advertisement
▼
Scroll to page 2
of
87
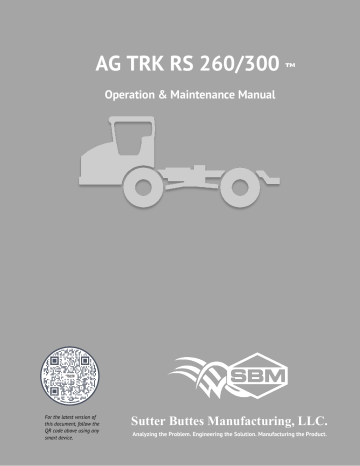
AG TRK RS 260/300 ™ Operation & Maintenance Manual For the latest version of this document, follow the QR code above using any smart device. Sutter Buttes Manufacturing, LLC. Analyzing the Problem. Engineering the Solution. Manufacturing the Product. Table of Contents TABLE OF CONTENTS.......................................................................................................................................................................2-5 1. INTRODUCTION ................................................................................................................................................................................ 6 1.1 1.2 1.3 1.4 1.5 1.6 ABOUT US ...................................................................................................................................................................................... 6 CONTACT INFORMATION ............................................................................................................................................................... 6 CALIFORNIA PROP 65 WARNING .................................................................................................................................................. 6 OPERATOR ORIENTATION.............................................................................................................................................................. 6 PRODUCT CHANGES ....................................................................................................................................................................... 6 SERIAL NUMBER LOCATION .......................................................................................................................................................... 7 2. SAFETY ................................................................................................................................................................................................ 7 Sutter Buttes Manufacturing 2.1 SBM SAFETY STATEMENT............................................................................................................................................................. 7 2.2 DECALS: LOCATION & NOMINCLATURE ....................................................................................................................................... 8 2.3 SAFETY ICONS NOMENCLATURE ................................................................................................................................................... 8 2.3 Personal Protection ............................................................................................................................................................. 9 2.3.2Prohibited Actions ............................................................................................................................................................. 9 2.3.3Hazard Avoidance ................................................................................................................................................. 10 2.4 GENERAL OPERATING SAFETY ................................................................................................................................................... 10 2.4.1 Electrocution Hazard ................................................................................................................................................... 10 2.4.2 Personal Protection Equipment (PPE) ................................................................................................................... 10 2.4.3 Fall Hazard...................................................................................................................................................................... 10 2.4.4 Seat Belt Use.................................................................................................................................................................. 10 2.4.5 Distracted Operation Hazard .................................................................................................................................... 10 2.4.6 Loss of Control Hazard ............................................................................................................................................... 11 2.4.7 Impaired Operator Hazard ........................................................................................................................................ 11 2.4.8 Crush Hazard (Rollover) ............................................................................................................................................. 11 2.4.9 Safe Distance ................................................................................................................................................................. 11 2.4.10 Child Hazard ................................................................................................................................................................ 11 2.4.11 Safety and Information Signs ................................................................................................................................ 11 2.4.12 Safety Guards .............................................................................................................................................................. 11 2.4.13 Damaged Parts Hazard ............................................................................................................................................ 12 2.4.14 Alterations and Modifications ............................................................................................................................... 12 2.4.15 Transporting Safety ................................................................................................................................................... 