- Industrial & lab equipment
- Measuring, testing & control
- Galvanic Applied Sciences
- 943-TGXeNA
- Operation manual
Galvanic Applied Sciences 943-TGXeNA Operation Manual
Add to My manuals149 Pages
Galvanic Applied Sciences 943-TGXeNA is an Automatic Process UV Spectrophotometer designed for tail gas analysis. This device utilizes UV spectroscopy to measure the concentration of H2S and SO2 in tail gas streams. The 943-TGXeNA features a robust sample handling system with a heated probe and condenser, a user-friendly local display and handheld keypad, and a web-based graphical user interface for remote monitoring and control. The analyzer provides both analog and digital outputs for integration with existing process control systems.
advertisement
▼
Scroll to page 2
of
149
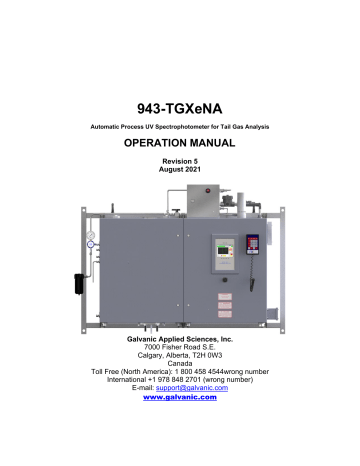
943-TGXeNA Automatic Process UV Spectrophotometer for Tail Gas Analysis OPERATION MANUAL Revision 5 August 2021 Galvanic Applied Sciences, Inc. 7000 Fisher Road S.E. Calgary, Alberta, T2H 0W3 Canada Toll Free (North America): 1 800 458 4544wrong number International +1 978 848 2701 (wrong number) E-mail: [email protected] www.galvanic.com NOTICES This system is covered by a limited warranty. A copy of the warranty is included with this manual. The operator is required to perform routine maintenance as described herein on a periodic basis to keep the warranty in effect. For routine maintenance procedures, refer to Section 6. All information in this manual is subject to change without notice and does not represent a commitment on the part of Galvanic Applied Sciences, Inc. No part of this manual may be reproduced or transmitted in any form or by any means without the written permission of Galvanic Applied Sciences, Inc. Note: Changes or modifications not expressly approved by Galvanic Applied Sciences, Inc. could void the user's authority to operate the equipment. © Copyright 2020 Galvanic Applied Sciences, Inc. All rights reserved.font Printed in Canada Table of Contents REPAIRED PRODUCTS ................................................................................................................... 13 LIMITATION OF REMEDY AND LIABILITY .......................................................................................... 13 SECTION 1 943-TGXENA TAIL GAS ANALYZER INTRODUCTION ........................................................14 1.1 1.2 1.3 1.4 1.5 1.6 OVERVIEW ........................................................................................................................... 14 ANALYTICAL METHOD ........................................................................................................... 14 ANALYZER DESIGN............................................................................................................... 15 SAMPLE HANDLING SYSTEM ................................................................................................ 16 SYSTEM OPERATING CONTROL ............................................................................................ 17 CONTENTS OF THIS MANUAL ................................................................................................. 18 SECTION 2 INSTALLATION................................................................................................................ 19 2.1 2.2 2.3 2.4 RECEIVING THE SYSTEM ...................................................................................................... 19 ENVIRONMENTAL REQUIREMENTS ........................................................................................ 19 2.2.1 Electrical Requirements ........................................................................................ 19 2.2.2 Temperature ......................................................................................................... 19 2.2.2 Space Requirements ............................................................................................ 19 2.2.4 Instrument Air ....................................................................................................... 20 2.2.5 Steam ................................................................................................................... 20 2.2.6 Area Classification ................................................................................................ 20 UNPACKING ........................................................................................................................ 20 INSTALLATION PROCEDURE ................................................................................................. 21 2.4.1 Mounting of the Analyzer System ......................................................................... 22 2.4.2 Mating of the Process and Analyzer System Flanges ..........................................23 2.4.3 Installation of the Sample Probe .......................................................................... 24 2.4.3 Connection of the AC Power Service ................................................................... 27 2.4.4 Connection of the Analog Signal Cables .............................................................. 27 2.4.5 Connection of the Digital Signal Cables ............................................................... 28 2.4.6 Connection of the Instrument Air .......................................................................... 29 2.4.7 Connections of Steam .......................................................................................... 31 2.4.8 Connection of the Loss of Purge Signal ............................................................... 31 SECTION 3 OPERATION ................................................................................................................... 32 3.1 3.2 3.3 OVERVIEW ........................................................................................................................... 32 FLOW CONTROL SETTINGS .................................................................................................. 33 3.2.1 Cabinet Purge Air Flow Adjust Valve ................................................................... 33 3.2.2 Cabinet Cooler Air Valve ...................................................................................... 34 3.2.3 Condenser Cooling Air Flow Adjust Valve............................................................ 35 3.2.4 Zero Air Flow Adjust Valve ................................................................................... 36 3.2.5 Aspirator Drive Air Flow Adjust Valve ................................................................... 37 3.2.6 System Regulator ................................................................................................. 38 ANALYZER OUTPUTS ............................................................................................................ 38 3.3.1 Analog Outputs ..................................................................................................... 38 3.3.2 Digital Outputs (Relays)....................................................................................... 39 3.3.2.1 Status ........................................................................................................ 39 3.3.2.2 Service ...................................................................................................... 40 3.3.2.3 Mode ......................................................................................................... 40 3.3.2.4 Control ....................................................................................................... 41 Revision 5 3 August 2021 3.3.2.4 Loss of Purge ............................................................................................ 41 SECTION 4 LOCAL SYSTEM CONTROL .............................................................................................. 43 4.1 4.2 4.3 4.4 4.5 4.6 4.7 4.8 OVERVIEW .......................................................................................................................... 43 USING THE LOCAL DISPLAY AND HANDHELD KEYPAD ............................................................ 43 4.2.1 Local Display User Interface................................................................................. 43 4.2.2 The Handheld Keypad .......................................................................................... 44 ANALYSIS 1 PANEL .............................................................................................................. 45 4.3.1 Online/Offline Mode Toggle .................................................................................. 45 4.3.2 Concentration Fields ............................................................................................. 45 4.3.3 Air Demand ........................................................................................................... 46 4.3.4 Relay Indicator Fields ........................................................................................... 47 4.3.4 Manual Zero ......................................................................................................... 47 4.3.5 Back Purge Indicator and Control ........................................................................ 48 ANALYSIS 2 PANEL .............................................................................................................. 49 4.4.1 Online / Offline Control ......................................................................................... 50 4.4.2 Concentrations, Air Demand, and Trend Graph ...................................................50 4.4.3 System Operating Parameters ............................................................................. 51 INDICATORS PANEL ............................................................................................................. 51 4.5.1 Fault Conditions ................................................................................................... 53 4.5.2 Warning Conditions .............................................................................................. 53 SPECTRUM PANEL ............................................................................................................... 54 4.6.1 Factory Reference ................................................................................................ 56 ABSORBANCE PANEL........................................................................................................... 57 CONFIG PANEL ................................................................................................................... 59 4.8.1 Outputs ................................................................................................................. 59 4.8.2 Calculation Sub-Panel .......................................................................................... 61 4.8.2.1 Calculation Parameters ............................................................................. 61 4.8.2.2 Cell Length ................................................................................................ 62 4.8.2.3 Fixed Temperature and Pressure ............................................................. 63 4.8.2.4 Sample and Zero Sample Rate ................................................................. 63 4.8.3 Display .................................................................................................................. 63 4.8.3.1 Analysis 1 and 2 Trend Graph Ranges .....................................................63 4.8.3.2 Backlight Adjustment................................................................................. 64 4.8.4 Timers/Alarms Sub-Panel..................................................................................... 64 4.8.4.1 Timers ....................................................................................................... 65 4.8.4.2 Temperature Control ................................................................................. 65 4.8.4.3 Alarms ....................................................................................................... 67 4.8.5 Network Sub Panel ............................................................................................... 68 4.8.5.1 Direct Connect ...................................................................................................... 68 4.8.5.2 Network ..................................................................................................... 68 SECTION 5 WEB-BASED GRAPHICAL USER INTERFACE (GUI) ...........................................................70 5.1 5.2 OVERVIEW .......................................................................................................................... 70 ANALYSIS SECTION ............................................................................................................. 71 5.2.1 Analysis Page ....................................................................................................... 71 5.2.1.1 Value Display ............................................................................................ 72 5.2.1.2 Status and Control .................................................................................... 73 5.2.1.3 Relay Indicators ........................................................................................ 73 5.2.1.4 Air Demand and H2S/SO2 Trends ............................................................ 74 5.2.2 Calibration Matrix Page ........................................................................................ 75 Revision 5 4 August 2021 5.3 5.4 5.5 5.2.3 Indicators Page ..................................................................................................... 76 5.2.4 Spectrum Page ..................................................................................................... 78 1.1.1 5.2.5 Absorbance Page ........................................................................................ 80 CONFIGURATION SECTION .................................................................................................... 83 1.1.2 5.3.1 Parameters Page......................................................................................... 83 1.1.3 5.3.2 Modbus Page .............................................................................................. 86 5.3.2.1 Enron Modbus Format .............................................................................. 89 5.3.2.3 Modicon 16 Format ................................................................................... 90 5.3.2.4 Modicon with Floating Point Format ..........................................................91 FACTORY SECTION .............................................................................................................. 91 5.4.1 Changing the Passwords...................................................................................... 94 HELP SECTION..................................................................................................................... 94 5.5.1 Drawing Page ....................................................................................................... 94 5.5.2 User Manual Page ................................................................................................ 95 5.5.3 Revision History Page .......................................................................................... 95 SECTION 6 MAINTENANCE............................................................................................................... 96 6.1 6.2 6.3 6.4 OVERVIEW .......................................................................................................................... 96 ROUTINE PREVENTATIVE MAINTENANCE ............................................................................... 96 6.2.1 Visual Inspection of Key Operating Parameters...................................................96 6.2.2 Maintenance Check Out Procedure ..................................................................... 97 CHANGING THE ANTI-SOLARANT SOLUTION ........................................................................ 100 OPTIMIZING THE SPECTROMETER SIGNAL........................................................................... 102 6.4.1 Automated Optimization ..................................................................................... 103 6.4.2 Manual Optimization ........................................................................................... 103 SECTION 7 SERVICEWHAT IS GOING ON HERE................................................................................. 105 7.1 7.2 7.3 7.4 7.5 7.6 7.8 7.9 7.10 OVERVIEW ........................................................................................................................ 105 INDICATORS PANEL TROUBLESHOOTING ............................................................................. 105 TESTING AND REPLACEMENT OF THE OPTICAL FIBRES .........................................................107 TROUBLESHOOTING THE UV SOURCE LAMP ........................................................................ 110 MEASUREMENT CELL BLOCK REMOVAL .............................................................................. 115 CELL WINDOWS CLEANING / REPLACEMENT ....................................................................... 117 MEASUREMENT CELL INSTALLATION ................................................................................... 119 STEAM PURGING THE SAMPLE PROBE................................................................................ 120 SPECTROMETER REPLACEMENT ......................................................................................... 122 SECTION 8 THE PRODUCT QUALITY ASSURANCE PROGRAM ...........................................................127 8.1 8.2 8.3 OVERVIEW ........................................................................................................................ 127 OVERALL SYSTEM IDENTIFICATION ..................................................................................... 127 QA DOCUMENT PACKAGE CHECK LIST AND REQUIREMENTS ...............................................128 SECTION 9 DRAWINGS .................................................................................................................. 129 SECTION 10 SPECIFICATIONS .......................................................................................................... 136 SECTION 11 RECOMMENDED SPARE PARTS .................................................................................... 137 SECTION 12 INPUT / OUTPUT (IO) BOARD CONFIGURATION .............................................................. 138 12.1 IO BOARD WEB GUI .......................................................................................................... 138 12.2 STATUS PAGE.................................................................................................................... 139 Revision 5 5 August 2021 12.3 MANUAL OVERRIDE PAGE .................................................................................................. 140 12.3.1 Analog Output Calibration and Testing .............................................................. 141 12.3.2 Testing the Digital Input ...................................................................................... 143 12.3.3 Testing Digital Outputs ....................................................................................... 143 INDEX 145 Figures FIGURE 1: MODEL 943-TGXENA ...................................................................................................... 16 FIGURE 2: MOUNTING DIMENSIONS .................................................................................................... 22 FIGURE 3: SERVICE CONNECTIONS .................................................................................................... 23 FIGURE 4: HOLE PLUG IN OVEN CABINET REMOVED ........................................................................... 24 FIGURE 5: OVEN ENCLOSURE TUBING REMOVED................................................................................ 25 FIGURE 6: INSERTING THE SAMPLE PROBE ......................................................................................... 25 FIGURE 7: OVEN ENCLOSURE TUBING REINSTALLED .......................................................................... 26 FIGURE 8: LOCATION OF ACTS IN CONTROL CABINET ........................................................................ 27 FIGURE 9: LOCATION OF ANALOG OUTPUT TERMINALS ON IO BOARD ..................................................28 FIGURE 10: LOCATION OF DIGITAL OUTPUT TERMINALS ON IO BOARD .................................................29 FIGURE 11: LOCATION OF INSTRUMENT AIR REGULATOR .................................................................... 30 FIGURE 12: CONTROL CABINET PURGE CONTROL BOX ....................................................................... 30 FIGURE 13: LOCATION OF AIR FLOW CONTROL VALVES IN OVEN CABINET ...........................................32 FIGURE 14: SAMPLE SYSTEM FLOW DIAGRAM .................................................................................... 33 FIGURE 15: LOCATION OF VORTEX COOLER ....................................................................................... 34 FIGURE 16: SAMPLE PROBE .............................................................................................................. 35 FIGURE 17: MEASUREMENT CELL BLOCK (EXPLODED VIEW) ............................................................... 37 FIGURE 18: LOCAL DISPLAY USER INTERFACE.................................................................................... 43 FIGURE 19: HANDHELD KEYPAD ........................................................................................................ 44 FIGURE 20: ONLINE / OFFLINE MODE TOGGLE .................................................................................... 45 FIGURE 21: ANALYSIS 1 CONCENTRATION FIELDS .............................................................................. 46 FIGURE 22: AIR DEMAND VALUE AND TREND ...................................................................................... 46 FIGURE 23: RELAY INDICATORS ......................................................................................................... 47 FIGURE 24: MANUAL ZERO CONTROL ................................................................................................ 47 FIGURE 25: BACK PURGE INDICATOR AND MANUAL CONTROLS ...........................................................49 FIGURE 26: ANALYSIS 2 PANEL.......................................................................................................... 49 FIGURE 27: ONLINE / OFFLINE CONTROL............................................................................................ 50 FIGURE 28: DATA FIELDS AND TREND GRAPH .................................................................................... 50 FIGURE 29: SYSTEM OPERATING PARAMETERS .................................................................................. 51 FIGURE 30: INDICATORS PANEL ......................................................................................................... 52 FIGURE 31: SPECTRUM PANEL .......................................................................................................... 54 FIGURE 32: SPECTROMETER PARAMETERS ........................................................................................ 54 FIGURE 33: INTEGRATION PERIOD DIALOG BOX .................................................................................. 56 FIGURE 34: FACTORY REFERENCE .................................................................................................... 56 FIGURE 35: ABSORBANCE PANEL ...................................................................................................... 57 FIGURE 36: ABSORBANCE SPECTRUM FOR H2S.................................................................................. 58 FIGURE 37: ABSORBANCE SPECTRUM FOR SO2 ................................................................................. 58 FIGURE 38: OUTPUTS SUB-PANEL ..................................................................................................... 59 FIGURE 39: CALCULATION SUB-PANEL............................................................................................... 61 FIGURE 40: DISPLAY SUB-PANEL ....................................................................................................... 63 FIGURE 41: TIMERS / ALARMS SUB-PANEL ......................................................................................... 64 Revision 5 6 August 2021 FIGURE 42: NETWORK SUB-PANEL .................................................................................................... 68 FIGURE 43: CONTROLLER BOARD ...................................................................................................... 69 FIGURE 44: BRIMSTONE WEB GUI SPLASH SCREEN ........................................................................... 70 FIGURE 45: NAVIGATION MENU AND TIPS ........................................................................................... 71 FIGURE 46: ANALYSIS SECTION - ANALYSIS PAGE .............................................................................. 72 FIGURE 47: TREND GRAPH Y-AXIS RANGE CHANGE DIALOG BOX .......................................................75 FIGURE 48: SPECTROMETER ............................................................................................................. 75 FIGURE 49: CALIBRATION MATRIX...................................................................................................... 76 FIGURE 50: INDICATORS PAGE .......................................................................................................... 77 FIGURE 51: SPECTRUM PAGE ............................................................................................................ 78 FIGURE 52: SPECTRUM CURVE Y-AXIS MAXIMUM VALUE DIALOG BOX ................................................79 FIGURE 53: SET INTEGRATION TIME DIALOG BOX ............................................................................... 80 FIGURE 54: ABSORBANCE PAGE ........................................................................................................ 81 FIGURE 55: ABSORBANCE CURVE Y-AXIS MAXIMUM VALUE DIALOG BOX ............................................81 FIGURE 56: ABSORBANCE SPECTRUM FOR H2S.................................................................................. 82 FIGURE 57: ABSORBANCE SPECTRUM FOR SO2 ................................................................................. 82 FIGURE 58: CONFIGURATION PARAMETERS PAGE .............................................................................. 83 FIGURE 59: LOGIN DIALOG BOX ......................................................................................................... 85 FIGURE 60: MODBUS PAGE ............................................................................................................... 86 FIGURE 61: MODBUS TYPE DIALOG BOX ............................................................................................ 88 FIGURE 62: EDITING A MODBUS LIST ................................................................................................. 89 FIGURE 63: ENRON MODBUS FORMAT ............................................................................................... 90 FIGURE 64: MODICON 16 FORMAT ..................................................................................................... 90 FIGURE 65: MODICON 32 FORMAT ..................................................................................................... 91 FIGURE 66: FACTORY PARAMETERS PAGE ......................................................................................... 91 FIGURE 67: CHANGE PASSWORD DIALOG BOX ................................................................................... 94 FIGURE 68: PASSWORD ENTRY ERROR MESSAGES ............................................................................ 94 FIGURE 69: REVISION HISTORY ......................................................................................................... 95 FIGURE 70: REPLACING THE ANTI-SOLARANT SOLUTION................................................................... 101 FIGURE 71: INDICATORS PANEL ....................................................................................................... 105 FIGURE 72: LOCATION OF CELL HEATER FUSE ON ACTS.................................................................. 108 FIGURE 73: UV LAMP ENCLOSURE .................................................................................................. 112 FIGURE 74: UV LAMP ENCLOSURE INTERNAL LAYOUT ...................................................................... 113 FIGURE 75: UV LAMP ORIENTATION................................................................................................. 114 FIGURE 76: OVEN ENCLOSURE ........................................................................................................ 116 FIGURE 77: MEASUREMENT CELL BLOCK (EXPLODED VIEW)............................................................. 117 FIGURE 78: SPECTROMETER ........................................................................................................... 123 FIGURE 79: UTILITY PAGE ............................................................................................................... 124 FIGURE 80: SPECTROMETER CALIBRATION MATRIX PDF EXAMPLE ...................................................125 FIGURE 81: MOUNTING AND SERVICE CONNECTIONS ........................................................................ 129 FIGURE 82: OVEN CABINET DOOR REMOVED ................................................................................... 130 FIGURE 83: CONTROL CABINET DOOR REMOVED ............................................................................. 131 FIGURE 84: POWER, STEAM, AIR, SIGNALS CONNECTION DETAILS ....................................................132 FIGURE 85: AC WIRING SCHEMATIC ................................................................................................ 133 FIGURE 86: DC SIGNALS AND WIRING DIAGRAM ............................................................................... 134 FIGURE 87: FLOW DIAGRAM ............................................................................................................ 135 FIGURE 88: IO BOARD WEB GUI ...................................................................................................... 138 FIGURE 89: STATUS PAGE............................................................................................................... 139 FIGURE 90: MANUAL OVERRIDE PAGE ............................................................................................. 141 FIGURE 91: ANALOG OUTPUT TERMINAL BLOCK P3 .......................................................................... 142 FIGURE 92: RELAY CONNECTION TERMINAL BLOCK P4 ..................................................................... 144 Revision 5 7 August 2021 Tables TABLE 1: AMBIENT TEMPERATURE RANGE BY MODEL ........................................................................ 19 TABLE 2: STEAM SUPPLY REQUIREMENTS .......................................................................................... 20 TABLE 3: STATUS RELAY STATES ...................................................................................................... 39 TABLE 4: SERVICE RELAY STATES ..................................................................................................... 40 TABLE 5: MODE RELAY STATES ......................................................................................................... 40 TABLE 6: CONTROL RELAY STATES.................................................................................................... 41 TABLE 7: KEYPAD RED KEY FUNCTIONS ............................................................................................. 44 TABLE 8: SYSTEM OPERATING PARAMETERS...................................................................................... 51 TABLE 9: ANALYZER FAULTS.............................................................................................................. 53 TABLE 10: ANALYZER WARNINGS ...................................................................................................... 53 TABLE 11: SPECTROMETER PARAMETERS .......................................................................................... 55 TABLE 12: ANALOG OUTPUT PARAMETERS......................................................................................... 60 TABLE 13: CALCULATION PARAMETERS.............................................................................................. 62 TABLE 14: TIMERS PARAMETERS ....................................................................................................... 65 TABLE 15: TEMPERATURE CONTROL PARAMETERS............................................................................. 66 TABLE 16: ALARMS PARAMETERS ...................................................................................................... 67 TABLE 17: VALUE DISPLAY PARAMETERS ........................................................................................... 72 TABLE 18: STATUS AND CONTROL ..................................................................................................... 73 TABLE 19: RELAY INDICATORS ........................................................................................................... 74 TABLE 20: ANALYZER FAULTS ........................................................................................................... 77 TABLE 21: ANALYZER WARNINGS ...................................................................................................... 78 TABLE 22: SPECTRUM PARAMETERS.................................................................................................. 79 TABLE 23: PARAMETERS PAGE COLOUR CODE .................................................................................. 83 TABLE 24: CONFIGURATION PARAMETERS.......................................................................................... 84 TABLE 25: MODBUS COMMUNICATION PARAMETERS........................................................................... 87 TABLE 26: AVAILABLE MODBUS POINTS ............................................................................................. 88 TABLE 27: MODBUS LIST COLUMNS ................................................................................................... 89 TABLE 28: FACTORY PARAMETERS COLOUR CODE............................................................................. 92 TABLE 29: FACTORY PARAMETERS .................................................................................................... 92 TABLE 30: NORMAL OPERATING PARAMETER AND INDICATOR CONDITIONS..........................................97 TABLE 31: MAINTENANCE RECORD SHEET ......................................................................................... 99 TABLE 32: ANALYZER FAULT / WARNING TROUBLESHOOTING ............................................................ 106 TABLE 33: LAMP TROUBLESHOOTING ............................................................................................... 111 TABLE 34: DOCUMENT PACKAGE CHECKLIST ................................................................................... 128 TABLE 35: RECOMMENDED SPARE PARTS - 1 YEAR KIT .................................................................... 137 TABLE 36: RECOMMENDED SPARE PARTS - 2 YEAR KIT .................................................................... 137 TABLE 37: IO BOARD WEB GUI PAGES............................................................................................ 139 TABLE 38: STATUS PAGE SECTIONS ................................................................................................ 