advertisement
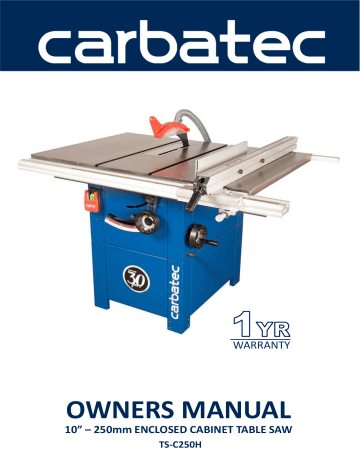
WARRANTY
OWNERS MANUAL
10” – 250mm ENCLOSED CABINET TABLE SAW
TS-C250H
Declaration of Conformity
Copied from CE Certificate
The undersigned, F. Nispel authorised by
Laizhou Fulin Machinery Co., Ltd.No. 275 Wenquan
East Road Laizhou, Shandong 261400 P.R. China declares that this product:
Model number
MJ2325D/MJ2330D Table Saw
manufactured by Laizhou Fulin Machinery Co. is in compliance with the following standards or standardisation documents inaccordance with Council
Directives
EN 61000-3-3: 1995+A1
EN 55014-2: 1997+A1
EN 61000-3-2: 2000
EN 55014-1: 2000+A1
WARNING!
Under no circumstances should
CHILDREN be allowed in work areas
IT IS RECOMMENDED THAT YOU WEAR EAR PROTECTION
WHEN USING THIS MACHINE
WARNING!
The symbols below advise that you follow the correct safety procedures when using this machine.
Fully read manual and safety instructions before use
Ear protection should be worn
Eye protection should be worn
Dust mask should be worn
Foot protection should be worn
Two man assembly
Keep hands away from moving parts and cutting area
03
Parts Index
Model Number: MJ2325D/MJ2330D
501196 10” and 501197 12” Saw Bench (Box 1 of 2)
1 off: Saw Table on upper chassis (with motor, table insert, saw blade & NVR Switch fitted)
2 off: Side Panels and Front & Back Panels
4 off: Lower Leg Columns
1 off: Side Table Extension
1 off: Dust Extraction Moulding 100mm
1 off: Dust Extraction Hose 100mm
Bag Containing:
8 off:
4 off:
4 off:
4 off:
16 off:
M8 x 25mm Square bolts, washer and nuts
M8 x 20mm Bolts, washers (for the connection of worktable & extension table)
M6 x 16mm Phillips s crews, washers/nuts
M8 x 16mm Bolts, washers and nuts
M8 x 16mm Bolts, washers and nuts
1 off Rear Extention Table
2 off: Extention Table Support Brackets
2 off: Clamping Plates with pre-drilled holes
Bag Containing:
4 off:
2 off
1 off:
M8 x 20mm Caphead Bolts and washers
Hand Wheels and locating keys
Mitre Fence and Mitre Fence Extension with clamping screw knobs
1 off:
1 off:
1 off:
1 off:
Mitre Fence Steel Plate with pre-driled holes
Saw Guard with Phillips screw/nut and coach bolt/knob
Riving knife
M6 x 40mm Coach bolt and knob
2 off:
1 off:
Bag Containing:
125mm and 50mm Hose Clips
30mm hose
1 off: Tommy Bar
1 off: Spanner for (Changing the Blade)
Bag Containing:
1 off: Push stick
2 off: 13/17mm Spanners
Hex Keys: 3,4,5,6 and 8mm
1 off: Instruction Manual
4B
15
16
17
18
18A
18B
19
19A
12
13
14
9
10
11
5
5A
5B
6
7
8
1
2
3
3A
4
4A
04
Parts Index
501196 10” and 501197 12” Saw Bench (Box 2 of 2)
1 off: Rip Fence Assembly (partially assembled)
1 off: Rip Fence Extension
1 off: Short Rip Fence (front rail)
1 off: Short Rip Fence (back rail)
Bag Containing:
2 off: ‘T’ bolts M6 x 70mm and M6 knobs
2 off: Plastic Capping Plates (for ends of the rip fence mounting bracket)
2 off: Plastic Capping Plates (for ends of front rip fence rail)
8 off: 4mm Round head self tapping screws
1 off: Micro Adjuster Assembly
951538 10” and 951541 12” Table Extension Kits (Box 1 of 2)
2 off: Extension Tables with M8 x 25mm ‘T’ bolts, washers and nuts
1 off: Table support leg
1 off: Threaded rubber foot
Bag Containing:
8 off: M8 x 30mm bolts, washers and nuts
2 off M8 x 20mm bolts washers and nuts
951538 10” and 951541 12” Table Extension Kits (Box 2 of 2)
1 off: Long Rip Fence (front rail)
1 off: Long Rip Fence (back rail)
1 off: Measuring scale extension label
951539 10” and 12” Sliding Table K its ( Box 1 of 2)
2 off: Sliding Table Mounting Brackets
2 off: Steel Clamping Plates (for Mounting brackets)
1 off Work Clamp and Tool Post
1 off: Sliding Table Assembly
Bag Containing:
6 off: M10 x 19mm Hex bolts (for table adjustment)
951539 10” and 12” Sliding Table kits ( Box 2 of 2)
1 off: Sliding Table Rail Assembly
1 off: Mitre Angle Rip Fence Assembly
05
Continues Over....
