- No category
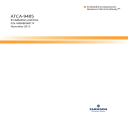
Artesyn ATCA-9405-Installation and Use
Add to my manualsadvertisement
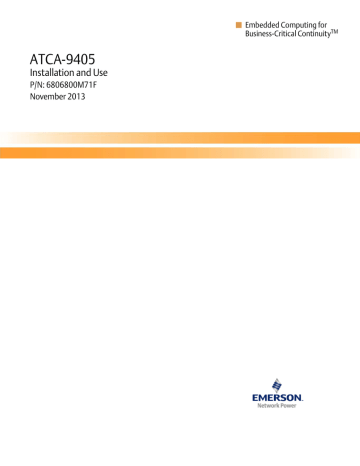
Chapter 2
Setup
2.1
Overview
This chapter describes the physical layout of the board, the setup process, and how to check for proper operation once the board has been installed. This chapter also includes troubleshooting, service, and warranty information.
2.2
Electrostatic Discharge
Before you begin the setup process, remember that the electrostatic discharge (ESD) can easily damage the components on the ATCA-9405 hardware. Electronic devices, especially those with programmable parts, are susceptible to ESD, which can result in operational failure.
Unless you ground yourself properly, static charges can accumulate in your body and cause
ESD damage when you touch the board.
Use proper static protection and handle ATCA-9405 boards only when absolutely necessary.
Always wear a wriststrap to ground your body before touching a board. Keep your body grounded while handling the board. Hold the board by its edges—do not touch any components or circuits. When the board is not in an enclosure, store it in a static-shielding bag.
To ground yourself, wear a grounding wriststrap. Simply placing the board on top of a staticshielding bag does not provide any protection—place it on a grounded dissipative mat. Do not place the board on metal or other conductive surfaces.
ATCA-9405 Installation and Use (6806800M71F) 29
Setup
2.3
ATCA-9405 Circuit Board
The ATCA-9405 circuit board is an ATCA blade assembly and complies with the PICMG 3.0 ATCA mechanical specification. It uses a 16-layer printed circuit board with the following dimensions:
Table 2-1 Circuit Board Dimensions
Width Depth Height Weight (typical)
12.687 in.
(322.25 mm)
11.024 in.
(280.01 mm)
< .84 in.
(<21.33 mm)
8.38 lb. (3.80 kg)
This is the typical weight for the ATCA-9405. Board weight varies slightly per configuration; contact
Technical Support if you require a specific configuration weight.
The
, shows the face plate layout for ATCA-9405 board.
Figure 2-1 Faceplate Layout
30
The face plate of the blade provides the following interfaces and control elements.
Table 2-2 Faceplate Interfaces
Processor
Packet Processor
Service Processor
Interfaces / Control Elements
One Serial Console port for Packet Processor 1 (only for maintenance purposes)
One Serial Console port for Packet Processor 2 (only for maintenance purposes)
One 10/100/1000Base-T Ethernet port shared for both Packet
Processors (only for maintenance purposes)
One USB port (only for maintenance purposes)
One Serial Console port (only for maintenance purposes)
One 10/100/1000Base-T Ethernet port (only for maintenance purposes)
ATCA-9405 Installation and Use (6806800M71F)
Setup
Table 2-2 Faceplate Interfaces (continued)
Processor
IPMC
Interfaces / Control Elements
Out of Service (OOS) LED
In Service (IS) LED
Attention (ATN) LED
Hot Swap (H/S) LED
Recessed Reset Button
For these interfaces, the maximum cable length should not exceed more than 3m.
2.3.1
Switch Settings
All mechanical switches are OFF in their default configuration. Switch OFF means high level for the connected signal and switch ON means low level for the connected signal.
ATCA-9405 Installation and Use (6806800M71F) 31
Setup
The switches are placed on component side 1. The Figure 2-2 on page 32
, shows the switch locations on the board.
Figure 2-2 Switch Location with Heat Sink SW1 and SW2
32 ATCA-9405 Installation and Use (6806800M71F)
Figure 2-3 Switch Location with Heat Sink SW3 and SW4
Setup
2.3.1.1
FPGA and CPLD/IPMC Switches
The switch settings are described in Table 2-3 on page 33 .
