advertisement
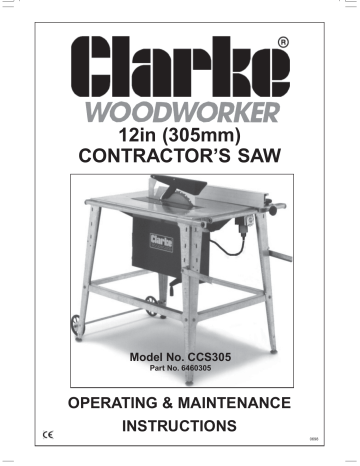
12in (305mm)
CONTRACTOR’S SAW
Model No. CCS305
Part No. 6460305
OPERATING & MAINTENANCE
INSTRUCTIONS
1
0698
Thank you for purchasing this CLARKE 12” (305mm) Contractors Saw, which is designed for light industrial use.
Before operating the machine, please read this booklet thoroughly and carefully follow the instructions. In doing so you will ensure the safety of yourself and that of others around you, and you can look forward to the Contractor’s Saw giving you long and satisfactory service.
GUARANTEE
This CLARKE product is guaranteed against faulty manufacture for a period of 12 months from the date of purchase. Please keep your receipt as proof of purchase.
This guarantee is invalid if the product is found to have been abused or tampered with in any way, or not used for the purpose for which it was intended.
Faulty goods should be returned to their place of purchase, no product can be returned to us without prior permission. This guarantee does not affect your statutory rights.
CONTENTS Page
Safety Precautions .................................................................. 3
Additional Precautions for Workshop Saws ......................... 5
Features ................................................................................... 6
Unpacking ............................................................................... 7
Assembly .................................................................................. 8
Electrical Connections .......................................................... 15
Adjustments ........................................................................... 16
Operation - Rip Sawing ....................................................... 17
Cross Cutting .................................................... 18
Maintenance ......................................................................... 19
Blade Renewal ....................................................................... 20
Specifications ......................................................................... 20
Parts List ................................................................................... 21
Parts & Servicing .................................................................... 21
Parts Diagram ........................................................................ 22
2
SAFETY PRECAUTIONS
GENERAL SAFETY RULES FOR OPERATING MACHINERY
CAUTION:
As with all machinery, there are certain hazards involved with their operation and use. Exercising respect and caution will considerably lessen the risk of personal injury. However, if normal safety precautions are overlooked or ignored, personal injury to the operator or damage to property may result.
• READ and BECOME FAMILIAR with the entire operating manual. Learn the machine’s applications and limitations as well as the specific potential hazards peculiar to it.
• EARTH ALL MACHINES. If the machine is equipped with a three-pin plug, it should be plugged into a three-pin electrical socket. Never remove the earth pin.
• ALWAYS ensure that ADEQUATE LIGHTING is available. A minimum intensity of
300 lux should be provided. Ensure that lighting is placed so that you will not be working in your own shadow.
• CHECK for DAMAGE. Before using the machine, any damaged part, such as a guard etc., should be checked to ensure that it will operate properly, and perform its intended function. Check for alignment of moving parts, breakage of parts, mountings and any other condition that may affect the machine’s operation. Any damage should be properly repaired or the part replaced. If in doubt, DO NOT USE the machine. Consult your local dealer.
• DISCONNECT the MACHINE from the power supply before servicing and when changing accessories such as blades, etc.
• KEEP GUARDS in place and in working order.
• ALWAYS WEAR SAFETY GOGGLES, manufactured to the latest European Safety
Standards. Also use face or dust mask if cutting operation is dusty.
Everyday eyeglasses do not have impact resistant lenses, they are NOT safety glasses.
• KEEP WORK AREA CLEAN. Cluttered areas and benches invite accidents.
• ALWAYS WEAR EAR PROTECTORS/DEFENDERS.
• DON’T FORCE the machine, it will do a better and safer job at the rate for which it was designed.
• REMOVE ADJUSTING KEYS AND WRENCHES. Form the habit of checking to see that keys and adjusting wrenches are removed from the machine before switching on.
3
• DRUGS, ALCOHOL, MEDICATION. Do not operate machine while under the influence of drugs, alcohol or any medication.
• USE RECOMMENDED ACCESSORIES. The use of improper accessories could be hazardous.
• NEVER LEAVE MACHINE RUNNING UNATTENDED. Turn power OFF. Do not leave machine until it comes to a complete stop.
