Engineering Data. NIBCO C705LFHD341834, C616HD34, MCP600RHD3412, C904HD114, C907HD114, MCP607HD34, C906-2, MCP607HD12, 604, C6032HD12
Add to My manuals56 Pages
advertisement
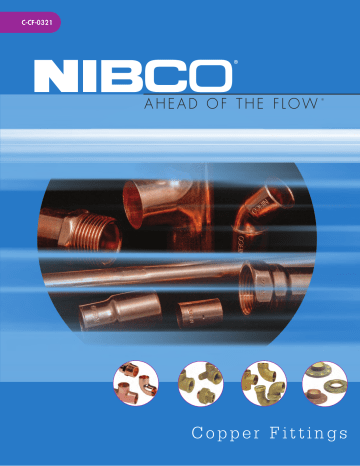
www.nibco.com
Engineering Data Installation Instructions
Brazing Alloy
Consumption . . . . . . . . . . . . . . . . . . . . . . . . . . . . . . . . . . . . . . . . . . . . . . . . . . . 40
Brazing Fittings
Dimensions . . . . . . . . . . . . . . . . . . . . . . . . . . . . . . . . . . . . . . . . . . . . . . . . . . . . 44
Installation Techniques . . . . . . . . . . . . . . . . . . . . . . . . . . . . . . . . . . . . . . . . 47-48
Copper Fittings Demensional Data
Solder Joing Fitting Ends . . . . . . . . . . . . . . . . . . . . . . . . . . . . . . . . . . . . . . . . . 43
Brazing Fitting Ends. . . . . . . . . . . . . . . . . . . . . . . . . . . . . . . . . . . . . . . . . . . . . . 44
Expansion and Contraction . . . . . . . . . . . . . . . . . . . . . . . . . . . . . . . . . . . . . . . . 45
Copper Tube Fittings
Brazing Information. . . . . . . . . . . . . . . . . . . . . . . . . . . . . . . . . . . . . . . . . . . . . . 40
Fitting Terms and Abbreviations. . . . . . . . . . . . . . . . . . . . . . . . . . . . . . . . . . . . 37
Plumbing System Failures. . . . . . . . . . . . . . . . . . . . . . . . . . . . . . . . . . . . . . . . . 38
Rated Internal Working Pressures . . . . . . . . . . . . . . . . . . . . . . . . . . . . . . . 41-42
Solder and Flux Requirements . . . . . . . . . . . . . . . . . . . . . . . . . . . . . . . . . . . . . 40
Solder Joint Specification. . . . . . . . . . . . . . . . . . . . . . . . . . . . . . . . . . . . . . . . . 39
Types of Joints . . . . . . . . . . . . . . . . . . . . . . . . . . . . . . . . . . . . . . . . . . . . . . . . . 37
Frequently Asked Questions . . . . . . . . . . . . . . . . . . . . . . . . . . . . . . . . . . . . . 49
Joints
Abbreviations . . . . . . . . . . . . . . . . . . . . . . . . . . . . . . . . . . . . . . . . . . . . . . . . . . 37
Brazing. . . . . . . . . . . . . . . . . . . . . . . . . . . . . . . . . . . . . . . . . . . . . . . . . . . . . 44-45
Soldering . . . . . . . . . . . . . . . . . . . . . . . . . . . . . . . . . . . . . . . . . . . . . . . . . . . . . . 43
Types . . . . . . . . . . . . . . . . . . . . . . . . . . . . . . . . . . . . . . . . . . . . . . . . . . . . . . . . . 37
Rated Internal Working Pressures . . . . . . . . . . . . . . . . . . . . . . . . . . . . . . . .41-42
Solder and Flux
Ratings. . . . . . . . . . . . . . . . . . . . . . . . . . . . . . . . . . . . . . . . . . . . . . . . . . . . . . . . 41
Requirements . . . . . . . . . . . . . . . . . . . . . . . . . . . . . . . . . . . . . . . . . . . . . . . . . . 40
eering
Solder Joint Fittings
Dimensions . . . . . . . . . . . . . . . . . . . . . . . . . . . . . . . . . . . . . . . . . . . . . . . . . . . . 43
Installation Techniques . . . . . . . . . . . . . . . . . . . . . . . . . . . . . . . . . . . . . . . . . . . 46
The Fine Art of Soldering . . . . . . . . . . . . . . . . . . . . . . . . . . . . . . . . . . . . . . . . 46
The Fine Art of Brazing . . . . . . . . . . . . . . . . . . . . . . . . . . . . . . . . . . . . . . . 47-48
Numerical Index
Numerical Index . . . . . . . . . . . . . . . . . . . . . . . . . . . . . . . . . . . . . . . . . . . . . . . . 51
Visit our website for the most current information.
36
NIBCO INC. WORLD HEADQUARTERS • 1516 MIDDLEBURY ST. • ELKHART, IN 46516-4740 • USA • PH: 1.800.234.0227
TECH SERVICES PH: 1.888.446.4226 • FAX: 1.888.234.0557 • INTERNATIONAL OFFICE PH: +1.574.295.3327 • FAX: +1.574.295.3455
www.nibco.com
The manufacturing plants at
Stuarts Draft, VA, Nacogdoches, TX and Reynosa, Mexico manufacture products under a Quality
Management System conforming to the current revision of ISO-9001
International Standards
www.nibco.com
A H E A D O F T H E F L O W
®
Copper
Tube Fittings
TYPES OF JOINTS
Flared Joint — The principle of the flared joint was first developed for copper tube plumbing in 1928 by NIBCO. The flared type joint is wholly a mechanical means of joining copper tubes. The tube nut is placed over the end of the copper tube to be joined; the tube end then is flared out at an approximate 45 degree angle by a flaring tool.