Table 2-3 Settings for Switch SW1
Switch Description
SW1-1 IPMI Boot Select
OFF = SPI Boot Flash is selected by IPMC
ON = SPI Boot Flash is selected by SW1-2
SW1-2 Manual Boot Select
OFF = Default SPI Boot Flash selected
ON = Recovery SPI Boot Flash selected
OFF
Default is selected by IPMC
SPI Flash
Default SPI Boot Flash is used
ATCA-9405 Installation and Use (6806800M71F) 33
Setup
34
Table 2-3 Settings for Switch SW1 (continued)
Switch Description
SW1-3 Debug Header Boot Select
This switch overrides selection done via
SW1-1 and SW1-2.
OFF = Boot from SPI Boot Flash (TSOP devices)
ON = Boot from SPI Debug Header
SW1-4 Reserved
OFF
OFF
Table 2-4 Settings for Switch SW2 (for debugging only)
Switch
SW2-1 Reserved
SW2-2 Reserved
SW2-3 Reserved
SW2-4 Reserved
Description
OFF
OFF
OFF
OFF
Table 2-5 Settings for Switch SW3
Switch Description
SW3-1 Enable E10-USB Emulator for H8S
OFF = Disabled
ON = Enabled
SW3-2 Enable H8S Programming via Debug Console
OFF = Disabled
ON = Enabled
SW3-3 Manual Payload Power Enable for Blade
OFF = IPMI controlled power enable for blade
ON = Manual power enable for blade
SW3-4 Manual Payload Power Enable for RTM
OFF = IPMI controlled power enable for RTM
ON = Manual power enable for RTM
OFF
OFF
OFF
OFF
Default
Boot from TSOP SPI Flash
Do not change
Default
Do not change
Do not change
Do not change
Do not change
Default
E10-USB Emulator disabled
H8S programming disabled
IPMI controlled power enabled
IPMI controlled power enabled
ATCA-9405 Installation and Use (6806800M71F)
Setup
Table 2-6 Settings for Switch SW4 (for debugging only)
Switch
SW4-1
SW4-2
SW4-3
(dual function)
SW4-4
Description
Manual Power Enable for Packet Processor 1
OFF = SP controlled PP1 power enable
ON = Manual PP1 power enable
Manual Power Enable for Packet Processor 2
OFF = SP controlled PP2 power enable
ON = Manual PP2 power enable
IPMC Watchdog Enable (SW3-3 = OFF)
OFF = Watchdog enabled
ON = Watchdog disabled
Reserved (SW3-3 = ON)
IPMC Console Output Selection
OFF = IPMC console output via debug connector
ON = IPMC console output via front panel connector
Default
OFF Software controlled (SP) power enable for PP1
OFF Software controlled (SP) power enable for PP2
OFF IPMC Watchdog Enabled
OFF Do not change
OFF IPMC Console Output via debugging header
ATCA-9405 Installation and Use (6806800M71F) 35
Setup
2.3.2
Safety Critical Hot Spots
The following figure shows the critical hot spots on the ATCA-9405 board.
Figure 2-4 Location of the Hot Spots
36
Temperature Spot 2 (on 48V DC/DC
Converter) = 100 °C (max) exact location: in the geometric middle of the heat spreader
Temperature Spot 1 (on Power Entry
Module) = 110 °C (max) exact location: on top of upper transformer housing
ATCA-9405 Installation and Use (6806800M71F)
Setup
2.3.3
Connector Pin Assignment
2.3.3.1
Face Plate Connectors
Refer
for the face plate layout.
2.3.3.1.1 USB Port
One standard USB Type-A connector for access to the USB interface of the Service Processor is available at the face plate.
Table 2-7 USB Connector Pin-out
2
3
Pin
1
4
Signal
VCC_USB
D-
D+
GND
2.3.3.1.2
Ethernet Ports
Two shielded RJ45 connectors with integrated transformers for 10/100/1000Base-T Ethernet are available at the front panel.
Table 2-8 Ethernet Connector Pin-out
6
7
4
5
8
2
3
Pin Signal
1 BI_DA+
BI_DA-
BI_DB+
BI_DC+
BI_DC-
BI_DB-
BI_DD+
BI_DD-
ATCA-9405 Installation and Use (6806800M71F) 37
Setup
2.3.3.1.3
Serial Console Ports
Three shielded RJ45 connectors (with Cisco style pin-out) for serial consoles are available at the front panel.