12 2.4.16 Tire Safety .................................................................................................................................................................... 12 2.4.17 Hydraulic System Safety .......................................................................................................................................... 13 2.4.18 Pneumatic System Safety........................................................................................................................................ 14 2.4.19 Electrical System Safety .......................................................................................................................................... 14 2.4.20 Fire Safety .................................................................................................................................................................... 15 2.4.21 Cab Emergency Exit .................................................................................................................................................. 15 2.5 OWNER/OPERATOR ACKNOWLEDGEMENT FOR SAFE OPERATION .......................................................................................... 16 3. VEHICLE SPECIFICATIONS ......................................................................................................................................................... 17 2 3.1 Vehicle Dimensions……………………………………………………………………………………………………..…………18 &19 4. GETTING STARTED ....................................................................................................................................................................... 20 4.1 COMPONENTS ............................................................................................................................................................................. 20 4.2 DAILY CHECKLIST ....................................................................................................................................................................... 21 5. OPERATING INSTRUCTIONS ..................................................................................................................................................... 22 5.1 SAFETY......................................................................................................................................................................................... 22 5.2 COLD START PROCEDURE .......................................................................................................................................................... 23 5.3 TRANSMISSION: DIRECTION, GEAR CONTROL AND MODE ....................................................................................................... 23 5.4 HIGH/LOW GEARING................................................................................................................................................................... 24 5.4.1 Switching between “Low Range” and “High Range” ........................................................................................ 24 5.4.2 Switching Between 2WD and 4WD ........................................................................................................................ 24 5.5 STEER MODE SELECTION ........................................................................................................................................................... 25 5.5.1 Engaging/Disengaging 4 Wheel Steer .................................................................................................................. 25 5.5.2 Engaging/Disengaging Crab Steer ......................................................................................................................... 25 5.6 PARKING BRAKE & EMERGENCY BRAKE OPERATION .............................................................................................................. 25 5.7 REFUELING................................................................................................................................................................................... 26 5.8 DIESEL EXHAUST FLUID (DEF) .................................................................................................................................................. 26 5.8.1 Filling the DEF Tank .................................................................................................................................................... 26 5.8.2 Fill Locations ................................................................................................................................................................. 26 5.8.3 DEF Storage .................................................................................................................................................................... 28 5.8.4 DEF Disposal………………………………………………………………………………………………………………………………………..28 6. CAB INTERIOR ............................................................................................................................................................................... 29 AgTrk RS260 /300™ 3 6.1 CONTROL CONSOLE .................................................................................................................................................................... 29 6.1.1 Gauge Cluster ................................................................................................................................................................ 29 6.1.2 Indicator Lights ............................................................................................................................................................. 30 6.2 UPPER CONTROL PANELS .......................................................................................................................................................... 