Additel 773, 783, and 793 User Manual
Add to My manuals79 Pages
Additel 773, 783, and 793 are a range of pressure controllers designed for automated production, pressure testing, and calibration. They provide high control stability, high control rate, and high measurement accuracy, making them a versatile solution for various applications. The controllers feature a modular design, allowing users to select pressure modules based on their range and accuracy requirements. Additionally, the 773 and 793 models have built-in pump sources, eliminating the need for an external air source. These controllers integrate numerous test functions, such as pressure switch test, pressure leak test, and automatic step test, enhancing the user's work efficiency.
advertisement
▼
Scroll to page 2
of
79
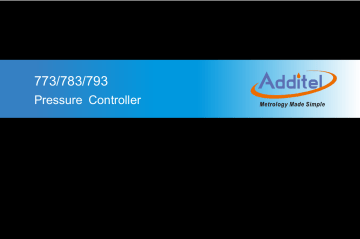
773/783/793 Pressure Controller 773/783/793Pressure Controller -------User Manual [Version number: 2403V01] Additel Corporation Statement This user manual provides operating and safety instructions for Additel 773/783/793 Pressure Controllers. To ensure correct operation and safety, please follow the instructions in this manual. Additel Corporation reserves the right to change the contents and other information contained in this manual without notice. Content SAFETY INSTRUCTIONS ........................................................................................................................................... 1 1.INTRODUCTION ...................................................................................................................................................... 3 1.1 OVERVIEW .....................................................................................................................................................................................3 1.2 MODELS SPECIFICATION ................................................................................................................................................................4 1.3 TECHNICAL SPECIFICATIONS ..........................................................................................................................................................5 2.FIRST TIME USE ....................................................................................................................................................12 2.1 CONTROLLER ILLUSTRATION ........................................................................................................................................................12 2.1.1 Front panel .........................................................................................................................................................................12 2.1.2 Inside Cabin Introduction ..................................................................................................................................................13 2.1.3 Back Panel Ports Description ..........................................................................................................................................15 2.2 FIRST TIME USE ............................................................................................................................................................................18 2.2.1 Power on .............................................................................................................................................................................18 2.2.2 Set date and time ..............................................................................................................................................................18 2.2.3 Output pressure .................................................................................................................................................................18 3.DISPLAY AND OPERATIONS .................................................................................................................................20 3.1 MAIN INTERFACE BRIEF INTRODUCTION ........................................................................................................................................20 3.2 MAIN INTERFACE DETAILED INTRODUCTION ..................................................................................................................................22 3.3 PRESSURE CONTROL ...................................................................................................................................................................27 3.3.1 Pressure control module ranges switching ....................................................................................................................27 3.3.2 Pressure output .................................................................................................................................................................29 I 3.3.3 Pressure measurement ....................................................................................................................................................31 3.3.4 Pressure unit ......................................................................................................................................................................32 4.SYSTEM SETTINGS ...............................................................................................................................................32 4.1 CONTROL SETTINGS .....................................................................................................................................................................33 4.2 MEASURE SETTINGS ....................................................................................................................................................................39 4.3 PERSONAL ...................................................................................................................................................................................39 4.3.1 Date time ............................................................................................................................................................................39 4.3.2 Display ................................................................................................................................................................................40 4.3.3 Sound ..................................................................................................................................................................................40 4.3.4 Language ............................................................................................................................................................................41 4.3.5 System unit .........................................................................................................................................................................41 4.4 SERVICES.....................................................................................................................................................................................41 4.4.1 System calibration .............................................................................................................................................................42 4.4.2 Advanced Configuration ...................................................................................................................................................46 4.4.3 Restore Factory .................................................................................................................................................................47 4.4.4 Firmware update ................................................................................................................................................................47 4.5 COMMUNICATION..........................................................................................................................................................................47 4.5.1 Protocol ...............................................................................................................................................................................47 4.5.2 Ethernet ..............................................................................................................................................................................48 4.5.3 RS232 .................................................................................................................................................................................48 4.5.4 WLAN ..................................................................................................................................................................................49 4.6 EXTENSION INTERFACE ................................................................................................................................................................50 II 4.6.1 Externally driven valves interface ....................................................................................................................................50 4.6.2 DO alarm output interface ................................................................................................................................................51 4.6.3 Pressure switch testing interface.....................................................................................................................................51 4.6.4 Manual output ....................................................................................................................................................................51 4.7 MAINTENANCE..............................................................................................................................................................................51 4.7.1 Maintenance and fluid change (for ADT793) .................................................................................................................51 4.7.2 Piston maintenance (for ADT793) ...................................................................................................................................52 4.7.3 System pressure relief ......................................................................................................................................................52 4.7.4 Accumulator maintenance (for ADT793) ........................................................................................................................53 4.7.5 Assisted aspiration (for ADT793) .....................................................................................................................................53 4.7.6 Front cabin door settings ..................................................................................................................................................54 4.7.7 System purge (for ADT793) .............................................................................................................................................54 4.7.8 Advanced diagnose ...........................................................................................................................................................54 4.8 PRODUCT INFORMATION...............................................................................................................................................................55 