Table 2-9 Serial Console Connector Pin-out (Cisco Style)
5
6
3
4
7
8
Pin
1
2
Signal
RTS#
NC
TXD
GND
GND
RXD
NC
CTS#
38 ATCA-9405 Installation and Use (6806800M71F)
2.3.3.2
On-board Connectors
The following figure shows the location of eUSB Drive Connector (P6) on ATCA-9405.
Figure 2-5 Location of On-board Connectors
Setup
ATCA-9405 Installation and Use (6806800M71F)
P6
39
Setup
2.3.3.2.1
eUSB Drive Connector
ATCA-9405 provides one 2x5 pin header and a mounting hole for eUSB drives like Smart
Modular Z-U130.
Table 2-10 eUSB Drive Connector Pin-out
5
6
3
4
Pin
1
2
7
8
9
10
D-
NC
D+
NC
Signal
VCC
NC
GND
NC
KEY
NC
40 ATCA-9405 Installation and Use (6806800M71F)
Setup
2.3.3.3
Back Panel Connectors
2.3.3.3.1 Overview
The AdvancedTCA backplane connectors reside in three zones, 1 to 3 as specified by the
AdvancedTCA standard and are called P10, P20 and 23, and P30, P31, and 32. The pinouts of all these connectors are given in this section.
Figure 2-6 Location of AdvancedTCA Connectors
ATCA-9405 Installation and Use (6806800M71F) 41
Setup
2.3.3.3.2 Zone 1 Connector
The Zone 1 connector is used to deliver power from the ATCA back plane to the ATCA-9405 baseboard. The pin out for this connector is defined by the ATCA specifications. The
ATCA-9405 does not implement Metallic Test or Ringing Generator Circuitry and therefore does not use pins 17 through 24.
Figure 2-7 P10 Backplane Connector Pinout
42
Table 2-11 Zone 1 Connector P10 Pin Assignment
7
8
9
10
5
6
Contact Destination
1 - 4 Reserved
IPMC ISC PC0
IPMC ISC PC1
11
12
IPMC ISC PC2
IPMC ISC PC3
IPMC ISC PD4
IPMC ISC PD5
IPMC ISC PD6
IPMC ISC PD7
Description
Reserved
Hardware Address Bit 0
Hardware Address Bit 1
Hardware Address Bit 2
Hardware Address Bit 3
Hardware Address Bit 4
Hardware Address Bit 5
Hardware Address Bit 6
Hardware Address Bit 7
ATCA-9405 Installation and Use (6806800M71F)
Setup
Table 2-11 Zone 1 Connector P10 Pin Assignment (continued)
29
30
31
32
25
26
27
28
33
34
Contact Destination
13 IPMC IMC PD0
14
15
16
17-24
IPMC IMC PD1
IPMC ISC PC5
IPMC ISC PC4
Not used
Shelf Ground
Logic Ground
Power Building Block
Power Building Block
Power Building Block
Power Building Block
Power Building Block
Power Building Block
Power Building Block
Power Building Block
Description
IPMB Clock Port A
IPMB Data Port A
IPMB Clock Port B
IPMB Data Port A
Not used
Shelf Ground
Logic Ground
Enable B
Voltage Return A
Voltage Return B
Early -48V A
Early -48V B
Enable A
-48V A
-48V A
2.3.3.3.3 Zone 2 Connector
The ATCA specifications define five identical connectors for the Zone 2 data transport. These connectors are referred to as Free Board connectors and are assigned reference designators
P20 through P24 as per the ATCA specifications.
The ATCA-9405 is a node board and uses only two of the five connectors P20 and P23. P20 is used to support clock synchronization interface and update channels and P23 is used to support the base and fabric channels.
ATCA-9405 Installation and Use (6806800M71F) 43
Setup
44
Tyco HM-Zd Plus connectors are used to support 40 Gigabit Ethernet through backplane.
