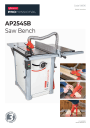
Axminster Professional AP254SB Dado Saw Package 230V Instructions
Add to My manuals36 Pages
Axminster Professional AP254SB Dado Saw Package 230V is a powerful and versatile saw designed for cutting grooves and slots in various materials. Featuring a robust cast iron table, adjustable fences, and a dedicated dado blade set, this machine allows you to create precise cuts with ease. It comes equipped with a riving knife for safety and a dust extraction port for a clean working environment. The AP254SB Dado Saw Package is perfect for woodworking projects requiring accurate grooves, dado cuts, and slots for cabinet making, furniture building, and more.
advertisement
▼
Scroll to page 2
of
36
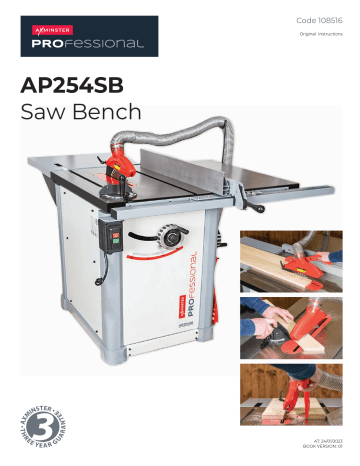
Code 108516 Original Instructions AP254SB Saw Bench AT: 24/01/2023 BOOK VERSION: 01 INDEX OF CONTENTS What’s in the box 02-03 Safety 04-05 Assembly 05-06-07-08-09-10-11 Set up / Levelling / Fine Tuning 12-13-14 General Use / Operation 15-16-17-18 Troubleshooting 19 Maintenance 19-20-21 Optional Accessories 22-23-24-25 Exploded Diagram/Parts Lists 26-27-28-29-30 Wiring Diagram 31 Declaration of Conformity 32-33 2022 The machines Serial Number is located on the specification label as shown. 2003256 Rear View A Rip-Fence Assembly K Riving Knife B Front Fence Rail L Flexible Hose Support Bracket + Fixings C Rear Fence Rail M Four Hose Clips D High and Low Aluminium Sub Fence N Dust Extraction Port E Right Hand Extension Table O Operating Handwheel Knobs F Rear Extension Table P 63mm Short Hose G Rear Extension Table Angle Support Brackets Q 63mm Long Hose H Mitre Fence R Tool Kit I Push Stick S Bolt Pack J Crown Guard T Main Table Saw The symbols below advise the correct safety procedures when using this machine. Fully read manual and safety instructions before use Ear protection should be worn Eye protection should be worn 2 Dust mask should be worn HAZARD WHAT’S IN THE BOX Fig A J A K B Fig F L N C Fig B O M Fig H D P Fig C Q E F Fig I R Fig D S G H Fig E T I Fig J 3 SAFETY The following is a list of safety precautions you must consider when using a Table saw: ALWAYS REMEMBER TO DISCONNECT THE POWER TO THE TABLE SAW WHEN MAKING REPAIRS OR ADJUSTING BLADES AND GUARDS. ALWAYS REMEMBER TO READ THROUGH THE MACHINE INSTRUCTIONS SUPPLIED. • Eye and ear protection are required when operating a Table saw. Dust extraction & respiratory PPE are highly recommended. • Make sure the blade is not in contact with the material when you start the saw. • Never leave the machine unattended when it is running. • Do not wear gloves, loose clothing, jewellery, or any dangling objects when operating a Table saw. •Keep the table top & surrounding work area free from excessive dust and debris to help prevent slipping or tripping. • Do not allow children to operate the machine. • At all times all guards must be in place and fully operational. If a guard seems to be missing or damaged, adjust, replace or repair immediately. • Maintain a balanced stance at all times so that you do not fall or lean against the blade or other moving parts. Do not overreach or use excessive force to perform any machine operation. • A riving knife MUST be used at all times when performing through cuts and must be positioned correctly. Kickback • The most common accidents among table saw users, according to statistics, can be linked to kickback, the high-speed ejection of timber from the table saw that can strike the operator. Kickback can also result in the operator’s hands making contact with the blade. • Ensure that the Rip fence is correctly aligned to the blade to help prevent the risk of timber kick back. • Never perform “free hand” cuts, a rip fence or mitre cross cut fence should always be used. Kickback Prevention • Never pull the timber through the blade from the rear of the machine, always push through from the front. • Tips to avoid the most common causes of kickback: • Disconnect the power to the Table saw when making repairs or adjusting blades and guards. • Make sure the riving knife is always aligned with the blade. A workpiece can bind or stop the flow of the cut if the riving knife is misaligned, and result in kickback. • Hands and fingers must be kept clear of the blade, always use push sticks when feeding smaller pieces into the blade. • Use a riving knife during every cut. The riving knife maintains the kerf in the workpiece, which will reduce the chance of kickback. • Use only the recommended blade