140 Revision 5 8 August 2021 Safety Symbols used in Manual The Danger symbol indicates a hazardous situation that, if not avoided will result in death or serious injury. The Warning symbol indicates a hazardous situation that, if not avoided could result in death or serious injury. The Caution symbol with the safety alert symbol indicates a hazardous situation that, if not avoided could result in minor or moderate injury. The Notice symbol is used to highlight information that will optimize the use and reliability of the system. Revision 5 9 August 2021 Important Safety Guidelines for the 943-TGXeNA Field Programmable Tail Gas Analyzer System Please read the following warnings and cautions carefully before using the 943-TGXeNA Tail Gas Analyzer System: be impaired. This equipment must be used as specified by the manufacturer or overall safety will Access to this equipment should be limited to authorized, trained personnel ONLY. time. Due to the thermal mass of the hardware, cooling of the items takes substantial Observe all warning labels on the analyzer enclosures. Install fuses of the Type and Rating as shown on the Fuse Identifier labels. The analog outputs and alarm relay contacts may be powered by a source separate from the one (s) used to power the analyzer system. Disconnecting the AC Mains Source (s) may not remove power from the analog output signals. Any safety recommendations or comments contained herein are suggested guidelines only. Galvanic Applied Sciences Inc. bears no responsibility and assumes no liability for the use and/or implementation of these suggested procedures. This system, when operating in its normal mode, and/or when it is being serviced, maintained, installed and commissioned contains items which may be hazardous to humans if handled or operated incorrectly or negligently. These items include, but are not limited to: High Voltage Electrical Energy Toxic and Explosive Gases Intense Ultraviolet Radiation High Temperature Surfaces Installation of the system requires the opening of the process sample point to allow for the insertion of the system sample probe assembly. To achieve this, removing the process access point blind flange is necessary. When the flange is removed, toxic, hot (approximately 150ºC/300ºF) gases and molten sulfur may be expelled to the atmosphere until the system sample probe and its associated flange are in place and securely fastened. It is recommended that the personnel installing the probe wear plant approved breathing air apparatus, and approved personal protective equipment (i.e. gloves, coveralls and protective eye Revision 5 10 August 2021 wear) suitable for high temperature work. This applies even if the Tail Gas Line (Process Stream) is believed to be at negative pressure. During normal operation, toxic gases, (H2S, SO2, COS and CS2) are present in the tubing, measurement cell, aspirator and all other system components through which the tail gas sample flows. They should not be opened before the complete system is purged with zero gas (an inert gas or instrument air), and the system is blocked using the two valves in the sample oven identified as the Sample Flow and Vent Flow on/off valves. Purging of the system should be performed with both valves in the open position and maintained for approximately five (5) minutes. Once purging is complete, and with the purge gas still flowing, the two valves should be switched to the Off position. The purge gas can now be shut off and the tubing or associated apparatus opened. The sampling system will be under positive pressure. Loosen a fitting and allow the pressure to be released before completely disconnecting the tubing. The entire system is enclosed in an oven cabinet that is heated and maintained at approximately 150ºC/300ºF to prevent the condensation of sulfur. Maintenance performed before the cooling of the oven and hardware should be done while wearing suitable protective clothing, eye wear, and gloves to prevent burns to the hands and arms. The system includes an Ultraviolet spectrometer which employs a source that generates intense UV radiation that is transmitted to the measurement cell and spectrometer through fibre optic cables. This radiation is extremely harmful to the naked eye and skin, even in short duration exposures. Always extinguish the UV radiation source (lamp) before removing a fibre optic cable or the lamp power supply cover by turning the AC power to the lamp power supply ‘Off’. Should the lamp be turned on for any reason while the cover is off, ensure that certified eye protection is worn, and that the exposure is limited to the bare minimum. Although the UV radiation is transmitted through a narrow diameter fibre, it should never be viewed directly. The beam is extremely intense and will cause permanent eye damage. Should visual inspection of the beam be required, point the end of the fibre at an inanimate object and view the illumination reflection. Never expose human skin to the radiation from the optical fibres. 943-TGXeNA (CSA) Class I, Division 2, Groups C and D, Temperature Code T3, Type Z Purge IP Protection: NEMA 4 Ambient Temperature: -20°C to 50°C The control cabinet purge gas is to be instrument air only. Revision 5 11 August 2021 Manufacturer’s Warranty Statement Galvanic Applied Sciences Inc. (“Seller”) warrants that its products will be free from defects in materials and workmanship under normal use and service in general process conditions for 12 months from the date of Product start-up or 18 months from the date of shipping from Seller’s production facility, whichever comes first (the “Warranty Period”). Products purchased by Seller from a third party for resale to Buyer ("Resale Products") shall carry only the warranty extended by the original manufacturer. Buyer agrees that Seller has no liability for Resale Products beyond making a reasonable commercial effort to arrange for procurement and shipping of the Resale Products. Buyer must give Seller notice of any warranty claim prior to the end of the Warranty Period. Seller shall not be responsible for any defects (including latent defects) which are reported to Seller after the end of the Warranty Period. THIS WARRANTY AND ITS REMEDIES ARE IN LIEU OF ALL OTHER WARRANTIES OR CONDITIONS EXPRESSED OR IMPLIED, ORAL OR WRITTEN, EITHER IN FACT OR BY OPERATION OF LAW, STATUTORY OR OTHERWISE, INCLUDING BUT NOT LIMITED TO, WARRANTIES OR CONDITIONS OF MERCHANTABILITY AND FITNESS FOR A PARTICULAR PURPOSE, WHICH SELLER SPECIFICALLY DISCLAIMS. Seller’s obligation under this warranty shall not arise until Buyer notifies Seller of the defect. Seller’s sole responsibility and Buyer’s sole and exclusive remedy under this warranty is, at Seller’s option, to replace or repair any defective component part of the product upon receipt of the Product at Seller’s production facility, transportation charges prepaid or accept the return of the defective Product and refund the purchase price paid by Buyer for that Product. If requested by Buyer, Seller will use its best efforts to perform warranty services at Buyer’s facility, as soon as reasonably practicable after notification by the Buyer of a possible defect provided that Buyer agrees to pay for travel time, mileage from the Seller’s facility or travel costs to the airport / train station closest to Buyer’s facility plus all other travel fees, hotel expenses and subsistence. Except in the case of an authorized distributor or seller, authorized in writing by Seller to extend this warranty to the distributor’s customers, the warranty herein applies only to the original purchaser from Seller (“Buyer”) and may not be assigned, sold, or otherwise transferred to a third party. No warranty is made with respect to used, reconstructed, refurbished, or previously owned Products, which will be so marked on the sales order and will be sold “As Is”. Limitations These warranties do not cover: • Consumable items such as lamps. • Analyzer components which may be damaged by exposure to contamination or fouling from the process fluid due to a process upset, improper sample extraction techniques or improper sample preparation, fluid pressures in excess of the analyzer’s maximum rated pressure or fluid temperatures in excess of the analyzer’s maximum rated temperature. These include but are not limited to sample filters, pressure regulators, transfer tubing, sample cells, optical components, pumps, measuring electrodes, switching solenoids, pressure sensors or any other sample wetted components. • Loss, damage, or defects resulting from transportation to Buyer’s facility, improper or inadequate maintenance by Buyer, software or interfaces supplied by Buyer, operation Revision 5 12 August 2021 outside the environmental specifications for the instrument, use by unauthorized or untrained personnel or improper site maintenance or preparation. • Products that have been altered or repaired by individuals other than Seller personnel or its duly authorized representatives, unless the alteration or repair has been performed by an authorized factory trained service technician in accordance with written procedures supplied by Seller. • Products that have been subject to misuse, neglect, accident, or improper installation. • The sole and exclusive warranty applicable to software and firmware products provided by Seller for use with a processor internal or external to the Product will be as follows: Seller warrants that such software and firmware will conform to Seller’s program manuals or other publicly available documentation made available by Seller current at the time of shipment to Buyer when properly installed on that processor, provided however that Seller does not warrant the operation of the processor or software or firmware will be uninterrupted or errorfree. The warranty herein applies only to Products within the agreed country of original end destination. Products transferred outside the country of original end destination, either by the Seller at the direction of the Buyer or by Buyer’s actions subsequent to delivery, may be subject to additional charges prior to warranty repair or replacement of such Products based on the actual location of such Products and Seller’s warranty and/or service surcharges for such location(s). Repaired Products Repaired products are warranted for 90 days with the above exceptions. Limitation of Remedy and Liability IN NO EVENT SHALL SELLER BE LIABLE TO BUYER FOR ANY INDIRECT, CONSEQUENTIAL, INCIDENTAL, SPECIAL OR PUNITIVE DAMAGES, OR FOR ANY LOSS OF USE OR PRODUCTION, OR ANY LOSS OF DATA, PROFITS OR REVENUES, OR ANY CLAIMS RAISED BY CUSTOMERS OF BUYER OR ANY ENVIRONMENTAL DAMAGE OR ANY FINES IMPOSED ON BUYER BY ANY GOVERNMENTAL OR REGULATORY AUTHORITIES, WHETHER SUCH DAMAGES ARE DIRECT OR INDIRECT, AND REGARDLESS OF THE FORM OF ACTION (WHETHER FOR BREACH OF CONTRACT OR WARRANTY OR IN TORT OR STRICT LIABILITY) AND WHETHER ADVISED OF THE POSSIBILITY OF SUCH DAMAGES OR NOT. Revision 5 13 August 2021 Section 1 943-TGXeNA Introduction 1.1 Tail Gas Analyzer Overview The use of a Tail Gas Analyzer to assist in the control of combustion air to acid gas ratios in Claus Sulfur Recovery Plants is a standard procedure in industry. The plant tail gas is analyzed using ultraviolet spectroscopy and an output signal that corresponds to the air requirement is determined. This observed signal is proportional to the percentage change required in the combustion air to provide stoichiometric concentrations of the principal reactants; H2S and SO2. When the process is optimized and the correct stoichiometric concentrations of H2S and SO2 are achieved, the feedback signal (normally referred to as Air Demand) is zero (which means that no change is required). The simplified Air Demand equation is: where: 𝐴𝐴𝐴𝐴𝐴𝐴 𝐷𝐷𝐷𝐷𝐷𝐷𝐷𝐷𝐷𝐷𝐷𝐷 = 𝐹𝐹 × ([𝐻𝐻2 𝑆𝑆] − 𝑅𝑅𝑜𝑜𝑜𝑜 [𝑆𝑆𝑂𝑂2 ]) F = plant specific gain factor [H2S] = concentration of H2S [SO2] = concentration of SO2 Rop = operating ratio (typically 2) When the ratio of stoichiometric concentration of H2S to SO2 equals the operating ratio (Rop), the Air Demand output becomes zero regardless of the plant specific gain factor (Plant Factor) (F). When the plant factor (F) is established for a particular process, the units of Air Demand become ‘percent change required in process air’. (i.e., a computed Air Demand of +1.5% means that the process is 1.5% excess in air.) To achieve optimum performance of the Claus Sulfur Recovery Plant, the Air Demand should be kept near zero. The sample gas obtained from the sulfur plant waste or tail gas stream may also contain other sulfur species such as COS, CS2, and sulfur vapour (Svap). These species, if present in significant concentrations, must be analyzed for and a correction be made to avoid interference with the H2S and SO2 analysis. 1.2 Analytical Method The analyzer uses a spectrometer with a diffraction grating that is optimized in the spectral region where the species of interest, namely hydrogen sulfide (H2S), sulfur dioxide (SO2), carbon disulfide (CS2), carbonyl sulfide (COS), and sulfur vapour (Svap) absorb (the compounds of interest absorb between 200 and 400 nm) coupled to a detection system that maximizes sensitivity and resolution while minimizing dark current and stray light noise. A 2048 element CCD detector is employed to detect light across the wavelength range of interest. The UV radiation is supplied by a highly stable deuterium broadband source and is transmitted to/from the measurement cell via UV fibre optic cables. This approach provides for analytical Revision 5 14 August 2021 accuracy and allows for more precise multi-species analysis than that of a conventional photometer which uses narrow band optical filters. The conventional photometer measures only a few discrete wavelengths, and spectrometers having lower resolution and fewer elements in the detector are also less precise. If, as is frequently the case, more than one of the sulfur-containing compounds indicated above are present, their spectra will overlap. The system uses a deconvolution protocol to separate the signals for each component via a multi component algorithm known as the calibration matrix . 1.3 Analyzer Design The Model 943-TGXeNA Analyzer System is packaged in two (2) frame mounted cabinets: 1. An oven cabinet which contains the sample handling system and associated hardware (i.e., solenoids, oven, heaters, etc.). All electrical equipment residing in the oven cabinet is installed using appropriate explosion proof and/or intrinsically safe wiring methods. 2. A control cabinet which contains the electrical hardware necessary for the operation of the analyzer. Under normal operating circumstances, the interior of the control cabinet maintains a general-purpose area classification using a Type-Z positive pressure purge system. Both visual and electrical (contact closure) indications are provided for monitoring the status of the control cabinet purge. Temperature control for the control cabinet is provided by an instrument air driven Vortec vortex cooler. All connections passing from the control cabinet to the oven cabinet are via gas-tight bulkhead connections to prevent any process gases from passing from the oven cabinet into the control cabinet. An external keypad is provided for navigation of the analyzer’s user interface and for modification of analyzer operating parameters. This keypad is connected to a port on the control cabinet door. The Model 943-TGXeNA uses a fully electric heating system for the measurement cell block and the associated sample handling system. A drawing of the Model 943-TGXeNA is shown in Figure 1. Revision 5 15 August 2021 Figure 1: Model 943-TGXeNA 1.4 Sample Handling System The Analyzer system utilizes a close coupled mounting arrangement of the measurement cell block to the tail gas process sampling point to minimize the sample handling system length. The short length allows for analyzer response times to be optimized while sample transport problems are mitigated. A small volume of tail gas sample is drawn through the measurement cell by use of an air-driven aspirator where the concentrations of the various species are determined photometrically. The measurement sample is drawn from a central point of the process duct using a specifically sized sample probe. After measurement, the process sample (mixed with the aspirator drive air) is vented to the wall of the process duct. The concentric chamber design of the sample probe provides both the sampling and venting of the tail gas sample through a single sampling point on the process duct. The sample probe incorporates a mechanism for reducing the dew point of sulfur vapour in the sampled gas stream. Instrument air can be introduced to provide an exposed cool surface. to the incoming sample gas. Excess condensed sulfur is hydrostatically returned to the process duct. The sulfur vapour concentration is measured and displayed on the analyzer display. The sulfur vapour concentration is useful for system troubleshooting. Incoming sample gas is filtered to 60 micron and drawn through the measurement cell by the aspirator. The measurement cell exposes a known length of sample to UV radiation for spectroscopic analysis. The aspirator is integral to the measurement cell and uses instrument air (or other inert gas) as the aspirator drive gas. The analyzer turns on the aspirator drive media only when no analyzer faults are detected. In the event of a fault condition, the analyzer automatically purges the entire sample handling system with instrument air. Analyzer zeroing is accomplished by introducing higher pressure instrument air (or other inert gas) upstream of the measurement cell. The zero gas flushes the entire sample handling system (probe to vent) and allows readings to be taken through the measurement cell when no Revision 5 16 August 2021 absorbing species are present. To the sample system, zeroing and back purging are the same thing. The default state (power ‘off’) of the analyzer is to have the sample system in the back purge mode. Valving is provided for isolating the sample system components from the process stream. A provision is included in the oven plumbing for the steam purging of the sample probe after a plant shut-down or turn-around, or in the event of plugging of the sample probe, should it be required. A temperature-controlled oven enclosure maintains all components exposed to the tail gas sample at higher than dew point values. The oven and sample probe are mounted to an interface plate, which in turn is directly mounted to the steam heated process duct sample nozzle (typically a 2-inch, 150 pound pipe flange configuration). Electrical heat is applied to the measurement cell to achieve precise temperature control of the entire oven enclosure, which contains the measurement cell block and the associated sample handling system tubing and valves. This electrical heat is supplemented using a steam heater in the bottom of the oven enclosure that provides additional heat from a medium pressure steam source. 1.5 System Operating Control The analyzer system operation is controlled by a dedicated data acquisition system which provides supervisory control of all analyzer inputs and outputs, performs all calculations, and provides the user interface. The system includes an onboard computer system which provides a graphic display of key system control parameters and their status, a digital display of the instantaneous value of the Air Demand, H2S, SO2, and COS, and historical graphic displays of the Air Demand, H2S and SO2. The entire control computer system, consisting of a Control Board and a Display Board, is mounted on the door of the control cabinet. Control cabinet access is not required for viewing or operation. The measurement of carbonyl sulfide (CS2) is an optional measurement. Analyzers which have not been ordered with this option cannot measure CS2. Four loop-powered 4 – 20 mA analog outputs are provided for the output of analyzer measurement parameters. These four analog outputs are user-configurable for the output parameter and range. Additionally, four solid-state relay outputs are provided for the output of system status data. An RS485 serial port is also provided which can be used for available for Modbus communication. Two Ethernet ports are provided for use either for Modbus TCP/IP communication OR for connection of a computer for GUI access. Aside from the Ethernet ports, one of which is located on the front door of the control cabinet and the other which is located on the control board, all inputs and outputs are found on the analyzer’s Input / Output Board inside the control cabinet. A handheld keypad is provided for user interface with the analyzer. Operation of the system with the keypad is described in Section 4. As an alternative, a web based graphical user interface (GUI) can be used to view and enter information on a remote basis. Operation using the web GUI is described in Section 5. Revision 5 17 August 2021 1.6 Contents of this Manual This manual contains the following information: Section 1: 943-TGXeNA Tail Gas Analyzer Introduction presents introductory information about the analyzer system. Section 2: Installation describes unpacking the analyzer, installing it in the facility and interfacing with other devices. Section 3: Operation of the System explains how the operator interacts with the analyzer. Section 4: Local System Control describes how the user enters data and views system parameters using the keypad and the local display Section 5: Web-based Graphical User Interface describes how to operate the analyzer and edit the analyzer configuration using the web-based graphical user interface. Section 6: Maintenance describes the various regular maintenance procedures that should be followed to keep the analyzer functioning normally. Section 7: Service gives some important service procedures that may be necessary to keep the analyzer in operational condition. Section 8: Product Quality Assurance includes various documentation of the Quality Assurance that was done at the factory prior to shipping. Section 9: Drawings gives a variety of generic drawings related to the analyzer system. Section 10: Spare Parts lists a number of items which may be required to maintain operation of the analyzer. Section 11: Specifications presents the specifications for the analyzer. Section 12: Input / Output Board Configuration provides information for the testing and calibration of the various inputs and outputs available on the analyzer’s IO board. Revision 5 18 August 2021 Section 2 Installation The initial installation of the analyzer system is usually completed by the purchaser. The start-up and commissioning is usually performed by Galvanic Applied Sciences Inc. personnel. 2.1 Receiving the System When the system arrives, inspect the packaging for external signs of damage. If there is any obvious physical damage, contact the shipping agent and Galvanic Applied Sciences to report the damage and request that the carrier's agent be present when the unit is unpacked. It is recommended that you retain the shipping container so that it may be used for future shipment of the unit, if necessary. 2.2 Environmental Requirements 2.2.1 Electrical Requirements The power input is 100 – 240 Vac, 1 phase, 50/60 Hz, 800 W. The operating voltage is specified on the serial number name plate 2.2.2 Temperature The ambient temperature range the analyzer can operate in is shown in Table 1. Table 1: Ambient Temperature Range by Model Model 943-TGXeNA Ambient Temperature Range -20 to 50°C (-4 to 122°F) Galvanic offers complete analyzer shelters from sunshades to complete buildings; please contact Galvanic Applied Sciences, Inc. (or your local representative) for additional information. 2.2.2 Space Requirements The 943-TGXeNA system is composed of two cabinets mounted side by side on a mounting frame. The dimensions of each cabinet are 30” (76 cm) H x 24” (61 cm) W x 12” (30 cm) D. The overall outer dimension of the system with the mounting frame is 41.75” (106 cm) H x 57” (145 cm W) x 16” (41 cm) D. The weight of the system is approximately 275 lb (125 kg); the exact weight will depend on the specifics of the analyzer. The installation location should allow both cabinet doors to swing open to at least 90 degrees. The analyzer should also be mounted so that the analyzer display is at or near eye level for ease of operation. Revision 5 19 August 2021 2.2.4 Instrument Air The system requires instrument air at 55 to 116psig (3.8 to 8 barg) at a delivery rate of 22 SCFM (37m3 / h). Instrument air is used for cabinet cooling, cabinet purge, zero gas, and aspirator drive air, so it is essential that the provided air meet the above pressure and flow rate requirements. The instrument air must be clean and dry, and meet the requirements for instrument air stipulated in ANSI/ISA Standard 57.3-1975 R (1981). 2.2.5 Steam For the Model 943-TGXeNA, a single low pressure steam supply is required, as indicated in Table 2. Table 2: Steam Supply Requirements Location Sample Probe Nozzle Minimum Pressure 2.8 barg (40 psig) Maximum Pressure 5.5 barg (80 psig) Minimum Temperature 140°C (285°F) Maximum Temperature 160°C (320°F) 2.2.6 Area Classification The hazardous area classification and ingress protection for the Model 943-TGXeNA is shown below: 943-TGXeNA Class I, Division 2, Groups C and D, Temperature Code T3, Type Z Purge IP Protection: NEMA 4 2.3 Unpacking The 943-TGXeNA analyzer system is packed for shipment in a wooden crate. Galvanic Applied Sciences Inc. advises unpacking the system according to the following procedure. 1. Remove the lid by undoing the marked lag bolts. 2. Once the lid is off, remove the excess packing material, boxes and sample probe from the shipping crate. The sample probe will be wrapped in packing material. Probes with a guide length of 5.5 feet (165cm) or longer are packed in a separate crate. 3. Visually inspect the small packages and the sample probe to ensure that no major damage has occurred. If damage has occurred, contact the shipping company and Galvanic Applied Sciences. Place the small packages and the sample probe aside in Revision 5 20 August 2021 a safe, secure storage area as they are not needed at this stage of the system installation. The analyzer weighs approximately 275 lb (125 kg). Use suitable precautions when removing it from the crate and placing it in the facility. 4. Locate and remove the four (4) bolts that secure the analyzer framework to the 2' x 4' boards at the bottom of the shipping crate. 5. Once the bolts are removed the analyzer system can be lifted from the crate. 6. Lay the analyzer system frame onto a structurally strong and level surface and inspect for any visual damage. 7. Remove the plastic wrap from the analyzer system to gain access to the doors of the cabinets. 8. Open the cabinet doors and carefully remove the packing material from inside each of the two (2) analyzer cabinets. Care should be taken while removing the cabinet packing material so that no hardware or wiring is damaged. 9. Inspect the internal equipment to ensure that no damage has occurred and that no components have become loose during transport. If any damage is visible contact Galvanic Applied Sciences Inc. immediately and do not proceed with the system installation. Do not attempt to facilitate repairs yourself as this will negate and/or invalidate any possible insurance claim or equipment warranty. 10. If no damage is apparent, the analyzer system is ready for transport to the installation (sample point) site. The analyzer system framework has two (2) lifting rings located at the top. Installation of proper clevises is recommended. The lifting rings are rated for approximately 227 kg / 500 lbs per ring. 2.4 Installation Procedure The installation procedure of the 943-TGXeNA analyzer system consists of the following steps 1. Mounting of the Analyzer System (Section 2.4.1) 2. Mating of the Process and Analyzer System Flanges (Section 2.4.2) 3. Connection of the AC Power Service (Section 2.4.3) 4. Connection of the Analog Signal Cables (Section 2.4.4) 5. Connection of the Digital Signal Cables (Section 2.4.5) 6. Connection of the Instrument Air Services (Section 2.4.6) 7. Connection of Steam (Section 2.4.7) 8. Connection of the ‘Loss of Purge Signal’ (Section 2.4.8) The user should fully understand each step of the installation process prior to proceeding with installation. If there are any concerns with the installation process, please contact Galvanic Applied Sciences Inc. for assistance. Revision 5 21 August 2021 2.4.1 Mounting of the Analyzer System The framework that is used in the analyzer system must be securely attached to a support structure provided by the end user. The support structure must be positioned so that when the analyzer framework is bolted in place, the flange of the analyzer cabinet and the process sample access point are correctly aligned. The plant support structure should be suitable for mounting the analyzer frame as shown in the Mounting Dimensions drawing given in Figure 2. Figure 2: Mounting Dimensions The steam jacketed ball valve must be installed on the process sample point before mounting the analyzer system. The Steam jacketed ball valve must remain closed until the sample probe is installed and connected in the sample handling oven. Figure 3 indicates the location of the various connections that must be made. Revision 5 22 August 2021 Figure 3: Service Connections 2.4.2 Mating of the Process and Analyzer System Flanges The analyzer is shipped with a 316 SS blind flange plate and gasket mounted inside the oven enclosure to prevent the process gas from flowing into the compartment before installation of the sample probe assembly. Check to ensure that this blind flange is in place and secure. Explosive, toxic and hot gases and molten sulfur may be released once the stream jacketed ball valve is opened. All company and/or regulatory agency safety procedures and rules should be adhered to. Breathing apparatus and personal protective equipment (ie. gloves, coveralls and protective eye wear) should be worn and a safety person(s) should be observing. Do not take unnecessary risks even if you believe the tailgas line to be at negative pressure. Before mounting the analyzer at the process (sample) connection, check to ensure that the following conditions have been met. 1. The bolt holes in the steam jacketed nozzle flange are large enough to accommodate the four (4) bolts on the analyzer system flange 2. The two (2) flanges are correctly aligned 3. A new gasket of proper size and material is available 4. The appropriately sized nuts are available to put onto the system flange bolts (5/8”, 11 UNC). The sample probe length is unique to each individual analyzer. The length of the probe is determined at time of ordering based on process pipe diameter and other relevant dimensions such that the probe provides a minimum of 25% (i.e at minimum one quarter of the pipe’s inner diameter) penetration into the process pipe. Revision 5 23 August 2021 If all the above conditions are satisfied: 1. Put the new gasket in place and move the analyzer system into position placing the four bolts through the steam jacketed nozzle flange holes. 2. Place the four nuts onto the bolts and tighten. 3. Inspect the flange connection using company and/or regulatory agency procedures to ensure that the connection is leak-tight (no gases are escaping). 4. Check that process gas is not leaking into the analyzer oven. When the analyzer system is securely fastened to the process sample point flange, make sure that the analyzer framework is secured to the support structure. This is to ensure that the framework and support structure, not the flange connection, are bearing the weight of the analyzer system. 2.4.3 Installation of the Sample Probe Once the analyzer system is securely installed on the process pipe, the sample probe can be installed by following the procedure below. 1. Remove the hole plug from the top of the oven cabinet as shown in Figure 4. Cover removed. Replace after sample probe installed. Figure 4: Hole Plug in Oven Cabinet Removed 2. Remove the black cover from the oven enclosure and disconnect the tubing connected to the measurement cell block as shown in Figure 5. Revision 5 24 August 2021 Tubing removed Figure 5: Oven Enclosure Tubing Removed 3. Insert the probe into the packing gland at the bottom of the oven indicated in Figure 6 until it reaches the steam jacketed ball valve. Sample probe Packing gland Figure 6: Inserting the Sample Probe 4. Open the steam jacketed ball valve and continue inserting the probe until the probe flange contacts the packing gland. Revision 5 25 August 2021 Explosive, toxic and hot gases and molten sulfur may be released once the stream jacketed ball valve is opened. All company and/or regulatory agency safety procedures and rules should be adhered to. Breathing apparatus and personal protective equipment (ie. gloves, coveralls and protective eye wear) should be worn and a safety person(s) should be observing. Do not take unnecessary risks even if you believe the tailgas line to be at negative pressure. 5. Tighten the packing gland and connect the tubing to the probe as shown in Figure 7. Make sure the three valves on the left of the oven enclosure (V1, V3, V5) are in the open position as shown in Figure 7. Close the two block valves indicated on the right side of Figure 7 (V2, V4). Install the probe RTD in the location indicated. Return to the closed position Probe RTD Location Installation Figure 7: Oven Enclosure Tubing Reinstalled If the connections are leak-tight and company safety personnel have deemed the atmosphere to be safe, breathing apparatus may now be removed. 6. Reinstall the hole plug at the top of the the oven cabinet. Revision 5 26 August 2021 2.4.3 Connection of the AC Power Service The conduit connections for the AC power cable(s) are at the bottom of the analyzer system, slightly to the right of the centreline, as indicated in Figure 4. The LIVE / HOT power lead is connected to the AC Terminal Strip (ACTS) Terminal 25, the NEUTRAL power lead is connected to ACTS:2, and the GROUND lead is connected to ACTS:21. The ACTS is located at the bottom left of the inside of the control cabinet, as shown in Figure 8. The fused terminals can be opened by lifting the tab. Figure 8: Location of ACTS in Control Cabinet Installation of the conduit, wiring, and disconnect deices must comply with all applicable, national, local, and company electrical codes. All connections must be ‘sealed’. DO NOT energize the AC power supply to the analyzer at this time. The analyzer system will be powered up at the time of commissioning by Galvanic Applied Sciences Inc. personnel. 2.4.4 Connection of the Analog Signal Cables The conduit connector for the Analog Signals, with the label ‘Analog Signals’, is provided on the bottom right side of the analyzer system control cabinet, towards the front of the cabinet, as indicated in Figure 3. There is a total of four analog output signal terminals available on the Input / Output (IO) Board inside the control cabinet, in the location indicated in Figure 9. Revision 5 27 August 2021 Figure 9: Location of Analog Output Terminals on IO Board The user may connect to any or all of the available analog output signal terminals as per their specific requirements. The analog outputs are all loop powered. When loop power is provided and the current loop between the analyzer and the external control computer is complete, green LEDs above the connection terminals will illuminate for each connected analog output signal connected. For a detailed drawing showing the analog signals connections on the IO board, refer to the DC Signals and Wiring DIagram drawing (Figure 86) in Section 9 of this manual. Installation of the conduit, wiring, and disconnect devices must comply with all applicable, national, local, and company electrical codes. All connections must be ‘sealed’. 2.4.5 Connection of the Digital Signal Cables The conduit connector for the Digital Signals, with the label ‘Digital Signals’, is provided on the bottom right side of the analyzer system control cabinet, towards the back of the cabinet, as indicated in Figure 3. There is a total of four digital signal (relay) terminals available on the Input / Output (IO) Board inside the control cabinet, in the location indicated in Figure 10. Revision 5 28 August 2021 Figure 10: Location of Digital Output Terminals on IO Board The user may connect to any or all of the available digital signal terminals as per their specific requirements. For a detailed drawing showing the digital signals connections on the IO board, refer to the DC Signals and Wiring Diagram drawing (Figure 86) in Section 9 of this manual. Installation of the conduit, wiring, and disconnect devices must comply with all applicable, national, local, and company electrical codes. All connections must be ‘sealed’. 