3. SIGNALS AND WIRING. Mitsubishi Electric MR-J2S-22KB, MR-J2S-40B1, MR-J2S-350B, MR-J2S-200B, Melservo-J2-SUPER series, MR-J2S-100B, MR-J2S-500B, MR-J2S-10B, MR-J2S-11KB, MR-J2S-70B
Add to My manuals225 Pages
advertisement
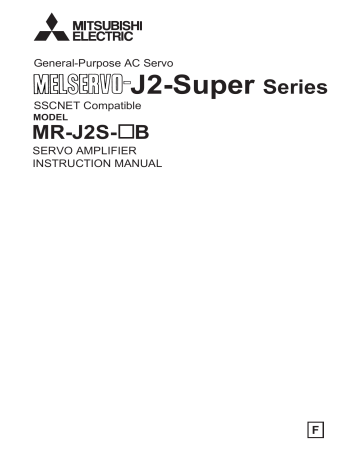
3. SIGNALS AND WIRING
3. SIGNALS AND WIRING
WARNING
Any person who is involved in wiring should be fully competent to do the work.
Before starting wiring, make sure that the voltage is safe in the tester more than 15 minutes after power-off. Otherwise, you may get an electric shock.
Ground the servo amplifier and the servo motor securely.
Do not attempt to wire the servo amplifier and servo motor until they have been installed. Otherwise, you may get an electric shock.
The cables should not be damaged, stressed excessively, loaded heavily, or pinched. Otherwise, you may get an electric shock.
CAUTION
Wire the equipment correctly and securely. Otherwise, the servo motor may misoperate, resulting in injury.
Connect cables to correct terminals to prevent a burst, fault, etc.
Ensure that polarity ( , ) is correct. Otherwise, a burst, damage, etc. may occur.
The surge absorbing diode installed to the DC relay designed for control output should be fitted in the specified direction. Otherwise, the signal is not output due to a fault, disabling the forced stop(EM1) and other protective circuits.
Servo
Amplifier
COM
(24VDC)
Servo amplifier
COM
(DC24V)
Control output signal
RA
Control output signal
RA
Use a noise filter, etc. to minimize the influence of electromagnetic interference, which may be given to electronic equipment used near the servo amplifier.
Do not install a power capacitor, surge suppressor or radio noise filter (FR-BIF option) with the power line of the servo motor.
When using the regenerative brake resistor, switch power off with the alarm signal.
Otherwise, a transistor fault or the like may overheat the regenerative brake resistor, causing a fire.
Do not modify the equipment.
POINT
CN1A, CN1B, CN2 and CN3 have the same shape. Wrong connection of the connectors will lead to a failure. Connect them correctly.
3 - 1
3. SIGNALS AND WIRING
3.1 Connection example of control signal system
POINT
Refer to Section 3.5 for the connection of the power supply system and to
Section 3.6 for connection with the servo motor.
3.1.1 MR-J2S-700B or less
(Note 9)
Servo configuration software
(Note 4)
Personal computer
Servo system controller
(Note 10, 14)
Bus cable (Option)
15m(49.2ft) or less
Servo amplifier
CN3
(Note 5, 8)
CN3
13 MBR
5
10
COM
VDD
20 EM1
3 SG
6 LA
16 LAR
7 LB
17 LBR
8 LZ
18 LZR
4 MO1
1 LG
10m(32.81ft) or less
RA1
(Note 2,6)
Magnetic brake interlock
When using the forced stop (EM1) or magnetic brake interlock (MBR), make sure to connect it.
(Note 3,4,7)
Forced stop
A
10k
14 MO2
11 LG
(Note 5)
CN1A
Plate SD
A
10k
2m(6.56ft) or less
Encoder A-phase pulse
(differential line driver)
Encoder B-phase pulse
(differential line driver)
Encoder Z-phase pulse
(differential line driver)
Control common
Analog monitor output
Max. 1mA
Reading in both directions
(Note15)
Cable clamp
(Option)
(Note 5) SW1
CN1B
Setting:0 (Note 1)
(Note 10, 14)
Bus cable
(Option)
MR-J2S-B
CN1A
(2 axis)
(Note 11)
SW1
CN1B
Setting 1
MR-J2S-B
CN1A
(3 axis)
(Note 11)
SW1
CN1B
Setting 2
(Note 13)
MR-A-TM
MR-J2S-B
CN1A
(n axis)
(Note 11)
SW1
CN1B
Setting: n 1
(Note 12) n 1 to 8
3 - 2
3. SIGNALS AND WIRING
Note 1. To prevent an electric shock, always connect the protective earth (PE) terminal (terminal marked ) of the servo amplifier to the protective earth (PE) of the control box.
2. Connect the diode in the correct direction. If it is connected reversely, the servo amplifier will be faulty and will not output signals, disabling the forced stop (EM1) and other protective circuits.
3. If the controller does not have a forced stop function, always install a forced stop switch (Normally closed).
4. When a personal computer is connected for use of the test operation mode, always use the maintenance junction card (MR-J2CN3TM) to enable the use of the forced stop (EM1). (Refer to section 12.1.6)
5. CN1A, CN1B, CN2 and CN3 have the same shape. Wrong connection of the connectors will lead to a fault.
6. The sum of currents that flow in the external relays should be 80mA max.
7. When starting operation, always turn on the forced stop (EM1). (Normally closed contacts) By setting “0001” in parameter No.23, the forced stop (EM1) can be made invalid.
8. When connecting the personal computer together with analog monitor outputs 1, 2, use the maintenance junction card (MR-J2CN3TM). (Refer to Section 12.1.3.)
9. Use MRZJW3-SETUP151E.
10. Use the bus cable at the overall distance of 30m(98.4ft) or less. In addition, to improve noise immunity, it is recommended to use a cable clamp and data line filters (three or four filters connected in series) near the connector outlet.
11. The wiring of the second and subsequent axes is omitted.
12. Up to eight axes (n 1 to 8) may be connected. The MR-J2S- B/MR-J2-03B5 servo amplifier may be connected on the same bus.
13. Always insert the termination connector (MR-A-TM) into CN1B of the servo amplifier located at the termination.
14. The bus cable used with the SSCNET depends on the preceding or subsequent controller or servo amplifier connected. Refer to the following table and choose the bus cable.
QD75M
Motion controller
Q172CPU(N)
Q173CPU(N)
A motion
MR-J2S- B MR-J2-03B5
Maintenance junction card
MR-J2S- B
MR-J2HBUS M
Q172J2BCBL M(-B)
Q173J2B CBL M
MR-J2HBUS M-A
MR-J2HBUS M
MR-J2-03B5
15. When the A1SD75M (AD75M) is used as the controller, encoder pulses may not be output depending on the software version of the controller. For details, refer to the A1SD75M (AD75M)
Manual.