size and type for the machine - see page (20) for recommendations. • Never attempt freehand cuts. • The workpiece must be fed parallel to the blade, otherwise kickback will likely occur. Always use the rip fence or mitre gauge to support the workpiece. • Ensure all blades are sharp and in good condition. • Never cut pieces smaller than the table insert size. • Make sure that the rip fence is parallel to the blade. If not, the chances of kickback are very high. Take the time to check and adjust the rip fence. • Long material should be supported at the same height as the saw table. • To avoid contact with a coasting blade, do not reach into the cutting area until the blade comes to a full stop. • Feed cuts through to completion. Anytime you stop feeding a workpiece that is in the middle of a cut, the chance of binding, resulting in kickback, is greatly increased. 4 SAFETY Tips for Kickback Protection Kickback can happen even if precautions are taken to prevent it. Listed below are some tips to protect you if kickback does occur: • Never place your hand behind the blade & never pull the timber through the cut. If kickback occurs, your hand will be pulled into the blade. • Stand to the side of the blade when cutting. An ejected workpiece usually travels directly in front of the blade. • Use a push stick to keep your hands further away from the moving blade. If a kickback occurs, the push stick will most likely take the damage that your hand would have received. • Wear safety glasses or a face shield. Your eyes and face are the most vulnerable part of your body. More safety information can be found at: http://www.hse.gov.uk/pubns/wis16.pdf ASSEMBLY - FOR SET UP / LEVELLING / FINE TUNING SEE PAGE 12 Fig 04 Fitting the Extraction Port Hose clips WARNING! THE MACHINE IS HEAVY ITS ADVISED TO HAVE HELP. 1. Remove the left side panel by removing the six caphead bolts / washers and place safely to one side. Remove cardboard box and other items from within the saw frame, see fig 01-02-03. Fixings 63mm Inner port flange spigot Fig 01-02-03 100mm Outer port Spigot M N Side panel 2. Locate the ‘Dust Extraction Port’ assembly’, ( N ). Remove the four screws and nuts from the extraction port and separate the inner and outer parts, see fig 04. Caphead bolt & washer 3. Postion both parts over the extraction port hole to the saws rear panel. NOTE: Fit the 100mm port spigot to the outer side of the rear panel. Secure using the four screws and nuts you removed eariler, see fig 05-06. Fig 05-06 The 63mm flange spigot is place inside the cabinet. Cardboard box & other parts 5 Continues over... ASSEMBLY Fitting the Right Hand Extension Table WARNING! WE ADVISE YOU GET ASSISTANCE AS THE CAST IRON TABLE IS HEAVEY. 1. Locate The right hand extension table ( E ) and the four long bolts / flat washers ( S ), see fig 10. Fig 10 The 100mm spigot placed on the outside of the cabinet 4. Locate the short flexible hose, ( P ) and two hose clips ( M ). Place a clip over each end of the hose and fit the hose over the saws dust housing outlets from inside the main saw frame. Nip-up the retaining clips to secure the hose in place, see fig 07-08-09. S E Fig 07-08-09 2. Position the extension table, ( E ) against the side of the main table, lineup the four threaded holes in both tables and secure in position with the long bolts / washers ( S ), see fig 11-12-13. Fig 11-12-13 S E 6 ASSEMBLY Fig 18 Fitting the Rear Fence Rail 1. Locate five short bolts / flat washers ( S ) and the rear fence rail ( C ), see fig 14. Fig 14 S G C 2. Position the rear fence rail ( C) to the rear of the saw bench across both main and right hand extension tables, lineup the pre-drilled holes and secure in place using the five short bolts / washers ( S ), see fig 15-16. 2. To the rear of the of the cabinet there are four threaded holes on each support column, with two caphead bolts mounted into the two upper holes on each side, see fig 16. Loosen the caphead bolts to give sufficient clearence for the next step. Fig 15-16 3. Locate the two angle support brackets ( G ). Lineup the key slots in the right hand side bracket and lower the bracket down over the two caphead bolts. Lightly tighten the bolts to secure the bracket in place. Repeat for the opposite side, see fig 19-20-21. C Fig 19-20 Key hole Caphead Bolts G Fitting the Rear Table Extension Table Fig 17 1. Locate the rear extension table ( F ), two angle support brackets, four short caphead bolts and four flat washers ( G ), see fig 17-18. F 