- Home
- Domestic appliances
- Large home appliances
- Dishwashers
- Hoshizaki
- JWE-2400CUA-R-25B
- Service manual
Hoshizaki JWE-2400CUA-L-25B, JWE-2400CUA-R-25B Service Manual
Add to My manuals79 Pages
Hoshizaki JWE-2400CUA-R-25B is a high-performance commercial dishwasher designed to meet the demands of busy foodservice operations. With its advanced features and reliable construction, this unit delivers exceptional cleaning results while maximizing efficiency and minimizing operating costs.
advertisement
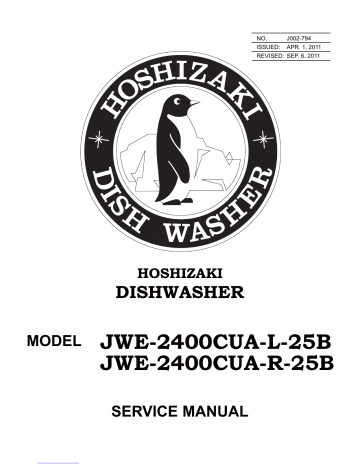
NO. J002-794
ISSUED: APR. 1, 2011
REVISED: SEP. 6, 2011
HOSHIZAKI
DISHWASHER
MODEL
JWE-2400CUA-L-25B
JWE-2400CUA-R-25B
SERVICE MANUAL
IMPORTANT
Only qualifi ed service technicians should install, service, and maintain the unit. No service or maintenance should be undertaken until the technician has thoroughly read this Service Manual. Failure to service and maintain the equipment in accordance with this manual may adversely affect safety, performance, component life, and warranty coverage.
Hoshizaki provides this manual primarily to assist qualifi ed service technicians in the maintenance and service of the unit.
Should the reader have any questions or concerns which have not been satisfactorily addressed, please call, write, or send an e-mail message to the Hoshizaki Technical
Support Department for assistance.
HOSHIZAKI AMERICA, INC.
618 Highway 74 South
Peachtree City, GA 30269
Attn: Hoshizaki Technical Support Department
Phone: 1-800-233-1940 Technical Support
Fax: 1-800-843-1056
E-mail: [email protected]
Web Site: www.hoshizaki.com
NOTE: To expedite assistance, all correspondence/communication MUST include the following information:
• Complete and detailed explanation of the problem.
IMPORTANT
This manual should be read carefully before the unit is serviced or maintenance operations are performed. Only qualifi ed service technicians should install, service, and maintain the unit. Read the warnings contained in this booklet carefully as they give important information regarding safety. Please retain this booklet for any further reference that may be necessary.
CONTENTS
I. Specifi cations ------------------------------------------------------------------------------------------------ 1
A. Specifi cation Sheet ------------------------------------------------------------------------------------- 1
1. JWE-2400CUA-L-25B ------------------------------------------------------------------------------ 1
2. JWE-2400CUA-R-25B ------------------------------------------------------------------------------ 2
B. Nameplate Rating --------------------------------------------------------------------------------------- 3
C. Dimensions/Connections ------------------------------------------------------------------------------ 4
1. JWE-2400CUA-L-25B ------------------------------------------------------------------------------ 4
2. JWE-2400CUA-R-25B ------------------------------------------------------------------------------ 5
II. General Information ---------------------------------------------------------------------------------------- 6
A. Construction ---------------------------------------------------------------------------------------------- 6
1. Dishwasher -------------------------------------------------------------------------------------------- 6
2. Booster Tank ------------------------------------------------------------------------------------------ 7
3. Control Box -------------------------------------------------------------------------------------------- 8
B. Functions -------------------------------------------------------------------------------------------------- 9
1. Increasing Rinse Water Flow Rate -------------------------------------------------------------- 9
C. Sequence of Operation -------------------------------------------------------------------------------- 9
1. Auto Fill Cycle ----------------------------------------------------------------------------------------- 9
2. Ready Cycle (Unit Inactive) ----------------------------------------------------------------------10
3. Wash Cycle/Rinse Cycle --------------------------------------------------------------------------10
4. Table Limit Switch -----------------------------------------------------------------------------------11
5. Emergency Stop Button ---------------------------------------------------------------------------11
6. Drain----------------------------------------------------------------------------------------------------11
D. Sequence of Operation Flow Chart ----------------------------------------------------------------12
E. Timing Chart ---------------------------------------------------------------------------------------------13
1. Auto Fill Cycle ----------------------------------------------------------------------------------------13
2. Wash Cycle/Rinse Cycle --------------------------------------------------------------------------14
F. Control Board and Operation Board ---------------------------------------------------------------15
1. Control Board Location ----------------------------------------------------------------------------15
2. Control Board Layout ------------------------------------------------------------------------------16
3. Control Board Diagram ----------------------------------------------------------------------------17
4. Operation Panel Layout ---------------------------------------------------------------------------18
5. Features -----------------------------------------------------------------------------------------------18
6. Controls, Adjustments, and Lamps -------------------------------------------------------------18
7. Service Menu and Error Log ---------------------------------------------------------------------19
8. Temperature Display -------------------------------------------------------------------------------21
9. Error Codes ------------------------------------------------------------------------------------------21
10. Buzzer -------------------------------------------------------------------------------------------------21
11. Operation Time Display ----------------------------------------------------------------------------22 i
12. Special Modes ---------------------------------------------------------------------------------------22
III. Service Diagnosis ----------------------------------------------------------------------------------------24
A. Diagnostic Procedure ---------------------------------------------------------------------------------24
B. Error Codes ----------------------------------------------------------------------------------------------26
1. Error Code Table ------------------------------------------------------------------------------------26
2. Error Code Log --------------------------------------------------------------------------------------27
3. Error Code Details ----------------------------------------------------------------------------------28
C. Service Flow Charts -----------------------------------------------------------------------------------41
1. Unit Will Not Start -----------------------------------------------------------------------------------41
2. Dishes Not Clean -----------------------------------------------------------------------------------43
3. Inadequate Rinse -----------------------------------------------------------------------------------45
4. Dishwasher Will Not Start Wash/Rinse Cycle -----------------------------------------------46
5. No or Inadequate Detergent/Rinse Aid Supply ----------------------------------------------47
6. Wash Tank Water Boils ----------------------------------------------------------------------------47
7. Wash Tank Water Not Draining ------------------------------------------------------------------48
D. Float Switch Check and Cleaning ------------------------------------------------------------------49
1. Float Switch Check ---------------------------------------------------------------------------------49
2. Float Switch Cleaning ------------------------------------------------------------------------------49
E. Thermistor Check --------------------------------------------------------------------------------------50
IV. Removal and Replacement of Components -------------------------------------------------------51
A. Removal of Panels -------------------------------------------------------------------------------------51
B. Removal and Replacement of Wash Pump Motors -------------------------------------------51
C. Removal and Replacement of Rinse Pump Motor ---------------------------------------------52
D. Removal and Replacement of Gear Motor ------------------------------------------------------55
E. Removal and Replacement of Conveyor ---------------------------------------------------------56
F. Removal and Replacement of Crankshaft --------------------------------------------------------57
G. Removal and Replacement of Control Box ------------------------------------------------------58
H. Removal and Replacement of Thermistor -------------------------------------------------------58
I. Removal and Replacement of Control Board or Operation Board --------------------------59
1. Control Board ----------------------------------------------------------------------------------------59
2. Operation Board -------------------------------------------------------------------------------------60
J. Removal and Replacement of Heater -------------------------------------------------------------61
K. Removal and Replacement of Float Switch -----------------------------------------------------62
L. Removal and Replacement of Thermostat -------------------------------------------------------63
V. Cleaning and Maintenance Instructions -------------------------------------------------------------64
A. Daily Maintenance -------------------------------------------------------------------------------------64
B. Weekly Maintenance ----------------------------------------------------------------------------------69
1. Heater --------------------------------------------------------------------------------------------------69
2. Exterior ------------------------------------------------------------------------------------------------69
C. Monthly Maintenance ---------------------------------------------------------------------------------69
1. Water Supply Line ----------------------------------------------------------------------------------69
D. Descaling (As Required) -----------------------------------------------------------------------------70
E. Shutdown -------------------------------------------------------------------------------------------------70
F. Long Storage, Relocation, Disposal, Transfer ---------------------------------------------------72
VI. Operating Instructions -----------------------------------------------------------------------------------72
VII. Technical Information -----------------------------------------------------------------------------------73
A. Water Circuit ---------------------------------------------------------------------------------------------73
B. Wiring Diagram -----------------------------------------------------------------------------------------74 ii
Important Safety Information
Throughout this manual, notices appear to bring your attention to situations which could result in death, serious injury, or damage to the unit.
WARNING
Indicates a hazardous situation which could result in death or serious injury.
NOTICE Indicates a situation which could result in damage to the unit or property.
IMPORTANT Indicates important information about the use and care of the unit.
WARNING
This product should be destined only to the use for which it has been expressly conceived. Any other use should be considered improper and therefore dangerous. The manufacturer cannot be held responsible for injury or damage resulting from improper, incorrect, and unreasonable use.
To reduce the risk of death, electric shock, serious injury, or fi re, follow basic precautions including the following:
• Only qualified service technicians should install, service, and maintain the unit.
• Electrical connection must be hard-wired and must meet national, state, and local electrical code requirements. Failure to meet these code requirements could result in death, electric shock, serious injury, fi re, or severe damage to equipment.
• This unit requires independent power supplies for the dishwasher and for the booster tank. See the nameplate for proper voltage and breaker/fuse sizes.
Failure to use proper breakers or fuses can result in tripped breakers, blown fuses, or damage to existing wiring. This could lead to heat generation or fi re.
• THIS UNIT MUST BE GROUNDED.
Failure to properly ground this unit could result in death or serious injury.
• Use the “ON/OFF” button on the operation panel to turn off the unit, then turn off the dishwasher and booster tank power supplies before servicing. Lockout/
Tagout to prevent the power supplies from being turned back on inadvertently.
• Do not make any alterations to the unit. Alterations could result in electric shock, injury, fi re, or damage to the unit.
• To avoid possible burns and spills, be sure to drain the wash tank and internal booster tank and let the components cool before servicing. When draining the internal booster tank, wait until the water temperature falls below 104°F (40°C).
• When disassembling components that have been in contact with detergent, wear rubber gloves and goggles. Before starting disassembly, thoroughly read the detergent safety instructions. Contact with skin may cause irritation and contact with eyes may cause blindness.
• When using an acidic descaling cleaner, wear rubber gloves and goggles.
Contact with skin may cause irritation, and contact with eyes may cause blindness. Do not use or mix with a dishwashing detergent. Some detergents may generate toxic chlorine gas.
iii
I. Specifi cations
A. Specifi cation Sheet
1. JWE-2400CUA-L-25B
AC SUPPLY VOLTAGE
POWER SUPPLY CAPACITY
AMPERAGE
STARTING AMPERAGE
ELECTRICAL COMSUMPTION
HEATER
DISHWASHER SIDE
3 phase 3-wire 208-230V/60Hz (±10%) /
208V : 18.4kVA(51.1A)
230V : 22.1kVA(55.5A)
Max Running 51.2A
Rated Motor 9.0A
26.0A
Max 19.86kW
Rated Motor 3.06kW
Power Factor 84%
16.80kW(230V)
19-3/4" × 19-3/4"(500 × 500mm)
16 plates (9.1” DIA)
BOOSTER SIDE
2 power supply lines 㩷
240/200/160racks/hour 㩷 adjustable in 3 steps (rotary switch)
114Gal/hour(432L/hour), 0.48 Gal/rack(1.8L/rack) - at 240rack/hour
20.5" (520mm)
Left to Right
W57.3" × D27.6" × H58.1" (W1,455 × D700 × H1,475mm)
Stainless Steel
Vertically Sliding Service Panel(Opening:W25.6" × H18.9")
Stainless Steel Adjustable 9.4" - 11.0"
208V : 20.6kVA(57.2A)
230V : 25.3kVA(63.5A)
Max Running 63.3A
Max 25.20kW
25.20kW(230V)
RACK SIZE
NUMBER OF LARGE DISHES / RACK
CAPACITY
WATER COMSUMPTION
PASSING HEIGHT
DIRECTION OF OPERATION
OUTSIDE DIMENSIONS
EXTERIOR
DOOR
LEG
WASH SYSTEM ,RINSE SYSTEM
PUMP
DRAIN SYSTEM
START
DRY SYSTEM
REFUSE DISPOSAL
DETERGENT
DISPLAY
TANK CAPACITY
HOT WATER SUPPLY
TEMPERATURE CONTROL
CONNECTION – WATER SUPPLY
– DRAIN
CONTROL
BOIL – DRY PROTECTION
SAFETY SYSTEM
Upper and Lower Fixed Spray
Wash 1HP x 2, Rinse 0.134HP
Draw Out Overflow Pipe, Overflow Drain
Rack Detection (Wash/Rinse)
Residual Heat Drying
Filter Collection
Not Provided
Wash Water Temperature / Rinse Water Temperature (selectable by switch)
Ready, Auto Fill, Wash, Error Code
27.2Gal (103L)
Automatic Hot Water Supply by
Microprocessor Control
Wash: 160ºF (71ºC) min.
