• of these a max. of 8 may be configurable modules
• module configuration by means of the DeviceNet-Manager
Order data
IM 253 DN
PW
ER
RD
BA
V-
CL
DR
CH
V+
ADR.
9 9
DC24V
+ 1
-
2
X 2
3 4
VIPA 253-1DN00
Type Order number Description
IM 253DN VIPA 253-1DN00 DeviceNet coupler
2-2 HB97E - IM - RE_253-1DN00 - Rev. 12/44
Manual VIPA System 200V
Structure
Front view
253-1DN00
Interfaces
1
IM 253 DN
PW
ER
RD
BA
V-
CL
DR
CH
V+
2
DeviceNet
ADR.
9 2
DC24V
+
1
-
2
X 2
3 4
VIPA 253-1DN00
3
4
V-
CL
DR
CH
V+
5
6
7
3
4
GND
CAN low
Drain
CAN high
DC 24 V
Chapter 2 Hardware description
[1] LED status indicator
[4] DC 24V power supply connector
X1
+
-
1
2
+ DC 24 V
0 V
DeviceNet interface The DeviceNet connection is provided by a 5pin Open Style connector.
The pin assignment is imprinted on the front of the module.
[V-] GND operating voltage
V-
CL
DR
CH
V+
[DR] DRAIN
[V+] DC 24V operating voltage
HB97E - IM - RE_253-1DN00 - Rev. 12/44 2-3
Chapter 2 Hardware description Manual VIPA System 200V
Power supply
LEDs
Every DeviceNet slave has an internal power supply. This power supply requires DC 24V. In addition to the electronics on the bus coupler, the supply voltage is also used to power any modules connected to the backplane bus. The "max. current drain at backplane bus" can be found in the Technical Data.
The power supply is protected against reverse polarity.
DeviceNet and backplane bus are galvanically isolated from each other.
Note!
The DeviceNet coupler does not require any current from the power that is available via the DeviceNet connector.
4 LEDs on the front show the current status of the module for the quick troubleshooting. A detailed description of the troubleshooting procedure by means of the LEDs and the backplane is available in a section of the chapter "diagnostics".
Label Color Description
PW green Power-LED: supply voltage available
ER
RD red DeviceNet or backplane bus bus error green Backplane bus status
Address selector
0 1
The address selector is used for:
• the definition of the unique DeviceNet address
• programming of the baudrate
Addresses:
0 ... 63: DeviceNet address
90:
91:
92: communication rate 125 kBaud communication rate 250 kBaud communication rate 500kBaud
2-4 HB97E - IM - RE_253-1DN00 - Rev. 12/44
Manual VIPA System 200V
Chapter 2 Hardware description
Technical data
Order number
Type
Technical data power supply
Power supply (rated value)
Power supply (permitted range)
Reverse polarity protection
Current consumption (no-load operation)
Current consumption (rated value)
Inrush current
253-1DN00
IM 253DN, DeviceNET slave
DC 24 V
DC 20.4...28.8 V
9
50 mA
800 mA
65 A
Max. current drain at backplane bus
Max. current drain load supply
Power loss
Status information, alarms, diagnostics
3.5 A
-
2 W
Status display yes
Interrupts no
Process alarm
Diagnostic interrupt
Diagnostic functions no no yes
Diagnostics information read-out
Supply voltage display
Service Indicator
Group error display none yes
- yes
Channel error display
Hardware configuration
Racks, max.
Modules per rack, max. none
1
32
Number of digital modules, max.
Number of analog modules, max.
Communication
32
8
Fieldbus DeviceNet
Type of interface
Connector
Topology
CAN
5-pin Open Style Connector
Linear bus with bus termination at both ends
9
Electrically isolated
Number of participants, max.
Node addresses
64
0 - 63
Transmission speed, min.
Transmission speed, max.
Address range inputs, max.
Address range outputs, max.
Number of TxPDOs, max.
Number of RxPDOs, max.
