advertisement
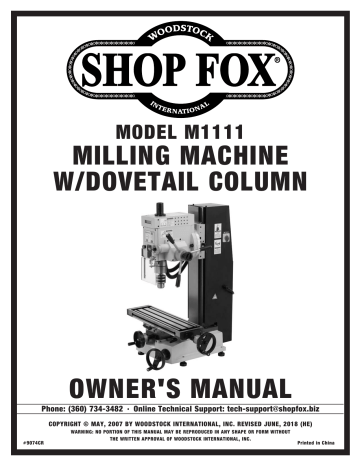
M1111 Mill with Dovetail Column
SERVICE
Troubleshooting
The following troubleshooting tables cover common problems that may occur with this machine. If you need replacement parts or additional troubleshooting help, contact our Technical Support. Note:
Before contacting Tech Support, find the machine serial number and manufacture date, and if available, your original purchase receipt. This information is required to properly assist you.
General Operation PROBLEM
Motor will not start. Feed handle tapping button does not work.
Control panel FORWARD and REVERSE buttons do not work.
POSSIBLE CAUSE
1. Control system delay operating.
2. Shop power supply is at fault.
3. Chip guard switch at fault (
Figure 37
).
4. Blown inverter fuse (
Figure 34
).
5. Blown power supply fuse (
Figure 35
).
6. Emergency stop button is pressed.
7. Main power switch at fault (
Figure 35
). 8. Shorted capacitor (
Figure 34
).
9. Shorted inverter (
Figure 34
).
10. Loose connections, open wiring.
11. Motor is at fault.
1. Machine is not in "
Tapping Mode
."
CORRECTIVE ACTION
1. Push and hold the START button for 2-sec onds or until a beep is heard, a quick tap of the finger will not start the mill or oper ate controls.
2. Correct any shop power supply problems causing breakers or fuses to trip and reconnect mill to power supply.
3. Fully close chip guard, or replace bad switch.
4. Repair for cause of short and replace 20A fuse.
5. Repair for cause of short and replace 20A fuse.
6. Reset switch or replace bad switch.
7. Turn dial on, or replace bad switch.
8. Replace capacitor.
9. Replace inverter unit.
10. Inspect wiring connections, plugs, and repair/replace as required ( required (
Page 32
).
Page 32
). 11. Inspect motor and repair/replace as 1. Press the START and then the TAPPING but ton (
Page 19
).
2. Replace tapping button slip ring switch.
2. Tapping button slip ring switch is at fault (
Figure 37
).
3. General electrical problem.
1. Machine is not in "
Milling Mode
2. General electrical problem.
." 3. Inspect circuit boards, wiring connections, plugs, and repair/replace as required (
Page 32
). 1. Holding for 2-seconds each or until a beep is heard, press the STOP and then the START buttons (
Page 19
).
2. Inspect circuit boards, wiring connections, plugs, and repair/replace as required (
Page 32
). -27-
Milling Operation and Finish Results PROBLEM
Poor surface finishes.
POSSIBLE CAUSE
1. Feed rate too fast.
2. Dull or bent cutter.
3. Spindle speed incorrect.
4. Lock lever(s) loose.
5. Spindle is extended too far down.
Vibration when running or cutting.
6. Gibs loose.
1. Feed rate too high.
2. Spindle is extended too far down.
Headstock hard to raise.
3. Loose table.
4. Loose gibs.
1. Headstock lock or gib is at fault.
2. Dovetail is binding.
3. Headstock lead screw is binding.
M1111 Mill with Dovetail Column
CORRECTIVE ACTION
1. Slow feed rate.
2. Replace or sharpen cutter.
3. Recalculate and reset spindle RPM (
Page 20
).
4. Tighten column and table locks when pos sible to maintain rigidity.
5. Retract the spindle into the headstock completely, and lower headstock to the work area to maintain maximum rigidity.
6. Adjust the gibs (
Pages 27 & 28
).
1. Slow feed rate or adjust RPM.
2. Retract the spindle into the headstock completely, and lower headstock to the work area to maintain maximum rigidity.
3. Tighten table locks.
4. Adjust the gibs (
Pages 27 & 28
).
1. Loosen/replace lock lever and adjust gib Adjust the gibs ( (
Page 29
).
and gears (
Page 28 Page 29
).
