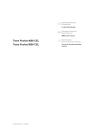
Werbung
▼
Scroll to page 2
of
163
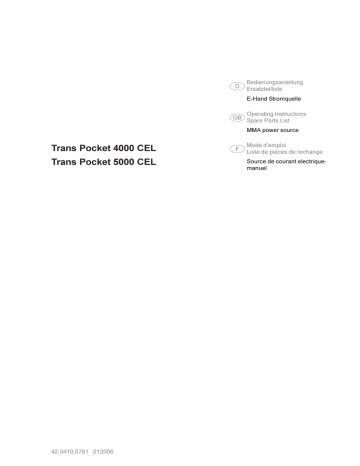
D Bedienungsanleitung Ersatzteilliste E-Hand Stromquelle GB Trans Pocket 4000 CEL Trans Pocket 5000 CEL 42,0410,0781 012006 F Sehr geehrter Leser Einleitung Wir danken Ihnen für Ihr entgegengebrachtes Vertrauen und gratulieren Ihnen zu Ihrem technisch hochwertigen Fronius Produkt. Die vorliegende Anleitung hilft Ihnen, sich mit diesem vertraut zu machen. Indem Sie die Anleitung sorgfältig lesen, lernen Sie die vielfältigen Möglichkeiten Ihres Fronius-Produktes kennen. Nur so können Sie seine Vorteile bestmöglich nutzen. Bitte beachten Sie auch die Sicherheitsvorschriften und sorgen Sie so für mehr Sicherheit am Einsatzort des Produktes. Sorgfältiger Umgang mit Ihrem Produkt unterstützt dessen langlebige Qualität und Zuverlässigkeit. Das sind wesentliche Voraussetzungen für hervorragende Ergebnisse. ud_fr_st_et_00491 012004 Sicherheitsvorschriften GEFAHR! WARNUNG! VORSICHT! „GEFAHR!“ Bezeichnet eine unmittelbar drohende Gefahr. Wenn sie nicht gemieden wird, sind Tod oder schwerste Verletzungen die Folge. „WARNUNG!“ Bezeichnet eine möglicherweise gefährliche Situation. Wenn sie nicht gemieden wird, können Tod und schwerste Verletzungen die Folge sein. „VORSICHT!“ Bezeichnet eine möglicherweise schädliche Situation. Wenn sie nicht gemieden wird, können leichte oder geringfügige Verletzungen sowie Sachschäden die Folge sein. HINWEIS! „HINWEIS!“ bezeichnet die Gefahr beeinträchtigter Arbeitsergebnisse und möglicher Schäden an der Ausrüstung. Wichtig! „Wichtig!“ bezeichnet Anwendungstipps und andere besonders nützliche Informationen. Es ist kein Signalwort für eine schädliche oder gefährliche Situation. Wenn Sie eines der im Kapitel „Sicherheitsvorschriften“ abgebildeten Symbole sehen, ist erhöhte Achtsamkeit erforderlich. Allgemeines Das Gerät ist nach dem Stand der Technik und den anerkannten sicherheitstechnischen Regeln gefertigt. Dennoch drohen bei Fehlbedienung oder Missbrauch Gefahr für - Leib und Leben des Bedieners oder Dritte, - das Gerät und andere Sachwerte des Betreibers, - die effiziente Arbeit mit dem Gerät. Alle Personen, die mit der Inbetriebnahme, Bedienung, Wartung und Instandhaltung des Gerätes zu tun haben, müssen - entsprechend qualifiziert sein, - Kenntnisse vom Schweißen haben und - diese Bedienungsanleitung vollständig lesen und genau befolgen. Die Bedienungsanleitung ist ständig am Einsatzort des Gerätes aufzubewahren. Ergänzend zur Bedienungsanleitung sind die allgemein gültigen sowie die örtlichen Regeln zu Unfallverhütung und Umweltschutz bereitzustellen und zu beachten. Alle Sicherheits- und Gefahrenhinweise am Gerät - in lesbarem Zustand halten - nicht beschädigen - nicht entfernen - nicht abdecken, überkleben oder übermalen. Die Positionen der Sicherheits- und Gefahrenhinweise am Gerät, entnehmen Sie dem Kapitel „Allgemeines“ der Bedienungsanleitung Ihres Gerätes. I ud_fr_st_sv_00466 012007 Allgemeines (Fortsetzung) Störungen, die die Sicherheit beeinträchtigen können, vor dem Einschalten des Gerätes beseitigen. Es geht um Ihre Sicherheit! Bestimmungsgemäße Verwendung Das Gerät ist ausschließlich für Arbeiten im Sinne der bestimmungsgemäßen Verwendung zu benutzen. Das Gerät ist ausschließlich für die am Leistungsschild angegebenen Schweißverfahren bestimmt. Eine andere oder darüber hinaus gehende Benutzung gilt als nicht bestimmungsgemäß. Für hieraus entstandene Schäden haftet der Hersteller nicht. Zur bestimmungsgemäßen Verwendung gehört auch - das vollständige Lesen und Befolgen aller Hinweise aus der Bedienungsanleitung - das vollständige Lesen und Befolgen aller Sicherheits- und Gefahrenhinweise - die Einhaltung der Inspektions- und Wartungsarbeiten. Das Gerät niemals für folgende Anwendungen verwenden: - Auftauen von Rohren - Laden von Batterien/Akkumulatoren - Start von Motoren Das Gerät ist für den Betrieb in Industrie und Gewerbe ausgelegt. Für Schäden, die auf den Einsatz im Wohnbereich zurückzuführen sind, haftet der Hersteller nicht. Für mangelhafte oder fehlerhafte Arbeitsergebnisse übernimmt der Hersteller ebenfalls keine Haftung. Umgebungsbedingungen Betrieb oder Lagerung des Gerätes außerhalb des angegebenen Bereiches gilt als nicht bestimmungsgemäß. Für hieraus entstandene Schäden haftet der Hersteller nicht. Temperaturbereich der Umgebungsluft: - beim Betrieb: -10 °C bis + 40 °C (14 °F bis 104 °F) - bei Transport und Lagerung: - 25 °C bis + 55 °C (-13 °F bis 131 °F) Relative Luftfeuchtigkeit: - bis 50 % bei 40 °C (104 °F) - bis 90 % bei 20 °C (68 °F) Umgebungsluft: frei von Staub, Säuren, korrosiven Gasen oder Substanzen, usw. Höhenlage über dem Meeresspiegel: bis 2000 m (6500 ft) ud_fr_st_sv_00466 012007 II Verpflichtungen des Betreibers Der Betreiber verpflichtet sich, nur Personen am Gerät arbeiten zu lassen, die - mit den grundlegenden Vorschriften über Arbeitssicherheit und Unfallverhütung vertraut und in die Handhabung des Gerätes eingewiesen sind - das Kapitel „Sicherheitsvorschriften“ und die Warnhinweise in dieser Bedienungsanleitung gelesen, verstanden und durch ihre Unterschrift bestätigt haben - entsprechend den Anforderungen an die Arbeitsergebnisse ausgebildet sind. Das sicherheitsbewusste Arbeiten des Personals ist in regelmäßigen Abständen zu überprüfen. Verpflichtungen des Personals Alle Personen, die mit Arbeiten am Gerät beauftragt sind, verpflichten sich, vor Arbeitsbeginn - die grundlegenden Vorschriften über Arbeitssicherheit und Unfallverhütung zu befolgen - das Kapitel „Sicherheitsvorschriften“ und die Warnhinweise in dieser Bedienungsanleitung zu lesen und durch ihre Unterschrift zu bestätigen, dass sie diese verstanden haben und befolgen werden. Vor Verlassen des Arbeitsplatzes sicherstellen, dass auch in Abwesenheit keine Personen- oder Sachschäden auftreten können. Selbst- und Personenschutz Beim Schweißen setzen Sie sich zahlreichen Gefahren aus, wie z.B.: - Funkenflug, umherumfliegende heiße Metallteile - augen- und hautschädigende Lichtbogen-Strahlung - schädliche elektromagnetische Felder, die für Träger von Herzschrittmachern Lebensgefahr bedeuten - elektrische Gefährdung durch Netz- und Schweißstrom - erhöhte Lärmbelastung - schädlichen Schweißrauch und Gase Personen, die während des Schweißvorganges am Werkstück arbeiten, müssen geeignete Schutzkleidung mit folgenden Eigenschaften verwenden: - schwer entflammbar - isolierend und trocken - den ganzen Körper bedeckend, unbeschädigt und in gutem Zustand - Schutzhelm - stulpenlose Hose III ud_fr_st_sv_00466 012007 Selbst- und Personenschutz (Fortsetzung) Zur Schutzbekleidung zählt unter anderem: - Augen und Gesicht durch Schutzschild mit vorschriftsgemäßem FilterEinsatz vor UV-Strahlen, Hitze und Funkenflug schützen. Hinter dem Schutzschild eine vorschriftsgemäße Schutzbrille mit Seitenschutz tragen. Festes, auch bei Nässe isolierendes Schuhwerk tragen Hände durch geeignete Handschuhe schützen (elektrisch isolierend, Hitzeschutz). Zur Verringerung der Lärmbelastung und zum Schutz vor Verletzungen Gehörschutz tragen. Personen, vor allem Kinder, während des Betriebes von den Geräten und dem Schweißprozess fernhalten. Befinden sich dennoch Personen in der Nähe - diese über alle Gefahren (Blendgefahr durch Lichtbogen, Verletzungsgefahr durch Funkenflug, gesundheitsschädlicher Schweißrauch, Lärmbelastung, mögliche Gefährdung durch Netz- oder Schweißstrom, ...) unterrichten, - geeignete Schutzmittel zur Verfügung stellen oder - geeignete Schutzwände und -Vorhänge aufbauen. Gefahr durch schädliche Gase und Dämpfe Beim Schweißen entstehender Rauch enthält gesundheitsschädliche Gase und Dämpfe. Schweißrauch enthält Substanzen, die unter Umständen Geburtsschäden und Krebs verursachen können. Kopf von entstehendem Schweißrauch und Gasen fernhalten. Entstehenden Rauch sowie schädliche Gase - nicht einatmen - durch geeignete Mittel aus dem Arbeitsbereich absaugen. Für ausreichend Frischluft-Zufuhr sorgen. Bei nicht ausreichender Belüftung Atem-Schutzmaske mit Luftzufuhr verwenden. Besteht Unklarheit darüber, ob die Absaugleistung ausreicht, die gemessenen Schadstoff-Emissionswerte mit den zulässigen Grenzwerten vergleichen. Folgende Komponenten sind unter anderem für den Grad der Schädlichkeit des Schweißrauches verantwortlich: - Für das Werkstück eingesetzte Metalle - Elektroden - Beschichtungen - Reiniger, Entfetter und dergleichen Daher die entsprechenden Materialsicherheits-Datenblätter und Herstellerangaben zu den aufgezählten Komponenten berücksichtigen. Entzündliche Dämpfe (z.B. Lösungsmittel-Dämpfe) vom Strahlungsbereich des Lichtbogens fernhalten. ud_fr_st_sv_00466 012007 IV Gefahr durch Funkenflug Funkenflug kann Brände und Explosionen auslösen. Niemals in der Nähe brennbarer Materialien schweißen. Brennbare Materialien müssen mindestens 11 Meter (35 ft.) vom Lichtbogen entfernt sein oder mit einer geprüften Abdeckung zugedeckt werden. Geeigneten, geprüften Feuerlöscher bereithalten. Funken und heiße Metallteile können auch durch kleine Ritzen und Öffnungen in umliegende Bereiche gelangen. Entsprechende Maßnahmen ergreifen, dass dennoch keine Verletzungs- und Brandgefahr besteht. Nicht in feuer- und explosionsgefährdeten Bereichen und an geschlossenen Tanks, Fässern oder Rohren schweißen, wenn diese nicht gemäß den entsprechenden nationalen und internationalen Normen vorbereitet sind. An Behältern in denen Gase, Treibstoffe, Mineralöle und dgl. gelagert sind/ waren, darf nicht geschweißt werden. Durch Rückstände besteht Explosionsgefahr. Gefahren durch Netz- und Schweißstrom Ein elektrischer Schlag ist grundsätzlich lebensgefährlich und kann tödlich sein. Spannungsführende Teile innerhalb und außerhalb des Gerätes nicht berühren. Beim MIG/MAG- und WIG-Schweißen sind auch der Schweißdraht, die Drahtspule, die Antriebsrollen sowie alle Metallteile, die mit dem Schweißdraht in Verbindung stehen, spannungsführend. Den Drahtvorschub immer auf einem ausreichend isolierten Untergrund aufstellen oder eine geeignete, isolierende Drahtvorschub-Aufnahme verwenden. Für geeigneten Selbst- und Personenschutz durch gegenüber dem Erd- oder Massepotential ausreichend isolierende, trockene Unterlage oder Abdeckung sorgen. Die Unterlage oder Abdeckung muss den gesamten Bereich zwischen Körper und Erd- oder Massepotential vollständig abdecken. Sämtliche Kabel und Leitungen müssen fest, unbeschädigt, isoliert und ausreichend dimensioniert sein. Lose Verbindungen, angeschmorte, beschädigte oder unterdimensionierte Kabel und Leitungen sofort erneuern. Kabel oder Leitungen weder um den Körper noch um Körperteile schlingen. Die Schweiß-Elektrode (Stabelektrode, Wolframelektrode, Schweißdraht, ...) - niemals zur Kühlung in Flüssigkeiten eintauchen - niemals bei eingeschalteter Stromquelle berühren. Zwischen den Schweiß-Elektroden zweier Schweißgeräte kann zum Beispiel die doppelte Leerlauf-Spannung eines Schweißgerätes auftreten. Bei gleichzeitiger Berührung der Potentiale beider Elektroden besteht unter Umständen Lebensgefahr. V ud_fr_st_sv_00466 012007 Gefahren durch Netz- und Schweißstrom (Fortsetzung) Netz- und Gerätezuleitung regelmäßig von einer Elektro-Fachkraft auf Funktionstüchtigkeit des Schutzleiters überprüfen lassen. Das Gerät nur an einem Netz mit Schutzleiter und einer Steckdose mit Schutzleiter-Kontakt betreiben. Wird das Gerät an einem Netz ohne Schutzleiter und an einer Steckdose ohne Schutzleiter-Kontakt betrieben, gilt dies als grob fahrlässig. Für hieraus entstandene Schäden haftet der Hersteller nicht. Falls erforderlich, durch geeignete Mittel für eine ausreichende Erdung des Werkstückes sorgen. Nicht verwendete Geräte ausschalten. Bei Arbeiten in größerer Höhe Sicherheitsgeschirr zur Absturzsicherung tragen. Vor Arbeiten am Gerät das Gerät abschalten und Netzstecker ziehen. Das Gerät durch ein deutlich lesbares und verständliches Warnschild gegen Anstecken des Netzsteckers und Wiedereinschalten sichern. Nach dem Öffnen des Gerätes: - alle Bauteile die elektrische Ladungen speichern entladen - sicherstellen, dass alle Komponenten des Gerätes stromlos sind. Sind Arbeiten an spannungsführenden Teilen notwendig, eine zweite Person hinzuziehen, die den Hauptschalter rechtzeitig ausschaltet. Vagabundierende Schweißströme Werden die nachfolgend angegebenen Hinweise nicht beachtet, ist die Entstehung vagabundierender Schweißströme möglich, die folgendes verursachen können: - Feuergefahr - Überhitzung von Bauteilen, die mit dem Werkstück verbunden sind - Zerstörung von Schutzleitern - Beschädigung des Gerätes und anderer elektrischer Einrichtungen Für eine feste Verbindung der Werkstück-Klemme mit dem Werkstück sorgen. Werkstück-Klemme möglichst nahe an der zu schweißenden Stelle befestigen. Bei elektrisch leitfähigem Boden, das Gerät mit ausreichender Isolierung gegenüber dem Boden aufstellen. Bei Verwendung von