Table 2-12 Zone 2 Connector P20 Pin Assignment
Row Interface a
1 CLK CLK1A+
8
9
6
7
10
4
5
2
3
Update
Channel
Fabric
Channel 15
Fabric
Channel 14
Fabric
Channel 13 b
CLK1A-
NC
NC
NC
NC
NC
NC NC
UC_TX2+ UC_TX2-
UC_TX0+ UC_TX0-
NC NC
NC
NC
NC
NC
NC c
CLK1B+
NC
NC
NC
NC
NC
NC
UC_RX2+
UC_RX0+
NC d
CLK1B-
NC
NC
NC
NC
NC
NC
UC_RX2-
UC_RX0-
NC e
CLK2A+ f
CLK2Ag
CLK2B+ h
CLK2B-
NC
NC
NC
NC
NC
CLK3A+ CLK3ACLK3B+ CLK3B-
UC_TX3+ UC_TX3UC_RX3+ UC_RX3-
UC_TX1+ UC_TX1UC_RX1+ UC_RX1+
NC NC NC NC
NC
NC
NC
NC
NC
NC
NC
NC
NC
NC
NC
NC
NC
NC
NC
Table 2-13 Zone 2 Connector P23 Pin Assignment
2
3
4
5
6
7
8
9
10
Row Interface a
1 Fabric
Channel 2
Fabric
Channel 1
NA
NA
NA
NA
Base
Channel 1
Base
Channel 2 b c d e
NC
NC
NC
NC
FC2_TX2+ FC2_TX2FC2_RX2+ FC2_RX2
-
FC2_TX0+ FC2_TX0FC2_RX0+ FC2_RX0
-
FC1_TX2+ FC1_TX2FC1_RX2+ FC1_RX2
-
FC1_TX0+ FC1_TX0FC1_RX0+ FC1_RX0
-
BC1_DA+ BC1_DABC1_DB+
BC2_DA+ BC2_DABC2_DB+
FC2_TX
3+
FC2_TX
1+
FC1_TX
3+
FC1_TX
1+
BC1_DBBC1_DC
+
BC2_DBBC2_DC
+
NC
NC
NC
NC
NC
NC
NC
NC
NC
NC
NC
NC
NC
NC
NC
NC f g h
FC2_TX3FC2_RX3+ FC2_RX3-
FC2_TX1FC2_RX1+ FC2_RX1-
FC1_TX3FC1_RX3+ FC1_RX3-
FC1_TX1FC1_RX1+ FC1_RX1-
BC1_DC-
BC2_DC-
NC
NC
NC
NC
BC1_DD+
BC2_DD+
NC
NC
NC
NC
BC1_DD-
BC2_DD-
NC
NC
NC
NC
ATCA-9405 Installation and Use (6806800M71F)
2.3.3.3.4 Zone 3 Connector
ATCA-9405 provides three connectors P30, P31, and P32 for connection to the RTM.
Table 2-14 Zone 3 Connector P30 Pin Assignments
Setup
Table 2-15 Zone 3 Connector P31 Pin Assignments
ATCA-9405 Installation and Use (6806800M71F) 45
Setup
Table 2-16 Zone 3 Connector P32 Pin Assignments
2.3.4
Debugging Headers
The following debugging headers are provided on the ATCA-9405. Please note that debugging headers are only used internally and may be removed later for cost reduction reasons. For more information regarding location and usage of debugging headers, please contact sales/marketing team.
46
Table 2-17 Debugging Header
Location Type
JP1 16-pin Header, 1.27mm pitch
Description
P2020 debugging header
MSRCID signals and second serial console port (UART1 interface)
JP2 8-pin Header, 1.27mm pitch P2020 Boot Flash header
JP3
JP5
P47
3-pin Header, 2.54mm pitch IPMC debug console
16-pin Header, 1.27mm pitch E10A-USB Emulator header for IPMC
P57
16-pin Header, 1.27mm pitch Packet Processor 1 debugging header
EJTAG support and second serial console port (UART1 interface)
16-pin Header, 1.27mm pitch Packet Processor 2 debugging header
EJTAG support and second serial console port (UART1 interface)
ATCA-9405 Installation and Use (6806800M71F)
Setup
Table 2-17 Debugging Header (continued)
Location Type
P7
Description
16-pin Header, 1.27mm pitch P2020 COP interface
P8 16-pin Header, 1.27mm pitch Management and Payload Power JTAG interface
2.3.4.1
IPMC Debug Console Header
A three pin header is provided to access IPMC debug console. The pin assignment is shown below.