7 Continues over... ASSEMBLY Fig 21 Fitting the Front Fence Rail & Fence Assembly 1. Locate the front fence rail ( B ) and five short bolts and flat washers ( S ), see fig 25. Lineup the pre-drilled holes in the fence rail with the ones to the front of the saws cast iron table and secure using the five bolts and washers ( S ) see fig 26-27. B Fig 25 4. Place the rear extension table ( F ) down onto the support brackets ( G ), lineup the threaded holes in the extension table with the elongated slots in the angle support brackets. Secure in place with the four short caphead bolts and washers, see fig 22-23-24. S Fig 26-27 Fig 22-23-24 B Caphead bolt & washer G 2. Find the rip fence assembly ( A ), lower the unit down over the front fence rail ( B ). Push down locking handle to lock the rip fence in place, see fig 28-29. Fig 28 F A 8 ASSEMBLY Fig 29 Fig 33 3. Locate the Aluminum sub fence ( D ). Position the sub fence against the rip fence assembly ( A ), lineup the ‘T’ slots in the fence ( D ) with the ‘T’ bolts in the rip fence and slide the sub fence on. Nip-up the three lift & shift handles on the rip fence ( A ) to secure the fence ( D ) in place, see 30-31. Fig 34 Fitting the Operating Handwheel Knobs Fig 30-31 Find the two handwheel knobs ( O ), 16mm spanner and 8mm Hex key ( R ). Lightly screw the handwheel knobs into the threaded hole in the operating wheels. Insert the Hex key into the caphead recess to the end of the knobs and while holding them in place nip-up the nuts with the spanner to secure in place, see 35-36. D ‘T’ Bolt Fig 35-36 O 8mm Hex key Mounting the Control Switch Box Lineup the two holes in the contol switch mounting bracket with the ones to the underside of the front fence rail ( B ), secure in position with the two small caphead scrrews and washers, see fig 32-33-34. 16mm Spanner Fig 32 9 Continues over... ASSEMBLY Fitting Flexible Hose Support Bracket Fig 40 1. Locate the flexible hose support bracket and two small caphead screws / washers ( L ), see fig 37. J K Fig 37 L Fig 41-42 Down 2. LIneup the holes in support bracket ( L ) with the two threaded holes to the side of the right hand extension table ( E ) and secure in place with the caphead screws / washers, see fig 38-39. Up Rise & Full operating wheel Fig 38-39 Locking knob E L 4. Loosen the two bolts that hold the riving knife clamping plate, see fig 43. Slide the riving knife ( K ) down between the plate and lightly tighten to hold the riving knife in place, see fig 44-45. Check that the tip of the knife has a clearance of 3-8mm between it and the blade and tighten. Replace the insert plate and countersink screws, see fig 46. Fig 43 Riving knive clamping plate Fitting the Riving Knife & Crown Guard 1. Locate the crown guard asssembly ( J )and the riving knife ( K ), see fig 40. Bolts 2. Release the locking knob to the centre of the rise & full operating wheel and raise the saw to its highest point by turning the wheel clockwise, see fig 41. 3. Remove the table insert plate by removing the five countersink screws, using the supplied 3mm Hex key. Place it and the screws safely to one side, see fig 42. 10 ASSEMBLY Fig 44-45 Fig 49 Fig 50 Fitting the Extraction Hose 1. Locate the long hose ( Q ) and the two remaining hose clips ( M ). K 2. Place a hose clip over one end of 63mm hose, slide the hose over the extraction outlet on the crown guard ( J ). Secure in place by lightly tightening the hose clip. Note: DO NOT OVERTIGHTEN, see fig 51. Fig 46 Fig 47 3. Fit the other end of the hose to the 63mm outlet on the 100mm spigot ( N ) to the rear of the machine as shown in fig 52. Insert the hose over the support bracket ( L ). Locking handle Slot 4. Replace both left & right side panels as explained on page 05. J Fig 51 Pin bolt Q M 5. Loosen the Locking handle on the crown guard ( J ). ntroduce the slot to the rear of the crown guard, see fig 47 down over the riving knife and insert the pin bolt into the curved slot in the rear of the riving knife, see fig 48-49. Lightly tighten the handle to secure the guard in place, see fig 50. Fig 48 Fig 52 N Curved slot 63mm Outlet 11 SET UP/ LEVELLING / FINE TUNING Always follow the step by step procedure in the instruction manual. A poorly set up saw will not perform to its full potential and may be dangerous to use. Fig 55-56 Three crucial things when setting up any table saw or panel saw•A ll extension tables are flat and level with the main saw table • All rip fences are in line with the blade • Sliding tables are set slightly above (0.5mm max) the level of the main saw table. In the set up of most machinery including tables saws, two tools that you will need to use are a 6” engineers square and a minimum 36”/910mm straight edge, without these toolbox essentials it is difficult to set the machine up accurately. 