9.2 DRILL BIT INSTALLATION/REPLACEMENT. Draper 12 Speed Floor Standing Drill, 600W, 12 Speed Floor Standing Drill
Add to My manuals24 Pages
advertisement
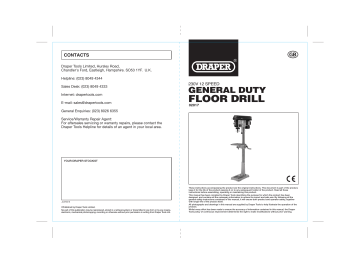
9. SETTING THE BENCH DRILL
9.2 DRILL BIT INSTALLATION/
REPLACEMENT - FIG. 14
The drilling machine is equipped with a geared chuck and a separate key to secure the bit in the chuck jaws.
Selection of the correct accessory is dependent on material type and the intended application.
Ensure the selected accessory is suitable and speed compatible with the drilling machine.
Place the bit into the chuck. Insert the chuck key into apertures % engaging the teeth.
Rotate the key clockwise to grip. All three apertures should be tightened to make certain of a firm grip.
Always use a good quality sharp drill bit/cutter.
WARNING: The drill bit will be hot after use.
%
FIG.14
9.3 NO-VOLT SWITCH - FIG. 15
In the event of a power supply disruption the machine will require manually restarting once power has been returned.
To switch the machine on, press the green button marked ‘I’
To switch the machine off, press the red button marked ‘O’. However, the yellow cover with integral red stop button must be left covering the switches so, in the event of an accident or emergency, striking the stop button will activate the off switch.
Prior to starting the drilling machine make a visual check, to ensure the guards are in place and correctly functioning, the bit is correctly installed with the chuck key removed and no other parts are damaged proving a potential hazard.
Ensure all locking handles are tight prior to starting the drilling machine.
FIG.15
- 16 -
5. HEALTH AND SAFETY INFORMATION
LOCATION:
1. Posture
Ensure when mounting the machine that the chosen location does not lead to unhealthy posture or repetitive strain during normal operation.
2. Lighting
Adequate lighting must be provided to ensure no operations are light impaired possibly leading to injury. Light should be from multiple sources to avoid any strobing effects from flourescent or LED sources.
3. Reach
Do not reach over or around the machine at any time.
UNEXPECTED START-UP:
1. Remove the plug
Remove the plug from the socket before carrying out adjustment, servicing or maintenance.
ERRORS OF FITTING:
1. Tools
Ensure a suitable tool for the job in hand is securely and correctly fitted prior to starting the machine.
Guards shall be fitted and in place at all times.
STABILITY:
1. Toppling
The drill shall be securely bolted down to a suitable and level surface to prevent the machine from overturning leading to injury.
2. Slipping
Ensure the area is clean of any residue cutting/lubrication fluid and other materials which may lead to a slip, trip or other such hazard.
5.3 CONNECTION TO THE POWER SUPPLY
Make sure the power supply information on the machine’s rating plate are compatible with the power supply you intend to connect it to.
The Drill comes supplied with a UK standard 3 pin plug fitted. It is designed for connection to a domestic power supply rated at 230V AC.
Because it is constructed mostly of metal parts, it is a Class 1 machine; meaning, it must have an earth connection in the power supply. This is to prevent electrocution in the event of a failure.
Apart from replacing the fuse in the plug, no other electrical work is recommended on this drill.
- 9 -
5. HEALTH AND SAFETY INFORMATION
Have this tool repaired by a qualified person.
This tool is designed to confirm to the relevant international and local standards and as such should be maintained and repaired by someone qualified; using only original parts supplied by the manufacturer: This will ensure the tool remains safe to use.
5.2 SPECIFIC SAFETY INSTRUCTION FOR DRILL PRESSES USE
ADDITIONAL SAFETY INSTRUCTIONS FOR FLOOR DRILLS
MECHANICAL HAZARDS:
1. Crushing
When setting/changing a tool or maintaining the machine avoid crushing injuries sustained between fixed and moving elements of the machine.