2.4.6 Connection of the Instrument Air The installation of the analyzer system requires the connection of instrument air to the air filter. The instrument air must be at a pressure of 80-100 psig (5.5-6.9 barg), and must be clean, dry, and oil-free as per ANSI/ISA Standard 57.3-1975 R (1981). The instrument air supplied to the analyzer must be capable of a sustained flow rate of 22 SCFM (37m3/hour) at 80 to 100 psig. Prior to connecting the instrument air line to the analyzer, all air lines should be blown down to remove any possible debris such as dirt, scale, water, oil, etc., that could contaminate the analyzer system.. The system air pressure regulator, complete with a pressure gauge, is mounted on the left side of the analyzer system as shown in Figure 11. Revision 5 29 August 2021 Figure 11: Location of Instrument Air Regulator Do not adjust the instrument air pressure with this regulator until all internal tubing has been installed in the oven enclosure as shown in Figure 8. Once all the tubing is installed, the instrument air pressure indicated on the gauge can be adjusted to a suitable value (typically 30-50 psig). The control cabinet is purged for two reasons: for hazardous area classification and to maintain a positive pressure inside the control cabinet to minimize the exposure of electrical equipment to the corrosive atmosphere commonly found in sulfur recovery units. The cabinet purge should be initiated as soon as practical after the analyzer system is installed until the analyzer is commissioned. The control cabinet purge flow control valve is located inside the purge control box mounted on top of the analyzer, shown in Figure 12. Figure 12: Control Cabinet Purge Control Box To open the purge control box, use the supplied purge system access key. As soon as instrument air is available, initiate a small purge air flow rate through the control cabinet. Normal purge flow rates cannot be adjusted until all conduit connections are sealed, and the Revision 5 30 August 2021 control cabinet door is latched closed. Once normal purge flow has been established, the conduit connections are sealed, and the control cabinet door is latched shut, the purge indicator on the front of the purge control box will change colour from red (insufficient cabinet pressure) to green (normal purge pressure). 2.4.7 Connections of Steam The steam pressure and temperature requirements for the sample probe steam jacketed nozzle is given in Table 2 of this manual. The steam inlet for the sample probe steam jacketed sample probe nozzle should be at the top of the nozzle, and the outlet should be at the bottom. The outlet of the nozzle should be connected to the inlet of the steam jacketed ball valve, and the outlet of the steam jacketed ball valve should be connected into the plant condensate collection system. All steam lines, the steam jacketed sample probe nozzle, the steam jacketed ball valve, and the flange between the nozzle and the analyzer system should all be well insulated to prevent heat loss and improve temperature control. 2.4.8 Connection of the Loss of Purge Signal The control cabinet purge control box shown in Figure 12 has an integrated pressure switch that can indicate loss of sufficient control cabinet protective purge air flow. This pressure switch is equipped with a discrete output to indicate loss of purge. The wires for this pressure switch are located on the right side of the purge control box. If these wires are connected to the plant control system, they can be used to generate an alarm in the control room if purge air is lost. The pressure switch discrete output will generate an alarm signal when the local purge indicator is red; when this indicator becomes green, no alarm signal is generated. Revision 5 31 August 2021 Section 3 3.1 Operation Overview The 943-TGXeNA analyzer system is designed to operate automatically with a minimum need for human intervention. Once installation, commissioning and initial start-up have been completed, the only human intervention required is when the system indicates a problem or when routine preventative maintenance is scheduled. Section 4 of this manual describes the local user interface (UI) displayed on the analyzer’s full-colour display and its operation using the handheld keypad. The analyzer system computer automatically performs all the normal operational procedures including sample flow initiation, analysis, back purge and zero calibration, range sensitivity selection, fault detection, temperature zone control, and fail-safe back purge in the event of an analyzer fault. Operators are alerted to an abnormal state or fault occurrence through indicators on the local display located on the control cabinet door as well as fault and warning relay contact closures. The only manual adjustments to system controls (not through the computer) are the flow control of various instrument air streams. Flow adjustment valves for the zero/purge gas flow rate, the aspirator drive air flow rate and the probe cooler (used for sulfur vapour condensation at the probe tip) air flow rate are located in the oven cabinet, as shown in Figure 13. Figure 13: Location of Air Flow Control Valves in Oven Cabinet Revision 5 32 August 2021 All valves are clearly labeled according to their title and function. The Flow Diagram drawing shown in Figure 14 provides a schematic of the flow streams in the analyzer sample handling system. Figure 14: Sample System Flow Diagram In normal operation, valves V1, V3, and V5 inside the oven enclosure are open. Isolation on/off block valves V2 and V4 are provided in the oven enclosure to do the sample probe steam-out procedure, if required. Refer to Section 7.9 for the sample probe steam out procedure. 3.2 Flow Control Settings The flow control settings govern system operation. Once the system has been commissioned and the flow rates have been set, only occasional adjustments should be required. Flow settings will be checked and verified when doing the recommended routine preventative maintenance procedure given in Section 6.2. 3.2.1 Cabinet Purge Air Flow Adjust Valve The Cabinet Purge Air Flow Adjust Valve controls the rate of purge air entering the control cabinet. The Cabinet Purge Air Flow Adjust Valve is located inside the purge control box mounted on top of the analyzer, shown in Figure 12. This control box can only be opened with the key that is supplied along with the analyzer system. As a minimum, this valve is adjusted until the control cabinet purge pressure indicator goes from Red to Green plus ½ a turn. The control cabinet door must be closed and fully latched (top and bottom latches both closed) when adjusting the cabinet purge air flow adjust valve. If the control cabinet overpressure relief valve mounted on the upper right hand side of the exterior of the control cabinet opens, reduce the cabinet purge flow rate until the valve is midway between the safe purge indication flag (Red to Green transition) and the over-pressure release point (audible ‘flapping’ of the relief valve). Revision 5 33 August 2021 The safe purge indication (Red to Green flag) occurs at a control cabinet pressure positive pressure of 1" H2O (0.25kPa) above atmospheric pressure. The over-pressure relief valve opens at a control cabinet pressure of 4" H2O (1kPa) above atmospheric pressure. The normal control cabinet purge flow rate is 1.3 SCFM (2.2m3/h), as governed by selected orifices mounted in the cabinet purge vents. Purging of the control cabinet is required for hazardous area classification and to mitigate corrosive element exposure on the system electrical equipment. This adjustment must be performed with the Cabinet Cooler Air Valve closed, as the cabinet cooler adds additional air flow into the control cabinet. If the cabinet cooler air valve is NOT closed when adjusting the purge air flow, it is possible that the cabinet internal pressure will be sufficient when the cooler is on (green flag) but insufficient when the cooler is off (red flag). Seventeen minutes of normal purge air flow is required before the interior of the control cabinet may be considered safe. DO NOT apply power to the control cabinet until the control cabinet has been purged, with a green flag indicated on the purge control box, for at least 17 minutes. If a green flag cannot be achieved, this indicates that there is a leak somewhere in the control cabinet that is preventing the necessary positive pressure from being established inside the control cabinet. Check the retaining nuts on the cabinet door latches and tighten if necessary. Also check the rubber sealing strip around the door opening for damage. 3.2.2 Cabinet Cooler Air Valve A vortex cooler is mounted on the top of the analyzer control cabinet to maintain the control cabinet interior temperature at or below a given setpoint. The location of the vortex cooler is shown in Figure 15. Figure 15: Location of Vortex Cooler Air flow is automatically switched on to the vortex cooler by a control solenoid when the temperature inside the control cabinet exceeds a user-configurable set-point (by default, 35°C). Additionally, there is a Cabinet Cooler Air Valve mounted behind the purge control box on the top of the control cabinet. This block valve is used for coarse flow rate adjustment to the cabinet cooler and is typically set to fully open or fully closed. Minor throttling of the air flow to the cabinet cooler is possible by opening this valve only partially. The interior temperature of the control cabinet is indicated on the analyzer display as Cabinet Temperature. When the cooler solenoid switches on, supplying air to the vortex cooler, the additional air flow into the control cabinet will cause the over-pressure relief valve to open. Revision 5 34 August 2021 3.2.3 Condenser Cooling Air Flow Adjust Valve Sulfur vapour is always present in tail gas streams in sulfur recovery units. However, the presence of this sulfur vapour inside the analyzer sample probe and sample handling system is detrimental for two reasons. Firstly, sulfur vapour can interfere with the measurement of both hydrogen sulfide and sulfur dioxide. Secondly, if sulfur vapour inside the sample probe or sample handling system were to condense, it could lead to flow blockages inside the probe or sample handling system. For this reason, the sample probe is designed to eliminate as much sulfur vapour from entering the sample probe and sample handling system as possible. This is accomplished using a ‘cold finger’ sample probe condenser at the probe tip that condenses sulfur vapour inside the process pipe, as shown in Figure 16. Figure 16: Sample Probe Sulfur condensing on the probe’s ‘cold finger’ is hydrostatically returned to the process stream and does not enter the sample probe. Air flow to the probe condenser is controlled via a solenoid valve. Actuation of the probe cooler solenoid is determined by either the temperature of the incoming sample gas OR by the sulfur vapour content in the incoming sample gas as measured by the analyzer. The control point for the probe cooler solenoid is user configurable – refer to Section 5.4 for more details. The Condenser Cooling Air Adjust Valve allows the user to control the flow rate of the instrument air used to cool the condenser section of the sample probe. Revision 5 35 August 2021 The concentration of sulfur vapour in the process sample gas that makes it into the probe and into the measurement cell is measured and displayed on the analyzer display as Sulfur Vapour (Svap). The Condenser Cooling Air Adjust Valve can be adjusted to reduce the sulfur vapour concentration. There is normally a long time constant associated with this adjustment. Several factors can impact the temperature of the gas exiting the probe. Factors that affect the temperature of the gas exiting the probe include: • • • • • Changes in process gas temperature Changes in cooling air temperature Changes in the process gas sample aspiration rate Elapsed time since a probe back-purge Duration of a probe back purge. During a zero-calibration sequence or back purge operation, instrument air is forced into the sample probe and the analyzer sample handling system, including the measurement cell. The indicated sulfur vapour concentration during and immediately after a back-purge operation is NOT representative of the sulfur vapour concentration in the process sample gas. The condenser cooling air flow adjust valve is typically opened two turns from fully closed. The optimal situtation is that the indicated concentration of sulfur vapour in the process sample gas exiting in the measurement cell is lower with the probe cooling air on than with the probe cooling air off, without causing plugging of the sample probe. 3.2.4 Zero Air Flow Adjust Valve The Zero Air Flow Adjust Valve is used to adjust the flow rate of the instrument air used for back purge and zero calibration operations. The zero calibration is performed when the analyzer is in back-purge condition, and the probe and sample handling system, including the measurement cell, are full of zero gas. Under normal operating circumstances, the valve is adjusted so that the response time from sample conditions to a stable zero reading is between 2 and 5 seconds, although depending on the sample probe length, this time may be somewhat longer. The stabilized zero response is determined by monitoring the time required for the analyzer gas concentration outputs to stabilize at near zero levels once the analyzer has been switched from sampling to zero (back purge) mode. Excessive zero air flow rates will overly cool oven components and may lead to cell temperature control issues. If the zero air flow rate is set too low, inadequate flushing of the measurement cell before a zero adjustment is made may result. If the analyzer is zeroed before the measurement cell has been adequately flushed with zero gas, the concentration readings obtained on sample gas after returning to sampling mode will likely be lower than expected. This valve is typically opened one turn from fully closed. In extraordinary circumstances, if sample system or sample probe clogging due to sulfur vapour condensation occurs, the Zero Air Flow Adjust Valve may be opened wide to provide a solid back purge pressure. Alternately, the Zero Air Flow Adjust Valve may be turned down to a trickle for an extended period (20-30 minutes) to allow the heat of the oven and probe nozzle to re-liquefy any solid accumulation (plugging) before increasing the flow rate dramatically to purge out the re-liquefied sulfur. If this is not successful in clearing a blockage in the probe, a steam purge of the probe will be required. Refer to Section 7.8. Revision 5 36 August 2021 3.2.5 Aspirator Drive Air Flow Adjust Valve The Aspirator Drive Air Flow Adjust Valve indirectly controls the rate of process sample gas extraction from the tail gas duct. The aspirator drive air is plumbed to a venturi-type eductor integral to the measurement cell block, as shown in the exploded view of the measurement cell in Figure 17. Figure 17: Measurement Cell Block (Exploded View) The aspirator has a narrow nozzle, and when flowing aspirator drive air passes out of this nozzle, it expands, causing the pressure on the aspirator suction port to drop. This aspirator suction port is connected to the outlet of the measurement cell. The design of the analyzer sample system is such that process sample gas is extracted from near the centre of the process duct and vented at the wall of the process duct through the same access port. Ideally, enough aspirator drive air is provided to present a measurement cell outlet pressure of 2-3" H2O (0.5 to 0.75 kPa) below the process duct pressure. This pressure differential across the measurement cell draws sample up the sample probe, and after the sample is drawn through the measurement cell it mixes with the aspirator drive air at the aspirator suction port and is expelled back down the sample probe nozzle and into the process pipe. In practice, the aspirator drive air flow is adjusted such that the response time from a zero signal to stable process measurement is less than 30 seconds, though the actual response time is highly dependent on the sample probe length – the longer the probe, the longer the response time will be. The adjustment of the aspirator drive air flow is made by monitoring the amount of time it takes for the displayed concentration values on the analyzer display to reach stable values after the analyzer has been switched from purge mode to sampling mode. An additional consideration that must be made when adjusting the aspirator drive air flow rate is that if the aspirator drive air flow is set too high, the aspirator air flow will draw a significant amount of heat out of the measurement cell block, and cause the displayed cell temperature to drop, potentially to below the low cell alarm setpoint. Thus, care must be taken when adjusting the aspirator drive air flow rate to obtain a balance between stable temperature control and rapid response time from zero to sample. Typically the aspirator drive air flow adjust valve is set to two turns from fully closed, but the optimal balance between temperature control and response time will depend on specific conditions of the Revision 5 37 August 2021 analyzer installation, including but not limited to steam temperature and pressure (both oven steam and probe nozzle steam), ambient temperature, aspirator drive gas temperature, and the quantity and quality of insulation applied to the steam lines, sample probe nozzle and ball valve, and analyzer flange. 3.2.6 System Regulator The system instrument air regulator is normally set to 30 psig. However, the specific value of this setting is not critical for system operation provided that the pressure is sufficient to provide adequate sample aspiration, system zeroing, and effective back purge. In situations where additional supply pressure is required, the system regulator may be adjusted to its maximum output of 50 psig without harming the analyzer. As the cabinet cooler draws significant flow of instrument air, it is advisable to do all adjustments of the zero and aspirator drive air with the cabinet cooler switched on. In this fashion, deficiencies with the pressure and / or flow rate of the instrument air supply can be immediately detected. 3.3 Analyzer Outputs The 943-TGXeNA analyzer generates both analog and digital output signals for connection to the users’ plant control system. The analog output signals are used to output calculated concentration and other pertinent analysis values, and are user-configurable for range, output parameter, and output behaviour. The digital output (relay) signals are used for outputting analyzer and purge status signals. 3.3.1 Analog Outputs There are four available analog outputs available on the 943-TGXeNA. The analog outputs are all loop-powered 4-20 mA outputs which are fully user configurable for output parameter, output range, and update behaviour when the analyzer is in back purge mode. Each analog output can be configured to output one of the following parameters: • • • • • • • Air Demand (range starts at negative full scale for 4 mA) H2S Concentration (% or PPM) SO2 Concentration (% or PPM) COS Concentration (% or PPM) CS2 Concentration (% or PPM) H2S:SO2 Ratio Sigma S (sum of H2S and SO2 concentrations) Each analog output can also be user configured to be either Track or Hold. Track and hold refer to the behaviour of the analog output when the analyzer is placed in back-purge mode. If an output is programmed to be Track, the output value will track along with the calculated values when the analyzer is placed in back purge mode, and thus will go to zero (4 mA) when the analyzer is in back purge mode. If an output is programmed to be Hold, it will hold the last known good value from when the analyzer was in sampling mode and continue to output this good concentration value until the analyzer goes back into sampling mode. Thus, the analog output will NOT go to 0 (4 mA) when the analyzer is in back-purge mode. Typically, an analog output configured to output air demand will be configured for Hold, while Revision 5 38 August 2021 concentration outputs are configured for Track, though this is entirely up to the user to decide. The value output by each analog output is updated once per second. The configuration of the analog outputs can be done either using the local display and keypad, as described in Section 4.8.1, or by using the Web GUI, as described in Section 5.4. 3.3.2 Digital Outputs (Relays) There are four digital outputs on the analyzer which are used for outputting analyzer status and other operational condition data. These digital outputs are all zero potential form C relay contacts, each isolated to 250 Vrms. The four status and operational relays are Status, Service, Mode, and Control. Each of these relays has an associated status indicator on the analyzer display for visual confirmation of the analyzer status. In addition to the 4 digital outputs associated with the analyzer operation, there is an independent Loss of Purge signal output connected to the purge control box on top of the analyzer control cabinet. The function of each relay is described in the following sections. 3.3.2.1 Status The Status output indicates whether there are any faults present that will force the analyzer into back-purge mode until the fault is cleared. Table 3 describes the Status relay states. Table 3: Status Relay States State Display Indicator Colour Normal Green Fault Red Explanation All monitored system parameters are within normal limits. No faults are present At least ONE of the following conditions is true: • Analyzer power is off • Measurement Cell temperature is outside specified range • Probe temperature is outside specified range NOTE: Only for analyzers equipped with probe temperature RTD • Measured sulfur vapour concentration is above specified fault setpoint • Spectrometer parameters are outside specified range • The system computer is unable to communicate with the I/O board • The system computer is unable to communicate with the spectrometer An analyzer with at least one fault condition present will be unable to carry out sampling and analysis of the process gas. When the fault condition clears, the analyzer will automatically perform an auto-zero calibration and then return to normal sampling mode. Revision 5 39 August 2021 3.3.2.2 Service The Service output indicates whether there is an issue with the analyzer that requires operator attention. Table 4 describes the Service relay states. Table 4: Service Relay States Condition Display Indicator Colour Normal Green Warning Red Explanation All monitored system parameters are within normal limits. No faults are present At least ONE of the following conditions is true: • Control cabinet interior temperature is outside specified range • Spectrometer integration period >500 ms • Sample Absorbance >2.0 AU • Sulfur vapour concentration exceeds specified warning set point • Spectrometer peak height at last zero calibration is too low An analyzer with any active warnings will continue in sampling mode and provide valid analysis results, although warnings indicate that there is an issue with the analyzer that, if left unchecked, could lead to a fault condition. The warning condition will clear when the parameter that caused the warning condition returns to its normal range. 3.3.2.3 Mode The Mode output indicates when a zero calibration, either manually requested or automatic, is in progress. Table 5 describes the Mode relay states. Table 5: Mode Relay States Condition Display Indicator Colour Run Green Calibrate Yellow Explanation Analyzer is not performing a zerocalibration run, either manual or according to an automated schedule. One of the following conditions is true: • A clock-triggered automatic zero calibration cycle is in progress • A manually requested zero calibration cycle is in progress • Analyzer power is off When this indicator is in the ‘Calibrate’ state, the analyzer is not measuring the process tail gas. After a calibration cycle is complete, the Calibrate state will persist for a specified time interval (the Zero Hold Interval), allowing process gas to reach the measurement cell Revision 5 40 August 2021 and the analyzer concentration measurements to return to stable process values prior to returning to the Run state. If there are any faults currently present (i.e. Status relay is in fault state) the Mode indicator CANNOT switch to Calibrate – Calibration is ONLY possible when all fault conditions are cleared, and the Status relay is in the Normal condition. The only condition under which the Status relay can be in Fault while the Mode relay is in Calibrate is if the analyzer power is off. 3.3.2.4 Control The Control output indicates whether the analog output signals are valid. Table 6 describes the Control relay. Table 6: Control Relay States Condition Display Indicator Colour Auto Green Manual Yellow Explanation ALL the following conditions are true: • Status indicator is Normal (i.e. no fault conditions present) • Mode indicator is in Run state (i.e. analyzer is not performing a zero calibration) • Online / Offline switch is in the Online position (i.e. analyzer is not under maintenance) • Analyzer power is on At least one of the conditions for the relay to be in the Auto state is NOT true. When the relay is in the Auto state, the analyzer is indicating that it believes that the data being output on the analog outputs are valid current measurements of the tail gas process steam. If the Control relay is in the Manual state, this indicates that the analyzer believes that the data being output may not be valid. The purpose of this indicator is to signify when the analyzer outputs are suitable for use as closed loop control inputs. When this indicator is in the Manual state, no control action should be taken based on the analyzer output signals. This indicator is generated on the basis of the other analyzer indicators, as well as the condition of the Online / Offline mode toggle on the display (refer to Section 4.3.1). The Control relay state is automatically returned to Auto once all the conditions required for the Auto state have been met. While the Control relay is in the Manual state, any analog output that is configured as Hold will be held. 3.3.2.4 Loss of Purge The Loss of Purge signal relay, which is an integral component of the Purge Control box on the top of the analyzer control cabinet, indicates the status of the analyzer’s control cabinet safety purge. When a safe positive pressure as described in Section 3.2.1 is present inside the analyzer’s control cabinet, the Purge indicator on the outside of the purge control box will be green and the purge fail relay will be in the normal state. When the safe positive pressure is lost, such as when purge air flow is lost or the control cabinet Revision 5 41 August 2021 door is opened, the purge indicator on the outside of the purge control box will be red and the Loss of Purge relay will be in the fault state. The relay contacts of the Loss of Purge relay MUST be connected to a plant alarm system in a continuously attended location, such as in the plant control room, in order to maintain the hazardous location certification of the analyzer. Revision 5 42 August 2021 Section 4 4.1 Local System Control Overview The operator can locally control the analyzer via the full colour, multi-page display mounted in the control cabinet in conjunction with the hand-held keypad that can be connected to a port on the control cabinet door. The keypad, in conjunction with the local display, can be used to view a variety of analysis and status information, as well as to make changes to some analyzer operational parameters. 4.2 Using the Local Display and Handheld Keypad 4.2.1 Local Display User Interface The local display user interface consists of a series of panels which are accessed via tabs at the top of the screen. The different panels of the local display user interface display a variety of different information and are described in sections 4.3 to 4.8 of this manual. The local display as it appears when the Analysis 1 panel is active is shown in Figure 18. Figure 18: Local Display User Interface Revision 5 43 August 2021 The coloured indicator circle at the top right of the display is visible on all panels. It provides a quick indication of the analyzer status. When it is green, the analyzer has no active faults or warnings - all monitored parameters are within their specified ranges. When it is yellow, this indicates that the Service relay is in the Warning state. When it is red, this indicates that the Status indicator is in the Fault state, and so the analyzer will remain in back-purge mode until the active fault(s) have cleared. 4.2.2 The Handheld Keypad The handheld keypad is used to navigate between the various panels of the local display user interface, perform a variety of control operations, and enter numerical data in usereditable fields. It is shown in Figure 19. Figure 19: Handheld Keypad The white keys on the keypad are used for numerical data entry, including a decimal point. The functions of the red keys are described in Table 7. Table 7: Keypad Red Key Functions Key Label PANEL PREV PANEL NEXT FIELD PREV FIELD NEXT HOME PURGE DEL EXIT ENTER Revision 5 Function Changes the active panel to the previous panel. The previous panel is the tab to the left of the currently displayed tab. When at the left-most tab, pressing this key will move to the right-most tab. Changes the active panel to the next panel. The next panel is the tab to the right of the current displayed tab. When at the right-most tab, pressing this key will move to the left-most tab. On a panel with actionable controls or editable fields, pressing this key will move to the previous (top to bottom, right to left) control or field. On a panel with actionable controls or editable fields, pressing this key will move to the next (top to bottom, left to right) control or field Returns to the Analysis 1 panel immediately from anywhere within the Local Display User Interface Pressing this key while the analyzer is in sampling mode will switch the analyzer to backpurge mode. Pressing this key while the analyzer is in back-purge mode, provided that the Status relay state is Normal, will place the analyzer in sampling mode. This key is functional on any panel of the local display user interface. Deletes the last numerical value. Only functional when editing a numerical data entry field. Leaves a data entry field when editing without saving the current value. Only functional when editing a numerical data entry field. After highlighting an editable numerical data entry field using the FIELD NEXT / FIELD PREV keys, pressing ENTER will allow the user to edit the data. After editing the numerical data using the numerical keys, pressing ENTER again will save the changes to the analyzer. 44 August 2021 The handheld keypad should only be connected to the analyzer or disconnected from the analyzer when the installation location is known to be non-hazardous. 4.3 Analysis 1 Panel The Analysis 1 panel shown in Figure 18 shows important current analytical parameter results, status indicators, and operator controls. 4.3.1 Online/Offline Mode Toggle The Online / Offline Mode Toggle at the top right of the Analysis 1 panel shown in Figure 20 is a button that can be used to toggle between Online and Offline modes. Figure 20: Online / Offline Mode Toggle When this toggle is set to Online, the indicator will be green. In this case, the Control relay will be in the Auto (green) state, indicating that the analyzer believes the data being output on the analyzer’s analog outputs to be valid. Prior to performing maintenance or other tasks that may cause the output data to become invalid, this control should be toggled to the Offline (red) state by using the FIELD NEXT / FIELD PREV keys to highlight it and then pressing ENTER to toggle it. When this control is set to Offline mode, it will become red. At the same time, the Control relay state will change from the Auto state to the Manual (yellow) state, indicating that the analyzer believes the output data to be invalid. Once maintenance is complete, this toggle should be set back to the Online state by again highlighting it using the FIELD NEXT / FIELD PREV buttons and pressing ENTER. The analyzer’s Online or Offline status does not affect the operation of the analyzer in any way. Rather, this function has been implemented as a convenience to the operator, as it provides an easy way for the operator to indicate to the control room that the analyzer is currently undergoing maintenance or servicing and thus the data being output by the analyzer is not valid. When the control is toggled from Offline to Online, the Control relay will change state from Manual to Auto ONLY if the conditions listed as prerequisite for the Auto state in Table 6 have been met. 4.3.2 Concentration Fields The concentration fields shown in Figure 21 are non-editable fields that show the current value of the concentrations for all analyzed components. Revision 5 45 August 2021 Figure 21: Analysis 1 Concentration Fields The analyzer’s physical measurement range, which is determined by the length of the measurement cell, is optimized for typical on-ratio (that is to say, non-upset) concentrations of H2S and SO2. COS and optionally CS2 concentrations are also displayed here. The sulfur vapour (Svap) is monitored to indicate when there may be a problem with the sulfur condenser “cold finger” at the tip of the sample probe (refer to Section 3.2.3) and to prevent sulfur plugging inside the analyzer sample handling system. 4.3.3 Air Demand The Air Demand field and Air Demand trend graph shown in Figure 22 show the current calculated Air Demand (% Excess Air) and the recent trend in the Air Demand data. The Air Demand field is read-only and cannot be edited. Figure 22: Air Demand Value and Trend The air demand reading is an indicator of the current process status relative to the optimal ratio (typically a 2:1 ratio H2S:SO2). If the air demand value is negative, this indicates that the H2S concentration is too high and there is insufficient air being added. If the air demand value is positive, this indicates that the SO2 concentration is too high and there is excess air being added. If the air demand is zero, this indicates that the H2S to SO2 ratio is at the optimal value and the air does not need to be adjusted. Revision 5 46 August 2021 The graphical trend displayed below the Air Demand field shows the trend in the air demand data over a recent period of time, with the current value at the right side of the graph. The xaxis (time) and y-axis (concentration) ranges of this graph can be adjusted on the Configuration Panel Display Sub-panel (refer to Section 4.8.3). This trend is updated once per second. 4.3.4 Relay Indicator Fields The relay indicators at the bottom right of the Analysis 1 panel indicate the current state of the analyzer’s four relay outputs. The relay indicators are shown in Figure 23. Figure 23: Relay Indicators The relay indicators provide at-a-glance status information. If all the indicators are green, this indicates that the analyzer is functioning normally with no faults or warnings active. If the Status indicator is red, this indicates the analyzer has at least one fault active, and is unable to sample until the fault condition(s) are cleared. If the Service indicator is yellow, this indicates that maintenance will be required soon. Refer to the Indicators panel to diagnose which fault(s) and / or warning(s) are active. See Section 4.5 for more details about specific faults and warnings. If Mode and Control are both yellow, this indicates the analyzer is carrying out a zero calibration. For more information on the relay outputs, refer to section 3.3.2. 