1. Firstly please ensure that the table saw is stable on the floor & doesnt rock or wobble, adjustment can be made via the feet located on the inside of the machine. You will need to remove both side panels to do this, see fig 53. Fig 53 4. Move the straight edge to the front of the saw then use a soft face clamp and a small piece of timber to align, the grub screws to level then tighten in place, see fig 57. Repeat the last process at the rear of the tables, see fig 58. Fig 57-58 Right Hand Extension Table 2. Once you have loosely bolted on the cast iron R/H extension table , align the front face to the main saw table,use a 36”/910mm straight edge or use the aluminium sub fence supplied with the saw, see fig 54. Fig 54 3. Place the straight edge in the middle of both tables across the seam, use a soft face mallet to tap the extension table up or down to align, then use the grub screws to level. Then tighten the central 2 bolts, see fig 55-56. 12 SET UP/ LEVELLING / FINE TUNING Rear Extension Table - Fig 62-63-64 5. Loosely Attached the rear extension table, then using the straight edge move the table up or down to align the main saw table, lock in place when aligned, see fig 59. Fig 59 6. The table should be set at the same height as the main saw table or very slightly lower (1mm max). This table should not be set higher than the saw table as it will prevent smooth feed through of timber. 7. Level the table insert to the main saw table by adjusting the grub screws on the underside of the table insert, see fig 60-61. Fig 65 Fence Fig 60-61 Table Bolt Rail Fence Rails & Fence 1. Ensure that the fence rail bracket is attached to the front of the tables. Slightly undo the hex cap screws underneath, measure the gap between the fence rail & table edge to ensure that this is the same end to end, see fig 62-63-64. 2. The mounting holes in the rear fence rail are slotted to allow movement up or down. Ensure that the bolts are loosened slightly then lift the rail up making sure that the fence is around 3-4mm above the saw table, see fig 65. 3-4mm 3. The T style rip fence has complete adjustment to align it to the saw blade / mitre fence slot & also to square it to the table. 4. Firstly slide the fence over to the mitre fence slot, align it then lock it off, see fig 66. If the fence seems out of line then simply adjust the left hand or right hand grub screws to align. You can also use these grub screws to take out any movement (wobble) in the fence, see fig 67. Fig 66-67 13 Continues over... SET UP/ LEVELLING / FINE TUNING 5. To square the fence to the table firstly slide the sub fence on at its high fence position, move it over towards the blade then with the fence locked check for square, see fig 68. 6. Adjustments are made by moving the grub screws on the top of the fence up or down, see fig 69. 7. Finally with the sub fence still in the high position slide the fence over until it makes very light contact with the blade. Then undo the 2 pozi screws to move the scale to read at zero, see fig 70. Fig 72 Fig 71 Stop collar Fig 68 Aligning / Adjusting the Riving Knife 1. It is important to ensure that the riving knife ( K ) is positioned correctly. The riving knife should be inline with the blade & between 3 - 8mm away from the edge of the blade, see fig 73-74. 2. To adjust the riving knife slightly undo the 2 bolts, this will allow up & down movement to gain the 3 - 8mm distance from the blade and will also allow for alignment adjusting via the four grub screws, see fig 75. Fig 69 Fig 73 3-8mm Clearance Fig 70 Fig 74 Riving knife inline with the blade Blade Fig 75 K Squaring the Blade to the Table 1. With the blade raised up to its highest point and not tilted, offer a square up to the right hand side of the blade plate avoiding the tips, see fig 71. 2. If the blade seems out of square a simple adjustment can be made by moving the stop collar located inside the machine on the threaded bar, see fig 72. Grub screws 14 Bolts GENERAL USE / OPERATION ALWAYS REMEMBER TO DISCONNECT THE POWER TO THE TABLE SAW WHEN MAKING REPAIRS OR ADJUSTING BLADES AND GUARDS. Fig 77 ALWAYS REMEMBER TO READ THROUGH THE MACHINE INSTRUCTIONS SUPPLIED. 