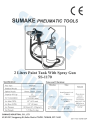
Sumake SS-1170 Owner's Manual
Add to My manuals12 Pages
Sumake SS-1170 is a professional-grade spray gun that comes with a 2-liter paint tank for extended use. With its adjustable air pressure, you can use it for a wide range of painting applications, from fine detailing to large-scale spraying. The external mix air nozzle ensures even distribution of paint particles for a smooth, consistent finish. The gun is made from durable materials and is designed to withstand the rigors of everyday use.
advertisement
▼
Scroll to page 2
of
12
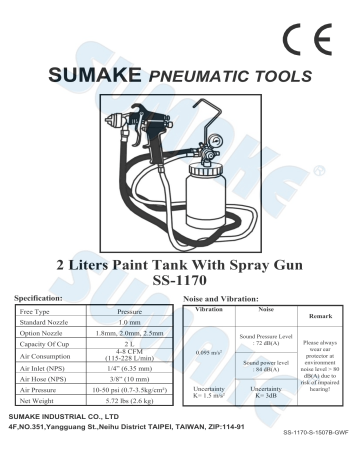
SUMAKE PNEUMATIC TOOLS 2 Liters Paint Tank With Spray Gun SS-1170 Specification: Noise and Vibration: Free Type Pressure Standard Nozzle 1.0 mm Option Nozzle 1.8mm, 2.0mm, 2.5mm Capacity Of Cup Air Consumption 2L 4-8 CFM (115-228 L/min) Air Inlet (NPS) 1/4” (6.35 mm) Air Hose (NPS) 3/8” (10 mm) Air Pressure 10-50 psi (0.7-3.5kg/cm²) Net Weight 5.72 lbs (2.6 kg) Vibration Noise Remark Sound Pressure Level : 72 dB(A) 0.095 m/s² Sound power level : 84 dB(A) Uncertainty K= 1.5 m/s² Uncertainty K= 3dB Please always wear ear protector at environment noise level > 80 dB(A) due to risk of impaired hearing! SUMAKE INDUSTRIAL CO., LTD 4F,NO.351,Yangguang St.,Neihu District TAIPEI, TAIWAN, ZIP:114-91 SS-1170-S-1507B-GWF OPERATION INSTRUCTIONS External Mix Air Nozzle Application OPERATION: Connect hose as shown in diagram. Fill cup with strained fluid mixed in accordance with manufacturer's recommendations on label of container. Fasten cover securely. Close air adjusting valve by turning clockwise. Set air pressure at oil and water extractor (transformer) to between 35 and 80 P.S.I., depending upon atomization desired. Set regulator on pressure cup to approximately 10 P.S.I. for enamels; 5 P.S.I. for lacquers. (Turn knob clockwise to increase pressure; to reduce pressure, turn knob counter-clockwise. Always release air in cup by momentarily opening air release valve on cover when attempting to reduce pressure.) Open air adjusting valve. With trigger fully pulled back, make several fast spray strokes against a flat surface. After adjustment of pressure, proper atomization will be indicated by an even distribution of finely divided paint particles. PLEASE RETAIN FOR FUTURE REFERENCE IMPORTANT: The most efficient atomization air pressure is the lowest air pressure that will properly atomize the paint. This will minimize the overspray, deposit more paint on the surface and eliminate paint wastage. If a faster coverage is necessary, first increase fluid pressure and then adjust atomization air pressure. If a slower coverage is more desirable, first reduce the fluid pressure and then adjust atomization air pressure. Always attempt to maintain the lowest pressures for maximum efficiency. For ease of removing cup cover and to prevent leakage, always thoroughly grease the threads on cup. CLEANING: Open air release valve on pressure cup cover. Reduce pressure in cup until gauge reads zero, (turn knob counter-clockwise). Loosen cup cover and set fluid tube on angle in cup. Loosen air nozzle two turns, place cloth over nozzle and pull the trigger to force paint into cup. Remove cover and clean cup and cover thoroughly. With approximately 1 /4 to 1 /2 cup of clean solvent, attach cover and set fluid pressure at approximately 10 P.S.I. Close air adjusting valve at spray gun. Trigger gun and allow solvent to flow into a container until it flow clear. Remove solvent; then clean air nozzle. If any dirt appears in orifice, clean with tooth pick; wire will damage nozzle. Blow nozzle and cup dry. Replace nozzle and cover loosely. Never allow solvent to remain in cup; solvent vapors tend to reduce service life of gasket. Separate storage of cup and cover recommended. CAUTION: If the cup is accidentally tipped over or held at too great an angle, fluid will load up the under side of cup cover, and leak into regulator. In the event this happens: Clean immediately. Internal Mix Air Nozzle Application Operation: The internal mix air nozzle accomplishes atomization by