4.8.1 Host .....................................................................................................................................................................................55 4.8.2 Control module...................................................................................................................................................................55 4.8.3 Internal pressire module ...................................................................................................................................................55 4.8.4 External module (when connected) ................................................................................................................................55 5.APPLICATION ........................................................................................................................................................56 5.1 PRESSURE UNIT CONVERSION ......................................................................................................................................................56 5.2 PRESSURE LEAK TEST ..................................................................................................................................................................57 5.3 PRESSURE SWITCH TEST..............................................................................................................................................................59 III 5.4 AUTO STEP ...................................................................................................................................................................................61 5.5 ABSOLUTE PRESSURE ERROR CALCULATOR ...............................................................................................................................62 6.SYSTEM DIAGNOSTICS .........................................................................................................................................64 6.1 ADT773/783...............................................................................................................................................................................64 6.2 ADT793 ......................................................................................................................................................................................66 Figure Content Figure 1 Basic structure of the front panel ....................................................................................................................... 12 Figure 2 Additel773/783/793pneumatic version interface Figure ..................................................................................... 15 Figure 3 Additel773/783/793hydraulic version interface Figure ....................................................................................... 16 Figure 4 Schematic diagram of liquid storage tank operation .......................................................................................... 19 Figure 5 Main interface view ............................................................................................................................................ 20 Figure 6 Typical connections for pneumatic version .......................................................... Error! Bookmark not defined. Figure 7 Typical connections for hydraulic version ............................................................ Error! Bookmark not defined. Figure 8 System Settings ................................................................................................................................................ 33 IV Safety Instructions 1. Safetyand Marks Indicates the user must refer to the instructions prior to use the controller. Indicates the terminals or sockets may have high voltage and user should avoid contact. 2. User Responsibilities To ensure safety, users must do the following: Before using this product, please make sure you have read and understand this user’smanual; Use the controller properly and use a medium that meets the requirements; Establish and follow safety procedures, operators must have relevant professional knowledge; Use the controller only when it is in good working condition; The controller should only be purchased and repaired at Additel or authorized distributors; The controller must be groundedto the AC power supply’s safety ground. 3.General Safety The controller can only operate safely and without failure if it is stored, transported, installed and used correctly; Avoid using the device in vibration, high temperature, high humidity and strong magnetic fieldenvironments; Do not insert any object into the controller; The voltage of the controller’s power supply may cause injuries to personnel. Even after switched off, dangerous voltage may exist; In the event of condensation, the controller must be dried out before being switched on; Make sure the pressure is vented before switching off the controller. 4.Warning Highpressure is potentially dangerous! It should only be installed and operated by professionals; 1 Tubing, valves and other equipment connected to the controller must be able to withstand the maximum pressure that will be exerted and allow for adequate safety redundancy; Do not use in dusty, steam, or corrosive gas environments. Do not use in explosive hazardous environments; Do not overpressure the controller; 5. Air source and medium requirements For controllers that need to access anair source, the stability and safety of the air source must be ensured. It is strongly recommended to install a pressure stabilizer, pressure safety valve (or equivalent functional device), isolation valve and release valve in the inputtubing of the pressure source, so that the controller can be usedsafely in the best condition; When the air source pressure is connected to the controller is greater than 5% of the maximum working pressure and meets the upper pressure limit (please refer to the label on the back of the controller for the maximum access pressure limit), a warning will be displayed on the controller interface. At this moment, the air source pressure should be adjusted to meet the controller's requirements; The vacuum source connected to the controller must be 1kPa or lower than the minimum vacuum working pressure. It is also recommended to set up a liquid collector in the vacuum source tubing to prevent the liquid in the DUT from directly entering the vacuum source and affecting the life of vacuum source.In serious cases it may directly cause damage to the vacuum source; For controllers that need to be connected to anair source, it is necessary to ensure that the air source is clean, dry and non-corrosive. Specifically, nitrogen with a purity of more than 99% is the preferred medium. If the nitrogen has undergone multi-stage compression, it is necessary to install an oil mist and particle filter in the tubing after the final stage of compression. We recommend that the filtration accuracy of the particle filter is less than 5um; 2 Usually, the compressed nitrogen in the industrial nitrogen bottle has been filtered and dried, it can be directly connected to the pressure supply tubing of the controller; if compressed air is selected as the gas source, an oil mist filter, dryer and particle filter need to be installed in the tubing after final compression; When inert gases other than compressed nitrogen or compressed air are used as the gas source for the controller, the damage and impact on personnel and the environment must be fully evaluated. It is absolutely prohibited to use flammable, explosive and toxic gases as the gas source for the controller. For controllers which use liquid as medium, the liquid medium in the liquid reservoirshould be replaced regularly and based on actual conditions. When replacing the liquid medium, it should meet the requirements of the equivalentmedium. For water mediumcontroller, it is strongly recommended to replace the water in the liquid reservoir once a week. 1. Introduction 1.1 Overview Additel’s773/783/793 pressure controllers highly integrate the latest control/measurement technology, modular design concepts, and easy-to-use/maintenance design ideas, providing a wide range from-14.35 psi to 15,000 psi. Among them, Additel773 is a low pressure model (-380 inH2O ~ 400 inH2O), Additel783-D (-14.35 psi ~ 35 psi), Additel783-1K(-14.35 psi ~ 1,000 psi), and Additel783-3.5K (-14.35 psi ~ 3,600 psi) are pneumatic models, Additel793 is hydraulic models (0~ 15,000 psi), achieving high control stability, highcontrol rate, and high measurement accuracy, making them an ideal solution for automated production, pressure test and calibration. Achieving wide range coverage and simplifying test calibration tasks, the 773/783/793 can quickly receive pressure control modules and a reference barometric pressure modules. Each pressure control module provides dual ranges and reading accuracies. This modular design allows users to choose the pressure modules flexibly according to range and accuracy requirements. At the same time, the quick plug-in feature of the module makes calibration work simple. 3 Manufacturing companies for pressure sensors and pressure transmitters have strict controls over the risk of production line shutdowns. Additel773/783/793 adopts a variety of easy-maintenance designs. Userscan quickly replace pressure control modules, pressure control components, clean the solenoid valve, finely filter contamination particles, optional external CPS anti-pollution device, and for the hydraulic controller, an optional external reservoir can be used for single cycle. These simple maintenance features make Additel773/783/793the powerful and reliable solutions for production line users. General pressure controllers require an external air source, and users must consider the configuration of the air source. Due to the different pressure ranges of the controllers, it is sometimes very troublesome to provide an airsource that might be too large or too small.The Additel773 and Additel 793 have built-in pump sources, which create pressure quickly and reliably. Users do not need an external air source. For the Additel783to achieve the fastest pressure control speed, a large flow of external air source is required,the user can configure the air source according to the conventional air source. Additel also provides a fully automatic air source solution. Call Additel for assistance. The automatic test functions will improve the user's work efficiency. Additel’s773/783/793 controllers integrate numerous test functions, such as pressure switch test, pressure leak test, pressure safety valve test, script task test, pressure automatic step test, External I/O alarm output, external drive valve control. 1.2 Models Specification Table 1 Models Specification Additel773/783/793 intelligent automatic pressure controller 4 Models ADT773 ADT783-D ADT783-1K ADT783-3.6K ADT793 Maximum pressure (-380~400) inH2O (-14.35~35) psi (-14.35~1,000) psi (-14.35~3,600) psi (0~15,000) psi control range (-0.95~1) bar (-0.99~2.5) bar (-0.99~70) bar (-0.99~250) bar (0~1,000) bar Low differential Differential pressure pressure Pressure media Gas Built-in pump External air source Pressure type Internal pressure control module Barometric pressure module(Optional) External pressure control module Absolute pressure switching [1] Gauge Gauge Gauge Gas Gas Gas √ - - - √ - √ √ √ - 2 2 2 2 1 1 1 1 1 1 - - - - √ √ √ √ √ √ Liquid (water or oil) Note: [1]Absolute pressure is achieved through the synthesis of the basic gauge pressure module and the optional atmospheric pressure module. 