NetWave NW6030 Installation, Operation And Maintenance Manual
Add to My manuals191 Pages
The NetWave NW6030 Analogue Microphone is a crucial component of any comprehensive maritime communication system. It's designed for clear and reliable voice transmission, capturing vital conversations and announcements onboard vessels. This unit is seamlessly integrated with NetWave's VDR system, ensuring secure recording and playback of audio data for safety and compliance purposes.
advertisement
▼
Scroll to page 2
of
191
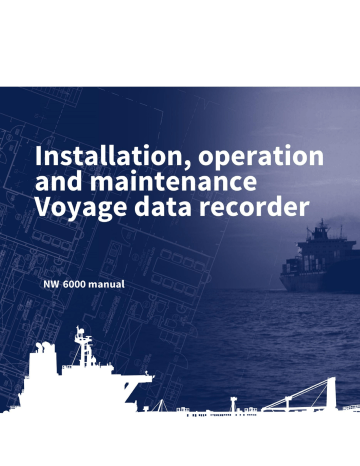
Contact Manufacturer: Orolia B.V. (NetWave Systems) Blauw Roodlaan 100 2718SJ Zoetermeer The Netherlands Telephone: +31 (0)88 11 81 500 +31 (0)6 215 021 67 (24/7) www.oroliamaritime.com [email protected] All rights reserved. Apart from exceptions provided by the law, nothing from this publication may be reproduced, duplicated and/or published, transmitted, transcribed, translated or stored in any form or by any means duplicated and/or published by means of photocopy, microfilm, storage in computer files or otherwise, which also applies to full or partial processing, without the written consent of Orolia Netwave Although the utmost care has been taken with this publication, errors and omissions cannot be entirely excluded. Orolia NetWave or its employees or subcontractors therefore accept no liability, not even for direct or indirect damage, occurring due to or in relation with the application of publications issued by Orolia NetWave. Table of content CONTACT ........................................................................................................................................................... 2 GENERAL.......................................................................................................................................................... 10 MANUAL ORGANIZATION ................................................................................................................................ 10 AMENDMENT RECORDS (VERSIONS)................................................................................................................ 11 SAFETY PRECAUTIONS AND WARNINGS .......................................................................................................... 13 ABBREVIATIONS .............................................................................................................................................. 15 TERMS ............................................................................................................................................................. 17 LIST OF SPECIFICATIONS .................................................................................................................................. 19 IMO GUIDELINES ON VOYAGE DATA RECORDER OWNERSHIP AND RECOVERY ................................................ 21 SERVICE REQUEST ............................................................................................................................................ 23 PART 1: INSTALLATION MANUAL ..................................................................................................................... 24 1. SPECIFICATION SHEET ............................................................................................................................. 24 2. INTRODUCTION ...................................................................................................................................... 25 2.1 2.2 2.3 2.4 2.5 2.5.1 2.5.2 2.6 2.6.1 2.6.2 2.7 2.8 2.9 2.10 OVERVIEW ........................................................................................................................................................ 25 ARCHITECTURE ................................................................................................................................................... 26 INTERFACING ..................................................................................................................................................... 27 POWER FAILURE ................................................................................................................................................. 27 NETWORK PROTOCOLS AND IP ADDRESS RANGES INCL. LWE ....................................................................................... 27 IP ADDRESS FOR ASSIGNMENT ............................................................................................................................... 28 SPECIFICATIONS FOR VIDEO USING LIGHT WEIGHT ETHERNET (IEC-61162-450) ............................................................ 28 MULTICAST ADDRESS RANGE ................................................................................................................................. 29 UDP MULTICAST PROTOCOL ................................................................................................................................. 29 USE OF MULTICAST ADDRESSES AND PORT NUMBERS.................................................................................................. 29 CABLING REQUIREMENTS ...................................................................................................................................... 29 MINIMUM REQUIREMENTS ................................................................................................................................... 29 TERMINATION .................................................................................................................................................... 29 CABLE RECOMMENDATION ................................................................................................................................... 30 3. INSTALLATION GUIDELINE ...................................................................................................................... 31 4. SYSTEM COMPONENTS ........................................................................................................................... 32 5. NW6000 VDR CORE MODULE (19” ENCLOSURE) ..................................................................................... 33 5.1 5.2 5.3 5.4 5.5 5.6 5.7 5.8 5.9 GENERAL........................................................................................................................................................... 33 LOCATION AND MOUNTING ................................................................................................................................... 33 POWER SUPPLY .................................................................................................................................................. 34 ETHERNET ......................................................................................................................................................... 35 CONTACTS ......................................................................................................................................................... 37 DATA COMMUNICATIONS ..................................................................................................................................... 37 INDICATORS ....................................................................................................................................................... 38 ERRORS ............................................................................................................................................................ 38 OPERATING INSTRUCTIONS ................................................................................................................................... 38 6. NW6010 BRIDGE CONTROL UNIT ............................................................................................................ 39 6.1 GENERAL........................................................................................................................................................... 39 Page 3/ 191 6.2 6.3 6.4 6.5 6.6 6.7 6.8 6.9 LOCATION AND MOUNTING ................................................................................................................................... 39 POWER ............................................................................................................................................................. 40 CONNECTIONS.................................................................................................................................................... 40 DATA COMMUNICATIONS ..................................................................................................................................... 41 INDICATORS ....................................................................................................................................................... 42 ERRORS ............................................................................................................................................................ 42 CONFIGURATION ................................................................................................................................................ 42 OPERATING INSTRUCTIONS ................................................................................................................................... 42 7. NW6060 VHF / AUDIO INTERFACE .......................................................................................................... 43 7.1 7.2 7.3 7.4 7.5 7.6 7.7 7.8 7.9 GENERAL........................................................................................................................................................... 43 POWER SUPPLY .................................................................................................................................................. 43 CONNECTIONS.................................................................................................................................................... 43 DATA COMMUNICATIONS ..................................................................................................................................... 44 INDICATORS ....................................................................................................................................................... 44 ERRORS ............................................................................................................................................................ 44 CONFIGURATION ................................................................................................................................................ 44 OPERATING INSTRUCTIONS ................................................................................................................................... 44 TESTING VHF RADIOS PROCEDURE ......................................................................................................................... 44 8. NW6030 ANALOGUE MICROPHONES ...................................................................................................... 46 8.1 8.2 8.3 8.4 8.5 8.6 8.7 8.8 8.9 GENERAL........................................................................................................................................................... 46 LOCATION AND MOUNTING ................................................................................................................................... 46 POWER ............................................................................................................................................................. 48 CONNECTIONS.................................................................................................................................................... 48 AUDIO SIGNALS .................................................................................................................................................. 48 INDICATOR ........................................................................................................................................................ 49 ERRORS ............................................................................................................................................................ 49 CONFIGURATION ................................................................................................................................................ 49 OPERATING INSTRUCTIONS ................................................................................................................................... 49 9. NW6031 AUDIO HUB .............................................................................................................................. 50 9.1 9.2 9.3 9.4 9.5 9.6 9.7 9.8 GENERAL........................................................................................................................................................... 50 LOCATION AND MOUNTING ................................................................................................................................... 50 POWER ............................................................................................................................................................. 50 CONNECTIONS.................................................................................................................................................... 51 INDICATOR ........................................................................................................................................................ 51 ERRORS ............................................................................................................................................................ 52 CONFIGURATION ................................................................................................................................................ 52 OPERATING INSTRUCTIONS ................................................................................................................................... 52 10. NW6044 VIDEO INTERFACE (OPTION) ................................................................................................... 53 10.1 GENERAL........................................................................................................................................................... 53 10.2 LOCATION AND MOUNTING ................................................................................................................................... 54 10.3 POWER SUPPLY .................................................................................................................................................. 55 10.4 CONNECTIONS.................................................................................................................................................... 55 10.5 DATA COMMUNICATIONS ..................................................................................................................................... 56 10.6 INDICATORS ....................................................................................................................................................... 56 10.7 ERRORS ............................................................................................................................................................ 56 10.8 PC SET-UP ......................................................................................................................................................... 56 10.9 CONFIGURATION ................................................................................................................................................ 57 10.10 VIDEO CHANNEL CONFIGURATION FILE ................................................................................................................... 58 10.11 VIDEO CONFIGURATION SUITE (VCS2) APPLICATION ................................................................................................. 61 Page 4/ 191 10.12 VIDEO CAPTURE ................................................................................................................................................. 62 10.13 HORIZONTAL POLARIZATION ................................................................................................................................. 63 10.14 VERTICAL POLARIZATION ...................................................................................................................................... 64 10.15 SIZING .............................................................................................................................................................. 65 10.16 HORIZONTAL/VERTICAL OFFSET............................................................................................................................. 65 10.17 DIMENSIONS...................................................................................................................................................... 67 10.18 INTERLACED IMAGE ............................................................................................................................................. 69 10.19 INTERLEAVED IMAGE ........................................................................................................................................... 74 10.20 RECALIBRATION .................................................................................................................................................. 76 10.21 ADJUSTMENTS TAB ............................................................................................................................................. 79 10.22 SHARPNESS........................................................................................................................................................ 80 10.22.1 PHASE ..................................................................................................................................................... 80 10.22.2 CPMP (CHARGE PUMP) ............................................................................................................................ 80 10.22.3 VCO (VOLTAGE CONTROLLED OSCILLATORS).................................................................................................. 80 10.23 GAIN/OFFSET .................................................................................................................................................... 81 10.24 CLAMP ............................................................................................................................................................. 82 10.25 COAST .............................................................................................................................................................. 83 10.26 SYNC-ON-GREEN (SOG) ...................................................................................................................................... 83 10.27 INFO TAB .......................................................................................................................................................... 84 10.28 VCS2 MENU OVERVIEW ...................................................................................................................................... 85 10.29 TEST VIDEO INPUTS ............................................................................................................................................. 86 11. NW6880 (FFRM) FLOAT FREE CAPSULE JOTRON TRON 40 MKII .............................................................. 87 11.1 GENERAL SPECIFICATIONS ..................................................................................................................................... 87 11.2 LOCATION AND MOUNTING ................................................................................................................................... 89 11.3 CONNECTION TEST WITH FLYING CABLE.................................................................................................................... 93 11.4 JUNCTION BOX ................................................................................................................................................... 94 11.4.1 GROUNDING OF CABLES AND JUNCTION BOX ................................................................................................... 94 11.4.2 WIRE SCHEMATIC JUNCTION BOX.................................................................................................................. 96 11.5 (LED) INDICATORS ON DOCKING MODULE................................................................................................................. 98 11.6 WARNINGS........................................................................................................................................................ 98 11.7 OPERATING INSTRUCTIONS ................................................................................................................................... 98 12. NW6860 (FRM) FIXED HSS CAPSULE ....................................................................................................... 99 12.1 12.2 12.3 12.4 12.5 12.6 12.7 12.8 12.9 GENERAL........................................................................................................................................................... 99 LOCATION AND MOUNTING ................................................................................................................................. 101 POWER SUPPLY ................................................................................................................................................ 101 INSTALLATION AND CONNECTIONS ........................................................................................................................ 101 DATA COMMUNICATIONS ................................................................................................................................... 104 INDICATORS ..................................................................................................................................................... 104 ERRORS .......................................................................................................................................................... 104 CONFIGURATION .............................................................................................................................................. 104 OPERATING INSTRUCTIONS ................................................................................................................................. 104 13. NW6890 FRM POE SPLITTER BOX FOR NON-NETWAVE CAPSULES .........................................................105 13.1 13.2 13.3 13.4 GENERAL......................................................................................................................................................... 105 LOCATION AND MOUNTING ................................................................................................................................. 105 POWER ........................................................................................................................................................... 105 CONNECTIONS.................................................................................................................................................. 106 14. NW64900 DATA ACQUISITION SYSTEM ................................................................................................107 14.1 GENERAL......................................................................................................................................................... 107 14.2 LOCATION AND MOUNTING ................................................................................................................................. 108 Page 5/ 191 14.3 POWER SUPPLY ................................................................................................................................................ 108 14.4 CONNECTIONS.................................................................................................................................................. 108 14.5 WIRING SCHEME............................................................................................................................................... 109 15. NW6410 WAVENET BUSCOUPLER ..........................................................................................................111 15.1 GENERAL......................................................................................................................................................... 111 15.2 LOCATION AND MOUNTING ................................................................................................................................. 111 15.3 POWER SUPPLY ................................................................................................................................................ 111 15.4 DAQ CARD POWER BUDGET .............................................................................................................................. 111 15.5 CONNECTIONS.................................................................................................................................................. 112 15.6 DATA COMMUNICATIONS ................................................................................................................................... 113 15.7 INDICATORS ..................................................................................................................................................... 113 15.8 ERRORS .......................................................................................................................................................... 113 15.9 CONFIGURATION .............................................................................................................................................. 113 15.10 OPERATING INSTRUCTIONS ................................................................................................................................. 113 16. NW64208/16 SERIAL/NMEA 8/16 CHANNEL ADAPTORS .......................................................................114 16.1 16.2 16.3 16.4 16.5 16.6 16.7 16.8 16.9 GENERAL......................................................................................................................................................... 114 MOUNTING ..................................................................................................................................................... 114 POWER SUPPLY ................................................................................................................................................ 114 CONNECTIONS.................................................................................................................................................. 115 DATA COMMUNICATIONS ................................................................................................................................... 117 INDICATORS ..................................................................................................................................................... 117 ERRORS .......................................................................................................................................................... 117 CONFIGURATION .............................................................................................................................................. 117 OPERATING INSTRUCTIONS ................................................................................................................................. 117 17. NW64308/16/24 DIGITAL 8/16/24 CHANNEL ADAPTORS ......................................................................117 17.1 17.2 17.3 17.4 17.5 17.6 17.7 17.8 17.9 GENERAL......................................................................................................................................................... 117 MOUNTING ..................................................................................................................................................... 117 POWER SUPPLY ................................................................................................................................................ 118 CONNECTIONS.................................................................................................................................................. 119 DATA COMMUNICATIONS ................................................................................................................................... 122 INDICATORS ..................................................................................................................................................... 122 ERRORS .......................................................................................................................................................... 122 CONFIGURATION .............................................................................................................................................. 122 OPERATING INSTRUCTIONS ................................................................................................................................. 122 18. NW64404/08/12 ANALOGUE 4/8/12 CHANNEL ADAPTORS ...................................................................123 18.1 18.2 18.3 18.4 18.5 18.6 18.7 18.8 18.9 GENERAL......................................................................................................................................................... 123 MOUNTING ..................................................................................................................................................... 123 POWER SUPPLY ................................................................................................................................................ 123 CONNECTIONS.................................................................................................................................................. 124 DATA COMMUNICATIONS ................................................................................................................................... 