- No category
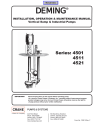
advertisement
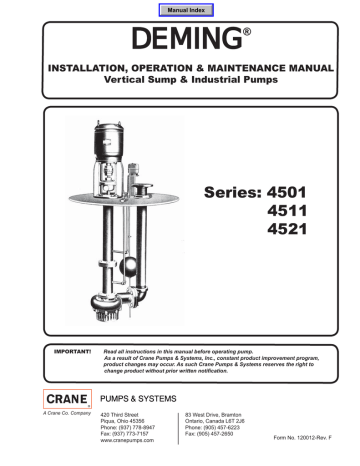
SAFETY FIRST!
Please Read This Before Installing Or Operating Pump. This information is provided for SAFETY and to PREVENT EQUIPMENT
PROBLEMS. To help recognize this information, observe the following symbols:
IMPORTANT! Warns about hazards that can result in personal injury orIndicates factors concerned with assembly, installation, operation, or maintenance which could result in damage to the machine or equipment if ignored.
CAUTION! Warns about hazards that can or will cause minor personal injury or property damage if ignored. Used with symbols below.
WARNING! Warns about hazards that can or will cause serious personal injury, death, or major property damage if ignored. Used with symbols below.
Hazardous fl uids can cause fi re or explosions, burnes or death could result.
Extremely hot - Severe burnes can occur on contact.
Biohazard can cause serious personal injury.
Hazardous fl uids can Hazardous pressure, eruptions or explosions could cause personal injury or property damage.
Rotating machinery
Amputation or severe laceration can result.
Hazardous voltage can shock, burn or cause death.
pump. Any wiring of pumps should be performed by a qualifi ed electrician.
WARNING ! To reduce risk of electrical shock, pumps and control panels must be properly grounded in accordance with the National Electric Code (NEC) or the Canadian
Electrical Code (CEC) and all applicable state, province, local codes and ordinances. Improper grounding voids warranty.
WARNING! To reduce risk of electrical shock, always disconnect the pump from the power source before handling or servicing. Lock out power and tag.
WARNING! Operation against a closed discharge valve will cause premature bearing and seal failure on any pump, and on end suction and self priming pump the heat build may cause the generation of steam with resulting dangerous pressures. It is recommended that a high case temperature switch or pressure relief valve be installed on the pump body.
CAUTION ! Never operate a pump with a plug-in type power cord without a ground fault circuit interrupter.
CAUTION ! Pumps build up heat and pressure during operation-allow time for pumps to cool before handling or servicing.
WARNING ! Do not pump hazardous materials
(fl ammable, caustic, etc.) unless the pump is specifi cally designed and designated to handle them.
CAUTION ! Do not block or restrict discharge hose, as discharge hose may whip under pressure.
WARNING ! Do not wear loose clothing that may become entangled in moving parts.
WARNING ! Keep clear of suction and discharge openings. DO NOT insert fi ngers in pump with power connected.
Always wear eye protection when working on pumps.
Make sure lifting handles are securely fastened each time before lifting. DO NOT operate pump without safety devices in place. Always replace safety devices that have been removed during service or repair. Secure the pump in its operating position so it can not tip over, fall or slide.
DO NOT exceed manufacturers recommendation for maximum performance, as this could cause the motor to overheat.
DO NOT remove cord and strain relief. DO NOT connect conduit to pump.
WARNING ! Cable should be protected at all times to avoid punctures, cut, bruises and abrasions. Inspect frequently. Never handle connected power cords with wet hands.
WARNING ! To reduce risk of electrical shock, all wiring and junction connections should be made per the NEC or CEC and applicable state or province and local codes. Requirements may vary depending on usage and location.
WARNING! Submersible Pumps are not approved for use in swimming pools, recreational water installations decorative fountains or any installation where human contact with the pumped fl uid is common.
WARNING! Products returned must be cleaned, sanitized, or decontaminated as necessary prior to shipment, to insure that employees will not be exposed to health hazards in handling said material. All Applicable
Laws And Regulations Shall Apply.
Bronze/brass and bronze/brass fi tted pumps may contain lead levels higher than considered safe for potable water systems. Lead is known to cause cancer and birth defects or other reproductive harm. Various government agencies have determined that leaded copper alloys should not be used in potable water applications. For non-leaded copper alloy materials of construction, please contact factory.
Crane Pumps & Systems, Inc. is not responsible for losses, injury, or death resulting from a failure to observe these safety precautions, misuse or abuse of pumps or equipment.
3
A - GENERAL INFORMATION
TO THE PURCHASER:
Congratulations! You are the owner of one of the fi nest pumps on the market today. These pumps are products engineered and manufactured of high quality components.
With years of pump building experience along with a continuing quality assurance program combine to produce a pump which will stand up to the toughest applications.
Check local codes and requirements before installation.
