Autarco PELD-MII Installation And Operation Manual
Add to My manuals32 Pages
Autarco PELD-MII is a Power Export Limitation Device used to limit the amount of power exported to the grid from solar PV systems. It can limit power export from up to 80 inverters simultaneously, enabling compliance with grid regulations and optimizing self-consumption of solar power.
advertisement
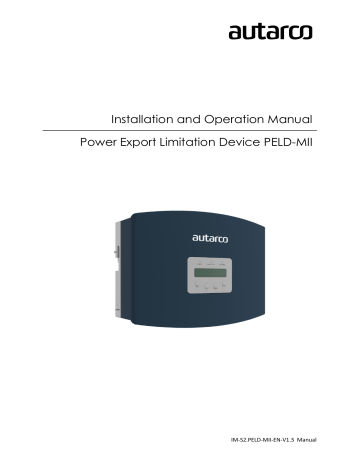
Installation and Operation Manual
Power Export Limitation Device PELD-MII
IM-S2.PELD-MII-EN-V1.3 Manual
Contact Information
Autarco Group B.V.
Schansoord 60
5469 DT Erp
The Netherlands www.autarco.com [email protected]
Other Information
This manual is an integral part of the unit. Please read the manual carefully before installation, operation or maintenance. Keep this manual for future reference.
Product information is subject to change without notice. All trademarks are recognized as the property of their respective owners.
© Autarco Group B.V.
All rights reserved.
2
Table of Contents
Make RS485 cable (COMM-INV port)
Connect the grid input to the distribution box.
Advanced Info-Technicians Only
3
Advanced Settings-Technicians Only
Single phase PELD specifications
Three-phase PELD specifications
4
1. Introduction
1.1 Read this first
This manual contains important information for use during installation and maintenance of the Power
Export Limit Device (PELD) with Autarco’s inverters.
To reduce the risk of electrical shock, and to ensure the safe installation and operation, the following safety symbols appear throughout this document to indicate dangerous conditions and important safety instructions.
WARNING! Indicates safety instruction, which if not correctly followed, can result in injury or property damages.
RISK OF ELECTRIC SHOCK! Indicates safety instructions, which if not correctly followed, could result in electric shock.
HOT SURFACE! Indicates safety instructions, which if not correctly followed, could result in burns.
1.2 Target Audience
This manual is intended for anyone who uses Autarco inverters in conjunction with a Power Export
Limiting Device (PELD). Before any further action, the operators must first read all safety regulations and be aware of the potential danger to operate high-voltage devices. Operators must also have a complete understanding of this device’s features and functions.
ATTENTION! Qualified personnel means a person with valid license from the local authority in:
● Installing electrical equipment and PV power systems (up to 1000 V).
● Applying all applicable installation codes and using Personal Protective Equipment.
● Analyzing and reducing the hazards involved in performing electrical work.
WARNING! Do not use this product unless it has been successfully installed by qualified personnel in accordance with the instructions in chapter 4 “Installation”.
5
1.3 Intended Application
This manual applies to the following products;
● S2.PELD10-MII For limiting up to 10 inverters at a time
● S2.PELD80-MII For limiting up to 80 inverters at a time
Please note that all current inverter models excluding the UX Series are capable of internal power export limitation using an external current clamp or consumption meter. The internal PELD functionality is only applicable for systems with one inverter. Please see the relevant inverter series manual for more information. External power export limitation with the help of the PELD is possible with all inverters.
6
2. Preparation
2.1 Safety instructions
DANGER! Do not touch any internal components whilst the inverter is in operation.
DANGER! Do not stand close to the PELD during severe weather conditions such as lighting, etc.
WARNING! The PELD may become hot during operation; please don’t touch the heat sink or peripheral surface during or shortly after operation.
NOTICE! Do not directly connect AC output of the inverter to any private AC equipment. The PV inverter is designed to feed AC power directly into the public utility power grid.
WARNING! The installation, service, recycling and disposal of the inverters must be performed by qualified personnel in compliance with national and local standards and regulations.
Please contact your dealer to get the information of an authorized repair facility for any maintenance or repairmen.
Any unauthorized actions including modification of product functionality of any form will affect the validation of warranty service; Autarco may deny the obligation of warranty service accordingly.
7
3 Overview
3.1 Front Panel Display
Figure 3.1: Front display
3.2 LED Status Indicator Lights
There are three LED status indicator lights at the front panel of the inverter, as shown in figure 3.1.
Light Status Description
ON Export Device power on
POWER
OFF Export Device power off
OPERATION
ALARM
ON
OFF
ON
OFF
Communication with inverter
No communication with inverter
Backfeed power over 100W or inverter fault.
