Schmalz SCPSi-UHV-HD 16 G02 NC Compact ejector technology for increased vacuum level and IO-Link functionality Operating Instructions
Add to My manuals72 Pages
advertisement
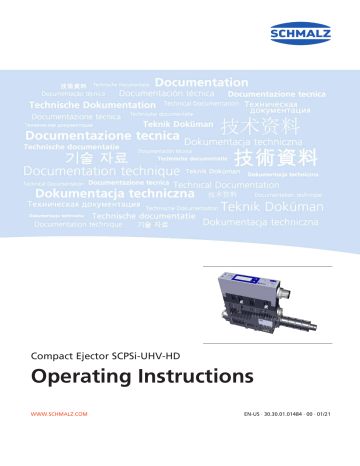
Compact Ejector SCPSi-UHV-HD
Operating Instructions
WWW.SCHMALZ.COM
EN-US · 30.30.01.01484 · 00 · 01/21
Note
The Operating instructions were originally written in German. Store in a safe place for future reference.
Subject to technical changes without notice. No responsibility is taken for printing or other types of errors.
Published by
© J. Schmalz GmbH, 01/21
This document is protected by copyright. J. Schmalz GmbH retains the rights established thereby. Reproduction of the contents, in full or in part, is only permitted within the limits of the legal provisions of copyright law. Any modifications to or abridgments of the document are prohibited without explicit written agreement from J. Schmalz GmbH.
Contact
J. Schmalz GmbH
Johannes-Schmalz-Str. 1
72293 Glatten, Germany
T: +49 7443 2403-0 [email protected]
www.schmalz.com
Contact information for Schmalz companies and trade partners worldwide can be found at: www.schmalz.com/salesnetwork
2 / 72 EN-US · 30.30.01.01484 · 00 · 01/21
Contents
Contents
EN-US · 30.30.01.01484 · 00 · 01/21 3 / 72
Contents
4 / 72 EN-US · 30.30.01.01484 · 00 · 01/21
Contents
EN-US · 30.30.01.01484 · 00 · 01/21 5 / 72
Important Information
1 Important Information
1.1 Note on Using this Document
J. Schmalz GmbH is generally referred to as Schmalz in these Operating instructions.
These Operating instructions contain important notes and information about the different operating phases of the product:
• Transport, storage, start of operations and decommissioning
• Safe operation, required maintenance, rectification of any faults
The Operating instructions describe the product at the time of delivery by Schmalz.
1.2 The technical documentation is part of the product
1. For problem-free and safe operation, follow the instructions in the documents.
2. Keep the technical documentation in close proximity to the product. The documentation must be accessible to personnel at all times.
3. Pass on the technical documentation to subsequent users.
ð Failure to follow the instructions in these Operating instructions may result in injuries!
ð Schmalz is not liable for damage or malfunctions that result from failure to heed these instructions.
If you still have questions after reading the technical documentation, contact Schmalz Service at: www.schmalz.com/services
1.3 Type Plate
The type plates (1) and (2) are permanently attached to the product and must always be clearly legible.
Type plate (1) contains the following information:
• EAC label
• Pneumatic symbol
• Part sales designation/type
• Part number
• Permitted pressure range
Type plate (2) contains the following information:
• CE label
• EAC label
• QR code
• Customer part number
• Coded date of manufacture
• Serial number
1
6 / 72
2
EN-US · 30.30.01.01484 · 00 · 01/21
Important Information
1.4 Warnings in This Document
Warnings warn against hazards that may occur when handling the product. The signal word indicates the level of danger.
Signal word
WARNING
CAUTION
NOTE
Meaning
Indicates a medium-risk hazard that could result in death or serious injury if not avoided.
Indicates a low-risk hazard that could result in minor or moderate injury if not avoided.
Indicates a danger that leads to property damage.
1.5 Symbol
This symbol indicates useful and important information.
ü This symbol represents a prerequisite that must be met prior to an operational step.
4 This symbol represents an action to be performed.
ð This symbol represents the result of an action.
Actions that consist of more than one step are numbered:
1. First action to be performed.
2. Second action to be performed.
EN-US · 30.30.01.01484 · 00 · 01/21 7 / 72
Fundamental Safety Instructions
2 Fundamental Safety Instructions
2.1 Safety
The ejector emits noise due to its use of compressed air.
WARNING
Noise pollution due to the escape of compressed air
Hearing damage!
4 Wear ear protectors.
4 The ejector must only be operated with a silencer.
WARNING
Uncontrolled movements of system components or falling of objects caused by incorrect activation and switching of the Ejector while persons are in the plant
(safety door opened and actuator circuit switched off)
Serious injury
4 Ensure that the valves and ejectors are enabled via the actuator voltage by installing a potential separation between the sensor and actuator voltage.
4 Wear the required personal protective equipment (PPE) when working in the danger zone.
CAUTION
Depending on the purity of the ambient air, the exhaust air can contain particles, which escape from the exhaust air outlet at high speed.
Eye injuries
4 Do not look into the exhaust air flow
4 Wear eye protection
2.2 Intended Use
The ejector is built in accordance with the latest standards of technology and is safe to operate upon delivery; however, hazards can still arise during use.
The ejector is designed to generate a vacuum for gripping and transporting objects when used in conjunction with suction cups. It is operated by a controller with discrete signals or via IO-Link.
Neutral gases are approved as evacuation media. Neutral gases include air, nitrogen and inert gases (e.g.
argon, xenon and neon).
The product is intended for industrial use.
Intended use includes observing the technical data and the installation and operating instructions in this manual.
8 / 72 EN-US · 30.30.01.01484 · 00 · 01/21
Fundamental Safety Instructions
2.3 Non-Intended Use
WARNING
Extraction of hazardous media, liquids or bulk material
Personal injury or damage to property!
4 Do not extract harmful media such as dust, oil mists, vapors, aerosols etc.
4 Do not extract aggressive gases or media such as acids, acid fumes, bases, biocides, disinfectants or detergents.
4 Do not extract liquids or bulk materials, e.g. granulates.
Schmalz accepts no liability for damages caused by non-intended usage of the ejector.
In particular, the following are considered non-intended use:
• Filling pressurized containers, driving cylinders, valves or other pressure-operated functional elements
• In potentially explosive atmospheres
• Use in medical applications
• Lifting people or animals
• Evacuation of objects that are in danger of imploding
• Ballistic applications
2.4 Personnel Qualifications
Unqualified personnel cannot recognize dangers and are therefore exposed to higher risks!
1. Task only qualified personnel to perform the tasks described in these Operating instructions.
2. The product must be operated only by persons who have undergone appropriate training.
These Operating instructions are intended for fitters who are trained in handling the product and who can operate and install it.
2.5 Modifications to the Ejector
Schmalz assumes no liability for consequences of modifications over which it has no control:
1. The ejector must be operated only in its original condition as delivered.
2. Use only original spare parts from Schmalz.
3. The ejector must be operated only in perfect condition.
EN-US · 30.30.01.01484 · 00 · 01/21 9 / 72
Product Description
3 Product Description
3.1 Ejector Designation
The breakdown of the item designation (e.g. SCPSi-UHV-HD 16 G02 NO) is as follows:
Property
Type of ejector
Nozzle size
Connection
Control
Variants
SCPSi-UHV-HD (ultra high vacuum-heavy duty)
0.7 mm; 1.1 mm; 1.6 mm
G02 (G1/8" internal thread)
Normally open (NO)
Normally closed (NC)
3.2 Ejector Structure
4
3
2
1
5
6
7
8
10
9
7
9
1
3
5
Blow off valve screw
Mounting hole (2x)
M12 electrical connection
Silencer cover with twist-and-lock closure
Silencer insert
2
4
6
G1/8" vacuum connection, marking 2 [V])
Display and operating element
G1/8" compressed air connection (marking 1
[P])
Exhaust outlet 8
10 Nozzle
10 / 72 EN-US · 30.30.01.01484 · 00 · 01/21
Product Description
3.3 Display and Operating Element in Detail
Simple ejector operation is ensured with 3 buttons, the 3-digit display and 4 LEDs for status information.
8 1 2 3 4
7
1 MENU BUTTON
3 LED vacuum limit value H1
5 UP BUTTON
7 LED process state “suction”
6 5
2 Display
4 DOWN BUTTON
6 LED vacuum limit value H2
8 LED process state “blow off”
Definition of the LED Indicators
The “suction” and “blow off” process states are each assigned an LED.
Display
LEDs both off
Ejector state
No suction from ejector
LED for the suction function is constantly lit Ejector is applying suction or in control mode
LED for the blow off function is constantly lit
Ejector blowing off
EN-US · 30.30.01.01484 · 00 · 01/21 11 / 72
Product Description
Meaning of the Vacuum Limit Value LEDs
The LEDs for the vacuum limit values H1 and H2 indicate the current level of the system vacuum relative to the configured limit values. Their display is independent of the switching function and assignment of the output, and independent of whether the condition monitoring function is active.
Display
LEDs both off
Ejector state
Rising vacuum:
Vacuum < H2
Falling vacuum:
Vacuum < (H2-h2)
H2 LED lit steadily
Both LEDs lit steadily
Rising vacuum:
Vacuum > H2 and < H1
Falling vacuum:
Vacuum > (H2-h2) and < (H1-h1)
Rising vacuum:
Vacuum > H1
Falling vacuum:
Vacuum > (H1-h1)
12 / 72 EN-US · 30.30.01.01484 · 00 · 01/21
Technical Data
4 Technical Data
4.1 Display Parameters
Parameter
Display
Resolution
Accuracy
Linearity error
Offset error
Temperature influence
Display refresh rate
Idle time before the menu is exited
5
1
±1
±2
±3
Value Unit
3 Digit
±1
±3 mbar
% FS
% mbar
%
1/s min
Comment
Red 7-segment LED display
—
T amb
= 25° C, based on FS (full-scale) final value
—
After zero-point adjustment, without vacuum
5° C < T amb
< 50° C
Only affects the 7-segment display
The display mode is accessed automatically when no settings are made in a menu.
4.2 General Parameters
Parameter Symbol
Working temperature
Storage temperature
Humidity
Precision of vacuum sensor
Degree of protection
Operating pressure (flow pressure)
Operating medium
T amb
T
Sto
H rel
---
P min.
0
-10
10
Limit value typ.
---
---
--max.
50
60
90
---
2
---
4.2
IP65
6
Unit
° C ---
° C ---
% r.h.
Free from condensation
± 3% FS (full scale)
--bar
Comment
---
---
Air or neutral gas, 5 µm filtered, with or without oil, class 3-3-3 compressed air quality in acc. with ISO 8573-1
4.3 Electrical Parameters
Parameter
Supply voltage
Power consumption from U
S/A
2) with NO variant
I
U
SA
S/A
Power consumption from U
S/A
2) with NC variant
I
S/A
Voltage of signal output (PNP) U
OH
Voltage of signal output
(NPN)
U
OL
I
OH
Power consumption of signal output (PNP)
Power consumption of signal output (NPN)
Voltage of signal input (PNP)
I
OL
U
IH
Symbol min.
22.8
—
Limit values typ.
24
50 4) max.
26.4
120
—
U
0
—
—
S/SA
15
-2
40
—
—
—
—
—
4) 70
V
2
S/SA
140
-140
U
A/SA
Voltage of signal input (NPN) U
IL
0 — 9
Unit
V DC mA mA
V
DC
V
DC mA mA
V
DC
V
DC
Comment
PELV 1)
U
S/A
= 24.0 V
U
S/A
= 24.0 V
I
OH
< 140 mA
I
OL
< 140 mA
Short-circuit-proof 3)
Short-circuit-proof 3)
In reference to Gnd
A/
SA
In reference to U
A/SA
EN-US · 30.30.01.01484 · 00 · 01/21 13 / 72
Technical Data
Parameter Symbol
Current of signal input (PNP)
Current of signal input (NPN)
I
IH
I
IL
Reaction time of signal inputs t
I
Reaction time of signal outputs t
O
—
—
—
1
Limit values
5
-5
3
—
—
—
—
200
Unit mA mA ms ms
Comment
—
—
—
Adjustable
1) The power supply must correspond to the regulations in accordance with EN60204 (protected extra-low voltage). The signal inputs and outputs are all protected against reverse polarity.
2) Plus the output currents
3) The signal output is protected against short circuits. However, the signal output is not protected against overloading. Constant load currents > 0.15 A may lead to impermissible heating and therefore the destruction of the ejector.
4) Mean value
4.4 Factory Settings
Code ctr dc5 t-1
-LbLo uni tYP dLY
X-1 h-1
X-2 h-2
XP1 hp1 tbL dPY
Eco
Pin o-2
Parameter
Limit value H1
Hysteresis value h1
Limit value H2
Hysteresis value h2
Limit value H1
Hysteresis value hP1
Blow off time
Control
Continuous suction
Evacuation time
Leakage value
Blow off function
Vacuum unit
Signal Type
Switch-off delay
Display rotation
ECO mode
PIN
Signal Output
Value of the factory setting
750 mbar
150 mbar
550 mbar
10 mbar
4.0 bar
0.2 bar
0.2 s
Activated = on
Deactivated = off
2 s
250 mbar/s
Externally controlled blow off = -E-
Vacuum unit in mbar =
-bA
PNP switching =
PnP
10 ms
Standard = 5td
Deactivated = oFF
User-defined
000
“Normally open” contact = no
The production setup profiles P-1 to P-3 are factory-set to have the exact same data set as the default data set P-0.
