Crossfire S 604T / S 604MT Owner Manual
Add to My manuals24 Pages
Crossfire S 604T / S 604MT is a constant speed welder designed for MIG (GMAW) & FCAW welding processes. The device is suitable for welding with solid and flux-cored wires. S 604MT model allows for 24 V welding. It is equipped with a wire feeder mechanism that ensures precise and stable wire feeding, which translates into high-quality welds. The device has a number of features that make it easy to use, including: adjustable welding parameters, digital display, and thermal overload protection.
advertisement
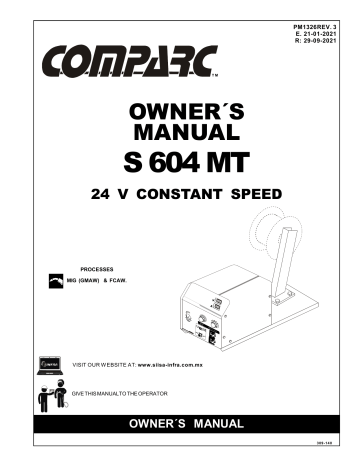
T M
OWNER´S
MANUAL
S 604 MT
24 V CONSTANT SPEED
PM1326REV. 3
E. 21-01-2021
R: 29-09-2021
PROCESSES
MIG (GMAW) & FCAW.
VISIT OUR W EBSITE AT: www.siisa-infra.com.mx
GIVE THIS MANUALTO THE OPERATOR
OWNER´S MANUAL
3 09 - 14 0
TABLE OF CONTENTS
SECTION 1 -- ARC WELDING SAFETY PRECAUTIONS .................................................... i
SECTION 2 -- SAFETY INFORMATION ............................................................................... 1
SECTION 3 - SPECIFICATION ............................................................................................. 1
3-1. Rating Label Location ............................................................................................................... 1
3-2. Specifications ........................................................................................................................... 1
3-3. Environmental Specification ..................................................................................................... 1
SECTION 4 - INSTALLATION .............................................................................................. 2
4-1. Site Selecction ......................................................................................................................... 2
4-2. Typical Connections Diagram ................................................................................................... 2
4-3. Connecting Welding Gun, Voltaje Clamp And Weld cable ......................................................... 3
4-4. 14 Pin Plug Information ............................................................................................................. 3
4-5. Installing Welding Gun .............................................................................................................. 4
4-6. Spool Wire Installation .............................................................................................................. 5
4-7. Shielded Gas Connection ......................................................................................................... 5
4-8. Welding Wire Installation .......................................................................................................... 5
SECTION 5 - OPERATION ................................................................................................... 7
5-1. Controls ................................................................................................................................... 7
SECTION 6 - MAINTENANCE & TROUBLESHOOTING .................................................... 9
6-1. Routine Maintenance ............................................................................................................... 9
6-3. Overload Protection ................................................................................................................. 9
6-3. Troubleshooting ..................................................................................................................... 10
SECTION 7 - ELECTRICAL DIAGRAMS ........................................................................... 11
SECTION 8 - PARTS LIST ................................................................................................. 12
8-1. Main Asembly ........................................................................................................................ 12
8-2. List Control Box ..................................................................................................................... 13
8-3. Part List Of Feeder Mechanism Of Wire ............................................................................... 14
WARRANTY
SECTION 1 - SAFETY PRECAUTIONS - READ BEFORE USING
WARNING
ARC WELDING can be hazardous.
- DANGER! - Indicates a hazardous situation which, if not avoided, will result in death or serious injury. The possible hazards are shown in the adjoining symbols or explained in the text
- Indicates a hazardous situation which, if not avoided, could result in death or serious injury. The possible hazards are shown in the adjoining symbols or explained in the text.
- The symbols shown below are used throughout this manual to call attention to and identify possible hazards. When you see the symbol, watch out, and follow the related instructions to avoid the hazard. The safety information given below is only a summary of the more complete safety information found in the Safety Standards.
- Only qualified persons should install, operate, maintain, and repair this unit.
- During operation, keep everybody, especially children, away.
ELECTRIC SHOCK can kill.
Touching live electrical parts can cause fatal shocks or severe burns. The electrode and work circuit is electrically live whenever the output is on. The input power circuit and machine internal circuits are also live when power is on. In semiautomatic or automatic wire welding, the wire, wire reel, drive roll housing, and all metal parts touching the welding wire are electrically live.
Incorrectly installed or improperly grounded equiment is a hazard.
1.- Do not touch live electrical parts.