26
27
28
29
30
31
20
21
22
23
24
24A
24B
24C
25
37
38
39
35
36
32
33
34
40
41
Parts index
951539 10” and 12” Sliding Table kits ( Box 2 of 2)
Mitre Angle Rear Quadrant (with lift and shift handle)
Table Fence Mounting Casting
Mitre Angle Rip Fence
2 off: Height Adjusting Blocks
1 off: Distance Stop (with lift and shift handle)
42
43
44
45
46
General Instructions for 230V Machines
Good Working Practices/Safety
The following suggestions will enable you to observe good working practices, keep yourself and fellow workers safe and maintain your tools and equipment in good working order.
WARNING!
KEEP TOOLS AND EQUIPMENT OUT
OF THE REACH OF YOUNG CHILDREN
Primary Precautions
The machines are supplied with a moulded 16 Amp plug (AW10BSB2) and 16 Amp plug (AW12BSB2) with a
3 core power cable. Before using the machine inspect the cable and the plug to make sure that neither are damaged. If any damage is visible, have the damaged item inspected/repaired by a suitably qualified person.
If it is necessary to replace the plug, it is preferable to use an ‘unbreakable’ type that will resist damage on site. Only use a 16 Amp plug, (AW10BSB2) and 16 Amp plug (AW12BSB2) and make sure the cable clamp is tightened securely. Fuse as required. If extension leads are to be used, carry out the same safety checks on them, and ensure that they are correctly rated to safely supply the current that is required for your machine.
Primary Precautions
The machine is not designed for sub-aqua operation, do not use when or where it is liable to get wet. If the machine is to be used outside and it starts to rain, stop work and move it inside. If machine has got wet; dry it off as soon as possible, with a cloth or paper towel.
DO NOT use 230V ac powered machines anywhere within a site area that is flooded or puddled, and do not trail extension cables across wet areas.
KEEP the machine clean; it will enable you to more easily see any damage that may have occurred.
CLEAN the machine with a damp soapy cloth if needs be, do not use any solvents or cleaners, as these may cause damage to any plastic parts or to the electrical components.
KEEP the work area as uncluttered as is practical, this includes personnel as well as material.
06
General Instructions for 230V Machines
UNDER NO CIRCUMSTANCES SHOULD CHILDREN
BE ALLOWED IN WORK AREAS
t is good practice to leave the machine unplugged until work is about to commence, also make sure to unplug the machine when it is not in use, or unattended.
Always disconnect by pulling on the plug body and not the cable. Once you are ready to commence work, remove any tools used in the setting operations and place safely out of the way. Re-connect the machine.
It is also recommended that you use switched supply outlets.
Carry out a final check e.g. check the cutting tool, drill bit, saw blade etc., is securely tightened in the machine, check you have the correct speed and function set, check that the cutting path of the timber is unobstructed, etc.
Most machines these days are fitted with NVR contact switches so that machines cannot remain inadvertently switched ‘ON’. However, it is a good habit to train yourself to check that the machine is not ‘switched on’ prior to connecting the mains supply, in case you happen to be using one of the older machines.
Make sure you are comfortable before you start work, balanced, not reaching etc.,
If the work you are carrying out is liable to generate flying grit, dust or chips, wear the appropriate safety clothing, goggles, gloves, masks etc., If the work operation appears to be excessively noisy, wear ear-defenders. If you wear your hair in a long style, wearing a cap, safety helmet, hairnet, even a sweatband, will minimise the possibility of your hair being caught up in the rotating parts of the machine, likewise, consideration should be given to the removal of rings and wristwatches, if these are liable to be a
‘snag’ hazard. Consideration should also be given to non-slip footwear, etc.
DO NOT work with cutting or boring machines of any description if you are tired, your attention is wandering or you are being subjected to distraction. A deep cut, a lost fingertip or worse; is not worth it!