3 - 3
3. SIGNALS AND WIRING
3.1.2 MR-J2S-11KB or more
(Note 7)
MR Configurator
(Servo configuration software)
Servo system controller
(Note 8, 12)
Bus cable (Option)
Cable clamp
(Option)
Personal computer
(Note 8, 12)
Bus cable
(Option)
15m(49.2ft) or less
Servo amplifier
(Note 4)
CN3
6
16
7
LA
LAR
LB
17 LBR
Encoder A-phase pulse
(differential line driver)
Encoder B-phase pulse
(differential line driver)
8 LZ
18 LZR
Encoder Z-phase pulse
(differential line driver)
1 LG
Plate SD
10m(32.81ft) or less
CN3
CON2
2 EM1
(Note 3, 6)
Forced stop
1
4
SG
DB
(Note 2, 5)
Dynamic brake
RA1 interlock
(Note 4)
CN1A
3 MBR RA2
Magnetic brake interlock
18 COM
15 VDD
CN4
1 interlock (DB), make sure to connect it.
2m(6.56ft) or less
MO1
When using the forced stop (EM1), magnetic brake interlock (MBR) or dynamic brake
10k Analog monitor
Max. 1mA
2 MO2
A
A
10k
Reading in
4 LG both directions
(Note
13)
(Note 4)
SW1
CN1B
Setting : 0
(Note 1)
MR-J2S-B
(Note 9)
SW1
CN1B
Setting : 1
MR-J2S-B
(Note 9)
SW1
CN1B
Setting : 2
(Note 11)
MR-A-TM
MR-J2S-B
(Note 9)
SW1
CN1B
Setting: n-1
(Note 10) n= 1 to 8
3 - 4
3. SIGNALS AND WIRING
Note 1. To prevent an electric shock, always connect the protective earth (PE) terminal (terminal marked ) of the base unit to the protective earth (PE) of the control box.
2. Connect the diode in the correct direction. If it is connected reversely, the interface unit will be faulty and will not output signals, disabling the forced stop and other protective circuits.
3. If the controller does not have a forced stop (EM1) function, always install a forced stop switch
(Normally closed).
4. CN1A, CN1B, and CN3 have the same shape. Wrong connection of the connectors will lead to a fault.
5. The sum of currents that flow in the external relays should be 80mA max.
6. When starting operation, always turn on the forced stop (EM1). (Normally closed contacts) By setting “0001” in DRU parameter No.23 of the drive unit, the forced stop (EM1) can be made invalid.
7. Use MRZJW3-SETUP151E.
8. Use the bus cable at the overall distance of 30m(98.4ft) or less. In addition, to improve noise immunity, it is recommended to use a cable clamp and data line filters (three or four filters connected in series) near the connector outlet.
9. The wiring of the second and subsequent axes is omitted.
10. Up to eight axes (n 1 to 8) may be connected. The MR-J2S- B/MR-J2-03B5 servo amplifier may be connected on the same bus.
11. Always insert the termination connector (MR-A-TM) into CN1B of the interface unit located at the termination.
12. The bus cable used with the SSCNET depends on the preceding or subsequent controller or servo amplifier connected. Refer to the following table and choose the bus cable.
MR-J2S- B MR-J2-03B5
QD75M
Motion controller
Q172CPU(N)
Q173CPU(N)
A motion
MR-J2S- B MR-J2-03B5
Maintenance junction card
MR-J2HBUS M
Q172J2BCBL M(-B)
Q173J2B CBL M
MR-J2HBUS M-A
MR-J2HBUS M
13. When the A1SD75M (AD75M) is used as the controller, encoder pulses may not be output depending on the software version of the controller. For details, refer to the A1SD75M (AD75M)
Manual.
3 - 5
3. SIGNALS AND WIRING
3.2 I/O signals
3.2.1 Connectors and signal arrangements
POINT
The pin configurations of the connectors are as viewed from the cable connector wiring section.
(1) MR-J2S-700B or less
CN1A
2
RD
4
1
LG
3
12
RD*
14
11
LG
13
TD
6
5
LG
TD*
16
15
LG
8
10
7
EMG
18
17
EMG*
9
BT
20
19
MITSUBISHI
MELSERVO-J2
CN1B
2
RD
4
1
LG
3
12
RD*
14
11
LG
13
TD
6
5
LG
TD*
16
15
LG
8
10
7
EMG
17
18
EMG*
9
BT
20
19
CN2
2
LG
4
1
LG
3
12
LG
14
11
LG
13
5 15
6 16
MD
8
10
7
MR
9
BAT
MDR
17
18
MRR
P5
19
20
P5
P5
The connector frames are
connected with the PE (earth)
terminal inside the servo amplifier.
CN3
1 11
2
RXD
4
MO1
6
LG
3
SG
5
COM
12
TXD
13
14
MBR
MO2
15
16
LG
LA LAR
7 17
8 18
LB LBR
LZ LZR
9 19
10 20
VDD EM1
3 - 6
3. SIGNALS AND WIRING
(2) MR-J2S-11KB or more
CN1A
Same as the one of the
MR-J2S-700B or less.
CN1B
Same as the one of the
MR-J2S-700B or less.
CN2
2
LG
4
1
LG
3
12
LG
14
11
LG
13
5 15
6 16
MD
8
10
7
MR
9
BAT
MDR
18
17
MRR
P5
19
20
P5
P5
CHARGE
CN4
1 MO1
2 MO2
4 LG
CN3
2
RXD
4
1
LG
3
12
TXD
14
11
LG
13
6
LA
8
LZ
10
5 15
16
7
LB
9
LAR
18
17
LBR
LZR
19
20
MITSUBISHI
The connector frames are
connected with the PE (earth)
terminal inside the servo amplifier.
CON2
1 14
2
SG
15
EM1
4
3
MBR
DB
5
VDD
17
6 19
16
18
COM
7 20
8 21
9 22
10 23
11 24
12 25
13 26
3 - 7
3. SIGNALS AND WIRING
3.2.2 Signal explanations
For the I/O interfaces (symbols in I/O column in the table), refer to Section 3.4.2.
(1) Connector applications
Connector
CN1A
CN1B
CN2
CN3
(Note)
(Note)
CN4
Name
Connector for bus cable from preceding axis.
Connector for bus cable to next axis
Encoder connector
Communication connector
(I/O signal connector)
Analog monitor output connector
CON2 IO signal connector
Note. These connectors are exclusive to the MR-J2S-11KB or more.
Function/Application
Used for connection with the controller or preceding-axis servo amplifier.
Used for connection with the next-axis servo amplifier or for connection of the termination connector.
Used for connection with the servo motor encoder.
Used for connection with the personal computer.
Serves as an I/O signal connector when the personal computer is not used.
Used to output analog monitor 1 (M01) and analog monitor
2 (M02).
Used to input a forced stop and output the dynamic brake interlock(DB), the electromagnetic brake interlock
(2) I/O signals
(a) Input signal
Forced stop
(b) Output signals
Electromagnetic brake interlock
Dynamic brake interlock
Signal
Encoder A-phase pulse
(Differential line driver)
Encoder B-phase pulse
(Differential line driver)
Encoder Z-phase pulse
(Differential line driver)
Analog monitor 1
Analog monitor 2
Symbol
MBR
DB
LA
LAR
LB
LBR
LZ
LZR
MO1
MO2
CN3
8
CN3
18
CN3
4
CN3
14
CN3
6
CN3
16
CN3
7
CN3
17
Connector Pin
No.
7kw or less
CN3
13
11kw or more
CON2
3
CON2
4
CN3
6
CN3
16
CN3
7
CN3
17
CN3
8
CN3
18
CN4
1
CN4
2
Function/Application
In the servo-off or alarm status, MBR turns off.
