Guide Specifications. Bryant 579F, 580D
Add to My manualsadvertisement
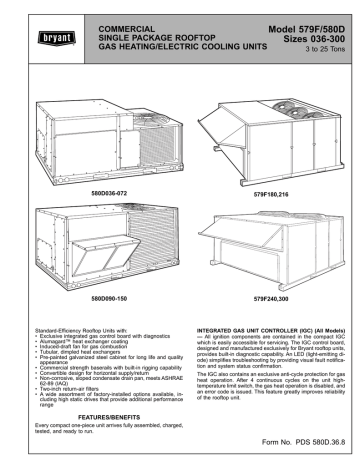
PACKAGED ROOFTOP ELECTRIC COOLING UNIT
WITH GAS HEAT — CONSTANT VOLUME APPLICATION
HVAC GUIDE SPECIFICATIONS
SIZE RANGE: 3 to 12 1 ⁄
2
TONS, NOMINAL (COOLING)
72,000 TO 250,000 BTUH, NOMINAL
(INPUT HEATING)
MODEL NUMBER: 580D
Part 1 — General
1.01 SYSTEM DESCRIPTION
Outdoor rooftop mounted, electrically-controlled heating and cooling unit utilizing a hermetic compressor(s) for cooling duty and gas combustion for heating duty. Unit shall discharge supply air vertically or horizontally as shown on contract drawings.
1.02 QUALITY ASSURANCE
A. Unit shall be rated in accordance with ARI Standards 210/
240 or 360 and 270. Designed in accordance with UL
Standard 1995.
B. Unit shall be designed to conform to ASHRAE 15, latest revision.
C. Unit shall be UL-tested and certified in accordance with ANSI Z21.47 Standards and UL listed and certified under Canadian standards as a total package for safety requirements.
D. Roof curb shall be designed to conform to NRCA
Standards.
E. Insulation and adhesive shall meet NFPA 90A requirements for flame spread and smoke generation.
F. Unit casing shall be capable of withstanding 500-hour salt spray exposure per ASTM B117 (scribed specimen).
G. Unit shall be designed in accordance with ISO 9001, and shall be manufactured in a facility registered to ISO 9002/
BS5750, Part 2.
H. Each 580D unit is subjected to completely automated run testing on the assembly line. Each unit contains a factorysupplied printout indicating tested pressures, amperages, data, and inspectors; providing certification of the unit status at the time of manufacture.
1.03 DELIVERY, STORAGE, AND HANDLING
Unit shall be stored and handled per manufacturer’s recommendations.
Part 2 — Products
2.01 EQUIPMENT (STANDARD)
A. General:
Factory assembled, single-piece heating and cooling unit.
Contained within the unit enclosure shall be all factory wiring, piping, controls, refrigerant charge (R-22), and special features required prior to field start-up.
B. Unit Cabinet:
1. Unit cabinet shall be constructed of galvanized steel, and shall be bonderized and coated with a prepainted baked enamel finish on all externally exposed surfaces.
2. Evaporator fan compartment interior cabinet surfaces shall be insulated with a minimum 1 ⁄
2
-in. thick, flexible fiberglass insulation, coated on the air side. Aluminum foil-faced fiberglass insulation shall be used in the gas heat compartment.
3. Cabinet panels shall be easily removable for servicing.
GUIDE SPECIFICATIONS — 580D036-150
4. Holes shall be provided in the base rails for rigging shackles to facilitate maneuvering and overhead rigging.
5. Unit shall have a factory-installed, sloped condensate drain pan made of a non-corrosive material, providing a minimum 3 ⁄
4
-in. connection with both vertical and horizontal drains, and shall comply with ASHRAE
Standard 62.
6. Unit shall have a factory-installed filter access panel to provide filter access with tool-less removal.
7. Unit shall have standard thru-the-bottom power connection capability.
C. Fans:
1. Evaporator Fan: a.
Fan shall be direct or belt driven as shown on the equipment drawings. Belt drive shall include an adjustable-pitch motor pulley.
b.