12.4Gal (47L)
Automatic Hot Water Supply by
Water Valve
Rinse: 180ºF (82ºC) min.
Thermistor Control: 182ºF(83ºC)-185ºF (85ºC) Thermistor Control: 163ºF(73 㩷 C) – 168 㩷㪝 (76 C)
Inlet: 3/4"FPT
Outlet: 1-1/2"MPT
Microprocessor control
Water Level Switch,
Bimetal Thermostat (Manual - Reset),
Thermistor (Auto - Reset)
Float Switch,
Bimetal Thermostat (Manual - Reset),
Thermistor (Auto - Reset)
Service Panel Switch, Emergency Stop by Microprocessor Control
Table Limit Switch, Emergency Stop Button, Conveyor Overload Protector
Net 430lb (195kg) / Gross 584lb (265kg) WEIGHT
PACKAGE
CERTIFICATION
ACCESSORIES-SUPPLIED
ACCESSORIES-REQUIRED
Carton + Crate
W62.6"×D32.9"×H65.9" (W1,590mm ×D 835mm × 1,675mm)
NSF ANSI-3, ETL, cETL, Energy Star
Universal rack (19-3/4" x 19-3/4"), Instruction manual, Installation manual
Maintenance sheet, Curtain(L), Curtain(S) x 2, Shaft - curtain(L), Shaft - curtain (S) x 2
Guard(L), Guard(R), Hook - Drain, Table limit Switch, Upper wash spray arm,
Operation box assembly, Cable cover, Inlet water strainer & Packing
Universal rack (addition), Ventilation hoods x 2, Drain Tempering Kit
OPERATION CONDITIONS
Ambient Temperature: 41 - 95ºF (5ºC - 35ºC), Voltage Range: Rated Voltage ±10%
Recommends Water Hardness : 4gpg (grains per gallon) (68.5ppm) or less
Water Supply Temperature: 110 - 167ºF (43ºC - 75ºC) ( Recommends 140 ºF (60ºC))
Water Supply Pressure (Gauge Static Pressure): 10 - 70PSIG (0.07 - 0.48 MPa)
Exhaust Requirements : 200CFM(Entrance End),400CFM(Discharge End)
* The rated properties are based on measurements at ambient temperature of 86ºF (30ºC) according to the Technical
Requirements for Electrical Appliances.
* We reserve the right to make changes in specifications and design without prior to notice.
1
2. JWE-2400CUA-R-25B
AC SUPPLY VOLTAGE
POWER SUPPLY CAPACITY
AMPERAGE
RACK SIZE
NUMBER OF LARGE DISHES / RACK
CAPACITY
WATER COMSUMPTION
PASSING HEIGHT
DIRECTION OF OPERATION
OUTSIDE DIMENSIONS
EXTERIOR
DOOR
LEG
WASH SYSTEM ,RINSE SYSTEM
PUMP
DRAIN SYSTEM
START
DRY SYSTEM
REFUSE DISPOSAL
DETERGENT
DISPLAY
DISHWASHER SIDE
3 phase 3-wire 208-230V/60Hz (±10%) /
208V : 18.4kVA(51.1A)
230V : 22.1kVA(55.5A)
Max Running 51.2A
Rated Motor 9.0A
26.0A
BOOSTER SIDE
2 power supply lines 㩷
208V : 20.6kVA(57.2A)
230V : 25.3kVA(63.5A)
Max Running 63.3A
STARTING AMPERAGE
ELECTRICAL COMSUMPTION
HEATER
TANK CAPACITY
HOT WATER SUPPLY
TEMPERATURE CONTROL
CONNECTION – WATER SUPPLY
– DRAIN
Max 19.86kW
Rated Motor 3.06kW
Power Factor 84%
16.80kW(230V)
Max 25.20kW
25.20kW(230V)
19-3/4" × 19-3/4"(500 × 500mm)
16 plates (9.1” DIA)
240/200/160racks/hour 㩷 adjustable in 3 steps (rotary switch)
114Gal/hour(432L/hour), 0.48 Gal/rack(1.8L/rack) - at 240rack/hour
20.5" (520mm)
Right to Left
W57.3" × D27.6" × H58.1" (W1,455 × D700 × H1,475mm)
Stainless Steel
Vertically Sliding Service Panel(Opening:W25.6" × H18.9")
Stainless Steel Adjustable 9.4" - 11.0"
Upper and Lower Fixed Spray
Wash 1HP x 2, Rinse 0.134HP
Draw Out Overflow Pipe, Overflow Drain
Rack Detection (Wash/Rinse)
Residual Heat Drying
Filter Collection
Not Provided
Wash Water Temperature / Rinse Water Temperature (selectable by switch)
Ready, Auto Fill, Wash, Error Code
27.2Gal (103L)
Automatic Hot Water Supply by
Microprocessor Control
Wash: 160ºF (71ºC) min.
12.4Gal (47L)
Automatic Hot Water Supply by
Water Valve
Rinse: 180ºF (82ºC) min.
Thermistor Control: 182ºF(83ºC)-185ºF (85ºC) Thermistor Control: 163ºF(73 㩷 C) – 168 㩷㪝 (76 C)
Inlet: 3/4"FPT
Outlet: 1-1/2"MPT
Microprocessor control CONTROL
BOIL – DRY PROTECTION
SAFETY SYSTEM
WEIGHT
Water Level Switch,
Bimetal Thermostat (Manual - Reset),
Thermistor (Auto - Reset)
Float Switch,
Bimetal Thermostat (Manual - Reset),
Thermistor (Auto - Reset)
Service Panel Switch, Emergency Stop by Microprocessor Control
Table Limit Switch, Emergency Stop Button, Conveyor Overload Protector
Net 430lb (195kg) / Gross 584lb (265kg)
PACKAGE
CERTIFICATION
ACCESSORIES-SUPPLIED
ACCESSORIES-REQUIRED
OPERATION CONDITIONS
Carton + Crate
W62.6"×D32.9"×H65.9" (W1,590mm ×D 835mm × 1,675mm)
NSF ANSI-3, ETL, cETL, Energy Star
Universal rack (19-3/4" x 19-3/4"), Instruction manual, Installation manual
Maintenance sheet, Curtain(L), Curtain(S) x 2, Shaft - curtain(L), Shaft - curtain (S) x 2
Guard(L), Guard(R), Hook - Drain, Table limit Switch, Upper wash spray arm,
Operation box assembly, Cable cover, Inlet water strainer & Packing
Universal rack (addition), Ventilation hoods x 2, Drain Tempering Kit
Ambient Temperature: 41 - 95ºF (5ºC - 35ºC), Voltage Range: Rated Voltage ±10%
Recommends Water Hardness : 4gpg (grains per gallon) (68.5ppm) or less
Water Supply Temperature: 110 - 167ºF (43ºC - 75ºC) ( Recommends 140 ºF (60ºC))
Water Supply Pressure (Gauge Static Pressure): 10 - 70PSIG (0.07 - 0.48 MPa)
Exhaust Requirements : 200CFM(Entrance End),400CFM(Discharge End)
* The rated properties are based on measurements at ambient temperature of 86ºF (30ºC) according to the Technical
Requirements for Electrical Appliances.
* We reserve the right to make changes in specifications and design without prior to notice.
2
B. Nameplate Rating
For certi fi cation marks, see the nameplate on the dishwasher.
We reserve the right to make changes in speci fi cations and design without prior notice.
3
C. Dimensions/Connections
1. JWE-2400CUA-L-25B
4
2. JWE-2400CUA-R-25B
5
II. General Information
A. Construction
1. Dishwasher
The illustration below shows JWE-2400CUA-L-25B (left-to-right rack fl ow).
Wash Spray Arm (stationary)
Wash Start Switch
Vertically Sliding
Service Panel
Rack Flow
Operation Panel
Emergency Stop Button
Rinse Spray Arm (stationary)
Rinse Start Switch
Conveyor
Table Limit Switch
Service Panel Switch
Conveyor Motor
Wash Tank (26 gallons)
Wash Tank Thermistor
Wash Tank Heater
Booster Tank
Water Valve
Backup Water
Level Float Switch
Water Level Float Switch
Water Level Sensor Water Level Safety
Float Switch
Wash Pump
(Upper/Lower Spray Arm)
Rinse Pump
Booster Tank Thermistor
Booster Tank Heater
6
2. Booster Tank Sheathed Heater [H7 - 15] Band Heater
Hot Water Outlet Pipe
Over fl ow Pipe
Top View
Thermostat Plate
Front View
Thermal Protector [TH7 - 12]
(heater boil dry protection)
Inlet Water
Valve [WV] Inlet Pipe
Water Level Float Switch [FS1]
(downward end)
Backup Water Level Float Switch [FS2]
(upward end)
Water Level Safety Float Switch [FS3]
(downward end)
Thermistor [TH2]
(hot water temperature control)
Thermal Protector [TH14]
Drain Hose
Strainer
7
3. Control Box
8
B. Functions
Upper Rinse Spray Arm
1. Increasing Rinse Water Flow Rate
Clean Pipe
The rinse water fl ow rate is factory adjusted to 1.90 gal/min
(7.2 L/min). To increase the fl ow rate to 3.17 gal/min (12 L/ min), follow the steps below. Hot water supply of at least
3.44 gal/min (13 L/min) and 113°F (45°C) will be required.
Lower Rinse
Spray Arm
1) Remove the upper and lower rinse spray arms.
2) Loosen the clean pipe nut, and remove the clean pipe.
Spacer
3) Remove the spacer (with 4.5 mm DIA hole) from the nut at the unit side.
4) Replace the clean pipe and the upper and lower rinse spray arms in their correct positions.
Nut
C. Sequence of Operation
The steps in the sequence are as outlined below.
1. Auto Fill Cycle
"AUTO FILL" lamp fl ashing and "RINSE TEMP." or "WASH TEMP." lamp on.
If BT WLF/S is open when the "ON/OFF" button is pressed, WV energizes after BT auto fi ll delay time (factory default: 10 seconds).
When BT WLF/S closes, WV de-energizes, the "AUTO FILL" lamp fl ashes and the auto fi ll cycle starts.
RPM energizes for length of time set by the auto fi ll cycle rinse time setting (factory default:
13 minutes). For details, see "Auto Fill Cycle Rinse Time" (service menu item 03) in "II.F.7.b)
Service Menu Chart."
At the end of the auto fi ll cycle, there is a 5-second dwell time. CB checks WT WLS. If WT
WLS is closed, BZ beeps, the "AUTO FILL" lamp goes off and the "READY" lamp comes on. If WT WLS is open, BZ beeps continuously, the "AUTO FILL" lamp goes off and "A1" fl ashes in the display. For details, see "III.B.3.a) Auto Fill Error (A1)."
If the BT water level goes down and BT WLF/S opens during the auto fill cycle, WV energizes after BT auto fi ll delay time (factory default: 10 seconds). For adjustment of this delay time, see "Booster Tank Auto Fill Delay Time" (service menu item 08) in "II.F.7.b)
Service Menu Chart." If delay time is set shorter, WV energizes/de-energizes frequently and BT may not supply hot water of proper temperature.
If SP is opened during the auto fi ll cycle, SPS opens, RPM de-energizes. The "AUTO FILL" lamp keeps flashing and the rinse cycle time keeps counting down. When SPS closes again, RPM energizes.
If WLS is closed when the "ON/OFF" button is pressed, the "READY" lamp comes on and the unit is ready to start.
Note:
1. If SP is opened during the auto fi ll cycle, RPM de-energizes to stop hot water supply.
If SP is left open for a long time, WT may not fi ll by the end of the auto fi ll cycle. In this case, WT WLS opens when the unit starts, and the supplementary fi ll cycle begins.
2. WTH is energized when WT WLS closes during the auto fi ll cycle.
3. BTH is energized during the auto fi ll cycle if WLSF/S is closed.
9
4. If BT WLF/S fails, BT BUWLF/S assumes control. If BT BUWLF/S remains closed for 1 minute, o1 or o2 error appears in the display. For details, see "III.B. Error Codes."
5. The wash/rinse start switch is inactive during the auto fi ll cycle.
2. Ready Cycle (Unit Inactive)
"READY" lamp and "RINSE TEMP." or "WASH TEMP." lamp on.
WT WLS closed. After a rinse cycle, RPM de-energizes, and the "READY" lamp comes on.
WTH energizes when WT water temperature is at the wash temperature setpoint or lower. WTH de-energizes when WT water temperature is 5°F (3°C) above the setpoint.
For details, see "Wash Temperature Setpoint" (service menu item 04) in "II.F.7.b) Service
Menu Chart."
BTH energizes when BT water temperature is 3°F (2°C) below the rinse temperature setpoint or lower. BTH de-energizes when BT water temperature reaches the setpoint.