).
2. Clean and relubricate dovetail and ways 3. Clean and relubricate headstock leadscrew -28-
M1111 Mill with Dovetail Column
Gibs and Backlash
During the life of your mill drill, you may have to adjust the gibs and the handwheels to remove any lash or loose ness that is a result of normal wear. Do not overtighten the gibs or half-nuts, or premature wear will occur.
To adjust the table gibs and the handwheel backlash, do these steps: 1.
DISCONNECT THE MILL FROM POWER!
2.
Loosen the four lock nuts (
Figure 29
).
3.
When properly adjusted, the table should move with slight resistance as felt in the handwheel. Each gib has multiple lock nuts and set screws that must also be adjusted. Make your adjustments equally and in small increments.
4.
Tighten the lock nuts.
5.
Remove the table end plate cap screws and the end plate (
Figure 30
).
6.
Locate the X-axis lead screw half-nut (
Figure 31
), and adjust both cap screws until the handwheel has approximately 0.003" backlash as shown by the dial.
7.
Repeat on the Y-axis leadscrew half-nut and lubricate the lead screws and gibs.
Figure 29.
Gib screws and adjustment.
End Plate Cap Screws
Figure 30.
Table end plate.
Half-Nut Cap Screw Lead Screw Half-Nut Lead Screw
Figure 31 .
Handwheel backlash adjustment.
-29-
M1111 Mill with Dovetail Column
To adjust the headstock gibs, do these steps: 1.
DISCONNECT THE MILL FROM POWER!
2.
Loosen the headstock lock lever (
Figure 32
).
3.
Loosen or tighten the upper and lower gib screws (
Figure 32
) in an alternating manner to adjust the headstock gib. The headstock should slide smoothly with no play or looseness. Do not overtighten the gibs or premature slide and gib wear will occur.
4.
Lubricate the headstock way and gib.
Upper Gib Screw Lower Gib Screw
Figure 32.
Headstock gib adjustment.
-30-
M1111 Mill with Dovetail Column
Service Lubrication
On an annual basis, or every six months under heavy use, we recommend that you clean and lubricate the headstock leadscrew and gears with white lithium grease and a light machine oil.
To lubricate the leadscrew and gears, do these steps: 1.
DISCONNECT THE MILL FROM POWER!
2.
Use the hex wrench to remove the two lower cap screws from the cabinet assem bly (see
Figure 33
).
3.
Hold the cabinet assembly, and remove the two upper cap screws (see
Figure 33
).
4.
Carefully lift and swing the cabinet assem bly out of the way from the column, and rest it aside.
5.
Using mineral spirits, a toothbrush, and rags, thoroughly clean the leadscrew and gears.
6.
Paint the headstock leadscrew and gear teeth with lithium grease, and oil the bear ings as outlined in
Figure 33
.
7.
Reinstall the cabinet assembly on the col umn. Upper Cap Screws Lithium Grease Cabinet Assembly Lithium Grease Lower Cap Screws
Figure 33.
Headstock leadscrew access and lubrication.
-31 Light Machine Oil
M1111 Mill with Dovetail Column
Electrical Safety Instructions
These pages are current at the time of printing. However, in the spirit of improvement, we may make changes to the electrical systems of future machines. Compare the manufacture date of your machine to the one stated in this manual, and study this section carefully.
If there are differences between your machine and what is shown in this section, call Technical Support at (360) 734-3482 for assistance BEFORE making any changes to the wiring on your machine. An updated wiring diagram may be available.
Note:
Please gather the serial number and manufacture date of your machine before calling. This information can be found on the main machine label.
SHOCK HAZARD.
Working on wiring that is connected to a power source is extremely dangerous. Touching electrified parts will result in personal injury including but not limited to severe burns, electrocution, or death. Disconnect the power from the machine before servicing electrical components!
QUALIFIED ELECTRICIAN.
Due to the inherent hazards of electricity, only a qualified electrician should perform wiring tasks on this machine. If you are not a qualified electrician, get help from one before attempting any kind of wiring job.
WIRE CONNECTIONS.
All connections must be tight to prevent wires from loosening during machine operation. Double-check all wires disconnected or connected during any wiring task to ensure tight connections.
WIRE/COMPONENT DAMAGE.
completing the task.