DO NOT use this machine within the designated safety areas of flammable liquid stores or in areas where there may be volatile gases. There are very expensive, very specialised machines for working in these areas,
THIS IS NOT ONE OF THEM .
CHECK that cutters, drills, blades etc., are the correct type and size, are undamaged and are kept clean and sharp, this will maintain their operating performance and lessen the loading on the machine.
If possible always fit dust extraction to machines that are producing high rates of sawdust, shavings, chips etc. Above all, OBSERVE....
make sure you know what is happening around you, and USE YOUR COMMON
SENSE.
REMEMBER, YOU ARE ULTIMATELY RESPONSIBLE
FOR YOUR OWN SAFETY THIS MACHINE IS
DESIGNED TO CUT TIMBER AND TIMBER
DERIVATIVE PRODUCTS. DO NOT USE FOR ANY
OTHER MATERIALS.
07
Specification
Model
Code
Rating
Power
501196
Trade
2.2kW 230V 1ph
Blade Dia/Bore
Blade Tilt
Max Depth of Cut @ 45˚
Max Depth of Cut @ 90˚
0-45°
60mm
75mm
Max Width of Cut with Fence (with optional table extensions) 840mm
Max Ripping Width (with optional table extensions)
Table Size (incl side table)
Table Height
Table Size With Extensions
Dust Extraction Outlet
Min Extraction Airflow Required
Overall L x W x H
Weight
990mm
800 x 830mm
865mm
Text
800 x 1,170mm
100mm
1,000 m
³
/hr
1,170 x 800 x 865mm
184kg
Initial Assembly
AW12BSB2
501197
Trade
3kW 230V 1ph
315 x 30mm
0-45°
75mm
100mm
1,160mm
1,320m
800 x 870mm
865mm
800 x 1,480mm
100mm
1,000m
³
/hr
2,030 x 840 x 865mm
215kg
Please read through the Section entitled Parts identification and Description, this will enable you to more readily identify those parts of the saw to which we will be referring.
Please note. Some of this assembly procedure is best accomplished by two persons.
Although the tasks are not impossible, some of the items are heavy and awkward, and a mishandling error could cause injury. Please think about what you are doing, your capabilities and your personal safety. We have added the ‘two person symbol’ to any operation that we recommend should be a two person task.
You will require: A pozi screwdriver in addition to the tools supplied.
Unpack all the boxes and check all the components against the “Part’s Index”.
If any parts or components are missing, please contact our customer services department using the procedures and telephone numbers listed in our catalogue, and you will be dealt with quickly and efficiently.
Please note: that, on occasion, the packing list is not strictly adhered to, please check all the boxes, packets etc, to make sure that all the parts have been accounted.
08
Initial Assembly
PLEASE RECYCLE ANY UNWANTED PACKAGING RESPONSIBLY
Saw Body Assembly
Having unpacked the boxes, put the parts and components where they are readily to hand. Break down the main box by knocking the sides away (be careful of exposed nails etc.) , but leave the machine sitting on its pallet. Identify the short rear panel with the dust extraction cutout (2) , locate the dust extraction moulding (4) and fit to the panel using the nuts and bolts (5) provided. (See fig 1) (The orientation of the moulding should leave the 30mm outlet pointing upwards i.e. pointing up the long length of the panel). Put the panel aside, and locate the lower leg columns (3) and 4 No. M8 x 20 (5A) bolts, nuts and double washers. Fix the lower legs to the upper legs using a washered bolt through the legs and secure with washer and nut, only turn the nuts up finger tight at this time. (See fig 2) Locate the rear extention table
(6) , table support brackets (7) , steel clamping plates (8) and 4 No. M8 x 20mm caphead bolts and washers (9) .
PLEASE NOTE: the manufacturer has fitted adjusting bolts to the brackets, these are the faces that back against the legs.
Offer the clamping plates (8) up to the inside face of the legs (3) , fasten the brackets using washered bolts
(9) through the bracket and the leg into the clamping plate. Tighten the bolts finger tight only at this time.
5A
Fig 1 4
3
Fig 2
5
2
Fig 3 7 Fig 4
8
09
Initial Assembly
Fig 5
9
With easy open access, now is a good time to fit the dust extraction hose. Locate the hose (4A) and the two 125mm hose clips (16) . Stretch the hose out to its full length. Slip the hose clips over the ends of the hose, fit the hose to the outlet on the saw box and the dust extraction moulding and tighten the hose clips to clamp them in place. (See figs 8-9-10)
Fig 9
Adjusting bolt
Fig 6
4A
7
Fit the hose over the dust extraction moulding and clamp in place
Fig 10
Table supporting brackets assembled
Locate the remaining three panels (2) and 20 No.