WV energizes/de-energizes when BT WLF/S opens/closes. For details, see "Rinse
Temperature Setpoint" (service menu item 05) in "II.F.7.b) Service Menu Chart."
Note:
1. The thermistors control WT and BT water temperatures.
2. If one of the thermistors has an open or short circuit, WTH or BTH de-energizes and an error code appears in the display.
3. WTH and BTH are controlled regardless of SPS operation.
3. Wash Cycle/Rinse Cycle
"WASH" lamp and "RINSE TEMP." or "WASH TEMP." lamp on.
When a rack is loaded from the wash compartment entrance and the wash start switch closes, WPM energizes, power is supplied to DFT and the "WASH" lamp comes on. WPM draws water from WT and sends it through the wash spray arms. The upper spray arm
WPM starts fi rst, followed by the lower spray arm WPM. Then, the conveyor starts to move the rack. After the wash start switch opens and the extended wash cycle time (factory default: 30 seconds) has expired, WPM de-energizes and power is cut to DFT. For details, see "Extended Wash Cycle Time" (service menu item 01) in "II.F.7.b) Service Menu Chart."
When the rinse start switch closes, RPM energizes and power is supplied to RFT. RPM draws water from BT and sends it through the rinse spray arms. Rinse aid is fed into the rinse water line and sprayed from the rinse spray arms together with rinse water. Any excess water in WT drains through the over fl ow pipe. After the rinse start switch opens and the extended rinse cycle time (factory default: 15 seconds) has expired, RPM deenergizes, power is cut to RFT, the "WASH" lamp goes off and the "READY" lamp comes on. For details, see "Extended Rinse Cycle Time" (service menu item 02) in "II.F.7.b)
Service Menu Chart."
After both WPM and RPM de-energize, the conveyor stops. If SP is opened during operation, SPS opens, WPM and RPM de-energize and the conveyor stops. If the wash/ rinse start switch is closed when SPS closes, WPM and RPM energize and the conveyor restarts.
Note:
1. If WT WLS opens after WPM energizes, WPM de-energizes and RPM energizes for the supplementary fi ll cycle time (factory default: 450 seconds) to supply hot water into
10
WT. The conveyor does not start during the supplementary fi ll cycle. "A3" appears in the display and the "AUTO FILL" lamp fl ashes. BZ beeps three times only at the beginning.
If WT WLS is still open after the supplementary fi ll cycle, another cycle starts. If WT
WLS still does not close, "A3" appears in the display, BZ beeps and the unit shuts down.
For adjustment of the supplementary fi ll cycle time, see "Supplementary Fill Cycle Time"
(service menu item 07) in "II.F.7.b) Service Menu Chart." For details, see "III.B.3.c)
Wash Tank Water Level Error (A3)."
2. If WT WLS and the wash start switch are closed after RPM runs for the supplementary fi ll cycle time, WPM energizes and the conveyor starts.
3. If SP is opened and closed during operation and the wash/rinse start switch is open, the unit does not resume operation. Load another rack to close the wash start switch. The unit resumes operation if SP is closed during the extended wash/rinse cycle time.
4. Table Limit Switch
If a rack reaches the end of the clean dishtable and actuates TLS lever (TLS closed),
WPM and RPM de-energize, the conveyor stops and "L1" appears in the display. When the rack is removed and TLS lever returns to the original position (TLS open), WPM and
RPM energize and the conveyor starts after 3 seconds unless the wash/rinse start switch is open.
5. Emergency Stop Button
To shut down the unit in case of emergency, press ESB on top of the unit (wash compartment exit side). To resume operation, turn ESB clockwise to unlock and press the
"ON/OFF" button on the operation panel.
Note: The unit is inoperative without ESB connected at the time of installation.
6. Drain
This unit does not have a drain valve.
The over fl ow pipe in WT drains excess water from WT. To completely drain WT, remove the over fl ow pipe.
To drain BT, use the “ON/OFF” button on the operation panel to turn off the unit, then turn off the dishwasher and booster tank power supplies. Lockout/Tagout to prevent the power supplies from being turned back on inadvertently.
Use BT drain hose to drain BT. WARNING! To avoid possible burns, allow BT water temperature to fall below 104°F (40°C) before draining.
Legend: BT –booster tank; BTH –booster tank heater; BUWLF/S –backup water level fl oat switch; BZ –buzzer; CB –control board; DFT –detergent feeder terminals (detergent feeder not provided by Hoshizaki); DS –door switch; ESB –emergency stop button;
RFT –rinse aid feeder terminals (rinse aid feeder not provided by Hoshizaki);
RPM –rinse pump motor; SP –service panel; SPS –service panel switch; WLSF/
S –water level safety float switch; TLS –table limit switch; WLF/S –water level fl oat switch; WLS –water level sensor; WPM –wash pump motor; WT –wash tank;
WTH –wash tank heater; WV –inlet water valve
11
D. Sequence of Operation Flow Chart
12
E. Timing Chart
1. Auto Fill Cycle
Booster Tank
13
2. Wash Cycle/Rinse Cycle
14
F. Control Board and Operation Board
• A Hoshizaki exclusive solid-state control board and operation board are employed in all
Hoshizaki dishwasher units.
• All models are pretested and factory set.
NOTICE
1. The control board and operation board are fragile; handle very carefully.
2. The control board and operation board contain integrated circuits, which are susceptible to failure due to static discharge. It is especially important to touch the metal part of the unit when handling or replacing the control board or operation board.
3. Do not touch the electronic devices on the control board or operation board or the back of the control board or operation board.
4. Do not attempt to repair the control board or operation board.
5. Do not short out power supply to test for voltage.
1. Control Board Location
The control box is located behind the front panel. Follow the instructions and warnings for safe and ef fi cient operation of the unit.
Control Box
15
2. Control Board Layout
Inputs and outputs are laid out on the control board as illustrated below.
Signal Input XA Connector (6P)
Signal Input XA Connector (10P)
Buzzer Output XA Connector (2P)
Power Input VH Connector (4P)
Thermistor Signal Input
XA Connector (4P)
1
4
CN8
1 CN7
10
8
CN6
1
5
1
CN5
1
CN9
6
CN11
3 1
1 2
CN10
High
CN13
2 1
CN12
3 1
1 4
CN1
Low VR1
Buzzer Volume
X5
X6
X7
X1
X2
X3
X4
CN2
1
6
1
7
CN3
1
5
CN4
Power Input VH Connector (6P)
Output VH Connector (7P)
Output VH Connector (5P)
Operation Board XA Connector (5P)
XH Connector (3P): not in use
XH Connector (2P): not in use
Booster Tank Water Level Safety
Signal Input XA Connector (3P)
16
3. Control Board Diagram
200VAC from Transformer
Transformer
11V 7.7V
[Communication]
Operation Panel
Board
(Shielded Wire)
Wash Tank Thermistor
Booster Tank Thermistor
Booster Tank Water
Level Safety Float Switch
Buzzer Output
Connector Voltages
(CN5)
5
1
4
(CN7)
3
2
(CN11)
1
2
(CN10)
1 (CN1) 4
1
(CN6)
CN2 : 200VAC
CN3 : 12VDC
CN4 : 12VDC
CN5 : 5VDC
CN7 : 5VDC
CN8 : 12VDC
CN9 : 1-2: 6VAC
5-6: 12VDC
CN10 : 12VDC
CN11 : 12VDC
(CN12)
(CN13)
1 (CN2) 6
X1
1
X2
3
X3
5
X4
7
X5
(CN3)
1
X6
3
X7
5
1
(CN4)
2
X13
MC4
X14
X15
MC1
X10
MC3
5
6
1
(CN9)
Booster Tank Heater
Wash Tank Heater
Rinse Pump
Upper Wash Pump
Water Valve
Lower Wash Pump
Conveyor
Wash Tank Electrode
(Water Level Sensor)
Table Limit Switch + Conveyor Overload
Booster Tank Water Level Float Switch
Booster Tank Backup Water Level Float Switch
Wash Start Switch
Rinse Start Switch
10
(CN8)
*1 Connectors CN 1 - 4 are VH Connectors
17
4. Operation Panel Layout
The operation panel is mounted on top of the unit (wash compartment exit side) and is connected to the CN5 connector on the control board.
Up Button
Water Temperature
Lamps
Down Button
"AUTO FILL" Lamp
Display
"READY" Lamp
"CHANGE" Button
"WASH" Lamp
"ON/OFF" Button
5. Features a) Display
This operation board uses an LED display to show system details and diagnostic information.
b) Service Menu and Error Log
A service menu ("01" to "19" and "21" to "25") allows for viewing and setting of system operating details and parameters. See "II.F.7. Service Menu and Error Log." c) Error Codes
Error codes ("A1" to "A3," "H1" to "H6," "L1," "L2," "b1," "b2," "o1," "o2") are designed to protect the unit. These codes give information or warnings in the event the unit is operating out of acceptable parameters. See "III.B. Error Codes."
6. Controls, Adjustments, and Lamps a) Water Temperature Lamps
Light up to indicate the water temperature shown in the display.
b) "AUTO FILL" Lamp
Flashes during the auto fi ll cycle, and goes off at the end of the cycle.
18
c) "READY" Lamp
Lights up when the auto fi ll cycle completes and the dishwasher is ready to wash.
d) "WASH" Lamp
Lights up during washing operation.
e) Up Button, Down Button
Indicates the total hours of operations in six digits by two digits each time.
Example: 123,456 hours are indicated by
Press to stop the beep in case of error.
Service personnel also use these buttons to change the controller settings.
f) Display
Indicates wash water temperature in wash cycle, rinse water temperature in rinse cycle, and error codes in case of trouble.
g) "CHANGE" Button
Press to change the wash water temperature shown in the display to the rinse water temperature.
h) "ON/OFF" Button
Turns on/off the power for operation.
i) Conveyor Speed Switch
Located on front panel. Changes the rack conveyor speed in three levels (high = 240 racks/hour, medium = 200 racks/hour, low = 160 racks/hour).
7. Service Menu and Error Log
The service menu ("01" to "19" and "21" to "25") may be used to change settings, acquire diagnostic information, and to view error history.
a) Service Menu Access
• Enter Service Menu: Use the "ON/OFF" button to turn off the unit. Press and hold the
"CHANGE" button, then press the "ON/OFF" button. "01" should appear on the display.
• Scroll: Use the up and down arrow buttons to scroll through the service menu list, settings, and data.
• View Service Menu Setting: Press the "CHANGE" button to view the selected menu setting.
• Change Setting: Use the up and down arrow buttons to change the setting value.
• Return to Service Menu List: Press the "CHANGE" button once again to return to the main service menu list.
• Exit Service Menu and Save Settings: Press the "ON/OFF" button to exit the service menu and save the settings. The display goes blank.
19
b) Service Menu Chart
Service
Menu
Item and Details Setting Range
01
02
03
04
05
06
07
08
09
10
11
12
Extended Wash Cycle Time
Extended Rinse Cycle Time
Auto Fill Cycle Rinse Time
Wash Temperature Setpoint
Rinse Temperature Setpoint
Booster Tank Heating Time
Supplementary Fill Cycle Time
Booster Tank Auto Fill Delay Time
Water Temperature Display
Booster Tank Auto Fill Timer
Booster Tank Temperature Correction
Water Temperature Display Change
1 to 99 seconds
(in 10 second steps)
1 to 99 seconds
(in 1 second steps)
0 to 99 minutes
(in 1 minute steps)
Fahrenheit 32 to 176°F
(in 1°F steps)
Celsius 0 to 80°
(in 1°C steps)
Fahrenheit 32 to 185°F
(in 1°F steps)
Celsius 0 to 85°
(in 1°C steps)
0 to 99 seconds
(in 10 second steps)
0 to 990 seconds
(in 10 second steps)
0 to 99 seconds
(in 1 second steps)
ON: wash water temperature
OFF: rinse water temperature
1 to 99 minutes
(in 1 minute steps)
Fahrenheit 0 to 9R
(in 1R steps)
Celsius 0 to 5K
(in 1K steps)
ON: alternate
OFF: fi xed
Fahrenheit or Celsius 13 Temperature Display Scale
14 Water Temperature Display Change
Cycle Time
1 to 10 seconds
(in 1 second steps)
15 Low Water Temperature Lock Function ON: lock function on
OFF: lock function off
16 Wash Tank Re fi ll Alert ON: alert on
OFF: alert off
17 Total Operation Time Before Alert 10 to 600 minutes
18
19
Display Hold Function
Power Supply Lock Function
21 through
Error Log
Note: To erase the log, press and hold the
NA
25 up and down buttons for 3 seconds with one of the error codes displayed. The unit beeps once and the entire log clears.