1.3 Technical Specifications 1. GeneralSpecifications Table 2 GeneralSpecifications Features Specifications 5 Power Requirements Power supply: AC100~240V, 50/60Hz Fuse: T3.15A 250Vac Maximum power consumption: 150W Chassis size: 17.32 × 5.23 × 14.96 in (440(W) × 133(H) × 380(D) mm) Size / Weight Rack mount dimensions: 3U-19” rack, Horizontal Direction Weight:Additel773: 17.6 kg / Additel783: 16.9 kg / Additel793: 20.7 kg Pressure module weight: 0.5 kg Operating ambient temperature: 10℃~50℃ Storage temperature: -20℃ ~ 70℃ (oil medium), 5 ~ 70 ℃ (water medium) Working humidity range: 5%RH~95%RH, no condensation Working altitude: <2000 m Environment Protection level: IP20, indoor use only Vibration level: 2g Impact intensity: 4g Warm-up time: 15 minutes Bare machines drop height: 250mm Conformity CE RS232, USB-A*2, LAN Communication WIFI, Bluetooth, GPIB, mouse, keyboard and other peripherals can be expanded through USB The SCPI command set is compatible with Additel780, PACE5000/6000, DRUCK DPI520, MENSOR, WIKA, FLUKE, and user customizable. 6 3-channel external drive valves, green terminal connector with lock External drive valve port Maximum drive capacity 24V/12W, port withstand voltage 30Vmax. One channel fixed to the CPS pollution prevention device, the remaining 2 channels can be used to controltheexternal vacuum pump and external isolationvalve. I/O alarm port Pressure switch test interface 3-channel, green terminal connector with a lock Volt-Free No/Nc relay, the maximum current-carrying capacity: 24 V / 0.5 A, 30 V max 1-way, lockable green terminal connector Maximum load 24V/0.1A, interface withstand voltage 30Vmax. Supports mechanical switch and electronic switch testing 7-inch capacitive touch screen, resolution 1280*800, reflective panels, black and white background switchable Display Communication update speed: 10 times/second. Display refresh rate: 5 times/second Pressure value maximum displays: ±9999999, display digits is adjustable External pressure 5-pin standard Lemo plug, connect external pressure control module(ADT161). control module port Opening the cabin door will automatically release the pressure for safe removal of modules. Inside of cabin: Internal pressure control module port For ADT773/783, 3 bays, from left to right including a high-pressure module bay, a low-pressure module bay, and a barometric pressure module bay. For ADT793, 2bays, from left to right,including a pressure module bay, and a barometric module bay. Warranty 1 year 7 Hose & Filter The estimated End of Life (EOL) expectancy for all hoses and filters (pneumatic and hydraulic) is End of Life approximately 10 years and should be replaced at the first sign of wear or damage. 2. Pressure control specifications Table 3 Pressure control specifications Pressure control specifications Model ADT773 ADT783-D ADT783-1K ADT783-3.6K ADT793 Maximum pressure (-380~400) inH2O (-14.35~35) psi (-14.35~1,000) psi (-14.35~3,600) psi (0~15,000) psi control range [10] (-0.95~1) bar (-0.99~2.5) bar (-0.99~70) bar (-0.99~250) bar (0~1,000) bar Low differential Differential pressure pressure Gauge Gauge Gauge √ √ √ √ √ 2 2 2 2 1 - - - - 1 Pressure type Absolute pressure switching [1] Number of internal pressure control modules Number of external control pressure modules 8 Maximum range of (-400~400) inH2O (-15~36) psi (-15~1,000) psi (-15~3,600) psi (0~15,000) psi internal module (-1~1) bar (-1~ 2.5) bar (-1~70) bar (-1~250) bar (0~1,000) Bar Minimum range of (-1~1) inH2O -(10~10) inH20 (-10~10) psi (-15~150) psi internal module (-2.5~2.5) mbar (-25~25) mbar (-0.7~0.7) bar (-1~10) bar Minimum range of external module Maximum high and low range ratio Range switching Mode[2] Pressuresupply source[3] Maximum supply pressure[4] Control mode Maximum overshoot Maximum load Volume Control response time[5] (-15~3,000) psi (-1~200) Bar (-15~1,000) psi - - - - - - 20:1 - - fixed, automatic fixed, automatic fixed, automatic fixed, automatic fixed, automatic Built-in air pump External air source External air source External air source Built-in liquid pump - 4bar 80bar 280bar - Fast, standard, Fast, standard, Fast, standard, Fast, standard, Fast, standard, custom custom custom custom custom <1%FS <1%FS <1%FS <1%FS <1%FS (-1~70) Bar <10,000 psi: 80 ml, 500 ml 1,000 ml 1,000 ml 1,000 ml 10,000~15,000 psi: 60 ml <10S <10S <10S <10S < 30S 9 Control stability[6] Lasting stable time <0.003%FS <0.003%FS <0.003%FS <0.005%FS Typical 0.001%FS Typical 0.001%FS Typical 0.001%FS Typical 0.003%FS >5min >5min >5min >5min >5min √ √ √ √ √ 6 mm Festo 6 mm Festo 1/4BSP M 1/4BSP M 1/4BSP M Air source port: Air source port: Air source port: 1MPa 14MPa 30MPa Vacuum port: Vacuum port: Vacuum port: <0.003%FS[7] Connect to CPS anti-pollution device Pressure port Air source interface[9] - safe pressure limit Interface filter[8] Built-in Reservoir Volume External Reservoir Extension 500kPa 500kPa 500kPa √ √ √ √ √ - - - - 800ml - - - - Optional Note: [1] After the reference atmospheric pressure module is installed, users can select gauge or absolute pressure. [2] Automatic range switching between internal pressure control module and external pressure control module is not supported; [3] Gas refers to clean and dry nitrogen or air; liquid refers to Diethylhexyl sebacate or deionized water; 10 [4] In order to achieve the best control effect, the source pressure should be adjusted to about 110% of the maximum range of the internal pressure control module or 1bar, whichever is greater; [5] The air pressure is tested under an external load volume 50 ml, 20% step, and the time to reach 0.005%FS stability. The hydraulic pressure is tested under an external load volume 10ml and 20% step, and the time to reach 0.005%FS stability; [6] In order to achieve the specified control stability, some additional stabilization time at the desired pressure may be needed depending on the configuration and pressure level. [7] The control stability is 0.003%FS or 0.05Pa, whichis the greater; [8] All pressure ports are installed with 40 ~ 100μm filters; [9] In order to prevent the inlet pressure of the air source from exceeding the safety limit, it is recommended to install a suitable pressure safety valve at the outlet of the air source; [10] The minimum negative pressure limit is given based on the atmospheric pressure value of 1bar. 11 2. First time use 2.1 Controller illustration 2.1.1 Front panel Figure 1 Basic structure of front panel Table 4 Front panel structure description 12 No. Description 1 Power button 2 Touchscreen 3 Front cabin door (open to see the pressure control modules, atmospheric pressure module) 2.1.2 Cabins Inside Introductions The pressure controlling modules (ADT151) are installed in the cabin, the upper edge of the cabin is simple to open. As the door opens, the controller will automatically release pressure, providing the safe removal and installation of the ADT151 modules. 1. Pneumatic controllers cabin inside: Figure 2 ADT773/783 cabin inside 13 2. Hydraulic controller cabin inside: Figure 3 Adt793 cabin inside 14 2.1.3 Back Panel Ports Description Figure 4 Additel773/783back panel 15 Figure 5 Additel793back panel Table 5 Additel773/783/793ports description No. Additel773/783 No. Additel793 1 Positive pressure source port, inside is1/8BSP F 1 Pressure reference level mark 2 Differential pressure reference port, inside is 1/8BSP F 2 Barometric measuring port, inside is 1/8BSP F 3 Pressure output /measureport, inside is 1/8BSP F 3 External reservoir inlet port, φ6 hose connected to the clean 16 liquid tank 4 Vacuum source supplyport, inside is 1/8BSP F, 4 ADT773 is blocked External reservoir outlet port , φ6 hose connected to the dirty liquid tank 5 Vent port, inside is 1/8BSP F 5 Pressure output /measurement port, G1/4 M 6 Barometric measuring port, inside is 1/8BSP F 6 Internal media drain port 7 Air exhaust port, inside is 1/8BSP F 7 Liquid filling and vent to atmosphere valve 8 -- 8 Accumulator 9 Lemoport for External module (ADT793 external module can be used as a pressure control module) 10 USB port 11 External drive valve connection ports, one of which is fixed to the CPS pollution prevention device, and the other two can be used to control external vacuum pumps and external isolation valves 12 I/O alarm output port 13 Pressure switch test port 14 Ethernet port 15 RS232 port 16 Controller shell grounding post 17 AC power supply (AC100~240V, 50/60Hz, maximum power 150W) 17 2.2 First time use 2.2.1 Power on 1. Press the power button to power on the unit; 2. The controller displays the startup interface; 3. After a short wait, the controller will enter the maindisplay; 2.2.2 Set date and time Click the system setting button under the main display, and enter into the personalization, there is a date and time setting, which can set the system date and time and display format of the controller; if it is connected to the Internet, you can directly click to synchronize the time. 2.2.3 Output pressure 1. ADT773/783 Set a pressure within the range as the target value in the main display, and the controller will control and output this pressure according to the target value. 2. ADT793 Fill medium: rotate the vent valve of the liquid reservoir first, remove the vent valve and then fill in the required working medium, as shown in Figure 4 for the liquid filling operation. The height of the medium needs to be between the Min and Max mark lines; Reinstall the vent valve and rotate the vent valve knob to open it; Connect an UUT on the output port or block it; In the main display, set a pressure within the range as the target value, and the controller will control and output 18 this pressure according to the target value. Figure 6 Liquid reservoir operation diagram 19 3. Display and operations 3.1 Main interface brief introduction The main interface consists of the top status bar and the pressure display area, as shown in Figure 7. Figure 7 Main interface 20 Table 6 Introduction to the display area of the main interface Instructions No. Display area 1 Pressure control range 2 Setpoint 3 Status Bar 4 System settings 5 Application 6 Parameters preview Parameter status is displayed. Click to set the parameter enable/disable status. 7 Running information Choose any four types of information for real-time display 8 Vent 9 Measure 10 Control 11 Zero 12 Pressure units 13 Real-time pressure reading Click to switch the pressure control range Click to set the setpoint WIFI, Bluetooth, U-flash, external modules, etc. Click here to view detailed status information Various settings of the device, including Control Settings, Measure Settings, Service, Personalization, communication settings, etc. Various applications provided by the device Quickly vent the pressure value in the controller to atmosphere In measure mode, the ADT151 pressure module will measure the pressure value of the UUT connect on output port. In control mode, the controller will output a high-precision pressure at the output port according to the set point. Make the controller quickly meet the zeroing conditions and perform the zeroing. Click to change the pressure units. Display the current pressure value, click it to set the pressure setpoint. 