M8x16mm (5B) bolts, nuts and double washers.
Take up the rear panel with the dust extraction moulding fitted and fit between the rear legs, using washered bolt through the leg and panel and securing with washer and nut. Again, secure
the nuts finger tight only. (See fig 7)
Fig 7
16
Fig 8
Fit the hose over to the saw box outlet and clamp in place
Fit the remaining panels to the legs, using the same securing sequence. Wriggle, push, pull, press, lever etc., the legs and the panels into the best alignment with the upper chassis and tighten the nuts and bolts using the spanners provided. (See figs 11-12)
Fig 11
16
4A
10
When everything is tightened up, the machine can now be tipped over, towards its blind face until it is resting on the pallet with its legs on the floor. Lift the machine upright. (See figs 13-14)
Fig 12
Initial Assembly
Fig 16
Locate the rear table (6) and the other 4 No. M8 caphead bolts and washers (9) . Mount the table onto the brackets, Note: that the securing bolts need to feed through the elongated holes in the bracket (7) , the rear extension table is spaced off the main table to allow clearance for the rear clamping rail and the rip fence. Leave all bolts finger tight at this time. (See figs 15-16)
Fig 13
Side Extension Table
Locate four M8 x 16mm hexhead bolts and washers.
Ensure the table is correctly orientated. Stand the back end of the side extension table (3A) on the floor, close to the front and edge of the main saw table (1) , with the underside of the table facing the front of the saw. Lift the table up and introduce a bolt and washer through the first hole in the table and screw it into the first threaded hole along the main table edge. Repeate for the remaining bolts.
Place a level across both table surfaces and tighten the bolts, (See figs A-B).
Side extension table
Fig A
3A
Blind face
1
Fig 14
Fig B
Fig 15
Elongated holes
7
11
M8 x 16 Bolt
Continues Over....
Initial Assembly
Fitting Hand Wheels
Locate the two hand wheels (10) . Remove the Hex screw and washer from both drive shafts and place aside. Insert a square key into each machined slot on the drive shafts and slide the hand wheels onto the shafts. Replace the Hex screws and washers and tighten securely , (See figs 17-18-19-20)
NOTE: Line up the key slot in the hand wheel with the square key and slide the wheel onto the shaft, tighten securely.
NOTE.
Please ensure that the rise and fall LOCK is unlocked before operating the mechanism.
Fig 17
Shaft
Key slot
Drive shaft for the tilt mechanism
Fig 18
Fig 20
10
Secure the hand wheel in place using a
Hex screw and washer then tighten using the supplied Hex key
Saw Guard Assembly
Locate the Riving Knife (14) , remove the 5 screws that secure the saw gullet, place both carefully aside.
(See figs 21 22) Raise the saw blade up to its highest point.
NOTE: The mounting plate for the riving knife has been factory set to ensure that the riving knife is aligned with the blade. DO NOT alter the setting bolts.
Fig 21
Key slot
Square key
Insert the hand wheel over the shaft for the tilt mechanism
Fig 19
Hex screw
14
Fig 22
12
Initial Assembly
Introduce the slot in the riving knife (14) over the two centre line bolts, behind the washers and nip the bolts to just hold the riving knife against the mounting plate. Set the riving knife so its close to the blade, (gap with in 8mm). Tighten the clamping bolts securely. (See figs 23-24)
Replace the saw gullet.
Mounting plate
Fig 23 Fig 24
14
8mm gap
Locate the saw hood guard (13) , the 30mm extraction hose (17) and the 50mm hose clips (16) .
Introduce the pin bolt through the pre-drilled hole in the guard (13) and lightly screw on the clamping knob. Lower the guard so the pin bolt fits into the curved slot in the riving knife then tighten the clamping knob to pinch the guard to the riving knife. (See fig 26-27)
Fig 25 Fig 26
Pin bolt
Curved slot
13
Fig 27
Clamping knob
Fig 28
17
16
Push the hose clips (16) over the ends of the hose (17) , push the hose onto the dust extraction outlet on the guard (13) and the main dust extraction moulding (4) and tighten the hose clips to hold it in place. (See figs 28-29)
13
Continues Over....
Initial Assembly
There is no requirement to remove the guard. The profile of the riving knife precludes the use of the saw for slotting or grooving, and the maximum depth of cut can be achieved with the guard in place.
NOTE: The positioning of the extraction hose could be a nuisance if you are cutting big boards, in such a case it is better to remove the hosing from the guard, then there is less risk getting the workpiece snagged and perhaps ‘slewing’ on the saw.