ON: stays on
OFF: goes off after preset time
ON: "Ch" keeps fl ashing until electrode is turned off
OFF: "Ch" goes off when "ON/
OFF" button is switched off
Display
1 to 99
1 to 99
0 to 99
32 to 176
0 to 80
32 to 185
0 to 85
0 to 99
0 to 99
0 to 99 on or oF
1 to 99
0 to 9
0 to 5 on or oF
°F or °C
1 to 10 on or oF on or oF
1 to 60 on or oF on or oF
Factory
Default
30
15
13
163
73
185
85
0
450
10 on
20
0
0 on
°F
5 oF oF
12 (2h) oF oF
Most Recent
Errors
21 is most recent.
"--" is displayed if the log is empty.
NA
20
8. Temperature Display
• Indicates the average water temperature read by the wash tank or booster tank thermistor.
Indicates water temperature selected by the water temperature lamps beside the display.
The factory default setting is to indicate wash water temperature and rinse water temperature alternately every 5 seconds. To adjust the display change cycle time, or to fi x the temperature display for either wash or rinse water temperature and indicate the other temperature while the "CHANGE" button is pressed, see service menu items 09, 12 and 14 in "II.F.7.b) Service
Menu Chart."
• The temperature display range is 32°F to 199°F (0°C to 99°C). To change the display scale, see "Temperature Display Scale" (service menu item 13) in "II.F.7.b) Service Menu Chart."
• The temperature display updates every 5 seconds for the wash tank and the booster tank.
9. Error Codes
In the event of operation outside of normal parameters, the control board identi fi es the issue with an error code and beeps. If more than one error occurs, the display cycles through the relevant error codes. For service corrections, see "III.B. Error Codes."
Error Codes
A1 Wash Tank Auto Fill Error
A2 Booster Tank Auto Fill Error
A3 Wash Tank Water Level Error o1
Booster Tank Water Level Error 1
(Booster Tank Water Level Float Switch Closed) o2
Booster Tank Water Level Error 2
(Booster Tank Water Level Float Switch Open)
H1 Wash Tank Thermistor Error (short)
H2 Wash Tank Thermistor Error (open)
H3 Booster Tank Thermistor Error (short)
H4 Booster Tank Thermistor Error (open)
H5 ROM/RAM Error
H6 EEPROM Error
L1 Conveyor Overload or Table Limit Error 1
L2 Conveyor Overload or Table Limit Error 2 b1 Booster Tank Error b2 Booster Tank Water Level Safety Error
10. Buzzer
• At the end of an auto fi ll cycle or other mode operation, the buzzer turns on for 0.1 second and off for 0.1 second 10 times.
• In case of an error, the buzzer turns on for 0.1 second and off for 0.9 second repeatedly until the error is reset. To turn off the beep, press the down button.
• When a button is pressed, the buzzer turns on for 0.1 second.
• To adjust the buzzer volume, use the volume control on the control board.
21
11. Operation Time Display
To indicate the total hours of operation in the display, press the up button on the operation panel. The number appears from the hundred-thousands place by two digits each for 1 second. The maximum number is 999,999 hours, and the display does not change for the higher numbers.
Example: 19,302 hours are indicated as
12. Special Modes
OFF OFF a) Continuous Wash Mode
The continuous wash mode (also used when descaling) allows the wash pump motor to run continuously. In this mode, the wash tank heaters and booster tank heaters remain deenergized.
To enter the continuous wash mode, use the "ON/OFF" button to turn off the unit. Press and hold the up and down buttons and the "CHANGE" button for 3 seconds and press the
"ON/OFF" button. As long as the service panel switch and wash tank water level sensor are closed, the wash pump motor runs and power is supplied to the detergent feeder terminals.
"PC" (preventative cleaning) appears in the display and the lamps are off.
To cancel the continuous wash mode, press the "ON/OFF" button.
b) Low Water Temperature Lock Function
To ensure the NSF speci fi ed minimum wash water temperature of 160
°
F, this unit is provided with a function to lock the washing operation until water in the wash water tank reaches 160
°
F even if a rack is loaded (factory default: OFF).
To activate this function, set service menu item 15 to "ON" referring to "II.F.7.a) Service Menu
Access." The minimum temperature of 160
°
F cannot be changed.
c) Alert Function
To keep water in the wash water tank clean, this unit is provided with functions to beep and fl ash "Ch" (= Change) in the display when wash water should be changed and to continue this alert until the wash water tank is re fi lled (factory default: OFF).
To activate this function, set service menu items 16, 17, 18 and 19 referring to "II.F.7.a)
Service Menu Access."
1) Set service menu item 16 to ON to activate this function (factory default: OFF).
2) Set service menu item 17 to the desired total operation time before alert [number in display x 10 minutes] (factory default: 12 (2 hours)). Change this setting according to the advice of the relevant health department and customer demands.
3) Set service menu item 18 to either OFF ["Ch" goes off after 10 minutes] or ON ["Ch" keeps fl ashing] (factory default: OFF). Even if set to ON, "Ch" goes off when the "ON/OFF" button on the operation panel is switched off.
22
4) Set service menu item 19 to ON to stop the beep when the "ON/OFF" button is switched off but to resume fl ashing "Ch" when the "ON/OFF" button is switched back on unless the wash water tank is re fi lled (factory default: OFF). Press the emergency stop button or turn off the external power supply to stop both the beep and "Ch" indication.
Set service menu item 19 to OFF to stop both the beep and "Ch" indication once the "ON/
OFF" button is switched off.
If service menu item 19 is set to ON, "Ch" keeps fl ashing even if service menu item 18 is set to OFF.
Alert Function Setting Flow
OFF
Wash Tank Re fi ll Alert Service Menu 16
Alert function OFF
[factory default]
ON
Set service menus
17 to 19
Total Operation Time
Before Alert
Service Menu 17
Display Hold Function
1 to 99
Alert starts after number in display
(1 to 99) x 10 minutes
[factory default: 12 (2 hours)]
* OFF
Service Menu 18
"Ch" goes off after 10 minutes
[factory default]
Power Supply Lock
Function
ON
"Ch" keeps fl ashing
(until "ON/OFF" button is switched off)
Service Menu 19
* ON
OFF Beep stops and "Ch" goes off when
"ON/OFF" button is switched off
[factory default]
Switching off "ON/OFF" button cancels beep but not "Ch" until wash water tank is re fi lled
* "Ch" keeps fl ashing even if service menu 18 is set to OFF
23
III. Service Diagnosis
WARNING
1. This unit should be diagnosed and repaired only by qualified service personnel to reduce the risk of death, electric shock, serious injury, or fi re.
2. Risk of electric shock. Use extreme caution and exercise safe electrical practices.
3. Moving parts (e.g., fan blade) can crush and cut. Keep hands clear.
4. Do not make any alterations to the unit. This could cause water leak, electric shock, or fi re.
5. To help reduce the risk of electric shock, do not touch switches with damp hands.
A. Diagnostic Procedure
The diagnostic procedure is a sequence check of the switches and sensors while operating the unit, by using the switch open/closed display mode.
Switch Open/Closed Display Mode
The switch open/closed display mode indicates when the wash start switch, rinse start switch, wash tank water level sensor, booster tank water level fl oat switch, and booster tank backup water level fl oat switch are open or closed.
To enter the switch open/closed display mode, use the "ON/OFF" button to turn on the unit. Press and hold the up and down buttons for 3 seconds. The following appears in the display:
Load a rack to engage the wash start switch and start a cycle. The display indicates whether a switch is open or closed. When a switch is closed, its corresponding segment is illuminated in the display. See the illustration below.
To resume the normal display, press the down button.
Booster Tank Backup Water Level Float Switch
Wash Start Switch
Booster Tank Water Level Float Switch
Rinse Start Switch
Wash Tank Water Level Sensor
24
It is recommended to conduct this sequence check in the auto fi ll cycle after draining the wash tank and booster tank. See “II.C. Sequence of Operation” for further details.
1) Use the “ON/OFF” button on the operation panel to turn off the unit.
2) Pull out the over fl ow pipe to drain the wash tank.
3) Drain the booster tank through the drain hose.
4) Replace the over fl ow pipe and drain hose in their correct positions.
5) Enter the switch open/closed display mode according to the above procedure.
6) Auto Fill Cycle a. After the service panel is closed and the “ON/OFF” button is pressed, the inlet water valve in the booster tank opens in 10 seconds to start water supply.
b. After a while, the booster tank water level float switch closes, segment C in the display comes on, and the inlet water valve closes to stop water supply.
c. The rinse pump starts to feed water to the wash tank. When the booster tank water level goes down, the water level fl oat switch opens, segment C in the display goes off, and the inlet water valve opens to start water supply.
d. After the rinse pump is energized for a preset time to fi ll the wash tank, the wash tank water level sensor closes, and segment E in the display comes on.
e. In normal operation, the booster tank backup water level fl oat switch does not close, and segment A in the display stays off. If the booster tank water level fl oat switch fails or the booster tank water level reaches the over fl ow level, segment A comes on.
7) Wash Cycle/Rinse Cycle a. When a rack is loaded from the wash compartment entrance and the wash start switch closes, segment B in the display comes on and the wash pump starts the wash cycle for a preset time. When the conveyor moves the rack forward and the wash start switch opens, segment B goes off and the wash pump stops after the preset time. Segment E in the display stays on.
b. If the booster tank is below the predetermined water level, segment C in the display stays off. The inlet water valve stays open until segment C comes on.
c. When the wash cycle ends and the rinse start switch closes, segment D in the display comes on and the rinse pump starts the rinse cycle for a preset time. When the rinse start switch opens, segment D goes off and the rinse pump stops after the preset time. When the rinse cycle starts, the booster tank water level goes down and segment C in the display goes off. The inlet water valve stays open until segment C comes on.
Diagnosis: If any problem is found by the above sequence check, refer to “III.B. Error
Codes,” “III.C. Service Flow Charts,” “III.D. Float Switch Check and Cleaning” and “III.E.
Thermistor Check.”
25
B. Error Codes
In the event of operation outside of normal parameters, the control board identi fi es the issue with an error code. For further service information, see "III.C. Service Flow Charts."
1. Error Code Table
Error
Code
Problem
A1
A2
A3
Operation
Wash Tank Auto Fill Error Whole unit stops
Water level in wash tank does not reach water level sensor after rinse pump has run for preset time.
Booster Tank Auto Fill Error Whole unit stops
In auto fi ll cycle, booster tank water level fl oat switch does not close within 10 minutes (or 20 minutes in "READY" mode) after inlet water valve is opened.
Wash Tank Water Level Error
Water level in wash tank goes below water level sensor in "READY" mode or during operation.
Booster Tank Water Level Error 1 (Booster
Tank Water Level Float Switch Closed)
Supplementary fi ll cycle starts
(Whole unit stops if water level sensor does not close after two cycles)
Whole unit stops
Reset
Use "ON/OFF" button to turn the unit off and then back on.
Use "ON/OFF" button to turn the unit off and then back on.
After supplementary fi ll cycle ends, alarm resets.
(If whole unit stops, use "ON/OFF" button to turn the unit off and then back on.)
Use "ON/OFF" button to turn the unit off and then back on.
o1
Both booster tank water level fl oat switch and booster tank backup water level fl oat switch have remained closed for 1 minute.
Booster Tank Water Level Error 2 (Booster
Tank Water Level Float Switch Open)
Whole unit stops
Use "ON/OFF" button to turn the unit off and then back on.
o2
H1
H2
H3
Booster tank water level fl oat switch is open and booster tank backup water level fl oat switch has remained closed for
1 minute.
Wash Tank Thermistor Error (short)
Thermistor senses abnormal temperature
(at or above 231°F (110°C)).
Wash Tank Thermistor Error (open)
Thermistor senses abnormal temperature
(at or below -6°F (-21°C)).
Booster Tank Thermistor Error (short)
Thermistor senses abnormal temperature
(at or above 231°F (110°C)).
Normal
(Wash tank heaters off)
Normal
(Wash tank heaters off)
Normal
(Booster tank heaters off)
After replacing failed component, alarm resets.
After replacing failed component, alarm resets.
After replacing failed component, alarm resets.
26
Error
Code
Problem
Booster Tank Thermistor Error (open)
H4
Thermistor senses abnormal temperature
(at or below -6°F (-21°C)).
ROM/RAM Error
H5
Control board ROM/RAM fails.
EEPROM Error
H6
EEPROM fails.
Conveyor Overload or Table Limit Error 1
L1
L2
Operation
Normal
(Booster tank heaters off)
Whole unit stops
Whole unit stops
Unit stops
Inverter sends conveyor overload signal or table limit switch closes.
Conveyor Overload or Table Limit Error 2
After unit stops with "L1" error and restarts, another error signal is sent within 3 seconds.
Booster Tank Error
Whole unit stops
Normal b1 b2
Booster tank error output contacts open.
Booster Tank Water Level Safety Error
Booster tank water level safety fl oat switch opens after booster tank water level fl oat switch closes.
Whole unit stops
Reset
After replacing failed component, alarm resets.
After replacing control board, alarm resets.
After replacing control board, alarm resets.
After error signal stops, alarm resets.
Use "ON/OFF" button to turn the unit off and then back on.
After booster tank error is resolved, alarm resets.
Use "ON/OFF" button to turn the unit off and then back on.