When using this signal, set 1 in the parameter No. 2.
When the dynamic brake is operated, DB turns off.
Outputs pulses per servo motor revolution set in parameter
No.38 in the differential line driver system. In CCW rotation of the servo motor, the encoder B-phase pulse lags the encoder A-phase pulse by a phase angle of /2.
The zero-phase signal of the encoder is output in the differential line driver system.
Used to output the data set in parameter No.22 to across
MO1-LG in terms of voltage. Resolution 10 bits
Used to output the data set in parameter No.22 to across
MO2-LG in terms of voltage. Resolution 10 bits
I/O Division
DO-1
DO-1
DO-2
DO-2
Analog output
Analog output
(c) Power supply
Internal power output for interface
Power input for digital interface
Common for digital interface
Control common
Shield
Signal
Signal
Symbol
EM1
Connector Pin
No.
7kw or less
11kw or more
CN3
20
CON2
2
Function/Application
Turn EM1 off (open EM1 common) to bring the motor to a forced stop state, in which the base circuit is shut off and the dynamic brake is operated.
Turn EM1 on (short EM1 common) in the forced stop state to reset that state.
I/O Division
DI-1
Symbol
VDD
COM
SG
LG
SD
Connector Pin
No.
Function/Application
7kw 11kw or less or more
CN3
10
CON2
15
Driver power output terminal for digital interface.
Used to output 24V 10% to across VDD-COM. Connect with COM.
Permissible current: 80mA
CN3
5
CN3
3
CN3
1
11
CON2
18
CON2
1
CN4
4
Driver power input terminal for digital interface.
Used to input 24VDC (200mA or more) for input interface.
Connect with VDD.
Common terminal to VDD and COM. Pins are connected internally.
Separated from LG.
Common terminal to MO1 and MO2.
Plate Plate Connect the external conductor of the shield cable.
3 - 8
3. SIGNALS AND WIRING
3.3 Alarm occurrence timing chart
CAUTION
When an alarm has occurred, remove its cause, make sure that the operation signal is not being input, ensure safety, and reset the alarm before restarting operation.
As soon as an alarm occurs, make the Servo off status and interrupt the main circuit power.
When an alarm occurs in the servo amplifier, the base circuit is shut off and the servo motor is coated to a stop. Switch off the main circuit power supply in the external sequence. To deactivate the alarm, power the control circuit off, then on or give the error reset or CPU reset command from the servo system controller. However, the alarm cannot be deactivated unless its cause is removed.
(Note)
Main circuit
Control circuit power ON
OFF
Base circuit
ON
OFF
Dynamic brake
Valid
Invalid
Servo-on command
(from controller)
ON
OFF
Brake operation
Power off
Brake operation
Power on
Alarm NO YES NO
1s
Reset command
(from controller)
ON
OFF
50ms or more
Alarm occurs.
Remove cause of trouble.
Note. Switch off the main circuit power as soon as an alarm occurs.
YES
60ms or more
NO
(1) Overcurrent, overload 1 or overload 2
If operation is repeated by switching control circuit power off, then on to reset the overcurrent (32), overload 1 (50) or overload 2 (51) alarm after its occurrence, without removing its cause, the servo amplifier and servo motor may become faulty due to temperature rise. Securely remove the cause of the alarm and also allow about 30 minutes for cooling before resuming operation.
(2) Regenerative alarm
If operation is repeated by switching control circuit power off, then on to reset the regenerative (30) alarm after its occurrence, the external regenerative brake resistor will generate heat, resulting in an accident.
(3) Instantaneous power failure
Undervoltage (10) occurs when the input power is in either of the following statuses.
A power failure of the control circuit power supply continues for 60ms or longer and the control circuit is not completely off.
The bus voltage dropped to 200VDC or less for the MR-J2S B, or to 158VDC or less for the MR-J2S
B1.
3 - 9
3. SIGNALS AND WIRING
3.4 Interfaces
3.4.1 Common line
The following diagram shows the power supply and its common line.
To conform to the EMC directive, refer to the EMC Installation Guide lines (IB(NA)67310).
Servo amplifier
24VDC
VDD
COM MBR
RA
DI-1
EM1
SG
<Isolated>
Servo motor
M
LA .etc
LAR
.etc
LG
SD
MO1
MO2
LG
TXD
RXD
Differential line driver output
35mA max.
Analog monitor output
RS-232C
CN2
Servo motor encoder
MR
MRR
LG
SD
Ground
3 - 10
3. SIGNALS AND WIRING
3.4.2 Detailed description of the interfaces
This section gives the details of the I/O signal interfaces (refer to I/O Division in the table) indicated in
Sections 3.2.2.
Refer to this section and connect the interfaces with the external equipment.
(1) Digital input interface DI-1
Give a signal with a relay or open collector transistor.
Servo amplifier
24VDC
VDD
R: Approx. 4.7
COM
For a transistor
Approx. 5mA
EM1
TR
V
CES
1.0V
I
CEO
100 A
Switch
SG
(2) Digital output interface DO-1
A lamp, relay or photocoupler can be driven. Provide a diode (D) for an inductive load, or an inrush current suppressing resister (R) for a lamp load. (Permissible current: 40mA or less, inrush current:
100mA or less)
(a) Inductive load
Servo amplifier
24VDC
VDD
COM
Load
MBR
SG If the diode is not connected as shown, the servo amplifier will be damaged.
3 - 11
3. SIGNALS AND WIRING
(b) Lamp load
Servo amplifier
24VDC
VDD
COM
MBR
SG
R
(3) Encoder pulse output DO-2
(Differential line driver system)
1) Interface
Max. output current: 35mA
Servo amplifier
LA
(LB, LZ)
Am26LS32 or equivalent
Servo amplifier
LA
(LB, LZ)
150
LAR
(LBR, LZR)
LG
SD
LAR
(LBR, LZR)
SD
100
High-speed photocoupler
2) Output pulse
Servo motor CCW rotation
LA
LAR
LB
T
LBR
/2
LZ
LZR
400 s or more
Time cycle (T) is determined by the settings of parameter No.33 and 38.
3 - 12
3. SIGNALS AND WIRING
(4) Analog output
Output voltage : 10V
Max. output current :1mA
Resolution :10bit
Servo amplifier
MO1
(MO2)
LG
10k
Reading in one or both directions
1mA meter
A
SD
3 - 13
3. SIGNALS AND WIRING
3.5 Power line circuit
CAUTION
When the servo amplifier has become faulty, switch power off on the amplifier power side. Continuous flow of a large current may cause a fire.
Switch power off at detection of an alarm. Otherwise, a regenerative brake transistor fault or the like may overheat the regenerative brake resistor, causing a fire.
POINT
For the power line circuit of the MR-J2S-11KB to MR-J2S-22KB, refer to
Section 3.12 where the power line circuit is shown together with the servo motor connection diagram.
3.5.1 Connection example
Wire the power supply/main circuit as shown below so that power is shut off and the servo-on command turned off as soon as an alarm occurs, a servo forced stop is made valid, or a controller forced stop is made valid. A no-fuse breaker (NFB) must be used with the input cables of the power supply.
