advertisement
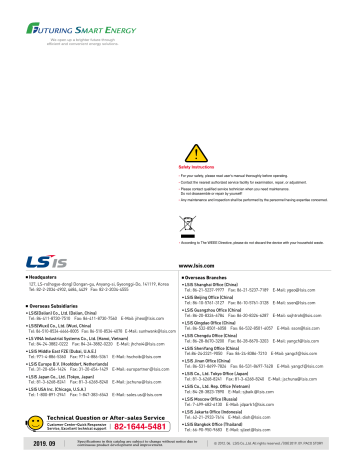
Safety Instructions
• For your safety, please read user's manual thoroughly before operating.
• Contact the nearest authorized service facility for examination, repair, or adjustment.
•
Please contact qualified service technician when you need maintenance.
Do not disassemble or repair by yourself!
•
Any maintenance and inspection shall be performed by the personnel having expertise concerned.
• According to The WEEE Directive, please do not discard the device with your household waste.
■ Headquaters
127, LS-ro(hogye-dong) Dongan-gu, Anyang-si, Gyeonggi-Do, 141119, Korea
Tel: 82-2-2034-4902, 4684, 4429 Fax: 82-2-2034-4555
■ Overseas Subsidiaries
• LSIS(Dalian) Co., Ltd. (Dalian, China)
Tel: 86-411-8730-7510 Fax: 86-411-8730-7560 E-Mail: jiheo @ lsis.com
• LSIS(Wuxi) Co., Ltd. (Wuxi, China)
Tel: 86-510-8534-6666-8005 Fax: 86-510-8534-4078 E-Mail: sunhwank @ lsis.com
• LS VINA Industrial Systems Co., Ltd. (Hanoi, Vietnam)
Tel: 84-24-3882-0222 Fax: 84-24-3882-0220 E-Mail: jhchoi4
@ lsis.com
• LSIS Middle East FZE (Dubai, U.A.E.)
Tel: 971-4-886-5360 Fax: 971-4-886-5361 E-Mail: hschoib @ lsis.com
• LSIS Europe B.V. (Hoofddorf, Netherlands)
Tel: 31-20-654-1424 Fax: 31-20-654-1429 E-Mail: europartner
@ lsis.com
• LSIS Japan Co., Ltd. (Tokyo, Japan)
Tel: 81-3-6268-8241 Fax: 81-3-6268-8240 E-Mail: jschuna @ lsis.com
• LSIS USA Inc. (Chicago, U.S.A.)
Tel: 1-800-891-2941 Fax: 1-847-383-6543 E-Mail: sales.us
@ lsis.com
■ Overseas Branches
• LSIS Shanghai Office (China)
Tel: 86-21-5237-9977 Fax: 86-21-5237-7189 E-Mail: ygeo @ lsis.com
• LSIS Beijing Office (China)
Tel: 86-10-5761-3127 Fax: 86-10-5761-3128 E-Mail: sson @ lsis.com
• LSIS Guangzhou Office (China)
Tel: 86-20-8326-6784 Fax: 86-20-8326-6287 E-Mail: sojhtroh @ lsis.com
• LSIS Qingdao Office (China)
Tel: 86-532-8501-6058 Fax: 86-532-8501-6057 E-Mail: sson @ lsis.com
• LSIS Chengdu Office (China)
Tel: 86-28-8670-3200 Fax: 86-28-8670-3203 E-Mail: yangcf
@ lsis.com
• LSIS ShenYang Office (China)
Tel:86-24 2321-9050 Fax: 86-24-8386-7210 E-Mail: yangcf @ lsis.com
• LSIS Jinan Office (China)
Tel: 86-531-8699-7826 Fax: 86-531-8697-7628 E-Mail: yangcf
@ lsis.com
• LSIS Co., Ltd. Tokyo Office (Japan)
Tel: 81-3-6268-8241 Fax: 81-3-6268-8240 E-Mail: jschuna @ lsis.com
• LSIS Co., Ltd. Rep. Office (Vietnam)
Tel: 84-28-3823-7890 E-Mail: sjbaik @ lsis.com
• LSIS Moscow Office (Russia)
Tel: 7-499-682-6130 E-Mail: jdpark1 @ lsis.com
• LSIS Jakarta Office (Indonesia)
Tel: 62-21-2933-7614 E-Mail: dioh @ lsis.com
• LSIS Bangkok Office (Thailand)
Tel: 66-90-950-9683 E-Mail: sjleet @ lsis.com
2019. 09
2012. 06. LSIS Co.,Ltd. All rights reserved. / (08) 2019. 09. PACO STORY
Electronic Motor Protection Relays
The new standard of next-generation motor protection relay
With smart protection and safe control,
We provide the cutting-edge digital total solution.
The new standard of next-generation motor protection relay
With smart protection and safe control,
We provide the cutting-edge digital total solution.
Electronic Motor Protection Relays
1. A list of standard models ······················································
2. EMPR Series
2-1. DMPi ···············································································
2-2. GMP ···············································································
2-3. IMP ··················································································
2-4. MMP ··············································································
3. EMPR Rated specifications ···················································
4. EMPR Accessories ····································································
5. EMPR Operating characteristics curve ·······································
6. Direct mounting EMPR new/old comparative table ·····················
7. Certificates ················································································
4
8
34
60
72
98
99
102
103
104
A list of standard models
Functions
AC
Control power
CT connection
Protection functions
(Current)
Protection functions
(Voltage)
Protection functions
(Power)
DC
Frequency
Single phase
Three-phase
External tunnel type
Internal tunnel type
Screw type
Pin type
Overcurrent
Undercurrent
Stall
Jam
Current Phase failure
Current Reverse phase
Current Phase unbalance
Ground fault(zero phase current)
Instant short circuit
Heat accumulation inverse time
Definite time
Ground fault (residual current)
Selective ground fault
Overvoltage
Undervoltage
Voltage Phase failure
Voltage Phase unbalance
Overvoltage Reverse phase
Overvoltage Ground fault
Overpower
Underpower
Over power factor
Under power factor
S/T
SZ/TZ
SB/TB
DMP-i
SI/TI
GMP22/40
SM/TM
SA/TA
2P/2PD/2PA
2T/2S
3P/3T/3S
3PR/3TR
/3SR
-
-
-
-
-
-
-
-
-
-
-
●
-
●
-
-
●
●
●
●
●
●
50/60Hz
●
●
-
●(T)
●(S)
-
●
AC/DC
85~260V
AC/DC
85~260V
-
-
-
-
-
-
-
-
-
-
-
●
-
●
●
●
●(Z/B)
-
●
●
●
●
50/60Hz
●
●
-
●(T)
●(S)
-
●
AC/DC
85~260V
-
-
-
-
-
-
-
-
-
-
-
●
-
●
●
●
-
●(I)
●
●
●
●
50/60Hz
●
●
-
●(T)
●(S)
-
●
AC/DC
85~260V
-
-
-
-
-
-
-
-
-
-
-
●
-
●
-
-
●
●
●
●
●
●
50/60Hz
●
●
-
●(T)
●(S)
-
●
110/220
100~260V
-
-
-
-
-
-
-
-
-
-
-
●
●(D)
-
-
-
-
-
●
●
-
●
-
50/61Hz
-
●
-
●(T)
●(S)
●(P)
●
100~260V 100~260V
-
-
-
-
-
-
-
-
-
-
-
●
-
-
-
●(3)
-
-
●
●
-
●
-
50/62Hz
-
●
-
●(T)
●(S)
●(P)
●
-
-
-
-
-
-
-
-
-
-
-
●
-
-
●(R)
●(3)
-
-
●
●
-
●
-
50/63Hz
-
●
-
●(T)
●(S)
●(P)
●
4 Electronic Motor Protection Relays
T/TE/TA
GMP60
TD/TDa
3T/3TR,
3S/3SR
3TZ/3TZR,
3TN/3TNR,
3SZ/3SZR,
3SN/3SNR
24/48/110/220
/380
180~480V
110/220V
-
-
-
-
-
-
-
-
-
-
-
-
●
-
-
-
-
-
●
●
-
●
-
50/64Hz
-
●
-
●(T)
-
-
●
110/220V
-
-
-
-
-
-
-
-
-
-
-
-
●(D)
-
-
-
-
-
●(a)
●
●
●
-
50/65Hz
-
●
-
●(T)
-
-
●
100~260V 100~260V
●(R)
●(3)
-
-
-
●
●
●
-
●
-
50/66Hz
-
●
-
●(T)
●(S)
-
●
-
-
-
-
-
-
-
-
-
-
-
-
-
-
-
-
-
-
-
-
-
-
-
●
●(N)
●(R)
●(3)
●(Z)
-
●
●
-
●
-
50/67Hz
-
●
-
●(T)
●(S)
-
●
2S/2SA
100~260V
-
-
-
-
-
-
-
-
-
-
-
●
-
-
-
-
-
-
●
●
-
●
-
50/68Hz
-
●
-
-
●(S)
-
●
GMP80
3S/3SR
100~260V
-
-
-
-
-
-
-
-
-
-
-
●
-
-
●(R)
●(3)
-
-
●
●
-
●
-
50/69Hz
-
●
-
-
●(S)
-
●
IMP
C
MMP
S P
AC/DC
85~245V
-
-
-
-
-
-
-
-
-
-
-
●
-
-
●
●
●
●
●
●
●
●
-
●
●
-
50/60Hz
●
●
-
100~260V 100~260V 100~260V
-
-
-
●
-
-
-
-
-
●
-
●
-
●
●
●
●
●
●
●
●
●
-
●
●
-
-
50/60Hz
●
●
-
-
-
-
-
-
-
-
-
-
-
-
●
-
●
●
●
●
●
●
●
●
●
-
●
●
-
-
50/60Hz
●
●
-
●
●
●
-
●
●
●
●
●
-
●
●
-
●
●
●
●
●
●
●
●
●
-
●
●
-
-
50/60Hz
●
●
-
Functions
AC
Control power
CT connection
Protection functions
(Current)
Protection functions
(Voltage)
Protection functions
(Power)
DC
Frequency
Single phase
Three-phase
External tunnel type
Internal tunnel type
Screw type
Pin type
Overcurrent
Undercurrent
Stall
Jam
Current Phase failure
Current Reverse phase
Current Phase unbalance
Ground fault(zero phase current)
Instant short circuit
Heat accumulation inverse time
Definite time
Ground fault (residual current)
Selective ground fault
Overvoltage
Undervoltage
Voltage Phase failure
Voltage Phase unbalance
Overvoltage Reverse phase
Overvoltage Ground fault
Overpower
Underpower
Over power factor
Under power factor
S/T
SZ/TZ
SB/TB
DMP-i
SI/TI
GMP22/40
SM/TM
SA/TA
2P/2PD/2PA
2T/2S
3P/3T/3S
3PR/3TR
/3SR
-
-
-
-
-
-
-
-
-
-
-
●
-
●
-
-
●
●
●
●
●
●
50/60Hz
●
●
-
●(T)
●(S)
-
●
AC/DC
85~260V
AC/DC
85~260V
-
-
-
-
-
-
-
-
-
-
-
●
-
●
●
●
●(Z/B)
-
●
●
●
●
50/60Hz
●
●
-
●(T)
●(S)
-
●
AC/DC
85~260V
-
-
-
-
-
-
-
-
-
-
-
●
-
●
●
●
-
●(I)
●
●
●
●
50/60Hz
●
●
-
●(T)
●(S)
-
●
AC/DC
85~260V
-
-
-
-
-
-
-
-
-
-
-
●
-
●
-
-
●
●
●
●
●
●
50/60Hz
●
●
-
●(T)
●(S)
-
●
110/220
100~260V
-
-
-
-
-
-
-
-
-
-
-
●
●(D)
-
-
-
-
-
●
●
-
●
-
50/61Hz
-
●
-
●(T)
●(S)
●(P)
●
100~260V 100~260V
-
-
-
-
-
-
-
-
-
-
-
●
-
-
-
●(3)
-
-
●
●
-
●
-
50/62Hz
-
●
-
●(T)
●(S)
●(P)
●
-
-
-
-
-
-
-
-
-
-
-
●
-
-
●(R)
●(3)
-
-
●
●
-
●
-
50/63Hz
-
●
-
●(T)
●(S)
●(P)
●
EMPR Series
Electronic Motor Protection Relays
GMP60 GMP80 MMP
T/TE/TA TD/TDa
3T/3TR,
3S/3SR
3TZ/3TZR,
3TN/3TNR,
3SZ/3SZR,
3SN/3SNR
2S/2SA 3S/3SR
IMP
C S P
24/48/110/220
/380
180~480V
110/220V
-
-
-
-
-
-
-
-
-
-
-
-
●
-
-
-
-
-
●
●
-
●
-
50/64Hz
-
●
-
●(T)
-
-
●
110/220V
-
-
-
-
-
-
-
-
-
-
-
-
●(D)
-
-
-
-
-
●(a)
●
●
●
-
50/65Hz
-
●
-
●(T)
-
-
●
100~260V
-
-
-
-
-
-
-
-
-
-
-
-
-
-
-
-
-
-
-
-
-
-
●
-
-
●
●
●
●
●
●
●
●
-
●
●
-
50/60Hz
●
●
-
-
-
-
-
-
-
-
-
-
-
-
●
-
-
●(R)
●(3)
-
-
●
●
-
●
-
50/69Hz
-
●
-
-
●(S)
-
●
-
-
-
-
-
-
-
-
-
-
-
●
-
-
-
-
-
-
●
●
-
●
-
50/68Hz
-
●
-
-
●(S)
-
●
-
-
-
-
-
-
-
-
-
-
-
-
●
●(N)
●(R)
●(3)
●(Z)
-
●
●
-
●
-
50/67Hz
-
●
-
●(T)
●(S)
-
●
●(R)
●(3)
-
-
-
●
●
●
-
●
-
50/66Hz
-
●
-
●(T)
●(S)
-
●
100~260V 100~260V 100~260V
AC/DC
85~245V
100~260V 100~260V 100~260V
-
-
-
-
-
-
-
-
-
-
-
●
-
●
●
●
●
●
●
●
●
●
-
●
●
-
-
50/60Hz
●
●
-
-
-
-
●
-
-
-
-
-
●
-
●
-
●
●
●
●
●
●
●
●
●
-
●
●
-
-
50/60Hz
●
●
-
●
●
●
-
●
●
●
●
●
-
●
●
-
●
●
●
●
●
●
●
●
●
-
●
●
-
-
50/60Hz
●
●
-
LSIS Co.,Ltd.
5
A list of standard models
DMP-i GMP22/40
Functions
S/T
SZ/TZ
SB/TB
SI/TI
Display
Auxiliary function
Communication function
Phase current
Ground current
Built-in ZCT
Active/Reactive Power
Electric Energy
Total Running Time
Display Failure Cause
Save Failure Cause
Display Load Factor
Display
Save Failure Cause
Display Alert
Set Return Method
Set Date/Time Information
Set Password
Set/Save Total Running Time
Set Operating Characteristics
Save Fault Wave
Self-test
Restart Limit
Select Starting Method
Built-in ZCT
Selective Ground Protection Setting
On/Off switch
Electric Energy Pulse Output(4~20mA)
4~20mA output
MODBUS RS-485
-
-
-
-
-
-
●
●
-
-
-
-
●
●
4 digit
7-segment
●
●
●
●
●
-
●
●
-
-
●
-
-
-
-
-
-
-
●
●
-
-
-
-
●
●
4 digit
7-segment
●
●
●
●
●
-
●
●
-
-
●
-
-
-
●(B)
-
-
-
●
●
-
-
-
-
●
●
4 digit
7-segment
●
●
●
●
●
-
●
●
●
-
●(B)
-
-
-
-
-
-
-
●
●
-
●(A)
●(A)
●(M)
●
●
4 digit
7-segment
●
●
●
●
●
-
●
●
-
-
●
-
SM/TM
SA/TA
2P/2PD/2PA
2T/2S
3P/3T/3S
-
-
-
-
-
-
-
-
-
-
-
-
-
-
-
-
-
-
-
-
-
-
●(A)
-
-
-
-
-
-
-
-
-
-
-
-
-
-
-
-
-
-
-
-
-
-
-
-
-
-
-
-
-
-
-
3PR/3TR
/3SR
-
-
-
-
-
-
-
-
-
-
-
-
-
-
-
-
-
-
-
-
-
-
-
-
-
-
-
6 Electronic Motor Protection Relays
-
-
-
-
-
-
-
-
-
-
-
-
-
-
-
-
-
-
-
-
●
-
●(A)
-
-
-
-
T/TE/TA
GMP60
TD/TDa
3T/3TR,
3S/3SR
3TZ/3TZR,
3TN/3TNR,
3SZ/3SZR,
3SN/3SNR
-
-
-
●
-
-
-
-
-
-
-
-
-
-
-
-
-
-
-
-
-
-
-
-
-
-
-
-
-
-
●
-
-
-
-
-
-
-
-
-
-
-
-
-
-
-
-
-
-
●(3T)
-
-
-
-
-
-
-
-
●(a)
-
-
-
-
-
-
-
●(a)
-
4 digit
7-segment
-
●
●(a)
-
-
-
-
●(a)
-
-
-
-
2S/2SA
-
-
-
-
-
-
-
-
-
-
-
-
-
-
-
-
-
-
-
-
-
-
●(A)
-
-
-
-
GMP80
3S/3SR
-
-
-
-
-
-
-
-
-
-
-
-
-
-
-
-
-
-
-
-
-
-
-
-
-
-
-
IMP
-
-
-
-
-
-
●
●
●
●
-
-
-
-
4 digit
7-segment
●
●
●
●
●
-
●
-
-
-
-
-
MMP
C S P
●
●
●
●
●
●
●
●
●
●
●(M)
●(M)
●
-
4 digit
7-segment
●
●
●
●
●
●
●
●
●
●
●
●
●
●
●
●
●
●
●
●
●
●
●(M)
●(M)
●
-
4 digit
7-segment
●
●
●
●
●
●
●
●
●
●
●
●
●
●
●
●
●
●
●
●
●
●
●(M)
●(M)
●
-
4 digit
7-segment
●
●
●
●
●
●
●
●
●
●
●
●
DMP-i GMP22/40
Functions
S/T
SZ/TZ
SB/TB
SI/TI
Display
Auxiliary function
Communication function
Phase current
Ground current
Built-in ZCT
Active/Reactive Power
Electric Energy
Total Running Time
Display Failure Cause
Save Failure Cause
Display Load Factor
Display
Save Failure Cause
Display Alert
Set Return Method
Set Date/Time Information
Set Password
Set/Save Total Running Time
Set Operating Characteristics
Save Fault Wave
Self-test
Restart Limit
Select Starting Method
Built-in ZCT
Selective Ground Protection Setting
On/Off switch
Electric Energy Pulse Output(4~20mA)
4~20mA output
MODBUS RS-485
-
-
-
-
-
-
●
●
-
-
-
-
●
●
4 digit
7-segment
●
●
●
●
●
-
●
●
-
-
●
-
-
-
-
-
-
-
●
●
-
-
-
-
●
●
4 digit
7-segment
●
●
●
●
●
-
●
●
-
-
●
-
-
-
●(B)
-
-
-
●
●
-
-
-
-
●
●
4 digit
7-segment
●
●
●
●
●
-
●
●
●
-
●(B)
-
-
-
-
-
-
-
●
●
-
●(A)
●(A)
●(M)
●
●
4 digit
7-segment
●
●
●
●
●
-
●
●
-
-
●
-
SM/TM
SA/TA
2P/2PD/2PA
2T/2S
3P/3T/3S
-
-
-
-
-
-
-
-
-
-
-
-
-
-
-
-
-
-
-
-
-
-
●(A)
-
-
-
-
-
-
-
-
-
-
-
-
-
-
-
-
-
-
-
-
-
-
-
-
-
-
-
-
-
-
-
3PR/3TR
/3SR
-
-
-
-
-
-
-
-
-
-
-
-
-
-
-
-
-
-
-
-
-
-
-
-
-
-
-
EMPR Series
Electronic Motor Protection Relays
GMP60 GMP80 MMP
T/TE/TA
-
-
-
-
-
-
-
-
-
-
-
-
-
-
-
-
-
-
-
-
●
-
●(A)
-
-
-
-
TD/TDa
-
-
-
-
●(a)
-
-
-
-
-
-
-
●(a)
-
4 digit
7-segment
-
●
●(a)
-
-
-
-
●(a)
-
-
-
-
3T/3TR,
3S/3SR
-
-
-
●
-
-
-
-
-
-
-
-
-
-
-
-
-
-
-
-
-
-
-
-
-
-
-
-
-
-
-
-
-
-
-
-
-
-
-
●(3T)
-
-
-
-
3TZ/3TZR,
3TN/3TNR,
3SZ/3SZR,
3SN/3SNR
-
-
-
●
-
-
-
-
-
-
2S/2SA
-
-
-
-
-
-
-
-
-
-
-
-
-
-
-
-
-
-
-
-
-
-
●(A)
-
-
-
-
3S/3SR
-
-
-
-
-
-
-
-
-
-
-
-
-
-
-
-
-
-
-
-
-
-
-
-
-
-
-
IMP
●
●
●
●
●
●
●
●
●
●
●(M)
●(M)
●
-
4 digit
7-segment
●
●
●
●
●
●
●
●
●
●
●
●
-
-
-
-
-
-
●
●
●
●
-
-
-
-
4 digit
7-segment
●
●
●
●
●
-
●
-
-
-
-
-
C S P
●
●
●
●
●
●
●
●
●
●
●(M)
●(M)
●
-
4 digit
7-segment
●
●
●
●
●
●
●
●
●
●
●
●
●
●
●
●
●
●
●
●
●
●
●(M)
●(M)
●
-
4 digit
7-segment
●
●
●
●
●
●
●
●
●
●
●
●
LSIS Co.,Ltd.
7
Revolutionary development of motor protection relays
Complete motor protection is realized with real time data processing and high precision.
8 Electronic Motor Protection Relays
DMPi Series
DMPi Series
Intelligent Digital Motor Protection Relays
• Definite / Inver se time option
and various protection methods
• Storage of failure causes
• Separated display part using cables
• MODBUS communication, 4 ~ 20mA DC output
• Operating time displayed for each model
C o n t e n t s
10 A list of standard models
11 Product characteristics
15 Rated specifications / Model numbering system
16 Operation & setting method
25 Terminal Configuration / Wiring & cable connection
31 Dimensions
LSIS Co.,Ltd.
9
A list of standard models
A list of standard models
Rated current
Connection method
Model No.
Overcurrent
0.5~6A
5~65A
Terminal type
Penetrated type
Terminal type
Penetrated type
DMP06i-S
DMP06i-SZ, SB
DMP06i-SI
DMP06i-SZI, SBI Note1)
DMP06i-T
DMP06i-TZ, TB
DMP06i-TI
DMP06i-TZI, TBI Note1)
DMP65i-S
DMP65i-SZ, SB
DMP65i-SI
DMP65i-SZI, SBI Note1)
DMP65i-T
DMP65i-TZ, TB
DMP65i-TI
DMP65i-TZI, TBI Note1)
●
●
●
●
●
●
●
●
●
●
●
●
●
●
●
●
Note) 1. It is possible to set up ground fault and instantaenous trip contacts separately.
●
●
●
●
●
●
●
Stall/
Locked rotor
●
●
●
●
●
●
●
●
●
●
●
●
●
●
●
●
Phase fail current
●
●
●
●
●
●
●
●
●
●
●
●
●
●
●
●
Phase unbalance
●
●
●
●
●
●
●
●
●
Reverse phase
Under current
Ground fault
●
●
●
●
●
●
●
●
●
●
●
●
●
●
●
●
●
●
●
●
●
●
●
●
●
●
●
●
●
●
●
●
-
●
-
●
●
-
●
-
●
-
-
●
-
●
-
●
●
●
-
-
-
●
●
●
●
-
Instant short circuit
-
-
-
-
●
●
Remarks
• If there is the function of
RS485 communication,
‘M’ is appended to its type name. If there is the function of
4~20mA DC output, ‘A’ is appended to its type name.
• RS485 communication function and 4~20mA
DC output function are not supported at the same time.
10 Electronic Motor Protection Relays
MCU
MCU
MCU
MCU
Slide S/W
Slide S/W
Return
Convenience
MCU
30mA 25A
MCU
25A
Total
Total
25A
Total
Total
Slide S/W
INV
Slide S/W
Return
MCU
30mA 25A
Return
Save
30mA
INV
25A
Slide S/W
Total
Save
Return
30mA
Save
25A
Total
MCU
MCU
30mA 25A
INV
INV
Slide S/W
Slide S/W
Return
Return
30mA
30mA
25A
25A
Save
Save
INV
Reliability
Save
MCU
Total
Save
Total
Slide S/W
Return
INV
INV
25A 30mA
Return
30mA
Slide S/W
Slide S/W
30mA 25A
Return
Total
30mA 25A
30mA
MCU
25A
INV
Slide S/W
INV
Slide S/W
Save
Return
30mA
MCU
25A
30mA 25A
Total
25A
Total
Total
Save
DMPi Series
Slide S/W
Slide S/W
30mA
MCU
25A
30mA 25A
Total
25A
Total
INV
Slide S/W
30mA 25A
Return
Return
30mA
MCU
25A
MCU
30mA 25A
MCU
INV
Slide S/W
INV
Slide S/W
Save
Return
Slide S/W
Return
Save
30mA Save 25A
Return
30mA 25A
30mA 25A
Total
Total
Integrated Digital Motor Protection Relay based on MCU(Microprocessor Control Unit)
Real Time Processing and High Precision are implemented.