The flared end is then drawn up by the tube nut so the inside surface is tightly secured against the ball seat of the fitting. This joint can be readily dismantled at any time and is, in effect, a type of union connection. Its use is generally restricted to soft (annealed) copper tubes since hard drawn tubes would be subject to splitting when flared (if the ends were not previously annealed). The flared ends of
NIBCO ® Flared Fittings are produced to the requirements of ASME
B16.26, “Cast Copper Alloy Fittings for Flared Copper Tube.”
Solder Joint — NIBCO pioneered the development of the solder joint and its application to the field of copper tube piping. Today the solder joint is widely adopted, as evidenced by the majority of cities and states that have written codes to include copper tube and solder joints as desirable for general plumbing, water lines, vent, stack, waste and drain lines, as well as other uses in industry. Testing has shown that often the solder joint has greater strength than the tubes being joined, depending upon the soldering alloy selected. While the method of preparing a solder joint is an exacting art to insure a full strength joint, it can be readily mastered by skilled tradesmen. It is for this reason — to insure the public of the protection afforded by properly prepared joints — that NIBCO ® products are marketed through the reputable sources of supply to the piping trades. Important procedures for preparing a solder joint are graphically illustrated in this catalog on page 46.
Brazed Joint — This type of joint has long been used wherever and whenever critical situations have been encountered in copper piping.
The joint itself is completed much in the same manner as the solder joint; however, considerably more heat and several refinements of technique require separate procedures that are described further in this catalog on pages 47-48.
Threaded Ends — To adapt copper tube to equipment having
National Standard Pipe Taper (NPT) threads or to add copper tube to existing iron pipe installations or other threaded connections, NIBCO provides fittings having both external and internal NPT threads.
These threaded ends are produced to the requirements of ASME
B1.20.1, “Pipe Threads, General Purpose (Inch).”
Flanges — To adapt copper tube to equipment having flanged connections, or to add copper tube to flanged pipe installations or other purposes, NIBCO provides flanges. The flanges are produced in two standard types widely used in this field where copper tube can serve — Class 150, comply with ASME B16.24, “Cast Copper Alloy
Pipe Flanges and Flanged Fittings Class 150, 300, 400, 600, 900, 1500 and 2500”; and Class 125, which conform to MSS SP-106, “Cast
Copper Alloy Flanges and Flanged Fittings Class 125, 150 and 300.”
Barbed Insert Fittings for Polybutylene (PB) — NIBCO offers a complete line of copper barbed insert fittings for joining PB tube.
The insert fittings are produced to the requirements of ASTM F1380.
Along with the insert fittings are copper crimp rings, which, when properly installed, provide a leak-tight mechanical joint. Transition fittings are available for adapting to new or existing threaded or solder joint ends.
Fitting Terms and Abbreviations
C
Ftg
F
M
Hose
Hub
Spigot
No Hub
O.D. Tube
S
SJ
Female solder cup
Male solder end
Female NPT thread
Male NPT thread
Standard hose thread
Female end for soil pipe
Male end for soil pipe
Used with mechanical coupling
Actual tube outside diameter
Straight thread
Slip joint
FL Flared
Visit our website for the most current information.
NIBCO INC. WORLD HEADQUARTERS • 1516 MIDDLEBURY ST. • ELKHART, IN 46516-4740 • USA • PH: 1.800.234.0227
TECH SERVICES PH: 1.888.446.4226 • FAX: 1.888.234.0557 • INTERNATIONAL OFFICE PH: +1.574.295.3327 • FAX: +1.574.295.3455
www.nibco.com
37
www.nibco.com
WHAT MAKES A PLUMBING SYSTEM FAIL?
F ailure in a copper plumbing system is rare, but may occur due to a variety of reasons. The most common causes of failure are:
1. Excessive fluid velocity causes erosion-corrosion or impingement (to strike or hit against) attack in the tube and/or fitting. For this reason, the copper plumbing industry has establish design velocity limits for copper plumbing systems to the following:
Hot Water > 140°F (60°C)
Hot Water 140°F (60°C)
2 to 3 feet per second
(0.6 to 0.9 meters per second)
4 to 5 feet per second
(1.2 to 1.5 meters per second)
Cold Water 5 to 8 feet per second
(1.5 to 2.4 meters per second)
2. Localized high velocities and/or turbulence. The presence of a dent, tube ends which are not reamed or deburred before soldering, and sudden changes in direction can all cause localized high velocity conditions.
3. Flux Corrosion is typified by pin hole leaks, generally in the bottom of a horizontal line. Fluxes are mildly corrosive liquid or petroleum-based pastes containing chlorides of zinc and ammonia. Unless the flux is flushed from the system, it will lay in the bottom of the tube and remain active. ASTM B 813, “Liquid and Paste Fluxes for Soldering Applications of Copper and Copper-Alloy Tube,” limits the corrosivity of soldering fluxes and ensures that these fluxes are flushable in cold water, which facilitates easy removal of flux residue following installation.
4. Galvanic Corrosion may be defined as the destruction of a material by electrochemical interaction between the environment and the material.
