- Home
- Domestic appliances
- Large home appliances
- Water heaters & boilers
- Lennox
- ML193DFE Gas Furnace
- Installation instructions
advertisement
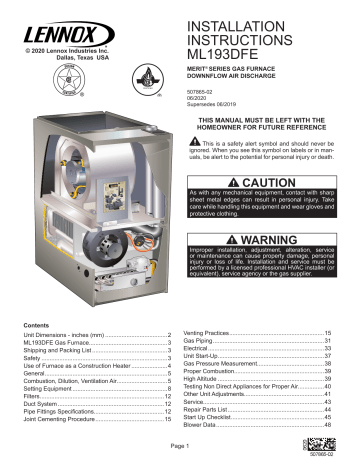
Filters
This unit is not equipped with a filter or rack. A field-provid ed filter is required for the unit to operate properly. TABLE
3 lists recommended filter size.
A filter must be in place whenever the unit is operating.
IMPORTANT
If a high efficiency filter is being installed as part of this system to ensure better indoor air quality, the filter must be properly sized. High efficiency filters have a higher static pressure drop than standard efficiency glass/foam filters. If the pressure drop is too great, system capacity and performance may be reduced. The pressure drop may also cause the limit to trip more frequently during the winter and the indoor coil to freeze in the summer, resulting in an increase in the number of service calls.
Before using any filter with this system, check the specifications provided by the filter manufacturer against the data given in the appropriate Lennox Product
Specifications bulletin. Additional information is provided in Service and Application Note ACC002
(August 2000).
TABLE 3
Furnace Cabinet Width Minimum Filter Size
17-1/2”
21”
16 x 25 x 1 (1)
Duct System
Use industry-approved standards to size and install the supply and return air duct system. Refer to ACCA Manual
D. This will result in a quiet and low-static system that has uniform air distribution. See FIGURE 19 for proper duct installation.
Supply Air Plenum
If the furnace is installed without a cooling coil, a removable access panel should be installed in the supply air duct. The access panel should be large enough to permit inspection of the heat exchanger. The furnace access panel must always be in place when the furnace is operating and it must not allow leaks into the supply air duct system.
NOTE - This furnace is not certified for operation in heat ing mode (indoor blower operating at selected heating speed) with an external static pressure which exceeds 0.5 inches w.c. Operation at these conditions may result in improper limit operation.
Duct Installation
Down-Flow Unit
SUPPLY
AIR
FIGURE 19
Return Air Plenum
NOTE - Return air must not be drawn from a room where this furnace, or any other gas-fueled appliance (i.e., water heater), or carbon monoxide-producing device (i.e., wood fireplace) is installed.
When return air is drawn from a room, a negative pressure is created in the room. If a gas appliance is operating in a room with negative pressure, the flue products can be pulled back down the vent pipe and into the room. This reverse flow of the flue gas may result in incomplete com bustion and the formation of carbon monoxide gas. This raw gas or toxic fumes might then be distributed throughout the house by the furnace duct system.
Use fiberglass sealing strips, caulking, or equivalent seal ing method between the plenum and the furnace cabinet to ensure a tight seal. If a filter is installed, size the return air duct to fit the filter frame.
Pipe & Fittings Specifications
All pipe, fittings, primer and solvent cement must conform with American National Standard Institute and the American Society for Testing and Materials (ANSI/ASTM) standards. The solvent shall be free flowing and contain no lumps, undissolved particles or any foreign matter that adversely affects the joint strength or chemical resistance of the cement. The cement shall show no gelation, stratification, or separation that cannot be removed by stirring.
Refer to the TABLE 4 below for approved piping and fitting materials.
Page 12
CAUTION
Solvent cements for plastic pipe are flammable liquids and should be kept away from all sources of ignition.
Do not use excessive amounts of solvent cement when making joints. Good ventilation should be maintained to reduce fire hazard and to minimize breathing of solvent vapors. Avoid contact of cement with skin and eyes.
