advertisement
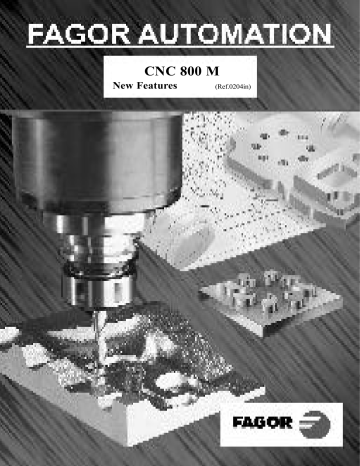
CNC 800 M
New Features
(Ref.0204in)
Version 2.1 (July 1995)
1. P627(1). DIVIDING FACTOR FOR ELECTRONIC HANDWHEEL FEEDBACK
SIGNALS
Machine parameter P627(1) is used with P612(6), P626(6) and P627(6) which indicate the multiplying factor for the electronic handwheel feedback signals for the X, Y and Z axis respectively.
Machine parameter P627(1) indicates whether all handwheel feedback signals are to be divided or not.
P627(1)=0 They are not divided.
P627(1)=1 All handwheel feedback signals are divided by two.
Examples for the X axis so the CNC assumes 100 pulses/turn with 25, 50 and 100 line handwheels:
25 line Fagor handwheel:
50 line Fagor handwheel:
100 line Fagor handwheel:
P612(6)=0 and P627(1)=0
P612(6)=1 and P627(1)=0
P612(6)=1 and P627(1)=1
25 x 4 / 1 = 100 lines
50 x 2 / 1 = 100 lines
100 x 2 / 2 = 100 lines
Version 2.4 (June 1996)
1. HANDWHEELS AFFECTED BY FEED-HOLD.
Until now, it was assumed that electronic handwheels operated like mechanical handwheels and, therefore, were not affected by Feedhold.
However, some applications require the electronic handwheels (manual pulse generators) to be affected by Feed-hold.
Machine parameter "P628(2)" indicates whether they are or not affected by Feed-hold.
P628(2) = 0
P628(2) = 1
Not affected
Affected.
2. AUTOMATIC TOOL CHANGERS (ATC)
With this feature, it is possible to manage tool changers at any time.
Until now, this was only possible while executing a program (P99996) in Automatic Mode.
Parameter setting:
Machine parameter "P628(3)" indicates whether the machine has an ATC or not.
P628(3) = 0
P628(3) = 1
No ATC.
The machine has an ATC.
In either case, the CNC considers machine parameter "P743" and "P745" .
P743
P745
Standard subroutine to be executed prior to a T function
Standard subroutine to be executed after a T function
The subroutines associated with the T function must contain the tool selection sequence and must be defined by the manufacturer in one of the special ISO-coded user programs: P99994 or P99996.
Both subroutines are defined by an integer between 0 and 89.
If set to 0, the CNC assumes that no subroutine is to be executed.
- 2 -
2.1 MACHINE WITH MANUAL TOOL CHANGER
Machine parameter "P628(3)" must be set to "0" (no ATC available).
Basic operation in JOG or DRO mode
Every time a new tool is selected, (T?? - START), the CNC acts as follows:
1.If machine parameter "P743" is set to a value other than "0", the CNC executes that standard subroutine.
2.The CNC outputs the BCD code and assumes the new tool.
3.If machine parameter "P745" is set to a value other than "0", the CNC executes that standard subroutine.
Basic operation while executing an automatic operation
Every time the execution of an automatic operation requires a tool change, (T01 active and the cycle requests T02), the CNC behaves as follows:
1.If machine parameter "P743" is set to a value other than "0", the CNC executes that standard subroutine.
2.It displays the message: "TOOL CHANGE" and interrupts program execution.
3.When the operator presses the [CYCLE START] key, the CNC outputs the BCD code and assumes the new tool.
4.If machine parameter "P745" is set to a value other than "0", the CNC executes that standard subroutine.
5.The CNC resumes the execution of the automatic operation.
Basic operation while executing the ISO-coded user program (99996) a ) One or both machine parameters "P743" and "P745" have been set to a value other than "0".
Every time the execution of the ISO program (99996) requires a tool changer, the CNC behaves as follows:
1.If machine parameter "P743" is set to a value other than "0", the CNC executes that standard subroutine.