2.- W ear dry, hole-free insulating gloves and body protection.
3.- Insulate yourself from work and ground using dry insulating mats or covers.
4.- Disconnect input power or stop engine before installing or servicing this equipment.
5.- Properly install and ground this equipment according to this
Owner's Manual and national, state, and local codes.
6.- Turn off all equipment when not in use.
7.- Do not use worn, damaged, undersized, or poorly spliced cables.
8.- Do not wrap cables around your body.
9.- Ground the workpiece to a good electrical (earth) ground.
10.- Do not touch electrode while in contact with the work (ground) circuit.
11.- Use only well-maintained equipment. Repair or replace damaged parts at once.
12.- Wear a safety harness to prevent falling if working above floor
level.
13.- Keep all panels and cover securely in place.
ARC RAYS can burn eyes and skin;
NOISE can damage hearing.
Arc rays from the welding process produce intense heat and strong ultraviolet rays that can burn eyes and skin. Noise from some processes can damage hearing.
1.- Wear a welding helmet fitted with a proper shade of filter (see ANSIZ49.1 listed in Safety Standards) to protect
FUMES AND GASES can be hazardous to your health.
Welding produces fumes and gases. Breathing these fumes and gases can be hazardous to your health.
1.- Keep your head out of the fumes. Do not breath the fumes.
2.- If inside, ventilate the area and / or use forced ventilation at the arc to remove welding fumes and gases.
3.- If ventilation is poor, use an approved air-supplied respirator.
4.- Read the Material Safety Data Sheets (MSDSs) and the manufacturer´s instruction for metal, consumables, coatings, and cleaners.
FLYING SPARK AND HOT METAL can cause injury
Chipping and grinding cause flying metal . As welds cool, they can throw off slag.
your face and eyes when welding or watching.
2.- Wear approved safety glasses. Side shields recommended.
3.- Use protective screens or barriers to protect others from flash and glade; warn others not to watch the arc.
4.- Wear protective clothing made from durable, flame- resistant mate rial (wool and leather) and foot protection.
5.- Use approved ear plugs or ear muffs if noise level is high.
5.- Work in a confined space only if it is well ventilated, or while wearing an air-supplied respirator. Shielding gases used for welding can displace air causing injury or death. Be sure the breathing air is safe.
6.- Do not weld in locations near degreasing, cleaning, or spraying operations. The heat and rays of the arc can react with vapors to form highly toxic and irritating gases.
7.- Do not weld on coated metals, such as galvanized, lead, or cadmium plated steel, unless the coating is removed from the weld area, the area is well ventilated, and if necessary, while wearing an airsupplied respirator. The coatings and any metals containing these elements can give off toxic fumes if welded.
1.- Wear approved face shield or safety goggles. Side shields recommended.
2.- Wear proper body protection to protect skin.
i
ii
WELDING can cause fire or explosion.
Sparks and spatter fly off from the welding arc. The flying sparks and hot metal, weld spatter, hot workpiece, and hot equipment can cause fires and burns. Accidental contact of electrode or welding wire to metal objects can cause sparks, overheating, or fire.
1.- Protect yourself and others from flying sparks and hot metal.
2.- Do not weld where flying sparks can strike flammable material.
3.- Remove all flammables within 35ft (10.7 m) of the welding arc. If this is not possible, tightly cover them with approved covers.
4.- Be alert that welding sparks and hot materials from welding can easily go through small cracks and openings to adjacent areas.
5.- Watch for fire, and keep a fire extinguisher nearby.
6.- Be aware that welding on a ceiling, floor, bulkhead, or partition can cause fire on the hidden side.
7.- Do not weld on closed containers surch as tanks or drums.
8.- Connect work cable to the work as close to the welding areas as practical to prevent welding current from traveling long, possibly unknown paths and causing electric shock and fire hazards.
9.- Do not use welder to thaw frozen pipes.
10.- Remove stick electrode from holder or cut off welding wire at contact tip when not in use.
11.- Wear oil-free protective garments such as leather gloves, heavy shirt, cuffless trousers, high shoes, and a cap.
CYLINDERS can explode if damaged.
Shielding gas cylinders contain gas under high pressure.
If damaged, a cylinder can explode. Since gas cylinders are normally part of the welding process, be sure to treat them carefully.
1.- Protect compressed gas cylinders from excessive heat, mechanical shocks, and arcs.
2.- Install and secure cylinders in an upright position by chaining them to a stationary support or equipment cylinder rack to prevent falling or tipping.