2. Error Code Log
Use the "ON/OFF" button to turn off the unit. Press and hold the "CHANGE" button, then press the "ON/OFF" button. "01" should appear on the display. Use the down arrow button to scroll to service menu items 21 through 25. 21 is the most recent error. Press the "CHANGE" button to view the selected service menu item. Press the "CHANGE" button once again to return to the main service menu list. If no errors exist in the log, "--" is displayed.
Press the "ON/OFF" button to exit the service menu. The display goes blank.
To erase the log, press and hold the up and down buttons for 3 seconds with one of the error codes displayed. The unit beeps once and the entire log clears.
27
3. Error Code Details a) Auto Fill Error (A1)
• If the water level sensor in the wash tank is not closed at the end of the auto fi ll cycle, the unit shuts down, "A1" appears in the display, and the buzzer sounds.
• To reset, use the "ON/OFF" button to turn the unit off and then back on.
• See the chart below for possible causes and remedies.
Code Error
A 1
Wash tank water level sensor is open at the end of the auto fill cycle.
Operation
Unit stops.
Continue
Overflow Pipe
Wash Tank Water Level
Sensor
Rinse Pump
Control Board
Out of position. Set in position.
Heavy scale or soil buildup.
Connector not properly connected.
Open circuit.
Clean.
Reconnect.
Repair or replace.
Defective. Replace.
Open circuit. Repair or replace.
Replace.
Control relay defective.
Defective.
Improper setting.
Replace.
Readjust.
Connector not properly connected.
Defective.
Reconnect.
Replace.
28
Continue
Booster Tank Water
Level Float Switch
Sticking (with float in
“ ON ” position).
Defective (with internal contacts in “ON” position).
Check and clean. See
“ III.D. Float Switch
Check and Cleaning.
”
Replace.
29
b) Booster Tank Auto Fill Error (A2)
• In the auto fi ll cycle, if the booster tank water level fl oat switch does not close within 10 minutes
(or 20 minutes in "READY" mode) after the cycle starts, the unit shuts down, "A2" appears in the display, and the buzzer sounds.
• To reset, use the "ON/OFF" button to turn the unit off and then back on.
• See the chart below for possible causes and remedies.
Operation
Code Error
A 2
Booster tank water level float switch does not close within 10 minutes (or 20 minutes in
“READY” mode) after the auto fill cycle starts.
Unit stops.
Get it ready.
Booster Tank
Strainer
Not ready for operation.
Water supply pressure too low.
Filter clogged.
Readjust.
Clean.
Open circuit. Repair or replace.
Water Valve
Filter clogged. Clean.
Defective. Replace.
Booster Tank Water
Level Float Switch
Connector not properly connected.
Open circuit.
Reconnect.
Repair or replace.
Control Board
Sticking.
Connector not properly connected.
Defective.
Check and clean. See
“ III.D. Float Switch
Check and Cleaning.
”
Reconnect.
Replace.
30
c) Wash Tank Water Level Error (A3)
• If the water level in the wash tank goes below the water level sensor in "READY" mode or during operation, the supplementary fi ll cycle starts, "A3" appears in the display, the "AUTO
FILL" lamp fl ashes, and the buzzer sounds three times only at the beginning.
• If the wash tank water level sensor is closed after the supplementary fi ll cycle, the alarm resets. If the wash tank water level sensor is still open after the supplementary fi ll cycle, another cycle starts.
If the wash tank water level sensor is closed after the second cycle, the alarm resets. If the wash tank water level sensor still does not close after the second cycle, the buzzer sounds, and the unit completely shuts down.
• See the chart below for possible causes and remedies.
Code Error
A 3
Wash tank water level sensor opens in
“ READY ” mode or during operation.
Operation
Auto fill cycle starts.
Overflow Pipe
Wash Tank Water Level
Sensor (Wash Tank
Electrode)
Control Board
Out of position. Set in position.
Heavy scale or soil buildup.
Connector not properly connected.
Open circuit.
Clean.
Reconnect.
Repair or replace.
Defective. Replace.
Connector not properly connected.
Defective.
Reconnect.
Replace.
Water level too low. See “ A1.
”
Auto Fill Cycle
31
d) Booster Tank Water Level Error 1 (Booster Tank Water Level Float Switch Closed)
(o1)
• If both the booster tank water level fl oat switch and the booster tank backup water level fl oat switch have remained closed for 1 minute, the booster tank heaters de-energize, "o1" appears in the display, and the buzzer sounds.
• The error resets if the booster tank backup water level fl oat switch opens or when the "ON/
OFF" button is used to turn the unit off and then back on.
• See the chart below for possible causes and remedies.
Operation
Unit stops.
Code Error o 1
Booster tank water level float switch and booster tank backup water level switch have remained closed for 1 minute.
Item
Water Valve
Possible Cause
Control relay contacts fused.
Defective.
Remedy
Replace.
Replace.
Booster Tank Water
Level Float Switch
Sticking.
Defective.
Check and clean. See
“ III.D. Float Switch
Check and Cleaning.
”
Replace.
Booster Tank Backup
Water Level Float
Switch
Sticking.
Defective.
Defective.
Check and clean. See
“ III.D. Float Switch
Check and Cleaning.
”
Replace.
Replace.
Control Board
Note: See “III.D. Float Switch Check and Cleaning.”
32
e) Booster Tank Water Level Error 2 (Booster Tank Water Level Float Switch Open)
(o2)
• If the booster tank water level fl oat switch is open and the booster tank backup water level fl oat switch has remained closed for 1 minute, the booster tank heaters de-energize, "o2" appears in the display, and the buzzer sounds.
• The error resets if the booster tank backup water level fl oat switch opens or when the "ON/
OFF" button is used to turn the unit off and then back on.
• See the chart below for possible causes and remedies.
Code Error o 2
Booster tank water level float switch is open and booster tank backup water level switch has remained closed for 1 minute.
Operation
Unit stops
Booster Tank Water
Level Float Switch
Booster Tank Backup
Water Level Float
Switch
Control Board
Sticking.
Open circuit.
Defective.
Sticking.
Defective.
Connector not properly connected.
Defective.
Reconnect.
Replace.
Check and clean. See
“ III.D. Float Switch
Check and Cleaning.
”
Repair or replace.
Replace.
Check and clean. See
“ III.D. Float Switch
Check and Cleaning.
”
Replace.
Note: See “III.D. Float Switch Check and Cleaning.”
33
f) Wash Tank Thermistor Error (H1, H2)
• If the wash tank thermistor senses a temperature at or above 231°F (111°C) (2.4k
Ω ), the thermistor leads are considered shorted and the wash tank heaters de-energize, "H1" appears in the display, and the buzzer sounds.
• If the wash tank thermistor senses a temperature at or below -6°F (-21°C) (517k Ω ), the thermistor leads are considered open and the wash tank heaters de-energize, "H2" appears in the display, and the buzzer sounds.
• After replacing the failed component, the alarm resets.
• See the chart below for possible causes and remedies.
Note: The auto fi ll cycle and the wash/rinse cycle will start even after this error occurs.
Code Error
Thermistor senses abnormal temperature.
H 1 / H 2
Operation
Continues (wash tank heater off).
Thermistor
Control Board
Connector not properly connected.
Open circuit (H2).
Reconnect.
Replace.
Short circuit (H1).
Defective.
Replace.
Replace.
Connector not properly connected.
Defective.
Reconnect.
Replace.
Note: See “III.E. Thermistor Check” and “IV.H. Removal and Replacement of Thermistor.”
34
g) Booster Tank Thermistor Error (H3, H4)
• If the booster tank thermistor senses a temperature at or above 231°F (111°C) (2.4k
Ω ), the thermistor leads are considered shorted and the booster tank heaters de-energize, "H3" appears in the display, and the buzzer sounds.
• If the booster tank thermistor senses a temperature at or below -6°F (-21°C) (517k Ω ), the thermistor leads are considered open and the booster tank heaters de-energize, "H4" appears in the display, and the buzzer sounds.
• After replacing the failed component, the alarm resets.
• See the chart below for possible causes and remedies.
Note: The auto fi ll cycle and the wash/rinse cycle will start even after this error occurs.
Code Error
Thermistor senses abnormal temperature.
H 3 / H 4
Operation
Continues (booster tank heater off).
Thermistor
Control Board
Connector not properly connected.
Open circuit (H4).
Reconnect.
Replace.
Short circuit (H3).
Defective.
Replace.
Replace.
Connector not properly connected.
Defective.
Reconnect.
Replace.
Note: See “III.E. Thermistor Check” and “IV.H. Removal and Replacement of Thermistor.”
35
h) ROM/RAM Error (H5)
• If a ROM/RAM error is detected, the unit shuts down, "H5" appears in the display, and the buzzer sounds.
• After replacing the failed component, the alarm resets.
• See the chart below for possible causes and remedies.
Code Error
ROM/RAM on control board fails.
H 5
Control Board
Defective.
Operation
Unit stops.
Replace.
i) EEPROM Error (H6)
• If an EEPROM error is detected, the unit shuts down, "H6" appears in the display, and the buzzer sounds.
• After replacing the failed component, the alarm resets.
• See the chart below for possible causes and remedies.
Code Error
EEPROM on control board fails.
H 6
Control Board
Defective.
Operation
Unit stops.
Replace.
Note: See “IV.I. Removal and Replacement of Control Board or Operation Board.”
36
j) Conveyor Overload or Table Limit Error 1 (L1)
• If the inverter sends an overload signal or the table limit switch closes, the unit shuts down,
"L1" appears in the display, and the buzzer sounds.
• After removing the jammed rack or the cause of the overload (the table limit switch opens or the inverter stops sending the overload signal), the alarm resets after 3 seconds, and the unit is ready to resume operation.
If the wash start switch is closed when the alarm resets, the upper spray arm wash pump starts fi rst, followed by the lower spray arm wash pump, then the conveyor moves.
If the rinse start switch is closed when the alarm resets, the rinse pump starts, then the conveyor moves.
The heaters stay energized while the unit is off with "L1."
• See the chart below for possible causes and remedies.
Code Error
L 1
Inverter sends conveyor overload signal or table limit switch closes.
Operation
Unit stops.
Conveyor
Gear Motor
Inverter
Table Limit Switch
Jammed.
Remove obstacle.
Defective (not moving smoothly).
Defective.
Repair.
Repair or replace.
Defective. Repair or replace.
Clean dishtable filled with racks.
Stays closed with reed switch defective or magnet off.
Remove racks.
Repair or replace.
37
k) Conveyor Overload or Table Limit Error 2 (L2)
• If the unit shuts down with "L1" in the display and restarts in 3 seconds after the cause of the overload is removed, and the inverter sends another overload signal within 3 seconds after the conveyor moves, the unit completely shuts down, "L2" appears in the display, and the buzzer sounds.
• To reset, use the "ON/OFF" button to turn the unit off and then back on.
If the unit shuts down with a conveyor overload error, the error signal from the inverter is reset, and the unit restarts after 3 seconds. If the cause of the overload (e.g. dish caught in conveyor) has not been removed by then, the unit starts and stops repeatedly. To prevent this repetition, if the same error occurs within 3 seconds, the unit remains shut down.
If the unit shuts down with the table limit switch closed, the unit restarts after one or more racks are removed, and the table limit switch does not normally close again within 3 seconds.
• See the chart below for possible causes and remedies.
Code Error
L 2
Inverter sends another conveyor overload signal or table limit switch closes again within 3 seconds after “L1” error resets and unit restarts.
Operation
Unit stops.
Jammed.
Remove obstacle.
Conveyor
Defective (not moving smoothly).
Defective.
Repair.
Gear Motor
Repair or replace.
Defective. Repair or replace.
Inverter
Improper operation. Instruct operator.
Table Limit Switch
Defective. Repair or replace.
38
l) Booster Tank Error (b1)
• If the booster tank error input contacts stay open for more than 2 seconds, "b1" appears in the display, and the buzzer sounds.
• If the booster tank error input contacts stay closed for more than 2 seconds, the alarm resets.
Note: The booster tank error input must be connected to indicate this error code.
Code Error
Booster tank sends error signal.
b 1
Operation
Continues.
Booster Tank
Control Board
Connection Cable
Defective.
Defective.
Repair or replace.
Replace.
Open circuit. Repair or replace.
Connector not properly connected.
Reconnect.
39
m) Booster Tank Water Level Safety Error (b2)
• If the booster tank water level safety fl oat switch opens after the booster tank water level fl oat switch closes, the unit shuts down, "b2" appears in the display, and the buzzer sounds.
• To reset, use the "ON/OFF" button to turn the unit off and then back on.
Operation
Code Error b 2
Booster tank water level safety float switch opens after booster tank water level float switch closes.
Unit stops
Water Heater
Strainer
Water Valve
Booster Tank Water
Level Safety Float
Switch
Control Board
Rinse Spray Arm
Pressure Reducing
Valve
Rinse Water Level
Water supply pressure too low.
Flow rate too low.
Filter clogged.
Open circuit.
