ESAB UNIONMELT™ UWM-2 (Series 5) Portable Flexible Welder Troubleshooting instruction
Add to My manuals20 Pages
advertisement
▼
Scroll to page 2
of
20
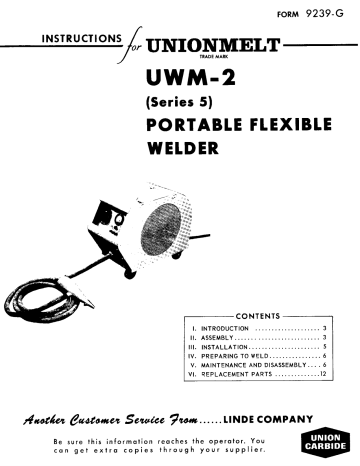
FORM 9239-G INSTRUCTIONS r UNIONMELT — UWM-2 (Series 5) PORTABLE FLEXIBLE WELDER CONTENTS |. INTRODUCTION .................... 3 |. ASSEMBLY....,..........,,.,..,,:.. 3 Ш. INSTALLATION...................... 5 IV. PREPARING TO WELD................ 6 V. MAINTENANCE AND DISASSEMBLY....6 VI. REPLACEMENT PARTS ..,........... 12 Another Customer Serucce From...... LINDE COMPANY UNION Be sure this information reaches the operator. You can get extra copies through your supplier. CARBIDE IMPORTANT The Series 2 UWM-2 Flexible Welder has a slightly different exterior cabinet and wire reel than the Series 3 machine. The Series 2 model also does not contain the wire straightening guide (see Figure 2). Both machines (Series 2 and 3) are exactly alike in every other respect. The Series 4 machine has 4 speed gearing instead of 3 speed gearing as in the Series 3 machine. Because of the increased drive speed, it is possible to use 3/32 inch diameter wire at higher currents. Consequently, 1/8 inch diameter wire is no longer recommended for general use. A stiffener has been added to the base plate in the Series 5 machine to increase the rigidity of the machine. Insulation has alse been added to the cover and base plate in the vicinity of the wire reel to prevent the wire from short-circuiting to. the cover or base. If series number is not shown separately, it is the first digit of the serial number. 2 The terms HELIARC, OXWELD and UNIONMELT are registered trade marks of Union Carbide Corporation. |. INTRODUCTION The UWM-2 Portable Flexible Welder consisting of a Wire Drive Mechanism and a Flexible At- tachment, is a complete welding machine for connection to a suitable source of welding power. It is especially designed for welding in positions that cannot be reached with mechanically operated weld- ing heads. It can be used without change for welding with either alternating or direct current. The weld is started by lightly scratching the end of the wire on the workpiece when sufficient UNIONMELT composition has been deposited to cover the arc. The UNIONMELT UWM-2 Welder has been satis - factorily used with welding currents up to 800 Amperes for 3/32 inch wire. (Arc voltage - 35 volts.) The welder can be used for both production and maintenance applications. It is particularly suit- able where a moderate amount of hand welding is done, and where continuous operation is not required. This booklet, with two other instruction booklets, provides all the necessary information for the installation, operation, and maintenance of the welder. The other booklets are: A. "Instructions and Parts Data for the Series Voltage Control for the UWM-2 (Series 2) Ma- chine,'' Form $286. B. "Instructions and Parts Data for the UNIONMELT Flexible Welding Attachment," Form 9159, If you donot have these booklets, you can obtain them from the LINDE district office nearest you. li. ASSEMBLY A. PRINCIPAL COMPONENTS AND SEQUENCE OF OPERATION The following paragraphs briefly explain the functions of the parts shown in Figures 1 and 2. The Standard Spoke-Type Wire Reel holds small coils of wire weighing up to 75 pounds. The reel is equipped with a brake which can be set to prevent ‘overrun, The Welding Head Assembly, in front of the wire reel, draws welding wire from the reel and feeds it thr ough the flexible attachment to the welding nozzle. The assembly consists of three main parts: A motor and gear reduction unit provides driving power to a feed roll. A pressure roll assembly forces the wire down into a vee-groove on the feed roll, providing positive traction and feeding. A busbar introduces welding current to the flexible cable. The Flexible Attachment Assembly (Required Accessory) carries the welding wire from the head to the weld zone. The assembly includes the weld- ing current cable and a flexible tube through which wire is fed. It terminates in a combination hopper and welding nozzle. The hopper holds UNIONMELT welding composition which flows down around the welding wire as welding progresses, The operator controls the flow of composition by raising and low- ering the hopper. Complete parts data ‘and opera- tional procedures for the Flexible Attachment are given in Form 9159, The Voltage Control Assembly automatically maintains the selected welding voltage. Its opera- tion depends upon the fact that the welding voltage