127 INDICATORS ..................................................................................................................................................... 127 ERRORS .......................................................................................................................................................... 127 CONFIGURATION .............................................................................................................................................. 127 OPERATING INSTRUCTIONS ................................................................................................................................. 127 19. CONNECTING TO THE VDR FOR CONFIGURATION OF THE SYSTEM ........................................................128 19.1 PHYSICALLY CONNECTING TO THE VDR.................................................................................................................. 128 19.2 CHECKING FOR CONNECTED SENSOR TO THE VDR.................................................................................................... 129 19.3 CHANGE OF TYPE OF THE VDR............................................................................................................................. 130 Page 6/ 191 19.4 CONFIGURING THE VDR..................................................................................................................................... 130 19.4.1 ON-LINE CHECK OF INCOMING DATA............................................................................................................ 130 19.4.2 CONFIGURATION PAGE ............................................................................................................................. 131 19.4.3 CONFIGURING THE OPT ........................................................................................................................... 135 19.4.4 CONFIGURING THE LWE VIDEO .................................................................................................................. 136 20. CREATING A DOWNLOAD FROM THE VDR SYSTEM ................................................................................138 20.1 DOWNLOAD DATA SET ....................................................................................................................................... 138 21. PLAYBACK SOFTWARE ...........................................................................................................................139 21.1 OBTAINING THE PLAYBACK SOFTWARE .................................................................................................................. 139 21.2 INSTALLATION OF PLAYBACK SOFTWARE - CLIENT/STANDALONE PC ............................................................................ 139 22. NW6000 WEB PAGE ...............................................................................................................................140 22.1 DASHBOARD .................................................................................................................................................... 140 22.2 INSTALLING OROLIA VDR CERTIFICATE.................................................................................................................. 141 22.3 LIVE VIDEO ...................................................................................................................................................... 143 22.4 ANNUAL PERFORMANCE TEST ............................................................................................................................. 144 22.5 CONFIGURATOR................................................................................................................................................ 144 22.5.1 LWE SETTINGS ....................................................................................................................................... 145 22.5.2 VLAN SETTINGS ..................................................................................................................................... 146 22.5.3 BAM SETTINGS ...................................................................................................................................... 147 22.5.4 ADVANCED SETTINGS ............................................................................................................................... 149 22.6 ANALYZE TOOL ................................................................................................................................................. 150 22.7 BAM TOOL ..................................................................................................................................................... 151 22.8 REBOOTING THE VDR ........................................................................................................................................ 152 23. BAM INTERFACE SPECIFICATION ............................................................................................................153 23.1 23.2 23.3 23.4 BRIDGE ALERT MANAGEMENT (BAM) ................................................................................................................. 153 MANUFACTURER ID .......................................................................................................................................... 153 SUPPORTED NMEA MESSAGES ........................................................................................................................... 153 ALERT IDENTIFIERS ............................................................................................................................................ 154 24. FREQUENTLY ASKED QUESTIONS ...........................................................................................................155 24.1 BROWSER SHOWS INSECURE WEBPAGE ................................................................................................................ 155 24.2 BROWSER COMPATIBILITY WITH VDR WEB SERVER ................................................................................................ 156 24.2.1 FIREFOX COMPATIBILITY ........................................................................................................................... 156 24.3 WHAT IS THE RECORDING CAPACITY OF THE VDR? .................................................................................................. 157 PART 2: OPERATOR AND MAINTENANCE MANUAL .........................................................................................158 1. ROUTINE MAINTENANCE .......................................................................................................................158 1.1 1.1.1 1.1.2 1.2 1.2.1 1.2.2 1.2.3 1.2.4 1.2.5 1.2.6 1.3 ANNUAL PERFORMANCE TEST ............................................................................................................................. 158 GENERAL......................................................................................................................................................... 158 REPLACEMENT/MAINTENANCE BEACON AND BATTERIES CORE MODULE ...................................................................... 158 OPERATIONAL PERFORMANCE TEST...................................................................................................................... 158 GENERAL......................................................................................................................................................... 158 AUDIO TEST ................................................................................................................................................... 160 VIDEO TEST .................................................................................................................................................... 161 NMEA TEST .................................................................................................................................................... 162 OPT LOG ........................................................................................................................................................ 163 ERRORS .......................................................................................................................................................... 163 TRON 40VDR FLOAT FREE CAPSULE ................................................................................................................... 164 Page 7/ 191 1.3.1 1.3.2 1.3.3 1.3.4 1.3.5 1.3.6 GENERAL......................................................................................................................................................... 164 NORMAL SELF-TEST ........................................................................................................................................... 164 EXTENDED SELF-TEST INCLUDING GPS-TEST ........................................................................................................... 164 ERRORS .......................................................................................................................................................... 165 VISUAL INSPECTION ........................................................................................................................................... 165 REPLACEMENT/MAINTENANCE HRU, EPIRB MODULE/BATTERY PACK, TRON 40VDR (CAPSULE AND BRACKET) ............... 166 2. NW6010 BRIDGE CONTROL UNIT ...........................................................................................................167 2.1 2.2 2.3 2.4 2.5 2.6 2.7 2.7.1 2.7.2 2.7.3 2.7.4 2.7.5 2.7.6 2.7.7 2.8 2.9 2.10 2.11 GENERAL......................................................................................................................................................... 167 LOCATION AND MOUNTING ................................................................................................................................. 167 INDICATORS ..................................................................................................................................................... 167 ERRORS .......................................................................................................................................................... 167 OPERATING INSTRUCTIONS ................................................................................................................................. 167 SCREEN DESCRIPTION......................................................................................................................................... 168 ALERT CONDITIONS INDICATED ON BCU ................................................................................................................ 169 POWER FAILURE ............................................................................................................................................... 169 RECORDING CHANNELS NMEA ........................................................................................................................... 169 RECORDING CHANNELS AUDIO ............................................................................................................................. 169 RECORDING CHANNELS VIDEO DATA...................................................................................................................... 169 STORAGE......................................................................................................................................................... 170 SWITCH .......................................................................................................................................................... 170 HARDWARE MALFUNCTION ................................................................................................................................. 170 OPERATING SCREENS ......................................................................................................................................... 170 ALERT LOGGING................................................................................................................................................ 171 SOFTWARE VERSION RECOGNITION ....................................................................................................................... 171 SCREEN TEST .................................................................................................................................................... 172 3 NW6880 TRON 40VDR FRM FLOAT FREE CAPSULE .................................................................................173 3.1 3.2 GENERAL......................................................................................................................................................... 173 LED INDICATION................................................................................................................................................ 173 4 NW6860 FIXED HSS CAPSULE .................................................................................................................174 4.1 4.2 4.3 GENERAL......................................................................................................................................................... 174 INDICATORS ..................................................................................................................................................... 174 ERRORS .......................................................................................................................................................... 174 5 PLAYBACK SOFTWARE ...........................................................................................................................175 5.1 5.2 5.3 5.4 5.5 5.6 5.7 5.8 5.9 5.10 SETTING UP THE PC ........................................................................................................................................... 175 OBTAINING THE PLAYBACK SOFTWARE .................................................................................................................. 176 INSTALLATION OF PLAYBACK SOFTWARE – CLIENT/STANDALONE PC........................................................................... 177 STARTING THE PLAYBACK APPLICATION ................................................................................................................. 178 CONFIGURATION FILE ........................................................................................................................................ 179 DOWNLOADING A DATASET FROM RECORDING MEDIUM ......................................................................................... 180 CHOOSING AN EXISTING DATASET ......................................................................................................................... 182 STARTING DATA PLAYBACK .................................................................................................................................. 183 CONVERSION OF EXTRACTED DATA ....................................................................................................................... 185 LOGGING FUNCTIONS......................................................................................................................................... 186 7. PLAYBACK SOFTWARE DETAILS ...................................................................................................................186 7.1 7.2 PASSWORDS .................................................................................................................................................... 186 PLAYBACK CONTROLS ........................................................................................................................................ 186 8. ANNEX I; EQUIPMENT DECOMMISSIONING ...........................................................................................187 Page 8/ 191 8.1 RMRS RULES FOR EQUIPMENT DECOMMISSIONING................................................................................................. 187 9. ANNEX II; ENERGY SAVING ....................................................................................................................189 9.1 9.2 VDR PCB CONTROLLERS .................................................................................................................................... 189 POWER CONSUMPTION CALCULATION ................................................................................................................... 189 10. ANNEX III; EQUIPMENT LABELLING RMRS .............................................................................................190 Page 9/ 191 General Manual organization The following publications are applicable to the NW6000 series of Voyage Data Recorders. NW6000-00 NW6000-10 NW6000-20 NW6000-60 NW6000-90 Operator and maintenance manual* Installation manual * Netwave SVDR VDR Annual Performance Report Form * Authority access manual VDR Commissioning PT and TA certificates * * This documentation needs to remain on board the vessel. The ‘Operator and maintenance manual’ and the ‘Installation manual’ used to be 2 separate documents. These are now merged into this document: ‘Installation, operation and maintenance Voyage data recorder NW6000-manual’. General part Please note that the general part of this document relates both to the Installation manual and Operator and maintenance manual. Part 1: Installation manual (NW6000-00) This part covers all physical and wiring aspects of the VDR installation up until the moment the system is powered-up and includes configuration of all sensors connected (recording channels) thereafter. It therefore covers all information required to commission the VDR and is intended for the authorized (certified) party installing the VDR. Part 2: Operator and maintenance manual (NW6000-10) This manual covers (where applicable) all user related operational aspects and is intended to inform and assist the crew in the day-to-day operation of the VDR, and especially the user functions of the Bridge Control Unit. USB-card The hardcopy version of this manual is provided with an USB-card. This USB-card contains: - the digital version of this manual. the User Manual of the TRON40 VDR. the Installation Manual of the TRON 40VDR. and the Playback software. Page 10/ 191 Amendment records (versions) When an amendment is incorporated into this publication, the details are recorded below. Where the equipment has been modified, the modification number shown on the Amendment Instruction Sheet is also to be recorded. Installation, operation and maintenance Voyage data recorder NW6000-manual Version Amendment reference Date 2.0 - Acquirement of NetWave Systems by the Orolia 19th of April 2017 Group. Legal name of entity is now Orolia B.V. instead of NetWave Systems B.V. Trading name NetWave Systems will be maintained. - New Declaration of Conformity because of name change (no other content change). - Use of new logos. 2.1 - Because of new wire colors of cable TRON 26th of February 2018 40VDR: update of paragraph 10.4.2. - Reference to Installation manual of Jotron TRON 40 VDR made, manual attached to USB-stick and placed on extranet web page. 2.2 - Correction in paragraph 10.4 on connections 13th of July 2018 Junction box VDR to FFRM TRON 40VDR. - Minor update paragraph 10.2 about location of FFRM TRON 40VDR. 2.3 - Update to include new functionalities in v1.6.3. 24th of April 2020 2.4 2.5 2.6 2.7 2.8 2.9 2.10 2.11 - reviewed and updated changes from 2.3 - added BAM specification - added PSU v2 - added Player V2 - added analogue microphones - removed digital microphones - tidied up document - BAM msg error; ACL should be ALC - Distinction made between IEC 61162-1/2 modules - Declaration of Conformity removed; included separately when available. - Typographical errors corrected - Additional wiring information added - Mains EMC NW6000-050 filter added - Updated battery information and use of batteries - updated Capsule image on page 100 - added FAQ on VDR recording capacity - corrected product codes - corrected figure numbers - removed NW64224 (24Chn NMEA) - updated note on NW6030 wiring - removed Wheelmark images - corrected error in Audio Hub wiring diagram - added updates to configuration utility Updated by C. van ‘t Riet C. van ‘t Riet C. van ‘t Riet HdH 5th June 2020 8th June 2020 HdH/JA JA/HdH 10th July 2020 JA 9th August 30th September 2020 JA JA 7th October 2020 JA 10th October 2020 JA 14th October 2020 JA Since this manual used to be two separated documents (‘Installation manual’ and ‘Operator and maintenance manual’) the amendment records of these documents are shown below. Amendments made as from the 19th of April 2017 are shown in the amendment record ‘Installation, Page 11/ 191 operation and maintenance Voyage data recorder NW6000-manual’ above. The version indicated in above amendment record is the version of this complete document. General part (Related to ‘Installation manual’ and ‘Operator and maintenance manual’) Version Amendment reference Date Instal.man ual: 1.12 Operat. And maint. Manual: 1.8 - ‘Installation manual’ and ‘Operator and maintenance manual’ merged into one document (reorganization of chapters). ‘General’ part is related to both manuals. - ‘Service request’ chapter added in General part. - USB-card enclosed to hard copy manual with the digital version of the manual, User Manual of the TRON 40VDR and Playback Software. Updated by 14th of March 2017 C. van ‘t Riet Amendment reference Date Updated by Addition in section 14 about new Docking Module (83180 MkII): new wire scheme and new led indication. - Declaration of Conformity enclosed (section 2.3). - Clarifications for TRON 40VDR (Section 14): wire scheme for new Docking Module MKII/Junction Box, clarifications of grounding of Junction box, new led indication on Docking module, more details about mounting position, use of vulcanizing tape added, settings of IP-address removed. - Restart VDR added (section 24.7). - Addition in section 24.2 about displayed ZDA time. 24th of August 2016 C. van ‘t Riet 31st of October 2016 C. van ‘t Riet Amendment reference Date Updated by - Addition in section 8.6 about calculation recorded time. - Addition in section 14.2 about displayed ZDA time. - Clarification of Russian mark of conformity Annex III. - ‘Restart VDR’ section 14.8 added. - ‘Led indication’ TRON 40VDR MKII section 11.2 added. 24th of February 2016 C. van ‘t Riet 19th of October 2016 C. van ‘t Riet Installation manual Version 1.10 1.11 Operator and maintenance manual Version 1.6 1.7 Page 12/ 191 Safety precautions and warnings To ensure compliance with the IMO standards, installation of the VDR must be performed by a NetWave Systems approved installation technician. Only a NetWave Systems Certified Technician should access the interior components of the VDR. The following precautions and warnings are general safety measures that personnel should understand and apply during installation, operation and maintenance of all VDR system equipment. PERSONAL PROTECTION Personal protection must be used whenever the possibility of an uncontrolled hazard exists. For example, a suitable face visor, gloves and a body apron should be worn when handling cathode ray tubes, as a precaution against injury in the event of breakage. Some VDR components are heavy; ensure you carry out proper lifting procedures while changing or transporting components. LETHAL HIGH VOLTAGES ARE PRESENT IN THE VDR High voltages are present in the Voyage Data Recorder. Do not open any of the units when the Voyage Data Recorder is operational unless fully qualified to do so. Only NetWave Systems Certified Technicians should undertake work on the system. A current of 100 mA passing through the human body for one second can kill. This can occur at voltages as low as 35V AC or 50V DC. Some equipment in the system uses electrical power that can be lethal. Whenever practical, before carrying out installation, maintenance or repair, personnel involved must: (1) Isolate the equipment from the electrical supply. (2) Make tests to verify that the isolation is complete. (3) Ensure that power cannot be accidentally reconnected. If it is essential to work on the equipment with power connected, work must only be undertaken by qualified personnel who are fully aware of the danger involved and who have taken adequate safety precautions to avoid contact with dangerous voltages. Wear proper safety attire and use the proper equipment while handling the VDR during transport and installation. POWER SUPPLY Prior to connecting the power supply of the VDR to the ship power, ensure the (emergency) ship power breaker is switched off. Always shut down the system and turn off the power before removing or installing any equipment. Page 13/ 191 GROUNDING All cable shields must be grounded to avoid interference from AC wiring, fluorescent lights, or other high magnetic or RF fields. NMEA data cables should be grounded at the source. All other cables should be grounded at both ends. The equipment in the VDR enclosure is grounded to the rack. All other peripheral equipment should be grounded. CABLING The cable sizes and types recommended for use with the must be utilized to ensure its proper operation. Failing to do so will void the warranty. HEALTH HAZARD This equipment contains materials which produce toxic fumes when ignited. The inhalation of dust and fumes or any contact with lubricants when cleaning the equipment may be temporarily harmful to health, depending on individual allergic reactions. Components which are broken or overheated may release toxic fumes or dust and must be treated with caution. Do not inhale the fumes and ensure that the dust and debris do not enter open cuts or abrasions. It is prudent to regard all damaged components as being potentially toxic, requiring careful handling and appropriate disposal. ELECTROSTATIC DISCHARGE Digital devices are susceptible to damage from electrostatic discharge (ESD); certain precautions must be taken when handling circuit cards, integrated circuits (ICs), and other sensitive devices. The maintenance technician should conform to the following guidelines when handling ESD sensitive devices: 1. Always wear a static protection wristband prior to contact with any electrostatic sensitive device. 2. Ensure that the wristband cable clip is firmly attached to a grounding point. 