No alarm
Figure 3.2: Status indicator lights
3.3 Keypad
There are four keys at the front panel of the PELD (from left to right): ESC, UP, DOWN and ENTER keys. The keypad is used for:
● Scrolling through the displayed options (the UP and DOWN keys);
● Access to modify the adjustable settings (the ESC and ENTER keys).
3.4 LCD
The two-line Liquid Crystal Display (LCD) is located at the front panel of the PELD, which shows the following information:
● PELD operation status and data
● Service messages for operators
8
4 Installation
4.1 Install location
To select a location for the PELD, the following criteria should be considered:
● The temperature of the PELD can reach up to 75 ℃ .
● The PELD is designed to work in extended temperature range from -25 ℃ to 60 ℃ .
● The PELD should be installed with a minimum of 300mm clearance from other devices.
4.2 Mounting the EPM
Attach the mounting plate horizontally on to the wall. Then mark A, B and C to fix the mounting plate
(see Figure 4.1).
Figure 4.1: Bracket
Drill three φ 8 holes and insert expandable plugs into the holes which make the bracket alignment. After that fix the bracket on the wall.(see Figure 4.2). Make sure that the wall is flat.
Figure 4.2: Fix the bracket on the wall
9
Hang the PELD in the bracket by the steps below (see figure 4.3)
Figure 4.3: Hang the PELD in the bracket
Fix the two screws at the side of the bracket to secure the PELD. Do not overtighten the screws. See figure
4.4.
Figure 4.4: Fix the two screws
10
4.3 Electrical Connections
The PELD is designed for electrical connection without removing the cover. The meaning of the symbols located at bottom of the PELD is listed below:
Grid
CT1/2/3
Comm_INV
Communication
AC voltage sampling terminal
AC current sampling terminals (CT1 only when 1 phase)
Communication with Autarco inverter
Connection for Monitoring Device or Software Upgrade Stick
Figure 4.5: Three-phase system with Autarco S2.PELD-MII
11
Figure 4.6: Three phase system with Autarco PELD
Figure 4.7: Single phase system with Autarco PELD
Note that the PELD shall be installed near the measuring point for current/voltage. The CT cables and grid input cable are usually limited in length. In order to shorten the length of CT and grid input cable, the PELD is recommended to be installed near the customer distribution box.
The PELD is delivered without CT’s. These must be ordered separately for the current range that has to be measured.
12
4.4 Make the Grid input cable
● Measure the distance from PELD to power distribution box. Choose the proper cable for grid input. Use a 5-core cable for Autarco 3 phase PELD and a 3-core cable for Autarco single phase
PELD. Check carefully the connections in the connector and make sure the cables inside the connector cannot touch each other.
● For three phase inverter installation connect L1, L2, L3 to pin 1, 2, 3 and connect N to pin4, connect PE to (see figure 4.8).
● For single phase installation, connect L, N and PE and N to pin4, connect PE to (see figure4.7) .
● Strip the end of cable to 3mm (see Figure 4.8)
● Feed the cable through the washer and use a suitable screwdriver to fix the wire to the connector
(see Figure 4.9)
13
4.5 Make RS485 cable (COMM-INV port)
● Refer to figure 4.16, the RS485 terminals for inverter and PELD are already assembled. RS485A is connected to yellow and RS485B to blue wire. Suggested RS485 cable: preferred 0.5-1.0mm
2 .
● Refer to figure 4.17, connect communication cable between inverter with PELD, and then measure the distance from PELD to inverter. Use proper cable for RS485 connection 0.5-1.0mm
2
14
● Follow step1 to assemble 2 connectors to each end of the cable. If the RJ45 comms ports are used on the inverter, you also may use standard Ethernet cables for connection from one inverter to the second one and so on. Then you only need to assemble one cable from the last inverter to
PELD.
● Make sure RS485A and RS485B connect to the same pin on each inverter !
4.6 Connect ground cable.
● The case of PELD is metal and must be grounded.
● Measure the distance from PELD to ground point, then prepare the proper grounding cable. The ground cable may be 2.5-4 mm.
● Use an O type terminal as an accessory to connect the ground cable to PELD. (Figure 4.18)
Figure 4.18 Assemble ground cable
4.7 Connect and fix the CT
In order to measure the backflow current, the CT’s shall be installed just behind the customer’s main switch (see figure 4.5).
Notice:
If the CT’s are installed in the wrong place or direction, the PELD will not work correctly.
● Switch off the main switch, disassemble line cable.
● Feed the cable through the CT or use CT’s that can be split. The direction of CT is very important.