Applicable to invertor circuits
It may be applied to the secondary inverter control circuit with its outstanding resistance to harmonic noise.
Permissible frequency range is 10~200Hz. When the percentage of harmonic is more than 30%, a harmonic filter is installed. (However, the ground fault protection function should be switched off.)
Function to store the cause(s) of failure / Fault
Up to 5 motor failure events may be saved in the system, so that the failure history can be easily identified.
Up to 5 motor failure events may be saved in the system, so that the failure history can be easily identified.
The display part is separated and attached to the front panel, so that information on current/operating time and setup can be viewed without taking out the unit. With the separated display, motor protection can be performed.
Communication function
~100A
~100A network configurations. Models with analog current signal (4~20mA DC) output are compatible with systems that uses the existing TD (Transducer).
A wide range of reset functions
Manual/Automatic/Electrical reset functions are provided for user convenience.
Date information display
When a failure occurs, the date and time of failure occurrence are saved in the system to accurately identify the date of motor failure.
Password setting
When changing the set values, a password must be inserted.
~100A
MCU
Save
Save
INV
When the predefined operating time has elapsed, related information is displayed so that operators may replace the motor bearing and check the refueling cycle.
~100A
Terminal/Penetrated types are shared for application in various installation environments
Terminal blocks are detachable, which makes them applied to various installation environments.
MCU
Total
Total
Slide S/W
~100A
INV
Slide S/W
Return
MCU
30mA 25A
Return
Save
30mA
INV
25A
Slide S/W
Total
Save
Return
25A
~100A
Thermal Inverse Time, Inverse Time and Definite Time Modes
According to user’s needs, the motor can be protected in the inverse time mode or definite time mode.
~100A
Three-phase digital ampere-meter
Three-phase current is displayed in cycle at intervals of 2 seconds for operators to check the motor state.
Various protection elements and additional functions
Single/3-phase is optional, and output contact as well as the operating time can be set.
Free Voltage power connection (AC/D85~260V) is possible with ZCT built-in option.
High Reliability
The current relay error is reduced from 5% to 3% and the minimum sensible current is lowered from 70% to 30% of the minimum rating. Phase fail/phase unbalance protection relay correction and delay time can be set.
Inverse time characteristic good for motor protection
Thanks to the inverse time characteristic in which a running time is determined by a size of overcurrent, the equipment is excellent at motor protection.
LSIS Co.,Ltd.
11
~100A
30mA
Save
25A
Total
~100A
Total
~100A
Save
Total Total
~100A
Product characteristics
Protection functions
Over current. Overload
Considering the start-up time of a motor and based on 600% of the rated current, operating time is set by 1sec unit ranging from 1 to 60 seconds to establish an overload characteristic curve (Class 1~60). When a definite time characteristic is chosen, overcurrent is detected from the set operating delay time (D-Time) regardless of the quantity of heat generated from the motor. Then, Trip is generated when overcurrent continues, exceeding the operating time (O-Time).
Stall/Locked Rotor
It is a function to prevent burning caused by locked rotor, startup failure and startup delay. When the level of load current increases due to overheating and overcurrent during operation or when the load torque exceeds the motor torque, such failure is detected to break the related circuits.
Phase Fail/Phase Unbalance
When phase fail occurs, a motor may not start to operate and the motor under operation will stop owing to the lack of torque or reverse phase current will continue to flow, generating heat. DMPi calculates the unbalance of three-phase current and when it reaches
100%, it operates at 3sec as phase fail. It can be set for tripping at 5sec when the phase unbalance in within 10~90%.
*Delay time may be set within the range of 0~200sec so that it does not function upon startup.
Reverse Phase
It is a function to prevent reversing of a motor. The phase difference of three-phase current is compared for operation within 0.1~1.0sec when the phase sequence has changed.
Reverse phase is checked only upon motor startup.
Under Current Protection
This equipment is mainly used to monitor no-load status caused by the separation or damage of the drive shaft of a motor, or to protect the idle rotation (no-load) status of pump. It is possible to set up 30~70% of rated current. At the time of third second, it runs.
Ground Fault
Ground fault leakage current is detected to prevent ground faults arising from electric leakage and secondary accidents (Phase faults and electric shock accidents). Current sensitivity and operating time are set differently according to the grounded system or purpose of protection. Current sensitivity can be set within the range of 30mA~3A and the operating time within the range of 0.05~5.0sec.
* Delay time may be set within the range of 0~200sec so that it does not function upon startup,
and built-in ZCT is provided according to the Type.
Instance
It is a function to protect a motor from short-circuit current. It operates within 50ms when fault current of more than 500~1500% is generated. Delay time may be set within the range of 0~200sec so that it does not function upon startup.
12 Electronic Motor Protection Relays
<Inverse time characteristic>
<Definite time characteristic>
Communication function
MODBUS specifications
Communication code
Communication speed
Communication parity
Fixed to 1bit
Communication data swap
Block diagram of communication system
1 ~ 247
9600, 19200, 38400, 57600 bps
None, Even, Odd
1bit
Limited to float, long data of Off / On (0x04 (Read input registers))
DMPi Series
GIPAM
SCADA
DCS
PLC
4~20mA
GIMAC
MODBUS/RS-485
Inverter Inverter
LSIS Co.,Ltd.
13
Product characteristics
Analog (4~20mA) output function
Specifications
• The measured values of current for the maximum phase among the measured values of
three-phase current are converted into DC 4~20mA and the measured values of current
can be displayed with a digital meter in the distance.
• 20mA output setting: 0.5~6A or 5~65A
Note) 1. At the setting mode of 0.5~6A, the level of current is measured from 0.15A, so 0A is measured when less than 0.15A
and the output value becomes 4mA. (When it is 0.15A, >4mA is actually measured.)
2. Measurement error based on temperature changes: ±0.15%/°C (Based on the room temperature of 25°C)
• Motor stop state: 4mA
• Setting value exceeding the rating: 20mA
20mA
resistance of the received meta (Generally 250 Ω) and line resistance.
16mA
13.6mA
16.8mA
20mA
12mA
(I Upper Limit – (I Lower limit)
TD Setting value
× Load current + 4mA
4mA
=
0A
0A
16mA
TD setting value
0.1A
1A
0.2A
2A
× Load current + 4mA
0.3A
3A
0.4A
4A
0.5A/0.5A~60A
5A/5A~60A
20mA
16mA
12mA
8mA
4mA
20mA
16mA
12mA
8mA
4mA
0.15A
1
10 20
2
30
3
40
4
50
5
Analog output when output setting is 6A (65A)
20mA
16.8mA
13.6mA
7.2mA
10.4mA
6A
60 65A
0A
0A
2A
20A
14 Electronic Motor Protection Relays
4A
40A
6A
60A
8A
80A
10A/0.5A~10A
100A/5A~100A
20mA
16mA
12mA
8mA
4mA
7.2mA
10.4mA
13.6mA
16.8mA
20mA
0A
0A
1A
10A
2A
20A
3A
30A
4A
40A
5A/0.5A~10A
50A/5A~100A
Rated specifications / Model numbering system
DMPi Series
Rated specifications
Connection method
Protection functions
Connection method
Operating time characteristics
Rated current
Display
Operating power
Reset method
Installation / Mounting method
Current
Tolerance Time
4~20mA output
Time setting
Startup delay
Operation delay
Composition
Aux. contact
Capacity
ZCT Input
Service environment
Insulation resistance
Lightning impulse voltage
Fast transient
Power consumption
Automatic
Manual
Contact minimum load
External
Built-in
Service temperature
Storage temperature
Relative humidity
Penetrated / Terminal type
Overcurrent, phase fail, phase unbalance, stall, locked rotor,reverse phase, ground fault (Type option)Instance (Type option)
Penetrated / Terminaltype
Thermal heat build-up inverse time / Non-thermal heat build-up inverse time / Definite time
0.5~6A/5~65A(Rating option upon placing an order)
4 digit, 7-Segment
AC/DC 85~260V(50Hz/60Hz)
1~20min (only for overcurrent)
(Electrical reset)
Display can be installed separately, 35mm DIN rail / Screw installation
±3%
±5%
±5%
1~200sec
1~60sec
3-SPST(Power supply 1a1b, i nstantaneous operation 1a) Note1)
3A/250VAC Resistive Load
100mA / 6VDC : (95-996, 97-98)
10mA / 5VDC ( 07-08)
200mA/100mV(Exclusive ZCT) Note2)
Support (Separate connection unnecessary Note2)
-20℃ ~ 60℃
-30℃ ~ 70℃
Below 50% RH (Without condensation)
100MΩ/500VDC
1.2X50us 5kV Prototype waveform supply
2kV/1Min
Below 2W
Note 1. See No. 21 to 23 of A-Group in Setting menu If single phase is set, the device measures R/S/T phase. In HMI, the maximum phase of three phases is displayed without any indication of phase.
2. It is used when zero current detection type is selected.
3. This product is used to protect a low-voltage motor with 1000V or less
Model numbering system
DMP 06i S Z I M 12 2a1b
Rated current
06i 0.5~6A
65i 5~65A
Connection method
S Terminal type
T Penetrated type
Ground fault
Z
-
B
None
External ZCT
Built-in ZCT
Additional function
Alarm
I + Instance
Note) “-” models have
Alarm + Operating Time
+ Failure History storage functions as the default.
“I” models have an additional instance protection function.
Communication
None
M RS485 MOD
A 4~20mA
Operating voltage
12 AC/DC85~260V
Auxiliary contact
2a1b
LSIS Co.,Ltd.
15
Operation & setting method
Display Explanation
Digital display
Phase display
Up button
Unit display
Load factor graph
Test / Reset button
Down button
Enter button
Type
Display
Button
16 Electronic Motor Protection Relays
Item
R S T N
Description
Display of R, S, T, or N phase
4 digit 7-segment
Display of a variety of information
(numbers, text)
BAR GRAPH Display of load factor (%) 50% ~ 120%
Remarks
If fixed, flickering
If 120% or more, flickering
In communication, flickering C
%
Display of communication status (C)
Load factor (%) display unit Depending on lighting status
A
TEST/RESET
ENTER
UP
DOWN
Current (A) display unit
Access TEST Mode and Release TRIP,
Go to the top of menu
Access Menu and Change &
Save Setting Values
Go to Items (Measurement Value, Group,
Menu, Parameter Increase)
Go to Items (Measurement Value, Group,
Menu, Parameter Decrease)
Display of information
DMPi Series
Operation & setting method
Before starting the motor, the following setting should be completed.
1. Check the test / Reset button.
1) First, check whether the connection method is appropriate. (Refer to the section on the connection method.)
2) Press the Test/Reset button once. ‘Test’ will be shown on the display and the device will be tripped.
3) When the Test/Reset button is pressed one more time during the device Trip, the display will be switched to the operating mode and the device will be reset for normal operation.
Note) To prevent trip failures, the system is designed to prevent operation of the Test/Reset button when the motor is running.
Note) Setup and setting values may change during the motor operation. Thus, please be cautious.
2. Setting method
1) Press Enter from the current display screen, and will appear on the screen. Use the Up or Down button to choose a group that
you want and press Enter to display a menu on the chosen group. Press the Test/Reset button again to return to the current display screen.
2) The first menu will be displayed in relation to the selected group. Use the Up or Down button to choose a menu that you want and press Enter.
The screen on setting values will be displayed. Press the Test/Reset button to display the group selection mode
Note) Start menu may vary according to the model specifications.
3) If you press the Up or Down button from the screen on setting values,
will appear on the screen. Here, use the Up or Down
button to change the value to P-00 and press Enter to return to the screen on setting values. The setting value will flicker and can be
changed with the Up or Down button.
After setting the value, press Enter. The value will be saved and the flicking values will be switched off.
4) With it switched on, press Enter to proceed to the next menu or press the Test/Reset button to go back to the previous menu.
Related menus can be set with the same procedure.
Note) Password insertion (P-00) is performed only once when changing the setting values. When no changes are made for 10 minutes, it can be re-inserted and changed.
Note) With it switched on, press Enter to proceed to the next menu or press the Test/Reset button to go back to the previous menu. Related menus can be set with the same procedure.
Note) When power is supplied for the first time or after power failure, the date information must be inserted at b-gr 4,S-d.
3. How to check the failure history
1) 1) Press the “Down + Up” buttons at the same time and the latest cause of a failure will be displayed on the screen.
Note) When there is no failure history, it will be displayed as “non”.
2) When saving more than 2 failure cases, use the Up or Down button to check any Event that you want. Then press Enter from the Event
display to view the details on the failure causes.
Note) There may be differences in details displayed according to the failure cause.
Note) 5 causes of Trip in total are saved and when it exceeds 5 cases, the previous data are deleted for storage.
4. Operating time setting
1) B group
When A group
is used for time setting (10~8,760). After the set operating time has elapsed, Trip state will be displayed with OrH.
is set with OrH, 07-08 contact will be output.
5. Total operating time and operating time check
1) Total operating time can be checked from B group ,
2) Operating time can be checked from B group,
Note) When no current flows in the motor, the operating time will be displayed as 0.
which is displayed in the following order: day/hour/minute.
which is displayed in the following order: hour/minute.
Note) The total operating time is saved every 10 minutes. When turned off, any value less than 10 minutes will be reset.
6. Heat quantity reset (The motor’s heat quantity is reset by force to switch to the cold mode.)
1) When the operating characteristics of A Group 2.CHA are set in the thermal heat build-up mode (th)
2) When the Test/Reset key is pressed under overload trip to return and then a motor is driven right away, the motor will be hot.
Thus, trip is immediately performed.
3) On the other hand, when the Enter + Test / Reset keys are pressed simultaneously under overcurrent trip to return
and then a motor is driven right away, the motor will be cold. Thus, trip will be executed after the set time.
LSIS Co.,Ltd.
17
Operation & setting method
7. Three-phase current circulation display
1) Three-phase operating current that automatically circulates is displayed at intervals of 2 seconds.
2) To view a specific phase on the circulation display, press Enter in relation to such phase for 2 seconds. The phase will flicker and be displayed.
3) If you want to display the circulating three-phase current again, use the Up or Down key to cancel the state for circulation display.
Menu configuration
R
S
T
N
C
%
A
120%
50%
R
S
T
N
C
%
A
120%
50%
R
S
T
N
C
%
A
120%
50%
Current Circulation Display
R
S
T
N
Current R
R
S
T
N
Current S
R
S
T
N
Current T
※ It is displayed cyclically every 2 seconds.
Cyclic display by key operation
R
S
T
N
C
%
A
120%
50%
R
S
T
N
C
%
A
120%
50%
※ Password window popup when changing
R
S
T
N
C
%
A
120%
50%
R
S
T
N
R
S
T
N
Flashing
120% C
%
A
50%
CORRECT
Flashing
120% C
%
A
50%
R
S
T
N
Flashing
C
%
A
120%
50%
※ After saving, it lights after input
Information display
Display information
Failure information
Alarm information
Selfdiagnosis information
18 Electronic Motor Protection Relays
Failure state
Overcurrent
Lock
Stall
Phase fail
Phase unbalance
Reverse phase
Under current
Ground fault (ZCT)
Instance
Set operating time has elapsed
Display communication error
External memory error
Additional display information
Fault current (R-phase, S-phase and T-phase)
Load factor, time
Fault current (R-phase, S-phase and T-phase)
Load factor, time
Fault current (R-phase, S-phase and T-phase)
Load factor, time
Fault current (R-phase, S-phase and T-phase)
Load factor, time
R-phase, S-phase and T-phase,
Unbalance factor, time
Time
Fault current (R-phase, S-phase and T-phase)
Load factor, time
Fault current (R-phase, S-phase and T-phase)
N-phase, time
Fault current (R-phase, S-phase and T-phase)
Load factor, time
An alarm is displayed if a cumulative running time excesses a set running time
When a communication error occurs between the display and body, please contact our office with the alarm maintained.
When there is an error in the backup memory, please contact our office with the alarm maintained.
Remarks
Operates at the set time
Operates within 0.5sec
Operates in 3sec
Operates in 3sec
(Delay time setting needed)
Ooperates in 5 sec
(Delay time setting needed)
Operates at the set time
Operates in 3sec
Operates at the set time
(Delay time setting needed)
Operate within 50ms
(Delay time setting needed)
Measuring Group Menu Parameter
DMPi Series
A-Group
Group
A
Display
CT Ratio
LOCK
STALL
Setting item
Single phase/Three-phase
Operating characteristic
(Overcurrent protection)
Operating time
Delay time
Rated current(6, 65)
Phase fail(100%)
Phase fail delay time
Phase unbalance
Phase unbalance delay time
Phase unbalance delay time
Phase unbalance delay time
Phase unbalance delay time
Setting value(Display value)
1P/3P dEF/n-th/th
1~60sec
1~200sec
Note2)
0.5~6A/5~65A
0.25/0.5/1~200
Off/200~800%
Off/150~500%
On/Off
0~200
Off/10~90%
0~200
Off/On Note5)
0.1~1.0
Off/30~90%
Note3)
-
-
O
-
-
O
O
O
O
O
O
Single phase Default
1P
O
3P n-th
60
200
6/65
1
Remarks
Note4)
Displayed upon 2.CHA dEFT setting
Maximum rated current display
(06i: 6A, 65i: 65A)
On
0
Off
Off
-
Off
0
Off
0.1
Off
Displayed upon 9.P-F setting
Displayed upon 10.PU setting
Displayed upon 13.rP setting
Phase unbalance delay time
Phase unbalance delay time
Off/0.03/0.05/0.1~3.0A
0.05, 0.1~5.0sec
O
O
Off
1
Displayed upon 16.gF setting
Phase unbalance delay time
Phase unbalance delay time
0~200sec
Off/500~1500% Note6)
0~200
O
O
200
Off
Phase unbalance delay time
Phase unbalance delay time
Phase unbalance delay time
2a, 1a1b, 2b
I-tp, I-AL, ALo, U-C, OrH, g-F Note7)
O
O
O
0
1a1b
I-tp
Phase unbalance delay time On/60~110% O
Note) 1. When setting A group 1.PHA menu with 1P, restricted setting with limited functions can be made.
2. Operating characteristic th refers to the thermal heat build-up inverse time characteristic and n-th refers to the non-thermal heat build-up inverse time characteristic. When th is used, the quantity of heat generated will be reset as power is turned off. Thus, please pay attention to it.
3. CT Ratio is fixed to 1 for 65A Type model.
4. Some menus will not be displayed depending on the function setting for each model.
5. Reverse phase will be detected for only 1.5 seconds after load is activated. It is recommended to set as Off for a motor not in normal-reverse operation.
6. In case of ‘Instance’, the maximum setting value may change according to the rated current setting.
7. For models with ground fault and instance protection functions, the ground fault and instantaneous trip contacts may be separately set for use.
On
Displayed upon 16.gF setting
Displayed upon 19.IC setting
Displayed upon 22.AL Alo setting
LSIS Co.,Ltd.
19
Operation & setting method
The output conditions of 95-96, 97-98 output contacts depending on the setting of A group 21.cS are as described below.
21.cS Setting
1a1b
2a
2b
주) NC: Normal Close, NO: Normal Open, O: Open, C: Close
Output conditions
Normal operation
Ground fault / Short circuit
Other failures, such as overcurrent, phase fail and reverse phase other than the ground fault
Normal operation
Ground fault/Short circuit
Other failures, such as overcurrent, phase fail and reverse phase other than the ground fault
Normal operation
Ground fault/Short circuit
Other failures, such as overcurrent, phase fail and reverse phase other than the ground fault
The output conditions of 07-08 output contacts depending on the setting of A group 22.AL are as described below.
Contact output type
95–96
NC Note)
97–98
NO Note)
O Note)
O
NO
O
C
NC
C
O
C Note)
C
NO
C
O
NC
O
C
23.Ar setting
I-tp
I-AL
U-C
OrH g-F
ALo
23.Ar setting
On
60~110%
Momentary current detected
Momentary current detected
Current flow below the set low current detected
Output exceeding the set operating time
Ground fault detection
Output conditions
Conforming to the 23.Ar setting described below
ALo setting from menu No.22
Current flow exceeding the measured minimun current value detected
Current flow exceeding the setting value
Note) The measured minimum current value is 30% of the minimum rated current value (0.15A for 0.6i type; 1.5A for 65i type)
Note)
Alarm output type
Motor operation
Motor stop
State maintained
State maintained
State maintained
Motor stop
07–08
C
C
C
C
C
Motor operation
State maintained
State maintained
07–08
C
C
B-Group
Group
B
Display Setting item
Total operating time
Operating time
Operating time setting
Date setting Note2)
Automatic reset Note3)
Communication network address
Communication speed
Swap On/Off
Setting value (Display value)
0~9999day/0~23Time/0~59min
0~9999 Time/0~59min
Off/10~8760
2017~2100yea/1~12month/1~31day/
0~23hour/0~59min
Off/1~20min
1~247
9.6k/19.2k/38.4k/56.7k
Single phase
Note1)
O
O
O
O
O
O
O
Default
-
-
Off
2017.07.01
00:00
Off
247
9.6k
Remarks
Note4)
Displayed only for
M485 model
On/Off O Off
Parity setting nonE/odd/EUEn O nonE
20mA setting 0.5~6/5~65 O 6/65
Note) 1. It can be set even when A group 1.PHA is set with the single phase (1P).
2. When power is supplied for the first time or after power failure, date must be set. For date setting, month, day, hour and minute should be respectively set for complete setting.
(After date setting, it is saved every 10 minutes. When power is supplied again after power failure, the date before such power failure will be saved.)
3. Automatic reset is restricted for overcurrent trip.
4. Menus vary according to the model. (refer to the remarks)
Displayed only for A420 model
20 Electronic Motor Protection Relays
DMPi Series
T
N
R
S
T
N
R
S
T
N
R
S
T
N
R
S
T
N
R
S
T
N
R
S
T
N
R
S
T
N
R
S
T
N
R
S
T
N
R
S T
N
R
S
T
N
R
S
T
N
R
S
T
N
R
S
T
N
R
S
T
N
R
S
T
N
R
S
T
N
R
S
T
N
R
S
T
N
R
S
T
N
R
S
T
N
R
S
T
N
R
S
T
N
R
S
Phase setting
This is a function tdo set current input either as single or three-phase.
T
N
R
S
T
N
R
S
T
N
R
S
T
N
R
S
T
N
R
S
T
N
R
S
C
C
A
120%
50%
50%
The DMPi main screen display (0.00A)
T
N
R
S
T
N
R
S
T
N
R
S
T
N
R
S T
N
R
S
T
N
R
S
C
C
A
120%
50%
1. Press Enter from the main screen. (A-gr)
C
C
A
120%
50%
2. Press Enter from the A-gr screen. (1. PHR)
C
%
A
120%
50%
C
%
A
120%
50%
C
%
A
120%
50%
3. Press Enter from the PHR screen and the initial value 3P will be displayed.
4. Here, use the Up / Down key to display P-99 from the screen. Change it into P-00 with the
Up/Down key and press Enter. You are now ready for setting. (Only required for initial setting)
T
N
R
S
T
N
R
S
T
N
R
S
T
N
R
S
T
N
R
S
T
N
R
S
C
%
A
120%
50%
5. The set value flickers. Use the Up / Down key to display ‘phase’ that is applicable depending on the motor specifications
(1P: single-phase; 3P: three-phase). Then, press Enter to save the setting. (1P)
① Choose either 1P or 3P; the default is 3P
② When 1P is selected, A group items such as “9.P-F”, “10.Pd”, “11.PU”, “12.Ud”, “13.rP” and
“14.rt” are excluded from the setting menu.
6. Press Test / Reset to return to the display screen.
Rated current setting
This is a function to set a rated current.
T
N
R
S
T
N
R
S
T
N
R
S
T
N
R
S
T
N
R
S
T
N
R
S
T
N
R
S
T
N
R
S
T
N
R
S
T
N
R
S
T
N
R
S
T
N
R
S
T
N
R
S
T
N
R
S
T
N
R
S
T
N
R
S
T
N
R
S
T
N
R
S
C
%
A A
A
C
C
%
50%
50%
C
C
%
120%
50%
50%
The DMPi main screen display (0.00A)
1. Press Enter from the main screen. (A-gr)
2. Press Enter from the A-gr screen. (1. PHR)
T
N
R
S
T
N
R
S
T
N
R
S
T
N
R
S
T
N
R
S
T
N
R
S
C
C
%
120%
50%
3. Press the Up-key menu 3 or 4 times from the PHR screen. (5.r-C)
T
N
R
S
T
N
R
S
T
N
R
S
T
N
R
S
T
N
R
S
T
N
R
S
C
%
%
120%
50%
4. Press Enter from the 5.r-C screen and the initial value 6.0A will be displayed.
T
N
R
S
T
N
R
S
T
N
R
S
T
N
R
S
T
N
R
S
T
N
R
S
C
C
%
120%
50%
5. Here, use the Up / Down key to set the value as 0.5~6.0A. Then, press Enter to save the setting.
① 6A model: Set by 0.1A unit ranging from 0.5A to 6A (the default is 6.0A)
② 65A model: Set by 1A unit ranging from 5A to 65A (the default is 65A)
6. Press Test / Reset to return to the display screen.
Note 1) Upon initial setting, P-99 is displayed on the screen. Here, use the Up / Down key to change it into P-00 and press Enter. You are now ready for setting.
