- Home
- Domestic appliances
- Climate control
- Temperature & humidity sensors
- Hirschmann
- PROFINET Digital-I/O
- Manual
advertisement
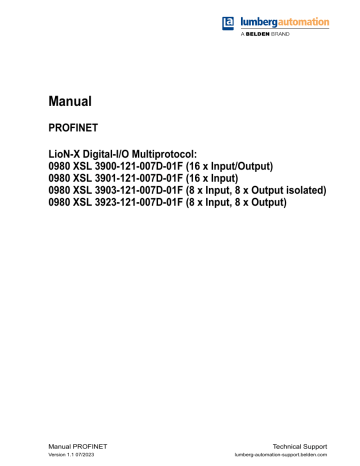
Manual
PROFINET
LioN-X Digital-I/O Multiprotocol:
0980 XSL 3900-121-007D-01F (16 x Input/Output)
0980 XSL 3901-121-007D-01F (16 x Input)
0980 XSL 3903-121-007D-01F (8 x Input, 8 x Output isolated)
0980 XSL 3923-121-007D-01F (8 x Input, 8 x Output)
Manual PROFINET
Version 1.1 07/2023
Technical Support lumberg-automation-support.belden.com
Contents
Contents
1 About this manual
1.2.1 Use of danger information
1.2.2 Use of general information
2 Safety instructions
3 Designations and synonyms
4 System description
5 Overview of product features
ii
13
16
22
11
9
Manual PROFINET
Version 1.1 07/2023
Contents
6 Assembly and wiring
6.2.1 LioN-X Digital-I/O multiprotocol variants
6.3.1 Ethernet ports, M12 socket, 4-pin, D-coded
6.3.2 Power supply with M12 power L-coded
6.3.3 I/O ports as M12 sockets
7 Starting operation
7.4 Setting the rotary encoding switches
8 Configuration and operation with SIEMENS
TIA Portal
8.1 Assigning a device name and IP address
8.2.1 Deleting the I/O configuration
8.2.2 Changing the I/O configuration
8.3 Parameterization of the Status/Control Module
44
38
28
Manual PROFINET
Version 1.1 07/2023 iii
8.3.3 DO Surveillance Timeout (ms)
8.3.5 DO Restart Mode after Failure
8.4 Media Redundancy Protocol (MRP)
8.5 Identification & maintenance (I&M)
8.5.1.1 I&M data of the PN-IO Device
8.5.2 Reading and writing I&M data
8.6 Fast Start Up (FSU) / Prioritized Startup
9 Process data assignment
9.1 0980 XSL 3900-121-007D-01F
iv
Contents
74
Manual PROFINET
Version 1.1 07/2023
Contents
9.2 0980 XSL 3901-121-007D-01F
9.3 0980 XSL 3903-121-007D-01F
9.4 0980 XSL 3923-121-007D-01F
9.8 PROFINET channel diagnostics mapping
10 Diagnostics
10.1 Detailed diagnostics description
10.1.1 Error of the system/sensor power supply U
Manual PROFINET
Version 1.1 07/2023
87
v
Contents
10.1.2 Error of the actuator power supply U
10.1.3 Overload/short-circuit of the I/O port sensor supply outputs 89
10.1.4 Overload/short circuit of the I/O port Ch. A as actuator outputs
10.1.5 Overload/short circuit of the I/O port Ch. B as actuator outputs
10.1.6 Generic parameter error
10.1.7 I/O mapping parameter error
10.2 Table of PROFINET diagnostic codes 94
11 IIoT functionality
11.1.2.3 Command topic (MQTT Subscribe)
11.1.3 MQTT configuration - Quick start guide
11.1.3.1 MQTT configuration via JSON
11.2.3 OPC UA configuration - Quick start guide
11.2.3.1 OPC UA configuration via JSON
11.3.1 Standard device information
11.3.3 Configuration and forcing
95
vi Manual PROFINET
Version 1.1 07/2023
Contents
11.4.2 REST API access via CoAP
11.4.3 CoAP configuration - Quick start guide
11.4.3.1 CoAP configuration via JSON
11.5.2 Syslog configuration - Quick start guide
11.5.2.1 Syslog configuration via JSON
11.6 Network Time Protocol (NTP)
11.6.2 NTP configuration - Quick start guide
11.6.2.1 NTP configuration via JSON
12 The integrated Web server
12.1 LioN-X 0980 XSL... variants
13 Technical data
13.3 Power supply of the module electronics/sensors
13.4 Power supply of the actuators
Manual PROFINET
Version 1.1 07/2023
149
155
vii
14 Accessories
Contents
167
viii Manual PROFINET
Version 1.1 07/2023
1 About this manual 1.1 General information
1 About this manual
1.1 General information
Please read the assembly and operating instructions in this manual carefully before starting up the devices. Keep the manual where it is accessible to all users.
The texts, figures, diagrams, and examples used in this manual are used exclusively to explain how to operate and apply the devices.
Please contact us if you have any detailed questions on installing and starting up the devices.
Belden Deutschland GmbH
– Lumberg Automation™ –
Im Gewerbepark 2
D-58579 Schalksmühle
Germany lumberg-automation-support.belden.com
www.lumberg-automation.com
catalog.belden.com
Belden Deutschland GmbH – Lumberg Automation™ – reserves the right to make technical changes or changes to this manual at any time without notice.
Manual PROFINET
Version 1.1 07/2023
9
1.2 Explanation of symbols 1 About this manual
1.2 Explanation of symbols
1.2.1 Use of danger information
Danger information is denoted as follows:
Danger: Means that death, serious physical injury or substantial damage to property will occur if the required safety measures are not taken.
Warning: Means that death, serious physical injury or substantial damage to property can occur if the required safety measures are not taken.
Caution: Means that minor physical injury or damage to property can occur if the required safety measures are not taken.
1.2.2 Use of general information
General information is denoted as follows:
Attention: Contains important information on the product, on how to manage the product, or on the respective section of the documentation to which your special attention is being drawn.
1.3 Version information
Version
1.0
1.1
Created
03/2023
07/2023
Changes
Table 1: Overview of manual revisions
Warning in ch. Setting the rotary encoding switches
on page 40
10 Manual PROFINET
Version 1.1 07/2023
2 Safety instructions 2.1 Intended use
2 Safety instructions
2.1 Intended use
The products described in this manual are decentralized I/O Devices on an
Industrial Ethernet Network.
We adhere to all safety standards when developing, producing, testing, and documenting our products. When you adhere to the handling specifications and safety instructions described for the configuration, assembly, and correct operation, there should not normally be any risks for people or equipment.
The modules fulfill the requirements of the EMC guidelines (89/336/EEC,
93/68/EEC and 93/44/EEC) and the low voltage guideline (73/23/EEC).
The devices are designed to be used in the industrial sector. The industrial environment is distinguished by the fact that the consumer is not connected directly to the public low voltage network. Additional measures are required for use in residential areas or in business and commercial sectors.
Attention: This equipment may cause radio interference in residential areas. In this case the operator may be requested to carry out appropriate measures.
The proper and safe operation of this product depends on proper transportation, storage, assembly, and installation, and careful operation.
During the configuration, installation, start-up, maintenance, and testing of the devices, adhere to the safety and accident-prevention guidelines for the specific application.
Only install cables and accessories that fulfill the requirements and regulations for safety, electromagnetic compatibility, and, where applicable, telecommunication end devices, as well as the specification information.
Information on which cables and accessories are permitted for the installation can be obtained from Lumberg Automation™ or is contained in this manual.
Manual PROFINET
Version 1.1 07/2023
11
2.2 Qualified personnel 2 Safety instructions
2.2 Qualified personnel
The configuration, installation, start-up, maintenance, and testing of the devices may only be performed by a qualified electrician who is familiar with the safety standards of the automation technology.
The personnel requirements are based on the requirement profiles described by ZVEI, VDMA, or equivalent organizations.
Only electricians who are familiar with the content of this manual are authorized to install and maintain the devices described. These are persons who
D based on their technical training, knowledge, and experience, and their knowledge of the pertinent standards, can evaluate the work to be carried out and identify any potential risks or
D based on working for several years in a related sector, have the same level of knowledge as they would have from the relevant technical training.
Only Belden Deutschland GmbH – Lumberg Automation™ – is permitted to make changes to the hardware or software of the products that go beyond the scope of this manual.
Warning: Making unqualified changes to the hardware or software, or non-adherence to the warning information contained in this manual, can result in serious personal injury or damage to equipment.
Attention: Belden accepts no liability for any damage caused by unqualified personnel or improper use. This automatically voids the warranty.
12 Manual PROFINET
Version 1.1 07/2023
3 Designations and synonyms
3 Designations and synonyms
DI
DIA
DO
DIO
CSP+
DCP
DevCom
DevErr
AOI
API
BF
Big Endian
BUI
CC
Ch. A
Ch. B
CIP
CoAP
DTO
DTU
DUT
EIP
ERP
ETH
FE
FME
FSU
Add-On Instruction
Application Programming Interface
Bus Fault LED
Data format with High-B on first place (PROFINET)
Back-Up Inconsistency (EIP diagnostics)
CC-Link IE Field
Channel A (Pin 4) of I/O port
Channel B (Pin 2) of I/O port
Common Industrial Protocol (media independent protocol)
Constrained Application Protocol
Control & Communication System Profile Plus
Discovery and Configuration Protocol
Device Comunicating (EIP diagnostics)
Device Error (EIP diagnostics)
Digital Input
Diagnostic LED
Digital Output
Digital Input/Output
Device Temperature Overrun (EIP diagnostics)
Device Temperature Underrun (EIP diagnostics)
Device under test
EtherNet/IP
Enterprise Resource Planning system
ETHERNET
Functional Earth
Force Mode Enabled (EIP diagnostics)
Fast Start-Up
Manual PROFINET
Version 1.1 07/2023
13
MQTT
MSB
M12
NTP
OLE
OPC UA
LLDP
Low-B
LSB
LVA
LVS
MIB
MP
GSDML
High-B
ICT
IIoT
ILE
IME
I/O
I/O port
I/O port pin 2
I/O port pin 4 (C/Q)
IVE
I&M
JSON
L+
LioN-X 60
Little Endian
14
3 Designations and synonyms
General Station Description Markup Language
High-Byte
Invalid Cycle Time (EIP diagnostics)
Industrial Internet of Things
Input process data Length Error (EIP diagnostics)
Internal Module Error (EIP diagnostics)
Input / Output
X1 .. X8
Channel B of X1 .. X8
Channel A of X1 .. X8
IO-Link port Validation Error (EIP diagnostics)
Identification & Maintenance
JavaScript Object Notation (platform independent data format)
I/O port pin 1, sensor power supply
LioN-X variants with a width of 60mm
Data format with Low-B on first place (EtherNet/IP)
Link Layer Discovery Protocol
Low-Byte
Least Significant Bit
Low Voltage Actuator Supply (EIP diagnostics)
Low Voltage System/Sensor Supply (EIP diagnostics)
Management Information Base
Multiprotocol: PROFINET + EtherNet/IP + EtherCAT ® +
Modbus TCP (+ CC-Link IE Field Basic)
Message Queuing Telemetry Transport (open networking protocol)
Most Significant Bit
Metric thread according to DIN 13-1 with 12 mm diameter
Network Time Protocol
Output process data Length Error (EIP diagnostics)
Open Platform Communications Unified Architecture (platform independent, service-oriented architecture)
Manual PROFINET
Version 1.1 07/2023
3 Designations and synonyms
RPI
RWr
RWw
RX
RY
SCA
PLC
PN
PWR
REST
RFC
SCS
SLMP
SNMP
SP
SPE
U
AUX
UDP
UDT
UINT8
UINT16
U
L
UL
UTC
Programmable Logic Controller
PROFINET
Power
REpresentational State Transfer
Request for Comments
Requested Packet Interval
Word data input as seen from the master station (CC-Link)
Word data output as seen from the master station (CC-Link)
Bit data input as seen from the master station (CC-Link)
Bit data output as seen from the master station (CC-Link)
Short Circuit Actuator/U
L
/U
AUX
(EIP diagnostics)
Short Circuit Sensor (EIP diagnostics)
Seamless Message Protocol
Simple Network Management Protocol
Single Protocol (PROFINET, EtherNet/IP, EtherCAT ®
Modbus TCP or CC-Link IE Field Basic)
,
Startup Parameterization Error (EIP diagnostics)
U
Auxiliary
, supply voltage for the load circuit (Actuator supply on
Class B ports)
User Datagram Protocol
User-Defined Data Types
Byte in PLC (IB, QB)
Unsigned integer with 16 bits or word in PLC (IW, QW)
U
Load
, supply voltage for the load circuit (Actuator supply on
Class A)
Underwriters Laboratories Inc. (certification company)
Coordinated Universal Time (Temps Universel Coordonné)
Table 2: Designations and synonyms
Manual PROFINET
Version 1.1 07/2023
15
4 System description
4 System description
The LioN modules ( L umberg Automation™ I nput/ O utput N etwork) function as the interface in an industrial Ethernet system: A central controller on the management level is able to communicate with the decentralized sensors and actuators on the field level. The line or ring topologies for which LioN modules can be used ensure not only reliable data communication but also significantly reduce the number of cables required and thus also the costs for installation and maintenance. They additionally enable easy and quick extension.
16 Manual PROFINET
Version 1.1 07/2023
4 System description 4.1 Device variants
4.1 Device variants
The following Digital I/O device variants are available in the LioN-X family:
Article number
935705001
Product designation Description I/O port functionality
935706002
935707001
935708001
0980 XSL 3900-121-007D-01F LioN-X M12-60 mm,
I/O Device
Multiprotocol (PN, EIP,
EC, MB, CC)
Security
0980 XSL 3901-121-007D-01F LioN-X M12-60 mm,
I/O Device
Multiprotocol (PN, EIP,
EC, MB, CC)
Security
0980 XSL 3903-121-007D-01F LioN-X M12-60 mm,
I/O Device
Multiprotocol (PN, EIP,
EC, MB, CC)
Security
0980 XSL 3923-121-007D-01F LioN-X M12-60 mm,
I/O Device
Multiprotocol (PN, EIP,
EC, MB, CC)
Security
16 x Input/Output universal
16 x Input
8 x Input, 8 x Output
Mixmodule, galvanic isolated
8 x Input, 8 x Output
Mixmodule, without galvanic isolation of the outputs
Table 3: Overview of LioN-X Digital-I/O variants
Manual PROFINET
Version 1.1 07/2023
17
4.2 I/O port overview 4 System description
4.2 I/O port overview
The following tables show the main I/O port differences of the LioN-X family.
Pin 4 and Pin 2 of the I/O ports can be configured partly to Digital Input or
Digital Output.
LioN-X 16DIO ports
Device variant
Port Pin 1 U
S
Pin 4 / Ch. A (In/Out) Pin 2 / Ch. B (In/Out)
0980 XSL
3900...
Info:
X4:
X3:
X2:
X1:
X8:
X7:
X6:
X5:
–
U
S
(4 A)
U
S
(4 A)
U
S
(4 A)
U
S
(4 A)
U
S
(4 A)
U
S
(4 A)
U
S
(4 A)
U
S
(4 A)
Type 3
DI
DI
DI
DI
DI
DI
DI
DI
Supply by U
L
DO (2 A)
DO (2 A)
DO (2 A)
DO (2 A)
DO (2 A)
DO (2 A)
DO (2 A)
DO (2 A)
Type 3
DI
DI
DI
DI
DI
DI
DI
DI
Supply by U
L
DO (2 A)
DO (2 A)
DO (2 A)
DO (2 A)
DO (2 A)
DO (2 A)
DO (2 A)
DO (2 A)
Table 4: Port configuration of 0980 XSL 3900... variants
18 Manual PROFINET
Version 1.1 07/2023
4 System description 4.2 I/O port overview
LioN-X 16DI ports
Device variant
0980 XSL 3901...
X5:
X4:
X3:
X2:
X1:
Info:
X8:
X7:
X6:
Port Pin 1 U
S
–
U
S
(4 A)
U
S
(4 A)
U
S
(4 A)
U
S
(4 A)
U
S
(4 A)
U
S
(4 A)
U
S
(4 A)
U
S
(4 A)
DI
DI
DI
DI
DI
DI
DI
Pin 4 / Ch.
A (Input)
Type 3
DI
Table 5: Port configuration of 0980 XSL 3901... variants
DI
DI
DI
DI
DI
DI
DI
Pin 2 / Ch. B
(Input)
Type 3
DI
Manual PROFINET
Version 1.1 07/2023
19
4.2 I/O port overview 4 System description
LioN-X 8DI8DO ports with galvanic isolation of the outputs
Device variant Port
Info:
0980 XSL
3903...