Refer to Figure 4.19, the side with words should face downstream. Reconnect the line cable to the main switch.
Figure 4.19 CT current pointing to inverter
15
● To prevent overheating, always make sure the secondary side of the CT’s is connected to the PELD before switching on power.
In figure 4.20 a few examples of Current Transformers can be found. It is possible to select your own brand and type as long as they meet the requirements and safety standards.
Figure 4.20: CT Ratio
Reminder: Set the CT Sampling Ratio in Advanced Settings; Set CT Parameter
4.8 Connect the grid input to the distribution box.
The grid input cable can be connected at the inverter grid breaker or an independent breaker.
Notice:
Do not connect the grid input cable to the load breaker, it could cause inverter loss of control when the load breaker trips.
NOTICE! Do not directly connect AC output of the inverter to any private AC equipment. The
PV inverter is designed to feed AC power directly into the public utility power grid.
Please follow figure 4.5 system diagram to connect grid input cable to the main switch.
The cable sequence must match the PELD grid terminal sequence.
4.9 Multi inverter connection
Please follow figure 4.5 system diagram to connect multiple-inverters. PELD can control maximum 10 inverters.
They may be different models. The firmware of the inverter must support EPM use.
The inverter RS485 address must be set to different values: please set address from 01 to 09.
Before starting up the inverter please follow 6.5.1 to set the inverter number in PELD.
16
4.10 Monitoring
Inverters that are connected to the PELD can be monitored by Autarco Ethernet/WiFi/GPRS stick or box.
WiFi/GPRS stick is used for single inverter monitoring.
Multiple-inverters must use WiFi/GPRS box to monitor via the PELD. Digital Monitoring Sticks (with “-D” in product code) will have capability to monitor multiple inverters via the peld after Q1 2021.
Notice: When an inverter is connected to PELD, no other monitoring device is allowed to be connected to the inverter.
17
5 Commission and decommission
5.1 Commissioning
● Connect the CT connectors, grid input terminal, RS485 terminal (INV) and monitoring device (if needed) to the PELD. Connect the other end of RS485 cable to the inverter(s).
Figure 5.1 Cable connections
● Close the breaker of the grid input and start up PELD
● The power LED(red) will light up. After the LCD-screen has started up, press up or down check if the active power is positive or 0. If the active power is negative, please check the direction of the
CT’s.
● Set inverter number for multi-inverters connection.
● Follow the instructions of the inverter to start up the inverter. If the PELD communicates with the inverter successfully, the green LED will light.
● The default allowed backflow power is 0. Please follow 6.5 to change the allowed backflow power if needed.
5.2 Decommissioning
In order to avoid the backflow power to the grid, please stop the inverter before stopping the PELD.
● Turn off the grid breaker of the inverter.
● Turn off the PV input breaker.
● Turn off the grid input breaker of PELD.
● Disconnect all cables of PELD, disassemble PELD after 5mins
18
6 Operation
6.1 Introduction
During normal operation, the display alternately shows the power of the grid side and the operation
Status. Screens can also be scrolled manually by pressing the UP and DOWN keys. Press the ENTER key to access to the Main Menu
There are 4 status messages:
● Normal: The system works normally.
● RS485 AllFail: PELD has lost communication with ALL inverters
● CT FailSafe: Current Sensor has failed.
● RS485 Fail: PELD has lost communication with one or more inverters
If you see a fault message, check all wiring and make sure RS485 + and – are wired the same on all inverters.
6.2 Main Menu
There are four submenus in Main Menu (see figure 6.1)
● Information
● Settings
● Advanced Info.
● Advanced Settings
19
6.2.1
Information
Autarco PELD main menu provides access to operational data and information. The information is displayed by selecting ‘’Information’’ from the menu and then scrolling up or down through the list. See figure 6.1.
Figure 6.1: Information list
6.2.2
Lock Screen
Pressing the ESC key returns to the Main Menu. Pressing the ENTER key locks (Figure 6.2(a)) or unlocks
(Figure 6.2 (b)) the screen.
Figure 6.2: Locks and Unlocks the screen of LCD
20
6.2.3
Settings
The following submenus are displayed when the Settings menu is selected.
● Set Time
● Set Address
6.2.4
Set Time
This function allows time and date setting. When this function is selected, the LCD will display a screen as shown in Figure 6.3
Figure 6.3: Set time
Press the UP/DOWN keys to set time and data. Press the ENTER key to move from one digit to the next
(from left to right). Press the ESC key to save the settings and return to the previous menu.
6.2.5
Set Address
This function is used to set the address when multiple inverters are connected to see monitoring.