TABLE 4
PIPING AND FITTINGS SPECIFICATIONS
Schedule 40 PVC (Pipe) D1785
Schedule 40 PVC (Cellular Core Pipe)
Schedule 40 PVC (Fittings)
Schedule 40 CPVC (Pipe)
Schedule 40 CPVC (Fittings)
SDR-21 PVC or SDR-26 PVC (Pipe)
SDR-21 CPVC or SDR-26 CPVC (Pipe)
Schedule 40 ABS Cellular Core DWV
(Pipe)
Schedule 40 ABS (Pipe)
Schedule 40 ABS (Fittings)
ABS-DWV (Drain Waste & Vent) (Pipe &
Fittings)
PVC-DWV (Drain Waste & Vent) Pipe &
Fittings)
F891
D2466
F441
F438
D2241
F442
F628
D1527
D2468
D2661
D2665
PRIMER & SOLVENT CEMENT
PVC & CPVC Primer
PVC Solvent Cement
CPVC Solvent Cement
ABS Solvent Cement
PVC/CPVC/ABS All Purpose Cement
For Fittings & Pipe of the same material
ABS to PVC or CPVC Transition Solvent
Cement
CANADA PIPE & FITTING & SOLVENT
CEMENT
PVC & CPVC Pipe and Fittings
PVC & CPVC Solvent Cement
ABS to PVC or CPVC Transition
Cement
POLYPROPYLENE VENTING SYSTEM
PolyPro® by Duravent
ASTM
SPECIFICATION
F656
D2564
F493
D2235
D2564, D2235,
F493
D3188
MARKING
ULCS636
InnoFlue® by Centrotherm
IMPORTANT
Exhaust and intake connections are made of PVC. Use
PVC primer and solvent cement when using PVC vent pipe. When using ABS vent pipe, use transitional solvent cement to make connections to the PVC fittings in the unit.
Use PVC primer and solvent cement or ABS solvent cement meeting ASTM specifications, refer to TABLE 4.
As an alternate, use all purpose cement, to bond ABS,
PVC, or CPVC pipe when using fittings and pipe made of the same materials. Use transition solvent cement when bonding ABS to either
PVC or CPVC.
Low temperature solvent cement is recommended during cooler weather. Metal or plastic strapping may be used for vent pipe hangers. Uniformly apply a liberal coat of PVC primer for PVC or use a clean dry cloth for ABS to clean inside socket surface of fitting and male end of pipe to depth of fitting socket.
Canadian Applications Only - Pipe, fittings, primer and solvent cement used to vent (exhaust) this appliance must be certified to ULC S636 and supplied by a single manu facturer as part of an approved vent (exhaust) system. In addition, the first three feet of vent pipe from the furnace flue collar must be accessible for inspection.
Page 13
Input Size
045
070
090
Vent Pipe
Dia. in.
6 1-1/2
2
2-1/2
3
6 1-1/2
2
2-1/2
3
2
2-1/2
3
Flush
Mount Kit
51W11
(US)
51W12
(CA)
3 YES
3 YES
3 YES
3 YES
3 YES
3 YES
3 YES
3 YES
3 YES
3 YES
3 YES
TABLE 5
OUTDOOR TERMINATION USAGE*
STANDARD
Wall Kit
3 inch 2 inch
22G44
(US)
4 30G28
(CA)
44J40 (US)
4 81J20
(CA)
Field
Fabricated
YES
YES
YES
YES
YES
YES
YES
YES
1
1
1
1
1
1
1
1
YES
YES
YES
YES
YES
YES
YES
YES
YES
YES
YES
5
5
5
5
5
5
5
5
YES
YES
YES
YES
YES
YES
YES
YES
5 YES
5 YES
5 YES
1-1.2 inch
4
71M80
(US)
44W92
2
2
2
2
2
2
2
2
(CA)
YES
YES
YES
YES
YES
YES
YES
YES
CONCENTRIC
4
2 inch
69M29
(US)
44W92
(CA)
YES
YES
YES
3 inch
60L46 (US)
4 44W93
(CA)
YES
YES
YES
NOTE - Standard Terminations do not include any vent pipe or elbows external to the structure. Any vent pipe or elbows external to the structure must be included in total vent length calculations. See vent length tables.
