Armario eléctrico. Esquemas. Fagor CNC 8070 para otras aplicaciones, CNC 8037 para fresadoras, CNC 8065 for lathes, CNC 8055 para otras aplicaciones, CNC 8055 for lathes, CNC 8065 para fresadoras, CNC 8060 for lathes, CNC 8037 para tornos, CNC 8065 for milling machines, CNC 8055 para fresadoras
Add to My manuals418 Pages
advertisement
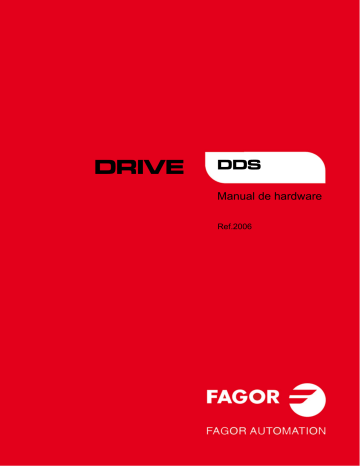
Esquemas de conexión
10.9
Armario eléctrico. Esquemas
PELIGRO.
Los esquemas de este capítulo no cumplen la Directiva Europea de Máquinas 2006/42/CE.
Para cumplir la Directiva Europea de Máquinas, usualmente se requiere PL d ó SIL 2 (fresadoras y tornos). El AXD/SPD alcanza PL d ó SIL 2 (véanse modelos en la Declaración de Conformidad). Además es necesario un controlador externo de seguridad PL d ó SIL 2 y tener en cuenta los conceptos del capítulo
.
Antes de representar los esquemas del armario eléctrico y que más adelante se documentan, léase esta breve explicación sobre las actuaciones que siguen los módulos en el proceso de arranque del sistema. Todas las referencias hechas a dispositivos eléctricos como p. ej. el interruptor - S1, contactor de potencia - KM1, el relé - KA3, ... vienen representados en los esquemas posteriores. Acuda a estos esquemas para interpretar los textos explicativos.
Alimentación de los circuitos de control
Alimentar los circuitos internos de control de cada regulador modular a través del módulo fuente o de cada regulador compacto a través de su fuente integrada, con 24 voltios, cerrando el interruptor principal de potencia o llave principal - S1. Consúltense los esquemas que se adjuntan más adelante para situar - S1 en el sistema.
Internamente, cada módulo hace una comprobación de su hardware y de su configuración.
Si el estado de cada regulador es correcto y no se han producido errores, cada regulador cierra su contacto DR.OK.
Si el estado de todos los reguladores que forman el sistema DDS es correcto y no se han producido errores, cada uno de ellos se lo comunica a la fuente a través del bus interno (sólo los reguladores modulares). Si además la fuente de alimentación tampoco registra ningún error entonces cierra su contacto System OK.
La fuente, entonces, inicia el proceso de carga del bus de potencia con arranque suave «Soft-Start».
Activar la entrada de control Speed Enable de cada regulador y la entrada System Speed Enable de la fuente de alimentación (véase la situación del relé - KA2 en los esquemas). El Control Numérico, a su vez, habilita la marca SPENA.
Activar la entrada de control Drive Enable de cada regulador (véase la situación del relé - KA3 en los esquemas). El Control Numérico, a su vez, habilita la marca DRENA.
NOTA.
El motor podrá seguir ahora la consigna dada por el CNC.
Todos los esquemas de circuitos de potencia y control en el armario eléctrico detallados en este capítulo son únicamente orientativos para el técnico que diseña la máquina, pudiendo ser ampliados o reducidos según su parecer atendiendo a las particularidades de la aplicación.
Línea de emergencia
La función del relé - KA1 es confirmar que el sistema está mecánica y eléctricamente en condiciones de funcionamiento. Este relé cierra su contacto cuando se cumplen todas y cada una de las siguientes condiciones:
El contacto System_OK de la fuente de alimentación está cerrado.
No se ha activado ninguna emergencia.
La temperatura del motor de cabezal es correcta, es decir, no se sobrecalienta y,
Ninguno de los ejes de la máquina ha alcanzado su final de carrera.
10.
DDS
HARDWARE
Ref.2006
· 345 ·
Esquemas de conexión
10.
