advertisement
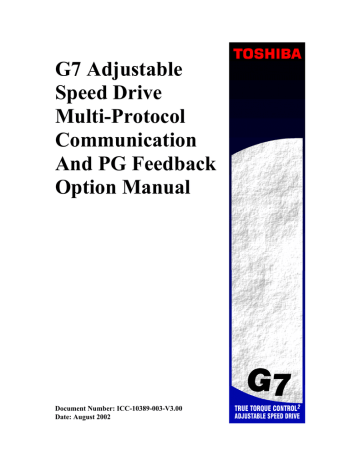
G7 Adjustable
Speed Drive
Multi-Protocol
Communication
And PG Feedback
Option Manual
Document Number: ICC-10389-003-V3.00
Date: August 2002
About This Manual
This manual was written by the TOSHIBA Technical Publications Group. This group is tasked with providing technical documentation for the G7 Adjustable Speed Drive. Every effort has been made to provide accurate and concise information to you, our customer.
Contacting TOSHIBA’s Customer Support Center
TOSHIBA’s Customer Support Center can be contacted to obtain help in resolving any G7 Adjustable
Speed Drive system problem that you may experience or to provide application information. The center is open from 8 a.m. to 5 p.m. (CST), Monday through Friday. The Support Center’s toll free number is US (800) 231-1412/Fax (713) 466-8773 — Canada (800) 527-1204.
You may also contact TOSHIBA by writing to:
TOSHIBA International Corporation
13131 West Little York Road
Houston, Texas 77041-9990
Attn: ASD Product Manager.
For further information on TOSHIBA’s products and services, please visit our website at
TIC.TOSHIBA.COM.
TOSHIBA is a registered trademark of the TOSHIBA Corporation.
All other product or trade references appearing in this manual are registered trademarks of their respective owners.
The information in this manual is subject to change without notice.
TOSHIBA International Corporation shall not be liable for technical or editorial omissions or mistakes in this manual, nor shall it be liable for incidental or consequential damages resulting from the use of information contained in this manual.
This manual is copyrighted. No part of this manual may be photocopied or reproduced in any form without the prior written consent of TOSHIBA International Corporation.
© Copyright 2002 TOSHIBA International Corporation.
All rights reserved.
Printed in the U.S.A.
TOSHIBA INTERNATIONAL CORPORATION
G7 Adjustable Speed Drive Multi-Protocol and PG Feedback Option
Please complete the Warranty Card supplied with the option and return it to Toshiba by prepaid mail.
This will activate the 12-month warranty from the date of installation; but shall not exceed 18 months from the date of purchase.
Complete the following information about the option and retain it for your records.
Model Number: ASD-MULTICOM-A or ASD-MULTICOM-B
Serial Number:
Date of Installation:
Inspected By:
Name of Application:
Important Notice
This user manual may not cover all of the variations of option applications, nor may it provide information on every possible contingency concerning installation, programming, operation, or maintenance.
The contents of this user manual shall not become a part of or modify any prior agreement, commitment, or relationship between the customer and TOSHIBA International Corporation.
The sales contract contains the entire obligation of TOSHIBA International Corporation. The warranty contained in the contract between the parties is the sole warranty of TOSHIBA
International Corporation’s ASD Division and any statements contained herein do not create new warranties or modify the existing warranty.
Any electrical or mechanical modifications to this equipment without prior written consent of
TOSHIBA International Corporation will void all warranties and may void any UL/CUL listing or other safety certifications. Unauthorized modifications may also result in equipment damage or personal injury.
This Manual’s Purpose and Scope
Currently, this manual covers the following G7 Adjustable Speed Drive options:
• ASD-MULTICOM-A (multi-protocol communications + PG feedback)
• ASD-MULTICOM-B (PG feedback only)
Not all sections of this manual will apply to the ASD-MULTICOM-B option. These sections will be indicated in their respective introduction paragraphs.
This manual provides information that will assist the qualified user in the safe installation, setup, operation, and disposal of the G7 Adjustable Speed Drive Multi-Protocol
Communication Option and PG Feedback Option. The information provided in this manual is applicable to the G7 Adjustable Speed Drive Multi-Protocol Communication Option and
PG Feedback Option only.
This operation manual provides information on the various features and functions of these powerful cost-saving devices, including
• Installation,
• System operation, and
• Mechanical and electrical specifications.
Table of Contents
1. Introduction ...........................................................................................................1
2. Safety Precautions .................................................................................................2
2.1
Installation Precautions ................................................................................................................ 2
2.2
Maintenance Precautions.............................................................................................................. 3
2.3
Inspection ..................................................................................................................................... 3
2.4
Storage ......................................................................................................................................... 3
2.5
Disposal........................................................................................................................................ 3
3. Board Overview.....................................................................................................4
4. Installation .............................................................................................................5
4.1
Installation Procedure................................................................................................................... 5
4.2
Wiring .......................................................................................................................................... 7
5. Environmental Specifications...............................................................................7
6. PG Feedback Operation........................................................................................8
6.1
PG Feedback Enable Setting ........................................................................................................ 8
6.2
PG Power Supply Voltage Selection ............................................................................................ 8
6.3
Pulse Input Selection.................................................................................................................... 9
6.4
PG Feedback Connection ........................................................................................................... 10
6.5
Maximum Input Frequency Using an Open Collector Encoder.................................................. 13
7. LED Indicators ....................................................................................................14
8. Network Configuration Parameters ..................................................................15
8.1
Profibus DP Configuration......................................................................................................... 16
8.2
Modbus RTU Configuration....................................................................................................... 17
8.3
DeviceNet Configuration............................................................................................................ 18
9. Profibus Interface................................................................................................19
9.1
Feature Summary........................................................................................................................ 19
9.2
Profibus Interface Connection.................................................................................................... 21
9.3
Unit Addressing.......................................................................................................................... 21
9.4
Profibus Exchanged Data Structures .......................................................................................... 22
9.4.1
Output (Control) Data Format .............................................................................................. 22
9.4.2
Input (Status) Data Format.................................................................................................... 25
9.5
Diagnostics................................................................................................................................. 31
9.6
Asynchronous Drive Parameter Access...................................................................................... 32
9.6.1
Parameter Number / Action Output Words............................................................................ 32
9.6.2
Parameter Number / Action Input Words .............................................................................. 33
G7 ASD Multi-Protocol Communication Option and PG Feedback Option Manual i
9.6.3
Drive Parameter Access Procedure .......................................................................................34
9.6.4
Register Access Error Codes..................................................................................................35
9.7
Parameters...................................................................................................................................35
10. RS-485 Interface...............................................................................................36
10.1
Physical Layer.............................................................................................................................36
10.2
Modbus RTU ..............................................................................................................................37
10.2.1
Configuration.....................................................................................................................37
10.2.2
Communication Formats....................................................................................................37
10.2.3
Modbus/ASD Register Mappings .......................................................................................38
10.2.4
ASD Scan Registers............................................................................................................39
10.2.5
Supported Modbus Functions ............................................................................................41
10.2.6
Programmable Pointer Registers.......................................................................................42
10.2.7
Response Delay Timer Function ........................................................................................42
10.2.8
LED Indicators...................................................................................................................43
10.2.9
Register Summary ..............................................................................................................43
11. DeviceNet Interface..........................................................................................45
11.1
Feature Summary ........................................................................................................................45
11.2
Unit Addressing ..........................................................................................................................46
11.3
Grounding ...................................................................................................................................46
11.4
Connection Information ..............................................................................................................46
11.4.1
Connection Sizes ................................................................................................................46
11.4.2
I/O Assembly Instances ......................................................................................................47
11.5
Object Specifications ..................................................................................................................48
11.5.1
Identity Object....................................................................................................................49
11.5.2
Message Router..................................................................................................................51
11.5.3
DeviceNet Object ...............................................................................................................52
11.5.4
Assembly Object.................................................................................................................54
11.5.5
Connection class ................................................................................................................58
11.5.6
Control Supervisor Object .................................................................................................62
11.5.7
Motor Data Object .............................................................................................................65
11.5.8
AC/DC Drive Object ..........................................................................................................67
11.5.9
Parameter Class.................................................................................................................72
11.6
Network Communication Loss Action........................................................................................73
12. Notes ..................................................................................................................75
G7 ASD Multi-Protocol Communication Option and PG Feedback Option Manual ii
1. Introduction
Congratulations on the purchase of the new G7 Adjustable Speed Drive (ASD) Multi-Protocol
Communication (ASD-MULTICOM-A) or PG Feedback (ASD-MULTICOM-B) Option.
ASD-MULTICOM-A / ASD-MULTICOM-B
These option cards provide the ability to connect various different pulse generator/feedback sources, such as encoders, to the G7 ASD. These PG input signals can then provide enhanced performance for vector control, pulsed speed command, and process (PID) control applications.
Two different types of pulse input circuitry are provided, which allows very flexible application and connectivity to a wide array of PG devices available on the market today.
ASD-MULTICOM-A
In addition to the PG feedback circuitry, this option card also provides connectivity to the most popular fieldbus networks in use today. These networks include Profibus, DeviceNet, and RS-485 based networks. Different option board firmware versions may provide varying levels of support for these different networks, so when using this manual, always keep in mind that the firmware version operating on your option board must match this manual’s respective revision for all documented aspects to apply.
The option board firmware version covered by each revision of the manual is indicated in the last section of the “Document Number” on the manual’s front cover. For example, if the Document Number on the front cover ends in “-V3.00”, then this manual is only applicable for version 3.00 option board firmware.
The method of determining your board’s firmware version varies depending on the network being used.
Please refer to the specific network interface sections of this manual to determine the method required for your installation.
This manual will primarily be concerned with the option’s hardware specifications, input characteristics, configuration, and installation and wiring precautions. For more advanced application-level information, please contact Toshiba’s ASD Marketing Department for copies of available application notes.
To maximize the abilities of your new ASD option, a working familiarity with this manual will be required. This manual has been prepared for the option installer, user, and maintenance personnel. With this in mind, use this manual to develop a system familiarity before attempting to install or operate the device.
G7 ASD Multi-Protocol Communication Option and PG Feedback Option Manual 1
2. Safety Precautions
Rotating shafts and electrical equipment can be hazardous. Installation, operation, and maintenance of the ASD and option shall be performed by Qualified Personnel only.
Qualified Personnel shall be:
• Familiar with the construction and function of the ASD and option, the equipment being driven, and the hazards involved.
• Trained and authorized to safely clear faults, ground and tag circuits, energize and de-energize circuits in accordance with established safety practices.
• Trained in the proper care and use of protective equipment in accordance with established safety practices.
Installation of ASD systems and associated options should conform to the 1999
National Electrical Code Article 110 (NEC) (Requirements For Electrical
Installations), all regulations of the Occupational Safety and Health
Administration, and any other applicable national, regional, or industry codes and standards.
DO NOT install, operate, perform maintenance, or dispose of this equipment until you have read and understood all of the following product warnings and user directions. Failure to do so may result in equipment damage, operator injury, or death.
2.1 Installation Precautions
• Use lockout/tagout procedures on the branch circuit disconnect before installing the option into the ASD.
• Avoid installation in areas where vibration, heat, humidity, dust, metal particles, or high levels of electrical noise (EMI) are present.
• Do not install the ASD or option where it may be exposed to flammable chemicals or gasses, water, solvents, or other fluids.
• Where applicable, always ground the option appropriately to prevent electrical shock to personnel and to help reduce electrical noise. The ASD’s input, output, and control power cables are to be run separately from the option’s associated cables.
Note: Conduit is not an acceptable ground.
• Turn the power on only after attaching the front cover.
• Follow all warnings and precautions and do not exceed equipment ratings.
• The ASD maintains a residual charge for a while after turning the ASD off. Wait at least ten minutes before servicing the ASD after turning the ASD power off.
Ensure that the Charge LED is off prior to beginning installation.
• For further drive-specific precaution, safety and installation information, please refer to the G7 Adjustable Speed Drive Operation Manual supplied with your drive.
G7 ASD Multi-Protocol Communication Option and PG Feedback Option Manual 2
2.2 Maintenance Precautions
• Use lockout/tagout procedures on the branch circuit disconnect before servicing the ASD or installed option.
• The ASD maintains a residual charge for a while after turning the ASD off. Wait at least ten minutes before servicing the ASD after turning the ASD power off.
Ensure that the Charge LED is off.
• Do Not attempt to disassemble, modify, or repair the option card. Call your
Toshiba sales representative for repair or service information.
• Turn the power on only after attaching the front cover and Do Not remove the front cover of the ASD when the power is on.
• If the ASD should emit smoke or an unusual odor or sound, turn the power off immediately.
• The heat sink and the discharge resistors may become extremely hot to the touch.
Allow the unit to cool before coming in contact or performing service on the ASD or option card.
• The system should be inspected periodically for damaged or improperly functioning parts, cleanliness, and to determine that the connectors are tightened securely.
2.3 Inspection
Upon receipt, perform the following checks:
• Inspect the unit for shipping damage.
• Check for loose, broken, damaged or missing parts.
Report any discrepancies to your Toshiba sales representative.
2.4 Storage
• Store the device in a well ventilated location (in its shipping carton, if possible).
• Avoid storage locations of extreme temperatures, high humidity, dust, or metal particles.
2.5 Disposal
• Contact the local or state environmental agency in your area for details on the disposal of electrical components and packaging.
• Do not dispose of the unit via incineration.
G7 ASD Multi-Protocol Communication Option and PG Feedback Option Manual 3
3. Board Overview
DIP Switch DS1
Refer to Sections 6.1 & 6.2
MMI Port
Reserved
Module Status / Network
Status LEDs
Refer to network sections
DeviceNet Connector
Refer to Section 11
Pulse Input Selection
Refer to Section 6.3
DATA_EXCHG LED
Refer to Section 9.1
PG Feedback Terminals
Refer to Section 6.4
RS-485 Terminals
Refer to Section 10
Control Board Connector
Refer to Section 4
Profibus Connector
Refer to Section 9
PG Circuit Ground
Refer to Section 6.4
NOTE: Not all indicated items are available on ASD-MULTICOM-B.
G7 ASD Multi-Protocol Communication Option and PG Feedback Option Manual 4
4. Installation
4.1 Installation Procedure
The interface cards for the G7 ASD have been designed for quick and simple installation. The card is connected to the drive's control board via an 80-pin connector, and is mechanically supported with nylon standoffs attached through the control PCB to the chassis. The only tools required for installation are a flat screwdriver, a #2 Phillips screwdriver and, for most installations, a utility knife to aid in the removal of the front cover's side access window. Each interface card kit includes one #51326A connector PCB and four #47220 nylon hex standoffs.
Before opening the drive, please observe all safety precautions as outlined on the unit's front cover and in the operation manual. After securing the unit against hazardous voltages, loosen the two lower fasteners and remove the cover, taking care not to damage the keypad-to-drive cable connection.
Remove the four pan head screws that secure the control PCB to the drive (refer to Figure 1) and replace with the #47220 1/2" hex standoffs provided. Make these substitutions one or two fasteners at a time to prevent any shifting of the control board.
#51326A
#47220
#47220
Figure 1: Screw Removal, Standoff and Connector PCB Installation
G7 ASD Multi-Protocol Communication Option and PG Feedback Option Manual 5
Install the #51326A connector PCB in the control board's 80-pin connector, making sure that the connector is fully seated. Next, position the option card and snap the connectors together. Finally, secure the card to the standoffs with the remaining pan head screws (see Figure 2).
