UNPACKING. PROPOINT 8682288
Add to my manuals
44 Pages
PROPOINT 8682288 is a 30-gallon two-stage truck mount air compressor designed for heavy-duty air tools and suitable for job sites that require high volume. It features a splash lubricated pump with cast-iron cylinders for longer life, an idle-down throttle control to reduce fuel consumption, a ball bearing crankshaft, and an oil level sight gauge. The enclosed two-piece heavy gauge belt guard, oversized flywheel, accessory support bracket, and automotive style bearing inserts on connecting rods ensure durability and reliability. Equipped with a Schmidt belt tightening device and an aftercooler, this air compressor delivers optimal performance.
advertisement
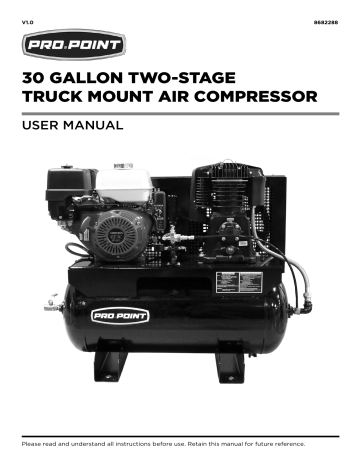
V1.0 30 GALLON TWO-STAGE TRUCK MOUNT AIR COMPRESSOR
5. Risk from Moving Parts
8682288
5.1 Serious injury may occur from moving parts such as belts, pulleys, flywheels or fans if they came in contact with you or your clothing. Never operate the air compressor without protective belt guards installed. Replace damaged protective covers or guards immediately.
5.2 Always drain air tanks completely before attempting any repairs or performing maintenance.
Never allow children or adolescents to operate air compressor.
5.3 Serious injury may occur if repairs are attempted with damaged, missing or removed protective guards, shrouds or missing covers. All repairs to the air compressor should be made only by authorized or trained service personnel.
6. Risk of Burn
Serious burn injuries could occur from touching exposed metal parts such as the compressor head, copper/braided discharge lines and engine exhaust muffler during operation and even after the compressor is shut down for some time. Never touch any of the exposed metal parts during operation and for an extended period of time after the air compressor has shut down. Do not attempt maintenance on the unit until it has been allowed to completely cool.
7. Risk of Injury from Lifting
Serious injury can result from attempting to lift an object that is too heavy. Always obtain assistance from others before attempting to lift any object that is too heavy for one person.
8. Flying Objects
8.1 Serious injury may occur from loose debris being propelled at high speeds from the compressed air stream. Always wear OSHA approved safety glasses to protect the eyes during operation of the air compressor.
8.2 Never point the air stream or tools at any point of your body, other people or animals.
Debris and dust may be ejected without warning. Always turn off the air compressor and drain tank pressure completely before attempting maintenance or attaching air tools. Release pressure slowly from the system.
9. Risk of Unsafe Operation
Serious injury or death may occur to you or others if air compressor is used in an unsafe manner. Review and understand all instructions and warnings in your owner’s manual. Know how to stop the air compressor. Do not operate until you are thoroughly familiar with all of the controls. Do not operate the compressor if fatigued or under the influence of alcohol or drugs. Stay alert while operating the compressor and pay close attention to the task at hand.
10. Risk of Damage to Air Compressor or Property
Failure to transport or operate the air compressor properly may result in major repair expenses. Oil leaks will damage carpets, painted surfaces, flooring and other items. Check oil levels daily and maintain proper oil levels. Always run compressor in a level, secure position that keeps it from tipping or falling during use. Do not operate without an air filter or in a corrosive environment. Always transport in a level position and use protective mats to keep truck beds clean, etc. Check drain bolts regularly and do not overfill machinery with oil.
11. Spark Arrestor
Please note that this product may not be equipped with a spark arresting muffler. If the compressor is operated around flammable materials or agricultural crops, brush, forests and grasslands, an approved spark arrestor must be installed, maintained and in good working order.