3.- Keep cylinders away from any welding or other electrical circuits.
4.- Never allow a welding electrode to touch any cylinder.
5.- Use only correct shielding gas cylinders, regulators, hoses, and fittings designed for the specific application; maintain them and associated parts in good condition.
6.- Turn face away from valve outlet when opening cylinder valve.
7.- Keep protective cap in place over valve except when cylinder is in use or connected for use.
8.- Read and follow instructions on compressed gas cylinders, associated equipment, and CGA publication P-1 listed in Safety Standards.
WARNING
ENGINES can be hazardous.
ENGINE EXHAUST GASES can kill.
Engines produce harmful exhaust gases.
1.- Use equipment outside in open, well-ventilated
areas.
E NG I NE F UE L can cau se f ire o r explosion .
Engine fuel is highly flammable.
1.- Stop engine before checking or adding fuel.
2.- If used in a closed area, vent engine exhaust outside and away from any building air intakes.
2.- Do not add fuel while smoking or if unit is near any sparks or open flames.
3.- Allow engine to cool before fueling. If possible, check and add fuel to cold engine before beginning job.
4.- Do not overfill tank - allow room for fuel to expand.
5.- Do not spill fuel. If fuel is spilled, clean up before starting engine.
MOVING PARTS can cause injury.
Moving parts, such as fans, rotors, and belts can cut fingers and hands and catch loose clothing.
1.- Keep all doors, panels, covers, and guards closed
and securely in place.
2.- Stop engine before installing or connecting unit.
3.- Have only qualified people remove guards or covers for maintenance and troubleshooting as necessary.
SPARKS can cause BATTERY GA-
SES T O EXPLODE; BATTERY ACID can burn eyes and skin.
Batteries contain acid and generate explosive gases.
1.- Always wear a face shield when working on a battery.
4.- To prevent accidental stating during servicing, disconnect negative
(-) battery cable from battery.
5.- Keep hands, hair, loose clothing, and tools away from moving parts.
6.- Reinstall panels or guards and close doors when servicing is finished and before starting engine.
2.- Stop engine before disconnecting or connecting battery cables.
3.- Do not allow tools to cause sparks when working on a battery.
4.- Do not use welder to charge batteries or jump start vehicles.
5.- Observe correct polarity (+ and -) on batteries.
ST EAM AND PRESSURIZED HOT
COOLANT can burn face, eyes, and skin.
The coolant in the radiator can be very hot and under pressure.
1.- Do not remove radiator cap when engine is hot. Allow engine to cool.
2.- Wear gloves and put a rag over cap area when removing cap.
3.- Allow pressure to escape before completely removing cap.
- Additional Symbols For Installation, Operation, And Maintenance
NOISE can damage hearing.
Noise from some processes or equipment can damage hearing.
- Wear approved ear protection if noise level is high.
-
FALLING EQUIPMENT can injure
Use lifting eye to lift unit and properly installed accessories only, NOT gas cylinders. Do not exceed maximum lift eye weight rating (see
Specifications).
Use equipment of adequate capacity to lift and support unit.
If using lift forks to move unit, be sure forks are long enough to extend beyond opposite side of unit.
Keep equipment (cables and cords) away from moving vehicles when working from an aerial location.
-
-
OVERUSE can cause OVERHEATING
Allow cooling period; follow rated duty cycle.
Reduce current or reduce duty cycle before starting to weld again.
Do not block or filter airflow to unit.
-
-
STATIC (ESD) can damage PC boards.
Put on grounded wrist strap BEFORE handling boards or parts.
Use proper static-proof bags and boxes to store, move, or ship PC boards.
ARC WELDING can cause interference.
Electromagnetic energy can interfere with sensitive electronic equipment such as microprocessors, computers, and computer-driven equipment such as robots.
Be sure all equipm ent in the welding area is electromagnetically compatible.
To reduce possible interference, keep weld cables as short as possible, close together, and down low, such as on the floor.
Locate welding operation 100 meters from any sensitive electronic equipment.
Be sure this welding machine is installed and grounded according to this manual.
If interference still occurs, the user must take extra measures such as moving the welding machine, using shielded cables, using line filters, or shielding the work area.
-Read and follow all labels and the Owner’s Manual carefully before installing, operating, or servicing unit.
Read the safety information at the beginning of the manual and in each section.
- Definitions
iii
SECTION 2 - SAFETY INFORMATION
The following safety alert symbol and signal words are used throughout this manual to call attention to and identify different levels of hazard and special instructions.
