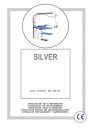
advertisement
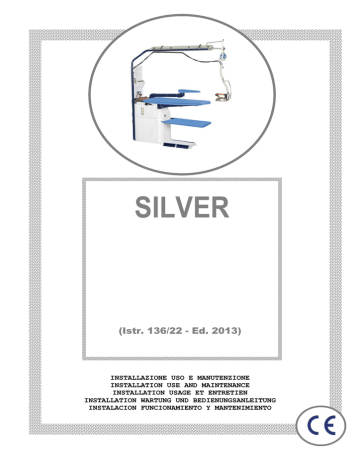
E N G L I S H C H A P T E R
Capitolo 4
INSTALLATION
AIR EXHAUST SHAFT CONNECTION
PACKING
The machine is packed into a special export cartoon (INDUPACK) fixed on a fumigated pallet.
TRANSPORT
All the installation operations must be undertaken only by competent personnel equipped with the necessary protection.
Do not use water jets against the machine for any reason and avoid sudden movement or violent blows. Do not carry the machine by hand, but only by forklift truck or tackle.
It is advisable to move the machine complete with the packing to where it is to be installed and then unpack the machine.
UNPACKING OF THE MACHINE
(SEE DRAWING PAGE 10-7, FIG. 1)
To connect the air exhaust shaft proceed as follows:
a) Remove the right side panel “POS. 28”
b) Assemble the shaft “POS. 27” with the four bolts supplied.
c) Insert the electric cable “POS. 7” on the side of the shaft and block it with the four clamps so that it does not obstruct any moving parts.
d) Insert the male terminals “POS. 2” in the female terminal “POS. 29” and push them together tightly, making sure that they are perfectly connected to guarantee good electrical contact.
e) Reassemble the right side panel “POS. 28”.
ROTATING IRON HOLDER
CONNECTION
Proceed as following:
a) Remove the indupack by using proper tools.
b) Remove the plastic protection.
c) Verify that the machine has not suffered damages during the transport.
d) Take away from the pallet all the accessories not fixed or bolted, as they can damage property, persons or animals when falling down.
e) Remove the bolts fixing the machine to the pallet
f) Sling the machine by means of two ropes
(verify that are suitable for the total weight of the machine), one at the rear and the other at the front side of machine; then lift it by means of forklift truck or tackle and place it where it must be installed, without moving it by hand.
g) When installation has been completed, carefully refit all the panels, protection devices and the accessories.
Various distances from the walls and other equipment must be observed during the installation of the machine in order to ensure smooth operation and good maintenance.
The equipment does not require any fixing to the floor.
It is recommended that the equipment should be installed dead level.
(SEE DRAWING PAGE 10-7, FIG. 1)
Proceed in the following way:
a) Insert the iron support “POS. 44” in the rotating iron holder “POS. 45” and fix it with the hand wheel “POS: 46”.
STEAM ELECTRIC VALVES
CONNECTION
(IRON AND STEAM BOARD)
(SEE DRAWING PAGE 10-7, FIG. 2)
Proceed as follows:
a) Connect the steam output electric valve of the iron “POS. 92” to the corresponding connection “POS. 91”.
b) In the case of a steam machine, connect the board steam valve “POS. 5” to the corresponding connection “POS. 89”.
c) Connect the board steam pipe “POS. 90” to the fitting of the board steam valve “POS. 5”.
d) Connect the valves to the electricity according to the numbers shown.
Page 4-1
E N G L I S H C H A P T E R
LAMP CONNECTION CONTROL PEDAL CONNECTION
(SEE DRAWING PAGE 10-7, FIG. 3)
Proceed as follows:
a) Fix the lamp holder rod “POS. 40” to the support assembled on the machine “POS. 41” without completely tightening the bolts.
b) Insert the lamp “POS. 42” in the lamp holder rod and turn it until its end meets the centre of the end of the board; this is so that the ironing board is correctly illuminated and to optimise the use of the iron. At this point you can tighten the bolts.
c) Connect the lamp electrically following the corresponding electrical outline (see chapter
11).
IRON CONNECTION
(SEE DRAWING PAGE 10-7, FIG. 3)
Proceed as follows:
a) For machines with the lighting group (with or without lamp):
1. Interlace the electrical cable and steam tube and fix them with the spring hooks on the lamp holder.
2. Connect the hook of the spring balance
“POS. 43” to the iron.
b) Connect the steam tube of the iron to the steam electric valve connector “POS. 92” (see
FIG. 2).
c) Connect the iron electrically to the socket
“POS. 93” (see FIG. 5).
ARM FORMS CONNECTION
70)
(diameter
(SEE DRAWING PAGE 10-7, FIG. 4)
Proceed as follows:
a) Place the arm forms supplied in their encasements in any order you wish “POS. 94” and “POS. 95”.
b) If the form heats electrically, connect it to the plug “POS. 96” (see FIG. 5).
(SEE DRAWING PAGE 10-7, FIG. 6)
If a steam pedal “POS. 88” is supplied, fix it on the front part of the base by hooking it to the proper grommet.