(1) For 3-phase 200 to 230VAC power supply
(Note 2)
Alarm
RA1
Controller forced stop
RA2
Forced stop OFF
ON
MC
MC
SK
NFB MC
Power supply
3-phase
200 to 230VAC
(Note 1)
L
11
L
21
P
P
1
L
1
L
2
L
3
Servo amplifier
Forced stop
VDD
COM
EM1
SG
Note 1. Always connect P-P
1
. (Factory-wired.) When using the power factor improving DC reactor, refer to
Section 12.2.4.
2. Configure up the power supply circuit which switches off the magnetic contactor after detection of alarm occurrence on the controller side.
3 - 14
3. SIGNALS AND WIRING
(2) For 1-phase 100 to 120VAC or 1-phase 230VAC power supply
(Note 1)
Alarm
RA1
Controller forced stop
RA2
Forced stop OFF
ON
MC
Power supply
1-phase 100 to
120VAC or
1-phase 230VAC
NFB MC
L
1
Servo amplifier
L
2
L
3
(Note 2)
L
11
L
21
MC
SK
Forced stop
VDD
COM
EM1
SG
Note 1. Configure up the power supply circuit which switches off the magnetic contactor after detection of alarm occurrence on the controller side.
2. Not provided for 1-phase 100 to 120VAC.
3 - 15
3. SIGNALS AND WIRING
3.5.2 Terminals
The positions and signal arrangements of the terminal blocks change with the capacity of the servo amplifier. Refer to Section 10.1.
Symbol
Connection Target
(Application)
Description
L
1
, L
2
, L
3
Main circuit power supply
Supply L
1
, L
2
and L
3
with the following power:
For 1-phase 230VAC, connect the power supply to L
1
/L
2
and leave L
3
open.
Power supply
Servo amplifier MR-J2S-10B to
3-phase 200 to 230VAC,
50/60Hz
1-phase 230VAC,
50/60Hz
1-phase 100 to 120VAC,
50/60Hz
L
70B
1
L
2
L
1
L
2
MR-J2S-100B
L
3 to 22K
MR-J2S-10B1 to 40B1
L
1
L
2
U, V, W
L
11
P
1
, L
21
Servo motor output
Power factor improving DC reactor
Control circuit power supply
Connect to the servo motor power supply terminals (U, V, W).
When not using the power factor improving DC reactor, connect P-P
1
. (Factorywired.)
When using the power factor improving DC reactor, disconnect the wiring across
P
1
-P
2
and connect the power factor improving DC reactor across P-P
1
.
Refer to Section 11.2.4.
Supply the following power to L
11
, L
21
.
Servo amplifier
Power supply
1-phase 200 to 230VAC,
50/60Hz
1-phase 100 to 120VAC,
50/60Hz
MR-J2S-10B to 700B
L
11
L
21
MR-J2S-10B1 to 40B1
L
11
L
21
P, C, D
N
Regenerative brake option
Return converter
Brake unit
1) MR-J2S-350B or less
When using servo amplifier built-in regenerative brake resistor, connect between P-D terminals. (Wired by default)
When using regenerative brake option, disconnect between P-D terminals and connect regenerative brake option to P terminal and C terminal.
2) MR-J2S-500B 700B
MR-J2S-500B and 700B do not have D terminal.
When using servo amplifier built-in regenerative brake resistor, connect P terminal and C terminal. (Wired by default)
When using regenerative brake option, disconnect P terminal and C terminal and connect regenerative brake option to P terminal and C terminal.
Refer to Section 12.1.1.
When using return converter/brake unit, connect to P terminal and N terminal.
Do not connect to servo amplifier MR-J2S-350B or less.
For details, refer to Section 12.1.2 to 12.1.3.
Protective earth (PE)
Connect this terminal to the protective earth (PE) terminals of the servo motor and control box for grounding.
3 - 16
3. SIGNALS AND WIRING
3.5.3 Power-on sequence
(1) Power-on procedure
1) Always wire the power supply as shown in above Section 3.5.1 using the magnetic contactor with the main circuit power supply (3-phase 200V: L 1 , L 2 , L 3 , 1-phase 230V: L 1 , L 2 , 1-phase: L 1 L 2 ).
Configure up an external sequence to switch off the magnetic contactor as soon as an alarm occurs.
2) Switch on the control circuit power supply L 11 , L 21 simultaneously with the main circuit power supply or before switching on the main circuit power supply. If the main circuit power supply is not on, the display shows the corresponding warning. However, by switching on the main circuit power supply, the warning disappears and the servo amplifier will operate properly.
3) The servo amplifier can accept the servo-on command within 3s the main circuit power supply is switched on. (Refer to paragraph (2) in this section.)
(2) Timing chart
SON accepted
(3s)
Main circuit
Control circuit
Base circuit
Servo-on command
(from controller) power
ON
OFF
ON
OFF
ON
OFF
60ms 10ms 60ms
(3) Forced stop
CAUTION
Install an forced stop circuit externally to ensure that operation can be stopped and power shut off immediately.
If the controller does not have a forced stop function, make up a circuit that switches off main circuit power as soon as EM1 is turned off at a forced stop. When EM1 is turned off, the dynamic brake is operated to stop the servo motor. At this time, the display shows the servo forced stop warning (E6).
During ordinary operation, do not use forced stop (EM1) to alternate stop and run. The service life of the servo amplifier may be shortened.
Servo amplifier
Forced stop
VDD
COM
EM1
SG
3 - 17
3. SIGNALS AND WIRING
3.6 Connection of servo amplifier and servo motor
3.6.1 Connection instructions
WARNING
Insulate the connections of the power supply terminals to prevent an electric shock.
CAUTION
Connect the wires to the correct phase terminals (U, V, W) of the servo amplifier and servo motor. Otherwise, the servo motor will operate improperly.
Do not connect AC power supply directly to the servo motor. Otherwise, a fault may occur.
POINT
Do not apply the test lead bars or like of a tester directly to the pins of the connectors supplied with the servo motor. Doing so will deform the pins, causing poor contact.
The connection method differs according to the series and capacity of the servo motor and whether or not the servo motor has the electromagnetic brake. Perform wiring in accordance with this section.
(1) For grounding, connect the earth cable of the servo motor to the protective earth (PE) terminal of the servo amplifier and connect the ground cable of the servo amplifier to the earth via the protective earth of the control box. Do not connect them directly to the protective earth of the control panel.
Control box
Servo amplifier
Servo motor
PE terminal
(2) Do not share the 24VDC interface power supply between the interface and electromagnetic brake.
Always use the power supply designed exclusively for the electromagnetic brake.
3.6.2 Connection diagram
POINT
For the connection diagram of the MR-J2S-11KB to MR-J2S-22KB, refer to Section 3.12 where the connection diagram is shown together with the power line circuit.
The following table lists wiring methods according to the servo motor types. Use the connection diagram which conforms to the servo motor used. For cables required for wiring, refer to Section 12.2.1. For encoder cable connection, refer to Section 12.1.4. For the signal layouts of the connectors, refer to Section
3.6.3.
For the servo motor connector, refer to Chapter 3 of the Servo Motor Instruction Manual.