• ALWAYS REMOVE PLUG from electrical outlet when adjusting, changing parts, or working on machine.
• AVOID DANGEROUS ENVIRONMENT. Don’t use power machines in damp or wet locations or expose them to rain. Keep your work area well illuminated.
DO NOT USE in explosive atmosphere (around paint, flammable liquids etc.).
• KEEP CHILDREN AWAY. All visitors should be kept a safe distance from the work area, especially whilst operating the unit.
• MAINTAIN MACHINE IN TOP CONDITION. Keep tools sharp and clean for the best and safest performance. Follow maintenance instructions.
• DON’T OVERREACH. Keep your proper footing and balance at all times. For best footing, wear rubber soled footwear. Keep floor clear of oil, scrap wood, etc.
• WEAR PROPER APPAREL. Loose clothing or jewellery may get caught in moving parts. Wear protective hair covering to contain long hair.
• MAKE WORKSHOP CHILDPROOF. Cover the saw adequately when not in use, to prevent children from damaging themselves by tampering with it.
• NEVER STAND ON THE MACHINE. Serious injury could occur if the machine is tipped or if a cutting tool is accidentally contacted. Do not store materials above or near a machine, such that it is necessary to stand on the machine to reach them.
• HANDLE WITH EXTREME CARE. Whenever transporting or installing machinery, and always use a lifting device.
• BE AWARE that many accidents are caused by carelessness due to familiarity.
ALWAYS concentrate on the job in hand, no matter how trivial it may seem.
4
ADDITIONAL SAFETY INSTRUCTIONS for WORKSHOP SAWS
• Wear safety goggles as protection against flying wood chips and saw dust. In many cases, a full face shield is even better protection. A dust mask is also recommended to keep saw dust out of your lungs.
• This saw is designed for light industrial use only.
• Clear the work table of all objects except the workpiece (tools, scraps, rulers etc.) before turning on the saw.
• Keep your fingers well away from the blade, use a push stick as you near the end of the cut.
• Switch off the saw and make sure the blade has come to a complete stop before clearing sawdust or off-cuts from the table.
• Make sure there are no nails or foreign objects in the part of the workpiece to be sawn.
• Set up the machine and make all adjustments with the power OFF and disconnected from the supply.
• DO NOT operate the machine with the guards removed. They must all be in place and securely fastened when performing any operation.
• Use ONLY approved replacement saw blades. Contact your local CLARKE dealer for advice. The use of inferior blades will increase the risk of injury.
• DO NOT saw any material that does not have a flat surface on which to bear.
• This machine is designed for cutting wood. DO NOT use for cutting metal or plastic.
• DO NOT attempt to cut round or tubular work (logs etc.).
• Do not cut pieces of material which are too small to be guided by hand.
• Do not feed the workpiece through the blade too quickly, hold material firmly and feed into blade at a moderate speed.
• When cutting a large piece of material, support it at the height of the table with supports or use an assistant.
• Never let go of a workpiece, ALWAYS maintain control.
• Never touch, or hold on to, a piece that has been cut off whilst the power is on or the blade is rotating.
• Ensure the surface on which the saw stands is firm, solid and non-slip.
• DO NOT use the saw for non-through-cut operations. The Upper Blade Guard
MUST be in place at all times.
5
FEATURES
The Contractor’s Saw may be used for rip cutting or cross cutting timber up to
70mm (2¾”) in depth.
A double height Rip Fence is provided and may be secured at any desired position for quick and accurate rip sawing. The max. width obtainable, using the rip fence is
280mm (11”).
For speed and accuracy, a guide is also provided for cross cutting. It is adjustable so that mitres of up to 45° may be created.
The Upper Blade Guard is hinged to allow it to ride over the timber as the timber moves over the blade.
IMPORTANT: The Blade Guard must always be in place.
The Lower Blade Guard comprises a box, on to which is mounted the motor and saw blade. A hinged cover gives access to the blade and other components.
IMPORTANT: This cover must always be in place and secure.
The box is secured by two pivot bolts and two large (Saw Blade) Tilt Adjuster knobs.
Slackening these knobs allows the complete box, with motor and blade, to move about the pivot bolts so that the blade may tilt by up to 45° - in one direction. It is then secured in position by tightening the same adjuster knobs.
Extending from the bottom of the box is a handle, used for raising and lowering the blade and is explained under ‘Operation’.