21 14 Manual step setting Click the middle number to set the step valuesand control the target pressure value by stepping up and down. 3.2 Main interface detailed introduction In order to quickly understand the operations of controller, please refer to the Figure 7 and follow below introductions. 1. Pressure control range (1) The current pressure control range can be switched by clicking it, gas and liquid controllers have different controlling module versions, that makes different displays. ADT773/783: indicates the High pressure internal module, indicates the Low pressure internal module. ADT793: indicates the Internal pressure module, indicatess the external pressure module. (2) The Manual mark in the upper right corner indicates that the current range mode is manually, and the Auto mark indicates automatic select pressure range; 2. Setpoint The current pressure set point is displayed, and you can click it to change the set point; click on the real-time pressure value in area 13, and you can also set the target value. 3. Status Bar The status bar can be clicked. After clicking, it will enter the "Control Center" interface, which provides more system setting operations. Time and date: The time is the system time; WIFI: icon identifies WIFI connection status and signal strength; LAN connection: 22 icon indicates Ethernet cable is plugged in; USB: Bluetooth: icon indicates that a USB device is plugged in; icon indicates that the Bluetooth is turned on; Message notification: icon will be highlighted in redwhen there is an abnormal message notification, users can click details information further to view the specific warning information; Contamination Prevention System: External pressure module: Vacuum pump: icon indicating that the CPS system is enabled, see 4.6.1 for details ; icon indicates that the external pressure module is online; icon for ADT783 only, indicates that the vacuum pump driver is selected on DRV1 or DRV2 ports. Load Volume Expander: icon for ADT793 only, indicates the load volume expander is selected on DRV1 port (It’s the same icon display as vacuum pump). In addition, in the detailed information, you can also quickly set the screen brightness, volume, RS232 serial port communication, select DRV1 or DRV2 ports, lock/unlock screen and reboot. 4. System settings The main settings of the controller are all here, including control settings, measure settings, personalization, service, communication, expansion interface, maintenance, and information. See Chapter 4 for a detailed introduction to each function. 5. Applications Click to enter the device applicationsmenu. The applications facilitate users to complete some common process operations. See Chapter 5 for details. 6. Parameters preview To view the settings of commonly used parameters, click it to enter the parameter preview setting interface to 23 quickly set the status of the features, but cannot set the specific parameters. (1) Icon display Control Mode: Icons mode; Slew Rate: (Fast) / (Standard) / (Custom), indicating using the corresponding control icon indicates the pressure control speed limitation is active; Vent Rate Limit: icon indicates the vent rate limitation is active (for ADT773/783 only); Height difference correction: icon indicatesthat the height difference correction is enabled; Filter: Tare: icon indicatesreading filtering is enabled; icon indicates that the tare is enabled. (2) Parameter preview settings Click it to enter into the parameter preview settings display, to set the display parameters Control mode: Three modes can be set: fast, standard, and customized; Control stability: The control stability can be set only for custom control mode, and other modes cannot be set. For details, see "Control Stability" in Chapter 4.1; Slew rate: The slew rate and pressure control speed limitations can be set only for custom mode, and other modes cannot be set. For details, seeChapter 4.1; Height difference correction: To set the height difference correction status and parameters, refer to "Height Difference Correction" in Chapter 4.1; Tare: To set tare status and parameters, refer to the “Tare” in Chapter 4.1; Filtering: To set the readings filtering status and parameters, refer to the “Filtering” in Chapter 4.2. 7. Running information Click to enter the running information display. The running information includes: statistics and livedata. You can 24 choose up to 4 of them for real-time display on the main display; click the “Reset” button to recalculate the running information; and click the “Clear” button to removeall the selected running information. (1) Statistics: Min (minimum value), Max (maximum value), Avg (average value), PP (peak-to-peak value), Rate (actual rate); (2) Live Data: ADT773/783: Supply (positive pressure source module), Vacuum (negative pressure source module), H (internal high-pressure module), L (internal low-pressuremodule), Switch (mechanical switch), Baro (Barometric pressure), Ext (external module); ADT793: Ac (accumulator pressure), I (internal pressure), Pin (pressure source module), Pctl (front-end pressure module), Piston (piston position), Switch (mechanical switch), Baro (Barometric pressure), Ext (external module). 8. Vent Rapidly release the pressure in the controller to the atmosphere. The pressure release time is related to the current pressure value, control rate, vent pressure andventing rate. 9. Measure In measure mode, the ADT151 pressure module will measure the pressure value of the UUT connect on output port. 10. Control In control mode, the controller will output a high-precision pressure at the output port according to the set point. 11. Zero Perform the zeroingwhen the zeroing conditions are met. After enable the automatic zeroing in the control settings, there will be a zeromark on this button: 25 The controller’s readingcannot exceed the vent pressure when try to zero(ADT793 vent pressure:1bar, ADT793W vent pressure:5bar; ADT783 vent pressure: can be set and viewed in the control settings) When the controller’s reading is higher than the vent pressure value, and try to zero it, it will prompt to reduce the pressure before performing the zeroing operation; When performing zeroing, the controller will perform a venting operation at first and wait until the internal zeroing conditions are met before performing zeroing. 12. Pressure unit Displays the currently set pressure unit, click it to set the displayed pressure unit. After the new pressure unit is set, the displayed real-time pressure value and operating information will follow the newly set pressure unit. 13. Real-time pressure value Displaysrea-time pressure reading, click it to set the target point. According to the set resolutions, the corresponding number of digits is displayed. 14. Manual step The manual step mode can be set as Step Value mode or Point List mode in the Advanced Setting of Control Settings. Step Value: When use the step value mode,click the number in the middle of and buttons to set the step value, click up or down buttons will changes the set points at the setted step value interval. Point List: When use the point list mode, click the number in the middle of the and buttons will pop up the step point list display, users can add or delete the step points, click up or down buttons at main display will switch 26 to the next points as the new setpoint. 3.3 Pressure control 3.3.1 Pressure control module ranges switching 1. ADT773/783 pressure ranges switching Select internal high pressure module or low pressure module as pressure control module. For ranges selection, users can selectauto range or manualy select ranges Figure 8 ADT773/783 Pressure Ranges Switching 27 2. ADT793pressure ranges switching (1) ADT793 can use the internal pressure moudle or external pressure module controlling module. (2) For ranges selection, users can select auto range or manualy select ranges. Figure 9 ADT793 Pressure Ranges Switching 28 as the pressure 3.3.2 Pressure output 1. Make connections (1) When use internal pressure module as controlling module. (ADT793: , ADT773/783: / ), the tubing connections are shown in below figure. 1) ADT773/783 Tubing connections Figure 10 ADT773/783 Typical Tube Connections with manifold and CPS 29 2) ADT793 Tubing Connections Figure 11 ADT793 Typical Tubing Connections with manifold and CPS 2. Input Setpoint Click the screen set point or pressure value display area and enter the setpoint; Or click to step upward or downward buttons to adjust the setpoint; The setpoints must be within the pressure control range of the controller; In addition to the range limits of the pressure control module, the setpoint is also limited by the setpoint limits in "Control Settings" (see Chapter 4.1 Setpoint Limit); When thesetpoint exceeds the current pressure range, the setting cannot be completed and needs to be 30 re-entered. 3. Start/stop pressure control After setting the setpoint, the controller immediately starts generating pressure and control pressure; In the vent or measure mode, click the "Control" button on the screen to start pressure control; Click the "vent" and "Measure" buttons on the screen to switch to the vent or measure mode to stop pressure control. 4. Pressure Stability When the current output pressure meets the control stability conditions in "Control Settings" (see Chapter 4.1), the pressure value turns to green, indicating that it is stable. 5. Manual step See manual step in Chapter 3.2.14 for details. 3.3.3 Pressure measurement 1. Switch to measure mode and select the required module and range; 2. Connect the external pressure controller to the output port of Additel controller; 3. External pressurization The external pressure controller must use the same media with Additel controller; It is prohibited to apply pressure beyond the range of the controller; If the external pressure exceeds the current using range, the reading value turns red and triggers the alarm; If the external pressure exceeds the controller's tolerance range, the system will be vented immediately and prompt over-pressure protection. 31 3.3.4 Pressure unit 1. Units switching: Click the pressure unit area in the main display to enter the pressure unit selection interface. Click the required unit to complete the pressure unit switching. 2. Unswitchable unit: In the unit selection interface, if any units are grayed out that means they cannot be selected, because the units cannot fully display all digits in the full range. 3. System unit configuration: The displayed switchable unitsare thesystem configured units. For details on the configuration of the system units, please see Chapter 4.3.5. 4. System settings In the main display, click the button icon enterthe system setting interface. System settings include eight major menus: Control settings, MeasureSettings, Personalization, Service, Communication, Expansion Interface, Maintenance and Information. 32 Figure 12 System settings 4.1 Control settings 1. Range mode Set the switching mode of the pressure control ranges. (1) Manual: Need to manually switch pressure control range, the default is manual mode; Auto: The range will be automatically switched according to the current pressure value. 