1. Before you begin to use your Table saw, you will need to establish that the machine and the blade you are intending to use are suitable for the material you are going to be cutting. 3. Does the machine have enough capacity to cope with the size of material you are cutting? 2. Slide the sub fence forward so the end of the sub fence is just beyond the mid way point of the blade, see fig 78. 3. Adjust the blade height to match the timber thickness - top of the blade around 20 - 25mm above the timber, see fig 79. 4. Always ensure that the blade guard & riving knife are fitted. Fig 78-79 2. Check the sharpness of the blade. Is it too fine or too coarse? See Blade Selection Info on page…. 20 Rip Cuts - Cutting Down the Grain 1. P osition the rip fence to the right of the saw blade and set the rip fence for desired width of cut using the scale on the front rail, or measure the distance between the R/H side of the blade teeth and the fence, see fig 76-77. Fig 76 4. Standing to one side of the machine press the green button & allow the machine to run up to full speed, see fig 80. 5. Use the left hand to hold the timber against the fence. Use the right hand to push the material down & through the saw, see fig 81. 15 Continues over... GENERAL USE / OPERATION Fig 80-81 Fig 83-84 6. Use a push stick for all cuts that will bring your hands within 250mm of the blade. Bevel Cuts - 7. Position the right hand so it is NOT in direct line with the saw blade. Remove the hand holding the stock down as it approaches the saw blade and use a push stick to guide the last 300mm of cut through the blade, see fig 82. Fig 82 1. Make sure the timber is planed flat, square, and with parallel edges. Any warp, deviation from square, or an angled edge, can lead to blade burn or to the timber being lifted from the table and risking kickback. 2. Using the tilt handle on the side of the machine set the over to the required angle, the riving knife & blade guard will tilt with the blade, set the blade height to clear the timber by around 20-25mm, see fig 85. Fig 85 8. Always push the workpiece completely past the blade at the end of a cut to reduce the possibility of kickback, see fig 83. 9. When ripping long boards use a support roller before & after the cut to support the workpiece as it comes through the saw, see fig 84. 16 GENERAL USE / OPERATION Fig 86 Fig 89 3. Position the sub fence to the lower position & the rip fence to the desired cut width, see fig 86. 9. Always push the workpiece completely past the blade at the end of a cut to reduce the possibility of kickback, see fig 90. 4. Standing to one side of the machine press the green button & allow the machine to run up to full speed, see fig 87. Fig 90 Fig 87 6. Use the left hand to hold the timber against the fence. Use the right hand to push the material down & through the saw, see fig 88. 10. When ripping long boards use a support roller before & after the cut to support the workpiece as it comes through the saw, see fig 91. Fig 91 Fig 88 7. Use a push stick for all cuts that will bring your hands within 250mm of the blade. 8. Position the right hand so it is NOT in direct line with the saw blade. Remove the hand holding the stock down as it approaches the saw blade and use a push stick to guide the last 300mm of cut through the blade, see fig 89. 11. When the right hand side off cut is small a second push stick should be used to push the offcut through & past the blade. 17 Continues over... GENERAL USE / OPERATION Cross cuts - Cutting Across the Grain Fig 94-95 20-25mm above the timber Crosscuts are usually made with a medium to fine tooth blade. See Blade Selection Info on page…. 20 1. Make sure the saw guard and riving knife are in place when crosscutting. 2. Always use the mitre gauge or sliding table when crosscutting, do not make crosscuts free hand!, see fig 92. Fig 92-93 Fig 96 3. Most workers prefer to use the left table slot for the mitre gauge when crosscutting, see fig 93. 4. Adjust the blade height to match the timber thickness - top of the blade around 20 - 25mm above the timber, see fig 94. 5. Select the desired cutting angle & ensure that all is locked in place, see fig 95. 6 Hold the workpiece against the mitre fence with the left hand and use the right hand to advance the mitre gauge and material through the cut, see fig 96. 7. Provide support for any material which extends beyond the edge(s) of the saw table. 