At one end of the box, (the rear end), a 48mm (1 7 /
8
”) dia hole is provided for use as a dust extraction outlet. If required it can be connected to a dust extraction device which will provide fast and efficient removal of sawdust. The dust extractor may be used continuously or intermittently depending upon your requirements.
Construction of the base unit is in heavy, corrosion resistant, galvanised steel and is maintenance free. The machine is nevertheless designed for indoor use. Should it be used outdoors, every attempt should be made to ensure it is protected from the elements. Do not use in wet conditions.
6
UNPACKING
Unpack the shipping carton in a clean flat area, so that you have ample room to work, and lay out all components neatly so that they may be clearly identified.
Check to ensure that no damage was suffered in transit. Should there be any damage, please contact your Clarke dealer immediately.
Check the parts, referring to fig.1 and the list which follows: Fig. 1
1
1.
Saw Blade
2.
Riving Knife
3.
Upper Blade Guard
4.
Rip Fence
5.
Rip Fence Support
6.
Quadrant
7.
Long Guide Bar (for cross cutting)
8.
Short Guide Bar (for ripping)
9.
Corner Support - 2 pcs
10.
Table Insert
11.
Table Top
12.
Leg - 4 pcs
13.
Short Strut - 2 pcs
14. Long Strut - 2 pcs
15. Handle - 2 pcs
16. Motor Assy.( incl. Switch Box assy).
17. Switch Box Bracket
18. Trailing Socket
19. Axle
20. Wheel - 2 pcs
21. Axle Bracket - 2 pcs
22. Lower Blade Guard Box Assy
23. Push Stick
A.
5 Scalloped Knobs ( 3 female - small, 2 male - large), 1 Winged Knob, 4 Feet and
1 Handle assy. (contained in one bag)
In addition to the foregoing list, the packing carton contains a bag with all necessary fixing screws, nuts, collars, and washers. Please refer to the parts list for details.
7
ASSEMBLY
A. Lower Blade Guard Box
1.
Place the table face down on a sheet of cardboard (or similar).
2.
Between the two side brackets lies a hinged flap. Lift and rotate it against spring pressure through 180 O so that it lies flat against the underside of the table. Hold it in this position temporarily with a suitable weight.
3.
Invert the lower blade guard box, and lower it into place between the two side brackets as shown in fig.2, ensuring the hinged door of the box faces the hinged flap.
Hinged
Flap with
B
Locate the box with two large scalloped knobs
(item A), one each side, through the slotted holes inthe side brackets as shown. Screw the knobs weight
Self locking nut home but do not tighten them fully.
These knobs are referred to as the Blade Tilt Adjuster Knobs.
C
Lower Blade
Guard Box
Fig. 2
Pivot Bolt Hole
Side Bracket
A
4.
Manoeuvre the box so that the pivot bolt holes (see fig 2), line up with the holes in the side brackets and insert the special shouldered bolts (item B), from inside the box.
Screw on the self locking nuts, ensuring the shoulders ofhe bolts are sitting snugly in the holes in both the box AND the side bracket. Tighten the self locking nuts, but only sufficiently so as to allow the box to pivot smoothly about the shouldered bolts, and then secure the box firmly by tightening the Blade Tilt Adjuster Knobs
(A).
B. Motor Assembly and Attachments
5.
Insert the motor shaft through the hole in the Blade Guard Box. The plastic cable housing on the motor should be facing you. i.e. when the table is on its feet, the plastic cable box will face downwards.
Secure the motor assembly to the moveable plate, within the box, using four
M5 x 25mm screws with flat and spring washers. Tighten the screws to no more than 12 lbf ft.
✓
Fig 2A
✗
NOTE: It is strongly advised that assistance be used to support the weight of the motor, when tightening the screws, to avoid the possibility of it tilting.
8
IMPORTANT: Make absolutely sure that the motors’ end plate sits snugly in the hole in the Blade Guard Box, as shown in Fig2A. The register on the end plate must be completely through the hole.
6.
Attach the Blade Height Adjuster Handle (fig.2 item C), to the adjuster bolt.
Line up the hole in the handle with that in the bolt, insert the roll pin provided and tap it into place.
C. Rip Fence and Cross Cut Guide Bars, and Legs
7.
Lay the Rip Fence and Cross Cut Guide Bars, together with the two Corner
Supports, alongside the table as shown in fig. 3. The rounded ends of the corner supports should be attached to the guide brackets, not to the table.
