Drawell DW-27mini DW-XRD-27mini Desktop XRD X-ray Diffractometer Technical Solution Owner's Manual
Add to My manuals61 Pages
advertisement
▼
Scroll to page 2
of
61
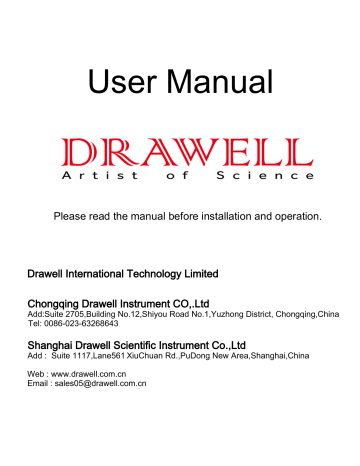
User Manual Please read the manual before installation and operation. Drawell International Technology Limited Chongqing Drawell Instrument CO,.Ltd Add:Suite 2705,Building No.12,Shiyou Road No.1,Yuzhong District, Chongqing,China Tel: 0086-023-63268643 Shanghai Drawell Scientific Instrument Co.,Ltd Add : Suite 1117,Lane561 XiuChuan Rd.,PuDong New Area,Shanghai,China Web : www.drawell.com.cn Email : [email protected] Content 1. OVERVIEW............................................................................................................................................................ 1 2.BASIC PRINCIPLE AND COMPOSITION......................................................................................................... 1 2.1 BASIC PRINCIPLE ................................................................................................................................................. 1 2.2 DIFFRACTOMETER COMPOSITION ........................................................................................................................ 2 2.3 X-RAY DETECTOR ............................................................................................................................................. 11 2.4 DIFFRACTION DATA PROCESSING AND ANALYSIS SYSTEM ................................................................................ 12 3 SELECTION OF MEASUREMENT METHOD AND CONTROL PARAMETERS ..................................... 14 3.1 X - RAY WAVELENGTH SELECTION .................................................................................................................... 14 3.2 MONOCHROMATIC METHOD SELECTION FOR X-RAYS ...................................................................................... 15 3.3 TUBE VOLTAGE AND CURRENT SELECTION ....................................................................................................... 15 3.4 SLIT SELECTION................................................................................................................................................. 16 3.5 SCAN MODE, METHOD AND SPEED SELECTION ................................................................................................. 17 4. PREPARATION OF POLYCRYSTALLINE DIFFRACTION SAMPLES..................................................... 20 4.1 PREPARATION OF BLOCK SAMPLES.................................................................................................................... 20 4.2 PREPARATION OF POWDER SAMPLES ................................................................................................................. 22 4.3 OTHER PROBLEMS IN PLATE SAMPLE PREPARATION.......................................................................................... 25 5. NOTES FOR THE USE OF X-RAY DIFFRACTOMETER............................................................................. 27 6 OPERATING CONDITIONS ............................................................................................................................... 28 7 MAIN TECHNICAL PARAMETERS OF XRD ................................................................................................. 28 8 XRD CONTROL SOFTWARE INSTALLATION.............................................................................................. 29 8.1 COMPUTER SYSTEM REQUIREMENTS ................................................................................................................. 29 8.2 XRD CONTROL SOFTWARE INSTALLATION ........................................................................................................ 31 8.3 COMMUNICATION PORT SETTING....................................................................................................................... 33 9 OPERATION PROCEDURE ............................................................................................................................... 33 9.1 XRD STARTUP ................................................................................................................................................... 33 9.2 XRD CONTROL SOFTWARE STARTUP................................................................................................................. 34 9.3 CONTROL SOFTWARE INITIALIZATION................................................................................................................ 36 9.4 XRD INITIALIZATION PARAMETERS SET ............................................................................................................ 37 10 SAMPLE MEASUREMENT .............................................................................................................................. 39 10.1 MEASUREMENT(REGULAR Θ-2Θ MEASUREMENT).......................................................................................... 40 10.2 GRAZING MEASUREMENT................................................................................................................................ 43 10.3 OMG (SWING) MEASUREMENT ....................................................................................................................... 46 11 COMMAND CONTROL .................................................................................................................................... 48 11.1 CONTROL COMMAND LIST............................................................................................................................... 48 12 CHANGING USER NAME AND PASSWORD................................................................................................ 50 12.1 ADDING USER AND PASSWORD........................................................................................................................ 50 12.2 CHANGING USER NAME AND PASSWORD ........................................................................................................ 50 12.3 DELETING USER NAME AND PASSWORD.......................................................................................................... 51 13 TURN-OFF THE X-RAY DIFFRACTOMETER ............................................................................................. 51 14 POSSIBLE PROBLEMS DURING CONTROL SOFTWARE RUNNING.................................................... 51 15 X-RAY DETECTOR REPLACEMENT METHOD......................................................................................... 52 15.1 DESCRIPTION OF THE PERFORMANCE OF VARIOUS DETECTORS...................................................................... 52 15.2 X-RAY DETECTOR REPLACEMENT ................................................................................................................... 53 15.3 X-RAY DETECTOR REPLACEMENT PRECAUTIONS ............................................................................................ 54 16 OTHER APPLICATIONS OF DIFFRACTOMETER ..................................................................................... 54 16.1 AUTOMATIC IDENTIFICATION ON FUNCTION ACCESSORIES.............................................................................. 55 16.2 SIX-SAMPLE CHANGER.................................................................................................................................... 56 1. Overview X-ray diffractometer (XRD) is a large and precise scientific instrument integrating optical, mechanical and electrical software. XRD can analyze the crystal structure of natural or synthetic, organic or inorganic, powder or block materials, and characterization of cell parameters, grain size, texture stress and qualitative and quantitative analysis. It is widely used in clay minerals, cement building materials, environmental dust, chemical products, pharmaceuticals, asbestos, rock ore, polymer and other fields. 2.Basic principle and composition 2.1 Basic principle The X-ray wavelength is close to the distance between the atomic surface inside the crystal. The crystal can be used as the spatial diffraction grating of the X-ray, that is, when a beam of X-ray hits the object, it is scattered by the atoms in the object, and each atom produces scattering waves. These waves interfere with each other, resulting in diffraction. The result of the diffraction wave superposition is that the intensity of the ray increases in some directions and decreases in others.The crystal structure can be obtained by analyzing the diffraction results. This is an important scientific prediction made by the German physicist Laue in 1912, which was immediately confirmed by experiments. In 1913, British physicists Bragg and his son, on the basis of Laue's discovery, not only successfully determined the crystal structures such as NaCl and KCl, but also proposed the famous formula as the basis of crystal diffraction: Bragg equation:nλ=2dsinθ In the equation, λ is the X - ray wavelength and n is any positive integer.When the X-ray is incident at a sweep Angle (the complementary Angle of the ray incidence Angle, also known as Bragg Angle) to the crystal plane with spacing d of the crystal plane of a lattice, the diffraction line that is enhanced by superposition will be obtained in the reflection direction in accordance with the above equation. X-rays and their diffraction x-rays are electromagnetic waves with very short wavelengths (0.06-20nm) that can penetrate materials of a certain thickness and make fluorescent materials glow, photographic emulsions, and gas ionization. X-ray is produced when the metal target is bombarded with high-energy electron beam. It has the specific wavelength corresponding to the elements in the target, which is called characteristic X-ray. For example, the corresponding X-ray wavelength of copper target is 0.154056nm. 1 For crystal materials, when the crystal to be measured is at a different Angle from the incident beam, those crystal faces satisfying Bragg diffraction will be detected, which are reflected in the XRD pattern as diffraction peaks with different diffraction intensity. For amorphous materials, the XRD pattern of amorphous materials shows some diffuse scattering peaks because there is no long-range order of atoms arranged in the crystal structure, but only short-range order in the range of a few atoms. 2.2 Diffractometer composition X-ray diffractometer has various forms and applications, but its basic structure is very similar. From application perspective, it is classified as single crystal diffractometer and polycrystal diffractometer.The object of single crystal diffractometer is single crystal sample, which is mainly used to determine the crystal structure of unknown crystal materials. Polycrystalline X-ray diffractometer, also known as powder diffractometer, is usually measured in bulk materials such as powder, polycrystalline metal or polymer.The diffractometer is mainly composed of the following four parts: 1 .X ray source with high stability: The X-ray source provides the required X-ray for measurement. Changing the anode target material of the X-ray tube can change the wavelength of the X-ray, and the output power can be changed to control the intensity of the X-ray source. 2 .Diffraction Angle measuring device (goniometer) : accurately measure the diffraction direction of the material crystal surface. 3 .X-ray detector: mounted on the goniometer, receives and transmits the diffraction intensity to the recording control unit to generate the diffraction pattern. 4 .Diffraction data processing and analysis system: X-ray diffractometer is equipped with special diffraction data processing and analysis software. 2.2.1 X ray source with high stability The X-ray generator of X-ray diffractometer is composed of X-ray tube, high voltage generator, tube voltage and tube current stabilization circuit and various protection circuits. X-ray tubes for modern diffraction are all thermionic diodes, either sealed or rotating.The maximum power of the former is within 2.5kw, depending on the target material; The latter is designed for high intensity x-rays and typically has a power ofmore than 10kW. The AL series X-ray diffractometer uses a ceramic X-ray tube (Figure 1-1). 2 Fig.1-1 Sealed ceramic tube The X-ray tube is essentially a vacuum diode, see the principle as shown in Figure 1-2. Fig. 1-2 Schematic diagram oftube When the cathode is heated with an electric current, a thermally radiated electron beam is released.Under the action of a high-voltage electric field, these electrons are accelerated and bombarded by the anode target to emit x-rays.The common anode targets are Cr, Fe, Co, Ni, Cu, Mo, Ag, W, etc. See the X-ray wavelengths and operating voltages of commonly used targets as shown in table 1-1. Table1-1 X-ray wavelengths and operating voltages of common targets Target Atomic No, Kα1 Vk/kV Work /kV material Cr 24 2.28962 2.29351 2.909 2.08480 2.0701 5.98 20 - 25 Fe 26 1.93597 1.93991 1.9373 1.75653 1.7433 7.10 25 - 30 Co 27 1.78892 1.79278 1.7902 1.62075 1.6081 7.71 30 Ni 28 1.65784 1.66169 1.6591 1.50010 1.4880 8.29 30 - 35 Cu 29 1.54051 1.54433 1.5418 1.39217 1.3804 8.86 35 - 40 Mo 42 0.70926 0.71354 0.7107 0.63225 0.6198 20.0 50 - 55 Ag 47 0.55941 0.56381 0.5609 0.49701 0.4855 25.5 55 - 60 The focal point of electron beam bombardment on the anode target surface is a thin rectangular shape (called line focal point). The grazing Angle of the X-ray emitted from the center ofthe ray exit window and the target surface is 3°-6 °.Therefore, the focal spot of the target surface is observed from the two exit Windows perpendicular to each other in the direction of emission, and the focal spot shape is different. Observed from the two exit Windows on the long edge of the focal spot 3 perpendicular to the direction of the discharge, the focal spot is linear, which is called the linear light source.When observed from the other two exit windows, the focal spot is a point light source. Residual stress and texture measurements generally require a point light source, while other applications generally require a line light source. Therefore, every time the diffractometer is installed with an X-ray tube, it is necessary to identify whether the X-ray exit window used is in the direction of line focus (the X-ray tube is marked). In addition, the goniometer is required to have a proper inclination Angle relative to the target plane. The rated power of the X-ray tube varies according to the type of target and the manufacturer.For long continuous operation, the recommended power is less than 80% of the rated value, which is beneficial to prolong the life of the X-ray tube. Only a small part of the power consumed by the X-ray tube is converted into X-ray power, and more than 99% is converted into heat and consumed. Therefore, the X-ray tube must be cooled by water flow from behind the target surface to avoid melting and destruction. In order to improve the heat exchange efficiency between the target surface and water, the cooling water is sprayed on the back of the electronic focus with a nozzle, and the flow rate is required to be greater than 3.5 L/min. The protection circuit of X - ray generator must be reliable. 