- No category
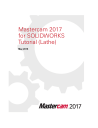
advertisement
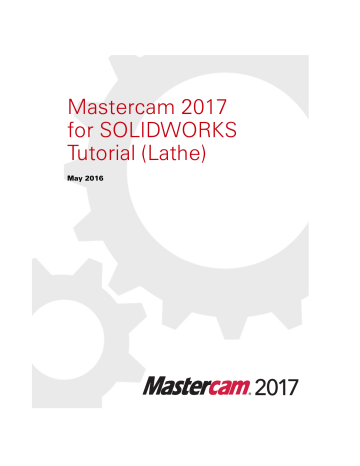
L E S S O N 4
4
C-Axis Drilling Operations
Lathe C-axis toolpaths are included with Mastercam for SOLIDWORKS for most common contour and drill applications. When you select one of these toolpaths,
Mastercam for SOLIDWORKS automatically sets the Tplane and Cplane to the appropriate settings for the desired application. These toolpaths also support Y-axis rotation and axis substitution. To use C-axis toolpaths, the active machine definition must support the appropriate axes. In this lesson, you use two operations to drill a hole through the part on the C-axis.
Lesson Goals
Add a toolpath group.
Create a C-axis drill operation.
Copy and modify an existing operation to create a new one.
Exercise 1: Adding a New Toolpath Group
Toolpath groups are subgroups that are “children” of machine groups. They inherit machining properties and other important properties from their parent groups. Toolpath groups house toolpath operations as well as other subgroups. They are useful for creating sets of toolpaths on the same machine that you will want to post separately.
Mastercam supports unlimited subgroups.
74 MASTERCAM 2017 FOR SOLIDWORKS / C-Axis Drilling Operations
In this exercise you organize your operations into two different toolpath groups: Outer
Diameter and C-Axis Drill.
1
In the Toolpaths Manager, right-click Toolpath Group-2, and select Groups,
Rename
from the pop-up menu.
2
Change the name of Toolpath
Group-2 to Outer Diameter, and press [Enter].
3
Create the C-Axis Drill toolpath group.
a
Right-click the machine group and select Groups, New Toolpath group from the menu.
b
A new toolpath group is created.
If necessary, move the insert arrow past the new toolpath group.
c
Rename the new toolpath group:
C-Axis Drill
, and press [Enter].
Exercise 2: Creating a C-Axis Drill Operation
TIP:
Use the Isometric view [Ctrl + 7] and Zoom to more easily see the model’s drill hole.
MCFSW LATHE TUTORIAL
1
Choose C-Axis Drill from the Lathe
Toolpaths menu.
CREATING A C-AXIS DRILL OPERATION 75
2
Highlight Cut-Extrude 2 on the SOLIDWORKS Flyout FeatureManager Design
Tree.
This is the correct feature but this toolpath only accepts a two-dimensional selection.
MCFSW LATHE TUTORIAL
76 MASTERCAM 2017 FOR SOLIDWORKS / C-Axis Drilling Operations
3
Expand Cut-Extrude 2, and select
Sketch8
.
The arc is selected.
4
Click the Points tab, and highlight the selection in the list box.
A drill point is placed at the center of the arc.
5
Click OK.
The C-Axis Toolpath - C-Axis Drill dialog box opens.
Enter the Toolpath Parameters
In addition to selecting tools and entering cutting values, the C-axis drill operation requires that you define the rotary axis motion.
MCFSW LATHE TUTORIAL
Select the tool
1
From the Tree View, open the Tool page.
CREATING A C-AXIS DRILL OPERATION 77
2
Click the Select library tool button.
The Tool Selection dialog box opens.
3
Choose 5.CENTER DRILL from the list, and click OK to return to the Tool page.
TIP:
Use the Tool List Filter to narrow the tools displayed in the list.
MCFSW LATHE TUTORIAL
78 MASTERCAM 2017 FOR SOLIDWORKS / C-Axis Drilling Operations
4
In the Comment window, type C-axis Drill - Center Drill.
Define Hole Depth
1
Open the Linking Parameters page.
MCFSW LATHE TUTORIAL
2
Enter an incremental cutting depth of -3.0.
CREATING A C-AXIS DRILL OPERATION 79
3
Keep all other options on the Linking Parameters page at their default values.
Configure Rotary Axis Motion
C-axis toolpaths automatically set the rotation type to Axis substitution around the Z axis. This gives you the choice of chaining either flat geometry which will be rolled around the cylinder, or geometry which is already properly positioned in
3D space.
1
Open the Rotary Axis Control page.
MCFSW LATHE TUTORIAL
80 MASTERCAM 2017 FOR SOLIDWORKS / C-Axis Drilling Operations
The Axis substitution option is the only rotation type available for Caxis drill operations.
2
Set Rotation direction to CW (clockwise), and confirm that the Unroll option is not selected.
3
Enter the Rotary diameter. Use the dimension from the blueprint on page 73,
or follow the procedure below.
a
Right-click in the Rotary
diameter
field, and select D =
Diameter of an arc
.
MCFSW LATHE TUTORIAL
b
Select the circular edge of the stock, and click OK.