Note1) (6.0 5.4A)
LSIS Co.,Ltd.
21
Operation & setting method
Overcurrent operating characteristic setting
This is a function to set the operating characteristic of the overcurrent element.
T
N
R
S
T
N
R
S
T
N
R
S
T
N
R
S
T
N
R
S
T
N
R
S
T
N
R
S
T
N
R
S
T
N
R
S
T
N
R
S
T
N
R
S
T
N
R
S
T
N
R
S
T
N
R
S
T
N
R
S
T
N
R
S
T
N
R
S
T
N
R
S
T
N
R
S
T
N
R
S
T
N
R
S
T
N
R
S
T
N
R
S
T
N
R
S
T
N
R
S
T
N
R
S
T
N
R
S
T
N
R
S
T
N
R
S
T
N
R
S
T
N
R
S
T
N
R
S
T
N
R
S
T
N
R
S
T
N
R
S
T
N
R
S
C
%
C
%
C
%
%
A
C
%
C
%
A
C
%
C
%
C
%
%
A
C
%
C
%
A
A
A
C
%
C
%
C
%
C
%
A
50%
50%
50%
50%
50%
50%
50%
50%
The DMPi main screen display (0.00A)
1. Press Enter from the main screen. (A-gr)
2. Press Enter from the A-gr screen. (1. PHR)
3. Press the Up-key menu once from the PHR screen. (2.CHA)
4. Press Enter from the 2.CHA screen to display ‘n-th’ (initial value).
5. The set value flickers. Use the Up / Down key to display the set value. Note1)
6. Press Enter for dEF setting.
① dEF (definite time), n-th (non-thermal heat build-up inverse time) or th (thermal heat build-up inverse time)
② When set as ‘n-th’ or ‘th’, “4.d-t” of the A group items is excluded from the setting menu.
7. Press Test / Reset to return to the display screen.
Note 1) Upon initial setting, P-99 is displayed on the screen. Here, use the Up / Down key to change it into P-00 and press Enter. You are now ready for setting.
Overcurrent operating time setting
This is a function to set the operating time of the overcurrent element.
T
N
R
S
T
N
R
S
T
N
R
S
T
N
R
S
T
N
R
S
T
N
R
S
T
N
R
S
T
N
R
S
T
N
R
S
T
N
R
S
T
N
R
S
T
N
R
S
T
N
R
S
T
N
R
S
T
N
R
S
T
N
R
S
T
N
R
S
T
N
R
S
T
N
R
S
T
N
R
S
T
N
R
S
T
N
R
S
T
N
R
S
T
N
R
S
T
N
R
S
T
N
R
S
T
N
R
S
T
N
R
S
T
N
R
S
T
N
R
S
T
N
R
S
T
N
R
S
T
N
R
S
T
N
R
S
T
N
R
S
T
N
R
S
C
%
A
%
A
C
C
A
%
A
C
%
A
%
A
C
C
A
%
A
C
C
%
C
%
A
A
A
C
%
A
%
A
50%
50%
50%
120%
120%
50%
120%
50%
120%
50%
120%
50%
120%
50%
The DMPi main screen display (0.00A)
1. Press Enter from the main screen. (A-gr)
2. Press Enter from the A-gr screen. (1. PHR)
3. Press the Up-key menu twice from the PHR screen. (3.O-t)
4. Press Enter and the initial value 60sec will be displayed.
5. Use the Up / Down key to display the set value on the screen. Note1)
6. Press Enter to set as 30sec. (60 ⇒ 30 sec)
7. Press Test / Reset to return to the display screen.
Note 1) Upon initial setting, P-99 is displayed on the screen. Here, use the Up / Down key to change it into P-00 and press Enter. You are now ready for setting.
22 Electronic Motor Protection Relays
DMPi Series
Overcurrent delay time setting
T
N
R
S
T
N
R
S
T
N
R
S
T
N
R
S
T
N
R
S
T
N
R
S
T
N
R
S
T
N
R
S
T
N
R
S
T
N
R
S
T
N
R
S
T
N
R
S
T
N
R
S
T
N
R
S
T
N
R
S
T
N
R
S
T
N
R
S
T
N
R
S
T
N
R
S
T
N
R
S
T
N
R
S
T
N
R
S
T
N
R
S
T
N
R
S
T
N
R
S
T
N
R
S
T
N
R
S
T
N
R
S
T
N
R
S
T
N
R
S
T
N
R
S
T
N
R
S
T
N
R
S
T
N
R
S
T
N
R
S
T
N
R
S
This menu is displayed only when the overcurrent operating characteristic is set as dEF (definite time).
C
C
A
%
A
C
C
A
%
A
C
C
A
%
A
C
C
A
%
A
C
%
A
%
A
C
%
C
%
C
%
%
A
A
A 50%
50%
50%
120%
120%
50%
120%
50%
120%
50%
120%
50%
120%
50%
The DMPi main screen display (0.00A)
1. Press Enter from the main screen. (A-gr)
2. Press Enter from the A-gr screen. (1. PHR)
3. Press the Up-key menu 3 times from the 1.PHR screen. (4.d-t)
4. Press Enter from the 4.d-t screen and the initial value 200 will be displayed.
5. Use the Up/Down key to display the set value on the screen. Note1)
6. Press Enter to set as 100sec. (200 100sec)
① Set by 1sec unit ranging from 1 sec to 200sec; the default is 200sec.
② When the overcurrent operating characteristic is set as ‘n-th’ or ‘th’, it is excluded from the setting menu.
7. Press Test/Reset to return to the display screen.
Note 1) Upon initial setting, P-99 is displayed on the screen. Here, use the Up/Down key to change it into P-00 and press Enter. You are now ready for setting.
Ground fault operating value setting
This is a function to set the operating value of ground fault.
T
N
R
S
T
N
R
S
T
N
R
S
T
N
R
S
T
N
R
S
T
N
R
S
T
N
R
S
T
N
R
S
T
N
R
S
T
N
R
S
T
N
R
S
T
N
R
S
C
C
%
C
%
A A
A 50%
50%
The DMPi main screen display (0.00A)
1. Press Enter from the main screen. (A-gr)
T
N
R
S
T
N
R
S
T
N
R
S
T
N
R
S
T
N
R
S
T
N
R
S
T
N
R
S
T
N
R
S
T
N
R
S
T
N
R
S
T
N
R
S
T
N
R
S
C
C
%
120%
50%
50%
C
C
%
120%
50%
2. Press Enter from the A-gr screen. (1. PHR)
3. Press the Up-key menu from the 1.PHR screen to proceed to 16.gF.
T
N
R
S
T
N
R
S
T
N
R
S
T
N
R
S
T
N
R
S
T
N
R
S
T
N
R
S
T
N
R
S
T
N
R
S
T
N
R
S
T
N
R
S
T
N
R
S
C
%
%
120%
50%
C
C
%
120%
50%
4. Press Enter from the 16.gF screen and the initial value OFF will be displayed.
5. Here, use the Up/Down key to set the value. Press Enter to save the setting.
Note1) (OFF
6. Press Test / Reset to return to the display screen.
Note 1) Upon initial setting, P-99 is displayed on the screen. Here, use the Up/Down key to change it into P-00 and press Enter. You are now ready for setting.
0.1A)
① Set by 0.1A unit ranging from 0.1A to 3.0A; or OFF, 0.03A, or 0.05A. (the default is OFF)
LSIS Co.,Ltd.
23
Operation & setting method
Ground fault operating time setting
This is a function to set the operating time of ground fault.
T
N
R
S
T
N
R
S
T
N
R
S
T
N
R
S
T
N
R
S
T
N
R
S
C
%
A A
A 50%
50%
The DMPi main screen display (0.00A)
T
N
R
S
T
N
R
S
T
N
R
S
T
N
R
S
T
N
R
S
T
N
R
S
C
%
% 1. Press Enter from the main screen. (A-gr)
T
N
R
S
T
N
R
S
T
N
R
S
T
N
R
S
T
N
R
S
T
N
R
S
T
N
R
S
T
N
R
S
T
N
R
S
T
N
R
S
T
N
R
S
T
N
R
S
C
C
%
C
C
%
2. Press Enter from the A-gr screen. (1. PHR)
3. Press the Up-key menu from the 1.PHR screen to proceed to 17.gt
T
N
R
S
T
N
R
S
T
N
R
S
T
N
R
S
T
N
R
S
T
N
R
S
C
%
%
4. Press Enter from the 17.gt screen and the initial value 1.0sec will be displayed.
T
N
R
S
T
N
R
S
T
N
R
S
T
N
R
S
T
N
R
S
T
N
R
S
C
C
%
5. Here, use the Up / Down key to set the value. Press Enter to save the setting. Note1)(1.0
① Set by 0.1sec unit ranging from 0.1sec to 5.0sec; the default value is 1.0sec.
6. Press Test / Reset to return to the display screen.
Note 1) Upon initial setting, P-99 is displayed on the screen. Here, use the Up/Down key to change it into P-00 and press Enter. You are now ready for setting.
Note 2) When the operating value of ground fault protection (16.gF) is set as OFF, it is excluded from the setting menu.
0.1sec)
Ground fault delay time setting
This is a function to set time for blocking operation of the ground fault element upon motor activation.
T
N
R
S
T
N
R
S
T
N
R
S
T
N
R
S
T
N
R
S
T
N
R
S
C
%
A A
A 50%
50%
The DMPi main screen display (0.00A)
T
N
R
S
T
N
R
S
T
N
R
S
T
N
R
S
T
N
R
S
T
N
R
S
C
C
% 1. Press Enter from the main screen. (A-gr)
T
N
R
S
T
N
R
S
T
N
R
S
T
N
R
S
T
N
R
S
T
N
R
S
C
C
%
2. Press Enter from the A-gr screen. (1. PHR)
T
N
R
S
T
N
R
S
T
N
R
S
T
N
R
S
T
N
R
S
T
N
R
S
C
C
%
3. Press the Up-key menu from the 1.PHR screen to proceed to 18.gd.
T
N
R
S
T
N
R
S
T
N
R
S
T
N
R
S
T
N
R
S
T
N
R
S
C
%
%
4. Press Enter from the 18.gd screen and the initial value 200sec will be displayed.
T
N
R
S
T
N
R
S
T
N
R
S
T
N
R
S
T
N
R
S
T
N
R
S
C
C
%
5. Here, use the Up / Down key to set the value. Press Enter to save the setting.
① Set by 1sec unit ranging from 0sec to 200sec; the default value is 200sec.
Note1) (200
6. Press Test / Reset to return to the display screen.
Note 1) Upon initial setting, P-99 is displayed on the screen. Here, use the Up/Down key to change it into P-00 and press Enter. You are now ready for setting.
Note 2) When the operating value of ground fault protection (16.gF) is set as OFF, it is excluded from the setting menu.
100sec)
24 Electronic Motor Protection Relays
Terminal Configuration / Wiring & cable connection
DMPi Series
Terminal Configuration
DMP06i
FAULT
A+ NC A95 96 97 98 07 08 ZCT+ ZCT- TRX+ TRX-
Engrave
A+, A-
95-96
97-98
07-08
ZCT+, ZCT-
TRX+, TRX-
420+, 420-
Description
Input terminal for operation power
When the power is ON (NC contact output)
When the power is ON (NO contact output)
Alarm contact output terminal
ZCT output connection
RS485 connect or 4~20mA output
DMPi-B built-in ground fault protection type
(1a1b)
DMPi-SB/TB
Operating
Power
A+ A-
Single pase motor
LSIS Co.,Ltd.
25
Terminal Configuration / Wiring & cable connection
DMPi-B built-in ground fault protection type
(2a)
DMPi-SB/TB
A+ A-
DMPi-B built-in ground fault protection type
(2b)
DMPi-SB/TB
A+ A-
26 Electronic Motor Protection Relays
DMPi-SBI / TBI, SI / TI built-in instant short-circuit protection type
(1a1b)
DMPi-SBI/TBI
DMPi-SI/TI
DMPi Series
A+ A-
DMPi-SZ / TZ external ground fault protection type
(1a1b)
DMPi-SZ/ TZ
Operating
Power
A+ A-
ZCT
Note) 1. R-phase must be penetrated when connecting a single-phase motor. (Although there are S, T-phase CT in the product, values are measured based on R-phase.)
ZCT
Single pase motor
Note)
LSIS Co.,Ltd.
27
Terminal Configuration / Wiring & cable connection
DMPi-SZ / TZ external ground fault protection type
(1a1b large-capacity motor applied with external CT)
DMPi-SZ/ TZ
A+ A-
ZCT
DMPi-SZ / TZ external ground fault protection type
(2a)
DMPi-SZ/TZ
A+ A-
28 Electronic Motor Protection Relays
ZCT
DMPi Series
DMPi-SZ / TZ external ground fault protection type
(1a1b large-capacity motor applied with external CT)
DMPi-SZ / TZ external ground fault protection type
(2b)
DMPi-SZ / TZ
A+ A-
ZCT
DMPi-SZI, TZI instant short-circuit protection and external ground fault protection type
(1a1b)
DMPi-SZ/ TZI
A+ A-
ZCT
LSIS Co.,Ltd.
29
Terminal Configuration / Wiring & cable connection
DMPi-SZI, TZI instant short-circuit protection and external ground fault protection type
(1a1b large-capacity motor applied with external CT)
DMPi-SZ/ TZI
A+ A-
ZCT
30 Electronic Motor Protection Relays
Dimensions
Integrated terminal type
Separated terminal type
M4
M4
76
68
76
68
76
68
M4
13.6
82 (Attached size)
89
13.6
82 (Attached size)
89
1
1
2.6
13.6
82 (Attached size)
89
5
1
2.6
5
2.6
5
41
41
M4
M4
41
76
68
76
68
76
68
Panel insertion
M4
13.6
82 (Attached size)
89
13.6
82 (Attached size)
89
1
1
2.6
13.6
82 (Attached size)
89 5
1
2.6
5
2.6
5
41
41
76
41
76
76
1.1
19
1.1
19
44.6
44.6
1.1
19 44.6
DMPi Series
M4
Unit : mm 76
76
M4
M4
76
82 (Attached size)
89
82 (Attached size)
89
1
1
1
82 (Attached size)
89
2.6
2.6
5
5
∅
12
2.6
∅
12
41
41
5
∅
12
41
76
76 M4
M4
76
M4
2.6
2.6
82 (Attached size)
89
82 (Attached size)
89
1
1
82 (Attached size)
89
5
1
5
2.6
5
41
41
41
55.5 (Cutting size)
55.5 (Cutting size)
55.5 (Cutting size)
76
76
76
LSIS Co.,Ltd.
31
M4
M4
Dimensions
76
68
76
68
Integrated penetration type
2.6
2.6
13.6
82 (Attached size)
89
13.6
82 (Attached size)
89
1
1
5
5
41
41
76
68
M4
76
M4
76
M4
13.6
82 (Attached size)
89
89
82 (Attached size)
89
1
1
2.6
2.6
2.6
∅ 12 41
∅
12
41
41
5
5
5
76
68
M4
M4
2.6
2.6
13.6
82 (Attached size)
89
13.6
82 (Attached size)
89
1
1
5
5
76
76
41
41
76
68
76
68
Separated penetration type
1.1
19 44.6
1.1
19 44.6
M4
M4
M4
76
76
Panel insertion
55.5 (Cutting size)
55.5 (Cutting size)
2.6
13.6
1
82 (Attached size)
89
82 (Attached size)
89
1
1
82 (Attached size)
89
5
2.6
5
2.6
41
5
76
41
41
1.1
19 44.6
32 Electronic Motor Protection Relays
76
76
55.5 (Cutting size)
76
M4
76
Unit : mm
82 (Attached size)
89
1
2.6
∅
12
41
5
M4
2.6
76
82 (Attached size)
89
1
41
5
MEMO
DMPi Series
LSIS Co.,Ltd.
33
motor protection relay!
With smart protection and safe control, we provide the cutting-edge digital total solution.
34 Electronic Motor Protection Relays
GMP Series
GMP Series
Electronic Motor Protection Relays
• Definite/inverse time protection of a variety of rating
• Ground fault protection model
• LED based display of failure cause
• MC direct coupling, penetration, and terminal types sharing
K R
KO
RE
EG
ISTER OF SH IP
PI
N
C o n t e n t s
36 A list of standard models
37 Product characteristics
38 Rated specifications / Order type
47 Motor selection / Model numbering system
48 Operation & setting method
53 Terminal Configuration / Wiring & cable connection
56 Dimensions
LSIS Co.,Ltd.
35
A list of standard models
Rated current
0.3~1.5
1~5
4.4~22A
4~20
8~40A
0.5~6
3~30
5~60A
0.5~60A
Connection method
Pin type note 1)
Screw type
Tunnel types
Pin type note 1)
Screw type
Tunnel types
Tunnel types
Type name
GMP22-2P Sol
GMP22-2PD Sol
GMP22-2P Sol
GMP22-2PA Sol
GMP22-3P Sol
GMP22-3PR Sol
GMP22-2S
GMP22-3S
GMP22-3SR
GMP22-2T
GMP22-3T
GMP22-3TR
GMP40-2PD Sol
GMP40-2P Sol
GMP40-2PA Sol
GMP40-3P Sol
GMP40-3PR Sol
GMP40-2S
GMP40-3S
GMP40-3SR
GMP40-2T
GMP40-3T
GMP40-3TR
GMP60T
GMP60TE
GMP60TA
GMP60TD
GMP60TDa overcurrent
●
●
●
Locked rotor
●
●
●
Phase failure
●
●
●
Phase unbalance
Reverse phase low current
-
-
- -
-
-
-
-
-
Ground
Fault
-
-
-
● ● ● - - - -
●
●
●
●
●
●
●
●
●
●
●
●
●
●
●
●
●
●
●
●
●
●
●
●
●
●
●
●
●
●
●
●
●
●
●
●
●
●
●
●
●
●
●
●
●
●
●
●
●
●
●
●
●
●
●
●
●
●
●
●
●
●
●
●
●
●
●
●
●
●
●
●
-
●
●
●
●
●
-
●
●
●
-
●
-
-
-
●
-
-
●
-
●
-
-
-
●
-
-
●
-
-
-
-
-
●
-
-
-
-
-
-
●
-
●
-
●
-
-
-
-
-
-
-
-
-
-
-
-
-
-
-
●
-
-
-
-
-
-
-
-
-
-
-
-
-
-
-
-
-
-
-
-
-
-
-
-
-
-
-
-
-
-
-
-
-
-
-
0.5~60A
0.5~
60A 주3)
Tunnel types
Screw type
GMP60-3T
GMP60-3TR
GMP60-3TZ 주2)
GMP60-3TN
GMP60-3TZR
GMP60-3TNR
GMP60-3S
GMP60-3SR
GMP60-3SZ
GMP60-3SN
GMP60-3SZR
GMP60-3SNR
GMP80-2S
●
●
●
●
●
●
●
●
●
●
●
●
●
●
●
●
●
●
●
●
●
●
●
●
●
●
●
●
●
●
●
●
●
●
●
●
●
●
●
●
●
●
●
●
●
●
●
●
-
●
●
●
-
●
●
-
-
●
-
●
●
-
●
-
-
-
-
-
-
-
-
-
-
-
-
-
-
-
16~80A
GMP80-2SA ● ● ● - - -
GMP80-3S
GMP80-3SR
●
●
●
●
●
●
●
●
-
●
-
-
Note) 1. Direct coupling type (Pin) supports direct coupling of Metasol MC. With your order, it is required to describe “Sol”.
2. For GMP60-3TZ/3TZR, use ZCT (100mA/40~55mV) for EMPR only.
3. In case of GMP60-3S Series, it is required to purchase a terminal block separately.
4. This product is designed for protecting a low-voltage motor with 1,000V or less. Therefore, it should not be used in high voltage lines.
-
-
-
36 Electronic Motor Protection Relays
●
-
●
●
-
-
●
●
●
-
-
●
●
Characteristic
Definite time
Definite time
Definite time
Definite time
Definite time
Definite time
Definite time
Definite time
Definite time
Definite time
Definite time
Definite time
Inverse time
Inverse time/
Automatic return
Inverse time
Inverse time
Inverse time
Inverse time
Inverse time
Inverse time
Inverse time
Inverse time
Inverse time
Inverse time
Inverse time
Inverse time
Definite time/
Automatic return
Definite time
Definite time/
Automatic return
Inverse time
Definite time
Inverse time
Definite time/
Automatic return
Inverse time
Inverse time
Inverse time
Inverse time
Inverse time
Inverse time
Inverse time
Inverse time
Definite time
Inverse time
Inverse time/
Automatic return
MCU MCU
Product characteristics
Slide S/W Slide S/W
GMP Series
Convenience Return
INV
MCU
MCU
MCU
Return
INV
30mA 25A
Slide S/W
INV
Slide S/W
Return
30mA 25A
Save
Total
Reliability
INV
INV
Save
INV
Slide S/W
Slide S/W
Return
Save
Return
30mA 25A
30mA 25A
30mA
MCU
25A
Total
Return
Slide S/W
30mA 25A
MCU
Return
MCU
25A
Return
Total
30mA
Total
25A
Total
INV
Save
Slide S/W
Save
Save
MCU
Save
INV
Slide S/W
Total
Return
30mA 25A
Return
INV
MCU
Return
INV
30mA 25A
Slide S/W
Integrated Digital Motor Protection Relay using MCU(Microprocessor Control Unit)
It offers real time data processing and high precision.
Applicable to invertor circuits
It may be applied to the secondary inverter control circuit with its outstanding resistance to harmonic noise.
(Usable frequency range: 20~200Hz, except for phase reversal model)
Save
Return
Save the last fault cause
At the time of power recover after power failure, it is possible to check the final operation cause.
(Test/Reset Key 2-time operation)Limited to GMP60-3T Series only
30mA
MCU
25A
Sharing of terminal contact type and penetration type
It is possible to detach and attach a terminal block and conveniently apply the product to a variety of installation conditions.
MCU
MCU
INV
EMPR
GMP22-2P/3P/3PR
GMP40-2P/3P/3PR
Contactor model
MC-9b, MC-12b, MC-18b, MC-22
MC-32a, MC-40a
INV
Save
INV
Slide S/W
Slide S/W
Return
Return
30mA 25A
Various Installation Ways
With the uses of screws and brackets for DIN-Rail, it is possible to install 35mm DIN-Rail.
30mA 25A
30mA
MCU
25A
Wide Current Control Range
Since this product has a wide current control range, it is more convenient than thermal overload relays.
~100A
Return
Total
30mA
Total
25A
Total
INV
Save
Slide S/W
Save
Save
Acquired S-Mark (safety certification) first in the industry
What is S-Mark (safety)?
S-Mark is used to approve a product’s safety, reliability, and safe design manufacturing in the way of reviewing the quality management system of its manufacturer.
If a product complies with safety certification standards,
~100A is applied to a product, a product package, or a product
MCU
~100A
Remarkable improvement in the characteristics of Nois
• This product solves the malfunction made by electromagnetic waves and surges which are the biggest problem of digital motor protection relays.
Save
INV
Slide S/W
Total
Inverse time characteristic good for motor protection
Thanks to the inverse time characteristic in which a running time is determined by a size of overcurrent, the product is excellent at motor protection.
~100A
LSIS Co.,Ltd.