Filter clogged.
Defective.
Open circuit or connector not properly connected.
Sticking.
Defective.
Connector not properly connected.
Defective.
Disconnected or water leaks from joint.
Clogged.
Defective.
Insufficient water supply.
40
Readjust.
Readjust.
Clean.
Repair or replace.
Clean.
Replace.
Repair or replace.
Check and clean. See
“ III.D. Float Switch
Check and Cleaning.
”
Replace.
Reconnect.
Replace.
Reconnect.
Clean.
Replace.
Readjust.
C. Service Flow Charts
1. Unit Will Not Start
Unit will not start
Main Power Supply
Emergency Stop Button
ON/OFF Button
Power Failure
No Water Supply
Service Panel
Service Panel Switch
Off, blown fuse, or tripped or defective circuit breaker.
Loose connection.
Not within specifications.
Pressed.
“OFF” position.
Water failure.
Shut off valve closed.
Strainer clogged.
Open.
Out of adjustment and/or open.
Turn on, replace, or check and reset. Call electrician if breaker trips repeatedly.
Tighten.
Refer to nameplate and correct.
Turn clockwise to reset.
Move to “ON” position.
Wait for recovery.
Wait for recovery.
Open.
Clean.
Close.
Adjust and/or replace.
Continue
41
Continue
Transformer
Wiring to Control Board
Control Board
Open coil winding.
Loose connections or open.
In alarm.
Defective.
Replace.
Check continuity and repair or replace.
See “III.B. Error
Codes.”
Replace.
42
2. Dishes Not Clean
Dishes not clean
Low Wash Pump
Output
Wash Spray Arms
Filter
Dish Rack
Dishes
Clogged with foreign matter.
Voltage drop.
Vapor lock due to clogged tank filter.
Vapor lock due to use of neutral cleaner.
Wash pump defective.
Clogged.
Out of position.
Low pump output.
Out of position.
Clogged
Improperly loaded.
Excessively dirty.
Clean.
Remove cause.
Clean tank filter.
Stop using neutral cleaner.
Replace.
Clean.
Set in position.
See “Low Wash Pump
Output”.
Place in position.
Clean.
Load correctly.
Prewash.
Continue
43
Continue
Detergent
Wash Tank Water
Heater Not Energized
Conveyor Speed
Voltage
No supply.
Insufficient supply.
Unspecified detergent used.
Dirty.
Temperature too low.
Temperature will not rise.
Control output error.
Magnetic contactor defective.
Overheat thermostat tripped.
Defective.
Too high.
Too low.
See “III.C.5. No or
Inadequate
Detergent/Rinse Aid
Supply.”
Refill or adjust detergent feeder.
Use specified detergent only.
Drain wash tank and supply fresh hot water.
Raise setting or see
“Heater Not
Energized”.
Reset overheat thermostat.
Check input/output and repair or replace.
Replace.
Reset manually.
Replace.
Adjust to medium or low.
Call electrician.
44
3. Inadequate Rinse
Inadequate rinse
Low Rinse Pump
Output
Rinse Spray Arms
Dish Rack
Rinse (Booster Tank)
Water
Rinse Cycle Time
Voltage
Clogged with foreign matter.
Rinse water line scaled.
Voltage drop.
Rinse pump defective.
Clogged.
Out of position.
Low pump output.
Improperly loaded.
Temperature too low.
Too short.
Too low.
Clean.
Clean.
Remove cause.
Replace.
Clean.
Set in position.
See “Low Rinse Pump
Output.”
Load correctly.
Raise setting or see
“ Heater Not
Energized.
”
Adjust longer.
Call electrician.
45
4. Dishwasher Will Not Start Wash/Rinse Cycle
Dishwasher will not start wash/rinse cycle
Wash Pump Inoperative
Rinse Pump Inoperative
Service Panel Magnet
Detection Error
Wash Start Switch
Rinse Start Switch
Protector tripped.
Locked with foreign matter.
Controller input/output error.
Magnetic contactor defective.
Protector tripped.
Locked with foreign matter/
Controller input/output error.
Relay defective.
Service panel not fully closed.
Magnet out of position.
Service panel switch out of position.
Magnetic material caught between service panel and tank.
Defective.
Defective.
46
Wait until wash pump cools.
Remove obstacles.
Check input/output and repair or replace.
Replace.
Wait until Rinse Pump cools.
Remove obstacles.
Check input/output and repair or replace.
Replace.
Close completely.
Set in position.
Set in position.
Remove.
Replace.
Replace.
5. No or Inadequate Detergent/Rinse Aid Supply
No or inadequate detergent/rinse aid supply
Empty.
Detergent/Rinse Aid
Clogged or kinked.
Supply Line (Injector,
Vinyl Hose, Strainer)
Air in line.
Detergent Pump
Supply volume too low.
Defective.
Refill.
Clean or straighten.
Purge air.
Set to proper volume.
Replace.
6. Wash Tank Water Boils
Wash tank water boils
Thermistor
Out of position.
Disconnected (open).
Set in position.
Reconnect.
Defective.
Contact fused.
See “III.E. Thermistor
Check.”
Replace.
Magnetic Contactor
Heater Control Relay
Bad contacts.
Defective.
Check for continuity and replace.
Replace.
Control Board
Note: See “III.E. Thermistor Check” and “IV.H. Removal and Replacement of Thermistor.”
47
7. Wash Tank Water Not Draining
Wash tank water not draining
Drain Hose
Drain Pipe
(Overflow Pipe)
Clogged.
Pinched.
Raised.
Clogged.
Unclog.
Correct.
Correct.
Unclog.
48
D. Float Switch Check and Cleaning
(for Booster Tank Water Level Float Switch and Backup Water Level Float Switch)
If an abnormal input signal is found by “III.A. Diagnostic Procedure” or the error code “o1” or
“o2” is displayed, check and clean/replace the fl oat switches according to the procedure below.
1. Float Switch Check
To check the fl oat switches, follow the steps below.
1) Use the “ON/OFF” button on the operation panel to turn off the unit, then turn off the dishwasher and booster tank power supplies. Lockout/Tagout to prevent the power supplies from being turned back on inadvertently.
2) Remove the front panel and top panel of the booster tank.
3) Remove the control box cover, and disconnect the CN8 connector from the control board
(see “II.F.2. Control Board Layout”).
4) To check the booster tank water level fl oat switch, check for continuity across the orange and red wires (#1 and #2) on the CN8 connector. Con fi rm that the fl oat switch is open when the fl oat is down and closed when the fl oat is up.
5) To check the booster tank backup water level fl oat switch, check for continuity across the pink and light blue wires (#3 and #4) on the CN8 connector. Con fi rm that the fl oat switch is open when the fl oat is down and closed when the fl oat is up.
6) If any problem is found, repair or replace the fl oat switch.
7) If the fl oat switch is scaled up or dirty, clean it according to “2. Float Switch Cleaning.”
2. Float Switch Cleaning
Depending on local water conditions, scale may build up on the fl oat switches. Scale on the switches can cause the fl oats to stick. In this case, the fl oat switches should be cleaned.
1) Use the “ON/OFF” button on the operation panel to turn off the unit, then turn off the dishwasher and booster tank power supplies. Lockout/Tagout to prevent the power supplies from being turned back on inadvertently.
2) Remove the front panel and top panel of the booster tank.
3) Use a soft brush to remove scale or soil on the fl oat switches, or wipe down the fl oat switches with a mixture of 1 part of Hoshizaki “Scale Away” and 25 parts of warm water.
4) Rinse the parts thoroughly with clean water.
5) If the fl oat switch is removed, replace it in its correct position. Be careful not to confuse the positions and directions of the booster tank water level fl oat switch and the booster tank backup water level fl oat switch. Make sure the fl oats can move freely in the vertical directions (see “II.A.2. Booster Tank”).
6) Replace the booster tank panels.
49
E. Thermistor Check
If the error code “H1” “H2” “H3” or “H4” or an abnormal temperature [above 231°F (111°
C) or below -6°F (-21°C)] appears in the display, or the wash tank water boils, check the thermistor(s) according to the procedure below. If replacement is required, see “IV.H.
Removal and Replacement of Thermistor.”
1) Use the “ON/OFF” button on the operation panel to turn off the unit, then turn off the dishwasher and booster tank power supplies. Lockout/Tagout to prevent the power supplies from being turned back on inadvertently.
2) Remove the front panel, then pull out the control box.
3) Remove the control box cover, then disconnect the CN7 connector from the control board
(see “II.F.2. Control Board Layout”).
4) To check the wash tank thermistor, check the resistance across the white wires (#1 and
#2). To check the booster tank thermistor, check the resistance across the pink wires (#3 and #4). See the table below for proper resistance and temperature relations.
Temperature [°F (°C)] Resistance [k Ω ]
194 (90) 4.30 to 4.62
176 (80) 5.87 to 6.38
158 (70) 8.13 to 8.96
140 (60)
104 (40)
11.5 to 12.8
24.3 to 28.0
68 (20)
32 (0)
56.3 to 67.1
145.6 to 180.6
5) If any problem is found, replace the thermistor according to “IV.H. Removal and Replacement of Thermistor.”
50
IV. Removal and Replacement of Components
WARNING
1. This unit should be diagnosed and repaired only by qualified service personnel to reduce the risk of death, electric shock, serious injury, or fi re.
2. Use the “ON/OFF” button on the operation panel to turn off the unit, then turn off the dishwasher and booster tank power supplies. Lockout/Tagout to prevent the power supplies from being turned back on inadvertently.
3. When draining the booster tank, wait until the water temperature falls below
104°F (40°C) to avoid possible burns.
4. To avoid possible burns and spills, be sure to drain the wash tank and booster tank and let the components cool before servicing.
5. When disassembling components that have been in contact with detergent, wear rubber gloves and goggles. Before starting disassembly, thoroughly read the detergent safety instructions. Contact with skin may cause irritation and contact with eyes may cause blindness.
6. When reassembling components, be sure to use new O-rings and gaskets.
A. Removal of Panels
1) The front panel and side panels (L) and (R) are inserted inside the tank rim at the top and secured with 2 screws at the bottom. Unscrew and pull down to remove.
Note: The side panel at the booster tank side is not removable.
2) To replace, reverse the above procedure.
B. Removal and Replacement of Wash Pump Motors
To remove:
1) Use the “ON/OFF” button on the operation panel to turn off the unit, then turn off the dishwasher and booster tank power supplies. Lockout/Tagout to prevent the power supplies from being turned back on inadvertently.
2) Drain the wash tank.
3) Remove the front panel.
4) Remove the fan motors.
5) Disconnect the wash pump motor wiring at the closed end connectors.
6) Remove the bands, and disconnect the wash pump motors from the tank discharge outlets and suction inlets.
7) Loosen the wash pump motor bracket mounting screws to remove the wash pump motors together with the brackets.
8) Remove the pump plugs and the brackets from the wash pump motors.
To replace:
Note: Be sure to use new O-rings and gaskets.
1) Attach the brackets and the pump plugs to the wash pump motors.
2) Fit the O-rings to the wash pump motor discharge outlets and suction inlets.
3) Hook the brackets on the mounting screws left on the unit.
51
4) Make sure the O-rings are in place, and attach the wash pump motors to the tank discharge outlets and suction inlets. Secure the connections with the bands.
5) Tighten the bracket mounting screws.
6) Fill the tank with water, then check for water leaks from the joints. If there is a water leak, check the connections, and retighten the bands. If there are no water leaks, drain the tank.
7) Connect the wiring. When finished, cover the connections with the original plastic sheet cover and secure with a nylon tie. Make sure the connections are situated so that water and condensation cannot reach the connections.
Note: Be careful not to mix up the wire colors. Miswiring will cause reversal of the pump motor, resulting in improper operation.
8) Replace the front panel.
9) Make a trial run, and check for water leaks.
Fan Motor
Bracket
Pump Plug
Wash Pump Motor
(Lower Spray Arm) Fan Motor
Band
O-Ring
Wash Pump Motor
(Upper Spray Arm)
C. Removal and Replacement of Rinse Pump Motor
1) Use the “ON/OFF” button on the operation panel to turn off the unit, then turn off the dishwasher and booster tank power supplies. Lockout/Tagout to prevent the power supplies from being turned back on inadvertently.
2) Remove the front panel.
3) Use the booster tank drain hose to drain the booster tank.
WARNING! To avoid possible burns, allow the rinse water temperature to fall below 104°F (40°C) before draining.
4) The rinse pump motor is located at the rear right side of the machine compartment
(JWE-2400CUA-L-25B) or located behind the control box and at the rear left side of the machine compartment (JWE-2400CUA-R-25B).
5) Remove the fan motor in front of the rinse pump motor.
52
6) Disconnect the rinse pump motor wiring at the closed end connectors.
7) Remove the nut from the fl exible tube at the rinse pump motor discharge outlet and the bolts securing the bracket to the unit base.
8) Remove the band from the pipe joint of the booster tank discharge pipe behind the rinse pump motor and the fl exible tube at the rinse pump motor suction inlet. Pull the end of fl exible tube out of the booster tank discharge pipe.