3 - 18
3. SIGNALS AND WIRING
Servo motor
HC-KFS053 (B) to 73 (B)
HC-MFS053 (B) to 73 (B)
HC-UFS13 (B) to 73 (B)
HC-SFS121 (B) to 301 (B)
HC-SFS202 (B) to 702 (B)
HC-SFS203 (B) 353 (B)
HC-UFS202 (B) to 502 (B)
HC-RFS353 (B) 503 (B)
HC-SFS81 (B)
HC-SFS52 (B) to 152 (B)
HC-SFS53 (B) to 153 (B)
HC-RFS103 (B) to 203 (B)
HC-UFS72 (B) 152 (B)
Connection diagram
Servo amplifier
U
V
W
Servo motor
U (Red)
V (White)
W (Black)
(Green)
(Note 1) 24VDC
B1
EM1
B2
To be shut off when servo-off or alarm occurrence
Motor
(Note 2)
Electromagnetic brake
CN2
Encoder cable Encoder
Note:1. To prevent an electric shock, always connect the protective earth (PE) terminal of the servo amplifier to the protective earth (PE) of the control box.
2. This circuit applies to the servo motor with electromagnetic brake.
Servo amplifier Servo motor
U
V
W
U
V
W
Motor
(Note 1) 24VDC
B1
B2
EM1
To be shut off when servo-off or alarm occurrence
(Note 2)
Electromagnetic brake
CN2
Note:1. To prevent an electric shock, always connect the protective earth (PE) terminal of the servo amplifier to the protective earth (PE) of the control box.
2. This circuit applies to the servo motor with electromagnetic brake.
Servo amplifier Servo motor
U
V
W
Encoder cable
U
V
W
Encoder
Motor
(Note 1) 24VDC
B1
B2
EM1
To be shut off when servo-off or alarm occurrence
(Note 2)
Electromagnetic brake
CN2
Encoder cable
Encoder
Note:1. To prevent an electric shock, always connect the protective earth (PE) terminal of the servo amplifier to the protective earth (PE) of the control box.
2. This circuit applies to the servo motor with electromagnetic brake.
3 - 19
3. SIGNALS AND WIRING
3.6.3 I/O terminals
(1) HC-KFS HC-MFS HC-UFS3000r/min series
Power supply connector
5557-04R-210
1 3
2 4
View b a
Encoder cable 0.3m (0.98ft.)
With connector 1-172169-9
(Tyco Electronics) b
Pin
1
2
3
4
Signal
U
V
W
(Earth)
Power supply lead
4-AWG19 0.3m (0.98ft.)
Power supply connector (molex)
Without electromagnetic brake
5557-04R-210 (receptacle)
5556PBTL (Female terminal)
With electromagnetic brake
5557-06R-210 (receptacle)
5556PBTL (Female terminal)
Power supply connector
5557-06R-210
1 4
2 5
3 6
View b
Encoder connector signal arrangement
Pin
1
2
5
6
3
4
1
MR
4
MD
7
P5
2 3
MRR BAT
5
MDR
6
8
LG
9
SHD
View a
Signal
U
V
W
(Earth)
(Note) B1
(Note) B2
Note:For the motor with
electromagnetic brake,
supply electromagnetic
brake power (24VDC).
There is no polarity.
3 - 20
3. SIGNALS AND WIRING
(2) HC-SFS HC-RFS HC-UFS2000 r/min series a
Encoder connector b
Brake connector c
Power supply connector
Servo motor side connectors
Servo motor
For power supply For encoder
HC-SFS81(B)
HC-SFS52(B) to 152(B)
HC-SFS53(B) to 153(B)
HC-SFS121(B) to 301(B)
HC-SFS202(B) to 502 (B)
HC-SFS203(B) 353(B)
CE05-2A22-
23PD-B
CE05-2A24-
10PD-B
HC-SFS702(B)
HC-RFS103(B) to 203 (B)
CE05-2A32-
17PD-B
CE05-2A22-
23PD-B
HC-RFS353(B) 503(B)
CE05-2A24-
10PD-B
HC-UFS72(B) 152(B)
HC-UFS202(B) to 502(B)
CE05-2A22-
23PD-B
CE05-2A24-
10PD-B
MS3102A20-
29P
Electromagnetic brake connector
The connector for power is shared.
MS3102A10SL-
4P
The connector for power is shared.
MS3102A10SL-
4P
Power supply connector signal arrangement
CE05-2A22-23PD-B CE05-2A24-10PD-B CE05-2A32-17PD-B
Key
F
G
H
E
D
View c
A
B
C
Signal
U
V
W
(Earth)
Key
Pin
D
E
F
G
H
A
B
C
(Note)
B1
(Note)
B2
E
F
D
G
View c
Note:For the motor with
electromagnetic brake,
supply electromagnetic
brake power (24VDC).
There is no polarity.
A
C
B
Encoder connector signal arrangement
MS3102A20-29P
Key
K
J
L
M
H
T
N
A
P
B
C
D
E
S R
G
F
View a
Pin
D
E
A
B
C
Signal
MD
MDR
MR
MRR
G
H
J
BAT
LG
Pin
P
R
S
T
K
L
M
N
Signal
SD
LG
P5
Signal
U
V
W
(Earth)
(Note)
B1
(Note)
B2
Key
Pin
C
D
A
B
E
F
G
D
C
Note:For the motor with
electromagnetic brake,
supply electromagnetic
brake power (24VDC).
There is no polarity.
A
B
Pin
A
B
C
D
Signal
U
V
W
(Earth)
Electromagnetic brake connector signal arrangement
MS3102A10SL-4P
Key
Pin
A
B
Signal
(Note)
B1
(Note)
B2
A
View b
B
Note:For the motor with
electromagnetic brake,
supply electromagnetic
brake power (24VDC).
There is no polarity.
3 - 21
3. SIGNALS AND WIRING
3.7 Servo motor with electromagnetic brake
CAUTION
Configure the electromagnetic brake circuit so that it is activated not only by the interface unit signals but also by a forced stop (EM1).
Contacts must be open when servo-off, when an alarm occurrence and when an electromagnetic brake interlock (MBR).
Servo motor
RA EM1
Circuit must be opened during forced stop (EM1).
24VDC
Electromagnetic brake
The electromagnetic brake is provided for holding purpose and must not be used for ordinary braking.
Before performing the operation, be sure to confirm that the elecromagnetic brake operates properly.
POINT
Refer to the Servo Motor Instruction Manual for specifications such as the power supply capacity and operation delay time of the electromagnetic brake.
Note the following when the servo motor equipped with electromagnetic brake is used:
1) Do not share the 24VDC interface power supply between the interface and electromagnetic brake. Always use the power supply designed exclusively for the electromagnetic brake.
2) The brake will operate when the power (24VDC) switches off.
3) Switch off the servo-on command after the servo motor has stopped.
(1) Connection diagram
Servo amplifier
VDD
COM
MBR RA
24VDC
RA
Forced stop
B1
Servo motor
B2
(2) Setting
In parameter No.21 (electromagnetic brake sequence output), set the time delay (Tb) from electromagnetic brake operation to base circuit shut-off at a servo off time as in the timing chart in (3) in this section.