37
Return
30mA 25A
Save Save
Total Total
~100A
Rated specifications / Order type
GMP22-2P, 2PD 1c
GMP22-2P(1c)
GMP22-2PD(1c)
Specification (Direct type EMPR)
Connection: Accessible electronic contactors Minimum direct connection with width 44mm : MC-9b, 12b, 18b, 22b
Auxiliary contact 1SPDT 1c (N type) note1)
Current setting range 0.3~1.5/1~5/4.4~22A
Operating time characteristics Inverse time, Definite time (PD)
Number of built-in CT (deflector) 2 (R, T phase)
Operating power
Return (reset) method/time
Using Inverter Secondary
AC 110/220V (±10%)
Manual/Electrical return
Available
Protection
Certification
Type
Overcurrent
Lock/Stall
Phase failure
UL, CE
GMP22-2P (1c) Sol note 2)
GMP22-2PD (1c) Sol note 2)
Contactor
MC-9b, 12b, 18b, 22b
W=44
Contactor
Direct connection
Order type
Type
Pin type
Model/CT
GMP22-2P(1c)
- 2CT type
GMP22-2PD(1c)
- 2CT type
Operating characteristics Current setting range
Inverse time
(0~30sec)
0.3 - 1.5A
1 - 5A
Definite time
D-Time : 0~60sec
O-Time : 5sec(Fixed)
4.4 - 22A
0.3 - 1.5A
1 - 5A
4.4 - 22A
0.3 - 1.5A
1 - 5A
4.4 - 22A
0.3 - 1.5A
1 - 5A
4.4 - 22A
0.3 - 1.5A
1 - 5A
4.4 - 22A
0.3 - 1.5A
1 - 5A
Order type
GMP22-2P(1c) 1.5A Sol
GMP22-2P(1c) 5A Sol
GMP22-2P(1c) 22A Sol
GMP22-2P(1c) 1.5A [N]
GMP22-2P(1c) 5A [N]
GMP22-2P(1c) 22A [N]
GMP22-2P(1c) 1.5A [R]
GMP22-2P(1c) 5A [R]
GMP22-2P(1c) 22A [R]
GMP22-2PD(1c) 1.5A Sol
GMP22-2PD(1c) 5A Sol
GMP22-2PD(1c) 22A Sol
GMP22-2PD(1c) 1.5A [N]
GMP22-2PD(1c) 5A [N]
GMP22-2PD(1c) 22A [N]
GMP22-2PD(1c) 1.5A [R]
GMP22-2PD(1c) 5A [R]
4.4 - 22A GMP22-2PD(1c) 22A [R]
Note) 1. 1c contacts have two types of products: N-type (Fail Safe/Normal Energyed) and R-type(Non Fail Safe / Normal De-Energyed). In terms of product reliability, N-type (Fail Safe) product is recommended to be used.
2. The product detects phase failure of the phase (R, T) connected with two CTs in order for protection.
Technical information
Installation
Tolerance
Frequency
Aux. contact Ratings
Insulation resistance
Lightning impulse voltage
Fast Transient Burst
Environment
Trip indicator
Application specification
Direct connection to contactors (not alone)
Current : ±5%
Time : ±5% (or±0.5sec)
50/60Hz
5A/250VAC Resistive load
Min 100㏁ at 500Vdc
1.2×50㎲ 5kV With standard waveform (IEC1000-4-5)
2kV/5min (IEC1000-4-4)
Operation : -25~70℃
Storage : -30~80℃
Relative humidity : 30~90%RH(No freezing)
Red LED
UL508, IEC60947-1
38 Electronic Motor Protection Relays
Type
Pin type
Model/CT
GMP22-2P(1c)
- 2CT type
GMP22-2PD(1c)
- 2CT type
Operating characteristics Current setting range
Inverse time
(0~30sec)
0.3 - 1.5A
1 - 5A
Definite time
D-Time : 0~60sec
O-Time : 5sec(Fixed)
4.4 - 22A
0.3 - 1.5A
1 - 5A
4.4 - 22A
0.3 - 1.5A
1 - 5A
4.4 - 22A
0.3 - 1.5A
1 - 5A
4.4 - 22A
0.3 - 1.5A
1 - 5A
4.4 - 22A
0.3 - 1.5A
1 - 5A
4.4 - 22A
Order type
GMP22-2P(1c) 1.5A Sol
GMP22-2P(1c) 5A Sol
GMP22-2P(1c) 22A Sol
GMP22-2P(1c) 1.5A [N]
GMP22-2P(1c) 5A [N]
GMP22-2P(1c) 22A [N]
GMP22-2P(1c) 1.5A [R]
GMP22-2P(1c) 5A [R]
GMP22-2P(1c) 22A [R]
GMP22-2PD(1c) 1.5A Sol
GMP22-2PD(1c) 5A Sol
GMP22-2PD(1c) 22A Sol
GMP22-2PD(1c) 1.5A [N]
GMP22-2PD(1c) 5A [N]
GMP22-2PD(1c) 22A [N]
GMP22-2PD(1c) 1.5A [R]
GMP22-2PD(1c) 5A [R]
GMP22-2PD(1c) 22A [R]
GMP Series
GMP22-
Pin type
GMP22-
P, PR
Screw type
GMP22 S, SR
Tunnel type
GMP22 T, TR
Specification
Various connection methods :
Electronic contactors applied
Auxiliary contact
Current setting range
Operating time characteristics
Number of built-in CT (deflector)
Operating power
Return (reset) method/time
Using Inverter Secondary
Pin, Screw, Tunnel type : MC-9b, 12b, 18b, 22b
2SPST (1a1b at energization)
0.3~1.5/1~5/4.4~22A
Inverse time
2 (R, Tphase) or 3
AC 100~260V
Manual/Electrical return (Standard)
Manual/Auto/Electrical return (2PA)
Available (Exclude GMP22-3PR, 3TR, 3SR)
*GMP22-2PA automatically returns within 60 seconds in case of overcurrent.
Protection
Type (GMP22-
)
Overcurrent
Lock/Stall
Phase failure
2P, 2PA, 2T, 2S note)
Phase unbalance
Reverse phase -
-
Certification UL, CE (Exclude 2PD)
Note) The product detects phase failure of the phase (R, T) connected with two CTs in order for protection.
3P, 3T, 3S
-
Order type
Mounting type
Direct mount onto a Metasol MC
Model/CT
GMP22-2P (1a1b)
- 2CT type
Screw type
Tunnel type
Electronic contactor
MC-9b, 12b, 18b, 22b
Install Screw/Rail
Install Screw/Rail
GMP22-2PA (1a1b)
- 2CT type
- Automatic return
GMP22-3P
- 3CT type
GMP22-3PR
- 3CT type
- Reverse phase
protection
GMP22-2S
- 2CT type
GMP22-3S
- 3CT type
GMP22-3SR
- 3CT type
- Reverse phase
protection
GMP22-2T
- 2CT type
GMP22-3T
- 3CT type
- Reverse phase
protection
0.3 - 1.5A
1 - 5A
4.4 - 22A
0.3 - 1.5A
1-5A
4.4-22A
0.3 - 1.5A
1 - 5A
4.4 - 22A
0.3 - 1.5A
1 - 5A
4.4 - 22A
0.3 - 1.5A
1-5A
4.4-22A
0.3 - 1.5A
1 - 5A
4.4 - 22A
Current setting range
0.3 - 1.5A
1 - 5A
4.4 - 22A
0.3 - 1.5A
1-5A
4.4-22A
0.3 - 1.5A
1 - 5A
4.4 - 22A
0.3 - 1.5A
1 - 5A
4.4 - 22A
Inverse time
3PR, 3TR, 3SR
Order type
GMP22-2P(1a1b) 1.5A Sol
GMP22-2P(1a1b) 5A Sol
GMP22-2P(1a1b) 22A Sol
GMP22-2PA(1a1b) 1.5A Sol
GMP22-2PA(1a1b) 5A Sol
GMP22-2PA(1a1b) 22A Sol
GMP22-3P 1.5A Sol
GMP22-3P 5A Sol
GMP22-3P 22A Sol
GMP22-3PR 1.5A Sol
GMP22-3PR 5A Sol
GMP22-3PR 22A Sol
GMP22-2S 1.5A
GMP22-2S 5A
GMP22-2S 22A
GMP22-3S 1.5A
GMP22-3S 5A
GMP22-3S 22A
GMP22-3SR 1.5A
GMP22-3SR 5A
GMP22-3SR 22A
GMP22-2T 1.5A
GMP22-2T 5A
GMP22-2T 22A
GMP22-3T 1.5A
GMP22-3T 5A
GMP22-3T 22A
GMP22-3TR 1.5A
GMP22-3TR 5A
GMP22-3TR 22A
LSIS Co.,Ltd.
39
Rated specifications / Order type
GMP40-
Specification
Various connection methods :
Electronic contactors applied
Auxiliary contact
Current setting range
Operating time characteristics
Number of built-in CT (deflector)
Operating power
Return (reset) method/time
Using Inverter Secondary
Pin, Screw, Tunnel type : MC-32a, 40a
2SPST (1a1b at energization)
4~20/8~40A
Inverse time, Definite time (2PD)
2 (R, T phase) or 3
AC 100~260V
Manual/Electrical return (Standard)
Manual/Auto/Electrical return (2PA)
Available (Exclude GMP40-3PR, 3TR, 3SR)
*GMP40-2PA automatically returns within 60 seconds in case of overcurrent.
Inverse time
Pin type
GMP40 P, PR
Screw type
GMP40 S, SR
Tunnel type
GMP40 T, TR
Protection
Type (GMP22 )
Overcurrent
Lock/Stall
Phase failure
Phase unbalance
2P, 2PD, 2PA, 2T, 2S
note)
3P, 3T, 3S
Reverse phase -
Certification UL, CE (Exclude PD, PA)
Note) The product detects phase failure of the phase (R, T) connected with two CTs in order for protection.
-
Order type
Mounting type
Direct mount onto a Metasol MC
Model/CT
GMP40-2P
- 2CT type
Screw type
Tunnel type
Electronic contactor
MC-32a, 40a
Install Screw/Rail
Install Screw/Rail
GMP40-2PA
- 2CT type
- Automatic return
GMP40-2PD
- 2CT type
- Defined Time
characteristics
GMP40-3P
- 3CT type
GMP40-3PR
- 3CT type
- Reverse phase
protection
GMP40-2S
- 2CT type
GMP40-3S
- 3CT type
GMP40-3SR
- 3CT type
- Reverse phase
protection
GMP40-2T
- 2CT type
GMP40-3T
- 3CT type
GMP40-3TR
- 3CT type
- Reverse phase
protection
3PR, 3TR, 3SR
4 - 20A
8 - 40A
4 - 20A
8 - 40A
4 - 20A
8 - 40A
8 - 40A
4 - 20A
8 - 40A
4 - 20A
8 - 40A
4 - 20A
8 - 40A
Current setting range Order type
4 - 20A GMP40-2P 20A Sol
8 - 40A
4-20A
8-40A
4-20A
GMP40-2P 40A Sol
GMP40-2PA 20A Sol
GMP40-2PA 40A Sol
GMP40-2PD 20A Sol
8-40A
4 - 20A
8 - 40A
4 - 20A
GMP40-2PD 40A Sol
GMP40-3P 20A Sol
GMP40-3P 40A Sol
GMP40-3PR 20A Sol
GMP40-3PR 40A Sol
GMP40-2S 20A
GMP40-2S 40A
GMP40-3S 20A
GMP40-3S 40A
GMP40-3SR 20A
GMP40-3SR 40A
GMP40-2T 20A
GMP40-2T 40A
GMP40-3T 20A
GMP40-3T 40A
GMP40-3TR 20A
GMP40-3TR 40A
40 Electronic Motor Protection Relays
GMP Series
GMP22/40-
Front face configuration
GMP22
Current setting
GMP22 GMP40
0.3 - 1.5A
4 - 20A
1 - 5A
4.4 - 22A
8 - 40A
-
LED
2CT type : Red LED
3CT type : 2 colors LED
(Red/Green)
Operation status indication
Trip cause indication normal Overcurrent
Overcurrent Phase failure
Phase unbalance (3CT)
Reverse phase
(3CT)
GMP40
Sharing of Installation and Contact
Operation time adjustment dial
0~30sec (Class 5-10-20-30)
Set the operating time of inverse time characteristic
Set time is the trip time at 6 x set current
*GMP22/40-2PD has the characteristic of
definite time.
Model numbering
Test / Reset button
Screw installation ↔ Rail installation sharing
Terminal connection type and penetration type have the common use structure of DIN rail and screw installation.
Technical information
Tolerance
Frequency
Aux. contact Ratings
Insulation resistance
Lightning impulse voltage
Fast Transient Burst
Environment
Trip indicator
Application specification
Terminal connection type ↔ penetration type sharing
If the terminal block of terminal connection type is removed, it is possible to make a penetration type
Current : ±5%
Time : ±5% (or ±0.5sec)
50/60Hz
5A/250VAC Resistive load
Minimum 100㏁/500VDC
1.2×50㎲ 5kV With standard waveform (IEC60255-22-5)
2kV/1min (IEC61000-4-4)
Operation : -25~70℃
Storage : -30~80℃
Relative humidity : 30~90%RH (No freezing)
2CT : Red LED, 3CT : Red/Green 2 colors LED
IEC60947-1
LSIS Co.,Ltd.
41
Rated specifications / Order type
GMP60T
GMP60T
If external CT (current transformer) is used, the product is applicable to a large current of 60A or more.
Specification
(
Tunnel type
/
Economic type EMPR
)
Connection methods
Auxiliary contact
Current setting range
Operating time characteristics
Number of built-in CT (deflector)
Operating power
Return (reset) method/time
Using Inverter Secondary
Tunnel type
1SPDT 1c (N type) note 1)
0.5~6/3~30/5~60A
Definite time
2 (R, T type)
AC24V/48V/110V/220V/380V(440)
AC180~480V
AC110V/220V (GMP60TA)
Manual/Electrical return (Standard)
Manual/Auto/Electrical return (60TA)
Available
Definite time
Protection
Type (GMP22 )
Overcurrent
Lock/Stall
Phase failure
Operation time setting
Auto-return setting
Certification UL, CE
GMP60T
0~30sec
note 2)
GMP60TE
note 2)
5sec (Fixed)
GMP60TA note 2)
5sec (Fixed)
0~120sec
Note) 1. 1c contacts have two types of products: N-type (Fail Safe/Normal Energyed) and R-type(Non Fail Safe / Normal De-Energyed). In terms of product reliability, N-type (Fail Safe) product is recommended to be used
2. The product detects phase failure of the phase (R, T) connected with two CTs in order for protection.
-
Order type
Mounting type Model/CT
Pin type GMP60T
- 2CT type
GMP60TE
- 2CT type
- Economic type
GMP60TA
- 2CT type
- Auto-return
Operating characteristics Current setting range
Defined Time characteristics
D-Time : 0~30sec
O-Time : 0~15sec
0.5 - 6A
3 - 30A
5 - 60A
Defined Time characteristics
D-Time : 0~30sec
O-Time : 5sec (Fixed)
Defined Time characteristics
D-Time : 0~30sec
O-Time : 5sec (Fixed)
A-Time : 0~120sec
0.5 - 6A
3 - 30A
5 - 60A
0.5 - 6A
3 - 30A
5 - 60A
Order type
GMP60T 6A
GMP60T 30A
GMP60T 60A
GMP60TE 6A
GMP60TE 30A
GMP60TE 60A
GMP60TA 6A
GMP60TA 30A
GMP60TA 60A
*Auto Reset: applicable only at Overcurrent Trip
Technical information
Install
Tolerance
Frequency
Aux. contact Ratings
Insulation resistance
Lightning impulse voltage
Fast Transient Burst
Environment
Trip indicator
Application specification
42 Electronic Motor Protection Relays
Screw / rail mounting
Current : ±5%
Time : ±5% (or ±0.5sec)
50/60Hz
5A/250VAC Resistive load
Minimum 100㏁/500VDC
1.2×50㎲ 5kV With standard waveform (IEC60255-22-5)
2kV/1min (IEC61000-4-4)
Operation : -25~70℃
Storage : -30~80℃
Relative humidity : 30~90%RH (No freezing)
Red LED
IEC60947-1
GMP Series
GMP6-TD, TDa
GMP60-TD
GMP60-TDa
Current control range by
Rated Current Setting DIP S/W:
0.5A~60A
Specification
(
Tunnel type
/
3-phase current indication type EMPR
)
Connection methods
Auxiliary contact
Current setting range
Current Ratio
Operating time characteristics
Number of built-in CT (deflector)
Operating power
Return (reset) method/time
Using Inverter Secondary
Tunnel type
2SPST (1a1b at energization)
0.5~60A
0.25, 0.5, 1~120 (0.125~600A)
Definite time
2 (R, T type)
AC 110V/220V (Separate)
Manual (GMP60-TD)
Manual/Auto (GMP60-TDa)
Available
Type GMP60-TD
Protection
Overcurrent
Lock/Stall
Phase failure
Low current note )
Auto-return setting -
-
Operation time setting
Save the last fault cause
-
-
Note) The product detects phase failure of the phase (R, T) connected with two CTs in order for protection.
GMP60-TDa note )
Definite time
Order type
Mounting type
Tunnel type
Screw / rail mounting
Model/CT
GMP60-TD
- 2CT type
GMP60-TDa
- 2CT type
- Low Current
Protection
- Auto-return
Operating characteristics Current setting range Order type
Defined Time characteristics
D-Time : 1~60sec
O-Time : 0.5~30sec
Defined Time characteristics
D-Time : 1~60sec
O-Time : 0.5~30sec
A-Time : 1~20min
0.5 - 60A
0.5 - 60A
GMP60-TD 6/60A
GMP60-TDa 6/60A
Technical information
Install
Tolerance
Frequency
Aux. contact Ratings
Insulation resistance
Lightning impulse voltage
Fast Transient Burst
Environment
Trip indicator
Application specification
Screw / rail mounting
Current : ±5%
Time : ±5% (or ±0.5sec)
50/60Hz
5A/250VAC Resistive load
Minimum 100㏁/500VDC
1.2×50㎲ 5kV With standard waveform
2kV/1min
Operation : -25~70℃
Storage : -30~80℃
Relative humidity : 30~90%RH (No freezing)
7-Segment, 3-phase current value, trip cause
IEC60947-1
LSIS Co.,Ltd.
43
Rated specifications / Order type
GMP60-3T/3TR, 3S/3SR
GMP60-3T
GMP60-3TR
Specification
(
Tunnel type
/
Screw type EMPR
)
Connection methods
Auxiliary contact
Current setting range
Operating time characteristics
Number of built-in CT (deflector)
Operating power
Return (reset) method/time
Using Inverter Secondary
Tunnel type / Screw type
2SPST (1a1b at energization)
0.5~60A
Definite time
3
AC 100~260V
Manual/Electrical return
Available (Exclude GMP60-3TR)
Protection
Type
Overcurrent
Lock/Stall
Phase failure
Phase unbalance
Reverse phase
Save the last fault cause
GMP60-3T, 3S
-
* To use a terminal connection type (Screw Type), please purchase a terminal block separately.
Terminal Block
Order type
Mounting type Model/CT
Tunnel type GMP60-3T
- 3CT type
Screw type
GMP60-TR
- 3CT type
- Reverse phase
protection
GMP60-3S
- 3CT type
If external CT (current transformer) is used, the product is applicable to a large current of 60A or more.
GMP60-3SR
- 3CT type
- Reverse phase
protection
Technical information
Install
Tolerance
Frequency
Aux. contact Ratings
Insulation resistance
Lightning impulse voltage
Fast Transient Burst
Environment
Trip indicator
Application specification
44 Electronic Motor Protection Relays
Screw / rail mounting
Current : ±5%
Time : ±5% (or ±0.5sec)
50/60Hz
5A/250VAC Resistive load
Minimum 100㏁/500VDC
1.2×50㎲ 5kV With standard waveform (IEC60255-22-5)
2kV/1min (IEC61000-4-4)
Operation : -25~70℃
Storage : -30~80℃
Relative humidity : 30~90%RH (No freezing)
Red / Green 2 colors LED, Red LED
IEC60947-1
Definite time
GMP60-3TR, 3SR
Operating characteristics Current setting range Order type
Defined Time characteristics
D-Time : 0.2~60sec
O-Time : 0.2~15sec
0.5~60A GMP60-3T 6/60A
Defined Time characteristics
D-Time : 0.2~60sec
O-Time : 0.2~15sec
0.5~60A GMP60-3TR 6/60A
Defined Time characteristics
D-Time : 0.2~60sec
O-Time : 0.2~15sec
Defined Time characteristics
D-Time : 0.2~60sec
O-Time : 0.2~15sec
0.5~60A
0.5~60A
Please order a penetration type and a terminal block separately and assemble them before use.
GMP Series
GMP60-3TZ/3TZR, 3TN/3TNR, 3SZ/3SZR, 3SN/3SNR
GMP60-3TZ, 3TZR
GMP60-3TN, 3TNR
Specification
(
Ground Fault Protection EMPR
)
Connection methods
Auxiliary contact
Tunnel type / Screw type
2SPST (1a1b at energization)
Current setting range
Operating time characteristics
Number of built-in CT (deflector)
Operating power
Return (reset) method/time
Definite time characteristics
Using Inverter Secondary
0.5~60A
Definite time
3
AC 100~260V
Manual/Electrical return
D-Time : 0.2~60sec
O-Time : 3sec
Available (Exclude GMP60-3TZR, 3TNR)
Note) If inverter load has an error, turn OFF ground fault function.
note)
GMP60-3TZ, 3TN Type
Overcurrent
Lock/Stall
Protection
Phase failure
Phase unbalance
Ground Fault
Reverse phase
Save the last fault cause
-
Definite time
GMP60-3TZR, 3TNR
Order type
Mounting type Model/CT
Tunnel type
Screw / rail mounting
Zero phase current detection (0.1~2.5A)
(Separate ZCT required)
Operating characteristics
GMP60-3TZ
Current setting range
0.5 - 60A
0.5 - 60A
Order type
GMP60-3TZ 6/60A
GMP60-3TZR 6/60A
Residual current detection
(0.5~6A)
GMP60-3TN
GMP60-3TNR -
Reverse phase protection
GMP60-3SZ
0.5 - 60A
0.5 - 60A
GMP60-3TN 6/60A
GMP60-3TNR 6/60A
Tunnel type
Zero phase current detection(0.1~2.5A)
(Separate ZCT required)
0.5 - 60A
0.5 - 60A
GMP60-3SZ 6/60A
GMP60-3SZR 6/60A
Residual current detection(0.5~6A)
GMP60-3SN
GMP60-3SNR -
Reverse phase protection
0.5 - 60A
0.5 - 60A
GMP60-3SN 6/60A
GMP60-3SNR 6/60A
Note) 1. In case of terminal connection type, please order a penetration type and a terminal block separately and assemble them before use.
2. In case of ZCT, use ZCT (100mA/40~55mV) for EMPR only.
Technical information
Install
Tolerance
Frequency
Aux. contact Ratings
Insulation resistance
Lightning impulse voltage
Fast Transient Burst
Environment
Trip indicator
Application specification
Screw / rail mounting
Current : ±5%
Time : ±5% (or ±0.5sec)
50/60Hz
5A/250VAC Resistive load
Minimum 100㏁/500VDC
1.2×50㎲ 5kV With standard waveform (IEC60255-22-5)
2kV/1min (IEC61000-4-4)
Operation : -25~70℃
Storage : -30~80℃
Relative humidity : 30~90%RH (No freezing)
Red / Green 2 colors LED, Red LED
IEC 61000, IEC60947-1
LSIS Co.,Ltd.
45
Rated specifications / Order type
GMP80
GMP80
Specification
Connection methods
Auxiliary contact
Current setting range
Operating time characteristics
Number of built-in CT (deflector)
Operating power
Return (reset) method/time
Using Inverter Secondary
Screw type (No direct connection with Metasol MC)
2SPST (1a1b at energization)
16~80A
Inverse-time
2 (R, T type) or 3
AC 100~260V
Manual/Electrical return (Standard)
Manual/Auto/Electrical return (GMP80-2SA)
Available (Exclude GMP80-3SR)
GMP80-3S Model numbering
Overcurrent
Functions
Locked rotor
Phase loss
Certification
Phase unbalance
Reverse phase
UL, CE
GMP80-2S
-
note)
GMP80-2SA
-
-
note)
Note) The product detects phase failure of the phase (R, T) connected with two CTs in order for protection.
-
Order type
Mount/Connection
Screw type
Setting range
16 - 80A
Catalog No.
GMP80-2S 80A
Model numbering system / CT
GMP80-2S
- 2CT
GMP80-2SA
- 2CT
- Automatic return
GMP80-3S
- 3CT
GMP80-3SR
- 3CT
- Reverse phase
protection
16 - 80A
16 - 80A
16 - 80A
GMP80-2SA 80A
GMP80-3S 80A
GMP80-3SR 80A
Rated specifications
Tolerance
Frequency
Aux. contact Ratings
Insulation resistance
Lightning impulse voltage
Fast Transient Burst
Environment
Trip indicator
Application specification
Current : ±5%
Time : ±5% (or ±0.5sec)
50/60Hz
5A/250VAC Resistive load
Min 100㏁ at 500V DC
1.2×50㎲ 5kV With standard waveform (IEC60255-22-5)
2kV/1min (IEC61000-4-4)
Operation : -25~70℃
Storage : -30~80℃
Relative humidity : 30~90%RH (No freezing)
Red LED (2CT : 1, 3CT : 2)
UL508, IEC60947-1
Inverse-time
GMP80-3SR
46 Electronic Motor Protection Relays
Motor selection / Model numbering system
GMP Series
Motor selection
Current
80
06
20
40
1.5
5
22
30
60
Current setting range (A)
0.3-1.5
1-5
4.4-22
4-20
8-40
16-80
0.5-6
3-30
0.5-60
3-phase motor rating kW (Hp)
~0.18
0.18~0.75
1.1~4
0.75~3.7
2.2~7.5
4~18.5
0.09~0.75
0.37~5.5
1.1~11
220~240VAC
(~0.25)
(0.25~1)
(1.5~5.5)
(1~5)
(3~10)
(5.5~25)
(0.13~1)
(0.5~7.5)
(1~15)
Full Load Current for the Motor(A)
1.5
4.8
18.8
17.4
34
79
4.8
26
48
0.12~0.55
0.25~1.5
3~7.5
2.2~7.5
4~15
7.5~37
0.12~2.2
1.1~11
3~22
380~440VAC
3-phase motor rating kW (Hp)
Note) The above data can be different depending on a motor degree and a manufacturer. They are the reference values of AC Degree 3 Standard Squirrel Cage Motor.