370
DDS
HARDWARE
Ref.2006
i
NOTA. Nótese que en paralelo con la cadena de «fines de carrera» se incluirá un pulsador (N. A., N ormalmente A bierto) que permite (por maniobra en el PLC) deshabilitar el movimiento de los ejes de la máquina en sentido contrario .
Tras la activación del relé - KA1, se cierra su contacto asociado que permite, tras pulsar el botón ON, el suministro de potencia trifásica al sistema cerrando el contactor - KM1. Para cancelar el suministro de potencia pulsar el botón OFF.
Reset de errores
Ante la aparición de un error en algún regulador, su contacto Drive OK y por tanto, el contacto System OK de la fuente que lo alimenta, se encontrarán en estado abierto. El relé - KA1 estará desactivado y su contacto asociado abierto y no será posible suministrar potencia a la fuente de alimentación hasta que se elimine la causa que provoca el error, siempre que se trate de un error no reseteable.
NOTA.
Es posible eliminar algunos errores llamados «errores reseteables» aplicando 24 Vdc al pin Error Reset de la fuente de alimentación.
Para obtener información sobre estos errores, ver capítulo 14 del manual
«man_dds_soft.pdf».
Con el contacto asociado al pulsador ON se hace un reset de errores. Este procedimiento puede hacer que Drive OK y System OK se cierren activando el relé - KA1 y todavía con ON pulsado, habilitar - KM1.
NOTA.
Esta configuración del circuito une el reset de errores y el encendido del sistema en un único pulsador.
Activación del System Speed Enable de la fuente de alimentación y del Speed Enable de los reguladores
La activación de la señal System Speed Enable de la fuente de alimentación se ejecuta tras el cierre del contacto KA2 con 24 Vdc como consecuencia de la activación del relé - KA2. Véase que - KM1 ya ha sido cerrado con anterioridad.
Ahora, el CNC podrá habilitar cada uno de los ejes (CNC Enable) y tras la activación de los relés - KA4, - KA5, - KA6 y - KA7 habilitar la señal Speed
Enable de cada uno de los reguladores.
Activación del Drive Enable de los reguladores
El cierre del contacto asociado al relé - KA2 excita con 24 Vdc el relé KA3 que habilita la señal Drive Enable de todos los reguladores.
NOTA.
Nótese que el relé - KA3 es un relé de retardo a la desconexión en el que puede programarse el tiempo t de retardo deseado. Permite mantener cerrado el contactor - KM1 durante la frenada de un sistema los segundos necesarios para darle tiempo a la fuente a devolver a la red la energía excedente en la frenada (siempre y cuando el sistema disponga de fuentes con devolución) y haya conexión a red (- S1 cerrado), obviamente. El tiempo t de retardo con el que debe programarse el relé - KA3 deberá ser siempre algo superior al tiempo que va a tardar el sistema en detenerse totalmente.
INFORMACIÓN.
En los esquemas que más adelante se proporcionan, el piloto luminoso en verde (ON green) es indicador de la habilitación de la señal
System Speed Enable de la fuente, es decir de la señal Speed Enable en cada regulador ligado a ella y de la señal SPENA del CNC (transmitida a cada regulador via SERCOS-II o CAN) y de la posterior presencia del par motor (señal Drive Enable en cada regulador y señal DRENA del CNC). El piloto luminoso en rojo (OFF red) es indicador de que todas las señales anteriores están deshabilitadas.
· 346 ·
Esquemas de conexión
NOTA. Recuérdese que el regulador sólo atiende a la consigna externa de velocidad cuando las señales Drive Enable, Speed Enable y System
Speed Enable (además de las señales DRENA y SPENA del CNC) están activas (24 Vdc).
Las causas que pueden provocar una parada pueden ser por:
apertura del interruptor principal de potencia -S1 , por fusión de uno o varios fusibles o simplemente la existencia de un corte eléctrico durante el funcionamiento del sistema. Se produce un frenado con rampas de emergencia si éstas fueron parametrizadas inicialmente. Independientemente de la fuente instalada no será posible devolver a la red el excedente energético provocado por la frenada (recuérdese que la red ha quedado abierta). Se origina un aumento de la tensión en el bus de potencia como consecuencia del almacenamiento de esa energía en los condesadores.