Stromverteilern, Doppelkopf-Aufnahmen, etc., folgendes beachten: Auch die Elektrode des nicht verwendeten Schweißbrenners / Elektrodenhalters ist potentialführend. Sorgen Sie für eine ausreichend isolierende Lagerung des nicht verwendeten Schweißbrenners / Elektrodenhalters. Bei automatisierten MIG/MAG Anwendungen die Drahtelektrode nur isoliert von Schweißdraht-Fass, Großspule oder Drahtspule zum Drahtvorschub führen. ud_fr_st_sv_00466 012007 VI EMV- und EMFMaßnahmen Es liegt im Verantwortungsbereich des Betreibers, dafür Sorge zu tragen, dass keine elektromagnetischen Störungen an elektrischen und elektronischen Einrichtungen auftreten Werden elektromagnetische Störungen festgestellt, ist der Betreiber verpflichtet, Maßnahmen für die Störungsbehebung zu ergreifen. Mögliche Probleme und Störfestigkeit von Einrichtungen in der Umgebung gemäß nationalen und internationalen Bestimmungen prüfen und bewerten: - Sicherheitseinrichtungen - Netz-, Signal- und Datenübertragungsleitungen - EDV- und Telekommunikationseinrichtugen - Einrichtungen zum Messen und Kalibrieren Unterstützende Maßnahmen zur Vermeidung von EMV-Problemen: a) Netzversorgung - Treten elektromagnetische Störungen trotz vorschriftsgemäßem Netzanschluss auf, zusätzliche Maßnahmen ergreifen (z.B. geeigneten Netzfilter verwenden). b) Schweißleitungen - so kurz wie möglich halten - eng zusammen verlaufen lassen (auch zur Vermeidung von EMF-Problemen) - weit entfernt von anderen Leitungen verlegen c) Potentialausgleich d) Erdung des Werkstückes - Falls erforderlich, Erdverbindung über geeignete Kondensatoren herstellen. e) Abschirmung, falls erforderlich - Andere Einrichtungen in der Umgebung abschirmen - Gesamte Schweißinstallation abschirmen Elektromagnetische Felder können Gesundheitsschäden verursachen, die noch nicht bekannt sind: - Auswirkungen auf die Gesundheit benachbarter Personen, z.B. Träger von Herzschrittmachern und Hörhilfen - Träger von Herzschrittmachern müssen sich von ihrem Arzt beraten lassen, bevor sie sich in unmittelbare Nähe des Gerätes und des Schweißprozesses aufhalten - Abstände zwischen Schweißkabeln und Kopf/Rumpf des Schweißers aus Sicherheitsgründen so groß wie möglich halten - Schweißkabeln und Schlauchpakete nicht über der Schulter tragen und nicht um den Körper und Körperteile wickeln Besondere Gefahrenstellen Hände, Haare, Kleidungsstücke und Werkzeuge von beweglichen Teilen fernhalten, wie zum Beispiel: - Ventilatoren - Zahnrädern - Rollen - Wellen - Drahtspulen und Schweißdrähten Nicht in rotierende Zahnräder des Drahtantriebes oder in rotierende Antriebsteile greifen. VII ud_fr_st_sv_00466 012007 Besondere Gefahrenstellen (Fortsetzung) Abdeckungen und Seitenteile dürfen nur für die Dauer von Wartungs- und Reparaturarbeiten geöffnet / entfernt werden. Während des Betriebes - Sicherstellen, dass alle Abdeckungen geschlossen und sämtliche Seitenteile ordnungsgemäß montiert sind. - Alle Abdeckungen und Seitenteile geschlossen halten. Austritt des Schweißdrahtes aus dem Schweißbrenner bedeutet ein hohes Verletzungsrisiko (Durchstechen der Hand, Verletzung von Gesicht und Augen, ...). Daher stets den Brenner vom Körper weghalten (Geräte mit Drahtvorschub). Werkstück während und nach dem Schweißen nicht berühren - Verbrennungsgefahr. Von abkühlenden Werkstücken kann Schlacke abspringen. Daher auch bei Nacharbeiten von Werkstücken die vorschriftsgemäße Schutzausrüstung tragen und für ausreichenden Schutz anderer Personen sorgen. Schweißbrenner und andere Ausrüstungskomponenten mit hoher Betriebstemperatur abkühlen lassen, bevor an ihnen gearbeitet wird. In feuer- und explosionsgefährdeten Räumen gelten besondere Vorschriften - entsprechende nationale und internationale Bestimmungen beachten. Stromquellen für Arbeiten in Räumen mit erhöhter elektrischer Gefährdung (z.B. Kessel) müssen mit dem Zeichen (Safety) gekennzeichnet sein. Die Stromquelle darf sich jedoch nicht in solchen Räumen befinden. Verbrühungsgefahr durch austretendes Kühlmittel. Vor dem Abstecken von Anschlüssen für den Wasservorlauf oder -rücklauf, das Kühlgerät abschalten. Für den Krantransport von Geräten nur geeignete Last-Aufnahmemittel des Herstellers verwenden. - Ketten oder Seile an allen vorgesehenen Aufhängungspunkten des geeigneten Last-Aufnahmemittels einhängen. - Ketten oder Seile müssen einen möglichst kleinen Winkel zur Senkrechten einnehmen. - Gasflasche und Drahtvorschub (MIG/MAG- und WIG-Geräte) entfernen. Bei Kran-Aufhängung des Drahtvorschubes während des Schweißens, immer eine geeignete, isolierende Drahtvorschub-Aufhängung verwenden (MIG/MAG- und WIG-Geräte). Ist das Gerät mit einem Tragegurt oder Tragegriff ausgestattet, so dient dieser ausschließlich für den Transport per Hand. Für einen Transport mittels Kran, Gabelstapler oder anderen mechanischen Hebewerkzeugen, ist der Tragegurt nicht geeignet. Gefahr eines unbemerkten Austrittes von farb- und geruchlosem Schutzgas, bei Verwendung eines Adapters für den Schutzgas-Anschluss. Das geräteseitige Gewinde des Adapters, für den Schutzgas-Anschluss, vor der Montage mittels geeignetem Teflon-Band abdichten. ud_fr_st_sv_00466 012007 VIII Gefahr durch SchutzgasFlaschen Schutzgas-Flaschen enthalten unter Druck stehendes Gas und können bei Beschädigung explodieren. Da Schutzgas-Flaschen Bestandteil der Schweißausrüstung sind, müssen sie sehr vorsichtig behandelt werden. Schutzgas-Flaschen mit verdichtetem Gas vor zu großer Hitze, mechanischen Schlägen, Schlacke, offenen Flammen, Funken und Lichtbögen schützen. Die Schutzgas-Flaschen senkrecht montieren und gemäß Anleitung befestigen, damit sie nicht umfallen können. Schutzgas-Flaschen von Schweiß- oder anderen elektrischen Stromkreisen fernhalten. Niemals einen Schweißbrenner auf eine Schutzgas-Flasche hängen. Niemals eine Schutzgas-Flasche mit einer Schweißelektrode berühren. Explosionsgefahr - niemals an einer druckbeaufschlagten Schutzgas-Flasche schweißen. Stets nur für die jeweilige Anwendung geeignete Schutzgas-Flaschen und dazu passendes, geeignetes Zubehör (Regler, Schläuche und Fittings, ...) verwenden. Schutzgas-Flaschen und Zubehör nur in gutem Zustand verwenden. Wird ein Ventil einer Schutzgas-Flasche geöffnet, das Gesicht vom Auslass wegdrehen. Wird nicht geschweißt, das Ventil der Schutzgas-Flasche schließen. Bei nicht angeschlossener Schutzgas-Flasche, Kappe am Ventil der Schutzgas-Flasche belassen. Herstellerangaben sowie entsprechende nationale und internationale Bestimmungen für Schutzgas-Flaschen und Zubehörteile befolgen. Sicherheitsmaßnahmen am Aufstellort und beim Transport Ein umstürzendes Gerät kann Lebensgefahr bedeuten! Das Gerät auf ebenem, festem Untergrund standsicher aufstellen - Ein Neigungswinkel von maximal 10° ist zulässig. In feuer- und explosionsgefährdeten Räumen gelten besondere Vorschriften - entsprechende nationale und internationale Bestimmungen beachten. Durch innerbetriebliche Anweisungen und Kontrollen sicherstellen, dass die Umgebung des Arbeitsplatzes stets sauber und übersichtlich ist. Das Gerät nur gemäß der am Leistungsschild angegebenen Schutzart aufstellen und betreiben. Beim Aufstellen des Gerätes einen Rundumabstand von 0,5 m (1 ft. 7.69 in.) sicherstellen, damit die Kühlluft ungehindert ein- und austreten kann. Beim Transport des Gerätes dafür Sorge tragen, dass die gültigen nationalen und regionalen Richtlinien und Unfallverhütungs-Vorschriften eingehalten werden. Dies gilt speziell für Richtlinien hinsichtlich Gefährdung bei Transport und Beförderung. IX ud_fr_st_sv_00466 012007 Sicherheitsmaßnahmen am Aufstellort und beim Transport (Fortsetzung) Vor jedem Transport des Gerätes, das Kühlmittel vollständig ablassen, sowie folgende Komponenten demontieren: - Drahtvorschub - Drahtspule - Schutzgas-Flasche Vor der Inbetriebnahme, nach dem Transport, unbedingt eine Sichtprüfung des Gerätes auf Beschädigungen vornehmen. Allfällige Beschädigungen vor Inbetriebnahme von geschultem Servicepersonal instandsetzen lassen. Sicherheitsmaßnahmen im Normalbetrieb Das Gerät nur betreiben, wenn alle Schutzeinrichtungen voll funktionstüchtig sind. Sind die Schutzeinrichtungen nicht voll funktionsfähig, besteht Gefahr für - Leib und Leben des Bedieners oder Dritte, - das Gerät und andere Sachwerte des Betreibers - die effiziente Arbeit mit dem Gerät. Nicht voll funktionstüchtige Sicherheitseinrichtungen vor dem Einschalten des Gerätes instandsetzen. Schutzeinrichtungen niemals umgehen oder außer Betrieb setzen. Vor Einschalten des Gerätes sicherstellen, dass niemand gefährdet werden kann. - Wartung und Instandsetzung Das Gerät mindestens einmal pro Woche auf äußerlich erkennbare Schäden und Funktionsfähigkeit der Sicherheitseinrichtungen überprüfen. Schutzgas-Flasche immer gut befestigen und bei Krantransport vorher abnehmen. Nur das Original-Kühlmittel des Herstellers ist auf Grund seiner Eigenschaften (elektrische Leitfähigkeit, Frostschutz, Werkstoff-Verträglichkeit, Brennbarkeit, ...) für den Einsatz in unseren Geräten geeignet. Nur geeignetes Original-Kühlmittel des Herstellers verwenden. Original-Kühlmittel des Herstellers nicht mit anderen Kühlmitteln mischen. Kommt es bei Verwendung anderer Kühlmittel zu Schäden, haftet der Hersteller hierfür nicht und sämtliche Gewährleistungsansprüche erlöschen. Das Kühlmittel ist unter bestimmten Voraussetzungen entzündlich. Das Kühlmittel nur in geschlossenen Original-Gebinden transportieren und von Zündquellen fernhalten Ausgedientes Kühlmittel den nationalen und internationalen Vorschriften entsprechend fachgerecht entsorgen. Ein Sicherheitsdatenblatt erhalten Sie bei Ihrer Servicestelle oder über die Homepage des Herstellers. Bei abgekühlter Anlage vor jedem Schweißbeginn den Kühlmittel-Stand prüfen. Bei fremdbezogenen Teilen ist nicht gewährleistet, dass sie beanspruchungsund sicherheitsgerecht konstruiert und gefertigt sind. Nur Original-Ersatzund Verschleißteile verwenden (gilt auch für Normteile). Ohne Genehmigung des Herstellers keine Veränderungen, Ein- oder Umbauten am Gerät vornehmen. Bauteile in nicht einwandfreiem Zustand sofort austauschen. ud_fr_st_sv_00466 012007 X Wartung und Instandsetzung (Fortsetzung) Sicherheitstechnische Überprüfung Bei Bestellung genaue Benennung und Sach-Nummer laut Ersatzteilliste, sowie Seriennummer Ihres Gerätes angeben. Der Betreiber ist verpflichtet, mindestens alle 12 Monate eine sicherheitstechnische Überprüfung am Gerät durchführen zu lassen. Innerhalb desselben Intervalles von 12 Monaten empfiehlt der Hersteller eine Kalibrierung von Stromquellen. Eine sicherheitstechnische Überprüfung durch eine geprüfte Elektro-Fachkraft ist vorgeschrieben - nach Veränderung - nach Ein- oder Umbauten - nach Reparatur, Pflege und Wartung - mindestens alle zwölf Monate. Für die sicherheitstechnische Überprüfung die entsprechenden nationalen und internationalen Normen und Richtlinien befolgen. Nähere Informationen für die sicherheitstechnische Überprüfung und Kalibrierung erhalten Sie bei Ihrer Servicestelle. Diese stellt Ihnen auf Wunsch die erforderlichen Unterlagen zur Verfügung. Entsorgung Werfen Sie dieses Gerät nicht in den Hausmüll! Gemäß Europäischer Richtlinie 2002/96/EG über Elektro- und ElektronikAltgeräte und Umsetzung in nationales Recht, müssen verbrauchte Elektrowerkzeuge getrennt gesammelt und einer umweltgerechten Wiederverwertung zugeführt werden. Stellen Sie sicher, dass Sie ihr gebrauchtes Gerät bei Ihrem Händler zurückgeben oder holen Sie Informationen über ein lokales, autorisiertes Sammel- und Entsorgungssystem ein. Ein Ignorieren dieser EU Direktive kann zu potentiellen Auswirkungen auf die Umwelt und ihre Gesundheit führen! Sicherheitskennzeichnung Geräte mit CE-Kennzeichnung erfüllen die grundlegenden Anforderungen der Niederspannungs- und Elektromagnetischen Verträglichkeits-Richtlinie (z.B. relevante Produktnormen der Normenreihe EN 60 974). Mit dem CSA-Prüfzeichen gekennzeichnete Geräte erfüllen die Anforderungen der relevanten Normen für Kanada und USA. Datensicherheit Für die Datensicherung von Änderungen gegenüber den Werkseinstellungen ist der Anwender verantwortlich. Im Falle gelöschter persönlicher Einstellungen haftet der Hersteller nicht. XI ud_fr_st_sv_00466 012007 Urheberrecht Das Urheberrecht an dieser Bedienungsanleitung verbleibt beim Hersteller. Text und Abbildungen entsprechen dem technischen Stand bei Drucklegung. Änderungen vorbehalten. Der Inhalt der Bedienungsanleitung begründet keinerlei Ansprüche seitens des Käufers. Für Verbesserungsvorschläge und Hinweise auf Fehler in der Bedienungsanleitung sind wir dankbar. ud_fr_st_sv_00466 012007 XII Inhaltsverzeichnis Allgemeines ................................................................................................................................................... Prinzip der digitalen Gerätefamilie ........................................................................................................... Gerätekonzept .......................................................................................................................................... Einsatzgebiete .......................................................................................................................................... 