(~0.75)
(0.33~2)
(4~10)
(3~10)
(5.5~20)
(10~50)
(0.13~3)
(1.5~15)
(4~30)
Full Load Current for the Motor(A)
1.6
4
17
17
32.5
74
5.5
24
46.5
Model numbering system
GMP 22 2 P R a 1.5A
220 1a1b Sol
Frame Nominal Current Type
1.5A
22
40
5A
22A
20A
40A
Direct
Coupling,
Penetration
80
60
60A
80A
06A
30A Penetration
CT Type
2 2CT
3 3CT
Type
P Pin type
S
T
Screw type
Tunnel type
TE Economic
PD
Direct Coupling
(Definite Time)
TD
Current Display
(Definite Time)
TZ
Ground Fault Protection
Reverse
Phase
R
Reverse
Protection
Available
Classification
-
Existing
Model a
Operation
Time
Function
Nominal
Current
1.5A
Current Adjustment
Range (A)
0.3~1.5
5A 1~5
22A
20A
4.4~22
4~20
Control Voltage
110/220 AC100~260V
24
48
AC24V
AC48V
110 AC110V
40A
80A
8~40
16~80
220 AC220V
380 AC380 (440)V
06A 0.5~6 480 AC180~480V
30A
60A
3~30
0.5~60 note)
Note) For GMP60-TD, GMP60-TDa
GMP60-3TZ (R), 3TN (R), 3T (R)
Note) AC24V, AC48V,
AC380/440V, and
AC480V are GMP60T model.
Aux. contactor
1c(N)
1c(R)
1a1b
Note) When the power is applied, the system is in the contacting status.
• In case of 1c(N) power supply, 95~96 are
Closed.
• Regardless of 1c(R) power, 95~98 are Closed.
-
Model Type
Screw type
Tunnel type
Sol
Metasol
Direct
Coupling
(Pin)
LSIS Co.,Ltd.
47
Operation & setting method
Inverse time characteristic
1. Check the rated voltage and apply the control
power to A1 and A2 terminal
If 220V power is supplied to a model for AC110V, overvoltage occurs and thereby EMPR has a failure.
RC (A) Knob
O.L LED (2CT) O.L/Fault LED (3CT)
Test/Reset button
Time Knob
2.
With Test/Reset button, check that output contact works normally.
1) If Test/Reset button is clicked once, O.L (display lamp) representing Trip is turned on. If EMPR is Tripped, output contact works.
2) If Test/Reset button is clicked again at the time of EMPR Trip, the display lamp is turned off and the equipment resets to its original state.
3) Auto reset function (Auto Reset)
• In case of overcurrent Trip, the equipment automatically returns after one minute (GMP22-2PA/GMP40-2PA),
• In case of overcurrent Trip, the equipment automatically returns after 0~120 seconds (variable setting) (GMP60T-A).
Note) To prevent a Trip accident, Test/Reset button is designed not to work while a motor is running.
3 .
Set the operating time
An operating time is based on 600% of rated current in the characteristic curve.
1) Set up the position of operating time control knob (Time Knob) in consideration of a staring time and starting current.
(E.g., on the assumption that a starting current accounts for 600%of normal operating current and a staring time is 10 seconds, set Time Knob to about 11~12 seconds with 10-20% margin.)
2) An available operating time ranges from 0 to 30 seconds.
3) In case that Time Knob is set to 10 seconds, if the starting current or 600% of rated current is supplied for 10 seconds, immediate Trip occurs.
Note) For a motor with frequent forward/reverse starting, such as a motor of crane or hoist, an EMPR with the characteristic of definite time is recommended
4 . Set up a rated current.
Setting is based on the rated current of a motor (normal operating current).
1) Check that a motor’s rated current is within the current control range of EMPR.
2) Set RC (Rating Current) Knob up to the maximum and run the motor.
3) In normal operation state, slowly turn RC Knob counter clockwise and stop at the point that overcurrent display lamp (O.L) flickers. At this point, the actual load current value
(100%) of the motor is displayed.
4) From the point, turn RC Knob clockwise. Set up the knob at this point that O.L lamp is turned off (less than motor full load current).
(e.g., when overcurrent display lamp is turned off at 20A, set current = 20×1.1=22A)
UJNF
DVSSFOU
48 Electronic Motor Protection Relays
GMP Series
5 .
Check status of operation by LED
2CT : Overcurrent, Phase failure, Lock/Stall
3CT : Overcurrent, Phase failure, Reverse phase, Phase unbalance, Lock/Stall
1) In case of overcurrent
• If there will be an overcurrent during motor operation, the red color of LED will flicker at 0.4 second intervals.
After tripping because of overcurrent, the red color of LED will light up.
2) In case of phase failure (2CT EMPR can protect motor from R or T phase failure.)
• If a motor stops running due to phase failure, stall current flows. As a result, it is possible to protect the motor against overcurrent.
If the motor keeps running in phase failure, it is necessary to protect against phase failure.
• If phase failure occurs in three-phase load (3CT), Trip occurs within three seconds. (O.L LED is turned on)
R-phase phase failure - Fault LED flickers once (0.4 second) at an interval of three seconds.
S-phase phase failure - Fault LED flickers twice at an interval of three seconds.
T-phase phase failure - Fault LED flickers three times at an interval of three seconds
3) In case of phase unbalance
• If phase unbalance factor of three phase is about 50% or more after its calculation, Fault LED only flickers at an interval of 0.4 second
and then trips after five seconds. (After Trip, the same display as phase failure appears.)
4) In case of Reverse phase
• Trip occurs within 1 second, and the lamp flickers red and green in turn (GMP22/40/60-R type) or O.L LED and Fault LED flicker (GMP80-3SR).
In this case, to detect reverse phase, a load current should be more than the minimum current setting range of EMPR.
5) LED operation status
Condition
Normal LED OFF
LED Status LED Diagram Remark
Over current
Phase unbalance
(50%, 3CT)
Over current
R
0.4 Second intervals
0.4 Second intervals
O.L LED light up
1 time for 3 seconds
Phase failure
(3CT)
S 2 time for 3 seconds
T 3 time for 3 seconds
Phase failure (2CT)
Red LED light up for 0.9 sec
LED goes off for 0.1 sec
Reverse phase (3CT)
Red & Green color LED flicker alternately
Note) There are two red color LEDs for O.L (Overload) & Fault in the model of GMP80-3S/SR
ㅈ
0.9
0.1
GMP 80-3S/3SR model, only red color LED will flicker.
GMP 80-3S/3SR model,
O.L LED will light up and also FAULT LED will flicker.
GMP 80-3S/3SR model,
Red/Green LED will flicker.
LSIS Co.,Ltd.
49
Operation & setting method
Definite time characteristic 1
1 .
Check the rated voltage and apply the control power to A1 and A2 terminal
If 220V power is supplied to a model for
AC110V, overvoltage occurs and thereby
EMPR has a failure.
O.L LED
Test/Reset button
O-Time knob current(s)
2. Check the Test/Reset button operation
D-Time knob RC (A) knob time(%)
1) If Test/Reset button is clicked once, O.L
(display lamp) is turned on, EMPR is
Tripped, and output contact runs.
2) If Test/Reset Button is clicked once again when EMPR is Tripped, the display lamp is turned off and the equipment returns to its original state
(Reset).
Note) 1. To prevent a Trip accident, Test/Reset button is designed not to work while a motor is running. 2. If Test/Reset button is clicked twice within 0.5 second, it is possible to check the final failure cause.
3. Set the operating time
D-Time (Delay Time) : 0~30 sec
It refers to the time of delaying EMPR operation in order to prevent Trip from a motor’s staring current.
1) With the use of D-Time Knob, set up a delay time taken from motor starting to normal running current.
2) If you are unaware of a start delay time, set it to the maximum time and measure how long it takes to reach the normal starting current of the motor, and then set it up again. (Reference: in case of general load, set it to about 3~5 seconds.)
Note) If actual load current fails to detect during a set time, a motor can be damaged. Set up a delay time rightly.
O-Time (Operating Time) : 0~15 sec
It refers to the time taken from the start of overcurrent to EMPR Trip. After the set O-Time, EMPR is Tripped.
1) With the use of O-Time Knob, set up an operating time.
2) If O-Time is the minimum value, EMPR is immediately tripped as soon as overload occurs. (Reference: generally, set it to 4~6 seconds.)
A-Time (Auto Reset Time): 0~120 seconds; set up an automatic reset time in auto reset type.
4.
Set the operating current
Setting is based on the rated current of a motor (normal operating current).
1) Check that a motor’s rated current is within the current control range of EMPR.
2) Set RC (Rating Current) Knob up to the maximum and run the motor.
3) In normal operation state, slowly turn RC Knob counter clockwise and stop at the point that overcurrent display lamp (O.L) flickers. At this point, the actual load current value (100%) of the motor is displayed.
4) From the point, turn RC Knob clockwise. Set up the knob at this point that O.L lamp is turned off (less than motor full load current).
Generally, set it to 110~120% of actual load current (set to a value lower than a motor full load current).
5 .
Check the LED condition when operation
1) GMP60T
Condition
Operation normal Off
Red O.L LED Remarks
Overcurrent
Trip over-current
Flicker
On
Flicker during overcurrent
The EMPR is tripped
2) GMP60-3T/3TR
The same as the LED operation state in operation.
50 Electronic Motor Protection Relays
GMP Series
Definite time characteristic 2 (GMP60-TD, TDa)
1 .
Function & Setting menu
1) Set up “Slide S/W, Rated current, and Current transformer ratio” on the basis of a motor’s full load current.
To change Slide S/W, turn OFF control power. In the No. 1 menu (1.Cty), make sure to change to a relevant rated current.
Full Load Current
0.6A or less
Wire penetration
4 times
Slide S/W
6A
Rated current
(1.Cty)
6A
Current ratio (5.Ctr)
0.25
0.7~1.5A
1.6~6A
6~60A
60~100A
100A or more
Twice
Once
Once
Once
Once
6A
6A
60A
6A
6A
6A
6A
60A
6A
6A
0.5
1
10
20
CT Ratio (Primary/Secondary)
2) In the ‘0000’ display state, click Test/Reset button to go to Setting Mode (‘Test’ is displayed on screen).
Click FUN button to search for items and set up various values with the use of SEL button.
3) Push FUN button until ‘Stor’ is displayed, and make sure to save a value with SEL button.
4) If saved completely, ‘0000’ is displayed on screen. If no button operation occurs in ten seconds in the value setting process,
the current screen goes to initial screen.
5) If Test/Reset button is clicked in operation, it is possible to check “Set Current/D-T/O-T”.
In case of Trip, it is possible to check failure current/failure cause with the use of SEL button.
Note) While a motor is running, a set value is unable to be changed, but is able to be checked only.
2. Setting Menu
FUNC SEL Description
Current type selection
Trip time setting
Time delay setting
Rated current setting
Current ratio setting
Phase loss enable
Undercurrent setting
Automatic reset setting
Operation hour setting
Total running hour check
Running hour check
Store
Default Value
6A
30
60
6/60
Off
Off
-
-
1
Off
Off
Remarks
Set the same with rated current S/W
Set 0.5 to 30 sec
-
Set 1~60 sec
-
Operation in less than 3 sec
For TDa model only (Overcurrent operation)
For TDa model only (Off, 1~20min)
For TDa model only
-
For TDa model only (Up to 10 years, 1 hour unit)
For TDa model only (Up to 10 years, 1 hour unit)
Note) 1. Check final failure cause: push FUN+SEL (combination buttons) (if there is no failure cause, 'non' is displayed.)
2. Operating time setting: 'OrH' is displayed after a set operating time(Of, f10~8760 hours setting allowed)
3. Fault status configuration
Protection
Over current
Undercurrent
Phase Loss
LOCK
Approaching Running Time
FND
O-L
U-C
PF-r
PF-t
Loc
OrH
Note) 1. If the set operating time in ‘
2. How to check ‘ ’ and ‘
’passes, ‘
’
Description
More than set current : Within the set time
Lower than the undercurrent set ratio : Within 3S
Over 70% of the rate of unbalance : Within 3S
Over 70% of the rate of unbalance : Within 3S
More than lock set current ratio : Within 1S
When Running time approaches at setting time
’ is displayed and EMPR has no output.)
Remarks
For TDa model only
R Phase Loss
T Phase Loss
For TDa model only
FUNC
Press the SEL button
Press the SEL button
Daily Display
Operation time indicator
Press the SEL button
Press the SEL button
Description
Daily Display Press the SEL button
In case of ‘
If ‘
’, if power is Off, the minute unit based time is removed.
’ is checked, an operating time represents a total running time taken until a motor is turned Off. It is displayed in the units of day, hour, and minute.
Time Remaining, Display minutes
Time Remaining, Display minutes
LSIS Co.,Ltd.
51
Operation & setting method
Definite time characteristic 3 (GMP60-3TZ, TZR / 3TN, TNR)
1. This product has the characteristic of definite time.
For setting, see pages 21
&
22.
❷ ❸ ❹
2.
Protective function: overcurrent, locked rotor,
phase loss, phase unbalance, ground fault
(and phase reverse)
1) Overcurrent : trip within 3 sec. after D-time at 105% or more
2) Locked rotor : trip within 1 sec. after D-time at 300% or more
3) Phase loss : trip within 3 sec. (phases unbalance rate over 70%)
4) Phase unbalance : trip within 5 sec. (phases unbalance rate over 50%)
5) Ground fault : trip within 0.5 sec. after D-time at over 110% or under
90% of set value
6) Reverse phase: if two out of R, S, and T phases are changed with
each other and a current flows.
Run in 1 second (no detection after TDim- e)
3. Overcurrent trip time
1) Time delay(D-time) setting: between 0.2-60 sec.
2) Trip time(O-time) setting: fixed at 3 sec.
❶
❺ ❻ ❼
❽
Note) 1. Make power off before changing the rated current with S/W ①
2. The setting range of RC (A) KNOB ⑥ is recognized as 0.5 ~ 6A or 5 ~ 60 According to the setting value of S/W ①. The value of the scale for RC (A) KNOB ⑥ is 0.5, 1, 2, 3, 4, 5, 6 or 5, 10, 20, 30, 40, 50, 60(A) from the left.
3. Last fault cause function indicates the LED status for the last TRIP.
4. Other Functions
1) Last fault cause data stored
• to display it press TEST/RESET button 2 times within 0.5 sec.
• PWR LED flicking in case of no fault
Note) In case of load less than minimum rating of EMPR make the number of
penetrating through CT more than 2 times. If not, error may happen to phase loss .
5. Status of LED configuration
NO
❶
❷
Function
6A/60A
PWR.
Setting
Slide switch
Red LED
❸
❹
❺
❻
❼
❽
Fault
GF
D-Time (S)
RC (A)
GR (A)
Test/Reset
Red / Green LED
Red LED
KNOB
KNOB
KNOB
Button
Description
Maximum rated current (6A/60A) setting
Lights up when power is ON
Blinking in the failure mode
Overcurrent / unbalance in progress :
Overcurrent TRIP :
Phase loss (unbalance) TRIP
·R-phase :
·S-phase :
·T-phase :
·Reverse phase :
Lights up after blinking in the event of ground fault
Delay time (0.2 to 60 sec.)
Rated current setting: 0.5~6A/5~60A
Zero phase current detection type
Sensitivity current setting (0.1~2.5A)
Residual current detection type
Sensitivity current setting (0.5~6A)
TRIP / RESET alternately perform
1. Check relay contacts - displays fault cause
2. RESET
Remark
-
-
Red LED
Green LED
-
-
-
Pressing 2 times within
0.5 sec.
the final failure cause is displayed
52 Electronic Motor Protection Relays
Terminal Configuration / Wiring & cable connection
GMP Series
Terminal Configuration
GMP22-2P (1c) Sol
GMP22-2PD (1c) Sol
A1 A2 96 95 98
GMP22-2P (1a1b) Sol
GMP22-3P Sol
GMP22-2PA (1a1b) Sol
GMP22-3PR Sol
A1 A2 95 96 97 98
GMP40-2P Sol
GMP40-2PD Sol
GMP40-2PA Sol
GMP40-3P Sol
GMP40-3PR Sol
A1 A2 95 96 97 98
GMP22-2S
GMP22-3S
GMP22-3SR
GMP40-2S
GMP40-3S
GMP40-3SR
U/2/T1
V/4/T2
W/6/T3
R/1/L1 S/3/L2 T/5/L3
A1 A2 96 95 97 98
GMP22-2T
GMP22-3T
GMP22-3TR
GMP40-2T
GMP40-3T
GMP40-3TR
U/2/T1
V/4/T2
W/6/T3
A1 A2 95 96 97 98
A1 A2 95 96 98
U/2/T1 V/4/T2 W/6/T3
GMP60T
GMP60TE
GMP60TA
GMP60-TD
GMP60-TDa
A1 A2 95 96 98
U/2/T1
V/4/T2
W/6/T3
GMP80-2S
GMP80-3S
GMP80-3SR R/1/L1 S/3/L2 T/5/L3
GMP60-3TZ, TZR
GMP60-3TN, TNR
GMP60-3T, TR
U/2/T1 V/4/T2 W/6/T3
주)
A1 A2 95 96 97 98 Z1 Z2
95 96
A1 A2 95 96 97 98
Engrave
A1, A2
95, 96, 98
95-96
97-98
Z1, Z2
U/2/T1, V/4/T2, W/6/T3
R/1/L1, S/3/L2, T/5/L3
Description
Input terminal for operation power
Output terminals at power-on
When the power is ON (NC contact output)
ZCT output connection
Power side connection
Load side connection
Note) 1. GMP60-3TN/3TNR and GMP60-3T/3TR models are not wired to Z1 and Z2 terminals.
2. In case of 1c(N), only if control power (A1, A2) is On, output contact occurs (if power Off or Trip, 95-96 :
Open, 95-98 : Close)
3. In case of 1c(R), output contact occurs regardless of control power (A1, A2). (Contact chattering can occur in a very vibrating place.)
LSIS Co.,Ltd.
53
Terminal Configuration / Wiring & cable connection
GMP22-2P 1c(N)
GMP22-2P 1c(R)
GMP60T 1c(N)
GMP60T 1c(R)
Fuse Fuse
Off Off
On On
Trip Trip
Fuse
Fuse
Off
(Reset)
Off
(Reset)
On
GMP22-2P 1c(N)
On
Trip
Trip
Fuse Fuse
Trip Trip
Off
(Reset)
Off
(Reset)
On On
Fuse
CD_ CD_
Fuse
Trip
Trip
GMP60T 1c(N)
Off
(Reset)
On
Off
(Reset)
On
GMP22-2P 1c(R)
Note) 1. In case of 1c(N), only if control power (A1, A2) is On, output contact occurs (if power Off or Trip, 95-96 : Open, 95-98 : Close)
2. In case of 1c(R), output contact occurs regardless of control power (A1, A2). (Contact chattering can occur in a very vibrating place.)
GMP-(1a1b)
Fuse
Off
(Reset)
On
Trip
GMP60T 1c(R)
GMP - (1a1b)
Note) 1. To use a single-phase motor, connect it with R & T phases of EMPR. 3CT Type is not allowed in a single-phase motor.
2. Output contact occurs only if control power (A1, A2) is On. (1a1b)
54 Electronic Motor Protection Relays
If external CT combination
GMP60-3TZ, TZR
GMP60-3TN, TNR
GMP60-3T, 3TR
GMP Series
Fuse
Off
(Reset)
On
Trip note)
Note) 1. In case of GMP60-3TZ/3TZR model, wire ZCT to Z1 and Z2 terminals.
2. In case of GMP60-3TN/3TNR and GMP60-3T/3TR models, do not wire ZCT to Z1 and Z2 terminals. (no need of ZCT)
3. Output contact occurs only if control power (A1, A2) is On. (1a1b)
Fuse
Off
(Reset)
On
MCM Digital contactor for power
MCD Digital contractor for operating
MCS Digital contactor for starting
19T Timer
19X Auxiliary relay
Control power
Y▵ wiring
Note) 1. A reverse phase protection model (-R Type) is not applicable to a single-phase motor.
2. GMP60-3TN is unable to provide ground fault protection for a single-phase motor. (GMP60-3TZ applied)
3. Output contact occurs only if control power (A1, A2) is On. (1a1b)
If a single-phase motor
LSIS Co.,Ltd.
55
Dimensions
GMP22-2P (1c) Sol
GMP22-2PD (1c) Sol
TDSFX
TDSFX
TDSFX
TDSFX
TDSFX
TDSFX
GMP22-2P (1a1b) Sol
GMP22-3P Sol
GMP22-2PA (1a1b) Sol
GMP22-3PR Sol
TDSFX
TDSFX
TDSFX
TDSFX
GMP40-2P Sol
GMP40-2PD Sol
GMP40-2PA Sol
GMP40-3P Sol
GMP40-3PR Sol
TDSFX
TDSFX
TDSFX
56 Electronic Motor Protection Relays
Unit : mm
0.15kg
Unit : mm
0.18kg
Unit : mm
0.20kg/0.22kg
GMP Series
Unit : mm
0.19kg/0.21kg
GMP22-2S
GMP22-3S
GMP22-3SR
GMP40-2S
GMP40-3S
GMP40-3SR TDSFX
TDSFX
GMP22-2T
GMP22-3T
GMP22-3TR
GMP40-2T
GMP40-3T
GMP40-3TR
TDSFX
TDSFX
GMP80-2S
GMP80-3S
GMP80-3SR
TDSFX
TDSFX
TDSFX
TDSFX
Unit : mm
0.14kg/0.16kg
.IPMF
.IPMF
Unit : mm
0.42kg/0.46kg
LSIS Co.,Ltd.
57
TDSFX
TDSFX
TDSFX
TDSFX
TDSFX
Dimensions
GMP60T
GMP60TE
GMP60TA
TDSFX
TDSFX
.IPMF
Unit : mm
0.14kg
GMP60-TD
GMP60-TDa
GMP60-3TZ, TZR
GMP60-3TN, TNR
GMP60-3T, TR
TDSFX
TDSFX
Unit : mm
0.25kg
26.8
R2.5
62.25
R2.5
7.2
8.2
55.4
61 75
47
Penetration type (Tunnel Type) Terminal connection type (Screw Type) – to attach a terminal block
Unit : mm
Note) If terminal connection type (Screw Type) is used, purchase a terminal block separately.
58 Electronic Motor Protection Relays
MEMO
GMP Series
LSIS Co.,Ltd.
59
Perfect Selection of Motor Protection
& Monitoring Device!
With the compact system structure and advanced protection functions, the device provides new standards of next-generation motor protection relay.
A6 60 Electronic Motor Protection Relays
Perfect Selection of Motor Protection
& Monitoring Device!
With the compact system structure and advanced protection functions, the device provides new standards of next-generation motor protection relay.
IMP Series
IMP Series
Intelligent Motor Protection Relays
• Ground fault protection for both zero current/residual current
• Support rated current 0.12~100A without external current transformer
• Definite/inverse time selection and diverse protection factors
• Basic application of ground fault/instance protection
• Separation of the display part with the use of Cable
• MODBUS communication and 4~20mA DC output
C o n t e n t s
62 Product characteristics
64 Rated specifications / Model numbering system
65 Operation & setting method
69 Terminal Configuration / Wiring & cable connection
70 Dimensions
LSIS Co.,Ltd.
61
Product characteristics
Slide S/W
Slide S/W
Slide S/W
Slide S/W
Convenience
MCU
MCU
INV
INV
Slide S/W
Slide S/W
Return
Return
30mA 25A
30mA 25A
Return
30mA
MCU
25A
MCU
25A
MCU
INV
Save
INV
INV
25A
Slide S/W
MCU
30mA
30mA
25A
25A
Return
30mA 25A
Slide S/W
Slide S/W
25A
Return
Save
30mA 25A
30mA
Save
Total
Slide S/W
Slide S/W
Total
Save
Return
Slide S/W
Slide S/W
25A
25A
30mA 25A
30mA
Total
25A
Return
30mA
MCU
25A
25A
Comprehensive Digital Motor Protection Relay with the MCU (Microprocessor Control Unit)
Real-time processing and high precision
MCU
INV
Applicable to Inverter Circuits
Thanks to its characteristics to harmonic noise, it can be applied to the inverter control circuits. The available frequency range is 20~200Hz. When the relative harmonic factor is over 30%, a harmonic filter should be installed (However, the ground fault function should be off).