Fig.3
Corner Support
(R
Gu ip F
(sh ort)
Ba r e)
Corner Support
(Cross Cut) Guide Bar (long)
With a leg placed in the inside of the corner of the table, insert the screws through the brackets, table top and leg, using the flat and spring washers supplied. (i.e. a flat washer next to the screw head, and a flat washer followed by a spring washer with the nut).
Use the M5 x 20mm screws where the thickness of the guide brackets is to be taken into account, and M5 x 15mm screws otherwise.
Do not tighten the nuts at this stage - leave them finger tight. The guide brackets and all four legs should now be loosely bolted in place.
D. Legs and Struts
8.
Attach the long and short leg struts to the legs ensuring the screws are entered in the elongated holes in the struts, with the long strut on top of the short one, and the open angle of the strut facing you, (i.e. will normally be facing downwards).
Ensure flat and spring washers are used, as detailed previously.
9
9.
Attach a rubber foot to each leg, placing a flat washer either side of the hole in the leg. Screw on the nut and tighten securely.
E. Wheels and Axle Assy
10. In order to install the wheels and axle assembly, first attach all components to the axle as follows:
Refer to fig 4, and on to each end in turn, thread on:
1.
a wheel
2.
a 10mm flat washer
3.
the axle bracket, with the angle portion facing outwards as shown, in fig. 4, and the sloping edge downwards towards the foot - as shown
in Fig 4A
4.
an 8mm flat washer
5.
an 8mm spring washer
6.
an M8 nut, which may be tightened securely.
Fig.4
Angle portion facing outwards
Axle
Fig.4A
Foot
A
B C D
F
E
A
C
Sloping edge of bracket facing down towards the foot
Attach the brackets to the legs, (on the opposite end of the table to that carrying the short guide bar), with the screws, flat and spring washers provided.
11. With assistance, turn the table to an upright position and rock it vigorously,to ensure it is completely stable and that no part in under stress. When satisfied, tighten all nuts systematically starting at the top and working down.
It is recommended that you use gloves during this operation as protection against the sharp edges that you may encounter.
NOTE: a. Before tightening the screws securing the guide bar brackets, pull the brackets apart as far as possible on their elongated holes. (indicated by the arrows in fig
3) b. For future reference, the FRONT of the table is that end carrying the short guide bar.
10
F.
Switch Box
12. Attach the switch box to its bracket using the four 15mm self tapping screws provided, and attach the bracket to the Table, in the manner shown in Fig 5.
Use two 5M x 15mm screws,with nuts, flat and spring washers provided.
Fig.5
G. Lifting Handles
13. Attach the lifting handles (two channel sections), to the sides of the
L H Front and R H Front legs,as shown in fig 6, ensuring flat washers and self locking nuts are used with the handle pivot screws. Do not over tighten the lock nut but allow the handle to pivot smoothly.
With the Handle Stops, use flat washers at the screw heads,and flat and spring washers with the securing nuts.
Handle StopCollar Fig.6
Self Locking Nut Collar Handle
H. Riving Knife
14. Raise the spring loaded hinged flap beneath the table and open the door to the lower blade guard box.
Slide the Riving Knife through the slot in the table insert, and locate it on the two studs on the upper left of the plate carrying the motor assembly, shown in fig 7.
Thread on the 8mm flat washers and M8 self locking nuts, but do not fully tighten them at this stage.
I.
Saw Blade
15. To install the saw blade, it is necessary to remove the Outer Flange and the
Blade Securing Bolt from the motor shaft. To do this, hold the motor shaft, using a 17mm spanner on the flats milled on the shaft, and unscrew the blade securing bolt noting that it has a LEFT HAND THREAD.
Locate the saw blade on the shaft, ensuring the blade teeth face down at the front of the table.
Replace the outer flange, ensuring the flat in its bore engages correctly with the flat on the motor shaft.
Finally, replace the blade securing bolt, with its spring washer, and tighten it to approx. 25lbf ft whilst holding the shaft with a 17mm spanner.
11
Upper Blade Guard Mounting
Riving Knife
Fig. 7
Outer Flange
Lower Blade
Guard Box
Blade Securing
Bolt
Blade Height Adjuster
WARNING
Take great care when handling the saw blade.
Blade teeth are extremely sharp, and carelessness could cause severe injury.
16. With the saw blade in place, the Riving Knife must be adjusted to ensure the correct clearance is set between it and the saw blade. It is important that this adjustment is maintained at all times and must be checked regularly.
Adjust the riving knife on its mounting studs so that a gap of 3mm is set between it and the saw blade around the complete length of the riving knife, as shown in fig.8.