If there is a second steam pedal supplied “POS.
98” and if is to be used, it must be assembled on the opposite side of the machine.
(
WATER CONNECTION
FOR MACHINE WITH BOILER)
(SEE DRAWING PAGE 10-3)
Fit a 3/8" zinc-platted gas pipe to within 100 cm of the machine.
Fit a ball valve with tube connector “POS. 66” to the end of the tube, and connect it by a rubber hose (Øint 13 mm) suited to the mains water pressure to the water input ”POS. 14”.
In the case of the boiler being feed from a water tank, request the manufacture for information regarding the modifications to be made to the pump.
Connect the drainage gate valve “POS. 17” to the drain using a rigid heat-insulated pipe.
In the case of there not being a drain near by, or the drainage of hot water not being allowed, use a 15-20 litre tank to collect the boiler waste water
(the water can then be disposed of when it has cooled).
N.B.: if local regulations regarding the contamination of the water mains so require, install a water feed tank or one-way flow device to prevent the back-flow of possibly polluted water to the water mains (for example, a GIACOMINI R
624).
N.B.: it is advisable to avoid connecting a water softener as the use of treated water in small electrical boilers causes the formation of copious quantities of foam which is drawn in to the machine when steam is used, with consequent damage to the clothes.
In the case of excessively hard water(more than
17° French=12° English), a water softener may be installed to reduce the dissolved salts by no more than 5° (French) or 3.5° (English).
Page 4-2
E N G L I S H C H A P T E R
COMPRESSED AIR CONNECTION
(ONLY FOR STEAMING TABLE OR FOR
MACHINE WITH STEAM/AIR GUN)
The machine needs to be compressed air, without condensation or oil, at a pressure of 7 bars (100 psi).
Fit a rilsan or zinc-platted 3/8" gas pipe to within 1 meter of the machine.
Assemble a three-way ball tap or a sliding tap on its end “POS. 25”.
This 3-way ball valve serves to feed the machine
(position 1 = ON = OK) or to turn off the supply
(position 0 = STOP) by discharging the air remaining in the machine through the silencer.
This ensures that whenever any maintenance is required, there is the guarantee that there is no danger from compressed air (jets of air, etc.) simply by turning the air ball valve to the 0 =
STOP position (or letting the ring nut slip).
Using a pipe in rilsan, inside=6mm (0,23 inches) resistant up to a pressure of at least 20 bars (290 psi), connect the tap to the compressed air filter “POS. 13” of the machine, if supplied, to the air valve “POS. 47”, if supplied, and to the stain removed pistol, if supplied.
STEAM AND CONDENSATION
RETURN CONNECTION
(FOR MACHINES WITHOUT BOILER)
As illustrated in drawing page 10-4, the machine can be directly connected to a small boiler, without drainage.
As a result, it is imperative that: fed with clean
a) The height ‘H’ from the floor to the condensation drainage hole is greater than a minimum of 200 mm (8 inches) from the water level ‘K’ in the boiler, measured on the same plane;
(SEE DRAWING PAGE 10-3)
(SEE DRAWING PAGE 10-4)
b) A steel or copper pipe with the recommended minimum diameter is used;
c) The pipes are at a constant angle, with curves of at least 50 mm (2 inches) radius, that there are no constrictions or narrowing in the pipes (e.g. tight gate valve connection) and that the length of each pipe is not greater than
2.5 metres (=100 inches).
All these precautions are imperative in order to avoid water being siphoned back equipment. into the
If it is not possible to observe these precautions, a traditional connection must be made, using
ELECTRICAL CONNECTION
BOILER WASHING
(SEE DRAWING PAGE 10-5)
Ensure that the mains voltage and phase correspond with the data given on the machine specification plate (see page 2-1).
Prepare an electrical line dimensioned as indicated on the table shown in the drawing on page 10-5. Insert the cable in the holder “POS. 8”, block it with the collar “POS. 9” and connect with the clamps to the electrical current.
The electrical supply line must be fitted with an automatic differential heat safety cutout switch 30 mA with a mechanical plug and socket block.
The machine as per the rules in force must be connected to a good earth, or the guarantee will not be honoured. Before first testing the machine, check that none of the electrical connectors have worked loose during transport.
After connection to the electricity supply, check the rotation direction of the motors (fan).
If the direction is wrong, invert the connection of two of the three phases supply wires. Replace all the panels and protection devices when the electrical connections have been completed.
(FOR MACHINE WITH BOILER)
(SEE DRAWING PAGE 10-3)
When a new machine is installed, or when restarting after it has been stopped for more than a condensation gate valve, as illustrated in Drawing page 10-4 (figure on the top).
For this type of connection, take a 1/2" steel gas pipe from the top of the central steam conduit and fit it 100 cm from the machine.
Fit a ball valve “POS. 67” to this pipe so as to isolate the machine from the plant.
The connection between the ball valve and the machine steam input “POS. 4” can be made using a copper tube with an internal diameter of 14 mm.