Generally, it is slow but persistent in character and requires the presence of dissimilar metals. Galvanic corrosion requires the flow of an electric current between certain areas of dissimilar metal surfaces. To complete the electric circuit, there must be two electrodes, an anode and a cathode, and they must be connected by an electrolyte media (water) through which the current can pass. The amount of metal which dissolves at the anode is proportional to the number of electrons flowing, which in turn is dependent upon the potential and resistance of the two metals. The use of dissimilar metals in a plumbing system may or may not create a problem. For instance, copper and steel are perhaps the most common dissimilar metals found together in a plumbing system. In closed systems, such as a chilled or heating water piping, the use of dissimilar metals may not create a serious problem; this is because there is virtually no oxygen in the water and corrosion relations tend to be stifled. Where dissimilar metals must be used, some codes require that they should be separated by dielectric union or a similar type of fitting. The effectiveness depends upon; distance between the metals on the electromotive-force series
(EMF) chart, ratio of cathode to anode area, degree of aeration, amount of agitation, temperature, presence of dissolved salts, and other factors.
ABBREVIATED EMF SERIES
(Electromotive-Force Series; Common Piping Materials in Sea Water)
CATHODE (+) Passive
GOLD – Fixtures, Faucets, Plating
PLATINUM
SILVER – Brazing alloys, Silver-bearing solders
TITANIUM – Condenser tubes
MONEL (67% Ni - 33% Cu) – Specialty piping & equipment
CUPRO-NICKEL – Condensers, Marine, Nuclear
COPPER – Pressure, DWV, Gases, Air, Refrigeration, etc.
BRASS (85/15 - Red) – Cast fittings, Valves
BRASS (70/30 - Yellow) – Gas-cocks, Fittings, Connectors
LEAD – Solder, Pipe, Sheet, Coating, Lining
TIN – Solders, Coating, Lining
CAST IRON – Pressure, DWV
WROUGHT IRON – Pressure
MILD STEEL – Fire Protection
ALUMINUM – Refrigeration, Irrigation, some Solar
GALVANIZED STEEL – Pressure, DWV
ZINC – Coatings, Linings, some Fittings
MAGNESIUM – Water Heater Anodes, Cathodic protection for pipelines
ANODE (-) Active; Sacrificial Material
5. Dezincification is a type of corrosion in which brass dissolves as an alloy and the copper constituent redeposits from solution onto the surface of the brass as a metal, but in the porous form. The zinc constituent may be carried away from the brass as a soluble salt, or may be deposited in place as an insoluble compound. Dezincification is normally associated with brass valves where the zinc content exceeds 15%. Generally, areas of high stress, such as valve stems and gate valve bodies, are primary targets of attack.
6. On rare occasion problems of corrosion by aggressive water, possibly aggravated by poor design or workmanship, do exist. Aggressive, hard well waters that cause pitting can be identified by chemical analysis and treated to bring their composition within acceptable limits. Typically these hard waters are found to have high total dissolved solids (t.d.s.) including sulfates and chlorides, a pH in the range of 7.2 to 7.8, a high content of carbon dioxide (CO
2
) gas (over 10 parts per million, ppm), and the presence of dissolved oxygen (D.O.) gas. Soft acidic waters can cause the annoying problem of green staining of fixtures or “green water”. Raising the pH of such waters to a value of about 7.2 or more usually solves the problem, but a qualified water treatment specialist should be consulted.
7. Aggressive soil conditions can be a cause for external corrosion of copper piping systems. Non-uniform soil characteristics, such as different soil aeration, resistivity, or moisture properties, between adjacent sections of tube can create galvanic corrosion cells. Soils contaminated with high concentrations of road salts or fertilizers containing ammonia, chlorides, and nitrogen are known to combine with water to form acids. Any metal pipe laid in ash or cinders is subject to attack by the acid generated when sulfur compounds combine with water to form sulfuric acid.
U.S. customary units in this document are the standard; the metric units are provided for reference only. The values stated in each system are not exact equivalents.
Visit our website for the most current information.
38
NIBCO INC. WORLD HEADQUARTERS • 1516 MIDDLEBURY ST. • ELKHART, IN 46516-4740 • USA • PH: 1.800.234.0227
TECH SERVICES PH: 1.888.446.4226 • FAX: 1.888.234.0557 • INTERNATIONAL OFFICE PH: +1.574.295.3327 • FAX: +1.574.295.3455
www.nibco.com
www.nibco.com
A H E A D O F T H E F L O W
®
Copper Tube Fittings
continued
SOLDER JOINT SPECIFICATION
1. Soldering Clearance (between the outside of the tube and the inside diameter of the solder cup) and the Depth of the Solder
Cup (into which the tube is inserted).
Chart 1 – Soldering Clearance and Solder Cup Depth
Nominal Maximum Minimum Maximum Depth
Size
of Fitting
I.D. of
Fitting
O.D. of
Tube
Clearance for Soldering
Solder Cup
(Inches) Inch (mm) Inch (mm) Inch (mm) Inch (mm)
1/4 0.381 (9.66) 0.374 (9.50) 0.007 (0.18) 0.31 (7.9)
3/8 0.506 (12.85) 0.499 (12.67) 0.007 (0.18) 0.38 (9.7)
1/2 0.631 (16.03) 0.622 (15.80) 0.009 (0.23) 0.50 (12.7)
5/8 0.756 (19.20) 0.749 (19.02) 0.007 (0.18) 0.62 (15.7)
3/4 0.881 (22.38) 0.872 (22.20) 0.009 (0.23) 0.75 (19.1)
1 1.132 (28.75) 1.123 (28.54) 0.009 (0.23) 0.91 (23.1)
1 1.382 (35.10) 1.373 (34.88) 0.009 (0.23) 0.97 (24.6)
1 1.633 (41.48) 1.623 (41.22) 0.010 (0.25) 1.09 (27.7)
2
(34.0)
2.133 (54.18) 2.123 (53.92) 0.010 (0.25) 1.34
2 2.633 (66.88) 2.623 (66.62) 0.010 (0.25) 1.47
(37.3)
3
(42.2)
3.133 (79.58) 3.123 (79.32) 0.010 (0.25) 1.66
3 3.633 (92.28) 3.623 (92.02) 0.010 (0.25) 1.91 (48.5)
5 5.133
(67.6)
The National Bureau of Standards Report BMS58, “Strength of Soft-Soldered Joints in
Copper Tubing,” reporting on tests conducted with 3 /
4
-inch tubing and fitting, says “When the clearance is greater than 0.010 inch (0.25 mm), there is difficulty in filling the joint properly.”