varies with the gap between the welding wire and the work, When the gap is wide, the welding volt- age is high; when the-gap is narrow, the welding voltage is low. The control maintains a constant voltage by varying the speed of the wire feed motor and consequently the rate at which wire is fed into the weld zone. When it senses" an increase in the welding voltage, it feeds the wire into the weld faster. This shortensthe gap between the wire and the work, decreasing the voltage. If the welding voltage begins to drop, the control slows the wire feed, the melt- off rate exceeds the feed rate, and the gap lengthens. This resultsin raising the voltage, A more detailed description of how the control works is given in the instruction booklet on the voltage control Form 9286, The Current Relay connects the motor and con- trol across the weld zone so that they may feed wire at a controlled rate. The relay is actuated when welding current flows through the welding cables. The Condenser across the contacts of the relay re- duces the arcing at the contacts, thereby lengthening their life. B. ADDITIONAL EQUIPMENT REQUIRED A complete installation for use with either aiter- nating or direct current must include the following: 1. A Flexible Attachment-(10 or 17 Feet in length.) 2. A welding transformer of suitable capacity for a.c, welding, or a welding generator or recti- tifier transformer for d.c. welding. 3. Control cable for connections to the voltage con- trol box. Typeof cable and method of connection is included in the installation section of this book. 4. Suitable lengths of 4/0 welding cable for elec- trode and "ground" connections. 5. Welding cable lugs. 6. Welding cable "eround" clamp. VOLTAGE CONTROL WIRE FEED MOTOR FLEXIBLE ATTACHMENT (ACCESSORY) CURRENT RELAY AND CONDENSER WIRE STRAIGHTENING GUIDE (OMITTED IN SERIES 2 MACHINES) WIRE REEL FEED ROLL PRESSURE ROLL T—- WELDING HEAD ASSEMBLY BUS BAR CLAMP i FIG. 2 — UWM-2 — Right Side View with Side Covers Removed C. OPTIONAL ACCESSORIES an inching control on the handle of the Flexible At- Conversion kits (Part No. 374421 for 10-ft, At- tachment. For detailed information, refer toinstruc - tachment and Part No, 374422 for 17-ft. Attachment) tion booklet F-9822, "Instructions and Parts List for are available which provide the standard UWM-2 with Remote Inching Control of UWM-2." Ш. INSTALLATION The UWM-2 is completely assembled before it tionsand Parts List For UWM-2 Series Voltage is shipped, except for the flexible attachment, and Control), the control and welding cables. (a) Unscrew the nut from the back of the plug and remove the rubber bushing. A. FLEXIBLE ATTACHMENT To instali the flexible attachment, simply insert the end of the hose through the opening in the machine cabinet, and into the busbar clamp. Then tighten the clamp screw. For the location of these parts, see Figure 2. (c) Separate the front insulation from the rear insulation by removing the round-head ma- chine screw which holds them together. B. ELECTRICAL CONNECTIONS Before separation, scribe a match-mark on 1. CONTROL CABLE the two pieces so that you can reassemble them in their original position. {(b) Unscrew the two fillister head screws and slip the insulation out of the plug shell. Do not unscrew the Phillips screw. Remove the contact unit. All the internal electrical connections on the (d) Thread the cable through the nut, bushing, welder are made before it is shipped. However, and plug shell, Strip back about 3/4 inch of because the length of the control cable depends the outer covering of the cable. upon the equipment location, the cable is not sup- plied with the welder. A completely assembled standard eight-conductor cable and plug may be purchased from LINDE in lengths of 25, 50 and (e) Remove approximately 3/16 inch of insula- tion from eachofthe conductors. Clean and tin the exposed ends. 75 feet. Be sure to specify the length of cable (f} Clean the contacts and solder them to the desired when ordering. If you prefer to make conductors using a non-corrosive flux. Do up your own cable and plug assembly, it should not allow solder to bulge out around the neck be noted that only four leads are required. of the contact. Remove all excess flux with No. 16 gage ‘‘Tirex’’ Type ‘‘S’’ four-conductor alcohol or other volatile cleaner. rubber clad cord - 0.877 inch O.D., or the equiv- (=} Place the conductors in the correct positions alent will be satisfactory. It willalso be neces- in the back insulation. If the contacts do not sary to order one