4.3.4 Manual Zero The Manual Zero control is used to manually initiate a zero calibration cycle. It is shown in Figure 24. Figure 24: Manual Zero Control The Model 943-TGXeNA performs a zero calibration in order to check and adjust the analyzer’s zero baseline. It is ONLY performed when the analyzer is in back purge and the measurement cell is filled with a gas that doesn’t absorb UV radiation in the wavelength range of interest (i.e. instrument air or nitrogen). The zero calibration sets the absorbance baseline to 0 AU across the entire measurement wavelength range during this process. To initiate a Manual Zero Calibration cycle, simply use the FIELD NEXT / FIELD PREV buttons to highlight the Manual Zero control, then press ENTER. The zero calibration sequence is identical whether triggered manually using the Manual Zero control, automatically when all Revision 5 47 August 2021 existing faut conditions are cleared and prior to the analyzer returning to sampling mode, or automatically according to the set Auto Calibration Frequency (refer to Section 4.8.4 for more details on Auto Calibration). No span calibration is required under normal circustances for an installed analyzer. There is no span calibration functionality available on the Model 943TGXeNA. A Manual Zero zero calibration cycle CANNOT be initiated while the analyzer has any fault conditions (Status relay is red) present. Using this control while the Status relay is red will have no effect. When a zero calibration cycle is triggered, the zero calibration sequence proceeds in the following order: 1. The Mode relay output state changes to Calibrate (yellow) and the Control relay output changes to Manual (yellow) 2. Any analog outputs configured for Hold behaviour will hold the last value they were outputting prior to the zero calibration cycle being initiated. 3. The Zero / Sample solenoid switches off, allowing zero gas to purge the analyzer’s sample handling system, including the measurement cell, as well as the sample probe. This purge continues for the duration specified by the Zero Purge Interval parameter (refer to Section 4.8). 4. Once the zero purge time has elapsed, the computer collects 10 spectrometer scans on zero gas and averages them together to calculate a new zero baseline. 5. The Zero / Sample solenoid switches on, allowing sample gas to be drawn back up the probe and into the analyzer sample handling system and measurement cell by the aspirator. 6. During this period, any analog outputs configured for Hold behaviour will continue to hold the last value output prior to the initiation of the calibration cycle The analyzer waits for the number of seconds specified by the Zero Hold Interval parameter of the configuration data (Section 4.8.4) to allow the calculated concentration values to stabilize at on-line values before updating the analog outputs. 7. If no pre-existing fault conditions are present, the Mode relay output changes to Run (green) and the Control relay output changes to Auto once the Zero Hold Interval time has elapsed. 4.3.5 Back Purge Indicator and Control The fail-safe condition of the analyzer is to have instrument air flowing through the measurement cell, the analyzer sample handling system, and the sample probe. This is a condition known as back purge. The Back Purge indicator and manual controls are shown in Figure 25. Revision 5 48 August 2021 Figure 25: Back Purge Indicator and Manual Controls The back purge indicator shows the current back purge status. If it is green, this indicates that the analyzer is currently drawing sample into the measurement cell. If it is red, this indicates that the analyzer is currently in back purge, either due to the analyzer being manually placed into back purge OR due to a fault condition causing an automatic back purge OR because the analyzer is currently carrying out a zero calibration cycle. Below the Back Purge Indicator are two check boxes which can be used to manually set the analyzer into back purge or sampling mode. To choose which mode is active, select the desired mode using the FIELD NEXT / FIELD PREV buttons and press ENTER to choose. Alternatively, pressing the PURGE button will switch to the currently inactive mode (i.e. pressing purge while the analyzer is sampling will cause it to switch to back purge mode and vice versa). Prior to performing any maintenance, particularly if any sample system tubing is to be disconnected, the analyzer should be placed into back purge mode and purged for at least 5 minutes. This will prevent any toxic gases from remaining in the sample system if tubing is to be disconnected. If Sample is selected but the back purge indicator remains red, this indicates that a fault condition likely exists. Once the fault condition(s) are cleared, the analyzer will automatically return to sampling mode after first performing a zero calibration cycle. If the analyzer is set to back purge mode while a fault condition exists, the analyzer will NOT automatically return to sampling mode when the fault condition(s) are cleared. 4.4 Analysis 2 Panel The Analysis 2 panel shown in Figure 26 displays a variety of analysis information and system operating parameters. Figure 26: Analysis 2 Panel Revision 5 49 August 2021 4.4.1 Online / Offline Control At the top right of the Analysis 2 panel is the Online / Offline toggle control, as shown in Figure 27. Figure 27: Online / Offline Control This toggle has the same function on the Analysis 2 panel as it does on the Analysis 1 panel. Refer to Section 4.3.1 for details. 4.4.2 Concentrations, Air Demand, and Trend Graph Like the Analysis 1 panel, the Analysis 2 panel displays live concentration values for all monitored parameters, as well as a trend graph showing recent data trends. Refer to Figure 28. Figure 28: Data Fields and Trend Graph Unlike the Analysis 1 panel, the Analysis 2 panel does not show the Sulfur Vapour (Svap) concentration, but it does show all other concentration values (including CS2 if the analyzer is configured for this measurement). On the Analysis 2 panel, the largest data fields are for the percentage concentrations of H2S and SO2, with the COS, CS2 (if present) and Air Demand fields being smaller in size. The trend graph shown below the H2S and SO2 indicators indicates the recent trend in concentration for all measured parameters displayed on this panel. The colour of each component’s trend line matches the colour of that component’s data field on this panel. The Air Demand, on this panel indicated as Air, does not have a line on the trend graph on this panel. The trend graph is updated once per second, with the most recent result being found on the right side of the graph. The x-axis (time) and y-axis (concentration) ranges of this graph can be adjusted on the Configuration Panel Display Sub-panel (refer to Section 4.8.3). Revision 5 50 August 2021 4.4.3 System Operating Parameters The Analysis 2 panel also displays several important system operating parameters, as shown in Figure 29. Figure 29: System Operating Parameters The approximate normal operating ranges for these parameters and an explanation of each parameter is given in Table 8. Table 8: System Operating Parameters Parameter Operating Range (Typical) Cell Pressure 670 – 1100 mmHg Cell Temperature 140 – 160°C Probe Temperature Cabinet Temperature 4.5 110-120°C 5 – 45°C Explanation Indicates the measured pressure inside the measurement cell, in millimetres of mercury (760 mmHg is atmospheric pressure at sea level). The cell pressure should be observed to drop by around 50 mmHg (or more) when the analyzer is switched from back-purge to sampling. If the pressure does not drop at all, or rises, when the analyzer is switched from back purge to sampling, this is an indication of a probe plugging problem. Refer to section 7.9 for details. Indicates the measured temperature of the measurement cell block. If temperature goes outside user configurable range, analyzer will go into fault mode. Measures the temperature of the gas coming out of the sample probe. If temperature falls outside user configurable range, analyzer will go into fault mode. Indicates the temperature inside the control cabinet via a temperature sensor on the analyzer spectrometer. Indicated temperature depends on ambient environmental temperature. If temperature falls outside user configurable range, a warning will be triggered. NOTE: If this temperature exceeds 45°C for a long period of time, irreparable damage to the spectrometer could result. Indicators Panel The Indicators panel shown in Figure 30 indicates which fault and warning conditions (if any) are currently active and a historical record of the last 25 fault / warning events. Revision 5 51 August 2021 Figure 30: Indicators Panel The top 6 rows in the historical grid are for fault conditions, while the bottom five rows are for warning conditions. Every time a fault or warning occurs, an X is placed in the farthest right cell for that fault or warning (i.e. the current situation). When that fault or warning is cleared, the X moves one to the left, and a new empty cell appears in the farthest right cell of that fault or warning. A new column is added to the entire grid any time a fault or warning appears or is cleared; there is no specific time at which a new column is added, so just by looking at the historical grid it is not possible to determine the exact time at which a fault or warning appeared or was cleared. The column of coloured squares at the right is a column of indicators that indicates current status. If all these squares are green, there are no active faults or warnings, and the analyzer is operating normally. If at least one of the fault indicators is red, the analyzer will be in fault condition and cannot analyze sample; this fault condition cannot clear until ALL of the fault indicators change to green. The analyzer will continue to operate if any of the warning indicators are yellow, but maintenance is suggested as soon as is convenient as several warning conditions could result in fault conditions in the future if not dealt with. To clear this historical faults and warnings, use the FIELD NEXT or FIELD PREV buttons to highlight the Clear Fault / Warning History button at the bottom of the panel, then press ENTER to clear. Note that any faults or warnings which are currently active WILL NOT clear from the historical grid, and will remain in the right most column. Revision 5 52 August 2021 4.5.1 Fault Conditions Table 9 describes each of the fault conditions listed in the fault table on the Indicators panel. Table 9: Analyzer Faults Fault Cell Temperature High High Sulfur Measure Range Reference Range Dark Range I/O Board Explanation Measurement cell temperature is either below Low Cell Temperature setpoint or above High Cell Temperature setpoint. Measured sulfur vapour content exceeds high sulfur vapour concentration fault setpoint Spectrometer signal is out of range while analyzer is measuring sample (signal either off scale or too low). Spectrometer signal is out of range while analyzer is in back purge mode (signal either off scale or too low) Spectrometer dark level (i.e. signal when no light is present) is either too low or too high. System computer is unable to communicate with Input / Output board and / or spectrometer Some of these faults may clear by themselves (particularly the cell temperature fault and the high high sulfur fault) but others may require maintenance or even hardware replacement to resolve. Refer to Section 7.2 for more detail on how to troubleshoot active faults. 4.5.2 Warning Conditions Table 10 describes each of the warnings listed in the warning table on the Indicators panel. Table 10: Analyzer Warnings Warning Cabinet Temperature High Absorbance High Integration Period Low Reference Peak High Sulfur Vapour Explanation Control cabinet internal temperature is either below low cabinet temperature setpoint or above high cabinet temperature setpoint. Measured absorbance as shown on the Absorbance spectrum exceeds 2.0 AU when analyzer is in sampling mode. Typically indicates that measured concentration of at least one component is out of range Integration period required to obtain an in-range spectrometer signal when analyzer is in back purge mode > 500 milliseconds. Spectrometer signal peak height when analyzer is in back purge mode <24000 A/D counts Measured sulfur vapour content exceeds high sulfur vapour concentration warning setpoint Some of these warnings may clear by themselves, particularly the cabinet temperature warning and the high sulfur vapour warning, but others will not be able to be cleared without performing maintenance on the analyzer. Refer to section 7.2 for more detail on how to troubleshoot active warnings. Revision 5 53 August 2021 4.6 Spectrum Panel The Spectrum panel shown in Figure 31 shows the current transmission spectrum being received by the control computer from the analyzer’s spectrometer. Figure 31: Spectrum Panel The transmission spectrum shows the intensity of ultraviolet light, in A/D counts, being received at every pixel of the spectrometer. The spectrometer has a total of 2048 pixels, with an approximate 0.3nm resolution between the pixels. The x-axis of the spectrum is unlabelled, but it shows the wavelength range with the shortest wavelengths at the left and the longest wavelengths on the right. Only a range of 530 of these pixels is actually used for calculating the concentration values. The higher the A/D counts are for a given wavelength, the greater the intensity of the light transmitted through the measurement cell to the detector at that specific wavelength is. In the bottom right corner of the panel are a series of three fields giving data about spectrometer parameters, shown in Figure 32. Figure 32: Spectrometer Parameters These three parameters are described in Table 11. Revision 5 54 August 2021 Table 11: Spectrometer Parameters Parameter Peak Height First Vector Pixel Dark Level Explanation Displays the peak height of the transmission spectrum, in A/D counts. Should be approximately 28000-29000 when analyzer is in back purge mode. Displays the intensity of light being received at the first vector pixel, in A/D counts. The first vector pixel is the first pixel that is used for calculating concentration values. Displays the intensity of light being received when the spectrometer is dark (i.e. no light present). This value should be in a range between 400 and 900 A/D counts. Below the spectrum are two buttons referring to a parameter called Integration Period, the Set Integ. Time button and the Optimize Integ. Time button. The integration period is the duration of time that light is collected by the pixels of the spectrometer before being read by the control computer. For example, in Figure 31 the integration time is given as 123.69 milliseconds. This means that the light incident on the spectrometer pixels is allowed to accumulate for 123.69 milliseconds before being read by the control computer; the spectrometer pixels are then zeroed and allowed to collect light again. The displayed transmission spectrum, then, shows the intensity of light collected at every pixel in this duration of time. The integration time is a compromise to optimize the resolution while minimizing noise in the spectrum. A short integration time will optimize the resolution and show fine detail in the spectrum, but the noise level may be relatively high. Contrarily, a long integration time will reduce noise, but fine detail in the spectrum may be lost. The integration time has a maximum value of 1000 milliseconds. The optimal integration time for the current analyzer conditions can be automatically calculated by pressing the Optimize Integ. Time button. Use the F4 / F3 keys to highlight this button, then press ↵ to optimize the integration time. Once pressed, the control computer will adjust the integration time such that the peak height of the displayed spectrum reads approximately 28000 A/D counts. If this peak height cannot be achieved even with a maximum integration time of 1000 ms, this indicates a problem with the analyzer’s optical system. Refer to section 7.2 for troubleshooting tips. Optimizing the Integration Time should ONLY be performed when the analyzer is in back purge mode. Attempting to optimize the integration time when the analyzer is in sampling mode may negatively affect the analyzer baseline, and thus the analyzer’s analytical results. As an alternative to automatically optimizing the integration period, the operator may choose to manually adjust the integration period instead. Use the FIELD NEXT / FIELD PREV keys to highlight the Set Integ. Time Button, then press ENTER. The Integration Period dialog box shown in Figure 33 will then be presented. Revision 5 55 August 2021 Figure 33: Integration Period Dialog Box The current value of the integration time is displayed in the Old Value field. A new integration period can be entered into the New Value field using the white numerical keys and the decimal point key. Once the desired value has been entered into the New Value field, press ENTER, then highlight the Okay button and press ENTER again. To discard changes, highlight the Cancel button and press ENTER. After manually editing the integration period, check the indicated Peak Height. If the peak height displays 32000, this indicates that the peak height is off scale, as the full scale for the spectrometer reading is 32000 A/D counts. The integration period should be reduced until the indicated peak height drops below 32000. If the indicated peak height is less than 24000, the integration period should be increased. If the integration time is already at 1000 ms, this indicates a problem with the analyzer’s optical system. Refer to Section 7.2 for more details on troubleshooting analyzer problems. 4.6.1 Factory Reference The Factory Reference is a zero gas transmission spectrum that was saved at the factory at the time of analyzer factory calibration. When the Show Factory Reference checkbox is checked by using the FIELD NEXT / FIELD PREV keys to highlight and then pressing ENTER to check the box, the factory reference spectrum is shown superimposed on the same axes as the currently displayed spectrum. The Spectrum panel with the Factory Reference being displayed is shown in Figure 34. Figure 34: Factory Reference Revision 5 56 August 2021 Take note of the following rules-of-thumb when comparing the pink trace of the factory reference with the red trace of the current transmission spectrum: • The factory reference should be largely similar to the current transmission spectrum when the analyzer is in back purge mode. If it is not, there is likely an issue with the analyzer optical system. Refer to Section 7.2 for troubleshooting techniques. • The factory reference should be notably different from the current transmission spectrum, as it is in Figure 34, when the analyzer is in sampling mode. If the sampling spectrum is the same or very similar to the factory reference, this could indicate an issue with plugging in the sample probe. Refer to Section 7.9 for details on how to clear a plugged probe. The New Reference button is used to make the analyzer use the currently displayed transmission spectrum to calculate a new zero baseline without carrying out a full zero calibration cycle. Highlight the New Reference button by using the FIELD NEXT / FIELD PREV keys, then pressing ENTER. Pressing New Reference DOES NOT cause the analyzer to automatically go into back purge mode. Be sure the analyzer is in back purge mode prior to using this function otherwise the calculated analyzer results after calculating the new reference WILL NOT BE VALID! 4.7 Absorbance Panel The Absorbance panel shown in Figure 35 shows the currently calculated absorbance spectrum as well as the current concentration of all of the analyzed components in the tail gas stream. Figure 35: Absorbance Panel Revision 5 57 August 2021 The absorbance spectrum is calculated by subtracting the current transmission spectrum from the transmission spectrum that was obtained the last time the analyzer carried out a zero calibration cycle OR when the New Reference button was pressed on the Spectrum panel, whichever was most recent. The y-axis of this spectrum is absorbance units (AU). When the analyzer is in back purge mode, the absorbance spectrum should be a horizontal line at an absorbance of 0 AU. If it is not, and the analyzer is NOT in a fault condition, first confirm that the current transmission spectrum in back purge is largely similar to the factory reference spectrum, then immediately carry out a new zero calibration cycle OR use the New Reference function on the Spectrum panel. After the zero calibration cycle is complete, confirm that the absorbance spectrum does become a horizontal line at 0 AU. The shape of the absorbance spectrum when sampling depends primarily on the concentrations of H2S and SO2 in the sample. Other components are generally not present in high enough concentrations to be visibly recognizable on the absorbance spectrum. Figures 36 and 37 show the typical appearance of absorbance spectra for H2S only and SO2 only. Figure 36: Absorbance Spectrum for H2S Figure 37: Absorbance Spectrum for SO2 In most typical operating conditions, the tail gas stream will not contain only H2S or only SO2, so typically the displayed absorbance spectrum will appear as a combination of the H2S spectrum and the SO2 spectrum, as shown in the spectrum in Figure 35. The exact magnitude of the absorbance for a given species will depend on the concentration of that species as well as the measurement cell length. For a given analyzer, however, the higher the concentration of the measured species is, the higher the absorbance (i.e. peak height) will be for that species. Revision 5 58 August 2021 The concentrations shown below the absorbance spectrum are calculated by using a calibration matrix specific to the analyzer’s spectrometer to mathematically convert the absorbance spectrum into concentration values. For more information on the calibration matrix, refer to Section 5.2.2. 4.8 Config Panel The Configuration panel is used to configure a broad range of analyzer operating parameters. It has a total of 5 sub-panels, each of which is used to configure a certain type of operating parameters. To change from one sub-panel to the next, press the PANEL NEXT or PANEL PREV keys on the keypad. Note that pressing PANEL NEXT from the right most sub-panel (Network) will return to the Analysis 1 tab and pressing PANEL PREV from the left-most subpanel (Outputs) will go back to the Absorbance panel. Unauthorized modification of the values of many of the parameters available in the Config panel could result in the analyzer becoming unable to function correctly. The parameters on this panel should ONLY be changed by factory-trained personnel or under the direction of Galvanic Applied Sciences Inc. 4.8.1 Outputs The Outputs sub-panel shown in Figure 38 is used to configure the four analyzer analog outputs Figure 38: Outputs Sub-Panel There is a total of four analog outputs that can be set up. To access a specific analog output, use the FIELD NEXT / FIELD PREV keys to highlight the Select Analog Output: button, Revision 5 59 August 2021 then press ENTER to move to the next analog output. When on Analog Output 4, pressing this button again will move back to Analog Output 1. The configuration options available for all four analog outputs are identical. The output parameters available are listed in Table 12. Table 12: Analog Output Parameters Parameter None Air Demand H2S %, SO2 %, COS %, CS2 % Sigma S H2S/SO2 Ratio H2 / Analog Output 3 H2S ppm, SO2 ppm, COS ppm, CS2 ppm Description No data will be output on the analog output. The Air Demand value will be output on the analog output. Scale ranges from negative Full Scale (4 mA) to positive Full Scale (20mA) The percentage value of the H2S or SO2 or COS or CS2 concentration will be output on the analog output. Scale ranges from 0 (4 mA) to Full Scale (20 mA) The sum of the H2S and SO2 concentrations, in percent, will be output on the analog output. Scale ranges from 0 (4 mA) to Full Scale (20 mA) The ratio of H2S concentration to SO2 concentration will be output on the analog output. Scale ranges from 0 (4 mA) to Full Scale (20 mA) The signal being input into Analog Input 3 (from a hydrogen sensor or other measurement device that outputs an analog signal) will be output on the analog output. Scale ranges from 0 (4 mA) to Full Scale (20 mA) The parts per million value of the H2S or SO2 or COS or CS2 concentration will be output on the analog output. PPM concentration is obtained by multiplying the percentage concentration by 10 000, so full scale should be chosen accordingly. Scale ranges from 0 (4 mA) to Full Scale (20 mA). The full-scale value for the analog output can be entered into the Full Scale field by highlighting it using the FIELD NEXT / FIELD PREV keys, then pressing ENTER to enter data entry mode. Enter in the desired full-scale value, then press ENTER again to save. Press EXIT to discard any changes. Above the Full Scale field are two check boxes marked Track and Hold. When Track is selected, the analog output value will track with the displayed concentration value even when the analyzer is in back purge mode; hence, when Track is selected, during zero calibration cycles and any other times when the analyzer is placed into back purge mode, the signal output to the DCS will be zero. When Hold is selected, the analog output value will hold the last good process value any time the analyzer switches into back purge mode until the analyzer is back on line in sampling mode; in this way, the analog output will never drop to zero even during zero calibration cycles or other times the analyzer is placed into back purge mode. Highlight the desired analog output behaviour by using the FIELD NEXT / FIELD PREV keys to highlight the desired choice, then pressing ENTER to select. After making any changes on this sub-panel, it will be necessary to save them permanently to the analyzer. Use the FIELD NEXT / FIELD PREV keys to highlight the Save button in the bottom right-hand corner of the sub-panel, then press ENTER to save changes to the analyzer. Alternatively, to revert all changes made on this sub-panel, use the FIELD NEXT / FIELD PREV keys to highlight the Revert button and press ENTER to confirm. Revision 5 60 August 2021 4.8.2 Calculation Sub-Panel The Calculation sub-panel shown in Figure 39 is used to set a variety of parameters that are related to the calculation of analysis results by the control computer. Figure 39: Calculation Sub-Panel To edit any parameter on this page, use the FIELD NEXT / FIELD PREV keys to highlight the desired parameter, then press ENTER to enter the editing dialog. Use the numerical keys and the decimal point key to enter in the desired value, then press ENTER. Select the Okay button and press ENTER again. Once all desired edits have been completed, select the Save button at the bottom right of the screen and press ENTER to save changes permanently. Alternatively, selecting Revert and pressing ENTER will return all edited values to their previously saved values. Unauthorized modification of the values of ANY of the calculation parameters listed in on this sub-panel could negatively affect the validity of data output by the analyzer. Calculation-related parameters should ONLY be changed by factorytrained personnel or under the direction of Galvanic Applied Sciences Inc. 4.8.2.1 Calculation Parameters The calculation parameters outlined in red are explained in Table 13. Revision 5 61 August 2021 Table 13: Calculation Parameters Parameter Normal Value Explanation Plant factor term used in the Air Demand calculation (Section 1.1). Gain term applied to the air demand output to adapt the process variable (Air Demand) to the plant’s front-end air adjustment capability. Defined by the equation below: 𝑃𝑃𝑃𝑃 = Plant Factor -3 Operating Ratio 2 H2S, SO2 Span ≈1 COS, SVAP, CS2 Span 1 (if used); 0 (if not used) 4.8.2.2 −𝑄𝑄𝑡𝑡𝑡𝑡 × 100 [𝐻𝐻2 𝑆𝑆]𝑎𝑎𝑎𝑎 × 𝑄𝑄𝑎𝑎𝑎𝑎 Where: • PF = Plant Factor • Qtg = Typical tail gas flow rate (moles per unit of time) • [H2S]ag = Typical molar concentration of H2S in acid gas feed stream • Qag = Typical acid gas feed stream flow rate (moles per unit of time) Once the plant factor has been established for a given process, the units of air demand become % Excess Air, so a positive air demand means that the air input to the furnace should be reduced and negative air demand means that the air input to the furnace should be increased. Stoichiometric ratio of H2S to SO2 at which the air demand becomes zero (i.e. no change required to input air), regardless of the numerical value of the plant factor term. In a standard Claus Process sulfur recovery unit, the optimal ratio is 2:1, however other sulfur recovery unit processes may use different ratios. Span factor applied to the calculated concentration of H2S, SO2 prior to being displayed on analyzer screen and output on analyzer outputs. Can be used to make fine adjustments to analyzer calibration. Span factor applied to the calculated concentration of COS, sulfur vapour, CS2 prior to being displayed on analyzer screen and output on analyzer outputs. If set to zero (default for COS and CS2) displayed concentrations will be zero. Cell Length The Cell Length parameter specifies the length of the measurement cell in centimetres (cm). The cell length is measured from the inside surface of one cell window to the inside surface of the other cell window. According to the Beer-Lambert law, the absorbance of a sample gas is directly proportional to the path length of light passing through that sample gas, so the cell length is a necessary parameter for calculation of the absorbance and thus the concentration of the species of interest. The cell length for a given analyzer is determined by the required measuement range for that analyzer; the higher the required measurement range, the shorter the cell length will be. Cell lengths can vary from as short as 1 cm to as long as 15 cm. The specific cell length for a given analyzer is indicated on the analyzer’s factory QC documentation. Revision 5 62 August 2021 4.8.2.3 Fixed Temperature and Pressure The calculated concentrations are compensated for both temperature and pressure. Typically, this temperature and pressure compensation uses the live values from the analyzer’s cell temperature and pressure measurement sensors. However, there is also the capability to use static values of temperature and pressure for this compensation. To use a Fixed Temperature and / or a Fixed Pressure value for compensation of concentration values, use the FIELD NEXT / FIELD PREV keys to highlight the checkbox of the fixed value to be used, then press ENTER to place an X in the box. 4.8.2.4 Sample and Zero Sample Rate The values shown in the Sample Rate and Zero Sample Rate fields determine how frequently the analyzer updates the displayed concentrations and air demand when the analyzer is in sampling mode (Sample Rate) and in back purge mode (Zero Sample rate). The time values entered in these two fields are in units of milliseconds. The default value for each sampling rate is 500 ms. 4.8.3 Display The Display sub-panel, shown in Figure 40, allows the user to configure certain parameters that affect how data is displayed on the analyzer’s local display screen. Figure 40: Display Sub-Panel 4.8.3.1 Analysis 1 and 2 Trend Graph Ranges The displayed x and y axes for the trend graphs shown on the Analysis 1 and Analysis 2 panels can be configured by the user on this panel using the Analysis 1/2 X Range and Analysis 1/2 Y Range data entry fields. The Y ranges are concentrations, affecting the displayed vertical ranges on the Air Demand trend on the Analysis 1 panel and the Component concentration trends on the Analysis 2 panel. These scales can be adjusted if any of the trend lines are found to be commonly going off of the currently displayed scale. The X ranges are time, affecting the amount of time represented by the displayed Revision 5 63 August 2021 trend lines. The maximum time range that can be displayed on the trend graphs on both panels is fifteen minutes. Changing the displayed scale on the Analysis 1 / Analysis 2 trend graphs does NOT change the scale on the analog outputs for these parameters. These scales are for display purposes ONLY and have no effect on any other aspect of the analyzer operation. To edit any of these parameters, simply highlight the field for the parameter to be edited using the FIELD PREV / FIELD NEXT keys, then use the numerical keys and decimal point key to enter the desired value and press ENTER again. Alternatively, the up or down arrows beside the data entry field can be highlighted using the FIELD PREV / FIELD NEXT keys, and then the ENTER key can be continuously pressed until the desired value is obtained. 4.8.3.2 Backlight Adjustment The intensity of the analyzer display’s backlight can be adjusted on this sub-panel. Simply use the FIELD NEXT / FIELD PREV keys to highlight either the More (brighter) or Less (dimmer) buttons, then press the ENTER Key continually until the display brightness is adjusted the desired level. When the slider is at the left-most position, the display backlight is completely off, and when at the right-most position the backlight is turned on to 100% power. Once all desired changes have been made on the Display sub-panel, use the FIELD NEXT / FIELD PREV keys to highlight the Save button, then press ENTER to save all changes permanently to the analyzer. Alternatively, select the Revert button and press ENTER to revert all changes made since the last time the Save button was pressed. 4.8.4 Timers/Alarms Sub-Panel The Timers/Alarms sub-panel shown in Figure 41 is used to configure a variety of parameters related to timers, temperature control, and alarm setpoints. Figure 41: Timers / Alarms Sub-Panel Revision 5 64 August 2021 To edit a parameter on this sub-panel, use the FIELD NEXT / FIELD PREV keys to highlight the parameter to be edited, then press ENTER to bring up the data entry dialog box. Enter the desired value for the parameter using the numerical keys and the decimal point key, then press ENTER to save. When all desired changes have been made, use the FIELD NEXT / FIELD PREV keys to highlight Save, then press ENTER to save all changes permanently to the analyzer. Alternatively, highlight Revert, and press ENTER to revert all changes made since the last time the Save button was pressed. 