2. Depth of Solder Penetration drastically affects the breaking load of the joint. When there is too great a soldering clearance, there is no capillary flow to assure complete solder penetration.
As shown in the chart below, the holding power of the 3 /
4
-inch joint is directly proportional to the depth of solder penetration.
For example: If you get only one-third penetration, you get approximately one-third the strength needed to assure complete satisfaction.
Chart 2 – Type K 3 /
4
" Tubing
HOW TO BE SURE OF PROPER TOLERANCES
It is apparent that all of the scientific apparatus used to test tube and fittings, according to the dimensions indicated in Chart 1, would be impractical to use on the job. It is therefore essential that you install tube and fittings manufactured by companies known to be dedicated to the highest quality control standards. Should you encounter a condition where there is difficulty in filling the joint properly, NIBCO will analyze the trouble without charge. Just send six inches of the tube, along with the fitting and our technicians will provide you with an authoritative report.
Solder penetration of one-third the cup depth — breaking load, approximately 2,100 lb. (955 kg)
Solder penetration of the entire cup depth — breaking load approximately 7,000 lb. (3175 kg)
Visit our website for the most current information.
U.S. customary units in this document are the standard; the metric units are provided for reference only. The values stated in each system are not exact equivalents.
NIBCO INC. WORLD HEADQUARTERS • 1516 MIDDLEBURY ST. • ELKHART, IN 46516-4740 • USA • PH: 1.800.234.0227
TECH SERVICES PH: 1.888.446.4226 • FAX: 1.888.234.0557 • INTERNATIONAL OFFICE PH: +1.574.295.3327 • FAX: +1.574.295.3455
www.nibco.com
39
www.nibco.com
BRAZING INFORMATION
Copper Water
Tube Size
(In Inches)
1/4
3/8
Brazing A Filler Required
Inches (mm)
0.25
B
0.38
B
Torch Tip
Drill Size No.
Acetylene Consumption
C.F.H. (C.M.H.)
For Estimating Purposes
Oxygen Pressure (Approx.)
PSI (kPa)
Acetylene Pressure (Approx.)
PSI (kPa)
3
3 1/2
7.90 (200.0) 35
10.50 (207.0) 35
70.0 (2.0) 7 1 /
2
(52) 7 1 /
2
(52)
70.0 (2.0) 7 1 /
2
(52) 7 1 /
2
(52)
A Approximate consumption when brazing one cup of the fitting. Actual consumption depends on workmanship.
For filler sizes shown, one pound of filler alloy provides 1,068 inches (27.13 mm) of 1 /
16
-inch wire or 475 inches (12,065 mm) of 3 /
32
-inch wire.
B 1 /
16
-inch (1.59 mm) diameter wire; all other is 3 /
32
-inch (2.38 mm) diameter.
Nom. Size Joint
(In Inches)
1/4
3/8
1/2
5/8
3/4
1
1 1/4
1 1/2
2
2 1/2
3
3 1/2
4
5
6
8
SOLDER AND FLUX REQUIREMENTS
General Use
0.097
0.159
0.261
0.389
0.548
0.856
1.115
1.480
2.380
3.225
4.335
5.786
7.446
11.392
15.815
26.955
Solder Required, LB (kg)
Drainage Use
1.2
1.4
1.5
–
2.8
–
4.2
–
–
–
–
–
–
–
–
–
(0.5)
(0.6)
(0.7)
(1.3)
(1.9)
Solder requirements in this table are based on estimate of weight of solder used to prepare
100 solder joints of sizes shown.
Two (2) ounces (0.06 kg) of solder flux will be required for each pound (0.45 kg) of solder.
U.S. customary units in this document are the standard; the metric units are provided for reference only. The values stated in each system are not exact equivalents.
Visit our website for the most current information.