3 3 3 3 Beschreibung des Bedienpanels ................................................................................................................... 4 Allgemeines ............................................................................................................................................. 4 Beschreibung des Bedienpanels .............................................................................................................. 4 Anschlüsse .................................................................................................................................................... 7 Stromquelle TP 4000 CEL / TP 5000 CEL ............................................................................................... 7 Fernbedienung TR 2000 .......................................................................................................................... 7 Fernbedienung TR 3000 .......................................................................................................................... 8 Fernbedienung TR 4000 .......................................................................................................................... 9 Fernbedienung TR 1000 / TR 1100 .......................................................................................................... 9 Fernbedienung TP 08 ............................................................................................................................. 10 Optionen ...................................................................................................................................................... Verteiler „LocalNet passiv“ ..................................................................................................................... Verteiler „LocalNet aktiv“ ........................................................................................................................ Polwender .............................................................................................................................................. 12 12 12 13 Vor der Inbetriebnahme ............................................................................................................................... Allgemeines ........................................................................................................................................... Bestimmungsgemässe Verwendung ...................................................................................................... Aufstellbestimmungen ............................................................................................................................ Netzanschluss ........................................................................................................................................ 14 14 14 14 14 Fahrwagen „Everywhere“ montieren ........................................................................................................... Allgemeines ........................................................................................................................................... Stromquelle auf Fahrwagen montieren .................................................................................................. Griffteil an der Stromquelle montieren .................................................................................................... Bedienung des Griffteiles ....................................................................................................................... 15 15 15 16 17 Stabelektroden-Schweißen ......................................................................................................................... Allgemeines ........................................................................................................................................... Vorbereitung ........................................................................................................................................... Stabelektroden-Schweißen .................................................................................................................... Funktion Hot-Start .................................................................................................................................. Funktion Eln (Kennlinien-Auswahl) ........................................................................................................ Funktion Anti-Stick ................................................................................................................................. 18 18 18 18 19 19 21 WIG-Schweißen .......................................................................................................................................... Allgemeines ........................................................................................................................................... Vorbereitung ........................................................................................................................................... WIG-Schweißen ..................................................................................................................................... Option TIG-Comfort-Stop ....................................................................................................................... 22 22 22 22 24 Das Setup-Menü: Ebene 1 .......................................................................................................................... Allgemeines ........................................................................................................................................... In das Setup-Menü für Parameter Verfahren einsteigen ........................................................................ Parameter ändern .................................................................................................................................. Das Setup-Menü verlassen .................................................................................................................... 25 25 25 25 25 Parameter ................................................................................................................................................... 26 Stabelektroden-Schweißen .................................................................................................................... 26 WIG-Schweißen ..................................................................................................................................... 26 Das Setup-Menü: Ebene 2 .......................................................................................................................... Allgemeines ........................................................................................................................................... Parameter ändern .................................................................................................................................. Das Setup-Menü verlassen .................................................................................................................... 1 27 27 27 27 Parameter 2nd ............................................................................................................................................ 28 Allgemeines ........................................................................................................................................... 28 Parameter 2nd ....................................................................................................................................... 28 Schweißkreis-Widerstand r ermitteln .......................................................................................................... 29 Allgemeines ........................................................................................................................................... 29 Schweißkreis-Widerstand r ermitteln ..................................................................................................... 29 Schweißkreis-Induktivität L anzeigen .......................................................................................................... 30 Schweißkreis-Induktivität L anzeigen ..................................................................................................... 30 Fehlerdiagnose und Fehlerbehebung ......................................................................................................... Allgemeines ........................................................................................................................................... Angezeigte Service-Codes ..................................................................................................................... Stromquelle TP 4000 CEL / TP 5000 CEL ............................................................................................. 31 31 31 32 Pflege, Wartung und Entsorgung ................................................................................................................ Allgemeines ........................................................................................................................................... Bei jeder Inbetriebnahme ....................................................................................................................... Alle 2 Monate ......................................................................................................................................... Alle 6 Monate ......................................................................................................................................... Entsorgung ............................................................................................................................................. 34 34 34 34 34 34 Technische Daten ........................................................................................................................................ Allgemeines ........................................................................................................................................... TP 4000 CEL .......................................................................................................................................... TP 4000 CEL MV ................................................................................................................................... TP 5000 CEL .......................................................................................................................................... TP 5000 CEL MV ................................................................................................................................... 35 35 35 36 36 37 2 Allgemeines Prinzip der digitalen Gerätefamilie Die TP 4000 CEL / 5000 CEL stellt ein weiteres Bindeglied in der neuen Generation der volldigitalisierten Stromquellen dar. Mit der TP 4000 CEL / 5000 CEL steht erstmals eine speziell für die Verfahren Stabelektroden-Schweißen und WIGSchweißen (mit Berührungszünden) konzipierte volldigitale Stromquelle zur Verfügung. Abb.1 Stromquelle TP 4000 CEL / TP 5000 CEL Die neuen Stromquellen sind vollkommen digitalisierte, mikroprozessorgesteuerte Inverter-Stromquellen. Ein interaktiver Stromquellen-Manager ist mit einem digitalen Signalprozessor gekoppelt, und zusammen steuern und regeln sie den gesamten Schweißprozess. Laufend werden die Ist-Daten gemessen, auf Veränderungen wird sofort reagiert. Die von Fronius entwickelten Regel-Algorithmen sorgen dafür, dass der jeweils gewünschte Soll-Zustand erhalten bleibt. Dadurch ergeben sich eine bisher unvergleichliche Präzision im Schweißprozess, exakte Reproduzierbarkeit sämtlicher Ergebnisse und hervorragende Schweißeigenschaften. Gerätekonzept Typisch für die neuen Geräte sind besondere Flexibilität sowie äußerst einfache Anpassung an unterschiedliche Aufgabenstellungen. Gründe für diese erfreulichen Eigenschaften sind zum einen das modulare Produktdesign, zum anderen die vorhandenen Möglichkeiten der problemlosen Systemerweiterung. Sie können Ihre Maschine praktisch an jede spezifische Gegebenheit anpassen. So gibt es z.B. für die Stromquellen TP 4000 CEL / TP 5000 CEL den Polwender, der ein rasches Umschalten der Polarität an den Schweißstrom-Buchsen ermöglicht. Insbesondere bei Verwendung von CEL-Elektroden, kann hierdurch eine besonders gute Wurzelfassung beim Schweißen von Wurzellagen erreicht werden. Eine große Auswahl an Fernbedienungen und WIG-Schweißbrennern, sowie das raumsparende Fahrwagen-Konzept, ermöglichen in praktisch jeder Situation die Erzielung perfekter Schweißergebnisse, bei bestmöglicher Ergonomie und geringstmöglichem Zeitaufwand. Die Fernbedienungen werden mit unterschiedlichen anwenderspezifischen Bedienkonzepten angeboten. Für das Stabelektroden-Schweißen steht darüber hinaus die kompakte Drahtlos-Fernbedienung TP 08 zur Verfügung. Diese Fernbedienung ermöglicht eine kabellose Korrektur des eingestellten Schweißstromes während der Schweißpausen. Einsatzgebiete In Gewerbe und Industrie gibt es zahlreiche Anwendungsbereiche für die TP 4000 CEL / TP 5000 CEL. Bezüglich der Materialien eignen sie sich selbstverständlich für den klassischen Stahl, ebenso wie für Chrom/Nickel. Die TP 4000 CEL / 5000 CEL mit 380 oder 480 A erfüllen selbst die höchsten Ansprüche der Industrie. Konzipiert sind sie für den Einsatz im Apparatebau, im ChemieanlagenBau, im Maschinen - und Schienenfahrzeug-Bau sowie in Werften. 