Fig 29 17 Fig 30
4
4B
Rip Fence Assembly
Locate the M8 x 25mm SQUARE head bolts washers and nuts (4B) . The best way to fit the rails is to introduce the bolts through the holes in the front and rear edges of the tables, hold in position by adding the washer and fitting the nut a couple of turns onto the bolt. (See figs 30-31)
Fig 31 22 Fig 32
4B
Select the front short rip fence guide rail (22) , introduce the square head of the furthest right hand bolt into the channel in the extrusion; slide the rail along the front of the machine picking up all the bolt heads as you go along. (See fig 32) Reach under the table edge and lightly tighten all the nuts. (See fig 33) Repeat the process for the back rail (23) . (See fig 34)
Fig 33 Fig 34
23
14
Initial Assembly
Locate the capping plates for the front rail (24B) and using the self tapping screws (24C) , secure in place. (See fig 35) Set the front rail in position, remembering that it must be slightly inside the front left hand edge of the main saw table, so that the sliding table does not collide with it.
Tighten ONLY the 3 bolts in the main saw table. Repeat the process for the back rail.
Capping plate
Fig 35 20 Fig 36
24B
22
24C
Locate the Rip Fence assembly (20) , fit the rip fence assembly to the saw by ensuring the clamping lug at the rear of the fence is hooked over the back rail (23) , lower the fence and manoeuvre the bracket over the front guide rail (22) . (See fig 36)
Micro-Adjuster Assembly
Locate the Micro-Adjustor (25) there are two Phillips screws through the adjustor mounting bracket with square nuts on them. Ensure the nuts are undone sufficiently to allow them to slide into the channel in the Rip Fence mounting bracket, position as required, normally slightly to the right of the rip fence, (See figs 37-38) and tighten the screws securely.
Fig 37 Fig 38
25
Tighten the Phillips screws securely
Locate the capping plates for the Rip Fence Mounting Bracket (24A) and fit carefully using the self tapping screws. (See figs 39-40)
Fig 39 Fig 40
24A
15
Initial Assembly
Rip Fence Extention
Locate the Rip Fence Extension (21) , the two M6 x
70mm ‘T’ bolts and M6 knobs (24) . Slot the two ‘T’ bolts into the fence extension recess, see figs 41 and 42. Slot the bolts into the pre-drilled holes in the fence extension and secure in place with the M6 knobs. (See fig 43-44)
NOTE: The rip fence extension (21) can be repositioned to the opposite direction for guiding thin timber pieces through. (See fig 45) tighten to clamp the extension in place. (See fig 46)
Introduce the nose of the bar (12) into the required
‘T’ slot in the main table. (See fig 47)
Note: With the rear extension table fitted it is not possible to push the small mitre fence completely through. However, the travel is such that the fence is able to travel well past the cutting edge of the saw.
Fig 46
12
Fig 47
Fig 41 Fig 42 11
Fig 43
21
Fig 45
24
Fig 44
M6 Knob
Hose Support Bracket
Locate the hose support bracket and the Hex bolt/ nut. insert the bolt through the pre-drilled hole in the bracket and loosely screw on the nut. Insert the bolt into the end of the rear guide rails ‘T’ slot, see fig
A until the bracket support is upaginst the guide rail.
Tighten the nut to secure the asssembly in position.
(See fig B)
Fig A
Hex blot
Fig B
Mitre Fence
Locate the Mitre Fence and Extension (11) , loosen the clamping screw knobs on the extension and slot each into the slot recesses on the mitre fence,
16
Hose support bracket
Initial Assembly
WARNING!! THE EXTENSION TABLES
ARE VERY HEAVY YOU WILL REQUIRE A
SECOND PERSION TO HELP!
951538 10” and 951541 12”
Table Extension Kits (Box 1 of 2)
Mounting Extension Wings
Setup 1
Select one of the extension tables (26) , locate four
M8 x 30mm hexhead bolts and washers (30) . Ensure the table is correctly orientated (the front edge of the table is bevelled). Stand the back end of the table on the floor, close to the front and edge of the main saw table (1) , with the underside of the table facing the front of the saw. Lift the table up and introduce a washered bolt through the first hole in the table and screw it into the first threaded hole along the main table edge.
it almost home. The extension should be hanging approximately in its correct position held by the two bolts. Introduce and almost screw home the other two bolts and washers. Using a level, align the top and front edges at the front of the saw, nip the front bolt to hold the extension in place; carefully manoeuvre the rear of the extension to align the two top edges and ‘nip’ the rear bolt.
Check this movement has not disturbed the alignment at the front of the table, if it has, repeat the procedure until the front and top edges are aligned. Tightened all the bolts securely. (See figs
48-49-50 and 51) Repeat using the other extension table (26) for the opposite side of the saw bench (1) .