18 TROUBLESHOOTING Table saws & panel saws are relatively simple machines, with all machinery regular cleaning, servicing & the use of extraction (all preventative maintenance) are essential to get the best from your saw. ‘My table saw won’t cut straight” • Check that your fence is in line with the blade, also check that the blade is square to the table. Information on how to correct this will be found in this instruction manual. • • • • • • • • “My saw slows down when cutting” “Why am I getting a lot of splintering along the cut edge” The blade is probably blunt or too coarse, if a smoother cleaner cut is required then change the blade for one with more teeth. Lowering the blade height to about 25mm above the timber can also help. Slow your feed speed down & check that the fence is in line with the blade as back cutting can occur. “Excessive vibration ” • Blade may be blunt or too fine for the thickness of material. verfeeding, slow down the feed through O the blade. • • • • Drive belt may be loose or worn. Check that your fence is in line with the blade. Ensure that the saw is not running on a long extension lead. Motor capacitor may be faulty. The blade may be damaged, check the blade , replace if any missing teeth or burn marks are seen. Check that the blade is fitted correctly. Check fence to blade alignment, adjust as necessary. The saw is not positioned on a flat stable floor surface. The timber may not stable and sat flat on the table, you may be getting board bounce, choose a flatter surface. MAINTENANCE DISCONNECT THE MACHINE FROM THE MAINS SUPPLY. • Check blades for ware or damage • Clean inside the machine, slides, threads, Preventative maintenance is crucial if you want your machine to perform to its full potential. I.E. Use good quality resin free sharp blades; this will greatly cut down the load put on to motors, drive belts and gears. Use adequate extraction, this will help keep the machines internal mechanisms clean and also help keep your work area clear from dust and shavings. gears and remove all off cuts & debris. • Lubricate slides, threads, gears • Check drive belt for ware or damage Periodically or after quite heavy use it is recommended • Clean guards & check for damage that the following maintenance be made to the table saw. • Check alignment of fences & guides • Clean & wax cast iron tables 19 Continues over... MAINTENANCE Fig 99 Blade Selection/Info ALWAYS ensure that you are using the correct blade dimensions, the blade diameter, the bore size & the kerf (cutting width) match the blade that is supplied with the table saw from new. Coarse Blade Low tooth count, around 20 - 30 teeth, ideal for table saws to do ripping cuts down the grain where a smooth finish is not so important, see fig 97. Fig 97 Blade Change DISCONNECT THE MACHINE FROM THE MAINS SUPPLY. Removing Blade 1. Undo the six screws and remove the table insert, then wind the blade up to its highest point, see fig 100. Fig 100 General Purpose Blade Medium tooth count, around 40 - 50 teeth, where a user may cut a wide range of timber both natural & man made board & doesn’t want to change blades too often, see fig 98. Fig 98 2. Insert the tommy bar into the hole on the inner spindle collar then use the 22mm spanner to undo the blade nut THIS IS A LEFT HAND THREAD, THE NUT WILL TURN THE SAME DIRECTION AS THE BLADE ROTATION, see fig 101-102. Fig 101 Fine Tooth Blade High tooth count, around 60 - 100 teeth suited to cutting finer delicate thinner timbers where a smooth finish & limited breakout is required. Also the ideal blade for cutting faced man made boards, see fig 99. NOTE: NOT RECOMMENDED FOR RIP CUTS! 22mm Spanner 20 Tommy bar MAINTENANCE Fig 102 Fig 105 Outer clamping flange Inner clamping flange Left handed thread Nut 3. Remove the nut, the outer clamping flange and the 3. Refit the outer clamping flange & retighten the blade blade. Take care not to lose the blade locating bush, also clamping nut. Replace the table insert, see fig 107. take care not to damage the blade during removal, see fig 103. 4. Before powering up the machine rotate the blade by hand to ensure all is running true, also ensure that the blade guard is repositioned. Fig 103 5. The riving knife will not need adjusting providing the same, correct blade has been fitted. Fig 106 NOTE: Ensure the blade is seated over the locating bush Blade locating bush Refitting the Blade 1. Before fitting the blade ensure that the inner & outer clamping flanges & blade plate are clean & free from wood dust, see fig 104-105. 