NOTA. Recuérdese que la energía almacenada en los condensadores responde a la expresión: Energía almacenada = 0.5 C·V ²
Superado un cierto valor de la tensión de bus (760/770 Vdc) es activado el circuito de Ballast con el fin de disipar ese excedente energético en una resistencia (interna o externa) y el motor efectúa una parada controlada (con par motor).
Si aún habiéndose activado el circuito de Ballast, hubiese algún problema en el mismo (p. e. una mala conexión de la resistencia externa) la tensión de bus seguiría aumentando hasta alcanzar su valor máximo permitido (790 Vdc) y sería activado el código de error E215 de sobretensión del bus. Se deshabilitaría la función Drive Enable y el motor se detendría por rozamiento y sin par motor.
apertura del contactor de potencia - KM1 , debido a la apertura del contacto asociado al relé - KA1. El mecanismo de frenado sería el mismo que en el caso anterior si se dispone de una fuente PS-65A o una
PS-25B4. Si la fuente es regenerativa (XPS o RPS) se produce un frenado con rampas de emergencia siempre que éstas hayan sido parametrizadas inicialmente. Se devuelve a la red el excedente energético provocado por la frenada justo unos segundos antes de la apertura del contactor - KM1 gracias al retraso a la desconexión del relé - KA3. Si, por la razón que fuere, siguiese aumentando la tensión en el bus de potencia, el mecanismo de frenado sería el mismo que el seguido en el caso anterior.
NOTA. Recuérdese que las fuentes RPS no incorporan circuito de Ballast y en el caso de ser requerido por las características de la aplicación habrá que recurrir a algún circuito de Ballast comercial.
10.
Control del freno de mantenimiento
En algunas aplicaciones (p. ej. para el eje vertical Z de una fresadora) se dispone de un freno electromecánico blocante sobre el rótor del motor.
ADVERTENCIA.
¡Este freno no se utilizará nunca para frenar ejes en movimiento. Únicamente sirve para inmovilizar o bloquear ejes verticales que previamente se han detenido!
Así, el freno bloquea el rótor cuando éste pierde tensión en sus bornes.
Cuando la máquina está fuera de servicio, inmoviliza el eje vertical Z para que éste no caiga por efecto de la fuerza gravitatoria.
NOTA.
El tiempo de reacción de un freno integrado en un motor FAGOR de eje de avance puede variar, dependiendo del modelo, entre 7 y 97 ms.
DDS
HARDWARE
OBLIGACIÓN.
Durante el tiempo empleado en el bloqueo del freno del eje vertical es necesario mantener el motor con par. Ver parámetro GP9 en el capítulo 13 del manual «man_dds_soft.pdf».
Ref.2006
· 347 ·
370
DDS
HARDWARE
Ref.2006
· 348 ·
Esquemas de conexión
10.
OBLIGACIÓN.
En el momento de conexión de la máquina no debe desbloquearse nunca el freno hasta que el sistema haya tomado el control de ese eje. Ver variable TV100 en el capítulo 13 del manual · man_dds_soft.pdf · .
Recuérdese que:
Los circuitos de control en reguladores compactos y en fuentes de alimentación (RPS, XPS y PS-25B4) son alimentados con +24 Vdc por una fuente auxiliar que incorporan internamente. Las fuentes PS-65A necesitarán de la fuente auxiliar externa APS-24 para alimentarlos al no disponer de una integrada.
Tanto en reguladores compactos ACD/SCD/CMC como en fuentes de alimentación principal PS y XPS, para tensiones de línea de 400/460 Vac, alimentar la fuente auxiliar con tensión de línea bifásica de 400/460 Vac. No así en fuentes de alimentación principal RPS donde la fuente auxiliar deberá ser alimentada con tensión trifásica de 400/460 Vac.
Con reguladores modulares AXD 2.50-S0-0-B-L diseñados para tensiones de línea de 200/240 Vac (véase "-L" en su referencia comercial), instalar y alimentar la fuente de alimentación principal PS-37-L con tensiones de línea trifásica de 200/240 Vac. El sistema necesitará además de una fuente auxiliar externa de 24 Vdc para alimentar los circuitos de control al no disponer de fuente integrada.