Table 2-18 IPMC Debug Console Header Pin Assignment
Pin
1
3
4
Signal
GND
IPMC_TXD
IPMC_RXD
2.3.4.2
COP Header
A 16-pin header is provided for access to P2020 COP interface. The pin assignment is shown below.
Table 2-19 COP Header Pin Assignment
5
6
3
4
7
8
Pin Signal
1
2
TDO
QACK
TDI
TRST#
RUNSTOP
Target Power
TCK
CKSTP_IN#
ATCA-9405 Installation and Use (6806800M71F) 47
Setup
Table 2-19 COP Header Pin Assignment (continued)
14
15
16
Pin Signal
9 TMS
10
11
12
13
NC
SRESET#
GND
HRESET#
KEY
CKSTP_OUT#
GND
2.3.4.3
EJTAG Header
A separate 16-pin header is provided to access each Packet Processor EJTAG interface. The pin assignment is shown below.
Table 2-20 EJTAG Header Pin Assignment
7
8
9
10
11
12
5
6
3
4
Pin
1
2
Signal
TRST#
UART1_RXD
TDI
UART1_TXD
TDO
GND
TMS
GND
TCK
NC
RESET#
KEY
48 ATCA-9405 Installation and Use (6806800M71F)
Table 2-20 EJTAG Header Pin Assignment (continued)
Pin
13
14
15
16
Signal
NC
Target Power
NC
NC
The standard EJTAG connector has only 14 pins, thus do not connect to pin 15 and 16.
Setup
2.4
ATCA-9405 Setup
Following items are required to setup and check the operation of the ATCA-9405:
ATCA chassis and power supply
Console cables for EIA-232 ports (Cisco style pin out)
Computer terminal
Save the antistatic bag and box for future shipping or storage.
ATCA-9405 Installation and Use (6806800M71F) 49
Setup
2.4.1
Power Requirements
Make sure that the blade is used in an ATCA shelf connected to -60 VDC up to -48 VDC, according to Telecommunication Network Voltage (TNV-2). A TNV-2 circuit is a circuit whose normal operating voltages exceed the limits for a safety-extra-low-voltage (SELV) under normal operating conditions, and which is not subject to over-voltages from telecommunication networks.
Table 2-21 Typical Power Requirements
Configuration
Dual CN6880 running at 1.2GHz with 16GB DDR3 memory each,
P2020 running at 1.0GHz with 2GB DDR3 memory, 16GB USB Flash
Drive, Linux booted on P2020, Ethernet Switch fully initialized,
Cavium Octeon RiscCore Stress test running on all 64 CN6880 cores, board running at room temperature.
Dual CN6880 running at 1.0 GHz with 16GB DDR3 memory each,
P2020 running at 1.0GHz with 2GB DDR3 memory, 16GB USB Flash
Drive, Linux booted on P2020, Ethernet Switch fully initialized,
Cavium Octeon RiscCore Stress test running on all 64 CN6880 cores, board running at room temperature.
Dual CN6880 running at 800 MHz with 16GB DDR3 memory each,
P2020 running at 1.0GHz with 2GB DDR3 memory, 16GB USB Flash
Drive, Linux booted on P2020, Ethernet Switch fully initialized,
Cavium Octeon RiscCore Stress test running on all 64 CN6880 cores, board running at room temperature.
ARTM-9405B-16X10GE (maximum Power consumption)
Rated Voltage
Exception in the US and Canada
Operating Voltage
Exception in the US and Canada
Power
235 W
215 W
195 W
36 W
-48 VDC to -60 VDC
-48 VDC
-39 VDC to -72 VDC
-39 VDC to -60 VDC
The exact power requirements for the ATCA-9405 circuit board depends upon the specific configuration of the board, including the CPU frequency and amount of memory installed on the board.