14 / 72 EN-US · 30.30.01.01484 · 00 · 01/21
4.5 Performance Data
Type
Nozzle size [mm]
Max. vacuum 1 [%]
Suction rate 1 [l/min]
Max. blow off capacity 1 [l/min]
Air consumption 1 (suction) (l/min]
Sound level 1 , unobstructed suction
[dB(A)]
Sound level 1 , suction [dB(A)]
Weight [kg]
1) at 4.5 bar
4.6 Dimensions
Technical Data
SCPS UHV HD 07
0.7
13
17.2
62
64
SCPS UHV HD 11
1.1
91
27.8
120
37.5
68
75
0.21
SCPS UHV HD 16
1.6
53.2
105.6
75
77
B
18
B1
18.6
d
4.4
d3
2.6
H5
5.5
H6
31.5
L
135
All specifications are in mm
L1
150
D
16.5
L2
91.5
G1
G1/8" internal threa d
G2
G1/8" internal threa d
G3
M12x
1-M
L3
22
L4
31
L5
83.8
H
99
X1
36.9
H2
40.8
H3
47.5
X2
16
Y1
12
H4
16.5
Y2
12
EN-US · 30.30.01.01484 · 00 · 01/21 15 / 72
Technical Data
4.7 Pneumatic Circuit Plans
SCPSi...NO...
SCPSi...NC...
16 / 72 EN-US · 30.30.01.01484 · 00 · 01/21
Operating and Menu Concept
5 Operating and Menu Concept
The parameters can also be set using three buttons. The current system status and the settings are shown on a display.
The unit is operated via three buttons on the foil keypad. Settings are configured using software menus.
The operating structure is divided into settings in the main menu and configuration menu. Setting the ejector in the main menu is sufficient for standard applications. The advanced configuration menu is available for applications with special requirements.
If settings are changed, undefined states of the system may occur for a short time (for approx. 50 ms).
5.1 Enabling the Menu
Menus can be protected against unauthorized access by defining a PIN [
Pin
] in the configuration menu.
When the lock is active, [
Loc
] flashes on the display or the PIN is requested.
The menus are accessed as follows:
1. Press the button
ð The display changes to input
2. Use the or buttons to enter the first digit of the PIN
3. Confirm using the button
4. Enter the remaining digits in the same way.
5. To enable the device using the menu, press the button
The lock is activated again automatically after you leave the selected menu or close the function.
The PIN [ 000 ] must be set for permanent deactivation of the lock.
Tips and Tricks for Parameter Setting
• By pressing the or button for approx. 3 seconds, the value to be changed is scrolled through quickly
• If you exit the changed value by briefly pressing , the value will not be applied.
5.2 Main Menu
All the settings for standard ejector applications can be configured and read through the main menu:
1. Open the main menu by pressing the button.
2. Use or to select the desired adjustable parameter.
3. Confirm the selection with the key.
4. Use the or keys to set the value of the parameter.
5. To save and exit the menu, press and hold the key for at least 2 seconds.
ð The displayed value flashes to confirm.
EN-US · 30.30.01.01484 · 00 · 01/21 17 / 72
Operating and Menu Concept
The following table shows an overview of the display codes in the main menu:
Display code x-1 h-1 x-2 h-2 tbL
CAL
Parameter
Vacuum limit value H1
Hysteresis value h-1
Vacuum limit value H2
Hysteresis value h-2
Blow off time
Calibration
Explanation
Value at which the control function deactivates
(only if ctr
= on
and oN5
are active)
Hysteresis value for the control function
“Part Present” check switching value
“Part Present” check hysteresis value
Only activated for
E-t
or l-t
Calibrate the vacuum sensor
The factory settings for the parameters are listed in the Technical Data section.
5.3 Configuration Menu
An extended configuration menu is available for applications with special requirements.
1. Open the configuration menu by pressing the button for more than 3 seconds.
ð During activation, [
-C-
] appears.
2. The parameters are set in accordance with the description in the Main Menu section.
The following table shows an overview of the display codes in the configuration menu:
Display code ctr dC5 t-1
-L-
Parameter
Air saving function
Deactivate auto.
control shutoff
Max. permissible evacuation time
Max. permissible leakage
Possible settings on oFF on5 on oFF
Configurable between 0.01 and
9.99 s in 0.01 increments off
Values from 0 to
999 mbar/s can be configured in
1 mbar/s increments
Explanation
Control active
Control inactive
Valve protection function active (max. permissible leakage is monitored)
Suppresses the automatic valve protection function when set to
YE5
.
Cannot be activated when
Ctr
= off
.
Permissible evacuation time; evaluation in IO-
Link only bLo o-2 tYP
Blow off function
Signal output 2
Signal Type
-E-
1-t
E-t no nc
No monitoring
Menu item only displayed when ctr
=
On5
Unit: millibar per second
This value is used for onS and CM warnings. The adjustable leakage value can be used to judge the quality of the suction process. Evaluation in
IO-Link only.
Externally controlled
Internally controlled (triggered internally, time can be set)
Externally controlled (triggered externally, time can be set)
Configure output 2, “Part Present” check for normally open for normally closed
Define signal type for inputs and outputs
18 / 72 EN-US · 30.30.01.01484 · 00 · 01/21
Operating and Menu Concept
Display code dLY uni dPY
Eco
Pin rE5
Parameter Possible settings
H2 switching signal delay
Vacuum unit
PnP nPn
Values:
200
10
and
,
50
oFF
,
Display rotation
Display in ECO mode
PIN
Reset
-bA
-ix
-PA
5td
Red oFF on
Value from 001 to
999
YES
Explanation
Signal type PNP, input/output on = 24 V
Signal type NPN, input/output on = 0 V
Delays the switching signals
X1
and
X2
Unit: milliseconds
Define the displayed vacuum unit
Vacuum level in mbar
Vacuum level in inHg
Vacuum level in kPa
Display configuration
Standard rotated 180°
Configure the display
ECO mode is deactivated – the display remains on
ECO mode is activated – the display switches off
Specify the PIN, lock the menus
If the PIN is
000
, then the device is not locked.
Set all parameter values to factory settings.
The factory settings for the parameters are listed in the Technical Data section.
5.4 System Menu
A special menu is available for reading out system data such as counters, the software version, part numbers and serial numbers.
1. Open the system menu by simultaneously pressing the and buttons for more than 3 seconds.
ð During activation,
-5-
appears.
2. The parameters are set in accordance with the description in the Main Menu section.
The following table shows an overview of the display codes in the system menu:
Display code Parameter cc1 cc2
5oC
Type
5nr
Counter 1
Counter 2
Software function
Part number
Serial number
Explanation
Suction cycles
Number of valve switches
Software on the internal controller
Format of the part no., example: 10.02.02.00383
Provides information about the production period
EN-US · 30.30.01.01484 · 00 · 01/21 19 / 72
Operating and Menu Concept
5.5 Individual Functions
Displaying the vacuum level:
Outside of the menu, the ejector is in display mode and the current vacuum level is displayed.
In display mode, a specific function is assigned to each key.
Displaying the supply voltage:
4 Press the button
ð The supply voltage that is currently applied to the ejector is displayed in volts.
After 3 seconds, the screen returns to the vacuum display.
The displayed voltage is a guideline value and is used for comparative measurements.
Displaying the operating mode:
4 Press the button
ð The current operating mode is displayed.
It is either standard I/O (SIO) mode [
510
] or IO-Link mode [
10L
].
In IO-Link mode, you can also press the button again to view the IO-Link Standard (1.0, 1.1) that is currently in use.
After 3 seconds, the screen returns to the vacuum display.
20 / 72 EN-US · 30.30.01.01484 · 00 · 01/21
Operating Modes
6 Operating Modes
All the ejectors in the SCPSi series can be operated in two operating modes:
• Via direct connection to inputs and outputs (standard I/O = SIO) or
• Connection via a communication line (IO-Link)
By default, the ejector always runs in SIO mode, but it can be switched in and out of IO-Link mode by an
IO-Link master at any time.
6.1 SIO Operating Mode
In SIO mode, all input and output signals are connected to a controller, either directly or using intelligent terminal boxes. For this purpose, in addition to the supply voltage, two input signals and one output signal should be connected to allow the ejector to communicate with the controller.
The following basic ejector functions are used:
• Inputs
– Suction ON/OFF
– Blow off ON/OFF
• Output
– Feedback 2 (“Part Present” check)
The “Blow off” signal does not have to be used if the ejector is operated with internal time control in blow off mode. This allows operation on a single port in a configurable terminal box (using 1xDO and
1xDI).
The parameters are set and the internal counters are read out using the operating and display elements.
The energy and process control functions are unavailable in SIO mode.
6.2 IO-Link Operating Mode
When operating the ejector in IO-Link mode (digital communication), the supply voltage, the ground and the communication line are connected to a controller, either directly or using intelligent terminal boxes.
The communication line for IO-Link (C/Q line) is always connected with an IO-Link master port (point-topoint connection). It is not possible to connect multiple C/Q lines to a single IO-Link master port.
Connecting the ejector via the IO-Link provides access to a number of additional ejector functions alongside the basic functions of suction, blow off, feedback, etc. They include:
• The current vacuum level
• Selection of four production profiles
• Errors and warnings
• Ejector system status display
• Access to all parameters
• Functions for energy and process control
So that all the modifiable parameters can be read directly via the higher-level controller, modified and written back to the ejector.
Evaluation of the condition monitoring and energy monitoring results allows you to draw direct conclusions regarding the current handling cycle and perform trend analysis. The ejector supports the IO-Link revision 1.1 with four bytes of input data and two bytes of output data. It is also compatible with IO-Link masters that use the 1.0 revision. In this case, one byte of input data and one byte of output data are supported. The exchange of process data between the IO-Link master and the ejector is cyclical. Parameter data (acyclical data) is exchanged by the user program in the control unit using communication modules.
EN-US · 30.30.01.01484 · 00 · 01/21 21 / 72
Operating Modes
6.2.1 Process Data
The cyclical process data is used to control the ejectors and receive current information reported from the ejector. There is a difference between the input data (Process Data In) and the controlling output data
(Process Data Out).
The input data Process Data In is used to report the following information cyclically:
• Vacuum limit values H1 and H2
• CM-Autoset acknowledgment
• EPC-Select acknowledgment
• The ejector device status in the form of a status traffic light
• Multifunctional EPC values
The output data Process Data Out is used to control the ejector cyclically:
• Vacuum on/off
• Blow off active
• Setup mode
• CM Autoset
• EPC-Select: switching the multifunctional EPC values
• Switching production setup profiles P0–P3
• Inlet pressure in 0.1 bar (measured value from external pressure sensor, 0 = function inactive)
A detailed description of the process data can be found in the data dictionary.
The corresponding device description file (IODD) is available for integration into a higher-level control unit.
6.2.2 Parameter Data
In addition to the process data that is exchanged automatically, the IO-Link protocol provides an acyclical data channel for identification data, setting parameters or general feedback from the device. The available data objects are referred to as ISDU with IO-Link and are to be uniquely addressed within a device through their index and subindex.
Controller manufacturers usually provide a specialized function module – e.g. the “IOL_CALL” module for
Siemens controllers – to enable these parameters to be accessed from a control program.
Information about which parameter data the device provides and how this data is displayed as ISDU objects can be found in the “Data Dictionary”.
6.2.3 IO-Link
The ejector can be operated in IO-Link mode to enable intelligent communication with a controller. The ejector’s parameters can be set remotely using IO-Link mode. The energy and process control (EPC) function is also available in IO-Link mode. It is divided into 3 modules:
• Condition monitoring (CM): Condition monitoring to increase system availability
• Energy monitoring (EM): Energy monitoring to optimize the vacuum system’s energy consumption
• Predictive maintenance (PM): Predictive maintenance to increase the performance and quality of the gripping systems
22 / 72 EN-US · 30.30.01.01484 · 00 · 01/21
General Description of Functions
7 General Description of Functions
7.1 Picking up the Workpiece (Vacuum Generation)
The ejector is designed for handling and holding workpieces by means of a vacuum in combination with suction systems. The vacuum is generated in a nozzle according to the Venturi principle, using suction generated by the flow of accelerated compressed air. Compressed air is channeled into the ejector and flows through the nozzle. A vacuum is generated immediately downstream of the motive nozzle; this causes the air to be sucked through the vacuum connection. The air and compressed air that have been removed by the suction exit together via the silencer.
The venturi nozzle on the ejector is activated and deactivated using the suction command:
• In the NO (normally open) variant, the venturi nozzle is deactivated when the suction signal is received.
• In the NC (normally closed) variant, the venturi nozzle is activated when the suction signal is received.
An integrated sensor records the vacuum generated by the venturi nozzle. The exact vacuum level is shown on the display and can be read from the IO-Link process data.