X8:
X7:
X6:
X5:
X4:
X3:
X2:
X1:
–
Pin 1 U
S
–
–
–
–
U
S
(4 A)
U
S
(4 A)
U
S
(4 A)
U
S
(4 A)
DI
DI
–
–
–
–
DI
DI
Pin 4 / Ch. A (In/Out)
Type 3 Supply by U
L
–
–
DO (2 A)
DO (2 A)
DO (2 A)
DO (2 A)
–
–
DI
DI
–
–
–
–
DI
Pin 2 / Ch. B (In/Out)
Type 3 Supply by U
L
DO (2 A)
DO (2 A)
DO (2 A)
DO (2 A)
–
DI
–
–
–
Table 6: Port configuration of 0980 XSL 3903... variants
20 Manual PROFINET
Version 1.1 07/2023
4 System description 4.2 I/O port overview
LioN-X 8DI8DO ports without galvanic isolation of the outputs
Device variant Port
Info:
0980 XSL
3923...
X8:
X7:
X6:
X5:
X4:
X3:
X2:
X1:
–
Pin 1 U
S
–
–
–
–
U
S
(4 A)
U
S
(4 A)
U
S
(4 A)
U
S
(4 A)
DI
DI
–
–
–
–
DI
DI
Pin 4 / Ch. A (In/Out)
Type 3 Supply by U
L
–
–
DO (2 A)
DO (2 A)
DO (2 A)
DO (2 A)
–
–
DI
DI
–
–
–
–
DI
Pin 2 / Ch. B (In/Out)
Type 3 Supply by U
L
DO (2 A)
DO (2 A)
DO (2 A)
DO (2 A)
–
DI
–
–
–
Table 7: Port configuration of 0980 XSL 3923... variants
Manual PROFINET
Version 1.1 07/2023
21
5.1 PROFINET product features 5 Overview of product features
5 Overview of product features
5.1 PROFINET product features
Data connection
The connection option provided by LioN-X is the widely used M12 connector with D-coding for the PROFINET IO network.
The connectors are also color-coded to prevent the ports from being mixed up.
Data transmission rates
Support of 100 Mbit/s with auto crossover and auto negotiation corresponding to IEEE 802.3.
PROFINET RT IO Device
The LioN-X I/O Device supports PROFINET RT (real-time). This allows the transmission of time sensitive process data between network components in real-time communication.
PROFINET specification V2.41, Conformance Class C (CC-C)
The LioN-X I/O Device complies with the PROFINET specification V2.41 and meet the requirements of Conformance Class C (CC-C) for the integrated switch. This means the device can be used in PROFINET IRT networks.
Integrated switch
The integrated Ethernet switch with Conformance Class C (CC-C) has two
PROFINET ports and thus supports the establishment of a line or ring topology for the PROFINET IO network.
Media Redundancy Protocol
The additionally implemented Media Redundancy Protocol (MRP) enables the design of a highly available network infrastructure.
22 Manual PROFINET
Version 1.1 07/2023
5 Overview of product features 5.1 PROFINET product features
Fast Start-Up (FSU)
Fast Start-Up is an accelerated start-up process that enables a LioN-X I/O
Device to start communicating on a PROFINET network after a very short time. This makes a faster tool change possible, for example. Thanks to the
FSU feature, the network is ready to communicate in less than 500 ms.
Shared Device
With the shared device functionality, two controllers can access the same
I/O device via a PROFINET interface. This option is done by copying the configuration of the I/O device into the first and second controller and assigning it to the second controller as shared device. Every sub slot with I/
O data can be assigned to one of the two PLCs which share the I/O data of the I/O device.
DCP
The Masters use the DCP protocol to automatically assign IP addresses.
Net Load Class III
The devices offer advanced robustness against net load according to Net
Load Class III.
LLDP
The LLDP protocol is used to detect devices in the vicinity (neighborhood detection).
SNMPv1
The SNMPv1 protocol (according PROFINET standard V2.35) handles network component monitoring and communication between Master and
Device (cannot be operated stand-alone).
Alarm and diagnostic messages
The modules support extended PROFINET alarm and diagnostic messages.
1 Measured according to the specification: Internal switch is able to forward telegrams.
Manual PROFINET
Version 1.1 07/2023
23
5.1 PROFINET product features 5 Overview of product features
I&M functions
Identification and maintenance data (I&M) means information stored on the module. The identification data consist of manufacturer details for the module and can only be read. The maintenance data consist of system specific details created during the course of configuration. The modules can be uniquely identified online via the I&M data.
The device supports I&M data related to the PNO 2.832 standard (integration for PROFINET, Edition 2):
D I&M0 … I&M3 for the interface module (access slot, sub-slot 0x8000)
GSDML-based configuration and parameterization of the I/O ports
The GSDML offers the option of configuring and parameterizing the I/O ports on the master devices within an engineering tool of a PLC.
24 Manual PROFINET
Version 1.1 07/2023
5 Overview of product features 5.2 Integrated Web server
5.2 Integrated Web server
Network parameter display
Get an overview of network parameters such as the IP address, subnet mask and gateway.
Displaying diagnostics
View diagnostics via the integrated Web server.
User management
Use the integrated Web server for convenient management of all users.
Manual PROFINET
Version 1.1 07/2023
25
5.3 Security features 5 Overview of product features
5.3 Security features
Firmware signature
The official firmware update packages contain a signature which helps prevent the system against manipulated firmware updates.
Syslog
The LioN-X multiprotocol variants support the traceability of messages centrally managed and logged via Syslog.
User manager
The Web server provides a user manager to help protect the Web interface against unauthorized access. You can manage the users by groups with different access levels “Admin” or “Write”.
Default user settings:
User: admin
Password: private
Attention: Change the default settings to help protect the device against unauthorized access.
26 Manual PROFINET
Version 1.1 07/2023
5 Overview of product features 5.4 Other features
5.4 Other features
Interface protection
The devices have reverse polarity, short-circuit and overload protection for all interfaces.
For more details, see section
on page 34.
Failsafe
The devices support a failsafe function. This allows you to define the behavior of every single channel configured as an output in the case of a loss of the
PLC communication.
Industrial Internet of Things
LioN-X is industry 4.0 ready and supports the integration in IIoT networks via
REST API and the IIoT-relevant protocols MQTT, OPC UA and CoAP.
Color-coded connectors
The colored connectors help you avoid confusion in your cabling.
IP protection classes: IP65 / IP67 / IP69K
The IP protection class describes environmental influences that the devices can be exposed to without risk and without suffering damage or causing a risk for the user.
The whole LioN-X family offers IP65, IP67 and IP69K.
Manual PROFINET
Version 1.1 07/2023
27
6.1 General information 6 Assembly and wiring
6 Assembly and wiring
6.1 General information
Mount the device on a flat surface using 2 screws (M4x 25/30). The torque required here is 1 Nm. Use washers for all fastening methods as per DIN 125.
Attention: The devices have a ground connection with an M4 thread for the conduction of interference currents and the EMC immunity. This is labeled with the symbol for the ground and the designation "FE"
Attention: Use a low-impedance connection to connect the device to the reference ground. When using a grounded mounting surface, you can make the connection directly via the fixing screws.
Attention: If the mounting surface is ground-free, use a ground strap or a suitable FE line (FE = Functional Earth). Use an M4 screw to connect the ground strap or the FE line to the ground point and if possible put a washer and a toothed washer below the fixing screw.
28 Manual PROFINET
Version 1.1 07/2023
6 Assembly and wiring 6.2 Outer dimensions
6.2 Outer dimensions
6.2.1 LioN-X Digital-I/O multiprotocol variants
Figure 1: 0980 XSL 3900-121-007D-01F
Manual PROFINET
Version 1.1 07/2023
29
6.2 Outer dimensions 6 Assembly and wiring
Figure 2: 0980 XSL 3901-121-007D-01F
30 Manual PROFINET
Version 1.1 07/2023
6 Assembly and wiring 6.2 Outer dimensions
Figure 3: 0980 XSL 3903-121-007D-01F
Manual PROFINET
Version 1.1 07/2023
31
6.2 Outer dimensions 6 Assembly and wiring
Figure 4: 0980 XSL 3923-121-007D-01F
32 Manual PROFINET
Version 1.1 07/2023
6 Assembly and wiring 6.2 Outer dimensions
6.2.2 Notifications
Attention:
For UL applications , be sure to use a UL-certified cable with a suitable evaluation to connect the devices (CYJV or PVVA). To program the control, please refer to the OEM information, and only use suitable accessories.
Only approved for interior use. Please note the maximum elevation of
2000 meters. Approved up to a maximum soiling level of 2.
Warning: Terminals, housings field-wired terminal boxes or components can exceed temperatures of +60 °C (140 °F).
Warning: For UL applications at a maximum ambient temperature of +70 °C (158 °F):
Use temperature-resistant cables with heat resistance up to at least
+125 °C (257 °F) for all LioN-X and LioN-Xlight variants.
Warning: Observe the following maximum output power for the sensor supply of Class A devices:
Max. 4.0 A per port; for UL applications max. 5 A for every port pair
X1/X2, X3/X4, X5/X6, X7/X8; max. 9.0 A in total (with derating) for the whole port group X1 .. X8.
Warning: Observe the following maximum output power for the sensor supply of Class A/B devices:
Max. 4.0 A per port; for UL applications max. 5.0 A from U
S
power supply for every port pair X1/X2, X3/X4, X5/X6, X7/X8 and max. 5.0 A from U
AUX
power supply in total for port group X5/X6/X7/X8; max.
9.0 A in total (with derating) for the whole port group X1 .. X8.
Manual PROFINET
Version 1.1 07/2023
33
6.3 Port assignments 6 Assembly and wiring
6.3 Port assignments
All the contact arrangements shown in this chapter show the frontal view of the connection area for the connectors.
6.3.1 Ethernet ports, M12 socket, 4-pin, D-coded
Color coding: green
Figure 5: Schematic drawing, ports X01, X02
Port
Ethernet
Ports X01, X02
2
3
Pin
1
4
Signal
TD+
RD+
TD-
RD-
Table 8: Assignment of ports X01, X02
Function
Transmit data plus
Receive data plus
Transmit data minus
Receive data minus
Caution: Risk of destruction!
Never connect the power supply to the data cables.
34 Manual PROFINET
Version 1.1 07/2023
6 Assembly and wiring 6.3 Port assignments
6.3.2 Power supply with M12 power L-coded
Color coding: gray
Figure 6: Schematic diagram of the M12 L-coding (connector X03 for Power
In)
Figure 7: Schematic diagram of the M12 L-coding (socket X04 for Power
Out)
Power supply
2
3
Pin
1
4
5
Signal
U
S
(+24 V)
GND_U
L
GND_U
S
U
L
(+24 V)
FE
Function
Sensor/system power supply
Ground/reference potential U
L
Ground/reference potential U
S
Load supply
Actuator supply
Functional ground
Table 9: Pin assignments ports X03 and X04
Attention: Only use power supply units for the system/sensor and actuator supply that correspond to PELV (Protective Extra
Low Voltage) or SELV (Safety Extra Low Voltage). Power supplies according to EN 61558-2-6 (transformers) or EN 60950-1 (switching power supply units) fulfill these requirements.
Manual PROFINET
Version 1.1 07/2023
35
6.3 Port assignments 6 Assembly and wiring
Attention: For the input module 0980 XSL 3901-xxx, the two contacts
1 and 5 are not required for the voltage supply of the actuator.
Nevertheless, these two contacts are bridged together on the plug and socket side to enable a 5-pole forwarding of the voltage supply to a subsequent module.
6.3.3 I/O ports as M12 sockets
Color coding: black
Figure 8: Schematic drawing I/O port as M12 socket
36 Manual PROFINET
Version 1.1 07/2023
6 Assembly and wiring
6.3.3.1 I/O ports
0980 XSL 3900-121...
16DIO
X1 .. X8
0980 XSL 3901-121...
16DI
X1 .. X8
Pin
1
2
3
4
5
4
5
Pin
1
2
3
0980 XSL 39x3-121...
8DI8DO
X1 .. X4
8DI8DO
X5 .. X8
4
5
1
2
3
4
5
2
3
Pin
1
IN
FE n.c.
Signal
+24 V
IN
GND U
S
OUT
GND U
L
OUT
FE
Table 10: Pin assignments I/O ports
Signal
+24 V
IN/OUT
GND
IN/OUT
FE
Signal
+24 V
IN
GND U
S
IN
FE
6.3 Port assignments
Function power supply +24 V
Ch. B: Digital input or digital output
Ground/reference potential
Ch. A: Digital input or digital output
Functional ground
Function power supply +24 V
Ch. B: Digital input
Ground/reference potential
Ch. A: Digital input
Functional ground
Function power supply +24 V
Ch. B: Digital input
Ground/reference potential
Ch. A: Digital input
Functional ground
–
Ch. B: Digital output
Ground/reference potential
Ch. A: Digital output
Functional ground
Manual PROFINET
Version 1.1 07/2023
37
7.1 GSDML file 7 Starting operation
7 Starting operation
7.1 GSDML file
A GSD file in XML format is required to configure the LioN-X variants.
All device variants are grouped in a single GSDML file. The file can be downloaded from the product pages on our online catalog: catalog.belden.com
On request, the GSDML file is also sent by the support team.
The GSDML file and the associated bitmap files are grouped together in an archive file named GSDML-V2.41-BeldenDeutschland-LioN-Xyyyymmdd.xml
.
yyyymmdd stands for the date on which the file was issued.
Download this file and unpack it.
In Siemens TIA Portal ® you create a new project and open the hardware manager under Configure a device . Under the menu command Options >
Manage general station description files (GSD) the GSD file is installed by defining the file path.
The LioN-X variants are then available in the hardware catalog.
7.2 MAC addresses
Every device has three unique assigned MAC addresses that cannot be changed by the user. The first assigned MAC address is printed onto the device.
38 Manual PROFINET
Version 1.1 07/2023
7 Starting operation 7.3 State on delivery
7.3 State on delivery
PROFINET parameters in state on delivery or after a factory reset:
PROFINET name:
IP address:
Subnet mask:
Device designations:
Vendor ID:
Device ID:
Name not assigned
0.0.0.0
0.0.0.0
0980 XSL 3900-121-007D-01F
0980 XSL 3901-121-007D-01F
0980 XSL 3903-121-007D-01F
0980 XSL 3923-121-007D-01F
0x016a
0x0400
Manual PROFINET
Version 1.1 07/2023
39
7.4 Setting the rotary encoding switches
7 Starting operation
7.4 Setting the rotary encoding switches
The following LioN-X variants support multiprotocol application for the protocols EtherNet/IP (E/IP), PROFINET (P), EtherCAT ® (EC), Modbus TCP
(MB) and CC-Link IE Field Basic (CC):
D 0980 XSL 3900-121-007D-01F
D 0980 XSL 3901-121-007D-01F
D 0980 XSL 3903-121-007D-01F
D 0980 XSL 3923-121-007D-01F
Caution: Risk of device damage due to memory malfunction
Any interruption of the power supply to the device during and after protocol selection can lead to a corrupt device memory.
After selecting a protocol followed by a restart of the device, the new protocol is initialized. This can take up to 15 seconds. During this time the device is not usable and the LED indicators are out of function.
When the protocol change is complete, the LED indicators return to normal operation and the device can be used again.
D Make sure that the power supply is maintained during the entire process.
The LioN-X multiprotocol variants allow you to select different protocols for communication within an industrial Ethernet system. In this way Digital I/O devices with multiprotocol function can be integrated into different networks without it being necessary to purchase products specific for each protocol.
This technology also gives you the option to use the same I/O Device in different environments.
Using rotary encoding switches at the lower front of the devices, you can easily and conveniently set both the protocol and the address of the device, if the protocol to be used supports this. Once you have made a protocol selection and started the cyclical communication, the device stores this setting permanently and uses the selected protocol from this point on. To use another supported protocol with this device, perform a factory reset.
The multiprotocol devices have a total of three rotary encoding switches.
With the first rotary encoding switch (x100) you set the protocol by using the
40 Manual PROFINET
Version 1.1 07/2023
7 Starting operation 7.4 Setting the rotary encoding switches corresponding switch position. Additionally, x100 is used to set the third last digit of the IP address for EIP.
With the other rotary encoding switches (x10 / x1), you set the last two digits of the IP address when you are using EtherNet/IP, Modbus TCP or CC-Link
IE Field Basic.
Protocol
EtherNet/IP
PROFINET
EtherCAT ®
Modbus TCP
CC-Link IE Field x100
0-2
P
EC
MB
CC x10
0-9
–
–
0-9
0-9 x1
0-9
–
–
0-9
0-9
Table 11: Assignment of the rotary encoding switches for each protocol
The setting you make to select a protocol is described detailed in the protocolspecific sections.
In delivery state no protocol settings are stored in the device. In this case only the desired protocol has to be chosen. To take over a changed rotary encoding switch setting (protocol setting), a power cycle or “Reset” from the
Web interface is necessary.
Once you have set the protocol using the rotary encoding switches, the device stores this setting when it starts in cyclic communication. Changing
Manual PROFINET
Version 1.1 07/2023
41
7.4 Setting the rotary encoding switches
7 Starting operation the protocol using the rotary encoding switch is no longer possible after this point. The device will always start using the stored protocol from that point on. The IP address can be changed depending on the selected protocol.
To change the protocol, carry out a factory reset. In this way you restore the factory settings of the respective device. How you perform the factory reset
for your device is described in chapter Factory reset on page 43.
If you position the rotary encoding switch in a manner that is invalid, the device signals this to you with a blink code (the BF/MS LED blinks in red three times).