mixing the air and fluid within the air nozzle. NOTE: The steps are the same as with external mix nozzles, except the air and fluid pressure settings are different. Close air adjusting valve by turning clockwise. Set air pressure at oil and water extractor (transformer) to approximately 45 P.S.I. Open air adjusting valve and allow air to enter the gun. Set fluid pressure at 20 lbs. and adjust higher or lower until desired atomization is effected. Air pressure should be alternately adjusted. SS-1170T-I-1007B-GW EC DECLARATION OF CONFORMITY We: SUMAKE INDUSTRIAL CO., LTD. 4F, No. 351, Yangguang St., Neihu District, Taipei City, Taiwan declare in sole responsibility that the equipment Equipment: 2 LITERS PAINT TANK WITH SPRAY GUN Model/ Serial No.: SS-1170 to which this declaration applies, complies with these normative documents: Machinery Directive: 2006/42/EC and conforms to the following EN standard, EN ISO 12100: 2010 EN 1953:2013 Name and Signature/Position Date and Place 2014/9/15 Mike Su – Managing Director Taipei, Taiwan SS-1170-D-1507C-GWF SS-1170(S) SS-1180(S) SPRAY GUN SPRAY GUN PARTS LIST No. Parts No. 1 1170S-01 Q'ty No. Parts No. Air Nozzle W/Brass Cap 1 22 1170S-22 Housing 1 1170S-04 Fluid Nozzle -1.0 1 1170S-23 Paint Needle Complete -1.0 1 1170S-04A Fluid Nozzle -1.8 1 1170S-23A Paint Needle Complete -1.8 1 1170S-04B Fluid Nozzle -2.0 1 1170S-23B Paint Needle Complete -2.0 1 1170S-04C Fluid Nozzle -2.5 1 1170S-23C Paint Needle Complete -2.5 1 5 1170S-05 Head 1 26 1170S-26 Fluid Control Assembly 1 6 1170S-06 Screw 1 30 1170S-30 Air Valve 1 7 1170S-07 Gun Body 1 36 1170S-36 Screw 1 8 1170S-08 Air Regutafor 1 37 1170S-37 Stud 1 14 1170S-14 Cow Hide Washer 1 38 1170S-38 Trigger 1 15 1170S-15 Pocking Nut 1 39 1170S-39 Screw 1 17 1170S-17 Needle Valve Sleeve 1 40 1170S-40 Air Connection 1 21 1170S-21 Gasket 1 42 1170S-42 Spanner 1 4 Description 23 Description Q'ty SS-1170(S)1180(S)-P-1102B-GW SS-1170(T) 2 LITERS PAINT TANK PARTS LIST No. 1 2 3 4 5 6 7 8 9 10 11 12 13 14 15 16 Parts No. 1170T-01 1170T-02 1170T-03 1170T-04 1170T-05 1170T-06 1170T-07 1170T-08 1170T-09 1170T-10 1170T-11 1170T-12 1170T-13 1170T-14 1170T-15 1170T-16 Description Q'ty 5/16 Hex Jam Nut 1 No.6-32 x 1/4 Rd. Hd. M.Screw 1 Check Valve Washer 1 Center Post Assembly 1 Cup (2 Qt.) 1 Cover Gasket (Rubber) 1 Relief Valve Stem 1 Check Valve 1 Check Valve Spring 1 Fluid Outlet 1 Fluid Tube (2 Qt.) 1 Cover Assembly 1 Container Cover 1 Check Valve Bracket 1 Handle 1 Regulator Assembly 1 SS-1170(T)-P-0509A-GW SPRAY GUN Original instructions SUMAKE Industrial Co. Ltd. Read all these safety instructions before operating this product and save these instructions. The tool has been manufactured in conformity with the instruction of EU machine directive. The EU mark will be considered void in the event of inexpert repairs, the use of non-original parts and in case of non-observance of the safety instructions in the user’s manual. Possible direct or indirect consequential damages are not the responsibility of SUMAKE Industrial co., Ltd. General safety rules: 1. Watch the tool at all times when in use. 2. People under the influence of alcohol or drugs are not allowed to use, repair or maintain the tool. 3. Keep unqualified persons, children, etc. away from the tool. 4. Keep work area clean and with sufficient daylight or artificial lighting. The work area on which the machine is used must be cleaned up. Disorder is a potential cause of accidents. 5. Danger of explosion. Never use oxygen and combustible gas as an air supply for the tool which many be ignited by spark and cause fire or explosion. 6. Never use gasoline or other flammable liquids to clean the tool. 7. Do not use air tools in potentially explosive atmospheres such as in the presence of flammable liquids, cleaning solvents, fluid energy or stored gases. 8. Do not expose air tools to rain. Do not use air tools in damp or wet locations. 9. When a fault or failure is detected, the tool must immediately be disconnected from the air supply and returned for repair. 