COPYING THE DRILLING OPERATION 81
A built-in calculator reads the dimensions of the selected arc directly into the
Rotary diameter field.
4
5
6
Click OK to create the toolpath.
Save the part.
Backplot and/or Verify this toolpath following the procedures you learned in
Exercise 3: Copying the Drilling Operation
The final drill operation uses the same geometry and many of the same parameters as
the center drill operation you created in Exercise 2. In this exercise, you copy and paste
one operation in the Toolpaths Manager in order to quickly create a new one.
MCFSW LATHE TUTORIAL
82 MASTERCAM 2017 FOR SOLIDWORKS / C-Axis Drilling Operations
1
2
Right-click and drag the drill toolpath you just created to the bottom of the operation list.
Release the mouse button and choose Copy after from the rightclick menu.
Mastercam for SOLIDWORKS creates a new operation.
3
If necessary, move the insert arrow past the new toolpath.
Exercise 4: Modifying the Drilling Parameters
In this exercise, you create the drill through operation by modifying the parameters in the center drill operation that you copied.
1
Click new toolpath’s Parameters folder to open the dialog box.
MCFSW LATHE TUTORIAL
MODIFYING THE DRILLING PARAMETERS 83
2
Open the Tool page.
3
4
Click the Select library tool button, and select the 6 mm drill.
Type C-axis Drill in the Comment field.
5
Open the Linking Parameters page.
MCFSW LATHE TUTORIAL
84 MASTERCAM 2017 FOR SOLIDWORKS / C-Axis Drilling Operations
6
Using the dimension on page 73,
enter the cut depth.
7
Open the Tip Comp page.
Use this page to configure how the tool drills all the way through the stock.
a b
Select the Tip Comp checkbox to activate the parameters on the page.
Enter a 1.0 mm breakthrough amount.
This insures that the full diameter of the tool breaks through the bottom of the stock.
8
9
Click OK.
The new toolpath is marked dirty in the Toolpaths Manager.
MCFSW LATHE TUTORIAL
MODIFYING THE DRILLING PARAMETERS 85
10
Regenerate the toolpath, and save your part.
You have completed machining the outer diameter of the hose nozzle. In the next lesson, you prepare for machining the inner diameter with Mastercam for SOLID-
WORKS’s cutoff and stock flip operations.
MCFSW LATHE TUTORIAL
86 MASTERCAM 2017 FOR SOLIDWORKS / C-Axis Drilling Operations
MCFSW LATHE TUTORIAL
advertisement
* Your assessment is very important for improving the workof artificial intelligence, which forms the content of this project
advertisement
Table of contents
- 1 Title Page
- 5 Introduction
- 6 Tutorial Goals
- 6 General Tutorial Requirements
- 9 General Setup
- 9 Lesson Goals
- 9 Getting Ready to Work
- 12 Exercise 1: Loading a Machine Definition
- 15 Exercise 2: Creating a Work Coordinate System (WCS)
- 15 Lathe Coordinates
- 19 Exercise 3: Setting Up the Stock in the Main Spindle
- 22 Exercise 4: Defining the Chuck Jaws
- 27 Facing, Roughing, and Finishing the Outer Diameter
- 27 Lesson Goals
- 27 Exercise 1: Facing the Part
- 31 Exercise 2: Roughing the Outer Diameter
- 39 Exercise 3: Finishing
- 42 Exercise 4: Backplotting the Toolpaths
- 47 Adding Grooves and Threads
- 47 Lesson Goals
- 47 Exercise 1: Grooving on the Outer Diameter: Multiple Chains
- 54 Exercise 2: Grooving on the Outer Diameter: Rough Pass Only
- 56 Exercise 3: Finishing with Plunge Cuts
- 62 Exercise 4: Adding a Thread Toolpath
- 68 Exercise 5: Verifying the Toolpaths
- 73 C-Axis Drilling Operations
- 73 Lesson Goals
- 73 Exercise 1: Adding a New Toolpath Group
- 74 Exercise 2: Creating a C-Axis Drill Operation
- 81 Exercise 3: Copying the Drilling Operation
- 82 Exercise 4: Modifying the Drilling Parameters
- 87 Cutoff and Stock Flip
- 87 Lesson Goals
- 87 Exercise 1: Cutting Off the Part
- 91 Exercise 2: Programming a Stock Flip
- 99 Machining the Inner Diameter
- 99 Lesson Goals
- 99 Exercise 1: Creating New Tools in the Lathe Tool Manager
- 107 Exercise 2: Facing the Back of the Part
- 108 Exercise 3: Drilling the First Inner Diameter
- 111 Exercise 4: Drilling the Second Inner Diameter
- 114 Exercise 5: Roughing and Finishing the Third Inner Diameter
- 122 Exercise 6: Adding an ID Thread
- 125 Exercise 7: Refining Your Verification Results
- 131 Post Output
- 131 Lesson Goals
- 131 Exercise 1: Renumbering Tools
- 133 Exercise 2: Posting
- 134 Conclusion
- 134 Mastercam for SOLIDWORKS Resources
- 135 Mastercam for SOLIDWORKS Documentation
- 135 Contact Us