WARNING
WARNING statements identify procedures or practices which must be followed to avoid seriuos personal injury or loss of life.
CAUTION
CAUTION statements identify procedures or practices which must be followed to avoid minor personal injury or damage to this equipment.
IMPORTANT:
Statements identify special instructions necessary for the most efficient operation of this equipment.
SECTION 3 - SPECIFICATION
3-1. Rating Label Location
The serial number and rating information for this product is located on the front. Use rating label to determine input power requirements and/or rated output.
3-2. Specifications
This equipment will deliver rated output at an ambient air temperature up to 104F ( 40 °C).
Type of
Input
Power
Welding Power
Source Type
Wire Feed
Speed Range
Wire Diameter
Range
Welding Circuit
Rating
IP
Rating
24 Volts AC
Single Phase
4 Amperes
50/60 Hz
Constant Voltage
(CV) DC With
14-Pin And
Contactor
Control
75 to 900 ipm
(1.9 To 25.4
mpm)
0.23 To 1/8 in
(0.6 To 3.1 mm)
Max Pool
Weigth:
33 lb (15 kg)
100 Volts,
500 Amperes
100% Duty
Cycle
IP21S
Overall
Dimensions
Weigth
Length: 25 1/2in
650 (mm)
Width:11 in
(280 mm)
Heidth: 14 in
(356mm)
38.5 lb
(17.5kg)
3-3. Environmental Specifications
A. Temperature Specifications
Operating Temperature Range
14 to 104°F (-10 to 40°C)
*Output is derated at temperatures above 104°F (40°C)
Storage/Transportation Temperature Range
-4 to 131°F (-20 to 55°C)
1
PM1326
SECTION 4 INSTALLATION
4-1. SITE SELECTION
CAUTION
1.- WIRE FEEDER.
2.- LIFTING EYE.
3.- RUBBER SUPPORTS(UNDER WIRE FEEDER).
4.- INSTALLATION SLOT.
W hen installing wire feeder ov er a lifting eye on a welding power source, be sure all f our rubber feet on base of feeder sit securely on top of welding power source.
5.- WIRE SPOOL/REEL.
6.- GAS CILYNDER (NOT INCLUDE).
7.- WELDING POWER SOURCE.
Position wire feeder on welding power source so that welding wire or wire spool/reel does not touch gas cilynder.
SEE SAFETY R U LES A T TH E B EGG INING O F M A NU A L
BEFOR E PR OCEED
Do not put feeder were welding wire hits cilynder.
6
5
7
1
FIGURE 4-1.SITE SELECTION
4-2. TYPICAL CONNECTIONS DIAGRAM
3
4
2
Reverse polarity ( Positive Electrode )
CV Welding
Power Source
Supplying 24Vac to feeder
Input cable
Positive (+) Weld cable
Negative (-) Weld cable
Gas Hose to Cylinder
Wire feeder
WORK
Straight Polarity ( Negative Electrode )
CV Welding
Power Source
Supplying 24Vac to feeder
Input cable
Positive (+) Weld cable
Negative (-) Weld cable
Gas Hose to Cylinder
Wire feeder
WORK
FIGURE 4-2 EQUIPMED CONECCTION DIAGRAMS
2
PM1326
4-3. CONNECTING WELDING GUN, VOLTAGE CLAMP AND WELD CABLE
1.- REMOTE 14 CABLE
3
4
2.- SHIELDING GAS VALVE INLET
5
6
3.- FUSE F1
4.- SWITCH S1
5.- WIRE FEED INLET
6.- CABLE TO WELDING
POWER SOURCE
2
6
4-4. CONNECTING 14-PIN PLUG
REMOTE-14 Socket
OUTPUT
(CONTACTOR)
G N D
C
REMOTE OUTPUT
CONTROL
E
D
F
A / V
H
NOTE: Remaining sockets are not used
A
B
I
J
G
K
INFORMATION
24 V a.c. Protected by CB2 (10 Amperes).
Contact closure to "A" completes 24 V a.c. contactor control circuit.
120 V a.c. Protected by CB1(10 Amperes).
Contact closure to "I" completes 120 V a.c. contactor control circuit.
Circuit common for 24 and 120 V a.c. circuits.
Chassis common.
Command reference 10 V d.c.
0 to +10 V d.c. input command signal from remote control.
Remote control circuit common.
Current feedback 0-10 V d.c. 1 Volt per100 weld output Amperes.