eight-pole female contact unit, slip readily into the back insulation, remove Part No. 90W45 and one plug shell, Part No. the excess solider which is causing atight fit. 90W39. The directions below tell how to disas- semble the plug and attach the cable to it (see (h} Place the contacts in the front insulation Fig. 3): (according to color code on the wiring dia- gram in Form 9285). Then secure the front and back insulations together with the ma- chine screw. If the insulations do not fit together evenly, remove the front insulation and check to see that the contacts are prop- erly seated in the back insulation. Electrical connections are shown in Form 9285 which is attached to Form 9286 (Instruc- FRONT (i) Pull the plug shell over the insulations and INSULATION replace the two fillister head screws. PHILLIPS SCREW FILLISTER ЭСАЕМ CONTACTS \ (j) Replace the rubber bushing and nut. NUT ~~ (ON 2. WELDING CABLE To connect the welding current cable, skin SCREW off about an inch of insulation from the end of the cable. (Cable size: 4/0.) Tin the bare end to prevent its unraveling. Insert the cable end intothe connector at the rear of the carriage. FIG. 3 ~ Exploded View of Plug and Cable Assembly Tighten the clamp. RUSBER BUSHING À GONDUCTORS FILLISTER SCREW BACK INSULATION IV. PREPARING TO WELD A. INSTALLING WELDING WIRE ON THE REEL 1, HOW TO INSTALL A COIL OF WIRE a) Loosen the thumbnuts on the retaining fingers of the four wire reel arms. b) Turn the fingers so that they point toward the hub. c) Remove the wrapping paper from the wire coil, but do not remove the binding wires. d) Use the outer end ofthe coil asthe starting end. (The inner end of some coils is tagged ''Start This End.’ Disregard such instructions.) Slide the wire coil onto the reel with the starting end in the proper feed position. ey If the inner end of the coil is not anchored to the core of the coil, secure it under the anchoring setscrew on the reel. f) Turn the reel fingers outward and tighten the thumbscrews, g) Secure the starting end of the coil between the feed and pressure rolls of the wire feed mech- anism. It may be necessary to remove one or two of the coil binding wires, but do not remove all of the binding wires. h) Tighten the hub spring retaining screw to pro- vide some friction drag for the reel. The spring pressure should be sufficient to prevent the wire coil fromunwinding. However, it should not be so great as to overload the wire feed motor. i) Remove the remaining binding wires from the coll. 2. BRAKE SPRING SELECTION The wire reel is assembled with brake spring 287.64 and a 1/2-inch plain steel washer. (See Figure 22.) This spring and washerare used for almost all applications. For lighter braking action, replace the spring and washer with spring 92W12 and guide washer 18N26 which are supplied in a cloth bag tied to the reel. If tightening the brake screw fails to prevent the wire from unwinding from the secured end,a cardboardor sheet metalring may be inserted between the reel and the coil of wire. B. ADJUSTMENTS FOR WIRE DIAMETER The UWM-2 Portable Flexible Welder can be used with 3/32 and 5/64-inch wire. (The same feed rollisusedfor all wire sizes.) However, when going from one wire size to another, the proper tip must be installed in the Flexible Attachment. Complete instructions on how to change from one wire size to another are given in Form $159 ‘‘Instructions and Parts List for the UNIONMELT Flexible Attach- ment.” C. MAKING THE WELD COMPLETE INSTRUCTIONS ON HOW TO MAKE THE WELD, PROCESS DATA, AND OPERATIONAL HINTS, ARE GIVEN IN FORM 9159 “INSTRUCTIONS AND PARTS LIST FOR THE ‘UNIONMELT’ FLEX- IBLE ATTACHMENT.”' V. MAINTENANCE AND DISASSEMBLY A. MAINTENANCE Little maintenance is required tokeepthe Port- able Flexible Welder in good operating condition. It is important, however, that the feed’and pressure rolls, the wire feed motor, and the flexible attach- ment be kept clean and free of foreign material. THE GRADUAL ACCUMULATION OF DIRT, WIRE PARTICLES, AND "UNIONMELT" WELDING COM- POSITION WILL EVENTUALLY CAUSE JAMMING UNLESS THEY ARE SYSTEMATICALLY REMOVED. FOR THIS REASON, THE WELDING HEAD PARTS SHOULD BE CLEANED AT LEAST ONCE FOR EVERY FIGHT HOURS OF OPERATING TIME, THE FLEXIBLE ATTACHMENT WIRE TUBE SHOULD BE CLEANED EACH TIME A NEWCOIL OF WIRE IS IN- STALLED. CLEANING IS BEST ACCOMPLISHED BY BLOWING THE PARTS WITH DRY COMPRESSED AIR. 1. WELDING HEAD The gear reduction housing is packed with grease when shipped from the factory. If the assembly is taken apart, it