3. Keep all sensitive components in their protective pouches until required. Page 14/ 191 Abbreviations API ARPA BAM BCU CCTV CD ROM CM COG DAQ EBL ECDIS EPFS EPIRB FSP GPS HSS IEC IMO INS IP LCD LED NMEA PC PMC PRF POE (PoE) PSU RIP ROM ROV SINAD SNTP SOG SOLAS SSL STW TFTP ULB UPS USB UTC VCR Application Program Interface Automatic Radar Plotting Aid Bridge Alert Management Bridge Control Unit Closed Circuit Television Compact Disk Read Only Memory Core Module Course Over Ground Data Acquisition Electronic Bearing Line Electronic Chart Display Information System Electronic Position Fixing System Emergency Position Indicating Radio Beacon Field Service Program Global Positioning System Hardened Storage Server International Electro technical Commission International Maritime Organization Integrated Navigation System Internet Protocol Liquid Crystal Display Light Emitting Diode National Marine Electronic Association Personal Computer Protective Memory Capsule Pulse Repetition Frequency Power over Ethernet Power Supply & Switch Unit Radar Interlay Processor Read Only Memory Remotely Operated Vehicle Signal to Noise and Distortion Simple Network Time Protocol Speed Over Ground Safety of Life at Sea Secure Sockets Layer Speed Through Water Trivial File Transfer Protocol Underwater Locator Beacon Uninterruptible Power Supply Universal Serial Bus Coordinated Universal Time Video Cassette Recorder Page 15/ 191 VDR VESA VHF VRM Voyage Data Recorder Video Electronics Standards Association Very High Frequency Variable Range Marker Page 16/ 191 Terms Alerts Announcement of abnormal situations and conditions requiring attention. Alerts are divided in four priorities: Emergency Alarms, Alarms, warnings and cautions. Alarm High priority of an alert. A condition requiring immediate attention and action, to maintain the safe navigation and operation of the ship. Bridge workstation Position at which a person is expected to be when performing one of the normal bridge duties at, for example, the following workstations: • centre line conning. • bridge wing(s). • main radar. • chart table. • helmsman. • communication. Caution Lowest priority of an alert. A condition which does not warrant a CAUTION or warning condition, but still requires attention and out of the ordinary consideration of the situation or of given information. Combined EPIRB/VDR capsule Single unit which meets all the requirements of a satellite EPIRB (as required by the carriage requirements of SOLAS IV) and all the requirements of a VDR (as required by the carriage requirements of SOLAS V). Configuration Data Describes the vessel's equipment, its installation on the vessel and its relation to the VDR. The storage and playback software uses this data to store the data record and to convert the data record into information that assists casualty investigation during playback. Data Any item of information received by the VDR for recording, including numerical values, text and audio or radar signals and including all configuration data, except where specifically stated or where the context dictates otherwise. Dedicated reserve power source A battery, with suitable automatic charging arrangements, dedicated solely to the VDR. This battery is contained within the Core Module. Only authorized batteries, available from Orolia Netwave, are to be used with the NW6000. Failure to do so, will invalidate certification for the NW6000. Page 17/ 191 Fixed recording medium Part of the Final Recording Medium which is protected against fire, shock, penetration and a prolonged period on the ocean floor. It is expected to be recovered from the deck of the vessel that has sunk. It has a means of indicating location. Float-free recording medium Part of the Final Recording Medium which should float-free after a sinking. It has a means of indicating location. Long-term recording medium Permanently installed part of the Final Recording Medium. It provides the longest record duration and a readily accessible interface for downloading the stored data. Module A physically separated part within a Unit, i.e. signal adaptor or other (part of) assembly. Playback equipment Any data medium with the playback software, the operational instructions and any special parts required for connecting a commercial-off-the-shelf laptop computer to the VDR. Playback software Copy of the software program to provide the capability to download the stored data and play back the information. The software should be compatible with an operating system available with commercial-off-the-shelf laptop computers and where non-standard or proprietary formats are used for storing the data in the VDR, the software should convert the stored data into open industry standard formats. Playback system System including the playback equipment that is capable of downloading and playing back the recorded data. Recorder, Voyage Data Recorder, VDR Complete system, including any items required to interface with the sources of input signals, their processing and encoding, the final recording medium, the playback equipment, the power supply and dedicated reserve power source. Resolution Smallest detectable increment between two values. Signal source, sensor Any sensor or device external to the VDR, to which the VDR is connected and from which it obtains signals and data to be recorded. Unit A physical part of the VDR contained in a separate housing, i.e. CM (Core Module) or BCU (Bridge Control Unit). Page 18/ 191 List of Specifications NEN-EN-IEC 61996-1: Maritime navigation and radio communication equipment and systems Ship borne voyage data recorder (VDR) -- Part 1: Performance requirements, methods of testing and required test results (IEC 61996-1:2013, IDT) IMO A.658(16): Use and fitting of retro-reflective materials on life-saving appliances IMO A.662(16): Performance standards for float-free release and activation arrangements for emergency radio equipment IMO A.694(17): General requirements for ship borne radio equipment forming part of the Global Maritime Distress and Safety System (GMDSS) and for electronic navigational aids IMO A.810(19): Performance standards for float-free satellite emergency position-indicating radio beacons (EPIRBs) operating on 406 MHz IMO A.830(19):1995, Code on CAUTIONs and indicators IMO A.861(20): Performance standards for ship borne voyage data recorders (VDRs) IMO MSC.81(70): Testing of life-saving appliances IMO MSC.163(78): Performance standards for ship borne simplified voyage data recorders(SVDR). IMO MSC.333(90): Adaption of revised performance standards for Ship borne Voyage Data Recorders (VDRs) Eurocae: ED56A – Minimum operational performance specification (MOPS) for cockpit voice recorder system VESA:1996, Video electronics standards association – Discrete monitor timings standard 1.0, Revision 0.7 (DMTS) SAE AS8045A: Engineering society for advancing mobility land, sea, air, and space – Minimum performance standard for underwater locating devices – Acoustic-self-powered IEC 60068-2-27:1987, Environmental testing – Part 2: Tests – Test Ea and guidance: Shock IEC 60936-1:1999, Maritime navigation and radio communication equipment and systems – Radar – Part 1: Ship borne radar – Performance requirements – Methods of testing and required test results IEC 60936-3: Maritime navigation and radio communication equipment and systems – Radar – Part 3: Ship borne radar with chart facilities – Methods of testing and required test results IEC 60945:2002, Maritime navigation and radio communication equipment and systems – General requirements – Methods of testing and required test results Page 19/ 191 IEC 61097-2: 2002, Global maritime distress and safety system (GMDSS) – Part 2: COSPAS SARSAT EPIRB – Satellite emergency position-indicating radio beacon operating on 406 MHz – Operational and performance requirements, methods of testing and required test results IEC 61097-7:1996, Global maritime distress and safety system (GMDSS) – Part 7: Ship borne VHF radiotelephone transmitter and receiver – Operational and performance requirements, methods of testing and required test results IEC 61162 (parts 1,2,450), Maritime navigation and radio communication equipment and systems – Digital interfaces IEC 61260: Electroacoustics – Octave-band and fractional-octave-band filters IEC 61672 (all parts), Electroacoustic – Sound level meters IEC 61993-2, Maritime navigation and radio communication equipment and systems – Automatic identification systems (AIS) – Part 2: Class A ship borne equipment of the universal automatic identification systems (AIS) – Operational and performance requirements, methods of test and required test results IEC 62288 Ed.2, MARITIME NAVIGATION AND RADIOCOMMUNICATION EQUIPMENT AND SYSTEMS – Presentation of navigation-related information on ship borne navigational displays – General requirements, methods of testing and required test results NEN-EN-IEC 61162-450, (en) Maritime navigation and radio communication equipment and systems - Digital interfaces - Part 450: Multiple talkers and multiple listeners Ethernet interconnection VESA: 1996 Video electronics standards association - Discrete monitor timings standard 1.0, Revision 0.7 (DMTS) IEC 62923:2018 Maritime navigation and radiocommunication equipment and systems – Bridge alert management – Part 1 and Part 2. Page 20/ 191 IMO guidelines on Voyage Data Recorder ownership and Recovery 1.Ownership of VDR information The ship owner will, in all circumstances and at all times, own the VDR and its information. However, in the event of an accident the following guidelines would apply. The owner of the ship should make available and maintain all decoding instructions necessary to recover the recorded information. 2.Recovery of VDR and relevant information Recovery of the VDR is conditional on the accessibility of the VDR or the information contained therein. 2.1. Recovery of the VDR information should be undertaken as soon as possible after an accident to best preserve the relevant evidence for use by both the investigator1 and the ship owner. As the investigator is very unlikely to be able to instigate this action soon enough after the accident, the owner must be responsible, through its on-board standing orders, for ensuring the timely preservation of this evidence. 2.2. In the case of abandonment of a vessel during an emergency, masters should, where time and other responsibilities permit, take the necessary steps to preserve the VDR information until it can be passed to the investigator. 2.3. Where the VDR is inaccessible and the information has not been retrieved prior to abandonment, a decision will need to be taken by the flag State in co-operation with any other substantially interested States on the viability and cost of recovering the VDR balanced against the potential use of the information. If it is decided to recover the VDR the investigator should be responsible for coordinating its recovery. The possibility of the capsule having sustained damage must be considered and specialist expertise will be required to ensure the best chance of recovering and preserving the evidence. In addition, the assistance and co-operation of the owners, insurers and the manufacturers of the VDR and those of the protective capsule may be required. 3.Custody of VDR information In all circumstances, during the course of an investigation, the investigator should have custody of the original VDR information in the same way that the investigator would have custody of other records or evidence under the Code for the Investigation of Marine Casualties and Incidents. 3.1. The term investigator refers to the Marine Casualty Investigator as per the terms of the Code for Investigation of Marine Casualties and Incidents. 3.2. Refer to paragraph 4.11 of the Code for the Investigation of Marine Casualties and Incidents, as adopted by resolution A.849(20). 3.4. In all circumstances the investigator is responsible to arrange downloading and read-out of the information and should keep the ship owner fully informed. In some cases, the assistance of specialist expertise may be required. Page 21/ 191 4.Access to the VDR information 4.1 A copy of the VDR information must be provided to the ship owner at an early stage in all circumstances. 4.2 Further access to the information will be governed by the applicable domestic legislation of the flag State, coastal State and other substantially interested States as appropriate and the guidelines given in the Code for the Investigation of Marine Casualties and Incidents. 4.3 Any disclosure of VDR information should be in accordance with section 10 of the Code for the Investigation of Marine Casualties and Incidents. Page 22/ 191 Service request In case there are difficulties and assistance is required please perform an Operational Performance Test as described in the chapter ‘Routine maintenance’ (Operator and maintenance manual). Please download the data set as described in ‘Download data set from the VDR system’ (Operator and maintenance manual) and send the following files to [email protected] so Netwave Systems can assist in fault finding. Page 23/ 191 Part 1: Installation manual 1. Specification sheet Unit Type Number Dimensions (mm) (H x D x W) Weight (kg) Specifications Core module NW6000 484 x 450 x 45 16.5 (incl. batteries) - PSU (110/230 Vac, 50/60 Hz) / 100 Watt - Includes mains filter - Built-in UPS - 10 port switch (8 x PoE, 2 x Non-PoE) - CPU unit with min. 30 days storage Bulkhead mount frame and cover NW6900 744 x 464 x 115 11 (excl. core module) - Internal wiring - External RJ45 connector bank Bridge Control Unit NW6010 150 x 100 x 134 1.8 Microphone (Internal & External) NW6030 70 x 83 x 83 0.4 Audio Hub NW6031 35 x 152 x 106 0.35 VHF Interface NW6060 180 x 87 x 47 0.5 Hardened FRM NW6860 411 x 311 27.5 Float Free FRM • • NW6880 533 x 240 x 218 5.4 Interface Module NW64900 182 x 232 x 436 2~3 (subject to 1 - 7 module interfaces) Video Interface NW6044 38 x 240 x 184 1 - Powered from Core module thru PoE 4” touch color screen Panel mounted with frame (IP20) Powered from Audio Hub Analogue LED identification light Powered using PoE Bulkhead mounted Powered using PoE 2 line-in Interface for microphones Bulkhead mounted (IP20) Powered thru PoE from core module Deck mounted protective capsule for 48 days (IP68) 90 day under water locator beacon Powered thru PoE from core module Includes 3m maritime CAT-6 cable Bulkhead mounted in protective cover for 48 days storage (IP67) Powered thru PoE from core module DIN rail mounted interface NMEA (up to 38k4) (multiple 8 port) Digital sensors (multiple 8 port) Analogue sensors (multiple 4 port) Additional 24 Vdc power Input/Output For non-networked video 4 channels video Bulkhead/DIN rail mounting 24 VDC / 12 watt Orolia Netwave recommends maritime CAT-6 ethernet cable for connecting all units to the core module switch. Complete system runs from 110 (60Hz) to 230 Vac (50 Hz) through the core module. Page 24/ 191 2. Introduction 2.1 Overview The Voyage Data Recorder (as required by Chapter V of the International Convention for Safety of Life at Sea (SOLAS taking into account the IMO resolutions), records the outputs from sensors (connected external equipment of which the outputs need to be recorded) and ultimately passes the data to three physically separated Final Recoding Media (fixed, float-free and long-term) so that the data can be recovered and played back. The purpose of the VDR system is to record (on multiple storage media) the data originating from various types of sensors. This may be digital, analogue, serial, audio or video information directly originating from ship’s equipment with an Ethernet output compliant to the IEC61162-450 LWE standard, (and for radar IEC 62388:2007) or originating from similar sensor equipment with the use of an intermediate interface as part of the VDR system. The VDR’s Core Module receives and processes any item of information received from the sensors (directly or via an interface) and distributes that data, which is monitored for integrity and compressed, to all Final Recording Media consisting of the Fixed Recording Medium, the FloatFree Recording Medium, and the Long Term Recording Medium. Where Units are described in this manual, data transfer between the Core Module (CM) and these unit is IEC61162-4501 (LWE: Lightweight ethernet) compliant where practical. The same standard serves to interface to any other compliant equipment beyond the domain of the VDR itself. Where external (to the VDR) sensors do not provide data in the IEC 61162-450 or IEC62238 (radar Ethernet) format, interfaces are required and available as an integral part of the VDR. A very basic example may be a GPS with a serial IEC61162 (NMEA) output which requires a conversion to the IEC61162-450 (LWE standard) before it is sent onto the VDR network. 1 IEC 61162-450 Maritime navigation and radio communication equipment and systems -Digital interfaces - Part 450: Multiple talkers and multiple listeners - Ethernet interconnection Page 25/ 191 2.2 Architecture This particular VDR is characterized by a distributed data acquisition and conversion model which allows data to be acquired close to the sensor, converted into the LWE standard within the interface (i.e. NW 6410 WaveNet Buscoupler in conjunction with NW 64208 NMEA adaptor) unit or VDR sensor (i.e. microphone) and stored onto multiple recording media. Since most data is converted and formatted within the interface or sensor itself, CPU processing or overhead within the Core module is relatively low which enhances the system’s stability. This architecture allows for flexible configuration and maximum scalability. Figure 5.1.1 System overview Page 26/ 191 2.3 Interfacing Provided sensors are connected and configured to be recorded. Th following (minimum) data is stored (line numbers refer to IEC61996-1:2013). 4.6.1 Date and time 4.6.2 Ship’s position 4.6.3 Speed 4.6.4 Heading 4.6.5 Bridge audio 4.6.6 Communications audio 4.6.7 Radar data 4.6.8 ECDIS 4.6.9 Echo sounder 4.6.10 Main CAUTIONs 4.6.11 Rudder order and response 4.6.12 Engine and thruster order and response 4.6.13 Hull openings (doors) status 4.6.14 Watertight and fire door status 4.6.15 Accelerations and hull stresses 4.6.16 Wind speed and direction 4.6.17 AIS 4.6.18 Rolling motion 4.6.19 Configuration data 2.4 Power failure All available data is recorded until ship’s power to the VDR fails, and from then only selected data (bridge audio) is recorded for a further two hours after which recording stops automatically. 2.5 Network protocols and IP address ranges incl. LWE Network protocol requirements. The VDR implements IPv4 and supports for the following specific network protocols: • • • • ARP IP UDP ICMP – Address Resolution Protocol – Internet Protocol – User datagram Protocol – Internet Control Message Protocol Page 27/ 191 2.5.1 IP address for assignment The VDR network is configurable with an address range of 172.16.0.1 to 172.31.255.254 with a 16-bit network address mask. The assigned IP address is fixed during normal operation of the VDR, including powering the equipment down and up. The VDR does not rely on (external) DHCP functionality and to overcome IP-address conflicts, caution must be observed not to connect a DHCP server (with the same IP range enabled) into the (VDR) network. This VDR uses the following (default) IP addresses. Core module Microphones Data acquisition devices Video interfaces* Gateways Reserved for future use 172.16.8.2 172.16.10.1 172.16.15.1 172.16.20.1 172.16.25.1 172.16.30.1 to 172.16.10.254 to 172.16.15.254 to 172.16.20.254 to 172.16.25.254 to 172.16.30.254 (subnet mask: 255.255.0.0) *networks outside this range are also permissible and are detected during the initial probe. It is not required to set the IP address of an LWE source to be within the VDR network . 2.5.2 Specifications for video using Light Weight Ethernet (IEC-61162-450) This VDR is prepared for recording of video, using the IEC-61162-450 standard. Connection of video devices, using this protocol, can be achieved using the Ethernet ports on the switch. Available IP and port range: Maximum datagram input rate, per second and with a maximum size of 1472 bytes each: - For processing by the VDR: 4096 datagrams Received but not intended for the VDR: 8192 datagrams Received but not intended for the VDR (50% performance rate): 4096 datagrams Logging All errors can be viewed in the appropriate logs and are available via the BCU (error log) and via download of the Long-Term Storage medium (coremod log, error log, lwe-sys log). Page 28/ 191 All logs are also stored on the Fixed and Float Free Recording mediums, however it needs to be considered that a download of minimal 14 hours needs to be made (without interruption), to be sure to have these files available. Files are synchronized with the external storage media upon change, therewith it is ensured to have the correct data stored at the (F)FRM at all times. Messaging Netwave supports the MSM and SBM message types. 2.6 Multicast address range The range 239.192.0.1 to 239.192.0.64 is reserved for current and future use in the application layer protocols however the VDR does not use multicast addresses in the range 239.192.0.1 to 239.192.0.64. 2.6.1 UDP multicast protocol Senders and receivers use the UDP protocol as defined by ISOC RFC 768. 2.6.2 Use of multicast addresses and port numbers Port numbers are allocated from the Dynamic Port range that IANA has reserved for dynamic and/or private port numbers (range 49152 to 65535, inclusive). Any port-numbers used may be derived from the VDR configuration utility. 2.7 Cabling requirements The VDR hardware platform is completely reliant on Ethernet and it is therefore of the utmost importance that the installation cabling is within the technical specifications. 2.8 Minimum requirements Minimum requirements for the Ethernet cable. CAT6/7 4 pair S/FTP cable with individual pair foils and an overall braid, preferably fully compliant with the category 7 standards. Its bandwidth and performances must extend to 1000MHz. Cable must meet the electrical and mechanical requirements of the shipping industry. 2.9 Termination When terminated i.e. to LANmark-7 GG45 connectors it meets the Class F requirements (ISO/IEC 11801:2002). It enables to reach the full bandwidth on the link and secures the future proofing of the installation. When used with LANmark-6 Cat. 6 connectivity, optimal headroom to 250MHz Class E performance must be ensured. Page 29/ 191 2.10 Cable recommendation To provide optimal shielding maritime CAT.7 S/FTP 23 AWG LSFROH SHF1 is preferred which is specifically suited for installation on board ships and sea movable constructions, has a high shielding performance and can withstand harsh environments. Cable length max. 100m* unless otherwise specified in cable diagram. Cable screen must be grounded unless otherwise specified on connection diagram. *Length is measured from cable entrance/socket to cable entrance/socket. All equipment to be grounded with 6mm2 wire unless otherwise specified. Core Identification: For compatibility with above cable types following applies: BU - blue NC - neutral color: white or black or transparent If applicable, only for FMKHC 2x2x0.75 use conversion table: 1BU 1NC 2BU 2NC - BK BN BU GY Page 30/ 191 3. Installation guideline The planning and installation shall be carried out in the following steps: - - Determine which shipboard equipment (sensors) need to be connected, considering the relevant IMO resolutions. Determine which ports from the various units (adaptors) are required to acquire the data from these sensors. Determine where the units are to be positioned to minimize the cable length between them. Carry out the physical installation, interconnect the units by means of an Ethernet cable. Maximum length of Ethernet cable is 100 m. Maximum length of cable between digital microphones < 15 m up to a total of max. 100 m. Maximum length of cable between Audio Hub and an analogue microphone is 150m. Check for external power requirements (i.e. 24V for video module). VDR is provided with ample grounding points. Please ensure that these grounding points are being used according standard installation practices. Power the VDR and name the recording channels which are to be recorded. Enter the compulsory vessel data. Name the recording channels. Adjust the video settings. Check the recorded data against the settings by means of the replay software. Complete the file downloads as per the Annual Performance documentation and the commissioning report and send this to the manufacturer to obtain valid certificates and warranty. This information provided should at least contain: o o o o o o o o Overview drawings of the Bridge/wheelhouse Wiring connection drawing from sensors with identifiers Configuration files Data samples as per documentation Photographs of installed units and cabling/connections Vidchan files (Video configuration when video module is applied) NW6000-90 VDR Commissioning PT and TA Certificates TRON40 programming report Page 31/ 191 4. System components The VDR consists of the following main Units: NW6000 VDR Core Module (19” enclosure) NW6000-100* NW6000-160** NW6000-200* NW6000-300* NW6000-0155* NW6000-050 CM 100W Power Module CM 160W Power Module CM Network Module CM CPU Module 4x 6V 12Ah SLA battery Mains EMC Filter NW6000-920** CM bulkhead enclosure NW6010 Bridge Control Unit NW6030 NW6031 NW6060 Microphone Interior and Exterior rated IP67 Audio hub – 6 audio ports VHF Audio Interface NW6044** Video Interface 4 channel NW6880 NW6860-1000 NW6890** FRM Float Free Capsule Jotron TRON 40 FRM (Final Recording Medium) fixed SS Capsule FRM PoE Splitter Box f. HVR04 NW6410 WaveNet Buscoupler NW64208*** NW64216*** Serial/NMEA 8 CH adaptor Serial/NMEA 16 CH adaptor NW64308*** NW64316*** NW64324*** Digital 8 CH adaptor Digital 16 CH adaptor Digital 24 CH adaptor NW64404*** NW64408*** NW64412*** Analogue 4 CH adaptor Analogue 8 CH adaptor Analogue 12 CH adaptor NW64900 DIN enclosure for DAQ adaptors * ** *** These modules/parts are integrated (exchangeable) within the Core Module These modules/parts are optional The quantity and characteristics of these adaptors are dependent on the final configuration of the VDR specific to each vessel. Page 32/ 191 5. NW6000 VDR Core Module (19” enclosure) 5.1 General Fitted on or near the bridge, this unit is designed for 19” rack- or bulkhead mounting in a protected environment. The actual siting of the equipment is generally shown on the approved compartment layout for the ship. Cable entry facilities have been provided to accommodate the ship’s cabling that is connected to this unit. Ensure adequate space is provided for ventilation, cable access and maintenance access. The Core Module integrates 3 functions from 3 independent modules being (from left to right in figure above) power supply (UPS), data-switch, and CPU (central processing unit). These modules are interconnected via a backplane within the enclosure. The batteries required for the Uninterruptable Power Supply (the dedicated reserve power as per IEC61996-1:2013) are included within this enclosure. The batteries are accessible by removing the top cover of the unit. The batteries need to be replaced every two years. 5.2 Location and mounting Determine the location of the CM, allowing space for wiring to enter the cabinet and batteries to be replaced, as well as connectors to be accessible. The Core Module may be placed on the bridge, within the bridge console or external thereto, or in any technical room in the vicinity of the ship’s bridge provided adequate protection against environmental conditions is provided as follows: Temperature: Humidity: -15 to +55 C. (storage +70 C.) max. 60% relative humidity (at 40 C.) If the bulkhead-mounting enclosure is used, mount the bracket with your choice of bolts supplied with the unit. Make sure the bracket is mounted with the slotted holes in the correct vertical direction. Make sure it is horizontal. Keep 50 mm of free space above the bracket to provide sufficient ventilation for this unit. Page 33/ 191 Slide the CM into the cabinet or bulkhead enclosure by making use of the hinges and screw/tighten the 2 bolts at the back to secure the unit. Connect the Ground stud to a suitable safety ground. 5.3 Power Supply The CM is powered from 110-230Vac (+/- 10%) 50 Hz to 60Hz with a maximum frequency deviation of 5% (IEC60945). The power consumption is rated at maximum of 100W for the entire VDR system, thus including all PoE (power over Ethernet) connections (up to 15.4W each). Total power from PoE is limited to 65W. This power consumption does not include any devices external to the VDR where these must be powered individually from the ship’s power source. Mains power cables: type: 3-core mains, 3x1,5 mm2, braided, flame retardant, halogen free. The power-connector and cable are provided within the standard scope of supply and indication for the position for the L (Brown), N (Blue) and GND (Yellow/Green) connections are also indicated within the plug-connector. The leads must be connected to the supply as follows. Brown Blue Yellow/Green L N Ground The 3 leads (L, N, GND) must have a minimal diameter of 2,0 mm2 or AWG14. To meet EMC compliance for IEC 60945 the supply into the NW6000 must use a series connected mains filter. The NW6000-050 Mains Filter adapter is provided for this purpose with all NW6000 core modules. On the Power Supply Module, 2 LEDs are provided indicating the presence of mains (110/230 Vac nominal range) as well as the readiness of the internal UPS (Uninterruptable Power Supply) which includes the charge state of the batteries within the Core Module. Page 34/ 191 When the LED’s are lit, following status is indicated: Green LED (steady) main power supply is provided Green LED (flashing) main power not available, system on battery power Yellow LED battery power < 22 Vdc The PSU also contains the ability to completely power down the system and isolate the batteries, required on some installations where the vessel is laid up for long periods. This can be achieved without having to dismantle the core module if using the optional NW6000-160 PSU (PSU v2). To isolate the batteries… 1) Remove the bulkhead cover. If this is not being used, you need to be able to access the front of the core module where the PSU module is exposed. 2) Switch off the mains at the mains inlet socket on the PSU. 3) For PSU v1 option slide out the power module. For PSU v2 option, using a pen or small screwdriver, push in the battery isolation switch to completely power down the system. The system can be powered up again using the mains ON/OFF switch on the PSUv2 or reinserting the PSU v1 module. 5.4 Ethernet The Core module has 10x Ethernet ports out of which 8 provide PoE. A patch cable between the CM CPU module and the CM data switch must be present at all times. The LEDs on the left side of the data switch connectors indicate whether or not PoE(Power over Ethernet ) is provided to the device connected to each individual port whereas the individual Ethernet ports each have a green and yellow LED. Green LED Yellow LED OFF ON OFF ON Ethernet link not established. Either the RJ-45 cable is unplugged or defective; the nodes on the LAN are switched off. Ethernet link properly established. No traffic detected on the Ethernet. (pulsing): LED glows each time an Ethernet packet (originating from/directed to any node on the Ethernet) is detected. Please ensure to mount all ferrites supplied with individual product that use the PoE port. Please refer to the connection diagram on the following page. Page 35/ 191 Page 36/ 191 Weight Color IP rating IP20 grey 16,5 kg MAIN POWER 230V AC 3A 3 x 2,5 mm2 ALARM (RELAY, NC) to Bridge Alarm Management System (SR.5) FIXED & LOCKED INTERNAL INTERCONNECT - do not remove - CMF 1.11-1.12 NOTE: Ports CMF 1.1-1.8 are (auto sensing) PoE 802.3af compliant and may also be used without PoE requirement CMF 1.11 INTERNAL INTERCONNECT to CMF 1.9 CMF 1.12 DATA (IEC61996-1:2013) or to bridge network (fail-over) CMF 1.9 INTERNAL INTERCONNECT to CMF 1.11 (SR.1) CMF 1.10 optional to bridge network / DATA port (IEC61196-1:2013 (SR.3) CMF 1.1 - to Fixed Capsule Final Recording Medium (drawing N6-1.3) (SR.1) CMF 1.2 - to Free Floating Final Recording Medium (drawing N6-1.5) (SR.1) CMF 1.3 - to Bridge Control Unit / Bridge Display Unit (drawingN6-1.4) (SR.1) CMF 1.4 - to DAQ Data Acquisition Modular System (drawing N6-1.8) (SR.1) CMF 1.5 - (optional) sensor data i.e. DAQ / IEC61162-450 (LWE) / IEC62338 (PoE 802.3af) CMF 1.6 - (optional) sensor data i.e. DAQ / IEC61162-450 (LWE) / IEC62338 (PoE 802.3af) CMF 1.7 - (optional) sensor data i.e. DAQ / IEC61162-450 (LWE) / IEC62338 (PoE 802.3af) CMF 1.8 - (optional) sensor data i.e. DAQ / IEC61162-450 (LWE) / IEC62338 (PoE 802.3af) CMF 1.1-1.10 5.5 Contacts The CM Power modules also serves to provide an external CAUTION contact which must be connected to a central CAUTION system, when present on the ship. The following contacts are provided: During normal operational mode of the VDR (without any CAUTIONs internal to the VDR) the CAUTION relay is held energized (by the VDRs Central Processing Unit) and the CAUTION contacts are closed. If the VDR presents an error or (power) fails, the contacts will open to their default (NO). This allows remote CAUTION (Bridge Alarm) management systems to register the VDR (internal!) CAUTIONs. The VDR CAUTION does not reflect any CAUTIONs external to the VDR itself (i.e. of sensors or equipment connected thereto). 5.6 Data communications The CM fully relies on Ethernet connections to the other (sensor) devices which must be IEC61162-450 or IEC62388 compliant and provide data within the VDRs specified (commissioned) IP-range (refer to Network configuration). The CM has 8 x 10/100 TX PoE port and two 10/100/1000TX uplink ports, delivering 802.3af compliant PoE @48V. The total power budget is 65W with max. 15.4W per port. The CM has two gigabit Ethernet ports for larger uplink bandwidth one of which is to be connected to the CM’s CPU module. Page 37/ 191 5.7 Indicators Each network-port provides Link and Activity LEDs. Green LED Link speed (Green LED); The LED is on when there is a link connection, otherwise, the LED is off. Yellow LED LED is flashing when there is activity on the link. Otherwise, the LED is off. 5.8 Errors If errors occur within the Core Module these will be indicated on the display of the Bridge Control Unit. 5.9 Operating instructions After commissioning of the VDR system, this unit does not require (crew) operating instructions. Page 38/ 191 6. NW6010 Bridge Control Unit 6.1 General The Bridge Control Unit (BCU) serves both as an interface for serial/NMEA data as well to display the operational status and provide user functionality like, but not limited to, operational performance tests. 