2. Slide the blade centering bush onto the spindle, then slide the blade onto the spindle ensuring that the blade is positioned over the blade locating bush, see fig 106. Fig 107 Fig 104 21 OPTIONAL ACCESSORIES Dado Blade Set 3 This 204mm diameter Dado Blade Set comprises 2 x 24 tooth TCT outer blades, 6 inner chipper blades and 4 spacers. The chippers and spacers fit between the outer TCT blades. Simply select the inner chippers and spacers required to cut the width of slot required. The outer blades are 3.2mm. The inner chippers are 4 x 3.0mm, 1 x 2.2mm and 1 x 1.5mm. The spacers are 2 x 0.4mm and 2 x 0.3mm. NOTE: THE DADO HEAD SHOULD NEVER BE USED TO CUT THROUGH THE TIMBER, IT IS FOR MACHINING GROOVES USING LIGHT, MULTIPLE CUTS! Layout the TCT outer blades, chipper blades & the spacers. THE DADO BLADE CAN CUT GROOVES UP TO A MAXIMUM 18MM IN WIDTH DEPENDING ON CAPACITY OF THE MACHINE BEING USED! Tooth pointing inward DISCONNECT THE MACHINE FROM THE MAINS SUPPLY BEFORE CONTINUING! 1 4 Inner blade Outer blade Make sure the teeth of the inner and outer blades are facing inward. 5 Find a scrap piece of timber the thickness of the cut as a guide. Place the inner blade against the timber and start stacking the chipper blades on top. Make sure the teeth are spaced equally and pointing foward. Remove the standard blade and riving knife and place safely away. 6 2 Correct! 22 OPTIONAL ACCESSORIES 7 11 Wrong! DO NOT OVERLAP the blade teeth. Use the supplied spacers between the blades to make small adjustments in the height. 8 12 Outer TCT blade Correct! The teeth equally spaced and pointing forward. 9 Wrong! The teeth not equally spaced and not pointing forward. Place the outer TCT blade on top and check the tooth is the same depth as the timber. If the blade is too high/low, rearrange the chipper blades and spacers until the correct depth is reached. 10 13 Chipper blade Outer TCT blade 23 OPTIONAL ACCESSORIES 14 17 Inner TCT blade Spacer 18 Turn the ‘Dado’ blade assembly over so the inner TCT blade is on top in preparation for installation. 15 19 Plate flange Outer plate flange/nut Clean the inner and outer plate flanges Make sure the plate flange slots over the nut’s recess. 20 16 Teeth forward 21 Slide the inner TCT blade over the shaft and up against the inner plate flange. Make sure the teeth are pointing forward. Mount each blade and spacers in turn onto the shaft. Important note: make sure to space the blade teeth equally as shown in fig 17. Once all the blades are on, replace the outer flange/nut and resecure. Replace the insert plate. 24 OPTIONAL ACCESSORIES Sliding Table Accessory Overhead Crown Guard Accessory 25 EXPLODED DIAGRAM/PARTS LISTS Diagram/Parts List A 26 EXPLODED DIAGRAM/PARTS LISTS No. Description QTY 40 Hex.Nut M12 4 1 Mitre Gauge Assembly 1 41 Tie-In B 1 2 Main Worktable 1 42 Tie-In A 1 3 Washer 8Mm 50 43 Dust Collection Hose 1 4 Spring Washer 8Mm 10 44 Supporting Bracket A,Rear Extension Table 1 5 Extension Table 1 45 Supporting Bracket B,Rear Extension Table 1 6 Rear Fence Rail 1 46 Semi-Round Key 3X16 2 7 Front Fence Rail 1 47 Big Washer 4 2 8 End Cap,Front Fence Rail 2 48 Cross Recessed Pan Head Screw M4X8 2 9 Support Bracket,Fence Rail 1 49 Hex.Socket Cap Head Screw M8X12 4 10 Main Switch 1 50 Hex.Socket Cap Head Screw M6X20 15 11 Mounting Bracket,Switch 1 51 Hex.Nut M8 24 12 Hex.Socket Cap Head Screw M6X10 6 52 Cross Recessed Pan Head Screw M5X20 4 13 Hex.Socket Countersunk Head M5X15 5 53 Hex.Nut M5 4 14 Hex.Socket Cap Head Screw M8X25 4 54 Washer 6 21 15 Hex.Bolt M8X16 12 55 Column Frame,Machine Body 1 16 Hex.Socket Cap Head Screw M5X12 2 56 Right Panel,Machine Body 1 17 Scale 1 57 Rear Panel,Machine Body 1 18 Dust Hose Support 1 58 Left Panel,Machine Body 1 19 Rear Extension Table 1 59 Screw Rod 4 20 Rear Trunnion 1 60 Leveling Foot 2 21 Fron Trunnion 1 61 Connecting Board,Machine Body 2 22 Tilt Leadscrew Nut 1 62 Hex.Socket Set Screw M6X6 2 23 Circlips For Shaft 1 63 Angle Scale 1 24 Tilt Leadscrew 1 64 Wave Washer 21 1 25 Tilt Limit Block 1 65 1 26 Mounting Support 1 Hex.Socket Cap Head Screw M10X80(Half Screw) 27 Stopping Hoop 1 66 Washer 5 14 28 Handwheel 1 67 Hex.Socket Cap Head Screw M5X25 8 29 Table Insert 1 68 Cable Gland M20 1 30 Retainer Ring 2 69 Knob 1 31 Hex.Socket Set Screw M8X6 6 70 Front Panel,Machine Body 1 32 Locking Nail 1 71 Rip Fence Assembly 1 33 Step Screw 4 72 Hex.Socket Set Screw M8X10 4 34 Big Washer 12 8 73 Hex.Socket Cap Head Screw M8X16 22 35 Mechanism Assembly 1 74 Hex.Socket Cap Head Screw M8X20 4 36 Blade Guard 1 75 Right [Anel