4.8.4.1 Timers The parameters in the orange Timers box are described in Table 14. Table 14: Timers Parameters Parameter Normal Value Auto Cal Interval 240 (min) Zero Purge Interval ≥15 (sec) Zero Hold Interval ≥30 (sec) 4.8.4.2 Explanation The time period that elapses between subsequent zerocalibration cycles. The interval is timed from the completion of the previous calibration cycle, regardless of whether that calibration cycle was automatically or manually initiated. The maximum value is 16666.7 min. The minimum value is zero, in which case the automatic zero calibration function is disabled. The automatic zero calibration will NOT run when there are any fault conditions present. The time period that elapses after the analyzer is placed into back purge mode for a zero calibration cycle (either manual or automatic) prior to the initiation of the zero calibration cycle. This value should be at least 10 seconds longer than the minimum amount of time required to completely purge the measurement cell of all sample gas and fill it completely with zero gas. The final 10 seconds of this interval are used to collect zero data used in the calculation of the new zero baseline. The exact value of this parameter will depend on a variety of analyzer conditions, including but not limited to probe length and zero gas pressure / flow rate. The amount of time the analog outputs and relay outputs are held in the calibration state after the completion of the new zero baseline calculation. During this time period, sample gas is drawn through the measurement cell by the aspirator, and measured concentration values climb up to normal process values. At the completion of this interval, the analog outputs are begin to update as normal, and the relay outputs are returned to normal on-line state. The exact value of this parameter will depend on a variety of analyzer conditions, including but not limited to probe length and aspirator drive air pressure / flow rate. Temperature Control The parameters in the green Temp. Control box are described in Table 15. Revision 5 65 August 2021 Table 15: Temperature Control Parameters Parameter Normal Value Cell Setpoint 150°C Cell Prop Band 1.0% Cabinet Setpoint 35°C Cabinet Deadband ≥3°C Probe Setpoint ≈110°C Probe Deadband ≥3°C Revision 5 Explanation Temperature control setpoint for the measurement cell. The setpoint for the cell MUST be set well above the condensation point of sulfur vapour (≈120°C) to avoid plugging due to accumulation of liquid sulfur inside the analyzer sample handling system. Proportional term of the measurement cell electric heater PID temperature control algorithm. Temperature control setpoint for the interior of the analyzer control cabinet. If the control setpoint is exceeded, the cabinet cooling air solenoid energizes, providing air flow to the control cabinet vortex cooler. Control cabinet temperature set point deadband. Indicates the number of degrees BELOW the control cabinet temperature setpoint the temperature must drop before switching off the cabinet cooler cooling air flow. A larger number will reduce the number of actuation cycles for the cabinet cooler solenoid, potentially extending its useful life. Temperature control setpoint for the sample gas exiting the probe. If the temperature of the gas exiting the probe into the analyzer sample system exceeds this temperature, the probe cooler solenoid activates and the probe cooler switches on. NOTE: This parameter is only active when the Control with RTD function is selected in the Web GUI (refer to section 5.4). Probe temperature setpoint deadband. Indicates the number of degrees BELOW the probe setpoint the probe gas temperature must drop before switching off the probe cooler air flow. A larger number will reduce the number of actuation cycles for the probe cooler solenoid, potentially extending its useful life. NOTE: This parameter is only active when the Control with RTD function is selected in the Web GUI (refer to section 5.4). 66 August 2021 4.8.4.3 Alarms The parameters in the red Alarms box are described in Table 16. Table 16: Alarms Parameters Parameter Normal Value Low Cell ≈135°C Low Probe ≈100°C High S8 Warn 0.5% High S8 Fault 0.75% Revision 5 Explanation Measurement cell fault temperature setpoint. If the cell temperature falls below this setpoint, a cell temperature fault will be activated, causing the Status relay to switch to Fault state and the Control relay to switch to Manual state. The low cell temperature fault setpoint should be set below the cell temperature setpoint but still well above the sulfur vapour condensation temperature of ≈120°C to ensure that the analyzer will go into fault before the temperature is low enough to cause sulfur vapour to condense in the analyzer sample system. There is a 3°C deadband on this setpoint. If the cell temperature rises to more than 3°C above this setpoint, and no other fault conditions exist, the analyzer will then perform a zero calibration cycle and then return to normal operation. Probe temperature fault temperature setpoint. If the probe temperature falls below this setpoint, a probe temperature fault will be activated, causing the Status relay to switch to Fault state and the Control relay to switch to Manual state. There is a 3°C deadband on this setpoint. If the probe temperature rises to more than 3°C above this setpoint, and no other fault conditions exist, the analyzer will then perform a zero calibration cycle and then return to normal operation. NOTE: This alarm is only active the Control with RTD function is selected in the Web GUI (refer to section 5.4). Sulfur vapour concentration warning setpoint. If the sulfur vapour rises above this concentration, a sulfur vapour warning will be triggered in the analyzer and the Service relay will switch to the Warning state. Sulfur vapour above this concentration could start to interfere with the measurement of H2S and SO2, causing a decrease in sensitivity. Sulfur vapour concentration fault setpoint. If the sulfur vapour rises above this concentration, a sulfur vapour fault will be triggered in the analyzer and the Status relay will switch to Fault and the Control relay will switch to Manual. This fault can only be cleared once the sulfur vapour content in the sample gas drops below the setpoint. Sulfur vapour concentrations exceeding this setpoint are likely to result in sulfur plugging the probe and/or analyzer sampling system. 67 August 2021 4.8.5 Network Sub Panel The Network sub-panel shown in Figure 42 is used to view the network settings for the local Ethernet connection and view/edit the network settings for the remote Ethernet connection. Figure 42: Network Sub-Panel 4.8.5.1 Direct Connect The Direct Connect box shows the network parameters for the local Ethernet port on the front door of the analyzer’s control cabinet, below the display screen. The Ethernet port on the analyzer’s door is used for connecting a laptop computer to the analyzer with an Ethernet cable locally. The IP Address field shows the analyzer’s IP address for use when the analyzer is connected to a local PC, and is not editable by the user. This value is entered into the navigation bar of a web browser running on the local PC and is used to access the analyzer’s web-based graphical user interface (GUI). Refer to Section 5 for more details. The Netmask and MAC Address fields show other network related parameters. The Status field shows the current status of the network connection. If there is no computer connected to the analyzer, it will read Inactive. If there is a computer connected to the analyzer, it will read Active and one of the two green Ethernet Speed LEDs below the display (either 1000Mb/s or 100Mb/s depending on the connected computer’s hardware) will illuminate. 4.8.5.2 Network The Network box shows the network parameters for the analyzer when it is not directly connected to a local PC but rather connected to a remote PC via the plant’s local area network (LAN). The Ethernet port used for LAN connections, either via the web GUI (Section 5) or Modbus TCP/IP, is on the right side of the analyzer’s controller board Revision 5 68 August 2021 mounted on the inside of the control cabinet door, behind the analyzer display. The location of the Ethernet port on the controller board is shown in Figure 43. Figure 43: Controller Board The Ethernet cable connecting from the analyzer to the plant’s LAN can be connected to the indicated port (the other port is used to connect from the controller board to the Ethernet port on the analyzer control cabinet door). When the connection is established between the analyzer and the LAN, a solid green LED will illuminate inside the port below the cable, and a blinking orange LED will illuminate inside the port above the cable indicating data transfer is occurring. One of the two Ethernet Speed LEDs below the analyzer display (either 1000Mb/s or 100Mb/s depending on LAN hardware) will also illuminate, and the Status field in the Network box will show Active. If the plant’s LAN can automatically assign an IP Address, Netmask, Gateway, and Name Servers to the analyzer when it is connected to the LAN, the type of network chosen should be DHCP. Use the FIELD NEXT / FIELD PREV keys to highlight DHCP, then press ENTER to place an X in the checkbox. The analyzer will then automatically be assigned the relevant network parameters and the fields will then populate. If the plant’s LAN cannot automatically assign the necessary network parameters when the analyzer is connected to the LAN, it will be necessary to input them manually. Use the FIELD NEXT / FIELD PREV keys to highlight Manual, then press ENTER to place an X in the checkbox. The IP Address, Netmask, Gateway, and Name Servers fields will then become editable. Obtain the correct values for these parameters from the plant’s IT department, then use the numerical keys and decimal point key to enter these parameters into the analyzer. Once all changes have been made, use the FIELD NEXT / FIELD PREV keys to highlight the Apply button, then press ENTER to save changes. Once the analyzer has a correct IP address and other parameters assigned, it will be possible to connect to the analyzer from anywhere within the plant’s LAN by using the IP address. Revision 5 69 August 2021 Section 5 5.1 Web-based Graphical User Interface (GUI) Overview The Model 943-TGXeNA Tail Gas Analyzer can be monitored, configured and controlled by use of a web-based GUI on a personal computer connected to the analyzer via an ethernet connection, either as a direct local connection or remotely through the plant’s local area network (LAN). The necessary IP address for each type of connection is indicated in the Config panel’s Network sub-panel as described in Section 4.8.5. Once the PC is physically connected to the analyzer via an Ethernet connection, and either the remote or local connection is shown on the analyzer display as Active, simply type in the IP address of the active connection into the navigation bar of a web browser running on the connected computer. While other browsers may also be able to succesfully access the web GUI, for best results Galvanic Applied Sciences recommends the use of Mozilla Firefox. Any changes that are made to the analyzer configuration via the web GUI and saved to the analyzer will be displayed on the analyzer’s local display. After entering in the IP address to the web browser navigation bar and pressing Enter, the web GUI splash screen shown in Figure 44 will be displayed. Figure 44: Brimstone Web GUI Splash Screen Once the web GUI has finished loading, the Analysis page described in Section 5.2.1 is shown. The Brimstone web GUI is divided into two sections – a Navigation menu shown in Figure 45 on the left and an information page on the right. The Navigation menu is used to navigate through the various available information pages. Revision 5 70 August 2021 Figure 45: Navigation Menu and Tips The Navigation menu is divided into four sections: Analysis, Configuration, Factory, and Help. Each of these sections may have several data display pages. The information pages for a given section can be displayed by pressing the (+) sign to the right of the section name. Note that only one section can be expanded at a time; expanding a different section of the Navigation menu will collapse any previously expanded sections. After clicking on a specific information page to access it, a list of tips associated with the displayed information page will be displayed on the left side of the window, below the navigation window. These tips will provide information on how to interpret, interact with, and/or modify the data displayed in the information window. 5.2 5.2.1 Analysis Section Analysis Page The Analysis page shown in Figure 46 displays information and controls that mirror the data and controls shown on the analyzer’s local display Analysis 1 and Analysis 2 panels. Revision 5 71 August 2021 Figure 46: Analysis Section - Analysis Page The Analysis page is divided into 5 sections, each displaying different information. 5.2.1.1 Value Display The Value Display section displays concentration data, calculated analysis data, and analyzer parameter as described in Table 17. Table 17: Value Display Parameters Parameter Air Demand H2S SO2 COS CS2 Sulfur Vapour Cell Pressure Cell Temperature Probe Temperature Cabinet Temperature Revision 5 Description Present air demand, in % excess air based on currently measured H2S and SO2 concentrations, calculated as per equation in Section 1.1. Present calculated concentration of H2S in percent Present calculated concentration of SO2 in percent Present calculated concentration of COS in percent Present calculated concentration of CS2 in percent NOTE: CS2 is an optional measurement. Only analyzers configured with this option will be capable of measuring CS2 Present calculated concentration of sulfur vapour in percent Present measured pressure inside the sample measurement cell in mmHg Present measured concentration of the measurement cell block assembly in °C Present measured temperature of the sample gas exiting the probe in °C The present measured temperature of the interior of the analyzer’s control cabinet in °C. 72 August 2021 The values displayed in this section are live values and cannot be edited. The associated setpoints and alarm setpoints for the pressure and temperature values can be edited in the Configuration section’s Parameters page. Refer to Section 5.3.1. 5.2.1.2 Status and Control This section displays indicators indicating general status of the analyzer as well as controls that can be used to manually control certain aspects of the analyzer operation. The status indicators and controls shown in this section are described in Table 18. Table 18: Status and Control Indicator / Control Online Status Sample / Backpurge Sample Backpurge Manual Zero 5.2.1.3 Description Shows the current online status of the analyzer. • Solid Green – Online: Analyzer is online. Analyzer considers output values to be valid. • Flashing Red – Offline: Analyzer is offline. Analyzer considers output values to be invalid, as during analyzer maintenance. Control relay is set to Manual. Online status does not affect operation of analyzer, but rather exists as a convenience to operator as a remote indication that the analyzer data is valid or invalid. NOTE: Online status can ONLY be changed locally using the keypad. Refer to Section 4.3.1 Shows the current sampling status of the analyzer: • Solid Green – Sample: Analyzer is in sampling mode analyzing process sample gas • Flashing Red – Back purge: Analyzer sample system is being purged with zero gas, as during zero calibration cycle, manual back purge, or fault state back-purge. Pressing this button will place the analyzer in sampling mode if currently in back-purge mode. NOTE: Analyzer can only be placed into sampling mode if no fault conditions are present. Pressing this button will place the analyzer in back purge mode if currently sampling. NOTE: Analyzer should be placed into back-purge mode prior to carrying out any maintenance on the analyzer itself OR on the sulfur recovery unit in which it is installed. Pressing this button will switch the analyzer automatically to back purge mode (if currently sampling) and carry out a zero calibration cycle as described in Section 4.3.4. NOTE: Analyzer can only carry out a zero calibration cycle if there are no fault conditions currently present. Relay Indicators This section displays the current status of the analyzer’s four digital (relay) outputs, which are used to provide an indication of the status of various aspects of the analyzer operation. A basic overview of the four relay indicators is given in Table 19; for a more complete discussion of the function of these four relay outputs refer to Section 3.3.2. Revision 5 73 August 2021 Table 19: Relay Indicators Relay Indicator Status Service Mode Control 5.2.1.4 Description Shows the current state of the Status relay. • Solid Green – Normal: No fault conditions noted in any of the parameters monitored by the analyzer. Analyzer can analyze process sample. • Flashing Red – Fault: At least one fault condition is noted in the parameters monitored by the analyzer. Analyzer is incapable of analyzing process sample until all current fault conditions are cleared. Shows the current state of the Service relay • Solid Green – Normal: No warning conditions noted in any of the parameters monitored by the analyzer. If Status relay is also green, no maintenance is currently required, and analyzer condition is completely normal. • Flashing Red – Warning: At least one warning condition noted in parameters monitored by the analyzer. If Status relay is green, analyzer is still capable of analyzing process ample, but maintenance should be scheduled as soon as possible to resolve warning condition. Shows the current state of the Mode relay • Solid Green – Run: Analyzer is not carrying out a zerocalibration cycle. If Status relay is also green, analyzer is currently monitoring process sample. • Flashing Red – Calibrate: Analyzer is currently carrying out a zero-calibration cycle, either automatically initiated by timed schedule, or manually initiated from keypad or web GUI. Shows the current state of the Control relay • Solid Green – Auto: Analyzer is currently in automatic control, which means that analyzer output signals can be considered valid values and can be used for plant control purposes if required. • Flashing Red – Manual: Analyzer is currently in manual control, either as a result of fault condition(s) being present, the analyzer being placed into Offline mode, or due to a zero-calibration cycle (manual or automatic) being in progress. Analyzer output signals should be deemed to be invalid and NOT used for plant control purposes. Air Demand and H2S/SO2 Trends The Air Demand Trend and H2S/SO2 Trend displays show the graphical trend in these results over the past 17 minutes. They are updated once ever second, and the latest reading is at the extreme right of the each of the trend lines. The shaded areas shown above and below the trend lines in Figure 46 indicates the distance between the current trend line and the zero baseline. The colour code of the trend lines is the same as the colour code of the numerical data fields in the Value Display section. Revision 5 74 August 2021 The X-axis (time) for these trend graphs cannot be changed. However, should the data be found to be often off the scale, it is possible to change the y-axis (concentration) scale to ensure that all data is on the scale. To change the Y-axis scale, right click on the graph for which the scale is to be changed, then select Y-axis Range. The dialog box shown in Figure 47 will then appear. Figure 47: Trend Graph Y-Axis Range Change Dialog Box When the trend graph y-axis range is changed, the concentration range given in the trend header will change to reflect the new range. Changing the displayed scale on the Air Demand or H2S/SO2 trend graphs does NOT change the scale on the analog outputs for these parameters. These scales are for display purposes ONLY and have no effect on any other aspect of the analyzer operation. 5.2.2 Calibration Matrix Page The Model 943-TGXeNA uses a spectrometer that connects to the control computer via a USB connection for the collection of the spectrum data needed for the calculation of concentration values and the air demand value. The spectrometer is shown in Figure 48. Figure 48: Spectrometer Every spectrometer has a uniquely determined Calibration Matrix which allows the control computer to convert the spectrum data it reads from the spectrometer into measured concentration values for every measured component. The Calibration Matrix is a 12-column x 530 row (older versions of the analyzer firmware use a 9 column by 530 row) matrix that is Revision 5 75 August 2021 used in the linear algebraic calculations that produce the displayed concentration values. The Calibration Matrix page of the Analysis section in the web GUI, shown in Figure 49, allows the user to look at the calibration matrix being used by the analyzer. Figure 49: Calibration Matrix Each spectrometer’s unique calibration matrix is determined by Galvanic Applied Sciences Inc. during the production of the analyzer in which it is incorporated. The calibration matrix is determined by incorporating the molar absorptivity data of the gases to be measured with the specific spectral resolution and sensitivity characteristics of that spectrometer. The Calibration Matrix page allows the user to determine whether the installed calibration matrix is correct for the installed spectrometer by comparing the displayed calibration matrix with the calibration matrix file that is associated with the spectrometer’s unique serial number. The serial number of each spectrometer is found on the body of the spectrometer, as visible in Figure 48. As the calibration matrix is unique to a given spectrometer, if at any time an analyzer’s spectrometer requires replacment, a new calibration matrix for that spectrometer must be installed onto the analyzer’s computer. Refer to Section 7.10 for the procedure to upload a calibration matrix to the analyzer. 5.2.3 Indicators Page The Indicators page shown in Figure 50 shows almost the same information as the Indicators panel on the analyzer’s local display, with the addition of two additional faults and one additional warning. Revision 5 76 August 2021 Figure 50: Indicators Page The specific faults shown on the Indicators page are listed in Table 20. Table 20: Analyzer Faults Fault Measure Out of Range Reference Out of Range Dark Out of Range Low Cell Temperature High Cell Temperature Low Probe Temperature High Probe Temperature IO Board Explanation Spectrometer signal is out of range while analyzer is measuring sample (signal either off scale or too low) Spectrometer signal is out of range while analyzer is in back purge mode (signal either off scale or too low) Spectrometer dark level (i.e. signal when no light is present) is either too low or too high Measurement cell temperature is below low cell temperature fault setpoint Measurement cell temperature is above high cell temperature fault setpoint Temperature of gas exiting the probe is below the low probe temperature setpoint Temperature of gas exiting the probe is above the high probe temperature setpoint Control computer is unable to communicate with the IO board or spectrometer Some of these faults may clear by themselves but others may require maintenance or even hardware replacement to resolve. Refer to Section 7.2 for more detail on how to troubleshoot active faults. Table 21 describes each of the warnings listed int the warning table on the Indicators page. Revision 5 77 August 2021 Table 21: Analyzer Warnings Warning Low Cabinet Temperature High Cabinet Temperature Low Reference Peak High Integration Period High Absorbance High Sulfur Vapour Explanation Control cabinet internal temperature is below low cabinet temperature setpoint Control cabinet internal temperature is above high cabinet temperature setpoint Spectrometer signal peak height when analyzer is in back purge mode <24000 A/D counts Integration period required to obtain an in-range spectrometer signal when analyzer is in back purge mode > 500 milliseconds. Measured absorbance >2.0AU when analyzer is in sampling mode. Measured sulfur vapour content exceeds high sulfur vapour concentration warning setpoint Some of these warnings may clear by themselves but others will not be able to be cleared without performing maintenance on the analyzer. Refer to section 7.2 for more detail on how to troubleshoot active warnings. 5.2.4 Spectrum Page The Spectrum page shown in Figure 51 shows identical information to the Spectrum panel on the analyzer’s local display. Figure 51: Spectrum Page The Spectrum Curve, or transmission spectrum, displayed on this page shows the intensity of light measured at each of the 2048 pixels of the spectrometer. The exact X (pixel number) and Y (A/D counts) coordinates of each data point on the curve can be determined by placing the mouse cursor over the data point of interest. The Y-axis scale can be adjusted by clicking on the Change Spectrum Curve Display Y Axis button. The Y-Axis Maximum Value dialog box shown in Figure 52 will then appear. Revision 5 78 August 2021 Figure 52: Spectrum Curve Y-Axis Maximum Value Dialog Box Enter in the desired maximum value for the Y-Axis scale (the minimum will always be zero) and click on Save. Note that the normal maximum peak height for the spectrum curve is around 28000-29000 A/D counts when the analyzer is in back-purge mode. The displayed spectrum is updated once per second; to change to a static spectrum simply place a checkbox into the Stop Polling checkbox. Once changed to a static spectrum, a specific section of the X-axis can be zoomed into by left clicking and holding on the desired starting pixel then dragging the green highlight that appears to the desired end pixel. After releasing the left mouse button, the selected pixel range will expand to fill the whole graph field. The zoomed in section will also be shown in green the Panorama View field, which shows an overview of the entire collected spectrum. To return to the full spectrum, left click and hold at the left side of the Panorama View field and drag the green area all the way the right side, and the Spectrum Curve view will return to the full spectrum. To save the displayed spectrum to a CSV file on the connected PC, click on the Save Spectrum button and saving to the desired filename. There are four numerical parameters displayed at the bottom of the Spectrum Page. These parameters are described in Table 22. Table 22: Spectrum Parameters Parameter Spectrum Peak First Vector Pixel Level Dark Level Integration Time Explanation Displays the peak height of the spectrum, in A/D counts. Should be approximately 28000-29000 when analyzer is in back purge mode. Displays the intensity of light being received at the first vector pixel, in A/D counts. The first vector pixel is the first pixel that is used for calculating concentration values. Displays the intensity of light being received when the spectrometer is dark (i.e. no light present). This value should be in a range between 400 and 900 A/D counts. The integration time, or integration period, is the duration of time that light is collected by the pixels of the spectrometer before being read by the control computer. For example, in Figure 50 the integration time is given as 123.69 milliseconds. This means that the light incident on the spectrometer pixels can accumulate for 123.69 milliseconds before being read by the control computer; the spectrometer pixels are then zeroed and allowed to collect light again. The displayed transmission spectrum, then, shows the intensity of light collected at every pixel in this time period. Maximum value 1000ms. The optimal integration time for the current analyzer conditions can be automatically calculated by clicking the Optimize Integration Time button. Once clicked, the control computer will adjust the integration time such that the peak height of the displayed spectrum reads approximately 28000 A/D counts. If this peak height cannot be achieved even with a maximum integration time of 1000 ms, this indicates a problem with the analyzer’s optical system. Refer to section 7.2 for details on how to troubleshoot analyzer problems. Revision 5 79 August 2021 Optimizing the Integration Time should ONLY be performed when the analyzer is in back purge mode. Attempting to optimize the integration time when the analyzer is in sampling mode may negatively affect the analyzer baseline, and thus the analyzer’s analytical results. As an alternative to automatically optimizing the integration time, the operator may choose to manually adjust the integration time instead. Click on the Set Integration Time button, and the Set Integration Time dialog box shown in Figure 53 will appear. Figure 53: Set Integration Time Dialog Box Enter the desired integration time (range between 1 and 1000ms) into the field, then press OK. After manually editing the Integration Time, check the indicated Spectrum Peak. If the spectrum peak displays 32000, this indicates that the peak height is off scale, as the full scale for the spectrometer reading is 32000 A/D counts. The integration time should be reduced until the indicated peak height drops below 32000. If the indicated spectrum peak is less than 24000, the integration time should be increased. If the integration time is already at 1000 ms, this indicates a problem with the analyzer’s optical system. Refer to Section 7.2 for more details on troubleshooting the analyzer’s optical system. When the Display Factory Reference checkbox is checked by clicking on it, the factory reference spectrum is shown superimposed on the same axes as the currently displayed spectrum. Take note of the following rules-of-thumb when comparing the pink trace of the factory reference with the red trace of the current transmission spectrum: • The factory reference should be largely similar to the current transmission spectrum when the analyzer is in back purge mode. If it is not, there is likely an issue with the analyzer optical system. Refer to Section 7.2 for troubleshooting techniques. • The factory reference should be notably different from the current transmission spectrum when the analyzer is in sampling mode. If the sampling spectrum is the same or very similar to the factory reference, this could indicate an issue with plugging in the sample probe. Refer to Section 7.9 for troubleshooting of sampling problems. The New Reference button is used to make the analyzer use the currently displayed transmission spectrum to calculate a new zero baseline without carrying out a full zero calibration cycle. Clicking New Reference DOES NOT cause the analyzer to automatically go into back purge mode. Be sure the analyzer is in back purge mode prior to using this function otherwise the calculated analyzer results after calculating the new reference WILL NOT BE VALID! 5.2.5 Absorbance Page The Absorbance page shown in Figure 54 shows identical information to the Absorbance panel on the analyzer’s local display. Revision 5 80 August 2021 Figure 54: Absorbance Page The Absorbance Curve, or absorbance spectrum, shown on this page shows the absorbance of the gas in the measurement cell, in absorbance units (AU) across the range of 530 spectrometer pixels that are used by the analyzer for analysis. The exact X (pixel number) and Y (AU) coordinates of each data point on the curve can be determined by placing the mouse cursor over the data point of interest. The Y-axis scale can be adjusted by clicking on the Change Absorbance Curve Display Y Axis button. The Y-Axis Maximum Value dialog box shown in Figure 55 will then appear. Figure 55: Absorbance Curve Y-Axis Maximum Value Dialog Box Enter in the desired minimum and maximum values for the Y-Axis scale and click on Save. Note that the normal absorbance curve will rarely go above 1.5 AU or drop below 0 AU. The displayed spectrum is updated once per second; to change to a static spectrum simply place a checkbox into the Stop Polling checkbox. Once changed to a static spectrum, a specific section of the X-axis can be zoomed into by left clicking and holding on the desired starting pixel then dragging the green highlight that appears to the desired end pixel. After releasing the left mouse button, the selected pixel range will expand to fill the whole graph field. The zoomed in section will also be shown in green the Panorama View field, which shows an overview of the entire collected spectrum. To return to the full spectrum, left click and hold at the left side of the Panorama View field and drag the green area all the way the right side, and the Absorbance Curve view will return to the full absorbance spectrum. The absorbance spectrum is calculated by subtracting the current transmission spectrum from the transmission spectrum that was obtained the last time the analyzer carried out a zero calibration cycle OR when the New Reference button was pressed on the Spectrum panel, whichever was most recent. The y-axis of this spectrum is absorbance units (AU). When the analyzer is in back purge mode, the absorbance spectrum should be a horizontal Revision 5 81 August 2021 line at an absorbance of 0 AU. If it is not, and the analyzer is NOT in a fault condition, first confirm that the current transmission spectrum in back purge is largely similar to the factory reference spectrum, then immediately carry out a new zero calibration cycle OR use the New Reference function on the Spectrum panel. After the zero-calibration cycle is complete, confirm that the absorbance spectrum does become a horizontal line at 0 AU. The shape of the absorbance spectrum when sampling depends primarily on the concentrations of H2S and SO2 in the sample. Other components are generally not present in high enough concentrations to be visibly recognizable on the absorbance spectrum. Figures 56 and 57 show the typical appearance of absorbance spectra for H2S only and SO2 only. Figure 56: Absorbance Spectrum for H2S Figure 57: Absorbance Spectrum for SO2 In most typical operating conditions, the tail gas stream will not contain only H2S or only SO2, so typically the displayed absorbance spectrum will appear as a combination of the H2S spectrum and the SO2 spectrum. The exact magnitude of the absorbance for a given species will depend on the concentration of that species as well as the measurement cell length. For a given analyzer, however, the higher the concentration of the measured species is, the higher the absorbance (i.e. peak height) will be for that species. The concentrations shown below the absorbance spectrum are calculated by using a calibration matrix specific to the analyzer’s spectrometer to mathematically convert the Revision 5 82 August 2021 absorbance spectrum into concentration values. For more information on the calibration matrix, refer to Section 5.2.2. 5.3 Configuration Section The Configuration section consists of two pages that allow the user to configure many of the analyzer’s basic operating parameters as well as the Modbus output if required. 5.3.1 Parameters Page The Parameters page shown in Figure 58 shows a list of operational parameters that can be viewed or edited. Figure 58: Configuration Parameters Page The parameters given on this page are grouped together by colours which indicate the type of parameter they are. The colour grouping for the various parameters is given in Table 23. Table 23: Parameters Page Colour Code Background Colour Pink Blue Grey Green Revision 5 Type of Parameter Temperature-related parameters, including both control and fault / warning setpoints Parameters related to the analyzer’s analytical results Calibration cycle timing and spectrometer related parameters All other parameters that do not fit in any of the other groups. 