2.The CNC outputs the BCD code and assumes the new tool.
3.If machine parameter "P745" is set to a value other than "0", the CNC executes that standard subroutine.
4.The CNC resumes program execution.
b) Both machine parameters "P743" and "P745" have been set to "0".
Every time the execution of the ISO program (99996) requires a tool changer, the CNC behaves as follows:
1.The CNC outputs the BCD code and assumes the new tool.
2.It executes the internal standard subroutine N99, which:
Displays the message: "TOOL CHANGE" and interrupts program execution (M00).
3.When the operator presses the [CYCLE START] key, the CNC resumes program execution.
- 3 -
2.2 MACHINE WITH AUTOMATIC TOOL CHANGER (ATC)
Machine parameter "P628(3)" must be set to "1" (ATC available).
Basic operation in JOG or DRO mode
Every time a new tool is selected, (T?? - START), the CNC acts as follows:
1.If machine parameter "P743" is set to a value other than "0", the CNC executes that standard subroutine.
2.The CNC outputs the BCD code and assumes the new tool.
3.If machine parameter "P745" is set to a value other than "0", the CNC executes that standard subroutine.
Basic operation while executing an automatic operation
Every time the execution of an automatic operation requires a tool change, (T01 active and the cycle requests T02), the CNC behaves as follows:
1.If machine parameter "P743" is set to a value other than "0", the CNC executes that standard subroutine.
2.The CNC outputs the BCD code and assumes the new tool.
3.If machine parameter "P745" is set to a value other than "0", the CNC executes that standard subroutine.
4.The CNC resumes the execution of the automatic operation.
Basic operation while executing the ISO-coded user program (99996) a ) One or both machine parameters "P743" and "P745" have been set to a value other than "0".
Every time the execution of the ISO program (99996) requires a tool changer, the CNC behaves as follows:
1.If machine parameter "P743" is set to a value other than "0", the CNC executes that standard subroutine.
2.The CNC outputs the BCD code and assumes the new tool.
3.If machine parameter "P745" is set to a value other than "0", the CNC executes that standard subroutine.
4.The CNC resumes program execution.
b ) Both machine parameters "P743" and "P745" have been set to "0".
Every time the execution of the ISO program (99996) requires a tool changer, the CNC behaves as follows:
1.The CNC outputs the BCD code and assumes the new tool.
2.It executes the internal standard subroutine N99, which:
Displays the message: "TOOL CHANGE" and interrupts program execution (M00).
3.When the operator presses the [CYCLE START] key, the CNC resumes program execution.
- 4 -
3. TREATMENT OF THE M19 (SPINDLE ORIENT)
When using ATC, the spindle must be oriented before changing tools.
This features implements function M19 to manage spindle orientation.
M19 should be included in the standard subroutine to be executed before the T function (machine parameter P743).
Requirements:
The spindle must have a spindle encoder installed.
This encoder must be connected via connector "A5", which is the same one used for the electronic handwheel associated with the Z axis.
To use this feature on machines having a handwheel associated with the Z axis, connector "A5" must be shared by the handwheel and the spindle encoder.
Precautions on machines having a Z axis handwheel:
· Both feedback devices must be commutated (handwheel and spindle encoder).
· The CNC interprets the feedback signals at connector "A5" as follows:
In "Spindle Orient" mode" (M19) as spindle feedback.
In "Open Loop Spindle" mode (M3, M4, M5) as handwheel pulses.
· If the spindle switches from "Spindle Orient" mode to "Open Loop" mode without swapping the feedback device at connector
"A5", the CNC will take the spindle pulses as handwheel pulses.
Parameter setting:
Machine parameter "P800" indicates whether there is a spindle encoder installed or not and, consequently, whether "Spindle
Orientation" is available or not.
P800 = 0 No spindle encoder installed. "Spindle Orient" not available.
P800 <>0 Spindle encoder line count (number of pulses/rev).
Besides having an spindle encoder (P800 other than 0), the following machine parameters must also be set:
P609(2)
P700
P601(7)
P612(8)
P619(6)
P719
P717
P718
P916
Spindle counting direction
Spindle speed when operating in M19
Sign of the spindle analog output associated with M19.
Type of spindle encoder reference mark (home).
Spindle orient in both directions (Negative S also possible).