2.2.2 Diffraction angle measuring device Diffractometer goniometer is the most precise mechanical component of X-ray diffractometer, which is used to accurately measure the diffraction Angle. See the principle as shown in figure 1-3. Figure 1-3 Schematic diagram of goniometer The sample table is located at the center of the goniometer, and the center axis ON of the sample table is perpendicular to the center axis O of the goniometer (vertical surface).The sample table can rotate around the central axis of measuring Angle and its own central axis. 4 After the sample is loaded on the sample table, the surface of the sample is required to be strictly re-aligned with the center of the goniometer. The incoming ray is emitted from the focus F of the X-ray tube and irradiates to the sample surface through the incident aperture system S1 and H, while the reflected ray enters the counter D through M and S2. The focus F of the tube and the receiving aperture G are on the same circumference, which is called the goniometer (or diffractometer) circle, and the plane in which the circle is called the goniometer plane. The sample table and counter are fixed on two coaxial disks respectively, driven by two motors. During the diffraction measurement, the sample rotates around the central axis of the goniometer, constantly changing the Angle θ between the x ray and the sample surface. The counter moves along the circle of the goniometer and receives the diffraction intensity corresponding to each diffraction angle 2θ. θ and 2θ can be driven individually or automatically, as needed, so thatθ and 2θ are driven at a combined angular speed of 1:2. Scanning range of goniometer: forward up to 165°;The negative direction can reach - 10° (The Angle measurement range of instruments of different manufacturers is slightly different. Please refer to the user manual when using it). The absolute accuracy of Angle measurement can reach 0.01°, and the repetition accuracy can reach 0.0001. The diffraction geometry of the goniometer is designed according to bragg-brentano focusing and case studies. As shown in figure 1-4, the focus F of the X-ray tube and the receiving slit G of the counter are located on the same focusing circle with the sample surface, so the diffracted beam emitted from point F can be focused at G spot after diffracted by the sample. The focusing circle intersects the goniometer circle only at one point, except for the X - ray tube focus F. That is, no matter how the diffraction conditions change, under certain conditions, only one diffraction line can focus on the goniometer circle. Therefore, the counter moving along the goniometer circle can only measure the diffraction lines one by one. Figure 1-4 Diffraction geometry ofthe goniometer 5 According to the requirements of the focusing condition, the sample surface should always have the same surface as the focusing circle.However, the radius of curvature of the focusing circle changes constantly during the measurement process, but the sample surface cannot achieve this, so it can only be treated approximately. The plate sample is adopted to keep the sample surface always tangent to the focusing circle, that is, the center of the focusing circle always lies on the normal line ofthe sample surface. In order to make the counter always on the sample surface (i.e., parallel to the surface of HKL diffraction side) of the diffraction direction. Rotate the sample surface and the counter in the same direction around the center axis of the goniometer at the same time, and maintain the angular velocity relationship of 1:2, that is, when the sample surface and x-ray become theta Angle, the counter is just at the position of 2 theta Angle. Thus, the powder polycrystal diffractometer always detects diffraction surfaces that are parallel to the surface ofthe sample. 2.2.2.1 Slit system The goniometer is equipped with a slit system. It is impossible to control the divergence along the long side of the slit if only the usual slit aperture is used, resulting in the non-uniform width of the diffraction ring. In order to eliminate this phenomenon, a joint aperture system consisting of slit diaphragm and Soller diaphragm are adopted in the goniometer optical path, as shown in figure 1-6. Figure 1-6-1 aperture slit ofthe goniometer 6 Figure 1-6-2 Goniometer slit position Soller slit S1, S2: the Soller slit consists of a set of parallel, closely spaced sheets of heavy metals (Ta or Mo) that limit the axial divergence of x-rays in the goniometer so that X-ray beams can be approximately viewed as divergent beams that diverged only in the plane ofthe scanning circle. It is designed between the source and the sample, and between the sample and the detector. During installation, the slice should be parallel to the goniometer plane so that the X-ray divergence in the direction of the vertical goniometer plane can be controlled at about 2°.The total emission Angle of the cable slit of the diffractometer (2 x slice spacing/slice length) is about 3.50°. Therefore, the measurement error of diffraction Angle caused by axial divergence is relatively small, and the peak distortion is also relatively small. Therefore, better peak shape can be obtained, and better diffraction Angle resolution can be obtained. The function of the divergent slit diaphragm H is to control the energy and divergence of such rays, and thus to limit the area of exposure of x rays to the sample. For example, for an X-ray tube with a hot focal spot size of 1mm x 10mm and an effective projection focal spot of 0.1mm x 10mm, the sample is irradiated with a width of 20mm and an irradiated area of 200mm2 (20mm x 10mm) when a 1° divergent slit aperture is used, 2θ=18°. As 2θ angle increases, the width (or area) exposed decreases.If only the diffraction line with high diffraction angle is measured, a larger divergent slit aperture can be selected to obtain a larger incoming ray energy. The function of the anti-scattering slit M is to block the parasitic scattering beyond the diffraction line (such as scattering from the edge of each slit stop and scattering from other metal 7 accessories along the path) from entering the detector, which helps to reduce the background. It should be slightly wider than the width ofthe diffraction beam. The receiving slit aperture G is used to control the energy of the diffraction line entering the counter. Its size can be selected according to the specific requirements of experimental measurement. The apertures and slits are available in a variety of widths, and the smaller the slits, the less receptive but more accurate they are. 2.2.2.2 Filter system The light emitted from the X-ray tube is a complex source with a mixture of wavelengths, including continuous spectrum, Kα and Kβ characteristic spectrum.When all of these wavelengths are diffracted, very complex diffraction information cab be obtained. In addition, when an X-ray of one wavelength exposes on the sample, it is possible to excite the characteristic ray (X-ray fluorescence) of the sample itself. In order to obtain the diffraction information of a single wavelength, the method of inserting filter or adding monochromator is usually used to remove Kβ radiation and fluorescent radiation. The filter and monochromator are generally arranged between the sample and the receiving slit. The filter material and radiation wavelength can be selected reasonably by utilizing the absorption limit of the material to the X-ray absorption process, so as to obtain a good diffraction pattern.Polycrystalline X - ray diffraction experiments use K - series to identify X - ray sources. However, in many cases, the diffraction pattern corresponding to Kβ rays is not expected to appear in the diffraction pattern, because it complicates the diffraction pattern and hindering the analysis of the spectrum. The solution to this problem is to put a filter between the X-ray source and the sample to absorb Kβ rays.The selection of filter material should take advantage of the characteristics of K absorption limit. If we choose such a material as the filter, its K absorption limit lies just between Kα and Kβ of the radiation source, and we should pay attention to be as close as possible to Kα . This is because the 8 filter absorbs Kβ very strongly, but absorbs Kα very little. After filtering, only Kα is left (figure 1-6). Figure 1-7 Function ofthe filter To eliminate the background of the diffraction pattern, the most effective method is to use a crystal monochromator (figure 1-8). The common practice is to install a curved crystal monochromator on the diffraction line. The diffraction line (primary diffraction line) generated by the sample diffraction is projected to the single crystal in the monochromator through the aperture system, and the orientation of the single crystal is adjusted so that the Angle between a certain highly reflective crystal plane (high atomic density crystal plane) and the primary diffraction line is exactly equal to the Bragg Angle radiated by the crystal plane to Kα . In this way, the secondary diffraction line issued by the single crystal after diffraction is the pure Kα . diffraction line corresponding to the sample diffraction line. The crystal monochromator eliminates both the Kβ ray and the background produced by continuous and fluorescent x-rays.However, the graphite curved crystal monochromator of the diffraction beam commonly used cannot eliminate the radiation of Kα2, so the secondary diffraction line focused by the curved crystal monochromator is given by the counter as the double diffraction peak of Kα1 and Kα2 9 Figure 1-8. Monochromator function Graphite crystal monochromator uses 0002 reflector. With a graphite-curved crystal monochromator, the diffraction intensity for Kα is approximately 70% lower than that without the monochromator, which is equivalent to the reduction in diffraction intensity with the filter chip. The graphite monochromator is used to test the iron base sample on CuKα radiation where the back base can be lowered effectively and a satisfactory result can be obtained. However, the monochromator is not effective for samples with the same X-ray tube target elements. Because the fluorescent x-rays produced by the continuous X-ray excitation of the sample have the same wavelength as the signature x-rays emitted by the X-ray tube. Seen from figure 1-9, when Cu target radiation is used to test samples containing copper element, the abnormal phenomenon from low to high will occur at a low Angle. 10 Figure 1- changes in the background of copper diffraction spectrum -containing sample scanned with a graphite monochromator 2.3 X-ray detector The main function of the counter is to convert the energy of X-ray photons into electrical impulses.Radiation detectors commonly used in X-ray diffractometers are proportional counter, scintillation counter, and semiconductor detector. Scintillation detector For various X-ray wavelengths used in crystal X-ray diffraction, the quantum efficiency is up to 100%. Good stability and long service life; In addition, it has a very short resolution time (class 10-7s), so it is virtually unnecessary to consider the counting loss caused by the detector itself. Soft X - rays for crystal diffraction also have some energy resolution. Proportional detector When the proportional counter receives X-ray photons, it only produces local electron avalanche effect at its receiving position, and the electric pulse generated is output to both ends of the counter. The distance between the two ends and the pulses generated at different positions is different, so there is a certain time difference between the different pulses. This time difference gives the proportional counter position resolution in the direction of the core wire. A corresponding electronic measurement system can simultaneously record the number and energy of incoming X-ray photons and where they are absorbed by the counter. Proportional detector is a high speed measurement counter.It is suitable for recording diffraction patterns at high speed, measuring transient changes (such as phase transitions), measuring unstable samples that are prone to change over time and samples that are vulnerable to X-ray damage, and measuring microsamples and weak diffraction information (such as diffuse scattering). Semiconductor detector With the development of science and technology, scientists have 11 developed many new semiconductor detectors such as Semiconductor array, semiconductor line array, silicon drift chamber, etc. based on lithium Ge (Li), lithium Si (Li), HPGe of high purity germanium, and metal barrier detectors. A proportional or scintillation detector, often called a "point detector," can only accept an intensity of 2θ angle at any given moment. Advanced diffractometer can choose to configure line array or array detector to receive multiple 2θ angle diffraction at the same time, its sample measurement speed can be increased dozens of times. 