2. Pressure type Pressure type can be switched between Gauge pressure and absolute pressure 33 3. Control mode (1) Fast: In fast mode, the slew rate is fixed at the maximum value, the control stability is also fixed at a fixed value. (2) Standard: In standard mode, the slew rate is also fixed at the maximum value, the control stability is alsofixed at a fixed value; (3) Custom: In custom mode, the slew rate limit can be enabled or disabled, the slew rate can be set if enabled.If it is disabled, the slew rate will be set to maximum value, and the control stability can be set, (0.001~1)%FS for ADT773/783, (0.005~1)%FS for ADT793, and the stability time can be set from 1s to 60s. 4. Stable control Can only be set when the control mode is custom mode, the stable judgement conditions can be set. (1) StableTime: If the difference between the output pressure and the setpoint meets the requirements and remains stable for the setstable time, the pressure control is considered stable, (1 ~ 60 ) seconds are settable; (2) Stability Setting: Set the stability judgement type, %FS or Fluctuation value types can be selected; (3) Stability: Set the specific value of the %FS or Fluctuation value, to judge if the pressure is stable or not according to compare the setted value here and the difference between the output pressure and the setpoint; (4) During the control process, the pressure can be determined to be stable if the following two conditions are met at the same time: 1) To achieve stable conditions: When the stability is set to "%FS": |output pressure – setpoint|<= The pressure module range used by the pressure control × stability; When the stability is set to "Fluctuation value": |output pressure –Setpoint|<= stability 2) Continue to meet 1) conditions to reach pressure stabilization time. 5. Slew rate limit 34 This feature is visible and settable only when the control mode is custom mode, you can choose to enable or disable it: (1) When set to disable, the slew rate defaults to the maximum value ; (2) When set to enable, the slew rate can be set. 6. Slew rate It can be set only when the control mode is custom mode, and the slew rate limit is enabled. In other cases, it defaults to the maximum value. (1) Set the maximum rate during pressure control. The maximum slew rate during pressure control will not exceed the settedupper limit; (2) The slew rate displays "maximum", which means that the controller will approach the set point at the maximum slew rate. 7. Vent pressure The maximum pressureof controller when performing the venting operation, the value range is (100 ~ 1000)kPa. (1) When the current pressure value is higher than the venting pressure set value, the controller will firstly reduces the pressure to the venting pressure value at the vent rate, and then executes the venting; (2) When the current pressure is lower than this venting pressure set value, the controller will immediately execute venting operation. (3) Note: This function can only be set forADT773/783. 8. Setpoint limit According to the control module range, input a smaller range as the upper and lower limits of the pressure control to ensure that the pressure output to the UUT will not exceed its range. (1) This feature is invalid when disable it. The setting will be stored and will remain after reboot; 35 (2) The upper and lower limits of the set point limits can be set when enable it, and the pressure control target value will be limited by thelimits; (3) It will not allow to set this set point if the target value exceeds the Setpoint limit. 9. Head Height Correction (1) Enable: You can choose to enable or disable the height difference correction function; (2) Corrected value: Read-only display of the correction value of the current height difference; Unit system: Choose metric (SI) or imperial (BS) system; Height difference: The input range is ( -1000 ~ 1000 ) cm; Standard density of medium: ADT783: Click to select air, nitrogen or custom value; ADT793: Click to select purified water, sebacate oil or customized value; Gravity acceleration: the gravity acceleration value of the position, the input range is ( 9 ~ 10 ) m/s 2 ; Temperature: ambient temperature, the input range is (0~50 ) ℃. 10. Tare It can be set to enable or disable. After it is enabled, you can enter the corresponding tare value and it will take effect immediately after saving. (3) Enable: You can choose to enable or disable the tare function; Tare value: The value that needs to be tared. The input range is (-99999 ~ 999999 ), and the unit is the using pressure unit. 11. Auto Zeroing (1) This function is invalid when disabled; (2) The pressure reading will be automatically zeroed when the meet the zeroing conditions (refer to Clearing in 36 3.2 ). 12. Exacuation pressure The maximum pressure value when performing the emptying operation inside the equipment, the value range is (100 ~ 1000)kPa. (3) When the current pressure value is higher than the emptying pressure set value, the equipment first reduces the pressure to the emptying pressure value at the emptying rate, and then performs the emptying operation; (4) When the current pressure is lower than this venting pressure set value, the device will immediately perform venting operation. (5) Note: This function can only be set for the Pneumatic version. 13. Advanced settings (1) For ADT773/783 1) Vent rate limit Enableor disable the vent rate limit of the ADT783 units. Enable: when the current pressure value is higher than the venting pressure setting value, the controller first reduces the pressure to the venting pressure at the vent rate, and then executes the venting operation. Disable, when the current pressure value is higher than the venting pressure setting value, the controller first reduces the pressure to the venting pressure at the maximum rate, and then executes the venting operation. 2) Vent rate Only for the ADT773/783, the maximum pressure reducing rate from the current pressure value to the venting pressure when the current pressure is higher than venting pressure. 3) Gauge zero mode When the set point is 0 (gauge pressure), the processing methods can be selected: 37 Control: Use pressure control method to control the pressure to 0 (gauge pressure) Vent/Draining: When controlling the 0 (gauge pressure) point, directly execute the vent or draining process 4) Volume fixed It can be set to enable and disable. If there is a large volume between the controller and the UUT, this function needs to be enabled and set the volume to make the controlling more accurate and faster. 5) Volume When enable the Volume fixed feature, the volume value needs to be entered. 6) Manual step Mode Step value or point list can be selected. For details parameter, please refer to section 3.2. 7) Default Barometric Value Only effective when the barometric pressure module is not online, the settable range is (60~120)kPa.a (2) For ADT793 1) Vent Stable Convert Measure Can enable or disable this feature, if enable, after venting and stabilizing for a while, the control mode will switch to measurement mode, and the time can be set by the stable dwell time. 2) Stable dwell time It’s valid when the Vent Stable Convert Measure feature is enabled, set the time to switch to measurement mode after venting stable, the time range can be set (1~180)s. 3) Manual step Mode, same with ADT773/783 4) Default Barometric Value, same with ADT773/783 38 4.2 Measure settings The pressure module that needs to be set can be selected on the left side of the displayand set the module parameters on the right side. The measurement parameters of the module include: 1. Unit Switch pressure units for the selected module. 2. Resolution Set the number of digits to display the pressure value; (1) High-precision modules can be selected from 5, 6, and 7; (2) Low precision modules can be selected from 4, 5, and 6. 3. Filter The filter feature can be enabled or disabled, and the filter type and related coefficient can be set. (1) Filter type: first-order filtering or average filtering can be selected; (2) Filter coefficient: Visible when the filter type is first-order filtering, the filter coefficient range is (0.01 ~ 1); (3) Filter sampling time: Visible when the filter type is average filtering, the time value range is (1 ~ 20 ) seconds. 4.3 Personal Personal includes settings for Datetime, Display, Sound,Language and System unit. 4.3.1 Date time Table 7 Date time Items Valid values Time 00:00 : 00 ~ 23:59:59 Date Description Time setting Date setting 39 Date Format Year - Month - Day / Month - Day - Year / Day - Month - Year Date format settings 24-hour clock On/Off Whether to use 24- hour clock display or not Delimiter .- / Date separator settings Time zone Select suitable time zones Depending on the location of the device, select the appropriate time zone Synchronize update time when connected to Synchronization time the Internet 4.3.2 Display Table 8 Display setting Items Valid values Brightness Set brightness in a bar form Mode Light mode / Dark mode Description Set screen brightness Set the background and base color 4.3.3 Sound Table 9 Sound settings 40 Items Valid values Description Volume Set the volume in a bar form Touch tone ON / OFF Touch tone settings Prompt tone ON / OFF Prompt tone settings Over range alarm ON / OFF Over range alarm sound setting Device volume settings Switch On/Off prompt tone ON / OFF Switch on/off tone setting 4.3.4 Language The controller provides multiple languages. Users can select the desired language through this menu, and the selection will take effect immediately. 4.3.5 System unit 1. Pressure units This feature can be selectively added to the system pressure units among all pressure units, and the display order of the pressure units can be adjusted, and the pressure units can also be customized. (1) Add all: Add all units supported in all pressure units to the system pressure units; (1) Clear all: Clear the system pressure units. When the system pressure units is empty, you cannot exit this function directly; (2) Restore default: To restore system pressure units to factory default; (3) Custom: Set custom units. Supports maximum 5 custom units; (4) Sorting: Set the system pressure units displayed order. 2. Rate units Set the rate unit of the system, 1/s or 1/min. 3. Temperature units Set the temperature units of the system, K, ℃ or ℉. 4.4 Services System services include: system calibration, advanced configuration, restore factory and firmware update. 41 4.4.1 System calibration Input password to enter system calibration. The factory default password is: 123456 . 1. Pressure module calibration (1) Tubing connection The internal pressure module can be calibrated in either internal pressurization or external pressurization mode; When selecting internal pressurization mode, please connect the controller pressure output port to a reference pressure device; When selecting external pressure mode, please connect the controller to the pressure output port of the external reference pressure controller; When calibrating an external pressure device, if therange of the controller covers the UUT, either internal or external pressure mode can be used. If not covered, only external pressurization is an option. (2) Select Calibration Module Select the pressure module to be calibrated and select multi-point calibration (3) Multi-point calibration 1) Click multi-point calibration to enter the calibration interface; 2) Last time calibration data: the data and date of the last calibration will be displayed at first after entering. If it has not been calibrated, will display "- - - ". 