50 ATCA-9405 Installation and Use (6806800M71F)
Setup
2.4.2
Environmental Considerations
As with any printed circuit board, make sure that the air flow to the board is adequate. Chassis constraints and other factors greatly affect the air flow rate. The environmental requirements are as follows:
Table 2-22 Environmental Requirements
Requirement
Temperature
Airflow
Operating
+5 ºC (+41 °F) to +40 ºC (+104 °F)
(normal operation) according to NEBS
Standard GR-63-CORE
-5 ºC (+23 °F) to +55 ºC (+131 °F)
(exceptional operation) according to
NEBS Standard GR-63-CORE
The blade is designed to operate in a chassis that provides 35 CFM across the blade for the stated temperature range
Temperature change
+/- 0.5 ºC/min according to NEBS
Standard GR-63-CORE
Relative humidity 5% to 90% non-condensing according to
Emerson-internal environmental requirements
Vibration 1 g from 5 to 100 Hz and back to 5 Hz at a rate of 0.1 octave/minute
Shock
Free fall
Half-sine, 11 m/Sec, 30 mSec/sec2
-
Non-Operating
-40 ºC (-40 °F) to +70 ºC (+158 °F)
(may be further limited by installed accessories)
+/- 0.5 ºC/min
5% to 95% non-condensing according to Emerson-internal environmental requirements
5-20 Hz at 0.1 g2/Hz
20-200 Hz at -3.0 dB/octave
Random 20-200 Hz at -3 m/Sec2
Blade level packaging
Half-sine, 6 mSec at 180 m/Sec2
1,200 mm/all edges and corners
1.0 m (packaged)
100 mm (unpacked)
ATCA-9405 Installation and Use (6806800M71F) 51
Setup
Figure 2-8 Air Flow Graph
52
During the safety qualification of this blade, the following on-board locations were identified as critical with regards to the maximum temperature during blade operation. To guarantee proper blade operation and to ensure safety, you have to make sure that the temperatures at the locations specified in the following table are not exceeded. If not stated otherwise, the temperatures should be measured by placing a sensor exactly at the given locations.
Table 2-23 Critical Temperature Limits
Component
Cavium CN6880 PP1
Cavium CN6880 PP2
DDR3 DIMM Modules
PCI-Express Switch
Ethernet Switch
Thermal Design Power
72 W
72 W
6.9 W
2.9 W
33.5 W
Maximum Case or Junction
Temperature
Tj = 101°C
Tj = 101°C
Tc = 85°C
Tj = 110°C
Tj = 115°C
If you integrate the blade in your own system, contact your local sales representative for further safety information.
ATCA-9405 Installation and Use (6806800M71F)
Setup
2.4.3
Hot Swap
The ATCA-9405 can be Hot Swapped, as defined in the ATCA specification. This section describes how to insert and extract an ATCA-9405 module in a typical ATCA system. (These procedures assume the system is using a shelf manager.)
The ATCA-9405 Rear Transition Module (RTM) has its own Hot Swap LED and switch, and it can be Hot Swapped in/out independently of the face plate. If the face plate is not present, then the RTM will not be powered. If the face plate is Hot Swapped out, the blue LED of the
RTM illuminates. In either case, the RTM can be safely removed.
Personal Injury or Product Damage
The product is supplied by a TNV-2 voltage. This voltage is considered hazardous. Make sure that the external power supply meets the relevant safety standards.
Make sure that TNV-2 is separated from dangerous voltages (mains) through double or reinforced insulation.
Inserting a board
1. Insert the ATCA-9405 into an available slot.
2. Push the face plate handle (tab).
The blue Hot Swap LED on the front panel (see
) flashes a long blink to indicate that the board insertion is in progress and the system management software is activating the slot.
Then the blue LED turns off, indicating the insertion process is complete, and payload power is present.
ATCA-9405 Installation and Use (6806800M71F) 53
Setup
Removing a board
1. Pull out the handle (tab) on the ATCA-9405 front panel at one click.
A short blink indicates that the board is requesting permission for extraction.
2. Remove the board when the blue LED on the front panel is on (no payload power).
Do not remove the ATCA-9405 while the blue LED is blinking.
2.5
Troubleshooting
In case of difficulty, use the following checklist:
Check that the ATCA-9405 circuit board is seated firmly in the carrier
Check that the system is not overheating
Check the cables and connectors to be certain that they are secure
Check that your terminal is connected to a console port
2.5.1
Technical Support
If you need help in resolving a problem with your ATCA-9405, visit www.emerson.com/embeddedcomputing . Keep the following information ready:
ATCA-9405 serial number identification, see Figure "Serial Number and Product ID" on page 27
.