Figure 2
If your option card is equipped with a data connector along its right side edge, you will need to remove the side access window of your drive's cover before reinstalling it. Place the cover upside down on a level surface (see Figure 3), and with downward pressure on your utility knife, cut along the two vertical grooves. Next, bend the resulting flap back and forth several times until it snaps apart. Clean up the opening as necessary and reattach the front cover to the drive.
Figure 3
Bend and break apart
Cut these two edges
G7 ASD Multi-Protocol Communication Option and PG Feedback Option Manual 6
4.2 Wiring
•
•
Use shielded wire for control signals and ground the unit with shielded wire.
Applicable wire size for terminal block TB1 is 0.2 to 2.5mm
2
.
•
Strip off the end of the wire by about 5mm.
•
For connecting wires, use a screwdriver that has a blade tip of 0.4mm thickness and 2.5mm width.
•
Tightening torque of the terminal block screws should be 0.22 to 0.25Nm.
•
Never route the signal or communication network lines and main circuit power wires
together. Separate the signal and communication network lines and the main circuit power wires by more than 200mm.
•
Use 0.75mm
2
wire for connecting the option’s PGCC terminal to the drive’s CC terminal.
•
Use 0.75mm
2
wire for connecting the option’s ground lug (TB2) to the drive’s G/E terminal.
5. Environmental Specifications
Item Specification
Operating Environment
Operating Temperature
Storage Temperature
Relative Humidity
Vibration
Cooling Method
Indoors, less than 1000m above sea level, do not expose to direct sunlight or corrosive / explosive gasses
-10
∼ +50°C (+14 ∼ +122°F)
-40
∼ +85°C (-40 ∼ +185°F)
20%
∼ 90% (without condensation)
5.9m/s
2
{0.6G} or less (10
∼ 55Hz)
Self-cooled
G7 ASD Multi-Protocol Communication Option and PG Feedback Option Manual 7
6. PG Feedback Operation
This section applies to both ASD-MULTICOM-A and ASD-MULTICOM-B option boards.
6.1 PG Feedback Enable Setting
To enable PG feedback with the option, set the position of switch #4 on DS1 to the ON position as shown in the figure below.
Switch #4 for PG enable
PG disabled: set all switches to OFF
(default for ASD-MULTICOM-A).
ON
OFF
1 2 3 4
PG enabled: set switch #4 to ON
(default for ASD-MULTICOM-B).
6.2 PG Power Supply Voltage Selection
The PG feedback option is capable of providing a PG power supply of 5V, 6V, 12V or 15V. To select the desired PG power supply voltage, properly set the position of switch #1, switch #2, and switch #3 on
DS1 as shown in the figure below. Table 1 provides the proper switch settings.
ON
OFF
1 2 3 4
Table 1: PG Power Supply selection
Power Supply Switch 1 Switch 2 Switch 3
5V OFF OFF OFF
15V ON ON ON
G7 ASD Multi-Protocol Communication Option and PG Feedback Option Manual 8
6.3 Pulse Input Selection
Two different types of pulse input circuitry are provided. To select the desired pulse input circuitry, properly set the position of jumpers JP1~JP6 as shown in the figure below. Table 2 provides the proper jumper settings.
Type 1 selected:
Line driver input
Type 2 selected:
Open collector input
Jumpers for Pulse Input selection
Pulse Input Type
Table 2: Jumper Settings
Characteristics
Rated voltage output with emitter/follower combination.
Higher noise-immunity characteristics.
High-speed response. Long-distance transmission capability.
Need to pay attention to waveform irregularity.
Input voltage (V
PGA1-PGA2
Input circuit diagram:
) range: 8.3V-16.6V
Type 1
Line Driver
G7 ASD Multi-Protocol Communication Option and PG Feedback Option Manual 9
Pulse Input Type Characteristics
Lower noise-immunity characteristics.
Need to pay attention to waveform irregularity and distortion.
Input circuit diagram:
Type 2
Open Collector
6.4 PG Feedback Connection
The pulse input signals are connected to terminal block TB1. Table 3 provides terminal descriptions for terminal block TB1. PGA1 and PGA2 are connected for Phase A, PGB1 and PGB2 are connected for
Phase B, and PGZ1 and PGZ2 are connected for Phase Z. The wiring for Phase Z is done only when using a Z-marker is necessary. The polarity of the pulse input signals should be as follows:
+ Side: PGA1, PGB1, PGZ1
- Side: PGA2, PGB2, PGZ2
Table 3: Terminal description for TB1
Terminal
Number
Terminal
Name
Function Specification
1 PGA1
Pulse train speed command input
(Phase A input)
3 PGB1
Pulse train speed command input
(Phase B input)
PG feedback input
Pulse train speed command input
(Phase Z input)
7 PGVC
PG power supply terminal
8 PGCC
Selectable: line driver / open collector
Maximum input frequency:
60kpps (2 phases)
120kpps (single phase)
Pulse duty cycle:
50 ± 10%
Minimum input current requirement:
2.5mA
Selectable:
5VDC, 6VDC, 12VDC, 15VDC
G7 ASD Multi-Protocol Communication Option and PG Feedback Option Manual 10
The pulse input signals should have the waveform of the figure below in terms of motor rotation direction. The encoder installation direction and signal wiring should be done accordingly.
Forward rotation or reverse rotation is determined from the quadrature orientation of the Phase A and
Phase B feedback pulses. Therefore, it should be noted that when connections are wrong, there is a
possibility for abnormal rotation of the motor.
Forward rotation
Phase A
Reverse rotation
Phase A
Phase B
Phase B
PGA1
PGA2
PGB1
PGB2
A
A
B
B
PG
X
1
X
2
X
T
3
X
4
Phase difference:Xn≧0.15T(n=1,2,3,4)
When single-phase PG feedback is used, connect to terminals PGA1 and PGA2 only. The determination of forward rotation and reverse rotation is impossible: only speed control is applicable.
G7 ASD Multi-Protocol Communication Option and PG Feedback Option Manual 11
Example of line driver (pulse input type 1) encoder connection:
ASD
G/E
PG
CC
G/E TB2
PGA1
PGA2
PGB1
PGB2
PGVC
PGCC
A
A
B
B
VCC
0V
When single-phase PG feedback is used, connect to terminals
PGA1 and PGA2 only.
Connect PGCC of option unit to CC of inverter.
Example of open collector (pulse input type 2) encoder connection:
ASD
G/E
PG
CC
G/E TB2
PGA1
PGA2
PGB1
PGB2
PGVC
PGCC
VCC
A
VCC
B
VCC
0V
When single-phase PG feedback is used, connect to terminals
PGA1 and PGA2 only.
Connect PGCC of option unit to CC of inverter.
G7 ASD Multi-Protocol Communication Option and PG Feedback Option Manual 12
6.5 Maximum Input Frequency Using an Open
Collector Encoder
When using an open collector (pulse input type 2) encoder, the rise time of the voltage when the encoder’s internal transistor turns OFF tends to be longer than the fall time when the transistor turns
ON. Therefore, if the input frequency becomes high enough, the pulse duty cycle cannot maintain the
50±10% specification. For the pulse duty cycle to be within the specified range, the generated frequency from the open collector encoder needs to be below a maximum input frequency. To calculate the maximum input frequency for an open collector (pulse input type 2) encoder, use the following equations:
(eq.1)
Maximum input
0.8
frequency (Pulses/s)
×
A
−
Voltage rise time(s)
=
3
×
10
−
6
(s)
Single phase input: A=2
Two phase input: A=4
(eq.2)
Voltage rise time
=
Encoder exclusive pulse rise time
+
(
R x C
)
Encoder exclusive pulse rise time (s) ............ Refer to encoder specifications.
R (Ω) (Input resistance)................................. internal resistance 1000 (Ω) + external resistance value (if there is external resistance).
Example
C (F) (Cable static capacitance) .................... Refer to cable specifications.
Encoder ...........LBJ-005-500 (SUMTAK), 2-phase output, pulse rise time= 0.35 x 10
-6
(s)
Cable ...............Any Brand
Using equation (eq.2)
Static capacitance=120 x 10
–12
(F/m) x 10 (m)
Voltage rise time = Encoder exclusive pulse rise time + (R x C)
= [0.35 x 10
-6
(F/m) x 10 (m)]
= 1.55 x 10
–6
(s)] + [1000 (Ω) x 120 x 10
(s)
–12
Using equation (eq.1)
0.8
Maximum input frequency (Pulses/s)
×
A
−
Voltage rise time(s)
=
3
×
10
−
6
(s)
Maximum input frequency = 87912 (Pulse/s) for single phase input
= 43956 (Pulse/s) for two phase input
G7 ASD Multi-Protocol Communication Option and PG Feedback Option Manual 13
7. LED Indicators
This section applies to ASD-MULTICOM-A option boards only.
The interface board contains two bi-color red/green status LEDs. The lower LED indicates the Module
Status (MS), and the upper LED indicates the Network Status (NS). Refer to Figure 2. The use and context of these LEDs is network-specific: refer to each network’s section in this manual for further information.
NS (Network Status)
MS (Module Status)
PCB
Figure 2: LED Indicators
G7 ASD Multi-Protocol Communication Option and PG Feedback Option Manual 14
8. Network Configuration Parameters
This section applies to ASD-MULTICOM-A option boards only.
Because the Multicom interface supports several different fieldbus physical layers and protocols, some configuration must be performed prior to inclusion on the network to inform the Multicom interface which network it is being asked to communication via, and what the characteristics of that network are.
This configuration is performed by setting ASD parameters F890 ~ F894, which are collectively known as the “Network Configuration Parameters”.
Note that the values of these 5 Network Configuration Parameters are only read by the Multicom
interface upon initialization after a drive reset or power-up condition. Therefore, if any of these parameters are changed, be sure to reset the drive to enable the changes (as will be explained later, this may actually involve resetting the drive twice: once when changing the “Network Selection” parameter to validate the chosen network, and then once more when changing any of the configuration items associated with the chosen network). Also note that although parameters F890 ~ F894 are always available, whether or not all of these configuration parameters are actually used by the Multicom interface will depend on the Multicom interface’s firmware version and the selected network.
The primary network selection is chosen by parameter F890 (refer to Table 4).
Table 4: Network Selection
Parameter Function Settings
F890
Network
Selection
0: Profibus DP
1: Modbus RTU
2: DeviceNet
0
The function and adjustment ranges assigned to parameter F890 are fixed; that is to say that parameter
F890 is always the “Network Selection” parameter. The functions and adjustment ranges of the remaining network configuration parameters (F891 ~ F894), however, will vary based on the setting of parameter F890. For example, when parameter F890 is configured for Profibus DP communications, then parameter F891 is unused, and its upper and lower adjustment limits will both be “0”. When parameter F890 is configured for Modbus RTU communications, however, then parameter F891 is used to select the Modbus network baud rate, and its adjustment range then becomes 0 ~ 7.
As previously mentioned, the values of the Network Configuration Parameters are validated by the
Multicom interface only during a drive initialization procedure. Therefore, when the drive and the
Multicom interface are initializing, the settings of the Network Configuration Parameters are read and internally saved by the Multicom interface. These internally-saved values will not change until the next initialization procedure. For this reason, two drive resets may be required when modifying the Network
Configuration Parameters: one to change and validate the network selection (parameter F890), and another one to change and validate the remaining Network Configuration Parameters (parameters F891
~ F894) if necessary.
This behavior may best be explained through the use of an example. Say, for instance, that the
Multicom interface is currently configured for Profibus DP communications (parameter F890 = 0).
Let’s also say that we would like to reconfigure the Multicom interface to communicate via Modbus
RTU at 38.4kbaud with even parity, and that all configuration parameters are currently at their factorydefault values:
1. Apply power to the drive. The drive and Multicom interface initialize. Parameter F890 is set to 0, so the Multicom interface internally configures itself for Profibus DP communications.
G7 ASD Multi-Protocol Communication Option and PG Feedback Option Manual 15
2. Change parameter F890 from its current setting of “0” to “1” to select Modbus RTU communications. Press the “ENTER” key on the drive’s panel to write the change. At this point, the Multicom interface is still configured for Profibus DP communications, so parameters F891 ~ F894 will not be adjustable beyond “0”.
3. Reset the drive (fault the drive and reset it, or momentarily power it off). Now, parameter
F890 is set to 1 during initialization, so the Multicom interface internally configures itself for
Modbus RTU communications.
4. Now when we inspect parameter F891 (now “Modbus baud rate”), the value will be 5.
Therefore, we need to change parameter F891 from its current setting of “5” (9600 baud) to
“7” (38.4kbaud). Press the “ENTER” key on the drive’s panel to write the change. At this point, the internal Modbus baud rate is still configured for 9600 baud (until the next initialization sequence takes place).
5. Similarly, change parameter F892 (now “Modbus parity & stop bits”) from its factory-default value of “1” (no parity/2 stop bits) to “2” (even parity).
6. Reset the drive once more. Now, when the drive and Multicom interface initialize, the
Multicom interface will initialize with Modbus RTU communications at 38.4kbaud and even parity. The network configuration is now completed.
Once the network configuration parameters are configured for a specific network, their settings for that network will be retained even if a different network is chosen and the second network’s configuration parameters changed. Continuing with the above example for demonstration, even if a different network is chosen, and parameters F891 ~ F894 associated with that network are changed, and then Modbus
RTU communications are once again selected by changing parameter F890 to “1”, the Modbus baud rate will still be set to 38.4kbaud, and the parity will still be set to “even” when drive/Multicom initialization has completed.
8.1 Profibus DP Configuration
When parameter F890 is selected for Profibus DP communications, no additional network configuration is required. The additional Network Configuration Parameters, therefore, are unused (refer to Table 5).
Table 5: Profibus DP Network Configuration Parameters
Parameter Function
F891
F892
F893
F894
Unused
Unused
Unused
Unused
Settings
N/A (Always 0)
N/A (Always 0)
N/A (Always 0)
N/A (Always 0)
Default
0
0
0
0
G7 ASD Multi-Protocol Communication Option and PG Feedback Option Manual 16
8.2 Modbus RTU Configuration
When parameter F890 is selected for Modbus RTU communications, then the additional Network
Configuration Parameters are assigned the functions as indicated in Table 6.
Table 6: Modbus RTU Network Configuration Parameters
Parameter Function
F892
F893
Parity & Stop Bits
Response Delay
Settings
0: 300 baud
1: 600 baud
2: 1200 baud
3: 2400 baud
4: 4800 baud
5: 9600 baud
6: 19.2 kbaud
7: 38.4 kbaud
0: no parity (1 stop bit)
1: no parity (2 stop bits)
2: even parity
3: odd parity
0 ~ 200 (0.00s ~ 2.00s)
F894 Unused N/A (Always 0)
5
1
0
0
G7 ASD Multi-Protocol Communication Option and PG Feedback Option Manual 17
8.3 DeviceNet Configuration
When parameter F890 is selected for DeviceNet communications, then the additional Network
Configuration Parameters are assigned the functions as indicated in Table 7.
