advertisement
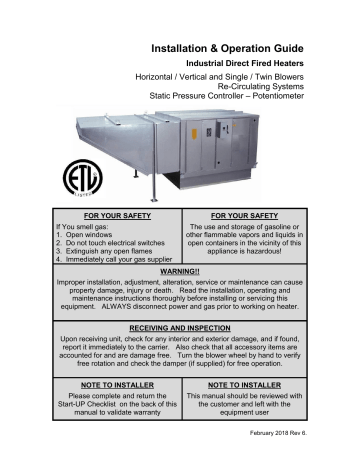
START-UP PROCEDURE 80/20
Check for signs of damage. Do not operate if damage exists and contact your manufacture ’s sales representative. Units are easier to fix before the equipment is installed.
Check all installation clearances.
Clearance from Combustibles
Top: 6” Sides: 6” Base: 0”
Clearance for Serviceability
Unit: 24” Service Accesses: 48”
Check that the unit has been set level and secured.
Unit must have adequate structural support or the equipment or building may be damaged.
Curb and unit must be leveled or the unit may leak or be damaged.
Gasket and caulk the seam between the curb and unit base
Screw or weld the unit’s base to the curb to avoid damage to the equipment.
Check that the accessories are set level and secured.
Accessories must have adequate structural support or the equipment or building may be damaged
Gasket, caulk, and screw each accessory to unit seam
Check that the unit’s intake and discharge are free of debris
Check that the filters are installed in the (optional) filter section of the intake hood in accordance to the air flow direction
Check that the unit’s ductwork size and length match the minimum ductwork size chart
Check that all field wiring has been completed in accordance to the factory supplied wiring diagram
Field wires are shown as dashed lines on the wiring prints
Check that all terminal screws are tight and that wires are in place
Check pulley alignment. Correct if necessary
Check that the power supply matches the nameplate voltage, phase, and amperage
Record the voltage on the Start-Up Sheet
Check that the gas type and pressure matches the nameplate type and pressure
Check that the gas type and pressure matches the nameplate type and pressure
Contact the service department if the power or gas supply needs to be changed in the field. Different parts might be necessary for the change
Turn the Summer Off Winter switch to OFF
Set the Maxitrol Set-Point to the maximum
Turn the main power disconnect ON
Bump the blower motor starter to check the blower wheel rotation
The decal is located on the blower housing
If the rotation is backwards, turn off the power and correct the wiring
The rotation can be corrected by interchanging two legs of 3 phase power on the disconnect or blower motor start contactor
SOW SWITCH
MAXITROL
SET-POINT
DIAL
18
Turn the blower service switch ON. The
(optional) intake or discharge damper motor will start to open. Once the damper is 70% open the damper motor internal end switch will close and energize the blower motor starter.
Check that the motor amp draw is less than the FLA (full load amps) of the blower motor.
The fan RPM may need to be
BLOWER
SERVICE
SWITCH reduced to decrease motor amps.
Opening the driver pulley decreases
RPM and motor amps.
Closing the driver pulley increases
RPM and motor amps.
Record the motor amps on the Start-
Up Sheet.
If the RPM was adjusted in the field use a tachometer to record the new RPM on the
Start-Up Sheet.
Check the belt tension after any RPM adjustments. See the belt tension detail.
Operate unit at design RPM and 100% outdoor air. Check the air flow pressure drop in 100% fresh air and re-circulating mode. Use the recirculating damper motor control to switch the unit between modes.
The damper is controlled by one of the following control options;
Manual Switch – Potentiometer - Photohelic
This will ensure the proper pressure drop across the burner profile.
The air flow switch on the re-circulating units is a low and high air flow switch and opens below
0.15 in w.c. and above 0.95 in w.c.
The target pressure drop range for the re-circulating unit is 0.40-0.60 w.c. at 70°F. If the ambient air temperature is less than 60°F, operate the burner at a discharge temperature of 70 degrees while measuring pressure drop.
Use the profile plates or blower RPM to increase or decrease the pressure drop.
Record the pressure drops on the Start-Up Sheet.
If the pressure drop is too low, in fresh and return air mode, add more blank-off panels to the burner profile opening and bypass fresh air and return air damper, which will increase the pressure drop. (There must be at least 2 inches of area minimum around the burner.) If the correct air flow pressure drop is still not achieved adjust the blower drives to increase the blowers RPM.
If the pressure drop is too high, in fresh mode only, remove or adjust the bypass damper blankoff panels, which will decrease the pressure drop. The return air damper opening may need to be adjusted to maintain the correct air flow pressure drop when switching back to return air mode.
If the pressure drop is too high, in fresh and return air mode, remove or adjust the bypass fresh air and return air damper blank-off panels, which will decrease the pressure drop. If the correct air flow pressure drop is still not achieved adjust the blower drives to decrease the blowers RPM.
If the pressure drop is too high, in fresh and return air mode, remove or adjust the bypass fresh air and return air damper blank-off panels, which will decrease the pressure drop. If the correct air flow pressure drop is still not achieved adjust the blower drives to decrease the blowers RPM.