Housing
Material
Mounting
Mechanical data
Dimensions (WxHxD)
125 kbit/s
500 kbit/s
256 Byte
256 Byte
-
-
PPE / PA 6.6
Profile rail 35 mm
25.4 x 76 x 78 mm
Environmental conditions
Operating temperature
Storage temperature
Certifications
UL508 certification
0 °C to 60 °C
-25 °C to 70 °C yes
HB97E - IM - RE_253-1DN00 - Rev. 12/44 2-5
Chapter 2 Hardware description
Additional
Technical Data
Manual VIPA System 200V
Function specific data
Network topology
Communication medium
Communication rate
253-1DN00
Linear bus, tap lines up to
6m length
Screened 5core cable
125, 250, 500kBaud
Overall length of the bus
Combination with peripheral modules
up to 500m
Number of modules max. 32
(of it maximally 8 parameterizable)
2-6 HB97E - IM - RE_253-1DN00 - Rev. 12/44
Manual VIPA System 200V
Chapter 3 Deployment
Chapter 3 Deployment
Overview
Contents
This chapter contains the description of the VIPA DeviceNet slave.
Another section of this chapter concerns the configuration by means of the
DeviceNet-Manager of Allen - Bradley. This section describes the configuration of the DeviceNet coupler and the System 200V modules.
A summary of the diagnostic messages conclude the chapter.
Topic Page
Chapter 3 Deployment ..................................................................... 3-1
Configuration by means of the DeviceNet-Manager ............................. 3-4
Specifying baudrate and DeviceNet address ........................................ 3-5
Test in conjunction with the DeviceNet ................................................. 3-6
Module configuration in the DeviceNet-Manager .................................. 3-7
I/O addressing of the DeviceNet scanner ........................................... 3-12
HB97E - IM - RE_253-1DN00 - Rev. 12/44 3-1
Chapter 3 Deployment Manual VIPA System 200V
Basics DeviceNet
General
DeviceNet
DeviceNet is an open low-end network that is based upon the physical properties of CAN-Bus. The bus is also used to supply the devices with the required DC 24V power.
You can use DeviceNet to install direct connections between your control system and simple industrial devices like sensors and switches as well as technologically advanced devices like frequency converters and barcode readers.
Direct interfacing improves communications between the different devices and provides important diagnostic facilities at the device level.
DeviceNet is an open device net standard that satisfies the user profile for industrial real-time system applications.
The DeviceNet protocol has an open specification that is the property of and administered by the independent vendor organization "Open DeviceNet
Vendor Association" ODVA.
This is where standardized device profiles are created to provide compatibility and exchangeability on logical level for simple devices of the same type.
In contrast to the classical source–destination model, DeviceNet uses a modern producer/consumer model that requires data packets with identifier fields for the identification of the data.
This approach caters for multiple priority levels, more efficient transfers of
I/O data and multiple consumers for the data.
A device that has data to send produces the data on the network together with an identifier. All devices requiring data listen for messages. When a device recognizes a suitable identifier, they act and consume the respective data.
DeviceNet carries two types of messages:
•
I/O messages
Messages that are subject to critical timing constraints and that are contain data for control purposes that can be exchanged by means of a single or multiple connections and that employ identifiers with a high priority.
•
explicit messages
These are used to establish multi-purpose point-to-point communication paths between two devices which are used for the configuration of network couplers and for diagnostic purposes. These functions usually employ identifiers of a low priority.
Messages that are longer than 8Byte are subject to the fragmentation service. A set of rules for master/slave, peer-to-peer- and multi-master connections is also available.
3-2 HB97E - IM - RE_253-1DN00 - Rev. 12/44
Manual VIPA System 200V
Chapter 3 Deployment
Communication medium
Bus access method
Addressing
EDS file
DeviceNet employs a master line/tap line topology with up to 64 network nodes. The maximum distance is either 500m at a rate of 125kBaud, 250m at a rate of 250kBaud or 100m at a rate of 500kBaud.
The length of the tap lines can be up to 6m while the total length of all spur lines depends on the baudrate.