Table 7: DeviceNet Network Configuration Parameters
Parameter Function
F892
F893
F894
Settings
0: 125kbaud
1: 250kbaud
2: 500kbaud
Network
Communication
Loss Action
Selected I/O
Assembly
Instance Set
0 = Set all consumed data to 0
1 = Retain last data values
2 = Issue STOP command to drive
3 = Issue EMERGENCY OFF command to drive
4 = Run preset speed #1
5 = Run preset speed #2
6 = Run preset speed #3
7 = Run preset speed #4
8 = Run preset speed #5
9 = Run preset speed #6
10 = Run preset speed #7
11 = Run preset speed #8
12 = Run preset speed #9
13 = Run preset speed #10
14 = Run preset speed #11
15 = Run preset speed #12
16 = Run preset speed #13
17 = Run preset speed #14
18 = Run preset speed #15
0: Toshiba-specific
1: Basic speed control
2: Extended speed control
Unused N/A (Always 0)
0
0
0
0
G7 ASD Multi-Protocol Communication Option and PG Feedback Option Manual 18
9. Profibus Interface
This section applies to ASD-MULTICOM-A option boards only.
9.1 Feature Summary
The Multicom interface provides a wide array of network data access and drive control features.
Combined with the flexible configuration and high-speed data transfer capabilities of the Profibus network, this allows powerful networked control and monitoring systems to be designed. Some of the main features provided by the Multicom interface which allow for this control and configurability are briefly described here:
Protocol
Profibus DP (Decentralized Periphery) as specified in European standard EN 50170. The Multicom interface can also co-exist simultaneously on networks using Profibus-FMS.
Network Baud Rates
Supports all Profibus baud rates from 9.6kbaud to 12Mbaud. The network baud rate is automatically detected and continuously monitored during operation; no parameter settings are necessary.
Power Supply
Self-contained. Powered directly from the connected drive. No external power supply devices or connections are required.
Isolation
The drive is fully optically isolated from the Profibus network. By using optically isolated connections, grounding differential problems are eliminated and noise immunity characteristics are greatly improved.
Global Control Functions
• Freeze mode:
Input (monitor) data values are held constant within the Multicom interface until the next “freeze” command or an “unfreeze” command is received. Used primarily for synchronized monitoring of multiple Profibus nodes.
• Sync mode:
Output (control) data values are held constant within the Multicom interface until the next “sync” command or an “unsync” command is received. Used primarily for synchronized control of multiple Profibus nodes.
• Clear_Data:
Network Watchdog
All output (control) data values are cleared to “0”.
A network watchdog function is always operating within the Multicom interface (if selected at time of unit commissioning). In the event of a disconnection from the Profibus network or loss of the network master, the Multicom interface will automatically set its control data to 0.
G7 ASD Multi-Protocol Communication Option and PG Feedback Option Manual 19
Indicator
A green LED (LED1) is provided to indicate when the Multicom interface has achieved the
DATA_EXCHANGE state with the Profibus network master. This serves as a convenient indicator that the Profibus master and Multicom interface are configured properly and are exchanging data.
Profibus Network Connector
The network interface is a standard DB-9 female connector. The metallic housing of the DB-9 connector is typically connected to the network shield in the attached Profibus connector. The DB-9 housing can, in turn, then be connected to earth ground if desired.
Input/Output Data
The Multicom interface’s cyclic output (control) and input (status) data sizes are selectable (modular) in
16 different configurations representing sizes of between 4 and 40 bytes.
Via these data structures, any data item (command data, monitor data and configuration parameters) available in the drive can be accessed. For detailed explanations of the format and usage of the input/output data, refer to section 9.4.
G7 ASD Multi-Protocol Communication Option and PG Feedback Option Manual 20
9.2 Profibus Interface Connection
Table 8 provides DB-9 connector pin descriptions for Profibus connector CN3.
Table 8: Pin description for Profibus connector CN3
Pin
Number
Function In/Out
3
4
5
6
Profibus network “B” (positive) data line
RTS signal – direction control for fiber optic network interface
DGND – power supply ground internally connected to the interface board’s isolated ground
VP – power supply +5v internally connected to the interface board’s isolated P5.
-
-
In/out
Out
-
-
8
9
Profibus network “A” (negative) data line
RTS signal ground reference – internally connected to the interface board’s isolated ground
-
In/out
-
To connect to the Multicom interface, complete the following steps:
1. Connect the Profibus network cable to the DB9 connector marked “CN3” on the G7 Multicom
Option. Refer to the Profibus Specification for detailed network wiring guidelines. Ensure that the
Profibus network cable is tightly screwed onto the DB9 connector, and route the cable such that it is located well away from any drive input power or motor wiring. Also take care to route the cable away from any sharp edges or positions where it may be pinched.
2. Grounding is of particular importance for reliable, stable operation. Communication system characteristics may vary from system to system, depending on the system environment and grounding method used. The metallic housing of the DB9 connector (CN3) will be regarded as the
“Shield GND” of the Multicom interface. The “Shield GND” should be connected to the shield of the Profibus network cable through the Profibus connector. To ground the network cable shield, therefore, connect a wire to the “Shield GND”, and then connect the other end of the wire to an appropriate ground. For specific requirements regarding protective grounding and the Profibus network, refer to the Profibus Standard (EN 50 170, part 1).
9.3 Unit Addressing
The Profibus node (slave) address is set via parameter F802 (inverter number parameter). Although parameter F802 has an adjustment range from 0-255, only 0-126 is an allowable addressing selection for the Profibus network. Therefore, if parameter F802 is set to 127 through 255, the Multicom interface will default to an address of 126.
G7 ASD Multi-Protocol Communication Option and PG Feedback Option Manual 21
9.4 Profibus Exchanged Data Structures
9.4.1 Output (Control) Data Format
The size of the output data structure from the network master to the Multicom interface is modular and selectable from 4 to 40 bytes. The allocation of the maximum 40 bytes of the data structure is comprised of 1 fixed four-byte command, 1 fixed four-byte extended command, 1 fixed four-byte speed reference, 5 configurable four-byte scan data selections (selectable via drive parameters F831-F835), and 1 eight-byte structure for asynchronous parameter accesses. Refer to Table 9 for details.
Table 9: Output (Control) data
Offset Data Offset Data
0 Reserved
1 Reserved
2
3
Command high byte
Command low byte
4 Reserved
5 Reserved
6
7
Extended command high byte
Extended command low byte
20
21
22
23
Parameter F833 setting high byte
:
:
Parameter F833 setting low byte
24
25
Parameter F834 setting high byte
:
26
27
:
Parameter F834 setting low byte
8 Speed reference high byte
9 :
10 :
11 Speed reference low byte
12 Parameter F831 setting high byte
13 :
14
15
18
19
:
Parameter F831 setting low byte
:
Parameter F832 setting low byte
16 Parameter F832 setting high byte
17 :
28 Parameter F835 setting high byte
29 :
30 :
31 Parameter F835 setting low byte
32 Action bits / Reserved
34
35
36
38
39
Parameter number high byte
Parameter number low byte
Reserved
Parameter data to write high byte
Parameter data to write low byte
Locations marked “Reserved” in the above table are reserved for future use. Presently, all “Reserved” output data locations are ignored by the drive. Future releases of the drive firmware, however, may use these locations for data transfer.
Throughout the remainder of this section, references may be made to internal ASD parameter numbers and data definitions. For more information regarding the specific accessible ASD parameters, please refer to the appropriate ASD Serial Communication Interface Manual (obtainable from Toshiba).
G7 ASD Multi-Protocol Communication Option and PG Feedback Option Manual 22
• Command Word (Offsets 2 and 3)
Bit-mapped drive command word internally located at parameter 0xFA06. Table 10 provides the format of this command word.
Table 10: Command Word Format
Bit Function
15 Command priority
14 Speed reference priority
13 Control selection
12 Emergency OFF command
11 Coast stop command
10 Error counter reset command
9 Forward / reverse selection
7 DC injection braking command
6 PI control OFF command
5 Brake release command
4 Excitation current command
3 Brake close command
2 Fault reset command
1 Reserved
0 Run / stop selection
• Extended Command Word (Offsets 6 and 7)
0
N/A
N/A
Speed control
N/A
N/A
N/A
Forward
N/A
N/A
N/A
N/A
N/A
N/A
N/A
--
Stop
1
Option priority
Option priority
Torque / position control
Emergency OFF
Coast stop
Reset
Reverse
Jog
DC injection braking
PI control OFF
Brake release
Excitation current
Brake close
Reset
--
Run
Bit-mapped drive extended command word internally located at parameter 0xFA23. Table 11 provides the format of this extended command word.
Table 11: Extended Command Word Format
Bit Function 0 1
15 Reverse jog command
14 Forward jog command
13 Torque limit selection bit 2
12 Torque limit selection bit 1
11 V/F selection bit 2
10 V/F selection bit 1
9 Accel/decel selection bit 2
8 Accel/decel selection bit 1
N/A
N/A
2: Torque limit 3
0: Torque limit 1
2: V/F 3
0: V/F 1
2: Accel/decel 3
0: Accel/decel 1
Jog reverse
Jog forward
3: Torque limit 4
1: Torque limit 2
3: V/F 4
1: V/F 2
3: Accel/decel 4
1: Accel/decel 2
7 Brake test command
6 Brake response command
Brake close
Brake close
Brake release
Brake release
5 Reserved -- --
4 Reserved
3 Preset speed selection bit 4 12: 12 th
--
speed 13: 13 th
2
1
0
Preset speed selection bit 3
Preset speed selection bit 2
Preset speed selection bit 1
8: 8
4: 4 th th
speed 9: 9
speed 5: 5
0: OFF th th
speed 14: 14
speed 10: 10
speed
1: 1 st
speed
6: 6
2: 2 th nd th th
speed 15: 15
speed 11: 11
speed
--
7: 7
speed 3: 3 th rd th
speed th
speed
speed
speed
G7 ASD Multi-Protocol Communication Option and PG Feedback Option Manual 23
• Speed Reference Command (Offsets 8 ∼∼∼∼ 11)
Unsigned 16-bit value located at parameter 0xFA07. The data contained in the speed reference command word is the desired speed reference command multiplied by 100, and then converted to hexadecimal. In other words, if a speed reference command of 55.34Hz is desired, then 55.34 x 100 =
5534, which converted to hexadecimal is 0x159E. The speed reference command low byte (offset 11) must therefore contain 0x9E and the next-highest byte (offset 10) must contain 0x15.
If the speed reference command exceeds limiting drive parameters (such as the Upper Limit Frequency or Maximum Frequency), then the drive will ignore it, maintaining its current setting.
• Drive Command Scan Data (Offsets 12 ∼∼∼∼ 31)
Table 12 provides a list of the available command scan data selections (selectable via drive parameters
F831 ∼F835). The “Parameter” column indicates the drive’s internal parameter to which the corresponding selection is mapped.
Table 12: Drive Command Scan Data
F831
∼∼∼∼F835
Setting
10
11
12
13
4
5
6
7
8
9
1 RESERVED
2 RESERVED
3
-
-
-
Incremental speed reference 0.01Hz
Absolute torque limit
Positive torque limit
Negative torque limit
Torque command
Speed torque bias
Tension torque bias
0.01%
0.01%
- 0xFFFF
-
-
0 ~ 500
0 ~ 25000
0 ~ 25000
-
-
0xFA08
0xFA34
0x0441
0.01% 0 ~ 25000 0x0443
0.01% -25000 ~ 25000 0xFA33
0.01% -25000 ~ 25000
0.01% -25000 ~ 25000
0x0726
0x0727
Load balance gain
Drooping gain
Speed loop proportional gain
Speed loop integral gain
0.01
0.01
0.1
0.1
0 ~25000
0 ~ 10000
32 ~ 10000
100 ~ 2000
0x0728
0x0320
0x0376
0x0377
15 Load moment of inertia
16 RESERVED
-
0.0001
-
-
100 ~ 10000
-
0xFA50
0xFA35
-
Note 1: Items marked as “RESERVED” in Table 12 are reserved for future use. Selecting one of the corresponding values as command scan data will have no effect on drive operation.
Note 2: Although not disallowed, avoid configuring more than 1 scan command data parameter with the same command data selection (for example, do not set both F831 and
F832 to “3”, etc.). Unexpected drive behavior could result if different data values are written to the corresponding command locations.
Note 3: Parameters F831
∼
F835 are only validated on drive reset or power-up.
Therefore, if any of these parameters are changed, be sure to reset the drive to validate the changes.
Note 4: Data range checking is not performed on command scan items. If a value outside of a specific item’s valid range is written to the drive, that value will be accepted, but ignored by the drive.
G7 ASD Multi-Protocol Communication Option and PG Feedback Option Manual 24
• Action Bits / Parameter Number (Offsets 32 ∼∼∼∼ 35)
Parameter action bits and 16-bit parameter number. Refer to section 9.6 for a detailed explanation of these items.
• Parameter Data (Offsets 38 and 39)
During parameter writes, this contains the data to write. Refer to section 9.6 for a detailed explanation of this location.
9.4.2 Input (Status) Data Format
The size of the input data structure from the Multicom interface to the network master is modular and selectable from 4 to 40 bytes. The allocation of the maximum 40 bytes of the data structure is comprised of 1 fixed four-byte status, 1 fixed four-byte output speed reference, 6 configurable four-byte scan data selections (selectable via drive parameters F841-F846), and 1 eight-byte structure for asynchronous parameter accesses. Refer to Table 13 for details.
Table 13: Input (Status) data
0 Reserved
1 Reserved
2
3
Status high byte
Status low byte
4 Operating speed high byte
5 :
6 :
7 Operating speed low byte
20
21
Parameter F844 setting high byte
:
22
23
:
Parameter F844 setting low byte
24 Parameter F845 setting high byte
25 :
26 :
27 Parameter F845 setting low byte
8 Parameter F841 setting high byte
9 :
10 :
11 Parameter F841 setting low byte
12 Parameter F842 setting high byte
13 :
14
15
18
19
:
Parameter F842 setting low byte
16 Parameter F843 setting high byte
17 :
:
Parameter F843 setting low byte
28 Parameter F846 setting high byte
29 :
30 :
31 Parameter F846 setting low byte
32 Response bits / Reserved
34
35
36
38
39
Parameter number response high byte
Parameter number response low byte
Reserved
Parameter data response high byte
Parameter data response low byte
Locations marked “Reserved” in the above table are reserved for future use. Presently, all “Reserved” input data is set to 0 by the drive. Future releases of the drive firmware, however, may use these locations for data transfer.
G7 ASD Multi-Protocol Communication Option and PG Feedback Option Manual 25
• Status Word (Offsets 2 and 3)
Bit-mapped status word. Table 14 provides the format of this status word.
Table 14 : Status Word Format
Bit Function 0 1
15 Ready for operation status
(not including MOFF)
14 Drive healthy signal
13 Ready for operation status (not including ST)
12 Ready for operation status
(including ST)
11
10
9
7
6
5
4
3
2
1
Control mode status
Speed limit status
Forward / reverse status
DC injection braking
OL alarm status
PI control status
Alarm status
Serious fault status
Run / stop status
Alarm stop status
Not ready Ready
Alternating heartbeat: “0” for 1s, then “1” for 1s
Not ready
Not ready
Speed control
Normal
Forward
Normal
Normal
Normal
Normal
No alarm
Normal
Stopped
None
None
Ready
Ready
Torque / position control
Speed limiting
Reverse
Jogging
DC injection braking active
OL alarm
PI control inactive
Alarm
Serious fault
Running
Alarm stopped
Faulted
• Operating Speed (Offsets 4 ∼∼∼∼ 7)
Obtained from drive parameter 0xFE58. Continuously reports the drive’s operating speed. In order to determine the drive’s actual output speed, the data contained in the output speed must first be converted from hexadecimal to decimal, and then divided by 100. For example, if offset #6 is 0x12 and offset #7 is 0x34, then 0x1234 converted to decimal is 4660. Dividing this number by 100, the actual operating speed of 46.60Hz is obtained.