3) Configuration before calibration: click button to enter calibration configuration display Select pressure source: internal pressure or external pressure Height difference(only for ADT793): Since the height difference has a great impact on hydraulic calibration, it needs to be set. 42 Calibration point: It can be changed. Please ensure the entered calibration point is within the range of the internal pressure module, and ensure that the current set point is smaller than the subsequentset point. 4) Start calibration A. Click theNext button to execute calibration; B. Internal pressurization: According to the prompts of the controller, the controller outputs the pressure to the reference. After thepressure is stable, click the standard value which corresponding to the calibration point and input the readings of the reference. After confirmation, click button to proceed to the next point; Use same method to calibrate all points, click Save to complete the calibration. C. External pressurization: According to the prompts of the controller, use the external reference device to output pressure to the controller internal pressure modules. After the pressure is table, click the standard value which corresponding to the calibration point and input the readings of the reference. After confirmation, click button to proceed to the next point; Use same method to calibrate all points, click Save to complete the calibration. D. If there is too much difference between the entered standard value and the indicating value, it will be prompte to re-enter. E. After the calibration is successful, the new calibration data takes effect immediately, and the calibration date will take the current system date. (4) Cancel Zero Click Cancel zero to cancel the zeroing operation of the pressure module. (5) Restore factory calibration data 43 Click Restore Factory Calibration Data to restore the calibrationto the factory calibration data. 2. ADT793 Supply PressureModule Calibration Use the ADT151 pressure module as the reference to calibrate the internal supply pressure module and pressure sensor before booster to correct the pressure drift caused by long-term operation of the internal sensors. The output port must beblocked before the calibration. 3. ADT773/783Supply Pressure ModuleCalibration The pressure supply source sensor S1 and the vacuum source sensor S2 canbe zeroed here. Before calibration, please perform the following operations first: Please vent the supply source pressure at the "Supply" port Please vent the vacuum source pressure at the "Vacuum" port 4. Auto Tune (1) Function introduction Through the Auto Tune, the degradation of controller performance parameters caused by long-term use can be optimized, thereby improving pressure control stability and pressure control efficiency. (2) Preparation before execution For ADT773/783: Before execution, the supply pressure of the "Supply" port needs to be adjusted to the appropriate pressure range. For ADT793: Make sure the output port is blocked when executing. (3) Execution process Click the start button , the program will run automatically. You can check the current execution progress through the progress bar until the program is completed. (4) Restore Factory 44 After entering the application, click Restore Factory to restore the auto tune related data to the factory default. Note: It is only necessary to perform auto tune when the pressure control capability decreases. Invalid auto tune will affect the control effect. Please use this function with caution. 5. Automatic Module Calibration (1) Function Introduction The automatic module calibration function can quickly and automatically calibrate the internal pressure control module for user convenience. (2) Conditions of Use External standard modules need to be connected and connected correctly; The range of the external standard module needs to cover the range of the internal module. (3) Steps Need an external reference module is connected to enter the application. The steps are as follows: Display the reference and UUT information. For the ADT793, need to enter the height difference and click Calibrate to start the automatic calibration process. The equipment automatically detects whether the reference module range meets the calibration requirements of the internal pressure control module. If it meets the requirements, it will be calibrated. If it does not, it will prompt. During the calibration process, the internal pressure control module will be automatically calibrated in sequence until the calibration is completed. During the calibration process, you can click the return button to exit the calibration process, or click stop to interrupt the calibration process; After the calibration is completed, you can click Save to save the calibration results. 45 6. Calibration Record (1) The relevant information of each calibration operation is recorded, including calibration items, calibration time, and detailed calibration data; (2) The pressure module, liquid source module, autotune, etc. will be recorded separately, allowing users to search and browse based on calibration items and calibration time. 7. Calibration Expiration Reminder (1) You can set whether the calibration expiration reminder function of each module is enabled and set the expiration reminder date; (2) After enable the function, the expiration reminder can be set as a timed reminder or a cycle reminder. Timed reminder: remind once when the set expiration reminder date is reached. Cycle reminder: calculated from the set date and will be reminded once every time the set cycle is reached. The default reminder cycle is 180 days. (3) A module of the controller exceeds the calibration period, a prompt will be given when powering on or when the module comes online . 4.4.2 Advanced Configuration The factory default password is: 123456 to enter the Advanced Configuration. 1. Configuration Management Manage configuration information, divided into currentconfiguration, last configuration and backuprestore, to facilitate configuration import, export and restoration operations. 2. Remote Desktop Sharing The remote desktop sharing function can be started or stopped after entering.Need to access the network for this application. 46 3. Remote Assistance The remote assistance function can be enabled or disabled after entering. Need to access the network for this application. 4.4.3 Restore Factory 1. You need to enter a password to use factory reset. The factory default password is: 123456 . Data cannot be recovered after factory restore, so please use it with caution. 2. After entering the password, enter the factory reset interface, select restore settings only, and confirm. 4.4.4 Firmware update The control provides firmware update function. Currently, it only provides update using USB flash drive. 1. Copy the update file to the root directory of the USB flash drive; 2. After powering on, insert the USB flash drive into the USB port on the back of the controller; 3. Click Firmware Update, and the available update files in the USB flash drive will be automatically checked and displayed; 4. Click to select the update file you want to use, and the file will be unziped, and then the updating information will be displayed. You can click Start Update to update the firmware, or click Give Up to return. 5. After updates starts, you need to wait for a few minutes until the update process is completed. The systemwill automatically display the update result information. After confirmation, the controller will automatically reboot. 4.5 Communication The communication methods include: Protocol, Ethernet, RS232, ExternalWLAN 4.5.1 Protocol Currently supports SCPI, PACE 5000/6000, DPI520, Fluke6270A,WIKA-SCPI, CPC8000/6000/4000/3000. 47 4.5.2 Ethernet The controller communicates with the computer through a network cable. The communication parameters can be set and click the button to save and apply the settings. Table 10 Ethernet address acquisition method selection Items Valid values Description Select the device address acquisition methods; Address acquisition DHCP/ Manual DHCP: Parameters are automatically matched by the system. Manual: Parameters can be set manually IP Address 0.0.0.0 ~ 255.255.255.255 Set the controller host IP address Subnet Mask 0.0.0.0 ~ 255.255.255.255 Set the controller host subnet mask Gateway 0.0.0.0 ~ 255.255.255.255 Set the controller host source gateway Port 8000 Factory settings and cannot be changed Physical Address Factory settings and cannot be changed 4.5.3 RS232 Table 11 Serial port settings 48 Items Valid values Description Baud rate 9600, 19200,38400,57600, 115200,custom Data transmission rate during communication Data bits 7, 8 Data bits parameter settings in communication Stop bit 1, 2 Stop bits Parameter settings in communication Check Digit No parity, odd parity, even parity Verification method selection in communication 4.5.4 WLAN An external WIFI module is required to use this function. The controller communicates with the computer through the wireless network. The WLAN status and parameters can be set, the settings take effect directly after set, and click button to return. 1. Wireless communcation settings Table 12 Wireless communication settings Items Valid values WLAN On/Off Wireless network Depends on network environment Description Turn wireless network On/Off Select the wireless network access point. After connecting, the WIFI name and IP will be displayed. Select the device address acquisition Advanced options DHCP/ Manual method, the manual mode need further settings, refer to Table13. Physical Address Port Factory settings and cannot be changed 8000 Factory settings and cannot be changed 49 2. When selecting manual mode in the advanced options, the following table needs to be filled in manually: Table 13 Manual mode in wireless communication advanced options Items Valid values Description IP address 0.0.0.0 ~ 255.255.255.255 Set the controller host IP address subnet mask 0.0.0.0 ~ 255.255.255.255 Set the controller host subnet mask gateway 0.0.0.0 ~ 255.255.255.255 Set the controller host source gateway 4.6 Extension Interface The extension interfacesare divided into three areas, corresponding to the parts 11, 12 and 13 in Figure 4or Figure 5 respectively. Click to configure each interface separately. 4.6.1 Externally driven valves interface The interface can provide voltageto the external devices. One of the channels is fixedly configured for the CPS contamination prevention system, and the remaining two channels can be used by users to control external vacuum pump and external isolation valves. 1. CPS interface, you can configure to enable it or not. If enabled, it can only be used together with CPS. F disabled, it can be used as a general drive valve and controlled by manual output. 2. DRV interface, click to configure manual output or remote control If you select remote control, you can only control it through commands. If manual output is selected, it will be used as a general drive valve and controlled by manual output. 50 4.6.2 DO alarm output interface As an alarm output interface, DO hastwo output modes: manual output and status output. 