* Kits must be properly installed according to kit instructions.
1Requires field-provided outdoor 1-1/2” exhaust accelerator.
2Concentric kits 71M80 and 44W92 include 1-1/2” outdoor accelerator, when uses with 045 and 070 input models. When using 1-1/2 inch vent pipe, transistion to 2” pipe before installing concentric kit.
3 Flush mount kits 51W11 and 51W12 includes 1-1/2 in. outdoor exhaust accelerator, required when used with 045, 070 and 090 input models. When using 1-1/2” vent pipe, transition to 2” pipe before installing flushmount kit .
4 Termination kits 30G28, 44W92, 4493 and 81J20 are certified to ULC S636 for use in Canada only.
5 See table 10 for vent accelerator requirements.
6 Requires field provided 2” to 1-1/2” reducer.
Joint Cementing Procedure
All cementing of joints should be done according to the specifications outlined in ASTM D 2855.
NOTE - A sheet metal screw may be used to secure the intake pipe to the connector, if desired. Use a drill or self tapping screw to make a pilot hole.
DANGER
DANGER OF EXPLOSION!
Fumes from PVC glue may ignite during system check.
Allow fumes to dissipate for at least 5 minutes before placing unit into operation.
1 - Measure and cut vent pipe to desired length.
2 - Debur and chamfer end of pipe, removing any ridges or rough edges. If end is not chamfered, edge of pipe may remove cement from fitting socket and result in a leaking joint.
3 - Clean and dry surfaces to be joined.
4 - Test fit joint and mark depth of fitting on outside of pipe.
5 - Uniformly apply a liberal coat of PVC primer for PVC or use a clean dry cloth for ABS to clean inside socket
surface of fitting and male end of pipe to depth of fitting socket.
6 - Promptly apply solvent cement to end of pipe and inside socket surface of fitting. Cement should be applied lightly but uniformly to inside of socket. Take care to keep excess cement out of socket. Apply second coat to end of pipe.
NOTE - Time is critical at this stage. Do not allow primer to dry before applying cement
7 - Immediately after applying last coat of cement to pipe, and while both inside socket surface and end of pipe are wet with cement, forcefully insert end of pipe into socket until it bottoms out. Turn PVC pipe
1/4 turn during assembly (but not after pipe is fully inserted) to distribute cement evenly. DO NOT turn
ABS or cellular core pipe.
NOTE - Assembly should be completed within 20 seconds after last application of cement. Hammer blows should not be used when inserting pipe.
8 - After assembly, wipe excess cement from pipe at end of fitting socket. A properly made joint will show a bead around its entire perimeter. Any gaps may indicate an improper assembly due to insufficient solvent.
9 - Handle joints carefully until completely set.
Page 14
advertisement
Related manuals
advertisement
Table of contents
- 2 Unit Dimensions - inches (mm)
- 3 ML193DFE Gas Furnace
- 3 Shipping and Packing List
- 3 Safety
- 4 Use of Furnace as a Construction Heater
- 5 General
- 5 Combustion, Dilution, Ventilation Air
- 8 Setting Equipment
- 12 Filters
- 12 Duct System
- 15 Joint Cementing Procedure
- 15 Venting Practices
- 31 Gas Piping
- 33 Electrical
- 37 Unit Start-Up
- 38 Gas Pressure Measurement
- 39 Proper Combustion
- 39 High Altitude
- 40 Testing Non Direct Appliances for Proper Air
- 41 Other Unit Adjustments
- 43 Service
- 44 Repair Parts List
- 45 Start Up Checklist
- 48 Blower Data