10. It is not permitted to modify the tool in any way. 11. When not in use, keep tools in a dry place, either locked up or in a high place, out of the reach of children. 12. Do not force small air tools to do the job of a heavy –duty task. Do not use air tool for purpose of which was not intended. 13. Wear suitable ear protection at environment noise level >80dB(A) and safety spectacles when using the tool. Always wear approved safety goggles if work in dusty. This also applies to other persons in the nearby vicinity. 14. Do not wear loose clothing or jewelry. They can be caught in moving parts. Rubber gloves and non-skid foot wear are recommended when working outdoors. Wear protective hair covering to contain long hair. 15. Keep proper footing and balance at all times. 16. Use clamps or a vice to hold work-piece. It is safer than using your hand and free both hands to operate the air tool. 17. When not use, before performing service or changing accessories, please disconnect tool from air compressor. 18. Do not carry plugged in air tool with your finger on the switch trigger. Be sure switch is in the “OFF” position when connecting to air supply. 19. Watch what you are doing. Use common sense, even unsafe situation or unbalanced positions, particularly when you are tired. 20. Air powered tools can vibrate in use. Vibration, repetitive motions or uncomfortable positions may be harmful to your hands or arms. Stop using any tool if discomfort, tingling feeling or pain occurs. Seek medical advice before resuming use. 21. Multiple hazards. Read and understand the safety instructions before installing, operating, repairing, maintaining, changing accessories on, or working near the tool. Failure to do so can result in serious bodily injury. 22. Only qualified and trained operators should install, adjust or use the tool. 23. Do not modify the tool. Modifications may reduce the effectiveness of safety measures and increase the risks to the operator. 24. Do not discard the safety instructions – give them to the operator. 25. Do not use the tool if it has been damaged. 26. Tools shall be inspected periodically to verify the ratings and markings required by this document are legibly marked on the tool. The employer/user shall contact the manufacturer to obtain replacement marking labels when necessary. Safety precautions for projectile hazards 1. Disconnect the tool from the energy source when changing inserted tool or accessories. 2. Failure of the accessories may generate high velocity projectiles. 3. Always wear impact-resistant eye protection during operation of the tool. The grade of protection required should be assessed for each use. 4. The risks to others should also be assessed at this time. 5. Ensure that the work piece is securely fixed. Safety precautions for operating hazards 1. Use of the tool may expose the operator’s hands to hazards including crushing, impacts, cuts and abrasions and heat. Wear suitable gloves to protect hands. 2. Operators and maintenance personnel must be physically able to handle the bulk, weight and power of the tool. 3. Hold the tool correctly: be ready to counteract normal or sudden movements – have both hands available. 4. Maintain a balanced body position and secure footing. 5. Release the start and stop device in the case of an interruption of the energy supply. 6. Use only lubricants recommended by the manufacturer. 7. That unsuitable postures may not allow counteracting of normal or unexpected movement of the tool. 8. If the tool is fixed to suspension device make sure that the fixation is secure. 1 Safety precautions for repetitive motions hazards 1. When using the tool, the operator may experience discomfort in the hands, arms, shoulders, neck, or other parts of the body. 2. While using the tool, the operator should adopt a comfortable posture. Maintain secure footing and avoid awkward or off-balanced postures. The operator should change the posture during extended tasks which may help avoid discomfort and fatigue. 