Voltage feedback 0-10 V d.c. 1 Volt per 10 weld output Volts
3
PM1326
4-5. INSTALLING WELDING GUN
Turn Off wire feeder and welding power source.
Turn off wire feeder or welding power source before handling or moving clamp.
1 Fix Knob
2 Gun Locking Tab
3 Power Pin groove
4 Gun Connection End
Installing gun with gun locking tab in place system
Loosen power clamp knob to allow power pin of gun to clear the gun locking tab.
Push power pin into power clamp as far as possible to align the groove in the power pin of the gun with the gun locking tab.
Secure gun by tightening power clamp knob.
Installing gun with gun locking tab out of place system
When using a gun without the groove in the power pin, loosen fix knob.
This prevents the locking tab from extending into the pin gun connection.
Push pin into power clamp as far as possible.
Secure gun by tightening fix knob.
5 Gun Control Cable
Insert plug into Gun Control receptacle, and tighten threaded collar.
6 Pressure locking Clip
1 1
2
Gun Locking Tab In Place
2
Gun Locking Tab Out Of Place
6
3
4
PM1326
4
4-6. SPOOL WIRE INSTALLATION.
3
4
2
1
For 8" and 12" (standard) wire spools turn unit off and disconnect it.
1.- Hub spool.
2.- Pin of Hub spool.
3.- Wire spool / Reel.
4.- Hud spool cap.
Turn the hub spool cap clockwise and remove it. Install the wire spool, be sure the hub spool´s pin enters one of the holes of the wire spool. Reinstall the hub spool cap.
FIGURE 4-3 SPOOL WIRE INSTALLATION.
4-7. SHIELDED GAS CONNECTIONS.
WARNING
SEE SAFETY SIGNALS AT THE BEGINING THIS MANUAL
Be sure gas cylinder is held to running gear, wall, or other stationary support so cylinder can not fall and break off valve.
1
6
5
2
3
1.- CAP.
2.- CYLINDER VALVE.
Remove cap, stand to side of valve, and open valve slightly. Gas flow blows
dust and dirt from valve. Close valve.
3.- CYLINDER.
4.- REGULATOR /FLOWMETER.
5.- GAS HOSE CONNECTION.
6.- FLOW ADJUST.
Typical flow rate is 20 cfh ( Cubic Feet per Hour).
4 Tools needed:
Figure 4-4 Shielded gas connection.
28.5, 15.8mm (1-1/8",5/8")
4-8. WELDING WIRE INSTALLATION.
WARNING
SEE SAFET Y PR EC AUT IONS AT BEG G ININ G OF M ANUAL
FOR BASIC W ELDING I NFOR M AT ION.
1
2
5
7
WIRE
JOG
8
1.- WIRE SPOOL / REEL
2.- WELDING WIRE.
3.- WELDING WIRE ACCESS.
4.- INLET WIRE GUIDE.
5.- PRESSURE ADJUST KNOB.
6.- DRIVE ROLL.
7.- PRESSURE LEVER.
8.- WIRE JOG BUTTON (SEE FIG. 5-7).
3
4
6
5
PM1326
4-8. WELDING WIRE INSTALLATION - CONTINUATION
Hold Wire Tightly to Keep It From Unraveling
Open Pressure Assembly
ON
Pull and Hold Wire, Cut
Off End.
POWER
OFF
Push Wire Thru Guides Into
Gun; Continue to Hold Wire
Turn On Welding Power Source
The Output Contactor Switch Must
Be in Next Position:
Close and Latch Pressure
Assembly, Let Wire Go Of Wire
WIRE
JOG
Press Button Until Wire
Comes Out Gun.
Turn On Wire Feeder.
WOOD
Feed Wire, Check Drive Roll Pressure.
Tighten Knob Enough to Prevent Slipping
Cut Off Wire.
Close And Latch Door.
6
PM1326
CAUTION
5-1. CONTROLS
SECTION 5 OPERATION
SEE SAFETY SIGNAL AT THE BEGINING
THIS M A NUA L
REMOTE VOLTAGE
ADJUSTMENT CONTROL
WIRE SPEED
CONTROL
PURGE BUTTON
JOG BUTTON
BURN BACK
TIME
1 2
GUN TRIGGER
RECEPTACLE
TRIGGER MODE
SELECTOR
FIGURE 5-1 CONTROLS
3
1- Insulating Gloves.
2- Safety Glasses With Side Shields.
3- Welding Helmet.
Wear dry insulating gloves, safety glasses with side shields, and a welding helmet with a correct shade of filter (see ANSI Z49.1).