3 - 22
3. SIGNALS AND WIRING
(3) Timing charts
(a) Servo-on command (from controller) ON/OFF
Tb [ms] after the servo-on is switched off, the servo lock is released and the servo motor coasts. If the electromagnetic brake is made valid in the servo lock status, the brake life may be shorter.
Therefore, when using the electromagnetic brake in a vertical lift application or the like, set delay time (Tb) to about the same as the electromagnetic brake operation delay time to prevent a drop.
Coasting
Servo motor speed
0 r/min
Tb (60ms)
ON
Base circuit
OFF
Electromagnetic brake interlock (MBR)
Invalid(ON)
Valid(OFF)
(80ms)
Electromagnetic brake operation delay time
Servo-on command
(from controller)
ON
OFF
(b) Forced stop command (from controller) or forced stop (EM1) ON/OFF
Servo motor speed
Dynamic brake
Dynamic brake
Electromagnetic brake
Electromagnetic brake
Electromagnetic brake release
(180ms)
Base circuit
Electromagnetic brake interlock (MBR)
ON
OFF
Invalid (ON)
(10ms)
Valid (OFF)
Electromagnetic brake operation delay time
(180ms)
Forced stop command
(from controller) or
Forced stop (EM1)
Invalid (ON)
Valid (OFF)
3 - 23
3. SIGNALS AND WIRING
(c) Alarm occurrence
Servo motor speed
Dynamic brake
Dynamic brake
Electromagnetic brake
Electromagnetic brake
(10ms)
Base circuit
ON
OFF
Electromagnetic brake interlock (MBR)
Invalid(ON)
Valid(OFF)
Electromagnetic brake operation delay time
Trouble
No
Yes
(d) Both main and control circuit power supplies off
Servo motor speed (Note)
15 to 60ms
(10ms)
Dynamic brake
Dynamic brake
Electromagnetic brake
Electromagnetic brake
Base circuit
ON
OFF
Electromagnetic brake interlock(MBR)
Invalid(ON)
Valid(OFF)
No(ON)
Alarm
Main circuit power
Control circuit
Yes(OFF)
ON
OFF
Electromagnetic brake operation delay time
(Note 2)
Note. Changes with the operating status.
(e) Only main circuit power supply off (control circuit power supply remains on)
Servo motor speed
(10ms)
(Note 1)
15ms or more
Dynamic brake
Dynamic brake
Electromagnetic brake
Electromagnetic brake
Base circuit
ON
OFF
Electromagnetic brake interlock
(MBR)
Invalid(ON)
Valid(OFF)
Alarm
No(ON)
Yes(OFF)
Electromagnetic brake operation delay time
(Note 2)
ON
Main circuit power supply OFF
Note 1. Changes with the operating status.
2. When the main circuit power supply is off in a motor stop status, the main circuit off warning (A.E9) occurs and the trouble (ALM) does not turn off.
3 - 24
3. SIGNALS AND WIRING
3.8 Grounding
WARNING
Ground the servo amplifier and servo motor securely.
To prevent an electric shock, always connect the protective earth (PE) terminal of the servo amplifier with the protective earth (PE) of the control box.
The servo amplifier switches the power transistor on-off to supply power to the servo motor. Depending on the wiring and ground cablerouting, the servo amplifier may be affected by the switching noise (due to di/dt and dv/dt) of the transistor. To prevent such a fault, refer to the following diagram and always ground.
To conform to the EMC Directive, refer to the EMC Installation Guidelines (IB(NA)67310).
Control box
Servo motor
NFB
MC Servo amplifier
L
1
CN2
(Note 1)
Power supply
3-phase
200 to 230VAC,
1-phase
230VAC or
1-phase
100 to 120VAC
L
2
L
3
L
11
L
21
Encoder
U
V
W
U
V
W
M
CN1A
(Note 2)
Protective earth(PE)
Outer box
Ensure to connect it to PE terminal of the servo amplifier.
Do not connect it directly to the protective earth of the control panel.
Note: 1. For 1-phase 230VAC, connect the power supply to L
1
L
2
and leave L
3
open.
There is no L
3
for 1-phase 100 to 120VAC power supply.
2. To reduce the influence of external noise, we recommend you to ground the bus cable near
the controller using a cable clamping fixture or to connect three or four data line filters in series.
3 - 25
3. SIGNALS AND WIRING
3.9 Servo amplifier terminal block (TE2) wiring method
POINT
Refer to Table 12.1 2) and (4) in Section 12.2.1 for the wire sizes used for wiring.
3.9.1 For servo amplifier produced earlier later than January, 2006
(1) Termination of the cables
(a) Solid wire
After the sheath has been stripped, the cable can be used as it is.
Sheath
Core
Approx. 10mm
(b) Twisted wire
1) When the cable is inserted directly
Use the cable after stripping the sheath and twisting the core. At this time, take care to avoid a short caused by the loose wires of the core and the adjacent pole. Do not solder the core as it may cause a contact fault.
2) When the twisted wires are put together using a bar terminal
Use the bar terminal shown below.
Cable Size
[mm
2
] AWG
1.25/1.5
2/2.5
16
14
AI1.5-10BK
AI2.5-10BU
Bar Terminal Type
For 1 cable For 2 cables
AI-TWIN2 1.5-10BK
Crimping Tool Maker
CRIMPFOX ZA 3 Phoenix Contact
Cut the cable running out of bar terminal to less than 0.5 mm
Less than 0.5mm
When using a bar terminal for 2 cables, insert the cables in the direction where the insulation sleeve does not interfere with next pole, and pressure then.
Pressure
Pressure
3 - 26
3. SIGNALS AND WIRING
(2) Connection
(a) When the cable is inserted directly
Insert the cable to the end pressing the button with a small flat-blade screwdriver or the like.
Button
Small flat blade screwdriver or the like
Twisted wire
When removing the short-circuit bar from across P-D, press the buttons of P and D alternately pulling the short-circuit bar. For the installation, insert the bar straight to the end.
(b) When the twisted wires are put together using a bar terminal
Insert a bar terminal with the odd-shaped side of the pressured terminal on the button side.
Bar terminal for one wire or solid wire
Bar terminal for two wires
When two cables are inserted into one opening, a bar terminal for 2 cables is required.
3 - 27
3. SIGNALS AND WIRING
3.9.2 For the servo amplifier produced earlier than December, 2005
(1) Termination of the cables
Solid wire: After the sheath has been stripped, the cable can be used as it is.
Approx. 10mm
(0.39inch)
Twisted wire: Use the cable after stripping the sheath and twisting the core. At this time, take care to avoid a short caused by the loose wires of the core and the adjacent pole. Do not solder the core as it may cause a contact fault.
Alternatively, a bar terminal may be used to put the wires together.
Cable Size
[mm
2
] AWG
1.25/1.5
2/2.5
16
14
AI1.5-10BK
AI2.5-10BU
Bar Terminal Type
For 1 cable For 2 cables
AI-TWIN2 1.5-10BK
Crimping Tool Maker
CRIMPFOX ZA 3 or
CRIMPFOX UD 6
Phoenix Contact
(2) Connection
Insert the core of the cable into the opening and tighten the screw with a flat-blade screwdriver so that the cable does not come off. (Tightening torque: 0.3 to 0.4N m(2.7 to 3.5 lb in)) Before inserting the cable into the opening, make sure that the screw of the terminal is fully loose.