Fig 50
Fig 48
30
26
Fig 49
Fig 51
Screw the bolt in until it is almost home. You can now relax the lifting effort. The extension will hang pivoted on the bolt. Carefully lift the bottom end of the extension up until the edges are level and introduce a bolt and washer through the rear hole and the last threaded hole in the table edge, screw
17
Continues Over...
Initial Assembly
501196 10” and 501197 12”
Table Extension Kits (Box 2 of 2)
Locate the long Rip Fence (front rail) (32) and (back rail) (33) , remove the short rip fence front and back rails (22-23) from the saw bench (1) , (follow the instruction on pages 14 and 15, “Rip Fence
Assembly” to assemble the long rip fence rails.
NOTE: Make sure the both rip fence rails are parallel to the far left of the left extension table (26) , (See fig
52). Replace the rip fence assembly (20) on the saw bench (1) , as described on page 15.
First remove the rip fence assembly (20) and place safely aside, loosen both rip fence rails (32-33) and slide them to the right. Undo the four M8 x 30mm hex bolts and remove the left table. Attach the left table to the right table using the four M8 x 30mm bolts,washers and nuts as before, (WARNING:
YOU MUST ENSURE THAT THE NUTS IS FULLY
ENGAGED ON THE BOLTS BY SERVERAL TURNS,
BEFORE RELAXING THE LIFTING EFFORT).
Tighten all the bolts securely. (See fig 54)
Fig 54
Fig 52 26
26
The left extension table, with both fence rails parallel to the edge.
Fig 53
Fig 55
NOTE:
Rear Extension not available
27
Table Extension Kit, (Setup 1) assembled
Setup 2
The Left extension table (26) can be repositioned to the end of the right extension table to create a large surface area, in doing so it also free’s up the space to attach the sliding table assembly
(code no: 951539).
Locate the table support leg (27) , the threaded rubber foot (28) and two M8 x 20mm hex bolts, washers and nuts (31) .
Line up the two middle holes to outside edge of the table with the pre-drilled holes in the support leg bracket (27) and fasten securely using the M8 bolts, washers and nuts. (See figs 55-56)
Continues Over....
18
Initial Assembly
Fig 56 Fig 60
27
Screw the threaded rubber foot (28) on to the end of the support leg (27) , until it’s tight. (See fig 57)
Unlock the caphead clamping bolt of the support leg and allow the inner section to slide through until the foot is resting on the floor. DO NOT put the leg under tension at this time.
‘Nip’ up the clamp bolt
(See fig 58)
Fig 57
27
Fig 58
Measuring Scale Extension label
Fig 61
28
Support leg foot and caphead clamping bolt
Replace both long rip fence rails (32-33) as described on the previous page and replace the rip fence assembly (20) on the saw bench (1) , as described on pages 15 and 18.
The Measuring Scale extension label (34) can be used for the different setup configurations.
(See fig 60)
Fig 59
33 32
Table Extension Kit, (Setup 2) assembled
34
Replacing both rip fence rails
19
Setting the Machine
Tilt the blade fully over. Using a mitre square, set the angle of the saw to 45˚. Check that the index mark gives a corresponding reading against the scale. Adjust the pointer if necessary. Reset the blade upright, check that the angle scale reading is correct. (See figs 98-99)
Fig 98 Fig 99
Tilt index scale Pointer
Check that the index mark gives a corresponding reading against the scale.
45˚ Scale pointer
Set the rip fence a predetermined distance from the saw blade and lock in position. Check that the rip fence is held securely when it is locked in position. If the locking appears a little ‘slack’ adjust the position of the clamping lug at the rear of the rip fence by tightening the nut. (A)
Check that the preset distance corresponds to the measurement on the scale against the index mark in the magnifying lens. If not, adjust the position of the rip fence on its mounting bracket.
Fig 100 Fig 101
A
Index mark
Setting the Rip Fence (See figs 102-103)
Check that the fence (20) is parallel to the saw blade by sliding the fence up against it, press the clamping lever down to lock the fence in position. If you find the fence is not perpendicular to the blade loosen the three clamping bolts beneath the front rail, see fig 33 and manover the front rail until correct. Re-tighten the three clamping bolts. NOTE: Lubricate the fence rails and the underside of the rip fence clamp assembly (20) with a ptfe dry lubricant, so the fence assembly runs smoothly back and forth.
Fig 102 Fig 103
20
28
Setting the Machine
Setting the Mitre Fence
Fit the small mitre fence (11) to the machine. Loosen the clamping handle (A) .