3 Beschreibung des Bedienpanels Allgemeines Das Bedienpanel ist von den Funktionen her logisch aufgebaut. Die einzelnen für die Schweißung notwendigen Parameter lassen sich einfach mittels Taste anwählen und - mit dem Einstellrad verändern - während der Schweißung am Display anzeigen HINWEIS! Auf Grund von Softwareupdates können Funktionen an Ihrem Gerät verfügbar sein, die in dieser Bedienungsanleitung nicht beschrieben sind oder umgekehrt. Zudem können sich einzelne Abbildungen geringfügig von den Bedienelementen an ihrem Gerät unterscheiden. Die Funktionsweise dieser Bedienelemente ist jedoch identisch. Beschreibung des Bedienpanels WARNUNG! Fehlbedienung kann schwerwiegende Personen- und Sachschäden verursachen. Beschriebene Funktionen erst anwenden, wenn folgende Dokumente vollständig gelesen und verstanden wurden: diese Bedienungsanleitung sämtliche Bedienungsanleitungen der Systemkomponenten, insbesondere Sicherheitsvorschriften (2) (9) (6) (4) (11)(10) (12) (3) (7) Abb.2 Bedienpanel 4 (1) (5) (3) (8) Beschreibung des Bedienpanels (Fortsetzung) (1) Einstellrad ... zum Ändern von Parametern. Leuchtet die Anzeige am Einstellrad, kann der angewählte Parameter abgeändert werden. (2) Taste Parameteranwahl ... zur Anwahl folgender Parameter - Schweißstrom - Dynamik Leuchtet die Anzeige an der Taste Parameteranwahl und am Einstellrad, kann der angezeigte / angewählte Parameter mit dem Einstellrad abgeändert werden. Die Parameter können für sämtliche Verfahren, welche mittels Taste Verfahren (3) anwählbar sind, gesondert eingestellt werden. Die Parameter-Einstellungen bleiben so lange gespeichert, bis der jeweilige Einstellwert abgeändert wird. (3) Taste(n) Verfahren ... zur Anwahl des Schweißverfahrens - Stabelektroden-Schweißen - Stabelektroden-Schweißen mit CEL-Elektrode - Spezial-Verfahren - WIG-Schweißen mit Berührungszünden (4) Parameter Schweißstrom ... zur Anwahl des Schweißstromes. Vor Schweißbeginn wird automatisch ein Richtwert angezeigt, der sich aus den programmierten Parametern ergibt. Während des Schweißvorganges wird der aktuelle Ist-Wert angezeigt. (5) Parameter Schweißspannung ... Vor Schweißbeginn wird die Leerlauf-Spannung angezeigt. Während des Schweißvorganges wird der aktuelle Ist-Wert angezeigt. HINWEIS! Die Stromquelle verfügt über eine pulsierende Leerlauf -Spannung. Vor Schweißbeginn (Leerlauf) zeigt die Anzeige einen Mittelwert der Schweißspannung von ca. 60 V. Für Schweißstart und Schweißprozess steht jedoch eine Schweißspannung von maximal 95 V zur Verfügung. Optimale Zündeigenschaften sind gewährleistet. (6) Parameter Dynamik zur Beeinflussung der Kurzschluss-Stromstärke im Moment des Tropfenüberganges 0 weicher und spritzerarmer Lichtbogen 100 härterer und stabilerer Lichtbogen HINWEIS! Bei ausgewähltem Verfahren WIG-Schweißen kann der Parameter Dynamik nicht angewählt werden. (7) Taste Setup / Store ... zum Einstieg in das Setup-Menü HINWEIS! Durch gleichzeitiges Drücken der Taste Setup / -Store (7) und der Taste Parameteranwahl (2), wird an den Anzeigen die Software-Version angezeigt. Der Ausstieg erfolgt durch Drücken der Taste Setup / Store (7). (8) Netzschalter ... zum Ein- und Ausschalten der Stromquelle (9) Anschluss LocalNet ... standardisierter Anschluss für Systemerweiterungen (z.B. Fernbedienung,etc.) (10) Anzeige HOLD ... bei jedem Schweißende werden die aktuellen Ist-Werte von Schweißstrom und -spannung gespeichert - die Hold-Anzeige leuchtet. (11) Anzeige Übertemperatur ... leuchtet auf, wenn sich die Stromquelle zu stark erwärmt (z.B. durch überschrittene Einschaltdauer). Weiterführende Informationen im Kapitel „Fehlerdiagnose und Fehlerbehebung“ 5 Beschreibung des Bedienpanels (Fortsetzung) (12) Anzeige TP 08 ... leuchtet auf, wenn an der Stromquelle eine Fernbedienung TP 08 angeschlossen ist. Auch wenn die Fernbedienung TP 08 bereits wieder abgeklemmt wurde, leuchtet die Anzeige TP 08 weiterhin. Solange die Anzeige TP 08 leuchtet, können Strom und Dynamik nur an der Fernbedienung TP 08 eingestellt werden. Wiederherstellen der Einstellmöglichkeit von Strom und Dynamik an der Stromquelle und an anderen Systemerweiterungen: 1. 2. 3. TP 08 abklemmen Stromquelle ausschalten und wieder einschalten Anzeige TP 08 bleibt dunkel 6 Anschlüsse Stromquelle TP 4000 CEL / TP 5000 CEL (A) (-)-Strombuchse mit Bajonettverschluss ... dient zum - Anschluss für Stabelektrodenoder Massekabel bei der Stabelektroden-Schweißung (je nach Elektrodentype) - Stromanschluss des WIGSchweißbrenners (E) (F) (A) (B) (C) (D) (G) Abb.3 Vorder- u. Rückansicht Stromquelle TP 4000 CEL / TP 5000 CEL (B) (+)-Strombuchse mit Bajonettverschluss ... dient zum - Anschluss für Stabelektroden- und Massekabel bei der Stabelektroden-Schweißung (je nach Elektrodentype) - Anschluss für das Massekabel beim WIG-Schweißen HINWEIS! Bei Verwendung der Fernbedienung TR 3000, das StabelektrodenKabel grundsätzlich an der (+)-Strombuchse anschließen. (C) Blindabdeckung (D) Blindabdeckung (E) Blindabdeckung (vorgesehen für Anschluss LocalNet) (F) Blindabdeckung (vorgesehen für Anschluss LocalNet) (G) Netzkabel mit Zugentlastung Fernbedienung TR 2000 (24) Einstellregler Schweißstrom ... zur Anwahl des Schweißstromes (24) (25) Einstellregler Dynamik Stabelektroden-Schweißung ... zur Beeinflussung der KurzschlussStromstärke im Moment des Tropfenüberganges (25) 0 100 weicher und spritzerarmer Lichtbogen härterer und stabilerer Licht bogen HINWEIS! Parameter, die an der Fernbedienung einstellbar sind, können nicht an der Stromquelle geändert werden. Parameteränderungen können nur an der Fernbedienung erfolgen. Abb.4 Fernbedienung TR 2000 7 Fernbedienung TR 3000 (26) Anzeige Schweißstrom ... zur Anzeige des Schweißstromes. Vor Schweißbeginn wird automatisch ein Richtwert angezeigt, der sich aus den programmierten Parametern ergibt. Während des Schweißvorganges wird der aktuelle Ist-Wert angezeigt. (27)(26) (28) (27) Anzeige HOLD ... bei jedem Schweißende wird der aktuelle Ist-Wert des Schweißstromes gespeichert - die Hold-Anzeige leuchtet. (28) Einstellregler Schweißstrom ... zur Anwahl des Schweißstromes. Abb.5 Fernbedienung TR 3000 - Ansicht von oben (29) Auswahlschalter Verfahren ... zur Anwahl des Schweißverfahrens - Stabelektroden-Schweißen - Stabelektroden-Schweißen mit CEL-Elektrode - Spezial-Verfahren - WIG-Schweißen mit Berührungszünden (29) (30) Abb.6 Fernbedienung TR 3000 - Ansicht von links (30) Auswahlschalter Schweißstrom-Bereich ... zur Auswahl des mittels Einstellregler Schweißstrom (28) einstellbaren Schweißstrom-Bereiches - min - 150 A: 0 geringstmöglicher Schweißstrom 10 Schweißstrom beträgt 150 A - 100 A - max: 0 Schweißstrom beträgt 100 A 10 größtmöglicher Schweißstrom (31) Einstellregler Dynamik Stabelektroden-Schweißen ... zur Beeinflussung der KurzschlussStromstärke im Moment des Tropfenüberganges 0 100 (32) (31) Abb.7 Fernbedienung TR 3000 - Ansicht von rechts (32) Umschalter für Polwender ... zur Ansteuerung des Polwenders (Option) + - 8 weicher und spritzerarmer Lichtbogen härterer und stabilerer Licht bogen Positives Schweißpotential an der (+)-Strombuchse Negatives Schweißpotential an der (+)-Strombuchse Fernbedienung TR 3000 (Fortsetzung) HINWEIS! Parameter, die an der Fernbedienung einstellbar sind, können nicht an der Stromquelle geändert werden. Parameteränderungen können nur an der Fernbedienung erfolgen. Fernbedienung TR 4000 (33) Taste Parameterumschaltung ... zur Anwahl und Anzeige der Parameter Schweißspannung und Schweißstrom, an der Digitalanzeige (33) (34) (35) (36) HINWEIS! Beim Ändern eines Parameters wird der Parameterwert zur Kontrolle kurz an der Digitalanzeige der Fernbedienung angezeigt. (34) Einstellregler Schweißstrom ... zur Anwahl des Schweißstromes Abb.8 Fernbedienung TR 4000 (35) Einstellregler Hotstart Stabelektroden-Schweißen ... beeinflusst den Schweißstrom während der Zündphase 0 keine Beeinflussung 10 100%ige Erhöhung des Schweißstromes während der Zündphase (36) Einstellregler Dynamik Stabelektroden-Schweißen ... zur Beeinflussung der Kurzschluss-Stromstärke im Momentdes Tropfenüberganges 0 weicher und spritzerarmer Lichtbogen 100 härterer und stabilerer Lichtbogen HINWEIS! Parameter, die an der Fernbedienung einstellbar sind, können nicht an Stromquelle geändert werden. Parameteränderungen können nur an der Fernbedienung erfolgen. Fernbedienung TR 1000 / TR 1100 Abb.10 Fernbedienung TR 1100 Abb.9 Fernbedienung TR 1000 9 Fernbedienung TR 1000 / TR 1100 (Fortsetzung) (38) (37) (38)(37) (37) Taste(n) Parameteranzeige ... zur Anwahl des anzuzeigenden Parameters (Schweißstrom, ...) (38) Taste(n) Parametereinstellung ... zum Ändern des gewählten Parameters (39) (39) Parameter Schweißstrom Abb.11 Bedienkonzept TR 1000 / TR 1100 Fernbedienung TP 08 Systemvoraussetzung: - Software-Version 2.81.1 (ZM) (ZO) (ZP)(ZQ) (ZN)(ZR) 1. 2. 3. (ZL) Mit Taste Verfahren (3) das Verfahren Stabelektroden-Schweißen anwählen Masseklemme am Werkstück befestigen und Elektrodenhalterung an der Fernbedienung TP 08 festklemmen TP 08 auf das Werkstück aufsetzen, so dass eine satte Verbindung zwischen Werkstück und den beiden Kontakten (ZL)entsteht (ZL) Abb.12 Fernbedienung TP 08 HINWEIS! Die Schweißspannung wird mit einer Verzögerung von 3 s auf die Schweißbuchsen geschaltet. Anschließend wird die Fernbedienung TP 08 mit der Schweißspannung versorgt, und die Anzeige (ZM) leuchtet auf. Wurde die Fernbedienung TP 08 seit dem letzten Einschalten der Stromquelle angeschlossen, können Strom und Dynamik nur an der Fernbedienung TP 08 eingestellt werden. Wiederherstellen der Einstellmöglichkeit von Strom und Dynamik an der Stromquelle und an anderen Systemerweiterungen: 1. 2. TP 08 abklemmen Stromquelle ausschalten und wieder einschalten (ZN) Taste Parameteranwahl ... zur Anwahl der Parameter Schweißstrom (ZO) Dynamik (ZP) (ZQ) Taste „+“ ... erhöht den angewählten Parameter (ZR) Taste „-“ ... verringert den angewählten Parameter HINWEIS! Unabhängig von den im Kapitel „Fehlerdiagnose und Fehlerbehebung“ angeführten Service-Codes, können an der Fernbedienung TP 08 folgende Service-Codes angezeigt werden: 10 Fernbedienung TP 08 (Fortsetzung) Service-Code: -oFFUrsache: Schlechter Kontakt mit dem Werkstück Behebung: Satte Verbindung zum Werkstück herstellen Service-Code: -E62Ursache: Übertemperatur der Fernbedienung TP 08 Behebung: TP 08 abkühlen lassen So lange die Stromquelle oder eine andere Systemerweiterung einen Service-Code anzeigt, ist die Fernbedienung TP 08 außer Funktion. 11 Optionen Verteiler „LocalNet passiv“ Mit dem Verteiler „LocalNet passiv“ können am Anschluss LocalNet der Stromquelle mehrere Systemerweiterungen gleichzeitig angeschlossen und betrieben werden - z.B. TR 3000 und TR 1100 gemeinsam. Abb.13 Verteiler „LocalNet passiv“ HINWEIS! Verteiler „LocalNet passiv“ funktioniert nur ordnungsgemäß, wenn beide Verteilenden benutzt / angeschlossen sind. Verteiler „LocalNet aktiv“ Bei dem Verteiler „LocalNet aktiv“ stehen an der Rückseite der Stromquelle insgesamt drei Anschlüsse LocalNet zur Verfügung. Der gleichzeitige Betrieb einer Vielzahl von Systemerweiterungen ist möglich. (57) (57) (56) HINWEIS! Bleiben einzelne Anschlüsse unbelegt, den Anschluss LocalNet aus Metall (56) bevorzugt verwenden. (56) Abb.14 Rückansicht TP 4000 / 5000 CEL mit Verteiler „LocalNet aktiv“ (57) Anschluss LocalNet aus Metall Anschluss LocalNet aus Kunststoff Ein wesentlicher Vorteil gegenüber dem Verteiler „LocalNet passiv“ ergibt sich bei Verwendung vorübergehend angeschlossener Teilnehmer, wie beispielsweise die Fernebedienung RCU 4000. Gegenüber dem Verteiler „LocalNet passiv“ können einzelne Anschlüsse nunbelegt bleiben, wenn die zusätzlichen Teilnehmer nicht mehr benötigt werden. 