Remember that the machine operates with steam at a pressure of 4 - 6 bars (58 - 87 psi), and therefore, if the machi ne is connected to a steam pressure, a generator working at a higher pressure reducer has to be installed.
Connect a 1/2" basin-type condensation, fitted with a filter ( SPIRAX SARCO HM 007 or JUCKER
SA8), to the condensation return junction drain
“POS. 3”.
A gate valve must be fitted after the drain to avoid backpressure.
A ball valve must be fitted on the condensation return pipe “POS. 68” (1/2" gas pipe) to allow the isolation of the machine from the plant.
Page 4-3
E N G L I S H C H A P T E R one week, the boiler must be thoroughly washed.
The procedure is as follows:
a) Turn on the boiler and bring it to a pressure of approximately 2 bars (30 psi).
b) Turn the boiler off and drain the water into the main drains or drainage tank half opening the tap “POS. 17”, taking care not to burn yourself.
c) When all the water has been drained, turn off the drainage valve “POS. 17. The water will probably be a dark colour.
d) Turn the boiler on again and bring it to a pressure of 2 bars (30 psi).
e) Repeat the cycle of point s b) - c) - d) four times. The water should progressively become cleaner. If it is still dirty, repeat the washing cycle another 3 or 4 times, until it is completely clean.
If the boiler is not w ashed as described above there is the risk of dirty water being siphoned back, or a rust colour visible during steaming.
USE OF THE TABLE
PRELIMINARY CONTROLS
For machine with built-in boiler (see draw ing page 10-3):
a) Check that the drainage ball valve “POS. 17” is well closed
b) Check that the water feed ball “POS. 66” is open
c) In the case of the steam machine or the air-
steam stain remov ed pistol, check that the ball tap for the compressed air feed “POS. 25” is open and discharges any condensation deposited in the compressed air filter bowl by turning the tap “POS. 1”.
d) If the machine has been stopped for a long time check that the pump is not jammed due to internal deposit. Check that the shaft turns manually using the carving for screwdriver on the shaft end, ventilation
N.B.: do not run the pump with the water valve closed, as this will ruin irreparably the pump.
For machine without boiler (see drawing page
10-4):
a) Check that the ball valves fitted on the steam pipe “POS. 67” and on the condensation return pipe “POS. 68” are open.
b) In the case of the steam machine or the
spot removed pistol, check that the ball tap for the compressed air feed “POS. 25” is open and discharges any condensation deposited in the compressed air filter bowl by turning the tap “POS. 1”.
At first, when the machine is cold, the steam will condense rapidly and it is therefore advisable to wait a few minutes before starting work so that the condensation can be drained off .
If this is not done , condensation formed will emerge from the steam pipes, damaging the garments being processed.
Page 4-4
START-UP OF THE MACHINE
(SEE DRAWING PAGE 10-6)
Proceed as following:
For machine w ith boiler (electronic lev el
control) (see Fig. 2):
a) Turn on the general electrical supply switch.
b) Turn on the main switch of the machine “POS.
69”: the main red lamp “POS. 58” will light up; in the case of a steam machine the orange lamp of the steam device will also light up
“POS. 80”.
c) Turn on the boiler switch “POS. 57”, and the red water feeding warning “POS. 56 light on and when the right water level has been reached the red warning of automatic switch on of heating elements “POS. 55” light on.
d) Check on the Manometer “POS. 71” that the steam pressure reaches to 2,8 bar (40 psi) or.
4,8 bar (70 psi
For machines without boiler (see Fig. 3):
a) Turn on the main switch of the electric power.
b) Turn on the main switch “POS. 79” on the electrical panel of the machine; in the case of a steam machine the red lamp of the steam device “POS. 80” will light up.
USING THE BOARD HEATER
(SEE DRAWINGS PAGE 10-6)
Turn on the board heater switch “POS. 82”.
The heat temperature is controlled by thermostat “POS. 83”; the maximum temperature that can be set is 150 °C= 300 °F.
USING THE HEATED ARM FORMS
Proceed in the following way: form.
(SEE DRAWINGS PAGE 10-6)
USING THE STEAM IRON
the
a) Rotate the arm form that you want to use by placing it in the work position.
b) Turn on the heating switch for the arm forms
“POS. 84”. The heating temperature is controlled by a thermostat on the inside of the
c) To help the use of the aspirator on the arm form, rotate the lever “POS. 48” counterclockwise until the aspirator is off the board and then orient it to the arm form.
(SEE DRAWINGS PAGE 10-6)
Proceed as follows:
a) A few minutes before beginning the finishing operation switch on the iron switch “POS. 85” and check that the knob of thermostat is about at the centre of the middle quadrant.
b) Hold the iron and push at regular intervals the push button until some steam comes out.
Verify that steam coming out from the iron is
E N G L I S H C H A P T E R not mixed worth water, as in this case this would mean that the temperature of the iron is too low therefore wait for some minutes.
c) If necessary, control the quantity of steam flux by means of the knob of steam valve.
N.B.: for use of the ‘Electronic Iron’, see specific manual relating to the iron.