6.2 Location and mounting The BCU may be mounted in a protected environment at any convenient location considering the compass safe distance as indicated on the unit. Prepare the location by cutting out a rectangle of 130x80 mm as well as 4 smaller rectangles as per the drawing below. Tip: Use the metal frame supplied to mark the cut-outs to be made. Secure the metal frame to the console or panel with 4 self-tapping screws (supplied) and insert the BCU unit until the back of the BCU aluminum front panel and the metal mounting frame are flush. The snappers supplied will secure the unit into the panel to which the BCU is fitted. PANEL CUT OUT 130 x 80 mm 4 x M3 self-tapping screws or equiv. Page 39/ 191 6.3 Power This unit has 1x 100 TX PoE port, receiving 802.3af compliant PoE @48V. The total power budget is 3.6 Watts. This device fully relies on the Ethernet PoE supplied from the Core Module without which it will not operate. 6.4 Connections The BCU allows for up to 3x NMEA (IEC61162-2) serial ports to be connected and recorded to the VDRs Core Module. These will typically be used i.e. for GPS, AIS, etc. Data rates supplied are up to 38k4 for all ports. The BCU provides an Auxiliary CAUTION relay with a contact rating of 28V DC, 200mA max. During correct functioning of the VDR, the relay contacts are in the NO position. When a CAUTION condition occurs or the VDR loses its power, the NC position is valid. (NC=normally closed, CO=COMMON contact, NO=normally open). NMEA connections to the BCU are to be connected as follows. Connector Data rate N1 N2 N3 NMEA channel 1 A NMEA channel 1 B NMEA channel 1 Common 4k8 ~ 38k4 N4 N5 N6 NMEA channel 2 A NMEA channel 2 B NMEA channel 2 Common N7 N8 N9 NMEA channel 3 A NMEA channel 3 B NMEA channel 3 Common Following sentences are supported. Date and time Ship’s position and datum used Speed (water and/or ground) Heading (true) Heading (magnetic) Depth (echo sounder) CAUTIONs Rudder order/response manual Rudder order/response automatic Engine order/response Hull openings, watertight doors Accelerations and hull stress Wind speed and direction AIS VDR alert output ZDA GNS, DTM, GLL, GGA, RMC, NSR VBW, VLW, VTG THS, HDT HDG DPT ALR, ALA, FIR, WAT, ACM RSA, ROR HTC, HTD ETL, PRC, TRC, TRD, RPM, XDR, ROR, RSA DOR, GEN, XDR HSS, XDR MWV, MWD VDM, VDO, ALR ALC, HBT, ALC Page 40/ 191 BCU LED1 ALARM Type & Serial number NC-CO-NO N1 ~~~~~~~~ N9 Serial / NMEA ETHERNET (PoE) to CM Fig. 6.4 Bridge Control Unit interfacing connections (back view) 6.5 Data communications The Bridge Control Unit fully relies on Ethernet connections to Core Module and has to be configured within the VDRs specified (commissioned) IP-range (refer to Network configuration). Page 41/ 191 6.6 Indicators The BCU has 1 LED to indicate that the power supplied to it is present, in other words, at least a PoE link is established to the core module. In the event the LED is illuminated (steady, green), the video display on the unit must work. Additionally, each network-port provides Link and Activity LEDs on the rear of the unit with the following status indications .... Link speed (Green LED) The LED is on when there is a link connection. Otherwise, the LED is off. Activity (Yellow LED) The LED is flashing when there is activity on the link. Otherwise, the LED is off. 6.7 Errors Error indication: in the event the LED on the back side of the unit is ON, the display is illuminated and showing text (buttons), but no valid (UTC) time is presented on the display, the data-link to the core module is not functional at that time. All other errors are presented on the display. The BCU provides an Auxiliary CAUTION relay of which the (dry) contact rating is 28V DC, 200mA max. During a correct functioning of the VDR, the relay contacts are in the NO position. When a CAUTION condition occurs or the VDR loses its power, the NC position is valid. (NC=normally closed, CO=COMMON contact, NO=normally open). 6.8 Configuration IEC61162-2 serial ports (3 off) speeds must be set during commissioning time. Please refer to chapter ‘Connecting to the VDR for configuration of the system’. 6.9 Operating instructions The BCU is equipped with a touch screen display with day and night display mode. Page 42/ 191 7. NW6060 VHF / Audio Interface 7.1 General The NW6060 VHF/ Audio-interface allows interfacing functions for up to two VHF audio channels. This primary function serves to gather audio (line-in) information from the VHF communications equipment. characteristics. Location and mounting This interface may be placed in a protected environment at a location most practical to realize the connections. 7.2 Power supply This is powered using PoE. 7.3 Connections 1. The NW6060 VHF / Audio Interface is connected to any of the PoE ports on the Core Module Core Module (CMF 1-8) by means of an Ethernet cable. 2. The NW6060 VHF / Audio Interface is connected to the VHF equipment by means of the VHF1 & 2 (line level) ports as follows: V1 VHF1 signal + V2 VHF1 gnd V3 VHF1 signal – V4 VHF2 signal + V5 VHF2 gnd V6 VHF2 signal – Page 43/ 191 7.4 Data communications The unit fully relies on Ethernet connections to the Core module devices which must be IEC61162450 compliant and the unit provides (audio) data within the VDRs specified (commissioned) IPrange (refer to Network configuration). 7.5 Indicators None. 7.6 Errors If errors occur within the interface these will be indicated on the display of the Bridge Control Unit. 7.7 Configuration The individual VHF channel IP-addresses must be set during commissioning time. Please refer to VDR Configuration functions. 7.8 Operating instructions After commissioning of the VDR system, this unit does not require (crew) operating instructions. 7.9 Testing VHF Radios procedure To test the VHF audio, a short broadcast must be completed. NOTE: When broadcasting on VHF, ensure that no transmissions are made that could be confused with anything other than a test transmission. The voice test should be performed from another VHF radio (VHF2) so that you are now testing the Rx signal recording of VHF1 and say the words “Test VHF1 Receive” followed by a voice count from 1 to 5 (or 10) and reverse the count back to 1, finishing the transmission with words “Test Out”. To test the VHF recording is as follows: 1. Check the VHF wire connection to the VDR to ensure it is correct. 2. Transmit the voice test as described above. A normal voice procedure is to say the words: “Test VHF1 Transmit”, Count from 1 to 10 and reverse the count back to 1, Finish the transmission with words “Test Out”. NOTE: When transmitting, ensure that the VHF is switched to a channel that cannot be confused with any local distress or working frequencies 3. Note test time. Page 44/ 191 4. Use a second VHF radio (not connected to VDR) to broadcast a second test on the same frequency to ensure that the audio received is recorded correctly. Again, note the time of the broadcast and receipt test. 5. Download a small data set using the VDR Player software. 6. Playback the data to ensure both transmit and receive data is recorded properly. It is advised that you combine live microphone sound/recording test with the VHF sound/recording test while you have all NMEA devices turned on as well as radar screen active (at least in STBY. Mode) so that your recording contains everything possible connected to the VDR. Page 45/ 191 8. NW6030 Analogue Microphones 8.1 General The analogue microphones are constructed from sea-water resistant materials with the main housing being durable anodized aluminum. There is one type which may be used in both a protected (internal) and unprotected (external) environment. As the name suggests the interface to the microphone is analogue and uses a differential analogue driver to send the audio signal to the Audio Hub (NW6031) for further processing before sending this to the VDR over a PoE connection. These microphones connect, via the NW6031 Audio Hub interface which provides power, directly into the VDR Ethernet network. Characteristics. • • • • • • • • IEC 61996 compliant in conjunction with the NW6031 Audio Hub IEC60945 compliant Single model for interior and exterior (IP66) Can be flush or surface mounted Powered from the NW6031 Audio Hub Differential analogue output On-board microphone and sound test capability Green LED indicator for location and audio test indication 8.2 Location and mounting One or more microphones positioned on the bridge (wings) must be placed such that conversation at or near the conning stations, radar displays, chart tables, etc. may be adequately recorded. As far as is practicable, the positioning of microphones shall also capture the input and output of intercom, public address systems and the audible CAUTIONs on the bridge (bridge mounted equipment). For recording purposes, the bridge is divided into recording areas. The number of recording areas determines the number of microphones required. The number of microphones plus the number of VHF inputs equals the number of audio channels recorded. Microphones are omni-directional with a radius of 4m. Microphones should be located above bridge workstations indoor and outdoor. The placement of the bridge microphones requires careful planning as recordings must meet IEC 61996 and the MSC.163(78) requirements. Page 46/ 191 The total maximum cable distance between microphone and Audio Hub (NW6031) is 150m. The microphone housings are provided with three mounting holes. The screw cover supplied with the NW6030 can be used to cover these. Please ensure that the additional rubber seal is added before placing the screw cover; this enables easier removal of the screw cover cap if necessary, during the service life of the microphone. The rubber seals provided with the microphones are used to minimize vibrations being carried into the microphones as well as providing a barrier between metals of different materials thus minimizing the effects of corrosion. Insert the top housing including microphone print, connect the cables and fix with screws on the side. Figure 8.2.1 Outline of NW6030 for surface mounting Page 47/ 191 The following shows the mounting dimensions for the NW6030: 8.3 Power The microphones fully rely on the Audio Hub (NW6031) interfaces. This provides a separately controlled power supply voltage to each microphone. • • • Power for the microphone is provided via the NW6031 Audio Hub. This is a controlled power source used to achieve audio testing. External power supplies cannot be used with the microphones as the 12h periodic operational audio test will no longer operate. 8.4 Connections To minimize cabling efforts and cost, the microphones must be individually connected to the NW6031 Audio Hub. • • Only one microphone can be connected to an NW6031 Audio Hub channel. Paralleling of microphones into Audio Hub channels is prohibited and will result in the microphone test failing and potentially may damage the electronics in the microphone itself. Please see NW6031 Audio Hub for wiring details. 8.5 Audio Signals Audio signals are amplified by an internal amplifier within a microphone. These are then connected to the NW6031 audio input enabling the analogue signals to be sampled and processed on the Audio Hub before being sent back to the VDR for recording purposes. The output data format is IEC61162-450 (LWE) compliant so that no further data manipulation or compression is required within the Core Module. Page 48/ 191 8.6 Indicator Each microphone has a green led built within the enclosure which is only visible and may be controlled during commissioning and (operational performance) testing. The microphone contains an internal buzzer which is used during audio testing. This sounds when the green led is ON and is normally OFF. 8.7 Errors If errors occur these will be indicated on the display of the Bridge Control Unit. 8.8 Configuration The microphone adopts the input that the microphone is connected to on the NW6031 Audio Hub. For example, Input 1 will have the description “AudioHub PN4001 Channel 1” when the system is probed initially. 8.9 Operating instructions After commissioning of the VDR system, the microphone does not require (crew) operating instructions. Microphone tests may be performed manually from the Bridge Control Unit. Page 49/ 191 9. NW6031 Audio Hub 9.1 General The Audio Hub is contained in an extruded aluminum housing. The NW6031 Audio Hub is powered from and communicates with the NW6000 using PoE. The audio hub provides 6 audio input channels which are simultaneously sampled. Digital processing used within the hub to convert sampled analogue data for communications back to the NW6000 over the PoE communications port. Characteristics. • • • • IEC 61996 compliant inputs for use with NW6030 Analogue Microphones IEC60945 compliant Powered from the NW6000 over PoE Each channel independently programmable for either NW6031 or VHF inputs. 9.2 Location and mounting One or more NW6031Audio Hubs may be used with the NW6000. The NW6030 requires a PoE connection with a maximum cable distance from the NW6000 of 100m The total maximum cable distance between microphone and Audio Hub (NW6031) is 150m. The audio hub uses pluggable terminal blocks for connecting to audio sources to be recorded. The NW6030 Analogue Microphone can be located 150m away from the audio hub. The NW6030 is required to be located in a protected environment using the mounting points are indicated in the outline drawing. 9.3 Power The power budget for the NW6031 with 6x NW6030 analogue microphones is 4W. No external power supply is required for use with the NW6030 or NW6031 as the NW6000 provides power to both via the NW6031 Audio Hub. Page 50/ 191 9.4 Connections The NW6031 audio hub inputs support the NW6031 Analogue Microphone and is wired as follows: The inputs are individually configurable to receive audio data from a VHF transceiver VDR interface and are wired as follows: Note: Connections to microphones also require using the provided ferrite clamps on both ends of cable. Cable needs to be looped as indicated in the drawing. 9.5 Indicator The NW6031 has no external indicators apart from the PoE indicators on the RJ45 socket. Link speed (Green LED) The LED is on when there is a link connection. Otherwise, the LED is off. Activity (Yellow LED) The LED is flashing when there is activity on the link. Otherwise, the LED is off. Page 51/ 191 9.6 Errors If errors occur these will be indicated on the display of the Bridge Control Unit. 9.7 Configuration NW6031 Audio Hub IP-addresses must be set during commissioning time. Please refer to VDR Configuration functions. All inputs default to NW6031 Analogue Microphone input by default after probing for the first time. These can be changed via the configurator for VHF inputs if required. 9.8 Operating instructions After commissioning of the VDR system, the NW6031 Audio Hub does not require (crew) operating instructions. Operational input testing (Microphone or VHF functions) tests may be performed manually from the Bridge Control Unit. Page 52/ 191 10. NW6044 Video Interface (option) 10.1 General Where radars or ECDIS systems do not provide an Ethernet port (compliant to IEC61162-450 or the IEC62388 radar video standard) and thus capable of broadcasting their information onto the VDR network, this optional video interface module may be deployed to capture RGB, RGBHV, Monochrome, and composite video information from radars, video cameras, ECDIS, and other video sources. This interface has 4 input ports for capturing images from a dedicated buffered output port of the video source. The module digitizes the video signal and then outputs the video data through an Ethernet port. Video modules can be configured for up to 4 inputs, enabling the VDR to capture and record images from the primary radar plus up to 3 additional video sources. During installation of the interface, the video system must be configured to accept each source’s video resolution, interlacing, refresh rate, etc. With each video interface a USB memory stick is provided with the Video Configuration Suite (VCS2) application which must be used to configure the video interface before it is connected to the CM. Information about the settings is gathered from the <VidChanX.ini> file (based on its VIDEOFORMAT entry information.) which is stored within the CM (core module) If more than 1 source is specified by the MAXSOURCES entry, then Control Input/Output connector signals are used to indicate the currently active source. The video signal configuration is read, and a new image is captured. If the system is configured for 2 or more video channels, then the next channel in the sequence is selected. If the video module fails to capture an image because there is no video signal (i.e., radar is OFF), an entry is made in the error log within the CM. However, this failure will not generate a video (error) caution on the BCU. A video (error) caution is only triggered when a failure is detected in the video capture hardware (i.e. bad or unpowered video module or Ethernet cable path failure. Page 53/ 191 10.2 Location and mounting When only one video channel is connected to the video module, the module is often mounted in the bottom cabinet of the source radar. When more than a single display needs to be recorded a practical location must be found considering minimal cable length between the (i.e. radar / ECDIS) displays and the interface. The Video Module is designed to be mounted on two rows of 35mm “Top Hat” style DIN Rail, two strips of DIN Rail must be installed. The module is held in place with clips on the back. NOTE: The DIN Rail is NOT supplied with the Video Module. Figure 10.2.1 - Video Module DIN Rail Clips Alternative mounting method would be to remove the 4 DIN Rail clips from the back of the Video Module and use 2 strips of high-quality heavy-duty Velcro (not supplied) to attach the Video Module to a clean and dry prepared surface within the radar cabinet. The Video Module must be grounded firmly to the ship using the ground stud on the rear of the module. This grounding must be done regardless of which mounting method is chosen by the installer. Page 54/ 191 10.3 Power supply The NW6044 requires an external 24Vdc power supply. The ship’s 24Vdc (emergency) power supply and be used if desired. The DC power supply connector sits next to the Ethernet port on the unit. 10.4 Connections The Video Module is connected to the CM (core module) via an Ethernet cable. Video Module Front Panel Connection Connector 10-30 VDC+ 10-30 VDCRJ45 connector Description Input power positive (ship) Input power negative (ship) Ethernet Connection to CM Table 9.4. A - Video Module Front Panel Connection Video Module Back Panel Connection Connector Video1 Video2 Video3 Video4 Description Channel 1 Video DB-15HD input Channel 2 Video DB-15HD input Channel 3 Video DB-15HD input Channel 4 Video DB-15HD input Table 9.4.B - Video Module Back Panel Connection In cases where the video module is not co-located with its video source the following video cable types are recommended to bridge the distance between video sources and the video module: 1. 75-ohm Coaxial cable - RG11 for cable lengths > 30m a. Reference: FLAMEX RG11AU b. Type: Marine Grade – Low Smoke, Halogen Free, Fire Retardant c. Approval: ABS, BV, DNV, GL, LRS or RINA 2. 75-ohm Coaxial cable – RG6 for cable lengths < 30m a. Reference: FLAMEX RG11AU b. Type: Marine Grade – Low Smoke, Halogen Free, Fire Retardant c. Approval: ABS, BV, DNV, GL, LRS or RINA 3. 75-ohm Coaxial cable – RG-59 for cable lengths < 10m The above cables must be converted to a 15-Pin Male VGA Plug at the Video Module end using a manufactured BNC to VGA cable assembly and possibly BNC F/F Unions to connect to the Video Module input. Page 55/ 191 We recommend the above specifications. Alternative cables may be suitable for installations. Contact us for verification before using cabling other than that specified in the table above. 10.5 Data communications The unit fully relies on Ethernet connection to the Core module which must be within the VDRs specified (commissioned) IP-range (refer to 2.5 Network configuration). 10.6 Indicators Link speed (Green LED): • • The LED is on when there is a link connection. Otherwise, the LED is off. Activity (Yellow LED) • • The LED is flashing when there is activity on the link. Otherwise, the LED is off. Power supply: red LED. 10.7 Errors If errors occur within the Core Module these will be indicated on the display of the Bridge Display Unit. 10.8 PC set-up To set up the Video Module a service PC should be connected to the module (LAN connection) and run the VCS2 remotely. To make this connection, complete the steps below: 1. 2. 3. 4. 5. 6. 7. Connect the laptop to the Ethernet port (labeled “Output”) located at the front of the Video Module. On the laptop’s desktop screen, open the Control Panel (Start > Control Panel). Double-click the ‘Network Connections’ icon, right-click the now visible ‘Local Area Connection’ icon and select ‘Properties’ from the right-click menu. Select “Internet Protocol (TCP/IP)” in the connection pane and press the ‘Properties’ button. Select the ‘Use the following IP address’ radio button, enter 192.168.199.1 in the ‘IP address’ field and 255.255.255.0 in the ‘Subnet mask’ field. Press ‘OK’. Select the ‘Advanced’ tab and press the ‘Settings’ button in the ‘Windows Firewall’ section. Select the ‘Advanced’ tab and press the ‘Settings’ button in the ‘Network Connection Settings’ section. Page 56/ 191 8. Press the ‘Add’ button and in the “Service Settings” window: i. ii. iii. iv. v. vi. Enter Video TCP in the ‘Description of service’ field. Enter 192.168.199.228 in the ‘Name or IP address’ field. Enter 3659 in the ‘External Port number for this service’ field. Enter 3659 in the ‘Internal Port number for this service’ field. Select the TCP radio button. Press ‘OK’. Press the ‘Add’ button and in the Service Settings window: 1. 2. 3. 4. 5. 6. a) b) c) d) e) 10.9 Description of service: Name or IP address’: External Port number for this service: Internal Port number for this service: Select the UDP radio button. Press ‘OK’. Enter Video UDP Enter 192.168.199.228 Enter 2649 Enter 2649 Press OK in the Advanced Settings window. Press OK in the Windows Firewall window. Press ‘Close’ in the Local Area Connection Properties window. Install VCS2 on the Service PC. Run VCS2 on the service PC. Configuration The required video capture interval is 15 seconds (4 images per minute) for each video source. The Core Module initiates the capture of video information and specifies its configuration. This includes: ▪ ▪ ▪ ▪ the video channel to be digitized. the sources of the vertical and horizontal syncs. the coefficients for the Phase Locked Loop (PLL) -generated pixel clock (or selection of an external clock); and the dimensions (number of samples and lines) of the captured frame. The video capture can be configured using the Video Configuration suite. ▪ Edit the <VidChanX.ini> file for each video source. Page 57/ 191 10.10 Video Channel Configuration File Each video channel has a separate video channel INI file: <VidChan1.ini>, <VidChan2.ini>, <VidChan3.ini>, and <VidChan4.ini>; these files are located in the C:\VDRApps directory. Manual editing of an existing <VidChanx.ini> file is generally not done unless the file fails to provide an adequate initial capture. This may be the case whereby a <VidChanx.ini> file is copied/supplied from a previous successful radar connection and the file fails to provide an adequate image capture on a new connection of the same type of radar. Below is a list of the contents within a <VidChanx.ini> file and their meaning. Parameter Typical Value HsRate1 80.0 Pclk1 135.0 VCO1 2 CPmp1 6 N1 0 Phase1 0 XDim1 1288 Remarks XOffset1 300 HSYNC rate in kHz for default source The exact pixel clock frequency (in MHz) for the system (as specified by the display’s manufacturer) Normally set based on the pixel clock rate (0=12-37MHz, 1=3774MHz, 2=74-140MHz, 3=140-170MHz) 0 to 7. Normally set based on values reported from <VideoConfigSuite.exe> If set to zero, defaults to PClk1*1000/HsRate1 0 to 31: Sharpens the image by accommodating for delays due to cable length and stray capacitance. Sets the captured width. It is recommended to set the XDimension 8 larger that the desired image, since the X-offset is adjustable only in multiples of 8. Shifts the image to remove black pixels at left edge. YDim1 1024 Sets the captured height. YOffset1 40 Shifts the image to remove black lines from top. Table 9.10.A - CLOCK Parameters Page 58/ 191 Parameter Typical Value HPOL1 1 VPOL1 1 XCLAMPPOL1 -1 XCOASTPOL1 1 PreCoast1 0 PostCoast1 0 Remarks 0 or 1. HSYNC Polarity - Changing this value will increase margin at the left of the image - Choose the value which produces the widest margin, and then adjust with XDim1 0 or 1. VSYNC Polarity Captured images will not be rectangular if incorrect value is chosen -1=Internal, 0= Negative, or 1= Positive. VCO1 2 -1=Internal, 0= Negative, or 1= Positive. 0 to 255. Number of clock synchronization pulses to skip prior to COAST signal 0 to 255. Number of clock synchronization pulses to skip after COAST signal 0 to 255. For composite signals only, used to differentiate a VSYNC from a HSYNC Must be present and must be same value as in [CLOCK] section CPmp1 6 Must be present and must be same value as in [CLOCK] section N1 0 Must be present and must be same value as in [CLOCK] section SyncThreshold1 Table 9.10.B - SYNCS Parameters Parameter Typical Value RGain1 75 0 to 255. Specifies A/D range for the red video line. GGain1 75 0 to 255. Specifies A/D range for the green video line. BGain1 75 0 to 255. Specifies A/D range for the blue video line. ROff1 128 0 to 255. Specifies DC offset for the red video line. GOff1 0 0 to 255. Specifies DC offset for the green video line. Remarks BOff1 0 0 to 255. Specifies DC offset for the blue video line. CVolt1 0 CPlace1 8 CLength1 20 VideoFormat1 1 0 = clamp to min voltage. 1 = clamp to midscale. Specifies when clamp occurs in pixel clocks from trailing edge of HSYNC. Specifies number of black pixels that participate in the DC restore clamp circuitry. RADAR = 1, CHART = 2 Table 9.10.C - VIDEO Parameters Page 59/ 191 Customize Entries in the VidChanX.ini Files Each entry in the <VidChanX.ini> file indicates the voltage level, timing, and signal characteristics of the video source. The values generated by Video Configuration Utility (VCS2) are based on VESA and Industry Standards and are adequate to capture initial images. If a video capture does not initiate, the most likely reason is that the VPOL1 field may be set wrong. The Video Configuration Utility (VCS2), if provided with a channel number, will capture and save a sample image to verify the proper state of the VPOL1 field. The image will be saved to the filename <TestImage.bmp>. The image will be annotated with a calibration grid to verify proper video alignment. In certain rare cases it may be necessary to optimize the video to correct the color balance. Page 60/ 191 10.11 Video Configuration Suite (VCS2) Application The Video Configuration Suite (VCS2) application is used to detect and adjust images to be captured by the Video Module. It has a built-in Auto Detection routine which detects many of the necessary parameters for the <VidChanX.ini> files. Existing <VidChanX.ini> files can also be directly modified within this application. Figure 10.11.1 - Video Configuration Utility User Interface Additional information: ▪ Maximum image height is 4095 pixels and maximum width is 2047 pixels. ▪ Maximum image size is 2062500 samples, which can accommodate images up to 1650x1250. Page 61/ 191 10.12 Video Capture The Video Configuration Utility automatically attempts to detect the video input on channel 1. To change the channel selection, click the radio button next to the number of the desired channel. To create settings for a new channel, click the New Video Channel button. If the channel uses Composite Syncs, select the “Composite” check box and use the associated radio buttons to indicate whether the composite sync is: ▪ ▪ on a separate TTL output; or SOG, Encoded in the input on the video channel. To reset all settings for the current channel, click the “Restore Default Settings” button. If the auto detection is successful the image will be displayed in the Capture area, and the Auto-Detection Status configuration data fields will display the appropriate information. If the auto detection fails, the capture must be manually configured. 1. Select a different Configuration Mode from the Configuration Mode drop list. 2. If you know the values of VSYNC and HSYNC, select Manual Configuration mode (the failsafe modes may help if you are unsure of the VSYNC and HSYNC rates). 3. Enter the VSYNC and HSYNC values. 4. Press Validate. 5. To load from a previous <VidchanX.ini> file a. select Manual Configuration mode; and b. press the “Load from INI button” and select the desired file. Page 62/ 191 Once an initial image has been captured (either through Auto-Detection or Manual Configuration mode), go to paragraph Horizontal Polarization to continue setup. Figure 10.12.1 - Successful auto detection 10.13 Horizontal Polarization The Horizontal Polarity setting is used to set the most possible black space to the left of the captured image. Complete the following steps to establish the correct Horizontal Polarity setting: 1. Click the Video Configuration Utility’s tab Configuration to open the Configuration page. 2. In the Polarity Section, select the other Horizontal button available either Positive or Negative and then: 3. Note the width of black space visible in the Image window on the left side of the image. 