Vacuum
[mbar]
H1
H1-h1
H2
H2-h2
OUT=on
OUT=off
Vacuum on Time [s]
The ejector has an integrated air saving function and automatically regulates the vacuum in suction mode:
• The electronics switch the venturi nozzle off as soon as the set vacuum limit value (switching point
H1) is reached.
• When objects with airtight surfaces are picked up, the integrated non-return valve prevents the vacuum from dropping.
• If the system vacuum drops below the limit value switching point H1-h1 due to leaks, the venturi nozzle is switched back on.
• Depending on the vacuum, the H2 process data bit is set once a workpiece is picked up safely. This enables the further handling process.
7.2 Depositing the Workpiece (Blowing Off)
In blow off mode, the vacuum circuit of the ejector is supplied with compressed air. This ensures that the vacuum drops quickly, allowing the workpiece to be deposited quickly.
The ejector provides three blow off modes for selection:
• Externally controlled blow off
• Internally time-controlled blow off
EN-US · 30.30.01.01484 · 00 · 01/21 23 / 72
General Description of Functions
• Externally time-controlled blow off
The current process state is indicated by the LED status indicators.
During blow off, [ -FF ] is shown on the display.
7.3 Operating Modes
The ejector can be operated in four operating modes:
• Direct connection to inputs and outputs (standard I/O = SIO)
• Connection via the communication line (IO-Link)
• “Manual mode,” operation using the ejector buttons
• Setup mode
By default, the ejector always runs in SIO mode, but it can be switched in and out of IO-Link mode by an
IO-Link master at any time.
If the ejector is connected to the supply voltage, it is in automatic mode and ready for operation. This is the normal operating mode, in which the ejector is operated by the system controller. A differentiation is made between SIO mode and IO-Link mode.
The ejector is always parameterized in automatic mode.
7.3.1 Automatic Operation
Once the ejector is connected to the power supply, it is ready for operation and enters automatic operation mode. This is the normal operating mode, in which the ejector is operated by the system controller.
The operating mode may be changed from automatic to manual mode using the buttons.
The ejector is always parameterized in automatic mode.
7.3.2 Manual Operating Mode
WARNING
Through an external signal, manual operation is exited, external signals are evaluated and system parts move.
Personal injury or damage to property due to collisions
4 Ensure that the danger zone of the system is clear of people during operation.
4 Wear the required personal protective equipment (PPE) when working in the danger zone.
WARNING
Falling objects due to incorrect operation in manual mode
Risk of injury
4 Higher level of attention
4 Ensure that there are no persons within the danger zones of the machine/system
In manual mode, a higher level of attention is advisable because incorrect operation may cause gripped parts to fall, resulting in injuries.
In manual mode, the “suction” and “blow off” ejector functions can be controlled independently of the higher-level controller using the buttons on the operating panel. In this operating mode, the “H1” and
“H2” LEDs both flash. Because the valve protection function is deactivated in manual mode, this function can be used to locate and rectify leaks in the vacuum circuit.
24 / 72 EN-US · 30.30.01.01484 · 00 · 01/21
General Description of Functions
Activating the Operating Mode
Press and hold the or button for more than 3 seconds. An M appears on the display while you do so.
The current process state is retained.
Manual suction
The button activates “suction” on the ejector.
Press the or button to exit the “suction” operating state again.
Manual blow off
The button activates “blow off” on the ejector for as long as the button is pressed.
Deactivating the Operating Mode
Using the button or through an external state change by signal inputs.
The valve protection function is not active in manual mode.
7.3.3 Setup Mode
Setting mode is used for locating and eliminating leakages in the vacuum circuit. Since the valve protection function is deactivated and the control is not deactivated, even at increased control frequencies.
In this operating mode, the “H1” and “H2” LEDs both flash.
Setting Mode Activated and Deactivated
4 Set the corresponding value using bit 2 in the output process data byte (PDO).
A change to bit 0 or bit 1 (suction or blow off) in the PDO also causes the ejector to exit setting mode.
This function is only available in IO-Link mode.
7.4 Vacuum Monitoring
The ejector has an integrated sensor for monitoring the current system vacuum. The vacuum level provides information about the process and has an effect on the following signals and parameters:
• The limit value H1
• The limit value H2
• The signal output H2
• The process data bit H1
• The process data bit H2
The limit values and associated hysteresis values are adjusted in the menu items x-1 , h-1 , x-2 and h-2
in the main menu or via IO-Link.
7.5 Control Function
The ejector allows you to conserve compressed air or prevent an excessive vacuum from being generated.
Vacuum generation is interrupted when the set vacuum limit value H1 is reached. If leakage causes the vacuum to fall below the hysteresis limit value (H1-h1), vacuum generation resumes.
The operating modes for the control function can be set under the [ ctr ] menu item in the configuration menu or via IO-Link.
EN-US · 30.30.01.01484 · 00 · 01/21 25 / 72
General Description of Functions
Operating mode
No control/continuous suction, H1 in hysteresis mode
[ ctr
] => [ oFF
]
Control function activated
[ ctr ] => [ on ]
Explanation
The ejector produces continuous suction with maximum power. This setting is recommended for very porous workpieces, which would otherwise cause vacuum generation to switch on and off continuously due to the high rate of leakage. The limit value evaluation for H1 is operated in hysteresis mode.
Can be adjusted only if the control shutoff is deactivated
([ dC5
] => [ oFF
])
The ejector switches off vacuum generation when the vacuum limit value H1 is reached. It switches it back on when the vacuum falls below the hysteresis limit value
(H1-h1). The limit value evaluation for H1 follows the control function. To protect the ejector, valve switching frequency monitoring is activated in this operating mode. If the readjustment is too fast, the control function is deactivated and the device switches to continuous suction.
Control function activated, leakage measurement activated
[ ctr
] => [ on5
]
Like the “Control function activated” operating mode; in addition, the system leakage rate is measured and compared to the adjustable leakage limit value [
-L-
]. If the actual leakage rate exceeds the limit value more than twice in succession, the control function is deactivated and the ejector switches to continuous suction.
Available control function operating modes
The control shutoff function can deactivate the automatic control shutoff.
The function can be set under the [ dC5
] menu item in the configuration menu or via IO-Link. If the
[ dC5
= oFF
] function is selected, the ejector switches to the “Continuous suction” operating mode when there is excessively high leakage and the valve switches too frequently. With the [ dC5 = on ] setting, continuous suction is deactivated, and the ejector continues in control mode despite a high leakage rate or control frequency greater than 6 times per 3 s.
In the event of undervoltage or a power failure, the NO ejector version reacts with continuous suction even though continuous suction is deactivated with [ dC5
= on
].
7.6 Blow off Functions
The ejector has three blow off functions in three different modes. The function is set under the [ blo
] menu item in the configuration menu or via IO-Link.
Explanations of the blow off modes:
Description
Externally controlled blow off
[ bL0
] => [
-E-
]
Internally time-controlled blow off
[ bLo ] => [ l-t ]
Externally time-controlled blow off
[ bLo ] => [ E-t ]
Explanation
The ejector switches to blow off mode for as long as the blow off signal is present.
The blow off signal is given priority over the suction signal.
After the suction signal is switched off, the ejector switches to blow off mode automatically for the set time (which can be adjusted using
[ tbL ]). With this function, the blow off signal does not have to be additionally controlled.
The blow off signal overrides the suction signal, even if the specified blow off time is very long.
The blow off starts with the blow off signal and is performed for the set time period [ tbL
]. Applying the blow off signal for a longer time does not lead to a longer blow off period.
26 / 72 EN-US · 30.30.01.01484 · 00 · 01/21
General Description of Functions
Description Explanation
The blow off signal overrides the suction signal, even if the specified blow off time is very long.
The length of the blow off time [ tbL ] is set in the main menu. This menu item is suppressed in operating mode [
-E-
].
The number displayed indicates the blow off time in seconds. Blow off times from 0.10 seconds to
9.99 seconds can be set.
7.7 Changing the Blow-Off Flow Rate on the Ejector
Do not overwind the stop on the valve screw. A minimum flow rate of approx. 15 % is always necessary for technical reasons. The blow-off volume flow can be set between 15 % and
100 %.
There is a valve screw below the vacuum connection that can be used to adjust the blow-off flow rate.
The valve screw is equipped with a stop on both sides.
Valve screw
-
+
1. Turn the valve screw clockwise to reduce the flow rate.
2. Turn the valve screw counterclockwise to increase the flow rate.
7.8 Monitoring the Supply Voltages
The ejector is not a voltage meter! However, the measured values and the system responses derived from them provide a helpful diagnostics tool for condition monitoring.
The ejector measures the supply voltages U
S
. The measured value can be read from the parameter data.
If the voltages are outside the valid range (min. 19.2 V and max. 26.4 V), the following status messages change:
• Device status
• Condition monitoring parameter
• An IO-Link event is generated
There is no guarantee that the ejector will operate as intended below a supply voltage of 19.2 V:
• The reaction to signal inputs is disabled.
• The “Part Present” check output retains its normal functionality.
• The current supply voltage can still be viewed using the button.
EN-US · 30.30.01.01484 · 00 · 01/21 27 / 72
General Description of Functions
• The pneumatic state of the ejector changes as follows:
– For the NO-type ejector, the ejector switches to the “suction” operating state
– For the NC-type ejector, the ejector switches to the “pneumatically OFF” operating state
7.9 Evaluating the Inlet Pressure
The available supply pressure level in the system cannot be measured by the ejector itself. However, the current measured value for the inlet pressure can be transmitted to the ejector from the system controller via IO-Link. In this case, the ejector evaluates the pressure level and activates a condition monitoring warning if the pressure level is not optimal. If there is a significant deviation, an error message is also generated.
A pressure level must also be transferred to enable the volume of compressed air consumed in the suction cycle to be estimated in the area of energy monitoring.
7.10 Calibrating the Vacuum Sensor
As the production conditions for the internally integrated vacuum sensor can vary, we recommend calibrating the sensor once it is installed in the ejector. To calibrate the vacuum sensor, the system's vacuum circuit must be open to the atmosphere.
The function for zero-point adjustment of the sensor is performed in the main menu under the parameter
CAL
or using IO-Link.
1. Press the button
ð The menu changes to input
2. Press the or button until cal appears on the display
3. Confirm with the button
4. When
YE5
appears, press the button to confirm.
ð The vacuum sensor is now calibrated.
A zero offset is only possible in the range of ± 3% around the theoretical zero position.
When the permissible limit is exceeded by ±3%, error code
E03
will appear on the display.
7.11 Signal Output
The ejector has a signal output. The signal output can be configured using the corresponding menu item.
The signal output OUT can be switched between [ no ] (normally open) and [ nc ] (normally closed) contact. You can switch it in the configuration menu using the [
0-2
] menu item or set it via IO-Link. The function of the limit value H2/h2 (“Part Present” check) is assigned to the signal output OUT.
The signal output is switched on or off when the system vacuum is higher or lower than the relevant threshold value.
The output type parameter can be used to switch between PNP and NPN. The signal inputs are also configured with this function. This setting can be switched using the [ tYP
] menu item in the configuration menu or via IO-Link.
7.12 Signal Type
The signal type, or the switching behavior (PNP or NPN) of the electrical signal inputs and the signal output, can be set on the device and therefore does not depend on the version. You can switch this setting using the [ tYP
] menu item in the configuration menu or via IO-Link. The ejector is factory set to PNP.
28 / 72 EN-US · 30.30.01.01484 · 00 · 01/21
General Description of Functions
7.13 Control Concept for NO Ejectors
“Suction” [IN1]
1
“Blow off” [IN2]
0
“Suction” state
0 bar
-p p
“Blow off” state
0 bar
1
0
7.14 Control Concept for NC Ejectors
“Suction” [IN1]
“Blow off” [IN2]
“Suction” state
1
0
1
0
-p
0 bar p
“Blow off” state
0 bar
7.15 Vacuum unit
You can choose between the following three units for the unit of the displayed vacuum level under the
[ uni
] menu item in the configuration menu or via IO-Link.
Unit
Bar
Pascal
InchHg
Setting parameter
[
-bA
]
[
-PA
]
[ -ix ]
Display unit mbar kPa inHg
The selection of the vacuum unit only affects the display. The units of the parameters that can be accessed via IO-Link are not affected by this setting.
EN-US · 30.30.01.01484 · 00 · 01/21 29 / 72
General Description of Functions
7.16 Switch-off Delay
You can use this function to set a switch-off delay for the H2 “Part Present” check signal. This can be used to mask short-term fluctuations in the vacuum level of the vacuum system. The duration of the switch-off delay can be set with the parameter [ dlY ] in the configuration menu or via IO-Link. The value can be set to 10, 50 or 200 ms. To deactivate this function, enter the value [
000
] (= off).
The switch-off delay affects the OUT
2
discrete output, the process data bit in IO-Link and the H2 status display
If the OUT
2
output is configured as a normally open contact [no], there will be an electrical switch-off delay. On the other hand, if it is configured as a normally closed contact [nc], there will be an equivalent switch-on delay.
7.17 ECO Mode
The ejector offers the option to switch off the display to save energy. If ECO mode is activated, the display is switched off and the system power consumption is reduced after 2 minutes if no buttons are pressed.
ECO mode can be activated and deactivated using the [ Eco ] parameter in the configuration menu or via
IO-Link.