G7 ASD Multi-Protocol Communication Option and PG Feedback Option Manual 26
• Drive Status Scan Data (Offsets 12 ∼∼∼∼ 31)
Table 15 provides a list of the available status scan data selections (selectable via drive parameters
F841-F846). The “Parameter” column indicates the drive’s internal parameter to which the corresponding selection is mapped. More detailed explanations of some of these status items follow
Table 15.
Table 15: Drive Status Scan Data
F841~F846
Setting
4
5
6
7
1
2
3
8
9
10
11
14
15
16
Alarm code monitor
-
-
Operating speed 0.01Hz
Real-time speed feedback 0.01Hz
Filtered speed feedback
Internal torque reference
Output current
Excitation current
0.01Hz
0.01% -32767 ~ 32767
0.01%
-
-
0 ~ 40000
0 ~ 40000
0 ~ 40000
0 ~ 32767
0.01% -32767 ~ 32767
0xFFFF
0xFC91
0xFE58
0xFE61
0xFE62
0xFE56
0xFE03
0xFE21
Torque current
Overload value
Accel / Decel torque reduction
Motor counter data
0.01% -32767 ~ 32767
0.01% 0 ~ 10000
0.01% -32767 ~ 32767
0xFE20
0xFE59
0xFE60
VI input
RR input
RX input
-
-
-
0.01%
0 ~ 65535
-
-
0 ~ 10000
0.01% 0 ~ 10000
0.01% -10000 ~ 10000
0xFE33
0xFC90
0xFE06
0xFE36
0xFE35
0xFE37
Note 1: Parameters F841
∼
F846 are only validated on drive reset or power-up.
Therefore, if any of these parameters are changed, be sure to reset the drive to validate the changes.
G7 ASD Multi-Protocol Communication Option and PG Feedback Option Manual 27
Alarm Code Monitor
Bit-mapped alarm code monitor word internally located at parameter 0xFC91. Table 16 provides the format of this alarm code monitor word.
Table 16: Alarm Code Monitor Word Format
Fault Code
Bit Function
15 Reserved
14 Reserved
13 Reserved
12 Communication error alarm
(logic / RS-485 / message transmission)
11 Communication error alarm
(scan transmission)
10 Cumulative run timer alarm
9 Dynamic braking resistor overload alarm
8 Over-torque alarm
7 Low current alarm
6 Low control power alarm
5 Low main power alarm
4 Over-voltage alarm
3 Overheat alarm
2 Motor overload alarm
1 Drive overload alarm
0 Over-current alarm
--
--
--
N/A
N/A
N/A
N/A
N/A
N/A
N/A
N/A
N/A
N/A
N/A
--
--
--
Alarm on
Alarm on
Alarm on
Alarm on
Alarm on
Alarm on
Alarm on
Alarm on
Alarm on
Alarm on
Alarm on
Current fault code internally located at parameter 0xFC90. Table 17 provides the list of fault codes with descriptions.
Table 17: Fault Codes
Fault Code
0001
0002
0003
0004
0005
0006
0007
0008
0009
000A
000B
000C
000F
Over-current fault during acceleration
Over-current fault during deceleration
Over-current fault during constant-speed run
Load-side over-current fault at start-up
Over-current fault of U-phase arm
Over-current fault of V-phase arm
Over-current fault of W-phase arm
Input error-phase fault
Output error-phase fault
Over-voltage fault during acceleration
Over-voltage fault during deceleration
Over-voltage fault during constant running speed overload overload
Dynamic braking resistor overload
0010 Overheat
OFF
Fault Description Panel Display
NERR
OC1
OC2
OC3
OCL
OCA1
OCA2
OCA3
EPH1
EPHO
OP1
OP2
OP3
OL1
OL2
OLR
OH
E
G7 ASD Multi-Protocol Communication Option and PG Feedback Option Manual 28
0021
0022
0024
0025
0026
0027
0028
0029
002A
002B
002C
Fault Code Fault Description
0012
0013
0014
0015
EEPROM write error
EEPROM initial read error (control EEPROM)
EEPROM initial read error (main circuit EEPROM)
Main RAM error
0016 Main ROM error error
0018
0019
001A
001B
Communication interruption error
Gate array error
Output current detect fault
Option board error
001C Flash memory error fault
001E
001F
Under-voltage fault (main power)
Under-voltage fault (control power)
Earth fault (software detection)
Earth fault (hardware detection)
Dynamic braking resistor over-current fault
DC section over-current fault during acceleration
DC section over-current fault during deceleration
DC section over-current fault during constant-speed run
Automatic tuning error
Drive type error
Sink / source selection error
Electromagnetic brake error
Encoder disconnected fault
Panel Display
UP1
UP2
OT
EF1
EF2
EFU
OCR
OC1P
OC2P
OC3P
ETN
ETYP
E-10
E-11
E-12
E-13
E-14
E-17
EEP1
EEP2
EEP3
ERR2
ERR3
ERR4
ERR5
ERR6
ERR7
ERR8
ERR9
UC
G7 ASD Multi-Protocol Communication Option and PG Feedback Option Manual 29
Input Terminals
Bit-mapped input terminal word internally located at parameter 0xFE06. Table 18 provides the format of this input terminal word.
Table 18: Input Terminals
Bit
Terminal Name
(Expansion Terminals)
Function
7
6
5
4
3
2
15
14
13
12
11
10
9
8
(B15)
(B14)
(B13)
(B12)
(B11)
(B10)
(B9)
(B8)
S4
S3
S2
S1
RES
ST
Input terminal selection 16
Input terminal selection 15
Input terminal selection 14
Input terminal selection 13
Input terminal selection 12
Input terminal selection 11
Input terminal selection 10
Input terminal selection 9
Input terminal selection 8
Input terminal selection 7
Input terminal selection 6
Input terminal selection 5
Input terminal selection 4
Input terminal selection 3
1
0
R
F
Input terminal selection 2
Input terminal selection 1
• Response Bits / Parameter Number (Offsets 32 ∼∼∼∼ 35)
Parameter
Number
F126
F125
F124
F123
F122
F121
F120
F119
F118
F117
F116
F115
F114
F113
F112
F111
0 1
OFF ON
OFF ON
OFF ON
OFF ON
OFF ON
OFF ON
OFF
OFF
OFF ON
OFF ON
OFF ON
OFF ON
OFF
OFF
OFF
OFF
ON
ON
ON
ON
ON
ON
Parameter response bits and 16-bit parameter number. Refer to section 9.6 for a detailed explanation of these items.
• Parameter Data (Offsets 38 and 39)
During parameter reads, this word contains the requested data response. Refer to section 9.6 for a detailed explanation of this location.
G7 ASD Multi-Protocol Communication Option and PG Feedback Option Manual 30
9.5 Diagnostics
When the drive faults, 1 byte of high-priority user diagnostics is supplied to the Profibus master. The format of the diagnostics byte is shown in Table 19.
Table 19: Drive Diagnostics
Bit #: 7 6 5 4 3 2 1 0
Reserved bits indicated in the above table are currently set to “0” by the Multicom interface, but may be used to transfer additional diagnostics data in future releases. When the drive’s fault condition is cleared, a diagnostics status update is generated indicating the drive’s exit from the faulted state.
G7 ASD Multi-Protocol Communication Option and PG Feedback Option Manual 31
9.6 Asynchronous Drive Parameter Access
9.6.1 Parameter Number / Action Output Words
To access drive parameters, 2 output words and 2 action bits are provided in the drive’s output data structure. The structure of these output words and action bits is as follows:
Action Bits
Bit #: 15 14 13 12 11
Reserved
Action bits (offset 32) Reserved (offset 33)
Parameter Number Word
Bit #: 15 12
Parameter number
Parameter number low byte (offset 35) high byte (offset 34)
Parameter Data Write Word
Bit #: 15 12
Parameter data
Parameter data to write high byte (offset 38)
Parameter data to write low byte (offset 39)
Note that all locations marked “Reserved” are ignored by the Multicom interface.
G7 ASD Multi-Protocol Communication Option and PG Feedback Option Manual 32
9.6.2 Parameter Number / Action Input Words
The response by the Multicom interface to parameter read and write requests is placed in 2 input words and 2 input bits of the input data structure. The structure of these data items is as follows:
Response Bits
Bit #: 15 14 13 12 11
Reserved
Parameter Number Response Word
Bit #: 15 12
Action response bits
(offset 32)
Parameter number
Parameter number response high byte
(offset 34)
Reserved (offset 33)
Parameter number response low byte
(offset 35)
Parameter Data / Error Code Response Word
Bit #: 15 12
Parameter data / error code
Parameter data response high byte (offset 38)
Parameter data response low byte (offset 39)
Note that all locations marked “Reserved” are set to 0 by the Multicom interface.
G7 ASD Multi-Protocol Communication Option and PG Feedback Option Manual 33
9.6.3 Drive Parameter Access Procedure
In order to read from a drive parameter or write to a drive parameter, two control bits are provided in the drive’s output data structure. These bits, labeled Req1 and Req0 in the Action Bits word, can have the following values:
Req1 Req0 Meaning
0 0.............. No action (idle state) read
1
1
0.............. Parameter write (RAM & EEPROM)
1.............. Parameter write (RAM only)
Similarly, when the drive responds to a parameter read or write request, two status bits are provided in the drive’s input data structure. These bits, labeled Resp1 and Resp0 in the Action Bits Response word, can have the following values:
Resp1 Resp0
0
0
1
Meaning
0.............. No action (idle state acknowledge)
1.............. Parameter read success acknowledge
0.............. Parameter write success acknowledge
1 1.............. Error
Note that the Multicom interface will respond with Resp1:Resp0 = 1:0 upon a successful parameter write, regardless of whether the write was to RAM & EEPROM or to RAM only.
Performing a parameter read or write action from the Profibus master involves the following process:
1. Send a “no action” code (Req1=0 and Req0=0). Every parameter access must begin from the idle state. Once this state is sent, the Profibus master must then wait for the Multicom interface to respond with an idle state acknowledge (Resp1=0 and Resp0=0).
2. If the action is to be a data write, set the parameter data in the parameter data write word. If the action is to be a data read, the parameter data write word value is irrelevant.
3. Set the parameter number and action code (Req1 and Req0). For an explanation of parameter numbers, refer to section 9.7.
4. Once the Multicom interface receives the read or write request, it will begin processing it. The time required to complete the request depends primarily on the specific register being requested and the drive’s internal state at the time of the request, but can vary from several milliseconds to several tens of milliseconds.
5. Once the Multicom interface has completed the request, it will place its response in the action bits response, parameter number response, and data / error code response locations:
• If the request was a read, and the read was performed successfully, this will be indicated to the master by Resp1:Resp0 changing from 0:0 to 0:1. The parameter number response will equal the accessed parameter number, and the resulting data read will be placed in the data / error code response word.
• If the request was a write, and the write was performed successfully, this will be indicated to the master by Resp1:Resp0 changing from 0:0 to 1:0. The parameter number response will equal the accessed parameter number, and the data written to the drive will be reflected in the data / error code response word.
• If an error occurred during the read or write request, this will be indicated to the master by
Resp1:Resp0 changing from 0:0 to 1:1. The parameter number response will equal the parameter number that the master was attempting to access, and an error code reflecting the failure cause will be placed in the data / error code response word. For a list of possible error codes, refer to section 9.6.4.
G7 ASD Multi-Protocol Communication Option and PG Feedback Option Manual 34
6. In order to perform another parameter read or write, the master must once again send a “no action” code (Req1=0 and Req0=0), and the Multicom interface must once again respond with an idle state acknowledge (Resp1=0 and Resp0=0) before the next read or write action can take place. Until a “no action” code is sent to the Multicom interface, the interface will ignore all data in the action bits, parameter number and parameter write data words. Also, as long as the master sends the “no action” code, the Multicom interface will loop-back in the parameter number response word and parameter data / error code response word whatever data is sent to it in the corresponding output words.
9.6.4 Register Access Error Codes
When a parameter read or write error occurs, one of the following error codes will be returned in the parameter data response word:
Error Code
Meaning
0x0000 ..................... cannot execute (access error)
0x0001 ..................... data error (written data value outside of valid range)
0x0002 ..................... invalid parameter number
0x0064 ..................... attempt to write to a read-only parameter
0x0065 ..................... attempt to read from a write-only parameter
0x0066 ..................... other / unclassified error
9.7 Parameters
The parameters that can be accessed via the parameter access method outlined in section 9.6 are defined in the Toshiba ASD Operation Manual and/or the ASD Serial Interface Manual. The accessible parameters, their access behaviors and data ranges may vary depending on the drive’s firmware revision.
The following parameters, which are not implemented in the drive, are used to access local information on the Multicom interface:
Parameter Function Read / Write Adjustment Range
0xFC82
Multicom interface firmware version/revision
Read only
High byte = firmware version
Low byte = firmware revision
If an attempt is made to write to this register, error code number 0x0064 (WRITE_TO_READONLY) will be returned in the parameter data/error code field of the acyclic data.
G7 ASD Multi-Protocol Communication Option and PG Feedback Option Manual 35
10. RS-485 Interface
This section applies to ASD-MULTICOM-A option boards only.
10.1 Physical Layer
Figure 3 shows the physical layer for the RS-485 portion of the Multicom interface. This circuit diagram is provided as an aid to the system (network) designer to ensure that externally-connected circuitry will provide the required voltages etc. necessary for sufficient and robust communications.
P5ISO
R37
47k
A
B
TB1:9
TB1:10
RS-485
NETWORK
ZD1
6.2V
ZD2
6.2V
GNDISO
ZD3
6.2V
ZD4
6.2V
GNDISO
R38
47k
GNDISO
TB1:11
R26
200
GNDISO
Figure 3: RS-485 Physical Layer
G7 ASD Multi-Protocol Communication Option and PG Feedback Option Manual 36
10.2 Modbus RTU
10.2.1 Configuration
Besides the Modbus network selection and configuration parameters (F890-F894) described in Section
8.2, the only other ASD parameter requiring configuration is the ASD’s “Inverter Number” parameter
(F802). This parameter setting is used as the drive’s Modbus station address.
Some important points to note regarding parameter F802:
• Parameter F802 is only validated after a drive reset. Therefore, if this parameter is changed, remember to reset the drive to validate the change.
• The standard factory setting for parameter F802 is 0, which is reserved for Modbus broadcast transmissions. To be valid, this parameter must be set to a value between 1 and 247. If parameter
F802 is 0 or 248
∼ 255 when Modbus communications are initialized, the Multicom interface’s
“Network Status” LED (the lower LED) will flash red to indicate the configuration error, and network communications will not be enabled.
If ASD control (frequency command input, RUN/STOP, etc.) is to be performed via the Modbus network, then the drive’s Command Mode Selection and/or Frequency Mode Selection parameters must be configured to use the communication card as the drive’s command source location, or the “option priority” bits of the basic command word (Modbus register 0x0A07) must be set accordingly. For information on the specific setting methods and values of the Command Mode and Frequency Mode
Selection parameters, please refer to the G7 Adjustable Speed Drive Operation Manual.