12 Polwender Systemvoraussetzung: - Software-Version 2.81.1 - Fernbedienung TR 3000 TR 3000 (32) (32) Abb.15 Ansteuerung des Polwenders in Verbindung mit TR 3000 13 (32) Umschalter für Polwender ... zur Ansteuerung des Polwenders (Option) + Positives Schweißpotential an der (+) - Strombuchse Negatives Schweißpotential an der (+) - Strombuchse Vor der Inbetriebnahme Allgemeines Bestimmungsgemässe Verwendung WARNUNG! Fehlbedienung kann schwerwiegende Personen- und Sachschäden verursachen. Beschriebene Funktionen erst anwenden, wenn folgende Dokumente vollständig gelesen und verstanden wurden: diese Bedienungsanleitung sämtliche Bedienungsanleitungen der Systemkomponenten, insbesondere Sicherheitsvorschriften Die Stromquelle ist ausschließlich zum Stabelektroden- und WIG-Schweißen, sowie zum Fugenhobeln, bestimmt. Eine andere oder darüber hinausgehende Benutzung gilt als nicht bestimmungsgemäß. Für hieraus entstehende Schäden haftet der Hersteller nicht. Zur bestimmungsgemäßen Verwendung gehört auch - das Beachten aller Hinweise aus der Bedienungsanleitung - die Einhaltung der Inspektions- und Wartungsarbeiten Aufstellbestimmungen Die Stromquelle ist nach Schutzart IP23 geprüft, das bedeutet: Schutz gegen Eindringen fester Fremdkörper größer Ø 12mm Schutz gegen Sprühwasser bis zu einem Winkel von 60° zur Senkrechten Die Stromquelle kann, gemäß Schutzart IP23, im Freien aufgestellt und betrieben werden. Die eingebauten elektrischen Teile sind jedoch vor unmittelbarer Nässeeinwirkung zu schützen. WARNUNG! Umstürzende oder herabfallende Geräte können Lebensgefahr bedeuten. Geräte auf ebenem und festem Untergrund standsicher aufstellen. Der Lüftungskanal stellt eine wesentliche Sicherheitseinrichtung dar. Bei der Wahl des Aufstellorts ist zu beachten, dass die Kühlluft ungehindert durch die Luftschlitze an Vorder- und Rückseite ein- und austreten kann. Anfallender elektrisch leitender Staub (z.B. bei Schmirgelarbeiten) darf nicht direkt in die Anlage gesaugt werden. Netzanschluss Geräte sind für die am Leistungsschild angegebene Netzspannung ausgelegt. Sind Netzkabel oder Netzstecker bei Ihrer Geräteausführung nicht angebracht, müssen diese den nationalen Normen entsprechend montiert werden. Die Absicherung der Netzzuleitung ist den Technischen Daten zu entnehmen. HINWEIS! Nicht ausreichend dimensionierte Elektroinstallation kann zu schwerwiegenden Sachschäden führen. Die Netzzuleitung sowie deren Absicherung sind entsprechend der vorhandenen Stromversorgung auszulegen. Es gelten die Technischen Daten auf dem Leistungsschild. 14 Fahrwagen „Everywhere“ montieren Allgemeines WARNUNG! Ein elektrischer Schlag kann tödlich sein. Ist das Gerät während der Installation am Netz angesteckt, besteht die Gefahr schwerwiegender Personen und Sachschäden. Sämtliche Arbeiten am Gerät nur durchführen, wenn der Netzschalter in Stellung - O - geschaltet ist, das Gerät vom Netz getrennt ist. Stromquelle auf Fahrwagen montieren (1) 1. (1) 2. Arretierungen (1) in die Bohrungen am Fahrwagen-Boden einsetzen Arretierungen (1) bis zum Anschlag schräg stellen Abb.16 Arretierungen einsetzen HINWEIS! Beim senkrechten Aufstellen der Stromquelle darauf achten, dass das Netzkabel weder geknickt, eingeklemmt, noch auf Zug belastet wird. 3. 4. 5. Abb.17 Stromquelle und Fahrwagen 6. X (2) (3) (2) (3) (2)(3) Abb.18 Beilagscheiben und Flügelmuttern ansetzen 15 Stromquelle vorsichtig an der Rückseite senkrecht aufstellen Fahrwagen vorsichtig an der Rückseite senkrecht aufstellen Fahrwagen gegen Stromquelle schieben, sodass Fahrwagen und Stromquelle einander zentrisch gegenüberstehen An den sechs Gewindebolzen Beilagscheiben (2) aufsetzen und Flügelmuttern (3) leicht andrehen Stromquelle auf Fahrwagen montieren (Fortsetzung) (4) 7. (4) 8. 9. (3) (3) Arretierungen durch Verschieben der äußeren Gewindebolzen (4) bis zum Anschlag geradestellen Sechs Flügelmuttern (3) festziehen Fahrwagen mit Stromquelle vorsichtig auf die Räder stellen (3) Abb.19 Arretierungen geradestellen und fixieren Griffteil an der Stromquelle montieren (1) (2) (2)(1) (2) (2) (3) Abb.20 Griffbleche einrasten lassen (1) (1) Abb.21 Griffbleche und Griffrohr HINWEIS! Beim Aneinanderfügen der beiden Griffbleche (1) darauf achten, dass die Arretierungen (2), an der Unterseite der Griffbleche (1), vollständig einrasten (Abb.20 und Abb.21). (3) (4) (1) (5) (6) (7) (8) 1. 2. (9) (9) (10) (10) Abb.22 Griffbleche und Griffrohr mittels Schrauben „Extrude-Tite“ fixieren 3. Am Griff der Stromquelle (4), Griffbleche (1) mittels Arretierungen (2) aneinander einrasten lassen (Abb.20 und Abb.21) Splint (8) des Griffrohres (3) in die Führungen (6) beider Griffbleche einsetzen HINWEIS! Zur Fixierung der Griffbleche (1) an der Oberseite jeweils zwei Schrauben ExtrudeTite an einer Seite (5) und zwei Schrauben Extrude-Tite an der anderen Seite (7) ansetzen, sodass sich die Schraubenköpfe jeweils an der Seite mit der größeren Bohrung befinden. Griffbleche (1) mittels vier Schrauben Extrude-Tite (5) und (7) an der Oberseite aneinander fixieren HINWEIS! Zur Fixierung der beiden Griffbleche (1) in der Mitte, jeweils zwei Schrauben Extrude-Tite an einer Seite (9) und zwei Schrauben Extrude-Tite an der anderen Seite (10) ansetzen, sodass sich die Schraubenköpfe jeweils an der Seite mit der größeren Bohrung befinden. 4. Griffbleche (1) mittels vier Schrauben Extrude-Tite (9) und (10) in der Mitte aneinander fixieren 16 Bedienung des Griffteiles HINWEIS! Bei eingefahrenem Griffteil (1) den Griffteil (1) unbedingt, durch Drehen nach links verriegeln. 1. Zum Einfahren des Griffteiles (1): - Griffteil (1) nach links drehen (entriegeln) - Griffteil (1) bis zum Anschlag einschieben - Griffteil (1) erneut nach links drehen (verriegeln) HINWEIS! Bei ausgefahrenem Griffteil (1) den Griffteil (1) unbedingt durch Drehen nach rechts verriegeln. (1) 2. Abb.23 Griffteil ausfahren 17 Zum Ausfahren des Griffteiles (1): - Griffteil (1) nach rechts drehen (entriegeln) - Griffteil (1) bis zum Anschlag herausziehen - Griffteil (1) erneut nach rechts drehen (verriegeln) Stabelektroden-Schweißen Allgemeines WARNUNG! Fehlbedienung kann schwerwiegende Personen- und Sachschäden verursachen. Beschriebene Funktionen erst anwenden, wenn folgende Dokumente vollständig gelesen und verstanden wurden: diese Bedienungsanleitung sämtliche Bedienungsanleitungen der Systemkomponenten, insbesondere Sicherheitsvorschriften WARNUNG! Ein elektrischer Schlag kann tödlich sein. Ist das Gerät während der Installation am Netz angesteckt, besteht die Gefahr schwerwiegender Personen und Sachschäden. Sämtliche Arbeiten am Gerät nur durchführen, wenn der Netzschalter in Stellung - O - geschaltet ist, das Gerät vom Netz getrennt ist. Vorbereitung 1. 2. 3. 4. 5. 6. StabelektrodenSchweißen Netzschalter in Stellung - O - schalten Netzstecker ausstecken Massekabel je nach Elektrodentype in Strombuchse (A) oder (B) einstecken und verriegeln Mit dem anderen Ende des Massekabels Verbindung zum Werkstück herstellen Schweißkabel je nach Elektrodentype in Strombuchse (A) oder (B) einstecken und durch Drehen nach rechts verriegeln Netzstecker einstecken VORSICHT! Gefahr von Personen- und Sachschäden durch elektrischen Schlag. Sobald der Netzschalter in Stellung - I - geschaltet ist, ist die Stabelektrode im Elektrodenhalter spannungsführend. Darauf achten, dass die Stabelektrode keine Personen oder elektrisch leitenden oder geerdeten Teile berührt (z.B. Gehäuse, etc.) 1. 2. Netzschalter (8) in Stellung - I - schalten (sämtliche Anzeigen am Bedienpanel leuchten kurz auf) Mit Taste Verfahren (3) eines der folgenden Verfahren anwählen: - Stabelektroden-Schweißen - Stabelektroden-Schweißen mit CEL-Elektrode - Spezial-Verfahren Die Schweißspannung wird mit einer Verzögerung von 3 s auf die Schweißbuchsen geschaltet. HINWEIS! Parameter, die an der Fernbedienung TR 2000 / 3000 / 4000 einstellbar sind, können nicht an der Stromquelle geändert werden. Parameteränderungen können nur an der Fernbedienung TR 2000 / 3000 / 4000 erfolgen. 3. 4. 5. 6. 7. Taste Parameteranwahl (2) drücken (Anzeige an der Taste muss leuchten) Mit Einstellrad (1) gewünschte Stromstärke einstellen (Wert kann an der linken Anzeige abgelesen werden) Taste Parameteranwahl (2) drücken (Anzeige an der Taste muß leuchten) Mit Einstellrad (1) gewünschte Dynamik einstellen (Wert kann an der linken Anzeige abgelesen werden) Schweißvorgang einleiten 18 StabelektrodenSchweißen (Fortsetzung) Grundsätzlich bleiben sämtliche mittels Einstellrad (1) eingestellten Parameter-Sollwerte bis zur nächsten Änderung gespeichert. Dies gilt auch, wenn die Stromquelle zwischenzeitlich aus- und wieder eingeschaltet wurde. Funktion HotStart Um ein optimales Schweißergebnis zu erzielen, ist in manchen Fällen die Funktion HotStart einzustellen. Vorteile: - Verbesserung der Zündeigenschaften, auch bei Elektroden mit schlechten Zündeigenschaften Besseres Aufschmelzen des Grund-Werkstoffes in der Startphase, dadurch weniger Kaltstellen Weitgehende Vermeidung von Schlacken-Einschlüssen - HINWEIS! Die Einstellung der verfügbaren Parameter dem Kapitel „SetupMenü: Ebene 1“ entnehmen. I (A) Legende: Hti 300A IH Hauptstrom = eingestellter Schweiß strom HCU Hot-start current = Hotstart-Strom ... 0 - 100 %, Werkseinstellung: 50 % Hti Hot-current time = Hotstrom-Zeit ... 0 -2,0 s, Werkseinstellung: 0,5 s HCU 200A IH 0,5 s 1s 1,5 s t Abb.25 Beispiel für die Funktion "Hot-Start" Funktionsweise Während der eingestellten Hotstrom-Zeit (Hti) wird der Schweißstrom auf einen bestimmten Wert erhöht. Dieser Wert ist um 0-100 % (HCU) höher als der eingestellte Schweißstrom (IH). Beispiel: Es wurde ein Schweißstrom (IH) von 200 A eingestellt. Für den Hotstrom-Zeit (HCU) wurden 50 % gewählt. Während der Hotstrom-Zeit (Hti, z.B. 0,5 s) beträgt der tatsächliche Schweißstrom 200 A + (50 % von 200 A) = 300 A. Funktion Eln (KennlinienAuswahl) Die Funktion Eln kann für die Verfahren „Stabelektroden-Schweißen“, „StabelektrodenSchweißen mit CEL-Elektrode“ und „Spezial-Verfahren“ gesondert parametriert werden. HINWEIS! Die Einstellung der verfügbaren Parameter dem Kapitel „SetupMenü: Ebene 1“ entnehmen. Parameter „con“ (konstanter Schweißstrom) Ist der Parameter „con“ eingestellt, wird der Schweißstrom, unabhängig von der Schweißspannung, konstant gehalten. Es ergibt sich eine senkrechte Kennlinie (4) (Abb.26). Der Parameter „con“ eignet sich besonders gut für Rutil-Elektroden und basische Elektroden, sowie für das Fugenhobeln. Der Parameter „con“ ist daher auch Werkseinstellung bei angewähltem Verfahren „Stabelektroden-Schweißen“. 19 Funktion Eln (KennlinienAuswahl) (Fortsetzung) Für das Fugenhobeln die Dynamik auf „100“ einstellen. Parameter „0,1 - 20“ (fallende Kennlinie mit einstellbarer Neigung) Mittels Parameter „0,1-20“ kann eine fallende Kennlinie (5) (Abb.26) eingestellt werden. Der Einstellbereich erstreckt sich von 0,1 A / V (sehr steil) bis 20 A / V (sehr flach). Die Einstellung einer flachen Kennlinie (5) ist nur für Cellulose-Elektroden empfehlenswert. HINWEIS! Bei Einstellung einer flachen Kennlinie (5), die Dynamik auf einen höheren Wert einstellen. Parameter „P“ (konstante Schweißleistung) Ist der Parameter „P“ eingestellt, wird die Schweißleistung, unabhängig von Schweißspannung und -strom, konstant gehalten. Es ergibt sich eine hyperbolische Kennlinie (6) (Abb.26). Der Parameter „P“ eignet sich besonders gut für Cellulose-Elektroden. Der Parameter „P“ ist daher auch Werkseinstellung bei angewähltem Verfahren „StabelektrodenSchweißen mit CEL-Elektrode“. HINWEIS! Bei Problemen mit zum Festkleben neigender Stabelektrode, die Dynamik auf einen höheren Wert einstellen. U (V) 60 con - 20 A/V 50 (4) (6) (2) (1) (3) (5) 40 30 20 (7) (8) 10 0 0 50 100 150 200 250 300 350 400 450 I (A) Abb.26 Mittels Funktion Eln auswählbare Kennlinien Legende: (1) Arbeitsgerade für Stabelektrode (2) Arbeitsgerade für Stabelektrode bei erhöhter Lichtbogen-Länge (3) Arbeitsgerade für Stabelektrode bei reduzierter Lichtbogen-Länge (4) Kennlinie bei angewähltem Parameter „con“ (konstanter Schweißstrom) (5) Kennlinie bei angewähltem Parameter „0,1 - 20“ (fallende Kennlinie mit einstellbarer Neigung) (6) Kennlinie bei angewähltem Parameter „P“ (konstante Schweißleistung) (7) Beispiel für eingestellte Dynamik bei angewählter Kennlinie (4) (8) Beispiel für eingestellte Dynamik bei angewählter Kennlinie (5) bzw. (6) Weiterführende Erklärungen (Abb.27) Die abgebildeten Kennlinien (4), (5) und (6) gelten bei Verwendung einer Stabelektrode, deren Charakteristik bei einer bestimmten Lichtbogen-Länge der Arbeitsgeraden (1) entspricht. Je nach eingestelltem Schweißstrom (I), wird der Schnittpunkt (Arbeitspunkt) der Kennlinien (4), (5) und (6) entlang der Arbeitsgeraden (1) verschoben. Der Arbeitspunkt gibt Auskunft über die aktuelle Schweißspannung und den aktuellen Schweißstrom. Bei einem fix eingestellten Schweißstrom (IH) kann der Arbeitspunkt entlang der Kennlinien (4), (5) und (6), je nach momentaner Schweißspannung, wandern. Die Schweißspannung U ist abhängig von der Lichtbogen-Länge 20 Funktion Eln (KennlinienAuswahl) (Fortsetzung) Ändert sich die Lichtbogen-Länge, z.B. entsprechend