Note: Use a hand mirror for easy removal.
9) Remove the rinse pump motor together with the bracket. Remove the band from the pipe joint of the rinse pump motor suction inlet pipe and fl exible tube to release the fl exible tube.
10) Unscrew the bracket, and remove the rinse pump motor.
11) To replace, reverse the above procedure.
Note:
1. Be careful not to mix up the wire colors. Miswiring will cause reversal of the pump motor, resulting in improper operation.
2. Cover the connections with the original plastic sheet cover and secure with a nylon tie. Make sure the connections are situated so that water and condensation cannot reach the connections.
3. Be sure to use new O-rings and gaskets. Be careful of the direction of the
U-packing for the suction inlet pipe.
12) Make a trial run, and check for water leaks.
Rinse Pump Motor
[JWE-2400CUA-L-25B]
* For JWE-2400CUA-R-25B, fan motor and rinse pump motor are located behind control box
Sunction Inlet Pipe
U-Packing
Discharge
Outlet Nut
Flexible Tube
Rinse Pump Motor
53
Fan Motor
Booster Tank
Drain Hose
[JWE-2400CUA-L-25B]
* View without rinse pump motor
Band
Booster Tank
Discharge Pipe
Rinse Pump Motor Suction Inlet
Flexible Tube
Rinse Pump Motor Suction Inlet
Flexible Tube
Band
Rinse Pump Motor
Booster Tank
Discharge Pipe
54
D. Removal and Replacement of Gear Motor
1) Use the “ON/OFF” button on the operation panel to turn off the unit, then turn off the dishwasher and booster tank power supplies. Lockout/Tagout to prevent the power supplies from being turned back on inadvertently.
2) Remove the front panel.
3) The gear motor is located behind the control box and at the rear left side of the machine compartment (JWE-2400CUA-L-25B) or located at the rear right side of the machine compartment (JWE-2400CUA-R-25B).
4) Disconnect the gear motor wiring at the closed end connectors.
5) Remove the bolts securing the bracket to the unit base and the nuts securing the bracket to the wash tank.
6) Loosen the 2 hexagon socket set screws for the coupling.
7) Slide up the coupling, and remove the gear motor together with the bracket.
8) Remove the gear motor from the bracket.
9) To replace, reverse the above procedure.
Note:
1. Fit the coupling securely on the gear motor shaft.
2. Apply a thread sealant to the hexagon socket set screws, and tighten them securely.
3. Align the gear motor shaft with the crankshaft from the wash tank.
4. Be careful not to mix up the wire colors.
10) Make a trial run, and check for water leaks.
Bracket
(Wash Tank)
Flinger
Coupling
Hexagon Socket
Set Screw
Nut
Gear Motor
Bracket
Bolt
55
E. Removal and Replacement of Conveyor
1) Remove the 4 bolts (2 at rear, 2 at both sides) securing the rear rack rail.
2) Hold the conveyor, and lift off the rear rack rail.
3) Take out the conveyor.
Slider
4) Remove the left and right frames from the conveyor.
5) Remove the 5 nuts each of the conveyor rails to release the hooks and the bearings.
6) To replace, reverse the above procedure.
Note: Be careful of the slider direction when fi tting the conveyor on the crankshaft slider.
7) Adjust the reed switch position.
8) Make a trial run, and check for water leaks.
• Push out the wider side
• Face the reinforcing rib side down
Align the end of reed switch to the center of hole
Reed Switch < Front View >
Roller
Frame
Rack Rail
Rack Rail
Conveyor
Frame
Conveyor
Hook
Bearing
Roller
Remove nuts
Frame
56
F. Removal and Replacement of Crankshaft
To remove:
1) Remove the front panel.
2) Remove the conveyor.
3) Loosen the 6 hexagon socket set screws for the stopper and the coupling.
4) Lift off the crank together with the shaft.
5) Loosen the screw securing the crank to release the crank from the shaft.
Note: Do not disassemble the housing, oil seals and bearing.
To replace:
1) Fit the housing (up) on the housing, and put the sleeve bearing and the crankshaft into the housing.
2) Fit the sleeve bearing, stopper, fl inger and coupling from the bottom of the crankshaft.
Secure the 2 hexagon socket set screws for the stopper with their ends in the crankshaft groove. Secure the 4 hexagon socket set screws for the coupling to connect the crankshaft and the gear motor.
Note: Apply a thread sealant to the hexagon socket set screws, and tighten them securely.
Key (Short)
3) Fit the housing cover, crank arm and keys, then secure them with the hexagon head bolt.
4) Replace the conveyor.
5) Make a trial run, and check for water leaks.
Note:
1. When replacing the bearing and shaft, apply plastics grease to the mating surfaces.
2. Be careful not to damage or pinch the oil seal lips.
Hex Head
Bolt
Crank Arm
Housing Cover
Crankshaft
Key (Long)
Bracket
(Wash Tank)
Sleeve Bearing
Flinger
Bracket
Coupling
Gear Motor
Housing (Up)
Oil Seal
Bearing
Oil Seal
Housing
Sleeve Bearing
Stopper
Hex Socket
Set Screw
57
G. Removal and Replacement of Control Box
WARNING
Do not touch the live parts during a trial run or servicing operations.
NOTICE
Be careful not to damage the wiring when handling the control box.
1) Use the “ON/OFF” button on the operation panel to turn off the unit, then turn off the dishwasher and booster tank power supplies. Lockout/Tagout to prevent the power supplies from being turned back on inadvertently.
2) Remove the front panel.
3) Slide out the control box.
4) Remove the control box cover. For component locations, see “II.A.3.
Control Box.”
Control Box
5) To remove the conveyor speed switch, turn the lever behind the volume in the direction of the arrow, remove the switch body, remove the nut behind the volume, and pull out the volume.
6) To replace, reverse the above procedure.
H. Removal and Replacement of Thermistor
NOTICE
1. The thermistors are fragile; handle very carefully.
2. Always use the recommended sealant (high thermal conductive type), Model
KE4560RTV manufactured by SHINETSU SILICONE, Part Code 60Y000-11, or Part Code 4A0683-01 or equivalent.
3. Do not shorten or cut the thermistor leads.
1) Use the “ON/OFF” button on the operation panel to turn off the unit, then turn off the dishwasher and booster tank power supplies. Lockout/Tagout to prevent the power supplies from being turned back on inadvertently.
58
2) Remove the front panel.
3) Slide out the control box.
4) Remove the plastic bag covering the thermistor connector, then disconnect the thermistor connector. If replacing the wash tank thermistor, disconnect the leads from the wash tank electrode. If replacing the booster tank thermistor, disconnect the closed end connectors for the booster tank water level fl oat switch and the booster tank backup water level fl oat switch.
5) Remove the tape or ties securing the thermistor leads, then pull out the thermistor from the wash tank or booster tank straight towards you.
6) Clean out all old sealant from inside the thermistor hole.
7) Route the wires from the new thermistor connector through the existing black plastic sleeve.
8) Apply the recommended sealant (KE4560RTV, Part Code 60Y000-11 or 4A0683-01) to the end of the new thermistor, then insert the thermistor quickly and securely.
9) Use tape or ties to secure the thermistor leads in their correct position.
10) Reconnect the thermistor connector and the wash tank electrode leads or the booster tank water level fl oat switch and booster tank backup water level fl oat switch leads, then bag and tie them.
11) Replace the control box and the front panel in their correct positions.
NOTICE
Be careful not to damage the wiring when handling the control box.
I. Removal and Replacement of Control Board or Operation Board
When replacing a control board or operation board, follow the precautions below.
NOTICE
1. The control board and operation board are fragile; handle very carefully.
2. The control board and operation board contain integrated circuits, which are susceptible to failure due to static discharge. It is especially important to touch the metal part of the unit when handling or replacing the control board or operation board.
3. Do not touch the electronic devices on the control board or operation board or the back of the control board or operation board.
4. Do not change wiring and connections.
5. Always replace the whole control board or operation board assembly if it goes bad.
6. Do not short out power supply to test for voltage.
1. Control Board
1) Use the “ON/OFF” button on the operation panel to turn off the unit, then turn off the dishwasher and booster tank power supplies. Lockout/Tagout to prevent the power supplies from being turned back on inadvertently.
2) Remove the front panel and the control box cover.
59
3) Disconnect the control board connectors from the control board.
4) Slide out the control board.
5) Install the new control board.
6) To replace, reverse the above procedure.
2. Operation Board
1) Use the “ON/OFF” button on the operation panel to turn off the unit, then turn off the dishwasher and booster tank power supplies. Lockout/Tagout to prevent the power supplies from being turned back on inadvertently.
2) Remove the screws securing the operation box and the cable cover to the top of the dishwasher.
3) Remove the 4 screws from the bottom of the operation box, and remove the cover.
4) Remove the screws securing the stay - OP, joint - operation (B), and operation panel
(B).
5) Disconnect the connector for the operation board cable and the cable - operation.
6) Install the new operation board.
Note: Remove the 2.0 mm dia tube (A) from the inside groove of the old board, and attach the tube (A) to the new board.
7) To replace, reverse the above procedure.
Note: Make sure the tubes are snug inside the joint - operation (B) and operation panel
(B).
Stay - OP
Joint - Operation (B)
Operation Panel (B)
Cable - Operation
Connector
Tube (B)
Tube (A)
Operation Board
60
J. Removal and Replacement of Heater
When replacing the wash tank heater or the booster tank heater, remove the nuts using a
7/8" crowfoot wrench.
When replacing the booster tank heater, move the clean dishtable above the booster tank before following the procedure below.
1) Use the “ON/OFF” button on the operation panel to turn off the unit, then turn off the dishwasher and booster tank power supplies. Lockout/Tagout to prevent the power supplies from being turned back on inadvertently.
2) Remove the front panel of the dishwasher (wash tank heater).
Remove the front panel of the booster tank (booster tank heater).
3) Use the over fl ow pipe to drain the wash water tank (wash tank heater).
Use the booster tank drain hose to drain the booster tank (booster tank heater).
WARNING! To avoid possible burns, allow the rinse water temperature to fall below 104°F (40°C) before draining.
4) Remove the tank fi lters and the separator (wash tank heater).
Remove the top panel of the booster tank (booster tank heater).
5) Disconnect the heater wiring at the closed end connectors.
6) Use a 7/8" crowfoot wrench to remove the nuts from the heater.
7) Remove the band from the heater inside the tank.
8) Remove the heater.
9) To replace, reverse the above procedure.
Note:
1. When rewiring the heater, refer to the wiring diagram to prevent miswiring.
2. The tightening torque for the nuts securing the heater must be no more and no less than 23 lbf•in.
3. To fit the band on the heater inside the tank, first slide the band from the front straight part to the back of the heater, hook one end in the square hole, and secure the other end with the bolt.
Bolt
Band
Heater
* The illustration shows the boster tank heater
Washer
Nut
61
* The illustration shows the boster tank heater
Bolt Heater
Band
Nut
Washer
Band Heater Square Hole
Cross-section: band fi tting
K. Removal and Replacement of Float Switch
When replacing the fl oat switch, move the clean dishtable above the booster tank before following the procedure below.
1) Use the “ON/OFF” button on the operation panel to turn off the unit, then turn off the dishwasher and booster tank power supplies. Lockout/Tagout to prevent the power supplies from being turned back on inadvertently.
2) Remove the front panel of the booster tank.
3) Use the booster tank drain hose to drain the booster tank. WARNING! To avoid possible burns, allow the rinse water temperature to fall below 104°F (40°C) before draining.
4) Remove the top panel of the booster tank.
5) Disconnect the heater wiring at the closed end connectors.
6) Remove the nuts from the fl oat switch.
7) To replace, reverse the above procedure.
Note:
1. Keep the fl oat switch straight in the proper direction to prevent contact with the tank walls and other parts.
2. The tightening torque for the nuts securing the fl oat switch must be no more and no less than 14 lbf•in.
62
L. Removal and Replacement of Thermostat
NOTICE
Always use the recommended sealant (high thermal conductive type), Model
KE4560RTV manufactured by SHINETSU SILICONE, Part Code 60Y000-11, or
Part Code 4A0683-01 or equivalent.
When replacing the thermostat in the wash water tank or the booster tank, remove the thermostat, clear any remaining sealant from the tank walls, apply a proper amount of the above recommended sealant to the new thermostat bulb, then install the new thermostat in its correct position.
63
V. Cleaning and Maintenance Instructions
A. Daily Maintenance
IMPORTANT
Be sure to clean the dishwasher after closing time every day. It is dif fi cult to remove heavy soils left overnight. In high temperature conditions, food scraps will rot and affect sanitary operation.
1) Remove the three curtains at the entrance, center, and exit of the wash compartment.
2) Open the service panel.
3) To remove the upper wash spray arm, hold it securely with one hand, then pull the front lever towards you with the other hand.
4) To remove the lower wash spray arm, hold both sides, slightly lift the front off the pins, pull the arm towards you, then lift off the back.