83 August 2021 Many of the parameters on this page are also available for editing on the analyzer’s local display using the analyzer keypad, though not all of them are. Table 24 gives an overview of the parameters available for editing on this page. Table 24: Configuration Parameters Parameter Editable via Keypad Local Display Editing Location Y Config – Timers/Alarms Y Config – Timers/Alarms N N/A Y Config – Timers/Alarms Cell temperature PID control parameter N N/A Cell temperature PID control parameter Probe Temperature Set Point Y Config – Timers/Alarms Probe Temperature Dead Band Y Config – Timers/Alarms Y Config – Timers/Alarms Y Config – Timers/Alarms Y Config – Timers/Alarms Cabinet Temperature Dead Band Y Config – Timers/Alarms Low Cabinet Temperature Alarm N N/A High Cabinet Temperature Alarm N N/A High SVAP Warning Y Config – Timers/Alarms High SVAP Alarm Y Config – Timers/Alarms Cell Temperature Set Point Low Cell Temperature Alarm High Cell Temperature Alarm Cell Temperature Proportional Band Cell Temperature Reset Time Low Probe Temperature Alarm High Probe Temperature Alarm Cabinet Temperature Set Point SVAP Set Point N N/A SVAP Dead Band N N/A Filter Points N N/A Auto Cal Intervall (min) Y Config – Timers/Alarms Revision 5 84 Explanation Control setpoint for analyzer’s measurement cell heaters. Cell temperature below which a cell temperature fault will be triggered Cell temperature above which a cell temperature fault will be triggered Control setpoint for probe cooler solenoid actuation NOTE: Only if probe control is set to RTD Number of degrees below probe temperature setpoint measured probe gas temperature must drop prior to probe cooler solenoid turning off NOTE: Only if probe control is set to RTD Probe gas temperature below which low probe temperature fault will be triggered Probe gas temperature above which high probe temperature fault will be triggered Control cabinet temperature above which the cabinet cooler will be turned on Number of degrees below cabinet temperature setpoint the cabinet temperature must drop prior to the cabinet cooler switching off Control cabinet temperature below which a cabinet temperature warning will be triggered Control cabinet temperature above which a cabinet temperature warning will be triggered. Sulfur vapour concentration above which a High Sulfur Vapour warning will be triggered Sulfur vapour concentration above which a high sulfur vapour fault will be triggered Sulfur vapour concentration above which the probe cooler will be turned on NOTE: Only if probe control is set to SVAP Amount the sulfur vapour concentration must drop below the set point before the probe cooler switches off NOTE: Only if probe control is set to SVAP Number of data points averaged together to produce the displayed concentration values Time interval from last zero calibration cycle (manual or automatic) to next scheduled auto zero calibration cycle. August 2021 Zero Purge (sec) Y Config – Timers/Alarms Zero Hold (sec) Y Config – Timers/Alarms Integration Time (ms) Y Spectrum Fixed Temperature (Enable) Y Config – Calculation Fixed Pressure (Enable) Y Config – Calculation Measure Analog Input 3 N N/A Analog Input 3 is Hydrogen N N/A Sample Rate Y Config – Calculation Zero Sample Rate Y Config – Calculation Time interval during a zero calibration cycle after switching to back purge and before calculating the new zero baseline Time interval during a zero calibration cycle after the analyzer has switched back to sampling mode and prior to the analyzer concentration outputs configured for Hold being updated again. Amount of time light is collected by spectrometer before the intensity is read to produce a spectrum Enable and select a fixed temperature value for temperature compensation of results NOTE: Live cell temperature value will be used for temperature compensation if this is not enabled. Enable and select a fixed pressure value for pressure compensation of results Note: Live cell pressure value will be used for pressure compensation if this is not enabled. Enable the measurement of a concentration sensor connected to Analog Input 3 on the IO Board. If enabled, this measurement will be displayed on the Analysis 2 panel of the local display. Enable the measurement of Hydrogen via a sensor connected to Analog Input 3 on the IO board. If this option and the previous option are enabled, this measurement will be displayed on the Analysis 2 panel of the local display. Rate at which the displays and output data are updated when the analyzer is in sampling mode Rate at which the displays and output data are updated when the analyzer is in back purge mode. When the page is first opened, it is opened in Read Only mode, which means that the values for the displayed parameters can only be viewed, not edited. To edit the parameters, first click on Change to Update Mode ( at the top right of the screen. The LOGIN dialog box shown in Figure 59 will then appear. Figure 59: Login Dialog Box Enter in the correct password, then click Login. To change a parameter: 1. Click on the parameter to be edited. The data entry field for that parameter will change to a white background. 2. Edit the parameter by typing in a new value. Some parameters such as Fixed Temperature Enable are non-numerical and can be edited by using the pull-down selection menu. 3. Once editing of the selected field is complete, press Enter on the keyboard. 4. Change any other parameters to be edited using the procedure in steps 1 to 3. Revision 5 85 August 2021 5. Once all necessary changes have been made, click on the Save to Unit button at the bottom of the screen to save all changes permanently to the analyzer. If it is necessary to cancel all changes made on this page, clicking Revert before clicking on Save to Unit will undo all changes made during that editing session. 5.3.2 Modbus Page The Modbus page shown in Figure 60 allows the user to configure Modbus output in one of three Modbus formats – Enron, Modicon-16, or Modicon-32. Figure 60: Modbus Page As there are many possible configurations for Modbus communication, this manual will only cover the basics. If the user requires assistance in configuring the Modbus for their specific application, the Service Department of Galvanic Applied Sciences Inc. will be able to assist. Contact the Service Department at [email protected] for more information. The bottom two lines of the Modbus page include several items that relate to communications parameters and numerical formats. The exact selection for each of these parameters will depend on the type of communication being used (RS485 or TCP/IP) as well as the specific DCS being used. These parameters are explained in Table 25. Revision 5 86 August 2021 Table 25: Modbus Communication Parameters Parameter IP Port Number Modbus Address 32 Bit Register Swap Mode Endian Baud Rate Data Bits Parity Stop Bits Explanation Port number to be used if the communication protocol being used is Modbus TCP/IP. Modbus address of the analyzer. This address needs to be entered into the DCS to allow the DCS to communicate correctly with the analyzer. If register swap is selected, the portion of the 32-bit register that follows the decimal point is transmitted in the first 16-bit word, and the portion that precedes the decimal point is transmitted in the second 16-bit word. If register swap is not selected, the portion that precedes the decimal point is transmitted first. NOTE: Only used if Modicon-32 format is chosen Sets the mode for beginning and ending messages. ASCII mode uses ASCII characters to mark the beginning and ending of messages, whereas RTU uses time gaps to mark the beginning and ending of messages. Choice will depend on the DCS being used. Selects between Big Endian and Little Endian. In Big Endian, the most significant bit is transmitted first, whereas in Little Endian, the least significant bit is transmitted first. Note: Only used if Modicon-32 format is chosen Selects the Baud Rate to be used for communication between the analyzer and the DCS. Usually 9600 but may differ depending on the DCS being used. Note: Only used if RS485 serial communication is used for Modbus Number of data bits transmitted at a time. Usually 8, but 7 may be used under some circumstances Note: Only used if RS485 serial communication is used for Modbus Type of parity checking used for data transmission. Usually None, but Even or Odd may be used under some circumstances. Note: Only used if RS485 serial communication is used for Modbus Number of bits marking the end of a transmitted byte. Usually 1 but may be 2 under some circumstances. Note: Only used if RS485 serial communication is used for Modbus The various items in the Available Points listing on the left side of the Modbus page can be accessed by clicking on the + sign. The items in this listing can be used to populate the Modbus Items list on the right side of the Modbus page by dragging and dropping them into the Modbus list. The general types of data in each folder in the Available Points list is given in Table 26. Revision 5 87 August 2021 Table 26: Available Modbus Points Folder Name Relay Status Fault Status Warning Status{XE “Available Points:Warning Status} Concentration Status{XE “Available Points:Concentration Status} Control Command{XE “Available Points: Control Command} Explanation Contains relay status points for each of the analyzer’s four relay outputs – Status, Service, Mode, and Control. This data is output in the Modbus list as either 0 (off) or 1 (on). Allows for the output of the status of all possible analyzer faults. This data is output in the Modbus list as either 0 (no fault) or 1 (fault) Note: Peripheral Fault point is the same as the IO Board fault displayed the Indicators panel on the analyzer local display. Allows for the output of the status of all possible analyzer warnings. This data is output in the Modbus list as either 0 (no warning) or 1 (warning). Allows for the output of all measured concentration data in both percentage and parts per million (PPM) as well as calculated values of Air Demand, H2S/SO2 Ratio, and Sigma S. This data is output in the Modbus list as either 16bit numerical data (Enron and Modicon-16) or floating point numerical data (Modicon-32). Allows for remote control of the analyzer via Modbus. If a 1 is placed into the register for any of these points, that will force that command to be performed. Available remote commands are Go Online, Go Offline, Force Zero (forces analyzer into back-purge mode), Manual Zero (performs a Zero Calibration Cycle), and Sample Mode (switches analyzer into Sampling mode if currently in back-purge mode and no faults are present. To set up a new Modbus list, click on Change to Update Mode. A LOGIN dialog box like the one shown in Figure 58 will appear. The default password is 2222. Press Login. Once the password has been correctly entered, the New, Load, and Save buttons will be activated. Click on New to set up a new Modbus list. The Modbus Type dialog box shown in Figure 61 will then appear. Figure 61: Modbus Type Dialog Box Select the desired Modbus type and click on OK. A new Modbus List the desired format will appear and can then be populated with items from the Available Points list. Clicking on the Save button will store a currently configured Modbus list to the analyzer memory. If a new Modbus list is then opened, pressing Load during the editing of this new list will reload the original Modbus list; pressing Save during the editing of this new list will overwrite the original Modbus list. Revision 5 88 August 2021 Regardless of the format chosen, a Modbus list consists of three columns that are described in Table 27. Table 27: Modbus List Columns Column Modbus Items Register Value Explanation Contains a series of “nodes” (folders) which are used to hold data in different numerical formats depending on the specific data being output. Points from the Available Points list can be dragged and dropped into the appropriate node. Shows the Modbus register number for each data point. Used for DCS programming to ensure that the DCS is reading the correct registers. Shows the real time value of each register. Useful for troubleshooting to ensure that the DCS is reading each register correctly. To add items to a Modbus list, left click on the desired point in the Available Points list and drag it over to the Modbus list. Once the node name of the node to which the point is to be added is highlighted in blue, release the left mouse button. The point will then be added to the list in that note. When additional data points are added to a node, they are added at the bottom of the list. Once data points have been added to a Modbus list, the Modbus list can then be further edited by right clicking on a specific data point. A menu like the one shown in Figure 62 will appear. Figure 62: Editing a Modbus List There are three options available. Clicking on Up will move the selected data point up in the Modbus list, unless the data point is already at the top of the list in the node, in which case this option will not have any effect. Clicking on Down will move the selected data point down in the Modbus list, unless the data point is already at the bottom of the list in the node, in which case this option will not have any effect. Clicking on Delete will remove the data point from the list. 5.3.2.1 Enron Modbus Format If Enron is chosen as the Modbus format, the Modbus list will contain 4 nodes as shown in Figure 63. Revision 5 89 August 2021 Figure 63: Enron Modbus Format The Enron Modbus format contains 4 nodes on the Modbus tree: Coils, Short Integers, Long Integers, and Floating Point. Coils are Boolean (i.e. ON or OFF) data points which have a value of either 0 or 1. Thus, points placed into the Coils should be points that have only an ON or an OFF state, such as Relay Status points, Fault Status points, or Warning Status points. Control Command points can also be placed into the Coils node for remote initiation of different commands. Short Integers are 16-bit whole numbers with either a positive or a negative sign. Long Integers are 32-bit whole numbers with either a positive or a negative sign. Floating Point values are also 32-bit numbers, but unlike the integers they do not have a sign, but they do have decimal points. Because the Floating Point node can display data that includes decimal points, it is the most suitable node to use for the output of concentration data and other calculated results. 5.3.2.2 Modicon 16 Format If Modicon 16 is chosen as the Modbus format , the Modbus list will contain 4 nodes as shown in Figure 64. Figure 64: Modicon 16 Format The Modicon 16 Modbus format contains 4 nodes on the Modbus tree: Output “Coils” Status, Input Status, Input Register, and Output “Holding” Register. The Input Status and Output “Coils” Status nodes contain Boolean data points. Data points in the Input Status node can be written to, so if any Control Command points are required, they should be placed into the Input Status node. Data points in the Output “Coils” Status node are read-only, so points placed into this node should include any data points from the Relay Status, Fault Status, or Warning Status nodes, as data points in these nodes are all read-only. Output “Holding” Registers are data points that are read-only outputs of analyzer data, such as concentration values and calculated values like Air Demand. The Input Register node is used for non-Boolean (i.e. numerical) data points that can be written to. The Modicon 16 format only outputs numerical data as 16-bit numbers. Thus, the ouptut of decimal point data in this format is not possible – all numerical data output in Modicon 16 is whole number only. Revision 5 90 August 2021 5.3.2.3 Modicon with Floating Point Format If Modicon 32 (Modicon with Floating Point) format is chosen as the Modbus format, the Modbus list will contain 4 main nodes on the Modbus tree, as in Modicon 16 format. However, the Input Register and Output “Holding” Register nodes contain sub-nodes, as shown in Figure 65. Figure 65: Modicon 32 Format These sub-nodes are the same in both the Input Register node and the Output “Holding” Register node, and are Register Short, Register Long, and Register Float. Thus, the input and output registers can output data in 16-bit (short), 32-bit (long), or 32bit with floating point (float) in the Modicon with Floating Point Modbus list. Long and Short registers can contain whole number integer data, while Floating Point registers can contain integer data with decimal points. The Output “Coil” Status and Input Status nodes are identical to Modicon 16 format. 5.4 Factory Section The Factory section in the Navigation menu consists of only a single page, the Factory Parameters page, which is shown in Figure 66. Figure 66: Factory Parameters Page Revision 5 91 August 2021 The parameters on this page are configured at the factory and in general should not require changing once the analyzer is in operation. When this page is first opened, it is opened in readonly mode. In order to make changes on this page, click on Change to Update Mode at the top right corner of the screen. A LOGIN dialog box like the one shown in Figure 59 will appear. After entering the correct password (default is 9713) the page will change to Update mode and these parameters can then be edited. The parameters displayed on this page are colour-coded as described in Table 28. Table 28: Factory Parameters Colour Code Background Colour Blue Grey Green Type of Parameter Parameters related to the analyzer’s analog outputs Parameters related to the analyzer’s spectrometer Parameters related to calculation of analytical results Most of the parameters that are available for editing on this page can be edited at the analyzer local display using the keypad, though a few cannot. The available parameters are described briefly in Table 29. Table 29: Factory Parameters Parameter Editable via Keypad Local Display Editing Location Air Demand Full Scale (/+) Y Config – Outputs Dark Start Pixel N N/A First Vector Pixel N N/A H2S, SO2, COS, CS2 SVAP span factor Y Config – Calculation Cell Length Y Config – Calculation Revision 5 92 Explanation In previous software versions, AO1 was hardcoded to output Air Demand, and this parameter was used to set the range of the air demand output. In current software version, all AOs can be configured individually, so this parameter has no real use. Pixel number (out of 2048) where the spectrometer starts looking at the dark level. The displayed dark level is an average of the dark level on all pixels between this pixel and the first vector pixel. NOTE: This parameter is unique to each spectrometer and should ONLY be changed if the spectrometer is changed. Pixel number (out of 2048) on the spectrometer that is used as the first pixel out of the 530 consecutive pixels that are used for analysis. NOTE: This parameter is unique to each spectrometer and should ONLY be changed if the spectrometer is changed. Span factors used for each measured component. The concentration of each component calculated from the absorbance spectrum and the calibration matrix are multiplied by these span factors to produce the displayed and output concentration value. Should be close to 1 for each component. Setting to 0 will make the analyzer unable to measure that component. Measurement cell length as measured from inside of one cell window to the inside of the other cell window. Should only be changed if the measurement cell block is replaced with a block with a longer or shorter measurement cell length. August 2021 Plant Factor Y Config – Calculation Operating Ratio Y Config – Calculation Probe Control N N/A Analog Output 1, 2, 3, 4 Setup Y Config – Outputs Analog Output 1, 2 ,3 4 Full scale Y Config – Outputs Analog Output 1, 2, 3, 4 Track or Hold Y Config – Outputs Plant factor in the Air Demand equation (refer to Section 1.1). Plant factor is calculated as per the equation shown in Table 13, Section 4.8.2.1. In most cases, this will be -3. Optimal ratio of H2S to SO2 for the sulfur recovery unit in which the analyzer is installed. In most cases, this will be 2. Indicates which control point is used for the actuation of the probe cooler solenoid. Three options are available: • Control with SVP No RTD Attached – probe cooler is actuated when sulfur vapour level rises above set point value. No probe temperature measurement RTD present, so probe temperature warning / fault are disabled. • Control with SVP (RTD is still attached) – probe cooler is actuated when sulfur vapour level rises above set point value. Probe temperature measurement RTD is present, so probe temperature warning / fault are active. • Control with RTD – probe cooler is actuated when measured probe temperature exceeds set point value. Probe temperature warning / fault active. Configures the parameter output on each of the analyzer’s four analog outputs. Available output parameters for each output as per Table 12, Section 4.8.1. Concentration value corresponding to an output of 20mA for each output. NOTE: For all parameters but air demand, 4 mA corresponds to a concentration of 0. For Air Demand, 4 mA corresponds to negative full scale. Configures each output for either track or hold behaviour. Refer to section 3.3.1 for more details. To change a parameter: 1. Click on the parameter to be edited. The data entry field for that parameter will change to a white background. 2. Edit the parameter by typing in a new value. Some parameters such as Probe Control are non-numerical and can be edited by using the pull-down selection menu. 3. Once editing of the selected field is complete, press Enter on the keyboard. 4. Change any other parameters to be edited using the procedure in steps a to c. 5. Once all necessary changes have been made, click on the Save to Unit button at the bottom of the screen to save all changes permanently to the analyzer. If it is necessary to cancel all changes made on this page, clicking Revert before clicking on Save to Unit will undo all changes made during that editing session. Revision 5 93 August 2021 5.4.1 Changing the Passwords When logged into Update mode on the Factory Parameters page, there is a button marked Change Password on the bottom of the page. When clicked, the Change Password dialog box shown in Figure 67 appears. Figure 67: Change Password Dialog Box There are two passwords for the web GUI: the Operator password, which allows the user to change parameters in the Configuration section of the analyzer (configuration parameters, Modbus), and the Factory password, which is used to make changes to the factory parameters. The Change Password dialog box can be used to change either of these passwords according to the procedure below: 1. To change the factory password, place a checkmark in the Factory Password checkbox. To change the operator password, leave this checkbox unchecked. 2. Enter in the current password in the Enter Old Password. 3. Enter the desired new password twice in the Enter New Password (twice) fields. 4. Click on OK 5. If the current password is entered correctly, and the new password entered twice matches, the dialog box will disappear, and the new password is now valid. If the current password is entered incorrectly, or the new passwords entered twice don’t match, the error messages shown in Figure 68 will appear. Figure 68: Password Entry Error Messages In either case, click on OK, then repeat the procedure taking care not to make the same mistake. 5.5 Help Section The Help section contains information that may be useful to the user for installation, operation, and troubleshooting of the Model 943-TGXeNA analyzer. 5.5.1 Drawing Page When the Drawing page is opened, a PDF showing generic drawings of the analyzer exterior, interior, and electronic schematics is downloaded from the analyzer and displayed. These drawings are also included in Section 9 of this manual. Revision 5 94 August 2021 5.5.2 User Manual Page When the User Manual page is opened, a PDF copy of this operator manual is downloaded from the analyzer and displayed. 5.5.3 Revision History Page When the Revision History page is opened, the revision number of the web GUI software installed on the analyzer is displayed, as shown in Figure 69. Please refer to this revision number when making inquiries about the analyzer software. Figure 69: Revision History Revision 5 95 August 2021 Section 6 6.1 Maintenance Overview The Model 943-TGXeNA is designed for automatic trouble-free operation under the continuous supervision and control of the analyzer’s control computer. However, periodic maintenance is required to keep the analyzer performing at optimal levels. Maintenance requirements include: • • Routine preventative maintenance (Section 6.2) Periodic operations to optimize performance (Section 6.3) In addition, a list of recommended spare parts to be kept on hand for reduced down-time is provided in Section 11. 6.2 Routine Preventative Maintenance Routine preventative maintenance of the 943-TGXeNA analyzer is used to ensure that the analyzer is continuing to operate in an optimal manner and all operating parameters are within a normal range. It consists of: • • • Visual Inspection of the Key Operating Parameters displayed on analyzer’s local display (Section 6.2.1) Verification of analyzer’s response time, both sample to zero and zero to sample (Section 6.2.2). Weekly completion of the Maintenance Check-out Procedure (Section 6.2.2). The operator should complete the Maintenance Record Sheet included in this section and maintain a file of record sheets to provide a time-based record of system operation. 6.2.1 Parameters Visual Inspection of Key Operating Table 30 shows the normal conditions of a variety of analyzer operational parameters and indicators. If the conditions and indicators displayed on the analyzer’s local display are indicating as shown in the table, the system is operating normally, and no further maintenance is required at this time. Revision 5 96 August 2021 Table 30: Normal Operating Parameter and Indicator Conditions Indicator / Parameter Online / Offline Backpurge Panel Location Normal Condition Analysis 2 Analysis 1 Relay Indicators Analysis 1 Fault Indicators Indicators Warning Indicators Indicators Cell Temperature Probe Temperature Cabinet Temperature Analysis 2 Analysis 2 Analysis 2 Air Demand Output Analysis 1 H2S and SO2 Analysis 2 Absorbance Absorbance Online (green) Off (green) • Status “Normal” (green) • Service “Normal” (green) • Mode “Run” (green) • Control “Auto” (green) • Cell Temperature (Green) • Probe Temperature (Green) • Measure Range (Green) • Reference Range (Green) • Dark Range (Green) • I/O Board (green) • Cabinet Temperature (green) • High Absorbance (green) • High Integration Period (green) • Low Reference Peak (green) • High Sulfur Vapour (green) Within normal range (140°C to 160°C) Within normal range (100°C to 120°C) Within normal range (10°C to 40°C) Depends on process, should be within -5% to +5%, change in air demand should be gradual and not sudden Depends on process, should not be off scale, ratio should be reasonably close to 2:1 H2S to SO2, any indicated changes on trend lines should be gradual and not sudden Peak absorbance given on absorbance graph should not exceed 2 AU 6.2.2 Maintenance Check Out Procedure It is recommended that this maintenance check be performed once per week and the Maintenance Record Sheet (Table 31) be completed at the same time. It is recommended that the completed record sheets are saved in a secure location. The information on the sheets can provide a time based record of system operation and may be useful for troubleshooting. The following procedure should be performed on a periodic basis and the Maintenance Record Sheet should be completed (Table 31): 1. Observe the present status of the analyzer indicated on the Analysis 1 and Analysis 2 panels. Record any fault conditions or abnormal values. Record the displayed values for the cell / probe temperatures as well as the cell pressure. Revision 5 97 August 2021 2. Place the analyzer in Offline mode using the Online / Offline control on the Analysis 2 panel. (Refer to Section 4.3.1) 3. Place the analyzer in back-purge by clicking the Back Purge check box on the Analysis 1 panel OR by pressing the PURGE key on the keypad. The displayed concentration and air demand outputs should stabilize to a near zero readings within seconds. Use a stopwatch to measure the time required for the readings to drop from stable process values to stable zero values. Record the stabilized zero concentration output values. The offset from zero will vary based on length of time since the last zero calibration cycle (manually initiated or automatic). 4. On the Spectrum panel, observe the raw scan signal and compare the shape of the scan trace to the Factory Reference. Note any extreme deviations from the factory referene. Record the value in the Peak Height field in approximate A/D counts (±1,000). 5. If the value in the Peak Height field is less than 16,000, the signal peak height should be optimized using the Optimize Integ. Time button. Refer to Section 4.6. 6. Return to the Analysis 1 panel. Ensure that the Status indicator is green (Normal) and the Service indicator is also green (Normal). Check the displayed concentration values. If they are not very close to zero (±0.02% for all indicated values) a Manual Zero should be performed. Refer to Section 4.3.4. 7. Return the analyzer to Sample mode by clicking on the Sample checkbox on the Analysis 1 panel OR by pressing the PURGE key on the keypad. Observe and record how long it takes for the concentration readings to stabilize at the process value. Record the stabilized process values. A long response time to a stabilized sample reading may indicate plugging of the sample system or filter, or inadequate aspirator drive air flow. Record any observed anomalies and/or valve position adjustments made. The response time from back purge to stabilized sample values should be >30 seconds, but the exact value depends on a variety of factors, including probe length and instrument air pressure. 8. Return the analyzer to Online by toggling the Online / Offline control back to the green Online state. Revision 5 98 August 2021 Table 31: Maintenance Record Sheet Processing Unit Number Analyzer Tag Number Analyzer Serial Number Date Time Instrument Technician As Found Forced Zero On Spectrum Configuration Forced Zero Off As Left Fault Condition Cell Temperature Cabinet Temperature Cell Pressure Integration Period Air Demand H2S SO2 Time to Stabilize Air Demand H2S SO2 Spectrum Peak Height Standard Spectrum Shape Optimize Integration Time New Integration Time Configuration Changed New Configuration Saved Time to Stabilize Fault Condition Cell Temperature Cabinet Temperature Cell Pressure Integration Period Air Demand H2S SO2 Yes/No Yes/No Yes/No Yes/No Notes: Revision 5 99 August 2021 6.3 Changing the Anti-Solarant Solution Radiation generated by the analyzer’s broadband UV Source Lamp in the short wavelength UV region (wavelength <200 nm) may degrade the transparency of the optical fibres to ultraviolet radiation in the measurement region over a period of time. An optical fibre directly exposed to the broadband source will eventually develop an absorption band that reduces fibre transmittance at wavelengths below 250 nm. The degree of fibre degradation is a function of accumulated exposure time. The Anti-Solarant Solution incorporated into the analyzer provides a high-pass liquid optical filter with a sharp cutoff region. The Anti-Solarant Solution filters out the short wavelength UV radiation which is the cause of the fibre degradation and prevents it from entering the fibre where it can cause damage. RUNNING A BRIMSTONE-943 ANALYZER WITHOUT ANTI-SOLARANT SOLUTION WILL NOT AFFECT THE ANALYSIS RESULTS. HOWEVER, OPERATING IN THIS MANNER COULD CAUSE IRREVERSIBLE DAMAGE TO THE ANALYZER’S OPTICAL FIBRES, AND SIGNIFICANTLY SHORTEN THEIR LIFESPAN. The Anti-Solarant Solution will eventually degrade to the point where it absorbs too much energy causing the integration period to approach the maximum of 1000 ms. When the analyzer is exhibiting a loss of spectrometer signal level (a high integration period >500ms required to reach 28,000 A/D counts), and all other potential causes of loss of spectrometer signal have been ruled out (dirty cell windows, lamp near the end of its lifespan, damaged optical fibres), the cause of the low response is likely expired anti-solarant solution. Under these circumstances, the anti-solarant solution will need to be replaced. Wear protective UV eye glasses at all times if the optical fibres are removed while the UV Source Lamp is powered up. The control cabinet door should NOT be opened while the analyzer is energized UNLESS the area is known to be non-hazardous. The anti-solarant solution should only be changed only by authorized personnel. It is not necessary to turn the UV source lamp off to perform this procedure. The UV lamp lifespan can be reduced by additional ON/ OFF cycles. The fluid holder may be warm. Wear Gloves when handling the fluid holder. Always handle optical fibres carefully and avoid any contact with the end of the fibre. Before proceeding with the following procedure, ensure that the analyzer is Off Line and purged with zero gas. Always handle optical fibres carefully and avoid any contact with the end of the fibre when it is disconnected. Before proceeding with the following procedure, ensure that the analyzer is Off Line and purged with zero gas. Refer to Figure 70 while performing the following procedure. Revision 5 100 August 2021 3 2 4 1 Figure 70: Replacing the Anti-Solarant Solution 1. Disconnect the source optical fibre from the fluid holder bracket on the UV Lamp Supply (Item #1 in Figure 70). Let the fibre hang freely and ensure that the end does not contact anything. It is suggested that a protective plastic cap is placed onto the end of the fibre. This fibre is removed from the light path to protect it from unfiltered exposure to the UV Source Lamp). 2. Loosen the light shield retaining screw on the bottom right-side of the fluid holder and remove the light shield. (#4 in Figure 70) 3. Loosen the fluid holder locking screw (s) on the left-side of the fluid holder using a 7/64" ball driver.(#2 in Figure 70) 4. Lift the fluid holder from the base by grasping the fluid holder filler plug (#3 in Figure 70). 5. Remove the filler plug from the top of the fluid holder. 6. Dump out the old anti-solarant solution. The Anti-Solarant Solution is not hazardous to the environment. Revision 5 101 August 2021 7. Rinse the chamber with a small amount of new anti-solarant solution. Shake and empty. Ensure that there are no solid deposits and the chamber windows are completely clear. 8. Fill the fluid holder with new anti-solarant solution. Tilt and tap the fluid holder to remove any air bubbles that may form. Leave a small amount of air space at the top of the fluid holder to allow for thermal expansion. Take care not to touch the Anti-Solarant Solution directly as the oils from your hands will contaminate the solution. 9. Replace the fluid holder filler plug. 10. Replace the fluid holder into the bracket. Orient the fluid holder so that the face with the word LAMP engraved on it faces the UV Source Lamp. DO NOT touch the fluid holder windows as dirt, grease and human skin oil will reduce their transparency to UV radiation. 11. Tighten the fluid holder locking screw (s) on the left-side of the fluid holder (#2 in Figure 70). Unless the analyzer is installed in a high-vibration environment, hand tight is enough for these screws. 12. Reinstall the light shield and tighten the light shield retaining screws on the bottom right-side of the fluid holder.(#4 in Figure 70). 13. Remove the protective plastic cap from the disconnected source fibre and reconnect it to the fluid holder bracket (#1 in Figure 70). Hand tight is sufficient for this connection. 14. Reoptimize the spectrometer energy level as described in Section 6.4 6.4 Optimizing the Spectrometer Signal Optimization of the Spectrometer signal is periodically required to maintain a sufficient signal to noise ratio on the spectrometer output signal as the spectral output signal from the spectrometer will degrade over time. Commonly seen causes of this degradation include: • • • • • Degraded Anti-Solarant Solution Aging UV Source Lamp (output reduces over time) Dirty measurement cell windows Dirty optics Optical fibre problem For convenience, the energy level of the spectrometer output signal is gauged by observing the Peak Height as displayed on the Spectrum panel of the analyzer or the Spectrum page on the Web GUI. When optimizing the spectrometer signal, the normal target value for the peak height is 28000 counts (+/- 500). The spectrometer energy level can be optimized manually (for special cases), or automatically as a function of the analyzer. The automatic function will always target 28000 counts. Revision 5 102 August 2021 Prior to carrying out spectrometer signal optimization, the analyzer MUST be in back purge and offline mode. 6.4.1 Automated Optimization 1. Place the analyzer in back purge mode. This can be done by selecting the Back Purge field on the Analysis 1 panel and pressing the ↵ key to place an X in the box OR by pressing the PURGE key on the keypad. 2. Access the Spectrum panel, navigate to the Optimize Integ Time button and press ENTER. Make sure that the peak height after completion of this operation is ≈28000 A/D counts. 3. Return to the Analysis 1 Panel. 4. Request a Manual Zero by navigating to the Manual Zero button and pressing ENTER. 5. After the Manual Zero is completed, place the analyzer back in Sampling mode by selecting the Sample field and then pressing ENTER to put an x in the box OR pressing PURGE on the analyzer keypad. 6. Place the analyzer back into ONLINE mode by toggling the button on the Analysis 2 panel. 