4. Select the setting either Negative or Positive in the Horizontal section which provides the most amount of black to the left of the image and leave it on this setting. Page 63/ 191 10.14 Vertical Polarization Use the Vertical Polarity setting to correct skewed images. Upon initial capture, the image should appear with sides at perfect right angles to each other (similar to image #1 below). If it is vertically skewed (similar to #2 below), vertical Polarity must be adjusted. Figure 10.14.1 – Correct vertical polarity on left. Vertically skewed image on right. Once the image has been captured, complete the following steps to correct the vertical polarity setting: 1. If the image appears skewed, select Pos in the Vertical Section of the Polarity Selection. 2. If the skewing is not corrected, select Neg in the Vertical Section of the Polarity Selection. 3. Note which setting establishes a correct image with sides at right angles to each other. Page 64/ 191 10.15 Sizing To capture the entire image, the image size and offset values must be adjusted using the controls under the Sizing tab. When adjusting the sizes, remember that a proper capture should fill the Capture window and keep all 4 edges of the image within the Capture window. • Important! It is NOT mandatory to adjust the captured image so that it completely fills the entire capture window. • The image should be adjusted so that it is as close as possible to the top and left edges of the capture window to set the least amount of black space on the right and bottom of the capture window. 10.16 Horizontal/Vertical Offset First, adjust the Horizontal and Vertical offset: 1. Press the “Start” button in the Horizontal/Vertical Offset section on the Sizing tab page. 2. This will display the following warning: Figure 10.16.1 - Offset Adjustment Warning Page 65/ 191 3. Click OK and follow the instructions below to select the offset position. Figure 10.16.2 - Selecting the image offset 4. Position the crosshair on the top-left corner of the image by clicking on the top-left corner of the image in the Capture window. Horizontal and vertical values (co-ordinates will display in the Capture window. 5. You may also adjust the position of the crosshair by changing the New Offset text entry boxes for the X and Y values in the Horizontal/Vertical Offset section of the Sizing page. NOTE 1: Horizontal X Offset must be a multiple of 8. It is recommended to leave a small amount of black space to help determine RGB settings. NOTE 2: Use the Zooming and Panning/Scrolling options to ensure the corner of the image is placed as close as possible to the top left of the Capture window. 6. Click the Apply button in the lower right-hand corner of the Horizontal/Vertical Offset section. 7. The image will automatically re-adjust. NOTE: The “Sequence #” field under the Capture window will be red until the adjusted image is updated for the new setting. Page 66/ 191 10.17 Dimensions If part of the image is not visible in the Capture window after it is moved to the upper left corner, it may be necessary to adjust the image height and/or width. To adjust the image size: 1. Click the “Start” button on the Dimensions section of the Sizing page. 2. The following warning will be displayed. Figure 10.17.1 – “Adjusting the Image Size” Warning 3. Click Okay and the captured video image will appear as in below screenshot. Figure 10.17.2 - Setting the dimensions 4. Click and drag the cursor on the image to reveal a rectangle that defines the image size. Page 67/ 191 5. Click and drag the rectangle in the red transparent area. 6. Pan the image outside the current viewing area to select a larger size. 7. Alternatively, enter a Width and Height number by: a. Entering the desired width in the New Dimensions: Width scroll box (Must be multiple of 8). b. Entering the desired height in the New Dimensions: Height scroll box. 8. Click the Apply button in the lower right corner of the Dimensions section. 9. The “Extents Changed” dialogue box confirms that the image size is adjusted. 10. Click “OK”. Figure 10.17.3 - Image Dimensions Adjustment confirmation Page 68/ 191 10.18 Interlaced Image A video source may provide a captured interlaced image like the one below. The captured image appears vertically 2 or 3 times within the Capture window. To adjust a captured interlaced image, complete the following steps: Figure 10.18.1 - Interlaced image 1. On the Configuration Page, set the Vertical Polarity to the same setting (negative or positive) as indicated in the Auto-Detection Information Box. 2. Repeat for the Horizontal Polarity setting. 3. If either Polarity is different, change them to the setting indicated in the AutoDetection Information Box (for example, if the Auto-Detection indicated the Vertical Polarity is negative ensure it is set to negative once the image has been captured). Page 69/ 191 4. If the images captured are not fully visible, then the image height must be adjusted. i. Click the Sizing tab to open the Sizing page. ii. Click the Start button in the Dimensions section. iii. Increase the image height to make this lower image visible. iv. Adjust the Image Dimensions as written above; and v. Adjust the height as necessary. Figure 10.18.2 - Interlaced image with height too small Page 70/ 191 Figure 10.18.3 - Interlaced image with height set properly 5. Once the images are entirely visible; ensure a small amount of black space still appears at the top of the Capture window to allow for further adjustments. To increase the amount of black space at the top of the Capture window: i. Click the Start button in the Horizontal/Vertical Offset section of the Sizing page. ii. Decrease the Vertical Offset. NOTE: In most cases, the Vertical Offset value will only need to be decreased slightly (for example, if the setting is 24 adjust to 16.). 6. Zoom in on upper image using Zoom in toolbar button OR View\Zoom In menu item. 7. Use the scrollbars to pan the image and find the top edge of the first image. 8. Click the From Image button under the Line 0 Start scroll box. 9. A message will allow user to click a point to find the top edge of the image. 10. Once the top edge of the image is found, scroll down to the lower image. Page 71/ 191 11. Locate the top edge of the second image using the same process; however, click the “From Image” button in the Line 1 Start section instead for the bottom image. Figure 10.18.4 - Interlaced values chosen 12. The image values have now been set. 13. Click the Interlaced checkbox on the Sizing tab page. 14. The interlaced images automatically merge into a single image. 15. If the image does not appear corrected or the image’s numbers look blurry (see figure below), it is very likely the installer chose the wrong pixel coordinates. That means the image is interlaced incorrectly. To correct the interlacing and sharpen the image: i. Click the up or down arrow on the Line 0 Start scroll box, adjusting the value 1 pixel at a time. ii. Wait for the next image before making another adjustment. iii. Click the up or down arrow on the Line 1 Start scroll box, adjusting the value 1 pixel at a time. iv. Wait for the next image before making another adjustment. v. Repeat steps i-iv above until the image is clear and sharp. Page 72/ 191 16. Once the image is properly interlaced, it can now be adjusted to finish correcting the image. Figure 10.18.5 – Incorrectly Interlaced image To achieve the optimal image capture. After properly interlacing the image, the installer may need to adjust the Sizing page’s Horizontal/Vertical offsets, Width and Height dimensions. Figure 10.18.6 - Properly Interlaced Image Page 73/ 191 10.19 Interleaved Image If the captured image has a resolution of 1600 x 1200 pixels or greater, it may appear repeated within the Capture window as below. To correct this image, it must be properly interleaved. Complete the following steps: Figure 10.19.1 - Interleaved capture 1. Click the Sizing tab to open the Sizing page. 2. Click the Start button in the Horizontal/Vertical Offset section. 3. Use the New Offset X scroll box and Y scroll box to change the horizontal and vertical offsets to move the image as close to the top left hand corner of the Capture window as possible, as given above in the Offset adjustment section. 4. With the image in place, and using the Zooming options, determine the top edge of both images. Click the “From Image” under Line 0 Start to select the uppermost pixel for the top image and click the “From Image” under Line 1 Start to select the top edge for the bottom image. Note: Line 0 Start should usually be left at 0 and Line 1 Start should be adjusted. Page 74/ 191 5. Click the Interleaved checkbox to activate Interleaved mode. 6. If step 5 causes a prompt to increase the height of the image, click Yes (in most cases the image height will be too small). 7. Zoom into the image. 8. If the image does not look correct, adjust Line 1 Start one value at a time until it looks correct. Note: You may need to readjust the image dimensions to better fit the image into the capture window. Page 75/ 191 10.20 Recalibration Once the image has been captured (or adjusted in the case of an interlaced image), it must be checked to ensure a proper capture that fills the Capture window but keeps all 4 image sides (edges) visible in the window. Check the aspect ratio by looking for a skewed circle. If the image does not appear skewed and the aspect ratio is correct, then this section can be skipped. But, if the installer can see a skewed circle, or if the image has the wrong aspect ratio, then the captured image may need recalibration. Use the following steps to recalibrate the captured image: It is recommended that the installer write down all settings before making any changes to the captured image as it may be necessary to revert to these settings. 1. Once the image has been captured to the Capture window, ensure the Vertical Polarity and Horizontal Polarity is set properly. Figure 10.20.1 - Incorrect aspect ratio on capture Page 76/ 191 First, locate a circle in the radar image in the Capture window. A Variable Range Marker (VRM) or range ring, available on most radar images, provides effective circles for assessing recalibration. If the image requires recalibration the ring will appear more oval than round. In that case it is necessary to recalibrate the image by setting the proper aspect ratio. To begin recalibration, click the Sizing Tab which opens the Sizing page. Click the Start button in the Recalibration section at the bottom of the Sizing page. In the Capture window click and drag a rectangle around the circle OR click the Pick Points button to select the points of the circle in order. (Picking points may be easier.). 4. When 4 points of the circle are selected by either method above, click the Apply button. 5. This applies the adjusted value of the Phase Lock Loop PLL Multiplier Number (N) and recalibrates the captured image. 6. If the recalibrated image has improved but needs further recalibration, click and drag a rectangle around the circle, OR click the Pick Points button to select the points of the circle in order. (Picking points may be easier.). 7. When 4 points of the circle have been chosen, by either method above, click the Apply button. 8. This will apply the newly re-adjusted value of the PLL Multiplier Number (N). 9. If the circle in the newly recalibrated image appears more oval than in step vi, click Start to begin again. 10. Click Revert to Last to reset to the previous value of the PLL Multiplier (N). 11. Click Apply and repeat this procedure from step iv. 1. 2. 3. Figure 10.20.2 - Correct aspect ratio after recalibration 12. The Image Offset of the captured image will need to be re-adjusted. Follow the steps above: Horizontal/Vertical Offset to adjust the upper left corner of the image. Page 77/ 191 Note: With many radar images, it may be difficult to determine the true upper left corner of the captured image. The installer may have to adjust the image’s position several times to ensure it is as close as possible to the top left corner without losing any part of the image. Figure 10.20.3 - Recalibrated image with Image Offsets adjusted Page 78/ 191 10.21 Adjustments Tab To adjust the image quality, click the Adjustments tab to open the Adjustments page. This page includes 4 sections including: 1. 2. 3. 4. Sharpness Gain / Offset Adjustment Clamp Coast In these for sections the installer will find all the controls needed to adjust the image values as described below. Figure 10.21.1 - Adjustment Page Page 79/ 191 10.22 Sharpness The Sharpness section of the Adjustments page holds three scroll boxes to adjust the Phase, charge pump (CPMP), and the voltage-controlled oscillators (VCO). 10.22.1 Phase Once the image position is adjusted, is may still display pixilation (visible noise), banding, and/or soft edges. This means the image phase must be adjusted. To adjust the Phase: ▪ ▪ Enter a value or clicking the up/down controls on the Phase scroll box (The range available for adjustment is 0 to 31.). The image changes immediately to reflect the change. Continue to adjust the number until the image is sharp. Example: The image is highly pixilated at the left edge. Adjust Phase to 16. And the image appears clearer and more uniform. Adjust to 14, and the left edge of the image is now sharper, repeat until desired image quality is achieved. 10.22.2 CPMP (Charge Pump) When the image phase is sharpened, minor oscillation may still appear in the image. If so, it may be necessary to adjust the image CPMP. ▪ ▪ ▪ ▪ ▪ Check for oscillations at either the top of the image or near any straight black lines where they are most apparent. Note the image quality and use the CPMP scroll box to set CPMP between 0 and 3. The image is automatically updated to reflect the change. Note the image quality for improvement; and Make further adjustments as necessary. . Example: The image has varied individual lines of oscillation at its left edge. Adjust CPMP to 1. The left edge of the image is now much clearer and uniform. Adjust to 2. The left edge of the image is now sharp. 10.22.3 VCO (Voltage Controlled Oscillators) The VCO setting should NOT be adjusted unless the captured image is severely distorted. The VCO scroll box allows the installer to adjust the voltage-controlled oscillator. The range available for adjustment is 0 (default) to 3. Page 80/ 191 VCO range can be selected in accordance with the following table: Pixel Rate Range (MHz) Lower Upper Min 37 37 74 74 140 140 Max VCORNGE Setting OO O1 1O 11 VCO Gain, KVCO (MHz/V) 150 150 150 180 Table 9.22.3 - VCO Pixel rate range (MHz) 10.23 Gain/Offset To create a more uniform image, the installer can fine-tune the gain and/or offset in the Gain/Offset Adjustment section. This section includes: ▪ ▪ ▪ a histogram. red, Green and Blue Gain and Offset controls and. a Master Gain and Master Offset control. These controls give the installer three different options to adjust the Gain and Offset values for the Capture window. Adjusting Gain stretches the image vertically in the Capture window. Adjusting Offset shifts the image up and down in the Capture window. Figure 10.23.1 - Gain/Offset Adjustment Page 81/ 191 To fine tune the Gain and Offset using the histogram of Red, Green, and Blue icons: 1. 2. 3. 4. 5. Click on the histogram icon to be adjusted. Drag the icon and observe changes in the Capture window image. When the adjustment is finished, release the icon. The new value is displayed in the corresponding scroll box beneath the histogram. (The range is 0-255). Repeat the process for each of the controls in the histogram until the captured image is satisfactory. For example, click the Red Offset icon in the histogram and drag it up or down to adjust the Red Offset value. To fine tune the Gain and Offset Red, Green, and Blue separately, using scroll boxes and the Ref: selection: 1. Click on the scroll box for the value to be adjusted. 2. Set the Gain or Offset to the new value. (The range is 0 to 255). 3. Continue adjusting values until the image in the Capture window is fine tuned. To fine tune the Gain and Offset using the Master Gain and Offset scroll buttons: Adjusting Gain stretches the image vertically in the Capture window. 1. Click on the Master Gain scroll button to adjust the Gain of the entire image - instead of the individual Red, Green and Blue values (the range is 0 to 255). 2. Click on the Master Offset scroll button to adjust the Offset of the entire image - instead of the individual Red, Green and Blue values (the range is 0 to 255). Adjusting the offset shifts the image up and down in the Capture window. Figure 10.23.2 – Clamp and Coast sections of the Adjustments tab page 10.24 Clamp At the lower left of the Adjustments page is the Clamp section. It allows the installer to enable or disable the video capture HSync signal default. The Clamp controls are necessary so the installer can enable VSYNC signal capture if there is no HSYNC signal. ▪ Enable (Use HSYNC) check button: In the absence of a VSYNC signal, the video capture circuitry will use the HSYNC signal. This is the Clamp command default setting. Page 82/ 191 ▪ Disable (Positive) check button: The Disable (Positive) setting overrides the HSYNC signal and disables the Clamp command. ▪ Placement [0 – 255] and Duration [0 – 255] scroll boxes: These scroll boxes are only active if the Enable (Use HSync) check box is selected. They allow for the sampling of video to determine voltage corresponding to the image’s black levels. 10.25 Coast In the absence of a VSYNC signal, it may be necessary for the circuitry to obtain the HSYNC signal. ▪ Checked: In the absence of an HSYNC signal, the video capture circuitry will use the VSYNC signal. ▪ Unchecked: This setting overrides the usage of the VSYNC signal and, effectively, disables the “Coast” command. 10.26 Sync-on-Green (SOG) If a video source transmits via Sync-on-Green (SOG), the associated <VidChanX.ini >file (located in the C:\VDRApps directory) must be adjusted to include the following parameters: [CLOCK] HsRate1=xx.xxx XDim1=512 YDim1=800 [SYNCS] Source1=AD9887 N1=yyyy The HSYNC value (HsRate1=xx.xxx) can be obtained from the Video Config Suite application. The overall x dimension (N1=yyyy) is selected based upon the following: ▪ ▪ ▪ For HSync < 50: Set to 1200 For HSync between 50 to 70: Set to 1400 For HSync > 70: Set to 1600 It is recommended to use actual HSync value from the manufacturer’s radar (for example, the STN Atlas 6900 radar has a HSync of 37.5000 kHz). If HSync information is not immediately available from the radar manufacturer, complete the following procedure: 1. 2. 3. 4. 5. 6. 7. Open the Video Configuration Suite application. In the Configuration tab page, under the Configuration group, select “Composite”. Select the “SOG” radio button. The HSync and VSync values will appear in the Auto-Detection Status group. Record the HSync value and its polarity. Select Manual Configuration mode. Enter the HSync information and parameter information discussed at the beginning of this section into the applicable <VidChanX.ini >file. Page 83/ 191 Save the file. Click the Load <VidChanX.ini> file. Choose the <VidChanX.ini >file which was altered and saved in Step 5 above. 8. 9. 10. The above procedure provides an image in the Video Config Suite application that can be properly configured in accordance with paragraph ‘Video Configuration Suite (VCS2) Application’. If the HSync value was obtained via the Video Config Suite application, it is recommended that the installer carefully check to make sure that the VCO, CPMP, and Phase settings are correct for the captured image. Save Settings (REMEMBER!) Once the image has been adjusted correctly, click the Configuration tab page and click Save <VidChanX.ini> file to save the settings. 10.27 Info Tab Selecting the Info tab of the Video Configuration Utility opens the Info page. It provides statistics on the capture image. The Histogram window displays the histogram for the image. The Cross-Section window (indicated by the dashed red line) shows a graph of the current crosssection of the image, as well as minimum and maximum values of Red, Green, and Blue on the cross-section line. Channel Selection lets the user enable or disable which color channels are selected or deselected. For example, the installer can disable Green. The Status controls at the bottom of the page enable the installer to display information about the image such as: ▪ ▪ ▪ ▪ ▪ ▪ BPP (bits per pixel) Image size Cursor position RGB value at the cursor position Viewing bounds Zoom level Page 84/ 191 10.28 VCS2 Menu Overview This section provides an overview of the menu items available in the Video Diagnostics application. ▪ File Menu o o o o o ▪ View Menu o o o o ▪ Load Bitmap: Selecting this option opens a file selection window from which a user must choose a saved bitmap file to load to the Image window for viewing. Save Bitmap: This will save the current image to a bitmap file. Save Histogram: This will save the Histogram from the Info page to a CSV file (Comma Separated Value file). Save Cross-Section: This will save the cross-section of pixel data indicated by the dashed red line in the Capture window to a CSV file. Exit: This will exit the application. Zoom In: Zooms into the image. Zoom Out: Zooms out of the image. Fit to Window: Will cause the image the edges of the image to fill to the edges of the Image window. Full Screen: This sets the Video Configuration Utility to Full-Screen mode. Right click on the image in Full-Screen mode to access the menu. Toolbar o o o o o o o o o o Load: Load a bitmap, same as File->Load Bitmap. Pan Tool: Activate the Panning tool for the Image Window. This is the default. Eyedropper Tool: Activate the Eyedropper tool to choose a pixel and get the value. ZoomBox Tool: Activate the ZoomBox tool, which lets the user select an area to zoom. Zoom 1:1: Zooms to the original scale of the image. Zoom In: Increase the zoom magnification. Zoom Out: Decrease the zoom magnification. Fit to Window: Display the full image in the window. Fullscreen: Toggle between full screen mode and other views. Freeze Image: Toggle Freeze mode to freeze the current image, do not load any new images from the capture sequence. Page 85/ 191 10.29 Test Video Inputs To ensure that video capture has been properly configured: 1. 2. 3. 4. 5. Connect the interface to the CM. Deselect ‘Record’ from the ‘Tests’ menu. Select ‘Video Test’ from the ‘Tests’ menu. Maximize the Video Data window. Ensure the video is captured correctly (entire screen, correct color presentation and brightness/contrast and sharpness). 6. Once the settings are correct, place the VDR_Record application in record mode for several minutes. 7. Download the new data from the VDR on the playback station. 8. Play back the video data. NOTE: Refer to Appendix 5: Playback Software for download and playback instructions: 9. Ensure the video is presented correctly. If not, stop recording and make the necessary changes to the configuration: a. If the top edge of the image capture is not captured correctly, go to the VidChanX.ini file and increase the value assigned to CPMP1 field. b. If a color is not presented correctly on each capture, edit the Vdrparams.ini file video section so that the enhancedCompression field is set to 0. c. If the captured image has a primarily black background and noise is present at the low end of the captured signal, remove the noise by setting the noiseClipping field to 1 in [VIDEO] section of the <vdrparams.ini> file. This setting must be used with care. If there is no noise near the black level a change in the noiseClipping field may set most of the image to black. This setting is only used if enhanced compression is enabled. 10. Repeat steps 1 through 8 until the video presentation is correct. Page 86/ 191 11. NW6880 (FFRM) Float Free Capsule Jotron TRON 40 MKII 11.1 General specifications Be aware that all instructions provided by Jotron must be followed during installation. Information in this NetWave manual gives additional information regarding the TRON 40VDR in combination with the NW6000 VDR and summarizes information out from the installation manual of Jotron. For full information about the TRON 40VDR NetWave Systems refers to the installation and user manuals of Jotron. Both manuals can be found on the Extranet webpage of Orolia NetWave (www.oroliamaritime.com - Login) and both manuals are available on the USB-card enclosed the hardcopy version of this manual. Besides this the user manual is enclosed to the delivery box of the TRON 40VDR and can be found on the internet site of Jotron as well. According to the IEC61996-1:2013 (MSC.333 (90)/5.4.3) recording of the VDR data shall also take place on an approved free-floating Final Recording Medium for a period of not less than 48 hours. The unit to be installed in conjunction with this VDR is the Jotron TRON40 VDR which basically comprised of an EPIRB with internal memory to the VDR. External Supply type: Locator lights: Status indication: Frequency range: Programming: Operating life EPIRB: Weight approx: Material housing: Antennas: Antenna: Battery module: PoE Flashing Xenon light Test LED 406,028 / 121,5MHz IR 168 hours at -20°C 3.5 kg Polycarbonate with 10% glass fiber 406.028MHz, 121.5MHz Built in, vertical polarization, omnidir GPS Built in GPS patch antenna Lithium-Thionyl chloride (Li-SOCL2) Page 87/ 191 This device fully relies on the Ethernet PoE supplied from the Core Module. This unit has 1x 100Mbps TX PoE port, receiving 802.3af compliant PoE @48V. The total power budget is 4 Watts. The unit fully relies on Ethernet connections to the Core Module and provide datas within the VDRs specified (commissioned) IP-range (refer to Network configuration). The unit must be connected to any of the VDR Core Module ports. NW-6080 Float fr ee capsule Refer to N6-001.4 NW-6000 Cor e Modul e Refer to N6-001.2 Single wir e (PoE) ether net cabling Page 88/ 191 11.2 Location and mounting The protective capsule must be sited in the vicinity of the bridge on the external deck area of the vessel to maximize the probability of its survival and recovery following an incident. Criteria to be considered when assessing the optimum position shall include but not be limited to the following: • • • • Separation from fuel or other potential fire sources. Separation from probable sources of mechanical damage. Operational environment for continued serviceability. Accessibility for copying of recorded data and for routine maintenance. The TRON 40 shall be sited in the vicinity of the bridge on the external deck area of the vessel to maximize the probability of its survival and recovery following an incident. During replacement and new installation of TRON 40VDR it is important to pay attention to the location of the TRON40 Float Free Capsule. Strong RF signals from radars or other transmitting antennas can cause communication errors which in turn can result in malfunctioning of the TRON 40VDR. It is recommended to test the position of the Jotron device with a flying cable and an ICMP test first, before installing it (see paragraph ‘Connection test with flying cable’). Take following aspects into account for choosing the mounting location of the TRON 40VDR. - It is not recommended to locate the TRON 40VDR on the compass deck because of high risk of exposure to strong RF signals. - Find a new mounting location as far away as possible from any radar interference and/or other antennas conform Jotron specifications (see Jotron installation manual). Make sure the TRON 40VDR is not directly in line of sight of any radar, and at least 3 meters away from any antenna. - Stronger antenna signals (than the TRON 40VDR is approved for) can affect the VDR storage performance. The TRON 40VDR is approved for 100 V/m in the VHF frequency range 156 - 165 MHz. In other areas of the frequency range 150 kHz - 2 GHz the requirement is 10 V/m. A standard VHF antenna will have 10 V/m at distance of 3 meters in the antenna lobe. Therefore, the absolute minimum distance to a VHF antenna, at the same height needs to be no less than 3 meters. It is strongly recommended to have a much larger distance to other transmitting antennas. - RF signals from transmitting antennas are likely to be weaker at low levels. Therefore, reduction of interference may be achieved by installing the TRON 40VDR lower than all transmitting antennas. - It is recommended to find a location with “natural” shade from the radar systems. This would typically be on a wing opposite to the radar mast. Page 89/ 191 - Make sure the total cable length of original installation + new installation does not exceed 100 meters. - If the mounting of the TRON 40VDR requires a long outdoor cable, it is recommended to put the cable in a separate steel pipe, which is welded to the ship hull. This will protect the wire against RF signals interfering with the VDR signals. - Before final relocation it is advised to do a test with a flying cable to ensure proper functioning of the TRON 40VDR. - It is critical to choose a position where the released EPIRB will not get trapped by overhangs, rigging, antennas and so forth, in case the vessel will sink. - The EPIRB is supplied with an instruction plate that should be mounted next to the EPIRB so that is easily visible in an emergency. - The EPIRB must be installed in the vicinity of the navigation bridge, i.e. on the wings of the navigation bridge. Access via vertical ladder should not be accepted. - Since the mounting location is critical for the performance of the TRON 4VDR, please find below screenshots out from the TRON 40VDR Installation manual (revision J). Page 90/ 191 Page 91/ 191 Page 92/ 191 11.3 Connection test with flying cable Before connecting the TRON 40VDR device it is advisable to test the new position with a flying cable. Connection testing can be done with a running ICMP test by using the utility hrPing. This utility can be downloaded from: https://www.cfos.de/en/ping/ping.htm. Connect the TRON 40VDR to the flying cable (run as Admin), put it on the new position and run the ping utility in CMD by typing the following command: hrping.exe 172.16.30.10 -t -w 100 -s 15 -y 10 -gg Note: run hrping.exe by entering the full path name: C:\ ... \ ... \hrping.exe 172.16.30.10 -t -w 100 -s 15 -y 10 –gg Please note that IP-address for OEM differs. A graph, similar to the one below will be shown in case of a proper connection… Graphic 10.3.A: Good connection of TRON 40VDR Graphic below shows connection issues, the location of the TRON 40VDR is not suitable. Please locate the capsule in a different position. Graphic 10.3.B: Connection issues of TRON 40VDR Page 93/ 191 11.4 Junction box 11.4.1 Grounding of cables and junction box Please note that your connections may differ from pictures below, see paragraph ‘Wire schematic’. It is important that the grounding shields of the cables (of TRON 40VDR and VDR) are in contact with the cable glands of the junction box. Therefore, firstly strip off 7 cm of the cables to create 7 cm of grounding shield. Separate the grounding shields from the cables. Do not remove the grounding shields. Place the grounding shields over the screw-threads and enclose the cable glands on both sides of the junction box. In this way the grounding shields are connected to the metal cable glands. Note: by reopening the cable glands, the grounding shields will break, and the cable needs to be stripped off again. Page 94/ 191 To ensure water tightness make sure the cable glands are tightened well and the provided vulcanizing tape is placed around the 2 cable glands as shown on picture below. Page 95/ 191 11.4.2 Wire schematic Junction box There are 2 different cable types of the TRON 40VDR with 3 different cable connections (2 for cable type 1, 1 for cable type 2). Identify the serial number of the docking module and identify the cable type of TRON 40VDR to determine the applicable wire diagram. The serial number of the docking module can be found as indicated on picture below, this is not the serial number of the VDR EPIRB. Cable type 1 TRON 40VDR: Cable type 2 TRON 40VDR: Connect the TRON 40VDR to the VDR via the junction box as further described. Notes: - Connect inside the junction box on the VDR side White/blue and Blue wires together. - Connect inside the junction box on the VDR side the White/brown and Brown wires together. - Note that exchanging the DC + and DC – will not cause any damage, but the TRON 40VDR will not work. Connections NW6000 VDR side: Page 96/ 191 Cable type 1 Standard T-568B (of TRON 40 VDR MKI) Serial numbers docking module 0-7500 (summer 2014 - 2016) VDR-side Connector pin TRON 40VDR side Rx+ White/Orange 1 White/Orange Rx+ Rx- Orange 2 Orange Rx- Tx+ White/green 3 White/green Tx+ Tx- Green 4 Green Tx- N/A NOT connected 5 White/blue Connected but not used DC+ White/blue + Blue 6 Blue DC+ DC- White/brown + Brown 7 White/brown DC- N/A Not connected 8 Brown Connected but not used Cable type 2 Proprietary (of TRON 40 VDR MKII) Serial numbers docking module 7500-12000 (summer 2016 - October 2017) VDR-side Connector pin TRON 40VDR side Rx+ White/orange 1 Black Rx+ Rx- Orange 2 Brown Rx- Tx+ White/green 3 Green Tx+ DC+ White/blue + Blue 4 Orange DC+ N/A Unconnected 5 White Connected but not used Tx- Green 6 Yellow Tx/ DC- DC- White/brown + Brown 7 Blue DC- N/A Unconnected 8 Red Connected but not used Cable type 1 Standard T-568B (of TRON 40 VDR MKII) Serial numbers docking module > 11203 (from October 2017) VDR-side Connector pin TRON 40VDR side Rx+ White/orange 1 White/orange Rx+ Rx- Orange 2 Orange Rx- Tx+ White/green 3 White/green Tx+ Tx- Green 4 Green Tx- N/A Not connected 5 White/blue Connected but not used DC+ White/blue + Blue 6 White/brown DC+ DC- White/brown + Brown 7 Blue DC- N/A Not connected 8 Brown Connected but not used Page 97/ 191 Grease the 4 bolts of the junction box from top to bottom with some of the remaining silicone grease from the TRON 40VDR. This will prevent corrosion of the bolts and will enable the next engineer to open the junction box without replacing it. Some copper slip or other water dispersing formula can also be used. 11.5 (Led) indicators on docking module Below is a description of the LED lights on the Docking Module (83180 MKII). 