1. Manual output: manual control of opening and closing status 2. Status output: when configured as status output, activation status and system status need to be configured The activation state is the state performed by DO when the required system state is reached. The system status is the statusneed to detect, including: measure,control, vent, stable, unstable, and over-range; when the selected status is reached, DO is active. 4.6.3 Pressure switch testing interface 1. 24 V power supply interface to provide 24V voltage for switch testing 2. Switch connection port, click to select the type of switch 4.6.4 Manual output Click the Manual Output button to enter the manual control display. The ports configured as manual output in the external drive valve interface and DO alarm output interface can be controlled here. 4.7 Maintenance The applications for equipment maintenance 4.7.1 Maintenance and fluid change (for ADT793) 1. Function introduction The maintenance and fluid replacement function is used to guide the draining and filling of fluid, and it needs to be operated according to the controller prompt instructions and requirements. 2. Operation guide When filling liquid, the equipment must be in a horizontal state and do not exceed the MAX line. If it exceeds the 51 MAX line, extra liquid will be drained out from the vent hole during the pressure control process; It is recommended to change the oil medium every six months. 4.7.2 Piston maintenance (for ADT793) 1. Function introduction The piston maintenance function can be used as the first step troubleshooting method when there is a problem with the piston. Regularly performing the piston maintenance function can ensure that the piston is in good operating condition and extend the service life of the piston. 2. Steps Block the outputport, entering the piston maintenance display, and click the start button to start. There will be several sub-stages during the entire process. All the execution processed can be viewed through the progress bar. During the execution process, you can click the stop button to stop the process, and you can click the return button to exit the application and go back to previous display. 4.7.3 System pressure relief 1. Function introduction It is used to release the pressure at the output port and inside the instrument. This function is generally performed before maintenance and turn off. 2. Operating procedures After entering the system pressure relief interface, click the Start button to execute the application. The wholeexecution processes can be viewed through the progress bar. During the execution process, you can click the stop button to stop theprocess, and you can click the return button 52 to exit the application and go back to previous display. 4.7.4 Accumulator maintenance (for ADT793) 1. Function introduction When the accumulator pressure is too low, the accumulator needs to be replaced in time to ensure normal operation and extend the service life of the controller; when low pressure is detected for accumulator, an alarm will be prompted. 2. Operating procedures After entering the application, the time of the last accumulator testing and the accumulator pressure value will be displayed. Click Accumulator Test, to test the current pressure value of the accumulator at any time and determine whether it meets the requirements. Click Accumulator Replacement to enter the accumulator replacement process. Replace the accumulator according to the step prompts. After the replacement is completed, the accumulator pressure value will be tested again to ensure that the replaced accumulator can meet the requirements. 4.7.5 Assisted aspiration(for ADT793) 1. Function introduction When used for the first time or after liquid change, the equipment tubing is not filled with liquid, which may cause abnormal pressure control. The Assisted aspiration function can be performed to ensure that the equipment is in good operating condition. 2. Operating procedures When using an internal reservoir, open the vent valve; when using an external reservoir, close the internal reservoir vent valve and ensure that the external reservoir is vented to the atmosphere; After entering the Assisted aspiration display, click the start button to start executing the application; 53 During the entire execution process, the whole execution process can be viewed through the progress bar; You can click the stop button to stop the execution process, you can click the return button application and go back to previous display. to exit the 4.7.6 Front cabin door settings 1. Function introduction To set enable or disable whether to vent immediately once detect the cabin door is open. If it is enabled, the venting operation will be performed immediately when the front cabin door is opened. 4.7.7 System purge (for ADT793) 1. Function introduction If contamination exists in the system, it will be concentrated at the output valve, affecting the performance of the controlling. The system purge function can be used to flush away the contaminations, thereby improvingcontrol performance and achieving self-maintenance. 2. Operating procedures After entering the system purge function, click the start button and then start executing the application; , follow the prompts to block the output port, During the entire execution process, the whole execution progress can be viewed through the progress bar; You can click the stop button during execution to stop the execution processor click the return button exit the application or return to previous display. 4.7.8 Advanced diagnose 1. Function introduction Provide some diagnostic tools to facilitate locating the root cause of failures. 2. Operating procedures 54 to Enter the password "1 23456 " to enter the advanced diagnosedisplay. The diagnostic tools of the ADT773/783 and ADT793 are different. (1) For ADT793 Hydraulic circuit operation diagram: displays the current hydraulic information status, including valve status, pressure value of each sensor, pump operating status, etc., and can perform pressure control operations. (2) For ADT773/783 Gas circuit debugging: Display the current air pressure information status, including valve status, pressure value of each sensor, pump operating status, etc., and can perform pressure control operations. 4.8 ProductInformation 4.8.1 Host Host information includes Model, Serial number, Mainversion, Working medium, Output pressure range, etc. Please provide this informationto Additel/s service team if assistance is required. 4.8.2 Control module Control module information includes serial number, firmware version, and hardware version. 4.8.3 Internal pressure module Internal module information includes serial number, version and ranges information. 4.8.4 External module (when connected) External module information includes serial number, version and range information. 55 5. Application 5.1 Pressure unit conversion Figure 13 Pressure unit conversion 1. It has 10 groups of units for unit conversion. 2. Click the pressure value on the left side of a group (this group will be used as the basis for pressure unit 56 conversion), and set its pressure value, the other 9 pressure units will make the unit conversation to display the corresponding values. 3. Click on the right side of each group to set the pressure unit of the group; if the set unit is the selected group, the values of other groups will be re-converted based on the selected group; if the set unit is not the selected group, the value of the set group will be re-converted based on the selected group values and units; 4. Click "Decimal " to set the maximum number of decimal places for the pressure value to be displayed, with the value ranging from 0 to 6 ; 5.2 Pressure leak test Used to test the sealing performance of the overall equipment under the required pressure for a period of time 1. View test records Click the application to enter the application homepage, which displays historical test information. Click any of the historical test results to view them in more detail. In the test result interface, you can view test result storage parameters, test parameters, test result statistics, and test curves. Click button to view specific test data. Click the test button , you can enter the test process. 2. Parameter settings before testing After entering the application, click the test button to set the basic parameters. Table 14 Pressure leak test parameter settings Items Description Test pressure Set the required test pressure value according to the requirements Pressure type Gauge pressure or absolute pressure can be selected Basic parameters 57 Units Waiting time Range Select the required pressure unit. The default is the pressure unit of the last test. After the pressure stabilizes, the waiting time before starting the leak test timing, the range is 0 0 : 00:00~ 23 : 59 : 59 Testing time The time used for the leak test, the range is 0 0 :00:00~ 23 : 59 : 59 Range mode You can choose automatic or manual Module and range selection Select the module and range required for testing 3. Implement After completing parameters setting, click Confirmbutton Perform a zeroing before starting. to enter the execution display. Click the start button to startthe test; After the pressure reaches the set point and is stable, switch to measurement mode. After the countdown waiting time is over, the test countdown starts until the end of the test ; Can click button during execution to view the statistical information of the test results, click buttonto switch back to test curve display; Can click to stop during execution process to terminate the test and jump directly to the save interface; Can click 4. Save result button during execution process to stop and exit the testing. After test completed, click save button 58 to enter the save parameter settings interface. Save parameter settings: You can set the name, operator, model, serial number, ambient temperature, ambient humidity, remark information, etc. In the save parameter interface, click the save button to save the test result. 5. Export To Export Data a USB drive must be inserted into the USB port; On the home page of the application, click the export button to enter export display; Click to select the test results that need to be exported, or click the Select All button to select all test results; Click Confirm 6. Delete to export the selected test results to the USB flash drive. On the home page of the application, click the delete button to enter delete display; Click to select the test results that need to be deleted, or click the Select All button to select all test results; Click OK to delete the selected test results. 5.3 Pressure switch test 1. View historical test information Click the application to enter the application homepage, which displays historical test information. Click to view it. Click the test button to enter the switch test parameter setting interface. 