The address number can be assigned from ‘’01’’ to ‘’99’’ (see figure 6.4).
The default number is <01>
Figure 6.4: Set address
Press the UP/DOWN keys to set the address. Press the ENTER key to save the settings.
Press the ESC key to cancel the change and return to the previous menu.
6.3 Advanced Info-Technicians Only
Notice: Access to this area is for fully quali fi ed and accredited technicians only. To Enter menu “Advanced Info.” and “Advanced setting” you need a password.
Select “Advanced Info.” from the Main Menu. The screen will require the password as below.
Figure 6.5: Set password
21
The default password is “0010". Please press “down” to move the cursor, press “up” to select the number.
After entering the correct password the Main Menu will display a screen and be able to access the following information.
● INV Power
● CT connect status
● Version
● Model Inverter
● Communication Data
The screen can be scrolled manually by pressing the UP/DOWN keys. Pressing the ENTER key gives access to a submenu. Press the ESC key to return to the Main Menu.
6.3.1
Inverter Power
The screen shows the information of INV Power for each inverter which is connected to the PELD.
Figure 6.6: Inverter power
6.3.2
CT connect status
For the position of three-phase CT installation and direction of current detection refer to 4.3.
If marking on CT is towards the grid, then PELD detection will display OK as shown in fi gure 6.7.
Otherwise, the status will display ‘’NG” which indicates wrong CT direction.
Figure 6.7 CT Connect status
Note: it is possible that NG will be shown when the current-transformer is connected correctly if the cable is smaller than designed for. Make sure the cable lies centralized in the core for proper reading.
6.3.3
Software
The screen shows the model version and the software version of the inverter.
Figure 6.8: Software version
6.3.4
Model Inverter
The screen shows the rated power of the inverters that are connected to the PELD. Only one inverter will be shown currently.
22
Figure 6.9: Model inverter
6.3.5
Communication data
The screen shows the internal communication data of the inverter. This page is for service technicians only.
Figure 6.10: Communication data
6.4 Advanced Settings-Technicians Only
Notice: Access to this area is for fully quali fi ed and accredited technicians only. Please follow 6.4 to enter password to access this menu
The default password is “0010". Please press “down” to move the cursor, press “up” to select the number.
Select Advanced Settings from the Main Menu to access the following options:
● 1. Set inverter Quantity
● 2. Set Back fl ow Power
● 3. Set CT Parameter
● 4. Fail safe ON/OFF
● 5. Back fl ow Work Mode
● 6. PELD ON/OFF
● 7. System Upgrade
● 8. Set Password
6.4.1
Inverter Quantity Set
This submenu is used for setting the number of connected inverters.
Figure 6.11: Inverter quantity set
When you enter this screen, it shows the total number of inverters connected to the PELD. (see figure
6.11). The number (01~99) can be selected by pressing the UP/ DOWN keys. Press the ENTER key to set the inverter number, ESC key to return to the previous menu.
6.4.2
Backflow Power
This submenu is used to set allowed power that the inverters can insert back into the grid.
23
Figure 6.12: Set backflow power
Press the UP/DOWN keys to set data. Press the ENTER key to set backflow power, then press UP/DOWN keys to change the number (in units of 100 Watt).
Press the ESC key to save the settings and return to the previous menu.
6.4.3
Set CT Parameter
This function is used to change CT parameters if the customer selects different CT. The default CT parameter setting is 30: 1.
Figure 6.13: Set CT Parameter
Press the UP/DOWN keys to set data. Press the ENTER key to set the CT Parameter. Press the ESC key to save the settings and return to the previous menu.
Measuring range is 5 A.
Example: if you want to measure up to 300 A, CT parameter must be set 0060:1.
6.4.4
Failsafe ON/OFF
This submenu is used for setting fail safe on/off.
Fail safe shows whether there is communication or not between PELD and inverters.
The default setting is ‘’Run’’. Don’t change this parameter without a technician.
Figure 6.14: FailSafe ON/OFF
Failsafe ON: PELD will control the output power of the connected inverters.
Failsafe OFF: PELD will not control the output power of the connected inverters.
Failsafe operation works over the RS485-bus.
If one or more inverters lose communication with the PELD, the PELD’s LCD screen will display “RS485 fail”
The connected inverter will be forced to stop.
If all inverters lose communication with the PELD, then the LCD screen of PELD will display “RS485AllFail” and all inverters will be forced to stop.
When the Fail Safe is set to ‘’OFF’’ and communication is lost between PELD and inverters, the setting will not affect the output of the inverters.