NOTA. FAGOR no dispone de fuentes de alimentación principal ni auxiliar exterior que puedan ser alimentadas con tensiones de línea de
200/240 Vac. Todas están diseñadas para ser alimentadas con tensiones de línea de entre 400 (1- 10%) Vac y 460 (1+10 %) Vac.
En reguladores compactos ACD/SCD...-L diseñados para tensiones de línea de 200/240 Vac (véase "-L" en su referencia comercial), alimentar su fuente de alimentación auxiliar integrada con tensiones de línea bifásica de
200/240 Vac.
El cierre del interruptor principal de potencia -S1 debe llevar dos fases al conector X1 en presencia de reguladores compactos o de una APS-24 como fuente auxiliar de la PS-65A y al conector X3 en presencia de fuentes XPS o PS-25B4. En fuentes RPS serán tres fases en lugar de dos e irán al conector X1.
La apertura del contactor - KM1 no elimina el suministro de potencia a la fuente auxiliar en ningún caso. La apertura del interruptor principal - S1 sí que lo hace, manteniendo los +24 Vdc hasta que se produce la parada.
Arranque del sistema DDS con fuentes PS. Esquema de bloques
Esquemas de conexión
10.
F. H10/9
Proceso de arranque del sistema DDS con fuentes no regenerativas. Esquema de bloques.
DDS
HARDWARE
Ref.2006
· 349 ·
Esquemas de conexión
Arranque del sistema DDS con fuentes XPS ó RPS. Esquema de bloques
10.
370
DDS
HARDWARE
Ref.2006
F. H10/10
Proceso de arranque del sistema DDS con fuentes regenerativas. Esquema de bloques.
· 350 ·
advertisement
Related manuals
advertisement
Table of contents
- 7 DECLARACIÓN DE CONFORMIDAD CE
- 9 CERTIFICADO TÜV SÜD FUNCTIONAL SAFETY
- 13 ACERCA DEL MANUAL
- 14 ACERCA DEL PRODUCTO
- 15 CONDICIONES DE ENVÍO, ALMACENAJE, DESMANTELAMIENTO Y ELIMINACIÓN
- 17 HISTÓRICO DE VERSIONES
- 21 CONDICIONES DE SEGURIDAD
- 24 CALIDAD
- 25 DOCUMENTACIÓN RECOMENDADA
- 27 DESCRIPCIÓN
- 28 Descripción
- 29 Esquema general
- 30 Fases de configuración del sistema
- 31 Diagrama de aislamiento de un sistema en una máquina
- 32 Condiciones ambientales y de funcionamiento
- 32 Condiciones eléctricas
- 33 FUENTES DE ALIMENTACIÓN
- 34 Fuentes de alimentación no regenerativas
- 55 Fuentes de alimentación regenerativas
- 71 Fuentes de alimentación estabilizadas regenerativas
- 99 REGULADORES
- 100 Reguladores modulares
- 146 Reguladores compactos
- 184 Encendido de un regulador
- 187 MÓDULOS AUXILIARES
- 188 Filtros de red
- 190 Chokes
- 192 Resistencias de Ballast externas
- 197 Módulo de condensadores. CM
- 198 Fuente de alimentación auxiliar. APS
- 202 Módulo de protección del bus. BPM
- 207 CRITERIOS DE SELECCIÓN
- 207 Selección del motor síncrono y regulador asociado
- 212 Selección del motor asíncrono y regulador asociado
- 218 Selección de la fuente de alimentación
- 228 Guía de selección del módulo de condensadores
- 229 Guía de selección de la resistencia de Ballast
- 233 CONEXIÓN DE LAS LÍNEAS DE POTENCIA
- 233 Conexión a red
- 235 Fusibles de protección
- 237 Interruptor diferencial
- 238 Transformador de aislamiento o auto-transformador
- 240 Filtro de red
- 241 Inductancia de línea
- 242 Esquemas de distribución
- 246 Cables de conexión a red
- 247 CABLES
- 248 Cable de conexión a red. Conexión fuente-red
- 250 Cable de potencia. Conexión motor-regulador
- 252 Cables de captación motor
- 254 Cable adaptador CA-D1-D
- 255 Cable de captación directa
- 257 Cables de señal para control y comunicaciones