42 Manual PROFINET
Version 1.1 07/2023
7 Starting operation 7.5 SNMPv1
7.4.1 PROFINET
If you decide to use PROFINET, set the first rotary encoding switch to the value of "P".
7.4.2 Factory reset
A factory reset restores the original factory settings and thus resets the changes and settings you have made up to that point. It also resets the protocol selection. To perform a factory reset, set the first rotary encoding switch (x100) to 9, the second (x10) to 7, and the third (x1) also to 9.
Afterwards perform a power cycle and wait 10 seconds due to internal memory write processes.
During the factory reset, the U
S
LED is blinking red. After the internal memory write processes have finished, the U
S
LED returns to display static green or red light, in dependency of the actual U
S
voltage.
Factory Reset x100
9 x10
7 x1
9
Follow the steps from section Setting the rotary encoding switches
on page
40 again to select a new protocol.
For performing a factory reset via software configuration, see chapter
UA configuration on page 116 and the configuration section.
7.5 SNMPv1
The PROFINET IO device supports SNMP objects required by the
PROFINET specification as per protocol standard SNMPv1. These include objects from RFC 1213 MIB-II (System Group and Interfaces Group) and the
LLDP MIB.
Passwords:
D Read Community: public
D Write Community: private
Manual PROFINET
Version 1.1 07/2023
43
8 Configuration and operation with
SIEMENS TIA Portal ®
8 Configuration and operation with
SIEMENS TIA Portal
®
Attention: The displayed examples of SIEMENS TIA Portal ® have been made with TIA V15.
After installing the GSDML files for the LioN-X PROFINET variants, they are available in the hardware catalog under Other field devices >
PROFINET IO > IO > Belden Deutschland GmbH - Lumberg Automation >
Lumberg Automation LioN-X .
1.
First, configure the TIA Portal ® project and the control system in the usual way. Assign an IP address and subnet mask for the PROFINET port of the control unit.
2.
Then choose the desired device from the Hardware catalog:
Figure 9: TIA Portal ® Hardware catalog
44 Manual PROFINET
Version 1.1 07/2023
8 Configuration and operation with
SIEMENS TIA Portal ®
3.
Click on the article designations of the modules in the hardware catalog and drag and drop the desired device into the network view:
Figure 10: Network view
4.
Assign the device to the PROFINET network:
Figure 11: Assign device
5.
Switch to the device configuration view and select the device to display configuration options:
Manual PROFINET
Version 1.1 07/2023
45
8.1 Assigning a device name and IP address
8 Configuration and operation with
SIEMENS TIA Portal ®
Figure 12: Device configuration
8.1 Assigning a device name and IP address
PROFINET IO devices are addressed on PROFINET via a unique device name. This can be freely assigned by the user but may only be used once on the network.
1.
A click on the device icon or on the first line of the Device overview opens the settings for PROFINET interface > Ethernet addresses :
Figure 13: ETHERNET addresses
2.
Check that the control unit and the I/O device are on the same Ethernet
Subnet.
3.
Accept the default settings for IP address and device name or change them if desired.
46 Manual PROFINET
Version 1.1 07/2023
8 Configuration and operation with
SIEMENS TIA Portal ®
8.1 Assigning a device name and IP address
4.
For a correctly working setup, the chosen device name must be programmed online in the I/O device. When the HW is already installed, you can easily change to online mode. The new I/O device should already be accessible via PROFINET:
Figure 14: Go online
Figure 15: Online mode
5.
Enter the same device name as configured in the offline project:
Figure 16: Assign device name
Manual PROFINET
Version 1.1 07/2023
47
8.2 Configuring the I/O ports 8 Configuration and operation with
SIEMENS TIA Portal ®
8.2 Configuring the I/O ports
For device 0980 XSL 3900-121-007D-01F, all I/O channels are pre-configured by default as 16 DI/DO.
This means you can attach a sensor or an actuator to each I/O channel without additional configuration of the channel direction (input or output). When you attach a sensor, do not activate the appropriate digital output via PLC.
Figure 17: Channels pre-configuration
There are additional pre-configured channel setups available in the Catalog view. By removing the 16 DI/DO "Slot 1", you can set e.g. all I/O channels to
16 DO when choosing "Module 16 DO" from the Catalog .
The input and output addresses defined in the device overview can be changed.
48 Manual PROFINET
Version 1.1 07/2023
8 Configuration and operation with
SIEMENS TIA Portal ®
8.2 Configuring the I/O ports
8.2.1 Deleting the I/O configuration
1.
To delete the current I/O configuration, select the respective slot in the
Device overview :
Figure 18: Device overview
2.
Right click on the slot and select option Delete in the appearing menu:
Figure 19: Free I/O Slot 1
Manual PROFINET
Version 1.1 07/2023
49
8.2 Configuring the I/O ports 8 Configuration and operation with
SIEMENS TIA Portal ®
8.2.2 Changing the I/O configuration
The Module folder of the I/O device inside the Hardware catalog shows all configurable options that can be selected:
Figure 20: I/O channel configuration
Select the desired option, click and hold down the left mouse button to drag the configuration to a free slot:
There are three additional slots (2 .. 4) for optional output current and voltage measurements:
50 Manual PROFINET
Version 1.1 07/2023
8 Configuration and operation with
SIEMENS TIA Portal ®
8.3 Parameterization of the Status/
Control Module
8.3 Parameterization of the Status/Control
Module
Figure 21: Status/Control Module
Parameters of the 16 DI/DO device variant:
Figure 22: Parameters of the 16 DI/DO device variant
The variants 0980 XSL 3901… and 0980 XSL 3903... support sub-sets of the mentioned parameters. For variant 0980 XSL 3900…, the parameter subsets can be different in dependency of the chosen I/O configuration, e.g. "8DI" instead of "16 DI/DO".
Certain configuration parameters apply only to Digital Outputs or only to
Digital Inputs. For these to be effective, the corresponding channel must have output or input functionality and must also be configured accordingly.
Manual PROFINET
Version 1.1 07/2023
51
8.3 Parameterization of the Status/
Control Module
Configuration parameter
Surveillance Timeout
Failsafe
Auto Restart
Current Limit
Input Filter Time
Input Logic
8 Configuration and operation with
SIEMENS TIA Portal
Applicable for channel configuration
DIO, Output
DIO, Output
DIO, Output
DIO, Output
DIO, Input
DIO, Input
®
52 Manual PROFINET
Version 1.1 07/2023
8 Configuration and operation with
SIEMENS TIA Portal ®
8.3.1 General Parameters
8.3 Parameterization of the Status/
Control Module
Web Interface
The Web interface access can be set to "Enabled" or "Disabled" with this parameter. In case of the "Disabled" setting, the Web pages are not reachable.
Default: Enabled
Force Mode
The input and output I/O data can be forced (= changed) for implementation reasons. This can be done by different interfaces (e.g. Web-Interface, REST,
OPC UA, MQTT). With this function the possibility of forcing I/O data can be enabled or disabled.
Default: Disabled
Danger: Risk of physical injury or death! Unattended forcing can lead to unexpected signals and uncontrolled machine movements.
Manual PROFINET
Version 1.1 07/2023
53
8.3 Parameterization of the Status/
Control Module
8 Configuration and operation with
SIEMENS TIA Portal ®
External Configuration
Configuration and parameter data can be set over different external interfaces outside the GSDML configuration (e.g. Web interface, REST, OPC UA,
MQTT). With this option, the “External Configuration” can be enabled or disabled. An external configuration can only be done, if no cyclic PLC connection is active. Every new PLC connection overwrites the external configuration settings.
Default: Disabled
Report Alarms
This is a global switch for enabling or disabling all PROFINET alarms.
Default: Enabled
Report U
S
supply voltage fault alarms
The U
S
supply voltage fault alarm can be set to "Disabled" or "Enabled" with this parameter.
Default: Enabled
Report U
L
supply voltage fault alarms
The U
L
supply voltage fault alarm can be set to "Disabled", "Enabled" or "Auto
Mode" with this parameter.
In "Auto Mode", the U
L
diagnosis will be activated with the first rising slope detection after power-up.
Default: Disabled
Attention: "Report U
L
supply voltage fault" is disabled in the default setting to avoid diagnostic messages due to switching the supply voltage on or off later on.
54 Manual PROFINET
Version 1.1 07/2023
8 Configuration and operation with
SIEMENS TIA Portal ®
8.3 Parameterization of the Status/
Control Module
Report DO fault without U
L
The diagnosis of digital outputs can be configured in dependency of the U
L status.
When the output will be active without active U
L
while this parameter is set to
"Enabled", a diagnosis message will be generated for the output channel.
Default: Enabled
8.3.2 DI/DO Mapping
Byte/Channel order of Status/Control I/O data
With this parameter, 4 (Mode 1 – 4) pre-defined bit mappings for the digital
I/O bits can be selected.
Mode 5 can be used for a free, user defined mapping. The parameter settings
“Port X1 / Channel A” – “Port X8 / Channel B” must be used for this. These parameters enable all I/O channels to be freely assigned to a Bit in the Slot
1 I/O data. It should be noticed that duplicate assignments are not possible here. If faulty parameterization is detected in the LioN-X device, a fault will be registered.
When chosen Mode 1 – Mode 4, the “Port X1 / Channel A” – “Port X8 Channel
B” settings will be ignored in the LioN-X device.
Manual PROFINET
Version 1.1 07/2023
55
8.3 Parameterization of the Status/
Control Module
8 Configuration and operation with
SIEMENS TIA Portal ®
The chosen mapping will be used in the same way for input and output data direction.
Key
1 st Byte = low address byte in a Siemens PLC
2 nd Byte = high address byte in a Siemens PLC
(applicable for a Siemens PLC using Big-Endian format)
Mode 1:
Mode 2:
Mode 3:
Mode 4:
56 Manual PROFINET
Version 1.1 07/2023
8 Configuration and operation with
SIEMENS TIA Portal ®
Mode 5:
8.3 Parameterization of the Status/
Control Module
For detailed I/O mapping refer to chapter Process data assignment
on page
74.
Manual PROFINET
Version 1.1 07/2023
57
8.3 Parameterization of the Status/
Control Module
8 Configuration and operation with
SIEMENS TIA Portal ®
8.3.3 DO Surveillance Timeout (ms)
For channels configured as digital output, the firmware of the modules allows you to set a delay time before output status monitoring is enabled.
The delay time is referred to as the "Surveillance Timeout" and can be configured for each output channel. The delay time begins with a rising edge of the output control bit. After this time has elapsed, the output is monitored, and error states are reported by diagnostics.
The DO Surveillance-Timeout (ms) parameter can be set from 0 to 255 ms.
When an output channel is in static state, i.e., when the channel is permanently switched on or off, the typical filter value (not changeable) is
5 ms before a diagnostic message will be generated in case of a detected output error.
Default: 80 ms
8.3.4 DO Failsafe Behavior
The device supports a failsafe function for the channels used as digital outputs. During configuration of the devices, the status of the PROFINET IO device outputs can be defined after an interruption, or loss of communication on the PROFINET IO network.
58 Manual PROFINET
Version 1.1 07/2023
8 Configuration and operation with
SIEMENS TIA Portal ®
8.3 Parameterization of the Status/
Control Module
The following options can be selected:
D Set Low - the output channel is disabled and/or the output bit set to "0".
D Set High - the output channel is enabled and/or the output bit set to "1".
D Hold last – the last output state is kept.
Default: Set Low
8.3.5 DO Restart Mode after Failure
With this parameter, the digital output restart behavior can be set.
Manual PROFINET
Version 1.1 07/2023
59
8.3 Parameterization of the Status/
Control Module
8 Configuration and operation with
SIEMENS TIA Portal ®
D Automatic Restart after Failure:
In case of detecting an output short circuit or overload, the output will be switched off. However, after a time delay, the output will automatically be turned on again for checking if the overload or short circuit condition is active.
D Restart after Output Reset:
In case of detecting an output short circuit or overload, the output will be switched off.
The output will not be set automatically. Before the output can be turned on again, it must be logically reset by the PLC.
Default: Automatic Restart after Failure
8.3.6 DO Current Limit
With this option, the mode of the digital output switch can be selected.
D The following values are available: 0.5 A; 1.0 A; 1.5 A; 2,0 A; 2.0 A Max.
This means that the level for actuator overload diagnostic can be managed by this selection. 2.0 A Max.
means, that current limitation is not active and the maximum output current for this output is available.
60 Manual PROFINET
Version 1.1 07/2023
8 Configuration and operation with
SIEMENS TIA Portal ®
8.3 Parameterization of the Status/
Control Module
Default: High-Side Switch (2.0 A Max.)
8.3.7 DI Filter Time
With this parameter, the filter time of the digital input can be defined.
The following options are available:
Off; 1 ms; 2 ms; 3 ms; 6 ms; 10 ms; 15 ms
Default: 3 ms
Manual PROFINET
Version 1.1 07/2023
61
8.3 Parameterization of the Status/
Control Module
8 Configuration and operation with
SIEMENS TIA Portal ®
8.3.8 DI Input Logic
This parameter can be used to configure the logic of the channels used as digital inputs.
D NO (Normally Open):
A non-damped sensor has an open switching output (low signal) in this case. The device input detects a low signal and returns a "0" to the control unit.
The LED of the channel shows the physical input state.
D NC (Normally Closed):
A non-damped sensor has a closed switching output (high signal) in this case. The device input detects a high signal, inverts the signal, and returns a "0" to the control unit.
The channel LED displays, independent of the setting, the physical input state.
Default: NO (Normally Open) for all channels
62 Manual PROFINET
Version 1.1 07/2023
8 Configuration and operation with
SIEMENS TIA Portal ®
8.4 Media Redundancy Protocol
(MRP)
8.4 Media Redundancy Protocol (MRP)
Redundant PROFINET communication can be implemented with the LioN-
X devices via a ring topology without the use of additional switches. An
MRP redundancy manager terminates the ring, detects individual failures, and transmits the data packets on the redundant path in case of error.
The following conditions must be met to use MRP:
D All devices must support MRP.
D MRP must be enabled on all devices.
D Connections to the devices are only possible via the ring ports. A mesh topology is not permissible.
D A max. of 50 devices are permissible in the ring.
D All devices share the same redundancy domain.
D One device must be configured as the redundancy manager.
D All other devices must be configured as redundancy clients.
D Prioritized boot (FSU) is permissible.
D The response monitoring time of all devices must be greater than the reconfiguration time (typically 200 ms, min. 90 ms for LioN-X devices).
D It is recommended to use automatic network settings on all devices.
The following figures show a possible MRP ring configuration. The PLC is used as the redundancy manager while all other devices are clients. To detect an individual failure, it is advisable to use the diagnostics alerts.
Figure 23: Example of setting up an MRP redundancy client in TIA Portal ®
Manual PROFINET
Version 1.1 07/2023
63
8.4 Media Redundancy Protocol
(MRP)
8 Configuration and operation with
SIEMENS TIA Portal ®
Figure 24: Example of setting up the Watchdog time monitoring in TIA
Portal ® for using MRP
64 Manual PROFINET
Version 1.1 07/2023
8 Configuration and operation with
SIEMENS TIA Portal ®
8.5 Identification & maintenance
(I&M)
8.5 Identification & maintenance (I&M)
The PROFINET IO device has the ability to uniquely identify the devices installed in the system via an electronic nameplate. This device-specific data can be read acyclic by the user at any time. Furthermore, the installation date, location code and further descriptions can be stored in the device during installing the system. The I&M functions provide the following functionality.
8.5.1 Supported I&M features
8.5.1.1 I&M data of the PN-IO Device
For reading (I&M 0 - 3) and writing (I&M 1 - 3) I&M data, the appropriate
Hardware identifier for Slot 0: PROFINET Interface X1 must be chosen:
Figure 25: TIA Portal ® hardware identifier of PROFINET interface for I&M
0-3 RDREC/WRREC
Manual PROFINET
Version 1.1 07/2023
65
8.5 Identification & maintenance
(I&M)
8 Configuration and operation with
SIEMENS TIA Portal ®
The device-specific I&M features can be read (0-3) or written (1-3) via slot 0.
The specified index is used for mapping the data sets.