should be refilled after reassembly. If the old grease has been lost or is otherwise unusable, use ‘‘Texaco Regal Starfak Special’’ grease. This is available from LINDE in 5-lb. cans, under Part No. 92W10. Check the wirefeed motor brushes every six months, or every 200 hours of operation. Un- screw both brush plugs as indicated in Figure 4 ini particles may short circuit the commutator segments during the operation of the motor. After two sets of brushes have been worn out, check the commutator for wear. If the surface is worn, it should be smoothed by grinding or turning down on a lathe, and under- cutting the mica segments. Replacement of brushes and commutator maintenance should be performed only by an experienced electrician. 2. FLEXIBLE ATTACHMENT Complete maintenance instructions are given in Form 9159, B. DISASSEMBLY 1. WELDING HEAD To disassemble the welding head, first remove the welding cablefrom the busbar. Then remove the feed roll assembly from the drive shaft. Remove the entire welding head assembly from its mounting. Put all insulating washers, | FRAME e inde bushings, etc. in a handy place where they will FIG. 4 — Removal of Motor Brushes be available when the head is to be remounted. The welding head may now be disassembled in and lift out the brush and spring assemblies, It the following manner: is a good idea to mark each brush and holder with a pencil as the brush is withdrawn, so that it can be replaced in the original position. If the position of the brushes relative to the armature is changed, sparking is likely to occur when the motoris put back into operation, due to improper brush seating. (b) Removing the Pressure RollAssembly: With a 7/8-in. open end wrench, unscrew the mounting boltas shownin Figure 6. Remove the bolt and steel washer, and take off the pressure roll assembly. (a) Removing the Busbar: Unscrew the socket- head screws which hold the busbar to the gear reducer housing as shown in Figure 5. Remove the busbar assembly and the insulat- ing blocks. Examine the brushes. Make sure that each brush surface in contact with the motor com- mutator has the bright, polished finish that indicates good contact. The polished area should cover essentially all of the contacting surface of the brush, When replacing a brush in the motor, be . ae He AAA e br gh, Ча тична ho a te nu Dé gp zoe ro sure to put it back in the same brush holder and р o VID in its original position. Be sure that the brush e В - all rides freely in its holder, New brushes are approximately 3/4 in. long. When they have been worn down tuo 1/2-in. in length, they should be replaced with new ones, With the brushes removed, inspect the surface of the commutator. It should appear clean and s:uvoth, with a polished brown color where the brushes ride on it. If the surface appears rough, disassemble the motor and re- move the armature. Polish the commutator surface with No. 00 sandpaper and wipe clean. For this operation, it is preferable to rotate the armature in a lathe. e 258% EP u EZ EEE E oe CAUTION: Never use emery cloth or emery CTE BER ERS HERE KW о | . . мох г Я RE MUR daté ie stone for this operation. Emery is a con- ductor of electricity, and any residual loose FIG. 5 — Removing the Busbar welding wire. The roll should then be replaced with a new one to prevent the wire from binding and slipping during welding operations, Dis- assemble the assembly and replace the roll as follows: (a) Remove the pressure roll assembly from the welding head as explained in paragraph B-1-b on page 7. (b) Unscrew the retaining nut and washer from the roll shaft. Withdraw the shaft and re- move the roll from the yoke. (c) Check the pressure roll insert bushing for wear. Placetherollonthe shaft. If it wob- bles or has a sloppy fit, it should be re- placed, The roll and the bearing come аз а single unit. FIG. 6 — Unscrewing Mounting Bolt (4} Reassemble the new roll, shaft, washer, and nut in the order shown in Figure 8 below, (c) Removing the Gear Reduction Assembly: With a 3/8-in. wrench, unscrew the three hex nuts on the inner side of the gear hous- ing mounting flange (see Figure 7). Care- WASHER fully pry the gear reduction assembly away from the wire feed motor. Avoid damaging the paper gasket. | ЗНАЕТ se NUT WASHER FIG. 7 — Removing Motor Retaining Nuts (d) The welding head is reassembled by re- . versing the procedure given above. When FIG. 8 ~ Exploded View of Pressure Roll Assembly attaching the gear unit to the motor assem- bly, make sure the paper gasket is in place and in good