Network nodes can be removed from or inserted into the network without interruption of the network operation. New stations and failed stations are detected automatically.
DeviceNet employs a screened five-core cable as data communication medium.
DeviceNet uses voltage differences and for this reason it exhibits less sensitivity to interference than a voltage or current based interface.
Signals and power supply conductors are included in the same network cable. It is therefore possible to connect devices that obtain the operating voltage via the network as well as devices with an integrated power supply.
Furthermore it is possible to connect redundant power supplies to the network that guarantees the power supply when required.
DeviceNet operates according to the Carrier-Sense Multiple Access
(CSMA) principle, i.e. every station on the network may access the bus when it is not occupied (random access).
The exchange of messages is message orientated and not station orientated. Each message is provided with a unique and priorizing identifier. At any time only one station is able to occupy the bus with its messages.
The DeviceNet bus access control is subject to non-destructive, bit-wise arbitration. In this case non-destructive means that the successful station participating in the arbitration doesn't need to re-send its message. The most important station is selected automatically when multiple stations access the bus simultaneously. If a station that is ready to send recognizes that the bus is occupied, its send request is delayed until the current transfer has been completed.
All stations on the bus must be uniquely identified by means of an
ID address. Every DeviceNet device has addressing facilities.
The properties of the DeviceNet units are supplied in the form of an EDS file (Electronic Data Sheet) to configure a slave interface by means of your configuration tool.
HB97E - IM - RE_253-1DN00 - Rev. 12/44 3-3
Chapter 3 Deployment Manual VIPA System 200V
Configuration by means of the DeviceNet-Manager
Overview
Configuration of the DeviceNet-
Manager
The DeviceNet is configured by means of the DeviceNet-Manager software from Allen - Bradley.
The following steps are necessary for the configuration:
•
Configuration of the DeviceNet-Manager
•
Set baudrate and DeviceNet address of the module
•
Test the DeviceNet
•
Module configuration
•
I/O addressing of the DeviceNet scanner (master)
During the configuration the module specific data of the VIPA DeviceNet coupler are defined and supplied to the DeviceNet-Manager.
The following steps are required:
•
Insert the supplied disc into your PC.
•
Copy the file IM253DN.BMP to your PC into the directory
/DNETMGR/RES of the DeviceNet-Manager
•
The EDS file is located in a sub-directory of 501.VND on the disc. Copy the file 1.EDS into the directory
/DNETMGR/EDS/501.VND/0.TYP/1.COD
You can also copy the entire tree
501.vnd
|-- 0.typ
|--1.cod into the directory DNETMGR/EDS.
3-4 HB97E - IM - RE_253-1DN00 - Rev. 12/44
Manual VIPA System 200V
Chapter 3 Deployment
Specifying baudrate and DeviceNet address
Setting the baudrate
You may set the baudrate as well as the DeviceNet address when the power has been turned off. These will be transferred into the module when you turn the respective power supply on.
All stations connected to the bus communicate at the same baudrate. You may define the required rate by means of the address selector.
•
Turn off the power supply
•
Set the address selector to the wanted baudrate
Setting baudrate in kBaud
LED-indicator
RD-LED
ER-LED
•
Turn on the power supply
The selected transmission rate is saved to the EEPROM.
At this point your DeviceNet coupler is set to the correct baudrate.
When the baudrate has been saved successfully, the RD-LED (green) will be turned on.
When the baudrate was selected incorrectly, the ER-LED will be turned on.
Setting the
DeviceNet address
LED indicator
ER-LED
All stations connected to the bus must have a unique DeviceNet address.
The address can be defined by means of the address selector when the supply has been turned off.
•
Turn off the power supply
•
Set the address selector to the required address.
Please ensure that the address is unique in the system and that it is located between 0 and 63.
•
Turn on the power supply.
The selected address is saved to the RAM.
Note!
Any changes to the addressing will only become effective after a PowerON or an automatic reset. Changes to settings are not recognized during normal operations.
When the address is not valid or if it already exists the ER-LED (red) will be turned on after PowerON.