19
Close the burner gas shut off valve
This will allow the unit to fire the pilot only and will be opened at a later time
CLOSE VALVE
Set the Burner Intake On Off Switch above the outside air temperature
SET DIAL 10
DEGREES ABOVE
OUTDOOR TEMP
Turn the burner service switch ON
BURNER SERVICE
SWITCH
The Fireye Flame Safety Control energizes the ignition transformer and pilot gas valve
After the pilot flame is established, the main gas valves will open
At this time the pilot will be the only flame in the burner
The pilot regulator should be adjusted so the pilot flame signal is above 15 VDC
PILOT REGULATOR
Use the DC terminals under the Fireye cover to read the pilot flame signal
This will ensure that the unit will start in cold damp weather with a strong pilot flame signal
- +
POSITIVE TERMINAL
NEGATIVE TERMINAL
Record the pilot flame signal in the Start-Up Sheet
Record the low and high fire flame signal on the Start-Up Sheet
20
Setting High Fire
– Discharge Temp Method
Open the Burner Gas Shut Off Valve
OPEN VALVE
Measure the intake air temperature.
Add the intake air temperature to the unit ’s nameplate design temperature rise.
This result will be the desired high fire discharge temperature.
Example: Intake Temp 70 F
Design Temp Rise 72 F
Discharge Temp 142 F
GAS TYPE: NATURAL
MAX. TEMP. RISE: 140 F
DESIGN TEMP. RISE: 72 F
MAX. DISCHARGE TEMP.: 80
F
Use the Maxitrol Amplifier to override the heater into high fire.
On the A1014 amplifier remove the #4 wire
On the A1044 amplifier remove the #2 and
#4 wire
On the M-Series adjust the set-point to be
160 F
Adjust the manifold gas pressure to achieve the desired discharge air temperature.
See the details for the high fire pressure adjustment locations.
On manifolds with an MR212 modulation valve, adjust the small regulator inside the
MR212 modulation valve
On manifolds with either an M511 or M611 modulation valve, adjust the regulator located before the main gas valves
On manifolds with a combination gas valve, adjust the regulator under the brass cap on the combination gas valve.
Measure the discharge temperature using a thermometer. Laser thermometers are not as accurate as a thermocouple type.
If the discharge ductwork outlet is hard to reach, you may feed a thermocouple into the mixing tube inside the blower discharge.
HIGH FIRE
MR212
HIGH FIRE
M511 & M611
21
Setting High Fire
– Manifold Pressure Method
GAS TYPE: NATURAL
MAX. TEMP. RISE: 140 F
DESIGN TEMP. RISE: 72 F
MAX. DISCHARGE TEMP.: 80
F
Turn the burner service switch ON
Open the Burner Gas Shut Off Valve
OPEN VALVE
Use the Maxitrol Amplifier to override the heater into high fire.
On the A1014 amplifier remove the #4 wire
On the A1044 amplifier remove the #2 and #4 wire
On the M-Series adjust the set-point to be 160 F
Adjust the manifold gas pressure to achieve the desired manifold pressure
See the details for the high fire pressure adjustment locations.
On manifolds with an MR212 modulation valve, adjust the small regulator inside the MR212 modulation valve
On manifolds with either an M511 or M611 modulation valve, adjust the regulator located before the main gas valves
On manifolds with a combination gas valve, adjust
HIGH FIRE
MR212
HIGH FIRE
M511 & M611
the regulator under the brass cap on the combination gas valve.
The manifold pressure can be read at the 1/4” pressure tap located after the modulating gas valve.
22
Setting Low Fire
Use the Maxitrol amplifier to override the heater into low fire.
Remove the 24V power source from amplifier
Adjust the low fire setting on the modulation valve so the flame is 2-3 inches without dark spots
See the details for the low fire pressure adjustment locations
Use the burner observation port on the end of the unit to view the flame size
Replace all amplifier wires in the place they were removed to set high and low fire
Additional capacity is provided via a low fire bypass when
MR212 low fire capacity is insufficient. Additional adjustment is made via the R400S regulator installed in the low fire bypass.
LOW FIRE
MR212
M511 & M611
LOW FIRE
Final Start-Up
Set the Burner Intake On-Off Thermostat to the desired setting
This will automatically open the burner circuit when the outside air is above the selected temperature
Turn the blower and burner service switches OFF
Now the unit will be operated from the control panel only
Operate the unit from the remote panel checking the lights, switches, set-points, and optional thermostats or timers
Review the proper operation and sequence of operation with the customer to ensure that the unit is operated properly and that the customer does not misuse the equipment
Complete the Start-Up Sheet and fax it to the service department to validate the warranty
Start-Up Complete
23
advertisement
Related manuals
advertisement
Table of contents
- 3 WARRANTY
- 3 INSTALLATION
- 10 Gas Connection Diagram
- 11 Electrical
- 11 Copper Wire Ampacity
- 12 Variable Frequency Drive (VFD) Installation Instructions
- 14 Re-Circulating Damper Control Options
- 16 SEQUENCE OF OPERATIONS
- 16 – 80/20 Static Pressure Controller
- 17 – 80/20 Manual Potentiometer
- 18 START-UP PROCEDURE
- 24 AIR BALANCING
- 26 TEMPERATURE CONTROL SYSTEMS
- 27 UNIT COMPONENTS
- 27 M4RT1 Flame Safety Control
- 27 DC Flame Signal
- 28 Air Flow Switch
- 28 Modulating Gas System
- 28 High Temperature Limit
- 28 Electric Cabinet Heater
- 30 TROUBLESHOOTING
- 42 General Maintenance
- 43 Burner Orifice Drill Size
- 44 START-UP CHECKLIST