5) To remove the upper rinse spray arm, turn the top away from you to unhook, then lift off the end of the pipe.
64
6) To remove the lower rinse spray arm, push down the rising part to unhook, pull off the end of the pipe towards you, then take it out from between the rack rails.
7) Remove the separators.
8) Take out scraps from the removed tank filters, drain pipe and separators, and wash them clean with a scouring pad.
IMPORTANT
To prevent damage, do not hit the fi lters on the sink to drop scraps or to drain the fi lters.
9) If the wash spray arm and rinse spray arm nozzles are clogged, use a wire or brush to unclog and wash them clean.
Rinse
Spray Arm
Wash
Spray Arm
10) Wash the curtains.
65
11) Clean the wash compartment. Remove any scraps from inside the wash compartment and wash tank.
Use a scouring pad to wash off heavy soils. Remove any silverware left inside the wash compartment.
Silverware
12) Check the pump filters inside the wash tank. If they are clogged, clean them with a scouring pad.
13) Check the water level sensor. If it is dirty, clean it with a soft brush.
Pump Filter
IMPORTANT
Do not use a metal brush to clean the water level sensor. The surfaces may be damaged, or metal particles attached to the sensor may cause malfunction.
14) Replace the separators in their correct positions.
15) Install the left and right tank fi lters.
16) Insert the drain pipe.
66
17) To replace the upper wash spray arm, hold it with the nozzles facing down, and insert the joint into the pipe located at the back of the wash compartment. Lift up the front, then securely hook in the square hole.
Hook
18) To replace the lower wash spray arm, hold both sides with the nozzles facing up, and put it under the rack rails from the front. Insert the joint into the pipe located at the back of the wash compartment. Fit the holes on the pins at the front of the wash tank.
Rack Rail
19) To replace the upper rinse spray arm, insert the end of the pipe into the joint, then turn and hook the top.
Ring
67
20) To replace the lower rinse spray arm, put it between the rack rails, insert the end of the pipe into the joint, then turn and hook the front.
21) Install the curtain (L) in the wash compartment.
Ring
Curtain Rod
(longer)
22) Install the curtains (S) at the entrance and exit of the wash compartment.
Fit front fi rst
Curtain Rod
(shorter)
Fit in rear notch
68
23) Close the service panel.
WARNING
To prevent entrance of dust or insects and injuries by a sudden drop, do not leave the service panel open.
B. Weekly Maintenance
1. Heater
WARNING
To prevent burns, wait for 10 minutes after draining the unit to clean the interior.
Remove any scraps from the heater, and use a soft brush to wash off residue.
Soft Brush
Do not use a metal brush which may damage the surface.
Heater
2. Exterior
1) Wipe the exterior with a soft cloth.
2) Use a damp cloth containing a neutral cleaner to wipe off dirt. Then wipe away the residue with a clean cloth.
C. Monthly Inspection
1. Water Supply Line
Check the water supply line for damage, deformation, or water leak marks (stains). If any of these conditions are found, contact an authorized Hoshizaki service company.
Recommendation of safety inspection by service personnel
Even if there is no problem with its use, a product out of warranty may have a risk of electric shock, fi re, or water leak due to insulation degradation or aging of the electrical parts. Ask an authorized Hoshizaki service company for the following inspections (charged):
• Dust and dirt build-up or water leak inside the unit
• Aging conditions of the unit and its components
• Scale, silica, lime or other foreign matter in the water circuit
69
D. Descaling (As Required)
Use a descaler according to the supplier’s instructions.
WARNING
1. Carefully follow any instructions provided with the descaler.
2. Always wear liquid-proof gloves and goggles to prevent the descaler from coming into contact with skin or eyes.
3. To prevent generation of toxic chlorine gas, do not mix a descaler with a chlorinated cleaner.
1) Pull out the drain pipe to drain water from the wash tank. Start the auto fi ll cycle to fi ll the wash tank with hot water.
2) Use the “ON/OFF” button to turn off the unit. Refer to the descaler's directions and add the proper amount of descaler to the wash tank. The wash tank holds 26.4 gallons of water.
3) Press and hold the up and down buttons and the “CHANGE” button, then press the “ON/
OFF” button to select the “PC” (Preventative Cleaning) mode.
4) Refer to the descaler's directions for the proper duration of cleaning. When the proper amount of time has passed, press the “ON/OFF” button to stop cleaning.
5) Check the wash tank interior. Repeat steps 1) through 4) if necessary.
WARNING
Be careful not to burn yourself with the hot water or parts in the wash tank.
6) Drain the wash tank, then start the auto fi ll cycle. Run the dishwasher to rinse the wash tank thoroughly. Drain the wash tank.
E. Shutdown
NOTICE
If there is a possibility that the ambient temperature may fall below
32°F (0°C) and freeze the unit, be sure to drain the unit. The water supply line could be damaged and leak water, resulting in damage to the surrounding property.
Dishwasher
Water Heater
Water Supply Line
Shut-off Valve
Gas Supply Line
Shut-off Valve
Drain Valve
To drain out the water heater, close the water supply line shut-off valve, and open the drain valve and water supply valve.
Booster Tank Water Supply Valve
70
1) Press the “ON/OFF” button on the operation panel. The display and lamps go off.
2) Turn off the water heater.
3) Turn off the gas and water supplies.
IMPORTANT
To operate the water heater, follow its instruction manual.
4) Open the service panel.
Service Panel
Hook
IMPORTANT
Be sure to hook the service panel in its open position.
5) Pull out the drain pipe to drain water from the wash tank.
WARNING
When pulling out the drain pipe, be careful not to touch the wash water. It may cause burns or skin irritation. Turn the drain pipe if it is hard to pull out.
6) Remove the two tank filters without spilling scraps inside.
71
F. Long Storage, Relocation, Disposal, Transfer
When preparing the unit for long storage, shut down and clean the unit according to sections A - E.
If something seems wrong when restarting the unit after long storage, turn off the power supply, and immediately contact an authorized Hoshizaki service company.
WARNING
1. When restarting the unit after long storage, contact an authorized Hoshizaki service company. To prevent electric shock, do not restart the unit by yourself.
2. In case of relocation, contact an authorized Hoshizaki service company.
Improper installation may cause water leak, electric shock or fi re.
3. When disposing of the unit, contact an authorized Hoshizaki service company.
Leaving the unit may violate laws or cause an unexpected accident.
NOTICE
When selling or transferring this product, tape the instruction manual and the installation manual to the exterior to provide the new owner with information on safe and proper use of the product.
VI. Operating Instructions
• Before loading dishes in the rack, be sure to remove any leftovers (ex. meat, fish, vegetables), chopsticks, toothpicks, sticks, straws, paper products and plastics from the dishes. They may clog the piping and wash pump, resulting in reduction of washing performance or pump failure.
• Install the separator and tank filters without creating a large gap at the tank overlap.
Do not bang the tank fi lters and separator to clean or drain, or they may be deformed.
Leftovers and other foreign matter may enter the tank and clog the piping and wash pump, resulting in reduction of washing performance or pump failure.
• Insert the drain pipe (overflow pipe) after installing the separator. The separator may rise up to create a large gap at the tank overlap. Leftovers and other foreign matter may enter the tank and clog the piping and wash pump, resulting in reduction of washing performance or pump failure.
• After closing time, always clean the tank fi lters, wash/rinse spray arms and water level sensor. When disassembling the spray arms, check and remove any leftovers clogging the pipe joints. Otherwise the leftovers may become hard to remove or spoil.
• Read the instruction manual carefully to ensure safe and proper operation.
72
VII. Technical Information
A. Water Circuit
Detergent Feeder
(not provided)
Upper Wash
Spray Arm
Lower Wash
Spray Arm
Upper Rinse
Spray Arm
Backup Water
Level Float Switch
Lower Rinse
Spray Arm
Rinse Aid Feeder
(not provided)
Water Level
Float Switch
Inlet Water Valve
Wash
Water
Booster
Tank
Gear Motor
Hot Water
Wash Tank Heater
Wash Pump
(Lower Spray Arm)
Drain
Wash Pump
(Upper Spray Arm)
Drain Pipe
Rinse Pump
Water Level Sensor
Water Level Safety
Float Switch
Booster Tank Heater
• The wash water is sprayed by the two wash pumps from the upper and lower wash spray arms into the wash compartment.
• The rinse water is sprayed by the rinse pump from the upper and lower rinse spray arms into the wash compartment.
• The detergent is fed by the detergent feeder (not provided by Hoshizaki) through the detergent outlet (not provided by Hoshizaki) into the wash tank.
• The rinse aid is fed by the rinse aid feeder (not provided by Hoshizaki) into the rinse water line and sprayed from the upper and lower rinse spray arms into the wash compartment.
73
B. Wiring Diagram
74
advertisement
Key Features
- High-temperature sanitizing rinse ensures dishes are hygienically clean.
- Automatic fill and drain system simplifies operation and saves water.
- Energy-efficient design reduces utility costs.
- Compact size fits easily into tight spaces.
- Durable construction withstands heavy use.
- Easy-to-use controls and digital display for intuitive operation.
- Multiple wash cycles to accommodate various dishwashing needs.
- Self-diagnostic system simplifies troubleshooting.
- Low water and energy consumption for environmental sustainability.
Related manuals
Frequently Answers and Questions
What is the rinse water temperature?
What is the capacity of the unit?
What is the power consumption of the unit?
What is the warranty period?
What are the dimensions of the unit?
advertisement
Table of contents
- 6 I. Specifi cations
- 6 A. Specifi cation Sheet
- 6 1. JWE-2400CUA-L-25B
- 7 2. JWE-2400CUA-R-25B
- 8 B. Nameplate Rating
- 9 C. Dimensions/Connections
- 9 1. JWE-2400CUA-L-25B
- 10 2. JWE-2400CUA-R-25B
- 11 II. General Information
- 11 A. Construction
- 11 1. Dishwasher
- 12 2. Booster Tank
- 13 3. Control Box
- 14 B. Functions
- 14 1. Increasing Rinse Water Flow Rate
- 14 C. Sequence of Operation
- 14 1. Auto Fill Cycle
- 15 2. Ready Cycle (Unit Inactive)
- 15 3. Wash Cycle/Rinse Cycle
- 16 4. Table Limit Switch
- 16 5. Emergency Stop Button
- 16 6. Drain
- 17 D. Sequence of Operation Flow Chart
- 18 E. Timing Chart
- 18 1. Auto Fill Cycle
- 19 2. Wash Cycle/Rinse Cycle
- 20 F. Control Board and Operation Board
- 20 1. Control Board Location
- 21 2. Control Board Layout
- 22 3. Control Board Diagram
- 23 4. Operation Panel Layout
- 23 5. Features
- 23 6. Controls, Adjustments, and Lamps
- 24 7. Service Menu and Error Log
- 26 8. Temperature Display
- 26 9. Error Codes
- 26 10. Buzzer
- 27 11. Operation Time Display
- 27 12. Special Modes
- 29 III. Service Diagnosis
- 29 A. Diagnostic Procedure
- 31 B. Error Codes
- 31 1. Error Code Table
- 32 2. Error Code Log
- 33 3. Error Code Details
- 46 C. Service Flow Charts
- 46 1. Unit Will Not Start
- 48 2. Dishes Not Clean
- 50 3. Inadequate Rinse
- 51 4. Dishwasher Will Not Start Wash/Rinse Cycle
- 52 5. No or Inadequate Detergent/Rinse Aid Supply
- 52 6. Wash Tank Water Boils
- 53 7. Wash Tank Water Not Draining
- 54 D. Float Switch Check and Cleaning
- 54 1. Float Switch Check
- 54 2. Float Switch Cleaning
- 55 E. Thermistor Check
- 56 IV. Removal and Replacement of Components
- 56 A. Removal of Panels
- 56 B. Removal and Replacement of Wash Pump Motors
- 57 C. Removal and Replacement of Rinse Pump Motor
- 60 D. Removal and Replacement of Gear Motor
- 61 E. Removal and Replacement of Conveyor
- 62 F. Removal and Replacement of Crankshaft
- 63 G. Removal and Replacement of Control Box
- 63 H. Removal and Replacement of Thermistor
- 64 I. Removal and Replacement of Control Board or Operation Board
- 64 1. Control Board
- 65 2. Operation Board
- 66 J. Removal and Replacement of Heater
- 67 K. Removal and Replacement of Float Switch
- 68 L. Removal and Replacement of Thermostat
- 69 V. Cleaning and Maintenance Instructions
- 69 A. Daily Maintenance
- 74 B. Weekly Maintenance
- 74 1. Heater
- 74 2. Exterior
- 74 C. Monthly Maintenance
- 74 1. Water Supply Line
- 75 D. Descaling (As Required)
- 75 E. Shutdown
- 77 F. Long Storage, Relocation, Disposal, Transfer
- 77 VI. Operating Instructions
- 78 VII. Technical Information
- 78 A. Water Circuit
- 79 B. Wiring Diagram