HB97E - IM - RE_253-1DN00 - Rev. 12/44 3-5
Chapter 3 Deployment Manual VIPA System 200V
Test in conjunction with the DeviceNet
Approach
•
Connect the PC containing the DeviceNet-Manager and the VIPA
DeviceNet coupler to the DeviceNet.
•
Define the baudrate and the node address at the coupler.
•
Turn on the power supply of the bus coupler.
•
Start the DeviceNet-Manager.
•
Enter the same data rate into the manager that was selected at the bus coupler.
•
Start the function Network Who in the manager.
The following network windows is displayed:
Device Details
•
Bus coupler click with the right mouse button.
•
Select the function "Device Details" in the context menu.
The Device Details box is displayed on screen:
3-6
Here you may display DeviceNet address (node address), the Vendor
Code (in this case this is 501 for VIPA GmbH) and other internal information about every module on the bus.
HB97E - IM - RE_253-1DN00 - Rev. 12/44
Manual VIPA System 200V
Chapter 3 Deployment
Module configuration in the DeviceNet-Manager
Configuration in groups
Approach
The System 200V includes configurable modules like analog modules.
When you are using these modules in conjunction with a DeviceNet coupler the respective parameters have to be saved in the DeviceNet coupler.
The following conditions apply to the configuration:
•
DeviceNet manages the parameter data in groups.
•
Every DeviceNet coupler is able to process and store a maximum of
144Byte of parameter data.
•
These 144Byte are divided into 8 groups of 18Byte each.
•
Every group can contain the parameter data of 1 module.
•
Groups are identified by a prefix-No. (1 ... 8) in the parameter name.
•
The number of parameter bytes is defined in the parameter "Len" (1. parameter) of a group. The number of parameter bytes is available from the technical data contained in the documentation on the peripheral modules.
•
The group allocation for a module does not depend on the location or the installation sequence.
•
The allocation of the plug-in location is defined by means of the "Slot"parameter of a group (2. parameter).
•
The values may be entered as bit patterns by double-clicking a parameter.
•
Unused groups are identified by a "Value" 0000 0000.
Precondition: The IM 253DN coupler is active on the bus.
Below follows a description of how the parameter settings are defined in the
DeviceNet-Manager.
•
Execute the function WHO in the DeviceNet-Manager.
This will open a network window that includes your coupler.
•
Double-click the icon of the bus coupler where you want to modify the parameter data.
HB97E - IM - RE_253-1DN00 - Rev. 12/44 3-7
Chapter 3 Deployment
Parameter
Manual VIPA System 200V
The parameters are read from the coupler and displayed in the following window:
•
Locate an unused group in the list of parameters (Value=0000 0000)
You may display all 8 groups in the parameter list by choosing "All
Parameters" in the selection field Parameter Group.
•
Double click the "Len"-parameter
The following dialog box is displayed:
3-8
•
Enter the number of parameter bytes (bit coded) of the module that you are configuring. You can obtain the number from the documentation for the peripheral module. Set or reset the respective bits by clicking the checkbox.
•
Click [OK] to close the mask. The next parameter (slot) of the same group is displayed when you click the button [Next>>].
•
Now you have to enter the plug-in location number of the module you are configuring as a bit-code in the same manner.
You can retrieve the input range by means of the button [Param Help].
HB97E - IM - RE_253-1DN00 - Rev. 12/44
Manual VIPA System 200V
Chapter 3 Deployment
•
At this point you can enter the parameter bytes for your module one after the other by clicking [Next >>].
•
If you wish to configure other modules you have to select another unused group and proceed in the same manner.
•
When you have entered all parameters into the different groups you transfer and save the parameters in the DeviceNet coupler by clicking the [Save to Device] button.
The following selection window is opened:
Here you may decide whether you want to transfer all the parameters or only the parameters that were modified.
•
During the transfer the status text "Status: downloading" is displayed.
When the transfer has completed, the status text changes to "Status:
Device Values"
•
If you were to request the "Device Details", you may see that the bit
CONFIGURED is now also included in the status.