Minimum analog spindle output when in M19.
Spindle in-position zone when in M19
Proportional gain K of the spindle when in M19
Spindle Orient position when executing M19 without an "S" value.
Programming format
Spindle Orient is programmed as: "M19 S4.3", where:
M19 Indicates that the spindle is now moving in Closed loop.
S4.3
Indicates the number of degrees it has to move from the reference zero mark
Programming format while in DRO mode
To orient the spindle, proceed as follows:
* Press the keystroke sequence: [F] - [BEGIN] - [END]
* Key in [1] - [9] - [S] - (desired value) - [CYCLE START]
- 5 -
Basic operation
A "M19 S4.3" type block is executed as follows:
* The CNC outputs the M19 code as any other "M" function so the electrical cabinet can execute it.
* If the spindle was in open loop (M3, M4), the CNC slows the spindle down until its speed is below the value set by machine parameter "P700" and, then, homes the spindle.
* The CNC orients the spindle to the preset position (S4.3) and at the speed set by machine parameter "P700".
If a block containing only an "M19" is executed (without "S4.3"), the CNC orients the spindle to the position set by machine parameter "P916". If "P916=0", the spindle spins indefinitely at the rpm set for M19.
using machine parameter "P619(6)".
* The spindle will remain in closed loop until:
An M3, M4 or M5 is executed
An S ???? is executed
A Reset is carried out
An M30 is executed
An execution error comes up
Example:
M3 S1000
M19
M19 S100
S1000
M19 S200
Spindle in open loop and turning clock-wise.
Orient to 100° (from reference mark, home)
Spindle in open loop recovering its previous turning direction (M3):
Spindle in closed loop, home search and orientation to 200º from reference mark.
- 6 -
Version 3.1 (November 1997)
1. GENERATING AN ISO-CODED PROGRAM
With this CNC, the ISO code (low level) for an operation or a part-program may be generated.
To use this feature, machine parameter "P630(1)" must be set to "1".
This ISO program always has the number: 99996 and can be stored either at the CNC or at a PC.
Program 99996 is a special user program in ISO code and can be:
Generated from an operation or a part-program.
Edited at the CNC itself via menu option: "Auxiliary Modes - Edit program 99996"
Loaded into the CNC after being generated at a PC.
Generating the ISO program (99996) at the CNC.
This CNC has 11 K of memory space to store program 99996. If the generated program is larger than that, the CNC will issue the relevant error message.
To generate program 99996, proceed as follows:
* If it is an operation, select or define the desired operation.
* If it is a part-program, select the desired one in the part-program directory and place the cursor on its header ("PART 01435".
A listing of the operations it consists of must appear).
* Press the keystroke sequence: [CALC] [7]. The CNC will show the graphic simulation screen.
* Press . The CNC starts simulating the part and generating its ISO-coded program 99996.
* When done with the simulation, program 99996 stored in CNC memory will contain all simulated blocks in ISO code.
Generating the ISO program (99996) at a PC
Usually, the 99996 program generated from a part-program exceeds the available memory space of the CNC.
By using "DNC30", this program may be generated at a PC.
To do this, proceed as follows:
* Activate DNC communications and execute the DNC30 program at the PC.
* Select at the PC the menu option: "Program Management - Receive Digitizing".
* At the CNC, select the operation or place the cursor on the part-program header ("PART 01435"). A listing of the operations it consists of must appear).
* Press [CALC] [8]. The CNC will display the graphic simulation screen.
* Press . The CNC starts simulating the part and generating program 99996.
* When done with the simulation, the 99996 program generated at the PC will contain all the blocks simulated by the CNC in
ISO code.
This program can be executed at the CNC through the menu option: "Execute infinite program" of the DNC30.
Note: While generating the ISO-coded program, no tool compensation is applied when simulating. However, the generated program will have the corresponding G41 and G42.
- 7 -
2. RIGID TAPPING IS NOW AVAILABLE
From this version on, typical tapping is possible (with a clutch) "P630(3)=0" as well as rigid tapping "P630(3)=1".
For rigid tapping, the CNC must control the spindle checking its turning speed at all times and supplying the necessary analog voltage for the spindle to turn at the selected speed.
General considerations:
Rigid tapping is an interpolation between the spindle and the Z axis.