FIGURE 5-2 SAFETY EQUIPMENT
1- Work Clamp.
Use wire brush or sandpaper to clean metal at weld joint area. Use chipping hammer to remove slag after welding.
Connect work clamp to a clean, paint-free location on workpiece, as close to weld area as possible.
FIGURE 5-3 WORK CLAMP
1 Tools needed:
7
Place the switch in ON position to turn on the unit.
Place the switch in OFF position to turn off the unit.
FIGURE 5-4 INPUT POWER SWITCH
ON
POWER
OFF
PM1326
1.- WIRE SPEED CONTROL.
Use this control to select wire feed speed in speed ranges.
Turn in clock wise to increase speed. The numbers is a percentage respect a maximun rated speed (900ipm)
30
20
10
40
50
60
0
100
70
80
90
FIGURE 5-5 WIRE SPEED CONTROL
BURNBACK
5
4
6
3
2
7
8
1
9
0
10
BURNBACK
Use control to adjust the time that the welding wire is energized after wire feeding stops.
By adjusting control properly, the welding wire will not freeze in weld puddle or in contact tip of gun. If welding wire freezes to work, increase burnback time. If welding wire burns back into contact tip, decrease burnback time.
FIGURE 5-6 BURNBACK CONTROL
1
JOG BUTTON
1.- JOG BUTTON
Push and hold button to momentarilly energize feed welding wire at speed set on wire speed control without energizing welding circuit of shielding gas valve.
FIGURE 5-7 JOG BUTTON
GAS PURGE BUTTON.
Push and hold button to momentarilly energize gas solenoid and purge air from gun shielding gas regulator without energizing the welding circuit.
TRIGGER
PURGE
BUTTON
FIGURE 5-8 PURGE BUTTON
TRIGGER MODE SELECTOR.Use this control to select the desired trigger mode.
Select always one trigger mode:
1.
2T Trigger mode : When trigger is depressed, weld starts. When trigger is released, weld stops.
2.
4T Trigger mode : When trigger is depressed, weld starts. When trigger is released, weld remains. After depressing and releasing the trigger for the second time, weld stops.
FIGURE 5-9 TRIGGER MODE SELECTOR.
Install & Connect
Wire Feeder
Install & Prepare
Gun And Power
Source
Put On Personal
Safety Equipment
Set All
Controls.
Turn On
Shielding Gas
(If Applicable)
Turn On
Wire Feeder &
Power Source
Beging
Welding
Readjust
Controls If Is
Necessary
FIGURE 5-10 GAS METAL ARC WELDING (GMAW) & FLUX CORED ARC WELDING (FCAW).
8
PM1326
1- DIGITAL VOLTMETER.
It shows the output terminals voltage (in Volts) of the machine, but not necessarily the arc voltage, due to the resistance of the weld cables, loose connections, etc.
2- DIGITAL AM METER.
It shows the weld current value in Amperes.
REMOTE VOLTAGE ADJUSTMENT
Use this control to set the arc voltage.
1
2
SECTION 6 MAINTENANCE AND TROUBLESHOOTINS
6-1 ROUTINE MAINTENANCE.
TIME
EACH 3 MONTHS
MAINTENANCE
More than normal use: Check all labels ( see 6 month entry ), repair any damaged insulation or replace holder or work cable, 14 pin remote cable,gas hose, torch cable, clean and tighten connections at holder cable and work clamp.
EACH 6 MONTHS
Blow Out Or Vacuum inside,During Heavy Service Clean Monthly,clean all rotatory parts.
6-2 TROUBLESHOOTING.
TROUBLE
No wire feed
POSSIBLE CAUSE
Fuse F1.
Incorrect gun trigger connection
Gun trigger.
Motor M1.
Motor Control Board PC1.
Drive rolls pressure
Erratic wire feed
Drive rolls size.
Worn drive rolls.
Dirty drive rolls.
Motor Control Board PC1.
Too many slags in electrode
Electrode wire does not feed.
Wire does not feed until trigger is pulled, but continues feeds after trigger is released
Gas valve in wire feeder is ratting loudly along, with possibly erratic
wire feed or low speed.
Have a shortcircuit on torch between trigger al weld cables.
Have a shortcircuit on torch between trigger al weld cables.
RECOMMENDED ACTION
Check and replace F1 if necessary.
Check torch trigger connection.
See torch owner´s manual.
Replace motor M1.
Replace PC1.
Turn adjustment pressure nut in clock wise sense; until find the addecuate pressure.
Change addecuate size of drive rolls.