Version and part number of the operating system (if applicable)
Whether your board has been customized for options such as a higher processor speed or additional memory
License agreements (if applicable)
54 ATCA-9405 Installation and Use (6806800M71F)
Setup
2.5.2
Product Repair
If you plan to return the board to Emerson Network Power for service, visit www.emerson.com/embeddedcomputing to obtain a Return Merchandise Authorization
(RMA) number. List the items that you are returning and the board serial number, plus your purchase order number and billing information if your ATCA-9405 hardware is out of warranty.
Contact our Test and Repair Services Department for any warranty questions. If you return the board, be sure to enclose it in an antistatic bag, such as the one in which it was originally shipped.
Put the RMA number on the outside of the package so that we can handle your problem efficiently. Our service department cannot accept material received without an RMA number.
ATCA-9405 Installation and Use (6806800M71F) 55
Setup
56 ATCA-9405 Installation and Use (6806800M71F)
advertisement
* Your assessment is very important for improving the workof artificial intelligence, which forms the content of this project
Related manuals
advertisement
Table of contents
- 1 ATCA-9405
- 3 Regulatory Agency Warnings & Notices
- 5 Contents
- 15 About this Manual
- 15 Overview of Contents
- 16 Abbreviations
- 18 Conventions
- 19 Summary of Changes
- 21 Introduction
- 21 1.1 Overview
- 22 1.2 Components and Features
- 23 1.3 Functional Overview
- 24 1.4 Additional Information
- 24 1.4.1 Regulatory Compliance
- 26 1.4.2 RoHS Compliance
- 26 1.4.3 Notation
- 26 1.5 Ordering Information
- 27 1.6 Product Identification
- 29 Setup
- 29 2.1 Overview
- 29 2.2 Electrostatic Discharge
- 30 2.3 ATCA-9405 Circuit Board
- 31 2.3.1 Switch Settings
- 33 2.3.1.1 FPGA and CPLD/IPMC Switches
- 36 2.3.2 Safety Critical Hot Spots
- 37 2.3.3 Connector Pin Assignment
- 37 2.3.3.1 Face Plate Connectors
- 39 2.3.3.2 On-board Connectors
- 41 2.3.3.3 Back Panel Connectors
- 46 2.3.4 Debugging Headers
- 47 2.3.4.1 IPMC Debug Console Header
- 47 2.3.4.2 COP Header
- 48 2.3.4.3 EJTAG Header
- 49 2.4 ATCA-9405 Setup
- 50 2.4.1 Power Requirements
- 51 2.4.2 Environmental Considerations
- 53 2.4.3 Hot Swap
- 54 2.5 Troubleshooting
- 54 2.5.1 Technical Support
- 55 2.5.2 Product Repair
- 57 Packet Processor
- 57 3.1 Overview
- 58 3.2 CN6880 Processor
- 58 3.3 Cache
- 59 3.4 System Memory
- 59 3.4.1 Memory Interface
- 59 3.4.2 Memory Socket
- 60 3.4.3 Memory Modules
- 61 3.4.4 Thermal Sensor
- 61 3.5 Octeon U-Boot
- 61 3.5.1 NVRAM
- 62 3.5.2 Network Interfaces
- 62 3.6 SerDes Configuration
- 63 3.7 PCI Express Interface
- 63 3.8 Ethernet Interface
- 64 3.8.1 Front Panel Interface
- 64 3.8.2 Base and Fabric Interface
- 64 3.9 Interlaken Interface
- 65 3.10 USB Interface
- 65 3.11 UART Interface
- 66 3.12 I2C Interface
- 66 3.13 JTAG Interface
- 66 3.14 Interrupts
- 66 3.14.1 Packet Processor Interrupts
- 67 3.15 Power Supply
- 68 3.16 Cooling
- 69 Service Processor
- 69 4.1 Overview
- 70 4.2 P2020 Processor
- 70 4.3 Cache
- 70 4.4 Main Memory
- 70 4.4.1 Memory Interface
- 71 4.4.2 Memory Socket
- 71 4.4.3 Memory Modules