Data object Access Default value / Description
MANUFACTURER_ID
ORDER_ID
SERIAL_NUMBER
HARDWARE_REVISION
SOFTWARE_REVISION
REVISION_COUNTER
PROFILE_ID
PROFILE_SPECIFIC_TYPE
IM_VERSION
IM_SUPPORTED
2
2
2
2
2
4
2
Length
[byte]
2
20
16
Read
Read
Read
Read
Read
Read
Read
Read
Read
Read
0x016A (Belden Deutschland GmbH)
Order number of module in ASCII
Defined in production process in ASCII
Hardware revision of device
Software revision of device
Incremented for every statically stored parameter change on the PROFINET IO device (e.g., device name or IP address)
0xF600 (Generic device)
0x0003 (IO modules)
0x0101 (I&M Version 1.1)
0x000E (I&M 1 … 3 & 5 is supported)
Table 12: I&M 0 (Slot 0: PROFINET Interface X1, Index 0xAFF0)
Data object Length
[byte]
32
Access Default value / Description
TAG_FUNCTION
TAG_LOCATION 22
Read/
Write
Read/
Write
0x20 ff. (empty)
0x20 ff. (empty)
Table 13: I&M 1 (Slot 0: PROFINET Interface X1, Index 0xAFF1)
2 The serial number in the I&M data differs from the printed serial number on the housing. Printed serial number on housing: 9 characters article number + 9 characters ongoing number I&M0 serial number: 9 characters ongoing number (same last 9 characters as printed serial number on housing)
66 Manual PROFINET
Version 1.1 07/2023
8 Configuration and operation with
SIEMENS TIA Portal ®
8.5 Identification & maintenance
(I&M)
Data object Length
[byte]
16
Access Default value / Description
INSTALLATION_DATE Read/
Write
0x20 ff. (empty); Supported data format is a visible string with a fix length of 16 byte;
“YYYY-MM-DD hh:mm” or
“YYYY-MM-DD” filled with blank spaces
Table 14: I&M 2 (Slot 0: PROFINET Interface X1, Index 0xAFF2)
Data object Length
[byte]
54
Access Default value / Description
DESCRIPTOR Read/
Write
0x20 ff. (empty)
Table 15: I&M 3 (Slot 0: PROFINET Interface X1, Index 0xAFF3)
Manual PROFINET
Version 1.1 07/2023
67
8.5 Identification & maintenance
(I&M)
8 Configuration and operation with
SIEMENS TIA Portal ®
8.5.2 Reading and writing I&M data
In its standard library, SIEMENS offers TIA Portal ® system function modules that allow I&M data to be read and written. A data set contains a 6-byte
BlockHeader and the I&M record.
The data requested on reading, or the data to be written thus only start after the existing header. For writing, the header content must additionally be taken into account.
Table 16: Data set with BlockHeader and I&M Record on page
68 shows the structure of a data set.
D For reading I&M 0..3, the RDREC block must be configured with
LEN =
6 Byte Block Header + I&M data length
.
Data object
BlockType
BlockLength
BlockVersionHigh
BlockVersionLow
I&M Data
Length [byte]
2
2
1
1
I&M 0: 54
I&M 1: 54
I&M 2: 16
I&M 3: 54
Data type
Word
Word
Byte
Byte
Byte
Coding
I&M 0: 0x0020
I&M 1: 0x0021
I&M 2: 0x0022
I&M 3: 0x0023
I&M 0: 0x0038
I&M 1: 0x0038
I&M 2: 0x0012
I&M 3: 0x0038
0x01
0x00
Description
BlockHeader
I&M Record
Table 16: Data set with BlockHeader and I&M Record
68 Manual PROFINET
Version 1.1 07/2023
8 Configuration and operation with
SIEMENS TIA Portal ®
8.5 Identification & maintenance
(I&M)
8.5.2.1 I&M Read Record
I&M data can be read via the standard RDREC (SFB52) function block in the
Siemens PLC . The logical address of the slot/sub-slot (ID) and the I&M index
(INDEX) must be used as handover parameters. The return parameters show the length of the I&M data received and contain a status or error message.
Figure 26: Read example I&M0 of PROFINET IO device
Manual PROFINET
Version 1.1 07/2023
69
8.5 Identification & maintenance
(I&M)
8 Configuration and operation with
SIEMENS TIA Portal ®
Figure 27: Read example I&M0 on port X1 with connected IOL-Device
70 Manual PROFINET
Version 1.1 07/2023
8 Configuration and operation with
SIEMENS TIA Portal ®
8.5 Identification & maintenance
(I&M)
8.5.2.2 I&M Write Record
I&M data can be written via the standard WRREC (SFB53) function block in the Siemens PLC . The logical address of the slot/sub-slot (ID), the I&M index
(INDEX) and the data length (LEN) must be used as handover parameters.
The return parameters contain a status or error message.
Figure 28: Example of a completed I&M1 write action of a PROFINET IO device
Manual PROFINET
Version 1.1 07/2023
71
8.6 Fast Start Up (FSU) / Prioritized
Startup
8 Configuration and operation with
SIEMENS TIA Portal ®
8.6 Fast Start Up (FSU) / Prioritized Startup
The LioN-X devices with Fast Start-Up (FSU) support an optimized system start-up. This guarantees a faster restart after the power supply is restored.
Fast Start-Up can be activated for the LioN-X devices with PROFINET interface [X1] > Advanced options > Interface options with the option
Prioritized start-up .
For better FSU performance, the transmission settings of ports X01 and X02 should be set to:
72
Attention: The settings for the local and the partner port must be identical.
Manual PROFINET
Version 1.1 07/2023
8 Configuration and operation with
SIEMENS TIA Portal ®
8.6 Fast Start Up (FSU) / Prioritized
Startup
Measured boot times
PROFINET FSU time: 1)
< 450 ms
Start time with FSU activated: 2)
< 500 ms
Start time without FSU activated: 2)
~5500 ms
1) Measured according to specification: Internal switch is able to forward telegrams.
2) PLC reads one digital input and sets one digital output on I/O-Device after power-up of the DUT. The PLC is connected directly to DUT port X01 without any additional switch between PLC and DUT.
Manual PROFINET
Version 1.1 07/2023
73
9 Process data assignment
9 Process data assignment
This chapter describes the cyclic I/O data mapping between the PLC and the
I/O device. The mapping depends on the device specific setting of parameter
DI/DO Mapping .
For the DI/DO Mapping Mode configuration, see chapter
on page 55.
Key
X1A = Port 1, Channel A
1 st
Byte = low address byte in a Siemens PLC
2 nd
Byte = high address byte in a Siemens PLC
(applicable for a Siemens PLC using Big-Endian format)
74 Manual PROFINET
Version 1.1 07/2023
9 Process data assignment 9.1 0980 XSL 3900-121-007D-01F
9.1 0980 XSL 3900-121-007D-01F
9.1.1 16 DI/DO
9.1.1.1 Mapping Mode 1
Slot
1
Input/Output Bit 7 Bit 6
1 st
Byte
X8B X8A
2 nd
Byte
X4B X4A
Bit 5
X7B
X3B
Bit 4
X7A
X3A
Bit 3
X6B
X2B
Bit 2
X6A
X2A
Bit 1
X5B
X1B
Bit 0
X5A
X1A
9.1.1.2 Mapping Mode 2
Default setting
Slot
1
Input/Output Bit 7 Bit 6
1 st
Byte X4B X4A
2 nd Byte X8B X8A
Bit 5
X3B
X7B
Bit 4
X3A
X7A
Bit 3
X2B
X6B
Bit 2
X2A
X6A
Bit 1
X1B
X5B
Bit 0
X1A
X5A
9.1.1.3 Mapping Mode 3
Slot
1
Input/Output Bit 7 Bit 6
1 st Byte X8B X7B
2 nd Byte X8A X7A
Bit 5
X6B
X6A
Bit 4
X5B
X5A
Bit 3
X4B
X4A
Bit 2
X3B
X3A
Bit 1
X2B
X2A
Bit 0
X1B
X1A
9.1.1.4 Mapping Mode 4
Slot
1
Input/Output Bit 7 Bit 6
1 st
Byte
X8A X7A
2 nd
Byte
X8B X7B
Bit 5
X6A
X6B
Bit 4
X5A
X5B
Bit 3
X4A
X4B
Bit 2
X3A
X3B
Bit 1
X2A
X2B
Bit 0
X1A
X1B
Manual PROFINET
Version 1.1 07/2023
75
9.1 0980 XSL 3900-121-007D-01F 9 Process data assignment
9.1.1.5 Mapping Mode 5
The mapping for this mode depends on the user settings.
76 Manual PROFINET
Version 1.1 07/2023
9 Process data assignment 9.1 0980 XSL 3900-121-007D-01F
9.1.2 16 DI
9.1.2.1 Mapping Mode 1
Slot
1
Input
1 st
Byte
2 nd Byte
Bit 7 Bit 6
X8B X8A
X4B X4A
Bit 5
X7B
X3B
Bit 4
X7A
X3A
Bit 3
X6B
X2B
Bit 2
X6A
X2A
Bit 1
X5B
X1B
Bit 0
X5A
X1A
9.1.2.2 Mapping Mode 2
Default setting
Slot
1
Input
1 st
Byte
2 nd
Byte
Bit 7 Bit 6
X4B X4A
X8B X8A
Bit 5
X3B
X7B
Bit 4
X3A
X7A
Bit 3
X2B
X6B
Bit 2
X2A
X6A
Bit 1
X1B
X5B
Bit 0
X1A
X5A
9.1.2.3 Mapping Mode 3
Slot
1
Input
1 st
Byte
2 nd
Byte
Bit 7 Bit 6
X8B X7B
X8A X7A
Bit 5
X6B
X6A
Bit 4
X5B
X5A
Bit 3
X4B
X4A
Bit 2
X3B
X3A
Bit 1
X2B
X2A
Bit 0
X1B
X1A
9.1.2.4 Mapping Mode 4
Slot
1
Input
1 st
Byte
2 nd
Byte
Bit 7 Bit 6
X8A X7A
X8B X7B
Bit 5
X6A
X6B
Bit 4
X5A
X5B
Bit 3
X4A
X4B
Bit 2
X3A
X3B
Bit 1
X2A
X2B
Bit 0
X1A
X1B
9.1.2.5 Mapping Mode 5
The mapping for this mode depends on the user settings.
Manual PROFINET
Version 1.1 07/2023
77
9.1 0980 XSL 3900-121-007D-01F 9 Process data assignment
9.1.3 16 DO
9.1.3.1 Mapping Mode 1
Slot
1
Output
1 st
Byte
2 nd Byte
Bit 7 Bit 6
X8B X8A
X4B X4A
Bit 5
X7B
X3B
Bit 4
X7A
X3A
Bit 3
X6B
X2B
Bit 2
X6A
X2A
Bit 1
X5B
X1B
Bit 0
X5A
X1A
9.1.3.2 Mapping Mode 2
Default setting
Slot
1
Output
1 st
Byte
2 nd
Byte
Bit 7 Bit 6
X4B X4A
X8B X8A
Bit 5
X3B
X7B
Bit 4
X3A
X7A
Bit 3
X2B
X6B
Bit 2
X2A
X6A
Bit 1
X1B
X5B
Bit 0
X1A
X5A
9.1.3.3 Mapping Mode 3
Slot
1
Output
1 st
Byte
2 nd
Byte
Bit 7 Bit 6
X8B X7B
X8A X7A
Bit 5
X6B
X6A
Bit 4
X5B
X5A
Bit 3
X4B
X4A
Bit 2
X3B
X3A
Bit 1
X2B
X2A
Bit 0
X1B
X1A
9.1.3.4 Mapping Mode 4
Slot
1
Output
1 st
Byte
2 nd
Byte
Bit 7 Bit 6
X8A X7A
X8B X7B
Bit 5
X6A
X6B
Bit 4
X5A
X5B
Bit 3
X4A
X4B
Bit 2
X3A
X3B
Bit 1
X2A
X2B
Bit 0
X1A
X1B
9.1.3.5 Mapping Mode 5
The mapping for this mode depends on the user settings.
78 Manual PROFINET
Version 1.1 07/2023
9 Process data assignment 9.1 0980 XSL 3900-121-007D-01F
9.1.4 8 DI
9.1.4.1 Mapping Mode 5
Default setting
All 16 inputs are physically available, but only 8 inputs can be mapped to one input byte.
Slot
1
Input
1 st
Byte
Bit 7 Bit 6
X8A X7A
Bit 5
X6A
Bit 4
X5A
Bit 3
X4A
Bit 2
X3A
Bit 1
X2A
Bit 0
X1A
9.1.5 8 DI/8 DO, Opt. 1
9.1.5.1 Mapping Mode 5
Default setting
All 16 inputs/outputs are physically available, but only 8 inputs and 8 outputs can be mapped to one input byte and one output byte.
Slot
1
Input
1 st
Byte
Bit 7 Bit 6
X4B X4A
Bit 5
X3B
Bit 4
X3A
Bit 3
X2B
Bit 2
X2A
Bit 1
X1B
Bit 0
X1A
Slot
1
Output
1 st
Byte
Bit 7 Bit 6
X8B X8A
Bit 5
X7B
Bit 4
X7A
Bit 3
X6B
Bit 2
X6A
Bit 1
X5B
Bit 0
X5A
9.1.6 8 DI/8 DO, Opt. 2
9.1.6.1 Mapping Mode 5
Default setting
All 16 inputs/outputs are physically available, but only 8 inputs and 8 outputs can be mapped to one input byte and one output byte.
Manual PROFINET
Version 1.1 07/2023
79
9.1 0980 XSL 3900-121-007D-01F 9 Process data assignment
Slot
1
Slot
1
Input
1 st Byte
Output
1 st Byte
Bit 7 Bit 6
X8A X7A
Bit 7 Bit 6
X8B X7B
Bit 5
X6A
Bit 5
X6B
Bit 4
X5A
Bit 4
X5B
Bit 3
X4A
Bit 3
X4B
Bit 2
X3A
Bit 2
X3B
Bit 1
X2A
Bit 1
X2B
Bit 0
X1A
Bit 0
X1B
9.1.7 8 DI/8 DO, Opt. 3
9.1.7.1 Mapping Mode 5
Default setting
All 16 inputs/outputs are physically available, but only 8 inputs and 8 outputs can be mapped to one input byte and one output byte.
Slot
1
Input
1 st
Byte
Bit 7 Bit 6
X8B X7B
Bit 5
X6B
Bit 4
X5B
Bit 3
X4B
Bit 2
X3B
Bit 1
X2B
Bit 0
X1B
Slot
1
Output
1 st
Byte
Bit 7 Bit 6
X8A X7A
Bit 5
X6A
Bit 4
X5A
Bit 3
X4A
Bit 2
X3A
Bit 1
X2A
Bit 0
X1A
9.1.8 8 DI
9.1.8.1 Mapping Mode 5
Default setting
All 16 outputs are physically available, but only 8 outputs can be mapped to one output byte.
Slot
1
Output
1 st
Byte
Bit 7 Bit 6
X8A X7A
Bit 5
X6A
Bit 4
X5A
Bit 3
X4A
Bit 2
X3A
Bit 1
X2A
Bit 0
X1A
80 Manual PROFINET
Version 1.1 07/2023
9 Process data assignment 9.2 0980 XSL 3901-121-007D-01F
9.2 0980 XSL 3901-121-007D-01F
9.2.1 16 DI
9.2.1.1 Mapping Mode 1
Slot
1
Input
1 st
Byte
2 nd
Byte
Bit 7 Bit 6
X8B X8A
X4B X4A
Bit 5
X7B
X3B
Bit 4
X7A
X3A
Bit 3
X6B
X2B
Bit 2
X6A
X2A
Bit 1
X5B
X1B
Bit 0
X5A
X1A
9.2.1.2 Mapping Mode 2
Default setting
Slot
1
Input
1 st
Byte
2 nd Byte
Bit 7 Bit 6
X4B X4A
X8B X8A
Bit 5
X3B
X7B
Bit 4
X3A
X7A
Bit 3
X2B
X6B
Bit 2
X2A
X6A
Bit 1
X1B
X5B
Bit 0
X1A
X5A
9.2.1.3 Mapping Mode 3
Slot
1
Input
1 st Byte
2 nd Byte
Bit 7 Bit 6
X8B X7B
X8A X7A
Bit 5
X6B
X6A
Bit 4
X5B
X5A
Bit 3
X4B
X4A
Bit 2
X3B
X3A
Bit 1
X2B
X2A
Bit 0
X1B
X1A
9.2.1.4 Mapping Mode 4
Slot
1
Input
1 st
Byte
2 nd
Byte
Bit 7 Bit 6
X8A X7A
X8B X7B
Bit 5
X6A
X6B
Bit 4
X5A
X5B
Bit 3
X4A
X4B
Bit 2
X3A
X3B
Bit 1
X2A
X2B
Bit 0
X1A
X1B
Manual PROFINET
Version 1.1 07/2023
81
9.2 0980 XSL 3901-121-007D-01F 9 Process data assignment
9.2.1.5 Mapping Mode 5
The mapping for this mode depends on the user settings.
82 Manual PROFINET
Version 1.1 07/2023
9 Process data assignment 9.3 0980 XSL 3903-121-007D-01F
9.2.2 8 DI
9.2.2.1 Mapping Mode 5
Default setting
All 16 inputs are physically available, but only 8 inputs can be mapped to one input byte.