2.4 Diffraction data processing and analysis system The software system of X-ray diffractometer consists of two parts: data acquisition and processing software package and application software data processing software package. The data acquisition and processing software package can basically meet the requirements of general analysis, while the application software data processing software package is used to analyze the diffraction data system. Data collection and data processing software includes the following functions: 1. Automatic control of X-ray diffractometer includes X-ray generator, goniometer, recording control unit, etc.;Diffraction data are collected to form ASC code data files.Data processing includes automatic peak search, manual peak search, integral strength, peak height, center of gravity, background deduction, smoothing, peak magnification, multigraph, half height and width calculation, spectral print. 2. Application software data processing package: to identify the diffraction data files generated by diffractometers of different manufacturers at home and abroad, and make the most perfect processing ofthe diffraction data. 3. Basic data processing functions: peak search: automatic peak search, manual peak search.Peak marks can be marked by d value, 2θ Angle, intensity, intensity percentage, half height and width, peak number, crystal plane index (HKL), etc. 4. Diffraction data calibration: the diffraction data of the standard sample are used to calculate the response variable factors, and the original measured data are corrected to eliminate the influence of instrumental measurement or sample preparation and other factors on the measured results; 5. Background deduction: there are two kinds of background deduction methods: automatic deduction and manual deduction. The automatic background deduction method can choose linear method or parabolic fitting method; 6. Integral area calculation: the starting and ending angles can be determined, and the fitting method can also be used for automatic calculation; 12 7. Calculation of second-class stress and grain size: the half-peak width (true) and grain size of the peak are calculated by fitting method; 8. Stripping of Kα1 and α2:after the background is deducted, β line is automatically removed Kα2 is stripped, and the data file containing Kα1 is processed and saved for other analysis; 9. Smoothing: set smoothing points and choose smoothing methods, including full spectrum smoothing, only smoothing background, smoothing background adjustment peak, etc.; 10. Peak amplification: select the range of any spectrum, and zoom in and out ofthe spectrum at any multiple through the left and right mouse keys; 11. Correction ofthe spectrum: delete the redundant peaks of the spectrum and add the missing peak marks by using the left and right mouse keys; 12. Multi-drawing: open several data files at the same time, which can be processed separately or compared at the same time; 13. 3D drawing function: when more than 3 files are opened at the same time, 3D drawing can be performed. It is generally used to compare the diffraction data of the same sample under different conditions or produce the diffraction data of the same sample under different conditions; 14. Other functions: linear analysis, cell determination, second-class stress calculation, diffraction line indexing, etc.; 15. Data processing result printing: all the data can be printed out after processing, and can be previewed and modified before printing, such as: re-opening the window to enlarge the peak part, pulling up the weak peak, adding text annotation, selecting the printing format, etc.; 16. Physical phase qualitative analysis: the retrieval database can be generated by using the universal international database, or the card number can be selected from the card library to establish its own retrieval database. At the same time of data processing, data files can be used for retrieval.Select to search by all spectra, multiple peaks and single peak. The retrieval results can be manually interfered, such as input element information, elimination of similarity but no existence phase, multiple retrieval;Superposition of retrieval results, comparison of bar diagrams, and optional identification of molecular formula, substance name, HKL and other parameters, and printout of retrieval results; 17. Quantitative analysis: the method of quantitative analysis without standard samples is adopted. After the full spectrum fitting, qualitative analysis and sample composition determination, rapid quantitative analysis is conducted on the samples to determine the content of substances. 18. Full-spectrum fitting analysis of polycrystalline structure (WPF) : the fine-tuning and crystal structure analysis of the full-spectrum linear fitting can not only study the structure of 13 polycrystalline aggregates, but also the internal microstructure of crystals, such as impurities, dislocations, grain boundaries, lattice distortion and other defects in the crystals. 19. Diffraction spectrogram simulation: X-ray diffraction spectrogram is generated by simulating the arrangement structure diagram of material atoms. 3 Selection of measurement method and control parameters 3.1 X - ray wavelength selection Selection of suitable X-ray wavelength (selection of anode target) is the basis of sample measurement. The selection of the X-ray tube for that target depends on the element composition of the sample under test. The principle of target selection is to avoid using the wavelength that can be strongly absorbed by the sample, otherwise the sample will emit strong fluorescence radiation, increasing the background of the diffraction pattern. According to the rule of element absorption properties, the target selection rule is that the atomic number of the target material of X-ray tube should be smaller or equal than that ofthe lightest element in the sample (except calcium and elements lighter than calcium), and should not be greater than 1 at most.The strengths and uses of common targets are shown in table 1-2. Table 1-2 Specialty and application of common target materials Main specialties Application suitable for the measurement Almost all of them are determined by monochromator filtering, and the Cu samples are measured with high Target species Cu of the spacing between crystal surfaces at 0.1 -- 1nm fluorescence back base. If Kβ filter is used, it is not suitable for the determination of Fe series samples. The diffraction line ofthe Fe Co sample is strong. If it is The monochromator method is most suitable for the filtered by Kβ, the back base determination of Fe series samples. is high. Fe The back base ofthe Fe sample is small. Cr long wavelength Mo short wavelength The filter method is most suitable for the determination of Fe series samples This includes the applied determination of Fe samples, using the PSPC-MDG microzone (reflection method). Quantitative analysis ofAustenitic phase, transmission measurement of foil (small Angle scattering, etc) 14 W Continuous high X - ray intensity Laue photographic determination of single crystal 3.2 Monochromatic method selection for x-rays X-ray monochromatization and elimination of the back base are important detection techniques for the detection of tiny peaks. The correct selection of the filter can absorb a large amount of Kβ radiation, so that the Kβ value becomes a very small peak, whose intensity is roughly 1/100 of the intensity of Kα on the same diffraction surface. However, the escaped peak and continuous X rays longer than the Kαband cannot be removed, and the fluorescence X rays emitted by the sample are also recorded. The monochromator is a single crystal with a curved surface that is aligned so that it diffracts exactly with Kα radiation over the surface of the crystal, through which Kα radiation passes. However, the radiation of other wavelengths cannot pass through because it does not meet the single crystal diffraction conditions. It is thus possible to remove rays of any other wavelength except the characteristic ray. For example, Kβ diffraction line and the tiny peak caused by the pollution of external light source can also remove the fluorescence X-ray, continuous X-ray and escape peak. Therefore, the diffraction data obtained are of low back base and good quality, and the monochromator effect is not great for light element samples that are less affected by fluorescence X-ray or samples with the same elements as the target material. The combination of a detector with a high wavelength resolution and a wave height analyzer can be used to monochromatize the x-rays. It is possible to remove Compton scattering, which is effective for determining the amorphous radial distribution function of light element. If high power X-ray radiation is used in conjunction with a monochromator, the selection of radiation wavelength is not important.For example, when the graphite monochromator is used, the peak to back ratio of diffraction data is greatly improved when the Fe sample is measured by Cu radiation. In particular, it should be noted that, although the optical tube can be replaced to meet the measurement of different samples, in fact, the replacement of the optical tube is a time-consuming work, and it is easy to damage the optical tube, and even damage the high-voltage cable head.If the graphite monochromator is used, the optical tube may not be replaced. Samples containing Fe can be measured by using Cu radiation plus graphite monochromator. On the contrary, this combination of Cu and graphite monochromator will make the fluorescence background higher. 3.3 Tube voltage and current selection The intensity of the characteristic X-ray is proportional to the difference between the tube 15 voltage and the lowest excitation voltage to the NTH power, which is proportional to the tube flow.The n value of the tube voltage hour is close to 2, and decreases with the increase of the tube voltage. In addition, the continuous X-ray intensity that becomes the back base in the Kβ-filter method is proportional to the square of the tube voltage and proportional to the tube current. Therefore, for a variety of different targets, there are different optimal tube voltage values, as shown in table 1-3. Table 1-3 Specialty and application of common target materials Optimal tube voltage/kV Minimum Target materials excitation voltage /kV Max instensity Max peak-to-back ratio Common values Mo 20.0 60 45–55 55 Cu 8.86 40–55 25–35 40 Co 7.71 35–50 25–35 35 Fe 7.10 35–45 25–35 35 Cr 5.98 30–40 20–30 30 The maximum tube current value is determined according to the type of target and the maximum capacity of the generator.For sealed tubes, the tube current is generally 40mA. The actual power shall be less than 80% of the rated power. At the same time, when the tube current is too large, the filament temperature is high and the filament bends, resulting in the diffraction peak displacement. 3.4 Slit selection The size of the slit affects the diffraction intensity and resolution.Large slit can obtain larger diffraction intensity, but reduce resolution, while small slit can improve resolution but lose intensity. Generally, larger slit should be selected when intensity is increased, while smaller slit should be selected when high resolution is needed. In particular, receiving slit has a great influence on resolution. Each diffractometer is fitted with a variety of slits for selection. Among them, the purpose of divergent slit is to limit the beam from reaching beyond the sample to avoid causing a large number of additional scattering or lines; The receiving slit is designed to limit the X rays in the area near the Angle to be measured into the detector. Its width plays an important role in the resolution of the diffractometer, the intensity of the diffraction line and the peak-to-back ratio (the ratio of the intensity of the diffraction peak to the intensity of the background).Anti-scattering slit is the auxiliary slit in the optical path, which can limit the additional scattering caused by different reasons into the 16 detector. 1. Divergent slit(DS):As long as the exposure width does not exceed the sample width (standard width: 20mm), the wider the DS, the stronger the X-ray intensity.However, the data of DS=4° shows that the diffraction peak would also become wider and the resolution decreases significantly. 2. Divergent slit DS=1° is usually used in such conditions when the X-ray on the low diffraction Angle side of the incident Angle 2θ=20° is beyond the sample range, the relative intensity of the diffraction peak will be reduced due to the reduction of X-ray exposure.The diffraction peaks of some substances occur frequently below 20°(2θ), and these substances are measured using the DS=1/2°divergent slit. 3. Anti-scattering slit SS: cut off the external scattering line to prevent the increase of the back and limit the receiving Angle of the receiving slit (RS). It uses a slit size consistent with the DS. 4. Receiving slit RS: the slit that determines the receiving width. If this width becomes twice as wide, the integral intensity is also increased to twice as wide, and the resolution of the diffraction peak is reduced. Therefore, when multiple diffraction peaks overlap each other, it is better not to use too wide receiving slit. A receiving slit of RS=0.3mm is usually used.Each diffractometer is fitted with multiple sets of optional slits, selected manually. 