The acceleration and deceleration time for the spindle and the Z axis should be the same.
The following error (lag) of the spindle and that of the Z axis must be proportional. For example, if when tapping at F1000mm/min,
S1000rpm (pitch=1mm) the observed following error is Z=1mm and S=360º, it means that they are both perfectly synchronized.
A machine parameter is now available to adjust the spindle's response (acc/dec) for each spindle range (gear).
Since the Z axis gain is different for machining and for rigid tapping, the CNC offers 2 parameters, one for each case.
Output THREADING_ON (I97) is active when carrying out a rigid tapping.
Machine parameters related to the spindle:
P800 Number of spindle encoder pulses (0...9999)
P601(7) Sign of the analog S associated with M19 (0 or 1)
P609(2) Spindle counting direction (0 or 1)
P612(8) Type of spindle home marker pulse (0 = -, 1 = +)
P719 Minimum spindle analog voltage (0...255)
P719=0 ==> 2,5 mV
P719=1 ==> 2,5 mV
P719=10 ==> 25.0 mV (10 x 2.5)
P719=255 ==> 637.5 mV (255 x 2.5)
P717
The CNC internally applies a x4 multiplying factor to the pulses coming from the encoder.
Thus, with a 1000 line encoder and P717= 100, the in-position zone will be: (360°/4000)x100= ±9°
P718 Proportional spindle gain K (0...255)
It sets the analog voltage corresponding to a following error of 1 spindle encoder pulse.
Analog (mV.) = P718 x Following error (pulses) x 2.5 mV / 64
P751, P747, P748, P749 Duration of the spindle acc/dec ramp in ranges 1, 2, 3, 4 (0...255) Value 1=20 ms
P746 Feed-forward gain in rigid tapping (0...255)
P750 Z axis proportional gain K1 in rigid tapping (0...255)
P625(1) The tap entry is synchronized with the spindle home marker pulse
Feedback inputs:
P630(4) = 0 Connector A5 is used for spindle feedback and for the Z axis handwheel.
Both feedback devices must be switched externally.
P630(4) = 1 Connector A5 is only used for spindle feedback.
Connector A6 is used for the X axis handwheel.
Connector A4 is used for Y and Z axes handwheels.
PLC output O46 indicates which axis moves when turning the handwheel connected to A4.
"O46=0" for the Y axis and "O46=1" for the Z axis.
ISO Programming
It is programmed by means of function G33 (threading) indicating axis feedrate and spindle speed.
Examples: G33 Z -10 F1000 S1000 M3 F1000 S1000 M3
G33 Z-10
Functions G00, G01, G02 and G03 cancel function G33.
3. CURRENT CNC SOFTWARE VERSION
From this version on, when accessing the EPROM checksum screen [Auxiliary Modes] [Special Modes] [8]
The CNC will show the checksum of each EPROM and the current CNC software version. For example: Version 3.1
4. SCREEN SAVER
When machine parameter “P626(7)=1” the screen saver function acts as follows:
After 5 minutes without pressing any key or the CNC not receiving any new data for refreshing (updating) the screen, it goes blank. Video is restored when pressing any key or when the CNC receives data to update the screen.
- 8 -
5. SEMIAUTOMATIC LINEAR MILLING
To access this mode, select the linear milling mode and press to get into semiautomatic mode.
This operation cannot be stored as in a part-program.
The path angle (
α
) and length (L) must be defined.
Jog the axes with the handwheel up to the starting point and press the corresponding JOG key (just press it once, it does not have to be held down).
The axes will travel the indicated distance "L" in the indicated direction and at an angle " " or until the key is pressed.
6. SEMIAUTOMATIC ARC MILLING
To access this mode, select the arc milling mode and press to get into semiautomatic mode.
This operation cannot be stored in a part-program.
The rounding radius (R) must be defined. Its sign indicates the turning direction (R+ and R-)
Jog the machines with the handwheels to the desired starting point and press the corresponding JOG key (just press it once, it does not have to be held down). The machine will make a 90º arc in the indicated direction.
7. CROSS COMPENSATION
Besides compensating for measuring errors due to inaccurate leadscrews (leadscrew error), this CNC offers cross compensation in order to compensate for errors caused by one axis onto another. A typical case would be beam (ram) sag compensation.