A red dot in the lower right corner of the display indicates that the display has been switched off.
The display is reactivated by pressing any button or by an error message.
If you activate ECO mode using IO-Link, the display will immediately enter energy-saving mode.
7.18 Write Protection
A PIN can be used to prevent the parameters from being changed via the user menu.
The current settings are still displayed. The PIN is set to
000
on delivery. meaning access to the parameters is not locked. A valid PIN between 001 and 999 must be entered to activate write protection. If write protection is activated with a customer-specific PIN, the desired parameters can be changed within one minute after the correct code is entered. If no changes are made within one minute, write protection is automatically reactivated. The PIN 000 must be set again to permanently deactivate the lock.
Full access to the ejector is still possible via IO-Link even if a PIN is enabled. The current PIN can also be read out and changed/deleted (PIN =
000
) via IO-Link.
You enter the PIN using the
PIN
parameter in the configuration menu or via IO-Link.
In IO-Link mode, the “Device access locks” default parameter is available to prevent changes to parameter values using the user menu or IO-Link. You can also prevent the use of the Data storage mechanism described in IO-Link Standard V1.1.
Bit
0
1
2
Meaning
Parameter write access locked
(Parameters cannot be changed via IO-Link)
Data storage locked
(Data storage mechanism is not triggered)
Local parametrization locked
(Parameters cannot be changed via the user menu)
Coding for the device access locks
A menu lock using the Device access locks parameter has a higher priority than the menu PIN. In other words, this lock cannot be bypassed by entering a PIN and remains in SIO mode.
It can only be canceled via IO-Link, not via the ejector or the vacuum switch itself.
30 / 72 EN-US · 30.30.01.01484 · 00 · 01/21
General Description of Functions
7.19 Resetting to Factory Settings
This function restores the ejector configuration of the initial setup and the settings of the active production setup profile to the factory settings.
WARNING
By activating/deactivating the product, output signals lead to an action in the production process!
Personal injury
4 Avoid possible danger zone.
4 Remain vigilant.
The function is executed using the rE5
menu item in the configuration menu or via IO-Link:
1. Press the button for more than 3 seconds.
ð When the menu is locked, enter the valid PIN.
2. Use the or button to select the rE5
menu item.
3. Confirm using the button.
ð YE5
appears on the display.
4. Press the for more than 3 seconds.
ð The ejector is reset to the factory settings.
ð The display flashes for a number of seconds and then returns to display mode.
The function for resetting factory settings does not affect the following elements:
• The counter readings
• The zero-point adjustment of the sensor
• The IO-Link parameter “Application Specific Tag”
• The production setup profiles, which are currently deactivated
The factory settings for the ejector are listed in the Technical Data section.
7.20 Counters
The ejector has two internal counters, [ cc1
] and [ cc2
], which cannot be erased:
Counter 1 increases with each valid pulse at the “suction” signal input, meaning that it counts all the suction cycles during the ejector’s service life. Counter 2 increases each time the “suction” valve is switched on. As a result, the average switching frequency of the air saving function can be determined using the difference between counters 1 and 2.
Designation
Counter 1
Counter 2
Display parameter
[ cc1
]
[ cc2
]
Description
Counter for suction cycles (“suction” signal input)
Counter for the “suction valve” switching frequency
Displaying a Counter on the Operating Panel of the Ejector:
EN-US · 30.30.01.01484 · 00 · 01/21 31 / 72
General Description of Functions
ü Select the counter you wish to see in the system menu.
4 Confirm the counter by pressing the button.
ð The last three decimal places of the counter total are displayed (the digits x10 0 ). This corresponds to the least significant three digits. The decimal point at the far right lights up. This corresponds to the least significant three digits.
Use the and buttons to display the remaining decimal places of the counter total. The decimal points show which three-digit block of the complete counter value is shown on the display.
The counter total is comprised of the 3 number blocks together:
Displayed section
Digit block
10 6
0.48
10 3
61.8
10 0
593.
The current counter total in this example is 48 618 593.
7.21 Displaying the Software Version
The software version indicates the software currently running on the internal controller.
1. If the menu is locked: Enter a valid PIN code.
2. Use the or button to select the parameter [
5oc
].
3. Confirm using the button.
ð The value is displayed.
4 To exit the function, press the button.
7.22 Displaying the Part Number
The part number of the ejector is specified on the label and also stored electronically.
ü In the system menu, select the parameter Art .
1. Confirm using the button.
ð The first two digits of the part number are displayed.
2. You can press the or button to display the remaining digits of the part number. The decimal points shown are part of the part number.
The part number consists of 4 number blocks with a total of 11 digits.
Displayed section
Digit block
1
10.
2
02.0
3
2.00
The part number in this example is 10.02.02.00383.
4 To exit the function, press the button.
4
383
32 / 72 EN-US · 30.30.01.01484 · 00 · 01/21
General Description of Functions
7.23 Displaying the serial number
The serial number indicates the production period of the ejector.
ü In the system menu, select the 5nr parameter.
1. Confirm using the button.
ð The last three decimal places of the serial number are displayed (the digits x 10 0 ). The decimal point at the far right flashes. This corresponds to the least significant three digits.
2. You can press the or button to display the remaining decimal places in the serial number.
The decimal points show which three-digit block of the serial number is shown on the display.
The serial number consists of 3 number blocks:
Displayed section
Digit block
10 6
0.48
10 3
61.8
10 0
593.
The serial number in this example is 48 618 593.
4 To exit the function, press the button.
7.24 Production Setup Profiles
The ejector can store up to four different production setup profiles (P-0 to P-3) via IO-Link. All the important parameter data for handling the workpiece is stored in this case. The profiles are selected using the
PDO byte 0 process data byte. This gives users a quick and convenient option for adjusting the parameters to different workpieces.
The data set that is currently selected is displayed in the parameter data under “Production Setup.” This data is also the current parameters with which the ejector is working. They can be viewed using the menu.
In IO-Link mode, display the parameter data set (P-0 to P-3) currently in use:
1. Select the main menu
2. Press the button.
ð The parameter data set (P-0 to P-3) currently in use is briefly shown on the display.
In the default setting and in SIO mode, the P-0 production setup profile is selected.
7.25 Error Display
If an error occurs, it appears on the display in the form of an error code (“E number”). The vacuum switch’s response to an error depends on the type of error.
You can find a list of possible errors and the corresponding codes in the Warnings and Errors section.
Any operation being performed in the menu will be interrupted if an error occurs.
The error code can also be opened as a parameter using IO-Link.
7.26 Energy and Process Control (EPC)
In IO-Link mode, the energy and process control (EPC) function is available. It is subdivided into three modules:
• Condition monitoring (CM): Condition monitoring to increase system availability
• Energy monitoring (EM): Energy monitoring to optimize the vacuum system’s energy consumption
• Predictive maintenance (PM): Predictive maintenance to increase the performance and quality of the gripping systems.
EN-US · 30.30.01.01484 · 00 · 01/21 33 / 72
General Description of Functions
7.26.1 Condition Monitoring (CM)
Monitoring the valve switching frequency:
When the air saving function is activated and there is a high leakage level in the gripping system, the ejector switches between the suction and suction-off states very frequently. The number of valve switching procedures thus increases rapidly within a short time. To protect the ejector and increase its service life, the ejector switches the air saving function off automatically at a switching frequency of more than 6 times every 3 seconds and activates continuous suction; the ejector then remains in the suction state. In
IO-Link mode, the appropriate condition monitoring warning is also set. In addition, the system status light switches to yellow.
The basic monitoring for the valve protection function is also active in SIO mode.
Schematic diagram of the valve switching frequency
Vacuum
[mbar]
Suction ON Time [s]
With the [ dC5
= on
] setting, continuous suction is deactivated, and the ejector continues in control mode despite a high leakage rate or control frequency greater than 6 times per 3 s.
Monitoring the Control:
If the vacuum limit value H1 is never reached during the suction cycle, the “H1 not reached” condition monitoring warning is triggered and the system status light switches to yellow.
This warning is available at the end of the current suction phase and remains active until the next suction cycle.
Measuring and monitoring the evacuation times: t0 is the time from the beginning of a suction cycle to when the vacuum limit value H2 is reached (in ms).
t1 is the time from when the vacuum limit value H2 is reached to when the vacuum limit value H1 is reached (in ms).
34 / 72 EN-US · 30.30.01.01484 · 00 · 01/21
General Description of Functions
Evacuation times t0 and t1
Vacuum
[mbar]
Suction ON Time [s]
If the measured evacuation time t1 (from H2 to H1) exceeds the specified value [t-1], the “Evacuation time longer than t-1” condition monitoring warning is triggered and the system status light switches to yellow.
The specified value for the max. permitted evacuation time can be set under the [ t-1
] menu item in the configuration menu or via IO-Link. Setting the value to “0” deactivates monitoring. The maximum permitted evacuation time setting is 9.99 seconds.
Leakage monitoring:
In control mode ([ ctr
] = [ on5
]), the loss of vacuum within a certain period is monitored (mbar/s). There are two possible statuses.
Leakage L < permitted value -L-
If the leakage is lower than the set value, the vacuum continues to fall until it reaches the vacuum limit value H1-h1, and the ejector begins with suction again (normal control mode).
The condition monitoring warning is not activated and there is no effect on the system status light.
Leakage L > permitted value -L-
If the leakage is higher than the value, the ejector readjusts immediately.
If the permitted leakage is exceeded twice, the ejector switches to continuous suction.
The condition monitoring warning is activated and the system status light switches to yellow.
Vacuum Vacuum
H1
H1
H1-h1
H-h1
Time
Time
EN-US · 30.30.01.01484 · 00 · 01/21 35 / 72
General Description of Functions
Dynamic pressure monitoring:
If possible, a dynamic pressure measurement is taken at the start of every suction cycle. The result of this measurement is compared to the vacuum limit values set for H1 and H2.
If the dynamic pressure is greater than (H2 - h2) but less than H1, the corresponding condition monitoring warning will be set and the system status light will switch to yellow.
Leakage level evaluation:
This function determines the average leakage during the last suction cycle, divides it into subareas and makes it available as a parameter via IO-Link.
Autoset
The CM Autoset IO-Link function in the process output data allows the condition monitoring parameters for maximum permitted leakage [
-L-
] and the evacuation time [ t-1
] to be set automatically. The actual values from the last suction cycle are combined with additional tolerance and stored.
7.26.2 Energy Monitoring (EM)
To optimize the energy efficiency of the vacuum gripping systems, the ejector provides functions for measuring and displaying energy consumption.
Percentage-based air consumption measurement:
The ejector calculates the air consumption from the last suction cycle as a percentage. This value corresponds to the ratio for the full duration of the suction cycle and the active suction and blow off times.
Absolute air consumption volume:
An externally recorded pressure value can be supplied using the IO-Link process data. If this value is available, not only a percentage-based air consumption measurement, but also an absolute air consumption measurement can be performed. The actual air consumption of a suction cycle is calculated taking the system pressure and nozzle size into account.
An absolute air consumption measurement can be made only using a pressure value supplied externally via IO-Link.
The measured value for the absolute air consumption (air consumption per cycle) is reset at the start of suction and then continuously updated during the cycle. It can continue to change until after the end of blow-off.
Energy consumption measurement:
The ejector determines the electrical energy consumed during a suction cycle, including the energy it consumes itself and the energy consumed by the valve coils.
To determine the values for the air consumption as a percentage and the electrical energy consumption, the neutral phase of the suction cycle must also be taken into account. Therefore, the measured values can only ever be updated when the next suction cycle begins. Throughout the cycle, the measured values displayed then represent the results from the previous cycle.
7.26.3 Predictive Maintenance (PM)
For early detection of wear and other impairments to the vacuum gripper system, the ejector features functions for detecting trends in the quality and performance of the system. The leakage and dynamic pressure are measured for this purpose.
Measurement of leakage:
The leakage (represented as the vacuum drop per time unit in mbar/s) after the control function interrupts suction because the vacuum limit value H1 has been reached is measured.
36 / 72 EN-US · 30.30.01.01484 · 00 · 01/21
General Description of Functions
The measured value for the leakage rate and the related quality assessment in percent are reset at the start of every suction cycle and constantly updated during the cycle as moving averages. The values therefore remain stable until after the suction cycle is complete.
Measurement of dynamic pressure:
This measures the system vacuum achieved during unobstructed suction. The duration of the measurement is approx. 1 second. Therefore, to evaluate a valid dynamic pressure, uninterrupted suction is required for at least 1 second after starting the suction, i.e. the suction point must not be covered by a part.
Measured values below 5 mbar or above the vacuum limit value H1 are not regarded as valid dynamic pressure measurements and are rejected. The result of the last valid measurement is retained. Measured values that are higher than the vacuum limit value (H2-h2) and simultaneously lower than vacuum limit value H1 result in a condition monitoring event.
The dynamic pressure (vacuum during unobstructed suction) and the related performance assessment in percent are initially unknown when the ejector is switched on. As soon as a dynamic pressure measurement can be performed, they are updated and retain their values until the next dynamic pressure measurement.