USING THE AIR-STEAM STAIN
REMOVED PISTOL
Proceed as follows:
a) Place the part of the item to be cleaned on the end of the support and press the pedal “POS.
86” (see page 10-7, FIG. 6).
b) Press the left button of the gun to release the steam. For the first few seconds the steam is mixed with water. Therefore discharge the pistol for a few seconds until it is well heated.
c) Distribute the jet of st eam onto the stain with the gun, moving it in rotator way. Abundant steaming instantly di ssolves water-soluble stains.
d) If required dry the stained area spray stain with compressed air by pressing the button on the right of the gun. Move the gun rapidly back and forth in a zig-zag motion to remove the dampness in the stain with the air. The strong, concentrated vacuum allows rapid drying.
USING THE VACUUM AND BLOWING
DEVICES
(SEE DRAWING PAGE 10-7, FIG. 6) operate the table in the following way: to from trouser creases and to finishing etc) or on garments that are very creased.
USING THE STEAMING DEVICE
the
To ensure maximum efficiency it is advisable to
a) Vacuum, by pressing pedal “POS. 86”, used garments made from heavy materials (cotton
b) In other cases for finishing topper area of trousers, the trouser’s seam and the lining of jackets and coats preferably should be used blowing pressing pedal “POS: 87”, allowing to finish on an air cushion which enables the operation to increase production considerably .
c) It is advisable to work with the point of the board on the right, thus allowing the operator to hold on the garment with left hand and the iron with the right. At the same time it is possible to use the steam iron while operating blowing for drying the garment. This reduces considerably the movement of the garment itself. use.
Only when the pilot light is off can the steam be used by pressing the pedal “POS. 89”.
During steaming short busts of steam are blown out which will help the immediate flow of steam, especially towards the front part of the ironing board.
The thermostat placed on the outside of the machine “POS. 83” adjusts the temperature of the resistor of the superheater up to a maximum of
150°C=300°F, so that the ideal steam is reached on the ironing board.
By decreasing or increasing the temperature of the superheater it is possible to have wetter or drier steam. In this case the steam switch must be turned off “POS. 82”.
OPERATION OF THE ELECTRONIC
LEVEL
(SEE DRAWING PAGE 10-6 FIG. 2)
When the boiler is empty, the electronic timer, after 3 seconds from switch on, will call for water till to cover the probe.
The heating elements are switched off till the water has reached the water level sensor probe.
If after a further 2 minutes the water has not reached the right level for work, check that the water supply valve is not closed and if so, open the valve and reset the machine.
If the water supply is correct, first check the reason why water is not running in the boiler.
For further troubles or anomalies in operation, please read the chapter "Breakdowns to the boiler and to electronic level".
In operation when the correct water level is obtained the heating elements are switched on.
As the water level decreases and the level sensor probe becomes uncovered, the water pump and inlet valve are again switched on without switching off the heating elements that if after this 20 seconds delay the correct water level is not restored than the heating elements are switched off automatically.
If after 2 minutes, the water has not reached the level to work, the timer will block the water loading device safeguarding it
OPERATION OF THE SAFETY
THERMOSTAT
The safety thermostat is located in the electric panel: it cuts off the operation of the boiler group when the boiler body reaches 190°C; it must be manually reset.
(SEE DRAWINGS PAGE 10-6, 7)
By turning on the switch “POS. 82” the steam device is ready for use.
If the temperature of the table is low, the pilot light
“POS. 80” will light up which will signal the operator that the steam device is not ready for
Page 4-5
E N G L I S H C H A P T E R
SHUTTING DOWN OF THE
MACHINE
If the machine is fitted with a boiler, proceed as follows:
a) A few minutes before stopping work, turn off
b) When the boiler pressure has dropped below
c) Turn off the water supply ball valve “POS. 66”.
d) In the case of a steam machine or one w ith
e) Disconnect the switch of the electrical panel of
(SEE DRAWINGS PAGE 10-3 AND 10-6) the boiler by “POS. 57” and continue working until the steam is finished. approximately 1 bar (approximately 15 psi), open the discharge gate valve "POS.17", empty the boiler and then close the gate valve. Turn the boiler on again, and run in fresh water. As soon as the pump has stopped, turn the boiler off without draining it.
a steam stain removed pistol, close the ball tap assembled on the air compression line
“POS. 25”.
the machine “POS. 79” (machine with a boiler with a float level check) or
(machine with a boiler with an electronic level check), then the main switch on the electrical current line.
N.B.: it is advisable to carry out the procedure in
1b every evening to ensure a long and efficient boiler life and to avoid the siphoning-back water.
For machines w ithout boiler proceed as follows:
a) Close the two gate valves “POS. 67” fitted to the steam line and the condensation return
“POS. 68” (see page 10-4).
b) In the case of a steam machine or one with
a stain removed pistol, close the ball tap assembled on the air compression line “POS.
25”.
c) Turn off the electrical control board switch and then the main switch fitted to the electricity supply.