Damaged wires or components increase the risk of serious personal injury, fire, or machine damage. If you notice that any wires or components are damaged while performing a wiring task, replace those wires or components before
MODIFICATIONS
. Using aftermarket parts or modifying the wiring beyond what is shown in the diagram may lead to unpredictable results, including serious injury or fire.
MOTOR WIRING.
The motor wiring shown in these diagrams is current at the time of printing, but it may not match your machine. Always use the wiring diagram inside the motor junction box.
CAPACITORS/INVERTERS.
capacitors.
Some capacitors and power inverters store an electrical charge for up to 10 minutes after being disconnected from the power source. To reduce the risk of being shocked, wait at least this long before working on
CIRCUIT REQUIREMENTS.
power source.
You MUST follow the requirements at the beginning of this manual when connecting your machine to a
EXPERIENCING DIFFICULTIES.
(360) 734-3482.
If you are experiencing difficulties understanding the information included in this section, contact our Technical Support at
The photos and diagrams included in this section are best viewed in color. You can view these pages in color at www.shopfox.biz.
BLACK WHITE GREEN RED WIRING DIAGRAM COLOR KEY BLUE BROWN GRAY YELLOW YELLOW GREEN PURPLE ORANGE PINK LIGHT BLUE WHITE TUR-
-32-
M1111 Mill with Dovetail Column
Electrical Components
20 Amp Inverter Fuse Main Power Switch 20 Amp Fuse
Figure 35.
Main power switch and fuse.
Figure 34.
Motor power supply circuit board.
-33-
M1111 Mill with Dovetail Column
Figure 36.
Control panel electrical.
Figure 37.
Chip guard safety switch.
Figure 38.
Tapping button slip ring contact.
-34-
Figure 39.
Tachometer electrical.
M1111 Mill with Dovetail Column
Wiring Diagram (M1111)
Start Capacitor 1200MFD 250VAC FUSE 250VAC 20A Motor Power Supply PC Board/Inverter
See Figure 34
WARNING
ACCIDENTAL INJURY HAZARD!
Disconnect power supply before adjustments, setup, or maintenance!
Or S1 K3 K4 +5V GND SA SB SC Or SC SB SA 0 +5V Control Circuit Digital Tachometer Unit 0 0 0 0
See Figures 36 & 39
LS Rack Handle Tapping Switch
See Figure 37
PE4 Chip Guard Safety Switch
See Figure 37
Control Panel Circuit Board K3 K4 Digital Spindle Depth Unit
See Figure 36
Emergency Stop Switch
See Figure 36
0 0 0 0 -35 SR44 1.55V
+ Motor Power Circuit 230V MOTOR PE2 N1 1 L1 20A Fuse
See Figure 35
PE3 Power Lamp
See Figure 36
4 1 2 3 Main Power Switch
See Figure 35
PE1 N L1 Ground 110V Single-Phase Power Supply
advertisement
Related manuals
advertisement
Table of contents
- 4 INTRODUCTION
- 4 Woodstock Technical Support
- 5 Machine Specifications
- 7 Identification
- 8 SAFETY
- 8 Safety Instructions for Machinery
- 10 Additional Safety for Milling Machines
- 11 ELECTRICAL
- 11 110V Operation
- 11 Extension Cords
- 11 Electrical Specifications
- 13 SETUP
- 13 Unpacking
- 13 Inventory
- 15 Machine Placement
- 15 Cleaning Machine
- 16 Bench Mounting
- 17 Test Run and Spindle Break-In
- 18 OPERATIONS
- 18 General
- 19 Spindle Height Control
- 19 Table Travel
- 20 Headstock Travel
- 21 Drill Chuck
- 22 R-8 Collets
- 23 Control Panel
- 24 Calculating Spindle RPM
- 25 Milling/Drilling Mode
- 25 Tapping Mode
- 26 Accessories
- 28 MAINTENANCE
- 28 Schedule
- 28 Lubrication
- 29 SERVICE
- 29 Troubleshooting
- 30 Troubleshooting
- 31 Gibs and Backlash
- 33 Service Lubrication
- 35 Electrical Components
- 37 Wiring Diagram
- 38 PARTS
- 38 Column, Table, and Inverter
- 40 Headstock and Controls
- 43 Label Placement