Quality assessment:
To evaluate the overall gripping system, the ejector calculates a quality rating based on the measured system leakage. The greater the leakage in the system, the worse the quality rating of the gripping system.
Conversely, low leakage results in a high quality rating.
Performance calculation:
Similar to the quality assessment, the performance calculation is used to evaluate the system status. The performance of the gripping system can be assessed based on the determined dynamic pressure. Optimally configured gripping systems lead to low dynamic pressure and thus to high performance. Conversely, poorly configured systems result in low performance. Dynamic pressure events that exceed the vacuum limit value (H2-h2) always result in a performance rating of 0%. A dynamic pressure value of
0 mbar (indicator that a valid measurement was not obtained) also results in a performance rating of 0%.
7.26.4 Diagnostic Buffer
The condition monitoring warnings described above and the general error messages from the device are saved in an integrated diagnostic buffer. The content of this memory is made up of the last 38 events, starting with the most recent, and can be read out via an IO-Link parameter. For each event, the current reading of the suction cycle counter cc1 is also saved to allow subsequent temporal assignment of the events to other processes in the system. See the associated IO-Link Data Dictionary for the actual data display of the diagnostic buffer. The recording of these events is also active in SIO mode and the contents of the memory is retained after a power failure.
The memory is deleted manually using the IO-Link system command “Clear diagnostic buffer” or also by restoring the factory settings on the device.
7.26.5 EPC Data Buffer
The ejector provides a ten-stage data buffer to enable long-term monitoring and trend analysis of the most important key figures in a handling process. The current measured values for the evacuation time t1, leakage rate and dynamic pressure (vacuum during unobstructed intake), which are determined during the suction cycle, can be saved in this buffer. The values are saved automatically, always together with the execution of the autoset function in the condition monitoring area described above. For each data record, the current reading of the suction cycle counter cc1 is also saved to allow subsequent temporal assignment to other processes in the system. The contents of the EPC data buffer can be read out via an IO-Link parameter. See the associated IO-Link Data Dictionary for the actual data display of this buffer. The contents of the memory remains intact after a power failure.
EN-US · 30.30.01.01484 · 00 · 01/21 37 / 72
General Description of Functions
7.26.6 EPC Values in the Process Data
To quickly and easily capture the most important results from the condition monitoring [CM], energy monitoring and predictive maintenance functions, these are also made available via the process input data of the device. The top 3 bytes of the process output data are also configured as a multifunctional data range, consisting of an 8 bit value (“EPC Value 1”) and a 16 bit value (“EPC Value 2”).
The contents of this data that are currently supplied can be switched via the Process Data Out using the 2
“EPC-Select” bits.
The four possible ways in which this data is configured are listed in the table below:
EPC Values 1
PD Out
EPC-Select
00
01
10
11
PD In Byte 1
EPC Value 1
Current inlet pressure (unit 0.1 mbar)
Condition monitoring
Leakage rate (unit 1 mbar/s)
Supply voltage (unit 0.1 V)
0
1
1
1
EPC-Select Acknowledge
EPC value 2
PD Out
EPC-Select
00
01
10
11
PD In Byte 2
EPC Value 2
Current vacuum value (unit 1 mbar)
Evacuation time t1 (unit 1 ms)
Last measured dynamic pressure (unit 1 mbar)
Air consumption in the last cycle (unit 0.1 NL)
0
1
1
1
EPC-Select Acknowledge
The switch is made depending on the structure of the automation system with some time delay. However, to ensure that the different pairs of values can be read efficiently through a controller program, the bit
EPC-Select-Acknowledge is provided in the process input data. The bit always accepts the values shown in the table.
To read out all EPC values, the procedure illustrated in the following diagram is recommended:
1. Start with EPC-Select = 00.
2. Create the selection for the next value pair you require (e.g. EPC-Select = 01)
3. Wait until the EPC-Select-Acknowledge bit changes from 0 to 1.
ð The transmitted values correspond to the selection you have created, and can be adopted by the control system.
4. Switch back to EPC-Select = 00.
5. Wait until the EPC-Select-Acknowledge bit from the device is reset to 0.
6. Proceed in the same way for the next value pair (e.g. EPC-Select = 10).
The following diagram illustrates the sequence for the EPC system query.
38 / 72 EN-US · 30.30.01.01484 · 00 · 01/21
General Description of Functions
11
"EPC-Select"
[PDOut 0.5 …0.4]
01
10
00 00 00
“EPC-Select-Acknowledge"
[PDIn 0.3]
“EPC Value 1”
[PDIn 1]
"EPC-Value 2"
[PDIn 3 … 2]
Pressur e
CM Pressur e
Leakage Pressur e
Voltage Pressur e
Vacuum Evac. Time Vacuum
Dynamic pressure
Vacuum Air cons.
Vacuum
Controller applies valid EPC values
EN-US · 30.30.01.01484 · 00 · 01/21 39 / 72
Transport and Storage
8 Transport and Storage
8.1 Checking the Delivery
The scope of delivery can be found in the order confirmation. The weights and dimensions are listed in the delivery notes.
1. Compare the entire delivery with the supplied delivery notes to make sure nothing is missing.
2. Damage caused by defective packaging or occurring in transit must be reported immediately to the carrier and J. Schmalz GmbH.
40 / 72 EN-US · 30.30.01.01484 · 00 · 01/21
Installation
9 Installation
9.1 Installation Instructions
CAUTION
Improper installation or maintenance
Personal injury or damage to property
4 During installation and maintenance, make sure that the ejector is disconnected and depressurized and that it cannot be switched on again without authorization.
For safe installation, the following instructions must be observed:
1. Use only the connections, mounting holes and attachment materials that have been provided.
2. Carry out mounting and removal only when the device is in an idle, depressurized state.
3. Pneumatic and electrical line connections must be securely connected and attached to the ejector.
9.2 Mounting
The ejector may be installed in any position.
There are two 4.4 mm mounting holes for mounting the ejector.
A DIN rail mount for DIN rail TS35 can be used as a mounting option.
2
1
1 DIN rail mount for TS35 DIN rail, incl. plastic tapping screws
Max. tightening torque 0.5 Nm
2 2x M4 fastening screws with washers
When mounting with fastening screws, use M4 washers (2 Nm max. tightening torque).
For the start of operations, the ejector must be connected to the control via the connection plug with a connection cable. The compressed air required to generate the vacuum is connected via the compressed air connection. The compressed air supply must be supplied by the higher-level machine.
EN-US · 30.30.01.01484 · 00 · 01/21 41 / 72
Installation
The vacuum circuit is connected to the vacuum connection.
The installation process is described and explained in detail below.
9.3 Pneumatic Connection
CAUTION
Compressed air or vacuum in direct contact with the eye
Severe eye injury
4 Wear eye protection
4 Do not look into compressed air openings
4 Do not look into the silencer air stream
4 Do not look into vacuum openings, e.g. suction cups
CAUTION
Noise pollution due to incorrect installation of the pressure and vacuum connections
Hearing damage
4 Correct installation.
4 Wear ear protectors.
9.3.1 Connecting the Compressed Air and Vacuum
WARNING
Activating the compressed air causes the ejector module to be forced out of the hole.
Serious personal injury
4 Before activating the compressed air supply, make sure that the ejector module is fixed in place by the holder cap.
4 Wear eye protection
The G1/8" thread compressed air connection is marked with the number 1 on the ejector.
4 Connect the compressed air hose. The max. tightening torque is 3 Nm.
The G1/8" vacuum connection is marked with the number 2 on the ejector.
4 Connect the vacuum hose. The max. tightening torque is 3 Nm.
9.3.2 Instructions for the Pneumatic Connection
Use only screw unions with cylindrical G-threads for the compressed air and vacuum connection!
To ensure problem-free operation and a long service life for the product, only use adequately maintained compressed air and take the following requirements into account:
• Use of air or neutral gas in accordance with EN 983, filtered 5 μm, oiled or unoiled.
• Dirt particles or foreign bodies in the product connections, hoses or pipelines can lead to partial or complete malfunction.
42 / 72 EN-US · 30.30.01.01484 · 00 · 01/21
Installation
1. Shorten the hoses and pipelines as much as possible.
2. Keep hose lines free of bends and crimps.
3. Only use a hose or pipe with the recommended internal diameter to connect the product; otherwise, use the next largest diameter.
- On the compressed air side, ensure that the internal diameter has the dimensions required for the product to achieve its performance data.
- On the vacuum side, ensure that the internal diameters have the necessary dimensions for preventing high flow resistance. If the selected internal diameter is too small, the flow restrictor and the evacuation times increase and the blow off times are extended.
The following table shows the recommended line cross-sections (internal diameter):
Performance class
SCPSi UHV HD 07
SCPSi UHV HD 11
SCPSi UHV HD 16
4
4
4
Line cross-section (internal diameter) in mm 1) pressure side Vacuum side
4
4
6
1) Based on a maximum hose length of 2 m.
4 For longer hose lengths, the cross-sections must also be larger.
9.4 Electrical connection
WARNING
Electric shock
Risk of injury
4 Operate the product using a power supply unit with protected extra-low voltage
(PELV).
WARNING
By activating/deactivating the product, output signals lead to an action in the production process!
Personal injury
4 Avoid possible danger zone.
4 Remain vigilant.
NOTE
Incorrect power supply
Destruction of the integrated electronics
4 Operate the product using a power supply unit with protected extra-low voltage
(PELV).
4 The system must incorporate safe electrical cut-off of the power supply in compliance with EN60204.
4 Do not connect or disconnect the connector under tension and/or when voltage is applied.
EN-US · 30.30.01.01484 · 00 · 01/21 43 / 72
Installation
NOTE
Power load too high
Destruction of the vacuum switch, as there is no protection against overloading!
4 Prevent constant load currents > 0.1 A.
The electrical connection is established using a 5-pin M12 connector that supplies the vacuum switch with voltage, and contains the two input signals and the output signal. The inputs and outputs are not electrically isolated from one another.
The maximum line length for the supply voltage, the signal inputs and the signal output is:
• 30 m in SIO mode
• 20 m in IO-Link mode
Connect the ejector electrically using the plug connection 1 shown in the figure
1
1 Electrical connection plug, M12, 5-pin
ü Prepare a connection cable with an M12 5-pin connector (supplied by the customer).
4 Attach the connection cable to the electrical connection (1) on the ejector (max. tightening torque = hand-tight).
9.4.1 PIN Assignment
PIN assignment, 5-pin M12 connector
M12 connector PIN
1
2
3
4
Wire color 1)
Brown
White
Blue
Black
Symbol Function
U
S/A
IN1
Supply voltage for sensors/actuators
“Suction” signal input
GND
S/A
OUT
IN2
Ground for sensors/actuators
“Part Present” check signal output (H2/ h2)
“Blow off” signal input 5 Gray
1) When using Schmalz connection cable part no. 21.04.05.00080
44 / 72 EN-US · 30.30.01.01484 · 00 · 01/21
Installation
9.4.2 PIN Assignment in IO-Link Mode
PIN assignment, 5-pin M12 connector
M12 connector PIN
3
4
5
1
2
Wire color 1)
Brown
White
Blue
Black
Gray
Symbol Function
U
S/A
—
GND
S/A
C/Q
—
Supply voltage for sensors/actuators
—
Ground for sensors/actuators
IO-Link communication
—
1) When using Schmalz connection cable part no. 21.04.05.00080
9.5 Start of Operations
A typical handling cycle is divided into the following three phases: pickup, blowoff and idle.
To check whether sufficient vacuum has built up, the limit value H2 is monitored by an integrated vacuum sensor during suction and output to the higher-level controller via OUT.
Phase
1
Switching step
1
NC version
Signal
IN1
Status
Suction ON
Signal
NO version
IN1
Status
Suction ON
2 OUT Vacuum > H2 OUT Vacuum > H2
2
3
3
4
5
6
IN1
IN2
OUT
IN2
Suction OFF
Blow off ON
Vacuum <
(H2-h2)
Blow off OFF
IN1
IN2
OUT
IN2
Suction OFF
Blow off ON
Vacuum <
(H2-h2)
Blow off OFF active.
Signal status changes from inactive to active. Signal status changes from active to in-
EN-US · 30.30.01.01484 · 00 · 01/21 45 / 72
Operation
10 Operation
10.1 Safety Instructions for Operation
CAUTION
Depending on the purity of the ambient air, the exhaust air can contain particles, which escape from the exhaust air outlet at high speed.
Eye injuries
4 Do not look into the exhaust air flow
4 Wear eye protection
CAUTION
When the system is started in automatic operation, components move without advanced warning.
Risk of injury
4 Ensure that the danger zone of the machine or system is free of persons during automatic operation.
WARNING
Change of output signals when product is switched on or plug is connected
Risk of injury to persons and damage to property due to uncontrolled movements of the higher-level machine/system!
4 The electrical connection must be performed only by specialists who can evaluate the effects of signal changes on the overall system.
WARNING
Extraction of hazardous media, liquids or bulk material
Personal injury or damage to property!