10.2.2 Communication Formats
A brief note about Modbus communication formats: According to the
Modicon Modbus Protocol
Reference Guide, the specifications for the Modbus RTU communication mode is as follows:
Coding System: ............... 8-bit binary, hexadecimal 0 ∼ 9, A ∼ F
Two hexadecimal characters contained in each 8-bit field of the message
Bits per Byte: .................. 1 start bit
8 data bits, least significant bit sent first
1 bit for even/odd parity; no bit for no parity
1 stop bit if parity is used; 2 bits if no parity
Error Check Field: ......... Cyclical Redundancy Check (CRC)
According to the Modicon Modbus specification, therefore, the number of bits per byte in RTU mode is
1 start + 8 data + 1 parity + 1 stop (if parity is used), or 1 start + 8 data + 2 stop (if parity is not used), resulting in an RTU data frame that is fixed at 11 bits per byte.
In addition to these standard specified data frame sizes, the Multicom Modbus interface offers an optional configuration of providing for only 1 stop bit when no parity is selected. As indicated in Table
6 on page 17, by setting parameter F892 (Parity & Stop Bits) to “0”, the RTU data frame size is modified to consist of 1 start + 8 data + 1 stop bit = 10 bits per byte.
G7 ASD Multi-Protocol Communication Option and PG Feedback Option Manual 37
10.2.3 Modbus/ASD Register Mappings
The Multicom Modbus interface acts as a relatively straightforward network gateway for the ASD into which it is installed. In general, Modbus holding registers (4X references) are directly mapped to corresponding ASD registers (also sometimes referred to as “communication numbers” or “parameter numbers”) with a direct 1-to-1 correspondence. The relationship between Modbus holding registers and their ASD register counterparts is as follows:
Modbus holding register = ASD register + 1
This means that in order to access a specific ASD register, simply add 1 to its index and access that
Modbus holding register. The reason for this offset is due to the fact that ASD registers begin at index
0, while Modbus holding registers begin at index 1.
The only minor exception to the above 1-to-1 mapping takes place in the “upper address” registers in the
ASD. By inspecting the Toshiba Serial Communications Manual, one can observe that the ASD registers are divided into two distinct regions within the full 0x0000 ~ 0xFFFF ASD register map: the
“lower address” range covers from 0x0000 to 0x09FF, and the “upper address” range covers from
0xFA00 to 0xFFFF (not all values within those ranges access valid ASD registers, of course). For access consistency and because some Modbus clients are unable to access holding registers with indexes greater than 9999
10
(0x270F), the Multicom Modbus interface automatically maps all “upper address”
ASD registers into the contiguous region immediately following the “lower address” range. To take advantage of this feature, simply drop the initial “F” on any register index in the “upper address” range
(and add 1 to that number to obtain the corresponding Modbus register), and the register request will automatically access the correct internal ASD register.
For example, if we wish to read ASD register 0xFE06 (input terminal status), we would change the
0xFE06 to 0x0E06, and then add 1 to obtain the resultant Modbus register: 0x0E07 (3591
10
).
Therefore, making a request to read Modbus register 0x0E07 will return the input terminal status located at ASD register 0xFE06. If desired, it is also acceptable to access the “upper address” registers at their original locations, as their default (0xFXXX) locations can still be accessed. Continuing with the previous example, ASD register 0xFE06 can therefore be equally accessed by requesting either Modbus register 0x0E07 or 0xFE07 (65031
10
).
In order to avoid any possible confusion regarding this register-mapping scheme, this manual will always explicitly use the terms “ASD register” or “Modbus register” where the intended usage may not be clear. If the term “register” is used alone, then “Modbus register” will be the intended meaning by default.
With the exception of the “upper address” register mapping feature explained above and the programmable pointer registers feature detailed in Section 10.2.6, the Multicom Modbus interface does not in any way modify or otherwise alter valid register access requests originating from the Modbus client. By adhering to this design parameter, the availability and interpretation of any Modbus registers is entirely determined by the attached drive. In this way, the Modbus interface allows itself to become virtually “transparent” on the network, essentially allowing the Modbus client to carry on a dialog directly with the drive.
An overview of the entire mapping configuration can be found in Section 10.2.9.
G7 ASD Multi-Protocol Communication Option and PG Feedback Option Manual 38
10.2.4 ASD Scan Registers
Although all available ASD command, status and configuration data is accessible via the Modbus interface, there are certain fundamental command and status registers that virtually all applications will likely find useful. These fundamental registers will probably be accessed quite frequently, and “priority handling” of these select registers would therefore benefit network throughput.
For this reason, certain ASD registers can be configured for special handling, which provides very fast access response. These registers are referred to as “scan registers”. The Multicom Modbus interface provides three types of scan registers:
1. Fixed (read or write) read/status
The fixed scan registers listed in Table 20. These registers provide fast response to the indicated read or write request at all times.
Table 20: Fixed Scan Registers
ASD
Register
Modbus Register
Read /
Write
Function
(2567
10
(2596
10
(2568
10
) Write Option board frequency command
10
) Read
Table 21 provides a list of the available read/status scan selections. These are selectable via drive parameters F841-F846, which allows a total of six read scan registers to be configured.
Table 21: Drive Status Scan Data
F841~F846
Setting
1
2
3
4
5
6
7
8
9
10
11
12
13
14
15
16
Alarm code monitor
Output frequency
Real-time speed feedback
Filtered speed feedback
Internal torque reference
Output current
Excitation current
Torque current
Overload value
Accel / Decel torque reduction
Motor counter data
Fault code
Input terminal
VI input
RR input
RX input
Function
ASD
Register
N/A
0xFC91
0xFE58
0xFE61
0xFE62
0xFE56
0xFE03
0xFE21
0xFE20
0xFE59
0xFE60
0xFE33
0xFC90
0xFE06
0xFE36
0xFE35
0xFE37
Modbus Register
N/A
0x0C92 (3218
10
)
0x0E59 (3673
10
)
0x0E62 (3682
10
)
0x0E63 (3683
10
)
0x0E57 (3671
10
)
0x0E04 (3588
10
)
0x0E22 (3618
10
)
0x0E21 (3617
10
)
0x0E5A (3674
10
0x0E61 (3681
10
)
)
0x0E34 (3636
10
)
0x0C91 (3217
10
)
0x0E07 (3591
10
)
0x0E37 (3639
10
)
0x0E36 (3638
10
)
0x0E38 (3640
10
)
G7 ASD Multi-Protocol Communication Option and PG Feedback Option Manual 39
Table 22 provides a list of the available write/command scan selections. These are selectable via drive parameters F831-F835, which allows a total of five write scan registers to be configured.
Table 22: Drive Command Scan Data
F831
∼∼∼∼F835
Setting
Function
1 RESERVED
2 RESERVED
3
4
5
6
7
8
9
10
11
12
13
14
Incremental speed reference
Absolute torque limit
Positive torque limit
Negative torque limit
Torque command
Speed torque bias
Tension torque bias
Load balance gain
Drooping gain
Speed loop proportional gain
Speed loop integral gain
Output terminals
15 Load moment of inertia
16 RESERVED
ASD
Register
Modbus Register
N/A
N/A
N/A
0xFA08
0xFA34
0x0441
0x0443
0xFA33
0x0726
0x0727
0x0728
0x0320
0x0376
0x0377
0xFA50
0xFA35
N/A
N/A
N/A
N/A
0x0A09 (2569
10
)
0x0A35 (2613
10
)
0x0442 (1090
10
)
0x0444 (1092
10
)
0x0A34 (2612
10
)
0x0727 (1831
10
)
0x0728 (1832
10
)
0x0729 (1833
10
)
0x0321 (801
10
)
0x0377 (887
10
)
0x0378 (888
10
)
0x0A51 (2641
10
)
0x0A36 (2614
10
)
N/A
G7 ASD Multi-Protocol Communication Option and PG Feedback Option Manual 40
Scan Register Notes
• Items marked as “RESERVED” in Table 22 are reserved for future use. Selecting one of the corresponding values as command scan data will have no effect on drive operation.
• Configurable scan register selection parameters F831∼F835 and F841∼F846 are only validated on drive reset or power-up. Therefore, if any of these parameters are changed, be sure to reset the drive to validate the changes.
• Data range checking is not performed on command scan items. If a value outside of a specific item’s valid range is written to the Modbus interface, that value will be accepted by the interface, but ignored by the drive.
• Command scan data is written to drive RAM only, and therefore not retained when power is lost.
• Initial values for command scan data (before the first network update is received) are 0.
• Basic command (Modbus register 0x0A07) and extended command (Modbus register 0x0A24) registers: for these command words to have an actual effect on the drive’s operation, either the drive’s “command mode selection” parameter must be set such that option board commands are valid, or the “option priority” bit (bit #15) of the basic command word must be set via Modbus communications.
• Basic command (Modbus register 0x0A07): for a detail of this register, refer to Table 10 on page
23.
• Extended command (Modbus register 0x0A24): for a detail of this register, refer to Table 11 on page 23.
• Option board frequency command (Modbus register 0x0A08): for this value to have an actual effect on the drive’s operation, either the drive’s “frequency mode selection” parameter must be set such that option board frequency command is valid, or the “option priority” bit (bit #14) of the basic command word must be set via Modbus communications.
10.2.5 Supported Modbus Functions
The Multicom Modbus interface supports three Modbus commands: command 3 (0x03: read holding registers), command 6 (0x06: preset single register) and command 16 (0x10: preset multiple registers).
Not all drive registers support all commands (for example, certain drive registers may be read-only or write-only): refer to the Toshiba Serial Communications Manual for specific details about the various drive registers. Table 23 indicates the maximum number of registers that can be read/written in one packet transaction.
Table 23: Read / Write Limits
Command Read Max Write Max
6 N/A 1 register only
Except for scan register writes (refer to Section 10.2.4), all register writes update the drive’s EEPROM.
For this reason, do not write to any single non-scan register more than 10,000 times or EEPROM damage may occur.
G7 ASD Multi-Protocol Communication Option and PG Feedback Option Manual 41
10.2.6 Programmable Pointer Registers
Modbus registers 0x0C00 ~ 0x0C1F (3072
10
~ 3103
10
) and 0x0C20 ~ 0x0C3F (3104
10
~ 3135
10 collectively used by the Multicom Modbus interface as programmable pointer data and address
) are registers, respectively. Programmable pointer registers (PPR) allow the user to access non-consecutive
Modbus registers with only one Modbus transaction.
Registers 0x0C20 ~ 0x0C3F (the PPR “address” registers: 32 total) are used to define other Modbus register addresses from which you would like to read or write, and registers 0x0C00 ~ 0x0C1F (the PPR
“data” registers: 32 total) are the actual registers used to access the data pointed to by the address registers.
For example, if you would like to continuously read the data from ASD registers 0xFD00, 0xFE01,
0xFE04 and 0xFE05, the standard Modbus register configuration would require 3 read commands to be issued: one reading 1 Modbus register starting at register 0x0D01, one reading 1 Modbus register starting at register 0x0E02, and one reading 2 Modbus registers starting at register 0x0E05 (recall the
“+1” offset between drive and Modbus registers). To conserve network bandwidth and speed processing time, however, the PPRs can be used to allow the same information to be accessed, but by only issuing 1 command which reads 4 Modbus registers.
To configure this function, program as many address registers as necessary (up to 32) in the 0x0C20 ~
0x0C3F range with the Modbus register numbers you would like to continuously access. In this example, we would write a value of 0x0D01 (the first Modbus register we want to access), to register
0x0C20, a value of 0x0E02 to register 0x0C21, a value of 0x0E05 to register 0x0C22, and a value of
0x0E06 to registers 0x0C23. The data located at the relevant drive registers can then be obtained by accessing the corresponding data registers in the 0x0C00 ~ 0x0C1F range: data register 0x0C00 corresponds to address register 0x0C20, data register 0x0C01 corresponds to address register 0x0C21, etc. Therefore, the 4 registers that are to be monitored can now be accessed simply by issuing 1 holding register read command with a length of 4 starting from Modbus register 0x0C00. The returned data will be the data obtained from ASD registers 0xFD00, 0xFE01, 0xFE04, and 0xFE05 (in that order).
Notes:
• PPR address register setting values are MODBUS registers. That is, Modbus registers = ASD registers + 1.
• PPR address registers are updated immediately when changed (no drive reset is required).
• The values of the PPR address registers (0x0C20 ∼ 0x0C3F) are stored in the Modbus interface’s nonvolatile EEPROM. Therefore, do not write to any of these registers more than 100,000 times.
Typically, these registers would only be written to once, when the drive and Modbus network are first commissioned.
10.2.7 Response Delay Timer Function
As mentioned in section 8.2, ASD parameter F893 contains the setting for a response delay timer function. This function is useful for applications where it may not be desirable for the Modbus interface to respond immediately to the network after a read/write request. An example of this may be when a radio modem that must be switched from receive mode to transmit mode is being used.
The response delay timer is adjustable in 10ms increments from 0s to 2.00s (factory setting = 0s). A response delay of 0s means that there is no artificial delay inserted; response packets will be sent by the
Modbus interface as soon as they are available. When non-zero, the delay timer starts when a complete packet is received, and a response will not be sent until the timer has expired (at a minimum). Note that this time value only sets a minimum response delay value - depending on the quantity and location of
G7 ASD Multi-Protocol Communication Option and PG Feedback Option Manual 42
registers read / written, more time may actually be required by the Modbus interface before a complete response is formulated and ready to be returned to the network.
The response delay timer value is read only upon initialization. Therefore, if the delay value is changed, the drive must be reset for the new value to take effect.
10.2.8 LED Indicators
If the ASD’s “Inverter Number” parameter (F802) is not set to a value between 1 and 247, the Module
Status LED will flash red upon initialization to indicate the configuration error.
Whenever a faulty Modbus packet is detected, the Network Status LED will briefly flash red to indicate the faulty packet. This can be used as a helpful indicator when communications are not working, and will usually be the result of incompatible network settings (baud rate, parity, etc.) or reversed RS-485 wires.
10.2.9 Register Summary
Table 25 presents an overview of all accessible information within the entire Modbus register map.
Although the majority of the mapping directly accesses the corresponding ASD registers, not all ASD registers are available. The specific ASD registers that can be accessed are defined in the Toshiba
ASD
Operation Manual and/or the ASD Serial Interface Manual. In addition, the accessible registers, their access behaviors and data ranges may vary depending on such issues as the drive’s capacity and control firmware revision.
Table 24 lists the Modbus registers that access local information on the Multicom interface. These items are also indicated in Table 25.