3mm
3mm
✓
12
Fig.8
3mm
3mm ✗ ✗
In addition, the riving knife MUST be completely in line with the saw blade and not bent in any way.
It may be necessary to place shim washers (not supplied),on to the Riving Knife mounting studs, between the Riving Knife and the Blade Guard Box, in order to ensure the Riving Knife is correctly in line with the Saw Blade.
When satisfied,tighten the two self locking nuts to firmly secure the riving nife.
J.
Upper Blade Guard
18. Attach the Upper Blade Guard, with its’ single screw, to its mounting on top of the Riving Knife (shown in fig. 7), ensuring the self locking nut sits snugly in the recess in the blade guard. Do not over tighten the nut as the blade guard must pivot and drop easily under its own weight.
K. Rip Fence and Quadrant
19. The Rip Fence may be used in either high or low position and is shown in fig. 9.
With the fence in its lower position (as shown), the work will bear against face
‘A’and in its higher position, face ‘B’.
Rip Fence
20mm Screw
RIP FENCE - IN LOW POSITION
Fig. 9.
Scalloped Hand Wheel
A
Stud Quadrant
B
Scalloped Hand Wheel
Peg
Rip Fence Support
Rip Fence Support Securing Knob
Pointer
Lay the fence on the table and slide two M8 x20mm screws into the channel in the side of the fence as shown.
Position the screws, so that they line up with the holes in the side of the quadrant, and screw on a large scalloped hand wheel to each screw. This secures the quadrant to the rip fence.
A channel section - the Rip Fence Support, is then attached to the rip fence and quadrant sub assembly. This support connects the complete assembly to either guide bar, depending upon whether you are ripping or cross cutting.
13
It is attached by pushing the peg and the stud, on the top surface of the
Support, through the holes in the Quadrant, as shown, and screwing a Scalloped
Handwheel on to the stud. A Winged knob is screwed into thethreaded hole in the side of the Support and is used to secure the complete Rip Fence assembly to the Guide Bar. This is referrred to as the Rip Fence Support Securing Knob.
To set the Quadrant pointer to zero, slacken off the three hand wheels,
a) two securing the Rip Fence to the Quadrant, and b) one securing the Quadrant to the Rip Fence Support.
Raise the Upper Blade Guard and move the Rip Fence so that it lies alongside the saw blade. Tighten all three hand wheels once again when the Rip Fence is completely parallel to the saw blade. Finally, secure the complete Rip
Fence assembly to the Guide Bar with the Rip Fence Support Securing Knob.
NOTE: If the Rip Fence moves at all, when the Rip Fence Support Securing
Knob is tightened, throwing the Rip Fence out of parallel with the blade, slacken off the single hand wheel that secures the Quadrant to the Rip Fence Support, and move the Rip Fence with the Quadrant to compensate for this movement.
Tighten the hand wheel again when completed.
Once satisfied that the Rip Fence is completely parallel to the saw blade, check the position of the pointer. If necessary, slacken off the pointer securing screw, zero the pointer and re-tighten the screw.
Your Contractors Saw is now fully assembled.
Before use however, it is important to ensure that all electrical connections and various adjustments are correctly made in accordance with the instructions in the following pages.
14
ELECTRICAL CONNECTIONS
WARNING! THIS APPLIANCE MUST BE EARTHED
The Switch Box is provided with a ‘continental’ type trailing socket with an earth pin, to which a 3-Cord mains power cable should be connected. The minimum cross section of the conductors in the cable should be 1.5mm
2 and the cable type should be H05VV-F (minimum). The conductor insulation in the cable should be coloured:
Green&Yellow, Blue, and Brown and should be connected to the trailing socket according to the diagram below.
The Green/Yellow (EARTH) conductor MUST be connected to the single pin, with the Brown and Blue conductors connected to the terminals indicated.
To disassemble the unit, remove single screw in outer rubber shroud and prise out the socket assy.
Blue conductor
Cable clamp
EARTH pin EARTH pin
Yellow/Green conductor
(EARTH)
Brown conductor
Ensure cable clamp is tightened before plug is assembled
Ensure the cable clamp is secure and clamps the outer shroud, not the cords.
The other end of the power cable should be connected to a standard 230 Volt
(50Hz) electrical supply, either directly through a suitably fused isolator switch, or through a normal plug and socket arrangement using an approved 13amp BS
1363 plug.