UNPACKING
WARNING! Do not operate the tool if any part is missing. Replace the missing part before operating. Failure to do so could result in a malfunction and personal injury.
Visit www.princessauto.com for more information 5
8682288 30 GALLON TWO-STAGE TRUCK MOUNT AIR COMPRESSOR
Ensure that adequate lifting equipment is available for moving the air compressor.
V1.0
Remove the parts and accessories from the packaging and inspect for damage. Make sure that all items in the parts list are included.
IDENTIFICATION KEY
1. Safety-Relief Valve
The air compressor is equipped with a safety-relief valve that is designed to discharge tank pressure at a predetermined setting when a systems failure occurs. Check the safety valve periodically by pulling on the ring only when the tank pressure is completely drained.
The spring loaded valve should move freely within the safety valve body. An inoperable safety valve could allow an excessive amount of tank pressure to build causing the air tank to catastrophically rupture or explode.
Do not tamper with or attempt to eliminate the safety relief valve.
Fig. 1
2. Pressure Gauge(s)
Gauges to measure tank or storage pressure and another gauge attached to the regulator that indicates output or working pressure.
3. Drain Valves
One or more drain valves are installed to allow moisture to be drained on a daily basis from the compressor storage tanks. Open drains carefully and slowly to prevent scale, rust or debris from becoming expelled at a high rate of speed.
4. Air Intake Filter
Air intake filters are installed to prevent foreign matter from entering the engine or compressor pump. Check intake elements on a regular basis and either clean or replace as needed. Warm soapy water or low compressed air may be used to clean the elements.
Check intake canisters or elbow components for cracks or broken seals and replace if structural problems are found.
5. Pilot-Unloader Valve
A pilot-unloader valve is used on all gas-powered units. When the storage tank reaches the top pressure setting of the pilot valve, the air being compressed is discharged to atmosphere instead of into the storage tank. When the tank pressure drops to the low pressure setting of the pilot valve, the compressed air will be redirected to the air tank. Do not attempt to replace the pilot valve without first draining the tank pressure completely.
Refer to Pilot Valve Adjustment section for adjustment and fine-tuning instructions. Do not adjust above the following factory recommendations.
6 For technical questions call 1-800-665-8685
V1.0
CLASSIFICATION
I-Stage Compressor
II-Stage Compressor
30 GALLON TWO-STAGE TRUCK MOUNT AIR COMPRESSOR
PRESSURE SETTING
110-135 PSI
145-175 PSI
8682288
6. Sight Gauge/Dipstick
Prior to daily operation, make a habit of checking the oil level of the compressor pump and engine. Our belt-driven air compressors are equipped with a sight gauge to make the daily task of checking the oil level easier. Always maintain the oil level to read 2/3 full on the sight gauge. Engine oil level should be maintained to the top threads of either oil fill port with engine in a level position.
7. Check Valve
The air compressor is built with a check valve to seal off and maintain tank pressure after the top end pressure setting of pilot valve or pressure switch is reached. The check valve works in conjunction with the pressure switch relief valve to provide a loadless start for the compressor system. If the compressor has a mysterious leak after stopping that cannot be traced elsewhere, the check valve may require servicing/replacing.
8. Breather/Oil Fill Plug
All reciprocating air compressor pumps are built with a crankcase vent to relieve the pressure that is created by the downward movement of the piston in the pump cylinder.
Our belt-drive units vent through the oil-fill plug. Never operate the air compressor without the dipstick or oil-fill plug.
9. Automatic-Idle Control
This gas-powered air compressor is built with an engine idle control kit that automatically decreases the engine speed when the top end pressure setting of the pilot unloader valve is reached. The top RPM setting of the engine is factory set for maximum performance and service life. Do not alter the factory top RPM setting. The engine idle speed is factory set and controlled by a black plastic Philips head screw on the carburetor. A slight increase to the idle speed setting may be required when operating in colder temperatures. Turn screw clockwise in 1/4-turn increments to increase the idle speed. If the idle speed setting is too low, premature fouling of spark plug will occur.