Table 24: Local Modbus Interface Access
Modbus Register
0x0C00~0x0C1F /
0xFC00~0xFC1F
0x0C20~0x0C3F /
0xFC20~0xFC3F
0x0C82 / 0xFC82
Function
PPR data registers
PPR address registers
Multicom interface firmware version/revision
Read / Write
According to referenced register
Read/Write
Read only
Adjustment Range
According to referenced register
0x0001 ~ 0xFFFF
(1
10
~ 65535
10
)
High byte = firmware version
Low byte = firmware revision
G7 ASD Multi-Protocol Communication Option and PG Feedback Option Manual 43
Table 25: Register Map Overview
Modbus
Register Map
ASD Register
Map
Comments
FFFF
ASD Access
FFFF FFFE
ASD Access
FC83 FC82
FC82 FC81
Access Interface
Firmware Version
FC81 FC80
ASD Access
FC40 FC3F
FC3F FC3E
Access PPR address registers
FC20 FC1F
FC1F FC1E
Access PPR data registers
FC00 FBFF
FBFF FBFE
ASD Access
FA01 FA00
FA00 F9FF
ASD Access
1001 1000
1000 0FFF
Redirect to ASD upper address range
0C83 0C82
0C82 0C81
Access Interface
Firmware Version
0C81 0C80
Redirect to ASD upper address range
0C40 0C3F
0C3F 0C3E
Access PPR address registers
0C20 0C1F
0C1F 0C1E
Access PPR data registers
0C00 0BFF
0BFF 0BFE
Redirect to ASD upper address range
0A01 0A00
0A00 09FF
ASD Access
0001 0000
G7 ASD Multi-Protocol Communication Option and PG Feedback Option Manual 44
11. DeviceNet Interface
This section applies to ASD-MULTICOM-A option boards only. 5-pin pluggable terminal block TB3 provides a standard connection to DeviceNet networks.
11.1 Feature Summary
Application
Toshiba 7-Series ASDs, internally mounted
Terminations
One 5-pin pluggable gold-plated connector for DeviceNet bus connection. Refer to Figure 4 for wiring connections (this information is also silkscreened on the interface PCB next to TB3).
Figure 4: DeviceNet Network Wiring Connections (TB3)
Network Power Supply
According to ODVA DeviceNet Specifications.
LED Indicators
One bicolor red/green Module Status LED and one bicolor red/green Network Status LED. Behavior according to ODVA DeviceNet Specifications
Compatibility
Group 2 Server Only device utilizing the Predefined Master / Slave Connection Set.
Vendor-specific I/O POLL connection (8 bytes of data consumed and 8 bytes of data produced). This product has been self-tested by Toshiba International Corporation and found to comply with ODVA
Conformance Test Software Version A-13.
Node Isolation
Network power and signals are optically isolated from the ASD’s control power.
Bus Interface
Phillips 82C251 or equivalent transceiver.
G7 ASD Multi-Protocol Communication Option and PG Feedback Option Manual 45
11.2 Unit Addressing
The DeviceNet node (slave) address is set via parameter F802 (inverter number parameter). Although parameter F802 has an adjustment range from 0-255, only 0-63 is an allowable addressing selection for the DeviceNet network. Therefore, if parameter F802 is set to 64 through 255, the Network Status LED will light solid red upon initialization to indicate the configuration error. Correct the inverter number parameter setting and reset the drive to remove the error.
11.3 Grounding
Grounding is of particular importance for reliable, stable operation. Communication system characteristics may vary from system to system, depending on the system environment and grounding method used. In general, however, the following grounding checkpoints should be noted when connecting any communications system to adjustable speed drives:
Grounding method checkpoints
1. Make all ground connections such that no ground current flows through the case or heatsink of a connected drive.
2. Do not connect the DeviceNet network SHIELD to a power ground or any other potential noiseproducing ground connection (such as a drive’s “G/E” terminal).
3. Do not make connections to unstable grounds (paint-coated screw heads, grounds that are subjected to inductive noise, etc.)
For specific requirements regarding protective grounding and the DeviceNet network, refer to the
ODVA DeviceNet Specifications.
11.4 Connection Information
11.4.1 Connection Sizes
Connection Instance Produced Consumed
Polled I/O (Toshiba assembly)
Polled I/O (AC/DC drive profile)
8 bytes
4 bytes
8 bytes
4 bytes
Explicit Messaging 29 bytes 29 bytes
Notes
• For the Explicit Messaging connection, this is the maximum message length: shorter messages are also acceptable.
• For the Polled I/O connection, if the actual consumed data size is less than the connection instance’s consumed_connection_size attribute, the consumed data will be ignored, but the connection will otherwise produce normally. If the actual consumed data size is larger than the connection instance’s consumed_connection_size attribute, the consumed data will be ignored and the connection will not produce.
G7 ASD Multi-Protocol Communication Option and PG Feedback Option Manual 46
11.4.2 I/O Assembly Instances
The following table indicates which polled I/O assembly instances are currently supported by the
DeviceNet Interface:
Number
Decimal Hex
Type Name
20
21
70
71
100
0x14
0x15
0x46
0x47
0x64
Output
Output
Input
Input
Output
Basic speed control output
Extended speed control output
Basic speed status input
Extended speed status input
Toshiba-specific control output
150 0x96 Input Toshiba-specific status input
For more detailed information about these assembly instances, refer to section 11.5.4.5.
G7 ASD Multi-Protocol Communication Option and PG Feedback Option Manual 47
11.5 Object Specifications
This section contains the object specifications for all DeviceNet objects currently supported by the
DeviceNet Interface. Table 26 outlines those objects covered:
Table 26: Supported Objects
Object Class # of Instances Page
Identity Object
Message Router
DeviceNet Object
Assembly Object
Connection class
Control Supervisor Object
AC/DC Drive Object
1
1
1
6
2
1
1
49
51
52
54
58
62
67
Motor Data Object 1 65
Parameter Class 29 72
For definitions of all data types referred to in these object specifications, refer to the ODVA DeviceNet
Specifications. In general, however, the following are some of the most prevalent types:
SINT .................. Signed 8-bit integer value
USINT................ Unsigned 8-bit integer value
BYTE................. Bit string – 8-bits
INT..................... Signed 16-bit integer value
UINT.................. Unsigned 16-bit integer value
WORD ............... Bit string – 16-bits
UDINT............... Unsigned 32-bit integer value
G7 ASD Multi-Protocol Communication Option and PG Feedback Option Manual 48
11.5.1 Identity Object
Class code 0x01. This object provides identification of and general information about the device.
11.5.1.1 Identity Object Class Attributes
Attribute ID
Access
Rules
Name
Data
Type
Description
1 Get
UINT Revision of this object
UINT
Maximum instance number of an object currently created in this class level of the device
11.5.1.2 Identity Object Instance Attributes
Attribute
ID
Access
Rules
Description
Default
Value
1
1
Default
Value
71
UINT
UINT
Indication of general type of product
Identification of a particular product of an individual vendor
Revision of the item the
Identity Object represents
USINT
2
2
--
1
5 Get
Major
Revision
Minor
Revision
Status
USINT 1
WORD Summary status of device
UDINT
SHORT_
STRING
Serial number of device
Human-readable identification
--
Unique for each unit
Toshiba
Multicom
ASD Interface
G7 ASD Multi-Protocol Communication Option and PG Feedback Option Manual 49
11.5.1.3 Identity Object Common Services
Service
Code
Supported
Class Instance
Service Name
0x0E Yes Yes
Get_Attribute_
Single
Description of Service
Returns the contents of the specified attribute.
0x05 Yes Yes Reset
Invokes the Reset service for the device
Please note the following items about the Reset service:
• The Reset service resets only the interface board’s DeviceNet driver (not the drive into which the interface is installed).
• Both “Type 0” and “Type 1” resets are supported. With a “Type 0” reset, the DeviceNet driver is simply reset. With a “Type 1” reset, the DeviceNet object’s BOI attribute is returned to its factory default setting and then the DeviceNet driver is reset. All other nonvolatile DeviceNetrelated configuration parameters are accessible via drive parameters F891-F894 and can therefore be modified via the drive’s front panel if desired.
11.5.1.4 Identity Object Specific Services
The Identity Object provides no object specific services.
G7 ASD Multi-Protocol Communication Option and PG Feedback Option Manual 50
11.5.2 Message Router
Class code 0x02. The Message Router Object provides a messaging connection point through which a
Client may address a service to any object class or instance residing in the DeviceNet interface unit.
11.5.2.1 Message Router Class Attributes
Attribute ID
Access
Rules
Name
Data
Type
Description
1 Get UINT Revision of this object
11.5.2.2 Message Router Instance Attributes
Attribute
ID
Access
Rules
Name
Data
Type
UINT
Description
Maximum number of connections supported.
11.5.2.3 Message Router Common Services
Service
Code
Supported
Class Instance
Service Name
0x0E Yes Yes
Get_Attribute_
Single
11.5.2.4 Message Router Specific Services
The Message Router provides no object specific services.
Default
Value
1
Default
Value
2
Description of Service
Returns the contents of the specified attribute.
G7 ASD Multi-Protocol Communication Option and PG Feedback Option Manual 51
11.5.3 DeviceNet Object
Class Code 0x03. The DeviceNet Object provides for the configuration and status of a DeviceNet port.
11.5.3.1 DeviceNet Object Class Attributes
Attribute
ID
Access
Rules
Name
Data
Type
Description
Default
Value
1 Get Revision UINT Revision of this object. 2
11.5.3.2 DeviceNet Object Instance Attributes
Attribute
ID
Access
Rules
1 Get MAC ID
Description
USINT Node address
Default
Value
--
2 Get Baud Rate USINT Baud rate --
3 Get / Set BOI BOOL Bus-off interrupt 0
4 Get / Set
Bus-Off
Counter
USINT
Number of times CAN went to the bus-off state
0
STRUCT of:
Allocation
Choice Byte
Master’s MAC
ID
BYTE
USINT MAC ID of master
0
0xFF
Notes
• The MAC ID and Baud Rate attributes are not settable via the network (they are set via the drive’s parameter settings). Attempting a Set service will result in a “Service Not Supported” error.
• The setting of the BOI attribute is saved in the DeviceNet unit’s internal EEPROM. If the BOI value is set to TRUE, the DeviceNet interface will attempt to restart the network interface on the occurrence of a CAN bus-off event. This will continue to be the behavior until the Bus-Off
Counter attribute achieves a value of 255. If a CAN bus-off event occurs after this point, the unit will not attempt to restart the network interface: it will remain faulted and isolated from the network until the drive is reset or power cycled.
G7 ASD Multi-Protocol Communication Option and PG Feedback Option Manual 52
11.5.3.3 DeviceNet Object Common Services
Service
Code
Supported
Class Instance
Service Name
0x0E Yes Yes
Get_Attribute_
Single
0x10 N / A Yes
Set_Attribute_
Single
11.5.3.4 DeviceNet Object Specific Services
Service
Code
Supported
Class Instance
Service Name
0x4B N / A Yes
Allocate_
Master/Slave
_Connection_Set
0x4C N / A Yes
Release_Group_2
_Identifier_Set
Description of Service
Returns the contents of the specified attribute.
Modifies the value of the specified attribute.
Description of Service
Requests the use of the Predefined
Master/Slave Connection Set.
Indicates that the specified connections within the
Predefined
Master/Slave Connection Set are no longer desired. These connections are to be released (deleted).
G7 ASD Multi-Protocol Communication Option and PG Feedback Option Manual 53
11.5.4 Assembly Object
Class code 0x04. The Assembly Object binds attributes of multiple objects, which allows data to or from each object to be sent or received over a single connection.
11.5.4.1 Assembly Object Class Attributes
Attribute
ID
Access
Rules
Name
Data
Type
1 Get
Description
Revision UINT Revision of this object.
Default
Value
2
11.5.4.2 Assembly Object Instance Attributes
The Multicom DeviceNet unit contains 6 static assembly instances, with assigned instance IDs 20, 21,
70, 71, 100 and 150. Refer to section 11.5.4.5 for more details.
Attribute
ID
Access
Rules
Description
Default
Value
3
Get or
Get / Set
--
Output instances (20, 21 and 100) can be accessed via the Get and Set services, whereas input instances
(70, 71 and 150) can only be accessed via the Get service.
11.5.4.3 Assembly Object Common Services
Service
Code
Supported
Class Instance
Service Name
0x0E Yes Yes
Get_Attribute
_Single
0x10 N / A
Output instances only
Set_Attribute
_Single
Description of Service
Returns the contents of the specified attribute.
Modifies the value of the specified attribute.
11.5.4.4 Assembly Object Specific Services
The Assembly Object for static assemblies provides no object specific services.
11.5.4.5 Assembly Instance Details
As mentioned previously, the Multicom DeviceNet Interface provides the option of three different I/O assembly instance sets. The active set is chosen via ASD parameter F893 (refer to section 8.3).
Whenever changing the active assembly set, always remember to reset the drive to active the change.
G7 ASD Multi-Protocol Communication Option and PG Feedback Option Manual 54
0
1
2
3
11.5.4.5.1 Output Instance 20 (Basic Speed Control Output)
This is the ODVA AC/DC Drive Profile Basic Speed Control Output assembly. For more information, refer to the ODVA DeviceNet Specifications and the object explanations in this manual related to each of the fields of this assembly instance.
Byte # Bit 7 Bit 6 Bit 5 Bit 4 Bit 3 Bit 2 Bit 1 Bit 0
0
1
2
Speed Reference (Low Byte)
Fault Reset Run Fwd
3
Speed Reference (High Byte)
11.5.4.5.2 Output Instance 21 (Extended Speed Control Output)
This is the ODVA AC/DC Drive Profile Extended Speed Control Output assembly. For more information, refer to the ODVA DeviceNet Specifications and the object explanations in this manual related to each of the fields of this assembly instance.
Byte # Bit 7 Bit 6 Bit 5 Bit 4 Bit 3 Bit 2 Bit 1 Bit 0
Speed Reference (Low Byte)
Fault Reset Run Rev
Speed Reference (High Byte)
Run Fwd
G7 ASD Multi-Protocol Communication Option and PG Feedback Option Manual 55
2
3
0
1
11.5.4.5.3 Output Instance 100 (Toshiba ASD Command)
This is a vendor-specific output assembly instance that provides direct access to the most critical control components of the G7 ASD. For more information, refer to the explanations for the referenced attributes contained in the AC/DC Drive Object in section 11.5.8.6 on page 69. Note that bytes #0 and
#1 are mapped to the “G7 Command Word” attribute (attribute ID #101) of the AC/DC Drive Object: the specific bits of this command word are shown in detail in the following table simply for ease of use.
Byte # Bit 7 Bit 6 Bit 5 Bit 4 Bit 3 Bit 2 Bit 1 Bit 0
0
1
2
DC Inject.
Braking
Command
Priority
PI Control
ON/OFF
Speed Ref.
Priority
Brake
Release
Control
Selection
Excitation
Curr Cmd.
Brake Close Fault Reset
Frequency Command (Low Byte)
Reset
Reserved
FWD /
REV
Run / Stop
Jog
3
4
5
Frequency Command (High Byte)
F831 Command Data (Low Byte)
F831 Command Data (High Byte)
6
F832 Command Data (Low Byte)
7
F832 Command Data (High Byte)
11.5.4.5.4 Input Instance 70 (Basic Speed Control Input)
This is the ODVA AC/DC Drive Profile Basic Speed Control Input assembly. For more information, refer to the ODVA DeviceNet Specifications and the object explanations in this manual related to each of the fields of this assembly instance.
Byte # Bit 7 Bit 6 Bit 5 Bit 4 Bit 3 Bit 2 Bit 1 Bit 0
Running1 Faulted
Speed Actual (Low Byte)
Speed Actual (High Byte)
G7 ASD Multi-Protocol Communication Option and PG Feedback Option Manual 56
3
4
5
6
7
11.5.4.5.5 Input Instance 71 (Extended Speed Control Input)
This is the ODVA AC/DC Drive Profile Extended Speed Control Input assembly. For more information, refer to the ODVA DeviceNet Specifications and the object explanations in this manual related to each of the fields of this assembly instance.