6.4.2 Manual Optimization 1. Place the analyzer in back purge mode. This can be done by selecting the Back Purge field on the Analysis 1 panel and pressing the ENTER key to place an X in the box OR by pressing the PURGE key on the keypad. 2. Access the Spectrum panel. 3. If the peak level is between 25,000 and 28,000 then no adjustment is required at this time. 4. If adjustment is necessary, optimize the peak signal height to ≈28,000 counts. Navigate to the Set Integ. TIme and press ENTER to display the Integration Period dialog box (Section 4.6). Enter a new integration period in the New Value field and press ENTER. After several seconds, the new raw signal will be displayed. New values for the Integration Period can be entered until the peak height is 28 000 counts +/- 1000 counts. 5. Once the peak height has been optimized, record the peak height value and the resulting integration period. 7. Return to the Analysis 1 Panel. 8. Request a Manual Zero by navigating to the Manual Zero button and pressing ENTER. Revision 5 103 August 2021 9. After the Manual Zero is completed, place the analyzer back in Sampling mode by selecting the Sample field and then pressing ENTER to put an x in the box OR pressing PURGE on the analyzer keypad. 10. Place the analyzer back into ONLINE mode by toggling the button on the Analysis 2 panel Revision 5 104 August 2021 Section 7 7.1 Servicewhat is going on here... Overview The Service section consists of procedures for determining the cause of a problem and includes a series of procedures to replace certain components. A major component failure should be handled by contacting Galvanic Applied Sciences, Inc. Galvanic Applied Sciences, Inc. offers service on a call-out basis and/or factory assistance on the 943-TGXeNA analyzer. For Service and/or Assistance Contact: Galvanic Applied Sciences Inc. 7000 Fisher Road SE Calgary, Alberta T2H 0W3 Canada Tel: 403-252-8470 TOLL FREE (CANADA/US): 1 (800) 458 4544 INTERNATIONAL +1 978 848 2708 Fax: 403-255-6287 Email: [email protected] 7.2 Indicators Panel Troubleshooting The Indicators panel shown in Figure 71 shows a historical record the most recent 25 fault / warning events. Refer to Section 4.5 for a full description of the information presented on this panel. Figure 71: Indicators Panel Revision 5 105 August 2021 Table 32 shows potential troubleshooting solutions for all displayed active faults and warnings on the Indicators panel. Table 32: Analyzer Fault / Warning Troubleshooting Fault / Warning Cell Temperature High High Sulfur Measure Range Reference Range Dark Range I/O Board Cabinet Temperature High Absorbance High Integration Period Low Reference Peak High Sulfur Vapor Revision 5 Troubleshooting Tips • Oven heater fuse is blown (ACTS:25) • Cell assembly is not securely clamped to the heaters • Oven heater(s) inoperative • Steam lines, sample probe nozzle, and analyzer flange are not sufficiently insulated • Set point for low temperature alarm is incorrect NOTE: If this fault is active but the temperature is above the low temperature set point, this indicates that the High Cell Temperature setpoint is set too low. This setpoint can only be set through the web GUI. Refer to Section 5.3.1 • The sulfur vapor concentration in the sample has risen to unacceptable levels. This usually indicates that the probe’s condenser tip is not cool enough to condense sulfur in the process pipe. • Probe cooler solenoid is not functioning • Probe cooler instrument air flow rate is not high enough • Check probe cooler air outlet on left side of analyzer for air flow • UV lamp is nearing the end of its useful life and requires changing • UV lamp is not operating • Fuse on UV power supply is blown (integral with the power switch on the bottom side of the UV lamp supply enclosure inside the control cabinet) • Fuse on ACTS28 is blown • Anti-Solarant solution transmissivity has degraded. • Cell windows are dirty • Optical Fibres have become damaged • Spectrometer problem, consult factory. • • • • • • • • • • • • • • • • • • • • • • • • The I/O board is not communicating with the controller board. The spectrometer is not communicating with the controller board Check ArcNet wiring. Check USB connection at spectrometer and at top of controller board Cabinet cooler air solenoid not functioning Air supply to Vortec cooler is turned off Analyzer is installed in direct sunshine and requires a sun shade . The H2S and or SO2 concentration is out of range (process issue) The analyzer is not zeroed. Switch analyzer to backpurge and ensure that the spectrum displayed on the Absorbance panel goes to zero; if it does not, immediately perform a Manual Zero UV lamp is nearing the end of its useful life UV lamp is not operating (only in conjunction with Measure / Reference range fault) Anti-Solarant solution transmissivity has degraded. Cell windows are dirty Optical fibres have been damaged ACTS 28 fuse or lamp power supply fuse blown (only in conjunction with Measure / Reference range fault) UV lamp is nearing the end of its useful life UV lamp is not operating (only in conjunction with Measure / Reference range fault) Anti-Solarant solution transmissivity has degraded. Cell windows are dirty Optical fibres have been damaged ACTS 28 fuse or lamp power supply fuse blown (only in conjunction with Measure / Reference range fault) Sulfur vapour concentration approaching fault set point Confirm probe cooler is operating by checking for air flow from probe vent on left side of analyzer cabinet. 106 August 2021 7.3 Testing and Replacement of the Optical Fibres When a High Integration Period warning is present, one of the possible causes of this warning is that one or both of the optical fibres have been damaged and are not able to transmit ultraviolet radiation normally. To eliminate or confirm the fibres as the source of the high integration period, they can be tested as a pair or, if necessary, individually to observe their transmission characteristics . The fibre optic cables will generally only require change-out if they suffer from mechanical damage or if they have been exposed directly to short wavelength ultraviolet radiation for prolonged time periods, as when the analyzer has been operated for prolonged periods without anti-solarant solution present. The fibre optic cable ends terminate into SMA type connectors and are intended to be installed with the seal body installed in the inter-cabinet seal fittings that connect the oven cabinet and the control cabinet. There are two cables. The shorter of the two fibres connects the UV Source Lamp in the control cabinet to the top side of the measurement cell in the oven cabinet. The longer of the two fibres connects the Spectrometer in the control cabinet to the bottom side of the measurement cell in the oven cabinet. The SMA connectors only need to be finger-tight. Do not overtighten the connectors as this may damage the cable. Remove the anti-solarant fluid holder and check if the High Integration Period warning is still present when operating without anti-solarant solution BEFORE proceeding with the fibre test procedure. If the High Integration Period warning clears when the anti-solarant fluid holder is removed, this indicates that the anti-solarant solution has degraded to a non-usable level and needs to be replaced as per the procedure described in section 6.3. Perform this replacement prior to testing the optical fibres. To test the optical fibres, and replace if necessary, follow the procedure below. 1. Place the analyzer in Offline mode by toggling the Online / Offline control toggle (Section 4.3.1) on the Analysis 2 panel to Offline (red). 2. Place the analyzer in back purge mode by pressing the PURGE key on the keypad OR by placing the X in the Back Purge check box on the Analysis 1 panel. 3. Access the purged control cabinet following proper user company and/or regulatory agency procedure. The control cabinet door may NOT be opened while the analyzer is energized UNLESS the area is known to be non-hazardous. Observe all the warning labels on the analyzer enclosures. DO NOT look at the end of disconnected fibres connected to the UV lamp or place them in contact with skin. The intense UV radiation transmitted through these fibres can cause eye and skin damage. Fibres should be capped immediately after disconnection to prevent acidental exposure to UV radiation. 4. Turn the oven heaters off by locating the Heater AC Power fuse terminal on terminal block ACTS:25. Lift the fuse terminal tab opening the terminal block and thus disconnecting the Heater AC Power fuse, as shown in Figure 72. Revision 5 107 August 2021 Figure 72: Location of Cell Heater Fuse on ACTS 5. Open the oven cabinet door and remove the black cover on the oven enclosure. The oven enclosure and all of its components are HOT (150°C). Wear appropriate personal protective equipment (gloves, eye wear, clothing etc) if working with hot surfaces or wait until surface have cooled to safe temperatures before performing maintenance tasks. 6. Disconnect the fibres from both the top right and the bottom right of the measurement cell block by unscrewing the nut and pulling out. 7. Joint the two loose ends of the optical fibres together by cutting the end off of one of the orange fibre caps and connecting both fibres into the same cap. Press the fibres into the cap so that both ends are in contact with one another. 8. Using the PANEL NEXT / PANEL PREV keys on the keypad, navigate to the Spectrum panel. 9. Use the FIELD NEXT / FIELD PREV keys to select Optimize Integ. Time and press ENTER to optimize the integration period. It may be necessary to press ENTER more than once to get a peak height ≈28000 A/D counts. 10. Use the FIELD NEXT / FIELD PREV keys to select Show Factory Reference and press ENTER to display the factory reference spectrum. 11. Observe the indicated integration time. If the observed integration period is <100 milliseconds AND the shape of the red current spectrum has no major differences from the factory spectrum, both fibres are undamaged and will not require replacement. If the lamp was replaced <6 months ago, the High Integration Period warning is likely due to dirty cell windows. Refer to Section 7.5 for cleaning / replacement procedure. Do not reinstall the fibres at the measurement cell at this time. However, if the integration period is >100 milliseconds OR the shape of indicated spectrum is Revision 5 108 August 2021 significantly different from the factory reference spectrum, it will be necessary to test the fibres individually. Continue to Step 12. 12. Loosen the two inter-cabinet seal fittings through which the fibres pass from the oven cabinet into the control cabinet and unscrew the retaining caps. Lift out the plastic retainers and pull gently outward on the cable and rubber seal plug until free from the fitting. Be careful that the ends of the Fibre Optic Cables do not become abraded by contact with other surfaces. Installing a protective plastic cap onto the end of the fibre is recommended. 13. Disconnect the fibre optic cables from the UV Lamp enclosure and the spectrometer by unscrewing the nuts and pulling the fibre optic cables out. The cables can then be pulled out through the cabinet seal fittings. 14. Connect one cable directly from the UV lamp enclosure to the spectrometer. Repeat steps 9 and 10 for this cable. Observe the integration time and the shape of the spectrum. If the integration time <50 milliseconds AND the peak shape is similar to the factory reference, the cable is good and does not require replacement. If the integration time >100 milliseconds OR the peak shape is significantly different from the factory reference spectrum, the cable should be replaced. 15. Repeat step 15 for the other fibre optic cable. 16. If both fibre optic cables are found to be good, and the UV lamp was last replaced <6 months ago, the High Integration Period warning is likely due to dirty measurement cell windows. Refer to Section 7.5 for cleaning / replacement procedure. If at least one cable is found to require replacement, obtain the necessary replacement(s) and then continue with this procedure. 17. Slide the short (source) fibre optic cable through the seal retaining cap, the rubber seal, and the fitting for the bottom inter-cabinet seal fitting, ensuring that the seal body on the fibre optic cable is closer to the control cabinet end. Connect the end of the fibre to the SMA fitting on the UV Lamp power supply and hand tighten the nut. Tighten the seal fitting. 18. Slide the long (detector) fibre optic cable through the seal retaining cap, the rubber seal, and the fitting for the top inter-cabinet seal fitting, ensuring that the seal body on the fibre optic cable is closer to the control cabinet end. Connect the end of the fibre to the SMA fitting on the spectrometer and hand tighten the nut. Tighten the seal fitting. 19. Route the fibres into the oven, making sure that the fibres are routed in the indents to avoid damage when the oven enclosure cover is secure. 20. Connect the short fibre to the SMA fitting on the top of the measurement cell. Connect the long fibre to the SMA fitting on the bottom of the measurement cell. Hand tighten the nuts. 21. Loosen the set screw holding the SMA Fittings into the measurement cell slightly so that the SMA fitting can rotate and slide in and out. Revision 5 109 August 2021 22. Use the PANEL NEXT / PANEL PREV keys to navigate to the Spectrum panel. Adjust the position of each SMA fitting in the measurement cell by rotating it slightly left and right and sliding it in and out to find the position that gives the greatest Peak Height. Once the optimal position is found for each fibre, re-tighten the set screw. The SMA connectors only need to be finger-tight. Do not overtighten the connectors as this may damage the cable. 23. Optimize the integration period by using the FIELD NEXT / FIELD PREV keys to highlight Optimize Integ. Time, then press ENTER. 24. Observe the optimized integration time. If the High Integration Period warning has cleared, no further work is required at this time. Proceed to the next step in this procedure. If the High Integration Period warning is still present, however, it is likely that the cell windows are dirty and/or damaged. Proceed to Section 7.5. 25. Make sure that both fibre optic cables are in their correct indent in the oven enclosure frame, then replace the oven enclosure cover and securely fasten both latches. 26. Reconnect the AC Power to the oven heaters by pushing down and snapping closed the oven heater fuse terminal cover (ACTS:25). The oven will begin heating to the set point temperature. 27. Close and latch the oven cover. 28. Close and latch the control cabinet and oven cabinet doors. 29. Confirm that the High Integration Period warning has not returned. 30. Once the measurement cell temperature rises to >140°C, and the Cell Temperature fault has cleared, use the PANEL NEXT / PANEL PREV keys to navigate to the Analysis 1 panel. Perform a manual zero calibration cycle by using the FIELD NEXT / FIELD PREV keys to highlight Manual Zero, then press ENTER.. 31. Once the manual zero calibration cycle is complete, place the analyzer into sampling mode by highlighting the Sample checkbox using the FIELD NEXT / FIELD PREV keys, then press ENTER. Alternatively, press the PURGE key 32. Once normal operation has been confirmed, return the Online / Offline control toggle on the Analysis 2 panel back to Online (green). 7.4 Troubleshooting the UV Source Lamp The UV Source Lamp requires replacement when either the lamp will not start, or when the energy output of the lamp has diminished to a point where a Peak Height of >20,000 A/D counts as displayed on the Spectrum panel cannot be achieved even with the maximum 1000 millisecond integration period. Before replacing the UV Source Lamp, it is advisable to eliminate all other potential sources of the problem, unless the time since the last replacement is >8 months (if using standard lifespan lamp, Galvanic part number BA7195) or >16 months (if using long life lamp, Galvanic part Revision 5 110 August 2021 number BA7532). Refer to the spectrum displayed on the Spectrum page and the lamp troubleshooting tips shown in Table 33. Table 33: Lamp Troubleshooting Spectrum Appearance • • Horizontal line, no peak observed • • Peak present, but peak height <20,000 with integration time 1000ms • • • Potential Cause Lamp supply fuse on ACTS burned out Lamp supply fuse in switch on bottom of black UV lamp enclosure burned out Lamp burned out Anti-solarant degraded and requires replacement Dirty / broken cell windows Damaged optical fibres Lamp degraded to beyond useful life Once the lamp has been switched off, it will not restart for a period of time as ignition of a hot lamp can cause serious problems. If the lamp is turned off or is no longer lit, it may be worthwhile to wait for 15-20 minutes before restarting it. If the lamp does not start after the cool down period, and it has been more than six months since the lamp has been replaced, then it should be replaced. The normal lifespan of a UV Source Lamp is about six months, but longer life spans are possible in circumstances where the restart count is low. If the lamp was replaced <8 months ago (standard lifespan lamp) or <16 months ago (long lifespan lamp) , it is advisable to investigate the other potential causes listed in Table 33 prior to replacing the lamp. The lamp life is inversely proportional to the number of restarts on a particular lamp. The lamp should ONLY be turned off when absolutely necessary to preserve lamp lifespan. An iris is installed on the lamp holder between the lamp and the fluid holder. The iris is preset at the factory with clean optics and a new lamp to obtain 28,000 counts at a <100 ms integration period. The setting of the iris is only to be changed in extreme situations. Please contact Galvanic Applied Sciences Inc. prior to making any changes to the iris position. To change the UV Source Lamp, follow the procedure below. 1. Place the analyzer in Offline mode by toggling the Online / Offline control toggle (Section 4.3.1) on the Analysis 2 panel to Offline (red). 2. Place the analyzer in back purge mode by pressing the PURGE key on the keypad OR by placing the X in the Back Purge check box on the Analysis 1 panel. 3. Access the purged control cabinet following proper user company and/or regulatory agency procedure. The control cabinet door may NOT be opened while the analyzer is energized UNLESS the area is known to be non-hazardous. Observe all the warning labels on the analyzer enclosures. Revision 5 111 August 2021 4. Lift the fuse terminal tab opening the terminal block and disconnect the UV Lamp Power Supply fuse, located at ACTS:28, next to the cell heater fuse tab indicated in Figure 72. Alternatively, place the UV Lamp power switch to the Off position. The location of the lamp power switch is indicated in Figure 73. Socket Head Cap Screw Figure 73: UV Lamp Enclosure 5. Remove the UV Lamp Enclosure lid by removing the four (4) socket head cap screws and pulling the cabinet lid outwards. The lamp enclosure lid has a safety cutoff switch underneath it that will automatically cut off power to the lamp supply enclosure when the lid is removed. However, for safety reasons the power supply should ALWAYS be shut off as described in Step 4 prior to removal of the lid. Revision 5 112 August 2021 Figure 74 shows the internal layout of the UV lamp enclosure. Refer to this picture while performing the next steps of this procedure. 1 3 2 Figure 74: UV Lamp Enclosure Internal Layout 6. Remove the two plastic hole plugs from the top of the UV Lamp Enclosure to gain access to the lamp retaining screws. The location of these two hole plugs is indicated in Figure 74 by the red circle (#1). 7. Disconnect the three (3) lamp connection wires from the terminal strip, circled in yellow in Figure 74 (#2). 8. Remove the two lamp retaining screws (5-40 x 3/8") from the lamp retaining ring using a 3/32" ball driver passed through the removed hole plugs. The location of the front retraining screw is marked by the blue circle (#3) in Figure 74. 9. Remove the lamp. 10. Place the new lamp in the lamp retainer on the lamp mount assembly. Ensure the lamp is facing the correct direction. Refer to Figure 75 for the correct UV source lamp orientation. Revision 5 113 August 2021 This side faces towards the anti-solarant fluid holder. Figure 75: UV Lamp Orientation DO NOT touch the front face (light emitting side) of the lamp. Dirt, grease, and human skin oils can affect the lamp spectral performance. Always handle the lamp by the metal base. DO NOT apply power to the lamp with the cover removed. Intense UV radiation can cause severe eye damage. 11. Replace the two lamp retaining screws (5-40 x 3/8") and tighten using a 3/32" ball driver passed though the holes on the top of the lamp enclosure. 12. Replace the two plastic plugs on the top of the lamp enclosure. 13. Reconnect the three wires from the lamp to the terminal strip. The wires are colour coded on the terminal strip. Connect the lamp’s blue wire to the blue terminal, the red wire to the red terminal, and the black wire to the black terminal. If the lamp has two black wires instead of a blue and a black, connect one of the black wires to the blue terminal and the other to the black terminal. 14. Reinstall the UV lamp enclosure cover. Tighten the cover cap screws. 15. Reconnect the AC terminal block fuse terminal on terminal block ACTS:28 by pressing down and snapping it into place. Place the UV Lamp power switch to the ON position. 16. Close and latch the control cabinet door. 17. Ensure that the analyzer is still in backpurge mode. 18. Using the keypad, navigate to the Spectrum panel. 33. Optimize the integration period by using the FIELD NEXT / FIELD PREV keys to highlight Optimize Integ. Time, then press ENTER. 34. Observe the optimized integration time. If the High Integration Period warning has cleared, no further work is required at this time. Proceed to the next step in this procedure. If the High Integration Period warning is still present and the fibres have Revision 5 114 August 2021 already been tested as described in Section 7.3, however, it is likely that the cell windows are dirty and/or damaged. Proceed to Section 7.5 – 7.6 35. Use the PANEL NEXT / PANEL PREV keys to navigate to the Analysis 1 panel. Perform a manual zero calibration cycle by using the FIELD NEXT / FIELD PREV keys to highlight Manual Zero, then press ENTER. 36. Place the analyzer into sampling mode by highlighting the Sample checkbox using the FIELD NEXT / FIELD PREV keys, then press ENTER. Alternatively, press the PURGE key. 37. Once normal operation has been confirmed, return the Online / Offline control toggle on the Analysis 2 panel back to Online (green). 7.5 Measurement Cell Block Removal The measurement cell block will require removal only when there is a suspected sampling problem or if it becomes necessary to clean or change the cell windows and/or O-Rings. A sampling problem could be due to system plugging or collection of nongaseous material in the measurement cell. The measurement cell is to be removed by trained and authorized personnel only. Follow the procedure to remove the measurement cell block from the analyzer. 1. Place the analyzer in Offline mode by toggling the Online / Offline control toggle (Section 4.3.1) on the Analysis 2 panel to Offline (red). 2. Place the analyzer in back purge mode by pressing the PURGE key on the keypad OR by placing the X in the Back Purge check box on the Analysis 1 panel. 3. Access the purged control cabinet following proper user company and/or regulatory agency procedure. The control cabinet door may NOT be opened while the analyzer is energized UNLESS the area is known to be non-hazardous. Observe all the warning labels on the analyzer enclosures. DO NOT look at the end of disconnected fibres connected to the UV lamp or place them in contact with skin. The intense UV radiation transmitted through these fibres can cause eye and skin damage. Fibres should be capped immediately after disconnection to prevent acidental exposure to UV radiation. 4. Turn the oven heaters off by locating the Heater AC Power fuse terminal on terminal block ACTS:25. Lift the fuse terminal tab opening the terminal block and thus disconnecting the Heater AC Power fuse, as shown in Figure 72. 5. Open the oven cabinet door and remove the black cover on the oven enclosure. Revision 5 115 August 2021 The oven enclosure and all of its components are HOT (150°C). Wear appropriate personal protective equipment (gloves, eye wear, clothing etc) if working with hot surfaces or wait until surface have cooled to safe temperatures before performing maintenance tasks. 6. Allow zero gas to flow for approximately five (5) minutes to remove all toxic gases from the sample system. 7. Ensure all five block valves in the oven enclosure are in the closed position. Fully close the Zero Air Flow Adjust valve. 8. Remove the Fibre Optic Cables from both ends of the measurement cell. Carefully hang the cables in a location where the ends of the cables cannot not contact anything. Cap the ends of the two fibres with the orange protective caps. 9. Loosen one of the cell tubing fittings to vent positive pressure zero gas that may be trapped in the sample system. 10. To remove the measurement cell block, tubing connected to the measurement cell block assembly must first be removed. Disconnect the fittings circled in Figure 76. Figure 76: Oven Enclosure Process gas is still present at the probe side of these valves. To prevent the release of toxic gases, ONLY disconnect tubing from the cell side of these valves, NOT the probe side. 11. Using a 7/64” ball driver, remove the 6-32 x 3/8” screw securing the cell RTD to the cell block Carefully place the cell RTD behind the cell block where it will be out of the way. Place the screw in the storage box in the control cabinet to prevent it from getting lost. 12. Loosen the four ¼-20 x 2” heater bracket mounting screws from the cell block face using a 3/16” ball driver. Before removing the last screw entirely, place your fingers Revision 5 116 August 2021 under the cell block to catch the plate as you release the last screw. Place the screws in the storage box in the control cabinet. 13. Carefully remove the measurement cell block from the analyzer. Disconnect any additional tubing as required to remove the measurement cell block, bearing in mind the warning displayed in Figure 76. 7.6 Cell Windows Cleaning / Replacement Under normal operating conditions, cell window replacement is necessary only when the particular window becomes cracked, chipped, etched or stained to a non-cleanable degree. However, under normal operating conditions, it is possible for the cell windows to become sufficiently dirty to reduce their transparency to ultraviolet radiation, which can lead to a High Integration Period warning. Cleaning or changing the cell windows is most easily accomplished by removing the entire measurement cell assembly from the oven enclosure, as described in Section 7.6. It is recommended that the measurement cell assembly is opened in a clean environment such as a bench top. Follow the procedure below to open up the measurement cell and clean / replace the cell windows and their associated O-rings. Refer to Figure 77 while performing this procedure. Figure 77: Measurement Cell Block (Exploded VIew) 1. Remove the cell as described in Section 7.5. 2. With the measurement cell in a vertical position, remove the top cell end fitting. Leave the SMA fibre connector in place in the cell end fitting body. Revision 5 117 August 2021 3. Remove the top O-ring. If it is not on the cell window, then it will be in the end cap Oring groove. Discard if there is any sign of damage or deformation. A fine tipped tool may be required to remove the O-Ring from the groove in the cell end fitting. The cell window may also stick to the cell end fitting when it is removed. 4. If the cell window did not come out with the cell end fitting, turn the measurement cell over, holding your hand over the open end, and gently shake until the cell window drops into your hand. Set the window aside on a clean surface. Remove the bottom ORing (if it didn’t drop into your hand with the window). A fine tipped tool may be required. Discard the O-ring if there is any sign of damage or deformation. The cell window may stick to the inner O-Ring and be difficult to remove. If it is, cap all but one port on the top of the measurement cell and blow into the open port, holding a hand under the cell end to catch the cell window. The air pressure should be sufficient to loosen the cell window and allow it to be removed. 5. Repeat Steps 1-4 for the other cell window. If the other cell window sticks to the inner O-Ring, it may be removed by passing a soft tipped tool through the measurement cell and pushing on it gently from the inside until it comes loose. 6. Inspect both windows for damage and/or contaminants. If the windows are damaged (chipped, cracked, discoloured, etc.) discard and replace them with new ones. If the windows are not damaged, they should be cleaned with isopropyl alcohol, using a nonabrasive lint free tissue such as KimWipes® or a cotton swab. Thoroughly rinse the cleaned surface with pharmaceutical grade distilled water. They should be wiped dry using a soft, lint free cloth or tissue. Commercially available lens or window cleaning solutions or prepackaged lens cleaning wipes ARE NOT to be used. These products may contain a compound which leaves an UV absorbing coating on the cell window, which could lead to continued High Integration Period warnings. 7. Inspect the measurement cell body. Clean with isopropyl alcohol, using a nonabrasive lint free tissue such as KimWipes® or a cotton swab. Thoroughly rinse the cleaned surface with pharmaceutical grade distilled water and dry completely before reassembly. 8. Hold the measurement cell vertically and install the new bottom O-Ring in the top window recess, ensuring that it is centred and sitting in the O-Ring seat. 9. Insert the cell window. Handle the window by its edges to prevent fingerprints on the transparent surfaces of the window. 10. Place the top O-ring onto the window and replace the cell end fitting. The O-Ring will self-align as the end fitting is tightened. Tighten the end fitting to hand-tight only. Do not overtighten the cell end fittings. Overtightening these fittings could cause damage or break the windows. Also ensure that there is no crossthreading to avoid damaging the interior threads on the sample cell block.The cell end fitting should screw on smoothly. DO NOT FORCE! Revision 5 118 August 2021 11. Repeat steps 8 to 10 to install the O-rings and window for the other window. Look through the cell and verify that there is an unobstructed light path, with no dirt or other visible contaminants on the cell windows. It may be necessary to remove one or both of the SMA connectors to check the light path. Replace the connectors to hand-tight when done. 12. When both windows are installed, the measurement cell assembly is ready for reinstallation as described in Section 7.8. 7.8 Measurement Cell Installation Once the cell windows have been cleaned or replaced, the measurement cell can be reinstalled in the oven enclosure by following the procedure below. 1. Place the measurement cell in its approximate position focusing on the engagement of the 3/8” elbow Swagelok® fitting connection on the bottom left of the measurement cell block. Once this fitting is engaged, the aspirator drive air inlet fitting on the top left of the measurement cell can also be reconnected to finger tight. 2. Hold the heater bracket plate in place behind the measurement cell block with fingers. Install one (1) of the four (4) ¼-20 x 2" heater bracket screws with a 3/16" ball driver. Do not fully tighten at this point. A small screwdriver or awl may be used to align the tapped holes in the bracket with the screw holes in the measurement cell. 3. Install the remaining screws. Once all four screws have been partly screwed in, they can all be tightened. 4. Install any remaining removed tubing that has yet to be re-installed. 5. Tighten all the Swagelok® fitting connections that were opened during the measurement cell removal process. 6. Open the Zero Air Flow Control valve to about 2 turns. This will pressurize the measurement cell and related plumbing to about 20 psig. 7. Open all the sample flow control valves (V1, V3, V5). Leak check all fittings with Snoop or similar liquid leak detector. Tighten any loose fittings. 8. Connect the short fibre to the SMA fibre connector on the top of the measurement cell. Connect the long fibre to the SMA fibre connector on the bottom of the measurement cell. Hand tighten the nuts. 9. Loosen the set screw holding the SMA fibre connector into the measurement cell slightly so that the SMA fibre connector can rotate and slide in and out. 10. Use the PANEL NEXT / PANEL PREV keys to navigate to the Spectrum panel. Adjust the position of each SMA fibre connector in the measurement cell by rotating it slightly left and right and sliding it in and out to find the position that gives the greatest Peak Height. Once the optimal position is found for each fibre, re-tighten the set screw. Revision 5 119 August 2021 The SMA fibre connector set screws only need to be finger-tight. Do not overtighten the set screws as this may damage the SMA fibre connector. 11. Optimize the integration period by using the FIELD NEXT / FIELD PREV keys to highlight Optimize Integ. Time, then press ENTER. 12. Reinstall the cell RTD with the 6-32 x 3/8" screw using a 7/64" ball driver. 13. Make sure that both fibre optic cables are in their correct indent in the oven enclosure frame, then replace the oven enclosure cover and securely fasten both latches. 14. Reconnect the AC Power to the oven heaters by pushing down and snapping closed the oven heater fuse terminal cover (ACTS:25). The oven will begin heating to the set point temperature. 15. Close and latch the oven enclosure cover. 16. Close and latch the control cabinet and oven cabinet doors. 17. Once the measurement cell temperature rises to >140°C, and the Cell Temperature fault has cleared, use the PANEL NEXT / PANEL PREV keys to navigate to the Analysis 1 panel. Perform a manual zero calibration cycle by using the FIELD NEXT / FIELD PREV keys to highlight Manual Zero, then press ENTER. 18. Once the manual zero calibration cycle is complete, place the analyzer into sampling mode by highlighting the Sample checkbox using the FIELD NEXT / FIELD PREV keys, then press ENTER. Alternatively, press the PURGE key. 19. Once normal operation has been confirmed, return the Online / Offline control toggle on the Analysis 2 panel back to Online (green). The oven can take up to two hours to reach operating temperature. While the cell temperature is below the Low Cell Temperature fault set point, the system will continue to back purge and maintain a fault indication to the control room. 7.9 Steam Purging the Sample Probe Steam Purging the Sample Probe is recommended only when a plug in the probe is suspected and should only be performed as a last resort to avoid the possibility of steam or condensate contamination in the sample cell, particularly on the cell windows. The residue of some boiler water chemicals on the cell windows will cause a loss of spectrometer energy, potentially resulting in High Integration Period warnings or even a fault condition in a worst-case scenario. There are some indications potential warning signs that may indicate the potential need to perform a steam purge of the probe. These include but are not limited to: • Revision 5 Absorbance spectrum and concentration readings remaining at zero even when the analyzer is switched to sampling mode – this indicates that there may be a blockage on the sample inlet side of the probe that is preventing sample from being drawn up the probe and into the measurement cell. 120 August 2021 • • Cell pressure increasing dramatically when analyzer is switched to sampling mode – this indicates that there may be a blockage on the vent side of the probe that prevents the aspirator drive air from entering the process pipe; this will cause a high sample cell pressure. Response time from zero to sample increases for a set aspirator drive air flow rate – this indicates a partial blockage in the sample probe that is restricting the flow rate in the probe and thus increasing the response time. Prior to performing a steam purge, the method described in Section 3.2.1 using adjustments in the zero air flow to clear obstructions in the probe and analyzer sampling system should be attempted. Only if this method is unsuccessful should the steam purge procedure be performed. Steam Purging the Sample Probe is to be performed by trained and authorized personnel only. To perform the a steam purge of the sample probe assembly, follow the procedure below: : 1. Place the analyzer in Offline mode by toggling the Online / Offline control toggle (Section 4.3.1) on the Analysis 2 panel to Offline (red). 