40
NIBCO INC. WORLD HEADQUARTERS • 1516 MIDDLEBURY ST. • ELKHART, IN 46516-4740 • USA • PH: 1.800.234.0227
TECH SERVICES PH: 1.888.446.4226 • FAX: 1.888.234.0557 • INTERNATIONAL OFFICE PH: +1.574.295.3327 • FAX: +1.574.295.3455
www.nibco.com
www.nibco.com
A H E A D O F T H E F L O W
®
Copper Tube Fittings
continued
RATED INTERNAL WORKING PRESSURES OF JOINTS
MADE WITH COPPER WATER TUBE AND SOLDER TYPE FITTINGS, PSI (BAR)
Maximum Gauge Working Pressure for Standard Water Tube Sizes [Note (1)]
Working Temperature
Joining Material °F °C
1 /
8
" though 1" 1 1 /
PSI BAR
4
" through 2" 2 1 /
PSI BAR
2
" through 4"
PSI BAR
5" through 8"
PSI BAR
10" to 12"
PSI BAR
Saturated Steam
LB (kg)
All Sizes
Alloy Sn50
50-50 Tin-Lead solder
[Notes (2), (3)]
100
150
200
38 200
66
93
150 (10)
100 (7)
125 (9) 100 (7)
90 (6) 75 (5)
90 (6)
70 (5)
70 (5)
50 (3)
Alloy Sb5
250
100
95-5 Tin-Antimony solder 150
[Note (4)]
250
121 85 (6) 75 (5) 50 (3) 45 (3) 40 (3)
38 1090
93 505
121 270 (19) 210 (15)
705 (49)
175 (12)
(46) 340 (23)
165 (11)
280 (19)
230 (16)
120 (8)
Alloy E 100 38 710 ( 10) (32)
150
200
66
93 375 (26)
320 (22)
290 (20)
250 (17)
(11) (17)
205 (14)
(10) (30)
(16)
195 (13)
320 (22)
215 (15)
170 (12)
145 (9)
Joining materials at or
above 593°C
250 121
100 38
150 66
200 93
250 121
1035
710
440
430
(9)
(10)
(11)
(11)
(49)
(30)
(56)
(24)
670 (46)
Pressure-temperature ratings consistent with the materials and procedures employed.
15
15
15
625 (43) 340 (23)
(11)
(30) 320 (22) 15
(18) 200 (14)
195 (13)
[Note (7)]
GENERAL NOTE:
For extremely low working temperatures in the 0°F to 200°F range, it is recommended that a joint material melting at or above 1000°F be employed [see Note (5)].
NOTES:
(1) Standard water tube sizes per ASTM B 88
(2) ASTM B 32 Alloy Grade Sn50
(3) The Safe Drinking Water Act Amendment of 1986 prohibits the use of any solder having a lead content in excess of 0.2% in potable water systems.
(4) ASTM B 32 Alloy Grade Sb5
(5) ASTM B 32 Alloy Grade E
(6) ASTM B 32 Alloy Grade HB
(7) These joining materials are defined as brazing alloys by the American Welding Society.
(8) The solder joint exceeds the strength of Types K, L & M tube in drawn and annealed tempers.
(9) The solder joint exceeds the strength of Types L & M tube in drawn temper and Type K tube in annealed temper.
(10) The solder joint exceeds the strength of Type M tube in drawn temper and Types L & K in annealed temper.
(11) The solder joint exceeds the strength of Type L tube in annealed temper.
RATED INTERNAL WORKING PRESSURES OF JOINTS
MADE WITH FLARED FITTINGS AND COPPER WATER TUBE
Nominal Size Joint
(In Inches)
3/8, 1/2, 3/4, 1,
1 1/4, 1 1/2, 2
A ASME B16.26
Temperature, °F (°C) A
100 (38)
Pressure, PSI (BAR) A
175 (12)
RATED INTERNAL WORKING PRESSURES OF
POLYBUTYLENE TUBE AND COPPER BARBED INSERT FITTINGS
Nominal Size Joint
(In Inches)
3/8, 1/2, 3/4, 1
Temperature, °F (°C)
73 (23)
140 (60)
180 (82)
200 (93)
Pressure, PSI (BAR)
200 (14)
160 (11)
100 (7)
80 (5)
Visit our website for the most current information.
U.S. customary units in this document are the standard; the metric units are provided for reference only. The values stated in each system are not exact equivalents.
NIBCO INC. WORLD HEADQUARTERS • 1516 MIDDLEBURY ST. • ELKHART, IN 46516-4740 • USA • PH: 1.800.234.0227
TECH SERVICES PH: 1.888.446.4226 • FAX: 1.888.234.0557 • INTERNATIONAL OFFICE PH: +1.574.295.3327 • FAX: +1.574.295.3455
www.nibco.com
41
www.nibco.com
RATED INTERNAL WORKING PRESSURE 1 FOR COPPER FITTINGS, PSI (BAR)
Nominal Water
Size
(In Inches) (-29° to 38°C)
1/4
3/8
1/2
5/8
3/4
1
1 1/4
1 1/2
2
2 1/2
3
3 1/2
4
5
6
8
912 (62)
779 (54)
722 (50)
631 (43)
582 (40)
494 (34)
439 (30)
408 (28)
364 (25)
336 (23)
317 (22)
304 (21)
293 (20)
269 (19)
251 (17)
270 (19)
(66°C)
775 (53)
662 (46)
613 (42)
537 (37)
495 (34)
420 (29)
373 (26)
347 (24)
309 (21)
285 (20)
270 (19)
258 (18)
249 (17)
229 (16)
213 (15)
230 (16)
(95°C)
729 (50)
623 (43)
577 (40)
505 (35)
466 (32)
395 (27)
351 (24)
327 (23)
291 (20)
269 (19)
254 (17)
243 (17)
235 (16)
215 (15)
201 (14)
216 (15)
Water Temperature Range
(120°C)
729 (50)
623 (43)
577 (40)
505 (35)
466 (32)
395 (27)
351 (24)
327 (23)
291 (20)
269 (19)
254 (17)
243 (17)
235 (16)
215 (15)
201 (14)
216 (15)
(149°C)
714 (49)
610 (42)
565 (39)
495 (34)
456 (31)
387 (26)
344 (23)
320 (22)
285 (20)
263 (18)
248 (17)
238 (16)
230 (16)
211 (15)
196 (14)
212 (15)
(177°C)
608 (42)
519 (36)
481 (33)
421 (29)
388 (27)
330 (23)
293 (20)
272 (19)
242 (17)
224 (15)
211 (15)
202 (14)
196 (13)
179 (12)
167 (12)
180 (12)
(204°C)
456 (31)
389 (27)
361 (25)
316 (21)
291 (20)
247 (17)
219 (15)
204 (14)
182 (13)
168 (12)
159 (11)
152 (10)
147 (10)
135 1 (9)
125 1 (8)
135 1 (9)