4 Do not extract harmful media such as dust, oil mists, vapors, aerosols etc.
4 Do not extract aggressive gases or media such as acids, acid fumes, bases, biocides, disinfectants or detergents.
4 Do not extract liquids or bulk materials, e.g. granulates.
10.2 General Preparations
Always carry out the following tasks before activating the system:
1. Before each start of operations, check that the safety features are in perfect condition.
2. Check the ejector for visible damage and deal with any problems immediately (or notify your supervisor).
3. Ensure that only authorized personnel are present in the working area of the machine or system and that no other personnel are put in danger by switching on the machine.
There must be no people in the system danger area while it is in operation.
46 / 72 EN-US · 30.30.01.01484 · 00 · 01/21
Operation
10.3 Typical Suction Cycles
The diagrams below show some typical vacuum processes during a suction cycle. The diagrams also indicate the times at which EPC measured values are updated.
Handling cycle with dynamic pressure measurement and average leakage:
Typical suction cycle
SUCTION BLOW
OFF
NEUTRAL SUCTION
Vacuum t
Condition monitoring
Evacuation time t0
Evacuation time t1
Dynamic pressure
Leakage
Air consumption
El. energy consumption
EN-US · 30.30.01.01484 · 00 · 01/21 47 / 72
Operation
Handling cycle with dynamic pressure measurement and excessive leakage:
Typical suction cycle
SUCTION BLOW
OFF
NEUTRAL
Vacuum
SUCTION
Condition monitoring
Evacuation time t0
Evacuation time t1
Dynamic pressure
Leakage
Air consumption
El. energy consumption
Handling cycle with leakage > L and readjustment:
Typical suction cycle
SUCTION
Vacuum
BLOW
OFF
NEUTRAL SUCTION t t
Condition monitoring
Evacuation time t0
Evacuation time t1
Dynamic pressure
Leakage
Air consumption
El. energy consumption
48 / 72 EN-US · 30.30.01.01484 · 00 · 01/21
Handling cycle with very high leakage (H1 is not reached):
Typical suction cycle
SUCTION
Vacuum
BLOW
OFF
NEUTRAL SUCTION
Operation
Condition monitoring
Evacuation time t0
Evacuation time t1
Dynamic pressure
Leakage
Air consumption
El. energy consumption
Handling cycle with excessive evacuation time t1:
Typical suction cycle
SUCTION
Vacuum
BLOW
OFF
NEUTRAL SUCTION t
Condition monitoring
Evacuation time t0
Evacuation time t1
Dynamic pressure
Leakage
Air consumption
El. energy consumption
EN-US · 30.30.01.01484 · 00 · 01/21 t
49 / 72
Troubleshooting
11 Troubleshooting
11.1 Help with Faults
Fault
No IO-Link communication
Ejector does not respond
Vacuum level is not reached or vacuum is created too slowly
Load cannot be held
Cause
Incorrect electrical connection
Master not correctly configured
IODD connection does not work
No actuator supply voltage
No compressed air supply
Ejector is faulty.
Solution
4 Check electrical connection and pin assignment
4 Check the master configuration to see whether the port is set to IO-Link
4 Check for the appropriate
IODD; the IODD is dependent on the number of ejectors
4 Check electrical connection and pin assignment
4 Check the compressed air supply.
4 Check the ejector and contact Schmalz Service if necessary.
4 Replace screen Press-in screen in contaminated
Silencer is dirty
Hose or screw unions are leaking
Leakage at suction cup
Operating pressure too low
Internal diameter of hose line too small
Vacuum level too low
Suction cup too small
4 Replace silencer insert
4 Replace or seal components
4 Eliminate leakage from suction cup
4 Increase operating pressure, observe maximum limits
4 Observe recommendations for hose diameter
4 Increase the control range for the air saving function
4 Select a larger suction cup
50 / 72 EN-US · 30.30.01.01484 · 00 · 01/21
Warnings and Errors
12 Warnings and Errors
12.1 Error Messages in SIO Operation
When a known error occurs, this is reported in the form of an error number. In SIO mode, error messages are shown on the display. An “ E ” followed by the error number appears on the display.
The following table shows all the error codes:
Code displayed
E01
E02
E03
E07
E08
E12
E17
E18
FFF
-FF
Explanation
Electronics error – internal data management, EEPROM
Electronics error – internal communication
Zero-point adjustment of the vacuum sensor outside ± 3% FS
Supply voltage is too low
IO-Link communication is interrupted
Short circuit on output 2
Supply voltage is too high
Input pressure outside operating range
Present vacuum exceeds the measurement range
Overpressure in vacuum circuit; this normally happens exclusively in blow off mode.
Error codes in SIO mode
The error [E01] remains on the display after being shown once. Delete the error by switching off the power supply. If this error occurs again after the power supply is switched back on, then the device must be replaced.
12.2 Warnings and Error Messages in IO-Link Mode
In IO-Link mode, status information is available in addition to the error messages displayed in SIO mode.
The table below shows the IO-Link events:
Any condition monitoring events that occur during the suction cycle cause the system status light to immediately switch from green to yellow. The specific event that caused this switch can be seen in the “Condition monitoring” IO-Link parameter.
EN-US · 30.30.01.01484 · 00 · 01/21 51 / 72
Warnings and Errors
Any condition monitoring events that occur during the suction cycle cause the system status indicator light to immediately switch from green to yellow/orange. The event that caused this switch can be seen in the “Condition monitoring” IO-Link parameter.
The table below explains the coding of the condition monitoring warnings:
Bit
2
3
4
0
1
5
7
Event
Valve protection function activated
Set limit value t-1 for evacuation time exceeded
Set leakage limit value -L- exceeded
Limit value H1 was not reached
Dynamic pressure > (H2 - h2) and < H1
Supply voltage U
S
outside the operating range
Input pressure outside operating range
Update
Cyclic
Cyclic
Cyclic
Cyclic
As soon as a corresponding dynamic pressure value has been determined
Constant
Constant
The four bits with the lowest values describe events that can only occur once per suction cycle. They are reset at the start of every suction cycle and remain stable until after suctioning has finished.
Bit number 4, which describes dynamic overpressure, is initially deleted when the device is switched on and is updated when a dynamic pressure value is detected.
Bits 5 and 7 are regularly updated independently of the suction cycle, and reflect the current values for the supply voltage and system pressure.
The values measured by the condition monitoring system, namely the evacuation times t
0
and t
1
and the leakage value L, are reset at the beginning of the suction process and updated once they have been measured.
12.3 System Status Light in IO-Link Mode
The overall status of the ejector system is displayed as a traffic light using 3 bits in process data input byte
0. All warnings and errors are taken into account when defining the status of the traffic lights.
This basic display provides immediate information about the status of the ejector with all its input and output parameters.
System status displayed
Green
Yellow
Red
Description of the status
System is working perfectly with optimal operating parameters
Warning – Condition monitoring warnings in place; ejector system not functioning perfectly
Check operating parameters
Error – Error code provided in parameter error; safe operation of the ejector within the operating limits is no longer ensured
• Cease operation
• Check the system
IO-Link system status light
52 / 72 EN-US · 30.30.01.01484 · 00 · 01/21
Maintenance
13 Maintenance
13.1 Safety
Maintenance work may only be carried out by qualified personnel.
4 Create atmospheric pressure in the ejector's compressed air circuit before working on the system!
WARNING
Risk of injury due to incorrect maintenance or troubleshooting
4 Check the proper functioning of the product, especially the safety features, after every maintenance or troubleshooting operation.
NOTE
Incorrect maintenance work
Damage to the ejector!
4 Always switch off supply voltage before carrying out any maintenance work.
4 Secure it so that it cannot be switched back on.
4 The ejector must only be operated with a silencer and press-in screens.
13.2 Cleaning the Ejector
1. For cleaning, do not use aggressive cleaning agents such as industrial alcohol, white spirit or thinners. Only use cleaning agents with pH 7–12.
2. Remove dirt on the exterior of the device with a soft cloth and soap suds at a maximum temperature of 60° C. Make sure that the silencer is not soaked in soapy water.
3. Ensure that no moisture can reach the electrical connection or other electrical components.
13.3 Replacing the Silencer Insert
Heavy infiltration of dust, oil, and so on, may contaminate the silencer insert and reduce suction capacity.
Cleaning the silencer insert is not recommended due to the capillary effect of the porous material.
If the suction capacity decreases, replace the silencer insert:
ü Deactivate the ejector and disconnect it from the supply lines.
1. Unlock the silencer cover by turning the bayonet fastener 90°.
EN-US · 30.30.01.01484 · 00 · 01/21 53 / 72
Maintenance
1
2. Remove the silencer cover.
3. Replace the silencer insert (1).
13.4 Cleaning or Changing the Nozzle
The easy access to the silencer insert and nozzle provided by the silencer cover with bayonet fastener ensures that the nozzle is easy to clean and replace.
ü The ejector is deactivated and disconnected from the supply lines.
ü The silencer cover and silencer insert are removed (
(> See ch. Replacing the Silencer Insert, Page 53)
).
1. Pull the nozzle out of the holder.
ð The nozzle is removed together with the
O-ring.
2. Check the nozzle and clean or replace it if necessary.
54 / 72 EN-US · 30.30.01.01484 · 00 · 01/21
Maintenance
3. Install any cleaned or new nozzle in the correct position. Ensure that the O-ring is fitted.
O-Ring
13.5 Replacing the Press-In Screens
The vacuum and compressed air connections of the ejectors contain press-in screens. Dust, chippings and other solid materials may be deposited in the screens over time.
4 If you notice that the performance of the ejectors has declined, replace the screens.
13.6 Replacement of the Device with a Parameterization Server
The IO-Link protocol provides an automated process for transferring data when a device is replaced. For this Data storage mechanism, the IO-Link master mirrors all setting parameters for the device in a separate non-volatile memory. When a device is swapped for a new one of the same type, the setting parameters for the old device are automatically saved in the new device by the master.
ü The device is operated on a master with IO-Link version 1.1 or higher.
ü The Data storage feature in the configuration of the IO-Link port is activated.
4 Ensure that the new device is restored to the factory settings before it is connected to the IO-Link master. If necessary, reset the device to the factory settings.
ð The device parameters are automatically mirrored in the master when the device is configured using an IO-Link configuration tool.
ð Changes to the parameters made in the user menu on the device or via NFC are mirrored in the master.
Changes to the parameters made by a PLC program using a function module are not automatically mirrored in the master.
4 Manually mirroring data: After changing all the required parameters, execute ISDU write access to the “System Command” parameter [0x0002] using the command “Force upload of parameter data into the master” (numerical value 0x05) (see Data Dictionary).
Use the Parameterization server function of the IO-Link master to ensure that no data is lost when switching the device.
EN-US · 30.30.01.01484 · 00 · 01/21 55 / 72
Warranty
14 Warranty
This system is guaranteed in accordance with our general terms of trade and delivery. The same applies to spare parts, provided that these are original parts supplied by us.
We are not liable for any damage resulting from the use of non-original spare parts or accessories.
The exclusive use of original spare parts is a prerequisite for the proper functioning of the ejector and for the validity of the warranty.
Wearing parts are not covered by the warranty.
Opening the ejector will damage the “tested” labels. This voids the warranty.
56 / 72 EN-US · 30.30.01.01484 · 00 · 01/21
Spare and Wearing Parts, Accessories
15 Spare and Wearing Parts, Accessories
15.1 Spare and Wearing Parts
Maintenance work may only be carried out by qualified personnel.
4 WARNING! Risk of injury due to improper maintenance!
After performing any maintenance or repair work, check that the system is functioning correctly, particularly the safety features.
NOTE
Incorrect maintenance work
Damage to the ejector!
4 Always switch off the supply voltage before carrying out maintenance work.
4 Secure it so that it cannot be switched back on.
4 Ejector must be operated only with a silencer and press-in screens.
The following list contains the most important spare and wearing parts.
Part no.
10.02.02.05030
10.02.02.03376
10.02.02.06259
10.02.02.06279
10.02.02.05052
10.02.02.06343
Designation
Silencer insert
Screen
Ejector vacuum kit (assembled); size 07 nozzle set
VACU-SET 07 12.80x76.60 SCPS
Ejector vacuum kit (assembled); size 11 nozzle set
VACU-SET 11 12.80x76.60 SCPS
Ejector vacuum kit (assembled); size 16 nozzle set
VACU-SET 16 12.80x76.60 SCPS
Ejector maintenance kit
WART SCPS/SCPSi-O-Ring-SET
Legend:
• W earing part = W
• S pare part = S
15.2 Accessories
Part no.