When you have entered the parameter values and downloaded them into the DeviceNet coupler, the peripheral modules connected via the backplane bus have been configured accordingly.
HB97E - IM - RE_253-1DN00 - Rev. 12/44 3-9
Chapter 3 Deployment
Example
Manual VIPA System 200V
The following example is intended to show the configuration of the System
200V. Let us assume that the system has the following structure:
DN-
Slave
DI 8 DI 8 DI 8 DO 8 DO 8 DO 8 DO 8 DO 8 DO 8 AI 8
Param.
10 Byte
IM253DN SM221 SM221 SM221 SM221 SM221 SM221 SM221 SM221 SM231 SM231
Slot 0 Slot 1 Slot 2 Slot 3 Slot 4 Slot 5 Slot 6 Slot 7 Slot 8 Slot 9 Slot 10
The example shows a DeviceNet coupler with 10 modules; however, the modules installed in plug-in locations 1 to 9 can not be configured.
Below follows the description of the configuration of the analog-module in location 10:
Precondition: - the hardware was assembled and is active on the bus.
- the Allen - Bradley DeviceNet-Manager was installed.
•
Execute the function WHO in the DeviceNet-Manager and open the parameter window by double-clicking the DeviceNet coupler.
•
Locate an unused group in the parameter list (Value=0000 0000)
•
Double-click the "Len"-parameter.
3-10
The analog module has 10Byte of parameter data. Enter this value as a bit-coded value.
•
Click [Next>>] and enter the location 10 as the "slot".
•
You may now enter the parameter bytes of your module by clicking
[Next >>] repeatedly.
HB97E - IM - RE_253-1DN00 - Rev. 12/44
Manual VIPA System 200V
Parameter
Chapter 3 Deployment
The analog input module has the following parameters:
Byte Bit 7 ... Bit 0
0 Diagnostic alarm byte:
Bit 5 ... 0: reserved
Bit 6: 0: Diagnostic alarm inhibited
1: Diagnostic alarm enabled
Bit 7: reserved
Default
00h
1 reserved
2 Function no. channel 0 (see module description)
3 Function no. channel 1 (see module description)
4 Function no. channel 2 (see module description)
5 Function no. channel 3 (see module description)
6 Option byte channel 0
7 Option byte channel 1
8 Option byte channel 2
9 Option-byte channel 3
00h
2Dh
2Dh
2Dh
2Dh
00h
00h
00h
00h
•
When all parameters have been entered into the group you transfer and save the parameters in the DeviceNet coupler by means of
[Save to Device].
•
During the transfer the status text is displayed as "Status: downloading".
When the transfer has been completed the status text changes to
"Status: Device Values".
Note!
Parameters may be changed at any time. For this purpose you have to click
[Load from Device], then enter the required changes and save them by means of [Save to Device].
HB97E - IM - RE_253-1DN00 - Rev. 12/44 3-11
Chapter 3 Deployment Manual VIPA System 200V
I/O addressing of the DeviceNet scanner
DeviceNet scanner configuration
The DeviceNet coupler determines the modules installed on the backplane bus automatically and uses the result to generate the number of input and output bytes.
You have to determine these two values when you configure the input/output modules and enter them in the DeviceNet scanner (master):
• produced connection size (number of input bytes)
• consumed connection size (number of output bytes)
The addressing results from the sequence of the modules (plug-in location
1 ... 32) and the base address that was defined in the DeviceNet scanner for the bus coupler.
•
Set the DeviceNet scanner to connection type POLL IO.
•
Define the parameters:
"Receive data size" = number of input bytes
"Transmit data size" = number of output bytes
•
Define the base address (mapping) of receive data and transmit data as required.
•
Activate the DeviceNet coupler IM 253DN in the scan list.
•
Start the DeviceNet scanner.
When the DeviceNet scanners have been configured, the input and output modules are accessible via the defined addresses.