1 The fitting pressure rating applies to the largest opening of the fitting.
RATED INTERNAL WORKING PRESSURES OF
CAST COPPER ALLOY FLANGES AND FLANGED FITTINGS
Nominal Size Joint
(In Inches)
1/2, 3/4, 1, 1 1/4,
1 1/2, 2, 2 1/2,
3, 4, 5, 6, 8
(also 10" for
Class 125)
Temperature
°F (°C) A
0 – 150 (0 – 66)
175 1 (79)
200 1 (93)
225 (107)
250 (121)
275 (135)
300 (149)
350 (177)
406 (208)
Class 125 A, B
105 (7)
100 (7)
1 95 (7)
1 90 (6)
1 90 (6)
1 85 (6)
1 85 (6)
1 75 (5)
1 70 (5)
Pressure (PSI)
Class 150 B
210 (14)
205 (14)
195 (13)
190 (13)
180 (12)
175 (12)
170 (12)
150 (10)
140 1 (9)
A MSS SP-106
B ASTM B584, UNS C83800 and UNS C84400
C ASTM B62, UNS C83600 and ASTM B584, UNS C83600
Class 150 A, C
225 (15)
220 (15)
210 (15)
205 (14)
195 (13)
190 (13)
180 (12)
165 (11)
150 (10)
U.S. customary units in this document are the standard; the metric units are provided for reference only. The values stated in each system are not exact equivalents.
Visit our website for the most current information.
42
NIBCO INC. WORLD HEADQUARTERS • 1516 MIDDLEBURY ST. • ELKHART, IN 46516-4740 • USA • PH: 1.800.234.0227
TECH SERVICES PH: 1.888.446.4226 • FAX: 1.888.234.0557 • INTERNATIONAL OFFICE PH: +1.574.295.3327 • FAX: +1.574.295.3455
www.nibco.com
www.nibco.com
A H E A D O F T H E F L O W
®
Copper Fittings
Dimensional Data
The mechanics of making both the solder joint and the brazing joint are comparatively similar. Complete instructions on proper techniques of both of these joining methods are outlined in this catalog on pages 46-48.
A very important consideration in Copper Piping is the selection of the proper bonding medium. As a general rule, the working temperature of the installation is a more important consideration than the working pressures. If the working temperature is not over
250°F (121°C), either 50-50%* or 95-5% solder can be used successfully. However, if the temperature exceeds 250°F (121°C), a low temperature brazing alloy should be used, with a melting temperature somewhat in excess of 1000°F (538°C).
According to BMS report No. 58, joints made with tin or tin-alloy solders should not be subject continuously to temperatures above
250°F (121°C). A number of brazing alloys are available and a careful study should be made in every case to determine the proper alloy for the particular application.
* The Safe Drinking Water Act Amendment of 1986 prohibits the use in potable water systems of any solder having a lead content in excess of 0.2%.
DIMENSIONAL DATA – SOLDER JOINT FITTING ENDS
Nominal
Tube
Solder Joint Fittings – Tolerances
Male End (Fitting Connector)
Diameter
Female End (Solder Cup)
Diameter
Solder Joint Fittings
Copper Alloy – Pressure 1, 2
Solder Joint Fittings
Copper Alloy – Drainage 3, 4
Fitting End Length Solder Cup Length Fitting End Length Solder Cup Length
Min. Max. Min. Max. Min. Min. Min. Min.
1/8
1/4
3/8
1/2
5/8
3/4
1
0.248 (6.30) 0.251 (6.38) 0.252 (6.40) 0.256 (6.50) 0.31 (7.9) 0.25 (6.4) N/A N/A N/A N/A
0.373 (9.47) 0.376 (9.55) 0.377 (9.58) 0.381 (9.68) 0.38 (9.7) 0.31 (7.9) N/A N/A N/A N/A
0.497 (12.62) 0.501 (12.73) 0.502 (12.75) 0.506 (12.85) 0.44 (11.2) 0.38 (9.7) N/A N/A N/A N/A
0.622 (15.80) 0.626 (15.90) 0.627 (15.93) 0.631 (16.03) 0.56 (14.2) 0.50 (12.7) N/A N/A N/A N/A
0.747 (18.97) 0.751 (19.08) 0.752 (19.10) 0.756 (19.20) 0.69 (17.5) 0.62 (15.7) N/A N/A N/A N/A
0.872 (22.15) 0.876 (22.25) 0.877 (22.28) 0.881 (22.38) 0.81 (20.6) 0.75 (19.1) N/A N/A N/A N/A
1.122 (28.50) 1.127 (28.63) 1.128 (28.65) 1.132 (28.75) 0.97 (24.6) 0.91 (23.1) N/A N/A N/A N/A
2 2.121
2 2.621 (66.57) 2.627 (66.73) 2.628 (66.75) 2.633 (66.88) 1.53 (38.9) 1.47 (37.3) N/A N/A N/A N/A
3 3.121
3 3.621 (91.97) 3.627 (92.13) 3.628 (92.15) 3.633 (92.28) 1.97 (50.0) 1.91 (48.5) N/A N/A N/A N/A
4 4.121
5 5.121
6 6.121
8
10
12
8.119 (206.22) 8.127 (206.43) 8.128 (206.45) 8.133 (206.58) 4.09 (103.9) 3.97 (100.8) 2.12 (53.8) 2.00 (50.8)
10.119 (257.02) 10.127 (257.23) 10.128 (257.25) 10.133 (257.38) 4.12 (104.6) 4.00 (101.6) N/A
12.119 (307.82) 12.127 (308.03) 12.128 (308.05) 12.133 (308.18) 4.62 (117.3) 4.50 (114.3) N/A
N/A
N/A
N/A
N/A
N/A
N/A
1 As shown Standard ASME B16.18
2 As shown Standard ASME B16.22
3 As shown Standard ASME B16.23
4 As shown Standard ASME B16.29
Visit our website for the most current information.