10.02.02.00158
21.04.05.00080
Designation
Connection cable
Connection cable
Note
M12, 5-pin, to 5-pin M12 connector, 1 m
M12, 5-pin, with open end, 5 m
S
S
S
S
Legend
W
S
EN-US · 30.30.01.01484 · 00 · 01/21 57 / 72
Decommissioning and Recycling
16 Decommissioning and Recycling
16.1 Disposing of the Ejector
1. Dispose of the product properly after replacement or decommissioning.
2. Observe the country-specific guidelines and legal obligations for waste prevention and disposal.
16.2 Materials Used
Component
Housing
Inner components
Silencer insert
Screws
Seals
Lubrication
Material
PA6-GF, PC-ABS
Aluminum alloy, anodized aluminum alloy, brass, galvanized steel, stainlesssteel, PU, POM
Porous PE
Galvanized steel
Nitrile rubber (NBR)
Silicone-free
58 / 72 EN-US · 30.30.01.01484 · 00 · 01/21
Attachment
17 Attachment
See also
2
SCPSi_V2 Data Dictionary 21.10.01.00065_02 2014-08-29.pdf [ } 61]
17.1 Overview of the Display Codes
Code x-1 h-1 x-2
Parameter
Limit value H1
Hysteresis value h1
Limit value H2 h-2 tbL
CAL cc1 cc2
5oc
Hysteresis value h2
Blow off time
Zero-point adjustment
Total counter 1
Total counter 2
Software function
Type Part number
5nr Serial number
Ctr Energy-saving function
(control) on5 Control function on with leakage monitoring dc5 Deactivate auto. control shutoff t-1
-LbLo
-E-
J-t
E-t o-2 no nc tYP
PnP nPn uni
-bA
-PA
Evacuation time
Leakage value
Blow off function
“External” blow off
“Internal” blow off
Comment
Switch-off value for air-saving function/control
Hysteresis of control
Switch-on value of the “Part Present” signal output (when the NO output is configured)
Hysteresis of “Part Present” check signal output
Set the blow off time for time-controlled blow off
Calibrating the vacuum sensor
Counter for suction cycles (“suction” signal input)
Counter for valve switching frequency
Displays the current software version
Displays the part number of the ejector
Displays the serial number of the ejector
Setting the control function
Control with leak monitoring active
Suppresses the automatic valve protection function when set to
YE5
.
Cannot be activated when
Ctr
= off
.
Set the maximum permitted evacuation time
Set the maximum permitted leakage
Menu for configuring the blow off function
Selection of externally controlled blow off
Select internally controlled blow off (triggered internally, time-adjustable)
Selection of externally controlled blow off (triggered externally; time-adjustable)
Menu for configuring the signal output
“External time-controlled” blow off
Signal Output
Normally open contact Setting of the signal output as a normally open contact
Normally closed contact Setting of the signal output as a normally closed contact
Signal Type
PNP signal type
NPN signal type
Vacuum unit
Menu for configuration of the signal type (NPN/PNP)
All input and output signals switch according to PNP (input / output on = 24 V)
All input and output signals switch according to NPN (input / output on = 0 V)
Setting the vacuum unit
Vacuum level in mbar
Vacuum level in kPa
The displayed vacuum is shown in mbar.
The displayed vacuum level is shown in kPa.
EN-US · 30.30.01.01484 · 00 · 01/21 59 / 72
Attachment
Code
-iH dLY dPY
5td
Red
Eco
Pin
Loc
Unc rE5
Parameter
Vacuum level in inHg
Switch-off delay
Display rotation
Default display
Rotated display
ECO mode
PIN
Menu locked
Menu unlocked
Reset
Comment
The displayed vacuum is shown in inches of Hg.
Setting the switch-off delay for OUT2 (delay)
Setting the display position (rotation)
Display is not rotated
Display is rotated by 180°
Setting ECO mode
Entry of the PIN for unlocking the menu
Parameter modification locked.
The buttons and menus are unlocked.
All adjustable values are reset to the factory settings.
17.2 EC Conformity
EU Conformity Declaration
The manufacturer Schmalz confirms that the product Ejector described in these Operating instructions fulfills the following applicable EU directives:
2014/30/EU
2011/65/EU
Electromagnetic Compatibility
RoHS Directive
The following harmonized standards were applied:
EN ISO 12100
EN 61000-6-3+A1+AC
EN 61000-6-2+AC
EN IEC 63000
Safety of machinery — General principles for design — Risk assessment and risk reduction
Electromagnetic compatibility (EMC) - Part 6-3: Generic standards - Emission standard for residential, commercial and light-industrial environments
Electromagnetic compatibility (EMC) - Part 6-2: Generic standards - Immunity for industrial environments
Technical documentation for the assessment of electrical and electronic products with respect to the restriction of hazardous substances
The EU Declaration of Conformity valid at the time of product delivery is delivered with product or made available online. The standards and directives cited here reflect the status at the time of publication of the Operating instructions.
60 / 72 EN-US · 30.30.01.01484 · 00 · 01/21
IO-Link Data Dictionary
21.10.01.00065/02
IO-Link Implementation
Vendor ID
Device ID
SIO-Mode
Baudrate
Minimum cycle time
Processdata input
Processdata output
Process Data
Process Data In
PD In Byte 0
PD In Byte 1
PD In Byte 2
PD In Byte 3
Name
Signal H2 (part present)
Signal H1 (automatic air saving function)
-
CM-Autoset acknowledged
EPC-Select acknowledged
Device status - green
Device status - yellow
Device status - red
EPC value 1
EPC value 2, high-byte
EPC value 2, low-byte
4
5
6
7
7…0
7…0
7…0
Bits
0
1
2
3
J. Schmalz GmbH
SCPSi series
29.08.2014
J. Schmalz GmbH
Aacher Straße 29, D 72293 Glatten
Tel.: +49(0)7443/2403-0
Fax: +49(0)7443/2403-259 [email protected]
IO-Link Version 1.1
234 (0x00EA)
100243 (0x018793)
Yes
38.4 kBd (COM2)
3.5 ms
4 byte
2 byte
IO-Link Version 1.0 (legacy mode)
234 (0x00EA)
100242 (0x018792)
Yes
38.4 kBd (COM2)
3.0 ms
1 byte
1 byte
1 of 11 ro ro ro ro ro ro ro ro ro ro ro
Access Availability
IO-Link V1.1, V1.0
IO-Link V1.1, V1.0
-
IO-Link V1.1, V1.0
IO-Link V1.1 only
IO-Link V1.1, V1.0
IO-Link V1.1, V1.0
IO-Link V1.1, V1.0
IO-Link V1.1 only
IO-Link V1.1 only
IO-Link V1.1 only
Remark
Vacuum is over H2 & not yet under H2-h2
Vacuum is over H1 & not yet under H1-h1 unused
Acknowledge that the Autoset function has been completed
Acknowledge that EPC values 1 and 2 have been switched according to
EPC-Select:
0 - EPC-Select = 00
1 - otherwise
Device is working optimally
Device is working but there are warnings
Device is not working properly, there are errors
EPC value 1 (byte)
Holds 8bit value as selected by EPC-Select
(see PD Out Byte 0)
EPC value 2 (word)
Holds 16bit value as selected by EPC-Select
(see PD Out Byte 0)
SCPSi Data Dictionary
IO-Link Data Dictionary
21.10.01.00065/02
Process Data Out Name
Vacuum
Blow-off
Vacuum with forced control
CM Autoset
PD Out Byte 0
EPC-Select
Bits
2
3
0
1
5..4
7..6
7…0
SCPSi series
29.08.2014
Access wo wo wo wo
Availability
IO-Link V1.1, V1.0
IO-Link V1.1, V1.0
IO-Link V1.1, V1.0
IO-Link V1.1, V1.0
wo wo wo
IO-Link V1.1 only
IO-Link V1.1, V1.0
IO-Link V1.1 only
J. Schmalz GmbH
Aacher Straße 29, D 72293 Glatten
Tel.: +49(0)7443/2403-0
Fax: +49(0)7443/2403-259 [email protected]
Remark
Vacuum on/off
Activate Blow-off
Vacuum on/off with continuous suction disabled
(regardless of dCS parameter)
Perform CM Autoset function and save EPC data in buffer
Select the function of EPC values 1 and 2 in PD In
(content is 2 bit binary coded integer)
0:
EPC value 1 = Input pressure (0.1 bar)
EPC value 2 = System vacuum (1 mbar)
1:
EPC value 1 = CM-Warnings (see ISDU 146 for bit definitions)
EPC value 2 = Evacuation time t1 (1 msec)
2:
EPC value 1 = Leakage of last suction cycle (1 mbar/sec)
EPC value 2 = Last measured free-flow vacuum (1 mbar)
3:
EPC value 1 = Primary supply voltage (0.1 Volt)
EPC value 2 = Air consumption of last suction cycle (0.1 NL)
Select Production Profile
(content is 2-bit binary coded integer)
0: Activate Production Setup Profile P0
1: Activate Production Setup Profile P1
2: Activate Production Setup Profile P2
3: Activate Production Setup Profile P3
Pressure value from external sensor (unit: 0.1 bar)
Profile-Set
PD Out Byte 1 Input pressure
ISDU Parameters
(all ISDUs use subindex 0 only)
ISDU Index hex
Display
Appearance dec
16
Identification
0x0010 Vendor name
17 0x0011 Vendor text
Parameter
J. Schmalz GmbH
Data width Value range Access Default value
15 bytes
15 bytes
2 of 11 ro ro
J. Schmalz GmbH www.schmalz.com
Manufacturer designation
Internet address
Remark
SCPSi Data Dictionary
IO-Link Data Dictionary
21.10.01.00065/02
21
24
18
20
250
251
22
23
12
0x0012
0x0014
0x00FA Art
0x00FB
0x0016
0x0017 SoC
Product name
Product text
Article number
Article revision
Hardware revision
Firmware revision
0x0015 Snr
0x000C
Serial number
0x0018 Application specific tag
Parameter
Access Locks
Device access locks
77
69
0x004D Pin
Initial Setup
PIN code
0x0045 bLo Blow-off mode
71
73
0x0047 o-2
0x0049 tyP
OUT2 function
Signal type
75 0x004B dLY Output filter
74 0x004A uni Vacuum display unit
79
76
68
0x004F dpy Display rotation
0x004C Eco
Eco-Mode
Production Setup - Profile P0
0x0044 ctr Air saving function
J. Schmalz GmbH
8 bytes
30 bytes
14 bytes
2 bytes
2 bytes
4 bytes
9 bytes
0...32 bytes
2 bytes
2 bytes
0 - 7
0 - 999
1 byte
1 byte
1 byte
1 byte
1 byte
1 byte
1 byte
0 - 2
0 - 1
0 - 1
0 - 3
0 - 2
0 - 1
0 - 1
1 byte 0 - 2
3 of 11 rw rw
0
0
0
0
0
1
0
0
0 rw rw rw rw rw rw rw rw 1 ro ro ro rw ro ro ro ro
J. Schmalz GmbH
Aacher Straße 29, D 72293 Glatten
Tel.: +49(0)7443/2403-0
Fax: +49(0)7443/2403-259 [email protected]
SCPSi_V2 General product name
SCPSi 00 G2 NC M12-5 Order-Code
10.02.02.*
00
Order-Nr.