MAINTENANCE
“POS. 69” of
The following instructions are of prime importance in keeping the machine perfectly efficient, ensuring its maximum performance, and avoiding expensive down time.
The first part of this section is divided into maintenance chapters according to periodic schedules.
N.B.: the frequency indicated (weekly, monthly, etc.) is indicative and refers to a machine that operates under ‘normal’ conditions.
The individual customer has to decide on the exact frequency of the maintenance work on the basis of the following guidelines:
The amount of work done by the machine;
The hardness of the water, which causes a greater or lesser scaling of the boiler heating element;
The amount of dust in the air;
Other local working conditions.
All the maintenance operations must be undertaken with the machine completely switched off, and in particular:
a) The general electrical power switch must be off and the plug removed from the socket;
b) The water supply ball valve (for machines with boiler) “POS. 66” (see drawing page 10-3) must be closed. The boiler drainage valve
“POS. 17” (see drawing page 10-3) must be closed;
c) The two gate valves “POS. 67” fitted to the steam line and the condensation return “POS.
68” (see page 10-4) must be closed.
d) In case of machine with steaming device or with steam air gun the compressed air ball valve “POS. 25” (see page 10-3) must be closed and all the compressed air in the machine must be discharged.
e) The hot parts of the machine must be left to cool (internal pipes, valves, the boiler, if fitted, etc.) in order to avoid burns.
Only by observing all these precautions, and the particular conditions relating to the individual maintenance jobs, is it possible to carry out maintenance work on the machine with complete safety. Remember ‘ you can nev er by too
careful’!
In order to make potential dangers more evident, adhesive symbols have been applied to critical parts of the machine: the meaning of these symbols is explained in deta il in the red section at the beginning of this manual (Prescription, danger and indication signals).
N.B. In any case, the maintenance w ork must be undertaken only by competent personnel who can take personal responsibility for their own safety and that of other persons, animals and property. The law , and in particular the latest EU Directiv es, severely punish the owner of a machine w ho allows maintenance work to be carried out by non-qualified personnel
WEEKLY MAINTENANCE
Machine with boiler:
a) Boiler safety valves: check carefully its correct working and that it does not vent steam. In the case of a malfunction, replace the safety valve: request the services of a competent technician whole
Page 4-6
E N G L I S H C H A P T E R
b) Also check the correct functioning of the gauge, pressure gauge and pump.
For machine with and without boiler:
a) In the case of a steam machine, check the air compressor filter, empty the water depo-sited in the filter bowl using the discharge tap.
SIX MONTHLY / YEARLY
MAINTENANCE
For machines with boiler, (electronic lev el control) proceed as follows:
a) Carefully clean the heat ing elements of any scaling. This is of a great importance for the performance of the boiler, and it is easy to do.
Simply remove the flange with the heating elements and carefully clean them. During this operation it is important to disconnect the copper tube that connects the pump to boiler, and clean the joint, where the water enters into the boiler, of any deposits that may be obstructing it. the
b) Check the various gaskets and gate valves as continuous heating and cooling can cause leaks. Should there be leaks, remove the gaskets and gate valves and replace with new to prevent further leaks.
c) Clean the water filter fitted to the feed electrovalve. To do this, remove the sleeve, remove the filter inside the electrovalve and clean the latter with compressed air.
d) Disconnect the copper pipes that connect the gauge and the pressure gauge and clean them internally to remove any scaling.
e) In case of boiler with the electronic lev el
control remove the probe and carefully clean it of any sediment or scaling using an emery cloth. Assuring that the spindle/electrode doesn't revolve in the sonde support body, otherwise tighten the superior nut.
f) Check the wear of the board padding and, if necessary, substitute it. The board padding is considered a part of the normal wear and tear since ironing tends to matt the padding and decrease the aspiration and steaming capacities of the board.
g) Carry out a visual inspection inside the boiler, at least once a year, to control the conditions of the inside walls and the presence of possible scales and/or corrosions. Carefully clean the inside of the pipe containing the probe.
h) Disassemble the safety valve and clean the joint, on which is assembled, of any scaling.
Also check that the valve is not obstructed.
For machine without boiler a) Clean the filter fitted on the condensation return pipe that, if dirty, stops drainage and allows the siphoning back of water.
For all the machines:
a) Clean the air pipe from any impediment (dirty) that stops the airflo w during the ventilation phase.
b) Check the condition of all the plates on the machine (warnings instructions). If they are in replace them. labels and and poor condition,
BREAKDOWNS
Problem:
Causes: Action:
IMMEDIATELY FOLLOWING INSTALLATION FOR MACHINES WITH BOILER
1. The water feeding light is on; the pump works and produces a strange noise without stopping.
2. The boiler does not gain water pressure and the feeding light is on.
3. The mercury switches spark.
1. Water is not reaching the machine.
2. The drainage gate valve is not tightly closed.
3. Do not worry this is the normal functioning of the switches.
1. Check the reason for the water not reaching the machine. Letting the pump run without water will damage it beyond repair.