U.S. customary units in this document are the standard; the metric units are provided for reference only. The values stated in each system are not exact equivalents.
NIBCO INC. WORLD HEADQUARTERS • 1516 MIDDLEBURY ST. • ELKHART, IN 46516-4740 • USA • PH: 1.800.234.0227
TECH SERVICES PH: 1.888.446.4226 • FAX: 1.888.234.0557 • INTERNATIONAL OFFICE PH: +1.574.295.3327 • FAX: +1.574.295.3455
www.nibco.com
43
www.nibco.com
DIMENSIONAL DATA – BRAZING FITTING ENDS
Male End (Fitting Connector) Diameter
Nominal
Water Tube
Inches)
Female End (Brazing Cup) Diameter Fitting End
Length
Solder Cup
Length
3/8 0.497 (12.62) 0.501 (12.73) 0.502 (12.75) 0.506 (12.85) 0.26
1/2 0.622 (15.80) 0.626 (15.90) 0.627 (15.93) 0.631 (16.03) 0.28
5/8 0.747 (18.97) 0.751 (19.08) 0.752 (19.10) 0.756 (19.20) N/A
3/4 0.872 (22.15) 0.876 (22.25) 0.877 (22.28) 0.881 (22.38) 0.31
1 1.122 (28.50) 1.127 (28.63) 1.128 (28.65) 1.132 (28.75) 0.34
1/4 1.372 (34.85) 1.377 (34.98) 1.378 (35.00) 1.382 (35.10) 0.37
1/2 1.621 (41.17) 1.627 (41.33) 1.628 (41.35) 1.633 (41.48) 0.40
2 2.121 (53.87) 2.127 (54.03) 2.128 (54.05) 2.133 (54.18) 0.47
1/2 2.621 (66.57) 2.627 (66.73) 2.628 (66.75) 2.633 (66.88) 0.53
3 3.121 (79.27) 3.127 (79.43) 3.128 (79.45) 3.133 (79.58) 0.59
1/2 3.621 (91.97) 3.627 (92.13) 3.628 (92.15) 3.633 (92.28) 0.65
4 4.121 (104.67) 4.127 (104.83) 4.128 (104.85) 4.133 (104.98) 0.72
5 5.121 (130.07) 5.127 (130.23) 5.128 (130.25) 5.133 (130.38) 0.81
6 6.121 (155.47) 6.127 (155.63) 6.128 (155.65) 3.133 (79.58) 0.94
8 8.119 (206.22) 8.127 (206.43) 8.128 (206.45) 8.133 (206.58) 1.28
10 10.119 (257.02) 10.127 (257.23) 10.128 (257.25) 10.133 (257.38) N/A N/A N/A N/A
12 12.119 (307.82) 12.127 (308.03) 12.128 (308.05) 12.133 (308.18) N/A N/A N/A N/A
1 In accordance with MS SP-73
U.S. customary units in this document are the standard; the metric units are provided for reference only. The values stated in each system are not exact equivalents.
Visit our website for the most current information.
44
NIBCO INC. WORLD HEADQUARTERS • 1516 MIDDLEBURY ST. • ELKHART, IN 46516-4740 • USA • PH: 1.800.234.0227
TECH SERVICES PH: 1.888.446.4226 • FAX: 1.888.234.0557 • INTERNATIONAL OFFICE PH: +1.574.295.3327 • FAX: +1.574.295.3455
www.nibco.com
www.nibco.com
A H E A D O F T H E F L O W
®
EXPANSION AND CONTRACTION
In the majority of low-pressure heating systems employing copper tube and installed in small houses or private dwellings, provision for expansion and contraction is relatively simple. Mains, risers, and branches to radiators should be free or floating at one end of the line. Holes should be large enough to permit free movement of the tube, and care should be exercised so that pipe hangers and supports permit unrestricted movement and do not anchor the tube.
Wrought copper tube hangers that are both practicable and neat in appearance are available.
Unusually long runs of copper tubing should be provided with an expansion bend or loop. By bending soft temper copper tube, a simple form of expansion loop can be made. With the addition of combination flared-tube to solder joint fittings, as illustrated in
Figure 1, these types of loops can be used when space or other limitations exist. The correct proportions of such expansion loop to meet various conditions are shown in the accompanying table.
FIGURE 1 a. U-Bend b. Coiled Loop
The above chart is calculated using 10ft (3.05m) of copper tubing as the reference point. You may use it as follows: 100ft (30.5m) of copper tube, with a 200°F (93.3°C) temperature change. Reference point .2256 inches for 10ft, (5.73mm for 3.05m), multipy by 10 for
100ft (30.5m), resulting in an answer of 2.256 inches (57.3mm) of expansion or contraction.