11.6 Warnings If warnings occur these will be indicated on the display of the Bridge Control Unit. 11.7 Operating instructions After commissioning of the VDR system, this unit does not require (crew) operating instructions. Page 98/ 191 12. NW6860 (FRM) fixed HSS Capsule 12.1 General The hardened storage server (HSS) forms the Fixed Final Recording Medium and is colored bright orange for ease of location in the event of an incident. The HSS is designed to be mounted on the ´monkey island´ - and is fitted with an acoustic beacon to aid underwater recovery by a Remotely Operated Vehicle (ROV) or diver in the event of an incident. The unit is designed to withstand the extreme shock, impact, pressure and heat exposure requirements of the IEC Performance standards which mirror those enforced by the maritime and aerospace authorities. The HSS has the capacity to store audio, radar video and other data for a rolling 48-hour (minimum) period as defined in the regulations. All power and data are passed to the HSS via one single Ethernet cable. Connection is via a waterproof connector. The HSS has a release mechanism to facilitate underwater recovery both by a diver or a ROV. Suitable handles are provided to ensure that the capsule may be retrieved safely after release. The HSS has an externally mounted underwater location beacon (ULB) with an activation sensor to avoid inadvertent activation due to spray/rain/hosing off. The HSS (memory module) protective capsule is painted a highly visible fluorescent orange with the required text: VOYAGE DATA RECORDER, DO NOT OPEN and REPORT TO AUTHORITIES. When the HSS has been damaged after an incident, e.g. the HSS was exposed to fire or the ship has sunk, it may be returned to the manufacturer for the data to be extracted. Alternatively, authorities may apply for instructions on how to extract the recorded data. The HSS meets the following specifications: • • • • • • • • Fully meets IMO Resolution A.861(20) and all applicable Safety of Life at Sea (SOLAS) Regulations. Fully compliant to the IEC 61996-1:2013 Ship borne Voyage Data Recorder Performance Requirements and IEC60945, Maritime navigation and Radio communication systems - General requirements. Records a minimum of 48 hours of voyage data. Single wire Power and high speed (100BaseT) Ethernet communications. Reliable solid-state recording (2+ years data retention unpowered). Fitted with an acoustic underwater location beacon operating in the frequency band of 25 kHz to 50 kHz with a battery life of at least 90 days, which meets SAE AS 8045A. Tamper resistant capsule design. The final storage medium within the HSS retains the recorded data for a period of at least two years, following termination of recording, under the specified operational and storage conditions. Page 99/ 191 • • • • • • • • • • 64 GB memory. Exceptional read, write and erase performance. Built-in proprietary technology for full hard-disk emulation, high data reliability and maximum flash lifetime. Data integrity with Error Detection Code/Error Correction Code (EDC/ECC) based on a combination of BCH and Hamming algorithms. Data protected in hardware with digital signature: RSA with 64-byte key. 4-bit Error Detection Code/Error Correction Code (EDC/ECC), based on a patented combination of BCH and Hamming code algorithms. Guaranteed data integrity even after power loss. Transparent bad-block management. Dynamic and static wear-levelling. Wear levelling algorithm that provides more than 5 million write / erase cycles for reliable data storage over an extended period. The Hardened Storage Server (HSS) design ensures survivability of critical voyage data to the following severe environmental conditions: • • • • Impact shock - 50 g half sine-wave pulse for 11 milliseconds. Penetration - 250 kg mass dropped 3 meters impacting with 100 mm diameter pin. Fire exposure - 1100 ˚C for 1 hour and 260 ˚ C for 10 hours. Deep sea pressure - 30 days in sea water at 60 MPa (an equivalent depth of 6000m). The capsule and its reflective materials comply with IMO regulations and may not be painted/colored with other materials other than those included in the Overhaul Kit NW9800-980. Page 100/ 191 12.2 Location and mounting The protective capsule must be sited in the vicinity of the bridge on the external deck area of the vessel to maximize the probability of its survival and recovery following an incident. The capsule shall be positioned clear of rigging and other potential obstructions and as near to the centreline of the ship as practically possible. Criteria to be considered when assessing the optimum position shall include but not be limited to the following: • • • • • • • Separation from fuel or other potential fire sources. Separation from probable sources of mechanical damage. Operational environment for continued serviceability. Accessibility for copying of recorded data and for routine maintenance. Facilitation of underwater removal and retrieval by both divers and ROVs. There shall be a clear unobstructed space in the vicinity of the capsule to allow an ROV or diver to work. Compass safe distance = 60 cm. The HSS consists of two sub-assemblies. A deckmount sub-assembly is directly fastened to the ship and provides watertight cable entries for the single wire WaveNet connection. A removable sub-assembly (the capsule) is attached to the mounting base with a unique quick release mechanism for recovery by either a diver or ROV. 12.3 Power supply This unit has 1 x 1000 TX PoE port, receiving 802.3af compliant PoE @48V and fully relies on the Ethernet PoE supplied from the Core Module. The total power budget is 6 Watts. 12.4 Installation and connections NW-6000 Core Module Refer to N6-001.2 Single wire (PoE) ethernet cabling The unit must be connected to any of the VDR Core Module ports (with the optional addition of a junction box) with a maximum of 100-meter network cable (CAT 6 or higher). It is preferred not to use any connection between the Core Module and the storage medium. The unit is to be configured within the VDRs specified (commissioned) IP-range (refer to 2.5 Network configuration). Page 101/ 191 The HSS consists of two sub-assemblies. A deckmount subassembly is directly fastened to the ship and provides watertight cable entries for the single wire WaveNet connection. Together with the deck mount a set of stainless-steel bolts are provided to be used for bolting the deckmount on a suitable position on deck. A removable sub-assembly (the capsule) is attached to the mounting base with a unique quick release mechanism for recovery by either a diver or ROV. To ensure water tightness between sub-assembly and deckmount, a roll of vulcanized tape is delivered, which needs to be attached underneath the quick release mechanism after connecting the cable to CPU of the storage medium. A) Deckmount Install the stainless-steel deck mount on a suitable place using the supplied bolts as per regulatory requirement. (Freedom of access and retrieval, approx. 1-meter free space around). B) Cabling Lead the network cable through the gland at the side of the deck mount and ensure that sufficient length is available (30 cm). The M16 gland is an EMC gland requiring that the shield of the cable be exposed and connected within the gland on entry to the deck mount. (Network cable is not standard supply) C) Connector Attach a suitable RJ-45 (preferably industrial type) connector to the network cable as connection instruction provided with the connector. (RJ45 connector can be purchased separately on request) Page 102/ 191 D) After attaching the RJ-45 connector to the network cable, plug the connector in the network plug on the blue CPU housing as below. E) Once the storage medium and the deckmount are placed upon each other, attach the vulcanized tape around the flanges to ensure water tightness. Stretch around 50cm of vulcanized tape and make sure to wrap it twice around the seam that is between the capsule and the deckmount. F) Place the locking mechanism. Page 103/ 191 12.5 Data communications The unit fully relies on Ethernet connections to the Core Module within the VDRs specified (commissioned) IP-range (refer to 2.5 Network configuration). 12.6 Indicators When in unassembled state (and viewed form the bottom of the capsule part) a LED is available to determine Link, Activity, and Error status during service. Link (Green) • • The LED is on when there is a link connection. Otherwise, when no power is received, the LED is off. Activity (Yellow) • • The LED is flashing when there is activity on the link. Otherwise, the LED is green. Error (Red) • The LED is steady when the CPU unit within the capsule is faulty. • The LED is flashing when the link to the memory-part is faulty. 12.7 Errors If errors occur these will be indicated on the display of the Bridge Display Unit. 12.8 Configuration The unit does not require any manual configuration. 12.9 Operating instructions After commissioning of the VDR system, this unit does not require (crew) operating instructions. Page 104/ 191 13. NW6890 FRM PoE Splitter Box for non-Netwave capsules 13.1 General This junction box provides 24V DC to power the HVR04 Final Recording Medium from a single PoE network cable originating from the CM (core module). This junction box is not required to install the standard fixed capsule or the Jotron free floating FRM. This principle serves the performance criteria for the VDR which include continued operation (recording of specific data) during a power-failure. In that case the PoE (power) will be available for two hours. NW-6000 Core Module 24V 13.2 FRM PoE Splitter Refer to N6-001.2 Single wire (PoE) ethernet cabling Location and mounting This junction box with integrated power splitter is mounted in the vicinity of the fixed capsule (in an unprotected environment (IEC60945) but may also be placed below-deck. 13.3 Power This device fully relies on the Ethernet PoE supplied from the Core Module. This unit has 1 x 100 TX PoE ports, receiving 802.3af compliant PoE @48V. The total power budget is 3,6 Watts. Page 105/ 191 13.4 Connections Ethernet OUT to HVR04 Ethernet OUT Ethernet IN (fm Core Module (PoE) PoE IN SHIELD 24V OUT to HVR04 24 VDC OUT to P D (powered device) + Page 106/ 191 14. NW64900 Data Acquisition System 14.1 General This data acquisition system (DAQ) aims to provide a flexible, scalable and universal platform to interface analogue, digital or serial sensors to the VDR. The architecture allows for a single wire Ethernet (which includes PoE, power over Ethernet) to connect to the CM (core module). Within the DAQ various modules provide input ports for analogue, digital and serial signals to be recorded by the VDR. Up to 8 additional DIN-rail mounted DAQ modules may be mounted for each Buscoupler. The DAQ system relies on the ‘busbar’ integrated within the DIN rail, serving the function of power and data distribution. Within the DAQ, the so called ‘WaveNet Buscoupler’ plays a vital role since it has multiple functions: Function 1: to convert PoE to supply power suitable to the various (input) modules to be placed on the DIN busbar integrated within the (DIN)rails. Function 2: to concentrate the data coming from the input ports of the various modules and to communicate to the CM (core module) in compliance with the IEC61162-450 LWE (light weight ethernet) specification. Function 3: to act (optionally) as a data concentrator/repeater, providing accumulated data in a universal serial (NMEA) output-form to serve other devices beyond the VDR. Page 107/ 191 14.2 Location and mounting The DAQ may be situated in any protected environment. 14.3 Power Supply This device fully relies on the Ethernet PoE supplied from the Core Module. This unit has 1 x 100 TX PoE ports, receiving 802.3af compliant PoE @48V. The total power budget is 12 Watts. 14.4 Connections From the DAQ, containing the Buscoupler and (typically) multiple adaptors, there is only one single Ethernet cable to be connected to the CM. NW-6000 Core Module Ethernet (PoE) Page 108/ 191 14.5 Wiring scheme All DIN rail mountable adaptors have a unified connector and wiring identification scheme. Please note that there are 3 different sizes of adaptors (depending on port characteristics and number of ports), with a varying number of connectors and wires. Consequently, these adaptors differ in width. The connector and wiring identification are as follows. Page 109/ 191 Please note: the largest width adaptor is shown with connectors in rows A, B and C. Smaller adaptors, with less channels, will have 1 row (A) or 2 rows (A and B). Top rows are identified by a T-prefix, whereas the bottom rows have a B-prefix. Page 110/ 191 15. NW6410 WaveNet Buscoupler 15.1 General There must always be 1 buscoupler (BC) within any DAQ to provide data communications to the Core Module. There cannot be more than a single Buscoupler on a single DIN busbar. 24V AUX output, resettable fuse at 750 mA, 24V AUX input, max 1A. 15.2 Location and mounting The NW6410 WaveNet Buscoupler connects to the DIN busbar by mounting it from the top first and only in a vertical direction. Once the adaptor is attached to the DIN rail it should not be shifted in a horizontal direction (!) since this will render the feathering contacts between the module and the DIN useless and the system will fail beyond repair. 15.3 Power supply This unit has 1 x 1000 TX PoE port, receiving 802.3af compliant PoE @48V and fully relies on the Ethernet PoE supplied from the Core Module. The total power budget is 12 Watts. 15.4 DAQ Card Power Budget The typical power budget required by the DAQ cards are as follows… Part Number NW6410 NW64208 NW64216 NW64308 NW64316 NW64324 NW64404 NW64408 Description Bus coupler 8 x NMEA 16 x NMEA 8 x DIN 16 x DIN 24 x DIN 4 x AIN 8 x AIN Power Budget (W) 3.00 1.39 2.78 0.87 1.70 3.40 3.12 6.24 For example: 1 x Bus Coupler (3W) – always required for each DAQ system. 1 x 16 NMEA (2.78W) 1 x 24 DIN (3.4W) Requires 9.18W which is within the 12W budget. Page 111/ 191 15.5 Connections This adaptor has following ports: Ethernet to be connected to the Core Module (or other brands’ IEC61162-450 compliant VDR or otherwise) Channel 1 Channel 2 Channel 3 NMEA (IEC61162-2) input port (4k8 up to 38K4 Bd) NMEA (IEC61162-2) input port (4k8 up to 38K4 Bd) NMEA (IEC61162-2) input port (4k8 up to 38K4 Bd) Power A Power B Power IN, 24 VDC for non PoE applications Power OUT, 24 VDC to providing voltage sourcing for dry contacts (max 50 mA) Figure 15.5.1 - Connection figure Buscoupler Page 112/ 191 Figure 15.5.1 - Connection table Buscoupler 15.6 Data communications The adaptor has 1 x 10/100 TX PoE and three serial ports (IEC61162-2). In default ‘VDR mode’ in order to offload its data - it relies on the ethernet connection to the core module which must be IEC61162-450 compliant. 15.7 Indicators Led PWR Link Data PoE 15.8 Function Power supply to DIN Busbar established Connected to Core Module Communications Power Supply by PoE OK Errors If errors occur within the Buscoupler these will be indicated on the display of the Bridge Display Unit. 15.9 Configuration The unit does not require any manual configuration. 15.10 Operating instructions After commissioning of the VDR system, this unit does not require (crew) operating instructions. Page 113/ 191 16. NW64208/16 Serial/NMEA 8/16 channel adaptors 16.1 General These adaptors provide input ports for serial / NMEA data with baud rates up to 38k4. They are available in 8 and 16 channel configurations within a harmonized configuration and wiring scheme. These adapters are compliant with IEC 61162-1. These adaptors send serial NMEA data (IEC61162-1), 4k8 up to 38K4 baud) they receive from their input ports onto the busbar ‘backplane’ for further processing by the Buscoupler which in its turn streams the data onto the (VDR) network. 16.2 Mounting These adaptors connect to the DIN busbar within the DAQ enclosure by mounting them from the top first and only in a vertical direction. Once the adaptor is attached to the DIN rail it should not be shifted in a horizontal direction (!) since this will render the feathering contacts between the adaptor and the DIN useless and the system will fail beyond repair. 16.3 Power Supply These adaptors receive their power (indirect PoE converted to 24V DC) via the DIN rail mounted NW6410 Buscoupler. Page 114/ 191 16.4 Connections For physical connector and wiring identification please refer to the figures below. Figure 16.4.1 – Connection figure NMEA Module 8 channels Page 115/ 191 Figure 16.4.2 – Connection figure NMEA Module 16 channels Figure 16.4.3 – Connection table NMEA Modules Page 116/ 191 16.5 Data communications The adaptor sends its data to the NW6410 Buscoupler for further processing and streaming onto the VDR network. In default ‘VDR mode’ in order to offload its data – the Buscoupler relies on the ethernet connection to the Core Module. 16.6 Indicators All adaptors have the number of ‘channel LEDs’ (CH1~24) corresponding with their size (8,16,24) and each row of 8 channels has a LINK led which indicates if that part of the adaptor has power and has established a data-link with the Buscoupler. 16.7 Errors If errors occur within the adaptor these will be indicated on the display of the Bridge Control Unit. 16.8 Configuration The baud-rate is auto-sensing, and the unit does not require any manual configuration (other than to set the recording channel name associated with the physical connection during the commissioning process). 16.9 Operating instructions After commissioning of the VDR system, this unit does not require (crew) operating instructions. 17. NW64308/16/24 Digital 8/16/24 channel adaptors 17.1 General ON level 5-24V DC, max. input current 1mA. The modules are available in 8,16 and 24 channel configurations within a harmonized configuration and wiring scheme. These adaptors send digital data they receive from their input ports onto the busbar ‘backplane’ for further processing by the Buscoupler which in its turn streams the data onto the (VDR) network. 17.2 Mounting These adaptors connect to the DIN busbar within the DAQ enclosure by mounting them from the top first and only in a vertical direction. Once the adaptor is attached to the DIN rail it should not be shifted in a horizontal direction (!) since this will render the feathering contacts between the adaptor and the DIN useless and the system will fail beyond repair. Page 117/ 191 17.3 Power Supply These adaptors receive their power (indirect PoE converted to 24V DC) via the DIN rail mounted NW6410 Buscoupler. Please note that for digital contacts additional 24 VDC will need to be supplied from either separate power supply or from 24 VDC output on the buscoupler. Page 118/ 191 17.4 Connections For physical connector and wiring identification please refer to the figures below. Figure 17.4.1 – Connection figure Digital Module 8 channels Page 119/ 191 Figure 17.4.2 – Connection figure Digital Module 16 channels Page 120/ 191 Figure 17.4.3 – Connection figure Digital Module 24 channels Page 121/ 191 Figure 17.4.5 – Connection figure Digital Modules 17.5 Data communications The adaptor sends its data to the NW6410 Buscoupler for further processing and streaming onto the VDR network. In default ‘VDR mode’ in order to offload its data - the Buscoupler relies on the ethernet connection to the Core Module. 17.6 Indicators All adaptors have the number of ‘channel LEDs’ (CH1~24) corresponding with their size (8,16,24) and each row of 8 channels has a LINK led which indicates if that part of the adaptor has power and has established a data-link with the Buscoupler. 17.7 Errors If errors occur within the adaptor these will be indicated on the display of the Bridge Display Unit. 17.8 Configuration The unit is auto-sensing, and the unit does not require any manual configuration for voltage or current (other than to set the recording channel name associated with the physical connection during the commissioning process). 17.9 Operating instructions After commissioning of the VDR system, this unit does not require (crew) operating instructions. Page 122/ 191 18. NW64404/08/12 Analogue 4/8/12 channel adaptors 18.1 General These adaptors provide input ports for analogue data with voltage levels between -10V to +10V and -20mA to +20mA current. Depending upon the port-wiring combination, a choice may be made for voltage measurement or current measurement. 18.2 Mounting These adaptors connect to the DIN busbar by mounting them from the top first and only in a vertical direction. Once the adaptor is attached to the DIN rail it should not be shifted in a horizontal direction (!) since this will render the feathering contacts between the adaptor and the DIN useless and the system will fail beyond repair. 18.3 Power Supply These adaptors receive their power (indirect PoE converted to 24V DC) via the DIN rail mounted NW6410 Buscoupler. Page 123/ 191 18.4 Connections Depending upon which connector entry is chosen, a choice is made between voltage and current measurement. For physical connector and wiring identification please refer to the figures below. Figure 18.4.1 – Connection figure Analogue Module 4 channels Page 124/ 191 Figure 18.4.2 – Connection figure Analogue Module 8 channels Page 125/ 191 Figure 18.4.3 – Connection figure Analogue Module 12 channels Page 126/ 191 Figure 18.4.4 – Connection table Analogue Modules 18.5 Data communications These adaptors send analogue data (-10V to +10V or -20mA to -20mA) they receive from their input ports onto the busbar ‘backplane’ for further processing by the Buscoupler which in its turn streams the data onto the (VDR) network. 18.6 Indicators All adaptors have the number of ‘channel LEDs’ (CH1~24) corresponding with their size (8,16,24) and each row of 8 channels has a LINK led which indicates if that part of the adaptor has power and has established a data-link with the Buscoupler. 18.7 Errors If errors occur within the adaptor these will be indicated on the display of the Bridge Display Unit. 18.8 Configuration The input is auto-sensing, and the unit does not require any manual configuration (other than to set the recording channel name associated with the physical connection during the commissioning process). 18.9 Operating instructions After commissioning of the VDR system, this unit does not require (crew) operating instructions. Page 127/ 191 19. Connecting to the VDR for configuration of the system In the event the VDR is available in a fully operational state - the method to connect to the VDR is as follows. 1. With an Ethernet cable, physically connect to the VDR (Core Module (CM); data port) with any PC (or laptop, notebook) with a Windows Operating System. 2. Change the IP address of the PC to be within the IP-range of the VDR and set it to 172.16.8.199. 3. Open a web-browser and go to the URL 172.16.8.2 or https://nw6000.orolia.local. 4. If necessary, download & install the Player & Conversion Software as well as the Manual for these from the VDR to the PC. The VDR Playback software can also be obtained from the Netwave Systems extranet. For login details, please check with Netwave Systems ([email protected]). 5. Run the Playback software and select the configuration TAB for configuring the system. 19.1 Physically connecting to the VDR The VDR’s Ethernet ports on the Core Module are auto-sensing and you should not have to change your Ethernet cable, however, if you encounter problems obtaining access to the VDR Core Module, check the following: a. The Ethernet cable between the PC (Laptop, notebook computer) and the CM should be a standard, readymade patch-type cable to overcome potential straight-thru vs. crossover Ethernet cabling issues. Change the cable if required. - A straight-thru cable has identical ends. A crossover cable has different ends. A straight-thru is used as a patch cord in Ethernet connections. A crossover is used to connect two Ethernet devices without a hub or for connecting two hubs. A crossover has one end with the Orange set of wires switched with the Green set. Odd numbered pins are always striped, even numbered pins are always solid colored. Looking at the RJ-45 with the clip facing away from you, Brown is always on the right, and pin 1 is on the left. No more than 1/2" of the Ethernet cable should be untwisted otherwise it will be susceptible to crosstalk. Page 128/ 191 19.2 Checking for connected sensor to the VDR Connect to the VDR and using a browser select the configuration TAB for configuring the system on https://nw6000.orolia.local. Before configuring the VDR, it is important to get an understanding and check of all connected sensors to the VDR. For this purpose, the VDR Web Server provides an NMEA Analyzing tool. Once connected to the VDR, below in the screen (red circle) you will immediately be indicated whether the core module is available on-line. Red is wrong, green is correct. Page 129/ 191 19.3 Change of type of the VDR There I no longer the ability to change the type of the VDR as in the older Player V1. The VDR is now configured via it’s web pages. 