Fan wheel shall be double-inlet type with forwardcurved blades.
c.
Bearings shall be sealed, permanently lubricated ball-bearing type for longer life and lower maintenance.
2. Evaporator fan shall be made from steel with a corrosion-resistant finish and shall be dynamically balanced.
3. Condenser fan shall be of the direct-driven propeller type and shall discharge air vertically.
4. Condenser fan shall have aluminum blades riveted to corrosion-resistant steel spiders and shall be dynamically balanced.
5. Induced-draft blower shall be of the direct-driven, single inlet, forward-curved centrifugal type, made from steel with a corrosion-resistant finish and shall be dynamically balanced.
D. Compressor(s):
1. Fully hermetic type, internally protected.
2. Factory spring-shock mounted and internally spring mounted for vibration isolation.
3. On independent mounting circuits (090-150).
E. Coils:
1. Evaporator and condenser coils shall have aluminum plate fins mechanically bonded to copper tubes with all joints brazed.
2. Tube sheet openings shall be belled to prevent tube wear.
3. Evaporator coil shall be of the face-split design which proves effective in removing additional moisture from the supply air.
F. Heating Section:
1. Induced-draft combustion type with energy saving direct-spark ignition system and redundant main gas valve.
2. The heat exchanger shall be of the tubular-section type constructed of a minimum of 20-gage steel coated with a nominal 1.2 mil aluminum-silicone alloy for corrosion resistance.
3. Burners shall be of the in-shot type constructed of aluminum-coated steel.
4. All gas piping shall enter the unit cabinet at a single location.
67
5. The integrated gas controller (IGC) board shall include gas heat operation fault notification using an LED
(light-emitting diode).
6. Unit shall be equipped with anti-cycle protection with one short cycle on unit flame rollout switch or 4 continuous short cycles on the high-temperature limit switch. Fault indication shall be made using an LED.
7. The IGC board shall contain algorithms that modify evaporator-fan operation to prevent future cycling on high-temperature limit switch.
8. The LED shall be visible without removal of control box access panel.
G. Refrigerant Components:
Refrigerant circuit components shall include:
1. Fixed orifice feed system.
2. Refrigerant strainer.
3. Service gage connections on suction, discharge, and liquid lines.
H. Filter Section:
1. Standard filter section shall consist of factoryinstalled, low velocity, throwaway 2-in. thick fiberglass filters of commercially available sizes.
2. Filter face velocity shall not exceed 320 fpm at nominal airflows.
3. Filter section should use only one size filter.
4. Filters shall be accessible through an access panel with ‘‘no-tool’’ removal.
I. Controls and Safeties:
1. Unit Controls:
Unit shall be complete with self-contained low-voltage control circuit protected by an auto-reset device.
2. Safeties: a.
Unit shall incorporate compressor overtemperature and overcurrent safety devices to shut off compressor.
b.
Heating section shall be provided with the following minimum protections:
1) High-temperature limit switch.
2) Induced-draft motor speed sensor.
3) Flame rollout switch.
4) Flame proving controls.
J. Operating Characteristics:
1. Unit shall be capable of starting and running at
115 F ambient outdoor temperature, meeting maximum load criteria of ARI Standard 210/240 or 360.
2. Compressor with standard controls shall be capable of operation down to 25 F ambient outdoor temperature.
K. Electrical Requirements:
All unit power wiring shall enter unit cabinet at a single factory-predrilled location.
L. Motors:
1. Compressor motors shall be cooled by refrigerant gas passing through motor windings and shall have line break thermal and current overload protection.
2. Evaporator-fan motor shall have permanently lubricated bearings and inherent automatic-reset thermal overload protection.
GUIDE SPECIFICATIONS — 580D036-150 (cont)
3. Totally enclosed condenser-fan motor shall have permanently lubricated bearings, and inherent automaticreset thermal overload protection.