Article revision
03
2.01
000000001
***
Hardware revison
Firmware revision
Serial number
User string to store location or tooling information
SCPSi series
29.08.2014
Bit 0:parameter access lock (lock ISDU-write access)
Bit 1: data storage lock
Bit 2: local parameterization lock (lock menu editing)
0 = menu editing unlocked
>0 = menu editing locked with pin-code
0 = Externally controlled blow-off (-E-)
1 = Internally controlled blow-off – time-dependent (I-t)
2 = Externally controlled blow-off – time-dependent (E-t)
0 = NO
1 = NC
0 = PNP
1 = NPN
0 = Off
1 = 10ms
2 = 50ms
3 =200ms
0 = mbar
1 = kPa
2 = inHg
0 = standard
1 = rotated
0 = off
1 = on
0 = not active (off)
1 = active (on)
2 = active with supervision (onS)
SCPSi Data Dictionary
IO-Link Data Dictionary
21.10.01.00065/02
78
100
101
102
103
106
107
108
184
185
186
187
188
180
181
182
183
200
201
202
203
204
205
206
207
0x004E dCS Disable continuous suction
0x00B5
0x00B6
0x00B7
0x00B8
0x00B9
0x00BA
0x0064 H-1
0x0065 h-1
0x0066 H-2
0x0067 h-2
0x006A tbL
0x006B t-1
Setpoint H1
Hysteresis h1
Setpoint H2
Hysteresis h2
Duration automatic blow
Permissible evacuation time
0x006C -LPermissible leakage rate
0x00B4
Production Setup - Profile P1
Air saving function
Disable continuous suction
Setpoint H1
Hysteresis h1
Setpoint H2
Hysteresis h2
Duration automatic blow
0x00BB
0x00C9
Permissible evacuation time
0x00BC Permissible leakage rate
0x00C8
Production Setup - Profile P2
Air saving function
Disable continuous suction
0x00CA Setpoint H1
Hysteresis h1 0x00CB
0x00CC Setpoint H2
0x00CD
0x00CE
0x00CF
Hysteresis h2
Duration automatic blow
Permissible evacuation time
J. Schmalz GmbH
1 byte
1 byte
2 bytes
2 bytes
2 bytes
2 bytes
2 bytes
2 bytes
1 byte
1 byte
2 bytes
2 bytes
2 bytes
2 bytes
2 bytes
2 bytes
2 bytes
1 byte
2 bytes
2 bytes
2 bytes
2 bytes
2 bytes
2 bytes
2 bytes
0 - 1
998 >= H1 >= (H2+h1)
(H1-H2 >= h1 > 10
(H1-h1 >= H2 >= (h2+2)
(H2-2) >= h2 >= 10
100 - 9999
0, 10 - 9999
1 - 999 rw rw rw rw rw rw rw rw
0 - 2
0 - 1
998 >= H1 >= (H2+h1)
(H1-H2 >= h1 > 10
(H1-h1 >= H2 >= (h2+2)
(H2-2) >= h2 >= 10
100 - 9999
0, 10 - 9999
1 - 999 rw rw rw rw rw rw rw rw rw
0 - 2
0 - 1
998 >= H1 >= (H2+h1)
(H1-H2 >= h1 > 10
(H1-h1 >= H2 >= (h2+2)
(H2-2) >= h2 >= 10
100 - 9999
0, 10 - 9999 rw rw rw rw rw rw rw rw
4 of 11
1
0
750
150
550
10
200
2000
550
10
200
2000
250
1
0
750
150
0
750
150
550
10
200
2000
250
J. Schmalz GmbH
Aacher Straße 29, D 72293 Glatten
Tel.: +49(0)7443/2403-0
Fax: +49(0)7443/2403-259 [email protected]
0 = off
1 = on
Unit: 1 mbar
Unit: 1 mbar
Unit: 1 mbar
Unit: 1 mbar
Unit: 1 ms
Unit: 1 ms
Unit: 1 mbar/sec
Profile P-1
(selected by PD Out 0 - Profile-Set = 1)
SCPSi series
29.08.2014
Profile P-2
(selected by PD Out 0 - Profile-Set = 2)
SCPSi Data Dictionary
IO-Link Data Dictionary
21.10.01.00065/02
208
224
225
226
227
228
220
221
222
223
0x00D0 Permissible leakage rate
0x00DC
Production Setup - Profile P3
Air saving function
0x00DD
0x00DE
0x00DF
0x00E0
0x00E1
0x00E2
Disable continuous suction
Setpoint H1
Hysteresis h1
Setpoint H2
Hysteresis h2
Duration automatic blow
0x00E3 Permissible evacuation time
0x00E4
Commands
Permissible leakage rate
2 0x0002 System command
120 0x0078 CAL
123
40
0x007B rES
Observation
0x0028
41
64
66
65
0x0029
0x0040
0x0042
0x0041
Calibrate vacuum sensor
Restore to factory defaults
Process Data In Copy
Process Data Out Copy
System vacuum
Supply voltage
Input pressure
2 bytes
1 byte
1 byte
2 bytes
2 bytes
2 bytes
2 bytes
2 bytes
2 bytes
2 bytes
1 - 999 rw
0 - 2
0 - 1
998 >= H1 >= (H2+h1)
(H1-H2 >= h1 > 10
(H1-h1 >= H2 >= (h2+2)
(H2-2) >= h2 >= 10
100 - 9999
0, 10 - 9999
1 - 999 rw rw rw rw rw rw rw rw rw
250
550
10
200
2000
250
1
0
750
150
1 byte
1 byte
1 byte
1
1
1 byte (V1.0)
4 bytes (V1.1)
1 byte (V1.0)
2 bytes (V1.1)
2 bytes
2 bytes
2 bytes 0 - 99 wo wo wo ro ro ro ro rw 0
J. Schmalz GmbH 5 of 11
J. Schmalz GmbH
Aacher Straße 29, D 72293 Glatten
Tel.: +49(0)7443/2403-0
Fax: +49(0)7443/2403-259 [email protected]
Profile P-3
(selected by PD Out 0 - Profile-Set = 3)
SCPSi series
29.08.2014
0x05 (dec 5): Force upload of parameter data into the master
0x82 (dec 130): Restore device parameters to factory defaults
0xA4 (dec 164): Clear diagnostic buffer
0xA5 (dec 165): Calibrate vacuum sensor
1 = Calibrate vacuum sensor
(can also be executed by switching PD Out 0 Bits 2 and 3 simultaneously from 0 to 1)
1 = Restore to factory defaults
Copy of currently active process data input
Copy of currently active process data output
Current vacuum level (unit: 1 mbar)
Supply voltage as measured by the device (unit: 0.1 Volt)
Pressure value from external pressure sensor (unit: 0.1 bar)
SCPSi Data Dictionary
IO-Link Data Dictionary
21.10.01.00065/02
130
Diagnosis
Error
0x0082 Exx
Counter
0x008C cc1
Active error code
140 Vacuum-on counter
141 0x008D cc2
146.0
0x0092
Valve operating counter
Condition Monitoring [CM]
Condition monitoring
146.1
0x0092
146.2
0x0092
146.3
0x0092
146.4
0x0092
146.5
0x0092
146.6
0x0092
146.7
0x0092
Condition monitoring
Condition monitoring
Condition monitoring
Condition monitoring
Condition monitoring
Condition monitoring
Condition monitoring
147 0x0093 Leakage area
148
149
155
156
157
0x0094 Evacuation time t
0
0x0095 Evacuation time t
1
0x009B
Energy Monitoring [EM]
Air consumption per cycle in percent
0x009C Air consumption per cycle
0x009D Energy consumption per cycle
1 byte
4 bytes
4 bytes
1 Bit
1 Bit
1 Bit
1 Bit
1 Bit
1 Bit
1 Bit
1 Bit
1 byte
2 bytes
2 bytes
1 byte
2 bytes
2 bytes
J. Schmalz GmbH 6 of 11 ro ro ro ro ro ro ro ro ro ro ro ro ro ro ro ro ro
SCPSi series
29.08.2014
J. Schmalz GmbH
Aacher Straße 29, D 72293 Glatten
Tel.: +49(0)7443/2403-0
Fax: +49(0)7443/2403-259 [email protected]
1-99 = Error code displayed by the device
Total number of suction cycles
Total number of times the suction valve has been switched on
1 = Valve protection active
1 =Evacuation time t1 above limit [t-1]
1 = Leakage rate above limit [-L-]
1 = H1 not reached in suction cycle
1 =Free-flow vacuum > (H2-h2) but < H1
1 = Primary voltage US outside of optimal range unused
1 = Input pressure outside of operating range
0 = no actual value
1 = Leakage of last suction cycle is >200mbar/s
2 = Leakage of last suction cycle is between 133 … 200mbar/s
4 = Leakage of last suction cycle is between 67 ... 133mbar/s
8 = Leakage of last suction cycle is <67mbar/s
Time from start of suction to H2 (unit: 1 ms)
Time from H2 to H1 (unit: 1 ms)
Air consumption of last suction cycle (unit: 1 %)
Air consumption of last suction cycle (unit: 0.1 Nl)
Energy consumption of last suction cycle (unit: 1 Ws)
SCPSi Data Dictionary
IO-Link Data Dictionary
21.10.01.00065/02
160
161
162
163
131
132
133
0x00A0
Predictive Maintenance [PM]
Leakage rate
0x00A1
0x00A2
Free-flow vacuum
Quality
0x00A3
0x0083
Performance
Diagnostic Buffer
Diagnostic buffer (all entries)
0x0084
0x0085
Diagnostic buffer (newest)
EPC Data Buffer
EPC data buffer (all entries)
134 0x0086 EPC data buffer (newest)
2 bytes
2 bytes
1 byte
1 byte
228 bytes
6 bytes
100 bytes
10 bytes ro ro ro ro ro ro ro ro
SCPSi series
29.08.2014
J. Schmalz GmbH
Aacher Straße 29, D 72293 Glatten
Tel.: +49(0)7443/2403-0
Fax: +49(0)7443/2403-259 [email protected]
Leakage of last suction cycle (unit: 1 mbar/sec)
Last measured free-flow vacuum (unit: 1 mbar)
Quality of last suction cycle (unit: 1 %)
Last measured performance level (unit: 1 %)
Newest 38 entries in the diagnostic buffer (encoding see table below)
Newest entry in the diagnostic buffer (encoding see table below)
Newest 10 entries in the EPC data buffer
(encoding see table below)
Newest entry in the EPC data buffer (saved at last autoset)
(encoding see table below)
J. Schmalz GmbH 7 of 11 SCPSi Data Dictionary
IO-Link Data Dictionary
21.10.01.00065/02
Availability of EPC data during suction cycle
J. Schmalz GmbH
Aacher Straße 29, D 72293 Glatten
Tel.: +49(0)7443/2403-0
Fax: +49(0)7443/2403-259 [email protected]
SCPSi series
29.08.2014
J. Schmalz GmbH 8 of 11 SCPSi Data Dictionary
IO-Link Data Dictionary
21.10.01.00065/02
Diagnostic Buffer - Details
Data Format of Single Entry (ISDU 132)
Bytes 0…1 Bytes 2…5
0x1201
0x1202
0x1203
0x1207
0x0207
0x1208
0x1402
0x1403
0x1404
0x1405
0x0405
0x14AA
Diagnostic-Type (MSB first) Counter cc1 (MSB first)
Data Format of Diagnostic Buffer (ISDU 131)
Bytes 0…5 Bytes 6…11 Bytes 12…17
Entry 1 (newest) Entry 2 Entry 3
Encoding of Diagnostic-Type
Diagnostic-Type
0x1401
Description
Notifications
Notification: Device powered on
Notification: Diagnostic buffer cleared
Notification: Parameters restored to factory defaults
Notification: Vacuum sensor calibrated successfully
Notification: Manual mode entered
Notification: Manual mode exited
Notification: Corrupted entry
Errors
Error E01: Internal Error
Error E02: Internal Error
Error E03: Vacuum sensor calibration failed
Error E07 appeared: Primary voltage US too low
Error E07 disappeared: Primary voltage US too low
Error E08 appeared: IO-Link communication interrupted
J. Schmalz GmbH
J. Schmalz GmbH
Aacher Straße 29, D 72293 Glatten
Tel.: +49(0)7443/2403-0
Fax: +49(0)7443/2403-259 [email protected]
SCPSi series
29.08.2014
…
…
Bytes 223…228
Entry 38 (oldest)
Remark
Counter value cc1 of when the entry was recorded
Remark
Buffer of 38 entries (newest to oldest) with encoding as in ISDU 131
Remark
9 of 11
Single entry was written incorrectly - do not evaluate
Remains until next power-on
Remains until next power-on
SCPSi Data Dictionary
IO-Link Data Dictionary
21.10.01.00065/02
0x1101
0x1102
0x1104
0x1108
0x1110
0x0110
0x1120
0x0120
0x1180
0x0180
0x0208
0x120C
0x020C
0x1211
0x0211
0x1212
0x0212
Error E08 disappeared: IO-Link communication interrupted
Error E12 appeared: Short-circuit at OUT2
Error E12 disappeared: Short-circuit at OUT2
Error E17 appeared: Primary voltage US too high
Error E17 disappeared: Primary voltage US too high
Error E18 appeared: Input pressure outside operating range
Error E18 disappeared: Input pressure outside operating range
Condition Monitoring Warnings
CM-Warning: Valve protection activated
CM-Warning: Evacuation time t1 above limit [t-1]
CM-Warning: Leakage rate above limit [-L-]
CM-Warning: H1 not reached in suction cycle
CM-Warning appeared: Free-flow vacuum > (H2-h2) but < H1
CM-Warning disappeared: Free-flow vacuum > (H2-h2) but < H1
CM-Warning appeared: Primary voltage US outside of optimal range
CM-Warning disappeared: Primary voltage US outside of optimal range
CM-Warning appeared: Input pressure outside of operating range
CM-Warning disappeared: Input pressure outside of operating range
J. Schmalz GmbH 10 of 11
J. Schmalz GmbH
Aacher Straße 29, D 72293 Glatten
Tel.: +49(0)7443/2403-0
Fax: +49(0)7443/2403-259 [email protected]
SCPSi series
29.08.2014
Remains until next suction cycle
Remains until next suction cycle
Remains until next suction cycle
Remains until next suction cycle
SCPSi Data Dictionary
IO-Link Data Dictionary
21.10.01.00065/02
SCPSi series
29.08.2014
J. Schmalz GmbH
Aacher Straße 29, D 72293 Glatten
Tel.: +49(0)7443/2403-0
Fax: +49(0)7443/2403-259 [email protected]
EPC Data Buffer - Details
Data Format of Single Entry (ISDU 134)
Bytes 0…1 Bytes 2…3
Evacuation time t1 (MSB first) Leakage rate (MSB first)
Data Format of EPC Data Buffer (ISDU 133)
Bytes 0…9 Bytes 10…19 Bytes 20…29
Entry 1 (newest) Entry 2 Entry 3
Implemented IO-Link Events
Event code
0x1000
0x5100
0x5110
0x8C01
0x1800
0x1801
0x1802
Event name
General malfunction
General power supply fault
Primary supply voltage over-run
Simulation active
Vacuum calibration OK
Vacuum calibration failed
System pressure fault
Bytes 4…5
Free-flow vacuum (MSB first)
…
…
Event type
Error
Error
Warning
Warning
Notification
Notification
Warning
Bytes 6…9
Counter cc1 (MSB first)
Bytes 90…99
Entry 10 (oldest)
Remark
Counter value cc1 of when the data was recorded
Remark
Buffer of 10 entries (newest to oldest) with encoding as in ISDU 133
Remark
Internal error e.g. E01 / E02
Primary supply voltage US too low
Primary supply voltage US too high
Manual mode active
System pressure outside of operating range
J. Schmalz GmbH 11 of 11 SCPSi Data Dictionary
advertisement