condition. If torn or otherwise (e) Replace the shoulder bolt and draw up tight damaged, replace it with a new one. Align with the hex nut. Remount the assembly on the spur gear teeth. Be sure the two units the welding head, and adjust the pressure fit up snugly before screwing them together. screw. This will indicate that the motor shaft spur gear is interlocked correctly with the spur 3. WIRE FEED MOTOR gear in the gear reducer unit. After the gear reduction unit has been re- When replacing the busbar, be sure to include moved from the motor assembly, as described all insulation to properly insulate the busbar from in paragraph 1|-c, the motor may be disassembled the gear housing. for maintenance. Note: Anexperiencedelectric motor repairman should do this work. 2. PRESSURE ROLL ASSEMBLY (a) Unscrew both brush plugs, and remove the After long service, the pressure roll may brush and spring assemblies. (See Figure develop a deep groove where it contacts the 4.) Note how each brush is withdrawn so that it may be replaced in the same posi- tion. Match-mark the brushes and holders. ARMATURE ^ SPRING SPACER (b) Unscrew the two motor housing screws as shown in Figure 9, un 7 ern Zn SHROUD 4. GEAR REDUCTION UNIT For repair purposes, or for changing the gear reduction ratio, it is recommended that the complete Gear Reduction Assembly be ordered. This assembly is complete, packed with grease, and ready for mounting on the motor assembly. ACliberal trade-in allowance forthe old assem- bly will be given, provided it is in repairable condition. FIG. $ - Removing Motor Housing Screws In certain cases, however, immediate field repairs may be required. The Gear Reduction Assembly is disassembled inthe following man- ner (this shouid be done only by an experienced machinist): (c) Withdraw the motor end housing. (d) Lift out the motor armature, and remove the shroud. (a) First disassemble the welding head. Re- move the gear reductionunit from the wire (e) To remove the motor field, unscrew the two feed motor. retaining screws as shown in Figure 10, (b) Mark all bearing caps A, B, C, and Das shown in Figures 12 and 13 and remove. age WORM AND | | 1 г м A | u | GEAR В" И En apre” RM: AND GEAR “A” carts FIG. 10 — Removing Field Retaining Screws a (f) To reassemble, reverse the procedure out- lined above, An exploded view of the motor is shown in Figure 11. FIG. 12 — Welding Heod Gear Reduction Unit Lo CAP 'C" FEED ROLL SHAFT GEA eee # CAP BAEZ PORT 'B° PORT ‘С PORT A” CAP 4° CAP ‘D en иски 'в"— В > я "oq FEED ROLL SHAFT ANO GEAR (O BEARING 'G" F7. WORM AND oa ° GEAR 'B a WORM GEAR "3" © fe, oat “BEARING 'H WORM AND GEAR 2 PORT 'D" (с) (9) (е) (f) (8) (h) (i) FIG. 13 — Welding Head Gear Reduction Unit (Exploded View) From the motor side of the gear housing, tap out bearing F through port B. Use a brass or copper drift for this operation, to avoid damage to the bearing. Lift out the worm and gear A, Press worm and gear B from port A until bearing G is clear of the housing. Insert a yoke, with a slot about 5/8-inch wide, between bearing G and the housing. Clamp two 3/16-inch diameter x 5-inch long bronze wires in a vise, parallel to each other and about 3/4-inch apart, Insert them through the motor side of the housing, so that they straddle worm B and bear against worm gear B, Press out worm B through port D from port À, Lift out worm gear B and bearing H. (j) Substitution of complete sets of worms and gears may now be made and the parts reas- sembled by reversing the foregoing proce- dures, A worn worm or gear should not be used with a new mate in a set, (x) To complete the disassembly, press out the roll drive shaft and gear through port C from the motor side of the housing. (1) To reassemble, reverse procedure shown above. When the intermediate worm and gear B are locked in position by caps D and A, care must be taken by careful peeling of shims to assure centering of the worm gear B on worm A. A worn worm or gear should not be used with a new mate ina set. 5. FLEXIBLE ATTACHMENT Complete maintenance instructions are giv- en in Form 9159. Z-WMN Jo ин 470 1очоизиешиа — у| *91 sil = He + lab „Вс LE = E LAS VI ur (OY. | 11 VI. HOW TO ORDER REPLACEMENT PARTS . All replacement parts are keyed on the drawings which follow. Two types of numbers are used on these drawings: A. Standard Part Numbers. These are usually formed by two pairs of digits with a letter between (for example: 01N21, 18V69). A few parts may have straight digit sequence (3389) or one letter followed by several digits (A-654221). Each standard part number is accompanied by a descriptive word or words. B. Hardware Numbers. These are eight digit numbers (for example: 6120-3910), Hardware numbers are usually accompanied on drawings by a one word description. . Order standard parts by part number and part name, as shown on drawings. DO NOT ORDER BY PART NUMBER ALONE, . For hardware, look up number in hardware list at back of book. You will find there a full description. "Hardware" items can usually be purchased locally. When ordering hardware from LINDE be sure to include the complete description given in the hardware list. Donot order hardware by the number alone, When ordering, be sure to state quantity of each part needed. . Always state the series or serial number of the machine on which the parts are to be used, The serial number is stamped on the unit nameplate, The ''series no." is the first digit of the serial number, wherever the serial number starts with a digit, followed by a letter, When the serial number starts with one or two letters, always give the complete number. Indicate any special shipping instructions. . Order replacement parts from the LINDE District Office nearest you. 12 ¡aay эл М adA -axodg ym *(g so113s) 62310 “ON WPd Z-WMN 844] 18PISM IPNUOW 8192H04 L'IJWNOINN — S1 “913 82310 — (13 LI)IN3WMOVLIV 3181X 314 O122-02%9 H3HSYM WOOT(b) 9882-02b9-4IHSTA HOO Te) 9880-02£9-LNN (2) 1881-0£ 19-M3995 12) 06310 — (14 OUINSMNHOVLIT 378IX 3 14 (ON IANS LION] ÂYOSS 799 PASE ——A TEMHISSV 53103 Mi OFGNTOIN Fev JOGWAS SIAL HLIM SLIM 0262-02 9-YIHSVMA WOOT Ib) ¿160-O££9-1NN (tb) BE ¿1-O£19-M3Y0S[0) ¡GNQ1-— 935945 \ о (Ta DIA 335) OIA6GE — AI9MN3SSY AY UN 1N3IYSHNO 2E92-02%9-H3HSYM 49071 [b) 9£10-O££9-1nN[b) Bbll-b219-MI49S (bd) GE MEG —-103X1418 315 VHZ2) 0122-02b9-H3JHS TM 100 > 00I10-0Ot £9-L1MN 20 11-#E19-M 3495 6IN¢c2—HOLY INSNI 62 M26 — YOLOANNOD (97,8) 6112-9806-9NIBAL LMI6-dWy 19 ¿1N61- 91 7 21152 —-W355Yy 371899 ОФМЕб- ЗУ 7 0980 -Of¢9-HYIHSYM (a) 2212-0Z2b9-Y3HSVMA 3901(8) 2980-02£9-1NN18) E981-O£19-M34095 (8) 2¿rN22—13I3IHS "SNI (ez ola 31%) EBABI— ATIWISSY 133% 3HiM O1IO-OEFI-HYAHSYM ID} 09£2-0219-YIHSVMAMNIDON ly) IZ10-O££9-1NN lp) plil-pel9-MaHoS (PF) (4 IOGHAS SILL HLiM SLUWA TIO SIDO TIA) DIAGZ —AIBWISSV YIAOO #1800-0E19-M349SI9) 0010-0££9-1NNfb) 901!1-9£19-M23Y95[b) Ib N2Z-Y 39d" (tb) - 21906 — HISN30ONOS CBIO-OLE9-LNAN (=) BRIL-PEII-M3HDS (2) BIASZ-1U044NS 18N61-439%d5S — BEING - OLY WISN O61Z-OZb9-HIHSTM HOO 12) с826 WIOJ 295 swosborg Bulsiy 2043 LON (97'914 HIS) bbAG2 —AIBAISSV QOV3H INIOTIM G916-02%9- H3HSYM HI01- g8I6-FIrT9-1LNN 0060 $LI9-M3435 cpGO-bLLI9-MI1495 - 8£ M £6 —(IAIMSIY83ILSVO (2) S¿00-0€b9-YIHSVMIZ ) bOGO-VEI9-M3IYOS (2) 6900-bL19-M389S (3) dk veonde-30% SONT IN! INS SYM ZAG2Z-4 IGW3ASSY 3 0122-02#9-NaHsum WO) 7 0010-O££9-1NN tb) 6901--£19--M3Y095 (bp) 3E 93-0203 HIHSYM 1907 [91) 95 Ю-0$9-11М {90 22 11-yL£19-MIYIS (91) Jo A L ——.. 22 7 O \ (@ZAG2 NI OFJOHTONI) FOSO-FEII-M3N9S cans! - Pe TNA ыы в А К nn An | A) 13IMSTDLZ) ¡9N91-LIASVO 114 I-b£19-M3H8095(b) 1¿S2-02b9-H43IHSVM 4907 (4) 2612-026 I-UIHSTM RI) ¿160-0€£9 —1MN (p) 0161-02 19-M3Y95 [b) S6LN@I— YANOD 9866 @МУ $856 SWHOT FAS GIASZ— ATBW1ISSY OY LNOO 39v110A 68N6I— LINOVHB (CONC! NOMS FiVIOT- Thad at Ailes CbNbO-— LYOddNS #5r1-0159-L3A14 19} 6592-02#9-N3HSVM Bl 2980-02£9-10MN [B) OSSI-OEI9-M3H9S [8] 59146-02b9-YIHSVM 4307 62M96-HI1VWD (bp) £810-O€£9-1MN 12) 9pS0-S$299-1108 SOBNGI HJADO ¿880-027 199-UIHSTM 09881-0£19-M3Y95 82 M95-S80NA [SICNTINI) #62AGZ—-AIGWISSY HOOG 13 FEED ROLL- 29439 MOTOR AND GEAR REDUCTION ASSEMBLY PRESSURE ROLL ASSEMBLY — 25V29— (FOUR SPEED GEAR}—29V43 (SEE FIG.20) — (SEE FIG.17) 1 ( | SCREW-6134-0115 | | iY NUT-6325-0365 — WASHER-6430-0110 SUPPLIED AR — - BUS BAR — 19N6l (2)WASHER — 19N58 OSVE7 WRENCHES (2) INS. PLATE —19N56 (4) SCREW-6134-0217 | (4) INS. BUSHING —- 19N57 NOTE — WHEN REFILLING GEAR HOUSINGS USE TEXACO REGAL STARFAK GREASE PART NO S2WI10 (5-LA CAN) FIG. 16 — Welding Head Assembly — 2944 e > à {3iNUT- 6320-0995 ¢ (3) WASHER-6430-79 GASKET—4 | ZA, o ¢ OF FEED ROLL A po al Li TT | - .. à MOTOR ASSEMBLY 57V26 (SEE FIG.19) = GEAR UNIT REPLACEMENT PARTS (SEE FIG.18) FIG. 17 — Motor & Gear Reduction Assembly — 29V43 14 Ааше$$ у чоцопрэы 41099 — Bl ‘| 0060-5<19-№ 35525) BLNLI— A VO $/0¢-0209-97 1d ЭВА — ONIHSNG S1M16 — ОМУ 39 {37401 375) М, 3939 в ИНОМ / сьмв—омыузв f£ ¿MI6 —143SNH E) SIGNTIONI ATFILVH VATS $e Alt? — ONISNOH FSFHL FOV Io Fe VIA IN (PEMIP Ni OFOTIONI Td MIG—LYISNI (2) m ran 33$} м. 5939 £10-b£I19-M3489S OCMI6 — 91714 OCSO-PEIS-MIYISIE) di 13S МУНЕ 3935 „Р. &7 39 @ УСМ OBNIE— dy (T79Vi 135} 4,47 39 „Я, HPF GbM48—ONIUV 38 GOM48 — 1735 (F1EVL 3357 9. WHOM 0060-b219-M3YOS (E) SPMZE — ONIN 38 ВА — 470 OOSO-FEIS-MIUIS [EI 6SN6l {NYO FT-SIOIMZE ON 180d FSV IG HVIHWLS 77934 OOPX 31 SN INISNOH e039 ONT TAFE NFHM — © ОМ {07345 УПОРА! Did B OVIT OPAST HO BOLO | (03395 FIHNGIILIAISG у i м узы | (03345 3180001 NHAIS JONTION ОМ Об $ ВИЗУ à ae в АИ FONVHINT YFINOLSNO HOF FIGU WAY SHIBWISSY ONIMOTIOS GIONIWNODTS LON SLIND NOLLONGIA APO 30 Va 38 O TH T JLON l'E Hi га Wars I\ranı 77e¢n0g/| [Wee Be} 3789004! 