If a standard 13 amp plug is used,the conductors in the power cable should be connected as follows:
The GREEN & YELLOW conductor to terminal marked with a letter “E” or Earth symbol “ “.
The BROWN conductor to terminal marked with a letter “L”.
The BLUE conductor to terminal marked with a letter “N”.
If connecting to a mains supply through a circuit breaker or RCD, the colours of the conductor insulation may not correspond with the colours in the mains cable from the trailing socket, in which case, you should proceed as follows. Connect:
The GREEN & YELLOW conductor to the terminal marked with a letter “E” or
Earth symbol “ “ or coloured GREEN or YELLOW & GREEN.
The BROWN conductor to the terminal marked with a letter “L” or coloured RED.
The BLUE conductor to the terminal marked with a letter “N” or coloured BLACK.
We strongly recommend the machine be connected via a residual current device.
15
Fuse rating
The fuse in the plug or circuit, must be rated at 13 amps and the plug fuse must be
ASTA or BS approved to BS1362.
Cable extension
If a cable extension is needed, it is essential that it complies with the following specification.
Extension length Conductor section
Up to 15m 2.5mm
2
From 15 to 50m 4.0mm
2
ADJUSTMENTS
CAUTION
Before carrying out any adjustments, the machine must be disconnected from the electrical mains supply.
1.
Before use for the first time
IMPORTANT
:
Before starting your machine for the first time, it is important to ensure that the blade is central within the Blade Insert, and does not come into contact with the Insert when tilted to 45 0 .
Tilt the blade to 45 0 and rotate by hand to ensure there is no contact between it and the table insert. Should an adjustment be necessary, slacken the nuts securing the 8 countersunk screws that secure the two Side Brackets to the table
(shown in fig. 2), and move the complete lower guard box and side bracket assembly so that the blade is: a. parallel with the edge of the table b. central within the table insert so that there is no contact between the blade and insert.
Tighten the nuts securing the 8 countersunk screws when satisfied and recheck.
2.
Before each use
IMPORTANT
:
Each time you use the machine, you must ensure the components are correctly adjusted and checked for security BEFOREHAND.
A.
For normal ripping or cross cutting, the blade should be exactly square (at 90°), to the table. To check and adjust, you should proceed as follows:
16
1.
Raise the blade to its maximum height by using the Blade Height Adjuster
Handle mounted beneath the Lower Blade Guard box.
2.
Place a small square on the table and slide it up to the blade. Check to ensure the blade is square - at 90°.
3.
If adjustment is required, slacken off both Blade Tilt Adjuster knobs slightly, allowing the box to be moved, so that the blade is correctly aligned.
Finally, retighten the adjuster knobs and recheck.
4.
When the blade is square, check to ensure the pointer, mounted on the
Lower Blade Guard Box, is pointing to zero. If necessary, slacken off the pointers’ mounting screw, zero the pointer and retighten the screw.
It should be noted that although an angle gauge is provided so that bevels up to 45° may be produced, it should not be relied upon for absolute accuracy. You should always check with a protractor where absolute accuracy is desired.
B.
The Riving Knife is essential in preventing kickback and producing a good clean cut without chattering or binding taking place.
Before use, check to ensure it is straight and directly in line with the blade, with the correct clearance of 3mm maintained between it and the blade along its full length (see fig. 8 on page 12).
Should the Riving Knife become out of shape or misaligned, it must be gently eased back into line, or if the damage is more severe, it must be removed and bent back into shape accordingly or replaced.
Adjustment is made by slackening off the two securing nuts (within the Lower
Blade Guard Box), moving the Riving Knife to achieve the correct clearance, and finally fully tightening the securing nuts.
C.
Check to ensure the blade teeth are sharp and the blade is sound. If teeth are chipped, or cracks are apparent, the blade must be renewed.
D .
Always check to ensure that the Lower Blade Guard Box and the Lower Blade
Guard Box Cover are firmly secured.
E.
Ensure the Upper Blade Guard is in place, pivots freely, and falls under its own weight.
OPERATION
1. Rip Cutting
You should always set the depth of the blade to the thickness of the wood plus
2mm. i.e. the blade should only just break the surface of the wood. This is to obtain maximum efficiency and to protect and preserve the saw blade teeth, particularly when cutting thin sections.
Blade depth is set by raising or lowering the blade using the adjuster handle mounted beneath the blade guard box.
17
True, straight line rip cutting, is best done by guiding the work against the rip fence.