der Arbeitsgeraden (2), ergibt sich der Arbeitspunkt als Schnittpunkt der entsprechenden Kennlinie (4), (5) oder (6) mit der Arbeitsgeraden (2). Gilt für die Kennlinien (5) und (6): In Abhängigkeit von der Schweißspannung (Lichtbogen-Länge) wird der Schweißstrom (I) ebenfalls kleiner oder größer, bei gleichbleibendem Einstellwert für IH. (9) Arbeitspunkt bei hoher Lichtbogenlänge Arbeitspunkt bei eingestelltem Schweißstrom (IH) Arbeitspunkt bei geringer Lichtbogenlänge U (V) 60 (6) (2) 50 (1) 40 (3) (5) 30 20 (4) (8) 10 0 0 50 100 150 200 250 300 350 400 450 I (A) IH - 50 % IH + Dynamik Abb.27 Einstellbeispiel: IH = 250 A, Dynamik = 50 Legende: (1) Arbeitsgerade für Stabelektrode (2) Arbeitsgerade für Stabelektrode bei erhöhter Lichtbogen-Länge (3) Arbeitsgerade für Stabelektrode bei reduzierter Lichtbogen-Länge (4) Kennlinie bei angewähltem Parameter „con“ (konstanter Schweißstrom) (5) Kennlinie bei angewähltem Parameter „0,1 - 20“ (fallende Kennlinie mit einstellbarer Neigung) (6) Kennlinie bei angewähltem Parameter „P“ (konstante Schweißleistung) (8) Beispiel für eingestellte Dynamik bei angewählter Kennlinie (5) oder (6) (9) Mögliche Stromänderung, bei angewählter Kennlinie (5) oder (6), in Abhängigkeit von der Schweißspannung (Lichtbogenlänge) Der Schweißstrom (I) im Bereich (9) kann höchstens um 50 % geringer werden als der eingestellte Schweißstrom (IH). Nach oben wird der Schweißstrom (I) durch die eingestellte Dynamik begrenzt. Funktion AntiStick HINWEIS! Die Funktion Anti-Stick kann im „Setup-Menü: Ebene 2“ aktiviert und deaktiviert werden (Kapitel „Setup-Menü: Ebene 2“). Bei kürzer werdendem Lichtbogen kann die Schweißspannung soweit absinken, dass die Stabelektrode zum Festkleben neigt. Außerdem kann es zu einem Ausglühen der Stabelektrode kommen. Ein Ausglühen wird bei aktivierter Funktion Anti-Stick verhindert. Beginnt die Stabelektrode festzukleben, schaltet die Stromquelle den Schweißstrom sofort ab. Nach dem Abtrennen der Stabelektrode vom Werkstück, kann der Schweißvorgang problemlos fortgesetzt werden. 21 WIG-Schweißen Allgemeines WARNUNG! Fehlbedienung kann schwerwiegende Personen- und Sachschäden verursachen. Beschriebene Funktionen erst anwenden, wenn folgende Dokumente vollständig gelesen und verstanden wurden: diese Bedienungsanleitung sämtliche Bedienungsanleitungen der Systemkomponenten, insbesondere Sicherheitsvorschriften WARNUNG! Ein elektrischer Schlag kann tödlich sein. Ist das Gerät während der Installation am Netz angesteckt, besteht die Gefahr schwerwiegender Personen und Sachschäden. Sämtliche Arbeiten am Gerät nur durchführen, wenn der Netzschalter in Stellung - O - geschaltet ist, das Gerät vom Netz getrennt ist. Vorbereitung 1. 2. 3. 4. 5. 6. 7. 8. WIG-Schweißen Netzschalter in Stellung - O - schalten Netzstecker ausstecken Massekabel in Strombuchse (B) einstecken und verriegeln Mit dem anderem Ende des Massekabel Verbindung zum Werkstück herstellen Schweißkabel des WIG Gasschieber-Schweißbrenners in Strombuchse (A) einstekken und durch Drehen nach rechts verriegeln Druckminderer auf der Gasflasche (Argon) aufschrauben und festziehen Gasschlauch mit Druckminderer verbinden Netzstecker einstecken VORSICHT! Gefahr von Personen- und Sachschäden durch elektrischen Schlag. Sobald der Netzschalter in Stellung - I - geschaltet ist, ist die Wolframelektrode des Schweißbrenners spannungsführend. Darauf achten, dass die Wolframelektrode keine Personen oder elektrisch leitenden oder geerdeten Teile berührt (z.B. Gehäuse, etc.) 1. Netzschalter (8) in Stellung - I - schalten (sämtliche Anzeigen am Bedienpanel leuchten kurz auf) 2. Mit Taste Verfahren (3) das Verfahren WIG-Schweißen anwählen - Schweißspannung wird mit einer Verzögerung von 3 s auf die Schweißbuchse geschaltet. HINWEIS! Parameter, die an der Fernbedienung TR 2000 / 3000 / 4000 einstellbar sind, können nicht an der Stromquelle geändert werden. Parameteränderungen können nur an der Fernbedienung TR 2000 / 3000 / 4000 erfolgen. 3. 4. 5. Taste Parameteranwahl (2) drücken (Anzeige an der Taste muss leuchten) Mit Einstellrad (1) gewünschte Stromstärke einstellen (Wert kann an der linken Anzeige abgelesen werden) Gas-Sperrventil am WIG Gasschieber-Brenner öffnen und am Druckminderer gewünschte Schutzgas-Menge einstellen HINWEIS! Die Zündung des Lichtbogens erfolgt durch Werkstück-Berührung der Wolframelektrode. 22 WIG-Schweißen (Fortsetzung) 6. 7. 8. Gasdüse an der Zündstelle aufsetzen, sodass zwischen Wolframelektrode und Werkstück 2-3 mm Abstand bestehen (Abb.28a) Schweißbrenner langsam aufrichten bis die Wolframelektrode das Werkstück berührt (Abb.28b) Schweißbrenner anheben und in Normallage schwenken - Lichtbogen zündet (Abb.28c) a) Gasdüse aufsetzen b) Zünden durch Werkstückberührung c) Lichtbogen gezündet Abb.28 Lichtbogen zünden 9. Schweißung durchführen HINWEIS! Die zum Schutz von Wolframelektrode und Schweißung erforderliche Gas-Nachstömzeit nach Schweißende hängt vom Schweißstrom ab. Schweißstrom Gas-Nachströmzeit 50 A 6s 100 A 7s 150 A 8s 200 A 9s 250 A 12 s 300 A 13 s 350 A 14 s 400 A 16 s 10. Zum Beenden des Schweißvorganges WIG Gasschieber-Brenner vom Werkstück abheben, bis Lichtbogen erlischt. 11. Nach Schweißende Gas-Nachströmzeit entsprechend der Richtwerte in der Tabelle abwarten 12. Gas-Sperrventil am WIG Gasschieber-Schweißbrenner schließen Grundsätzlich bleiben sämtliche mittels Einstellrad (1) eingestellten Parameter-Sollwerte bis zur nächsten Änderung gespeichert. Dies gilt auch, wenn die Stromquelle zwischenzeitlich aus- und wieder eingeschaltet wurde. 23 Wichtig! Die Aktivierung und Einstellung der Option TIG-Comfort-Stop erfolgt mittels Parameter CSS. Der Parmeter CSS ist im „Setup-Menü - Ebene 2“ untergebracht. 1. 2. 3. 4. 1. 2. 3. 4. 5. Schweißen Schweißbrenner heben: Lichtbogen wird deutlich verlängert Schweißbrenner absenken: - Lichtbogen wird deutlich verkürzt - Funktion TIG-Comfort-Stop hat ausgelöst Höhe des Schweißbrenners beibehalten - Schweißstrom wird rampenförmig abgesenkt (Downslope) - Lichtbogen erlischt Gas-Nachströmzeit abwarten und Schweißbrenner vom Werkstück abheben I eingestellter Schweißstrom t Downslope Gas-Vorströmung Abb.30 Ablauf WIG-Schweißen bei aktivierter Option TIG-Comfort-Stop 24 Gas-Nachströmung Das Setup-Menü: Ebene 1 Allgemeines Es steckt bereits eine Menge an Expertenwissen in den digitalen Stromquellen. Jederzeit kann auf optimierte, im Gerät abgespeicherte Parameter zurückgegriffen werden. Das Setup-Menü bietet einfachen Zugriff auf dieses Expertenwissen sowie einige zusätzliche Funktionen. Es ermöglicht eine einfache Anpassung der Parameter an die unterschiedlichen Aufgabenstellungen. In das SetupMenü für Parameter Verfahren einsteigen HINWEIS! Die Funktionsweise wird anhand des Verfahrens „StabelektrodenSchweißen“ erklärt. Die Vorgangsweise beim Ändern anderer Parameter Verfahren ist ident. Die verfügbaren Parameter können für sämtliche Verfahren, welche mittels Taste Verfahren (3) anwählbar sind, gesondert eingestellt werden. Die Parameter-Einstellungen bleiben so lange gespeichert, bis der jeweilige Einstellwert abgeändert wird. 1. 2. 3. 4. 5. 6. Netzstecker einstecken Netzschalter (8) in Stellung - I - schalten Mit Taste Verfahren (3) das Verfahren „Stabelektroden-Schweißen“ anwählen Taste Setup / Store (7) drücken und halten Taste Verfahren (3) drücken Taste Setup / Store (7) loslassen Die Stromquelle befindet sich nun im Setup-Menü des Verfahrens „StabelektrodenSchweißen“ - der erste Parameter HCU (Hotstartstrom) wird angezeigt. Parameter ändern 1. 2. Mit der Taste Verfahren (3) den gewünschten Parameter anwählen Mit dem Einstellrad (1) den Wert des Parameters ändern Das Setup-Menü verlassen 1. Taste Setup / Store (7) drücken HINWEIS! Änderungen werden durch Verlassen des SetupMenüs gespeichert. Das Setup-Menü für die Verfahren „Stabelektroden-Schweißen mit CEL-Elektrode“ und „Spezial-Verfahren“ ist identisch mit dem Menü für das Verfahren „Stabelektroden-Schweißen“. HINWEIS! Eine vollständige Auflistung der Parameter für das Verfahren „StabelektrodenSchweißen“ befindet sich im Kapitel „Parameter Verfahren“. Abb.31 Beispiel für das Verfahren „StabelektrodenSchweißen“ 25 Parameter StabelektrodenSchweißen Die Funktion HCU (Hotstart-Strom) und der verfügbare Einstellbereich wird im Kapitel „Stabelektroden-Schweißen“ beschrieben. HCU Hot-start current - Hotstart-Strom Einheit Einstellbereich Werkseinstellung m/min 0 - 100 % 50 % Hti Hot-current time - Hotstrom-Zeit Einheit Einstellbereich Werkseinstellung m/min 0 - 2,0 s 0,5 s FAC Factory - Stromquelle zurücksetzen Taste Setup / Store (7) 2 s gedrückt halten, um Auslieferungszustand wieder herzustellen - wird am Display „PrG“ angezeigt, ist die Stromquelle zurück gesetzt HINWEIS! Wird die Stromquelle zurückgesetzt, gehen alle persönlichen Einstellungen im Setup-Menü: Ebene 1 verloren. Auch die Funktionen der zweiten Ebene des Setup-Menüs (2nd) werden nicht gelöscht. 2nd zweite Ebene des Setup-Menüs (siehe Kapitel „Das Setup-Menü: Ebene 2“) WIG-Schweißen 2nd zweite Ebene des Setup-Menüs (siehe Kapitel „Das Setup-Menü: Ebene 26 2“) Das Setup-Menü: Ebene 2 Allgemeines Die Funktionen Eln (Kennlinien-Auswahl), r (Schweißkreis-Widerstand), L (Anzeige Schweißkreis-Induktivität) und ASt (Anti-Stick) wurden in einer zweiten Menüebene untergebracht. In zweite Menüebene (2nd) wechseln 1. 2. 3. 4. Wie im Kapitel „Das Setup-Menü: Ebene 1“ beschrieben, den Parameter „2nd“ anwählen Taste Setup / Store (7) drücken und halten Taste Verfahren (3) drücken Taste Setup / Store (7) loslassen Die Stromquelle befindet sich nun in der zweiten Menüebene (2nd) des Setup-Menüs. Die Funktion „Eln“ (Kennlinien-Auswahl) wird angezeigt. Parameter ändern 1. 2. Mit der Taste Verfahren (3) den gewünschten Parameter anwählen Mit dem Einstellrad (1) den Wert des Parameters ändern 1. Das Setup-Menü verlassen Taste Setup / Store (7) drücken HINWEIS! Änderungen werden durch Verlassen der zweiten Menüebene (2nd) gespeichert. HINWEIS! Eine vollständige Auflistung der Parameter für das Setup-Menü, Ebene 2, befindet sich im Kapitel „Parameter 2nd“. Abb.32Setup-Menü, Ebene 2 27 Parameter 2nd Allgemeines Parameter 2nd HINWEIS! Für das Verfahren WIG-Schweißen stehen nur die Parameter r (Schweißkreis-Widerstand) und L (Schweißkreis-Induktivität) zur Verfügung. Die Funktion Eln (Kennlinien-Auswahl) kann für die Verfahren „Stabelektroden-Schweißen“, „Stabelektroden-Schweißen mit CEL-Elektrode“ und „Spezial-Verfahren“ gesondert eingestellt werden. Die Einstellung bleibt so lange gespeichert, bis der jeweilige Einstellwert abgeändert wird. Die Funktion Eln (Kennlinien-Auswahl) und die verfügbaren Einstellungen werden im Kapitel „Stabelektroden-Schweißen“ beschrieben. Eln Electrode-line - Kennlinien-Auswahl - con / 0,1 - 20 / P Werkseinstellung: für Verfahren Stabelektroden-Schweißen: con für Verfahren Stabelektroden-Schweißen mit CEL-Elektrode: P für Spezial-Verfahren: con Die Funktion r (Schweißkreis-Widerstand) wird im Kapitel „Schweißkreis-Widerstand ermitteln“ beschrieben. CSS Comfort Stop Sensitivity - Empfindlichkeit des Ansprechverhaltens von TIG-ComfortStop: 0,5 - 5,0 / Werkeinstellung: OFF Wichtig! Als Richtwert für den Parameter CSS ist ein Einstellwert von 2,0 empfehlenswert. Kommt es jedoch häufig zu einem ungewollten Beenden des Schweißvorganges, den Parameter CSS auf einen höheren Wert einstellen. Je nach Wert des Parameters CSS ist zum Auslösen der Funktion Tig-Comfort-Stop eine bestimmte Verlängerung des Lichtbogens erforderlich: bei CSS = 0,5 - 2,0 geringe Verlängerung des Lichtbogens bei CSS = 2,0 - 3,5 mittlere Verlängerung des Lichtbogens bei CSS = 3,5 - 5,0 große Verlängerung des Lichtbogens r r (resistance) - Schweißkreis-Widerstand- x Milliohm(z.B. 11,4 Milliohm) Die Funktion L (Schweißkreis-Induktivität) wird im Kapitel „Schweißkreis-Induktivität L anzeigen“ beschrieben. L L (inductivity) - Schweißkreis-Induktivität - x Mikrohenry (z.B. 5 Mikrohenry) Die Funktion Ast (Anti-Stick) wird im Kapitel Stabelektroden-Schweißen beschrieben. ASt Anti-Stick - On / OFF Werkseinstellung: ON 28 Schweißkreis-Widerstand r ermitteln Allgemeines Durch die Ermittlung des Schweißkreis-Widerstand r ist es möglich, auch bei unterschiedlichen Schweißkabel-Längen immer ein gleichbleibendes Schweißergebnis zu erzielen; die Schweißspannung am Lichtbogen ist unabhängig von Schweißkabel-Länge und -Querschnitt immer exakt geregelt. Der Schweißkreis-Widerstand wird nach der Ermittlung am rechten Display angezeigt. r ... Schweißkreis-Widerstand... x Milliohm (z.B. 11,4 Milliohm) Die Schweißspannung entspricht bei korrekt durchgeführter Ermittlung des Schweißkreis-Widerstandes r exakt der Schweißspannung am Lichtbogen. Wird die Spannung an den Ausgangsbuchsen der Stromquelle manuell gemessen, so ist diese um den Spannungsabfall des „Kabels Schweißpotential“ höher als die Schweißspannung am Lichtbogen. HINWEIS! Der Schweißkreis-Widerstand r ist abhängig von den verwendeten Schweißkabeln. Die Ermittlung des Schweißkreis-Widerstandes r ist daher SchweißkreisWiderstand r ermitteln - bei einer Änderung von Schweißkabel-Länge oder -Querschnitt zu wiederholen für jedes Schweißverfahren (mit den zugehörigen Schweißkabeln) separat durchzuführen 1. Masseverbindung mit Werkstück herstellen HINWEIS! Stellen Sie sicher, dass der Kontakt „Masseklemme - Werkstück“ auf gereinigter Werkstück-Oberfläche erfolgt. 