INV
MCU
MCU
INV
25A
Slide S/W
MCU
30mA
30mA
25A
25A
Return
Return
30mA 25A
Slide S/W
Slide S/W
25A
Storage of Fault Events
Up to 5 fault events can be stored for easy fault history management.
One-Body Type and Separate Body Type
The display can be attached to the panel front so that current, operation time and settings can be checked without fetching the unit. With the display separated, the motor protection is available.
Communication support type
RS-485 MODBUS communication with various systems.The model with analogue signals (4~20mA) is compatible with transducer systems.
30mA 25A
30mA
Save
MCU
Save
Various Reset Functions
Manual, automatic and electric reset functions are provided for customer convenience.
Date and Total Operating Time Setup
When a fault occurs, its date and time are stored for easy checkup. When the total operation time is over, it is displayed for changing motor bearings or supplying oil.
Settings are protected with a password.
Total
Total
Slide S/W
Slide S/W
Save
Total operating time and operating time setting
When the predefined operating time has elapsed, related information is displayed so that operators may replace
~100A
~100A
Quick Setup
All settings can be decided quickly on the display.
30mA 25A
30mA
Total
25A
Wide Setting of Ground Fault Current Sensitivity 30mA~25A
Zero current sensing by zero sequence CT. zero current sensing by Residual circuit.
~100A
Save
Total
Total
Save
Save
Save
Total
Total
Total
62 Electronic Motor Protection Relays
Save
Save
~100A
~100A
Thermal Inverse Time, Inverse Time and Definite Time Modes
According to user’s needs, the motor can be protected in the inverse time mode or definite time mode.
3-Phase Digital Ampere-Meter
3-phase current is displayed every two seconds for motor monitoring.
Wide Current Setting Range: 0.125~100A for One Model
With the slide S/W, the current setting range can be decided 0.5~10A or 5~100A. Depending on the number of CT penetration, even 0.125A current can be protected. (Wire penetration hole is required).
Total
Total
~100A
~100A
IMP Series
Overcurrent-51
By setting up an operating time in the 1-60 seconds unit on the basis of 6005 of rated current in consideration of a motor’s starting time, it is possible to configure the overload characteristic curve of Class 1-60.
If Definite Time Characteristic is selected, the equipment starts to detect overcurrent after the set operating delay time (D-Time) regardless of a motor’s generated heat. If overcurrent continues to be supplied after an operating time (O-Time), Trip occurs.
<Inverse Time Characteristic> <Definite Time Characteristic>
Stall/Locked Rotor-48/51LR
This function is used to prevent the loss and damage made by a motor’s rotor stall, starting failure, and staring delay, and to detect an increased load current by overheat overload in operation or the case that load torque exceeds motor torque in order to block a circuit. Overcurrent function by starting current works after a set delay time
Under Current-37
This function is used to monitor the no-load caused by the separation or damage of a motor’s drive shaft, or to prevent a pump’s idle rotation (no-load). It is possible to set up to
30~70% of rated current. It works within three seconds.
Phase Fail/Phase Unbalance-47P
If phase failure occurs, a motor fails to start. A motor in operation stops due to shortage of torque or has overheat due to continuous reverse phase current.
IMP calculates phase unbalance of three-phase current. It is possible to select one of the two cases: if the calculated result is 70% or more, this function is executed within 1.5 seconds; if phase unbalance factor is 10-70%, trip occurs within three seconds.
* In a single-phase motor, turn OFF phase fail and phase unbalance protection function.
Reverse Phase
This function is used to prevent a motor’s reverse rotation. After the phase difference of three-phase current inputs is compared, this function is executed within 0.1 second if the phase sequence changes. Reverse phase is checked only if a motor starts up.
In a single-phase motor, turn OFF this function.
Ground Fault-51G
This function is used to detect ground fault leakage current. In other words, it aims to prevent leakage-induced ground fault and secondary accidents (short circuit and electric shock).
It is possible to set up a current sensitivity and an operating time differently depending on grounding system or protection purpose.
It is possible to set a current sensitivity to 30mA~25A and an operating time to 0.05~1.0 second.
LSIS Co.,Ltd.
63
Rated specifications / Model numbering system
Integral type
Extention type
Model numbering system
IMP C
Rated specifications
Protection
Connection method
Operating Time Characteristics
Rated current
Display
Operating power
Over current, Lock/Stall, Phase failure, Phase unbalance, Reverse phase,
Under current, Ground fault, Short circuit
Extention type
Heat accumulation inverse time / inverse time / definite time
0.5~10A/5~100A (Separate)
4digit, 7-Segment
AC/DC 85~245V (50Hz/60Hz)
Return method
Installation / installation method
Current
Tolerance
Auto 1~20min
Manual / Electrical On/Off Selectable
Time
4~20mA Output
Display can be installed separately, 35mm DIN rail / Screw installation
±5%
±5%
±5%
Time setting
Aux. contact
Startup delay
Operation delay
Configuration
Capacity
Contact minimum load
1~200sec
1~60sec
3-SPST(Power supply 1a1b, instantaneous operation 1a) Note1)
3A/250VAC Resistive Load
10mA / 5VDC
ZCT Input 200mA/100mV (Exclusive ZCT) Note2)
Environment
Operation
Storage
-10~55℃
-20~70℃
Relative humidity Below 80%RH (No freezing)
Insulation Resistance 100Mohm/500VDC
Power consumption
Fast Transient
Power consumption
Certification
1.2X50us 5kV Prototype waveform supply
2kV/1Min
Below 3W
CE
Note) 1. See No. 17-19 of A-Group in Setting menu.
2. It is used if zero current detection type is selected.
3. This product is designed for protecting a low-voltage motor with 1,000V or less. Therefore, it should not be used in high voltage lines.
A420 10A 110/220
Factors Protected
C Current
Communication
NO
A420
None
4~20mA Output
M485 Modbus/RS-485
Current adjustment range
10 0.5~10A
100 5~100A
Control Voltage
110/220 AC/DC85~245V
24/36 AC/DC24~36V
64 Electronic Motor Protection Relays
Operation & setting method
IMP Series
1 .
Check the TEST/RESET button
1) Check wires.
2) Note) While the motor is running, the Test/Reset key does not work.
3) Press again the Test/Reset key to reset the EMPR.
Note) While the motor is running, the Test/Reset key does not work.
Current value and information display
R S T-phase display
Motor state LED
Motor startup button
2. Setting
1) Press the Enter key. Then “P-99” is displayed.
Use the Up/Down keys to change the password.
Trip/alarm release button
Go to previous step,
Fix/circulate measurement screen
Go to items (set value increase)
2) Press the Enter key to enter A-gr setup mode.
Use the Up/Down keys to select a group and Press the Enter key to enter the selected group. Press the Test/Reset key to move back to the previous mode.
3) In the A-Grp mode, Press the Enter key. Then “1.CHA” is displayed.
Use the Up/Down keys to select an item and Press the Enter key to enter the selected item.
Press the Test/Reset key to move back to the previous mode.
4) Use the Up/Down keys to set up the value and Press the Enter key to save it.
Note) When the power is supplied first or is resupplied after a power failure, must set up the date in b-gr, 5.S-d.
Set up the rated current S/W while the power is off.
Unit display LED
Operation mode LED
Communication status LED
Select operation mode
Go to menu, Change and save set value
Go to items (set value decrease)
3 .
Quick Setup
1) Press the “Up and Enter” keys at the same time. “UPLD” is displayed and settings are uploaded to the display.
2) Insert the display to the body without settings, and then press the Test key to enter the test mode.
3) Press the “Down and Enter” keys at the same time. “TEST” is displayed and downloading is completed.
4) Press the Test key to return to the normal mode.
Note) Communication settings cannot be uploaded or downloaded.
4 .
Setting Checkup
1) Press the Enter key.
2) Use the Up/Down keys to select a group and Press the Enter key to enter the selected group.
Press the Test/Reset key to move back to the previous mode.
3) Use the Up/Down keys to select an item and Press the Enter key to enter the selected item.
4) Press the Enter key again to check settings.
5 . Failure Event Checkup
1) Press the Up and Down keys at the same time to display “1.O-C” (recent failure events).
Note) When no failure events are stored, “1.non” is displayed.
2) Use the Up/Down keys to select an event and press the Enter key to go to the selected event.
3) The R-phased failure current is displayed. Every time the Down key is pressed, S-phased failure current, Tphased failure current,
overload rate and date are displayed one after the other.
4) Press the Test/Reset key to move back to the previous mode.
5) Press the Up and Down keys at the same time to get out of the failure event checkup mode.
6 .
Forced Thermal Reset
When the system is tripped while it is in the thermal inverse time mode, if you want to turn the EMPR into the cold mode by resetting the motor’s heat amount, Press the Enter and Test/Rest keys at the same time.
* When a trip occurs due to the thermal excess current, if the motor is started right after it is reset, as the motor is hot, it is highly likely that the motor is tripped again.
LSIS Co.,Ltd.
65
Operation & setting method
Setting Menu (A Group)
Group
A
Menu Setting Value dEF/th/n-th
1~60s
1~200s
0.5~10A/5~100A
0.25, 0.5, 1~200 note 1)
Off, 200~800%
Off, 150~500%
Off/On
Off, 10~70%
Off/On
Off, 30~90%
0ff, 0.03, 0.05/0.1~3A
Off, 20~500% (FLCmin) note 2)
0.05, 0.1~1.0s
On/Off
Off, 500~1000%
I-tp, I-AL, ALo, U-C, OrH
On, 60~110/10% note 3)
1A1b, 2A, 2b
Operation Time (sec)
Delay Time (sec)
Rated Current
Lock Protection (sec)
Stall Protection (sec)
Open Phase
Unbalance Protection (%)
Reverse Phase
Description
Operation Characteristics (Definite/Thermal Inverse/Inverse)
CT Ratio (4 times, twice, once)
Under Current Protection (%)
Ground Fault Operation Current (Zero sequence CT) (A)
Ground Fault Operation Current (Residual circuit) (FLCmin)
Ground Fault Operation Time(sec)
Ground Fault Delay During Start
Instantaneous Protection (%)
07-08 Output setting (see the output information described below.)
07-08 Output setting (current or no current, and alarm)
Contact (95-96, 97-98) Setting
Note) 1. In case of CT ratio, rated current setting S/W is not displayed; in case of 100A product, 5.Ctr(CT) item is not displayed.
2. In case of 10A rating, it is possible to set to 0.1~2.5A; in case of 100A rating, it is possible to set to 1~25A.
3. No. 18 menu appears only if “ALo” is enabled in No. 17 menu.
(On: if a current is recognized, 07-08 contacts are displayed. 60~110%: if an on-load current value is higher than a set load factor, 07-08 contacts are displayed.)
4. No. 17 menu operation
17.AL Setting
I-tp
I-AL
U-C
OrH
18.Ar Setting
ALo
On
60~110%
Output conditions
Detect instantaneous current
Detect instantaneous current
Detect on-load less than low current set value
Set and display operating time
Select 18.Ar setting
If ALo is set in the No. 17 menu
Display on-load status( I > 0A)
On-load of current higher than a set value
Alarm display type
Motor operation
Motor stop
Keep status
Keep status
Keep status
07-08
NC
NC
NC
NC
Comply with the set value of the No. 18 item
Motor operation 07-08
Keep status
Keep status
NC
NC
Default Value n-th
60
If dEF
Max. value
1
Off
Off
Off
Off
Off
Off
On
Off
I-tp
Off
Off
-
On
1A1b
19.cS Setting
1A1b
2A
2b
Output conditions
Normal operation status
Ground fault/leakage accident
Failures including overcurrent, phase failure, reverse phase, and ground fault
Normal operation status
Ground fault/leakage accident
Failures including overcurrent, phase failure, reverse phase, and ground fault
Normal operation status
Ground fault/leakage accident
Failures including overcurrent, phase failure, reverse phase, and ground fault
66 Electronic Motor Protection Relays
NO
NO
NC
NC
NC
NO
Contact display type
95-96 97-98
NC
NO
NO
NO
NC
NC
NO
NC
NO
NC
NO
NC
IMP Series
Setting Menu (B Group)
Group
B
Menu
On/Off
Off, 1~20min
Hour/Minute
Off, 1~8760 time
Setting Value
2009/01.01/00:00
Day/time : min
0.5~10/5~100A
1~247
96/192/384
On/Off
Note) 1. If power is first supplied or power is recovered after outage, make sure to enter date information (5.-sd).
2. Auto reset is applied only to overcurrent Trip.
Description
Electric Reset
Automatic Reset (min)
Run Time
Run Time Setup (Hour)
YY/MM/DD/ HH:MM (View/Setup)
Total Run Time
20mA Output settings
Communication address
Communication speed
SWAP
Default Value
On
Off
Time Check
-
-
Time Check
A420 model
M485 model
Operation Display
display Description
Over current Trip
Under current Trip
Remark
Operate within predefined time.
Operate within 3 seconds
Open Phase Trip
Unbalance Trip
Lock Trip stall Trip
Reverse Phase Trip
Operate within 1.5 seconds when the unbalance rate is over 70%.
Operate within 3 seconds. note 4)
Operate within 0.5 seconds. note 4)
Operate within 3 seconds.
Operate within 0.1 second.
Ground Fault Trip
Instantaneous Trip
Operate within predefined time.
Operate within 0.05 seconds.
Elapsed Time (No Trip) The operation time is reset when the Reset key is pressed.
Communication Fault between Body and Display
(Press the ENTER/RESET key to return to the normal mode)
Different program version between main body and display part
Reverse Phase Current
R Phase
S Phase
T Phase Load Rate Unit
Communication Status
Ground Fault Current
Note) kW, kVar, and V indicate the specification of the voltage models
(under development).
Note) 1. The maximum allowable operating time of Loc function and reverse phase function is +50mSec.
2. Reverse phase function is detected for one second at the time of startup.
3. The allowable operating time of the instant function is +20mSec.
4. Inverse time: detect after O.t, Definite time: detect after D-t
7 .
IMP Specifications for Low Voltage 3-Phase Induction Motors (Reference)
Full Load Current for the Motor
0.7A or less
0.7~1.6A
1.6~8A
7~100A
90~120A
120A~160A
160~240A
240~320A
320~400A
400~480A
480~640A
Current
Selection S/W
0.5~10A
5~100A
0.5~10A
IMP Settings
Wire Tunnel
4 times
Twice
Once
Once
Once
Once
Once
Once
Once
Once
Once
CT ratio
0.25
0.5
1
80
100
120
160
1
30
40
60
External CT
-
-
-
-
SCT-150
SCT-200
SCT-300
SCT-400
500 : 5
600 : 5
800 : 5
220V
0.1
0.25
1.5
90
110
132
160
25
30
45
55
Note) 1. This table is written based on the full load current.
2. The CT is selected as a reference for the EMPR’s current setting range.
Unbalance Rate
Motor Output (Less than kW)
380V
0.18
0.55
3
160
200
250
320
45
55
75
110
Current Unit
Load Rate Display
440V
160
200
250
320
55
55
90
132
0.2
0.6
3.7
LSIS Co.,Ltd.
67
R상
S상
역상분 전류
T상
지락전류
불평형률 전류단위
부하율 단위 통신상태 부하율표시
Operation & setting method
8.Analog (DC 4~20mA) Output
1) The biggest current out of measured 3-phase currents is converted into DC 4mA~20mA and the current measured remotely by digital meter can be displayed.
2) When there is no current, 4mA is sent. If the current goes beyond the predefined value, 20mA is sent.
20mA
16mA
13.6mA
12mA from 3A. Thus, when the current is under 0.3A (3A), 0A is measured and output is 4mA. (To measure the load current correctly, an appropriate CT should be used).
16.8mA
13.6mA
Note) The allowable burden is less than 500Ω. Considering the receiver resistance (usually 250Ω) and track resistance), the shielding cable should be used.
Analogue output when the output is set to be 5A (50A)
4mA
0A
0A
0.1A
1A
0.2A
2A
13.6mA
3A
0.4A
4A
20mA
0.5A/0.5A~60A
5A/5A~60A
12mA
8mA
4mA
0.15A
8mA
4mA
0A
0A
0.15A
1 0.1A
1A
2
20
0.2A
2A
3
30
0.3A
3A
4
40
0.4A
4A
5
50
0.5A/0.5A~60A
5A/5A~60A
Analogue output when the output is set to be 10A (100A)
16.8mA
13.6mA
20mA
10.4mA
8mA
7.2mA
13.6mA
4mA
8mA
0A
4mA
0A
0.15A
10.4mA
7.2mA
10 2A
20A
2
20 4A
40A
3
30
16.8mA
6A
60A
4
40 8A
80A
5
50
6A
60A
100A/5A~100A
20mA
16mA
0A
0A
2A
20A
4A
40A
13.6mA
60A
8A
80A
20mA
10A/0.5A~10A
100A/5A~100A
12mA
8mA
7.2mA
10.4mA
4mA
20mA
16mA
8mA
13.6mA
7.2mA
10.4mA
13.6mA
16.8mA
7.2mA
0A
0A
10.4mA
1A
10A
2A
20A
3A
30A
4mA
16.8mA
20mA
20mA
4A
40A
5A/0.5A~10A
50A/5A~100A
20mA
16mA
0A
0A
1A
10A
2A
20A
13.6mA
3A
30A
4A
40A
20mA
5A/0.5A~10A
50A/5A~100A
12mA
8mA
7.2mA
10.4mA
4mA
0A
0A
1A
10A
2A
20A
3A
30A
4A
40A
5A/0.5A~10A
50A/5A~100A
0A
0A
2A
20A
4A
40A
6A
60A
8A
80A
10A/0.5A~10A
100A/5A~100A
68 Electronic Motor Protection Relays
Terminal Configuration / Wiring & cable connection
IMP Series
Terminal Configuration
Terminal layout
VR VS TRX(+) TRX(-) 05 06
A1 A2
(-)
95 96 97 98 07 08 Z1
ZCT
Z2
Communication specification
• Operation mode: Differential
• Distance: Max. 1.2km
• General RS-485 shielded twist 2-pair cable
• Baud rate: 9600/19200/38400bps
• Transmission Method : Half-Duplex
• Max. In/Output Voltage : -7V~+12V
Engrave
A1(+), A2(-)
95-96
97-98
07-08
Z1, Z2
TRX(+)
TRX(-)
VR/VS/VT
05-06
Description
Input terminal for operation power
When the power is ON (NC contact output)
When the power is ON (NO contact output)
Converted to the NC mode only when an instantaneous trip occurs.
Output terminal for the zero-phase sequence current transformer
RS485 terminal (TRX+) Or 4~20mA (+) output
RS485 terminal (TRX-) Or 4~20mA (-) output
3-phase voltage input terminal
AC/DC85~245V
M485, A420 Type
Remark
Settings Menu Reference
Specific ZCT (for the EMPR)
Output terminal for voltage protection
Specifications not available for IMP-C models
Note) 1. The 3-phase voltage input terminal and 05-06 output terminal should be connected only for voltage protection models, which will be released in the future.
2. For RS485 connection, the terminal resistance should be 120Ω.
3. For 4~20mA current, the maximum burden should be less than 500Ω.
Note 1)
With the External CT
Note) 1. When the zero-phase-sequence current transformer is used to detect ground faults, connect the ZCT.
2. When the single-phase motor is used, all phases are connected except the S phase, and open-phase, unbalance and ground fault should be set OFF.
3. It is possible to change settings of output contact(95-96, 97-98, 07-08) at your discretion.
LSIS Co.,Ltd.
69
Dimensions
One-Body Type
Unit : mm
Separate Body Type
Note) The cable should be purchased separately (1m/1.5m/2m/3m).
Unit : mm
70 Electronic Motor Protection Relays
17 17 56 17
17
M4 M4
22 M4
90 90
90
26 26 44
26
44
44
MEMO
IMP Series
LSIS Co.,Ltd.
71
Innovative Upgrade of Motor Control Panel!
More compact and Safer! We implement perfect motor protection.
A6 72 Electronic Motor Protection Relays
• Power, Voltage, Current (measurement error: 1%)
• Power, Voltage, Current, Power Factor Protection
• Harmonic measurement (1st to 16th )
• Diverse motor starting types
(Full voltage, Y-D, Reversible, Reactor, Inverter Starting)
• Modbus communication and 4~20mA
One model with various motor starting types
One S-EMPR model is applicable to various motor staring types, such as full voltage starting, Y-△ starting, reversible staring, Reactor starting, and Inverter starting.
A variety of SCADA functions based on sequence structure
With a simple sequence, it is possible to not only control local operation panel (LOP) and MCC panel, but conduct Supervisory
Control And Data Acquisition through SPLC or DCS based auto operation and communication.
MMP Series
MMP Series
Smart Electronic Motor Protection Relays
• Current, Voltage, Power Measurement,
and Power Factor Protection
• Instantaneous interruption compensation and restarting
• Harmonic measurement (1 st to 16 th )
• Modbus communication and 4~20mA
C o n t e n t s
74 Product characteristics
83 Rated specifications / Model numbering system
84 Operation & setting method
90 Terminal Configuration / Wiring & cable connection
96 Dimensions
LSIS Co.,Ltd.
73
Product characteristics
Convenience
Slide S/W
Slide S/W
MCU
MCU
30mA
30mA
MCU
25A
25A
INV
MCU
Slide S/W
25A
30mA 25A
Slide S/W
MCU
30mA 25A
INV
Return
INV
Slide S/W
25A
25A
Return
30mA
Save
25A
Total
25A
25A
Save
Slide S/W
Slide S/W
MCU
MCU
30mA 25A
30mA
MCU
25A
Comprehensive Digital Motor Protection Relay with the MCU (Microprocessor Control Unit)
Providing real-time processing and high precision
INV
MCU
Slide S/W
Applicable to invertor circuits
It can be installed in the downstream of a speed driver where harmonic noise exists. The allowable frequency range is 10 to 400Hz.
A harmonic filter must be used if THD (Total Harmonic Distortion) is over 30%.
* Set the ground fault mode off to avoid the trip due to current unbalace.
* Voltage parameters are not available. Power measurement accuracy is not guaranteed.
Function to store the cause(s) of failure / Fault
Up to 5 motor failure events may be saved in the system, so that the failure history can be easily identified.
25A
30mA 25A
Slide S/W
30mA 25A
One-Body Type and Separate Body Type
The display unit can be separated from the device to mount on the face of the panel, which enables the access to the unit without opening the door. All the functions remain unchanged after the separation.
INV
Return
INV
Slide S/W
25A
25A
Communication function (RS485 Modbus and 4~20mA output)
With universal RS485/Modbus communication types, it is possible to establish various system and communication networks.
Analog current signal (4~20mA) output is compatible with conventional TD(Transducer) based system.
A wide range of reset functions
Manual/Automatic/Electrical reset functions are provided for user convenience.
Return
30mA
Save
25A
25A
Date information display
When a failure occurs, the date and time of failure occurrence are saved in the system to accurately identify
25A
Save
Save
Total
Save
Total
Total
Total
Save
Total
Save
Total operating time and operating time setting
When the predefined operating time has elapsed, related information is displayed so that operators may replace
Total
Total
Quick Setup
Same setting for another devices in different panels can be done simply via the display unit.
~100A
~100A
Total
~100A
74 Electronic Motor Protection Relays
MCU
MCU
INV
Slide S/W
Return
30mA 25A
Reliability
Save
Total
MCU
INV
Slide S/W
30mA 25A
INV
Slide S/W
Save
INV
Return
Slide S/W
30mA 25A
MCU
Return
Return
Save
30mA 25A
Total
Total
Save
Total
MCU
INV
Slide S/W
MCU
Return
MMP Series
30mA 25A
INV
Slide S/W
Return
30mA
Save
25A
Thermal heat build-up inverse time/inverse time/definite time selection function
It is possible to select one of two types of inverse time and definite time in order to protect a motor perfectly.
Wide setting range and Dual protection
Providing Ground fault protection by dual detections -Zero-phase current and Residual current levels.
~100A
Up to 100A the device can be used without external CT to providing convenience and cost-effective solution.
Total
Save
Total
Various Motor Starting Modes
I n a Single Device several starting modes of operation available : Full voltage start, Y-
Reactor start, Inverter start.
△ start, Reversible start,
Metering of Current, Voltage and Energy (with 1% accuracy for A & V)
Real-time energy metering with high accuracy to support energy-saving Current / Voltage THD measurements (16 harmonic)
Carrying out complex relay functions related to Current, Voltage, Energy and Power Factor
Overpower alarm supported for energy monitoring
~100A
Self-diagnosis and Sequence monitoring
Providing a self-diagnosis function such as internal memory check in order to check fault conditions quickly
Power loss and Restarting
Device restarts after the momentary power loss for less than 30 seconds and returns to the former state.
Time-delay setting between 0 to 300 sec. is available to prevent overload from all the motors' restarting at the same time.
Frequent-Starting Protection
The number of automatic resets for the set time (20 minutes) is settable to provide frequent-starting protection.
LSIS Co.,Ltd.