NOTE: There are 3 preset positions available with the small mitre fence. +45˚ , 0˚ , and -45˚ , these are achieved using lugs in the casting and a push/pull pin against which the lugs are stopped. The pin has to be fully withdrawn to allow the fence to pivot from one side to the other.
Set the face to zero angle using the preset position.
Check that the angle is correct (and the lug is on the correct side of the pin). Check that the indexing pointer gives the correct reading against the scale.
Adjust the pointer if necessary. Check left and right positions. Check the pointer is still correct. If the preset positioning is wrong, set the fence with a square/mitre gauge, set the pointer accurately against the scale and clamp the fence in position without recourse to the presets. Remove the small mitre fence from the table and stow carefully aside.
(See figs 104-105)
Fig 104
A
Fig 105
Pointer
Pin
11
Scale
Fit the small mitre fence (11) into the machines ‘T’ slot. Loosen the clamping handle (A) .
Check that the indexing pointer gives the correct reading against the scale.
Checking the Belt Tension
Check the belt tension, see figs 106-107, the belt should be tight, but not unduly so. Remove all tools and stow away. Check that the machine tables are clear. Lower the saw to leave about 25mm protruding, set the saw upright.
Fig 106 Fig 107
B
Motor assembly
A
Belt (A) and Belt tensioner bolt (B)
CHECK that everything that should be tight, is tight; saw blade guard, rise and fall lock mechanism, fence clamps etc.
29
Continues Over....
Setting the Machine
Connect the machine to the mains supply, lift the switch shroud and give the machine a quick burst. i.e. On/Off. Check that everything is sound and feels O.K. (No knocking, scraping, belt squeal, rubbing etc.,)
Give the machine a longer run, and ‘SLAP’ the Emergency switch shroud down. Check that this gives a fast and easy method of switching the machine off, without searching for the stop switch button.
When you are happy that everything seems O.K. switch the machine off, disconnect from the mains supply. Locate the two upper side panels and their fixing bolts and secure them in place.
Specific Instructions/Precautions for the Saw Bench
Make sure the saw blade is the correct type for the job in hand.
Do not force the saw, if the saw begins to stall you are forcing the cut or over working the saw.
Ensure that the saw blade is clean and sharp.
Resin build up on the blades will increase the friction of the saw passing through the timber, and cause over heating of the blade, blunt teeth will work harder tearing the fibre of the timber as opposed to shearing it, also with subsequent overheating. Both faults unnecessarily load the machine beyond normal usage, and shorten its longevity.
Do not use blades that are deformed in any way.
Do not remove the blade guard. The design of the riving knife on the machine will not allow for slotting or blind grooving, so there is no reason to remove the guard. There is adequate clearance under the guard for the capacity of the machine (75mm).
Do not remove the riving knife. Do not use any blades that cut a smaller kerf than the riving knife thickness.
Make sure the riving knife is correctly adjusted to the blade and is securely fastened.
If the table insert becomes damaged or broken, and will not support the timber ‘up close’ to the blade, replace it.
30
Do not start the saw with the workpiece touching the blade.
Do not commence sawing until the blade has run up to full speed.
After switching off, never try to slow the saw down more quickly by applying side pressure to the blade.
Apply the old joiner’s adage of never getting hands within one handbreadth of the blade.
Leave the machine disconnected from the mains supply until you are about to commence work. Always disconnect the machine if you are leaving it unattended.
Never leave the vicinity of the machine unless the blade has come to a complete stop.
Do not attempt to carry out any maintenance, corrective work, setting up etc., unless the machine is disconnected from the mains supply.
If any tools have been used during setting up procedures, make sure they are removed from the machine and stowed safely away.
Do not attempt to carry out cross cutting operations freehand, always use the mitre fence for small stuff and the sliding carriage for larger work pieces.
Unless you are an experienced machine operator, do not attempt to rip freehand, always use the guiding facility of the rip fence.
It is perfectly acceptable to support guide and feed the timber with your hands whilst ripping stuff of some length, however, as you approach
Specific Instructions/Precautions for the Saw Bench the blade ensure that the push stick is to hand, and you use it.
Remember the emphasis of the push should be between the blade and the fence and close to the fence. Use your free hand to support and guide the material on the offside of the saw blade and at least 100mm away from it. If the timber does not extend to at least 100mm to the offside of the saw blade, the material possibly? does not need guiding or supporting.
Check (especially on site), that there are no foreign objects e.g. old nails, screws, small stones etc embedded in the material you are about to cut. If necessary take a wire brush to the timber before working.
If you are being assisted whilst using the saw
(by a take off or support number, remember there is only one sawyer at a machine, and they stand in front of it. The assistant does not push, pull, guide etc., unless specifically asked or instructed to do so by the sawyer.