Section,Machine Body 1 37 Ratchet Lever 1 76 Screw 1 38 Locking Bolt,Blade Guard 1 77 Push Stick 1 39 Hex.Bolt M8X25 4 78 Thrust Washer 30X17X0.8 2 27 EXPLODED DIAGRAM/PARTS LISTS Diagram/Parts List B No. Description QTY 22 Thin Nut M20X1.5 4 1 Driving Pulley B 1 23 Stopping Hoop B 1 2 Shaft Pulley 1 24 Locking Nail B 1 3 Shaft Base 1 25 Lifting Worm Wheel 1 4 Arbor Shaft Sleeve 1 26 Press Board,Riving Knife 1 5 Arbor Shaft Ending Bushing 1 27 Hex.Socket Countersunk Head M8X20 1 6 Blade Shaft 1 28 Pulling Rod Shaft 1 7 Hex.Socket Cap Head Screw M8X25 3 29 Spring Washer 6 2 8 Washer 10 1 30 Hex.Bol M8X25 2 9 Hex.Socket Cap Head Screw M6X12(Left) 1 31 Spring Washer 8 5 10 Hex.Socket Cap Head Screw M10X30 1 32 Washer 8 5 11 Driving Belt 1 33 Hex.Socket Cap Head Screw M6X12 3 12 Saw Blade 1 34 Hex.Socket Set Screw M8X6 6 13 Mounting Base 1 35 Hex.Bolt M8X16 2 14 Connection Rod Of Riving Knife Bracket 1 36 Cross Recessed Pan Head Screw M5X8 2 15 Riving Knife Bracket 1 37 Hex.Socket Cap Head Screw M8X16 1 16 Semi-Round Key 3X16 2 38 Spring Pin 6X10 2 17 Connection Seat 1 39 Key 5X20 1 18 Lifting Worm 1 40 Arbor Flange 1 19 Washer 6 5 41 Arbor Shaft Bushing A 1 20 Riving Knife 1 42 6004 Bearing 3 21 Shaft 1 43 Arbor Shaft Bushing B 1 28 EXPLODED DIAGRAM/PARTS LISTS 44 Thrust Washer 30X17X0.8 2 54 Hex.Socket Set Screw M6X6 3 45 Hex.Nut M8 3 55 Handle 1 46 Hex.Socket Flat Head Set Screw M8X6 2 56 Pointer Seat 2 47 Motor 1 57 Pointer B 1 48 Torsion Spring 1 58 Hex.Socket Cap Head Screw M10X80 1 49 Dust Collection Cover 1 59 Thin Nut M16X2 (Left) 1 50 Dust Outlet,Dust Collection Cover 1 60 Variable Diameter Sleeve 1 51 Cross Recessed Pan Head Screw M5X10 3 61 Hex.Nut M6 2 52 Hex.Bolt M8X40 1 62 Hex.Self-Locking Nut M8 1 53 Handwheel 1 63 Key 8X25 1 QTY 14 Hex.Self-Locking M6 2 Diagram/Parts List C No. Description 1 Pad 2 15 Hex.Socket Set Screw M10X10 2 2 Sling Rail Carrier 1 16 Rip Fence 1 3 Locking Block 1 17 Hex.Socket Cap Head Screw M6X12 2 4 Locking Cam 1 18 Hex.Nut M6 2 5 Nylon Screw 3 19 Semi-Round Step Bolt M6X35 1 6 Fence Lock Knob 1 20 Semi-Round Step Bolt M8X35 1 7 Pointer 1 21 Hex.Self-Locking M8 1 8 Spring 1 22 Washer 5 2 9 Bearing 61900 1 23 Cross Recessed Pan Head Screw M5X10 2 10 Bearing Bushing 1 24 Spring Pin 5X32 1 11 Bearing Support 1 25 T-Bolt 4 12 Washer 6 2 26 Ratchet Lever 4 13 Hex.Socket Countersunk Screw M6X22 1 27 Big Washer 6 4 29 Continues over... EXPLODED DIAGRAM/PARTS LISTS Diagram/Parts List D 30 No. Description QTY 1 Mitre Gauge Guide Rod 1 2 Cross Recessed Countersunk Screw 1 3 Rail Washer 1 4 Hexagon Socket Set Screws M6X12 3 5 Hex.Socket Pan Head Screw M6X20 1 6 Hex.Socket Set Screw M6X6 2 7 Mitre Gauge Base 1 8 Scale 1 9 Stop Pin 1 10 Block Indicator 1 11 Spring Washer 5Mm 2 12 Stop Spring 1 13 Hex.Socket Cap Head Bolt M5X12 2 14 Mitre Gauge Knob 1 15 Stopping Knob 1 16 Self-Locking Nut M6 1 17 Washer 6Mm 1 18 Stop Pin 1 WIRING DIAGRAM 31 DECLARATION OF CONFORMITY 32 DECLARATION OF CONFORMITY 33 34 35 The Axminster guarantee Buy with confidence from Axminster! So sure are we of the quality, we cover all parts and labour free of charge for three years! For more information visit axminstertools.com/3years The packaging is suitable for recycling. Please dispose of it in a responsible manner. EU Countries Only Do not dispose of electric tools together with household waste material. By law they must be collected and recycled separately. Axminster Tools, Axminster Devon EX13 5PH axminstertools.com
advertisement
Key Features
- Cast iron table
- Adjustable fences
- Dado blade set
- Riving knife
- Dust extraction port
Related manuals
Frequently Answers and Questions
How do I adjust the riving knife on the AP254SB?
Slightly undo the two bolts on the riving knife clamping plate, then slide the riving knife up or down to achieve the desired clearance (3-8mm) from the blade. Use the four grub screws for fine alignment. Tighten the bolts securely.
What are the different blade types available for the AP254SB and when should I use them?
The manual describes three types: Coarse Blade (20-30 teeth) for ripping cuts, General Purpose Blade (40-50 teeth) for a range of timber, and Fine Tooth Blade (60-100 teeth) for smoother cuts on finer timbers. You should select the blade based on the material you're cutting and the desired finish.
Why is the blade nut on the AP254SB left-handed?
This is a safety feature. The nut is designed to turn the same direction as the blade rotation so that it tightens when the blade is turning clockwise.