To use cross compensation, one must define the axis to be compensated and the one inflicting the error onto the other one when moving.
Machine parameters related to cross compensation:
P623(1)
P620(5)
Cross compensation applied to the X axis (0=No, 1=Yes)
Cross compensation applied to the Y axis (0=No, 1=Yes)
P620(4) Cross compensation applied to the Z axis (0=No, 1=Yes)
P623(2), P623(3) Axis inflicting the error onto the other one.
X
Y
Z
Affected (compensated) axis
P623(1) P620(5) P620(4)
1
0
0
0
1
0
0
0
1
X
Y
Z
Moving ("guilty") axis
P623(3) P623(2)
0
1
1
1
0
1
Examples: Compensate Y for Z axis movementP620 ( * * * 1 0 * * *)
Compensate X for Y axis movementP620 ( * * * 0 0 * * *)
P623 ( * * * * * 0 0 0)
P623 ( * * * * * 1 0 1)
8. FUNCTION M80 WHEN "Z" AS A DRO AXIS
This feature is available when the Z axis is set to work as a DRO axis. "P617(4)=1".
Whenever the Z axis has to be moved, the CNC shows the text: "Act upon Z".
Also, from this version on, it executes the auxiliary function M80. With this function, it is possible to act upon the hydraulic or mechanical device that controls the Z axis.
- 9 -
9. MACHINE SAFETY REGULATION
This CNC offers the following features to comply with machine safety regulations.
Enabling of the CYCLE START key from the PLC
This feature is available when machine parameter "P630(5)=1"
PLC output O25 indicates whether the CYCLE START key is enabled (=1) or not (=0)
Axes movements controlled by Feed-Hold. (It was already available)
Feed-Hold input, pin 15 of connector I/O 1, must be normally high.
If while moving the axes, the Feed-Hold input is brought low, the CNC keeps the spindle turning and stops the axes with 0V or velocity command (analog signal) and keeping their enables ON.
When this signal is brought back up, the CNC will resume the movement of the axes.
Axes jogging feedrate limited by PLC.
This feature is available when machine parameter "P630(5)=1"
When activating PLC output O26, the CNC assumes the feedrate set by machine parameter "P814"
Handwheel managed by the PLC.
Machine parameter "P628(2)" indicates whether the axes movements with handwheels are affected by Feed-Hold (=1) or not (=0)
Machine parameter "P630(2)" indicates whether the multiplying factor indicated by the MFO switch position is applied (=0) or the one indicated by the PLC outputs O44 and O45 (=1) (already available)
O44
0
1
0
Spindle control from the PLC.
1
O45
0
0
1
1
According to switch setting
Same as x1 setting of the switch
Same as x10 setting of the switch
Same as x100 setting of the switch
This feature is available when "P630(5)=1"
Output O27 =1 "tells" the CNC to apply the spindle analog voltage set by the PLC. The value of this analog signal is set at register
R156 and sent to the CNC by mark M1956.
R156= 0000 1111 1111 1111 => + 10V.
R156= 0000 0111 1111 1111 => + 5V.
R156= 0000 0011 1111 1111 => + 2,5V.
R156= 0000 0000 0000 0000 => + 0V.
R156= 0001 1111 1111 1111 => -
R156= 0001 0111 1111 1111 => -
10V.
5V.
R156= 0001 0011 1111 1111 => 2,5V.
R156= 0001 0000 0000 0000 => 0V.
Also, PLC output O43, lets you control the rotation of the spindle. (Already available).
It must be normally low.
If it is brought up, the CNC stops the spindle.
When it is brought back up, the CNC restarts the spindle.
Information for the PLC on the status of the machine reference (home) search
I88 Home search in progress.
I100 X axis home search done.
I101 Y axis home search done.
I102 Z axis home search done.
- 10 -
Additional CNC information for the PLC
R120 The lower half of this register indicates the last key pressed.
This value is maintained for 200 milliseconds unless another key is pressed before then.
This register can be canceled from the PLC after being processed.