Byte # Bit 7 Bit 6 Bit 5 Bit 4 Bit 3 Bit 2 Bit 1 Bit 0
0
1
At
Reference
Ref From
Net
Ctrl From
Net
Ready
Running2
(REV)
Drive State
Running1
(FWD)
Warning Faulted
2
Speed Actual (Low Byte)
3
Speed Actual (High Byte)
11.5.4.5.6 Input Instance 150 (Toshiba ASD Status)
This is a vendor-specific input assembly instance that provides direct access to the most often-used status components of the G7 ASD. For more information, refer to the explanations for the referenced attributes contained in the AC/DC Drive Object in section 11.5.8.6 on page 69. Note that bytes #0 and
#1 are mapped to the “G7 Status Word” attribute (attribute ID #111) of the AC/DC Drive Object: the specific bits of this status word are shown in detail in the following table simply for ease of use.
Byte # Bit 7 Bit 6 Bit 5 Bit 4 Bit 3 Bit 2 Bit 1 Bit 0
0
1
2
DC Inject.
Braking
Ready (exc.
MOFF)
OL Alarm
Status
Drive
Healthy
PI Status
Ready (exc.
ST)
Alarm
Status
Ready (inc.
ST)
Serious
Fault
Control
Mode
Output Frequency (Low Byte)
Run / Stop
Status
Speed Limit
Alarm Stop
Status
FWD /
REV Status
Fault Status
Jog Status
Output Frequency (High Byte)
F841 Status Data (Low Byte)
F841 Status Data (High Byte)
F842 Status Data (Low Byte)
F842 Status Data (High Byte)
G7 ASD Multi-Protocol Communication Option and PG Feedback Option Manual 57
11.5.5 Connection class
Class code 0x05. The Connection Class allocates and manages the internal resources associated with both I/O and Explicit Messaging Connections.
11.5.5.1 Connection Class Attributes
Attribute
ID
Access
Rules
Name
Data
Type
Description
Default
Value
1 Get Revision UINT Revision of this object. 1
11.5.5.2 Connection Class Instance Attributes
The Instance IDs utilized by the DeviceNet Interface connection objects are shown in the following table:
Connection
Instance ID #
Description
1
2
References the Explicit Messaging Connection
References the Polled I/O Connection
G7 ASD Multi-Protocol Communication Option and PG Feedback Option Manual 58
11.5.5.2.1 Master/Slave Explicit Messaging Connection Object Instance Attributes
Attribute
ID
1
Access
Rules
Get state USINT
Description
State of the object
Indicates connection type
Default
Value
--
0
9
12
Get / Set
Get / Set produced
_size consumed
_size expected_ packet_rate watchdog_ timeout_action produced_ connection_ path_length produced_ path consumed_ connection_ path_length consumed_ connection_ path
UINT
UINT
USINT
UINT
UINT
UINT
USINT
UINT
Array of
USINT
UINT
Array of
USINT
UINT
Placed in CAN ID field when transmitting
CAN ID field value denoting received messages
Defines producing / consuming message groups
Max number of bytes transmitted across this connection
Max number of bytes received across this connection
Defines timing associated with this connection
Inactivity/watchdog timeout action
Number of bytes in produced_connection
_path attribute
Specifies Application
Object(s) whose data is to be produced by this connection
Number of bytes in consumed_ connection_path attribute
Specifies Application
Object(s) whose data is to be consumed by this connection
Defines minimum time between new data production
0x0403 +
(MAC ID
<< 3)
0x0404 +
(MAC ID
<< 3)
0x21
29
29
2500
1
0
Empty
0
Empty
0
G7 ASD Multi-Protocol Communication Option and PG Feedback Option Manual 59
11.5.5.2.2 Poll Connection Object Instance Attributes
Attribute
ID
1
Access
Rules
Get state USINT
Description
State of the object
Default
Value
--
Indicates connection type
1 produced
_connection
_size consumed
_connection
_size
9 Get / Set expected_ packet_rate
12 Get / Set watchdog_ timeout_action produced_ path_length produced_ connection_ path consumed_ connection_ path_length consumed_ path
UINT
UINT
USINT
UINT
UINT
UINT
USINT
UINT
Array of
USINT
UINT
Array of
USINT
UINT
Placed in CAN ID field when transmitting
CAN ID field value denoting received messages
Defines producing / consuming message groups
Max number of bytes transmitted across this connection
Max number of bytes received across this connection
Defines timing associated with this connection
Inactivity/watchdog timeout action
Number of bytes in produced_connection
_path attribute
Specifies Application
Object(s) whose data is to be produced by this connection
Number of bytes in consumed_ connection_path attribute
Specifies Application
Object(s) whose data is to be consumed by this connection
Defines minimum time between new data production
0x03C0 +
MAC ID
0x0405 +
(MAC ID
<< 3)
0x01
8
8
0
0
6
20 04 24
96 30 03
6
20 04 24
64 30 03
0
G7 ASD Multi-Protocol Communication Option and PG Feedback Option Manual 60
11.5.5.3 Connection Class Common Services
Service
Code
Supported
Class Instance
Service Name
0x05 No Yes
Description of Service
Reset
Used to reset all resettable connection objects.
0x0E Yes Yes
0x10 N / A Yes
Get_Attribute
_Single
Set_Attribute
_Single
Returns the contents of the specified attribute.
Modifies the value of the specified attribute.
11.5.5.4 Connection Class Specific Services
The Connection Class provides no object specific services.
G7 ASD Multi-Protocol Communication Option and PG Feedback Option Manual 61
11.5.6 Control Supervisor Object
Class Code 0x29. The Control Supervisor Object models all the management functions for devices within the “hierarchy of Motor Control Devices”.
11.5.6.1 Control Supervisor Object Class Attributes
Attribute
ID
Access
Rules
Name
Data
Type
Description
1 Get Revision UINT Revision of this object.
Default
Value
1
11.5.6.2 Control Supervisor Object Instance Attributes
Attribute
ID
Access
Rules
Description
3
4
5
Get / Set
Get / Set
Get / Set
Run1
Run2
NetCtrl
BOOL
BOOL
BOOL
Refer to ODVA
Run/Stop Event Matrix
Refer to ODVA
Run/Stop Event Matrix
1=Drive control from
DeviceNet
Default
Value
0
0
0
--
--
--
0
--
--
12 Get / Set FaultRst BOOL 0 → 1 = fault reset 0
--
Note
When the drive is faulted and the FaultRst attribute is set, the interface card will also be reset.
Dependent on system timing, therefore, a response to setting this attribute may or may not be produced.
G7 ASD Multi-Protocol Communication Option and PG Feedback Option Manual 62
11.5.6.3 Control Supervisor Object Common Services
Service
Code
Supported
Class Instance
Service Name
0x0E Yes Yes
Get_Attribute_
Single
Description of Service
Returns the contents of the specified attribute.
0x10 N / A Yes
Set_Attribute_
Single
Modifies the value of the specified attribute.
0x05 N / A Yes Reset Resets to the “start-up” state
Note
The Control Supervisor Object’s “Reset” service resets only the Control Supervisor Object state machine (attribute #6). It does not reset the drive or the interface card. To reset the drive and interface card when the drive is faulted, access the FaultRst attribute (attribute #12) via either the polled I/O connection or explicit messaging connection. To reset the interface card only, issue a “Reset” service to the Identity Object.
11.5.6.4 Control Supervisor Object Specific Services
The Control Supervisor object provides no object specific services.
11.5.6.5 Control Supervisor Object Attribute Semantics
This section will detail any specific information that may be useful when accessing the attributes of the
Control Supervisor Object, whether directly via explicit messaging or indirectly via I/O assembly objects.
Run1 / Run2
Indirectly map to the “run/stop selection” bit (bit #0) of the G7 command word (refer to Table 10 on page 23) via the AC/DC drive profile’s Run/Stop Event Matrix.
NetCtrl
Maps directly to “command priority” bit (bit #15) of the G7 command word (refer to Table 10 on page
23). When this attribute (and therefore command word bit #15) is “1”, the option command word
(derived from the AC/DC drive profile object attributes when AC/DC drive profile I/O assemblies are active) becomes the drive’s active command source, regardless of the ASD’s Command Mode selection parameter. When this attribute is a “0”, the option command word will no longer override the
Command Mode selection parameter, but the option command word may still be used by the ASD as its overall command source if the
Command Mode selection parameter is set to “Use Communication Card
(option)”.
State / Running1 / Running2 / Ready
Refer to the DeviceNet Specification for details regarding these attributes.
Faulted
Maps directly to the “fault status” bit (bit #0) of the G7 status word (refer to Table 14 on page 26).
Warning
This attribute is not used and will always report “0”.
FaultRst
Maps directly to the “fault reset” bit (bit #2) of the G7 command word (refer to Table 10 on page 23).
G7 ASD Multi-Protocol Communication Option and PG Feedback Option Manual 63
CtrlFromNet
This attribute mirrors the value set in attribute #5 “NetCtrl”.
G7 ASD Multi-Protocol Communication Option and PG Feedback Option Manual 64
11.5.7 Motor Data Object
Class Code 0x28. This object serves as a database for motor parameters.
11.5.7.1 Motor Data Object Class Attributes
Attribute
ID
Access
Rules
Name
Data
Type
Description
1 Get Revision UINT Revision of this object.
11.5.7.2 Motor Data Object Instance Attributes
Attribute
ID
Access
Rules
3 Get / Set MotorType
Description
USINT Type of attached motor
Default
Value
1
Default
Value
7
6 Get / Set RatedCurrent UINT Rated stator current --
7 Get / Set RatedVoltage UINT Rated base voltage --
12 Get / Set PoleCount UINT Number of motor poles
11.5.7.3 Motor Data Object Common Services
Service
Code
Supported
Class Instance
Service Name
0x0E Yes Yes
Get_Attribute_
Single
0x10 N / A Yes
Set_Attribute_
Single
--
Description of Service
Returns the contents of the specified attribute.
Modifies the value of the specified attribute.
11.5.7.4 Motor Data Object Specific Services
The Motor Data object provides no object specific services.
11.5.7.5 Motor Data Object Attribute Semantics
This section will detail any specific information that may be useful when accessing the attributes of the
Motor Data object via explicit messaging.
MotorType
Valid settings for this attribute are those detailed in the ODVA DeviceNet Specifications for an “AC
Motor Class”, namely 3 (PM synchronous), 6 (wound rotor induction) and 7 (squirrel cage induction).
G7 ASD Multi-Protocol Communication Option and PG Feedback Option Manual 65
This attribute value is retained in the Multicom board’s nonvolatile EEPROM, but is not used in any way for drive control (i.e. it is for user reference only).
RatedCurrent
This attribute indirectly maps to ASD parameter number F600 “ Electronic Thermal Protection #1”
(found in the Motor Parameters Group). This mapping is “indirect” due to parameter F600 being default set in units of % rated drive current. Therefore, when the RatedCurrent attribute is changed with a SET service, the drive’s rated current is used as a basis to determine the corresponding percentage value to enter into ASD parameter F600.
For example, if the ASD has a rated current of 5.0A (represented as 50 in 100mA units), and the attached motor has a FLA rated current of 3.5A, then SETting the RatedCurrent attribute to 35 (3.5A represented with its designated 100mA units) will cause parameter F600 to obtain a value of (35/50) x
100% = 70%.
Note that parameter F600 is only read by the Multicom interface upon drive initialization and as the result of a DeviceNet SET service. Therefore, be sure to reset the drive whenever parameter F600 is changed locally via the LCD EOI to validate the new setting.
RatedVoltage
This attribute directly maps to ASD parameter number F306 “ #1 Max Output Voltage” (found in the
Motor Parameters Group). Note that parameter F306 is only read by the Multicom interface upon drive initialization and as the result of a DeviceNet SET service. Therefore, be sure to reset the drive whenever parameter F306 is changed locally via the LCD EOI to validate the new setting.
PoleCount
This attribute directly maps to ASD parameter number F411 “ Number of Motor Poles” (found in the
Motor Parameters Group). Note that parameter F411 is only read by the Multicom interface upon drive initialization and as the result of a DeviceNet SET service. Therefore, be sure to reset the drive whenever parameter F411 is changed locally via the LCD EOI to validate the new setting.
G7 ASD Multi-Protocol Communication Option and PG Feedback Option Manual 66
11.5.8 AC/DC Drive Object
Class Code 0x2A. The AC/DC Drive Object models the functions specific to an AC or DC drive.
11.5.8.1 AC/DC Drive Object Class Attributes
Attribute
ID
Access
Rules
Name
Data
Type
Description
Default
Value
1 Get Revision UINT Revision of this object.
11.5.8.2 AC/DC Drive Object Instance Attributes
Attribute
ID
Access
Rules
Description
1
Default
Value
--
4
6
Get / Set
Get / Set
NetRef
DriveMode
BOOL
1=Drive reference from
DeviceNet
USINT Operation mode
0
0
--
8 Get / Set SpeedRef INT
Speed reference in
RPM
0
--
100
101
102
Get / Set
Get / Set
Get / Set
Frequency
Command
Command
Word
F831 Command
Data
103 Get / Set
F832 Command
Data
110 Get
Output
Frequency
111 Get Status Word
Data
F842 Status
Data
UINT
WORD
UINT
UINT
UINT
Frequency command in
Hz (x 100)
Bit-mapped command word
Write command value to selected item
Write command value to selected item
Output frequency in Hz
(x 100)
WORD Bit-mapped status word
UINT
UINT
Read status value from selected item
Read status value from selected item
0
0x0000
0
0
--
--
--
--
G7 ASD Multi-Protocol Communication Option and PG Feedback Option Manual 67
Attribute
ID
120
121
Access
Rules
Get / Set
Universal
Register
Get / Set Universal Data
Description
UINT
Universal ASD data register address
UINT Universal ASD data
Default
Value
0
--
11.5.8.3 AC/DC Drive Object Common Services
Service
Code
Supported
Class Instance
Service Name
0x0E Yes Yes
Get_Attribute_
Single
0x10 N / A Yes
Set_Attribute_
Single
11.5.8.4 AC/DC Drive Object Specific Services
The AC/DC drive object provides no object specific services.
Description of Service
Returns the contents of the specified attribute.
Modifies the value of the specified attribute.
11.5.8.5 AC/DC Drive Object Detailed Explanations
As can be seen in the table in section 11.5.8.2, the AC/DC drive object is comprised of two independent portions: a standard portion which is associated with the ODVA’s AC/DC drive profile (the attributes above the dual wavy table separator lines), and an extended portion which is vendor-specific for the
Toshiba G7 ASD (the attributes below the table separator lines). With the exception of the Universal
Register and Universal Data attributes (which are always valid and active), these two halves of the object are mutually exclusive in that only one set of attributes will be linked to the drive’s actual command and status information at any given time. Which half of the attributes is linked to the drive’s command and status information is determined by ASD parameter F983, which selects the active I/O assembly instance set.
As detailed in section 11.5.4, when parameter F893 is set to “0”, vendor-specific Toshiba I/O assembly instances 100 and 150 are active. These assembly instances map directly to AC/DC drive object attributes 100-113.