2. Pressure switch test parameter settings Set the parameter information of the pressure switch. The relevant parameters are introduced in the following table: Table 15 Pressure switch test parameter settings Items Valid values Description 59 Range Pressure type Pressure switch range Gauge pressure, absolute pressure, differential pressure Set the upper limit, lower limit and unit Set the pressure type of the switch Switch type Mechanical switch, PNP, NPN Set the type of switch Action type High, Low Set switch action type Set point Within the switching range Deadband range Within the switching range Accuracy(FS) 0.5%, 1%, 1.5%, 2%, 2.5%, 4%, custom Cycles 1, 2, 3 Click next button Set the default action point of the switch Set the deadband range. After the test, the data must meet the requirements of the switching difference range. Set the switch accuracy, one of the requirements that the data after testing must meet Set the number of testing cycles to enter the range selection interface; 3. Select range and range mode Select pressure module and range mode; Click the confirm button 4. Implement to enter the execution interface. Click the start button to run the test; You can click the data button during executionto display data details, click the curve button back to curve display; You can click the stop button test; 60 during execution to stop the test, click the return button to change to stop and exit the When the execution is completed, click the save button to enter the save information display, fill in the name, operator, model, serial number, ambient temperature, ambient humidity, remarks and other information ; Click the save button to complete the test, and the test results are displayed in the historical information on the home page. 5. Export and delete Need a USB flash driver insert in the controller to export the dates On the home page of the application, click the delete button to enter the delete display, select the test results that need to be deleted, click OK button to delete all selected results; On the home page of the application, click the export button to enter the export display, select the test results to be exported, click OK button 5.4 Auto step to export the test results to the USB flash drive. 1. Click Auto step icon to enter the application home page, click the parameters position on the above of the display to enter the auto step settingsdisplay. The autostep parameters are shown in the table below; Table 16 Auto step settings Items Valid values Description Stroke mode Round trip, One way Set the stroke mode Cycle Count 0 ~ 1000 Set the number of cycles Step Mode Points,percent, value, custom Set the auto step mode Cycle interval 0 ~ 3600 seconds Dwell time 0 ~ 3600 seconds Set the interval time between the end of each cycle and the start of the next cycle The pressure stable remaining time for one point 61 Control Range Module range currently available for pressure control Cannot Step range exceed the Module range used for auto step controllable pressure range of the selected control Set auto step output range range. Number of step points Step value Step value 2 ~ 21 Set the step points. 5% ~ 100% Can be set when step mode is percent The step range is related to the step points range Can be set when step mode is value It can be edited when the step mode is Step point list custom, and it’s read only in other Displays a list of set points for autostep modes. 2. After the parameters setting is completed, users can Vent or Zero the controller. 3. Click the start button to run the auto step process; 4. After starting, each step point is executed sequentially. Users can also click 5. Click button topausethe step process, or click 5.5 Absolute Pressure Error Calculator or to swtich step points; button to stop the step process. Through the range and accuracy of barometric pressure and gauge pressure, the range and accuracy of absolute pressure can be synthesized, which is convenient for users to use. 1. Barometer pressure settings 62 (1) Select the barometer pressure source, users can select the internal Barometer module or Custom Barometer. (2) If select the internal barometer module, the range and accuracy spec is from the barometer module. (3) If select custom barometer, need to set the error type, range etc. Error type selection:relative error and absolute error Range setting: Need to set the range lower, upper limits and units. Accuracy: It needs to be filled in when selecting reference error as the error type.The settable range is (0.001 ~ 10 ) %FS; Precision: It needs to be filled in when selecting absolute error as the error type. The settable range is dependent on the pressure range. 2. Intrernal barometer module mode error calculation (1) At the gauge pressure range, select the module range that participates in the synthetic error. Other parameters cannot be set. (2) At the absolute pressure range, the resultant absolute pressure range and error are automatically calculated. The resultant error type is the same as that at the gauge pressure range. 3. Custom barometer mode error calculation (1) Click Add Custom Range Control under Gauge Pressure Range to set relevant parameters. For the setting process, refer to the settings for custom atmospheric pressure in "1". (2) After the setting is completed, the synthesized absolute pressure range and error are automatically calculated at the absolute pressure range. The synthesized error type is the same as the custom range type at the gauge pressure range. 63 6. System diagnostics 6.1 ADT773/783 Table 17 ADT773/783 system diagnostics Fault name Target pressure overpressure protection Error code 300 301 Solution 1. Perform auto tune operation 1. Please check whether there are leaks in the equipment and connecting tubing 2. Perform auto tune operation 1. Please check the positive pressure air source pressure S1 The target pressure cannot 302 be controlled stably 2. Please check whether there are leaks in the equipment and connecting tubing 3. Perform auto tune operation 1. Please check the negative pressure air source pressure S2 303 2. Please check whether there are leaks in the equipment and connecting tubing 3. Perform auto tune operation 304 The target pressure cannot be reached during boosting 305 306 The target pressure cannot 307 be reached during decompression 64 308 1. Please check whether there are leaks in the equipment and connecting tubing 1. Please check the positive pressure air source pressure S1 2. Please check whether there are leaks in the equipment and connecting tubing 1. Unable to deflate under negative pressure 1. Please check whether the CPS circuit connection and gas line connection are normal. 1. Unable to deflate under positive pressure 309 310 311 reached 315 316 cannot be connected Internal low high-pressure module cannot be connected High and low range module installation error Low range module overpressure alarm Low range module 1. Please check whether there are leaks in the equipment and connecting tubing be reached for a long time, and the system has automatically stopped controlling. Please follow the corresponding fault prompts or consult the user manual to handle it accordingly. Unable to drain High pressure module 2. Please check whether there are leaks in the equipment and connecting tubing 1. Due to the fault {here is the fault code: such as 305}, the target pressure cannot System protection when target pressure cannot be 1. Please check the negative pressure air source pressure S2 1. Please check whether the CPS circuit connection and gas line connection are normal. 1. Please check whether the drain valve can be opened normally 1. Please confirm whether the high-pressure module has been installed. If it has 320 been installed, reinstall the high-pressure module. 2. Restart the device 321 1. Restart the device 2. Reinstall the low-pressure module 1. Please reinstall the high and low-pressure modules. The measuring range of the 322 high-pressure module must be greater than or equal to the measuring range of the low-pressure module. 323 324 1. Please check whether the gas line connection is normal 2. Please check whether the calibration data of the low-pressure module is normal. 1. Please check whether the gas line connection is normal 65 overpressure protection High range module overpressure alarm Internal module overpressure protection External module overpressure alarm External module overpressure protection The external module is not connected to the tubing 2. Please check whether the calibration data of the low-pressure module is normal. 325 326 1. Please check whether the gas line connection is normal 2. Please check whether the high-pressuremodule calibration data is normal. 1. Please check whether the gas line connection is normal 2. Please check whether the high-pressure module calibration data is normal. 327 1. Please check whether the external module tubing connection is normal. 328 1. Please check whether the external module tubing connection is normal. 329 1. Please check whether the external module tubing is connected normally 2. Please check whether there is leakage in the external module tubing 1. Please check whether the gas line connection of the atmospheric pressure Atmospheric pressure module over-pressure alarm 330 module is normal. 2. Please check whether the calibration data of the atmospheric pressure module is normal. 6.2 ADT793 Table 18 ADT793 system diagnosis Fault name Target pressure overpressure protection 66 Error code 200 Solution 1. Perform auto tune operation 1. The control cannot be stabilized due to too small a control pressure (this item is The target pressure cannot be controlled stably 201 displayed when the set point value is determined to be less than 100kPa) 2. Check the equipment for leaks 3. Perform auto tune operation The target pressure cannot be reached during boosting 202 203 1. Check whether the liquid level in the liquid storage tank is too low 2. Check the equipment for leaks 1. Check the equipment for leaks 2. Perform auto tune operation The target pressure cannot be reached during 204 1. Perform self-tuning operation decompression Accumulator pressure is low Internal low pressure module overpressure protection 209 1. Please execute "Accumulator Charging", the entrance is located in "System Settings" -> "Maintenance" 214 1. Restart the device and re-control the pressure 215 1. Restart the device 216 1. Check the pressure connection of the external module 217 1. Please check whether the external module tubing is connected normally Internal high pressure module overpressure protection External module overpressure protection The external module is not 67 connected to the tubing Internal low-pressure module cannot be connected Internal module cannot be connected 68 2. Please check whether there is leakage in the external module tubing 270 1. Restart the device 271 1. Restart the device
advertisement
Key Features
- Modular design
- High control accuracy
- Wide pressure range
- Built-in pump sources (773 & 793)
- Multiple test functions
- Easy maintenance
- SCPI command set compatibility
- External drive valves
- I/O alarm output
- Pressure switch testing interface
Related manuals
Frequently Answers and Questions
What are the different pressure ranges available for the 773, 783, and 793 models?
The 773 model has a low pressure range of (-380~400) inH2O. The 783 models offer different pressure ranges: ADT783-D (-14.35~35) psi, ADT783-1K (-14.35~1,000) psi, and ADT783-3.6K (-14.35~3,600) psi. The 793 model is a hydraulic model with a range of (0~15,000) psi.
What type of pressure measurement is offered by the controllers?
The controllers provide both gauge and absolute pressure measurements. Absolute pressure is achieved through the synthesis of the basic gauge pressure module and the optional atmospheric pressure module.
Do I need an external air source for all the models?
The 773 and 793 models have built-in pump sources, eliminating the need for an external air source. The 783 models require an external air source.