R121 bit 1 Indicates that the Milling operation is selected (=1) bit 2 Indicates that the Positioning operation is selected (=1) bit 3 Indicates that the Pocket Milling operation is selected (=1) bit 4 Indicates that the Boss Milling operation is selected (=1) bit 5 Indicates that the Corner Roughing operation is selected (=1) bit 6 Indicates that the Surface Milling operation is selected (=1) bit 7 Indicates that one of the machining operations (Center punching, Drilling, etc.) is selected (=1) bit 8 Indicates that the "Auxiliary Modes" option is selected (=1) bit 9 Indicates that the "Tool Calibration" option is selected (=1) bit 10 Indicates that the "Graphic Simulation" mode is selected (=1) bit 16 Indicates that the mode relevant to following cycle parameters: "finising pass, finishing feedrate, finishing tool and safety distances on X and Z" is selected (=1)
- 11 -
Version 3.3 (March 1998)
1. MODULAR CNC
The modular 800M CNC consists of the Central Unit module (CPU), the Monitor and the keyboard.
Central Unit.
It is usually located in the electrical cabinet and is mounted by means the holes it has for this purpose on its support lid. Dimensions in mm.
When installing it, observe enough clearance to swing the
Central Unit open for future access to its interior.
To swing the central unit open, undo the two knurled nuts at the top and swing it open while holding its body.
Monitor.
It may be mounted anywhere on the machine, preferably at operator's eye level.
9" Amber and 10" Color Monitor
1.Contrast
2.Brightness
3.Two 3.15A/250V fast fuses (F), one per mains line, to protect the mains input.
4.Power switch.
5.220 Vac mains and ground connection.
6.General ground connection terminal. Metric 6mm
7.15-pin SUB-D type male connector for connecting it with the Central Unit.
- 12 -
14" Color Monitor
X2 15-pin SUB-D type male connector for connecting it with the Central Unit.
1.General ground connection terminal. Metric 6mm
2.220 Vac mains and ground connection.
Monitor enclosures.
9" & 10 Monitor
14" Monitor
A, B, C, D
25 mm
100 mm
E
150 mm
50 mm
Keyboard.
It may be mounted anywhere on the machine.
Rear panel
1.25-pin SUB-D type female connector for connecting it with the Central Unit.
2.Buzzer volume adjusting potentiometer.
3.Buzzer.
- 13 -
Connector for connecting the Central Unit with the Monitor.
FAGOR AUTOMATION provides the cable required for this connection. It comes with a 15-pin SUB-D type male connector at one end and a 15-pin SUB-D type female connector at the other.
Both connectors have a latching system UNC4.40 by means of two screws.
The supplied cable has 6 twisted pairs of 0.34 mm² wires (6 x 2 x 0.34mm²), with overall shield and acrylic cover. It has a specific impedance of 120 Ohms. Its maximum length must be 25 meters (82 feet).
The cable shield is soldered to the metal hoods (housings) of both connectors and connected to pin 1 at both the Central Unit and Monitor/keyboard connectors.
PIN SIGNAL
10
11
12
13
7
8
9
5
6
3
4
1
2
14
15
Metal hood
GND
H
R
G
V
I
B
Not connected
Not connected
I
R
H
V
G
B
Shield
Shield
Heat shrink
Outside shield soldered to metal hood
Metal hood
Connector for connecting the Central Unit with the keyboard.
FAGOR AUTOMATION provides the cable required for this connection. It comes with a 25-pin SUB-D type male connector at each end.
Both connectors have a latching system UNC4.40 by means of two screws.
The supplied cable has 25 wires of 0.14 mm² (25 x 0.14mm²), with overall shield and acrylic cover. Its maximum length must be 25 meters (82 feet).
The cable shield is soldered to the metal hoods (housings) of both connectors and connected to pin 1 at both the Central Unit and Monitor/keyboard connectors.
PIN SIGNAL
14
15
16
17
9
10
11
12
13
4
5
6
7
8
1
2
3
18
19
20
21
22
23
24
25
Metal hood
C8
C10
C12
C14
C7
D1
D3
D5
D7
GND
C9
C11
C13
C15
C1
C3
C5
C0
C2
C4
C6
D0
D2
D4
D6
Shield
Shield
Heat shrink
Outside shield soldered to metal hood
Metal hood
- 14 -
2. PROGRAMMING IN ISO CODE. NEW FUNCTION F34
P1 = F34 Parameter P1 takes the value of the tool causing the call to the subroutine associated with the tools.
Do not mistake it with function F24 which returns the number of the tool currently being used.