4. Induced-draft motor shall have permanently lubricated sealed bearings and inherent automatic-reset thermal overload protection.
M. Special Features:
*
*
*
Certain features are not applicable when the features designated * are specified. For assistance in amending the specifications, contact your local sales office.
1. Roof Curbs (Horizontal and Vertical): a. Formed galvanized steel with wood nailer strip and shall be capable of supporting entire unit weight.
b. Permits installation and securing of ductwork to curb prior to mounting unit on the curb.
2. Integrated Economizers: a. Integrated integral modulating type capable of simultaneous economizer and compressor operation.
b. Includes all hardware and controls to provide cooling with outdoor air.
c. Equipped with low-leakage dampers, not to exceed 3% leakage at 1 in. wg pressure differential
(variable sliding plate economizer only) or parallel blade design.
d. Capable of introducing up to 100% outdoor air.
e. Parallel opposed blade economizer shall be equipped with a barometric relief damper with up to 30% of return air (036-072) or 45% of return air
(090-150) relief. The variable sliding plate economizer is equipped with 30% of return-air relief
(036-150).
f. Designed to close damper during loss-of-power situations with emergency power supply (variable sliding plate economizer) or spring return built into motor (parallel opposed blade economizer).
g. Dry bulb outdoor-air thermostat (variable sliding plate economizer) or enthalpy (parallel opposed blade economizer) protection shall be provided as standard.
h. Variable sliding plate economizer is a guillotinestyle damper, and the parallel opposed blade economizer is a parallel blade design.
i. Parallel opposed blade economizer shall provide control of internal building pressure through its inherent power exhaust function.
j. Parallel opposed blade economizer shall be capable of exhausting up to 100% outdoor air.
NOTE: Parallel opposed blade type economizer shall also be available with power exhaust.
3. Manual Outdoor-Air Damper:
Manual damper package shall consist of damper, birdscreen, and rainhood which can be preset to admit up to 50% outdoor air for year round ventilation.
4. 100% Two-Position Damper: a. Two-position damper package shall include single blade damper and motor. Admits up to 100% outdoor air.
68
*
* b. Damper shall close upon indoor (evaporator) fan shutoff.
c. Designed to close damper during loss of power situations.
d. Equipped with 15% barometric relief damper.
5. 25% Two-Position Damper: a. Two-position damper package shall include single blade damper and motor. Admits up to 25% outdoor air.
b. Damper shall close upon indoor (evaporator) fan shutoff.
c. Designed to close damper during loss of power situations.
d. Equipped with barometric relief damper.
6. Solid-State Enthalpy Control: a. For use with variable sliding plate economizer package only.
*
* b. Capable of sensing outdoor-air heat content (temperature and humidity) and control economizer cut-in point to have minimum heat content air passing over the evaporator coil for most efficient system operation.
7. Differential Enthalpy Sensor: a. For use with economizer only.
b. Capable of comparing heat content (temperature and humidity) of outdoor air and return air and controlling economizer cut-in point at the most economical level.
8. Head Pressure Control Package:
Consists of solid-state control and condenser-coil temperature sensor to maintain condensing temperature between 90 F and 110 F at outdoor ambient temperatures down to −20 F by condenser-fan speed modulation or condenser-fan cycling.
9. LP (Liquid Propane) Gas Conversion Kit:
Package shall contain all the necessary hardware and instructions to convert a standard natural gas unit for use with liquefied propane gas.
* 10. Commercial Programmable Thermostat:
Seven-day commercial progammable thermostat shall be capable of auto-changeover, F/C, 3-stage heating and 2-stage cabling. Thermostat shall also be equipped with complete system status display.
GUIDE SPECIFICATIONS — 580D036-150 (cont)
* 11. Flue Shield:
Provides protection from the hot sides of the gas flue hood.
* 12. Thermostat and Subbase:
Provides staged cooling and heating automatic (or manual) changeover, fan control, and indicator light.