3. If the operator experience symptoms such as persistent or recurring discomfort, pain, throbbing, aching, tingling, numbness, burning sensation or stiffness, these warning signs should not be ignored. The operator should tell the employer and consult a qualified health professional. Safety precautions for accessory hazards 1. Disconnect power tool from energy supply before changing the accessory. 2. Only use sizes and types of accessories and consumables that are recommended by the tool manufacturer. Safety precautions for workplace hazards 1. Slips, trips and falls are major causes of workplace injury. Be aware of slippery surfaces caused by use of the tool and also of trip hazards caused by the air line. 2. Proceed with care in unfamiliar surroundings. Hidden hazards may exist, such as electricity or other utility lines. 3. The tool is not intended for use in potentially explosive atmospheres and is not insulated from coming into contact with electric power. 4. Make sure there are no electrical cables, gas pipes etc. that could cause a hazard if damaged by use of the tool. Safety precautions for dust and fume hazards 1. Dusts and fumes generated when using the tool can cause ill health (for example: cancer, birth defects, asthma and/or dermatitis); risk assessment of these hazards and implementation of appropriate controls of is essential. 2. Risk assessment should include dust created by the use of the tool and the potential for disturbing existing dust. 3. Operate and maintain the power tool as recommended in these instructions, to minimise dust or fume emissions. 4. Direct the exhaust so as to minimise disturbance of dust in a dust filled environment 5. Where dusts or fumes are created, the priority shall be to control them at the point of emission. 6. All integral features or accessories for the collection, extraction or suppression of airborne dust or fumes should be correctly used and maintained in accordance with the manufacturer’s instructions. 7. Use respiratory protection as instructed by your employer or as required by occupational health and safety regulations. Safety precautions for noise hazards 1. Unprotected exposure to high noise levels can cause permanent, disabling, hearing loss and other problems such as tinnitus (ringing, buzzing, whistling or humming in the ears). 2. Risk assessment of these hazards and implementation of appropriate controls of is essential. 3. Appropriate controls to reduce the risk may include actions such as damping materials to prevent work pieces from ‘ringing’. 4. Use hearing protection as instructed by your employer or as required by occupational health and safety regulations. 5. Operate and maintain the power tool as recommended in these instructions, to prevent an unnecessary increase in noise. 6. If the tool has a silencer, always ensure it is in place and in good working order when the tool is operating. 7. Select, maintain and replace the consumable/inserted tool as recommended in these instructions, to prevent an unnecessary increase in noise. Safety precautions for vibration hazards 1. Exposure to vibration can cause disabling damage to the nerves and blood supply of the hands and arms. 2. Wear warm clothing when working in cold conditions and keep your hands warm and dry. 3. If you experience numbness, tingling, pain or whitening of the skin in your fingers or hands, stop using the assembly power tool for non-threaded mechanical fasteners, tell your employer and consult a physician. 4. Support the weight of the tool in a stand, tensioner or balancer, because the operator can then use a lighter grip to support the tool. Additional safety instructions for pneumatic power tools 1. Always shut off air supply, drain hose of air pressure and disconnect tool from air supply when not in use, before changing accessories or when making repairs. 2. Never direct spraying air or liquid at yourself or anyone else. 3. Whipping hoses can cause severe injury. Always check for damaged or loose hoses and fittings. 4. Cold air shall be directed away from the hands. 5. Whenever universal twist couplings (claw couplings) are used, lock pins shall be installed and whipcheck safety cables shall be used to safeguard against possible hose-to-tool and hose-and-hose connection failure. 