31 6.2.1 Cab Halo Left Switch Bank........................................................................................................................................ 31 6.2.2 Cab Halo Center Switch Bank .................................................................................................................................. 31 6.2.3 Cab Halo Right Switch Bank ..................................................................................................................................... 31 6.3 RIGHT HAND CONSOLE .............................................................................................................................................................. 32 6.4 AIR RIDE SEAT ADJUSTMENTS ................................................................................................................................................... 33 6.5 BUDDY SEAT ............................................................................................................................................................................... 33 6.6 STEERING COLUMN ADJUSTMENTS............................................................................................................................................ 34 6.7 REMOTE THROTTLE .................................................................................................................................................................... 34 7. GENERAL MAINTENANCE .......................................................................................................................................................... 35 7.1 PERSONAL SAFETY...................................................................................................................................................................... 35 7.2 TORQUE VALUES ......................................................................................................................................................................... 37 7.2.1 Critical Torque Requirements .................................................................................................................................. 37 7.2.2 General Torque Chart (Imperial) ............................................................................................................................. 38 7.2.3 General Torque Chart (Metric) ................................................................................................................................. 38 7.3 FLUIDS AND FILTERS .................................................................................................................................................................. 39 7.3.1 Fluid Requirements ..................................................................................................................................................... 39 7.3.2 Filter Requirements ..................................................................................................................................................... 39 7.4 LUBRICATION .............................................................................................................................................................................. 39 7.5 ENGINE MAINTENANCE............................................................................................................................................................... 40 7.5.1 Engine Oil and Filter ................................................................................................................................................... 40 7.5.2 Fuel System .................................................................................................................................................................... 41 7.5.3 DEF Filters ...................................................................................................................................................................... 41 7.5.4 Cooling System ............................................................................................................................................................. 41 7.5.5 Engine Air Intake .......................................................................................................................................................... 41 7.6 TRANSMISSION MAINTENANCE .................................................................................................................................................. 42 7.6.1 Checking Transmission Fluid Level ....................................................................................................................... 42 7.6.1.1 Fluid Level Check Using Dipstick Method ........................................................................................................ 42 7.6.1.2 Fluid Level Check Using the Electronic Shift Selector Method ................................................................ 44 7.7 TRANSFER CASE MAINTENANCE ................................................................................................................................................ 46 7.8 AXLES .......................................................................................................................................................................................... 46 7.8.1 King Pins ......................................................................................................................................................................... 46 7.8.2 Tie Rod ............................................................................................................................................................................. 46 7.8.3 Planetary and Differential ......................................................................................................................................... 