19.4 Configuring the VDR For configuring the VDR, use a laptop with specifications as described above. Connecting to the VDR enables access to its configuration files once the user has been authenticated using their username and password. Configuration of the VDR settings is available for authenticated users. Changes are committed to the VDR by saving them once they have been configured. Once saved the VDR will reboot and the newly saved configuration settings will be used. 19.4.1 On-line check of incoming data. Currently the NW600 provides the facility to show NMEA received data and Live Video for sources that have been configured. This requires that the user runs a “probe” and commits devices to the VDR using the Save function. After reboot the Live Video and NMEA Analyzer can be used to show incoming data… Page 130/ 191 19.4.2 Configuration page The NW6000 Configuration web page is used to configure the system. On navigating to ‘Configuration’ the certified service engineer will have the option to configure the VDR and to provide a correct representation of recorded data from all the storage media. Open the ‘Configuration’ option with password available to certified service engineer. The current configuration for the VDR is available when the Configuration page opens. Select ‘Probe’ to show currently installed devices. Select SCAN to scan all the hardware connected to the VDR and present the sensors on the left side of the opened window and merge with the existing configuration if required. The configurator will enable configuration of devices in the installed devices list. The configuration, including installed devices, will only take effect when saved to the VDR. Page 131/ 191 Configuration will start vessel particulars, to be filled. A. Vessel name, IMO and MMSI numbers must be filled. B. Start with the configuration of the VDR system. These are Video, Audio and NMEA sources. Page 132/ 191 C. Open a specified field (i.e. buscoupler) and rename the found hardware modules when desired In the menu structure on open the buscoupler and name the input of each connected NMEA input (max 3 configurable between 4800-38400Bd) as per tab. • Proceed in similar fashion for all related modules. Configuring AIM (Analogue Input Module) Insert the name of the connected signal. • Perform the same method for setting up the Digital Signals. • PN2xxx are used for the VHF module; insert desired names for the channels. • PN4xxx are used for the NW6030 Analogue Microphones connected to an NW6031 Audio Hub; please give a proper name in the fields which is giving an obvious name to the location. These names should be later mentioned as well in the final commissioning documentation. • After filling all fields, start with player configuration (top half of left menu (blue circle)). • In similar fashion, fill all required fields to make the Player V2 understand incoming signals. Page 133/ 191 Please pay attention to the configuration of the Global Navigation Satellite System (GNSS). During installation it is required that position of the antenna will be registered by location on the vessel in General Settings. In the additional notes field please add the required z – coordinate (measured from high water line). Additional VDR critical sensors are configured in Critical Settings… Further, the system can and will accept Glonass/GPS (“GN”) and Glonass (“GL”) receiver messages, to be filled at the Talker ID. Once all pages have been filled, save the configuration to the VDR. Page 134/ 191 19.4.3 Configuring the OPT Select the OPT Configuration button to configure Operational Performance Test for NMEA, Audio and Video sources. Add categories for groups of NMEA OPT items. Dragging or double clicking the NMEA sources will add that item to the currently selected category. OPT categories will become visible on the BCU once the OPT is performed (see example underneath). Once the system is completely configured then the OPT configuration will be saved with ‘save to VDR’. Page 135/ 191 19.4.4 Configuring the LWE video To configure the video channels via the LWE 450 protocol, please take the following steps. 1. Connect to the NW6000 Web pages at https://nw6000.orolia.local 2. Make sure all video channels are enabled and are sending data over the VDR network. 3. Press SCAN on the Configurator “Probe” page, the VDR will now search for all available video channels. 4. The video channels will become visible in the NEW DEVICES list based on the configured identifiers (i.e. EC0001 and RA0001). Add these to the INSTALLED DEVICES list. 5. Select the VIDEO SETTNGS page to see details on each video source that has been added or is already available.: 6. Based on the information from the device, the Description, location, source and timeout field will be preconfigured, please update to ensure a correct representation of the situation on board the vessel. Page 136/ 191 Recording Mode As it is not required to record all available image sources at the same time (only the source used for navigation), the NW6000 allows two methods for recording sources of the same type. 1. DEFAULT: Devices with the same type are recorded in round-robin. For two sources of ECDIS source 1 is recorded first and then source 2 when it arrives in the following time slot. Thus, every 30s both are recorded. 2. ALWAYS: In this case all sources regardless of type are always recorded. So, in the previous example both ECDIS images received in a time slot will be recorded. SAVE settings to the VDR using the Save page. Source type: this defines the type of image source that is transmitting the message. In line with the VDR performance standard, as a minimal requirement the VDR shall record ECDIS, SBAND and XBAND radar images. Configuration is only possible when the VDR is under maintenance, and the service engineer will have to login using the provided password during training and certification. Page 137/ 191 20. Creating a download from the VDR system Download of data from the NW6000 uses the same interface as used with configuring the system. This is a dedicated ethernet port on the CM switch. To perform a download requires installation of the Player software and configuration of the PC used for the download. 20.1 Download data set To download a data set from the NW6000, please set your PC to fixed IP address 172.16.8.199 using local area connection network. Fill the following IP addresses: IP address: 172.16.8.199 Submask: 255.255.0.0 Playback of voyage data now uses Player V2. This is a separate application and available via the NW6000 Web Interface. The manual for configuring the Player V2, and also, it is operation, is available within the Player V2. Downloading from fixed capsule or float free might require a long time. It is recommended to download from the long-term storage in the core module. Choose the required data set from long term storage medium in core module for download to your computer. Give it a recognizable name and place for easy retrieval for play back. Due to system design of data recording on float free capsule, during normal operation the downloading of most recent stored data on the capsule might lead to download interruptions as recording has priority over downloading. Repeat download might correct the required dataset. For incident retrieval this is not applicable as no data storage and downloading inference will occur. Page 138/ 191 21. Playback software 21.1 Obtaining the Playback software - The Playback software can be found on the USB-card enclosed to the hard copy version of this manual. Please note that the Playback software version on the USB-card may not be the most recent software version since a new version can be released as from the moment the manual and USB-card are sent out. In case another software version is required than provided on the USB-card, the 2 following options are left. - The Playback software can be downloaded from the VDR (software is present on Core Module). Connect your PC to the data-port of the Switch. Open an internet browser and type the following address ‘172.16.8.2’ (IP-address of Core Module). The Playback software can be downloaded on this page. - The playback software can be downloaded from www.oroliamaritime.com - login (only accessible for service engineers). Additional playback software, which may be downloaded from the Netwave website is available for use in shore-side offices. This additional software is necessary for the playback of data once it has been removed from the ship and transported to the office environment. The computer on which the Playback application is being installed must have its regional and language options adjusted to English. This may be done by double clicking the ‘Regional Options’ icon in the Control Panel window and selecting ‘English’ from the language drop down list. It is recommended that either ‘English (United States)’ or ‘English (Canada)’ is selected. However, any of the available English options are acceptable. 21.2 Installation of Playback software - Client/Standalone PC The installation of playback software is automated and requires little interaction. The install is performed via a self-extracting executable file and is automatically installed to the C:\Program Files\Netwave\VDR directory, with a shortcut placed on the Windows desktop. The install file will normally be named “Install VDR Playback.exe”. To begin the installation, complete the steps listed below. 1. 2. 3. Double click the file ‘Install VDR Playback.exe’. Choose the directory to which the executable will be installed. Perform the installation. Page 139/ 191 22. NW6000 Web page The VDR webpage can be accessed by using the http://nw6000.orolia.local on core modules with software version 1.5.17 or lower. Later versions require a certificate to be installed. The webpage is secured and therefore needs to be accessed with https://nw6000.orolia.local. 22.1 Dashboard The dashboard contains links for downloading the Playback software, Authority manual and the Orolia certificate used for HTTPS. Figure 22.1.1 – Dashboard page Page 140/ 191 22.2 Installing Orolia VDR Certificate After upgrading the core module from v1.5.17 or later, access the VDR with http://172.16.8.2 to download the “Installer Orolia Certificate”. Save the downloaded file “setup-orolia-certificate.zip” and uncompress the file with for example WinZip or 7Zip. Execute the file “setup-orolia-certificate.exe”. The following message can be shown by the Windows operating system. Click on “More info” and press the “Run anyway” button… Page 141/ 191 Then click the button “install” to proceed with the installation. Click the button “Finish” to end the installation. Access the VDR webpage with a browser by using https://nw6000.orolia.local/ Page 142/ 191 22.3 Live Video The Live Video webpage will display all configured video channels. This includes the video channels from a Video module (NW6044) as well as connected LWE video channels. See chapter 7.7 how to configure video channels. Figure 22.3.1 – Live video page, video channel Each configured video channel will be displayed on the Live video page. On top of the video image more information about the video source is available. Containing the following information. Description Source Location Active Device Channel Date time Description of the video channel. Set in the video playback software Name of the video source transmitted by the video source. The source information will be red when no image is available for recording. Location of the video channel. Set in the video playback software Indicates the status of the video channel. Transmitted by the video source Video device number. A device can contain multiple channels. The channel of the device. UTC time of the recorded image. Page 143/ 191 The video source information will be coloured in red when there is no recorded image or when the time between the connected computer and VDR is not synchronized. 22.4 Annual Performance Test Netwave Systems recommends performing an Annual Performance Test (APT) every 12 months referring to MSC.1/Circ.1222. The VDR page retrieves information from the VDR, that is required for the APT, and will be filled in automatically in the APT page. Additional information needs to be filled in by the APT performing certified engineer. Click on the button “Create APT report” to generate the APT in a pdf format. The pdf file will be stored on the VDR and needs to be send to [email protected] by the certified engineer when performing the APT. 22.5 Configurator The VDR configurator webpage contains VDR settings that can not be set by the Playback software. The configurator page also includes tools for configuration and troubleshooting. The following paragraphs describes each of the settings and tools. Page 144/ 191 22.5.1 LWE Settings Figure 22.5.1.1 – Configurator page, LWE settings X-Band When enabled will cause the VDR to record the LWE video sources transmitting X-Band images. In case there is also an X-Band source connected to a Video Module this setting can be switched off to disable the X-Band video recording from an LWE source. S-Band When enabled will cause the VDR to record the LWE video sources transmitting S-Band images. In case there is also an S-Band source connected to a Video Module this setting can be switched off to disable the S-Band video recording from an LWE source ECDIS When enabled will cause the VDR to record the LWE video sources transmitting ECDIS images. In case there is also an ECDIS source connected to a Video Module this setting can be switched off to disable the ECDIS video recording from an LWE source. Other When enabled will cause the VDR to record the LWE video sources from those other than the above-mentioned sources. Page 145/ 191 22.5.2 VLAN Settings The NW6000 VLAN implementation relies on a separate VLAN enabled switch which is connected to ETH1 on the VDR CPU. This requires a direct connection to this port in the core module. The VLAN-ID and associated network(s) are configured independently. NOTE: The VLAN switch on ETH1 needs to be configured independently. The ports used need to match the VLAN-ID associated with the networks in the VDR. The Network Config address control box uses CIDR notation to specify the network, the prefix and the IP address of the VDR on a VLAN e.g. 172.50.8.2/16 configures the VDR VLAN network as follows: 1) Network is 172.50.0.0 to 172.50.255.255 2) Network mask is 255.255.0.0 3) VDR IP address is 172.50.8.2 Figure 22.5.2.1 – Configurator page, VLAN settings Page 146/ 191 22.5.3 BAM Settings The VDR can be connected to a Bridge Alert Management (BAM) system if available. When enabled VDR alert messages will be transmitted to the BAM system. Full details of alert identifiers are available in the BAM Interface specification. Figure 22.5.3.1 – Configurator page, BAM settings BAM Enabled Slider Used to enable (as shown) or disable BAM. BAM Interface Used to enable the ports used for BAM transmission. Select “default” to transmit BAM messages via the ethernet network using LWE. Select “Serial” to transmit alert messages by using an output port on the BCU or Bus Coupler. Page 147/ 191 Figure 22.5.3.2 – Configurator page, BAM interface settings After setting the BAM Interface to serial the Fig.21.4.3. BAM dropdown list is shown. Select the desired output channel which is connected to the BAM system. The Bus Coupler and BCU ports can be used as inputs for NMEA signals or for BAM alert messages as output. Page 148/ 191 22.5.4 Advanced Settings Figure 22.5.4.1 – Advanced Settings Log Reboot This setting is used to control whether the NW6000 logs additional information when the platform reboots. This can be used to help track down problems if required and should be used in consultation with support. Scheduled restart This feature is used to restart the NW 6000 at periodic intervals. Once enabled the following options can be configured for the interval between restarts: 1) Weeks - 1-4. 2) Day - Saturday, Monday, ... 3) Hour - 1-24 Page 149/ 191 22.6 Analyze Tool The analyze tool scans real time incoming NMEA data sources and presents them in an easy to configure filterable list. This data can be used for configuring the playback software as well as trouble shooting connections. Figure 22.6.1 - Configurator page, Analyze tool The buttons in the left menu from top to down have the following functionality. Refresh Pause Stop Disable alerts clears the list and continues to scan. freezes updates to analyze table stops the analyzer timeouts for successive sentences are displayed in red. Figure 22.6.2 - Analyze tool, filter option Page 150/ 191 The filter option will show only data containing the text entered in the filter box. For example, typing “hdt” in the box will only show data containing the text “hdt”. Source M P Group T Fnc Sentence S Received Delay Device ID sending the data Module number Port number Group, hover over to receive additional information Talker Id Function Received sentence from source State of Sentence UTC time received message Time between last received message Figure 22.6.3 - Description list items 22.7 BAM Tool This BAM tool monitors, in real time, BAM alert messages and displays them in a list. The BAM Interface specification contains a list with ID’s and descriptions. Figure 22.7.1 – Configurator page, BAM Tool The buttons in the left menu from top to down have the following functionality. Refresh Stop Cat Prio State Man ID Ins Refresh Error clears BAM table. stops receiving BAM messages. Category of alert message. Hover over to receive additional information. Priority of the message. Acknowledge state Manufacturer mnemonic code Alert identifier. See Annex IV for the complete list Alert instance Time in seconds since last refresh Alert description Figure 22.7.2 – Description BAM list items Page 151/ 191 22.8 Rebooting the VDR The VDR will reboot automatically if the Save to VDR is accessed and the OK button is pressed. All configured settings will be stored to the VDR and will be used by the VDR after it reboots. Figure 22.8.1 – Configurator page, Save to VDR tool Once the installer has accessed the Configurator, using Authentication, the REBOOT button becomes available in the footer of all pages. Pressing the REBOOT button will reboot the VDR. All configuration that has not been saved to the VDR will be lost if REBOOT is used. After rebooting the VDR will use its previously stored settings. Page 152/ 191 23. BAM Interface Specification The following sections detail the BAM interface on the NW6000 in compliance with IEC 62923:2018. 23.1 Bridge Alert Management (BAM) BAM reporting is available as follows: Types Supported IEC 61162-1/2 IEC 61162-450 Maximum Number 1 1 BAM configuration is provided here in BAM Settings. 23.2 Manufacturer ID The Manufacturer ID for alert messages coming from the NW6000 is … Manufacturer ID = NWS 23.3 Supported NMEA Messages The NW6000 supports the following messages… f) ALF g) ALC h) ACN The heartbeat message, HBT, is sent by the NW6000 at intervals of 30s. Page 153/ 191 23.4 Alert Identifiers The description of the alert identifiers (ID) coming from the NW6000 are as follows: Alert ID 10002 10003 10004 10005 10006 10007 10008 10009 10010 10011 10012 10013 10014 10015 10016 10017 10018 10019 10020 10021 10022 10023 10024 10025 10026 10027 10028 Caption (max 16) NO TIME NO POSITION NO HEADING NO VIDEO NO NMEA NO ANALOG NO DIGITAL AUDIO ERROR BCU ERROR TRON40 ERROR HVR04 ERROR STORAGE ERROR FLOATFREE ERROR CONNECTION ERROR POWER FAILURE AUDIO TEST ERROR SWITCH ERROR SBAND ERROR XBAND ERROR ECDIS ERROR EXTERNAL STORAGE Description Time not received for 30s Position not received for 30s Heading not received for 30s VIDEO not received 'timeout' seconds NMEA not received for 'timeout' seconds No analog messages received for 30s No digital messages received for 30s Audio problem mic/vhf/michub Not in use Connection problem with BCU Connection problem Storage (Jotron) Connection problem HVR04 Problem mounting SSD on VDR Not in Use Not in Use Float Free storage alert Not in Use Configured Device never sent data after restart Power Failure (mains power gone) Microphone Test failed Error with switch (Not used now) No reception SBAND LWE video for 'timeout' seconds No reception XBAND LWE video for 'timeout' seconds No reception ECDIS LWE video for 'timeout' seconds Not in Use Not in Use Storage Failure on external (USB) storage Note: A second ALF message always accompanies the first message and contains additional channel information. Page 154/ 191 24. Frequently Asked Questions This section includes additional information which may help in diagnosing a problem(s). 24.1 Browser Shows Insecure Webpage 404 Not Found The latest update to the NW6000 internal web server includes secure web page access using https. This requires that there is a certificate installed on the machine that is being used to access the VDR web server and also requires the use of the NW6000 local hostname. This can cause some issues when using a browser to connect to VDR’s running v1.5.17 After upgrading a core module from version 1.5.17 to a higher version it is required to install an SSL certificate to be able to access the now secured -VDR webpages. When using the same computer, with the certificate installed, on an NW6000 VDR with core module version 1.5.17 the VDR page may be inaccessible resulting in the following error. Some browsers may automatically try to force to an SSL connection. To avoid this use http://nw6000.orolia.local An NW6000 VDR with a higher version than v1.5.17 can be accessed with https://nw6000.orolia.local/ - note the ‘s’ after http. Tip: Once this URL has been used to access the VDR, set it as a bookmark in your web browser for ease of use. Page 155/ 191 24.2 Browser Compatibility with VDR Web Server Browser Firefox Edge Chrome Access core module versions 1.5.17 and lower http://nw6000.orolia.local/ http://nw6000.orolia.local/ http://nw6000.orolia.local/ Browser Firefox Access core module versions v1.6.3 and higher Requires enabling the Windows certificate store. See below steps. Access with: https://nw6000.orolia.local/ https://nw6000.orolia.local/ https://nw6000.orolia.local/ Edge Chrome 24.2.1 Firefox Compatibility When using Firefox some additional steps are required to configure the browser for use with the NW6000. This requires enabling the NW6000 certificate in the Firefox certificates database. Enabling the Windows certificate store trust can be done following the below steps. Type about:config in the Firefox address bar. This will open a Firefox settings page. i) • In the search bar type “security. enterprise_roots.enabled”. Set the found setting to true. Page 156/ 191 24.3 What is the recording capacity of the VDR? Under IEC 61996-1 each of the recording mediums have the following recording requirements… Storage Area Long Term Recording Medium (LTRM) Fixed Recording Medium (FRM) Float Free Recording Medium (FFRM) Hours 720 48 48 Recordings include NMEA, Audio and Video data sources along with additional support files – config, log files etc. Each one is stored in a separately time stamped data file on all media. Older files are removed to make space for newer files. The storage space is always around 95% full as the system needs the additional 5% for managing files. For a system with the following configuration the amount of historic data that can be recorded is estimated as follows: NMEA 20x NMEA 4 x DIM 4 x AIM Sources Audio 6 x Mics 2 x VHF Video 4 x VGA 4 x VGA + 4 x LWE 450* 8 x LWE 450* 8 x LWE 450** Storage Time (h) LTRM FRM FFRM 2228 130 130 1729 101 101 2014 785 117 46 117 46 Note: 1. Audio and Video sources consume considerably more storage resources than NMEA. 2. Video recordings are typically stored every 15s from a source. Storage time is dependent on compression and picture format used by the source. The indicated number of hours in the previous table are indicative of measurements with image resolution as follows: a) VGA – 1696 x 1250 b) LWE 450* – 1920 x 1080 3. Video recordings with higher resolutions require additional storage space and could compromise the minimum storage requirements. For example: LWE 450** 3840 x 1080 with 90% compression indicated above. Although this satisfies the LTRM requirement it will not satisfy the FRM and FFRM requirement and will not be compliant with IEC 61996. The amount of time that has been stored, for each area compared to IEC61996 requirements, is available on the BCU status page. Page 157/ 191 Part 2: Operator and maintenance manual 1. Routine maintenance 1.1 Annual Performance Test 1.1.1 General Netwave Systems recommends performing an Annual Performance Test (APT) every 12 months referring to MSC.1/Circ.1222. The APT can only be performed by Netwave Systems certified agents. An overview of the global service network of Netwave Systems can be found on www.oroliamaritime.com under the tab ‘Service’. For assistance please contact our service department. Please note that an APT is valid/completed only when a Certificate of Compliance is issued. 1.1.2 Replacement/maintenance beacon and batteries Core Module The expiry date of the beacon and the reserve power source (4 batteries in the Core Module) will be checked during the APT but please note that these can expire in between the APT’s. Beacon The battery of the beacon needs to be replaced every 3 years. A beacon needs to be replaced every 6 years. Expiry date can be found on the label of the beacon or in the most recent APT checklist. Batteries Core Module The 4 batteries in the Core Module need to be replaced every 2 years after installation. Expiry date can be found on the ‘battery expiration date’ label (placed on the outside of the Core Module), on the expiry label of each battery or in the most recent APT checklist. 1.2 Operational Performance Test 1.2.1 General According to resolution MSC. 333(90) the Voyage Data Recorder needs to be able to perform a performance test at any time, e.g. annually or following repair or maintenance work to the VDR or any signal source providing data to the VDR. This test may be conducted using the Bridge Control Unit and should ensure that all the required individual data items are being recorded correctly. Netwave Systems highly recommends performing an Operational Performance Test (OPT) monthly. This test should be performed by using the Bridge Control Unit. The performance test will indicate the status of all connected sensors. To start the OPT, push ‘Menu’ on the opening screen. This screen provides the choice for the OPT. Page 158/ 191 2014/12/04 11:17:20 UTC # ALERTS: 0 STATUS RECORDING 40 of 42 channels 5593 / 720 Hours on Long Term Storage 204 / 48 Hours on Netwave Capsule 332 / 48 Hours on Free Float Capsule ALERTS MENU NIGHT 2014/12/04 11:17:25 UTC DIM DIM # ALERTS: 3 MENU RECORDING 40 of 42 channels 5593 / 720 Hours on Long Term Storage 204 / 48 Hours on Netwave Capsule 332 / 48 Hours on Free Float Capsule STATUS LOG SOFTW SCREEN OPT When touching the OPT button in MENU, the system will provide a choice of tests for the various devices. Choose the devices to be checked. Checking ‘ALL’ will list all connected devices. 2014/12/04 11:16:12 UTC SAVE & EXIT ALL # ALERTS: 0 AUDIO VIDEO OPT NMEA Page 159/ 191 1.2.2 AUDIO test For example, when choosing AUDIO, the screen will provide all connected audio sources. 2014/12/04 11:17:45 UTC # ALERTS: 3 AUDIO DOWN UP VHF 1 – PN2000.1 VHF 2 – PN2000.2 PN1014.1 – PN1014.1 PN1006.1 – PN1006.1 PN1002.1 – PN1002.1 PN1007.1 – PN1007.1 PN1008.1 – PN1008.1 BACK SELECT NIGHT By clicking on one of the microphone devices, the OPT will start a microphone test (beep in the microphone) and when passed, the MIC test will indicate ‘Passed ‘. Select each microphone accordingly. 2014/12/04 11:17:20 UTC PN1014.1 MIC Update time MIC Test BACK PASS # ALERTS: 0 DEVICE 2014/12/04 11:17:20 Passed FAILS PREV NEXT When the device passes the test, the ‘pass’ button should be pressed. Result will be logged as per required OPT logging. Page 160/ 191 Choosing the VHF will provide the VHF test screen. The audio level should be > 20 for ‘pass’. 2014/12/04 11:17:55 UTC VHF 1:2 VHF Update time Audio Level BACK # ALERTS: 3 Device 2014/12/04 11:17:52 45 PASS FAIL PREV NEXT After all audio devices have been checked, click ‘back’ and the system will get the operator in the main menu and i.e. video can be checked. 1.2.3 VIDEO test When choosing VIDEO on the OPT screen it will provide all connected video sources. 2014/12/04 11:18:15 UTC # ALERTS: 3 VIDEO RADAR X – TEST SCREEN 2 – TEST SCREEN 3 – TEST SCREEN 4 – TEST BACK SELECT NIGHT DOWN UP Select the line with the video source to be tested (i.e. Radar X). The display will start slowly to show the complete video screen. Page 161/ 191 It is required by clicking anywhere on the screen that the picture will zoom into the original display size. Clicking once again will provide the buttons. You can pan around the picture and ‘pass’ or ‘fail’ can be pressed. Outcome will be recorded in the logging. BACK PASS FAIL ZOOM PAN 1.2.4 NMEA test When choosing NMEA on the OPT screen it will provide all connected NMEA sources. 2014/12/04 11:18:45 UTC # ALERTS: 3 NMEA NAVIGATION ENGINE FIREDOORS BACK SELECT NIGHT DOWN UP Selecting one of the main categories will provide the following sensors: 2014/12/04 11:18:50 UTC # ALERTS: 3 NMEA GPS – DECK DEPTH – DECK SPEED – DECK AIS – DECK HEADING 1 – DECK HEADING 2 - DECK BACK SELECT NIGHT DOWN UP Page 162/ 191 Clicking on GPS, will provide the GPS data: 2014/12/04 11:18:52 UTC # ALERTS: 3 Device SI6002.4 GPS fix data (GGA) Update time 2014/12/04 11:18:52 Time 11:18:52 Lat 00°00'58" S Lon 015°00'58" W BACK SELECT NIGHT PREV NEXT When the operator decides that the presented data is correct, press ‘pass’ otherwise press ‘fail’ and arrange for check / service on the system for correction. The results of the tests will be logged into the Voyage Data Recorder and can be downloaded using the player wizard. 1.2.5 OPT log The VDR will log the last 10 Operational Performance Tests which are carried out on the system. These logs will be stored on all 3 storage media and can be checked by using the Playback software (see chapter ‘Playback Software’ - ‘Logging functions’ (Operation and maintenance manual) and check the OPT log-tab). 1.2.6 Errors In case there are difficulties and assistance is required, please download the data set as described in the chapter ‘Download data set from the VDR system’ (Operator and maintenance manual) and send the dataset to [email protected] so Netwave Systems can assist in fault findings. Page 163/ 191 1.3 TRON 40VDR Float Free Capsule 1.3.1 General The information about the TRON 40VDR provided in this chapter is based on the ‘User Manual’ of Jotron. For full information about the TRON 40VDR Netwave Systems refers to the User Manual of Jotron. This user manual: - is hardcopy enclosed to the delivery box of the TRON 40VDR. is available on the USB-card enclosed to this hardcopy Netwave manual. or can be found on the internet site of Jotron. The TRON 40VDR Float Free Capsule is under the regulation according to SOLAS Chap.IV reg.15.9.2 and IMO MSC.Circ 1039 guideline. The TRON 40VDR Float Free Capsule is compliant to this guideline. Although the TRON 40VDR is part of the APT/shore-based maintenance (GMDSS, see 1.3.6), Jotron recommends to test/inspect the TRON 40VDR monthly. There are three kinds of tests/inspections which should be performed. 1. Normal self test 2. Extended self-test including the GPS 3. Visual inspection 1.3.2 Normal self-test What the normal self-test does is send out a short test signal on 121,5 and 406,037MHz, testing the output of the transmitter. While transmitting the test signal, the battery voltage, output power and phase lock is tested. During the test of the 406MHz transmitter a test message is transmitted, this test message is coded with a special synchronization code and will not be recognized as real alert by the Cospas-Sarsat satellites. To perform the self-test, the EPIRB must be removed from the FB-40 bracket. 