When using a cable of 1.5mm
2 or less, two cables may be inserted into one opening.
Flat-blade screwdriver
Tip thickness 0.4 to 0.6mm
Overall width 2.5 to 3.5mm
To loosen.
To tighten.
Cable
Opening
Control circuit terminal block
Use of a flat-blade torque screwdriver is recommended to manage the screw tightening torque. The following table indicates the recommended products of the torque screwdriver for tightening torque management and the flat-blade bit for torque screwdriver. When managing torque with a Phillips bit, please consult us.
Product
Torque screwdriver
Bit for torque screwdriver
Model
N6L TDK
B-30, flat-blade, H3.5 X 73L
Maker/Representative
Nakamura Seisakusho
Shiro Sangyo
3 - 28
3. SIGNALS AND WIRING
3.10 Instructions for the 3M connector
When fabricating an encoder cable or the like, securely connect the shielded external conductor of the cable to the ground plate as shown in this section and fix it to the connector shell.
External conductor Sheath
Strip the sheath.
Screw
Core
External conductor
Sheath
Pull back the external conductor to cover the sheath
Cable
Ground plate
Screw
3 - 29
3. SIGNALS AND WIRING
3.11 Control axis selection
POINT
The control axis number set to SW1 should be the same as the one set to the servo system controller.
Use the axis select switch (SW1) to set the control axis number for the servo. If the same numbers are set to different control axes in a single communication system, the system will not operate properly. The control axes may be set independently of the bus cable connection sequence.
Set the switch to "F" when executing the test operation mode using MR Configurator (servo configuration software).
Axis select switch (SW1)
5
6
7
8 9
A
B
D
3
2
1 0
F
E
A
B
8
9
C
6
7
4
5
D
E
F
No.
2
3
0
1
Description
Axis 1
Axis 2
Axis 3
Axis 4
Axis 5
Axis 6
Axis 7
Axis 8
Not used
Not used
Not used
Not used
Not used
Not used
Not used
Test operation mode or when machine analyzer is used
(Refer to Section 6.1.2)
3 - 30
3. SIGNALS AND WIRING
3.12 Power line circuit of the MR-J2S-11KB to MR-J2S-22KB
CAUTION
When the servo amplifier has become faulty, switch power off on the amplifier power side. Continuous flow of a large current may cause a fire.
Switch power off at detection of an alarm. Otherwise, a regenerative brake transistor fault or the like may overheat the regenerative brake resistor, causing a fire.
POINT
The power-on sequence is the same as in Section 3.5.3.
3.12.1 Connection example
Wire the power supply/main circuit as shown below so that power is shut off and the servo-on signal turned off as soon as an alarm occurs, a servo forced stop is made valid, a controller forced stop, or a servo motor thermal relay alarm is made valid. A no-fuse breaker (NFB) must be used with the input cables of the power supply.
Servo motor thermal relay
RA3
(Note)
Alarm
RA1
Controller forced stop
RA2
Forced stop OFF ON
MC
MC
SK
3-phase
200 to
230VAC
NFB
Forced stop
MC
Servo amplifier
L
1
L
2
L
3
L
11
L
21
P
P
1
U
V
W
(Note 2)
Dynamic break Servo motor
HA-LFS series
U
V
W
M
CN2
MR-JHSCBL M cable
Encoder
BU
BV
BW
Fan
(Note3)
VDD
COM
EM1
SG
24VDC power supply
OHS1
RA3
OHS2 Servo motor thermal relay
Note 1. Configure up the power supply circuit which switches off the magnetic contactor after detection of alarm occurrence on the controller side.
2. When using the external dynamic break, refer to section 12. 1. 4.
3. There is no BW when the HA-LFS11K2 is used.
4. Always connect P-P
1
. (Factory-wired.) When using the power factor improving DC reactor, refer to
Section 12.2.4.
3 - 31
3. SIGNALS AND WIRING
3.12.2 Servo amplifier terminals
The positions and signal arrangements of the terminal blocks change with the capacity of the servo amplifier. Refer to Section 10.1.
Symbol
L
1
, L
2
, L
3
U, V, W
L
11
, L
21
P, C
N
P
1
, P
Connection Target
(Application)
Description
Main circuit power supply Supply L
1
, L
2
and L
3
with three-phase 200 to 230VAC, 50/60Hz power.
Servo motor output Connect to the servo motor power supply terminals (U, V, W).
Control circuit power supply Supply L
11
and L
21
with single-phase 200 to 230VAC power.
Regenerative brake option
Return converter
Brake unit
The servo amplifier built-in regenerative brake resistor is not connected at the time of shipment.
When using the regenerative brake option, wire it across P-C.
Refer to Section 12.1.1 for details.
When using the return converter or brake unit, connect it across P-N.
Refer to Sections 12.1.2 and 12.1.3 for details.
Protective earth (PE)
Connect this terminal to the protective earth (PE) terminals of the servo motor and control box for grounding.
Power factor improving DC reactors
P
1
-P are connected before shipment. When connecting a power factor improving
DC reactor, remove the short bar across P
1
-P. Refer to Section 12.2.4 for details.
3 - 32
3. SIGNALS AND WIRING
3.12.3 Servo motor terminals
Terminal box Encoder connector
MS3102A20-29P
Terminal box inside (HA-LFS11K2)
Encoder connector signal arrangement
MS3102A20-29P
Key
K
J
L
M
T
S
N
A
P
B
C
D
R E
H
G
F
F
G
H
Pin Signal
A MD
B
C
D
E
MDR
MR
MRR
BAT
LG
J
R
S
T
N
P
Pin Signal
K
L
M
SHD
LG
P5
Thermal sensor terminal block (OHS1, OHS2)
M4 screw
Motor power supply terminal block
(U, V, W) M6 screw
Cooling fan terminal block
(BU, BV) M4 screw
Earth terminal
M6 screw
Encoder connector
MS3102A20-29P BG72707B
Terminal block signal arrangement
OHS1OHS2
U V W
BU BV
Power supply connection screw size
Servo motor
HA-LFS11K2
Power supply connection screw size
M6
3 - 33
3. SIGNALS AND WIRING
Terminal box inside (HA-LFS15K2 HA-LFS-22K2)
Cooling fan terminal block (BU, BV, BW)
M4 screw
Thermal sensor terminal block (OHS1, OHS2)
M4 screw
Moter power supply terminal block
(U, V, W) M8 screw
Earth terminal M6 screw
Terminal block signal arrangement
BU BV BW OHS1OHS2
Encoder connector
MS3102A20-29P
U V W
Power supply connection screw size
Power supply connection screw size Servo motor
HA-LFS15K2
HA-LFS22K2
M8
Signal Name
Power supply
Cooling fan
Abbreviation Description
U V W Connect to the motor output terminals (U, V, W) of the servo amplifier.
Supply power which satisfies the following specifications.