2. Place the analyzer in back purge mode by pressing the PURGE key on the keypad OR by placing the X in the Back Purge check box on the Analysis 1 panel. 3. Open the oven cabinet door and remove the black lid on the oven enclosure. The control cabinet door may NOT be opened while the analyzer is energized UNLESS the area is known to be non-hazardous. Observe all the warning labels on the analyzer enclosures. The oven enclosure and all of its components are HOT (150ºC/300ºF). Wear appropriate personal protective equipment (gloves, eye wear, clothing etc) if you are working with hot surfaces or wait until surface have cooled to safe temperatures before performing maintenance tasks. 4. Close valves V1, V3, and V5. Prior to performing a steam purge, Galvanic Applied Sciences also recommends disconnecting the measurement cell side fittings on valves V1 and V3 and install plugs on these valves. This will prevent steam or condensate from entering the measurement cell. 5. Blow down the steam supply lines to be used for steam purging the sample probe assembly prior to connecting to the analyzer to clear the line of any condensate. 6. Connect steam supply lines to the Sample Side Access and/or Vent Side Access ports on the left side of the analyzer cabinet. 7. Switch valves V2 and V4 to the ON position. This will begin the steam purge process. Zero gas will be venting into the oven when the tubing is removed. 8. Re-install the oven enclosure cover. Ensure that the fibre optic cables are still routed in the indent in the oven enclosure frame to avoid damage when the oven enclosure cover is installed. Revision 5 121 August 2021 9. Steam Purge the Sample Probe for between 15 and 30 minutes. 10. When purging is complete, remove the oven enclosure cover. 11. Switch valves V2 and V4 to the OFF position. 12. Disconnect the steam supply lines from the Probe Access ports on the left side of the analyzer cabinet. Replace any sections of tubing that connect the measurement cell to valves V1 and V3 that may have been disconnected prior to the steam purge to allow the back purge air to begin flowing through the probe. 13. Re-install the oven enclosure cover. Ensure that the fibre optic cables are still routed in the indent in the oven enclosure frame to avoid damage when the oven enclosure cover is installed. 14. Close and latch the oven cabinet door. 15. Allow the back purge to continue for five to ten minutes. 20. Once the measurement cell temperature rises to >140°C, and the Cell Temperature fault has cleared, use the PANEL NEXT / PANEL PREV keys to navigate to the Analysis 1 panel. Perform a manual zero calibration cycle by using the FIELD NEXT / FIELD PREV keys to highlight Manual Zero, then press ENTER.. 21. Once the manual zero calibration cycle is complete, place the analyzer into sampling mode by highlighting the Sample checkbox using the FIELD NEXT / FIELD PREV keys, then press ENTER. Alternatively, press the PURGE key. 22. Once normal operation has been confirmed, return the Online / Offline control toggle on the Analysis 2 panel back to Online (green). The oven can take up to two hours to reach operating temperature. While the cell temperature is below the Low Cell Temperature fault set point, the system will continue to back purge and maintain a fault indication to the control room. 7.10 Spectrometer Replacement In very rare cases it may be necessary to replace the analyzer spectrometer. To replace the analyzer spectrometer, refer to Figure 78 while following the procedure below. Replacing the spectrometer is to be performed by trained and authorized personnel only. Revision 5 122 August 2021 2 1 3 4 Figure 78: Spectrometer 1. Place the analyzer in Offline mode by toggling the Online / Offline control toggle (Section 4.3.1) on the Analysis 2 panel to Offline (red). 2. Place the analyzer in back purge mode by pressing the PURGE key on the keypad OR by placing the X in the Back Purge check box on the Analysis 1 panel. 3. Access the purged control cabinet following proper user company and/or regulatory agency procedure. The control cabinet door may NOT be opened while the analyzer is energized UNLESS the area is known to be non-hazardous. Observe all the warning labels on the analyzer enclosures. DO NOT look at the end of disconnected fibres connected to the UV lamp or place them in contact with skin. The intense UV radiation transmitted through these fibres can cause eye and skin damage. Fibres should be capped immediately after disconnection to prevent acidental exposure to UV radiation. 4. Disconnect the USB cable from the front of the spectrometer (#1). 5. Disconnect the air trickle purge line connected to the bottom left corner of the spectrometer (if present) (#3) 6. Disconnect the detector fibre connected to the top of the spectrometer by unscrewing the nut and gently pulling it out of the SMA connector. (#2) Place an orange protective cap over the end of the fibre to prevent damage. 7. Remove the retaining screws that hold the spectrometer to the mounting bracket. (#4). Hold a hand under the spectrometer while removing it to prevent it from falling when the last screw is removed. Revision 5 123 August 2021 8. Mount the new spectrometer on the mounting bracket. It should be oriented with the USB port and serial number label facing forward. Reinstall and tighten fully all mounting screws. 9. Remove the protective cap from the detector fibre optic cable and connect it to the SMA connector on the top of the spectrometer. The nut only needs to be tightened to hand tight. 10. Connect the trickle purge line to the purge port on the spectrometer’s left side. 11. Connect the USB cable to the USB port on the front of the spectrometer. Once the new spectrometer has been installed in the analyzer, it will be necessary to install the new spectrometer matrix file associated with the new spectrometer into the analyzer. Follow the procedure below to update the spectrometer calibration matrix file. 1. Connect a laptop computer to the local Ethernet port. Ensure that the local Ethernet connection displayed in the Config panel Network sub-panel displays as Active. 2. In a web browser program on the connected PC, enter in the IP address of the analyzer followed by /Utility.html (for the local Ethernet port, this would be http://192.9.200.16/Utility.html) to access the Utility page shown in Figure 79. Figure 79: Utility Page 3. Under the Calibration Matrix Upload to Analyzer heading, click on the Browse button. Select the CSV format calibration matrix file with the file name indicated in the one-page PDF document provided along with the spectrometer. The folder in which this file and the calibration matrix will be found will have the spectrometer’s serial number (indicated on a label on the front of the spectrometer) as the folder name. For an example, refer to Figure 80. Revision 5 124 August 2021 Dark Start Pixel and First Vector Pixel to be input via web GUI. Spectrometer Serial Number – Make sure this matches spectrometer serial number label! File name of the spectrometer calibration matrix to be loaded Figure 80: Spectrometer Calibration Matrix PDF Example Select the file indicated by the Load File Named heading at the bottom right of this page, then press OK. Once the file has been selected, click on Calibration Matrix Upload to Analyzer to upload the file. Uploading an incorrect calibration matrix file may render the analyzer unusable. Be absolutely CERTAIN that the matrix file being uploaded is the correct file. If uncertain, contact Galvanic Applied Sciences Inc. for assistance. 4. Once the Calibration Matrix file has successfully uploaded to the analyzer, click on Reboot Analyzer to reboot the analzyer. The analyzer must be rebooted before it will start to use the new calibration matrix file. 5. Once the analyzer has rebooted, navigate to the Calibration Matrix page in the web GUI (refer to Section 5.2.2) and confirm that the first several rows of the displayed calibration matrix match the first several rows of the calibration matrix printed in the PDF file supplied with the spectrometer. 6. Navigate to the Factory Parameters section in the web GUI (refer to section 5.4). Switch to Update mode, then change the Dark Start Pixel value to the Dark value indicated at the bottom of the PDF file. Change the First Vector Pixel to the Start pixel indicated in Revision 5 125 August 2021 the PDF file. Once both parameters have been edited, click on Save to save the changes to the analyzer. Revision 5 126 August 2021 Section 8 8.1 The Product Quality Assurance Program Overview The Galvanic Applied Sciences product quality assurance program is designed to ensure that the system meets all manufacturing specifications and is built to meet the customer’s specific requirements. This chapter consists of a number of forms which provide the overall QA procedure and should be retained. 8.2 Overall System Identification Proposal Purchase Order Number Sales Order Reference Serial Number Customer Name Facility Address Primary Contact Name Primary Contact Telephone Number Primary Contact e-mail Inspection Software Revision Revision 5 127 August 2021 8.3 QA Document Package Check List and Requirements Table 34 is completed during the manufacturing process and QA inspection to ensure that the all relevant operations are performed. Table 34: Document Package Checklist Serial Number: _______________ Description Sample System Pressure Checked - System Heaters Sample System Pressure Checked – Sample System Purge System Checked Aspirator Performance Tested Gas Runs Complete (Calibration Data Sheet) Temperature Sensor Inputs Checked and Calibrated Analog Output Calibration Checked Digital Output Checked System 24VDC Supply Checked Span Factor Set Condenser Solenoid Function Checked Zero Solenoid Function Checked Control Cabinet Air Solenoid Function Checked Operation of Cell Heaters Checked Burn Oven for three (3) weeks Cell Pressure Transducer Checked. Dielectric Strength Test Certificate Completed Matrix and Cal Documents Completed Serial Numbers Recorded Oven Lid Latches Adjusted and Locked Revision 5 128 Initial Date August 2021 Section 9 Drawings Several generic analyzer drawings and schematics are provided in this section. These drawings are also available in PDF format via the Help section Drawing page in the web GUI. For serial number-specific drawings refer to the USB key that is shipped with the analyzer. Figure 81: Mounting and Service Connections Revision 5 129 August 2021 Figure 82: Oven Cabinet Door Removed Revision 5 130 August 2021 Figure 83: Control Cabinet Door Removed Revision 5 131 August 2021 Figure 84: Power, Steam, Air, Signals Connection Details Revision 5 132 August 2021 Figure 85: AC Wiring Schematic Revision 5 133 August 2021 Figure 86: DC Signals and Wiring Diagram Revision 5 134 August 2021 Figure 87: Flow Diagram Revision 5 135 August 2021 Section 10 Specifications Performance Specifications Auto Calibration Zero Drift User Selectable Frequency < 0.25% of full scale per day (based on autozero frequency of once/hour +/- 1% of Full Scale with pressure compensation (with all species present) +/- 1.0 % of Full Scale Better than 0.5% of full scale (with all species present) Analyzer – Near Instantaneous Total System – typically less than 30 seconds (depends on probe length) Accuracy Sensitivity Repeatability Response Time Physical Specifications Size - Outside Dimensions (including Mounting Frame) Analyzer cabinets Weight (Total System on Frame 57” W x 41.25” H x16” D (145 cm x 105 cm x 41 cm) Two cabinets, each 24” W x 30” H x 12” D (61 cm x 76.2 cm x 30 cm) Approximately 275 lbs (125 kg),varies with options Services Required Electrical Instrument Air Steam 100-240 Vac, 1 phase, 50/60 Hz, 800 W 17 SCFM at 80 psi (maximum case with Vortec Cooler) Nozzle – 50 psi Area Classification 943-TGXeNAHy Class I, Division 2, Groups C and D, Temperature Code T3, Type Z Purge IP Protection: NEMA 4 All specifications are subject to change as part of our ongoing product improvement program. Revision 5 136 August 2021 Section 11 Recommended Spare Parts It is recommended that the purchaser have the spare parts indicated in Table 35 (one year of spares) or Table 36 (two years of spares) at the plant site to expedite maintenance and service procedures. Spare Parts can be obtained from: Galvanic Applied Sciences Inc. 7000 Fisher Road SE Calgary, Alberta T2H 0W3 Canada Tel: 403-252-8470 TOLL FREE (CANADA/US): 1 (800) 458 4544 INTERNATIONAL +1 978 848 2708 Fax: 403-255-6287 Email: [email protected] Alternatively, local Galvanic gas products distributors in many countries and regions around the world may be contacted for spare parts assistance. Refer to the distributor list found at the following website: https://www.galvanic.com/service-support/representatives . Table 35: Recommended Spare Parts - 1 Year Kit Item Description Cell Window O Rings for Cell Windows UV Source Lamp Anti-Solarant Solution Fuse, 1.5 Amp Fuse, 2 Amp Fuse, 5 Amp, Slo-Blo Part Number BA7118 CO7134 BA7195 (standard lifespan) OR BA7532 (long lifespan) CO7312 PC7090 PC7089 PC7087 Quantity 2 20 1 Unit of Measurement each each each 1 1 1 1 Bottle Pkg of 5 Pkg of 5 Pkg of 5 Table 36: Recommended Spare Parts - 2 Year Kit Item Description Cell Window O Rings for Cell Windows UV Source Lamp Anti-Solarant Solution Fuse, 1.5 Amp Fuse, 2 Amp Fuse, 5 Amp, Slo-Blo Revision 5 Part Number BA7118 CO7134 BA7195 (standard lifespan) OR BA7532 (long lifespan) CO7312 PC7090 PC7089 PC7087 137 Quantity 4 32 2 (BA7195) OR 1 (BA7523) Unit of Measurement each each each 2 1 1 1 Bottle Pkg of 5 Pkg of 5 Pkg of 5 August 2021 Section 12 12.1 Input / Output (IO) Board Configuration IO Board Web GUI To access the web GUI used to configure the IO board, connect a PC to one of the Ethernet ports on the analyzer’s control board inside the control cabinet, and ensure that the local connection status displayed on the Config panel Network sub panel is showing as Active. The control cabinet door may NOT be opened while the analyzer is energized UNLESS the area is known to be non-hazardous. Observe all the warning labels on the analyzer enclosures. Enter the IP address of the analyzer followed by /io.html (i.e. for a locally connected computer the address would be http://192.9.200.16/io.html) into the address bar of a web browser running on the connected computer and press Enter. The IO board web GUI is shown in Figure 88. Figure 88: IO Board web GUI The Peripheral Board menu on the left side of the screen has four pages, as described in Table 37. Revision 5 138 August 2021 Table 37: IO Board Web GUI Pages Page Title Manual Section Status 12.2 Manual Override 12.3 Analog Inputs N/A Firmware N/A 12.2 Purpose Presents the current status of all inputs and outputs (analog and digital) on the IO board; all data is read only. Used for testing of digital outputs (solenoids and relays) as well as for calibration of the four analog outputs Used for calibration of the analog inputs used for pressure, temperature, and other analog signal measurement inputs to the IO board. NOTE: This section is for factory engineers only. Used for upgrading the IO board firmware. NOTE: This section is for factory engineers only. Status Page The Status page shown in Figure 89 shows the current status of the inputs and outputs that are under the supervision and control of the IO board. The information on this page is read-only and cannot be edited by the user. Figure 89: Status Page At the top of the page is an Online indicator which indicates whether the board is under the control of the analyzer’s control computer. In normal operation, this will always be green. The indicator will be red (Direct Board Control) only when the IO board has been switched to Direct Peripheral Board Control for calibration and/or testing of the board’s inputs and outputs. Refer to Section 12.3 for more information. The Firmware Revision field shows the current firmware version installed on the IO board, which may be useful for troubleshooting purposes. The On Board Temperature field shows the current temperature measured by the IO board’s on board temperature sensor. The remaining five boxes on this page are explained in Table 38. Revision 5 139 August 2021 Table 38: Status Page Sections Section Purpose Calculated Analog Outputs Shows the current calibrated value being received at each of the IO board’s four analog inputs. Displayed measurement units are based on the factory calibration of these inputs. Pressure is the measurement cell pressure input, RTD1 is the measurement cell temperature input, and RTD2 is the probe temperature input (if present). Shows the present expected current output, in milliamps, from each of the four analog outputs on the IO board. These current outputs are based on the analog output’s configured parameter and range. Relays (P4 Connector) Test Shows the current status of the IO board’s four digital (relay) outputs. A grey indicator indicates the relay is in the deenergized (alarm) condition, while a red indicator indicates that the relay is in the energized (normal) condition. P4 Connector indicates that the relay connections are made to the P4 terminal block on the IO board. Analog Inputs Solenoids (P6 Connector) Test Digital Input 12.3 Shows the current status of the IO board’s four solenoid control relays. A grey indicator indicates the solenoid is deenergized, while a red indicator indicates the solenoid is energized. P6 Connector indicates that the solenoid connections are made to the P6 terminal block on the IO board. • Solenoid 1 = cabinet cooler solenoid • Solenoid 2 = Sampling / Backpurge solenoid (energized = sample, deenergized = backpurge) • Solenoid 3 = probe cooler solenoid • Solenoid 4 = oven heater control relay Shows the current status of the IO board’s single digital input. Red indicates the digital input is receiving a signal, while grey indicates it is not receiving a signal. This input can be used for remote triggering of a zero calibration cycle. Manual Override Page The Manual Override page shown in Figure 90 allows the user to take control of the IO board for the purpose of calibrating and testing all available outputs, both analog and digital. This page allows the user to take control of and make changes to the configuration of the IO board of the analyzer. Any change made to the analog output calibration will permanently delete the present value. Access to this page should be limited to qualified users who understand the consequences of making changes on this page. Revision 5 140 August 2021 Figure 90: Manual Override Page In order to make any changes on this page, Direct Peripheral Board Control must first be enabled by placing an X in the checkbox. Once this is enabled, the IO board will be under manual control of the user and the analyzer’s control computer will have no control of this board until this direct board control is manually disabled. The analyzer should be placed into back purge mode and set to Offline state prior to performing any operations under Direct Board Control. When work is complete on this page, the Direct Board Control Enable checkbox must be unchecked manually to return the IO board to automatic control, otherwise the analyzer will be unable to function normally. 12.3.1 Analog Output Calibration and Testing Each Analog Output box allows the user to configure, calibrate, and test an analog output. To configure/calibrate/test an Analog Output, follow the procedure below. This procedure is identical for all four analog outputs: 1. Place a check mark in the Calibrate Analog Output x check box. The fields within the box will become active. Revision 5 141 August 2021 2. The value in the Zero field must be set to 4, and the value in the Span field must be set to 20. 3. Connect a multimeter set to milliamp measurement to the analog output to be calibrated. The analog outputs are all on terminal block P3 of the IO board. The terminals for each analog output are clearly marked on the board. Refer to Figure 91. Loop power available, current loop complete indicator LEDs, one per analog output. Figure 91: Analog Output Terminal Block P3 The analog outputs on the IO board are loop powered, so an external power supply must be provided. The multimeter must be placed in SERIES with the current loop. When the multimeter is connected correctly, a green LED above the analog output wiring connection on the IO board will illuminate to show that the current loop is closed and loop power is being provided, as indicated in Figure 91. 4. Press the Output Zero button. The output current from the analog output will change to approximately 4 mA. 5. Enter the reading from the meter in the Meter Reading field under the Zero heading and press the Auto Cal button. This will adjust the Zero output to exactly 4 mA. If the meter reading is still not exactly 4 mA, repeat the process. 6. Press the Output Span button. The output current from the analog output will change to approximately 20 mA. 7. Enter the reading from the meter in the Meter Reading field under the Span heading and press the Auto Cal button. This will adjust the Span output to exactly 20 mA. If the meter reading is still not exactly 20 mA, repeat the process. 8. The analog output is now calibrated. Press Capture to save the calibration to the board. 9. Test the output by entering the desired mA output in the Test(mA) field and then pressing the Output Test button. This will force the analog output to generate the entered value. In this way the analog output loop can be tested at several readings such as 0, 25, 50, 75 and 100 % of scale (4, 8, 12, 16 and 20 mA). It is advisable that this test be done in conjunction with control room staff to ensure the correct readings are being received not only at a multimeter connected to the analyzer but also at the DCS. Revision 5 142 August 2021 10. If there are any issues with the calibration discovered while performing the test procedure in Step 9, repeat the calibration process in steps 4-8 and test again. 11. Repeat the calibration process steps 1-10 for each additional analog output that needs to be calibrated. 12. When all analog outputs have been calibrated and tested, press Permanent Save to save all changes permanently to the analyzer. This process will take approximately 30 seconds to complete. Below the calibration and test fields for each analog are three read-only fields giving information about the analog output. The Description field shows the analog output number (AO1 – AO4), the Unit field shows the output measurement units (milliamps for all analog outputs), and the Calculated Value field shows the current output current, in milliamps, being output from that analog output. The intensity of the green indicator LED on the IO board for each analog output is directly proportional to the magnitude of the output current. That is to say, the LED will be brighter when outputting 20 mA than when outputting 4 mA. 12.3.2 Testing the Digital Input The IO board has a single digital input at terminal block P5 that is used for remote initiation of a zero calibration cycle. This digital input can be tested using the procedure below. 1. Ensure that Direct Board Control Enable is selected on the Manual Override page. 2. Switch to the Status page. 3. Connect a switch with a 12-24VDC power supply to the digital input terminal block to create an open circuit connected to the digital input terminal block. ‘ The digital input terminal is polarity insensitive. 4. When the switch is open and the circuit is not complete, the Digital Input indicator on the Status page will be grey (inactive). 5. When the switch is closed and the circuit is complete so that 12-24VDC is being received at P5, the Digital Input indicator on the Status page will be red (active). 12.3.3 Testing Digital Outputs There are four digital (relay) outputs available at P4 of the IO board, as shown in Figure 92. Revision 5 143 August 2021 Figure 92: Relay Connection Terminal Block P4 Each relay connection is clearly marked. Relay 1 is Status, Relay 2 is Service, Relay 3 is Mode, and Relay 4 is Control. The relays can be connected either as normally open (NO) whereby the circuit is only complete when the relay is energized or as normally closed (NC) whereby the circuit is complete when the relay is deenergized. There are also 4 solenoid connections at terminal block P6 on the IO board. To test the digital outputs, follow the procedure below. 1. Ensure that Direct Board Control Enable is selected on the Manual Override page. 2. Test each relay. If the relay is currently deenergized, the circle will be grey, and the checkbox will be empty. If the relay is currently energized, the circle will be red, and the checkbox will have a checkmark in it. To energize a deenergized relay, simply place a checkmark in the checkbox by clicking on it. To deenergize an energized relay, remove the checkmark in the checkbox by clicking on it. Confirm with the control room that the signals are being received correctly. If the install location is not too loud, it should also be possible to hear an audible ‘click’ when a relay is energized and deenergized. 3. Test each solenoid if necessary. If the solenoid is currently deenergized, the circle will be grey, and the checkbox will be empty. If the relay is currently energized, the circle will be red, and the checkbox will have a checkmark in it. To energize a deenergized solenoid, simply place a checkmark in the checkbox by clicking on it. To deenergize an energized solenoid, remove the checkmark in the checkbox by clicking on it. Solenoid energization and deenergization should produce audible clicks as the solenoid actuates. Revision 5 144 August 2021 Index Baud Rate, 87 Beer-Lambert Law, 62 Big Endian, 87 3 32 Bit Register Swap, 87 C A Cabinet Cooler Air Valve, 34 Cabinet Deadband, 66 Cabinet Purge Air Flow Adjust Valve, 33 Cabinet Setpoint, 66 Cabinet Temperature, 34, 51 Cabinet Temperature Dead Band, 84 Cabinet Temperature Set Point, 84 Calibration Matrix, 15, 75, 82 Calibration Matrix Page (Web Based GUI), 75 Calibratoin Matrix Absorbance, 62, 81 Absorbance Page (Web Based GUI), 80 Absorbance Panel, 57 Absorbance Spectrum, 81 Appearance in Back Purge, 58, 82 Appearance when Sampling, 58, 82 Calculation, 81 AC Power Connection Procedure, 27 AC Terminal Strip (ACTS), 27 Air Demand, 14, 46 Ambient Temperature Range, 19 Analog Input 3 is Hydrogen, 85 Analog Outputs, 17, 38, 59 Upload to Analyzer, 123 Cell Length, 62, 92 Cell O-Rings, 117 Cell Pressure, 51 Cell Prop Band, 66 Cell Setpoint, 66 Cell Temperature, 51 Calibration and Testing Procedure, 140 Configuration Parameters, 60 Hold, 38, 41, 60, 93 Signal Cable Connection, 27 Track, 38, 60, 93 Effect of Aspirator Drive Air Flow, 37 Cell Temperature Proportional Band, 84 Cell Temperature Reset Time, 84 Cell Temperature Set Point, 84 Cell Windows, 116 Analysis 1 Panel, 45 Manual Zero Control. See Manual Zero Relay Indicators, 47 Analysis 2 Panel, 49 Analysis Page (Web Based GUI), 71 Cleaning, 117 Cleaning / Replacement Procedure, 117 Cell WIndows Air Demand Trend, 74 H2S/SO2 Trend, 74 Relay Indicators, 73 Status and Control, 73 Value Display, 72 Replacement, 116 Condenser Cooling Air Adjust Valve, 36 Configuration Page Configurable Parameters, 84 Analysis Section, 71 Analyzer Dimensions, 19 Analyzer Support Structure, 22 Anti-Solarant Solution, 100 Configuration Panel, 59 Aspirator, 16, 37 Aspirator Drive Air Flow Adjust Valve, 37 Auto Cal Interval, 65, 84 Available Points, 87 Configuration Section, 83 Control Board, 17 Control Cabinet, 15 Control Output, 41, 74 Calculation Sub-Panel, 61 Display Sub-Panel, 63 Network Sub-Panel, 68 Outputs Sub-Panel, 59 Timers/Alarms Sub-Panel, 64 Changing Frequency, 100 Procedure for Changing, 100 Fault Status, 88 Relay Status, 88 D B Dark Level, 55, 79 Dark Start Pixel, 92 Data Bits, 87 Back Purge, 17, 36, 48, 73 Revision 5 145 August 2021 I Digital Input Testing, 142 Digital Outputs. See Relay Outputs Direct Connect, 68 Display Board, 17 Drawing Page (Web Based GUI), 94 Drawings Indicators Page (Web Based GUI), 76 Indicators Panel, 51 Ingress Protection (IP) Rating, 20 Installation Procedure, 21 Instrument Air AC Wiring Schematic, 132 Control Cabinet Door Removed, 130 DC Signals and Wiring Diagram, 133 Flow Diagram, 134 Mounting and Service Connections, 128 Oven Cabinet Door Removed, 129 Power, Steam, Air, Signals Connection Details, 131 Clearing Sample Handling System Blockages, 36 Flow Control Settings, 33 Pressure and Flow Requirements, 20 Pressure Regulator, 38 Pressure Regulator, 29 Supply Connection, 29 Probe Integration Period, 55, 85 E Automatic Optimization Procedure, 103 Manual Optimization Procedure, 103 Optimization, 55, 79 Enron Modbus Format, 89 Ethernet Port, 17 Integration Time. See Integration Period, See Integration Period IO Board, 17, 27, 28 Configuration Settings, 68 Local Connection. See Direct Connect Remote Connection. See Network Web Based GUI. See IO Board Web GUI IO Board Web GUI, 137 F Direct Peripheral Board Control, 138, 140 Manual Override Page, 139 Peripheral Board Menu, 137 Status Page, 138 Factory Parameters Page (Web Based GUI), 91 IP Port Number, 87 Available Parameters, 92 Factory Reference, 56 Factory Section, 91 Fault Condition, 16, 40, 52 K Keypad, 15, 44 Description of Each Type, 53, 77 Key Functions, 44 Fibre Optic Cables, 14, 100 Replacement, 107 SMA Connector, 107 Testing, 107 Testing / Replacment Procedure, 107 L Little Endian, 87 Local Display Filter Points, 84 First Vector Pixel, 55, 92 First Vector Pixel Level, 79 Fixed Pressure, 63, 85 Fixed Temperature, 63, 85 Absorbance panel. See Absorbance Panel Analysis 1 Panel. See Analysis 1 Panel Analysis 2 panel. See Analysis 2 Panel Config panel. See Configuration Panel Indicators panel. See Indicators Panel Spectrum panel. See Spectrum Panel User Interface, 43 H Loss of Purge Signal, 31, 41 Low Cabinet Temperature Alarm, 84 Low Cell Alarm Setpoint, 67 Low Cell Temperature Alarm, 84 Low Probe Alarm Setpoint, 67 Low Probe Temperature Alarm, 84 Hazardous Area Certification, 20 Help Section, 94 High Cabinet Temperature Alarm, 84 High Cell Temperature Alarm, 84 High Probe Temperature Alarm, 84 High S8 Fault Setpoint, 67 High S8 Warn Setpoint, 67 High SVAP Alarm, 84 High SVAP Warning, 84 Revision 5 / M Maintenance Check Out Procedure, 97 Manual Zero, 47, 73 146 August 2021 Manufacturer’s Warranty, 12 Mating of the Process and Analyzer System Flanges, 23 Measure Analog Input, 85 Measurement Cell Changing the Passwords, 94 Factory Password, 92 Peak Height, 55, 56 Plant Factor, 14, 62, 93 Probe Control, 93 Probe Deadband, 66 Probe Setpoint, 66 Probe Temperature, 51 Probe Temperature Dead Band, 84 Probe Temperature Set Point, 84 Product Quality Assurance Program, 126 Purge Control Box, 30, 33 Purge Flow Control Valve, 30 Purge Indicator, 31, 33 Installation, 118 Removal, 115 Modbus Address, 87 Modbus Items, 87 Modbus List Adding Items, 89 Loading a List, 88 Making a New List, 88 Rearranging Items, 89 Saving a List, 88 Modbus Page Q Available Points. See Available Points Communication Parameters, 86 Modbus Items. See Modbus Items QA Inspection, 127 Modbus Page (Web Based GUI), 86 Mode Output, 40, 74 Modicon with Floating Point Format, 91 Modicon-16 Modbus Format, 90 Modicon-32 Modbus Format. See Modbus with Floating Point Format Mounting Dimensions, 22 R Read Only mode (Web Based GUI), 85 Relay Outputs, 17, 39 Control. See Control Output Loss of Purge. See Loss of Purge Signal Mode. See Mode Output Service. See Service Output Signal Cable Connection, 28 Status. See Status Output Testing, 143 N Navigation Menu, 71 Network, 68 Response Time Sample, 37 Zero, 36 Automatic Configuration via DHCP, 69 Manual Configuration, 69 Revision History Page (Web Based GUI), 95 Routine preventative maintenance, 96 New Reference Function, 57, 80 Normal Operating Parameter and Indicator Conditions, 97 S O Safety Guidelines, 10 Safety Symbols, 9 Sample Handling System, 16 Sample Probe, 16 Offline Mode, 45, 73 Online / Offline Mode Toggle, 41, 45, 50 Effect on Control Relay, 41 Condenser, 16, 35 Installation Procedure, 24 Steam Purge, 17, 120 Steam Purge Procedure, 120 Online Mode, 45, 73 Operating Ratio, 14, 46, 62, 93 Operating Voltage, 19 Oven Cabinet, 15 Oven Enclosure, 17 Oven Heaters Sample Probe Nozzle, 17, 31 Sample Rate, 63, 85 Sampling Mode, 73 Serial Port, 17 Service Output, 40, 74 Solenoids Powering Off, 107 P Testing, 143 Parameters Page (Web Based GUI), 83 Parity, 87 Password (Web Based GUI), 85, 88 Revision 5 Span Factor, 62, 92 Spare Parts, 136 147 August 2021 Specifications Enclosure Layout, 112 Lifespan, 111 Mounting Orientation, 113 Power Off Switch, 112 Replacement Procedure, 111 Troubleshooting, 110 Hazardous Area Classification, 135 Performance, 135 Physical, 135 Required Services, 135 Spectrometer, 14, 54, 75, 78 Parameters, 54, 79 Replacement Procedure, 122 V Spectrum, 54, 78 Vortex Cooler, 34 Absorbance. See Absorbance Spectrum Comparison with Factory Reference, 57, 80 W Spectrum Page (Web Based GUI), 78 Spectrum Panel, 54 Spectrum Peak. See Peak Height Status Output, 39, 74 Steam Warning Condition, 40, 52 Description of Each Type, 53, 77 Web Based GUI Analysis Section. See Analysis Section Configuration Section. See Configuration Section Factory Section. See Factory Section Help Section. See Help Section Navigation Menu. See Navigation Menu Overview, 70 Utility Page, 123 Pressure and Temperature Requirements, 20 Supply Connections, 31 Steam Heater, 17 Steam Jacketed Ball Valve, 22 Stop Bits, 87 SVAP Dead Band, 84 SVAP Set Point, 84 Z T Zero Air Flow Adjust Valve, 36 Zero Calibration, 16, 36, 47 Transmission Spectrum. See Spectrum Troubleshooting Remote Trigger by DIgital Input, 142 Sequence of Events, 48 Potential Solutions, 106 Zero Gas, 16 Zero Hold Interval, 41, 48, 65, 85 Zero Purge Interval, 48, 65, 85 Zero Sample Rate, 63, 85 U Update Mode, 94 Update Mode (Web Based GUI), 85, 88, 92 User Manual Page (Web Based GUI), 95 UV Source Lamp, 14, 100 Revision 5 148 August 2021 Reason for Revision The changes incorporated in Revision 4 of the Operation Manual are in the addition of the level of detail for clarity only and do not affect product, processes or methods of protection used for approval. Revision 5 149 August 2021
advertisement
Key Features
- UV Spectroscopy
- H2S & SO2 Measurement
- Heated Sample Probe
- Condenser
- Local Display & Keypad
- Web-based GUI
- Analog & Digital Outputs
Related manuals
Frequently Answers and Questions
What is the purpose of the 943-TGXeNA analyzer?
The 943-TGXeNA analyzer is used to measure the concentration of hydrogen sulfide (H2S) and sulfur dioxide (SO2) in tail gas streams.
What type of technology does the analyzer use for measurement?
It utilizes UV spectroscopy to determine the concentration of H2S and SO2.
What are the advantages of using the 943-TGXeNA analyzer?
The analyzer provides accurate and reliable measurements, features a robust sample handling system, and offers both local and remote control options.
How can I access the analyzer's data remotely?
The 943-TGXeNA has a web-based graphical user interface (GUI) that allows you to monitor and control the analyzer remotely.
What type of outputs are available on the 943-TGXeNA analyzer?
The analyzer provides both analog and digital outputs for integration with process control systems.
advertisement