2. 3. 4. Netzstecker einstecken Netzschalter (8) in Stellung - I - schalten Funktion „r“ in der zweiten Menüebene (2nd) anwählen 5. Elektrodenhalter oder Spannkörper für Wolframelektrode fest an das Werkstück klemmen oder fest gegen das Werkstück drücken HINWEIS! Stellen Sie sicher, dass der Kontakt „Stabelektrode oder Wolframelektrode“ auf gereinigter Werkstück-Oberfläche erfolgt. 29 6. Taste Setup / Store (7) kurz drücken Schweißkreis-Widerstand wird errechnet; während der Messung wird am rechten Display „run“ angezeigt 7. Messung ist abgeschlossen, wenn am rechten Display der SchweißkreisWiderstand angezeigt wird (z.B. 11,4 Milliohm) Schweißkreis-Induktivität L anzeigen SchweißkreisInduktivität L anzeigen Die Verlegung der Schweißkabel hat wesentliche Auswirkungen auf die Schweißeigenschaften. Abhängig von Länge und Verlegung der Schweißkabel, kann eine hohe Schweißkreis-Induktivität entstehen - der Stromanstieg während des Tropfenüberganges wird begrenzt. Die Schweißkreis-Induktivität L wird während des Schweißvorganges errechnet und am rechten Display angezeigt. Abb.33Korrekte Verlegung eines Schweißkabels L ... Schweißkreis-Induktivität ... x Mikrohenry (z.B. 5 Mikrohenry) HINWEIS! Eine Kompensation der Schweißkreis-Induktivität kann nicht erfolgen. Es muss versucht werden, das Schweißergebnis durch korrekte Verlegung der Schweißkabel zu ändern. 30 Fehlerdiagnose und Fehlerbehebung Allgemeines Die digitalen Stromquellen sind mit einem intelligenten Sicherheitssystem ausgestattet; auf die Verwendung von Schmelzsicherungen konnte daher zur Gänze verzichtet werden. Nach der Beseitigung einer möglichen Störung kann die Stromquelle - ohne den Wechsel von Schmelzsicherungen - wieder ordnungsgemäß betrieben werden. WARNUNG! Ein elektrischer Schlag kann tödlich sein. Vor Öffnen des Gerätes Netzschalter in Stellung - O - schalten Gerät vom Netz trennen ein verständliches Warnschild gegen Wiedereinschalten anbringen mit Hilfe eines geeigneten Messgerätes sicherstellen, dass elektrisch geladene Bauteile (z.B. Kondensatoren) entladen sind VORSICHT! Unzureichende Schutzleiter-Verbindung kann schwerwiegende Personen- und Sachschäden verursachen. Die Gehäuse-Schrauben stellen eine geeignete Schutzleiter-Verbindung für die Erdung des Gehäuses dar und dürfen keinesfalls durch andere Schrauben ohne zuverlässige Schutzleiterverbindung ersetzt werden. Angezeigte Service-Codes HINWEIS! Erscheint eine hier nicht angeführte Fehlermeldung an den Anzeigen ist der Fehler nur durch den Servicedienst zu beheben. Notieren Sie die angezeigte Fehlermeldung sowie Seriennummer und Konfiguration der Stromquelle und verständigen Sie den Servicedienst mit einer detaillierten Fehlerbeschreibung. tP1 | xxx, tP2 | xxx, tP3 | xxx tP4 | xxx, tP5 | xxx, tP6 | xxx (xxx steht für eine Temperaturanzeige) Ursache: Übertemperatur im Primärkreis der Stromquelle Behebung: Stromquelle abkühlen lassen tS1 | xxx, tS2 | xxx, tS3 | xxx (xxx steht für eine Temperaturanzeige) Ursache: Übertemperatur im Sekundärkreis der Stromquelle Behebung: Stromquelle abkühlen lassen tSt | xxx (xxx steht für eine Temperaturanzeige) Ursache: Übertemperatur im Steuerkreis Behebung: Stromquelle abkühlen lassen Err | 049 Ursache: Phasenausfall Behebung: Netzabsicherung, Netzzuleitung und Netzstecker kontrollieren Err | 051 Ursache: Netz-Unterspannung: Netzspannung hat den Toleranzbereich (+/- 15%) unterschritten Behebung: Netzspannung kontrollieren 31 Angezeigte Service-Codes (Fortsetzung) Err | 052 Ursache: Netz-Überspannung: Netzspannung hat den Toleranzbereich (+/- 15%) überschritten Behebung: Netzspannung kontrollieren Err | PE Ursache: Die Erdstrom-Überwachung hat die Sicherheitsabschaltung der Stromquelle ausgelöst. Behebung: Stromquelle ausschalten, 10 Sekunden warten und anschließend wieder einschalten; Fehler tritt trotz mehrmaliger Versuche erneut auf - Servicedienst verständigen Err | bPS, Err | IP, dSP | Axx dSP | Cxx, dSP | Exx, dSP | Sy dSP | nSy Ursache: Die Erdstrom-Überwachung hat die Sicherheitsabschaltung der Stromquelle ausgelöst. Behebung: Stromquelle ausschalten, 10 Sekunden warten und anschließend wieder einschalten; Fehler tritt trotz mehrmaliger Versuche erneut auf - Servicedienst verständigen r | E30 Ursache: r-Abgleich: kein Kontakt zum Werkstück vorhanden Behebung: Stromquelle ausschalten, 10 Sekunden warten und anschließend wieder Massekabel anschließen; Satte Verbindung zwischen Elektrodenhalter und Werkstück herstellen r | E31 Ursache: r-Abgleich: Vorgang wurde durch wiederholtes Drücken der Taste Setup / Store (7) unterbrochen Behebung: Satte Verbindung zwischen Elektrodenhalter oder Spannkörper für Wolframelektrode und Werkstück herstellen - Taste Setup / Store (7) einmal drücken r | E33, r | E34 Ursache: r-Abgleich: Schlechter Kontakt zwischen Elektrodenhalter oder Spannkörper für Wolframelektrode und Werkstück Behebung: Kontaktstelle säubern, Elektrodenhalter oder Spannkörper für Wolframelektrode fest anklemmen oder gegen das Werkstück drücken, Masseverbindung überprüfen Kein Schweißstrom Netzschalter eingeschaltet, Anzeige Übertemperatur leuchtet Ursache: Lüfter in der Stromquelle defekt Behebung: Lüfter wechseln Kein Schweißstrom Netzschalter eingeschaltet, Anzeigen leuchten Ursache: Masseanschluss falsch Behebung: Masseanschluss und Klemme auf Polarität überprüfen Ursache: Stromkabel im WIG Gasschieber-Brenner unterbrochen Behebung: WIG Gasschieber-Brenner tauschen 32 Stromquelle TP 4000 CEL / TP 5000 CEL (Fortsetzung) Kein Schutzgas alle anderen Funktionen vorhanden Ursache: Gasflasche leer Behebung: Gasflasche wechseln Ursache: Gas-Druckminderer defekt Behebung: Gas-Druckminderer tauschen Ursache: Gasschlauch nicht montiert od. schadhaft Behebung: Gasschlauch montieren od. tauschen Ursache: WIG Gasschieber-Brenner defekt Behebung: WIG Gasschieber-Brenner tauschen Schlechte Schweißeigenschaften Ursache: falsche Schweißparameter Behebung: Einstellungen überprüfen Ursache: Masseverbindung schlecht Behebung: guten Kontakt zum Werkstück herstellen Ursache: kein oder zuwenig Schutzgas Behebung: Druckminderer, Gasschlauch, Brenner-Gasanschluss, etc. überprüfen Ursache: Schweißbrenner undicht Behebung: Schweißbrenner wechseln Schlechte Schweißeigenschaften zusätzlich starke Spritzerbildung Ursache: falsche Polung der Elektrode Behebung: Elektrode umpolen (siehe Angaben Hersteller) Schweißbrenner wird sehr heiß Ursache: Schweißbrenner zu schwach dimensioniert Behebung: Einschaltdauer und Belastungsgrenzen beachten Stromquelle hat keine Funktion Netzschalter eingeschaltet, Anzeigen leuchten nicht Ursache: Netzzuleitung unterbrochen, Netzstecker nicht eingesteckt Behebung: Netzzuleitung überprüfen, ev. Netzstecker einstecken Ursache: Netzabsicherung defekt Behebung: Netzabsicherung wechseln Ursache: Netzsteckdose oder -stecker defekt Behebung: defekte Teile austauschen Kein Schweißstrom Netzschalter eingeschaltet, Anzeige Übertemperatur leuchtet Ursache: Überlastung, Einschaltdauer überschritten Behebung: Einschaltdauer berücksichtigen Ursache: Thermo-Sicherheitsautomatik hat abgeschaltet Behebung: Abkühlphase abwarten; Stromquelle schaltet nach kurzer Zeit selbstständig wieder ein 33 Pflege, Wartung und Entsorgung Allgemeines Die Stromquelle benötigt unter normalen Betriebsbedingungen nur ein Minimum an Pflege und Wartung. Das Beachten einiger Punkte ist jedoch unerlässlich, um die Stromquelle über Jahre hinweg einsatzbereit zu halten. WARNUNG! Ein elektrischer Schlag kann tödlich sein. Vor Öffnen des Gerätes Netzschalter in Stellung - O - schalten Gerät vom Netz trennen ein verständliches Warnschild gegen Wiedereinschalten anbringen mit Hilfe eines geeigneten Messgerätes sicherstellen, dass elektrisch geladene Bauteile (z.B. Kondensatoren) entladen sind Bei jeder Inbetriebnahme - Netzstecker und Netzkabel sowie Elektrodenkabel, Schweißbrenner und Masseverbindung auf Beschädigung prüfen Prüfen, ob der Rundumabstand des Gerätes 0,5 m (1 ft. 8 in.) beträgt, damit die Kühlluft ungehindert zuströmen und entweichen kann HINWEIS! Zusätzlich dürfen die Lufteintritts- und Austrittsöffnungen keinesfalls verdeckt sein, auch nicht teilweise. Alle 2 Monate - Falls vorhanden: Luftfilter reinigen Alle 6 Monate - Geräte-Seitenteile demontieren und das Geräteinnere mit trockener, reduzierter Druckluft sauberblasen HINWEIS! Gefahr der Beschädigung elektronischer Bauteile. Elektronische Bauteile nicht aus kurzer Entfernung anblasen. - Entsorgung Bei starkem Staubanfall auch die Kühlluftkanäle reinigen Die Entsorgung nur gemäß den geltenden nationalen und regionalen Bestimmungen durchführen. 34 Technische Daten Allgemeines TP 4000 CEL HINWEIS! Ist die Stromquelle für eine Sonderspannung ausgelegt, gelten die Technischen Daten am Leistungsschild. Netzstecker, Netzzuleitung sowie deren Absicherung sind entsprechend auszulegen. Netzspannung 3x400 V Netzspannungs-Toleranz +/- 15 Netzabsicherung Primär-Dauerleistung 35 A träge (100 % ED) 12,9 kVA Cos Phi 0,99 Wirkungsgrad 90 % Schweißstrom-Bereich Stabelektrode WIG 10-380 A 10-380 A 40 % ED 60 % ED 100 % ED 380 A 360 A 320 A genormte Arbeitsspannung Stabelektrode WIG 20,4 - 35,2 V 14,5 - 33 V maximale Arbeitsspannung Stabelektrode 53 V (380 A) 80 V (10 A) Leerlauf-Spannung gepulst Scheitelwert Mittelwert Schweißstrom bei 10 min / 40°C 10 min / 40°C 10 min / 40°C 95 V 60 V Schutzart IP 23 Prüfzeichen S, CE Kühlart AF Isolationsklasse F Maße l / b / h mm 625/290/475 Gewicht 36,1 kg 35 Netzspannung 3x200-240 V 3x380-460 V Netzspannungs-Toleranz +/- 10% Netzabsicherung Primär-Dauerleistung 200-240 V: 63 A 380-460 V: 35 A (100 % ED) 12,9 kVA Cos Phi 0,99 Wirkungsgrad 90 % Schweißstrom-Bereich Stabelektrode WIG 10-380 A 10-380 A 40 % ED 60 % ED 100 % ED 380 A 360 A 320 A genormte Arbeitsspannung Stabelektrode WIG 20,4 - 35,2 V 14,5 - 33 V maximale Arbeitsspannung Stabelektrode 53 V (380 A) 80 V (10 A) Leerlauf-Spannung gepulst Scheitelwert Mittelwert Schweißstrom bei 10 min / 40°C 10 min / 40°C 10 min / 40°C Schutzart IP 23 Prüfzeichen S, CE Kühlart AF Isolationsklasse F Maße l / b / h mm 625/290/475 Gewicht TP 5000 CEL 95 V 60 V 40 kg Netzspannung 3x400 V Netzspannungs-Toleranz +/- 15 Netzabsicherung Primär-Dauerleistung 35 A träge (100 % ED) 16,3 kVA Cos Phi 0,99 Wirkungsgrad 90 % Schweißstrom-Bereich Stabelektrode WIG 10-480 A 10-480 A 40 % ED 60 % ED 100 % ED 480 A 415 A 360 A genormte Arbeitsspannung Stabelektrode WIG 20,4 - 39,2 V 14,5 - 38 V maximale Arbeitsspannung Stabelektrode 48 V (480 A) 80 V (10 A) Leerlauf-Spannung gepulst Scheitelwert Mittelwert Schweißstrom bei 10 min / 40°C 10 min / 40°C 10 min / 40°C 95 V 60 V Schutzart IP 23 Prüfzeichen S, CE Kühlart AF Isolationsklasse F Maße l / b / h mm 625/290/475 Gewicht 37 kg 36 Netzspannung 3x200-240 V 3x380-460 V Netzspannungs-Toleranz +/- 10% Netzabsicherung Primär-Dauerleistung 200-240 V: 63 A 380-460 V: 35 A (100 % ED) 16,3 kVA Cos Phi 0,99 Wirkungsgrad 90 % Schweißstrom-Bereich Stabelektrode WIG 10-480 A 10-480 A 40 % ED 60 % ED 100 % ED 480 A 415 A 360 A genormte Arbeitsspannung Stabelektrode WIG 20,4 - 39,2 V 14,5 - 38 V maximale Arbeitsspannung Stabelektrode 48 V (480 A) 80 V (10 A) Leerlauf-Spannung gepulst Scheitelwert Mittelwert Schweißstrom bei 10 min / 40°C 10 min / 40°C 10 min / 40°C 95 V 60 V Schutzart IP 23 Prüfzeichen S, CE Kühlart AF Isolationsklasse F Maße l / b / h mm 625/290/475 Gewicht 40,5 kg 37 38 ud_fr_st_et_00493 012004 WARNING! NOTE! Important! General remarks I ud_fr_st_sv_00467 012007 General remarks (continued) - ud_fr_st_sv_00467 012007 II - - - III ud_fr_st_sv_00467 012007 ud_fr_st_sv_00467 012007 IV Hazards from flying sparks V ud_fr_st_sv_00467 012007 ud_fr_st_sv_00467 012007 VI Particular danger spots VII ud_fr_st_sv_00467 012007 ud_fr_st_sv_00467 012007 VIII Danger from shielding-gas cylinders IX ud_fr_st_sv_00467 012007 ud_fr_st_sv_00467 012007 X Disposal Safety markings Data security XI ud_fr_st_sv_00467 012007 ud_fr_st_sv_00467 012007 XII 3 3 3 3 12 12 12 13 14 14 14 14 14 15 15 15 16 17 18 18 18 19 19 21 22 22 22 24 25 25 25 25 25 1 27 27 27 27 31 31 31 32 2 35 35 35 36 36 37 Fig.1 Machine concept 3 (2) (9) Fig.2 (6) (4) (11)(10) (12) (3) (7) Control panel 4 (1) (5) (3) (8) 5 6 (E) (F) (A) (B) (C) (D) (G) TR 2000 remote control unit (25) TR 2000 remote control unit 7 TR 3000 remotecontrol unit (27)(26) (28) Fig.5 (29) Fig.6 (30) (32) Fig.7 (31) 8 TR 3000 remotecontrol unit (continued ) TR 4000 remotecontrol unit (33) (34) (35) (36) Fig.8 TR 4000 remote-control unit Fig.9 Fig.10 TR 1100 remote-control unit TR 1000 remote-control unit 9 TR 1000 / TR 1100 remote-control unit (continued) (38) (37) (38)(37) (39) Fig.11 TR 1000 / TR 1100 control panel TP 08 remotecontrol unit (ZP)(ZQ) (ZN)(ZR) 1. 