HA-LFS11K2
Item
Voltage/frequency
Description single-phase 200 to 220VAC, 50Hz single-phase 200 to 230VAC, 60Hz
42(50Hz)/54(60Hz)
0.12(50Hz)/0.25(60Hz)
(Note)
BU BV BW
Power consumption [W]
Rated voltage [V]
HA-LFS15K2/22K2
Item
Voltage/frequency
Power consumption [W]
Rated voltage [V]
Description
Three-phase 200 to 220VAC, 50Hz
Three-phase 200 to 230VAC, 60Hz
32(50Hz)/40(60Hz)
0.30(50Hz)/0.25(60Hz)
Motor thermal relay OHS1 OHS2 OHS1-OHS2 are opened when heat is generated to an abnormal temperature.
Earth terminal
For grounding, connect to the earth of the control box via the earth terminal of the servo amplifier.
Note. There is no BW when the HA-LFS11K2 is used.
3 - 34
advertisement
Related manuals
advertisement
Table of contents
- 2 Safety Instructions
- 7 About processing of waste
- 8 COMPLIANCE WITH EC DIRECTIVES
- 10 CONFORMANCE WITH UL/C-UL STANDARD
- 11 About the manuals
- 12 CONTENTS
- 16 Optional Servo Motor Instruction Manual CONTENTS
- 18 1. FUNCTIONS AND CONFIGURATION
- 18 1.1 Introduction
- 19 1.2 Function block diagram
- 22 1.3 Servo amplifier standard specifications
- 23 1.4 Function list
- 24 1.5 Model code definition
- 25 1.6 Combination with servo motor
- 26 1.7 Structure
- 26 1.7.1 Parts identification
- 31 1.7.2 Removal and reinstallation of the front cover
- 34 1.8 Servo system with auxiliary equipment
- 40 2. INSTALLATION
- 40 2.1 Environmental conditions
- 41 2.2 Installation direction and clearances
- 42 2.3 Keep out foreign materials
- 43 2.4 Cable stress
- 44 3. SIGNALS AND WIRING
- 45 3.1 Connection example of control signal system
- 45 3.1.1 MR-J2S-700B or less
- 47 3.1.2 MR-J2S-11KB or more
- 49 3.2 I/O signals
- 49 3.2.1 Connectors and signal arrangements
- 51 3.2.2 Signal explanations
- 52 3.3 Alarm occurrence timing chart
- 53 3.4 Interfaces
- 53 3.4.1 Common line
- 54 3.4.2 Detailed description of the interfaces
- 57 3.5 Power line circuit
- 57 3.5.1 Connection example
- 59 3.5.2 Terminals
- 60 3.5.3 Power-on sequence
- 61 3.6 Connection of servo amplifier and servo motor
- 61 3.6.1 Connection instructions
- 61 3.6.2 Connection diagram
- 63 3.6.3 I/O terminals
- 65 3.7 Servo motor with electromagnetic brake
- 68 3.8 Grounding
- 69 3.9 Servo amplifier terminal block (TE2) wiring method
- 69 3.9.1 For servo amplifier produced earlier later than January, 2006
- 71 3.9.2 For the servo amplifier produced earlier than December, 2005
- 72 3.10 Instructions for the 3M connector
- 73 3.11 Control axis selection
- 74 3.12 Power line circuit of the MR-J2S-11KB to MR-J2S-22KB
- 74 3.12.1 Connection example
- 75 3.12.2 Servo amplifier terminals
- 76 3.12.3 Servo motor terminals
- 78 4. OPERATION AND DISPLAY
- 78 4.1 When switching power on for the first time
- 79 4.2 Start up
- 81 4.3 Servo amplifier display
- 83 4.4 Test operation mode
- 86 5. PARAMETERS
- 86 5.1 Parameter write inhibit
- 86 5.2 Lists
- 100 5.3 Analog monitor
- 103 5.4 Replacement of MR-J2-[]B by MR-J2S-[]B
- 103 5.4.1 Main modifications made to the parameters
- 104 5.4.2 Explanation of the modified parameters
- 108 6. GENERAL GAIN ADJUSTMENT
- 108 6.1 Different adjustment methods
- 108 6.1.1 Adjustment on a single servo amplifier
- 110 6.1.2 Adjustment using MR Configurator (servo configuration software)
- 111 6.2 Auto tuning
- 111 6.2.1 Auto tuning mode
- 112 6.2.2 Auto tuning mode operation
- 113 6.2.3 Adjustment procedure by auto tuning
- 114 6.2.4 Response level setting in auto tuning mode
- 115 6.3 Manual mode 1 (simple manual adjustment)
- 115 6.3.1 Operation of manual mode 1
- 115 6.3.2 Adjustment by manual mode 1
- 118 6.4 Interpolation mode
- 119 6.5 Differences in auto tuning between MELSERVO-J2 and MELSERVO-J2-Super
- 119 6.5.1 Response level setting
- 119 6.5.2 Auto tuning selection
- 120 7. SPECIAL ADJUSTMENT FUNCTIONS
- 120 7.1 Function block diagram
- 120 7.2 Machine resonance suppression filter
- 122 7.3 Adaptive vibration suppression control
- 123 7.4 Low-pass filter
- 124 7.5 Gain changing function
- 124 7.5.1 Applications
- 124 7.5.2 Function block diagram
- 125 7.5.3 Parameters
- 127 7.5.4 Gain changing operation
- 130 8. INSPECTION
- 132 9. TROUBLESHOOTING
- 132 9.1 Alarms and warning list
- 133 9.2 Remedies for alarms
- 139 9.3 Remedies for warnings
- 140 10. OUTLINE DIMENSION DRAWINGS
- 140 10.1 Servo amplifiers
- 147 10.2 Connectors
- 150 11. CHARACTERISTICS
- 150 11.1 Overload protection characteristics
- 151 11.2 Power supply equipment capacity and generated loss
- 154 11.3 Dynamic brake characteristics
- 156 11.4 Encoder cable flexing life
- 157 11.5 Inrush currents at power-on of main circuit and control circuit
- 158 12. OPTIONS AND AUXILIARY EQUIPMENT
- 158 12.1 Options
- 158 12.1.1 Regenerative brake options
- 167 12.1.2 Brake unit
- 169 12.1.3 Power regeneration converter
- 172 12.1.4 External dynamic brake
- 175 12.1.5 Cables and connectors
- 188 12.1.6 Maintenance junction card (MR-J2CN3TM)
- 189 12.1.7 Battery (MR-BAT, A6BAT)
- 190 12.1.8 MR Configurator (servo configurations software)
- 191 12.1.9 Power regeneration common converter
- 195 12.1.10 Heat sink outside mounting attachment (MR-JACN)
- 198 12.2 Auxiliary equipment
- 198 12.2.1 Recommended wires
- 201 12.2.2 No-fuse breakers, fuses, magnetic contactors
- 201 12.2.3 Power factor improving reactors
- 202 12.2.4 Power factor improving DC reactors
- 203 12.2.5 Relays
- 203 12.2.6 Surge absorbers
- 203 12.2.7 Noise reduction techniques
- 209 12.2.8 Leakage current breaker
- 211 12.2.9 EMC filter
- 214 13. ABSOLUTE POSITION DETECTION SYSTEM
- 214 13.1 Features
- 215 13.2 Specifications
- 216 13.3 Battery installation procedure
- 217 13.4 Confirmation of absolute position detection data
- 218 Appendix
- 218 App. Combination of servo amplifier and servo motor
- 219 REVISIONS