* 13. Condenser Coil Hail Guard Assembly:
Hail guard shall protect against damage from hail and flying debris.
14. NO x
Reduction Kit:
Package shall contain all necessary hardware and instructions to convert a standard natural gas unit to reduce the nitrous oxide (NOx) emissions to a level of 40 nanograms/joule or less for unit sizes 036-060 being installed in California Air Quality Management
Districts.
15. Controls Upgrade Kit:
Kit shall contain high-pressure, loss-of-charge/lowpressure, and freeze protection switches. It shall mount on factory-installed Schrader fittings.
16. Alternate Motor(s) and/or Drive(s) (036-060, 090,
120, 150):
Alternate motor(s) and drive(s) shall be factoryinstalled to provide additional performance range.
17. Flue Discharge Deflector:
Flue discharge deflector directs unit exhaust vertically instead of horizontally.
* 18. Condenser Coil Grille:
The grille protects the condenser coil from damage by large objects without increasing unit clearances.
19. Compressor Cycle Delay:
Unit shall be prevented from restarting for minimum of 5 min. after shutdown.
20. Thru-the-Bottom Service Connectors:
Kit shall provide connectors to permit gas and electrical connections to be brought to the unit through the basepan.
21. Fan/Filter Status Switch:
Provides status of indoor (evaporator) fan (ON/OFF) or filter (CLEAN/DIRTY). Status shall be displayed over communication bus when used with direct digital controls or with an indicator light at the thermostat.
69
PACKAGED ROOFTOP ELECTRIC COOLING UNIT WITH
GAS HEAT — CONSTANT VOLUME APPLICATION
HVAC GUIDE SPECIFICATIONS
SIZE RANGE: 15 TO 25 TONS, NOMINAL (COOLING)
172,000 to 360,000 BTUH, NOMINAL
(INPUT HEATING)
MODEL NUMBER: 579F
Part 1 — General
1.01 SYSTEM DESCRIPTION
Unit is an outdoor rooftop mounted, electrically controlled heating and cooling unit utilizing a reciprocating semihermetic compressor(s) for cooling duty and gas combustion for heating duty. Supply air shall be discharged downward or horizontally (with horizontal supply/return curb adapter assembly), as shown on contract drawings.
Standard unit shall include a manual outdoor-air inlet.
1.02 QUALITY ASSURANCE
A. Unit (180-290) shall be rated in accordance with ARI
Standards 270 and 360 and all units shall be designed in accordance with UL Standard 1995.
NOTE: The 579F300 is beyond the scope of the ARI certification program.
B. Unit shall be designed to conform to ASHRAE 15.
C. Unit shall be ETL and ETL, Canada tested and certified in accordance with ANSI Z21.47 Standards as a total package.
D. Roof curb shall be designed to conform to NRCA
Standards.
E. Insulation and adhesive shall meet NFPA 90A requirements for flame spread and smoke generation.
F. Unit casing shall be capable of withstanding 500-hour salt spray exposure per ASTM B117 (scribed specimen).
G. Unit shall be manufactured in a facility registered to ISO
9002/BS5750, Part 2.
1.03 DELIVERY, STORAGE, AND HANDLING
Unit shall be stored and handled per manufacturer’s recommendations.
Part 2 — Products
2.01 EQUIPMENT (STANDARD)
A. General:
The 579F unit shall be a factory assembled, single-piece heating and cooling unit. Contained within the unit enclosure shall be all factory wiring, piping, controls, refrigerant charge (R-22), and special features required prior to field start-up.
B. Unit Cabinet:
1. Unit cabinet shall be constructed of galvanized steel, bonderized and coated with a prepainted baked enamel finish.
2. Indoor blower compartment interior surfaces shall be insulated with a minimum 1 ⁄
2
-in. thick, 1 lb density neoprene cooled, fiberglass insulation coated on the air side. Aluminum foil-faced fiberglass insulation shall be used in the gas heat compartment.