3. PROGRAMMING IN ISO CODE. RIGID TAPPING
When carrying out rigid tapping in 800M mode, the CNC acts as follows:
1.Internally generates function M81 (switching feedback)
2.Carries out rigid tapping.
3.Internally generates function M82 (switching back to previous feedback)
Therefore, when programming rigid tapping in ISO code, function M81 must be programmed in block preceding rigid tapping and function M82 in the one following it.
4. 1000 LINE ENCODER AS A 1250 LINE ENCODER
With this feature, the CNC can use a 1000 line encoder as it were a 1250 line encoder.
P630(6) X axis 1000 line encoder as 1250 line encoder (0=No, 1=Yes)
P630(7) Y axis 1000 line encoder as 1250 line encoder (0=No, 1=Yes)
P630(8) Z axis 1000 line encoder as 1250 line encoder (0=No, 1=Yes)
A typical case: When using a motor with 1000 line encoder on a 5 mm pitch ballscrew.
The necessary calculations for setting axis resolution will be made using the selected line count (1000 or 1250 pulses).
5. PLCI. INPUT I104
When the Feedrate Override Switch on the operator panel is set on one of the handwheel positions (x1, x10, x100), input I104 is set to "1".
6. PLCI. R120 AND THE
From this version on, even when the
KEY
is disabled by parameter P618(1), PLCI register R120 contains its code when it is pressed.
Version 3.04 (March 2002)
1. TOOL COMPENSATION CANCELATION
Sometimes, it may be interesting to move the tool to a set position without applying its length compensation.
In these cases, program "T.0" and the CNC will acts as follows:
•
It does not change the tool (it does not call its associated subroutine).
•
It cancels its associated offset (assuming a zero length and radius compensation).
The "T.xx" instruction may be programmed at any time, even inside the program P99996 or in its associated subroutine. The CNC assumes the new "xx" offset. When programming "T.0", it assumes a zero tool length and radius compensation.
2. FEEDBACK SIGNAL DIVIDING FACTOR
Parameters P631(8), P631(7), P631(6), P631(5) and P631(4) are used with parameters P604(8), P604(7), P604(6), P604(5) and P616(8) that indicate the multiplying factor for the feedback signals of the X, Y, Z, W, V axes respectively.
X axis
P604(8)
Y axis
P604(7)
Z axis
P604(6)
W axis
P604(5)
V axis
P616(8)
P631(8) P631(7) P631(6) P631(5) P631(4)
They indicate whether the feedback signals are divided (=1) or not (=0).
P631(8)=0, P631(7)=0, P631(6)=0, P631(5)=0 and P631(4)=0 They are not divided
P631(8)=1, P631(7)=1, P631(6)=1, P631(5)=1 and P631(4)=1 They are divided by 2.
Example: To obtain a 0.01 mm resolution using a square-wave encoder mounted on the X axis whose pitch is 5 mm/turn.
Nr of pulses = Leadscrew pitch / (Multiplying factor x Resolution)
If P604(8)=0 & P631(8)=0
If P604(8)=1 & P631(8)=0
If P604(8)=0 & P631(8)=1
If P604(8)=1 & P631(8)=1 x4 multiplying factor x2 multiplying factor x2 multiplying factor x1 multiplying factor
Nr of pulses = 125
Nr of pulses = 250
Nr of pulses = 250
Nr of pulses = 500
- 15 -
3. FEEDBACK FACTOR.
The resolution of the axis is determined by the leadscrew pitch and the number of pulses of the encoder mounted on the motor.
Sometimes, the resolution resulting from the available leadscrew / encoder combination does not match any of the resolution values allowed for the machine parameters (1, 2, 5, 10 microns or ten-thousandths of an inch).
Example: With a 6 mm/turn leadscrew pitch and a 2500 line encoder, the resulting resolution values are:
Resolution = Leadscrew pitch / ( Nr of encoder pulses x multiplying factor).
With x1 multiplying factor2.4 micron resolution
With x2 multiplying factor1.2 micron resolution
With a x4 multiplying factor 0.6 micron resolution
A new axis machine parameter is now available to solve these cases and it is referred to as Feedback Factor in order to adapt the resulting resolution to the existing setup.
P819 Feedback factor for the X axis P820 Feedback factor for the Y axis P821 Feedback factor for the Z axis
Values between 0 and 65534, a "0" value means that this feature is not being used.