3.5 Scan mode, method and speed selection 3.5.1 Scan mode In the focusing method, 2θ/θ continuous scanning is used to keep the sample surface always in the state tangent to the focusing circle, which can obtain high X-ray intensity and resolution.According to the structure of the goniometer, there are two modes of motion: 2θ/θ scanning mode is with the tube fixed without movement, and the sample and detector rotate at an angular speed of 1:2 (figure 1-4); In the θ/θ scan, the surface of the sample remains horizontal (figure 1- 12a), with the tube and detector moving at the same speed relative to the sample. Figure 1-12 Various scan mode(a- Routine scan;b- Asymmetric scan;c-ω scan) During the film analysis, θ is fixed at a low Angle by the parallel beam path (FIG. 1- 13), and 2θ is scanned separately to obtain the diffraction of the sample at a certain depth (FIG. 1-12b), which is 17 a kind of grazing incidence scanning. Figure 1-12c is another special scanning method, called ω scan, which is used to represent the crystallization state ofthe sample. Fig. 1-13 Comparison of focusing and parallel paths 3.5.2 Scanning methods The diffractometer has two scanning methods: continuous scanning and step scanning. Regardless of the measurement method, all diffraction patterns can be given fairly quickly in the case of rapid scanning, which is suitable for the pre-detection of substances, especially for the identification or qualitative estimation of substances. Very slow scanning of the diffraction pattern is suitable for fine distinguishing the details of the diffraction pattern and quantitative measurement.For example, the quantitative analysis of mixture phase, the accurate measurement of crystal surface spacing, the study of grain size and lattice distortion, etc. Continuous scanning: both the sample and the detector rotate at a fixed speed at an angular velocity ratio of 1:2. During the rotation, the detector continuously measures the scattering intensity of the X-ray, and the diffraction lines of each crystal plane are received in turn. Modern diffractometers use electric motors to drive the goniometer. So actually the rotation is not strictly continuous, but progressive.This is especially obvious when the rotation speed is slow.But the detector and measuring system work continuously. The advantage of continuous scanning is high efficiency.For example, the scanning speed of 4°/min (2θ), the scanning range of 20°-80° diffraction pattern can be completed within 15 minutes, and also has good resolution, sensitivity and accuracy, because it is suitable for a large number of daily work (generally phase identification work). 18 Step scan: the sample stops at a certain delta θ of rotation, and then the measurement recording system goes to work, measuring the total (or counting rate) for a fixed period of time and recording the total with a 2θ Angle of the event. Then the sample is rotated a certain step diameter and then measured.And so on, step by step, to complete the scanning of the diffraction pattern Step size selection: continuous scan or step scan can be selected for diffraction data collection by computer. The "step size" of data collection should be selected appropriately in both methods.The sampling step size is small and the number of data increases. The total number of each step is larger and the counting error is smaller. However, if the step size is too large, the reproduction of diffraction peak will be affected. The step length is 1/5- 1/10 of the half height and width of the diffraction peak as the reference.0.02°is used as the benchmark for qualitative analysis. A step size of 0.01°-0.005 ° is sufficient for the accurate measurement of the diffraction peak shape. 3.5.3 Scanning speed The scanning speed of diffractometer affects the resolution of 2θ and the diffraction intensity. If the diffractometer is equipped with a point detector, a receiving slit of 0.2-0.3mm width is generally used, and the scanning speed is 1°/min (2θ) and the time constant is 1s, a diffraction pattern with good resolution can be obtained. Table 1-2 Specialty and application of common targets Measurement method Speed/time DS( SS) RS Scan area and others Quantification Continuous scan(0.02°) 4°- 8°/min 1°, 0.3mm 2°- 90° Organic quantification Continuous scan(0.02°) 4°- 8°/min Trace detection Continuous scan(0.02°) 1°- 2°/min Purpose General quantification (step width) 1/2°, 0.15mm 1°, 0.3mm 2°- 60° main diffraction peak region Quantitative diffraction Continuous scan(0.02°) 1°- 2°/min 1°,.3mm peaks, using a rotating sample table Lattice constant, grain size and Step scan(0.01°) 1–8s/step 1°, 0.2mm Step scan(0.02°) 1–2s/step 1/2°, Make sure there are 4-8 peaks. microstrain crystallinity 3°- 140° 19 0.3mm Radial distribution Step scan(0.1°-0.2°) 4–20s/step Step scan(0.01°-0.02°) 1– 10s/step 1/2°- 2° 3°- 150° function Rietveld refinement 1/2°- 1°, 0.2mm 10°- 130° 4. Preparation of polycrystalline diffraction samples Diffractometer operation is generally divided into several steps: preparation of diffraction sample, sample measurement (including selection of different measurement methods), and analysis of diffraction data. The basic feature of an X-ray powder diffractometer is that the sample used for measurement is composed of a collection of powders (many small grains). It is required that the sample contains a large amount of small grains. The orientation of the small grains is completely disordered, and the probability of finding any crystal plane (HKL) of any orientation within the range of the incident X-ray beam may be considered to be the same. Therefore, the relative diffraction intensity can reflect the relative size of the structure factor. This is the basis of all powder diffraction. Natural or synthetic organic or inorganic materials are basically two physical structures, powder and solid, which can be measured by a diffractometer. There is no general method for sample preparation, and selection should be made according to the actual situation. However, no matter which method is used, a prerequisite must be satisfied -- during the whole process of making the sample until the end of the diffraction experiment, the composition and physical and chemical properties of the sample on the chips must be the same as the original sample, and the reliability of the sample must be guaranteed. When focusing diffraction is used, the surface of the sample that satisfies the quasi-focusing geometry shall be smooth and compact, and shall be precisely tangent to the goniometer axis to lie precisely on the focusing circle. If the surface is uneven and the sample particles are in different planes, the diffraction lines generated by the sample particles that are no longer on the focusing circle will not fall on the focal point, thus it will increase the width of the diffraction peak and decreasing the resolution. 4.1 Preparation of block samples The following aspects should be noted in the preparation and application of block samples. Sampling: when using block samples, it should be noted that the samples should be 20 representative of the characterization. Some corner residues are not representative. In addition, it should be noted that the sampling direction should be consistent. In addition, it should be noted that the sampling direction should be consistent. Although, the general material is polycrystalline material, but more or less there will be selective orientation. In particular, some of the processed metal plate, wire, there are serious special orientation. Samples taken in the same direction are comparable. Sample size: block samples are generally fixed and measured with aluminum sample rack with hollow sample groove. Block samples only need one measurement surface. The sample frame size used by different diffractometers is slightly different. To obtain the maximum diffraction intensity, the sample size should be the same as the sample frame size, not less than 10mm x 10mm. The diffraction intensity is proportional to the volume of the sample diffracted. When the thickness is constant, it is actually proportional to the area of the measured surface (less than the sample area at high diffraction angles). In order to obtain the same experimental results as the large samples, the measurement time ofthe small samples must be extended. Grinding: the measuring surface must be a flat plate. No arcs are allowed in the grinding process. "Wet grinding" shall be used in the grinding process. Dry grinding produces high temperatures leading to phase transitions, oxidation, and stress. First, grind with coarse sandpaper and then with no less than sandpaper 320. Block sample fixation: the front (smooth, flat, facing down) of the aluminum hollow sample holder (figure 1- 11) is inverted on the glass plate, the block sample is placed in the middle of the sample frame, and the measurement is inverted face down on the glass plate. Then take the "vacuum slime" and stick the sample rack and sample. If the sample is very thin and the sample is very small, it is important to pay special attention to the fact that the slime is not exposed to the measurement surface, otherwise the slime is also involved in diffraction, and there are additional slime diffraction peaks in the measured diffraction spectrum. Figure 1-11 Aluminum hollow sample rack and sample loading Application scope of block sample: block sample is generally only suitable for phase 21 identification due to its anisotropy, not for phase quantitative analysis. But residual stress measurement, texture measurement and thin film sample measurement must be block sample. 4.2 Preparation of powder samples The powder samples of X-ray diffraction are required to have uniform particle size; The granularity is about 45μm; Sample shall not be less than 0.5g. See the specific preparation process as follows. Powder making: in order to ensure the representativeness of samples.First, we should take more samples to make powder. For mineral samples and metal alloy samples, a mineral pulverizer can be used to grind the powder into a particle diameter of about 45μm. Grinding and sizing: the mechanical properties of substances are usually expressed in terms of "hardness" and "strength".For the substance with high hardness or strength, it is not easy to grind them fine. In the grinding process of samples containing mixtures of various materials, some materials achieve the required granularity, while others are difficult to achieve the required granularity.For example, mixed graphite and diamond is grinded, a good sample will be never made. Therefore, in the process of grinding powder to distribute grinding and sizing, but not a grinding to the end. Otherwise, the particle size of some materials is already too fine, while the particle size of some materials is not up to the requirements. Materials less than 10μm will produce a microabsorption of the X-ray, which will reduce the diffraction intensity. If it is too thin and reaches below 100nm, the diffraction peak width will be caused. On the contrary, if the particles are too thick, the number of grains involved in diffraction is not enough, which will also reduce the diffraction intensity. In calculating the mass fraction of the various materials in the mixture, the result is lower than the actual mass fraction. Fixation of powder samples: there are many methods of fixation of powder samples for different experimental purposes. 4.2.1 Positive pressure method Take 0.5g powder sample and sprinkle it into the sample groove of the glass sample rack, so that the loose sample powder is slightly higher than the surface ofthe sample rack. Take frosted glass sheet (such as glass slide on sandpaper to grind rough surface) and lightly press the sample surface;Scrape off excess powder;Repeatedly flatten the sample surface so that it is compacting and not higher than the surface ofthe glass sample stand. Laboratories are generally equipped with glass sample racks with two depth sample tanks. When the sample size is large, the deep groove (0.5mm) sample rack is used; when the powder is small, the shallow groove (0.2mm) is used to obtain a larger sample area. If the sample size is not 22 sufficient to fill the sample tank, powder shall be scattered in the middle ofthe tank. The advantage of the positive pressure method is that sample preparation is simple, but the disadvantage is that the powder sample has a certain selective orientation, and the diffraction intensity does not match the strength I/I0 on the PDF card. If the sample is mixed with coarse particles, it is difficult to produce a flat sample. The positive pressure method is generally suitable for phase identification, which cannot be used for quantitative analysis. If the powder particles are thick and flow easily, a little paraffin oil can be applied to the bottom of the sample tank (sold in chemical stores), or a small amount of volatile liquid can be added to the powder sample. 4.2.2 Back pressure method Invert the aluminum sample frame onto a flat glass sheet with a rough surface or place a piece of sandpaper 320 on the flat glass sheet and then fasten the hollow sample frame;Sprinkle the powder from the back of the sample box into the box, press the sample lightly with your thumb, and then compact the powder.Turn the sample holder upside down and remove the flat glass sheet. The biggest advantage of backpressure method is that the measuring surface of the sample is compact, smooth and clean, which is strictly in line with the surface of the sample rack. If using smooth plate glass as the bottom, it will cause a serious alternative orientation. However, using ground-glass or high label sandpaper as the bottom, the powder in free fall will not roll. Compared with the positive pressure method, this method can reduce the alternative orientation of the powder sample, which matches PDF card strength better. This method can not only obtain a good peak Angle but also be used for quantitative analysis.In addition, if the sample contains coarse particles or powder with good fluidity, it is convenient for sample preparation.The disadvantage is that the sample preparation is a bit troublesome, and more sample has to be used. 4.2.3 Side loading (NBS sample loading) The method was proposed by the national bureau of standards (NBS).Cut off the top of one side of the aluminum sample holder, then clamp the sample holder with two pieces of glass, gently pour the powder into the incision of the sample holder, press it tightly, and remove the glass pieces on both sides. The biggest advantage of the side-loading method is that the samples have no special orientation, which meets the needs of quantitative analysis. The disadvantage is that the sample is difficult to compress. Attention shall be paid to sample splash when removing glass. 