2. Cutting or Severing
At all times the workpiece shall be clamped as manual support will lead to injury.
3. Entanglement
Switch off the machine for maintenance, workpiece loading/unloading, swarf/chip removal, cutting/lubrication fluid application as contact with rotating spindle or tool will cause entanglement and possibly lead to injury and entrapment.
4. Impact
Ensure the workpiece is securely clamped at all times to avoid sudden movement (rotation) or ejection causing injury. Ensure any special tools associated with tool exchange, i.e. chuck key are removed prior to attempting to start the machine.
5. Stabbing, Cutting or Puncture Wounds
Take care when handling the tools and avoid contact with swarf and burrs created during drilling as they are extremely sharp.
ELECTRICAL HAZARDS:
1. Contact with Live parts
During commissioning, maintenance and trouble shooting operations do not remove, open or expose any electrical, terminal and control boxes due to the danger of electrocution. If the main cable is damaged, unplug the machine immediately and have the cable replaced before continuing.
AUDIBLE HAZARDS:
Wear ear defenders during operation to avoid damage to hearing, however ensure this does not interfere with speech communications or audible warnings.
MATERIAL HAZARDS:
1. Contact and Inhalation
Wear personal protective equipment to avoid contact from harmful fluids, gases or dust thrown or created during the drilling process.
2. Fire or Explosion
Do not drill or drill in the vicinity of flammable or combustible materials.
9. SETTING THE BENCH DRILL
9.4 WORK TABLE ADJUSTMENT -
Figs. 16-19
For versatility, the work table can be raised or lowered, tilted ±45° or rotated 360° around the column.
To tilt the table, tighten nut & clockwise until the locating pin can be removed from the casting. Store in a safe location. Loosen the
24mm bolt % .
Adjust the table’s degree of tilt and re-secure with locking bolt % . Use the scale as a guide. Alternatively use a protractor off the table to the drill bit for more accuracy.
When the table is back in a level position insert the location pin for the factory setting.
Move the nut along the thread until the end of the thread is protected by the nut, allowing use of a small hammer to tap the pin in place.
To raise/lower the table working height, loosen locking handle and turn the height adjustment crank handle to raise or lower the table. Alternatively while locking handle is loose the table can be rotated
180° to further increase the distance between the chuck and workpiece. When the adjustments are complete re-secure locking handle .
The slots in the work table and base can accommodate locking bolts to secure a small vice enabling safe clamping of the workpiece.
CAUTION: A drill bit snagging on a piece of work will violently grab the piece of material, whipping it round and is likely to result in personal injury. Always ensure the workpiece is securely clamped.
FIG.16
FIG.17
&
FIG.18
%
- 8 - 17 -
FIG.19
advertisement
Related manuals
advertisement
Table of contents
- 2 1.2 REVISION HISTORY
- 2 1.3 UNDERSTANDING THIS MANUAL
- 2 1.4 COPYRIGHT NOTICE
- 5 4.3 HANDLING AND STORAGE
- 6 5.1 GENERAL SAFETY INSTRUCTIONS FOR POWER TOOL USE
- 8 5.2 ADDITIONAL SAFETY INFORMATION
- 9 5.3 CONNECTION TO THE POWER SUPPLY
- 11 7.2 WHAT’S IN THE BOX
- 12 8.1 BASE TO COLUMN
- 13 HEADSTOCK
- 13 8.4 PLUNGE HANDLES
- 13 8.5 CHUCK AND ARBOR
- 14 8.6 CHUCK GUARD
- 14 8.7 BENCH/FLOOR MOUNTING
- 15 9.1 SPINDLE SPEED ADJUSTMENT
- 16 9.2 DRILL BIT INSTALLATION/REPLACEMENT
- 16 9.3 NO-VOLT SWITCH
- 18 9.5 GENERAL DRILLING
- 18 9.6 DUST AND SWARF
- 23 1.2 REVISION HISTORY
- 23 1.3 UNDERSTANDING THIS MANUAL
- 23 1.4 COPYRIGHT NOTICE