Example
The following 6 modules have been installed into the backplane bus:
Plug-in location
Slot 0
Slot 1
Slot 2
Slot 3
Slot 4
Installed modules
DeviceNet coupler
Digital Out SM 222
Digital Out SM 222
Input data
-
Output data
-
1Byte
1Byte
Slot 5
Total:
Digital In SM 221 1Byte
Analog In SM 231 4Words
Analog Out SM 232
1+4*2=9Byte
4Words
1+1+4*2=10Byte
The result is:
• produced connection size: 9Byte (sum of input bytes)
• consumed connection size: 10Byte (sum of output bytes)
3-12 HB97E - IM - RE_253-1DN00 - Rev. 12/44
Manual VIPA System 200V
Chapter 3 Deployment
Diagnostics
Overview
The LEDs installed to display the status allow extensive diagnostics during the PowerON-procedure as well as during operation. The result of the diagnosis is determined by the combination of the different LEDs and the current operating mode.
Explanation:
LED Description
off
on
LED turned off
LED is permanently on
blinks LED blinks
The following operating modes are available depending on the position of the address selector:
•
DeviceNet mode (address selector in position 0 ... 63)
•
Configuration mode (address selector in position 90 ... 92)
DeviceNet mode
PowerON without
DeviceNet
LED Description
PW on
ER off
After PowerON the PW-LED is turned on and indicates a properly operating power supply. The RD-
RD blinks LED blinks since the configuration data, stored in the
BA off EEPROM, was transferred successfully into the
PW on peripheral modules.
After PowerON the PW-LED is turned on. The ER-
ER on
RD off
BA off
LED is on due to errors on the backplane bus or when the configuration data could not be transferred into the peripheral modules.
HB97E - IM - RE_253-1DN00 - Rev. 12/44 3-13
Chapter 3 Deployment Manual VIPA System 200V
PowerON with
DeviceNet without master
LED Description
PW on After PowerON the PW-LED is turned on.
ER off The RD-LED blinks because:
RD blinks
• the backplane bus is operating properly
BA blinks
• the configuration data was transferred successfully
from the EEPROM into the configurable peripheral modules.
PW on
The BA-LED blinks because:
• at least one additional device is active on the
DeviceNet,
• and the address set up on the coupler is unique.
After PowerON the PW-LED is turned on. The ER-
ER on LED is on due to one of the following conditions on the
RD off
BA off
PW on
ER on
• bad address or address occupied by another device
• data transfer rate is bad.
After PowerON the PW-LED is on.
The ER-LED is turned on when the configuration data
RD blinks could not be transferred into the configurable
BA blinks peripheral module.
The RD-LED blinks because
• the backplane bus is operating properly
• the configuration data was not transferred into the configurable peripheral modules.
The BA-LED blinks because
• at least one other device is active on the DeviceNet,
• the address set up on the coupler is unique.
3-14 HB97E - IM - RE_253-1DN00 - Rev. 12/44
Manual VIPA System 200V
Chapter 3 Deployment
PowerON with
DeviceNet and master
LED Description
PW on
ER on
After PowerON the PW-LED is on.
The ER-LED is turned on since the configuration data
RD blinks was not transferred into the configurable peripheral
BA on modules.
The RD-LED blinks because
• the backplane bus operates properly
• the configuration data was not transferred into the configurable peripheral modules.
The BA-LED is turned on
• because the coupler IM 253DN has established a
DeviceNet-connection to a master.
Note!
The IM 253DN coupler executes a reset after 30s.
An error that occurs during PowerON with DeviceNet and master displays the same combination of LEDs as a hardware error.
It is possible to distinguish between these cases:
• by interruption of the DeviceNet connection
→
ER-LED and RD are blinking!
• with a network WHO in the DeviceNet-Manager
→
in case of a hardware error the IM253DN
will not appear on the network.
Note!
Please call the VIPA hotline if a hardware error occurs!
Proper operation with DeviceNet and master
LED
PW on
ER off
RD on
BA on
Description
After PowerON the PW-LED is on. The RD-LED is turned on because the connection to the peripheral modules could be established via the backplane bus.