NOTE: Calculations for expansion and contraction should be based on the average coefficient of expansion of copper which is
0.0000094 per °F (0.00001692 per °C) between 77°F and 212°F
(25°C and 100°C). For example, the expansion for each 10ft (3.05m) of any size of tube heated from room temperature of 70°F (21.1°C) to
170°F (76.7°C), that is, 100°F (55.6°C) rise, is:
Rise Coefficient
100°F 10ft 12 inches 0.000094 0.1128 in.
(55.6°C) (3.05m) (1000mm) (0.00001692) (2.87mm) c. Offset and
Return
RADII OF COILED EXPANSION LOOPS AND DEVELOPED LENGTHS OF EXPANSION OFFSETS
Expected Expansion
Nominal
Tube R L R L R L R L R L R L R L R L
Size Inch (mm) Inch (mm) Inch (mm) Inch (mm) Inch (mm) Inch (mm) Inch (mm) Inch (mm) Inch (mm) Inch (mm) Inch (mm) Inch (mm) Inch (mm) Inch (mm) Inch (mm) Inch (mm)
1/4
3/8
1/2
3/4
1
1 1/2
2
2 1/2
6 (152.4) 38 (965.2) 9 (228.6) 54 (1371.6) 11 (279.4) 66 (1676.4) 12 (304.8) 77 (1955.8) 14 (355.6)
7 (177.8) 44 (1117.6) 10 (254.0) 63 (1600.2) 12 (304.8) 77 (1955.8) 14 (355.6) 89 (2260.6) 16 (406.4)
8 (203.2) 50 (1270.0) 11 (279.4) 70 (1778.0) 14 (355.6) 89 (2260.6) 16 (406.4) 99 (2514.6) 18 (457.2)
9 (228.6) 59 (1498.6) 13 (330.2) 83 (2108.2) 16 (406.4) 101 (2565.4) 19 (482.6) 117 (2971.8) 21 (533.4)
11 (279.4) 67 (1701.8) 15 (381.0) 94 (2387.6) 18 (457.2) 115 (2921.0) 21 (533.4) 133 (3378.2) 24 (609.6)
13 (330.2) 80 (2032.0) 18 (457.2) 113 (2870.2) 22 (558.8) 138 (3505.2) 25 (635.0) 160 (4064.0) 29 (736.6)
15 (381.0) 91 (2311.4) 21 (533.4) 129 (3276.6) 25 (635.0) 158 (4013.2) 29 (736.6) 183 (4648.2) 33 (838.2)
16 (406.4) 102 (2590.8) 23 (584.2) 144 (3657.6) 28 (711.2) 176 (4470.4) 32 (812.8) 203 (5156.2) 36 (914.4)
3 18 (457.2) 111 (2819.4) 25 (635.0) 157 (3987.8) 30 (762.0) 191 (4851.4) 35 (889.0) 222 (5638.8) 40 (1016.0)
3 1/2 19 (482.6) 120 (3048.0) 27 (685.8) 169 (4292.6) 33 (838.2) 206 (5232.4) 38 (965.2) 239 (6070.6) 43 (1092.2)
4
5
20 (508.0) 128 (3251.2) 29 (736.6) 180 (4572.0) 35 (889.0) 220 (5588.0) 41 (1041.4) 255 (6477.0) 45 (1143.0)
23 (584.2) 142 (3606.8) 32 (812.8) 201 (5105.4) 39 (990.6) 245 (6223.0) 45 (1143.0) 284 (7213.6) 51 (1295.4)
99 (2514.6) 17 (431.8) 109 (2768.6) 19 (482.6) 117 (2971.8) 20 (508.0) 126 (3200.4)
111 (2819.4) 19 (482.6) 122 (3098.8) 21 (533.4) 131 (3327.4) 22 (558.8) 140 (3556.0)
131 (3327.4) 23 (584.2) 143 (3632.2) 25 (635.0) 155 (3937.0) 26 (660.4) 166 (4216.4)
149 (3784.6) 26 (660.4) 163 (4140.2) 28 (711.2) 176 (4470.4) 30 (762.0) 188 (4775.2)
179 (4546.6) 31 (787.4) 196 (4978.4) 34 (863.6) 212 (5384.8) 36 (914.4) 226 (5740.4)
205 (5207.0) 36 (914.4) 224 (5689.6) 39 (990.6) 242 (6146.8) 41 (1041.4) 259 (6578.6)
227 (5765.8) 40 (1016.0) 249 (6324.6) 43 (1092.2) 269 (6832.6) 46 (1168.4) 288 (7315.2)
248 (6299.2) 43 (1092.2) 272 (6908.8) 47 (1193.8) 293 (7442.2) 50 (1270.0) 314 (7975.6)
267 (6781.8) 47 (1193.8) 293 (7442.2) 50 (1270.0) 316 (8026.4) 54 (1371.6) 338 (8585.2)
285 (7239.0) 50 (1270.0) 312 (7924.8) 54 (1371.6) 337 (8559.8) 57 (1447.8) 361 (9169.4)
318 (8077.2) 55 (1397.0) 348 (8839.2) 60 (1524.0) 376 (9550.4) 64 (1625.6) 402 (10210.8)
Visit our website for the most current information.
U.S. customary units in this document are the standard; the metric units are provided for reference only. The values stated in each system are not exact equivalents.
NIBCO INC. WORLD HEADQUARTERS • 1516 MIDDLEBURY ST. • ELKHART, IN 46516-4740 • USA • PH: 1.800.234.0227
TECH SERVICES PH: 1.888.446.4226 • FAX: 1.888.234.0557 • INTERNATIONAL OFFICE PH: +1.574.295.3327 • FAX: +1.574.295.3455
www.nibco.com
45
advertisement