6.4.5
Failsafe settings
24
Failsafe settings determine how the inverter operates if there is a loss of connection with any device.
There are 3 error modes
● RS485 AllFail: PELD has lost communication with ALL inverters
● RS485 Fail: PELD has lost communication with one or more inverters
● CT FailSafe: Current Sensor has failed.
Failsafe Error Mode With Failsafe On With Failsafe Off
RS485 All Fail All Inverters stop All Inverters will remain on
RS485 Fail Specific inverter OFF; others ON Affected inverter will remain on
CT Fail Safe PELD will stop all inverters All Inverters will remain on
6.4.6
Backflow Work Mode
This submenu is used for set back fl ow work mode: 01, 02. “01” is the default mode.
Figure 6.15: Backflow Work Mode
Mode “01” is the average limiting mode.
In this mode the average export power over 3 phases is 0. If the load on the 3 phases is not equal, this means that one phase may export power and another phase takes power from the net.
See the example in fi gure 6.16: the output power of the inverter on each phase is the average of the three-phase load power.
The output power of the inverter (4500 W) is higher than the phase with the lowest power (4000 W) from the three phases.
25
Figure 6.16: Mode 01
Mode “02” is the per phase limiting mode.
In this mode the export power is 0 on each phase. The inverter will generate a power equal to the lowest load power.
See the example in figure 6.17: the inverter only generates the power that equals to one of three-phase loads that has the lowest load power of a certain phase (here 4000 W).
Mode 02 is recommended in case of very uneven distribution of load on a 3 phase network.
Figure 6.17: Mode 02
6.4.7
PELD ON/OFF
This submenu is used for switching PELD on/off. It decides whether PELD works or not.
Figure 6.18: PELD Switch
26
Switching PELD on: the device can monitor and manage the working condition of inverters in real time, and it prevents backflow generated. Switching PELD off, means the device shuts down the function of controlling backflow power.
6.4.8
System Upgrade
The upgrade of PELD’s system can be realized through the RS485 communication port with an upgrade stick. Please consult our technical engineer for more details.
Figure 6.19: System Update
6.4.9
Set Password
Enter the current password before setting a new password. Press the DOWN key to move the cursor.
Press the UP key to revise the value. Press the ENTER key to execute the setting. Press the ESC key to return to the previous menu.
Figure 6.20: Reste Password
27
6.4.10 Restore Settings
When Restore Settings is selected, the LCD will display a message as shown in figure 6.21
Figure 6.21: Restore settings
Press the ENTER key to execute the setting.
Press the ESC key to return to the previous menu.
Notice: Do not do this on an active system. First stop operation.
6.4.11 Set EPM Regulator
This setting is used to set the total sum of the capacities of the connected inverters.
Figure 6.22: Capacity settings
Figure 6.23
28
8 Set Inverters
The PELD is available with different operation modes. To make sure that the inverters can work with the
MII version, set the inverters into the correct operation mode.
Notice: If you are using S2.PELD10-MII select 5G EPM
Notice: If 5G EPM is chosen, all inverters produced before Nov 30th 2019 need to update the firmware. Please contact [email protected]
for instructions on the firmware upgrade. The UX firmware must be V3A or higher.
Notice: If the setting is not correct. FailSafe operation will not work
29
9 Troubleshooting
The PELD is designed in accordance with the most important international safety and EMC requirements.
Before delivering to the customer, the PELD has been subjected to several tests to ensure its optimal operation and reliability.
9.1 Checklist
Please check the following;
● PELD: CT Sampling setting on PELD is correct
● PELD: Inverter Quantity and Total Power settings are correct
● Inverters have been set to PELD on
● PELD: 3 AC-phases (L1, L2 and L3) on the PELD must be connected in same order as the connected inverters to ensure proper measurements
● PELD: Check on screen if the active power is positive or 0; if not, check the direction of the CT’s.
● Inverter: check firmware version
9.2 Other Troubleshooting
In case of failure, the LCD screen will display an alarm message.
The PELD can show both alarms generated by the PELD and alarms generated by inverters. There are 3
PELD generated alarms that may appear on LCD:
● Backflow
There is a backflow current to the grid. Customer must stop the inverter, and check the connections for the RS485 cable between PELD and inverter.
● INV. fault
There are fault alarms in an inverter; please check inverter status.
● Fail safe o RS485 AllFail: PELD has lost communication with ALL inverters o RS485 Fail: PELD has lost communication with one or more inverters o CT FailSafe: Current Sensor has failed.
30
10 Specifications
10.1 Single phase PELD specifications
31
10.2 Three-phase PELD specifications
32
advertisement