23 4.2.4 S catter method The scatter method requires a "non-reflective" sample holder that is neither amorphous, like glass, which forms a scattering peak at a low diffraction angle, nor a material with a diffraction peak. Usually, we use a flat plate made of amorphous silicon, amorphous quartz, or monocrystalline silicon in a high exponential lattice plane, or other similar material. For the former, the amorphous scattering peak is not obvious and can be ignored. For the latter, although it is a crystal that can produce diffraction, the diffraction peak of the high exponential lattice is at a very high angle and is not in the measurement range (Generally the measurement angle is less than 90°). The scatter method is used when the sample size is small and the powder is directly sprinkled on the non-reflecting sample plate without pressing. Generally, the sample surface is moistened with a small amount of water or alcohol (for bonding), and then the sample is evenly sifted onto the sample plate with a suitable mesh number (300-350 mesh, mesh number refers to the number of mesh holes on the 1-inch length, the larger the number, the smaller the mesh holes, and the diameter of the 325 mesh screen is about 45μm). 4.2.5 Spray drying method Make the slurry by mixing the sample in a proportion of about 50% with a more volatile liquid that will not chemically react with the sample and will not dissolve the sample with a small amount of adhesive (polyethylene) and suspension agent. The slurry is then sprayed into a heating chamber to form a mist. The liquid in the slurry evaporates in the heating chamber, and the sample particles naturally settle onto a non-reflecting sample plate at the bottom of the heating chamber to produce a usable sample plate. Thus, a spherical particle with a size of about 50μm is formed by the aggregation of many small grains. The orientation of the small grains within the spherical particle is arbitrary. 4.2.6 Aerosol method Flush the air into an evacuated tube containing a powder sample. The sample is flushed to form an aerosol and then allowed to settle freely on a non-reflective sample plate placed at the bottom of the tube to obtain a usable sample.Thus, only 300 – 1000μg sample is used. 4.2.7 Sedimentation separation method Mix the sample with a liquid that will not chemically react with the sample and will not dissolve the sample into a suspension in the container. A sample plate is placed at the bottom ofthe container, and the sample will naturally settle on the sample plate. Samples of different particle sizes will settle at different rates, so particle size separation can be carried out. If the sample is a mixture of different materials, pay attention to the separation caused by the different specific gravity of different 24 materials. In order to do phase identification, it can be used to concentrate low-content phase, which is conducive to its detection. If quantitative analysis is made, the wrong conclusion may be drawn due to the density of different phases and the settling speed. Sedimentation separation is used for small sample size and the sample thickness can be controlled. If the sample size is very small, the diffraction intensity is very low, and the resolution is poor, it is necessary to reduce the scanning speed and extend the scanning time in order to get good testing results. 4.3 Other problems in plate sample preparation The following problems should be noted in the preparation of plate samples. Defects introduced in sample preparation: X-ray diffraction requires a perfect structure of the sample, that is, there should be no diffraction line widening or displacement of various defects, such as stress, dislocation, etc. If the sample is ground, it needs to be annealed appropriately to eliminate or reduce defects. However, if the annealing treatment changes the chemical and physical properties of the sample, the annealing treatment cannot be conducted. Generally phase-identified samples do not require annealing treatment. Thickness of organic sample: The filling depth is to ensure that the thickness of the sample can be met in the whole θ/2θ scanning range, so that the diffraction volume remains unchanged throughout the scanning range. For samples with different X-ray absorption coefficients, different thickness is required. In the equation, ρ is the density of the sample; μm is mass absorption coefficient of the sample to X-ray; γ is the depth of filling required when the incidence angle is θ. For experiments on the same experimental sample, all samples shall have the same filling depth of symmetrical Bragg reflection. Organic compounds are mainly composed of light elements such as C, H, O and N, which absorb very little x ray, so the x ray penetration is deep. In the high angle region, the X-ray penetration depth in the sample can reach about 2mm. Therefore, the glass sample frame with sample groove should not be used for sample preparation, but backpressure method can be used to ensure that the diffraction spectrum will not be affected by the sample frame. In addition, due to the deep penetration of X-ray in the organic sample, the diffraction line signals are not only from the surface of the sample. The diffraction line generated in the deep sample is not focused on the focusing circle, which widens the diffraction peak and reduces the resolution, resulting in inaccurate 2θ measurement. Fillers (such as heavy metal powders that do not produce 25 diffraction peaks at low angles) may be added to the organic sample to reduce the penetration depth of the X-ray in the sample. However, as the number of organic samples involved in diffraction in the sample decreases and the diffraction intensity decreases, the scanning speed needs to be reduced to obtain the high diffraction intensity. Sample treatment subject to oxidative deliquescence:Some samples must be made in a glove box.The general method is to seal the sample surface with scotch tape. The strong diffraction peak of the scotch tape is around 20°. For samples with diffraction range higher than this angle, the scotch tape will not affect the experimental results. If the diffraction range of the sample contains this angle, the diffraction spectrum of a scotch tape (blank sample) can be made, and the experimental spectrum of the sample to be tested can be obtained by subtracting the two. The addition of paraffin oil to the powder sample also acts as a barrier to the air. But it produces an amorphous scattering peak which can be deducted by removing the background. Handling of a small number of samples: The above mentioned processing methods for a small number of samples are too complicated, which is unnecessary if not for quantitative analysis. Generally, only high diffraction intensity and smooth spectral lines are desired.The x ray spot of a general X-ray tube is 1mm X 10mm, and the length perpendicular to the x ray direction is fixed at 10mm when it is projected on the sample surface, while the width parallel to the incident direction decreases with the increase of the diffraction angle. In order to obtain the strength at a high angle, powder samples are generally fixed to the center of the sample tank, and the length perpendicular to the incident direction is 10mm. However, if the purpose of the experiment is for quantitative analysis, this should not be conducted because the intensity ratio of the diffraction peak does not match the standard relative strength I/I0 . Strength correction is necessary for quantitative analysis. Enrichment method of phase to be measured: When the phase content of some objects is small, its diffraction peak intensity is low, the number of diffraction peak is also small, check index and diffraction card, it is difficult to make the accurate judgement. Using their different chemical and physical properties, It is an effective method to carry out phase free analysis accurately by enriching the minerals with less phase content (removing impurities to improve the mass fraction of a certain mineral in the sample) and then measuring the diffraction pattern. 1. Selection method: different minerals have different physical properties, such as appearance, shape and color. With these characteristics, a small number of particles with different appearance, shape and color are selected with tools to enrich a small amount ofminerals. 2. Hydrolysis method:For clay minerals, using its small crystal size and the characteristics ofwater decomposition, put the clay into an ultrasonic oscillator to vibrate to make the kaolinite in the clay become very fine particles. Put the sample into the settling tube, add the right amount of 26 water to let it settle freely, remove the fine slurry regularly. Repeat operations several times to remove most of the kaolinite, while few minerals that are not decomposed by rain and insoluble minerals can be settled. 3. Crushing separation method:In the phase analysis of corundum, due to the low content of impurities and minerals and the uniform dispersion, impurities and corundum are connected with each other, while the hardness of corundum and impurities is quite different. When grinding the samples, the parts with low hardness and defects are easy to crack, so the fine particles contain more impurities and minerals. Put the fine samples into the settling tube for free settlement, and remove the fine slurry regularly. After repeated operations, the fine particles are separated from the impurities and minerals. 4. Calcination method:In the qualitative analysis of the filler of organic abrasives, the filler content is low and it is bonded with resin and abrasives. Put the samples in a muffle furnace for calcining iat 700℃ for 1h. The organic materials are decomposed, burned, oxidized and turned into gas. Only abrams and fillers are left. As their granularity and density are different, further separation makes the filler settled. In practice, appropriate methods should be used to enrich a small amount ofminerals according to the different conditions ofthe samples so as to make accurate phase analysis. 5. Notes for the use of X-ray diffractometer When using new X-ray tubes or the X-ray tube that is down for a long time, the tube should be warmed up. During daily use, the current and voltage of the tube should be increased slowly, and excessive loading should be avoided. Make sure the x ray tube shall work within the permitted load range. After replacing the X-ray tube or focus, make sure whether there is water leaking or not. The window of the X-ray tube is very fragile, no matter in any case, it is forbidden to touch it, otherwise it is easy to cause the vacuum system leak; Do not touch the outer shell of the X-ray tube directly with your hands. If it is dirty or sticky with moisture, gently scrub it with a bleach cloth and dry it before use. It is not allowed to shoot very strong X-ray into the counter for a long time. High-intensity X-ray can damage the counter and shorten its service life. For example, when conducting a small Angle diffraction experiment (The lowest diffraction angle is usually less than 1°), the slit should be set to a minimum to prevent direct light from the X-ray tube from entering the detector directly and damaging the detector. 27 6 Operating conditions XRD is a large precision analytical instrument, according to the relevant standard JB/T9400-2010 X Ray Diffractometer Technical Conditions, the instrument must be operated in the following environment conditions. 1) Ambient temperature: 20±5℃; 2) Relative humidity :30% ~ 80%; 3) Power supply voltage: power supply: three-phase, 380vac, 50hz (if 60hz, please inform the manufacturer), single-phase capacity ≥30a 4) The grounding resistance is not greater than 4 ω; 5) There should be no high frequency and arc interference caused by machine tools, welding machines, high-frequency electric furnaces and other equipment in the power supply line of the diffractometer; 6) Cooling water quality shall meet the requirements of x-ray tube standards; 7) The surrounding environment shall be free from flammable and corrosive gas, dust and vibration. XRD is mainly composed of X-ray generator, Angle measurement system, circulating water cooling system, diffractometer control software and application software. All operations on XRD are conducted by sending corresponding control instructions to the diffractometer control unit through the computer 7 Main technical parameters of XRD Maximum power output: 3kW;Tube voltage: 10 ~ 60kV, tube current: 5 ~ 50mA, tube voltage and current stability: ≤0.005%; Metal ceramic X-ray tube, focus size 1 X 10mm or others; Goniometer structure: θs-θd; diffraction circle radius: 225mm; scanning mode: continuous scanning, step scanning and Omg scanning; 2θ measuring range: -3°—160°; minimum step width angle: 0.0001°, angle reproducibility: 0.0001°; the angle deviation of all peaks within the full spectrum shall not exceed ±0.02 degrees. The energy spectrum resolution of proportional detector is less than 25% (Cu K - ray), and the maximum linear detection rate is greater than 5×105cps. The energy spectral resolution of SDD detector is less than 187eV (Cu K) and the maximum linear detection rate is greater than 15×104cps. Dynamic range of semiconductor linear array detector:1×109 cps ,max range ≥ 9×107 cps, 28 background:≤ 0.1 cps;It has the function of high detection mode and removing fluorescence background mode. 8 XRD control software installation 8.1 Computer system requirements 1. Hardware configuration requirements: I5 processor or above, memory more than 4GB, hard disk not less than 120GB, DVD burn drive, GeForce series video card is recommended. 2. Operating system: the diffractometer control software runs on Wwindows10, 64-bit professional version or above. 3. XRD control software installation environment: the X-ray diffractometer control software needs the support of mathematical model calculation library. Before installing the software, please install the "Anaconda" operating environment correctly in the following order, and then restart the computer. 