Slot
1
Input
1 st
Byte
Bit 7 Bit 6
X8A X7A
Bit 5
X6A
Bit 4
X5A
Bit 3
X4A
Bit 2
X3A
Bit 1
X2A
Bit 0
X1A
9.3 0980 XSL 3903-121-007D-01F
9.3.1 8 DI/8 DO
9.3.1.1 Mapping Mode 5
Default setting
Slot
1
Input
1 st Byte
Bit 7 Bit 6
X4B X4A
Slot
1
Output
1 st
Byte
Bit 7 Bit 6
X8B X8A
Bit 5
X3B
Bit 5
X7B
Bit 4
X3A
Bit 4
X7A
Bit 3
X2B
Bit 3
X6B
Bit 2
X2A
Bit 2
X6A
Bit 1
X1B
Bit 1
X5B
Bit 0
X1A
Bit 0
X5A
9.4 0980 XSL 3923-121-007D-01F
9.4.1 8 DI/8 DO
9.4.1.1 Mapping Mode 5
Default setting
Manual PROFINET
Version 1.1 07/2023
83
9.5 DO currents X1 .. X4 9 Process data assignment
Slot
1
Slot
1
Input
1 st Byte
Output
1 st Byte
Bit 7 Bit 6
X4B X4A
Bit 7 Bit 6
X8B X8A
Bit 5
X3B
Bit 5
X7B
Bit 4
X3A
Bit 4
X7A
Bit 3
X2B
Bit 3
X6B
Bit 2
X2A
Bit 2
X6A
Bit 1
X1B
Bit 1
X5B
Bit 0
X1A
Bit 0
X5A
9.5 DO currents X1 .. X4
This module can be configured optionally in slots 2, 3 or 4 when digital outputs are used. The content is four UINT16 of the actual measured output current.
A measured value of 1000mA will be transferred as "0x03E8 = b0000001111101000".
Slot
2 .. 4
Input
1 st
Byte X1
2 nd
Byte X1
3 rd
Byte X2
4 th
Byte X2
5 th
Byte X3
6 th Byte X3
7 th Byte X4
8 th
Byte X4
7
15
7
15
7
Bit
15
7
15
6
14
6
14
6
Bit
14
6
14
5
13
5
13
5
Bit
13
5
13
4
12
4
12
4
Bit
12
4
12
3
11
3
11
3
3
11
Bit
11
2
10
2
10
2
Bit
10
2
10
1
9
1
9
1
1
9
Bit
9
0
8
0
8
0
0
8
Bit
8
9.6 DO currents X5 .. X8
This module can be optionally configured in slots 2, 3 or 4 when digital outputs are used. The content is four UINT16 of the actual measured output current.
A measured value of 1000mA will be transferred as "0x03E8 = b0000001111101000".
84 Manual PROFINET
Version 1.1 07/2023
9 Process data assignment 9.7 U
S
/U
L
voltages X03/X04
Slot
2 .. 4
Input
1 st Byte X1
2 nd
Byte X1
3 rd
Byte X2
4 th
Byte X2
5 th
Byte X3
6 th
Byte X3
7 th
Byte X4
8 th
Byte X4
7
15
7
15
7
Bit
15
7
15
5
13
5
13
5
Bit
13
5
13
6
14
6
14
6
Bit
14
6
14
3
11
3
11
3
3
11
Bit
11
4
12
4
12
4
Bit
12
4
12
2
10
2
10
2
Bit
10
2
10
0
8
0
8
0
0
8
Bit
8
1
9
1
9
1
1
9
Bit
9
9.7 U
S
/U
L
voltages X03/X04
This module can be optionally configured in slots 2, 3 or 4. The content is two
UINT16 of the actual measured supply voltage U
S
and U
L
.
A measured value of 24 V will be transferred as "0x5DC0 =
0b0101110111000000".
Slot
2 .. 4
Input
1 st Byte U
S
2 nd
Byte U
S
3 rd
Byte U
L
4 th
Byte U
L
Bit
15
7
15
7
Bit
14
6
14
6
Bit
13
5
13
5
Bit
12
4
12
4
Bit
11
3
11
3
Bit
10
2
10
2
Bit
9
1
9
1
Bit
8
0
8
0
Manual PROFINET
Version 1.1 07/2023
85
9.8 PROFINET channel diagnostics mapping
9 Process data assignment
9.8 PROFINET channel diagnostics mapping
Port
I/O Pin
I/O Channel
PN Diagn.
Channel
X8
2/4
B/A
8
X7
2/4
B/A
7
X6
2/4
B/A
6
X5
2/4
B/A
5
X4
2/4
B/A
4
Table 17: PROFINET channel diagnostics mapping
X3
2/4
B/A
3
X2
2/4
B/A
2
X1
2/4
B/A
1
86 Manual PROFINET
Version 1.1 07/2023
10 Diagnostics 10.1 Detailed diagnostics description
10 Diagnostics
10.1 Detailed diagnostics description
10.1.1 Error of the system/sensor power supply U
S
The voltage value for the incoming system/sensor power supply is monitored globally for the device. If the voltage drops below approx. 18 V, or exceeds approx. 30 V, an error message is generated
Caution: It must definitely be ensured that the supply voltage, measured at the most remote participant is not below 21 V DC from the perspective of the system power supply.
The following device diagnostic is generated:
Channel number of diagnostic 0x8000 (diagnostic not channel-specific)
Channel related diagnostic code
0x0002
Channel related diagnostic code message
Undervoltage
D For disabled U
S
supply voltage fault alarms, the U
S in case of voltage drops below approx. 18 V.
D For enabled U
S
supply voltage fault alarms, the U
S in case of voltage drops below approx. 18 V.
indicator LED is "off"
indicator LED is "red"
Manual PROFINET
Version 1.1 07/2023
87
10.1 Detailed diagnostics description 10 Diagnostics
10.1.2 Error of the actuator power supply U
L
The voltage value for the incoming U for the device. If U
L
L
power supply is monitored globally
supply voltage alarms are enabled, an error message is generated in case the voltage drops below approx. 18 V or exceeds approx.
30 V.
If output channels are active, additional error messages caused by the voltage failure are generated on the I/O ports. U
L
supply voltage alarms are disabled by default and can be enabled via parameterization.
The following device diagnostic is generated:
Channel number of diagnostic 0x8000 (diagnostic not channel-specific)
Channel related diagnostic code
0x0118
Channel related diagnostic code message
Low voltage or over voltage of actuator power supply (U
L
)
Extended description
Check wire connection and U inclusive tolerance
L
power supply
D For disabled U
L in case of voltage drops below approx. 18 V.
D For enabled U
L
supply voltage fault alarms, the U
L
supply voltage fault alarms, the U in case of voltage drops below approx. 18 V.
L
indicator LED is "off"
indicator LED is "red"
88 Manual PROFINET
Version 1.1 07/2023
10 Diagnostics 10.1 Detailed diagnostics description
10.1.3 Overload/short-circuit of the I/O port sensor supply outputs
In case of an overload or a short circuit between pin 1 and pin 3 (GND) on the ports (X1 .. X8), the following channel-specific diagnostic messages are generated:
0x01 .. 0x08 Channel number of diagnostics
Channel related diagnostic code
Channel related diagnostic code message
0x0102
Sensor short circuit
D The dedicated red port DIA indicator is active when an error is detected.
Manual PROFINET
Version 1.1 07/2023
89
10.1 Detailed diagnostics description 10 Diagnostics
10.1.4 Overload/short circuit of the I/O port Ch. A as actuator outputs
The digital outputs on the Channel A (pin 4) are protected against short circuits and overloads. In case of a fault, the output is automatically switched to "inactive" and then cyclically switched back to "active" when the default setting is used ( DO Restart Mode Parameter = “Automatic Restart after
Failure”).
In DO Restart Mode Parameter = “Restart after Output Reset”, the output must be set to "low" via PLC, before the output can be set again to "high".
When an output channel is activated (rising edge of the channel state), the channel errors are filtered for the period that you set using the Surveillance-
Timeout parameter during the configuration of the device. The value of this parameter can range from 0 to 255 ms; the factory setting is 80 ms.
The filter is used to avoid premature error messages when a capacitive load is activated.
The device sends the following PROFINET diagnostic message in the case of a fault:
0x01 .. 0x08 Channel number of diagnostics
Channel related diagnostic code
Channel related diagnostic code message
0x0100
Actuator short circuit or supply error channel A
D The dedicated red port DIA indicator is active when an error is detected.
90 Manual PROFINET
Version 1.1 07/2023
10 Diagnostics 10.1 Detailed diagnostics description
10.1.5 Overload/short circuit of the I/O port Ch. B as actuator outputs
The digital outputs on the Channel B (I/Q / pin 2) are protected against short circuits and overloads. In case of a fault, the output is automatically switched to "inactive" and then cyclically switched back to "active" when the default setting is used ( DO Restart Mode Parameter = “Automatic Restart after Failure”).
In DO Restart Mod e Parameter = “Restart after Output Reset”, the output must be set to "inactive" via PLC, before the output can be set again to
"active".
When an output channel is activated (rising edge of the channel state), the channel errors are filtered for the period that you set using the "Surveillance-
Timeout" parameter during the configuration of the device. The value of this parameter can range from 0 to 255 ms; the factory setting is 80 ms.
The filter is used to avoid premature error messages when a capacitive load is activated.
The device sends the following PROFINET diagnostic message in the case of a fault:
0x01 .. 0x08 Channel number of diagnostics
Channel related diagnostic code
Channel related diagnostic code message
0x0101
Actuator short circuit or supply error channel B
D The dedicated red port DIA indicator is active when an error is detected.
Manual PROFINET
Version 1.1 07/2023
91
10.1 Detailed diagnostics description 10 Diagnostics
10.1.6 Generic parameter error
When a device parameter will be written to an invalid address (e.g. Sub-Slot /
Index) or the parameter data content is detected as invalid for the device, the following device specific diagnostic messages will be generated:
Channel number of diagnostics
Channel related diagnostic code
Channel related diagnostic code message
0x8000 (diagnostics not channel-specific)
0x0010
Parameter error
10.1.7 I/O mapping parameter error
The individual I/O data mapping parameter of the Status/Control data will be checked by the PROFINET IO device. When an error is detected inside this parameter block (e.g. a bit is mapped twice), the following message will be generated:
0x8000 (diagnostics not channel-specific) Channel number of diagnostics
Channel related diagnostic code
Channel related diagnostic code message
0x011A
I/O mapping configuration faulty
92 Manual PROFINET
Version 1.1 07/2023
10 Diagnostics 10.1 Detailed diagnostics description
10.1.8 Force mode diagnostic
In case of activated forcing, the following diagnostic message will be generated:
Channel number of diagnostics
Channel related diagnostic code
Channel related diagnostic code message
0x8000 (diagnostics not channel-specific)
0x000A
Simulation active
10.1.9 Internal module error
Internal module error states (e.g. internal abnormal states) will be reported by the following diagnostic message. For detailed information also use the Web interface of the device.
0x8000 (diagnostics not channel-specific) Channel number of diagnostics
Channel related diagnostic code
Channel related diagnostic code message
0x0009
Error
Manual PROFINET
Version 1.1 07/2023
93
10.2 Table of PROFINET diagnostic codes
10 Diagnostics
10.2 Table of PROFINET diagnostic codes
The following table gives an overview of the defined diagnostic codes in
PROFINET (0x0000 – 0x17FF) specification. Not all listed codes are used.
Type Diagnostic code
0x0000
0x0002
0x0009
0x000A
0x0010
0x0118
0x011A
Definition
Reserved
Undervoltage
Error
Simulation active
Parameter error
Low voltage of actuator power supply (U
L supply
). Check power
I/O mapping configuration faulty
Error
Error
Error
Error
Error
Error
94 Manual PROFINET
Version 1.1 07/2023
11 IIoT functionality
11 IIoT functionality
The LioN-X variants offer a number of new interfaces and functions for the optimal integration into existing or future IIoT (Industrial Internet of
Things) networks. The devices continue to work as field bus devices which communicate with and are controlled by a PLC (Programmable Logic
Controller).
In addition, the devices offer common IIoT interfaces, which enable new communication channels besides the PLC. The communication is performed via IIoT-relevant protocols MQTT and OPC UA. With the help of these interfaces not only all information in a LioN-X device can be read. They also enable its configuration and control, if the user wishes. All interfaces can be configured extensively and offer read-only functionality.
All LioN-X variants provide user administration, which is also applicable for accessing and configuring the IIoT protocols. This allows you to manage all modification options for the device settings via personalized user authorizations.
All IIoT protocols can be used and configured independently of the field bus.
It is also possible to use the devices completely without the help of a PLC and control them via IIoT protocols.
Attention: When using the IIoT functionality, a protected local network environment without direct access to the Internet is recommended.
Manual PROFINET
Version 1.1 07/2023
95
11.1 MQTT 11 IIoT functionality
11.1 MQTT
The MQTT (Message Queueing Telemetry Transport) protocol is an open network protocol for machine-to-machine communication, which provides the transmission of telemetric data messages between devices. The integrated
MQTT client allows the device to publish a specific set of information to an
MQTT broker.
The publishing of messages can either occur periodically or be triggered manually.
11.1.1 MQTT configuration
In delivery state , MQTT functions are disabled . The MQTT client can be configured either using the Web interface or directly via a JSON object sent in an HTTP request. For more information see chapter
on page 114.
The configuration URL is: http://[ip-address]/w/config/mqtt.json
The configuration can also read back as a JSON file: http://[ip-address]/r/config/mqtt.json
The configuration is a JSON object. Each JSON member is a configuration element. The object must not contain all elements. Only the provided elements will be changed. The configuration changes apply only after a device restart.
96 Manual PROFINET
Version 1.1 07/2023
11 IIoT functionality 11.1 MQTT
The following configuration elements are available (default values in bold):
Element mqtt-enable broker login password port base-topic will-enable will-topic auto-publish publish-interval publish-identity publish-config publish-status publish-process commands-allowed force-allowed reset-allowed config-allowed
Data type string
Description boolean Master switch for the MQTT client.
string string string
IP address of the MQTT Broker
Username for MQTT Broker
Password for MQTT Broker number Broker port
Base topic boolean If true, the device provides a last will message to the broker string The topic for the last will message.
boolean If true, all enabled domains will be published automatically in the specified interval.
number The publish interval in ms if autopublish is enabled. Minimum is 250 ms.
boolean If true, all identity domain data will be published boolean If true, all config domain data will be published boolean If true, all status domain data will be published boolean If true, all process domain data will be published boolean Master switch for MQTT commands.
If false, the device will not subscribe to any command topic, even if specific command topics are activated below.
boolean If true, the device accepts force commands via MQTT.
boolean If true, the device accepts restart and factory reset commands via MQTT.
boolean If true, the device accepts configuration changes via MQTT.
Example data true / false
" 192.168.1.1
"
"admin" (Default: null )
"private" (Default: null )
1883
"iomodule_[mac]"
(Default: " lionx ") true / false
(Default: null ) true / false
2000 true / false true / false true / false true / false true / false true / false true / false true / false
Manual PROFINET
Version 1.1 07/2023
97
11.1 MQTT 11 IIoT functionality
Element qos
Data type
Description number Selects the "Quality of Service" status for all published messages.
Example data
0 = At most once
1 = At least once
2 = Exactly once
Table 18: MQTT configuration
MQTT response:
The resulting response is a JSON object with a "status" field. Status should be "0" if no error occurred and "-1" if there is an error.
In case of an error, the response contains an error array.
The error array contains an error object for each error occurred. The object consists of a field "Element" which names the config element which caused the error, and a field "Message" for the error message.
D A malformed JSON object produces an error.
D Not existing parameters produce an error.
D Parameters with a wrong data type produce an error.
It is not allowed to write all available parameters at once. You may write only one or a limited number of parameters.
Examples:
{"status": -1, "error": [{"Element": "publish-interval", "Message": "Integer
expected"}]}
{"status": 0}
{"status": -1, "error": [{"Element": "root", "Message": "Not a JSON
object"}]}
For more information see chapter MQTT topics
on page 99.
98 Manual PROFINET
Version 1.1 07/2023
11 IIoT functionality 11.1 MQTT
11.1.2 MQTT topics
MQTT mainly relates to topics. All messages are attached to a topic which adds context to the message itself. Topics may consist of a string and they are allowed to contain slashes
(/)
. In topic filters, there also wildcard symbols like e.g. (#) allowed.
11.1.2.1 Base topic
For all LioN-X variants there is a configurable Base topic which is the prefix for all topics. The Base topic can be chosen freely by the user. The Base topic can also contain selected variables as shown in
Table 19: Base topic variables
on page 99.
Variables in the Base topic have to be written in brackets ("[ ]"). The following variables are possible:
Variable mac ip0 ip1 ip2 ip3 name order serial
Description
The MAC address of the device
The name of the device
The ordering number of the device
The serial number of the device
IP address octets
Table 19: Base topic variables
Example:
The Base topic
"io_[mac]"
translates to
"io_A3B6F3F0F2F1"
.
All data is organized in domains. The domain name is the first level in the topic after the Base topic. Note the following notation:
Base-Topic/domain/.….
Manual PROFINET
Version 1.1 07/2023
99
11.1 MQTT 11 IIoT functionality
There are the following domains:
Domain name identity config status process
Definition
All fixed data which is defined by the used hardware and which cannot be changed by configuration or at runtime.
Configuration data which is commonly loaded once at startup, mostly by a
PLC.
All (non-process) data which changes quite often in normal operation.
All process data which is produced and consumed by the device itself or by attached devices.
Table 20: Data domains
Example content
Device name, ordering number, MAC address, port types, port capabilites and more.
IP address, port modes, input logic, failsafe values and more.
Bus state, diagnostic information,
Device status and data.
Digital inputs, digital outputs, cyclic data.