2. Close the drainage gate valve.
IMMEDIATELY FOLLOWING INSTALLATION FOR MACHINES WITHOUT BOILER
1. The steam is wet after the first few work cycles.
1. Causes
a) The drain has been installed in the wrong place.
1. Solutions:
a) Check that a steam trap is mounted to the condensation return pipe or find a
Page 4-7
E N G L I S H C H A P T E R
b) The check valve has been installed in the wrong direction, or has not been installed at all.
c) Water in the steam feed pipe. better place to install it.
b) Check the check valve flow direction, or install a check valve.
d) Siphoning in condensation return pipe. the
c) Install a steam trap at the end of the pipe between the steam feed pipe and the condensation return, or better upstream of the machine.
d) Eliminate the siphoning to create a slope towards the drain.
BREAKDOWNS ON THE BOILER AND ON THE ELECTRONIC LEVEL CONTROL
1. The water-feeding valve is open, but the electronic station alarm is on (red led is blinking and alarm is beeping).
2. Water is sucked back during steam generation at ironing start.
3. Water is sucked back during steaming, even after having restored the correct level (as per
Pos. 2).
4. No water in the boiler with consequent control group. heating elements burning due to the failure of the electronic level
1. Water is not fed into the boiler and the station is signalling the error.
2. Causes:
a) The machine has not been used for several hours.
b) The ball valve on the water pipe was not closed on the previous evening.
c) The ball valve is out of order and does not close properly.
3. Causes:
a) The electric feeding valve is out of order or dirty, and prevents the pin from closing tight, water leaks in.
b) Water is not drained every day from the boiler, and foam develops.
c) The boiler level gauge has lime scales (mostly on its end): the machine does not operate correctly and water is fed in continuously.
d) Interruption on wires and on connection contacts of the level gauge on the electric panel.
e) Electronic group failure.
4. If the correct water level into the boiler is not restored in 20 seconds the electronic group and the level gauge automatically switch off the heating elements, avoiding burning them. Obviously a
1. Check that water is actually fed into the machine and, if necessary, clean the passages as indicated at Pos. 5.
2. With the machine in operation, drain water from the boiler by opening the boiler drain ball valve slowly until the pump starts re-loading water. Now close the drain cock.
3. Solutions:
a) Replace the water-feeding valve.
b) Remember to drain the boiler every evening so as keep it free from foam and scales.
c) Disassemble the level gauge and carefully remove lime scales from the gauge body by means of emery cloth. Make sure that the pin/electrode does not rotate inside the gauge holder, if necessary screw the upper nut tight.
d) Restore continuity on wires and connection contacts between level gauge and electric panel.
e) Replace the electronic station inside the electric panel.
4. Replace the level gauge or the electronic group or both.
Performs the checking procedure as per Pos. 3C.
Page 4-8
E N G L I S H C H A P T E R failure of the level gauge or of the electronic group would
5. No water in the boiler due to a failure of the water-feeding group (electric valve, tubes and connections). prevent this automatism and would burn the heating elements.
5. Causes
a) No water from the feeding system.
b) The water filter assembled on the electric feed valve is clogged.
c) Electric feed valve failure.
6. The pump does not work.
7. Heating elements and pump lights are off and there is no pressure in the boiler.
d) Lime scales clog tubes and connections.
6. Causes
a) Scales block the pump rotor.
b) Pump motor burned.
7. The boiler temperature has reached 190°C and the safety thermostat has cutted off the operation of the boiler group.
5. Check the water feeding group :
a) Make sure that water is fed into the machine by removing the rubber pipe mounted on the feeding pipe holder.
b) Clean the filter net by disassembling the rubber feed pipe holder.
c) Check if the coil of the feed valve is burned, if so replace it.
d) Free and clean tubes and connections from lime scales.
6. Solutions:
a) Try to operate the pump rotor by rotating the motor shaft by means of a screwdriver applied into the slit on the pump motor side. If this fails, the pump cover must be disassembled, the brass fan must be cleaned and the checked. correct rotation
b) Replace the pump motor.
7. Turn off the machine and please contact the assistance.
More frequent prev entive maintenance is recommended in the future. (See Section
“Maintenance”).
BOILER HEATING ELEMENT BURNT OUT
1. The burnt-out element shows clear signs of melting of the external copper tube.
2. The burnt-out element is a whitish colour with blisters all along the heating element surfaces
1. Lack of water in the boiler due to malfunctioning of the water level control device.
2. The heating element is covered with thick scaling that inhibits the diffusion of heat
1. Carefully check the working of the water level control device and replace any worn parts.
2. Clean the boiler and remove all scaling before fitting a new heating element
More frequent prev entive maintenance is recommended in the future. (See chapter
“Maintenance”).
STEAM IRON
1. Steam iron does not heat. 1. Causes
a) Break of cable continuity.
b) Iron resistance burned.
1. Solutions:
a) Repair the electric cable continuity.
b) Replace resistance. the burned
Page 4-9
E N G L I S H C H A P T E R
2. Steam iron overheating.
3. From the iron comes water mixed with steam.
4. Steam overheated from the iron.
c) Iron thermostat contacts faulty.