Servicing should be performed by knowledgeable pump service contractors or authorized service stations.
b.) Slide a locking collar onto the top end of the rod and push rod through fl oat switch arm. Guide the bottom end of the rod through the bottom guide bracket (527) on the pump casing (1) and lock a collar on the end of the rod by tightening the collar set screw.
c.) Lock the collar on the rod below the fl oat about
4” above the bottom guide bracket, then lock the collar above the fl oat at the desired starting (or stopping) level in the sump.
d.) After setting the pump in the pit, push the fl oat switch arm down to its lowest position. Lift the fl oat rod about 1/2” and fasten the top collar on rod with collar resting on switch arm. Lock the last collar 1/2” below the switch arm.
NOTE: See fl oat assembly on page 10
This pump is designed for pumping raw or treated sewage, light sludge, slurries, industrial wastes and similar liquids containing solids. Standard pumps are assembled, adjusted and lubricated at the factory before shipment.
Motor and fl exible shaft coupling are normally shipped unmounted and are to be installed on the pump at job site.
2. Carefully lower the assembled unit into the pit. The support plate (23) should be approximately level and must rest evenly at all points before it is bolted to the
RECEIVING:
Upon receiving the pump, it should be inspected for damage or shortages. If damage has occurred, fi le a claim immediately with the company that delivered the pump.
If the manual is removed from the crating, do not lose or misplace.
STORAGE:
Short Term - Pumps are manufactured for effi cient performance following long inoperative periods in storage.
For best results, pumps can be retained in storage, as factory assembled, in a dry atmosphere with constant temperatures for up to six (6) months.
B - INSTALLATION
Standard pumps are completely assembled, carefully adjusted and lubricated at the factory before shipment.
3. Turn pump shaft by hand to make sure that it rotates freely after installation - but before turning on the power. If there is a bind in the rotation, make 4 checks and possible adjustments as follows:
A. Adjust the position of the impeller by loosening
(342) lock screw, loosen or tighten (66) adjusting nut to position the shaft and impeller above their lowest position by from 1/3 to 1/2 turn of the
Long Term - Any length of time exceeding six (6) months, but not more than twenty four (24) months. The units should be stored in a temperature controlled area, a roofed over walled enclosure that provides protection from the elements (rain, snow, wind blown dust, etc..), and whose temperature can be maintained between +40 deg. F and
+120 deg. F. Pump should be stored in its original shipping container and before initial start up, rotate impeller by hand to assure seal and impeller rotate freely.
SERVICE CENTERS:
For the location of the nearest Deming Service Center, check your Deming representative or Crane Pumps &
Systems Service Department in Piqua, Ohio, telephone
(937) 778-8947 or Crane Pumps & Systems Canada, Inc.,
Bramton, Ontario, (905) 457-6223.
B. If “A” does not correct binding, loosen top lock nuts
(294) of both the discharge pipe and the grease pipe (if furnished) by two or three turns. Then gradually tighten discharge pipe top lock nut while checking shaft until the maximum shaft freedom of rotation is attained.
C. If “B” does not free shaft, raise the pump out of the pit and lower the bottom lock nuts of the discharge and lubrication pipes. Then reset the pump, bolting it to its foundation and continue to tighten the top lock nut of the discharge pipe up to 1 or 2 turns until freedom of rotation is attained.
D. Tighten the lubrication pipe top lock nut to just bear on the pump plate, raise the pump out of the sump, tighten the bottom lock nuts of the discharge and lubrication pipes and reset the pump.
E. Recheck the freedom of shaft rotation.
F. Disengage motor half coupling (42) from pump half coupling.
4. Eliminate weight or strain of the piping connected to the pump before connecting this piping to the pump.
Recheck freedom of rotation (Section 3) after connecting system piping to pump discharge. A check valve and gate valve should be installed at the pump discharge to prevent back wash and pump back
spin.
assembled and partially adjusted before installing the pump. Insert plate and slide a locking collar (530) on the bottom of the rod,
5. Be certain to connect power lines to motor leads as shown on motor wiring diagram for the line voltage
(530).
4
advertisement
* Your assessment is very important for improving the workof artificial intelligence, which forms the content of this project
Related manuals
advertisement
Table of contents
- 3 SAFETY FIRST
- 5 INSTALLATION
- 5 FOR INSPECTION AND REPAIR OF LIQUID END
- 6 TO REMOVE TOP COLUMN ADAPTER
- 6 INSTALLING NEW BEARING BUSHINGS
- 6 REASSEMBLY OF COLUMN PIPE
- 6 ASSEMBLY OF LIQUID END
- 7 TO INSPECT OR REPLACE THRUST BEARING AND SEAL
- 9 GUIDE BEARING ASSEMBLY
- 11 CROSS-SECTION & PARTS LIST
- 15 WARRANTY & RETURNED GOODS