46 7.9 SUSPENSION MAINTENANCE ...................................................................................................................................................... 47 7.10 STEERING SYSTEM MAINTENANCE .......................................................................................................................................... 47 7.11 PNEUMATIC SYSTEM ................................................................................................................................................................ 47 7.12 TIRES ......................................................................................................................................................................................... 47 7.12.1 Tire Replacement ....................................................................................................................................................... 47 7.12.2 Wheel Torque Specifications ................................................................................................................................. 48 7.13 CAB MAINTENANCE .................................................................................................................................................................. 48 7.13.1 Cabin Air Filter ............................................................................................................................................................ 48 7.13.2 Cabin Pressurizer Air Filter ..................................................................................................................................... 48 7.13.3 Lights and Beacon ..................................................................................................................................................... 49 7.14 HVAC MAINTENANCE .............................................................................................................................................................. 49 7.15 BATTERY MAINTENANCE.......................................................................................................................................................... 49 7.16 HYDRAULIC SYSTEM MAINTENANCE ....................................................................................................................................... 49 7.17 POWDERCOAT FINISH MAINTENANCE ..................................................................................................................................... 50 8. TRANSPORTING ............................................................................................................................................................................ 50 TRANSPORTING SAFETY ............................................................................................................................................................. 51 BYSTANDERS………………………..…………………………………………………………………………………………………………..51 ROADWAY TRAVEL ...................................................................................................................................................................... 51 TRAILER HAULING....................................................................................................................................................................... 52 Sutter Buttes Manufacturing 8.1 8.2 8.3 8.4 9. LONG-TERM STORAGE ............................................................................................................................................................... 52 9.1 SAFETY......................................................................................................................................................................................... 52 9.2 PREPARING FOR STORAGE .......................................................................................................................................................... 53 10. COMPONENT IDENTIFICATION & REORDER INFORMATION ..................................................................................... 54 10.1 CHASSIS COMPONENTS DRAWINGS ........................................................................................................................................ 54 10.1.1 Engine & Transmission ........................................................................................................................................... 54 10.1.2 Engine & Transmission ........................................................................................................................................... 54 10.1.3 Engine Cooling & CAC Hoses ................................................................................................................................ 55 10.1.4 Cooling Package......................................................................................................................................................... 55 4 10.1.5 Transfer Case............................................................................................................................................................... 56 10.1.6 Drivelines ..................................................................................................................................................................... 56 10.1.7 Exhaust Assembly ...................................................................................................................................................... 57 10.1.8 Aftertreatment Shroud ............................................................................................................................................. 57 10.1.9 Engine Air Intake ....................................................................................................................................................... 58 10.1.10 Fuel Tank ................................................................................................................................................................... 