3. Cabinet panels shall be easily removable for servicing.
4. Filters shall be accessible through an access panel.
GUIDE SPECIFICATIONS — 579F180-300
5. Holes shall be provided in the base rails for rigging shackles to facilitate overhead rigging.
6. Unit shall have a factory-installed internal condensate drain connection and a sloped condensate pan.
C. Fans:
1. Indoor blower (evaporator fan): a.
Fan shall be belt driven. Belt drive shall include an adjustable pulley. The standard fan drive shall have a factory-installed low-medium static pressure fan drive. The alternate fan drive option shall have a factory-installed high static pressure fan drive.
b.
Fan wheel shall be made from steel with a corrosion resistant finish. It shall be a dynamically balanced, double-inlet type with forward-curved blades.
2. Condenser fans shall be of the direct-driven propeller type, with corrosion-resistant blades riveted to corrosion-resistant steel supports. They shall be dynamically balanced and discharge air upwards.
3. Induced-draft blower shall be of the direct-driven, single inlet, forward-curved, centrifugal type. It shall be made from steel with a corrosion-resistant finish and shall be dynamically balanced.
D. Compressor(s):
1. The reciprocating semi-hermetic compressor(s) has factory-installed external spring vibration isolation.
2. Factory-installed crankcase heater prevents refrigerant dilution of oil.
3. The 180 size semi-hermetic compressor shall be equipped with an electric unloader for capacity control. Additional field-supplied unloaders are not recommended on any 180-300 sizes.
4. Compressors shall be on mechanically and electrically independent circuits (216-300 sizes).
E. Coils:
1. Standard evaporator and condenser coils shall have copper or aluminum plate fins mechanically bonded to seamless internally grooved copper tubes with all joints brazed.
2. Optional precoated coils shall be coated with a baked-on organic, epoxy, phenolic coating.
F. Heating Section:
1. Induced-draft combustion type with energy saving direct-spark ignition system and redundant main gas valve.
2. The heat exchanger shall be of the tubular-section type constructed of a minimum of 20-gage steel coated with a nominal 1.2 mil aluminum-silicone alloy for corrosion resistance.
3. Burners shall be of the in-shot type constructed of aluminum-coated steel.
4. All gas piping shall enter the unit at a single location.
G. Refrigerant Components:
Refrigerant circuit components shall include:
1. Fixed expansion device with filter driers.
2. Service valve gage and connections on suction, discharge, and liquid lines.
3. Thermostatic expansion valve (size 180) or fixed orifice feed system (sizes 216-300).
70
H. Filter Section:
Standard filter section shall consist of 2 sizes of factoryinstalled 2-in. thick throwaway fiberglass filters of commercially available sizes.
I. Controls and Safeties:
1. Unit Controls: a.
Economizer control (optional) b.
Capacity control (2-step) c.
Unit shall be complete with self-contained lowvoltage control circuit.
2. Safeties: a.
Unit shall incorporate a solid-state compressor lockout which provides reset capability at the space thermostat, should any of the following safety devices trip and shut off compressor:
1) Compressor overtemperature, overcurrent.
2) Low-pressure switch.
3) Freezestats (evaporator coil).
4) High-pressure switch.
b.
Supply-air thermostat shall be located in the unit.
c.
Heating section shall be provided with the following minimum protections:
1) High-temperature limit switch.
2) Induced-draft motor speed sensor.
3) Flame rollout switch.
4) Flame proving controls.
5) Redundant gas valve.
J. Operating Characteristics:
1. Unit shall be capable of starting and running at 115 F ambient outdoor temperature per maximum load criteria of ARI Standard 360.
2. Unit with standard controls will operate in cooling down to an outdoor ambient temperature of 40 F on
579F180 units, to 35 F on 216 units, to 25 F ambient on 240 units, and to 48 F ambient on 300 units.
3. Unit shall be provided with fan time delay to prevent cold air delivery.
K. Electrical Requirements:
All unit power wiring shall enter unit cabinet at a single location.