Use the following formula to calculate the "Feedback factor":
Feedback Factor = (Gear ratio x Leadscrew Pitch / Encoder pulses) x 8.192
Examples: Gear ratio
Leadscrew Pitch
Encoder
Feedback factor
1
4000
2500
13,107.2
1
6000
2500
19,660.8
2
6000
2500
39,321.6
1
8000
2500
26,214.4
(microns)
(pulses/turn)
The machine parameters only admit integers, but the Feedback Factor sometimes may have decimals. In those cases, set the machine parameter to the integer part of that value and use the leadscrew error compensation table to make up for the decimal part.
The values for this table are calculated using the following formula:
Leadscrew position = Leadscrew error (microns) x Integer portion of feedback factor /Decimal portion of feedback factor
In this case: Gear ratio = 1 Pitch = 6000 Encoder = 2500
Feedback factor = 19,660.8
Machine parameter = 19660
For leadscrew error of 20 microns Leadscrew position = 20 x 19,660 / 0.8 = 491,520
The following table is obtained by using this calculation.
Leadscrew position Amount of error at that position
P0 = -1966,000
P2 = -1474,500
P4 = -983,000
P6 = -491,500
P1 =
P3 =
P5 =
P7 =
-0.080
-0.060
-0.040
-0.020
P8 = 0
P10 = 491,500
P12 = 983,000
P14 = 1472,500
P16 = 1966,000
P9 = 0
P11 = 0.020
P13 = 0.040
P15 = 0.060
P17 = 0.080
Headquarters (SPAIN): Fagor Automation S. Coop.
Bº San Andrés s/n, Apdo. 144
E-20500 Arrasate - Mondragón
Tel: +34-943-719200/039800
Fax: +34- 943-791712
+34-943-771118 (Service Dept.) www.fagorautomation.com
E-mail: [email protected]
advertisement
Related manuals
advertisement
Table of contents
- 1 New Features
- 2 Version 2.1
- 2 1. P627(1), Dividing Factor for Electronic Handwhell Feedback Signals
- 2 Version 2.4
- 2 1. Handwheels Affected by Feed-Hold
- 2 2. Automatic Tool Changers (ATC)
- 3 2.1 Machine with Manual Tool Changer
- 4 2.2 MAchine with Automatic Tool Changer (ATC)
- 5 3. Treatment of the M19 (Spindle Orient)
- 7 Version 3.1
- 7 1. Generating an ISO-CODED Program
- 8 2. Rigid Tapping is now Available
- 8 3. Current CNC Software Version
- 8 4. Screen Saver
- 9 5. Semiautomatic Linear Milling
- 9 6. Semiautomatic ARC Milling
- 9 7. Cross Compensation
- 9 8.Function M80 When "Z" as A dro Axis
- 10 9. Machine Safety Regulation
- 12 Version 3.3
- 12 1. Modular CNC
- 15 2. Programming in ISO Code new Function F34
- 15 3. Programming in ISO Code Rigid Tapping
- 15 4. 1000 Line Encoder As a 1250 Line Encoder
- 15 5. PLCI. Input I104
- 15 6. PLCI. R120 and the key
- 15 Version 3.04
- 15 1. Tool compensation cancelacion
- 15 2. Feedback signal dividing factor
- 16 3. Feedback factor
- 17 Operation Manual
- 19 INDEX
- 19 Comparison Table for FAGOR 800 M
- 19 New Features and Modifications
- 19 Introduction
- 19 1. Concepts
- 19 2. Basic Operations
- 20 3. Auxiliary Functions
- 20 4. Automatic Operations
- 21 5. Machining Operations
- 21 6. Working with Part-Programs
- 21 Error Codes
- 138 Programming Manual
- 140 INDEX
- 140 Comparison Table for FAGOR 800 M
- 140 New Features and Modifications
- 140 Introduction
- 140 1. Program Writing
- 140 2. Coordinate Programming
- 140 3. Reference System
- 141 4. Other Functions
- 141 5. Path Control
- 141 6. Additional Preparatory Functions
- 141 7. Tool Compensation
- 142 8. Machining Canned Cycles
- 142 9. Subroutines
- 142 10. Parametric Programming
- 142 Error Codes