- 72 4.4.4 Persistent Memory
- 73 4.4.5 Thermal Sensor
- 73 4.5 SP U-Boot
- 73 4.5.1 Environment Variables
- 74 4.5.2 Passing Parameter Set to the Operating System
- 74 4.5.3 Dynamic Variables Set During the Boot Phase
- 75 4.5.4 Variables for Controlling the Boot Progress
- 76 4.5.5 Firmware Update
- 76 4.5.6 Application/OS Boot
- 77 4.5.6.1 Default Boot Sequences
- 77 4.5.7 Memory/Address Map Initialization
- 77 4.5.7.1 Address Map
- 78 4.6 Local Bus
- 78 4.7 SerDes Configuration
- 79 4.8 PCI Express Interface
- 80 4.9 Ethernet Interface
- 80 4.9.1 Front Panel Interface
- 80 4.9.2 Base and Fabric Interface
- 81 4.10 SPI Interface
- 81 4.10.1 Boot Flash
- 81 4.10.2 Boot Flash Selection
- 82 4.11 USB Interface
- 82 4.11.1 USB Connector
- 83 4.11.2 e-USB Flash Drive
- 83 4.12 UART Interface
- 83 4.13 I2C Interface
- 84 4.13.1 Real Time Clock (RTC)
- 84 4.14 JTAG Interface
- 84 4.15 Interrupts
- 85 4.15.1 Service Processor Interrupts
- 85 4.16 Cooling
- 87 Ethernet Infrastructure
- 87 5.1 Overview
- 89 5.2 Ethernet Switch
- 90 5.2.1 Port Configuration
- 92 5.2.2 Two-Wire Serial Interface
- 92 5.2.3 Switch Management Interface
- 93 5.2.4 PHY Management Interface
- 94 5.3 Base Interface
- 94 5.4 Fabric Interface
- 97 5.5 Update Channel
- 97 5.6 Serial Redirection
- 99 Service Infrastructure
- 99 6.1 Overview
- 99 6.2 Port Configuration
- 100 6.3 Hot Plug Support
- 101 6.3.1 Serial Hot Plug Controller
- 102 6.4 I2C Slave Interface
- 102 6.5 JTAG Support
- 102 6.6 Lane Status
- 105 Mezzanine Module
- 105 7.1 Overview
- 109 Intelligent Peripheral Management Controller
- 109 8.1 Overview
- 109 8.2 Functional Overview
- 112 8.3 Firmware Architecture
- 113 8.4 HPM.1 Components
- 115 8.4.1 FPGA Firmware Upgrade
- 116 8.4.2 Payload Firmware Upgrade
- 116 8.4.3 IPMC Firmware Upgrade
- 117 8.4.4 Manual Rollback
- 117 8.4.5 Retrieving Versioning Information
- 118 8.5 Sensors
- 126 8.5.1 Firmware Progress, OS Boot, and Boot Error Sensor
- 126 8.5.2 Boot Bank Supervision Sensor
- 127 8.5.3 POST Results Sensor
- 127 8.5.4 Power Good Sensor
- 127 8.5.5 Power Interface Sensors
- 128 8.5.6 Reset Cause Sensor
- 128 8.5.7 Presence Sensors
- 128 8.5.8 Voltage and Temperature Sensors
- 130 8.6 POST
- 131 8.7 FRU Inventory
- 131 8.7.1 MAC Address FRU OEM records
- 133 8.8 Reset and Power Domains
- 134 8.9 Power Management
- 134 8.10 U-Boot Boot Configuration Parameters
- 136 8.11 Asynchronous Event Notification
- 137 8.12 Serial Line Selection
- 139 8.13 Built-in Terminal Server
- 140 8.13.1 Evaluating the Version of the Telnet Server Firmware
- 140 8.13.2 Establishing a Telnet Session
- 142 8.14 Fail Safe Logic and Watchdog Support
- 142 8.14.1 SP BMC Watchdog
- 143 8.15 Payload Interface
- 143 8.16 Payload Boot Bank Selection
- 144 8.17 Settable Graceful Shutdown Timeout
- 145 8.18 FPGA Health Check
- 145 8.19 Local System Event Log (SEL)
- 145 8.20 IPMI Hardware Watchdog
- 146 8.21 Emerson OEM Command Set
- 146 8.21.1 Set Serial Output Command
- 148 8.21.2 Get Serial Output Command
- 149 8.21.3 Set Feature Configuration
- 151 8.21.4 Get Feature Configuration
- 153 A Related Documentation
- 153 A.1 Emerson Network Power - Embedded Computing Documents
- 155 Safety Notes
- 159 Sicherheitshinweise