Replace drive rolls.
Clean drive rolls
Replace PC1.
Remove carefully slags arround tip torch using wood. NEVER use METALIC TOOLS to remove slags.
Replace torch.
Replace torch.
9
PM1326
6-3. OVERLOAD PROTECTION.
WARNING
2
SEE SAFETY SIGNAL AT THE BEGINING THIS M ANUAL
1
POWER
DISCONNECT and turn off wire feeder and power source
BEFORE proceed.
INAPPROPIATE FUSES can damage unit. Be sure to select correct fuse size and capacity according amperage used.
1.- FUSE COVER. Remove fuse cover.
2.- FUSE F1 (10 Amp.).
F1 fuse protects agains overloads to wire feeder. If F1 opens, unit shutdown.
Replace F1.
FIGURE 6-3 OVERLOAD PROTECTION
10
PM1326
SECTION 7 ELECTRICAL DIAGRAM.
11
PM1326
ITEM
3
4
1
2
PART No
FIG. 7-2
PP3658
PT3623
MR 01520
PB2389
SECTION 8 PARTS LIST
List 7-1 Main Assembly
D E S C R I P T I O N
Control Box.
Hub Reel
Support, arm
Rubber, support 1-1/8"
Chasis
QUANTITY
1
4
1
1
1
1
PM1326
FIG 7-2
4
Figure 7-1 Main assembly
2
3
12
Item No.
1
2
2a
3
13
14
16
17
17a
18
19
20
21
22
8
9
10
11
12
6
7
4
5
Part No.
PC3133
MV00768
PT1071
MP03020
MP08416
MS04011
PC3267
MS02534
PT2609
MI01227
MG02181
MB04284
MC11514
MF02310
MP00014
PT3636
MI01178
MI00665
MP02512
MR00503
PM1262
PC3266
PP4568
PT3602
I.D.
GS1
F1
PC1
S1
S2,S3
R1
RC2
M1
PC2
R2
PC3
S4
List 7-2 Control Box.
Description
Base box
Solenoid Valve
Retaining nut, Gas solenoid valve (not illustrated)
Overload Protection. Consisting of:
Fuse, 10A
Fuse Holder, 15A
PCB Control
Power Switch
Switch, Pushbutton, SPST, Jog/Purge
Potentiometer 2W, 10 KW.
Trigger Receptacle, 4 Socket
Wire feeder Assembly. (See page 14)
Cover
Nameplate
PCB Burnback, 2T-4T
Potentiometer 2W, 500KW
Knob
Insulator, Wire feed Assembly
Door access
Door Latch
PCB, Digital meters
Switch SPST
Insulator, inlet Wire Guide
Insulating Gromment, weld cable
Burnback name plate a a
Quantiy
1
1
1
1
1
1
1
1
1
1
1
1
1
1
1
1
1
1
1
1
1
1
1
1
13
FIGURE 7-2 CONTROL BOX ASSEMBLY.
PM1326
IT. No
1
2
3
4
5
8
9
6
7
10
11
12
PART No.
PB2324
-----
MB06013R
MG02270
MF02408R
MA04084R
ME02416R
MR10176R
MG02226R
MT08686R
MT08685R
PS2098
LIST 7-3 Part List of Feeder Mechanism of Wire
DESCRIPTION
Feed plate For Gun Locking Tab
Roll (Ask to your distributor)
Fixing arm compl. CWF400-600
Intermediate guide
Shaft D6X35
Retaining ring
Gas hose
Support washer
Inlet guid spiral
Screw M5x10
Screw M8x50
Gun loking tab
2
6
3
5
9
4
2
8
1
11
12
7
QUANTITY
1
4
1
1
2
1
1
4
1
4
1
1
10
FIGURE 7-3 Wire Feeder Assembly
14
PM1326
NOTES
WARRANTY POLICY
UNIFORM WARRANTY FOR SIISA MACHINES.
2°.- SOLDADORAS INDUSTRIALES INFRA S.A. DE C.V.
warranty will be F.O.B. Factory at Naucalpan México, or F.O.B. at an authorized service facility as determined by manufacturer. Therefore no compensation or reimbursement for transportation costs of any kind will be allowed.
SOLDADORAS INDUSTRIALES INFRA, S.A. DE C.V. (SIISA) ,
Warants his equipments (welding power sources, plasma cutting and accessories), from the delivery date to the customer within the warranty periods listed below, the manufacturer will repair or replace any warranted parts or components that fail due to such defects in material or workmanship on factory or service centers.
