advertisement
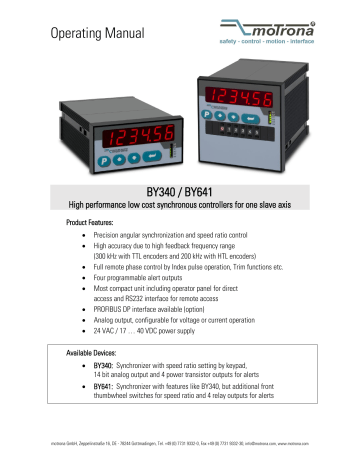
5.2.
Mechanical Phase and Position Considerations
Normally the synchronizer would always keep the angular phase or relative position between
Master and Slave, which has existed while the unit has been powered up, or which has been defined manually while the unit was kept in the Reset state.
However it may be desirable to adjust the relative position in standstill or on the fly, by means of manual or remote commands, or even to set a certain position automatically, triggered by external events. For this reason, phase trimming functions and index functions have been designed, which can be assigned to either the front keys or the control inputs. Once the desired phase adjust commands have been assigned, the final function can be specified by setting of the appropriate Operating Mode of the unit (see chapter 6 )
5.2.1.
Phase Trimming under Timer Control (Modes 1 – 4 and 7 – 8)
Activating one of the +/-Trim commands allows to temporary run the Slave at a speed which is slightly higher (Trim+) or slightly lower (Trim-) than the correct synchronous speed, which results in a displacement of phase between Master and Slave (Slave leads or lags the Master).
The differential speed to displace the phase is parameter adjustable. The system returns to closed-loop synchronous operation in a new relative position, as soon as the Trim command is released again.
5.2.2.
Phase Trimming under Impulse Stepper Control (Modes 5 and 6)
With this mode of operation the +/-Trim commands must be assigned to two of the Control
Inputs, which then operate as impulse inputs from a remote source (push button or PLC or else).
Every impulse applied to the Trim+ input will advance the Slave by one differential increment*) and every impulse applied to the Trim- input will retard the Slave with respect to the Master.
This method allows adjusting the relative position step by step
5.2.3.
Lead or Lag by a programmable distance (Mode 3)
With this mode, every impulse detected on the Index Master or Index Slave input will jump the
Slave forward or reverse by a fixed distance, as set to the Offset register. This method of phase displacement allows toggling the relative phase between two or more scheduled operating positions (e.g. 0°, 90°, 180° and back to 0°).
5.2.4.
Position Definition by Index Inputs (Modes 2, 6 and 8)
Index signals may be used do define and to automatically adjust mechanical positions or events between the drives (for an example see the figure under section 3 ). Index signals can be generated by proximity switches, photo cells or by use of the marker pulse of a HTL encoder.
Where you intend to use marker pulses from TTL encoders, you have to translate the Z and /Z information to HTL level before applying it to the controller.
While modes 2 and 6 are designed for immediate and tough correction of index errors, mode 8 provides a soft way of making corrections. The Trim register is used to approach a new position by means of an adjustable differential speed.
*) Mechanically, one differential increment equals to one Slave encoder increment divided by Factor2
By340_04b_oi_e.doc / Apr-16 Page 13 / 42
advertisement
Related manuals
advertisement
Table of contents
- 4 Safety Instructions and Responsibility
- 4 General Safety Instructions
- 4 Use according to the intended purpose
- 5 Installation
- 5 Cleaning, Maintenance and Service Notes
- 6 Available Models
- 7 Introduction
- 8 Electrical Connections
- 10 Power Supply
- 10 Auxiliary Outputs for Encoder Supply
- 10 Impulse Inputs for Incremental Encoders
- 11 Control Inputs Cont.1 – Cont
- 11 Switching Outputs K1 – K
- 11 Serial Interface
- 11 Analog Output
- 12 Principle of Operation
- 12 Synchronization
- 13 Mechanical Phase and Position Considerations
- 14 Operating Modes
- 15 Keypad Operation
- 15 Normal Operation
- 15 General Setup Procedure
- 16 Direct Fast Access to Speed Ratio Setting
- 17 Change of Parameter Values on the Numeric Level
- 18 Code Protection against Unauthorized Keypad Access
- 18 Return from the Programming Levels and Time-Out Function
- 18 Reset all Parameters to Factory Default Values
- 19 Menu Structure and Description of Parameters
- 19 Summary of the Menu
- 21 Description of the Parameters
- 32 Description of Commands and Outputs
- 32 Commands
- 33 Outputs
- 34 Display of Actual Values
- 35 Steps for Commissioning
- 36 Running the Adjust menu
- 37 Set Directions of Rotation
- 37 Tuning the Analog Output
- 38 Setting of the Proportional Gain
- 38 Hints for final operation
- 39 Appendix for model BY
- 39 Relay Outputs
- 39 Front Thumbwheel Switches
- 40 Technical Specifications & Dimensions
- 41 Dimensions of model BY