58 10.1.11 Diesel Exhaust Fluid DEF Tank .......................................................................................................................... 59 10.1.12 Battery Box……………..………………………………………………………………...……………………………………………………..59 10.1.13 Under-Cab Components ........................................................................................................................................ 60 10.1.14 Hydraulic Tank ......................................................................................................................................................... 60 10.1.15 Pneumatic Tanks ..................................................................................................................................................... 61 10.1.16 Cab HVAC Components………….………………….……………………………………………………………………………………61 10.1.17 Suspension Components……………………………………...…………...…………………………..…………………………….….62 10.1.18 Frame/Suspension………………………………………...……………………………………………………………….………….…….62 10.1.19 Platform…………………………………………………………..…………………………………………………...………………….………63 10.1.20 Exterior Cab Components……………………………………...……………………...………………………………………….…….63 10.1.21 Exterior Cab Components…………………...……...…………………………………………………………………………….…….64 10.1.22 Exterior Cab Components………………………...……...…………………………………………………………………….……….64 10.1.23 Front Console/Steering Column………………………………………….……………………………………...………….………65 10.1.24 Interior Cab Components………………………………………...…………………………………………………...…………….…..65 10.1.25 Control Console………………………………………….…………...…………...………………………………….…………….………..66 AgTrk RS260 /300™ 5 10.1.26 Cab Components - Headliner………………………………………………..………...…………………………………..….………66 10.1.27 Hood…………………………………………………………………………………………………………………………………….….……….67 10.1.28 Toolbox…………………………………………………………………………..……...…………………………………….………………….67 10.1 CHASSIS COMPONENTS DRAWING KEY & PART LIST…………………………………...………………………………..……………..68-75 10.2 GRAIN BIN COMPONENTS DRAWINGS..................................................................................................................................... 76 10.2.1 Grain Bin ....................................................................................................................................................................... 78 10.2.2 Bin Auger ...................................................................................................................................................................... 76 10.2.3 Lower Auger ................................................................................................................................................................ 77 10.2.4 Upper Auger................................................................................................................................................................. 77 10.2 GRAIN BIN COMPONENTS DRAWING KEY & PART LIST……….....………...….……....………………………………………….......78-79 10.3 SPRAYER COMPONENTS DRAWINGS ....................................................................................................................................... 80 10.3.1 Sprayer Components ................................................................................................................................................ 80 10.3.2 Tank Components ...................................................................................................................................................... 80 10.3.3 Pump Components .................................................................................................................................................... 81 10.3.4 Four-Link Boom Mount ............................................................................................................................................ 82 10.3 SPRAYER COMPONENT DRAWING KEY & PART LIST…….…………………………………....…………………………………….82-83 10.4 STOMPER COMPONENTS DRAWINGS ...................................................................................................................................... 84 10.4.1 Stomper Complete .................................................................................................................................................... 84 10.4.2 Stomper Trailer .......................................................................................................................................................... 84 10.4.3 Tow Hitch assembly………………………………………………………………..…………..…………………………………………….85 10.4 STOMPER COMPONENTS DRAWING KEY & PART LIST……………………………………………………………………………………………85-86 11. WARRANTY .................................................................................................................................................................................. 87 1. Introduction 1.1 About Us At Sutter Buttes Manufacturing, LLC, we design and fabricate quality, commercial grade orchard cabs for tractors, complete self-propelled bank outs, sprayers, spreaders, specialty ag trailers, and implements. SBM has always been concerned with producing the highest quality products possible. Our goal is to be an integrated part of our community, stewards of our environment, and providers to our local workforce. As farmers, we understand that the products you purchase from us are not only critical to your own livelihood, but also to the livelihood of everyone around you. Thank you for purchasing a vehicle manufactured by Sutter Buttes Manufacturing. Please take the time to read through this manual and any other documents that were provided you to have a complete understanding of your new vehicle. 