1. Release FB-40 top cover by removing the cotter pin. 2. Take TRON 40VDR out of the bracket. 3. Push and hold switch in TEST position for 15 seconds. Keep hands and other objects away from the antenna. 4. Test passed after one single flash only. 5. Release the switch and put the EPIRB back into the bracket. 1.3.3 Extended self-test including GPS-test To perform the extended self-test, the EPIRB must be removed from the FB-40 bracket. Note 1: The GPS test might take up to 2 minutes to be successful. Limit this test to max. once per month as this test will reduce the lifetime of the EPIRB battery. Note 2: This test includes the normal self-test and therefore only one of them are necessary. Note 3: The extended self-test is imitated to 60 for a period of 5 years. Page 164/ 191 1. Release FB-40 top cover by removing the cotter pin. 2. Take TRON 40VDR out of the bracket. 3. Move Switch to TEST-position twice within 3 seconds and release back to READY-position. 4. EPIRB will BEEP shortly every 3 seconds until GPS position acquired. 5. OK = 2 BEEPS. 6. Normal SELF TEST is performed after successful GPS TEST and position transmitted on 406.037 MHz. GPS position may also be received on an EPIRB Tester for verification. 1.3.4 Errors If the self-test detects a fault in the EPIRB module, one or more of the following indications are shown: # Flashes 1 2 3 4 5 6 7 Fault indication NONE Low power on 406 MHz transmitter Low battery voltage Low power on 121.5 MHz transmitter PLL on 406 MHz transmitter out of lock PLL on 121.5 MHz transmitter out of lock EPIRB module not programmed or programming not complete GPS-test error messages: a) 5 beeps: did not acquire GPS position b) 10 beeps: number of GPS TEST above limit (>60) 1.3.5 Visual inspection The TRON 40VDR should be easily removed and replaced in the Bracket. Check for defects on the EPIRB or brackets. Make sure that the TRON 40VDR and Bracket are not painted or covered with chemicals, oil, etc. Is the lanyard firmly attached to the TRON 40VDR (and not tied to the vessel)? Check the expiry dates on: ✓ EPIRB Battery ✓ Hydrostatic Release Unit (HRU) Page 165/ 191 1.3.6 Replacement/maintenance HRU, EPIRB Module/Battery pack, TRON 40VDR (capsule and bracket) The expiry date of the Hydrostatic Release Unit (HRU), EPIRB Module/Battery pack, TRON 40VDR (capsule and bracket) will be checked during the APT but please note that these can expire in between the APT’s. Hydrostatic Release Unit The HRU including Plastic Bolt needs to be replaced every 2 years. The expiry date can be found on the label of the HRU or in the most recent APT checklist. Replacement instructions can be found in the user manual of Jotron. This user manual is enclosed to the delivery box or can be found on the internet site of Jotron. EPIRB Module/Battery pack If the EPIRB is fitted on a vessel which requires GMDSS compliant equipment, the EPIRB shall be serviced, tested and approved (as required by SOLAS regulation IV/15.9.2 of SOLAS 1974 as amended with, in accordance with MSC/Circ.1039 guidelines for shorebased maintenance of Satellite EPIRBs) within 5 years, or by the date of battery expiry, whichever comes first. The expiry date can be found on the label of the EPIRB or in the most recent APT checklist. The TRON 40VDR battery must be changed at a Jotron SBM authorized workshop to be GMDSS compliant. If your TRON 40VDR is not under any international or national regulations, battery can be change by authorized Jotron representatives/partners/dealers. TRON 40VDR Float-Free Capsule/Bracket Jotron recommends replacing both the TRON 40VDR Float-Free Capsule and Bracket every 10th year. Page 166/ 191 2. NW6010 Bridge Control Unit 2.1 General The Bridge Control Unit (BCU) serves both as an interface for serial/NMEA data as well to display the operational status and provide user functionality like, but not limited to, operational performance tests. 2.2 Location and mounting The BCU may be mounted in a protected environment at any convenient location taking into account the compass safe distance as indicated on the unit. 2.3 Indicators The BCU has 1 LED at the back to indicate that the power supplied to it is present, in other words, at least a PoE link is established to the core module. In the event the LED is illuminated (steady, green), the video display on the unit must work. Furthermore, each network-port provides Link and Activity LEDs on the backside of the unit with following meaning. Link speed (Green LED); the LED is on when there is a link connection, otherwise, the LED is off. Activity (Yellow LED); the LED is flashing when there is activity on the link; otherwise, the LED is off. 2.4 Errors Error indication: in the event the LED on the back side of the unit is On, the display is illuminated and showing text (buttons), but no valid (UTC) time is presented on the display, the data-link to the core module is not functional at that time. All other errors are presented on the display. The BCU provides an Auxiliary ALERT relay of which the (dry) contact rating is 28V dc, 200mA max. During a correct functioning of the VDR, the relay contacts are in the NO position. When an ALERT condition occurs or the VDR loses its power, the NC position is valid. (NC=normally closed, CO=COMMON contact, NO=normally open). 2.5 Operating instructions The BCU is equipped with a touch screen display with day and night display mode. Page 167/ 191 2.6 Screen description The BCU will be used for control and monitoring of the Voyage Data Recorder. The opening screen will show number of channels being recorded, number of alerts applicable date and time (UTC) and recorded time of data. Recorded time will be determined by calculating the time between the first and last file registered in the storage medium. Alerts > Up > Down Menu Night/Day DIM Display specific alerts (if any) of the VDR Scroll down on the alert list Scroll down on the alert list Go back to previous screen Toggle between day to night display Backlight intensity of the display 2014/12/04 11:17:25 UTC # ALERTS: 3 STATUS RECORDING 42 of 42 channels 5593 / 720 Hours on Long Term Storage 204 / 48 Hours on Netwave Capsule 332 / 48 Hours on Free Float Capsule ALERTS MENU NIGHT DIM DIM By touching the ALERT button, screen will change from status to alert position and indicate all alerts applicable for the moment, with latest alert on top. 2014/12/04 11:17:25 UTC # ALERTS: 3 ALERTS (12h) NO AUDIO FROM PN1002.1 (12h) AUDIO TEST Failed on PN1001 (22h) NO DATA: SI6000.4.4 STATUS MENU NIGHT DOWN UP Page 168/ 191 2.7 Alert conditions indicated on BCU Any recording errors, being it data integrity, loss of sensor information or other circumstance as represented in the VDR Performance Standard will lead to an ALERT condition which stays active and displayed on the BCU. In case the ALERT is resolved, the text line will disappear. Following indications can appear on the BCU. (Between brackets time that ALERT is active) followed by ALERT indication: 2.7.1 Power Failure A) ‘Power failure (230 V gone)’ B) ‘Power failure: recording stopped’ Mains power (230 Vac) is lost. When main power was lost for more than 2 hours By regulation/design the recording will be stopped. Any power source which has been available at system start-up and which is disconnected (or lost its power) thereafter will generate a Power Failure ALERT. If the primary power source is lost, the battery-backup mechanism will secure continued operation of the VDR. In battery-backup mode, the VDR will continue to operate for 2 hours, after which time the VDR will switch off until normal power is restored. 2.7.2 Recording Channels NMEA A) B) C) D) ‘No data: … ‘ ‘No time on: ... ‘ ‘No position on: ...’ ‘No heading on: … ‘ NMEA data is not received on the NMEA channel No time received on configured NMEA channel No position received on configured NMEA channel No heading received on configured NMEA channel If any of the designated channels loses its signal an ALERT will be presented, including the source (channel name) of that signal. Designated Channels are those which have been set to active during commissioning and therefore have to be recorded. 2.7.3 Recording channels audio A) ‘No audio from: … ‘ B) ‘Audio test failed on …’ No audio from specific microphone or VHF Interface. Audio test failed on specific microphone. 2.7.4 Recording channels video data A) ‘Video connection problem’ B) ‘No image from: … ‘ No connection to the video device. No image received from specific video port. In the event of absence or malfunction of the video adaptor or the radar video signal, an ALERT is generated. Page 169/ 191 2.7.5 Storage A) Connection problem capsule’ No connection to the Netwave capsule B) Connection problem (type) capsule’ If other then Netwave capsule is connected. C) ‘Float free not accessible’ No connection to Float free capsule. In the event the system is either unable to read from data recently written into any of the Final Recording Media, a data volume becomes unavailable, or any data volume has an overflow, an ALERT will be generated. 2.7.6 Switch A) ‘Switch: problem with port ... ‘ Indicated port on switch has malfunction. 2.7.7 Hardware malfunction A) ‘Not active … ‘ Specified hardware not functioning. 2.8 Operating screens By pressing the MENU button, the operator will be guided through a number of additional information displays. 2014/12/04 11:17:25 UTC # ALERTS: 3 MENU RECORDING 42 of 42 channels 5593 / 720 Hours on Long Term Storage 204 / 48 Hours on Netwave Capsule 332 / 48 Hours on Free Float Capsule STATUS LOG SOFTW SCREEN OPT Page 170/ 191 2.9 Alert logging STATUS information will provide access to a logging screen which provides a list of last 25 logged events. Using PREV and NEXT the user will be led forward or aft through the menu. 2014/12/04 11:17:25 UTC # ALERTS: 3 LOG CONNECTION PROBLEM CAPSULE (2) 14/12/03 10:43:16 till 14/12/03 10:43:18 STATUS 2.10 PREV NEXT DOWN UP Software version recognition By choosing in the MENU display, the SOFTW button will provide all relevant software versions. 2014/12/04 11:17:40 UTC # ALERTS: 3 SOFTW DOWN UP BCP – SI6000 – v 0.6.0 BCU – PN5000 – v 0.4.17 CAP – PN7000 – v 0.4.3 MIC – PN1006 – v 0.9.4 MIC – PN1014 – v 0.9.4 MIC – PN1001 – v 0.9.1 MIC – PN1003 – v 0.9.4 ALERTS STATUS NIGHT Page 171/ 191 2.11 Screen test The Bridge Control Unit has screen test included. By choosing in the MENU display, the SCREEN button, the display will provide a rectangular black in white figure. This will test the correct brilliance. Page 172/ 191 3 NW6880 TRON 40VDR FRM Float Free Capsule 3.1 General According to the IEC61996-1:2013 (MSC.333 (90)/5.4.3) recording of the VDR data shall also take place on an approved free-floating Final Recording Medium for a period of not less than 48 hours. The unit to be installed in conjunction with this VDR is the Jotron TRON 40VDR which basically comprised of an EPIRB with internal memory to the VDR. 3.2 Led indication Below is a description of the LED lights on the Docking Module (83180 MKII). Page 173/ 191 4 NW6860 Fixed HSS Capsule 4.1 General The hardened storage server (HSS) forms the Fixed Final Recording Medium and is colored bright orange for ease of location in the event of an incident. The HSS is designed to be mounted on the ´monkey island´ - and is fitted with an acoustic beacon to aid underwater recovery by a Remotely Operated Vehicle (ROV) or diver in the event of an incident. The unit is designed to withstand the extreme shock, impact, pressure and heat exposure requirements of the IEC Performance standards which mirror those enforced by the maritime and aerospace authorities. The HSS has the capacity to store audio, radar video and other data for a rolling 48-hour (minimum) period as defined in the regulations. All power and data are passed to the HSS via one single Ethernet cable. Connection is via a waterproof connector. The HSS has a release mechanism to facilitate underwater recovery both by a diver or a ROV. Suitable handles are provided to ensure that the capsule may be retrieved safely after release. The HSS has an externally mounted underwater location beacon (ULB) with an activation sensor to avoid inadvertent activation due to spray/rain/hosing off. The HSS (memory module) protective capsule is painted a highly visible fluorescent orange with the required text: VOYAGE DATA RECORDER, DO NOT OPEN and REPORT TO AUTHORITIES. When the HSS has been damaged after an incident, e.g. the HSS was exposed to fire or the ship has sunk, it may be returned to the manufacturer for the data to be extracted. Alternatively, authorities may apply for instructions on how to extract the recorded data. 4.2 Indicators When in unassembled state (and viewed form the bottom of the capsule part) a blue LED is available to determine Link, Activity, and Error status during service. 4.3 Errors If errors occur these will be indicated on the display of the Bridge Display Unit. Page 174/ 191 5 Playback software 5.1 Setting up the PC To download a data set from the NW6000, please set your PC to fixed IP address 172.16.8.199 using local area connection network. Fill the following IP addresses: IP address: Submask: 172.16.8.199 255.255.0.0 Page 175/ 191 5.2 Obtaining the Playback software The Playback software can be found on the USB-card enclosed to the hard copy version of this manual. Please note that the Playback software version on the USB-card may not be the most recent software version since a new version can be released as from the moment the manual and USB-card are sent out. In case another software version is required than provided on the USB-card, the 2 following options are left. - The Playback software can be downloaded from the VDR (software is present on Core Module). Connect your PC to the data-port of the Switch. Open an internet browser and type the following address ‘172.16.8.2’ (IP-address of Core Module). The Playback software can be downloaded on this page. - The playback software can be downloaded from www.oroliamaritime.com - login (only accessible for service engineers). Additional playback software, which may be downloaded from the Netwave website is available for use in shore-side offices. This additional software is necessary for the playback of data once it has been removed from the ship and transported to the office environment. The computer on which the Playback application is being installed must have its regional and language options adjusted to English. This may be done by double clicking the ‘Regional Options’ icon in the Control Panel window and selecting ‘English’ from the language drop down list. It is recommended that either ‘English (United States)’ or ‘English (Canada)’ is selected. However, any of the available English options are acceptable. Page 176/ 191 5.3 Installation of Playback Software – Client/Standalone PC The Playback software can be installed as a standalone application on a laptop or PC. No licensing is required. Before the Player can be used, the application needs to be installed as described in following steps. 1. Copy or download file on your laptop or replay device in a folder like in the following screenshot. 2. Double click the “NetwavePlayerV2_xxx_setup.exe’’ (xxx = number of software release). 3. The installer will automatically install the Player, follow the instructions on the screen. Note: Most likely your windows safety software will warn you about the publisher of this software because Orolia NetWave is not an official Microsoft product manufacturer. Page 177/ 191 5.4 Starting the Playback Application The player can be started by pressing the Desktop icon for the player placed during installation. Once the player has started the Start App screen is displayed. This is used to launch player sessions. Click on Start App to start a playback session. The session can be used to playback a previously stored dataset or alternatively to download a dataset from a storage device which subsequently can be played back using the player. Tip: The player will start the app by opening a previous dataset if it still exists. With larger datasets this can take some time opening before the player is ready to start a session. This can be disabled by holding the left CTRL key when clicking the START APP button. In this case the user will have to either do a download or manually select a dataset to start a session. Page 178/ 191 5.5 Configuration File The vessel information displayed in the playback application is automatically configured via the ship’s configuration file. This file is created by the installation technician during the installation of the VDR and is stored within each of the three final recording media (LTRM, FRM and FFRM). Upon start-up of the Playback application, the last stored configuration file, applicable for the downloaded dataset, will automatically be loaded. Although the Playback can be modified to display specific items in the case of an incident the underlying data files and configuration history remains intact. With the NW6000, the ship’s configuration file is included in a dataset. When a dataset is selected the configuration file will be automatically reloaded as necessary. Page 179/ 191 5.6 Downloading a Dataset from Recording Medium After pressing the START APP button, oo download a dataset from one of the final recording mediums (FRM, FFRM or LTRM) select the DOWNLOAD button. Select a storage device to download from using the dropdown menu. The IP address of the VDR will be shown in the box under the stroage device selection. This is for reference only and cannot be modified. Once the CONNECT TO STORAGE DEVICE is pressed the Player will search for the previously selected storage device on the VDR network. Then the Player will present the time selection for the dataset to be downloaded. NOTE: The player will automatically position the download time to be the last 5 mins of data from the storage medium. As shown above there are several items that can be used to control the dataset time selection: 1) The control is used to select the date. Click on this to set a different date e.g. 2) The START TIME is used to set the hours and minutes to start downloading from. 3) The TOTAL RECORDING TIME is the time duration of the dataset that will be downloaded. Page 180/ 191 Tips: 1) The mouse scroll wheel or touchpad can also be used to change items in the selection boxes. 2) When selecting a date or time that results in a time that has not recording data to retrieve the relevant numbers will be changed and flashed red to either the start or end of the recording time. 3) Downloading a datset can be time consuming. Once the dataset has been downloaded the Player will then parse the data before playing back. This is a once off operation for a dataset download. Subequently the dataset can be played back when opened manually without this delay. All parsed data is stored in a folder ’.cache’ in the folder selected to download the dataset to. Choose the required dataset from long term storage medium in Core Module for download to your computer. Give it a recognizable name and place for easy retrieval for play back. Due to system design of data recording on float free capsule, during normal operation the downloading of most recent stored data on the capsule might lead to download interruptions as recording has priority over downloading. Repeat download might correct the required dataset. For incident retrieval this is not applicable as no data storage and downloading interference will occur. Downloading from fixed capsule or float free might require a long time. It is recommended to download from the long-term storage in the Core Module. Page 181/ 191 5.7 Choosing an existing dataset Once the playback software has been started (see Starting The Playback Application) then use following steps to import the dataset and to start a playback session from an existing folder. a. Select the MANUALLY import dataset button Note: Dataset needs to be available on the computer. b. Select the dataset to be imported and follow the instructions. Note: Opening the dataset can take some time depending on the size of the dataset. When dataset is loaded, the system will indicate that dataset is loaded (d). c. The system will indicate the ships IMO number in the SHIP CONFIGURATION field once the dataset has been loaded. Note: If the IMO is blank the Start Session button will be hidden and the playback cannot be made. Page 182/ 191 5.8 Starting data playback Once the dataset has been loaded, either manually or via a download from an existing final recording medium, the player can then start to perform a playback of the voyage data from the dataset. When a dataset has been imported into the Player the screen will contain something similar to the view on the right. Further details on this view is available in the Player V2 operator manual. To start playing back either a downlaoded or an existing dataset press the START SESSION button. This launches the playback but first a user code is required. For replay only, the default pasword is: ocean . When logged in with this password only replay is possible. Export of data and configuration file is possible as well as selecting pages. Once successfully logged in a window like that on the following page should appear. The playback application interprets information provided in the ship’s player-config.json.xxx and cm.config.xxx files. Therefore, the playback interface may contain elements and controls different from what appears below. An administrator password is required for configuring the Player. The password will be provided on request by our Service Department. Page 183/ 191 Figure 5.8.1 Sample dataset playback Page 184/ 191 5.9 Conversion of extracted data Once a dataset has been opened by the playback software it can be exported and converted to industry standard files. These converted files are from the downloaded dataset itself and can be moved to another medium for other use. To export data from the Player please select page ‘options’ and press the Export Converted Dataset button. When choosing Export Converted Dataset, the player wizard will automatically start to convert the data in the dataset to industrial standard: • • • Video into .bmp files Audio into .wav files NMEA into .txt files The converter will create a convert directory in the same directory as where the dataset is stored. Page 185/ 191 5.10 Logging functions The Voyage Data Recorder creates error and OPT logging and stores these on all 3 storage media. To get access to these logs, please check the error and/or OPT log tabs as presented in the player. The logs will be visible when a download is made from one of the storage media. Download from long term storage: Will provide all last 10 OPT’s and complete error log. Download from float free and/or fixed capsule. 7. Playback software details 7.1 Passwords There are 2 passwords required to playback data. The first password is necessary to playback a selected data set. The default password is “ocean” (case sensitive). It is supplied with the software. The second password is for configuration. This password is only available for Netwave certified service agents (provided during training). 7.2 Playback Controls Please refer to Player V2 operator manual for further information on using the Player V2. Page 186/ 191 8. Annex I; equipment decommissioning 8.1 RMRS Rules for equipment decommissioning Following actions to be taken into consideration by the owner according to the paragraph 219 of the “Technical Regulations on the Safety of Sea Transport Items”: The safety of decommissioned sea transport infrastructure item shall be ensured by the owner of such item or operating organization. During this period, it is necessary to perform regular monitoring of safety condition of the decommissioned sea transport infrastructure item which has been: 1. Standard Netwave Systems warranty conditions consists of warranty on the equipment which is valid for a period not exceeding 12 months after commissioning of the item or 18 months after delivery, whichever comes first. 2. If equipment (within or without a vessel utilization) has to be utilized: a. it should be done according to Netwave Systems recommendations, mentioned under item 3 below. b. the company utilizing ships (ship equipment) shall develop an appropriate utilization documentation for each ship (ship equipment) where technological process modes, scope and sequence of utilization stages are specified (ref. to paragraph 160 of the “Technical Regulations on the Safety of Sea Transport Items”). 3. Netwave Systems recommendations for utilization of VDR components according to “Interim provisions for the application of the Technical Regulations on the Safety on Sea Transport items in the RS activity”: a. Survey of materials and products prior to recycling must be carried out in conformity with requirements set in paragraphs 158 and 160 of “Technical Regulations”. Report by the established form 6.3.79RF has to be issued and documentation on recycling has to be approved by the bodies authorized for approval of documentation on recycling in conformity with the legislation specified in subparagraph “a” of the paragraph 160 of the “Technical Regulations”. b. All VDR components (NW6000 PSU, batteries, switch and CPU), optional Interface Boxes, microphones, should be switched off and disconnected from their power sources. c. All VDR components (NW6000 PSU, batteries, switch and CPU), optional Interface Boxes, microphones, should be disconnected from (Navigational) sensors and all other sources. It is recommended to protect wires and keep them for any future upgrade or installation of the 3rd party VDR, if ship is provided for utilization. d. All VDR components (NW6000 PSU, batteries, switch and CPU), optional Interface Boxes, microphones should be packed into standard cartons for transportation to the utilization company. Page 187/ 191 e. Utilization Company considers itself – How to utilize autopilot components according to Russian Federation rules for utilization of such components and paragraph 219 of the “Technical Regulations on the Safety of Sea Transport Items”. VDR PCB controllers can be easily dismounted form the metallic boxes and utilized separately, as electronic equipment! Page 188/ 191 9. Annex II; energy saving “Technical Regulations on the Safety of Sea Transport Items”, approved by the RF Government Order No.620 of 12 August 2010, declared following in the Paragraph 6: “Designers, builders and manufacturers of sea transport and infrastructure items shall ensure the energy efficiency of such items.” 9.1 VDR PCB controllers VDR PCB controllers are powered from 110/230 Vac vessel main power supply and internal power circuit provides excessive voltage protection (suppressor and fuses) and reverse polarity protection. VDR PCB controllers were developed in accordance with following Netwave Systems implementations: - Stability during VDR operation. Quality of selected components (brand name components). The “internal power supply circuit” module on PCB provides: o Fused protection. o Galvanic isolation by DC-DC conversion of the input 24VDC voltage into necessary values, and its stabilization on PCB. 9.2 Power consumption calculation NOTE: Below mentioned calculation is given with a three times extra power consumption, especially for APP PCB controllers. Reason of that: to calculate and select a proper power supply with some extra resources and possibility to add any optional components in the future VDR usage - like additional microphones and interfaces. Calculation of the Power consumption (Example): 1. 2. 3. 4. 5. 6. NW6000 core module incl charger: Power consumption ~0,3А x 230 Vac = 50W Microphone: Power consumption per each: ~0.08А x 24Vdc = ~2W VHF interface: Power consumption 1,5A x 24 Vdc = 4W Interface coupler module: Power consumption 0,08A x 24 Vdc = ~ 2W 8 channel Interface modules: Power consumption per each: ~ 0.08A x 24 Vdc = ~2 W Storage media (float free and hardened capsule) 12 W Calculation of the Power Consumption per NW6000 system: P = NW6000 core module + (2W x Number of microphones + VHF interface) + (2W x number of interface modules (8 channels) + 4W coupler) + storage media. Recommended Power Supply for the aforementioned example: 220 Vac, 120W (minimum) Taking power loss in cabling at approx. 10W. Page 189/ 191 10. Annex III; equipment labelling RMRS “Technical Regulations on the Safety of Sea Transport Items”, approved by the RF Government Order No. 620 of 12 August 2010, declared following: “Technical regulation items whose conformity with the Technical Regulations is confirmed shall have a conformity mark, as prescribed by the Russian Federation legislation on technical regulation.” Following components of NW6000 VDR System are labelled according to the Russian Federation Government Order “On Conformity Mark” No. 696 of 19 November 2003 and Section 20 of the “Technical Regulations on the Safety of Sea Transport Items” mentioned above: Core Module (/Bulkhead): Page 190/ 191 FRM Capsule: Current software versions on VDR indicated on the BCU (see chapter Software version recognition): 2014/12/04 11:17:40 UTC # ALERTS: 3 SOFTW DOWN UP BCP – SI6000 – v 0.6.0 BCU – PN5000 – v 0.4.17 CAP – PN7000 – v 0.4.3 MIC – PN1006 – v 0.9.4 MIC – PN1014 – v 0.9.4 MIC – PN1001 – v 0.9.1 MIC – PN1003 – v 0.9.4 ALERTS STATUS NIGHT Page 191/ 191
advertisement
Key Features
- High-quality audio capture
- Seamless VDR integration
- Reliable performance
- Durable construction
- Easy installation
Related manuals
Frequently Answers and Questions
How is the NW6030 connected to the VDR system?
The NW6030 is connected to the NetWave NW6010 Bridge Control Unit, which in turn interfaces with the VDR core module. This ensures that all audio data is recorded and managed by the VDR system.
What kind of audio signals does the NW6030 support?
The NW6030 supports analogue audio signals, making it compatible with a wide range of existing communication equipment.
What are the mounting options for the NW6030?
The NW6030 can be mounted in various locations on the vessel, ensuring flexibility and optimal audio capture.