STATIC WELDING MACHINES AND PLASMA
CUTTING
TRANSFORMER 3 YEARS
PORTABLE INVERTER TYPE WELDING
MACHINES
PORTABLE INVERTER WELDING MACHINE 2 YEARS
3°.- Repair time should not be more than 30 days starting from the reception of the product.
4°.- Spare parts could be adquired in the address attached to this policy.
5°.- The customer could ask the store where he bought the product to make efective this policy.
IN THE FOLLOWING CASES THIS WARRANTY
IS NOT VALID: a).- The warranty will not validin the case machines have been repaired or altered its perfomance order by a non-authorized person by SOLDA-
DORAS INDUSTRIALES INFRA S.A. DE C.V.
or has been used out of specifications of the same, abuses negligence or suffered any accident.
ENGINE DRIVEN WELDING MACHINES
RANGE AND POLARITY SW ITCH 1 YEAR
STATOR 3
YEARS
ROTOR 3 YEARS
KOHLER ENGINE 3 YEARS
(Manufacturer of engine "KOHLER" gives the warranty period).
ACCESSORIES
W IRE FEEDER (W ire feed Mechanism) 1 YEAR
TORCHS AND GUN TORCHS(MIG/TIG Process) 3 MONTHS
PLASMA CUTTING TORCHES
REMOTE CONTROL
W ATTER RECYCLER
RECTIFIER
CIRCUIT CARDS
ALL ELECTRICAL PARTS
3 MONTHS
3 MONTHS
3 MONTHS
1 YEAR
3 MONTHS
30 DAYS b).- This warranty is not applied to: contacts tubes, nozzles, electrodes, insulators, adapters contact tips, etc.
c).- in case the routine maintenance has not been applied.
d).- Ouput power terminals has not warranty when terminals lug usednot according to amperage to use and has not been tighten.
NOTE: In case this warranty is lost during the warranty period,
SOLDADORAS INDUSTRIALES INFRA S.A. de C.V.
will supply another one to the customer, presenting the purchasing bill or invoice.
It is recomended you write down this information and sending it to disribution center where you bought the product and sent it to SOLDADORAS INDUSTRIALES INFRA S. A. de C. V.
.
Calle Plasticos no. 17 Naucalpan de Juárez Estado de México.
Also when your equipment requires any repair, demand the previus form be filled by the Service Center Technician.
UNDER THE FOLLOWING CONDITIONS.
1°.- For making efective this warranty you should just have to show this policy with the product to the nearest service center or workshop throughout the country.
Customer Name:
Adress:
Model:
Serial No:
Date of Purchase:
Invoice No:
NOTES
SERVICE CENTER
MAP CANADA LTD
325 Healey Road, Unit 1, Bolton, ON
L7E 5C1 Canada
FAX
Phone: (905) 951-2788
Toll Free: (800) 757-4445
Fax: (905) 951-6256
SOLDADORAS INDUSTRIALES INFRA, S.A. DE C.V.
Plásticos No. 17 Col. San Francisco Cuautlalpan C.P. 53560
Naucalpan de Juárez Edo. de México
Phone: (52) 53-58-41-83 53-58-87-74 53-58-44-00
Fax: (52) 55-76-23-58
advertisement
Related manuals
advertisement
Table of contents
- 6 SECTION 2 -- SAFETY INFORMATION
- 6 SECTION 3 - SPECIFICATION
- 6 3-1. Rating Label Location
- 6 3-2. Specifications
- 6 3-3. Environmental Specification
- 7 SECTION 4 - INSTALLATION
- 7 4-1. Site Selecction
- 7 4-2. Typical Connections Diagram
- 8 4-3. Connecting Welding Gun, Voltaje Clamp And Weld cable
- 8 4-4. 14 Pin Plug Information
- 9 4-5. Installing Welding Gun
- 10 4-6. Spool Wire Installation
- 10 4-7. Shielded Gas Connection
- 10 4-8. Welding Wire Installation
- 12 SECTION 5 - OPERATION
- 12 5-1. Controls
- 14 SECTION 6 - MAINTENANCE & TROUBLESHOOTING
- 14 6-1. Routine Maintenance
- 14 6-3. Overload Protection
- 15 6-3. Troubleshooting
- 16 SECTION 7 - ELECTRICAL DIAGRAMS
- 17 SECTION 8 - PARTS LIST
- 17 8-1. Main Asembly
- 18 8-2. List Control Box
- 19 8-3. Part List Of Feeder Mechanism Of Wire