1.2 Contact Information Sutter Buttes Manufacturing, LLC 1221 Independence Place Gridley, CA 95948 (530) 846-9960 www.sutterbuttesmfg.com 1.3 California Prop 65 Warning 1.4 Operator Orientation Sutter Buttes Manufacturing WARNING: Diesel engine exhaust and some of its constituents are known to the State of California to cause cancer, birth defects and other reproductive harm. For more information, go to www.P65Warnings.ca.gov The directions left, right, front, and rear as used in this manual, are referenced from the operator’s perspective when seated in the cab and facing forward. 1.5 Product Changes The information, specifications, and illustrations in this manual are based on the information that was available at the time this material was written and are subject to change at any time without notice. 6 1.6 Serial Number Location The serial number placard is located on the left frame rail between the front bumper and the toolbox. 2. Safety 2.1 SBM Safety Statement Safety of the operators and bystanders is a main concern when developing and building new products. Designers and manufacturers include in as many safety features as possible. However, every year accidents occur in easily preventable circumstances, which could have been avoided by taking a little time with a more careful approach to handling the equipment. AgTrk RS260 /300™ 7 Safety First! Make the work environment safe by establishing periodic reviews of the safety rules and procedures found in this manual, as well as the related OEM manuals. This section covers the safety rules for operation and maintenance. All operators and maintenance personnel must read this manual before operating or performing maintenance on this unit. The information in this manual emphasizes “safety first”, however it is the responsibility of the owner and operator to create and provide a safe work environment. Most work-related accidents are caused by failure to observe basic safety rules or precautions. An accident can often be avoided by recognizing potentially hazardous situations. As you operate or maintain the unit, you must be alert to potential hazards. You must also have the necessary training, skills, and tools prior to performing any operational or maintenance procedures. Improper operation and maintenance of this unit could result in a dangerous situation that may cause injury or death. Review this manual and all safety data before operating, adjusting, or servicing the unit. Do not operate or maintain this unit until you have read and understand the information contained in this manual. Safety precautions and warnings are provided in this manual and on the unit. If these warnings are not heeded, bodily injury or death can occur to you or other persons. Some illustrations in this manual may show equipment with components removed for clarity. Do not operate the unit with any components removed. Death or serious injury may occur from operating this unit with missing components. SBM cannot anticipate every possible circumstance that might involve a potential hazard. The documentation and information in this manual are not inclusive. If a method of operation not specifically recommended by SBM is used, you must satisfy yourself that it is safe. You should also ensure that the unit will not be damaged or be made unsafe by the methods that you choose. 2.2 Decals: Location and Nomenclature The decals applied to this vehicle are critical to informing the user of potential hazards and providing information on how to operate functions of this vehicle. Replace any missing or damaged decals. 2.3 Safety Icons Nomenclature Sutter Buttes Manufacturing This manual has numerous safety icons. These safety icons provide important operating instructions which alert you to potential injury hazards. Safety Alert Symbol This is the safety alert symbol. It is used to alert you to potential physical injury hazards. Obey all safety messages that follow this symbol to avoid possible injury or death. This manual contains DANGERS, WARNINGS, CAUTIONS, and NOTICES, which must be followed to prevent the possibility of improper service, damage to the equipment, personal injury, or death. The following key words call the readers’ attention to potential hazards. Hazards are identified by the “Safety Alert Symbol” and followed by a signal word such as “DANGER,” “WARNING,” or “CAUTION”. 8 Indicates an imminently hazardous situation which, if not avoided, will result in death or serious injury. This signal word is limited to the most extreme situations. Indicates a potentially hazardous situation which, if not avoided, may result in serious injury or death. Indicates a potentially hazardous situation which, if not avoided, may result in minor or moderate injury. Indicates that equipment or property damage can result if instructions are not followed. 2.3.1 N AgTrk RS260 /300™ 9 Personal Protection Read the manual Hearing Protection Maintenance Procedure Eye Protection Stop Engine Hand Protection Place in Neutral Foot Protection Set Parking Brake Breathing Protection Remove Key First Aid Kit Wear Seat Belt Dispose of Waste Properly Inspect Equipment Use 3-point Contact Use Proper Tools Use Proper Support Use Proper Parts Product Tank 2.3.2 Prohibited Actions No Drugs or Alcohol No Riders Do Not Alter or Modify No Distractions Do Not Weld No Bystanders 2.3.3 Hazard Avoidance Chock Wheels Maintain Safe Distance Crushing Hazard (Body) Fire Hazard Flying Objects Hazard Pinch Point Hazard Crush Hazard (Rollover) Pressure Alert / Check Pressure Safety Alert Symbol Depressurize Safety Shields Dangerous Fumes Hazard Entanglement Hazard Slipping Injury High Pressure Fluid Hazard Explosion Hazard Falling Hazard Explosive Force Hazard (Tires) 2.4 General Operating Safety The performance and capabilities of your SBM AgTrk RS 260/300™ may exceed previous equipment you have owned. To successfully operate this equipment, you must first familiarize yourself with the contents of this manual, related OEM manuals, and all safety and warning decals. Never operate this vehicle under the influence of drugs or alcohol. 