- 261 Adaptador RS232/RS422 BE
- 262 Línea serie RS
- 269 INSTALACIÓN
- 270 Ubicación
- 277 Componentes inductivos
- 278 Instalación del sistema
- 281 Conexión entre módulos
- 297 Conexiones de alimentación
- 299 Conexión de señales de control y comunicaciones
- 318 Comprobar la instalación
- 319 SEGURIDAD FUNCIONAL
- 321 Características principales de las funciones de seguridad
- 322 Entrada Drive Enable y salida de feedback AS1-AS
- 323 Detección de fallos y reacción
- 325 Requisitos de diseño
- 327 Precauciones eléctricas
- 328 Riesgos residuales
- 329 Datos técnicos de las funciones de seguridad
- 330 Tiempo de respuesta de las funciones de seguridad
- 331 Cableado y puesta a tierra
- 332 Puesta en marcha
- 333 Mantenimiento, reparación y análisis de eventos peligrosos
- 335 Desmantelamiento y eliminación
- 336 Sobre seguridad eléctrica, condiciones ambientales y de CEM
- 337 ESQUEMAS DE CONEXIÓN
- 338 Regulador modular SPD con motor asíncrono de cabezal FM
- 339 Regulador modular AXD con servomotor síncrono de eje FKM
- 339 Regulador modular AXD con servomotor síncrono de eje FXM
- 340 Regulador modular AXD 2.50-S0-0-B-L con motor lineal
- 341 Regulador compacto SCD con motor asíncrono de cabezal FM
- 342 Regulador compacto ACD con servomotor síncrono de eje FKM
- 343 Regulador compacto ACD con servomotor síncrono de eje FXM
- 344 Regulador compacto ACD 1.25-S0-0-B-L con motor lineal
- 345 Armario eléctrico. Esquemas
- 351 Esquemas con fuente de alimentación PS-37-L
- 353 Esquemas con fuente de alimentación PS-65A
- 355 Esquemas con fuente de alimentación PS-25B
- 357 Esquemas con fuente de alimentación XPS
- 359 Esquemas con fuente de alimentación RPS
- 361 Esquemas de sistema compacto ACD/SCD, conexión SERCOS-II
- 364 Esquemas de sistema compacto ACD/SCD, conexión CAN
- 366 Esquemas de sistema mixto AXD/SCD, conexión SERCOS-II
- 367 Esquemas de sistema mixto AXD/SCD, conexión CAN
- 369 Esquema de conexión del freno
- 370 Maniobra *star-delta · al vuelo · en cabezales FM7, series E03|HS
- 371 DIMENSIONES
- 372 Fuentes de alimentación
- 381 Reguladores modulares
- 387 Reguladores compactos
- 390 Módulo de protección del bus, BPM
- 390 Módulo de condensadores, CM
- 391 Filtros de red
- 392 CHOKES XPS
- 393 CHOKES RPS
- 394 Resistencias de Ballast externas con termostato externo
- 394 Resistencias de Ballast externas con termostato interno
- 395 Resistencias de Ballast externa con termostato externo y ventilador
- 395 Termostato externo
- 397 MODELOS COMERCIALES
- 398 Servomotores síncronos
- 400 Motores asíncronos
- 402 Reguladores modulares
- 403 Reguladores compactos
- 404 Reguladores posicionadores
- 405 Fuentes de alimentación
- 406 Equipos auxiliares
- 407 Cables
- 409 Formato de pedido
- 410 Identificación de equipos
- 411 COMPATIBILIDAD
- 411 Tensión de red
- 411 Compatibilidades
- 412 Sustitución de módulos
- 412 Placa VECON
- 413 Boot para VECON
- 413 Tarjeta SERCOS (16 MBd)
- 414 Tarjeta CAN
- 414 Tarjetas CAPMOTOR-x
- 414 Tarjetas VECON-x
- 415 Tipo de captador y tarjeta CAPMOTOR-x
- 415 Reconocimiento de las fuentes RPS
- 415 Fuente auxiliar APS-24 junto a fuentes PS, XPS o RPS
- 415 Fuentes compatibles con motores FM
- 415 Reguladores AXD...- L a 200/240 Vac
- 415 Reguladores ACD/SCD...- L a 200/240 Vac
- 416 Tarjeta CONTROL del GAP en un regulador AXD/ACD
- 416 Ficheros «*.mot». Tablas de motores