Ensure the rip fence is set to produce your required width and is parallel to the blade.
Having taken all the necessary precautions previously stated, plug the machine into the mains supply, lift the STOP cover on the switch box, and switch ON the machine by pushing the start button (I).
Proceed to feed the work into the blade but do not force the work - a gentle pressure is all that is required.
The feed force should ALWAYS be applied between the saw blade and the fence and down on to the table, NOT on the section that will become the cut-off piece.
ALWAYS use a push stick when the end of the work approaches the blade, or for short work or work less than 6" wide.
NEVER hold on to the free piece that is cut off. It is important that it is not constrained in any way - it must be allowed to move laterally.
When switching off, by pushing the stop button (O), the blade should stop within 8 to 10 seconds. Should it take longer, then it will be necessary to adjust or renew the motor brake pads. In this event, you should consult your CLARKE dealer for advice.
2. Rip Cutting a Bevel.
Set the blade angle by slackening off the two Blade Tilt Adjuster knobs, which secure the Lower Blade Guard box, and position the blade using the angle gauge and pointer mounted on the side of the box. (If absolute accuracy is required, check the blade angle with a protractor)
Fully tighten the adjuster knobs and set the Rip Fence to give the desired width, before switching ON and feeding the work into the blade.
3.
Cross Cutting.
When cross cutting, remember to observe the following additional precautions:
• NEVER touch or hold on to the free piece whilst the saw blade is rotating.
This means that when feeding the workpiece through, you should NOT hold it on BOTH sides of the blade.
Remember, the free piece should not be constrained in any way. It must be allowed to move laterally.
• Long pieces of work must be supported at table height, and, the workpiece must be free to move easily. It is advised to use an assistant for very long pieces.
Remove the Rip Fence Assembly from the short Guide Bar by slackening off the Rip
Fence Support Securing Knob and lifting it off. Place it on the long Guide Bar as shown in fig 10.
Slacken off the hand wheel, securing the Quadrant to the Rip Fence Support, and move the Quadrant, with Rip Fence, to the desired angle as indicated by the pointer.
For normal cross cutting the pointer will be at 0°.
A cross cutting setup for cutting a mitre at 45° is shown in fig. 10. Again, if the angle is critical, check it with a protractor before tightening the Quadrant securing knob.
18
Cross Cut Guide
Fig 10.
Workpiece
Upper Blade
Guard
Rip Fence
Quadrant Saw Blade
Rip Fence
Support Bracket
Rip Fence Guide
DO NOT tighten the Rip Fence Support Bracket securing knob - leave it loose so that the Support, with the Rip Fence assembly, may slide along the Guide Bar.
Because the rip fence moves along the guide, towards the saw blade, it is essential to ensure that it is positioned so that it will not come into contact with the blade.
Before starting therefore, move the complete rip fence assembly along the guide to check the rip fence position in relation to the saw blade. If necessary, undo the two hand wheels, securing the rip fence to the quadrant, and re-locate the rip fence ensuring there will be no contact between the fence and the saw blade.
Tighten the hand wheels when satisfied.
Place the work against the Rip Fence, line up the cut, and, with the machine running, proceed to cut by sliding the Rip Fence, with the work, along the Guide Bar in the direction of the arrow, as shown in fig 10.
MAINTENANCE
IMPORTANT :
All maintenance and adjustments must be carried out with the machine switched OFF, and the power cable disconnected from the mains supply.
1. General
Maintenance is limited to:
• Ensuring the saw blade is kept sharp at all times.(Failure to do so could damage the motor).
• Changing the saw blade when necessary (see below).
• Maintaining adjustments (as explained on page 15).
• Ensuring that after each use you clean away any sawdust or wood chips with a low pressure air line or brush. This includes the inside of the Lower Blade Guard
Box.
19
Should the motor not function normally, it is possible that it has become clogged with sawdust, in which case it will be necessary to disassemble the motor in order to clean the various components. Contact your CLARKE dealer for advice.
2. Changing the Saw Blade
IMPORTANT: Exercise extreme care when handling the saw blade. The teeth are extremely sharp and careless handling could result in severe personal injury.
2.1 Open the Lower Guard Box door to reveal the saw blade.
2.2 Using a 13mm spanner remove the blade securing bolt, noting that it has a
LEFT HAND THREAD , followed by the outer flange and the saw blade.
NOTE: Flats are milled on the motor shaft, on to which a 17mm spanner may be fitted, in order to hold the shaft when removing the blade securing bolt.