2. 3. (ZL) (ZL) Fig.12 TP 08 remote-control unit 10 TP 08 remotecontrol unit (continued) 11 Fig.13 LocalNet distributor - passive (57) (57) (56) 12 TR 3000 (32) (32) 13 14 1. (1) (1) 2. 6. X 15 (2)(3) (4) 7. (4) 8. 9. (3) (3) (3) (1) (2) (2)(1) (2) (2) (3) (1) (1) Fig.21 Handle plates and handle tube (6) (7) (8) 1. 2. 3. 4. 16 (1) 2. . 17 Rod electrode welding 18 Legend: Hti 300A HCU IH HCU Hti 200A IH 0,5 s Fig. 25 1s 1,5 s t 19 ELN function (electrode-line selection) (continued) con - 20 A/V 50 (4) (6) (2) (1) (3) (5) 40 30 20 (7) (8) 10 0 0 50 100 150 200 250 300 350 400 450 I (A) 20 ELN function (electrode-line selection) (continued) U (V) 60 (6) (2) 50 (1) 40 (3) (5) 30 20 (4) (8) 10 0 0 50 100 150 200 250 300 350 400 450 I (A) IH - 50 % IH + Dynamik 21 TIG welding General remarks TIG welding 2. 3. 4. 5. 22 6. 7. 8. a) Place gas nozzle on workpiece 9. 50 A 6s 100 A 7s 150 A 8s 200 A 9s 250 A 12 s 300 A 13 s 350 A 14 s 400 A 16 s 23 2. 3. 4. Fig.29 TIG-Comfort-Stop 1. 2. 3. 4. 5. I 24 1. 2. 1. Fig.31 25 TIG welding 26 - 1. 27 Parameters 2nd General remarks Parameter 2nd 28 - 1. 2. 3. 4. 29 6. 7. 30 Err | 049 Cause: Remedy: Err | 051 Cause: Remedy: 31 Err | 052 Cause: Remedy: Err | PE Cause: Remedy: Err | bPS, Err | IP, dSP | Axx dSP | Cxx, dSP | Exx, dSP | Sy dSP | nSy Cause: Remedy: r | E30 r Remedy: | E33, r Cause: Remedy: | E31 Cause: r Mains fuse is faulty Change mains fuse 32 Poor welding properties Cause: Remedy: 33 - 34 Mains voltage 3x400 V Mains voltage tolerance +/- 15 % 35 A 12.9 kVA Cos Phi 0,99 Efficiency 90 % Rod electrode TIG 10 min / 40°C 10 min / 40°C 10 min / 40°C 40 % duty cycle 60 % duty cycle 100 % duty cycle 10 - 380 A 10 - 380 A 380 A 360 A 320 A Standard working voltage Rod electrode TIG 20.4 - 35.2 V 14.5 - 33 V Max. working voltage Rod electrode 53 V (380 A) 80 V (10 A) Open-circuit voltage pulsed peak value mean value 95 V 60 V IP 23 AF F 625/290/475 Weight 36.1 kg 35 Mains voltage 3x200-240 V 3x380-460 V Mains voltage tolerance +/- 10 % 200-240 V: 63 A 380-460 V: 35 A 0,99 12,9 kVA 90 % 10 min / 40°C 10 min / 40°C 10 min / 40°C 40 % duty cycle 60 % duty cycle 100 % duty cycle Standard working voltage Rod electrode TIG 20.4 - 35.2 V 14.5 - 33 V Max. working voltage Rod electrode 53 V (380 A) 80 V (10 A) Open-circuit voltage pulsed peak value mean value 95 V 60 V IP 23 AF F 625/290/475 Weight TP 5000 CEL 380 A 360 A 320 A 40 kg Mains voltage 3x400 V Mains voltage tolerance +/- 15 % 35 A 16.3 kVA Cos Phi 0,99 Efficiency 90 % Rod electrode TIG 10 min / 40°C 10 min / 40°C 10 min / 40°C 40 % duty cycle 60 % duty cycle 100 % duty cycle 10 - 480 A 10 - 480 A 380 A 360 A 320 A Standard working voltage Rod electrode TIG 20.4 - 39.2 V 14.5 - 38 V Max. working voltage Rod electrode 48 V (480 A) 80 V (10 A) Open-circuit voltage pulsed peak value mean value 95 V 60 V IP 23 AF F 625/290/475 Weight 37 kg 36 Mains voltage 3x200-240 V 3x380-460 V Mains voltage tolerance +/- 10 % 200-240 V: 63 A 380-460 V: 35 A 16.3 kVA Cos Phi 0,99 Efficiency 90 % Rod electrode TIG 10 min / 40°C 10 min / 40°C 10 min / 40°C 40 % duty cycle 60 % duty cycle 100 % duty cycle 10 - 480 A 10 - 480 A 480 A 415 A 360 A Standard working voltage Rod electrode TIG 20.4 - 39.2 V 14.5 - 38 V Max. working voltage Rod electrode 48 V (480 A) 80 V (10 A) Open-circuit voltage pulsed peak value mean value 95 V 60 V IP 23 AF F 625/290/475 Weight 40.5 kg 37 38 ud_fr_st_et_00500 012006 AVERTISSEMENT! ATTENTION! REMARQUE! Important! ud_fr_st_sv_00468 012007 ud_fr_st_sv_00468 012007 II - - - III ud_fr_st_sv_00468 012007 ud_fr_st_sv_00468 012007 IV V ud_fr_st_sv_00468 012007 Courants de soudage vagabonds ud_fr_st_sv_00468 012007 VI ud_fr_st_sv_00468 012007 ud_fr_st_sv_00468 012007 VIII ud_fr_st_sv_00468 012007 - ud_fr_st_sv_00468 012007 X Élimination XI ud_fr_st_sv_00468 012007 ud_fr_st_sv_00468 012007 XII 3 3 3 3 12 12 12 13 14 14 14 14 14 15 15 15 16 17 18 18 18 19 19 21 22 22 22 24 25 25 25 25 25 1 27 27 27 27 2 36 36 36 37 37 38 Installation de soudage TP 4000 CEL / TP 5000 CEL 3 (2) (6) (4) (9) Fig.2 (11)(10) (12) (3) (7) 4 (1) (5) (3) (8) 5 6 Raccords Source de courant TP 4000 CEL / TP 5000 CEL (E) (F) (A) Fig.3 (B) (C) (D) (G) (24) (25) Fig.4 7 (27)(26) (28) (29) Fig.6 (30) (32) (31) 8 Fig.8 Fig.9 9 (38) (37) (38)(37) (39) (ZP)(ZQ) (ZN)(ZR) 1. 2. 3. (ZL) (ZL) 10 11 (57) (57) (56) 12 Inverseur TR 3000 (32) (32) 13 14 (1) 1. (1) 2. Fig. 16 Placer les dispositifs de blocage 6. X 15 (4) 7. (4) 8. 9. (3) (3) (3) (1) (2) (2)(1) (2) (2) (3) (1) (1) (6) (7) (8) 1. 2. 3. 4. (11) 2. 17 4. - Légende : Hti 300A IH HCU 200A IH 0,5 s 1s 1,5 s t 19 con - 20 A/V 50 (4) (6) (2) (1) (3) (5) 40 30 20 (7) (8) 10 0 0 50 100 150 200 250 300 350 400 450 I (A) 20 50 (1) 40 (3) (5) 30 20 (4) (8) 10 0 0 50 100 150 200 250 300 350 400 450 I (A) IH - 50 % IH + Dynamik 21 1. 2. 3. 4. 5. 6. 7. 8. 9. Soudage TIG 2. 3. 4. 5. 22 Soudage TIG (suite) c) arc amorçé 9. Temps post-gaz 50 A 6s 100 A 7s 150 A 8s 200 A 9s 250 A 12 s 300 A 13 s 350 A 14 s 400 A 16 s 23 2. 3. 4. 1. 2. 3. 4. 5. I 24 Postflux de gaz - 1. 25 26 1. 2. - 27 Parameter 2nd 28 1. 2. 3. 4. 29 6. 7. 30 31 | E31 | E33, r | E34 32 | E30 33 34 - 35 TP 4000 CEL 3x400 V +/- 15 % 35 A 0,99 Rendement 90 % baguette TIG 40% ED* 60% ED* 100% ED* 10 min/40°C 10 min/40°C 10 min/40°C Tension de travail standard baguette TIG 10 - 380 A 10 - 380 A 380 A 360 A 320 A 95 V 60 V 20,4 - 35,2 V 14,5 - 33 V 53 V (380 A) 80 V (10 A) IP 23 AF 12,9 kVA F 625/290/475 Poids 625/290/475 36,1 kg S, CE 36 3x200-240 V 3x380-460 V +/- 10 % 200-240 V: 63 A 380-460 V: 35 A 0,99 Rendement 90 % baguette TIG 40% ED* 60% ED* 100% ED* 10 min/40°C 10 min/40°C 10 min/40°C Tension de travail standard baguette TIG 380 A 360 A 320 A 95 V 60 V 20,4 - 35,2 V 14,5 - 33 V IP 23 AF Classe d‘isolation 10 - 380 A 10 - 380 A 53 V (380 A) 80 V (10 A) 12,9 kVA F 625/290/475 625/290/475 Poids 40 kg S, CE 3x400 V +/- 15 % 35 A 0,99 Rendement 90 % baguette TIG 40% ED* 60% ED* 100% ED* 10 min/40°C 10 min/40°C 10 min/40°C Tension de travail standard baguette TIG 10 - 480 A 10 - 480 A 480 A 415 A 360 A 95 V 60 V 20,4 - 39,2 V 14,5 - 38 V 48 V (480 A) 80 V (10 A) IP 23 AF 16,3 kVA F 625/290/475 625/290/475 Poids 37 kg Signe d'homologation S, CE 37 3x200-240 V 3x380-460 V +/- 10 % 3x200-240 V 3x380-460 V 0,99 Rendement 90 % baguette TIG 40% ED* 60% ED* 100% ED* 10 min/40°C 10 min/40°C 10 min/40°C Tension de travail standard baguette TIG 10 - 480 A 10 - 480 A 480 A 415 A 360 A 95 V 60 V 20,4 - 39,2 V 14,5 - 38 V 48 V (480 A) 80 V (10 A) IP 23 AF 16,3 kVA F 625/290/475 Poids 625/290/475 40,5 kg Signe d'homologation S, CE 38 D Ersatzteilliste F I Lista parti di ricambio E Lista de repuestos P Lista de peças sobresselentes NL Onderdelenlijst N Reservdelsliste CZ Seznam náhradních dílů RUS Ñïèñîê çàïàñíûõ ÷àñòåé ud_fr_st_tb_00150 012002 Transpocket 4000 CEL Transpocket 5000 CEL Transpocket 4000 MV CEL Transpocket 5000 MV CEL 4,075,111 4,075,113 4,075,111,630 4,075,113,630 42,0200,8860 32,0405,0164 12,0405,0208 AM2,0200,8819 12,0405,0208 45,0200,0918 43,0004,0987 43,0004,0664 - MV 43,0001,1199 - 40A 43,0001,1213 - MV/US 80A 42,0300,1511 42,0407,0437 - MV 4,070,784,Z - TPCEL40 42,0400,0132 BE2,0201,1934 - MV 42,0300,1523 0 L4 CE TP AS U4 41,0005,0288 32,0409,2657 0 41,0003,0203 32,0409,2658 32,0409,2740 - MV 43,0001,1139 33,0005,4112 33,0005,4120 - MV 43,0006,0152 43,0003,0485 4,070,626,Z - NT24A 32,0405,0229 32,0405,0183 42,0406,0093 42,0406,0315 42,0406,0299 NT 43,0002,0358 33,0010,0335 32,0409,2816 S BP 24 A US T2 4,070,860,Z - UST2 43,0006,0168 41,0002,0060 4,070,738,Z - BPS42 4,070,772,Z - BPS53 43,0003,0031 Transpocket 4000/5000 Ersatzteilliste / Spare parts list / Listes de pièces de rechange / Lista de repuestos / Lista de pecas sobresselentes / Lista dei Ricambi el_fr_st_eh_00364 1/1 012005 * gewünschte Länge angeben * Specify the length required * Indiquer la longueur désirée * Indicar la longitud deseada * Indicare la lunghezza desiderat * indicar o comprimento desejado BE4,0460,0038 42,0406,0262 46,0460,0022 42,0400,0105 42,0406,0242 42,0407,0481 42,0406,0224 42,0405,0301 40,0003,0348 * 4,070,791 43,0003,0690 BE4,0460,0037 44,0001,0739 TR 3000 4,046,083 Ersatzteilliste / Spare parts list / Listes de pièces de rechange / Lista de repuestos / Lista de pecas sobresselentes / Lista dei Ricambi el_fr_st_fb_00483 1/1 012002 AM2,0200,9303 AM2,0200,9302 43,0008,0145 22,0405,0163 43,0001,1156 42,0200,6422 42,0201,1068 42,0407,0243 4,055,223 42,0407,0146 45,0200,1140 43,0003,0031 22,0405,0163 42,0407,0437 AM2,0200,9302 43,0004,2294 4,045,883 1/1 012002 CZ 709 00 OSTRAVA - Mariánské Hory, Kollárova 3 Tel: +420 595 693 811 Fax: +420 596 617 223 E-Mail: [email protected] 4600 Wels, Buxbaumstraße 2 Tel: +43 (0)7242 241-0 Fax: +43 (0)7242 241-3490 Service: DW 3070, 3400 Ersatzteile: DW 3390 E-Mail: [email protected] 760 01 ZLÍN ul. Malá (za čerp. st. ARAL) Tel: +420 577 311 011 Fax: +420 577 311 019 E-Mail: [email protected] 6020 Innsbruck, Amraserstraße 56 Tel: +43 (0)512 343275-0 Fax: +43 (0)512 343275-725 5020 Salzburg, Lieferinger Hauptstr.128 Tel: +43 (0)662 430763 Fax: +43 (0)662 430763-16 1100 Wien, Daumegasse 7, Team Süd / Ost Tel: +43 (0)1/600 41 02-7410 Fax: +43 (0)1/600 41 02-7490 Team Nord / West Tel: +43 (0)1/600 41 02-7050 Fax: +43 (0)1/600 41 02-7160 Haberkorn Ulmer GmbH 6961 Wolfurt, Hohe Brücke Tel: +43 (0)5574 695-0 Fax: +43 (0)5574 2139 http://www.haberkorn.com Wilhelm Zultner & Co. 8042 Graz, Schmiedlstraße 7 Tel: +43 (0)316 6095-0 Fax: +43 (0)316 6095-80 Service: DW 325, Ersatzteile: DW 335 E-Mail: [email protected] Wilhelm Zultner & Co. 9020 Klagenfurt, Fallegasse 3 Tel: +43 (0)463 382121-0 Fax: +43 (0)463 382121-40 Service: DW 430, Ersatzteile: DW 431 E-Mail: [email protected] BR FRONIUS do Brasil LTDA Av. Senador Vergueiro, 3260 Vila Tereza, Sao Bernado do Campo - SP CEP 09600-000, SĂO PAULO Tel: +55 (0)11 4368-3355 Fax: +55 (0)11 4177-3660 E-Mail: [email protected] Schweiz AG CH FRONIUS 8153 Rümlang, Oberglatterstraße 11 Tel: +41 (0)1817 9944 Fax: +41 (0)1817 9955 E-Mail: [email protected] CZ FRONIUS Česká republika s.r.o. 381 01 ČESKÝ KRUMLOV, Tovární 170 Tel: +420 380 705 111 Fax: +420 380 711 284 E-Mail: [email protected] 100 00 PRAHA 10, V Olšinách 1022/42 Tel.: +420 272 111 011, 272 742 369 Fax: +420 272 738 145 E-Mail: [email protected] 315 00 PLZEŇ-Božkov, Letkovská 38 Tel: +420 377 183 411 Fax: +420 377 183 419 E-Mail: [email protected] 500 04 HRADEC KRÁLOVÉ, Pražská 293/12 Tel.: +420 495 070 011 Fax: +420 495 070 019 E-Mail: [email protected] 586 01 JIHLAVA, Brněnská 65 Tel: +420 567 584 911 Fax: +420 567 305 978 E-Mail: [email protected] D F N FRONIUS Norge AS SK FRONIUS Deutschland GmbH 36119 Neuhof-Dorfborn bei Fulda, Am Stockgraben 3 Tel: +49 (0)6655 91694-0 Fax: +49 (0)6655 91694-10 E-Mail: [email protected] 57052 Siegen, Alcher Straße 51 Tel: +49 (0)271 37515-0 Fax: +49 (0)271 37515-15 38640 Goslar, Im Schleeke 108 Tel: +49 (0)5321 3413-0 Fax: +49 (0)5321 3413-31 10365 Berlin, Josef-Orlopp-Str. 92-106 Tel: +49 (0)30 557745-0 Fax: +49 (0)30 557745-51 3056 Solbergelva, P.O. BOX 32 Tel: +47 (0)32 232080, Fax: +47 (0)32 232081 E-Mail: [email protected] FRONIUS Slovensko s.r.o. 917 01 Trnava, Nitrianská 5 Tel: +421 (0)33 590 7511 Fax: +421 (0)33 590 7599 E-Mail: [email protected] 974 03 Banská Bystrica, Zvolenská cesta 14 Tel: +421 (0)48 472 0611 Fax: +421 (0)48 472 0699 E-Mail: [email protected] 90530 Wendelstein, Wilhelm-Maisel-Straße 32 Tel: +49 (0)9129 2855-0 Fax: +49 (0)9129 2855-32 51149 Köln, Gremberghoven, Welserstraße 10 b Tel: +49 (0)2203 97701-0 Fax: +49 (0)2203 97701-10 UA 21493 Talkau, Dorfstraße 4 Tel: +49 (0)4156 8120-0 Fax: +49 (0)4156 8120-20 70771 Leinfelden-Echterdingen (Stuttgart), Kolumbus-Straße 47 Tel: +49 (0)711 782852-0 Fax: +49 (0)711 782852-10 04328 Leipzig, Riesaer Straße 72-74 Tel: +49 (0)341 27117-0 Fax: +49 (0)341 27117-10 01723 Kesselsdorf (Dresden), Zum alten Dessauer 13 Tel: +49 (0)35204 7899-0 Fax: +49 (0)35204 7899-10 67753 Hefersweiler, Sonnenstraße 2 Tel: +49 (0)6363 993070 Fax: +49 (0)6363 993072 18059 Rostock, Erich Schlesinger Str. 50 Tel: +49 (0)381 4445802 Fax: +49 (0)381 4445803 81379 München, Gmunder Straße 37a Tel: +49 (0)89 748476-0 Fax: +49 (0)89 748476-10 83308 Trostberg, Pechleraustraße 7 Tel: +49 (0)8621 8065-0 Fax: +49 (0)8621 8065-10 94491 Hengersberg, Donaustraße 31 Tel: +49 (0)9901 2008-0 Fax: +49 (0)9901 2008-10 032006
Werbung
Verwandte Handbücher
Werbung
Inhaltsverzeichnis
- 5 Deutsch
- 57 English
- 109 Français
- 159 Spare Parts List
- 163 Fronius Sales and Service Offices
In anderen Sprachen
Es wurden nur Seiten des dokuments in Deutscher angezeigt