Operating Instructions
NOTE: Before using your table saw, go round and make sure everything is secure, down, that all tool, are cleared away from the work area.
CHECK the blade for sharpness, missing teeth, resin buildup, etc., clean if necessary CHECK the blade is securely clamped in place. (i.e. not loose).
WARNING!
Feeding Work by Hand
UNDER NO CIRCUMSTANCES SHOULD CHILDREN BE ALLOWED
IN THE WORK AREA AND KEEP TOOLS AND EQUIPMENT OUT
OF REACH OF YOUNG CHILDREN
CONNECT A DUST EXTRACTION MACHINE TO THE SAW
Start up the saw, wait until it has reached full speed and slowly feed the timber through using both handles, (making sure to keep your hands well clear of the blade and using a push stick for small pieces) , until the timber is behind the riving knife. Switch off the saw, wait until the blade has come to a complete stop and remove the timber. (See figs 108-109).
Fig 108 Fig 109
NOTE: Secure larger pieces of timber to the table by using the clamp assembly (37) , see page 23.
Use the small flat surface of the fence (21) to cut thin timber narrower that 120mm. (Use a push stick).
Thin Timber Thick Timber
21 21
31
Changing the Saw Blade
WARNING! DISCONNECT THE
MACHINE FROM THE MAINS!
Raise the saw blade to it’s highest point. Remove the saw blade guard. Remove the 5 screws that secure the table insert, place carefully aside and remove the table insert. (A) Using the spanner and the tommy bar provided, put the spanner onto the flats on the nut. Turn the saw until the tommy bar hole (B) is visible.
Insert the tommy bar (18) and turn the saw to allow it to rest against the front edge of the saw slot. The tommy bar hole is in the inside platewasher component. (See figs 110-111-112)
Fig 110 Fig 111
A
18
Fig 112
C
18A
Fig 113
Fig 114
B
D
Teeth pointing to the front
Fig 115
35
Slacken off the saw nut (remember left hand thread).
Remove the saw nut (C) , then remove the sawplate washer (D) and the saw blade. Now is a good time to give the interior of the machine, the dust extraction channels, etc. a thorough clean. (See figs 113-114)
Check the new blade for damage, missing teeth,sharpness etc. Fit the new blade, ensure that the teeth are pointing towards the front of the machine. (See fig 115) Put the sawplate washer onto the shaft and twist on the saw nut. Spin the nut up finger tight and check the saw is correctly seated.
Changing the Saw Blade
Tighten up the saw nut, using the tommy bar to hold the shaft steady. Check the riving knife is aligned with the saw blade, and correctly positioned. Replace the table insert and secure with the 5 screws. Replace the saw blade guard.
When everything is satisfactory, turn the saw blade once by hand to check it doesn’t foul anywhere.
Reconnect the machine to the mains supply.
Give the machine a ‘quick’ burst check ( i.e. quick
ON-OFF) to ensure everything is O.K. If everything is satisfactory, continue to use the machine. Check the old blade for sharpness, missing teeth, resin buildup, etc., clean if necessary and send for refurbishment/ resharpening if required. If the blade is not to be re-sharpened, clean and pack away in its stowage case.
Maintenance
Keep the saw as clean and free from saw dust build up as is practical. Periodically, remove the saw gullet and vacuum out and clean out the saw box and the extraction housing. Remove any resin build up in the saw box, using a proprietary resin cleaner.
Remove the upper side panels and clean the threaded drive shafts of the rise and fall and tilt mechanisms. At the same time check the belt drive, i.e. the belt is not ‘glazing’ with resin build up, likewise with the pulley wheels. Check the belt tension. If the belt (A) is becoming slack, loosen the motor hold down bolts (B) and drive the motor backward with its adjusting bolt (C) . (See figs 116-
117) Check the saw blade regularly for chipped, missing, damaged teeth etc. and remove any resin build up from the blade, riving knife etc.
If you have finished using the saw bench, clean above and below the work table and using a damp cloth wipe the saw bench over. If the saw bench is not going to be used for a period of time, use a rustproofing spray (see our catalogue), spray a light coat over the work table and place a dust sheet over the saw bench.
Fig 116
Motor assembly
Fig117
B
C
A
Belt (A) , Motor hold down bolts (B) and Belt tensioner bolt (C)
36
1 year from date of sale.
Carbatec Pty Ltd ABN 84 010 706 242 [email protected] | Phone 1800 658 111 | www.carbatec.com.au
Carbatec Pty Ltd
ABN 84 010 706 242 [email protected]
Phone: 1800 658 111
128 Ingleston Road, Wakerley
Queensland Australia 4154 www.carbatec.com.au
advertisement