There is often one topic used for all gateway related information and topics for each port. All identity topics are published just once at start-up, because this information should never change. All other topics are published either in a fixed interval or just triggered manually, according to the configuration.
100 Manual PROFINET
Version 1.1 07/2023
11 IIoT functionality 11.1 MQTT
Topic Content examples
[base-topic]/identity/ gateway
[base-topic]/identity/ port/n
[base-topic]/config/ gateway
[base-topic]/config/port/ n
[base-topic]/status/ gateway
[base-topic]/status/port/ n
[base-topic]/process/ gateway
[base-topic]/process/ port/n
Name, ordering number, MAC, vendor, I&M etc.
Port name, port type
Configuration parameters, ip address etc.
8
1
Port mode, data storage, mapping, direction 8
Bus state, device diagnosis, master events
Port or channel diagnosis, state
All Digital IN/OUT
Digital IN/OUT per port, pdValid
Table 21: Data model
1
8
1
8
Total publish count
1
Publish interval
Startup
Startup
Interval
Interval
Interval
Interval
Interval
Interval
An MQTT client which wants to subscribe to one or more of these topics can also use wildcards.
Full topic
[base-topic]/identity/gateway
[base-topic]/identity/#
[base-topic]/status/port/5
[base-topic]/+/port/2
[base-topic]/process/port/#
[base-topic]/config/#
Description
Receive only indentity objects for the gateway
Receive all data related to the identity domain
Receive only status information for port number 5
Receive information of all domains for port number 2
Receive only process data for all ports
Receive config data for the gateway and all ports.
Table 22: Use case examples
Manual PROFINET
Version 1.1 07/2023
101
11.1 MQTT
11.1.2.2 Publish topic
Overview of all publish JSON data for the defined topics:
Identity/gateway
Key product_name ordering_number device_type serial_number mac_address production_date fw_name fw_date fw_version hw_version family location country fax vendor_name vendor_address vendor_phone vendor_email vendor_techn_support vendor_url vendor_id device_id json_string json_string json_string json_string json_string json_string json_string json_string json_string json_string json_string json_string json_integer json_integer
Data type json_string json_string json_string json_string json_string json_string json_string json_string
Table 23: Identity/gateway
11 IIoT functionality
102 Manual PROFINET
Version 1.1 07/2023
11 IIoT functionality 11.1 MQTT
Config/gateway
Key fieldbus_protocol network_configuration rotary_switches ip_address subnet_mask report_ul_alarm report_do_fault_without_ul force_mode_lock web_interface_lock
Data type Range json_string json_string
PROFINET
EtherNet/IP
EtherCAT®
Modbus TCP
CC-Link IE Field
Basic
PROFINET:
D DCP
D Manual
EtherNet/IP:
D Manual
D Rotary
D DHCP
EtherCAT®:
D Manual
Modbus TCP:
D Manual
D DHCP
D Rotary
CC-Link IE Field
Basic:
D Manual
D Rotary json_integer 0 .. 999 json_string json_string json_boolean true / false json_boolean true / false json_boolean true / false json_boolean true / false
Default value
192.168.1.1
255.255.255.0
true false false false
Remarks
Manual PROFINET
Version 1.1 07/2023
103
11.1 MQTT
Config/gateway
Key fast_startup
Data type Range json_boolean true / false
Table 24: Config/gateway
11 IIoT functionality
Default value false
Remarks
PROFINET and EIP only
104 Manual PROFINET
Version 1.1 07/2023
11 IIoT functionality 11.1 MQTT
Status/gateway
Key Data type Range protocol system_voltage_fault actuator_voltage_fault internal_module_error simulation_active_diag us_voltage ul_voltage forcemode_enabled
Table 25: Status/gateway json_string PROFINET:
D UNKNOWN
D OFFLINE
D STOP
D IDLE
D OPERATE
EtherNet/IP:
D CONNECTED
D DISCONNECTED
EtherCAT®:
D PREOP
D SAFEOP
D OP
D INIT
D UNKNOWN
Modbus TCP:
D No Connections
D Connected
CC-Link IE Feld
Basic:
D ON
D STOP
D DISCONNECTED
D ERROR json_boolean true / false json_boolean true / false json_boolean true / false json_boolean true / false json_integer 0 .. 32 json_integer 0 .. 32 json_boolean true / false
Default value
Remarks in Volts in Volts
Manual PROFINET
Version 1.1 07/2023
105
11.1 MQTT
Process/gateway
Key Data type
Input_data output_data json_integer[] json_integer[]
Table 26: Process/gateway
Range
11 IIoT functionality
Default value
Remarks
106 Manual PROFINET
Version 1.1 07/2023
11 IIoT functionality 11.1 MQTT
Identity/port/1 .. 8
Key Data type Range port type max_output_power_cha max_output_power_chb channel_cha channel_chb json_integer json_string json_string json_string json_string json_string
1 .. 8
Digital Input
DIO
Digital Output
DIO Pin 4 Only
DI Pin 4 Only
DO Pin 4 Only
Not available
Unknown
2.0_mA
0.5_mA
2.0_mA
0.5_mA
Digital Input
Digital Output
DIO
Digital Input/Output
Auxiliary Power
Auxiliary with DO
Not available
Unknown
Digital Input
Digital Output
DIO
Digital Input/Output
Auxiliary Power
Auxiliary with DO
Not available
Unknown
Table 27: Identity/port/1 .. 8
Default value
Remarks
Manual PROFINET
Version 1.1 07/2023
107
11.1 MQTT 11 IIoT functionality
Config/port/1 .. 8
Key port direction_cha direction_chb restart_mode_cha restart_mode_chb input_polarity_cha input_polarity_chb input_filter_cha input_filter_chb do_auto_restart_cha do_auto_restart_chb failsafe_cha failsafe_chb surveillance_timeout_cha
Data type Range json_integer json_string json_string json_string json_string json_string json_string json_integer json_integer json_boolean true / false json_boolean true / false json_string json_string json_integer set_low set_high hold_last set_low set_high hold_last
0 .. 255
1 .. 8
NO
NC
NO
NC
Manual
Auto
Manual
Auto
Output
Input
Inactive
Auxiliary Power
DIO
Unknown
Output
Input
Inactive
Auxiliary Power
DIO
Unknown
Default value set_low set_low
80
Remarks ms ms
108 Manual PROFINET
Version 1.1 07/2023
11 IIoT functionality
Config/port/1 .. 8
Key surveillance_timeout_chb io_mapping_cha io_mapping_chb
Table 28: Config/port/1 .. 8
Data type Range json_integer json_integer
0 .. 255
0 .. 15 json_integer 0 .. 15
Status/port/1 .. 8
Key Data type Range port physical_state_cha physical_state_chb actuator_short_circuit_cha actuator_short_circuit_chb sensor_short_circuit current_cha current_chb current_pin1
Table 29: Status/port/1 .. 8 json_integer json_integer
1 .. 8
0 .. 1 json_integer 0 .. 1 json_boolean true / false json_boolean true / false json_boolean true / false json_integer json_integer json_integer
11.1 MQTT
Default value
80 channel number channel number
Remarks
16DIO only
16DIO only
Default value
Remarks mA mA mA
Manual PROFINET
Version 1.1 07/2023
109
11.1 MQTT 11 IIoT functionality
11.1.2.3 Command topic (MQTT Subscribe)
The main purpose of MQTT is to publish data from the device to a broker.
This data can then be received by any subscriber who is interested in this data. But also the other way round is possible. The device can subscribe to a topic on the broker and is then able to receive data. This data can contain configuration or forcing data. This allows the user to fully control a device via
MQTT only, without using other ways of communication like Web or REST.
If the configuration allows commands in general, the device subscribes to special Command topics on which it can receive commands from other MQTT clients. The Command topic is based upon the Base topic. It always has the following form:
[base-topic]/command
After the Command topic, there are fixed topics for different writeable objects.
The data format of the MQTT payload is always JSON. It is possible to set only a subset of the possible objects and fields.
[…]/forcing
Use the Command topic
[base-topic]/command/forcing
for Force object data. The Force object can contain any of the following properties:
Property forcemode digital
Data type boolean
array ( Table 31: Force object:
on page 111)
Example values true / false
Remarks
Forcing Authority: on/off
Table 30: Force object properties
110 Manual PROFINET
Version 1.1 07/2023
11 IIoT functionality 11.1 MQTT
For the Force object properties digital
and iol
, there are several value specifications arrayed:
Remarks Property port channel force_dir force_value
Data type integer string string integer
Example values
1, 2, 5
"a", "b"
"out", "in", "clear"
0, 1
Table 31: Force object: Digital
[…]/config
Use the Command topic
[base-topic]/command/config
for Config object data. The Config object can contain any of the following properties:
Property portmode ip_address subnet_mask gateway
Data type
array ( Table 33: Config object: Portmode on
page 112) string string string
Example values
"192.168.1.5"
"255.255.255.0"
"192.168.1.100"
Remarks
Table 32: Config object properties
Manual PROFINET
Version 1.1 07/2023
111
11.1 MQTT 11 IIoT functionality
For the Conig object property portmode
, there are several value specifications arrayed:
Remarks Property port channelA* channelB* inlogicA inlogicB filterA filterB autorestartA autorestartB
Data type integer string string string string integer integer boolean boolean
Example values
2
"dio", "di", "do", "iol",
"off"
"dio", "di", "do", "iol",
"off", "aux"
"no", "nc"
"no", "nc"
3
3 input filter in ms input filter in ms
Table 33: Config object: Portmode
*channelA = Pin 4, channelB = Pin 2
112 Manual PROFINET
Version 1.1 07/2023
11 IIoT functionality 11.1 MQTT
[…]/reset
Use the Command topic
[base-topic]/command/reset
for Reset object data about restart and factory reset issues. The Reset object can contain any of the following properties:
Remarks Property factory_reset system_reset
Data type boolean boolean
Example values true / false true / false
Table 34: Reset object properties
[…]/publish
Use the Command topic
[base-topic]/command/publish
for Publish object data.
Trigger publish of all topics manually (can be used when auto publish is off or long interval is set).
Manual PROFINET
Version 1.1 07/2023
113
11.1 MQTT 11 IIoT functionality
11.1.3 MQTT configuration - Quick start guide
Attention: Lumberg Automation
TM
is not responsible for any content of the referenced Web pages and provides no warranty for any functionality of the named third party software.
11.1.3.1 MQTT configuration via JSON
1.
Depending on your application case, download and install Insomnia or a comparable application: https://insomnia.rest/download/
2.
Configure MQTT:
POST:
[IP-address]/w/config/mqtt.json
114 Manual PROFINET
Version 1.1 07/2023
11 IIoT functionality
3.
Read MQTT:
GET:
[IP-address]/r/config/mqtt.json
11.1 MQTT
Manual PROFINET
Version 1.1 07/2023
115
11.2 OPC UA 11 IIoT functionality
11.2 OPC UA
OPC Unified Architecture (OPC UA) is a platform-independent standard with a service-oriented architecture for communication in and with industrial automation systems.
The OPC UA standard is based on the client-server principle and lets machines and devices, regardless of any preferred field bus, communicate horizontally among each other as well as vertically to the ERP system or the cloud. LioN-X provides an OPC UA server on field device level, with which an
OPC UA client can connect for information exchange secure in transmission.
11.2.1 OPC UA configuration
In delivery state , OPC UA functions are disabled . The OPC UA Server can be configured either using the Web interface or directly via a JSON Object sent in an HTTP request.
The configuration URL is: http://[ip-address]/w/config/opcua.json
The configuration can also read back as a JSON file: http://[ip-address]/r/config/opcua.json
The configuration is a JSON object. Each JSON member is a configuration element. The object must not contain all elements. Only the provided elements will be changed. All configuration changed applies only after a device restart.
116 Manual PROFINET
Version 1.1 07/2023
11 IIoT functionality
Tree overview of OPC UA objects:
11.2 OPC UA
All configuration elements are optional and do not need a specific order.
Not every element is required to be sent. This means that only configuration changes will be taken over.
Manual PROFINET
Version 1.1 07/2023
117
11.2 OPC UA 11 IIoT functionality
Optional: The configuration parameters of OPC UA can be set directly via the
Web interface. It is possible to download the Web interface for sharing with other devices.
Response:
The resulting response is a JSON object with a status field. Status should be
"0" if no error occurred and "-1" if there is an error.
In case of an error, the response contains an error array.
The error array contains an error object for each error occurred. The object consists of a field "Element" which names the config element which caused the error, and a field "Message" for the error message.
Examples:
{"status": -1, "error": [{"Element": "upcua-enable", "Message": "Boolean
expected"}]}
{"status": 0}
{"status": -1, "error": [{"Element": "root", "Message": "Not a JSON
object"}]}
118 Manual PROFINET
Version 1.1 07/2023
11 IIoT functionality
11.2.1.1 Gateway objects
Identity
Name
Device Name
Device ID
MAC address
Ordering Number
Serial Number
Production Date
Hardware Version
App Firmware Version
Fieldbus Firmware Version
IO Firmware Version
Running Fieldbus
Forcemode supported
Data type
UA_STRING
UA_STRING
UA_STRING
UA_STRING
UA_STRING
UA_STRING
UA_STRING
UA_STRING
UA_STRING
UA_STRING
UA_STRING
UA_BOOLEAN
Status (read)
Name
US present
UL present
US diagnosis
UL diagnosis
Internal Module Error diag
Data type
UA_BOOLEAN
UA_BOOLEAN
UA_BOOLEAN
UA_BOOLEAN
UA_BOOLEAN
Unit
Example
11.2 OPC UA
Forcing supported by module variant
Example
Manual PROFINET
Version 1.1 07/2023
119
11.2 OPC UA
Name
Forcemode diag
US voltage
UL voltage
Rotary position
Data type
UA_BOOLEAN
UA_DOUBLE
UA_DOUBLE
UA_UINT16
Forcing (read)
Name
Forcing active
Forcing client
Own Forcing
Forcing possible
Forcemode lock
Data type
UA_BOOLEAN
UA_STRING
UA_BOOLEAN
UA_BOOLEAN
UA_BOOLEAN
Config (read + write)
Name
IP address
Subnet Mask
Data type
UA_STRING
UA_STRING
Default Gateway IP
Suppress US diag
UA_STRING
UA_BOOLEAN
Suppress UL diag UA_BOOLEAN
Supppres Actuator Diag w/o UL UA_BOOLEAN
QuickConnect UA_BOOLEAN
Unit
V
V
11 IIoT functionality
Example
23.2
22.9
343
Example if forcemode is not active, string is empty
Indicates if OPC UA is currently forcing true if forcing by OPC UA is possible
Forcing locked by PLC
Example
120 Manual PROFINET
Version 1.1 07/2023
11 IIoT functionality 11.2 OPC UA
Process (read)
Name
Input Data
Output Data
Consuming Data
Producing Data
Commands (write)
Name
Restart
Factory reset
Forcemode enable
Forcemode disable
Arguments void void void void
Data type
UA_UINT16
UA_UINT16
UA_UINT16
UA_UINT16
Return
UA_INT32
UA_INT32
UA_INT32
UA_INT32
Example ioInput for all channels ioOutput for all channels
Data from the PLC to the device
Data from the device to the PLC
Example
Manual PROFINET
Version 1.1 07/2023
121
11.2 OPC UA 11 IIoT functionality
11.2.1.2 Ports objects
Identity
Name
Name
Type
Data type
UA_STRING
UA_STRING
Channel m ("Pin 4" / "Pin 2")
See details in
on page 123.
Status (read)
Name
Sensor Diag
Pin 1 Voltage
Pin 1 Current
Data type
UA_BOOLEAN
UA_DOUBLE
UA_INT16
Unit
V mA
Config (read + write)
Name
Pin 1 Current Limit
Data type
UA_INT16
Unit mA
Example
"X1"
"DIO"
Example
22.5
1900
Example
1000
122 Manual PROFINET
Version 1.1 07/2023
11 IIoT functionality
11.2.1.3 Channel objects
Identity (read)
Name
Name
Type
MaxOutputCurrent
Data type
UA_STRING
UA_STRING
UA_INT16
Status (read)
Name
Actuator Diag
Actuator Voltage
Actuator Current
Channel Failsafe
Data type
UA_BOOL
UA_DOUBLE
UA_INT16
UA_BOOL
Unit mA
Unit
V mA
Config (read + write)
Name
Surveillance Timeout
Failsafe Config
Data type
UA_UINT8
UA_ENUMERATION
Unit ms
Channel DIrection UA_ENUMERATION
Channel Current Limit
Auto Restart
UA_UINT16
UA_BOOL
Manual PROFINET
Version 1.1 07/2023 mA
11.2 OPC UA
Example
"X1A"
"DIO"
1300
Example
23.5
800
Example / Remarks
80 ms
Low
Hi
Hold Last
DIO
Input
Output
Inactive
2000 mA
123
11.2 OPC UA
Name
InputFilterTime
InputLogic
Data type
UA_UINT8
UA_ENUMERATION
Unit ms
Process (read)
Name
Output
Input
Consuming
Producing
Data type
UA_BOOLEAN
UA_BOOLEAN
UA_BOOLEAN
UA_BOOLEAN
Forcing (read + write)
Name
Force channel
Data type
UA_BOOLEAN
Force value
Simulate channel
UA_BOOLEAN
UA_BOOLEAN
11 IIoT functionality
Example / Remarks
3ms
NO
NC
Example / Remarks
Output type channels only.