378n00/| 378900} ¿INTO 13345 GONST |BONSTI | BINTO поз Гы Gas GH CHL Foes) | (Weld Es FIONIS!| FTSE Тау # S2N10 0339$ Oé¿NTO | GINTO | DENTO Vidi (CG HE ГОРЫ (GHz Гану этапов Госу Ра} FIOMGAL F79NISH УПО ZINIO 03345 OZNTO! 6INTO | BINIG 3718n09 Гани (GH faa (Wo 27 TIMES FTIMS/| 779416) O2N10 | GINIO | EZNTO aeNTO 3719NIS if, „En ин „т LAd LAG 4V39 | WEOM | 4V3D |4V398 NYOM Lfdi fo FLVIGFING SL NI SLNFWIOV Fd 34 YVID SO 51971 PBO2L-FEIS-M34I5 SPM 48— ONIN 38 boi /8— ONY Jd ЭВМ — 495 BONTO — 1 4¥HS [EN¿] —YIASOA ONT LY INSNI ¿EVO HL ES LM — HAHSVM ONIL IASNI 2 OSNG6I ~Y3HSYM 13315 LN pl 736 3-5116-CORD (20-IN} © TERMINAL 96W49 55\/73 <= STRAIN RELIEF N AD 7363-5416(524N) CORD NC PLUG SHELL—90W39 6-POLE MALE CONTACT UNIT-90W42 (8)"O"RING-85W50 (Yas (2)55W 74-SCREW BRACKET —-55W88 DOW78 SPRING NOTE. FOR EXCHANGE MOTORS, 3 EXTRA NUTS—6320-0995 AND 3 EXTRA WASHERS-6430-7994 ARE SUPPLIED. Foe N N ПР NN AS E E EE E EA, os. apart qu Fan. > aa Fi‘ N (2}55\84 FO css Saa À IN BRUSH ASSEMBLY ra a 7 = NN (3)55W90-STUD A a — o -TERMINAL 7 363-511G—CORD (54 -IN) COMPLETE LEAD & PLUG ASSEMBLY-18V40 GNGLUDES PLUG SHELL, CONTACT UMT, TERMINALS, CORDS & AINGS DOWSO BEARING I)55W75-5CREW (10 MM) (LEG ll San AAA г N LM N mr р NS A № | I IN: — Sl I re, 2 ‘eH | LENS 1 ence on {50V83} С SoW82- BAFFLE 55W86-ARMATURE 55W85- FIELD 55W81~ BRACKET 2} 55W76-SCREW (2}55W77?-LOCKWASHER 55W79-BEARING(8 MM) (2) 95W83-BRUSH SCREW (2) 55W87—BRUSH HOLDER FIG. 19 — 32 Volt Motor Assembiy — 57V26 ADJUSTING SCREW ASSEMBLY—25V69 INCLUDES KNOB-ISN98 SCREW-6133-0084 SCREW-6133-0149 WASHER 6430-0125 ARM-32W93 SPRING—21N 36 BLOCK-21N 61 SLEEVE-21N 71 STOP-32W96 BOLT—32W95 HAFT-21N 70 6430-0225 > ROLL ASSEMBLY 18V69 INGLUDES ВЕАКМС-93\50 NUT—S96Wol WASHER-6430-0110 J FIG. 20 — Pressure Roll Assembly — 25V29 16 — UPPER CONTACT ASSEMBLY-55W92 #CORD- 7363-5116 SPRING -55W94 GROMMET — 8IW54 [ SPRING-55W97 | N e +. = fs N > = q © ©) = SPRING- 55W95 — 4 : | = D) |! À | N O O O \ \ N IA I 1 | | | | | г! A | | | | 4 No i ' D < [| р LUG—-82W5I (ORDER AS REQUIRED) LOWER CONTACT ASSEMBLY —-55\93 6 SPECIFY LENGTH WHEN ORDERING. FIG. 21 — Current Relay Assembly — 29V10 (A) FINGER=ZENS I. Г 7 —i4) STUD-I8N28 А | u / INCLUDES ] le pl 4 РМ 6220955 Ч 5РЕМЕ—5495— || ! 4 (2) CLAMP-20N27 \ P)SCREW-ZON?B = (4\6124-0112 (2) JA SCREW | | / 4)6420-2360 и ; | | | LOCKWASHER И ЕР (SUPPLIED) (4) NUT SPRING —28764 — om iff | VE 6337-0 7 (EE NOTE) о ЧИ LES (SEE NOTE 1) a Run КЖ — 18N24 4% rt OT ry S rire "À 77 SEEN EW _ ee ¢ ча 72 WASHERTISNES Ni SHAFT ASSEMBLY | (2)DISK—IBN 25 6 Zn Iumauuoes ) SCREW-6134-1182 PIN-6225-0055 “i | PIN-6225-008! (INCLUDED IN IBENZB} т | | : CEE N Re 4 | | Nest ad MA)PIN-6224-006 | NOTE- REEL IS SUPPLIED + Lo H-APIN-6225-0045 | seit PINS IN POSITION SHOWN, | Г, ug" | FOR USE WITH WIRE CO) к y VIEW A" | WIDE. FOR me] 1.5 3. 349 dE Lu | |! | г А LL TRANSFER PINS TO SECOND a MeL 32 DA, 3 HOLE FOR COILS 2" WIDE, ns gi Г. 4 REVERSE FINGERS AND || LS НЕ Da 3 DA "DIA PLACE PINS AS FOR 3° COILS | ро | | | — — о al. ta | SUPPLIED NOTE 1- RE. BRAKE SPRINGS. 8 zu mn m | TON 92W 12 SPRING WHEN WIRE REEL If PACKED SEPARATELY; A = | u [IÈN26 |IGUIDE SPRING (28264) 8 WASHER(G420-0175) ARE ASSE 9" A À 8134-1112 _|LISCREW BLEND TO WISE REEL A AO NA] г + WHEN WIRE REELS ASSEMBLEC TO “HEL IARC OR 1G . ; 6134-0166 [SCREW _.| SIGMA WELDING MACHINES, SPRING (28264) 8 (4) 11/32" DRILL 6330-0121 [{4) NUT WASHER (6420-C'7S1R25 N97 SUPPLIED, SPE NG (G2W:215 чо 6420-2350 [[AILOCKWASHER]| — СИРЕВМ26) АВЕ АЗЗЕМВЕЕО Тб МНЕ НЕЕ. - FIG. 22 — Spoke-Type Wire Reel - 19V89 17 PART NO. 6020-4075 6110-1851 6124-1149 6130-0087 6130-1085 6130-1738 6130-1849 6130-1850 6130-1863 6130-1881 6130-1910 6130-1988 6130-2111 6132-2982 6133-0084 6133-0149 6133-0165 6133-0975 6133-2084 6134-0080 6134-0112 6134-0113 6134-0115 6134-0182 6134-0187 6134-0217 6134-0512 6134-0542 6134-0800 6134-0902 6134-0904 HARDWARE LIST FOR PORTABLE FLEXIBLE WELDER UWM-2 (SERIES 5)-- PART NO. 01E29 DESCRIPTION 1/4-in. Hex Socket Head Pipe Plug No. 6-32 x 3/8-in. Round Head Brass Screw 3/8-in.