2. Thermostat contacts faulty.
3. Causes:
a) Iron temperature too low.
b) In case of machine with boiler check that water to the iron is not a boiler suction due to anomalies of the boiler itself.
4. Iron temperature too high.
c) Replace the thermostat and the fuse.
2. Replace the thermostat.
3. Solutions:
a) Rotate the iron thermostat handwheel clockwise, increasing the iron temperature
b) See paragraph “Breakdowns to the boiler”
4. Rotate the iron thermostat handwheel anticlockwise, decreasing the iron temperature.
BREAKDOWNS TO THE STEAM/AIR SPOTTING GUN
(IF FITTED)
1. Steam available to the machine, but pushing the gun button no steam available from nozzle.
1. Causes:
a) Microswitch defective. contact
b) Break of the gun continuity. cable
c) Solenoid valve coil burned.
1. Solutions:
a) Check the microswitch contact and if necessary replace it.
b) Check the continuity and repair accordingly.
c) Replace burned coil.
EXHAUST FAN BREAKDOWNS
1. The exhaust fan does not work.
1. Causes:
a) Foreign objects block the fan.
b) The micro-switch on the pedal does not work.
c) The motor condenser burned out.
d) The motor is burned out. is
1. Solutions:
a) Unblock the fan byremoving the foreign bodies that are blocking it.
b) Change the micro-switch on the pedal.
c) Change condenser. the motor
d) Change the motor.
ORDERING SPARE PARTS
The spare parts must be ordered only by fax with codes and descriptions in order to ensure the rapid despatch of the parts.
IMPORTANT
For electrical components other than for
220V/230V/240V 50 Hz supply (check on the specification plate of the defective part), add to the order code the letter corresponding to the rating required as given in the following table:
A
B
C
D
E
220V/230V 60Hz.
240V 50Hz.
F
G
H
I
L
M
200V 50Hz.
200V 60Hz.
190V 50Hz.
115V 60Hz.
110V 60Hz.
208V 50Hz.
24V 50Hz.
240V 60Hz.
254V 50Hz.
Example 1:
A 230V 50 Hz coil remote required. control switch is
Complete order information:
Machine model: Table Type .....
Registration No. 110227
Code No. 04775 - coil remote switch 230V/50 Hz
1 piece
Example 2:
The same coil, but 254V, 50 Hz.
Complete order information:
Machine model: Table Type ..... control
Registration No. 110228
Code No. 04775/M coil remote control switch 254V/50 Hz
1 piece
Page 4-10
E N G L I S H C H A P T E R
N.B.
1. The parts that appear in this manual without an accompanying code number ARE NOT
AVAILABLE from stock.
2. The codes “POS.96” or “POS. 97” etc. that appear next to some parts have nothing to do with the spare part code for these parts, and should not therefore be quoted in orders for spare parts.
STORAGE OR DEMOLITION
THE SPECIFICATIONS, THE DESCRIPTIONS
AND THE ILLUSTRATIONS CONTAINED IN
THIS BOOKLET ARE NOT IN ANY WAY
BINDING. DUE TO CONTINUOUS RESEARCH
AND DEVELOPMENT TO IMPROVE OUR
PRODUCTS, THE MANUFACTURER
ALTER SPECIFICATIONS WITHOUT PREVIOUS
NOTICE.
MAY
We trust that these few pages w ill be of use to you and wish you ‘Buon lavoro!’ as we say in Italy — May your work go well!
Technical Office
In case of a long period storage, it is necessary to disconnect the hydraulics, electric and pneumatic feeding sources.
Machine with boiler:
a) Drain the boiler, the condensates tanks and also the water-feeding tank (if existing).
b) Drain all the water left into the pump, by unscrewing the hexagonal screw on the lower side of the pump casing (the side of the water feeding), then screw again.
c) Carefully clean the internal walls of the boiler of any sediment or scaling.
d) Clean the boiler connections and pipes to remove any scaling.
e) When all these operations have been completed, turn off the water feeding valves and the drainage valves.
Machine without boiler:
a) Drain the condensates tank (if existing).
b) Clean all connections removing any scaling.
c) Turn off all the steam feeding valves and the of condensate return valve.
For Machines fed by compressed air:
a) Drain the air inside the air filter cup.
Carefully refit all the panels of the machine and cover it with a cloth to shelter from the humidity and dust.
In case of demolition of the machine, proceed as follows:
a) Drain the boiler, the condensate tank and the water-feeding tank directly into the sewerage system after having made sure that no harmful impurities are inside the water.
b) Remove all the electric, pneumatic and hydraulics components from the panels where they are fixed.
c) Collect into proper container the following parts: plastic, bakelite, cast iron, iron, copper, brass, steel, fabrics, rubber etc. and take them away according to the rules in force.