Input type channels only.
Example / Remarks
Enable forcing with the current force value or disable forcing for this channel.
Output type channels only.
When changed by the user it will start forcing with the new value if forcing is enabled for opcua.
Output type channels only.
Enable simulation with the current force value or disable simulation for this channel.
Input type channels only.
124 Manual PROFINET
Version 1.1 07/2023
11 IIoT functionality 11.2 OPC UA
Name
Simulate value
Data type
UA_BOOLEAN
Example / Remarks
When changed by the user it will start simulation with the new value if forcing is enabled for opcua.
Input type channels only.
11.2.2 OPC UA address space
OPC UA provides different services on the LioN-X devices with which a client can navigate through the hierarchy of the address space and read or write variables. In addition, the client can monitor up to 10 attributes from the address space for value changes.
A connection to an OPC UA server is established via the endpoint URL: opc.tcp://[ip-address]:[port]
Various device data such as MAC address, device settings, diagnostics or status information can be read via Identity objects , Config objects , Status objects and Process objects .
Command objects can be read and written. This makes it possible, for example, to transfer new network parameters to the device, to use Force
Mode or to reset the entire device to its factory settings.
The following figures illustrate the OPC UA address space of the LioN-X devices. The objects and information displayed depend on the device variant used.
Manual PROFINET
Version 1.1 07/2023
125
11.2 OPC UA 11 IIoT functionality
11.2.3 OPC UA configuration - Quick start guide
Attention: Lumberg Automation
TM
is not responsible for any content of the referenced Web pages and provides no warranty for any functionality of the named third party software.
11.2.3.1 OPC UA configuration via JSON
1.
Depending on your application case, download and install Insomnia or a comparable application: https://insomnia.rest/download/
2.
Configure OPC UA:
POST:
[IP-address]/w/config/opcua.json
126 Manual PROFINET
Version 1.1 07/2023
11 IIoT functionality
3.
Read OPC UA:
GET:
[IP-address]/r/config/opcua.json
11.2 OPC UA
Manual PROFINET
Version 1.1 07/2023
127
11.3 REST API 11 IIoT functionality
11.3 REST API
The Representational State Transfer – Application Programming Interface
(REST API) is a programmable interface which uses HTTP requests to GET and POST data. This enables the access to detailed device information.
For all LioN-X variants, the REST API can be used to read the device status.
For the LioN-X multiprotocol variants, the REST API can also be used to write configuration and forcing data.
The customized Belden REST API is described in the following chapters.
11.3.1 Standard device information
Request method:
Request URL:
Parameters
Response format http GET
<ip>/info.json
n.a.
JSON
The goal of the "Standard device information" request is to get a complete snapshot of the current device status. The format is JSON.
128 Manual PROFINET
Version 1.1 07/2023
11 IIoT functionality 11.3 REST API
11.3.2 Structure
Name name order-id fw-version hw-version mac bus failsafe ip snMask gw rotarys ulPresent usVoltage_mv ulVoltage_mv inputs output
Data type string string string string string
Description
Device name
Ordering number
Firmware version
Hardware version
MAC address of the device number number string string string
0 = No connection
1 = Connection with PLC
0 = Normal operation
1 = Outputs are in failsafe
IP address of the device
Subnet Mask
Default gateway array of numbers (3) Current position of the rotary switches:
Array element 0 = x1
Array element 1 = x10
Array element 2 = x100 boolean True, if there is a UL voltage supply detected within valid range number number
US voltage supply in mV
UL voltage supply in mV (only available for devices with UL supply) array of numbers (2) Real state of digital inputs.
Element 0 = 1 Byte: Port X1
Channel A to Port X4 Channel B
Element 0 = 1 Byte: Port X5
Channel A to Port X8 Channel B array of numbers (2) Real State of digital outputs.
Element 0 =1 Byte: Port X1
Channel A to port X4 Channel B
Element 0 = 1 Byte: Port X5
Channel A to port X8 Channel B
Example
"0980 XSL 3912-
121-007D-00F"
"935 700 001"
"V.1.1.0.0 -
01.01.2021"
"V.1.00"
"3C B9 A6 F3 F6
05"
1
0
[128,3]
[55,8]
Manual PROFINET
Version 1.1 07/2023
129
11.3 REST API 11 IIoT functionality
Name consuming producing diag fieldbus
FIELDBUS
Object fieldbus_name state state_text
Data type Description array of numbers (2) Cyclic data from PLC to device array of numbers (2) Cyclic data from device to PLC array of numbers (4) Diagnostic information
Element 0 = 1 Byte:
Bit 7: Internal module error
(IME)
Bit 6: Forcemode active
Bit 3: Actuator short
Bit 2: Sensor short
Bit 1: U
L
fault
Bit 0: U
S
fault
Element 1 = 1 Byte:
Sensor short circuit ports
X1 .. X8.
Element 2 =1 Byte:
Actuator short circuit ports X1 Channel A to X4
Channel B
Element 3 = 1 Byte:
Actuator short circuit ports X5 Channel A to X8
Channel B
FIELDBUS Object
Example forcing channels string number number
FORCING Object
Array of CHANNEL
(16)
Currently used fieldbus
Fieldbus state
Textual representation of fieldbus state:
0 = Unknown
1 = Bus disconnected
2 = Preop
3 = Connected
4 = Error
5 = Stateless
Information about the forcing state of the device
Basic information about all input/output channels
130 Manual PROFINET
Version 1.1 07/2023
11 IIoT functionality
Name
CHANNEL
Object name type
Data type string number type_text config string number config_text inputState outputState forced simulated actuatorDiag sensorDiag string boolean boolean boolean boolean boolean boolean
11.3 REST API
Description
Name of channel
Hardware channel type as number:
0 = DIO
1 = Input
2 = Output
3 = Input/Output
4 = Channel not available
5 = Channel not available
6 = Channel not available
7 = Channel not available
8 = Channel not available
Textual representation of the channel type
Current configuration of the channel:
0 = DIO
1 = Input
2 = Output
3 = Channel not available
4 = Deactivated
5 = Channel not available
Textual representation of the current config
Input data (producing data) bit to the
PLC
Output data bit to the physical output pin
True, if the output pin of this channel is forced
True, if the input value to the PLC of this channel is simulated
True, if the output is in short circuit / overload condition
True, if the sensor supply (Pin 1) is in short circuit / overload condition
Example
Manual PROFINET
Version 1.1 07/2023
131
11.3 REST API 11 IIoT functionality
Name Data type maxOutputCurrent
_mA number current_mA number number voltage_mV
PORT Object port_type aux_mode string number
Description
Maximum output current of the output in mA
Measured current of the output in mA
(if current measurement is available)
Measured voltage of this output in mV
(if voltage measurement is available)
Example aux_text ds_fault ds_fault_text diag
DIAG Object error source string number string array of DIAG (n) number string message string
FORCING Object forcingActive forcingPossible boolean boolean
AuthPossible boolean ownForcing currentClient boolean string
Textual representation of the port type
Indicates the configured mode for the
Pin 2:
0 = No AUX
1 = AUX output (always on)
2 = Digital output (can be controlled by cyclic data)
3 = Digital input
Textual representation of the current aux mode
Data storage error number
Textual data storage error.
Array of port related events
"AUX Output"
Error code
Source of the current error.
Error message
Forcing information of the device
Force mode is currently active
True, if forcing is possible and force mode can be activated
True, if the JSON Interface can obtain forcing autorization
True, if forcing is performed by REST
API at the moment
Current forcing client identifier
"device"
"master"
"Supply Voltage fault"
132 Manual PROFINET
Version 1.1 07/2023
11 IIoT functionality 11.3 REST API
Name digitalOutForced digitalOutMask digitalInForced digitalInMask
Data type Description array of numbers (2) The force values of all 16 digital output channels.
array of numbers (2) The forcing mask of all 16 digital output channels.
array of numbers (2) The force values of all 16 digital input channels.
array of numbers (2) The forcing mask of all 16 digital input channels.
Example
11.3.3 Configuration and forcing
Method:
URL:
Parameters:
Post-Body:
POST
<ip>/w/force.json
None
JSON Object
Property forcemode
Data type boolean portmode digital
array ( Port mode object ) array ( Digital object
)
Table 35: Root object
Example values true / false
Description
Forcing authority on/off
Manual PROFINET
Version 1.1 07/2023
133
11.3 REST API
Property port channel
Data type integer integer direction inlogica inlogicb string string string
Table 36: Port mode object
Property port channel force_dir
Data type integer string string force_value integer
Table 37: Digital object
11 IIoT functionality
Example values
0..7
"a","b"
"dio","di","do", "off", "aux"
"no","nc"
"no","nc"
Remarks optional default is
"a"
Example values
0..7
"a","b"
"phys_out","plc_in","clear"
0,1
Remarks optional default is
"phys_out"
134 Manual PROFINET
Version 1.1 07/2023
11 IIoT functionality 11.4 CoAP server
11.4 CoAP server
The Co nstrained A pplication P rotocol (CoAP) is a specialized Internet application protocol for constrained networks such as lossy or low power networks. CoAP is useful especially in M2M (Machine to Machine) communication and can be used to translate simplified HTTP requests of low speed networks.
CoAP is based on the Server-Client principle and a service layer protocol that lets nodes and machines communicate with each other. The LioN-X multiprotocol variants provide CoAP server functionalities via a REST API interface over UDP.
11.4.1 CoAP configuration
In delivery state, CoAP functions are disabled . The CoAP server can be configured either using the Web interface or directly via a JSON object sent
in an HTTP request. For more information see chapter CoAP configuration -
Quick start guide on page 138.
The configuration URL is: http://[ip-address]/w/config/coapd.json
The configuration can also read back as a JSON file: http://[ip-address]/r/config/coapd.json
The configuration is a JSON object. Each JSON member is a configuration element. The object must not contain all elements. Only the provided elements will be changed. The configuration changes apply only after a device restart.
Manual PROFINET
Version 1.1 07/2023
135
11.4 CoAP server 11 IIoT functionality
The following configuration elements are available (default values in bold):
Element enable port
Data type boolean integer
(0 to 65535)
Description
Master switch for the CoAP server
Port of the CoAP server
Example data true / false
5683
Table 38: CoAP configuration
CoAP response:
The resulting response is a JSON object with a "status" field. Status should be "0" if no error occurred, and "-1" if there is an error.
In case of an error, the response contains an error array.
The error array contains an error object for each error occurred. The object consists of a field "Element" which names the config element that caused the error, and of a field "Message" for the error message.
Examples:
{"status": -1, "error": [{"Element": "upcua-enable", "Message": "Boolean
expected"}]}
{"status": 0}
{"status": -1, "error": [{"Element": "root", "Message": "Not a JSON
object"}]}
11.4.2 REST API access via CoAP
A connection to the CoAP server running on the LioN-X multiprotocol variants can be established via the following URL: coap://[ip-address]:[port]/[api]
For LioN-X, the following REST API Requests (JSON format) can be accessed via a CoAP endpoint:
136 Manual PROFINET
Version 1.1 07/2023
11 IIoT functionality
Type
GET
GET
GET
GET
GET
GET
GET
GET
GET
GET
API
/r/status.lr
/r/system.lr
/info.json"
/r/config/net.json
/r/config/mqtt.json
/r/config/opcua.json
/r/config/coapd.json
/r/config/syslog.json
/contact.json
/fwup_status
Table 39: REST API access via CoAP
11.4 CoAP server
Note
Manual PROFINET
Version 1.1 07/2023
137
11.4 CoAP server 11 IIoT functionality
11.4.3 CoAP configuration - Quick start guide
Attention: Lumberg Automation
TM
is not responsible for any content of the referenced Web pages and provides no warranty for any functionality of the named third party software.
11.4.3.1 CoAP configuration via JSON
1.
Depending on your application case, download and install Insomnia or a comparable application: https://insomnia.rest/download/
2.
Configure CoAP:
POST:
[IP-address]/w/config/coapd.json
138 Manual PROFINET
Version 1.1 07/2023
11 IIoT functionality
3.
Read CoAP configuration:
GET:
[IP-address]/r/config/coapd.json
11.4 CoAP server
Manual PROFINET
Version 1.1 07/2023
139
11.5 Syslog 11 IIoT functionality
11.5 Syslog
The LioN-X multiprotocol variants provide a Syslog client which can connect with a configured Syslog server and is able to log messages.
Syslog is a platform-independent standard for logging messages. Each message contains a timestamp as well as information about the severity level and the subsystem. The Syslog protocol RFC5424 is based on the Server-
Client principle and lets machines and devices send messages in the network and collect them centrally. (For more details on the used syslog standard, please refer to https://datatracker.ietf.org/doc/html/rfc5424 .)
LioN-X supports the storage of 256 messages in a ring buffer which are sent to the configured Syslog server. When the ring is full with 256 messages, the oldest message is always replaced by the newly arriving messages. All messages can be saved on the Syslog server. The Syslog client will not store any message permanently.
11.5.1 Syslog configuration
In delivery state , Syslog functions are disabled . The Syslog client can be configured either using the Web interface or directly via a JSON object sent in an HTTP request. For more information see chapter
on page 143.
The configuration URL is: http://[ip-address]/w/config/syslog.json
The configuration can also read back as a JSON file: http://[ip-address]/r/config/syslog.json
The configuration is a JSON object. Each JSON member is a configuration element. The object must not contain all elements. Only the provided elements will be changed. The configuration changes apply only after a device restart.
140 Manual PROFINET
Version 1.1 07/2023
11 IIoT functionality 11.5 Syslog
The following configuration elements are available (default values in bold):
Element syslog-enable global-severity server-address
Data type boolean integer
Description
Master switch for the Syslog client
Severity level of Syslog client
0 – Emergency
1 – Alert
2 – Critical
3 – Error
4 – Warning
5 – Notice
6 – Info
7 – Debug
The client will log all messages of severity according to the setting, including all below levels.
IP address of the Syslog server
Example data true / false
0/1/2/ 3 /4/5/6/7 server-port server-severity string (IP address) integer (0 to
65535) integer (0 to 7)
Server port of the Syslog server
192.168.0.51 (Default: null )
514
0/1/2/ 3 /4/5/6/7 Severity level of Syslog server
0 – Emergency
1 – Alert
2 – Critical
3 – Error
4 – Warning
5 – Notice
6 – Info
7 – Debug
Table 40: Syslog configuration
Manual PROFINET
Version 1.1 07/2023
141
11.5 Syslog 11 IIoT functionality
Syslog response:
The resulting response is a JSON object with a "status" field. Status should be "0" if no error occurred, and "-1" if there is an error.
In case of an error, the response contains an error array.
The error array contains an error object for each error occurred. The object consists of a field "Element" which names the config element that caused the error, and of a field "Message" for the error message.
Examples:
{"status": -1, "error": [{"Element": "upcua-enable", "Message": "Boolean
expected"}]}
{"status": 0}
{"status": -1, "error": [{"Element": "root", "Message": "Not a JSON
object"}]}
142 Manual PROFINET
Version 1.1 07/2023
11 IIoT functionality 11.5 Syslog
11.5.2 Syslog configuration - Quick start guide
Attention: Lumberg Automation
TM
is not responsible for any content of the referenced Web pages and provides no warranty for any functionality of the named third party software.
11.5.2.1 Syslog configuration via JSON
1.
Depending on your application case, download and install Insomnia or a comparable application: https://insomnia.rest/download/
2.
Configure Syslog:
POST:
[IP-address]/w/config/syslog.json
Manual PROFINET
Version 1.1 07/2023
143
11.5 Syslog
3.
Read Syslog configuration:
GET:
[IP-address]/r/config/syslog.json
11 IIoT functionality
144 Manual PROFINET
Version 1.1 07/2023
11 IIoT functionality 11.6 Network Time Protocol (NTP)
11.6 Network Time Protocol (NTP)
The LioN-X multiprotocol variants provide an NTP client (version 3) which can connect with a configured NTP server and is able to synchronize the network time at a configurable interval.
NTP is a network protocol which uses UDP datagrams to send and receive timestamps in order to synchronize with a local clock. The NTP protocol
RFC1305 is based on the Server-Client principle and exclusively supplies the synchronization with Coordinated Universal Time (UTC). (For more details on the used NTP standard, please refer to https://datatracker.ietf.org/doc/html/ rfc1305 .)
11.6.1 NTP configuration
In delivery state , the NTP client is disabled . The NTP client can be configured either using the Web interface or directly via a JSON object sent in an HTTP request. For more information see chapter
Quick start guide on page 147.
The configuration URL is: http://[ip-address]/w/config/ntpc.json
The configuration can also read back as a JSON file: http://[ip-address]/r/config/ntpc.json
The configuration is a JSON object. Each JSON member is a configuration element. The object must not contain all elements. Only the provided elements will be changed. The configuration changes apply only after a device restart.