-16 x 1-1/2-in. Hex-Head Cap Screw 1/4-in.-20 x 1/2-in. Fillister Head Ma- chine Screw 1/4-in.-20 x 5/16-in. Long Round-Head steel Machine Screw No. 10-32 x 1-1/2-in. Round-Head Ma- chine Screw No. 6-32 x 1/4-in. Round-Head Screw No. 6-32 x 5/16-in. Round-Head Ma- chine Screw No. 6-32 x 7/16-in. Round-Head Ma- chine Screw No. 8-32 x 5/8-in. Round-Head Ma- chine Screw No. 10-32 x 3/8-in. Round-Head Screw No. 5-40 x 1/8-in. Round-Head Screw 5/16-in.-18 x 1/2-in. Oval-Head Ma- chine Screw Parker-Kalon Type Z Self-Tapping Flat Head Screw 1/4-in.-20 x 1/4-in. Socket Headless Cup Point Setscrew 3/8-in.-16 x 1-1/2-in. Socket Headless Cup Point Setscrew 5/16-in.-18 x 5/8-in. Socket Headless Cup Point Setscrew No. 10-24 x 1/8-in. Socket Headless Cup Point Setscrew 1/4-in.-20 x 1/4-in. Long Socket Head- less Self-Locking Cup Point 1 /4-in.-20 x 3/4-in. Socket Head Cap Screw 5/16-in.-18 x 7/8-in. Socket Head Cap Screw 5/16-in.-18 x 1-in. Socket Head Cap Screw 5/16-in.-18 x 1-1/2-in. Socket Head Cap Screw 1/2-in.-20 x 2-in. Socket-Head Cap Screw 1/2-in.-13 x 1-1/4-in. Socket Head Cap Screw 1/4-in.-20 x 2-in. Socket Head Cap screw 1/4-in.-20 x 1-3/8 -in. Socket Head Cap screw 1/2-in.-13 x 1-1/2-in. Socket Head Cap screw No. 10-24 x 3/8-in. Socket Head Cap Screw No. 10-24 x 1/2-in. Socket Head Cap Screw No. 10-24 x 3/4-in. Socket Head Cap Screw 18 PART NO. 6134-1089 6134-1107 6134-1108 6134-1111 6134-1131 6134-1132 6134-1133 6134-1174 6134-1182 6134-1188 6134-1195 6160-2863 6224-0061 6224-0064 6225-0061 6310-0862 6314-0184 6320-0862 6320-0886 6320-0995 6325-0365 6330-0100 6330-0121 6330-0136 6330-0183 6330-0917 6334-0137 6334-0183 6337-0150 6410-0860 6420-0887 6420-0987 6420-2190 6420-2210 6420-2360 6420-2534 6420-2571 6420-2632 6420-2722 6420-2747 6420-2859 6420-2888 DESCRIPTION 1/4-in.-20 x 3/4-in. Hex-Head Cap Screw 1/4-in.-20 x 7/8-in. Hex-Head Cap Screw 1/4-in.-20 x 1-3/4-in. Hex-Head Cap Screw 5/16-in.-18 x 1/2-in. Hex-Head Cap Screw 3/8-in.-16 x 5/8-in. Hex-Head Cap Screw 3/8-in.-16 x 7/8-in. Hex-Head Cap Screw 3/8-in.-16 x l-in. Hex-Head Cap Screw 5/16-in.-18 x 1-1/4-in. Hex-Head Cap Screw 1/2-in.-20 x 2-in. Long Hex-Head Cap Screw 1/2-in.-13 x 2-in. Hex-Head Cap Screw 1/2-in.-13 x 1-in. Hex-Head Cap Screw No. 6-32 x 7/16-in. Oval-Head Stainless Steel Machine Screw 3/16-in. x 1/2-in, Producto Dowel Pin, No. RO-8 3/16-in. x l-in. Producto Dowel Pin, No. RO-11 No. 250-,250 x 2-in, Roll Pin Elastic Stop Nut Corp. No. 6-32 Hex Brass Nut 1/2-in.-20 Hex Brass Jam Nut No. 6-32 Hex Nut No. 8-32 Hex Nut No. 12-28 Hex Nut 5/16-in.-18 Square Machine Screw Nut 1 /4-in.-20 Hex Nut 5/16-in.-18 Hex Nut 3/8-in.-16 Hex Nut 1/2-in.-13 Hex Nut No, 10-32 Hex Nut 3/8-in.-24 Hex Jam Nut 1/2-in.-13 Hex Jam Nut 7/16 x 14-in. William's Co. Wing Nut (Type A) No. 6 Brass Washer No. 8 Plain Washer No, 5 Steel Washer 1/2-in. x 11/64 x 1/16-in. Lock Washer 1/4-in, « 3/32 x 1/16-in, Lock Washer 5/16-in, x 1/8 x 1/16-in. Lock Washer 1/4-in. x 3/32-in. x 3/64-in. ASA, Light Steel Lock Washer 5/16-in. x 1/8 x 5/64-in. Lock Washer 3/8-in. x 1/8 x 1/16-in. Lock Washer No. 6 A.S.A. Med. Lock Washer, Steel No. 10 x 3/64-in. x 3/64-in. Steel Lock Washer No. 6 x 3/64-in. x 1/32-in. Steel Lock Washer No, 8 x 3/64-in. x 3/64-in. Lock Washer (continued) 4 more A о EL pr I à ie ru, Arie > PART NO, 6420-2920 6420-9765 6430-0075 6430-0110 6430-0125 6430-0175 6430-0225 6430-0860 6510-1454 Hardware List (conciuded) DESCRIPTION PART NO, DESCRIPTION No. 10 x 1/16 x 3/64-in. Lock Washer 6550-0038 1/8-in. x 1/4-in. Round-Head Aluminum No. 1124 Shakeproof Lock Washer | Rivet 1/4-in. Steel Washer 6625-0546 1/2-in.-13 x 6-in. Threaded Eye Bolt 5/16-in. S.A.E. Plain Washer 7363-5116 $ Simplex Tirex Cord, Type "SO", 16 Ga., 3/8-in. Steel Washer (Black) 1-Conductor 1/2-in. S.A.E, Plain Washer 7363-5416 ¢ General Electric Cord, Type "S", 16 5/8-in. Steel Washer Ga., 4-Conductor No. 6 §.A.E, Plain Steel Washer 9086-2115 1-3/4=-in. I.D. x 1/8-in. Wall x 8-in. 1/8-in. x 3/16-in. Fiat Head Brass Long Neoprene Tubing Rivet @ Specify length when ordering. 19 LINDE COMPANY DIVISION OF UNION CARBIDE CORPORATION Offices in Principal Cities UNION CARBIDE General Office: New York Outside U.S. and Canada: LINDE DEPARTMENT in Canada: UNION CARBIDE CANADA LIMITED, Union Carbide International Company, Linde Gases Division, Toronto Division of Union Carbide Corporation 270 Park Avenue, New York 17, М. \., Ц.5.А. Lithographed in U, 5. A. F-93239-G IMD J-9030-62 =. м. pr u a ож,
advertisement