29 4. Important note : The computer controlling the operation of the diffractometer is not recommended to be connected to the world wide web (Internet);The import and export of 30 diffraction data is recommended to use DVD read-write drive, but not flash drive or other carriers susceptible to virus infection;When the diffractometer is released from the factory, there is a backup of diffractometer control software installation disk, diffractometer data processing software, diffraction data card library, which must be properly kept. 8.2 XRD control software installation The diffractometer control software and the diffraction data processing software of the corresponding version are installed correctly on all the ex-factory series diffractometer before they are released from the factory. The operator can start the corresponding diffractometer control system by double-clicking the software icon on the desktop. If you need to reinstall the diffractometer control software due to a computer operating system crash or control software upgrade for some reason, follow these steps strictly. 1. Insert the backup installation CD of "diffractometer control software" into the CD-ROM drive, and double-click the icon "XRD-Setup" on the control software installation disk, and the system will start to install the software. 2. Click "next" to view the installation agreement, computer user and other items. 3. Click the "next" button to modify the installation directory.Note: the installation system default directory is not recommended. The default directory is C:\ Program Files(x86)\ xxxx,Click the 31 "Change" button to modify the installation directory. It is not recommended to use the system directory in Windows 10 system. The system directory has installation permission, which may cause the software to fail to run normally. Please install the software to the non-system directory. 4. After the modification of installation directory, click "next" and select "installation". 5. Click the "finish" button to complete the installation ofthe control software. 6. After the installation ofthe diffractometer control software, create the shortcut icon on the computer desktop at the same time. 32 8.3 Communication port setting The computer realizes communication with the diffractometer through the network port, so after the installation of the diffractometer control software, the computer network communication port must be modified, the operation is as follows: Windows10 operating system bottom left "start" → Settings (control panel) → network and Internet→ Ethernet (TAB) → change adapter options → Ethernet (right) properties →Internet protocol version 4 (TCP/IPv4). Change the following options to: IP address:192.168.1.17 Subnet mask:255.255.255.0 Default gateway:192.168.1.1 9 Operation procedure 9.1 XRD startup The starting operation shall supply the power to three units, namely the computer, the water cooling device and the main unit ofthe diffractometer. 9.1.1 Water cooling device Power can be turned on by setting the switch on the front panel of the circulating water device to the "run" position. After the circulating water device is started, the "circulating water pressure" indicator is within the range of 0.25-0.3kg/cm2, and the "cooling coal pressure" indicator is within the range of 0.8-1.1mpa. At the same time, the orange indicator light of "water cycle" on the front panel is on, indicating that the circulating water cooling device works normally. If the orange indicator light "water cycle" is not on, indicating that the X-ray tube is blocked, please clean the X-ray tube according to the X-ray tube cleaning instructions. 33 Switch the front panel switch of the circulating water device to the "stop" position to cut off the power supply ofthe circulating water device. 9.1.2 Diffractometer host The power supply of the XRD host is located ON the front panel of the host. Press the green "ON" switch to connect the power supply of the host, and press the red "OFF" switch to cut off the power supply. Please make sure that the "emergency stop" button is under unpressed state before starting up, the water pump has been started normally and the water pipe is not leaking. 9.2 XRD control software startup When the diffractometer control software is installed correctly, create the shortcut key on the desktop. Double-click the shortcut icon to run the diffractometer control softwar. After entering the correct account and password, click the "login" button to start the diffractometer control software. If there is something wrong in the entered account or password, the control software will automatically exit. After the diffractometer control software is reinstalled or the diffractometer factory installation and debugging is completed, the default account is HY (in capital), and the default password is 517. After access to the diffractometer control software system, the user can set their own account and password according to the operation rules described in section 12. Tip: the diffractometer control software supports the English operation interface, the operator can switch according to the need. 34 The above process needs to wait for a period of time.The software takes time to complete the network connection between the computer and the host of the diffractometer, the initialization of the diffractometer system, the fault diagnosis of each component unit, and the calibration of the control parameters. If X-ray diffractometer is equipped with proportional detector or SDD detector, waiting about 10 seconds, if the front detector or semiconductor array detector has to wait about 50 seconds. The following hints may appear after this process: If the diffraction control software finds that the zero deviation values of θs and θd arm recorded by the control software during the calibration of the instrument's control parameters are inconsistent with those recorded in the table of the diffractometer parameters. This prompt might be caused by the following reasons: 1. The diffractometer software is reinstalled or upgraded. The zero deviation values of s and d arms recorded by the control software are not modified to correct values; 35 2. After recalibrating the zero deviation values of the θs and θd arms of the diffractometer, the zero deviation values of the θs and θd arms recorded in the control software are not modified into correct values; 3. During instrument maintenance, the control board of the diffractometer system is replaced, and zero deviation values of θs and θd arms recorded in the table of diffractometer parameters are not modified to correct values; 4. Other unforeseen reasons resulted in the loss of the zero deviation values of s and d arms recorded in the diffractometer parameter table. When the above prompts appear in the running process of control software, attention must be paid. If the reasons for the prompts are not determined, click the "cancel" button to skip them, and then check the specific operation according to 8.3. The access of above interface indicates that the host of the X-ray diffractometer has been initialized and a communication connection has been established for sample measurement. 9.3 Control software initialization After the diffractometer control software is reinstalled or upgraded, the diffractometer control software must be initialized to ensure that the parameters recorded by the control software are consistent with the configuration of the diffractometer host machine. Otherwise the diffractometer will not work properly. When starting the diffractometer control software to enter the sample measurement interface for the first time, press "Ctrl+Alt+D" to enter the initialization interface of the diffractometer control software: 36 Must be modified to match the diffractometer host model. refers to the zero deviation value of the θs and θd. After the Equipment model: AL-27MINI installation, maintenance and recalibration of the diffractometer, the service personnel will keep the TS:-X.XXXX , TD:-Y.YYYY data of TS: -x.xxxx and TD: -y.yyyy to the equipment file record, which must be modified to the correct value, otherwise the measurement data ofthe diffractometer will be completely wrong. The type settings of detector to be used: 1 as proportional detector, 2 as SDD detector, 3 as front detector, and 4 as array detector. CSDT: 1 Set the operating power of the X-ray diffractometer,1=3kW, 2=600W, 3=1.2kW; CuPull down to select the targets being used for X-ray diffraction, including Cu, Fe, Co, etc. POTY: 1 This parameter is only valid for 2800 Series diffractometer. When "CLOSE" is CWTY selected, the value of 2θ Angle of the diffractometer is read from the motor encoder.When "OPEN", GS_Flag CLOSE the diffractometer 2θ Angle value goniometer grating read out. The accuracy ofthe diffractometer 2θ reading from the grating is an order ofmagnitude higher than that from the motor encoder. After the modification of the above parameters, click the save button, and the diffractometer control software will automatically record the corresponding parameters. 9.4 XRD initialization parameters set After the diffractometer control software is normally started, it is necessary to check the recording parameters of the control software In the following cases: 1. Modify the folder storage location of the diffraction data file; 2. Reinstall or upgrade the diffractometer software; 3. After the zero deviation values of θs and θd arm of the diffractometer are recalibrated; 4. When the control panel of the diffractometer system is replaced during instrument maintenance; 37 5. When diffractometer detector type is replaced. Click the "set" button to enter the interface of parameter setting of diffractometer control software and confirm it one by one. Drop down to select the corresponding detector installed on the goniometer, Currently, the diffractometer control software supports four types of detectors: proportional, SDD, Detector type 1 semiconductor array, and linear array detector. Refers to the zero deviation value of the θs and θd arms. After the installation, maintenance and recalibration of the diffractometer, the service personnel will keep the TS:-X.XXXX , TD:-Y.YYYY data of TS: -x.xxxx and TD: -y.yyyy to the equipment files, and the instrument users must keep them properly.When either of these data is found to be inconsistent with the archival value, it must be modified as described in 8.3, otherwise the diffractometer measurements will be completely wrong. The time unit is minutes, indicating how long it will take to turn off the tube voltage and current of the X-ray tube after completing the sample measurement for the High voltage off time(min.)10 diffractometer. The range is 1-60 minutes. An appropriate time can effectively extend the service life of the X-ray tube, with a recommended value of 10 minutes. Linear array detector radius 232 These two parameters are calculated by the diffraction control software when the semiconductor array detector is used. They are only Centering channel 318 , valid for the semiconductor array detector. After the installation, maintenance and recalibration ofthe diffractometer, the service personnel will keep the two data to the equipment file record, and the instrument user must keep them properly. When either of these data is found to be inconsistent with the file value, it must be modified. Otherwise the diffractometer measurements will be completely wrong. □MDITXT format and MDI diffraction data file format are both ASC code files, which can be recognized by general diffractometer processing software JadeX.X, Storage data file format □TXT 38 among which TXT format other diffraction data processing software can be imported LOG Whether LOG When the "yes" selected, the diffractometer control software will record the working state of the diffractometer in real time to provide reference for the fault diagnosis ofthe diffractometer. When the "no" is selected, it will not be recorded. Data save path C\USER\TEST Sample measurement results of the data file, storage location folder name can be modified. Note: After reinstalling the software or upgrading the software, make sure to reset the "data saving path" storage data folder, otherwise the data will not be saved. Setting After the correction of all parameters in the button is completed, click the save button and the diffraction control software will record the modified parameters again. If the parameters ofthe diffractometer control software set are modified to take effect, the following operations shall be performed: Control software: click the " ×" button in the upper right corner to close the software, it will prompt whether to close the software, and click "ok" to close the software. Main unit power: the red (OFF) button on the main unit panel. Repeat operations 9.1 and 9.2, restart the diffractometer control software, and the parameter modification ofthe diffractometer control software will take effect 10 Sample measurement The control and parameter setting of the diffractometer are all based on the computer sending corresponding instructions to the host of the diffractometer, and the control unit of the host computer will complete the corresponding action control and data measurement, and send the measurement results back to the computer, forming a complete diffraction data file stored in the designated location of the computer's hard disk. According to the analysis purpose, the diffraction data processing software is used to process the measured data. 39 When X-ray diffractometer is not equipped with other measurement accessories, there are basically three measurement methods for sample measurement, which are as follows: Button (regular θ-2θ measurement): for qualitative and quantitative analysis, cell parameters and grain size measurement, full-spectrum fitting of refined crystal defects, et; Measurement The button is used to study the structural state of thin films and coated materials. In order to make "grazing" measurement, the incident light source must be ensured to be Gazing measurement parallel light. Otherwise, it is meaningless to choose this measurement method. Make sure that the incident light source is parallel light, the diffractometer must be equipped with parallel light sorra slit or Gobel mirror. Button swing measurement: to evaluate the crystal state of single crystal sample, thin film and coated sample (half peak width of diffraction peak). OMG 10.1 Measurement(Regular θ-2θ measurement) Instrument conditions: divergent slit 1°, scattering slit 1°, receiving slit 0.3mm or 0.2mm; Sample preparation: the quality of sample preparation has a crucial impact on the accuracy of measurement results. Insert the prepared diffraction samples to be measured into the sample table of the diffractometer goniometer according to the description of 3 and close the lead door. MeasurementThe operation interface is divided into three separate sections which are Measurement parameter setting area①, plotting area②, prompt area③. Measurement parameter setting area① Sample name TEST, Sample No. 1,After the sample measurement is completed, the diffractometer control software will form the name of the diffraction data file according to the following rules and store it in the folder set in section 8.3. Sample name # sample number # end time of measurement _ detector code.MDI (TXT) 40 The "detector code" is automatically generated by the control software according to the detector type used in the sample measurement, including 100 proportional detector, 200SDD detector and 300 semiconductor linear array detector. The above information will generate wo format diffraction data files as below: TEST#1#20200202- 135711_100.MDI TEST#1#20200202- 135711_100.TXT The diffraction data file name contains the end time of measurement, so even if the sample name + sample number is the same, the diffraction data file name will not be the same, so there is no need to worry about the loss ofthe diffraction data file. Only 30 English characters, Numbers and English underscores are allowed in TEST the sample name Sample name No.and 1 sample number. Chinese characters are also allowed, but not , Sample recommended, otherwise the diffraction data file will be lost. Refers to the 2θ Angle, the range 0°- 160°, stop angle - start angle represents measurement range, the "stop Angle value" must be greater than the "start Start anglethe 20 ,sample End angle 150 Angle value", otherwise an error will occur. Each step Angle measures time in seconds.Ranges from 0.1 to 10, with recommended values Measuring time 0.1of 0.5, 1, 2, and 3. The Angle of each rotation of θs and θd arm, Unit °, Range: 0.01-0.05°, recommended value:0.02 0.02. Step width angle sample measurement operation power of XRD, "tube voltage" range is 10-60kv, recommended value of 40 kV;"Tube current" 5mA--50mA, with a recommended Tube voltage 40 , tube current 40 value of 40mA; The product ofthe two representations is the operating power. After the measurement parameters are set, click the "start" button, and the diffractometer will start the sample measurement until the measurement is completed, and the complete diffraction data file will be stored in the specified folder. 41 During the sample measurement, you can click the "stop" button at any time to finish the current measurement. Plotting area It is used to display the information of sample measurement in real time. The X coordinate is the diffraction Angle value of 2, and the Y ordinate is the diffraction intensity value (CPS). Prompt area Display the error message during the setting of measurement parameters and the error message during the operation ofthe instrument. See all the prompt messages as follows: **C01 Command Error **C02 Out Of Range **C03 Wrong Parameter **C04 CPU Internal Error CPU works abnormally **C05 Door Error **C07 Water Error **C08 Power Failure **C09 Power Timeout **C10 TS Goniometer Down Limit **C11 TD Goniometer Down Limit **C12 TS Goniometer Up Limit **C13 TD Goniometer Up Limit **C14 Parameter error 42 10.2 Grazing measurement Instrument conditions: incident is parallel light, divergent slit 1/2° (or less), scattering slit 1°, receiving slit 0.3mm or 0.2mm. The incident light source is parallel light, which can be realized by the following two methods: Parallel light Soller slit: Compared with the sample, the conventional Soller slit is perpendicular to the sample surface, and the divergence ofthe slit is about 3°.The parallel light sola slit is parallel to the sample surface, and the divergence ofthe slit is less than 1°. The following images are the Soller slit and parallel light sola slit modules. 。 Regular Soller slit Parallel light Soller slit See the parallel light Soller slit replacement as shown below. Loosen the two fixing screws for the conventional cable slit and remove the cable slit. Install the parallel light Soller slit to the corresponding position and tighten the two fixing screws. The incident parallel light generated by the Soller slit has a large divergence, so it can only be used to analyze the structure of thicker films and coated samples, while the diffraction data can not be used to further explain other characteristics of the film. In the case of grazing scanning using parallel light generated by parallel light Soller slit, it is recommended to replace divergent slit DS with RS 0.1mm. Otherwise the slit widens and the parallel light diverges more. 43 Gobel mirror (multilayer reflector): the best method to obtain the parallel light is to use Gobel mirror (multilayer reflector). The divergence of the incoming parallel light is less than 0.1°. As shown in the figure below, the debugged multi-layer film emission key is installed in the metal cavity, and the Gobel mirror module permits plug and play. Regular Soller slit Gobel mirror (multilayer reflector) See the replacement of the Gobel mirror (multi-layer reflector) as follows: First loosen the conventional Soller slit screw and push right to remove it. Then push the Gobel mirror (multilayer reflector) to the calibration position to the left and tighten the set screw. The incident parallel light generated by Gobel has a small divergence, which can be used to analyze the structure of various films and coated samples, and the measured diffraction data can be used to further explain other characteristics of the film. In order to make the further study on the 44 structure of the film and the coated sample (orientation, stress, layer spacing, etc.), the diffractometer should be equipped with a film acessory or a multi-functional sample rack. Grazing measurement parameter setting Sample name TEST, Sample No. 1,After the sample measurement is completed, the diffractometer control software will form the name of the diffraction data file according to the following rules and store it in the folder set in section 8.3. Sample name # sample number # end time of measurement _ detector code.MDI (TXT) The "detector code" is automatically generated by the control software according to the detector type used in the sample measurement, including 100 proportional detector, 200SDD detector and 300 semiconductor linear array detector. The above information will generate wo format diffraction data files as below: TEST#1#20200202- 135711_100.MDI TEST#1#20200202- 135711_100.TXT The diffraction data file name contains the end time of measurement, so even if the sample name + sample number is the same, the diffraction data file name will not be the same, so there is no need to worry about the loss ofthe diffraction data file. Only 30 English characters, Numbers and English underscores are allowed in the sample name and sample number. Chinese characters are also allowed, but not Sample name TEST , Sample No. 1 recommended, otherwise the diffraction data file will be lost. Refers to the θd arm Angle, the range 0°-80 °stop angle - start angle represents the sample measurement range, the "stop Angle value" must be greater than the "start Start angle 20 , End angle 70 Angle value", otherwise an error will occur. Each step Angle measures time in seconds.Ranges from 0.1 to 10, with recommended values of 0.5, 1, 2, and 3. Measuring time 0.1 The Angle of each rotation of θd arm, Unit °, Range: 0.01-0.05°, recommended value: 0.02. Step width angle 0.02 sample measurement operation power of XRD, "tube voltage" range is 10-60kv, recommended value of 40 kV;"Tube current" 5mA--50mA, with a recommended Tube voltage 40 , tube current 40 value of 40mA; The product ofthe two representations is the operating power. Grazing angle 1 θs incidence angle of goniometer, selection range0-5°. It is related to the thickness of film and coated sample. The thinner the film is, the smaller the incidence Angle should be. Generally, the grazing Angle should not be more than 1°。 After the measurement parameters are set, click the "start" button, and the diffractometer will start the sample measurement until the measurement is completed, and the complete diffraction data 45 file will be stored in the specified folder. During the sample measurement, you can click the "stop" button at any time to finish the current measurement. 10.3 OMG (swing) measurement Instrument conditions: divergent slit 1/2° (or less), scattering slit 1°, receiving slit 0.3mm or 0.2mm. Omg Measurement parameter setting 1 , After the sample measurement is completed, the diffractometer control software will form the name of the diffraction data file according to the Sample name TEST Sample No. following rules and store, it in the folder set in section 8.3. Sample name # sample number # end time of measurement _ detector code.MDI (TXT) The "detector code" is automatically generated by the control software according to the detector type used in the sample measurement, including 100 proportional detector, 200SDD detector and 300 semiconductor linear array detector. The above information will generate wo format diffraction data files as below : TEST#1#20200202- 135711_100.MDI TEST#1#20200202- 135711_100.TXT The diffraction data file name contains the end time of measurement, so even if the sample name + sample number is the same, the diffraction data file name will not be the same, so there is no need to worry about the loss ofthe diffraction data file. Only 30 English characters, Numbers and English underscores are allowed in the sample name and sample number. Chinese characters are also allowed, but not Sample name TEST , Sample No. 1 46 recommended, otherwise the diffraction data file will be lost. 2θof diffraction surface to be measured, theoretical range 0- 160°. Diffraction plane 2θ Angle measurement width, theoretical range 0-160°, but OMG angle 28 not to 0. Measuring range 5 When making Omg (swing) measurements, the Omg and the measurement range parameters should satisfy the following relationships. 1. Omg angle: (Measuring range +(Omg measured angle value÷2))<80°; 2. Omg angle:((Omg measured angle value÷2)- Measuring range)>0°。 Each step Angle measures time in seconds.Ranges from 0.1 to 10, with recommended values of 0.5, 1, 2, and 3. Measuring time 0.1 The Angle of each rotation of θd arm, Unit °, Range: 0.01-0.05°, recommended value: 0.02. Step width angle 0.02 sample measurement operation power of XRD, "tube voltage" range is 10-60kv, recommended value of 40 kV;"Tube current" 5mA--50mA, with a recommended Tube voltage 40 , tube current 40 value of 40mA; The product ofthe two representations is the operating power. After the measurement parameters are set, click the "start" button, and the diffractometer will start the sample measurement until the measurement is completed, and the complete diffraction data file will be stored in the specified folder. During the sample measurement, you can click the "stop" button at any time to finish the current measurement. 47 11 Command control After starting the diffractometer control software, initializing the diffractometer system, fault diagnosis of each component unit, and calibrating the control parameters, the control software gets access to the "command control" state after entering the diffraction data measurement interface and pressing the key (Ctrl+Alt+S) at the same time. The diffractometer control unit receives instructions from the control computer and controls the main unit ofthe diffractometer to complete the corresponding command actions. The command control interface includes the command input area and the information display area. The command input area is used to fill in the control command to send to the diffractometer, and the information area is used to display the information returned by the diffractometer. After access to the command control interface, first send a return key to the host of the diffractometer. After the initialization of the control system, the online operation of the computer and the diffractometer will be completed. When the "XRD>" prompt is displayed in the information display area, the control command ofthe diffractometer can be entered. 11.1 Control command list CSANxxx.xx Turn the goniometer 2θ to the specified position CSTHxx.xx Rotate θs arm to the specified position CSTTxxx Rotate θd arm to the specified position CINTxx.xx Set measurement time CSTPx.xxxx Step width angle xxx.xx range 0- 160° xx.xx range 0-80° xx.xx range 0-80° xx.xx range 0.1- 10S 0.0x range 0.0002- 1° CSPESxxx Continuous scanning speed 连续扫描测量速度(°/S) CSPEMxxx CMODx Continuous scanning speed (°/min) Set the operating mode ofthe goniometer,CMOD1θs arm single-action, 48 CMOD2θd arm single-action, CMOD3θs and θd arm linkage CPAR View the diffractometer control parameters table CLWLxx Set the down limit ofthe single-channel amplifier CUPLxx Set upr limit of single-channel amplifier xx range 0-99 CMXSx.xxx Set the step width Angle using CMAX x.xxx range 0.001-9.999° CMXNxx Set the CMAX command to measure points xx range 1-99 CMXTxx.x Set the CMAX command to measure the time xx.x range 0.1-99.9 CMAX Take the current 2θ as the center, take CMXSx.xxx as the step width Angle, xx range 0-99 CMXNxx as the measurement points, and CMXTxx.x as the measurement time, to find the maximum counting intensity. CMESxxx: Take CINTxx.xx as the measured time to record strength value CDPLX:Output the current 2θ value and the intensity value with CINTxx.xx as measured time CDPLG: Output the current θd value and the intensity value with CINTxx.xx as measured time CDPLT: Output the current θs value and the intensity value with CINTxx.xx as measured time CSSCxxx.xx Based on the current stop position of the goniometer, take CINTxx.xx as the measurement time, CSTP0.0x as the step width Angle, CMODx as driving mode, and yyy.yy as the measurement range for the step measurement. CCTHxx.xx corrects the current θs arm Angle to xx.xx° CCTTxx.xx corrects the current θd arm Angle to xx.xx° CSHO CSHC Turn on the shutter. Turn offthe shutter C/ : pause the command.