Manual PROFINET
Version 1.1 07/2023
145
11.6 Network Time Protocol (NTP) 11 IIoT functionality
The following configuration elements are available (default values in bold):
Element
NTP client state
Server address
Server port
Update interval
Data type boolean string integer integer
Description
Master switch for the NTP client
IP address of the NTP server
Port of the NTP server
Interval at which the client will connect with the configured NTP server (see table row "Server address").
Note: This value is in seconds.
Example data true / false
192.168.1.50
123
1/2/10/ 60
Table 41: NTP configuration
NTP response:
The resulting response is a JSON object with a "status" field. Status should be "0" if no error occurred, and "-1" if there is an error.
In case of an error, the response contains an error array.
The error array contains an error object for each error occurred. The object consists of a field "Element" which names the configuration element that caused the error, and of a field "Message" for the error message.
Examples:
{"status": -1, "error": [{"Element": "ntpc-enable", "Message": "Boolean
expected"}]}
{"status": 0}
{"status": -1, "error": [{"Element": "root", "Message": "Not a JSON
object"}]}
146 Manual PROFINET
Version 1.1 07/2023
11 IIoT functionality 11.6 Network Time Protocol (NTP)
11.6.2 NTP configuration - Quick start guide
Attention: Lumberg Automation
TM
is not responsible for any content of the referenced Web pages and provides no warranty for any functionality of the named third party software.
11.6.2.1 NTP configuration via JSON
1.
Depending on your application case, download and install Insomnia or a comparable application: https://insomnia.rest/download/
2.
Configure NTP:
POST:
[IP-address]/w/config/ntpc.json
Manual PROFINET
Version 1.1 07/2023
147
11.6 Network Time Protocol (NTP)
3.
Read NTP configuration:
GET:
[IP-address]/r/config/ntpc.json
11 IIoT functionality
148 Manual PROFINET
Version 1.1 07/2023
12 The integrated Web server
12 The integrated Web server
All device variants are equipped with an integrated Web server which makes functions for the device configuration and the display of status and diagnostic information available via a Web interface.
The Web interface provides an overview of the configuration and status of the device. It is also possible to use the Web interface to trigger a reboot, reset to the factory defaults, or perform a firmware update.
Enter "http://" followed by the IP address, such as "http://192.168.1.5", in your
Web browser’s address bar. If the status page of the device is not displayed, check your browser and firewall settings.
Manual PROFINET
Version 1.1 07/2023
149
12.1 LioN-X 0980 XSL... variants 12 The integrated Web server
12.1 LioN-X 0980 XSL... variants
12.1.1 The Status page
The status page provides a quick overview of the current state of the device.
The left side shows a graphical representation of the module with all its LEDs and the positions of the rotary encoding switches.
The right side shows the "Device Information" table with some basic data for the module; for example, the variant, the cyclic communication status and a diagnostic indicator. The indicator shows whether diagnostics for the module exist.
The "Port Information" table shows the configuration and state of the I/O ports.
150 Manual PROFINET
Version 1.1 07/2023
12 The integrated Web server
12.1.2 The Ports page
12.1 LioN-X 0980 XSL... variants
The page shows detailed port information. In the field Port Diagnosis , incoming and outgoing diagnostics are displayed as clear text. Pin 2 and
Pin 4 contain information about the configuration and state of the port.
Manual PROFINET
Version 1.1 07/2023
151
12.1 LioN-X 0980 XSL... variants
12.1.3 The System page
12 The integrated Web server
The System page shows the basic information for the module like Firmware version, Device information, Ethernet, Network and Fieldbus information.
Restart Device
The module initializes a software reset.
152 Manual PROFINET
Version 1.1 07/2023
12 The integrated Web server 12.1 LioN-X 0980 XSL... variants
Reset to Factory Settings
The module restores to the default factory settings.
IP Settings
Use this parameter to change the current IP address of the module.
For PROFINET, this is only useful during commissioning. Normally, the PLC sets the IP address at start-up by detecting the PROFINET module via its device name.
Firmware Update
The module initializes a Firmware update.
For a firmware update choose the *.ZIP
container available on our website or ask our support team. Afterwards follow the instructions shown on your screen.
Manual PROFINET
Version 1.1 07/2023
153
12.1 LioN-X 0980 XSL... variants
12.1.4 The User page
12 The integrated Web server
The User page provides the user management of the Web interface.
New users with access rights "Admin" or "Write" can be added here. For security reasons please change the default admin password immediately after configuring the device.
Default user login data:
D User: admin
D Password: private
154 Manual PROFINET
Version 1.1 07/2023
13 Technical data
13 Technical data
The following sections give an overview of the most important functional data needed to operate the device. For further information and detailed technical data, see the respective Data Sheet of your required product in the product specific download area on catalog.belden.com
.
Manual PROFINET
Version 1.1 07/2023
155
13.1 General 13 Technical data
13.1 General
Protection class
(Only applies if the connectors are screwed together or if protective caps are used.)
Ambient temperature (during operation and storage)
IP65
IP67
IP69K
Weight
Ambient moisture
Housing material
Surface finish
Flammability class
Vibration resistance (oscillation)
DIN EN 60068-2-6 (2008-11)
Shock resistance
DIN EN 60068-2-27 (2010-02)
Fastening torques
Permitted cables
0980 XSL 3x00-121...
0980 XSL 3x01-121...
0980 XSL 3x03-121...
-40 °C .. +70 °C
(-40 °F .. +158 °F)
LioN-X 60 mm approx. 500 gr. (17.6 oz)
Max. 98% RH
(For UL applications: Max. 80% RH)
Die-cast zinc
Frosted nickel
UL 94 (IEC 61010)
15 g/5–500 Hz
50 g/11 ms
+/- X, Y, Z
M4 fixing screws 1 Nm
M4 ground connection
M12 connector
1 Nm
0.5 Nm
Ethernet cables according to IEEE 802.3, min. CAT 5 (shielded)
Max. length of 100 m, not routed out of facility (= local network)
Table 42: General information
3 Not under UL investigation.
156 Manual PROFINET
Version 1.1 07/2023
13 Technical data 13.2 PROFINET protocol
13.2 PROFINET protocol
Protocol
Conformance Class
Netload Class
Update cycle
GSDML file
Transmission rate
Transmission procedure
Autonegotiation
Vendor ID
Device ID
Supported Ethernet protocols
PROFINET feature
Switch functionality
PROFINET interface
Connections
Autocrossing
Electrically isolated Ethernet ports -> FE
Table 43: PROFINET protocol
PROFINET IO device V2.41
C (CC-C)
III
1 ms
GSDML-V2.41-LumbergAutomation-LioN-Xyyyymmdd.xml
100 Mbit/s, full duplex
100BASE-TX is supported
16A
H
0x0400 (same for all LioN-X variants)
Ping
ARP
LLDP
SNMPv1 (network diagnostics)
D Read Community: public
D Write Community: private
DCP
HTTP
TCP/IP
MRP Client
Fast Start UP (Prioritized startup)
Shared Device
Integrated
IRT is supported
2 M12 sockets, 4-pin, D-coded (see pin assignments)
2 M12 Hybrid male/female, 8-pin is supported
2000 V DC
Manual PROFINET
Version 1.1 07/2023
157
13.3 Power supply of the module electronics/sensors
13 Technical data
13.3 Power supply of the module electronics/ sensors
Port X03, X04
Nominal voltage U
S
Current U
S
Voltage range
Power consumption of module electronics
Power supply interruption
Voltage ripple U
S
Current consumption sensor system
(Pin 1)
M12-L-coded Power, connector/socket, 5-pole
Pin 1 / Pin 3
24 V DC (SELV/PELV)
Max. 16 A
21 .. 30 V DC
Typically 160 mA (+/-20 % at U
S
nominal voltage)
Max. 10 ms
Max. 5 %
0980 XSL 3x00-121...
0980 XSL 3x01-121...
0980 XSL 3x03-121...
Port X1 .. X8
(Pin 1)
Port X1 .. X4
(Pin 1) max. 4 A per port
(at T ambient
= 30° C) max. 4 A per port
(at T ambient
= 30° C)
Voltage level of the sensor power supply
Short circuit/overload protection of sensor supply
Reverse polarity protection
Operational indicator
(U
S
)
Min. (U
S
– 1.5 V)
Yes, per port
Yes
LED green:
LED red:
18 V (+/- 1 V) < U
S
U
S
< 18 V (+/- 1 V)
Table 44: Information on the power supply of the module electronics/ sensors
Attention: Do not exceed the following maximum currents for the sensor supply:
D Max. 4.0 A per port
158 Manual PROFINET
Version 1.1 07/2023
13 Technical data 13.4 Power supply of the actuators
D Max. 5.0 A for each port pair X1/X2, X3/X4, X5/X6, X7/X8
D Max. 9.0 A in total for the whole port group X1 .. X8
Pay attention to the derating!
13.4 Power supply of the actuators
Port X03, X04
Nominal voltage U
L
Voltage range
Current U
L
Voltage ripple U
L
Reverse polarity protection
Operational indicator (U
L
)
M12_L-coded Power, connector/socket, 5-pole
Pin 2 / Pin 4
24 V DC (SELV/PELV)
18 .. 30 V DC
Max. 16 A
Max. 5 %
Yes
LED green: 18 V (+/- 1 V) < U
L
LED red: U
L
< 18 V (+/- 1 V) or U
L
> 30 V (+/- 1 V)
* if "Report U
L
supply voltage fault" is enabled.
Table 45: Information on the power supply of the actuators
13.5 I/O ports
0980 XSL 3900-121...
0980 XSL 3901-121...
0980 XSL 39x3-121...
Ports X1 .. X8
Ports X1 .. X8
Ports X1 .. X4
Ports X5 .. X8
Table 46: I/O ports: Overview of functions
DI, DO
DI
DI
DO
M12 socket, 5-pin
Manual PROFINET
Version 1.1 07/2023
159
13.5 I/O ports 13 Technical data
13.5.1 Digital inputs
Input connection 0980 XSL 3900-121...
0980 XSL 3901-121...
0980 XSL 39x3-121...
24 V DC Nominal input voltage
Input current
Channel type
Number of digital inputs
Status indicator
Diagnostic indicator
Typically 3 mA
Normally open, p-switching
0980 XSL 3900-121...
0980 XSL 3901-121...
0980 XSL 39x3-121...
yellow LED for Channel A (Pin 4) white LED for Channel B (Pin 2) red LED per port
X1 .. X8
X1 .. X4
Table 47: I/O ports configured as digital input
Type 3 as per IEC
61131-2
16
8
13.5.2 Digital outputs
Attention: Do not exceed the following maximum currents for the sensor supply:
D Max. 2.0 A per port
D Max. 5.0 A for each port pair X1/X2, X3/X4, X5/X6, X7/X8
D Max. 9.0 A in total for the whole port group X1 .. X8 (X5 .. X8 at
8DI8DO devices)
Pay attention to the derating!
160 Manual PROFINET
Version 1.1 07/2023
13 Technical data 13.5 I/O ports
Output type
Nominal output voltage per channel
Signal status “1”
Signal status “0”
Max. output current per device
Max. output current per channel normally open, p-switching min. (U
L
-1 V) max. 2 V
0980 XSL 3900-121...
0980 XSL 39x3-121...
0980 XSL 3900-121... (X1 .. X8)
0980 XSL 39x3-121... (X5 .. X8) yes/yes Short-circuit/overload protected
Behavior in case of short circuit or overload
Number of digital outputs
9 A
9 A
2 A
2 A deactivation with automatic power-on (parameterized)
Status indicator
Diagnostic indicator
0980 XSL 3900-121... (X1 .. X8) 16
0980 XSL 39x3-121... (X5 .. X8) yellow LED per output Channel A (Pin 4) white LED per output Channel B (Pin 2) red LED per channel
8
Table 48: I/O ports configured as digital output
Warning: If devices with electric isolation and devices without electric isolation are used within the same system, the electric isolation of all connected devices is annulled.
Manual PROFINET
Version 1.1 07/2023
161
13.6 LEDs 13 Technical data
13.6 LEDs
LED
U
L
U
S
Color
Green
Red
*
OFF
Green
Red
X1 .. X8 A
Red flashing
OFF
Yellow
Red
X1 .. X8 B
OFF
White
Red
P1 Lnk/Act
P2 Lnk/Act
OFF
Green
Yellow flashing
OFF
Description
Auxiliary sensor/actuator voltage OK
18 V (+/- 1 V) < U
L
< 30 V (+/- 1 V)
Auxiliary sensor/actuator voltage LOW
U
L
< 18 V (+/- 1 V) or U
L
> 30 V (+/- 1 V)
*
if "Report U
L
supply voltage fault" is enabled.
None of the above conditions.
System/sensor voltage OK
18 V (+/- 1 V) < U
S
< 30 V (+/- 1 V)
System/sensor voltage LOW
U
S
< 18 V (+/- 1 V) or U
S
> 30 V (+/- 1 V)
Device performs a factory reset (position of rotary encoding switches: 9-7-9)
None of the above conditions.
Status of digital input or digital output on pin 4 line "on".
Short circuit on pin 4 line.
/ Overload or short circuit on L+ (pin 1) line
/ communication error
None of the above conditions.
Status of digital input or digital output on pin 2 line "on".
Short circuit on pin 2 line.
/ Overload or short circuit on L+ (pin 1) line
/ communication error
None of the above conditions.
Ethernet connection to another subscriber exists. Link detected.
Data exchange with another subscriber.
No connection to another subscriber. No link, no data exchange.
162 Manual PROFINET
Version 1.1 07/2023
13 Technical data 13.6 LEDs
LED
BF
Color
Red
Red flashing at
2 Hz
OFF
Description
Bus fault. No configuration, no or slow physical connection.
Link exists but no communication link to the PROFINET controller.
PROFINET controller has established an active connection to the device.
PROFINET module diagnostic alarm active.
Watchdog time-out; fail safe mode is active.
DIA Red
Red flashing at
1 Hz
Red flashing at
2 Hz, 3 sec
Red double flash
OFF
DCP signal service is initiated via the bus.
Firmware update
None of the above conditions.
Table 49: Information on the LED colors
Manual PROFINET
Version 1.1 07/2023
163
13.7 Data transfer times 13 Technical data
13.7 Data transfer times
The following tables give an overview of the internal data transfer times of
LioN-X.
There are three measured data direction values for each use case:
D PLC to DO: Transfer of a changed PLC output data to the digital output channel.
D DI to PLC: Transfer of a changed digital input signal on digital input channel to PLC.
D Round-trip time (RTT): Transfer of a changed PLC output data to digital output. The digital output is connected to a digital input. Transfer of the changed digital input signal on the channel to PLC. RTT = [PLC to DO]
+ [DI to PLC].
The measured values are taken from the ethernet data transmission line. The values are therefore without PLC processing times and PLC cycle time.
For calculation of user specific data transfer and round-trip times of possible input filters, PLC processing and cycles times must be taken into calculation.
164 Manual PROFINET
Version 1.1 07/2023
13 Technical data 13.7 Data transfer times
Use case 1:
LioN-X Digital-I/O configuration with enabled Web interface and disabled IIoT protocols
16DIO variant (0980 XSL 3900-121-007D-01F):
Data direction
PLC to DO
DI to PLC
RTT
Data transfer time in ms
Minimum
2.2
Average
3.6
3.1
6.0
3.0
7.6
Maximum
5.0
4.7
9.0
8DI/8DO variant without galvanic isolation (0980 XSL 3913-121-007D-01F):
Data direction
PLC to DO
DI to PLC
RTT
Data transfer time in ms
Minimum Average
1.9
2.1
4.0
3.2
2.6
5.8
Maximum
4.7
3.1
7.0
8DI/8DO variant with galvanic isolation (0980 XSL 3903-121-007D-01F):
Data direction
PLC to DO
DI to PLC
RTT
Data transfer time in ms
Minimum Average
2.2
3.3
6.0
3.6
4.0
7.6
Maximum
5.3
4.6
9.0
Manual PROFINET
Version 1.1 07/2023
165
13.7 Data transfer times 13 Technical data
Use case 2:
LioN-X Digital-I/O configuration with enabled Web interface and enabled IIoT protocols
16DIO variant (0980 XSL 3900-121-007D-01F):
Data direction
PLC to DO
DI to PLC
RTT
Data transfer time in ms
Minimum
3.4
Average
5.1
5.8
10.0
6.4
11.5
Maximum
7.6
7.6
14.0
8DI/8DO variant without galvanic isolation (0980 XSL 3913-121-007D-01F):
Data direction
PLC to DO
DI to PLC
RTT
Data transfer time in ms
Minimum Average
3.2
3.3
7.0
4.8
3.8
8.6
Maximum
7.1
4.3
11.0
8DI/8DO variant with galvanic isolation (0980 XSL 3903-121-007D-01F):
Data direction
PLC to DO
DI to PLC
RTT
Data transfer time in ms
Minimum Average
3.5
5.7
10.0
5.2
6.4
11.6
Maximum
7.6
7.1
14.0
166 Manual PROFINET
Version 1.1 07/2023
14 Accessories
14 Accessories
In order to get access to various types of accessories, please visit our
Web page: http://www.beldensolutions.com
Manual PROFINET
Version 1.1 07/2023
167
advertisement