The BA-LED is turned on because the coupler
IM 253DN established a DeviceNet connection with a master.
HB97E - IM - RE_253-1DN00 - Rev. 12/44 3-15
Chapter 3 Deployment Manual VIPA System 200V
Errors during the operation with
DeviceNet and master
LED
PW on
ER on
RD off
BA on
Description
After PowerON the PW-LED is on.
The ER-LED is turned on because an error was detected on the backplane bus.
The BA-LED is turned on because the IM 253DN coupler established a DeviceNet connection with
Note!
The IM 253DN coupler will execute a reset after 30s.
Change of state from operational to module error status
LED
PW on
ER on
RD off
BA off
Description
The ER-LED is turned on for 1 second because a module error was detected. Subsequently the coupler
IM 253DN will execute a reset. After the reset the coupler is re-started and it indicates the error by means of the respective LED combination.
Indicators after a re-start and a reset
LED
PW on
Description
The ER-LED is turned on permanently and the RD-LED
ER on blinks because the quantity of I/O data was changed by
RD blinks the failure of the module. The configuration data could
BA on not be transferred.
All Allen - Bradley scanners will display message #77.
PW on
ER off
RD on
BA on
The ER-LED is not turned on and the RD-LED is permanently on because the quantity of I/O data was modified by the failure of the module. The connection with the I/O modules was established.
All Allen - Bradley scanners will display message #77.
3-16 HB97E - IM - RE_253-1DN00 - Rev. 12/44
Manual VIPA System 200V
Chapter 3 Deployment
Change of state from operational to connection error status
Configuration mode
PowerON in configuration mode
Device error
LED Description
PW on The ER-LED blinks because the timer of the
ER blinks I/O connection detected an error. The RD-LED blinks
RD blinks because the I/O-connection does not exist any
BA on longer. All inputs and outputs are set to zero.
The BA-LED is turned on because the connection with the master is still established.
LED
PW on
ER off
RD on
BA off
Description
After PowerON the PW-LED is turned on and indicates that the power supply operates properly.
The RD-LED is turned on after a short delay since the baudrate was transferred into the EEPROM.
LED
PW on
ER on
RD off
BA off
PW on
ER on
Description
The address that was set up on the coupler is not valid.
Change the address to a valid setting:
•
0 ... 63 as DeviceNet address
•
90 ... 92 for the definition of the baudrate
When the coupler is not connected to the DeviceNet, an error was detected in the internal EEPROM or in
RD on
BA on
RAM. When a DeviceNet connection exists, it is also possible that an error has occurred during the transfer of the configuration data into the peripheral modules.
Note!
Errors that occur during PowerON with DeviceNet and master display the same combination of LEDs as a hardware error.
It is possible to distinguish between these cases:
• by interruption of the DeviceNet connection
→
ER-LED and RD are blinking!
• with a network WHO in the DeviceNet-Manager
→
in case of a hardware error the IM 253DN
will not appear on the network.
Please call the VIPA hotline if a hardware error occurs!
HB97E - IM - RE_253-1DN00 - Rev. 12/44 3-17
Chapter 3 Deployment Manual VIPA System 200V
3-18 HB97E - IM - RE_253-1DN00 - Rev. 12/44
advertisement
* Your assessment is very important for improving the workof artificial intelligence, which forms the content of this project
Related manuals
advertisement
Table of contents
- 3 Contents
- 5 About this manual
- 7 Safety information
- 10 Safety Information for Users
- 11 System conception
- 13 Dimensions
- 15 Installation
- 19 Demounting and module exchange
- 20 Wiring
- 22 Installation guidelines
- 25 General data
- 28 Properties
- 29 Structure
- 31 Technical data
- 34 Basics DeviceNet
- 36 Configuration by means of the DeviceNet-Manager
- 37 Specifying baudrate and DeviceNet address
- 38 Test in conjunction with the DeviceNet
- 39 Module configuration in the DeviceNet-Manager
- 44 I/ O addressing of the DeviceNet scanner
- 45 Diagnostics