75
Product characteristics
Protective functions
Product functions
Type
Currents
Voltages
Power
Function
Overcurrent
Locked Rotor
Stall
Phase loss
Imbalance
Phase reversal overcurrent
Undercurrent
Zero-phase ground current
Residual ground current
Instanteous
Select ground fault
Overvoltage
Undervoltage
Phase loss
Imbalance
Phase reversal overvoltage ground current overvoltage
Overpower
Underpower
Over power factor
Under power factor
MMP-C (Current type)
●
●
●
●
●
●
●
-
-
-
●
●
●
-
-
-
-
-
-
-
MMP-S (Select ground fault)
●
●
●
●
●
●
●
-
-
-
●
●
●
●
-
-
-
●
-
-
-
MMP-P (Power type)
●
●
●
●
●
●
●
●
●
●
●
●
●
-
●
●
●
●
●
-
●
Measurement function
Voltage(V)
Measurement
Current(A)
Zero-phase current(In)
Reverse current(I
2
)
Active power(W)
Reactive power(VAR)
Active power amount(WH)
Reactive power amount(WVARH)
PF
Voltage hamonics(%)
Current hamonics(%)
Range
0.00V~9999V
0.00A~9999A
0.00A~9999A
0.00A~9999A
0.000W~999.9MW
0.000W~999.9MVAR
0.000W~999.9MWH
0.000W~999.9MVARH
-1.00~1.00
0~100%
0~100%
Accuracy(%)
±1.0%
±1.0%
±3.0%
±3.0%
±1.0%
±1.0%
±1.0%
±1.0%
±0.03
±5.0%
±5.0%
Remarks
Phase1 : Phase voltage, Phase3 : Line voltage
Phase current
-
-
Forward
Forward
-
cosθ
2 nd -16 th odd harmonics
2 nd -16 th odd harmonics
76 Electronic Motor Protection Relays
Current protection
Over Current
The device provides overcurrent protection either with inverse-time or with definite-time element.
1) Inverse-time delay curve
The trip time decreases as the overcurrent increases in an inversetime curve.
Inverse-time delay curve
MMP Series
2) Definite-time delay curve
The operating time is unaffected by the magnitude of the overcurrent.
Definite-time delay curve
Stall/Locked Rotor
Stall activates when the motor is unable to rotate due to any externally mechanical obstruction, and Lock activates due to internal issue of the motor.
Phase Fail/Phase Unbalance
The motor is unable to start under phase loss. If it occurs while the motor is running it causes motor stopping by lack of torque, or significant rotor heating by reverse current. The S-EMPR calculates the percent three-phase unbalance current. If it exceeds 70%, which is determined to be phase loss, the device trips within 1.5 sec. If it is between 10 to 70% the device trips within3 sec. This function is disabled for a single-phase mode.
LSIS Co.,Ltd.
77
Product characteristics
Reverse Phase
This protection is for preventing the motor from reverse rotation. The device detects motor phase rotation and trips within 0.1 sec. if phase sequence is incorrect. It detects when the motor is starting.
* This function is disabled for a single-phase mode.
Under Current
If the real load current falls below the warning or trip level for longer than the time-delay setting, the device can issue a warning or trip signal.
Ground fault protection
Ground Fault
Stall activates when the motor is unable to rotate due to any externally mechanical obstruction, and Lock activates due to internal issue of the motor.
Zero-phase ground current
ZCT in or out of the product is used to detect zero current flowing in three phases.
Selective Ground Fault
If a non-grounding system has ground fault, the current over the zero current transformer of each distribution line flows from the load side to the power side in a good line, and from the power side to the load side in a bad line. This protection function is able to select and block a bad line by determining the direction of failure current on the basis of the zero voltage.
Instance
While an AC motor is running, if an actual load current value is higher than an set value of instantaneous current, Trip occurs in
50msec.
78 Electronic Motor Protection Relays
MMP Series
Selective Ground Fault Protection
If a non-grounding system has ground fault, the current over the zero current transformer of each distribution line flows from the load side to the power side in a good line, and from the power side to the load side in a bad line. This protection function is able to select and block a bad line by determining the direction of failure current on the basis of the zero voltage.
R
S
T
Ir
CLR
S EMPR
CB1
GPT
ZCT
1
Feeder 1
C1
In
Ic
1
Ig
Rg
CB2
S EMPR
ZCT
2
Feeder 2
C2
Ic
2
CB3
S EMPR
ZCT
3
C3
Feeder 3
Ic
3
CB4
S EMPR
ZCT
4
C4
Feeder 4
Ic
3
❶ - GPT : Grounding Potential Transformer
❷ - ZCT1, ZCT2, ZCT3, ZCT4 : Zero current transformer
❸ - CLR : Current-limiting resistor
❹ - CB : Circuit breaker
❺ - In : Current over GPT
❻ - S-EMPR MMP S : Smart digital motor protection relay
❼ - Ir : Current-limiting resistor current
❽ - Rg : Ground fault resistance at ground fault point
❾ - In : Current over GPT
❿ - C1, C2, C3, C4 : Line capacitance of each feeder
Operating characteristic
3°
Suppression area
87°
Directional
-Vo
3°
As shown the figure, the bad line (Feeder1) and the good line has an opposite current direction. With the use of this current direction, it is possible to select one. If another line has a failure, the charging current of the line flows in an opposite direction from the current flowing at the time of the accident.
Therefore, it does not run.
In a non-grounding system, the ground fault current is the sum of the line charging current and the limiting-resistance current. Since it is relatively small, zero CT(ZCT) is needed. This product has ZCT built in so that it is possible to make a system simply.
LSIS Co.,Ltd.
79
Product characteristics
Voltage & Power Protection
Over Current
Overvoltage protection detects the voltage levels and operates if they are greater than the setting to protect the sensitive loads or circuits against such condition.
Under Voltage
If the voltage levels fall below the setting the Undervoltage protection issues a warning or trip signal to protect the sensitive loads such as a inductive motor.
Phase Fail/Phase Unbalance
This protection operates if the percent phase-to-phase voltage unbalance is greater than the setting.
Used to prevent an excessive vibration of three-phase induction motor and a damage of the stator and rotor windings.
This function is disabled under a single-phase mode.
Reverse Phase
This protection operates if the percent phase reversal voltage is greater than the setting.
It detects when the motor is starting. This function is disabled for a single-phase mode.
Over Power
The overpower element operates if the three-phase active power exceeds the setting level.
This element can be used to prevent the power from entering the generator before disconnecting from the system when the generator operation is finished.
Under Power
The underpower element operates if the three-phase active power falls below the setting level.
Over Power Factor
The over power factor element operates if the power factor exceeds the setting level.
If the load is very small, especially for no-load the capacitive current may flow due to overcapacity of the capacitor in line, which causes the power loss of the line and transformer, and electric stress on motors. This element can be used to protect against such current.
Under Power Factor
The under power factor element operates if the power factor falls below the setting level.
If the power factor of a customer falls below that of a generator in a power plant the generator current increases over the rated current or the power output is limited. For this reason, the power factor of a customer is regulated.
In addition, the under power factor causes the increase of the input current which prevents the temperature rise in cables, transformers and motors.
80 Electronic Motor Protection Relays
Communications
Modbus Specification
Communication number
Baud rate
Communication Parity
Stop Bit
Communication data swap
Operation mode
Communication distance
Cable
Transmission Method
Max. In/Output Voltage
1~247
9600, 19200, 38400 bps
None, Even, Odd
1bit (fixed)
OFF / ON (Limited to float, long data of 0x04 (Read Input Registers) )
Differential
Max. 1.2km
RS-485 Shielded Twist 2-Pair Cable
Half-Duplex–
-7V~+12V
Communication system configuration
MMP Series
LSIS Co.,Ltd.
81
Product characteristics
Analog (4~20mA) output function
Specification
• This function measures the maximum out of the 3-phase currents and converts it into
DC 4~20mA for output, which can be converted back to the original value by a digital meter.
• 20mA Output Settings : 0.5~10A or 5~100A
Note) 1. In the 0.5~10A setting mode the device starts to measure from 0.15A, which means the current 0.15A or less is measured as 0A and the output becomes 4mA.
(0.15A when one> 4mA is being a real measurement)
2. Accuracy at 25°C : : ± 0.15% / ℃
• During stopping : 4mA
• Rated setting value or more : 20mA
• Load : 500Ω or less
Note) The allowable burden of cable must be less than 500Ω.Shielded cables are recommended in consideration of the resistance
of the receiving meter (typically 250Ω) and the line resistance.
* Output current =
=
(I upper - I lower)
TD setting
16mA
TD setting
× load current + 4mA
× load current + 4mA
13.6mA
16.8mA
20mA
20mA
16mA
12mA
8mA
4mA
82 Electronic Motor Protection Relays
0A
0A
0.1A
1A
0.2A
2A
0.3A
3A
0.4A
4A
Analog output for 10A (100A) output setting
20mA
16mA
12mA
8mA
4mA
0.15A
1
10
2
20
3
30
4
40
5
50
0.5A/0.5A~60A
5A/5A~60A
6A
60A
20mA
16mA
12mA
8mA
4mA
7.2mA
10.4mA
13.6mA
16.8mA
20mA
0A
0A
2A
20A
4A
40A
6A
60A
8A
80A
10A/0.5A~10A
100A/5A~100A
20mA
16mA
12mA
8mA
4mA
7.2mA
10.4mA
13.6mA
16.8mA
20mA
0A
0A
1A
10A
2A
20A
3A
30A
4A
40A
5A/0.5A~10A
50A/5A~100A
Rated specifications / Model numbering system
Rated specifications
Connection
Operation characteristic
Rated current
Display screen
Control Power
Reset
Auto
Manual
Mounting
Accuracy
Time delay
Start
Operation
Auxiliary contacts
Contact minimum load
ZCT input
I/O assured voltage
Environment
Insulation resistance
Lightning impulse voltage
Fast Transient
Power consumption
110V Type
220V Type
Operation Temp.
Storage Temp.
Humidity
Tunnel type (Passing through CT holes)
Thermal-inverse / Inverse / Definite
0.5~10A/5~100A (Select Rated on Order)
4 digit, 7-Segment, LED
110Vac or 220Vac 50/60Hz
1-20 minutes
ON / OFF selectable
Display unit : sepatately mountable
Current and voltage metering : ± 1% of rating or ± 2% of minimum rating
4~20mA output : ± 5%
1-200 seconds
1-60 seconds
6 contacts (3A / 250VAC at resistive load, power type based)
10mA / 5VDC
Basic installation of built-in ZCT
External ZCT (200mA/1.5mA, universal ZCT connectable)
63V ±10%
140V ±10%
-10~55℃
-20~70℃
RH 80% or under (non-condensing)
100MΩ/500VDC
1.2 × 50μs 5kV standard waveform applied
2kV/1Min
5W or under
MMP Series
Model numbering system
MMP C
C
S
P
Function
Current
Selective
Ground Fault
Power
B
B
Communication
Non
M RS485 & A420
10
Current Rating
10
100
0.5 ~ 10A
5 ~ 100A
220
Control Power
220
110
AC 220V
AC 110V
LSIS Co.,Ltd.
83
Operation and Setting
Before starting the motor, proceed as follows :
1. Connect the display unit to the main unit of the device and
then turn on. Verify that Power LED is switched on and
the measurement screen is displayed.
1) Verify the operations of ON, REVand STOP keys which are used to control motor starting.
Press ON key and then the red LED above the key is switched on and motor on signal is issued . Press STOP key and then the green LED above the key is switched on and motor on signal is stopped .
Note) REV key is activated when the motor control is set to reverse starting mode.
2) Verify the operations of a mode control key. Each time pressing L / R key
the control mode changes : MCC → AUTO → REMOTE → COM
3) When the device is booted up the measurement screen is display by default. Pressing Enter key allows to access the modes : Group → Menu → Setting value. Press Esc key to return to the previous mode.
Use Up & Down keys to change values in the screens of Measurement, Group, Menu,
Setting. When the relay / alarm operates press Reset key to reset.
Note) refer to a manual for the details.
2. Verify the operations of Test function and Reset key through trip.
1) Verify the wiring first. Press Enter key to access Group menu, and use Up / Down keys to access B Group as shown "b-gr" and press Enter to access Menu with displaying "1.Loc".
Use Up / Down keys to access "6.r-p" which denotes Phase reveral menu, and press Enter to access "CHEC" which denotes Setting value, and press Enter to view current wiring information.
Note) 1. The phase information is displayed only when current is applied. If there is no current "---" is displayed.
2. Voltage wiring information is available via "c-gr" (C group) → "8.urp" (Voltage phase reveral settings) → "CHEC" →
Pressing Enter Key. The phase information is available when a voltage is applied.
2) Turn on the motor and access "d-gr" which denotes D group and move to " " menu using
Up / Down keys and press Enter to access Fault items. Select the desired Fault item and press Enter to trip the device.
3) Press Reset key to reset the device and return to the measurement screen.
Note) In the first access to change a parameter "P-99" for password input is displayed. Press Up key to change it to "P-00" and
press Enter and then Setting change is allowed. If there is no input for 2 minutes it returns to the measurement screen.
3. Check the settings.
1) At normal state pressing Enter key access mode "A-gr" which enables setting. Select the desired group using the Up / Down keys and
press Enter key to enter the desired group. To enter previous mode, press the Esc key.
2) The desired group displays from No. 1 menu. Select the desired menu using the Up / Down keys and press Enter key to enter the setting mode.
To enter previous mode, press the Esc key.
3) Press Up / Down keys in the setting screen and then "P-99" is displayed. Press Up / Down keys to change the password to "P-00" and
press Enter to release it. After that select the desired value and press Enter to save the setting.
Note) Enter the date exactly when the power is turned on for the first time or recovered after the outage.
84 Electronic Motor Protection Relays
MMP Series
A-group
Group Menu Description
Single-phase / 3-phase 1P/3P
Setting range
A
Frequency
Characteristics (Over Current Protection)
Operating time
Time Delay
Rated current (10, 100) Note 2)
CT ratio
Starting mode
50/60
Off/dEF/th/n-th Note 1)
1~60sec (5/10/20/30/60)
1~200sec
0.5~10/5~100
0.25/0.5/1~200 dir/y-d/F-r/Ind/lut
Y start time (lut start time)
Y-D switching time
Outage compensation time
1~120sec (lut : 0.1~1sec)
0.05/0.1/0.2
Off/1~30sec
Restart time 0~300sec
Note) 1. Operating characteristic th denotes inverse-time curve with thermal-memory and n-th denotes inverse-time curve without thermal-memory .
2. For the 100A type there is no CT ratio as it is fixed as 1.
3. Some menu are not disabled depending on the related setting.
4. Phase reversal mode needs to be switched on only during test starting, or verify wiring via wiring CHEC function. it is recommended to turn off during normal running, .
(An error on phase reversal may occur due to noise.)
B-group
Group
B
Menu Description
LOCK
STALL
Phasee loss (current)
Phasee unbalance (current)
Phasee loss / unbalance Time-delay
Phase reversal (current)
Off/200~800%
Off/150%~500%
On/Off
Off/30~70%
0~200sec
Setting range
Off/On/CHEC Note 1)
Phase reversal operation time
Undercurrent
ZCT selection (PC mV, 1.5mA)
Ground fault (Zero-phase)
Ground fault (Residual current)
Ground fault operation time
Selective ground fault(SGR) current setting
Selective ground fault(SGR) voltage setting
0.1~1.0sec
Off/30~90%
100/1.5 Note 2)
Off/0.03/0.05/0.1~3.0
Off/30~100%
0.05~3.0sec
Off/0.03/0.05/0.1~3.0
8~80V
Selective ground fault(SGR) reference angle setting 0~90 angular measure
Selective ground fault(SGR) operating time 0.05~3.0sec.
Ground fault Time-delay(Ground fault, SGR) 0~200sec
Instantaneous protection
Output contact method
Current Y / N, Alarm
Ground fault Overvoltage
Operating time
Relay output selection
THD (voltage)
Off/500~5000%
I-tp, ALo, U-C, OrH
On/60~110%
Off/8~80V
0.05~3.0sec
u-AL, AtP
0~100%
Remarks
Note) 1. If CHEC set value of reverse phase is selected, wiring information additionally appears.
2 ZCT is selected differently depending on whether to use our product or other universal products.
3. Error assurance range 10A type: ~100A / 100A type: 50Hz~600A, 60Hz~720A
4. I-tp: Instantaneous trip, circuit breaker trip(interaction), Alo: instantaneous alarm, U-C: in case of low-current operation, OrH: if a motor’s continuous operating time is higher than a set value
In case of ALL setting, when all current relay factors (including I-tp) work, output (AUX-C3) appears.
5. No support is given for a single-phase motor.
LSIS Co.,Ltd.
85
0
3.0
60
Off
I-tp
On
Off
3.0
u-AL
Unit : %
Off
3.0
Off
80
0.1
Off
Enbd
Off
On
Off
0
Off
Default
Off
Off
3P
Default
5 (0)
0.2
Off
0
200
10
1 dir
60 n-th
60
Operation and Setting
C- group : Menu for Power type activation
Group Menu Description
Rated voltage (line to line)
C
Over voltage
Over voltage operation time
Under voltage
Under voltage operation time
Phasee loss (voltage)
Unbalance (voltage)
Phase reversal (voltage)
Phase reversal operation time
Rated power
Over power
Over power operation time
Under power
Under power operation time
Over power factor
Over power factor operation time
Under power factor
Under power factor operation time
Relay output selection
Reactive power (meter)
Free Power Amount
THD (Free Power Amount)
Note) No support is given for a single-phase motor.
0.1~1.0sec
0.1~999.9KW
Off/100~800%
1~100sec
Off/20~100%
1~100sec
Off/0.20~1.00
1~30sec
Setting range
110~480
Off/105~130%
1~30sec
Off/50~95%
1~30sec
Off/On
Off/5~40%
Off/On/CHEC
Off/0.20~1.00
1~30sec u-AL/u-tP
0~999.9 Mvar
0~999.9 Mvah
0~100%
Off
100
Off
30
1
999.9
Off
100
Off
30 u-tP
Unit :
Kvar
Unit :
Kvah
Unit : %
30
Off
30
Off
Off
Off
Default
380
Off
Remarks
86 Electronic Motor Protection Relays
MMP Series
D-group
Group
D
Menu Description
Total running time
Running time
Running time setting
Contactor check
Date note 1)
Contactor counter
Fault cause check note 1)
note 3)
Automatic reset time
Automatic reset number
Set number of times
Communication address note 4)
Off/1~5
Communication speed note 4)
Swap note 4)
1~247
9.6/19.2/38.4K
On/Off
Parity setting note 4) nonE/odd/EUEn
20mA setting note 4)
Stored data deletion
Operation test
0.5~10/5~100
All : for all subparameters
A-P : active energy rA-P : reactive energy trt : total running time
CCC : contactor counter
CALo : calories
FALt : fault events o-L : overcurrent test o-U : overvoltage test g-F : ground fault test
I-C : instantaneous test
Note) 1. The contactor operation is counted up to 65000cycles and then initialized.
2. The date setting can be stored after filling up month, day, hour and minute.
3. The trip cause can be stored up to 5 recent events and then the oldest event is deleted first.
4. 10.Ad, 11.bs, 12.SP, 13.Pr, 14.td are available for communication type products.
5. Data clear and test can be inputted in the normal state, and test items can be viewed while a motor is switched on.
Setting range
0~9999day / 0~23h / 0~59m
0~9999h /
0~59m
Off/10~8760
Off/On
2013~2100y
/ 1~12 (Mon), 1~31 (Day)
/ 0~23h, 0~59m
-
1. The most recent
2. The 2nd. recent
3. The 3rd. recent
4. The 4th. recent
5. The 5th. recent
OFF / 1~20m
-
-
-
Off
Off
247
9.6K
Off nonE
10/100
Default
-
-
Off
Off
2014.01.01.
0:00
-
LSIS Co.,Ltd.
87
Operation and Setting
4.
Up & downloading of all settings once (Quick setup)
1) Press Up and Enter keys at the same time at the status of normal, MCC mode and motor stop, then "UPLd" begins to flash on the screen which denotes the setting values of the device are being uploaded in the display unit and "U.END" is displayed when completed. Press Enter key to return to the measurement screen.
2) After installing the uploaded display unit onto the device that is not set yet, press Down and
Enter keys at the same time at the status of normal, MCC mode and motor stop, then "dnLd" begins to flash on the screen which denotes the setting values of the display unit are being downloaded in the device and "d.END" is displayed when completed.
Press Enter key to return to the measurement screen.
Note) 1. Up & downloading is available between the same models. If the models are different each other an error occurs with "d.Err" message.
2. Up & downloading of date, running time and fault cause are not available.
5. Checking fault history
1) Press Esc and Enter keys at the same time in the measurement screen, then the most recent fault cause in #7 menu of D-group is displayed.
Note) If there is no fault history "1.non" is displayed.
2) Use Up and Down keys to move to the desired one out of 5 fault events and select by pressing Enter key.
3) The fault current of phase R is displayed. Each time pressing the down key following informations are displayed in turn : fault current of phase S / fault current of phase T / overload ratio / date
4) To enter the previous mode, press Esc key.
5) Press Esc and Enter keys at the same time to return to the measurement screen.
6. Forced reset of thermal memory
Press Esc and Stop keys at the same time to make the tripped motor become a cold state by force when operating characteristic is set to inverse-time curve with thermal-memory (th).
If a motor is tripped due to overcurrent the immediate pressing of reset key at the hot state of the motor causes immediate tripping.
To avoid it reset via pressing Esc and Stop keys at the same time which makes the motor cold state.
88 Electronic Motor Protection Relays
MMP Series
Fault cause information
Screen Fault cause
Overcurrent
Current
Voltage
Voltage
Others
Ex)
Underpower
Over power factor
Under power factor
External input trip
Error.1 occured
Error.2 occured
Error.3 occured
Error.4 occured
Running hour over
Display comm. error
Version check
Lock
Stall
Phasee loss
Phasee unbalance
Phase reversal
Undercurrent
Instantaneous
Ground fault (ZCT)
Ground fault (Residual)
Overvoltage
Undervoltage
Phasee loss
Phasee unbalance
Phase reversal
Overpower phase, load rate, time
Additional information phase, load rate, time phase, load rate, time phase, unbalance rate, time phase, unbalance rate, time time phase, load rate, time phase, load rate, time phase and neutral, time phase and neutral, time phase, rate, time phase, rate, time phase, unbalance rate, time phase, unbalance rate, time time phase voltage, rate, time phase voltage, rate, time phase voltage, rate, time phase voltage, rate, time time
Current detected after motor off
No current detected after motor on
For / Rev starting signal input at the same time in local / auto mode
External storage memory error
Alarm occurs when accumulated running hour is over the setting value
Comm. error occur between display unit and device.
※ Please contact us.
Press Reset+Esc keys in normal state
LSIS Co.,Ltd.
89
Terminal Configuration / Wiring & cable connection
Terminal Configuration (S-EMPR MMP-PM)
Terminals
Va, Vb, Vc
Z1, Z2
Z2V, Z1V
4~20mA (+), (-)
TRX1+, TRX1-
TRX2+, TRX2-
A1, A2
C1
Lop/Stop, For,
Rev, Res, E/S
C2
Main, Y, D, Auto,
Volt
C3
Aux
Description
Voltage input
ZCT input
4~20mA output
RS485 communication
Control power input
Contact input Common
Contact input
Relay output Common
Relay output
Relay output Common
Relay output
-
Current model Blank
Remarks
Universal (Z1, Z2 : 1.5mA)
Z2V, Z1V Dedicated (Z2V, Z1V : 100mV)
Modbus(1 channel)
-
110Vac or 220Vac 50/60Hz
RES : Reset, E/S: Emergency Stop
-
D: Delta, VOLT : output contacts for voltage & power elements
Aux output Common
Current element output contacts
Voltage
Power supply
Terminal Configuration (S-EMPR MMP-CM)
Terminals
A1, A2
C1
Lop/Stop
For
Rev
Res
E/S
C2
Main
Y
D
Auto
C3
Aux
Z1,Z2
Z1V, Z2V
+,-
TRX+,TRX-
Description
Operating power input terminal
Contact point in put common
Remarks
110Vac or 220Vac 50/60Hz
Lop/Stop, For, Rev, Res, E/S contact point
Lop operation mode selection and external stop S/W -
External On(Forward) input S/W On input in Lop/Auto operation
Reverse input S/W in forward/reverse starting
External Reset S/W
REV input in Lop/Auto operation
Reset input in Lop operation
External Emergency Stop S/W
Contact point output common
Motor On output
Y-Delta starting: Y contact point output -
-
Main, Y, D, Auto contact point
If forward/backward staring, forward rotation output
Inverter starting: Inverter contact point output
Full voltage starting: No use
Forward/backward staring: No use
Reactor starting: No use
Y-Delta starting: Delta contact point output
Forward/backward staring: reverse rotation contact point output -
-
Reactor starting: Reactor (R) contact point output -
-
-
-
-
Inverter starting: Bypass contact point output
Full voltage starting: No use
Auto state signal output
Contact point output common
Current factors contact point output
Zero current transformer output connection terminal
Zero current transformer output connection terminal
4~20mA output
RS485terminal
-
-
If Auto state mode is selected
Aux contact point only
-
-
Universal ZCT(200mA/1.5mA)
-
ZCT(200mA/100mV) for DMP
Power supply
90 Electronic Motor Protection Relays
MMP Series
Terminal Configuration (S-EMPR MMP-SM)
Auto
Volt
C3
AUX
Vo+, Vo-
Z1,Z2
+,-
TRX+,TRX-
Terminals
A1, A2
C1
Lop/Stop
For
Rev
Res
E/S
C2
Main
Y
D
Description
Operating power input terminal
Remarks
110Vac or 220Vac 50/60Hz
Contact point in put common
Lop operation mode selection and external stop S/W -
Lop/Stop, For, Rev, Res, E/S contact point
External On(Forward) input S/W
Reverse input S/W in forward/reverse starting
External Reset S/W
On input in Lop/Auto operation
REV input in Lop/Auto operation
Reset input in Lop operation
External Emergency Stop S/W
Contact point output common
Motor On output
Y-Delta starting: Y contact point output
Inverter starting: Inverter contact point output
Full voltage starting: No use
Forward/backward staring: No use
Reactor starting: No use
-
-
-
-
-
-
Main, Y, D, Auto contact point
If forward/backward staring, forward rotation output
Y-Delta starting: Delta contact point output
Forward/backward staring: reverse rotation contact point output
Reactor starting: Reactor (R) contact point output
Inverter starting: Bypass contact point output -
-
-
-
Full voltage starting: No use
Auto state signal output
Ground fault overvoltage factors and current trip contact point output -
-
If Auto state mode is selected
Contact point output common
Other current factors contact point output
Zero voltage input
Zero current transformer output connection terminal
4~20mA output
RS485terminal
-
-
-
-
Aux contact point only
Universal ZCT(200mA/1.5mA)
Vo Vo
Power supply
DI
ZCT 4~20mA RS485
DO
*Attention in panel design
1. It is required to have grounding connection with all equipment.
2. It is required to minimize wiring as most as possible.
3. After a shield-type cable is applied, it is required to ground the shield.
*If induced voltage occurs
1. It is required to add a proper capacitor in parallel depending on the parasitic capacitance of product input part.
2. If induced voltage occurs even after the capacitor is added,
it is required to get auxiliary relay energyed in order for an input to make possible through an auxiliary contact point when a circuit is designed.