6. Do not exceed the maximum air pressure stated on the tool. 7. Never carry an air tool by the hose. Specific safety instructions Warnings shall be given about any specific or unusual hazards associated with the use of the power tool. Such warnings shall indicate the nature of the hazard, the risk of injury and the avoidance action to take. 2 General preparation and connection: 1. 2. 3. 4. 5. 1. 2. 3. 4. 5. 6. Before connecting the air hose, apply 4 to 5 drops of SAE#10-20 spindle oil at the air inlet. Also, every 3 to 4 hours of operation, oiling is necessary. Twist Teflon thread tape to ensure a proper seal air inlet. Then tighten the air coupler into air tool. The supplied compressed air must be clean and dry, with the appropriate oil mist. Use an air treatment unit; filter, regulator and lubricator. Please refer Fig.1 illustration shows the correct mode of connection to the air supply system which will increase the efficiency and useful life of the tool. The quick connect coupling and hose must have sufficient air flow capacity. We recommend an air hose with a diameter of 10mm (3/8”). To ensure a good performance. The operation pressure at the compressed air inlet please refer specification indication. Higher operating pressures may cause damaged or excessive wear. Operating pressures below 5.3bar may cause pressure or power loss. Risk of injury Compressed air can inflict serious injuries. Therefore never point the air hose at another person or yourself. Shut – off the air supply and disconnect the tool in case: ➢ You want to change or replace accessories. ➢ You want to clean, repair or maintain the tool. ➢ The tool is not going to use for some times. Check compressed air hose before use. If it is damaged, broken, torn, or deformed, the hose is not to be connected to the tool. Always check the pneumatic couplings before using the tool. If they show signs of damage, fracture, cracking or excessive corrosion, the respective tool or the air hose is not to be used. Use only qualified adapters and connectors, In case of wear they are to be replaced immediately. Only use air pipes that are fit for the use at maximum pressure. Maintenance instruction: 1. Dry the filter (fig1) and the air inlet of the tool. 2. Lubricate the quick connect coupling to prevent blocking. 3. Air tool require lubrication throughout the life of the tool. The air motor and bearing uses compressed air to start the tool. The moisture in compressed air will rust the air motor; you must lubricate the motor daily. 4. Avoid storing the tool in a location subject to high humidity. If the tool is left as it is used, the residual moisture inside the tool can cause rust. 5. Before storage, lubricate tool and run it for a few seconds. 6. Regular inspection of spindles, threads, and clamping devices in respect of wear and tolerances for location of abrasive products. 7. If the tool is too seriously damage to be used anymore, recycle raw material instead of disposing as waste. The machine, accessories and packaging should be sorted for environmental-friendly recycling. Check with your local authority or retailer for recycling advice. 3 SPRAY GUN-I-201304A NOTE www.SUMAKE.com www.AIRCOMPRESSOR.com.tw NOTE www.SUMAKE.com www.AIRCOMPRESSOR.com.tw
advertisement
Key Features
- 2-liter paint tank for extended use
- Adjustable air pressure for versatile use
- External mix air nozzle for even paint distribution
- Durable construction for long-lasting performance
Related manuals
Frequently Answers and Questions
What materials can I use with the Sumake SS-1170?
The Sumake SS-1170 is compatible with a wide range of paints, including enamels and lacquers.
How do I clean the Sumake SS-1170?
Refer to the cleaning instructions provided in the user manual.
What is the recommended air pressure for the Sumake SS-1170?
The recommended air pressure is between 35 and 80 PSI, depending on the desired atomization.
Can I use the Sumake SS-1170 for both external and internal mix applications?
Yes, the Sumake SS-1170 comes with both external and internal mix air nozzles.
advertisement