2.4.3 Electrocution Hazard 2.4.4 Personal Protection Equipment (PPE) Sutter Buttes Manufacturing Contact with electrical power lines will result in serious injury or death. Check the surrounding area for power lines that could contact the unit. Maintain at least 20 feet of clearance between the unit and any power lines Agricultural chemicals can be toxic. Exposure can cause serious injury or death. When working around or operating this unit, wear appropriate PPE in conjunction with the product being used. It is the owner’s responsibility to provide adequate Personal Protective Equipment when operating and servicing this vehicle. This may include, but is not limited to safety glasses, breathing respirators, gloves, steel-toed shoes, etc. 2.4.5 Fall Hazard Do not use the unit as a work platform. Do not stand on top of the unit at any time. Use the threepoint rule when ascending or descending the unit. Do not allow riders at any time unless they are properly seated in the buddy seat. 10 2.4.6 Seat Belt Use Wear your seat belt when operating this equipment. Make sure that any passenger in the buddy seat is also wearing their seat belt. 2.4.7 Distracted Operation Hazard Do not wear headphones, operate a computer, notebook, cell phone, or any other device that might distract your attention when operating this equipment. 2.4.6 Loss of Control Hazard Do not drive this equipment in high range or on public roads with product in the bed or tank. 2.4.7 Impaired Operator Hazard Do not attempt to operate this unit while under the influence of drugs or alcohol. 2.4.8 Crush Hazard (Rollover) Before leaving the operator’s seat: 1. Stop the vehicle. 2. Set the parking brake. 3. Shut off the engine and remove the ignition key. 2.4.9 Safe Distance Keep all bystanders, especially children, away from the unit while in operation. 2.4.10 Child Hazard AgTrk RS260 /300™ Do not permit children to play on or around the stored unit. 2.4.11 Safety and Information Signs Replace any missing or hard-to-read safety signs. 2.4.12 Safety Guards Do not operate this equipment without all safety guards and safety equipment in place and working correctly. 11 2.4.13 Damaged Parts Hazard Do not use this unit if it needs repair. If you believe the unit has a defect which could cause damage, injury, or death, you should immediately stop using the unit, and make any needed repairs before resuming operations. 2.4.14 Alterations and Modifications Never alter or change any of the components in this unit. Modifications could cause damage, injury, or death. Review the safety instructions with all operators annually. Visually inspect the unit for any loose bolts, worn parts, or damaged structural members and make the necessary repairs before using the unit. 2.4.15 Transporting Safety ALWAYS COMPLY WITH STATE AND LOCAL LAWS Use a towing vehicle and trailer of adequate size and capacity. Secure implement with proper tie-downs. Be especially observant of the height of the vehicle in transport position. Check the clearance of everything you will travel under. 2.4.16 Tire Safety Sutter Buttes Manufacturing Explosive Separation Hazard Do not attempt to mount tires without the proper equipment and experience. Failure to follow proper procedures when mounting a tire on a wheel or rim can produce explosive separation, which could result in serious injury or death. Always use a tire cage to air up a tire after repair or replacement. Explosive Hazard Never weld or heat a wheel and tire assembly with the tire mounted. The heat can cause an increase in air pressure, resulting in a tire explosion. Welding can structurally weaken or deform the wheel. Flying Objects Hazard Inflating or servicing tires can be dangerous. Whenever possible, trained personnel should be called to service and / or mount tires. When inflating tires, use a clip-on chuck and extension hose. Always stand to the side of the tire when inflating, and NOT in front of the tire assembly. If the tire is off the truck, always use a tire cage when inflating any tire. Make sure the tires are inflated evenly. 12 Crush Hazard Make sure the unit is completely supported with suitable stands before removing a wheel assembly or working under the vehicle after it has been raised off the ground. High Pressure Hazard Always maintain the correct tire pressure. Do not inflate tires above the recommended pressures listed on the tire sidewalls. Do not operate the vehicle with under inflated tires. Tire Damage Hazard Check tires for low pressure, cuts, bubbles, damaged rims, or missing lug nuts. Repair or replace any tire with these issues before operating the vehicle. Use approved Tires Do not operate tires beyond their rated speed and load capacities. The maximum speed and load ratings are printed on the side of each tire. Make sure replacement tires and wheels meet or exceed the speed and load ratings of the original tires and wheels. 2.4.17 Hydraulic System Safety High Pressure Fluids Wear proper PPE (hand and eye protection, etc.) when searching for a high-pressure hydraulic leak. Use a piece of cardboard or wood as a backstop instead of hands to identify and isolate leaks. AgTrk RS260 /300™ 13 Hydraulic fluid escaping under pressure can penetrate the skin. Openings in the skin and minor cuts are susceptible to infection from hydraulic fluid. If injured by a concentrated stream of hydraulic fluid, seek medical attention IMMEDIATELY. Without immediate medical treatment, serious infection or toxic reaction can develop if hydraulic fluid penetrates the surface of the skin. Trapped Air Hazard When installing, replacing, or repairing hydraulic system cylinders or parts, make sure that the entire system is charged and free of air before resuming operations. Failure to bleed the system of all air can result in improper machine operation, causing severe injury or property/equipment damage. High-Pressure Hazard Do not make any temporary repairs to the hydraulic lines, fittings, or hoses using tape, clamps, or adhesives. The hydraulic system operates under extremely high pressure and temporary repairs may fail suddenly and create a dangerous situation. Depressurizing the Hydraulic System Relieve pressure from the hydraulic system before removing hoses and/or connections. To relieve pressure from the hydraulic system: 1. Set the park brake. 