Page 4-11
advertisement
* Your assessment is very important for improving the workof artificial intelligence, which forms the content of this project
Related manuals
advertisement
Table of contents
- 15 INSTALLAZIONE
- 15 IMBALLO
- 15 TRASPORTO
- 15 MONTAGGIO CAMINO SCARICO ARIA
- 15 MONTAGGIO POGGIA-FERRO GIREVOLE
- 15 MONTAGGIO DELLA LAMPADA
- 15 MONTAGGIO FERRO DA STIRO
- 15 MONTAGGIO PEDALIERA
- 15 CON CALDAIA)
- 15 PISTOLE SMACCHIANTI)
- 15 COLLEGAMENTO ELETTRICO
- 15 CALDAIA)
- 15 USO DELLA MACCHINA
- 15 VERIFICHE PRELIMINARI
- 15 ACCENSIONE MACCHINA
- 15 TAVOLO
- 15 RISCALDATE
- 15 USO DEL FERRO DA STIRO
- 15 VAPORE
- 15 SOFFIAGGIO
- 15 USO DEL DISPOSITIVO VAPORIZZANTE
- 15 ELETTRONICO CALDAIA
- 15 SICUREZZA
- 15 DEL LAVORO
- 15 MANUTENZIONE
- 15 MANUTENZIONE SETTIMANALE
- 15 MANUTENZIONE SEMESTRALE/ANNUALE
- 15 GUASTI
- 15 MACCHINE CON CALDAIA
- 15 MACCHINE SENZA CALDAIA
- 15 LIVELLO ELETTRONICO
- 15 GUASTI AL FERRO
- 15 VAPORE (SE ESISTENTE)
- 15 GUASTI ALL’ASPIRATORE
- 15 RICHIESTA DEI PEZZI DI RICAMBIO
- 23 CHAPTER
- 23 INSTALLATION
- 23 PACKING
- 23 TRANSPORT
- 23 UNPACKING OF THE MACHINE
- 23 AIR EXHAUST SHAFT CONNECTION
- 23 ROTATING IRON HOLDER CONNECTION
- 23 (IRON AND STEAM BOARD)
- 23 LAMP CONNECTION
- 23 IRON CONNECTION
- 23 ARM FORMS CONNECTION (diameter 70)
- 23 CONTROL PEDAL CONNECTION
- 23 BOILER)
- 23 STEAM/AIR GUN)
- 23 BOILER)
- 23 ELECTRICAL CONNECTION
- 23 BOILER)
- 23 USE OF THE TABLE
- 23 PRELIMINARY CONTROLS
- 23 START-UP OF THE MACHINE
- 23 USING THE BOARD HEATER
- 23 USING THE HEATED ARM FORMS
- 23 USING THE STEAM IRON
- 23 PISTOL
- 23 USING THE STEAMING DEVICE
- 23 OPERATION OF THE ELECTRONIC LEVEL
- 23 SHUTTING DOWN OF THE MACHINE
- 23 MAINTENANCE
- 23 WEEKLY MAINTENANCE
- 23 SIX MONTHLY / YEARLY MAINTENANCE
- 23 BREAKDOWNS
- 23 FOR MACHINES WITH BOILER
- 23 FOR MACHINES WITHOUT BOILER
- 23 ELECTRONIC LEVEL CONTROL
- 23 BOILER HEATING ELEMENT BURNT OUT
- 23 STEAM IRON
- 23 GUN (IF FITTED)
- 23 EXHAUST FAN BREAKDOWNS
- 23 ORDERING SPARE PARTS
- 34 TRAVAIL
- 34 ENTRETIEN
- 34 ENTRETIEN PAR SEMAINE
- 34 ENTRETIEN SEMESTRIEL/ANNUEL
- 34 CHAPITRE
- 34 INSTALLATION
- 34 EMBALLAGE
- 34 TRANSPORT
- 34 MACHINE
- 34 MONTAGE CHEMINEE DECHARGE AIR
- 34 MONTAGE REPOSE-FER TOURNANT
- 34 REPASSER ET TABLE VAPORISANTE)
- 34 MONTAGE LAMPE
- 34 MONTAGE FER A REPASSER
- 34 MONTAGE GROUPE PEDALES
- 34 CHAUDIERE)
- 34 PISTOLETS DETACHANTS)
- 34 CHAUDIERE)
- 34 BRANCHEMENT ELECTRIQUE
- 34 CHAUDIERE)
- 34 PANNES
- 34 CHAUDIERE
- 34 NIVEAU ELECTRONIQUE
- 34 PANNES AU FER
- 34 VAPEUR (OU PRESENT)
- 34 PANNES A L’ASPIRATEUR
- 34 COMMANDE PIECES DE RECHANGE
- 34 STOCKAGE OU DEMOLITION
- 34 USAGE DE LA MACHINE
- 34 VERIFICATIONS PRELIMINAIRES
- 34 DEMARRAGE MACHINE
- 34 USAGE DISPOSITIF DE CHAUFFE TABLE
- 34 USAGE FORMES POUR BRAS CHAUFFEES
- 34 USAGE FER A REPASSER
- 34 SOUFFLAGE
- 34 USAGE DISPOSITIF VAPORISANT
- 34 ELECTRONIQUE DE LA CHAUDIERE
- 34 SECURITE