LSIS Co.,Ltd.
91
Terminal Configuration / Wiring & cable connection
Full Voltage Start
R
S
T
3Ø 3W 440V 60HZ
MMP
ZCT
52
MCCB
SHT
Z1
Z2
88M
MC
MCC
LOP(Local Operation Panel)
MCC
Lop
Stop For Reset
R
S
T
110Vac or
220Vac 50/60Hz
A2 C2
Lop/
Stop For Reset
Va
Vb
Vc
ZCT +
ZCT -
ZCT_V +
Z1
Z2
Z1_V
88M
88MX
A1 Main
88M
Auto
C2
Auto
Auto status contact
Auto
External TRIP
Trip1
SHT
E/S
COMM. Port
Modbus/ RS-485 &
4~20mA
Auto
VOLT
(Voltage elements)
AUX(Current elements)
C3
C1
Input(220VAC)
Lop/Stop, For, REV, RES,
E/S (C1 Common)
Output
Main, Y, D, Auto,
Volt (C2 Common)
I-tp, Alo, U-C, OrH, ALL
AUX output upon the selecting menu
(C3 Common)
COMM. Port
- RS-485
TRX1 +, TRX1 -
TRX2+, TRX2-
- 4~20mA :+, -
ZCT
Dedicate Z1_V, Z2 : 100mV
Universal Z1, Z2 : 1.5mA
MCCB
Aux
M
Note) In case of distance operation (LOP / AUTO), if a wiring distance is too long, induced voltage can cause malfunction. Therefore, bear in mind this point at the time of designing a panel.
Reversible operation
R
S
T
3Ø 3W 440V 60HZ
MMP
ZCT
MCC
LOP(Local Operation Panel)
MCC
Lop
(HY255)
Stop For Reset REV
Auto
C2
Auto
Auto status contact
For REV
External TRIP
Trip1
52
MCCB
SHT
Z1
Z2
88F
MC
110Vac or
220Vac 50/60Hz
88R
MC
R
S
T
Va
Vb
Vc
ZCT +
ZCT -
ZCT_V +
Z1
Z2
Z1_V
A2 C2
Lop/
Stop For Reset
A1
A1
MAIN Y
88R 88F
88F
A2
88FX
88F
88R
On
88R
A1
88RX
88F
On
88R
A2
REV
SHT
E/S
COMM. Port
Modbus / RS-485 &
4~20mA
Auto
VOLT
(Voltage elements)
AUX(Current elements)
C3
C1
Input(220VAC)
Lop/Stop, For, REV, RES,
E/S (C1 Common)
Output
Main, Y, D, Auto,
Volt (C2 Common)
I-tp, Alo, U-C, OrH, ALL
AUX output upon the selecting menu
(C3 Common)
COMM. Port
- RS-485
TRX1 +, TRX1 -
TRX2+, TRX2-
- 4~20mA :+, -
ZCT
Dedicated Z1_V, Z2 : 100mV
Universal Z1, Z2 : 1.5mA
MCCB
Aux
M
92 Electronic Motor Protection Relays
MMP Series
Y- D Start
R
S
T
3Ø 3W 440V 60HZ
MMP
ZCT
MCC
LOP(Local Operation Panel)
MCC
Lop
Stop For Reset
52
MCCB
SHT
Z1
Z2
88M
MC
88D
MC
110Vac or
220Vac 50/60Hz
R
S
T
Va
Vb
Vc
ZCT +
ZCT -
ZCT_V +
Z1
Z2
Z1_V
A2 C2
Lop/
Stop For Reset
88MX
88M 88D
88DX
88Y
On
88Y
88YX
88D
On
A1 Main Delta Y
88Y 88D
88Y
MC
88M 88D 88Y
Auto
Auto
C2
Auto status contact
For
External TRIP
Trip1
SHT
E/S
COMM. Port
Modbus/ RS-485 &
4~20mA
Auto
VOLT
(Voltage elements)
AUX(Current elements)
C3
C1
Input(220VAC)
Lop/Stop, For, REV, RES,
E/S (C1 Common)
Output
Main, Y, D, Auto,
Volt (C2 Common)
I-tp, Alo, U-C, OrH, ALL
AUX output upon the selecting menu
(C3 Common)
COMM. Port
- RS-485
TRX1+ , TRX1 -
TRX2+, TRX2-
- 4~20mA :+, -
ZCT
Dedicated Z1_V, Z2 : 100mV
Universal Z1, Z2 : 1.5mA
MCCB
Aux
M
Reactor Start
R
S
T
3Ø 3W 440V 60HZ
MMP
ZCT
52
MCCB
SHT
Z1
Z2
88M
MC
88R
MC
MCC
LOP(Local Operation Panel)
MCC
Lop
Stop For Reset
110Vac or
220Vac 50/60Hz
R
S
T
Va
Vb
Vc
ZCT +
ZCT -
ZCT_V +
Z1
Z2
Z1_V
A2 C2
Lop/
Stop For Reset
88M
88MX
88R
88RX
A1 Main Y
88M 88R
Auto
Auto
C2
Auto status contact
For
External TRIP
Trip1
SHT
E/S
COMM. Port
Modbus/ RS-485 &
4~20mA
Auto
VOLT
(Voltage elements)
AUX(Current elements)
C3
C1
Input(220VAC)
Lop/Stop, For, REV, RES,
E/S (C1 Common)
Output
Main, Y, D, Auto,
Volt (C2 Common)
I-tp, Alo, U-C, OrH, ALL
AUX output upon the selecting menu
(C3 Common)
COMM. Port
- RS-485
TRX1 +, TRX1 -
TRX2+, TRX2-
- 4~20mA :+, -
ZCT
Dedicated Z1_V, Z2 : 100mV
Universal Z1, Z2 : 1.5mA
MCCB
Aux
M
LSIS Co.,Ltd.
93
Terminal Configuration / Wiring & cable connection
Irreversible full voltage starting
E
MCC
LOP(Local Operation Panel)
MCC
Lop
Stop For Reset
CLR
E
GPT
110Vac or
220Vac 50/60Hz
A2 C2
Lop/
Stop For Reset
Vo-
Vo+
88MX
ZCT +
ZCT -
Z1
22 88M
On
A1 Main C1
88M
Auto
Auto
C2
Auto status contact
Auto
EXT
* Input
Lop/Stop, For, REV, RES, E/S (C1)
* Output
Main, Y, D, Auto, Volt (C2)
Aux (C3)
External TRIP
Trip 1
COMM. Port
COMM. Port
- RS -485
TRX1 +, TRX1 -
TRX2 +, TRX2 -
- 4~20mA : +, -
Modbus/ RS-485 or
4~20mA Output
Auto
Volt
Aux
C3
Reversible full voltage starting
MCC
LOP(Local Operation Panel)
MCC
Lop
Stop For Reset REV
Auto
C2
Auto
Auto status contact
FOR REV
External TRIP
Trip 1
E
CLR
E
GPT
110Vac or
220Vac 50/60Hz
Vo-
Vo+
A2 C2
Lop/
Stop For Reset REV
88MX
ZCT +
ZCT -
Z1
22
A1 Main
88M
On
88M
On
C1
88M
EXT
* Input
Lop/Stop, For, REV, RES, E/S (C1)
* Output
Main, Y, D, Auto, Volt (C2)
Aux (C3)
COMM. Port
COMM. Port
- RS -485
TRX1 +, TRX1 -
TRX2 +, TRX2 -
- 4~20mA : +, -
Modbus/ RS-485 or
4~20mA Output
Auto
Volt
Aux
C3
94 Electronic Motor Protection Relays
MMP Series
Inverter Start (Current)
R
S
T
3Ø 3W 440V 60HZ
MMP
ZCT
L1 L2 L3
T1
Inverter
T2 T3
52
MCCB
SHT
88M
MC
88I
MC
Z1
Z2
MCC
LOP(Local Operation Panel)
MCC
Lop
(HY255)
Stop For Reset REV
Auto
Auto
C2
Auto
상태
접점
FOR REV
External TRIP
Trip1
MCCB
Aux
110Vac or
220Vac 50/60Hz
88B
MC
Va
Vb
Vc
ZCT +
ZCT -
ZCT_V +
Z1
Z2
Z1_V
A2 C2
Lop/
Stop For Reset
88MX
6.149 mm
88IX 88BX
88B
On
88I
On
88M 88I 88B
A1 Main Delta Y
88B 88I
88M 88I 88B
REV
SHT
E/S
COMM. Port
Modbus/ RS-485 &
4~20mA
Auto
VOLT(Voltage elements)
C2
AUX(Current elements)
C3
C1
Input(220VAC)
Lop/Stop, For, REV, RES,
E/S (C1 Common)
Output
Main, Y, D, AUTO,
Volt (C2 Common)
I-tp, Alo, U-C, OrH, ALL
AUX output upon the selecting menu
(C3 Common)
COMM. Port
- RS-485
TRX1 +, TRX1 -
TRX2+, TRX2-
- 4~20mA :+, -
ZCT
Dedicated Z1_V, Z2 : 100mV
Universal Z1, Z2 : 1.5mA
M
Soft Starter Start
R
S
T
3Ø 3W 440V 60HZ
MMP
ZCT
L1 L2 L3
Inverter
T1 T2 T3
52
MCCB
88M
MC
Z1
Z2
SHT
By-pass
MCC MCC
Lop
Stop For Reset REV
Auto
C2
Auto
For
Auto status contact
REV
External TRIP
Trip1
110Vac or
220Vac 50/60Hz
A2 C2
Lop/
Stop For Reset
Va
Vb
Vc
88MX
Z1
Z2
Z1_V
A1
88M
Main
88M
REV
SHT
E/S
COMM. Port
Modbus/ RS-485 &
4~20mA
Auto
VOLT(Voltage elements)
C2
AUX(Current elements)
C3
C1
Input(220VAC)
Lop/Stop, For, REV, RES,
E/S (C1 Common)
Output
Main, Y, D, Auto,
Volt (C2 Common)
I-tp, Alo, U-C, OrH, ALL
AUX output upon the selecting menu
(C3 Common)
COMM. Port
- RS-485
TRX1 +, TRX1 -
TRX2+, TRX2-
- 4~20mA :+, -
ZCT
Dedicated Z1_V, Z2 : 100mV
Universal Z1, Z2 : 1.5mA
MCCB
Aux
M
LSIS Co.,Ltd.
95
Dimensions
Dimensions
100 24 15.5
43
100
112
125.9
65
Ø17
53.5
100
Ø66
Unit : mm
96 Electronic Motor Protection Relays
MEMO
MMP Series
LSIS Co.,Ltd.
97
EMPR Rated specifications
Rated specifications
Type
GMP-series
DMPi-series
IMP-series
Primary current
GMP22-2P/2PA, 3P/3PR
GMP22-2S, 3S/3SR
GMP22-2T, 3T/3TR
GMP22-2PD
GMP40-2P/2PA, 3P/3PR
GMP40-2S, 3S/3SR
GMP40-2T, 3T/3TR
GMP40-2PD
GMP80-2S, 3S/3SR
GMP60T, 60TE, 60TA
GMP60TD/TDa
GMP60-3T/3TR
GMP60-3TZ/3TZR
GMP60-3TN/3TNR
DMP06i
DMP65i
IMP-C-NO
IMP-C-A420
IMP-C-M485
S-EMPR MMP-CB/CM-10
S-EMPR-series
S-EMPR MMP-PB/PM-10
S-EMPR MMP-SB/SM-10
S-EMPR MMP-CB/CM-100
S-EMPR MMP-PB/PM-100
S-EMPR MMP-SB/SM-100
4~20
8~40
16~80
0.5~6
3~30
5~60
0.125~60
0.5~60
0.5~6
5~655~60
0.125~100
Current setting range(A)
0.3~1.5
1~5
4.4~22
0.125~10
5~100
Applied 3-phase motor capacity(KW)
220~240VAC 380~440VAC
~0.18
0.18~1.1
1.1~5.5
0.12~0.55
0.37~2.2
2.2~11
1.1~5.5
2.2~11
5.5~22
0.09~1.1
0.5~7.5
1.5~15
0.06~15
0.09~15
0.09~1.1
1.5~18.5
1.5~15
0.06~30
0.06~2.2
1.5~30
2.2~7.5
4~18.5
11~45
0.18~2.2
1.5~15
3.0~30
0.06~30
0.18~30
0.18~2.2
3.0~303.0~30
0.06~55
0.06~4
3.0~55
Operating characteristic
Inverse-time
Definite-time
Inverse-time
Definite-time
Inverse-time
Definite-time
Definite-time/Inverse-time
Definite-time
Definite-time(Ground Fault)
Definite-time/Inverse-time
(Instanteous/Ground Fault)
Definite-time/Inverse-time
(Instanteous/Ground Fault)
Definite-time/Inverse-time
(Current type)
Definite-time/Inverse-time
(Power type)
Definite-time/Inverse-time
(SGR type)
Definite-time/Inverse-time
(Current type)
Definite-time/Inverse-time
(Power type)
Definite-time/Inverse-time
(SGR type)
98 Electronic Motor Protection Relays
EMPR Optional accessories
EMPR Series
ZCT
(Zero-phase Seguence Current Transformer)
1) ZCT compact type (4 types)
Rated specifications
Code
76512123030
76512123050
76512123065
76512123080
Model name
LZT-030(V)
LZT-050(V)
LZT-065(V)
LZT-080 (V)
Dimensions
ZCT 30, 50, 65, 80(V)
30
6
I k
Inside diameter (mm)
30
50
65
80
Model name
LZT-030(V)
LZT-050(V)
LZT-065(V)
LZT-080(V)
Zero phase current transformer ratio
200mA/100mV LS-exclusive
A
30
50
65
80
B
59
84
101
120
C
36
48
57
68
D
78
105
120
136
Weight (kg)
0.5
0.7
0.9
1.5
Unit : mm
E
80
100
100
120
Unit : mm
F
90
110
110
130
A
B
30
Response to RoHS and a terminal cover exists
2) ZCT basic type (4 types)
Rated specifications
Code
76512121001
76512121002
76512121003
76512121004
Model name
LZT-030
LZT-050
LZT-065
LZT-080
Dimensions
ZCT 30
Inside diameter (mm)
30
50
65
80
Zero phase current transformer ratio
200mA/100mV (LS only)
Unit : mm
Weight (kg)
0.5
0.7
0.9
1.5
ZCT 50, 65, 80
Model name
LZT-030
A
30
B C D E
25 108 100 114
F
7
G
32
H I
Unit : mm
32 110
Ø
6
Model name
LZT-050
LZT-065
LZT-080
A
50
65
80
B C D E F
25 131 100 122 7
26 143 114 133 7
34 174 160 180 7
G
32
39
40
H
Unit : mm
I Ø
36 114 6
37 126 6
40 151 6
LSIS Co.,Ltd.
99
EMPR Optional accessories
CT
(Current Transformer)
Rated specifications
Classification Code Model name
3CT type
2CT type
1CT type
76012116026
76012116011
76012116012
76012116013
76012116014
76012116015
76012116016
76012116017
76012116018
76012116019
76012116020
76012116021
76012116022
76012116023
76012116024
76012116025
76012116001
76012116002
76012116003
76012116004
76012116005
76012116006
76012116007
76012116008
76012116009
76012116010
*Note: If the CT secondary cable thickness is 2.5mm2, the load of 3m is 0.52VA.
3CT-43
3CT-43
3CT-43
3CT-43
3CT-43
3CT-63
3CT-63
3CT-63
3CT-23
3CT-23
3CT-23
3CT-23
3CT-23
3CT-23
3CT-43
3CT-43
DCT-100
DCT-150
DCT-200
DCT-300
DCT-400
SCT-100
SCT-150
SCT-200
SCT-300
SCT-400
500A
600A
100A
150A
200A
300A
400A
100A
150A
200A
300A
400A
100A
150A
200A
250A
300A
350A
400A
400A
Primary current
50A
80A
100A
150A
180A
200A
Secondary current
Load(VA)
Penetrating hole [mm]
Upper installation
EMPR
5A
5A
5A
1.5
5
5
21×21
27×27
45×30
28.5×33.5
27.5×32.5
GMP22/40/60T
Remarks
DMP/IMP/DMPi entire series
GMP60-3T/3TN/3TZ
GMP22/40/60T
1) Error class: Class 1.0
2) Insulation voltage: 690V
3) Withstanding voltage:
4kV/min
4) Overcurrent strength:
40 x 1n
5) Insulation resistance:
10MΩ (DC 500V Megger)
6) Frequency: 50/60Hz
GMP22/40/60T
DMP/IMP/DMPi entire series
GMP60-3T/3TN/3TZ
GMP22/40/60T
Dimensions
3CT type (3CT )
E
38 53±1 w
K w
B
A
B
5
K v
K u u
D
Type
A
B
E
F
C
D
3CT-23
119
35
9
21.5
89
76
3CT-43
149
44
12
27
117
91
3CT-63
218
70
20
45/30
183
94
Dimensions
2CT type (DCT-
)
28.5
55
120
60
80
2- 5
100 Electronic Motor Protection Relays
EMPR Series
Dimensions
3 SCTs combined
1CT type (SCT )
Other options
Cable
Applied products
Spec.
purpose
Terminal block
IMP, DMPi series
1m, 1.5m, 2m, 3m
For separated display installation
Applied products
Spec.
purpose
MMP series
1m, 1.5m, 2m, 3m
For separated display installation
Applied products Terminal block with the application of GMP60-3T Series
Spec.
Less than 60A
Applied products
Spec.
DMPi series
Less than 65A
LSIS Co.,Ltd.
101
EMPR Operating characteristic curve
Class5 Class10
Class20 Class30
Class60 Definite time characteristic
102 Electronic Motor Protection Relays
Direct mounting EMPR new/old comparative table
EMPR Series
Type
Extended model
Number of sensors
Over current
Phase failure
Protective function
Locked rotor
Phase unbalance
Reverse phase
Aux. contact (at Energization)
Rating Current
GMP22-2P (1c)
GMP22-2PD (1c)
2
1SPDT (1c)
0.3~1.5, 1~5, 4.4~22A
GMP22-2P GMP22-3P GMP40-2P GMP40-3P
GMP22-2PA GMP22-3PR
GMP40-2PD
GMP40-2PA
GMP40-3PR
2
2SPST (1a1b)
0.3~1.5, 1~5, 4.4~22A
3 2
(PR)
2SPST (1a1b)
4~20, 8~40A
3
(PR)
Metasol
(New)
EMPR
Demension
Direct connection possible MC
MC-9b, 12b, 18b, 22b MC-9b, 12b, 18b, 22b MC-32a, 40a
Meta-MEC
(Old)
EMPR
Demension
Type of contactors
Wiring/Mounting Compatibity
Retrofit Type
(Tunnel)
GMC-9, 12, 18, 22
NO
GMP60T (1c)
GMP22-2T
GMC-9, 12, 18, 22
GMP22-2T
GMP60TA (1c)
NO
GMP22-3T
GMP22-3TR
GMP40-2T
GMP60T (1c)
GMP60TA (1c)
GMC-32, 40
NO
GMP40-3TR
*When you order a product with Metasol MC direct coupling type, it is required to write ‘Sol’ at the end of the product type name in order to identify from an old-type product
GMP40-3T
LSIS Co.,Ltd.
103
Certificates
A Species of
Certification
A Species of
Standard
Mark or certification
Type
GMP
DMPi
IMP
GMP40-3T
GMP40-3TR
GMP60-T
GMP60-TE
GMP80-2S
GMP80-3S
GMP80-3SR
DMP06i-S
DMPi06-SZ
DMPi06-SB
DMPi06-T
DMPi06-TZ
DMPi06-TB
DMPi65-S
DMPi65-SZ
DMPi65-SB
GMP22-2P
GMP22-3P
GMP22-3PR
GMP22-2S
GMP22-3S
GMP22-3SR
GMP22-2T
GMP22-3T
GMP22-3TR
GMP40-2P
GMP40-3P
GMP40-3PR
GMP40-2S
GMP40-3S
GMP40-3SR
GMP40-2T
DMPi65-T
DMPi65-TZ
DMPi65-TB
IMP-C NO 10A
IMP-C NO 100A
IMP-C A420 10A
IMP-C A420 100A
IMP-C M485 10A
IMP-C M485 100A
KC
KC
Korea
●
●
●
●
●
●
●
●
●
●
●
●
●
●
●
●
●
●
●
●
●
●
●
●
●
●
●
●
●
●
●
●
●
●
●
●
●
●
●
●
●
S-Mark
Korea
●
●
●
●
●
●
●
●
●
●
●
●
●
●
●
●
●
●
●
●
●
●
●
Safety certi
●
●
●
●
●
●
IEC
Approvals
UL GB
●
●
●
●
●
●
CE
Europe
●
●
●
●
●
●
●
●
●
●
●
●
●
●
●
●
●
●
●
●
●
●
● cUL
U.S.A/Canada
●
●
●
●
●
●
●
●
●
●
●
●
●
●
●
●
●
●
●
●
●
●
●
●
●
●
●
●
●
●
●
●
●
●
●
●
●
●
●
●
●
CCC
China
●
●
●
●
●
●
●
●
●
●
●
●
●
●
●
●
●
●
●
●
●
●
●
●
●
●
●
●
●
●
●
●
●
●
●
●
●
●
●
●
●
GOST
Russia
●
●
●
●
●
●
●
●
●
●
●
●
●
●
●
●
●
●
●
●
●
●
●
Gosstandart
Certificates
IEC
●
●
●
●
●
●
●
●
KEMA
Netherlands
K R
KO
RE
A R
EG
ISTER OF SH
IP
PI
N
G
RE
A R
K R
IP
PI
N
●
●
●
●
104 Electronic Motor Protection Relays
EMPR Series
A Species of
Certification
A Species of
Standard
Mark or certification
Type
MMP
MMP-C B 10A
MMP-C B 100A
MMP-C M 10A
MMP-C M 100A
MMP-S B 10A
MMP-S B 100A
MMP-S M 10A
MMP-S M 100A
MMP-P B 10A
MMP-P B 100A
MMP-P M 10A
MMP-P M 100A
KC
KC
●
●
●
●
●
●
Korea
●
●
●
●
●
●
Safety certi
S-Mark
Korea
IEC
Approvals
UL
CE
Europe cUL
U.S.A/Canada
●
●
●
●
●
●
●
●
●
●
●
●
GB
CCC
●
●
●
●
●
●
China
●
●
●
●
●
●
Gosstandart
Certificates
IEC
스마트전자식 모터보호계전기
GOST
Russia
KEMA
Netherlands
K R
KO
RE
A R
EG
ISTER OF SH
IP
PI
N
G
K R
RE
A R
EG
ISTER OF SH
IP
PI
N
LSIS Co.,Ltd.
105
MEMO
106 Electronic Motor Protection Relays
advertisement
* Your assessment is very important for improving the workof artificial intelligence, which forms the content of this project
Related manuals
advertisement