10. Cold-Start Valve
Our belt-driven portable units have a manual drain valve installed on the pump aftercooler to assist with cold weather starting. Open drain valve and allow the motor and pump to run unloaded for a minute to warm up. Close the drain and repeat the procedure if the motor or engine continue to struggle.
11. Schmidt Belt-Tightening Device
The gas-powered belt-driven portable air compressor has a unique system for maintaining proper belt tension. To maintain proper belt tension, first loosen the bolts on the bracket between engine and mounting plate. Then simply loosen the 1/2 in. locknuts (only until the washers beneath spin freely) that secure the engine to mounting plate.
Rotate the 3/4 in. fine thread bolt located on engine end of plate clockwise until the desired belt tension is reached.
Retighten the 1/2 in. locknuts and bracket bolts to maintain the adjusted belt tension.
12. Vibration Dampener(s)
The rubber pads installed beneath the portable tank assembly are very important to the proper operation of the air compressor. They provide protection from vibration that left unchecked could cause damage to many system components.
Fig. 2
Visit www.princessauto.com for more information 7
advertisement
* Your assessment is very important for improving the workof artificial intelligence, which forms the content of this project
Key Features
- 30-gallon tank capacity for extended use
- Two-stage pump for high volume and pressure
- Honda GX390 engine for reliable power
- Splash lubricated pump with cast-iron cylinders for durability
- Idle-down throttle control for fuel efficiency
- Ball bearing crankshaft for smooth operation
- Oil level sight gauge for easy monitoring
- Enclosed two-piece heavy gauge belt guard for protection
- Oversized flywheel for extra cooling
- Accessory support bracket for added functionality
Related manuals
Frequently Answers and Questions
What is the maximum pressure this air compressor can generate?
What is the CFM output of this air compressor at 90 PSI?
What type of engine does this air compressor use?
Does this air compressor have an oil level sight gauge?
What is the capacity of the fuel tank?
What is the decibel level of this air compressor?
What is the warranty period for this air compressor?
advertisement
Table of contents
- 1 30 Gallon Two-Stage Truck Mount Air Compressor
- 2 SPECIFICATIONS
- 2 INTRODUCTION
- 2 30 Gallon Two-Stage Truck Mount Air Compressor
- 3 SAFETY
- 3 HAZARD DEFINITIONS
- 3 WORK AREA
- 3 PERSONAL SAFETY
- 3 PERSONAL PROTECTIVE EQUIPMENT
- 3 PERSONAL PRECAUTIONS
- 4 SPECIFIC SAFETY PRECAUTIONS
- 5 UNPACKING
- 6 IDENTIFICATION KEY
- 8 ASSEMBLY & INSTALLATION
- 8 Location
- 8 Piping Fit-Up
- 9 Piping
- 9 OPERATION
- 9 Pre-Start Checklist
- 10 Gas Powered
- 11 Starting in Cold Temperatures
- 11 High-Altitude Operation
- 11 CARE & MAINTENANCE
- 12 Maintenance Hints
- 12 MAINTENANCE SCHEDULE
- 12 System Components
- 12 Drive Pulleys
- 12 Guards
- 13 Check Valves
- 13 Manual Shut-Off Valves
- 13 Safety-Relief Valves
- 13 Pilot Valve
- 13 Pressure Vessels
- 13 Pilot Valve Adjustment
- 13 Resetting Differential
- 13 Top-End Setting
- 13 Fine-Tuning Instructions
- 14 LUBRICATION
- 14 Oil Type Table
- 14 STORAGE
- 14 DISPOSAL
- 15 TROUBLESHOOTING
- 17 PARTS BREAKDOWN
- 17 PARTS LIST - Compressor
- 20 PARTS LIST – Pump
- 43 Blank Page
- 44 Blank Page