When parameter F893 is set to “1” or “2”, ODVA AC/DC drive profile standard I/O assembly instances
20 and 70 or 21 and 71 are active. In part, these assembly instances map directly to AC/DC drive object attributes 3-29.
When the Toshiba I/O assembly instances are active, AC/DC drive object attributes 3-29 are still available via explicit messaging GET/SET services, but these attributes are decoupled from the actual
G7 ASD operation. That is to say that status attributes (such as #7 SpeedActual) are not updated to reflect actual drive status, and command attributes (such as #8 SpeedRef) do not affect actual drive operation in any way. In this case, only those attributes that are specific to the Toshiba I/O assembly instances are coupled to the drive’s operation. For example, writing to attribute #100 (G7 Frequency
Command) will write to the drive’s option frequency command, and reading from attribute #110 (G7
Output Frequency) will always return the current value of the drive’s operating frequency.
G7 ASD Multi-Protocol Communication Option and PG Feedback Option Manual 68
When the ODVA AC/DC drive profile standard I/O assembly instances are active, the same concept detailed in the previous paragraph applies, except that the first half of the AC/DC drive object attributes are coupled to the actual ASD operation, and the second half of the attributes are decoupled (and should therefore be ignored).
11.5.8.6 AC/DC Drive Object Attribute Semantics
This section will detail any specific information that may be useful when accessing the attributes of the
AC/DC Drive Object, whether directly via explicit messaging or indirectly via I/O assembly objects.
AtReference
This attribute is “1” whenever SpeedActual is within ±1 RPM of SpeedRef.
NetRef
Maps directly to the “speed reference priority” bit (bit #14) of the G7 command word (refer to
G7
Command Word below). When this attribute (and therefore command word bit #14) is “1”, the option frequency command (derived from SpeedRef when AC/DC drive profile I/O assemblies are active) becomes the drive’s active frequency command, regardless of the ASD’s Frequency Mode selection parameter. When this attribute is a “0”, the option frequency command will no longer override the
Frequency Mode selection parameter, but the option frequency command may still be used by the ASD as its overall frequency command if the Frequency Mode selection parameter is set to “Use
Communication Card (option)”.
DriveMode
This attribute has no effect on drive operation: values written to it are for user reference only.
SpeedActual
The SpeedActual attribute is the motor’s synchronous operating speed in RPM, and is calculated using the following formula:
SpeedActua l = Int
120 x Output
Number of
Frequency (Hz)
Motor Poles
, where “Output Frequency” is the inverter’s current operating frequency and “Number of Motor Poles” is the value contained in the PoleCount attribute of the Motor Data Object (refer to section 11.5.7). Only the integer portion of the calculated result will be transmitted across the network.
SpeedRef
The SpeedRef attribute value is used in the following calculation to determine the ASD’s option frequency command value:
Frequency Command (Hz) =
SpeedRef x Number of Motor Poles
120
, where “Number of Motor Poles” is the value contained in the PoleCount attribute of the Motor Data
Object (refer to section 11.5.7).
RefFromNet
This attribute mirrors the value set in attribute #4 “NetRef”.
Frequency Command
Unsigned 16-bit value whose value is the desired ASD option frequency command multiplied by 100.
For example, if a frequency command of 55.34Hz is desired, then 55.34 x 100 = 5534
10
(0x159E). If the frequency command exceeds limiting drive parameters (such as the Upper Limit Frequency or
Maximum Frequency), then the drive will ignore it, maintaining its current setting.
Command Word
G7 ASD Multi-Protocol Communication Option and PG Feedback Option Manual 69
Bit-mapped drive option command word. Table 10 on page 23 provides the format of this command word.
F831 Command Data / F832 Command Data
Via ASD parameters F831 and F832, the user has the ability to select two additional high-speed scan command items to be written to the ASD. Table 27 provides a list of the available command scan data selections. The “Parameter” column indicates the drive’s internal parameter to which the corresponding selection is mapped. Once selected, the corresponding command data for the selected scan items can be written to the drive via AC/DC drive object attributes #102 and #103.
Table 27: Drive Command Scan Data
F831
∼∼∼∼F835
Setting
10
11
12
13
4
5
6
7
8
9
1 RESERVED
2 RESERVED
3
-
-
-
Incremental speed reference 0.01Hz
Absolute torque limit
Positive torque limit
Negative torque limit
Torque command
Speed torque bias
Tension torque bias
0.01%
0.01%
- 0xFFFF
-
-
0 ~ 500
0 ~ 25000
0 ~ 25000
-
-
0xFA08
0xFA34
0x0441
0.01% 0 ~ 25000 0x0443
0.01% -25000 ~ 25000 0xFA33
0.01% -25000 ~ 25000
0.01% -25000 ~ 25000
0x0726
0x0727
Load balance gain
Drooping gain
Speed loop proportional gain
Speed loop integral gain
0.01
0.01
0.1
0.1
0 ~25000
0 ~ 10000
32 ~ 10000
100 ~ 2000
0x0728
0x0320
0x0376
0x0377
15 Load moment of inertia
-
0.0001
-
-
100 ~ 10000
-
0xFA50
0xFA35
0xFA23
Note 1: Items marked as “RESERVED” in Table 27 are reserved for future use. Selecting one of the corresponding values as command scan data will have no effect on drive operation.
Note 2: Although not disallowed, avoid configuring both scan command data parametes
F831 and F832 with the same command data selection (for example, do not set both F831 and F832 to “3”, etc.). Unexpected drive behavior could result if different data values are written to the corresponding command locations.
Note 3: Parameters F831 and F832 are only validated on drive reset or power-up.
Therefore, if either of these parameters is changed, be sure to reset the drive to validate the changes.
Note 4: Data range checking is not performed on command scan items. If a value outside of a specific item’s valid range is written to the attribute (either via explicit messaging or an I/O assembly object), that value will be accepted by the Multicom interface, but ignored by the drive.
Item #16 in Table 27 (extended command) is a bit-mapped drive command word internally located at parameter 0xFA23. Table 11 on page 23 provides the format of this extended command word.
Output Frequency
Unsigned 16-bit value whose value is the current ASD operating frequency multiplied by 100. For example, if the ASD is currently running at 55.34Hz, then this attribute will be 55.34 x 100 = 5534
10
(0x159E).
G7 ASD Multi-Protocol Communication Option and PG Feedback Option Manual 70
Status Word
Bit-mapped ASD status word. Table 14 on page 26 provides the format of this status word.
F841 Status Data / F842 Status Data
Via ASD parameters F841 and F842, the user has the ability to select two additional high-speed scan status items to be read from the ASD. Starting on page 27 of this manual, Table 15, Table 16, Table 17 and Table 18 provide a list of the available status scan data selections and related supporting information. Once selected, the corresponding status data can be read from the drive via AC/DC drive object attributes #112 and #113.
Universal Register / Universal Data
These attributes provide direct network access to any internal drive data (configuration parameters, command data or status data). To use this powerful feature, just set the Universal Register attribute to the ASD register (also referred to as a “communication number”) that you wish to access, and then perform the desired operation (“Get” to read from the ASD register or “Set” to write to it) on the
Universal Data attribute. The operation on the Universal Data attribute will be directly performed on the data value contained in the internal drive register indicated by the Universal Register attribute.
Note that data written to or read from the drive is raw data, which is to say that no scaling (multiplier) is applied, and all data is expressed as integer values. Also note that the Set service will invoke a corresponding write request to the drive’s internal nonvolatile EEPROM memory, so that written values will be retained by the drive through power-off cycles.
Refer to the Toshiba Series 7 Serial Communications Interface Manual for detailed information on available drive registers, their allowable adjustment ranges, and any scaling factors that may apply.
To demonstrate an example operation, let’s say we would like to write a value of 85.00Hz to ASD parameter “Maximum Frequency” over DeviceNet via an explicit messaging transaction. The ASD register (communication number) for Maximum Frequency is 0011, which is a value of 0x0011 in hexadecimal or 17 in decimal. Therefore, we would Set the Universal Register attribute to 17
10
(0x0011). The Maximum Frequency register also has a scaling factor of 0.01Hz associated with it, which means the value that must be written to this register is 85.00Hz / 0.01Hz = 8500
10
(0x2134).
Therefore, all we need to do now is perform a Set service on the Universal Data attribute with a value of
8500
10
. In this same manner, any available ASD data can be accessed.
If the requested operation cannot be performed (typically due to such reasons as a non-existent ASD register being targeted, a data value that is out of range, or a Set (write) operation that is performed when the drive is running targeting a register that does not allow such action), a corresponding
DeviceNet error code will be returned.
G7 ASD Multi-Protocol Communication Option and PG Feedback Option Manual 71
11.5.9 Parameter Class
Class code 0x0F. The parameter class provides convenient access to various configuration parameters implemented as attributes of other objects. Table 28 lists the supported parameters and their referenced originating objects. For further information on a specific parameter (such as adjustment range, etc.) refer to the referenced originating object. Further information can also be found in the Electronic Data
Sheet (EDS).
Table 28: DeviceNet Interface Configuration Group Parameters
Parameter # Originating Object Originating Attribute Page
4 Motor PoleCount 65
NetCtrl
State
62
62
7 Control
8 Control
Running1
Running2
Ready
Faulted
62
62
62
62
FaultRst 62
12 Control 62
NetRef 67
16 AC/DC SpeedRef 67
18
19
20
21
22
AC/DC Drive
AC/DC Drive
AC/DC Drive
AC/DC Drive
AC/DC Drive
Frequency Command
Command Word
F831 Command Data
F832 Command Data
Output Frequency
67
67
67
67
67
23
24
25
26
AC/DC Drive
AC/DC Drive
AC/DC Drive
AC/DC Drive
Status Word
F841 Status Data
F842 Status Data
Universal Access Register
67
67
67
67
27 AC/DC Drive Universal Access Data
28 DeviceNet BOI
67
52
G7 ASD Multi-Protocol Communication Option and PG Feedback Option Manual 72
11.6 Network Communication Loss Action
ASD Parameter F892 configures the drive’s behavior upon loss of DeviceNet network communications.
For the purposes of setting this behavior, the chosen action will be performed both a result of a connection (inactivity) timeout as well as a network fatal fault (such as a loss of network power or network BUSOFF after initial successful network operation).
The primary behavior of the network interface and drive upon loss of communications is dictated by the setting of attribute #12 (watchdog_timeout_action) in the polled I/O connection object of the connection class. The polled I/O connection’s watchdog_timeout_action can take on the following three values:
0: Transition to timed out. This is the default value. The connection transitions to the “timed out” state and waits in this state until the connection is reset or deleted.
1: Auto delete. The connection is automatically deleted.
2: Auto reset. The connection remains in the “established” state and the inactivity/watchdog timer is restarted.
When the polled I/O connection’s watchdog_timeout_action attribute is configured with a value of either 0 (transition to timed out) or 1 (auto delete), the drive’s behavior upon loss of communications is controlled by the setting of ASD parameter F892. When the polled I/O connection’s watchdog_timeout_action attribute is configured with a value of 2 (auto reset), no drive action occurs during a timeout condition (the drive continues to operate at its last conditions).
By appropriately configuring ASD parameter F892, therefore, it is possible to create a solution that can provide some level of system “failsafe” operation in the event of master loss or total network failure.
SAFETY WARNING!
Because some of these settings will enable the drive to run automatically, the user must ensure that their system poses no danger of personal injury or equipment damage, as they may no longer be able
to control the drive from the network due to the loss of communications.
ASD parameter F892 provides the following selections (also refer to Table 7 on page 18):
0 = Set all consumed data to 0
1 = Retain last data values
2 = Issue STOP command to drive
3 = Issue EMERGENCY OFF command to drive
4..18 = Run preset speed #1..#15
Setting “0”: This is the default setting. When network communications are lost, the consumed I/O data will be set to 0. This will have the effect of stopping the drive and setting its frequency command to
0.00Hz. Note that the drive will not react to the effective STOP command, etc. unless the drive’s command mode selection parameter is set to use the option card as its command source.
Setting "1": The last consumed data is retained.
Setting "2": A STOP command is issued to the drive. Note that the drive will not react to the STOP command unless it is operating from the network command source at the time of the watchdog timeout.
Setting "3": An EMERGENCY OFF command is issued to the drive. Note that the drive will not react to the EMERGENCY OFF command unless it is operating from the network command source at the time of the watchdog timeout. The drive’s behavior during an EMERGENCY OFF event can be configured via ASD parameter F603.
G7 ASD Multi-Protocol Communication Option and PG Feedback Option Manual 73
Settings "4" through “18”: Command the drive to run preset speeds #1..#15. Preset speeds can be set via ASD parameters F018..F024 and F287..F294. Note that the drive will not react to the preset speed commands unless it is operating from the network command source at the time of the watchdog timeout.
Also note that the drive’s RUN/STOP command is not modified when these settings are selected.
Therefore, the drive will not actually run the preset speed if it was not already being issued a RUN command at the time of the watchdog timeout.
G7 ASD Multi-Protocol Communication Option and PG Feedback Option Manual 74
12. Notes
G7 ASD Multi-Protocol Communication Option and PG Feedback Option Manual 75
TOSHIBA INTERNATIONAL CORPORATION
INDUSTRIAL DIVISION
13131 West Little York Rd., Houston, TX 77041
Tel: [800] 231-1412 / [713] 466-0277 Fax: [713] 466-8773
World Wide Web http://www.tic.toshiba.com
Printed in U.S.A
advertisement
Related manuals
advertisement
Table of contents
- 9 Installation Precautions
- 10 Maintenance Precautions
- 10 Inspection
- 10 Storage
- 10 Disposal
- 12 Installation Procedure
- 14 Wiring
- 15 PG Feedback Enable Setting
- 15 PG Power Supply Voltage Selection
- 16 Pulse Input Selection
- 17 PG Feedback Connection
- 20 Maximum Input Frequency Using an Open Collector Encoder
- 23 Profibus DP Configuration
- 24 Modbus RTU Configuration
- 25 DeviceNet Configuration
- 26 Feature Summary
- 28 Profibus Interface Connection
- 28 Unit Addressing
- 29 Profibus Exchanged Data Structures
- 29 Output (Control) Data Format
- 32 Input (Status) Data Format
- 38 Diagnostics
- 39 Asynchronous Drive Parameter Access
- 39 Parameter Number / Action Output Words
- 40 Parameter Number / Action Input Words
- 41 Drive Parameter Access Procedure
- 42 Register Access Error Codes
- 42 Parameters
- 43 Physical Layer
- 44 Modbus RTU
- 44 Configuration
- 44 Communication Formats
- 45 Modbus/ASD Register Mappings
- 46 ASD Scan Registers
- 48 Supported Modbus Functions
- 49 Programmable Pointer Registers
- 49 Response Delay Timer Function
- 50 LED Indicators
- 50 Register Summary
- 52 Feature Summary
- 53 Unit Addressing
- 53 Grounding
- 53 Connection Information
- 53 Connection Sizes
- 54 I/O Assembly Instances
- 55 Object Specifications
- 56 Identity Object
- 58 Message Router
- 59 DeviceNet Object
- 61 Assembly Object
- 65 Connection class
- 69 Control Supervisor Object
- 72 Motor Data Object
- 74 AC/DC Drive Object
- 79 Parameter Class
- 80 Network Communication Loss Action