2.3 Reassemble in reverse order, ensuring: a.
the blade teeth are the correct way round, i.e. facing down at the front of the table.
b.
the flange is correctly mounted, with the flat in the bore of the flange mating correctly with the flat on the motor shaft.
c.
the blade securing bolt is tightened to no more than 25 lbf ft.
2.4 Finally, check to ensure the correct clearance is set between the riving knife and the blade. Adjust as necessary (See page 12).
SPECIFICATIONS
Motor - Voltage:
Input Current Rating
Fuse Rating
Power Rating:
Speed:
Capacitor
Duty cycle
Blade - Size:
Bore
230V 50Hz 1 phase.
10 Amps
13 Amps
2.2Kw
2,830RPM
25uF 450V
S6 60%
12” (300mm) TCT (24 teeth)
30mm
Noise level
Gross weight
Min 88dB Max 115dB
59 kg
Dimensions (at table - incl guides) L900xW710xH800mm (To table top)
Dimensions at base 895x660mm
Max Depth of cut
Max width of cut with Rip Fence
Cross cut mitre angle
Rip cut bevel angle
70mm
280mm (high) 220mm (low)
0 - 45°
0 - 45°
20
PARTS LIST
No. Description
1 Saw Blade
2 Riving Knife
3 Upper Blade Guard
4 Rip Fence
5 Rip Fence Support
6 Quadrant
7 Guide Bar - Long
8 Guide Bar - Short
9 Corner Support
10 Table Insert
11 Table Top
12 Legs
13 Leg Strut - Short
14 Leg Strut - Long
15 Handle
16 Motor Assy.
17 Switch Box Bracket
18 Switch Box Assy.
19 Axle
20 Wheel
21 Axle Bracket
22 Lower Guard Box
23 Push Stick
24 Trailing Socket
25 Tilt Adjuster Knob
26 Scalloped Knob (F)
27 Rip Fence Spt Knob
Qty Part No.
1 AK30501
1 AK30502
1 AK30503
1 AK30504
1 AK30505
1 AK30506
1 AK30507
1 AK30508
2 AK30509
1 AK30510
1 AK30511
4 AK30512
2 AK30513
2 AK30514
2 AK30515
1 AK30516
1 AK30517
1 AK30518
1 AK30519
2 AK30520
2 AK30521
1 AK30522
1 AK30523
1 AK30524
2 AK30525
3 AK30526
1 AK30527
No. Description Qty Part No.
28 Shouldered Pivot Bolt 2 AK30528
29 Handle Assy 1 AK30529
30 Inner Flange
31 Outer Flange
1
1
AK30530
AK30531
32 Washer
33 Blade Securing Bolt
34 Flat Washer 5mm
35 Spring Washer
1
1
AK03032
AK30533
60 AK30534
40 AK30535
36 Locknut M5
37 Screw M5x15mm
38 Screw M5x20mm
39 Screw M5x25mm
40 Collar
41 Bolt M8x20mm
42 Nut M5
43 Bolt M5x35mm
44 Locknut M8
5
4
4
2
1
2
AK30536
23 AK30537
13 AK30538
AK30539
AK30540
AK30541
38 AK30542
AK30543
AK30544
45 Flat Washer M10
46 Flat Washer M8
47 Spring Washer M8
48 Nut M8
49 Roll Pin
50 Hinged Flap
51 Spring (pair)
52 Foot
53 Pan Head Screw
2 AK30545
4 AK30546
2 AK30547
2 AK30548
1 AK30549
1 AK30550
1 AK30551
4 AK30552
4 AK30553
SPARE PARTS AND SERVICING
For Spare Parts and Servicing, please contact your nearest dealer, or
CLARKE International, on one of the following numbers.
PARTS - 0181 558 6696
SERVICE - 0181 556 4443
PARTS & SERVICE FAX - 0181 558 3622
Please note that the details and specifications contained herein, are correct at the time of going to print. However, CLARKE International reserve the right to change specifications at any time without prior notice.
21
PARTS DIAGRAM
1
51
50
22
NOTES
_________________________________________________________________________
_________________________________________________________________________
_________________________________________________________________________
_________________________________________________________________________
_________________________________________________________________________
_________________________________________________________________________
_________________________________________________________________________
_________________________________________________________________________
_________________________________________________________________________
_________________________________________________________________________
_________________________________________________________________________
_________________________________________________________________________
_________________________________________________________________________
_________________________________________________________________________
advertisement