(pause the current action); C// : reset command. CRST Turn the goniometer to the zero position CWHO check the online status of slave; CWTCS Use the starting channel of the effective channel of array detector Use the end channel of the effective channel of array detector CWTCF CSDT : set detector type, 1 is proportional detector, 2 is SDD detector, 3 is linear array detector; CWPA initializes parameter list CWTY Enter the target material type POTY Set the operating power of the diffractometer, 1 for 3kW and 2 for 600W SKMxx yy Raise tube voltage to xx kV, and the tube current to yy mA RKM Read the current tube voltage, tube current value 49 12 Changing user name and password Start the diffractometer control software. When getting access to the sample measurement interface, press "Ctrl+Alt+L" to enter the user name and password setting interface. User name and password stipulate that the user has the right to modify the control parameters of the diffractometer, and only the "UserRights" right can modify the measurement parameters.The diffractometer control software can set up at most three levels of permission password, each password has specified operation permission. User name, name characters must meet the requirements of Windows 10 system, allow English, Numbers and underscore 10 characters. UserName User password with a maximum of 10 digits and English characters Password There are three options for user permission Settings, namely: Super administrator, can use all software functions, including foreground parameter UserRights modification and background instruction setting. SuperAdmin Administrator, can set the measurement parameters, set the measurement method, query the measurement record and other information. Admin The sample can only be measured according to the measurement parameters and methods set by the higher authority. User 12.1 Adding user and password Get access to the user name and password setting interface, enter the edit box, click the right mouse button, you can edit. Fill in UserName and Password respectively, and select "UserRights" to complete the operation of adding users. 12.2 Changing user name and password Double-click on the "UserName" and "Password" positions to change the UserName and 50 Password. 12.3 Deleting user name and password Double-click the corresponding "UserName" and "Password" positions, and then press the "Delete" button in the corresponding row to Delete the user and Password. 13 Turn-off the X-ray diffractometer 1. Control software: click the " ×" button in the upper right corner to close the software, which will prompt whether to close it or not. Click "ok" to close the software. 2. Main unit power: red (OFF) button on the main unit panel 3. Cooling water device: rotate the knob switch ofthe water circulation device to the OFF position. 14 Possible problems during control software running Possible reasons for the following information prompt when running the diffractometer control software are as follows: 1. There is no network cable connection between the computer and the host ofthe diffractometer; 2. The main power ofthe diffractometer is not turned on; 3. Whether the computer port is set correctly, the host ofthe diffractometer and the computer are not in the same IP network segment; 51 4. Select the array detector in the software configuration parameters, but actually it uses other types of detectors; 5. Other fault causes may also lead to the failure of network communication between the computer and the diffraction host. After the measurement, the data file cannot be found: after the valid "sample name" and "sample number" are filled in before the sample measurement, the control software will automatically generate the data file name at the end of the sample measurement. Save the data file to the "Settings" → "data save path" folder, so you can see the location of the measurement data file in the "Settings" button. Data save path C\USER\TEST Note: after reinstalling the software or upgrading the software, be sure to reset the "data saving path" storage data folder, otherwise the data will not be saved. The test report cannot be saved correctly: the required font library is missing in the computer operating system, and the randomly configured installation disk has the font library required by "STSONG-TTF" software, which can be solved by reinstalling. Calculation function cannot be calculated correctly or the results cannot be displayed: the computer system lacks an "Anaconda" operating environment. Please reinstall the operating environment as described in section 7.1. 15 X-ray detector replacement method 15.1 Description of the performance of various detectors The diffractor control software supports 4 detectors to collect diffraction data, namely: closed proportional detector + graphite monochromator, silicon drift SDD detector, semiconductor linear array detector and semiconductor array detector. Closed proportional detector + graphite monochromator: good quality of testing data and the resolution of low Angle is strong. When the slit conditions are DS: RS 0.1, SS 1° and RS 0.3, the measurement of 2θ can start from 0.3°, and the spectrum plot structure refinement is required. Silicon drift SDD detector: The measured diffraction data are of good quality and the resolution of low Angle is strong. When the slit conditions are DS: RS 0.1, SS 1° and RS 0.3, the measurement of 2θAngle can start from 0.3°, especially for the samples containing Fe, Co and Ni elements, the fluorescence effect can be effectively removed, the spectrum plot quality is the best, and the plot structure refinement is required. The speed of sample measurement is more than 3 times higher than that of closed proportional detector and monochromator. 52 Semiconductor linear array detector: the sample measurement speed is fast, more than 30 times higher than closed proportional detector + monochromator.Due to its low energy fraction, it is not suitable for low Angle measurement.The quality of spectrum plot completely meets the general requirements of qualitative and quantitative analysis. Semiconductor array detector: the sample measurement speed is fast, more than 50 times higher than closed proportional detector + monochromator. Due to its low energy fraction, it is not suitable for low Angle measurement.The quality of spectrum plot completely meets the general requirements of qualitative and quantitative analysis. 15.2 X-ray detector replacement All diffractometer detectors are equipped with fixed seats when they are released from the factory or when they are upgraded, and the corresponding setting parameters of the optical path of the diffractometer are recorded when they are released from the factory. The operator can replace the detector by loosening the fixing screw of the detector and removing and assembling the selected detector along the dovetail direction. The detector is replaced by "plug and play" without any hardware adjustments. The following describes the operation process of replacing "closed proportional detector + monochromator" with "semiconductor linear array detector. 1. Turn off the main unit power. 2. Loosen the sealing proportional detector + monochromator fastening screw and pull it down to the right along the dovetail direction.The wire-array semiconductor detector to be replaced is pushed flat to the left in the dovetail direction to the indicated position. 3. Install the anti-scattering ray screen on the powder sample table (The gap between the screen and the diffraction surface of the sample has been fixed when it is released from the factory, so it should not be adjusted generally). 53 4. Replace the anti-scattering slit SS position with a randomly configured Ni filter (for Cu target), and remove the receiving slit RS. If you want the diffraction peak to be at a higher resolution, change the DS position ofthe divergent slit to 1/2°. Turn on the diffractometer to start the control software is started. button, select " line array detector" After selecting the "set" in the parameter item "Detector type". Modify “Centering channel 318” and “line array detector radius 232” to the recorded parameter values at the time of delivery. 5. Turn off the diffractometer control software and the power supply of the host. Turn on the power supply of the host again after a few seconds, start the diffractometer control software, and replace the detector. 15.3 X-ray detector replacement precautions 1. The main unit power of the diffractometer must be off during detector replacement. 2. After the detector is replaced, the power cable and signal cable connected with the detector shall not be disassembled and shall be properly placed in a position that does not affect the operation ofthe instrument. 3. After the detector is replaced, Make sure to check whether the slots at DS, SS and RS positions are correct. 16 Other applications of diffractometer In addition to conventional scanning measurement, diffractometer can be configured with various functional accessories to achieve special purpose measurement, further study of material structure, and broaden the application field of diffractometer. The main functional accessories ofthe diffractometer are as follows: 1) LTK-450 variable temperature accessory Diffractometer low temperature accessory is used to study the phase transition of crystal structure at low temperature. Adopt liquid nitrogen 54 refrigeration, add heat through PID control, heat the sample table to make the sample in the box to be stable at the set temperature. 2) HTK-1600 High temperature accessory The high temperature accessory of diffractometer is used to study the phase transition of crystal structure at high temperature.Pt plate is used for heating, adding heat through PID control, so that the sample box in the sample chamber is stable at the set temperature. 3) DCX-6 Sample changer Programming control, each boot can continuously test a number of samples, automatically saved into data files, reduce the labor intensity ofthe operator. 4) DWZYB-2 Multi-function sample rack:For sheet, block and film analysis; By reflection method, transmission method, simultaneous pour method, round casting method and sample rotation method, the tests such as pole diagram(Inverse pole diagram, ODF diagram), stress(ψ scanning), PHi scanning (film internal structure measurement) and texture orientation quantitative analysis are carried out。 16.1 Automatic identification on function accessories There are mounting seats for all kinds of functional accessories for diffraction. The diffractometer goniometer is mounted with a fixed seat and there are two positioning guide blocks on the fixed seat. The mounting seats for all kinds of functional accessories are located by the positioning guide block and installed on the fixed seat of the goniometer. The installation accuracy is less than 2µmm to meet the sample measurement requirements. Even if the functional accessories and the powder sample table are changed repeatedly, the optical system does not need to be corrected, and the plug and play is realized, which is convenient for operators to use. The goniometer is equipped with a corresponding coding mechanism between the fixed seat and the installation seat of the functional accessories. The diffractometer control software will automatically read the codes of various functional accessories and transfer them to the measurement 55 module of the corresponding functional accessories to realize automatic control of the functional accessories and sample measurement. 16.2 Six-sample changer The sample changer is for continuous measurement of powder samples. The installation mode is the same as other functional accessories. The diffraction control software can automatically identify the sample changer, plug and play, without adjusting the optical system. After installing the six sample changer on the diffractometer, the diffractometer control software will enter the following interface: After filling in the control parameters of the diffractometer correctly, click the "start" button, and the control software will control the diffractometer to measure the samples at each position according to the order of sample changer parameters. After the measurement of each location sample, the diffraction data file will be created according to the following rules and stored in the specified folder. 56 Sample name # sample number # commutator sample location # end time of measurement _ detector code. The above information will generate:TEST#1#6#20200202- 135711_100.MDI TEST#1#6#20200202- 135711_100.TXT The diffractometer control parameters are the same as described in the sample measurement. The changer parameters can be entered sequentially, such as 1,2,3,4,5,6, separated by ", ". It can also be filled out out of order, such as "4,3,1,2", the software automatically starts the measurement with 4→3→1→2 measurement sequence. 57 Drawell International Technology Limited Chongqing Drawell Instrument CO,.Ltd Add:Suite 2705,Building No.12,Shiyou Road No.1,Yuzhong District, Chongqing,China Tel: 0086-023-63268643 Shanghai Drawell Scientific Instrument Co.,Ltd Add : Suite 1117,Lane561 XiuChuan Rd.,PuDong New Area,Shanghai,China Web : www.drawell.com.cn Email : [email protected]
advertisement
Related manuals
advertisement