L. Motors:
1. All compressor motors shall be of the refrigerant cooled type with thermal and calibrated circuit breaker overload protection.
2. All fan motors shall have permanently lubricated, sealed bearings and inherent automatic-reset thermal overload protection or manual reset calibrated circuit breakers.
3. All indoor-fan motors 5 hp and larger shall meet the minimum efficiency requirements as established by the Energy Policy Act of 1992 (EPACT) effective October 24, 1997.
M. Special Features:
Certain features are not applicable when the features designated * are specified. For assistance in amending the specifications, contact your local sales office.
GUIDE SPECIFICATIONS — 579F180-300
*
*
*
*
*
1. Roof Curbs (Horizontal and Vertical): a. Formed of 18-gage galvanized steel with wood nailer strip and shall be capable of supporting entire unit weight.
b. Permits installing and securing ductwork to curb prior to mounting unit on the curb.
2. Horizontal Adapter Roof Curb:
Includes factory-assembled adapter and duct and substantially improves evaporator fan static performance.
3. Integrated Economizer: a. Integrated type capable of simultaneous economizer and compressor operation to provide cooling with outdoor air.
b. Equipped with low-leakage dampers not to exceed 3% leakage, at 1.0 in. wg pressure differential.
c. Capable of introducing up to 100% outdoor air.
d. Equipped with dry-bulb temperature control to govern economizer changeover.
e. Equipped with a mixed-air sensor that controls the economizer to a 55 F control point.
4. Two-Position Damper:
Two-position damper package shall include single blade damper and motor. Admits up to 25% outdoor air, and shall close upon unit shutoff.
5. Accessory Compressor Cycle Delay:
Compressor shall be prevented from restarting for a minimum of 5 minutes after shutdown.
6. Thermostats and Subbases:
To provide staged heating and cooling in addition to automatic (or manual) changeover and fan control.
7. Barometric Relief Damper Package: a. Package shall include damper, seals, hardware, and hoods to relieve excess internal pressure.
b. Damper shall close due to gravity upon unit shutdown.
8. Power Exhaust:
Package shall include an exhaust (propeller style) fan, 1 ⁄
2
Hp 208-230, 460 v (factory-wired for 460 v) motor, and damper for vertical flow units with economizer to control overpressurization of building.
9. Head Pressure Control Package:
Consists of an accessory outdoor-air package and a solid-state control with condenser coil temperature sensor for controlling condenser-fan motor speed to maintain condensing temperature between
90 F and 100 F at outdoor ambient temperature down to –20 F.
10. Low-Ambient Kits:
When used, allows units to operate at lower outdoor ambient temperatures. See trade prices for more information.
71
GUIDE SPECIFICATIONS — 579F180-300
* 11. Enthalpy Sensor: a. For use with economizer only.
b. Capable of comparing heat content (temperature and humidity) of outdoor air and indoor air and controlling economizer cut-in point at the most economical level.
NOTE: Two accessory enthalpy sensors are required for differential enthalpy control.
* 12. Commercial Programmable Thermostat:
Seven-day commercial progammable thermostat shall be capable of auto-changeover, F/C, 3-stage heating and 2-stage cooling. Thermostat shall also be equipped with complete system status display.
13. Winter Start Time-Delay Relay:
Used in conjunction with the accessory low-ambient kit or head pressure control device, permits operation in cooling at lower outdoor ambient temperatures. See price pages for more information.
14. Liquid Propane Conversion Kit:
Kit shall contain all the necessary hardware and instructions to convert a standard natural gas unit for use with liquified propane gas.
Copyright 1998 Bryant Heating & Cooling Systems
SPECIFICATIONS SUBJECT TO CHANGE WITHOUT NOTICE
UNIT MUST BE INSTALLED IN ACCORDANCE
WITH INSTALLATION INSTRUCTIONS
Printed in U.S.A.
9/98 CATALOG NO. 5258-001
advertisement
Related manuals
advertisement