2. 3. 4. 5. Stop the engine Turn the ignition key to the ON position, DO NOT start the engine. Toggle the control switch for the affected function three times. Turn the ignition key to the OFF position. Make sure all components in the hydraulic system are kept clean and in good working condition. 2.4.18 Pneumatic System Safety Compressed air can be dangerous if proper precautions are not taken. Always use proper PPE when servicing any pneumatic system and follow lockout/tagout procedure as required. Pneumatic system troubleshooting or maintenance should only be performed by a qualified technician. 2.4.19 Electrical System Safety Sutter Buttes Manufacturing Contact with electrical power lines will result in severe injury or death. Check the surrounding area for power lines that could contact the unit. Maintain at least 20 feet of clearance between the unit and any power lines. To avoid injury or death by risk of electric shock, always isolate the batteries away from the rest of the electrical system by switching the master disconnect to OFF. Follow lock out / tag out procedures as required. The only exception to this, is when you are testing circuits or components live. Electrical troubleshooting and maintenance should only be performed by qualified technicians. A simple mistake can cost thousands of dollars replacing expensive electronic components. Wear proper PPE, including safety glasses, whenever working around batteries. Always have a first aid kit, eyewash station, and acid neutralizer (baking soda) nearby. 14 Keep all sparks and open flames away from the batteries, as gas given off by electrolyte is explosive. Avoid contact with battery electrolyte. Wash any spilled electrolyte off your skin immediately, for at least 15 minutes. 1. To avoid injury or equipment damage, disconnect the battery ground cable (negative) before servicing any part of the electrical system. 2. Do not tip batteries more than 45°, to avoid electrolyte loss. 3. Keep all sparks and open flames away from the batteries. 4. Avoid contact with battery electrolyte. Thoroughly wash any spilled electrolyte off your skin immediately after contact. Use baking soda to neutralize acid spills. 2.4.20 Fire Safety It is the responsibility of the owner to provide and maintain adequate and proper fire suppression. It is the responsibility of the operator and maintenance personnel to know where the fire extinguishers are located, what type of fire they are rated for, and if they are fully charged. Keep all extinguishers secured in proper mounts. Any extinguisher that has been used or shows a low charge must be replaced immediately. Report all fires to your supervisor as soon as it is safe to do so. 2.4.21 Cab Emergency Exit In the event of an emergency, the right-side cab window can be used as an emergency exit if the door is blocked or otherwise cannot be opened. AgTrk RS260 /300™ 1. Use the red glass breaking tool located behind the right window to break the window. 2. Exit the cab through the opening in the glass, being careful not to cut yourself on any glass shards remaining on the window frame. 3. Do not operate the unit with a missing window. Contact your dealer for a replacement window before resuming operations. 15 2.5 Owner/Operator Acknowledgement for Safe Operation ACKNOWLEDGEMENT RECEIPT I, _______________________________ acknowledge receipt of the AG TRK RS 260/300™ User Manual. [PRINT NAME CLEARLY] Furthermore, I agree to familiarize myself with these instructions and work within their guidelines. I understand that these safety rules are not all inclusive but serve to complement the overall understanding of potential harmful situations. Customer Name: __________________________________ Company: _______________________________________ Date: ___________________________________________ Sutter Buttes Manufacturing OWNER NOTES: 16 3 Vehicle Specifications ENGINE TRANSMISSION TRANSFER CASE FRONT AXLE REAR AXLE GROSS AXLE WEIGHT RATING GROSS COMBINED WEIGHT RATING SUSPENSION STEERING SERVICE BRAKES PARKING BRAKES TIRES 23.1 - 26 12 PLY V-WHEELS STOMPING WHEELS BATTERIES FINISH Cummins B 6.7L Allison 3000RDS with dual shift mode Marmon-Herrington MGV-750 SISU SSDP12S with 5 planetary wheel end reduction SISU SSDP12S with 5 planetary wheel end reduction 26,500 lbs (12,000 kg) each - front & rear 88,200 lbs (40,000 kg) Leaf Spring Front & Rear Dual Cylinder hydrostatic 7" x 16" Drum S-cam air brakes automatic slack adjusters 30 sq in air chamber spring applied/air released 30 sq in chamber 22" x 65" diameter - 526 lbs. (239 kg) 17" x 76" diameter - 983 lbs. (446 kg) 44" x 68" diameter - 1617 lbs. (734 kg) Group 33 (2) 1000CCA Powdercoat 2021 RS260 RS300 UNIT AgTrk RS260 /300™ 17 ENGINE OIL TRANSMISSION OIL TRANSFER CASE FUEL DEF COOLANT HYDRAULIC RESERVOIR AIR CONDITIONING FRONT DIFFERENTIAL (SISU) REAR DIFFERENTIAL (SISU) AXLE HUB (SISU) TYPE 15W-40 API CJ-4 or CK-4 Allison TES295 or TES389 Gear Oil, 80-90 to 85-140 (API GL-5) ASTM 2D ISO 22241-1 or DIN 70700 CES 14603 AW-46 R134A Gear Oil, 80-90 to 85-140 (API GL-5) Gear Oil, 80-90 to 85-140 (API GL-5) Gear Oil, 80-90 to 85-140 (API GL-5) CAPACITY 17.6 qts (16.7L) 26.5 qts (25L) 13.5 pts (6.4L) 48 gal US (191L) 15 gal US (57L) 14 gal US (53L) 48 gal US (191L) 3.9 lbs (1.77 kg) 40 pts (19L) 40 pts (19L) 2 pts (1L) 3.1 Vehicle Dimensions Bare Chassis with Rice and Cane Tires Grain Bin with Rice and Cane Tires Sutter Buttes Manufacturing Tank Sprayer with Steel V-Wheels 18 Amazone Bin and Tires Stomper Trailer and Stomper Wheels AgTrk RS260 /300™ 19 4 Getting Started Item Description 1 Fuel Tank 2 DEF Tank 3 Battery Box 4 Emergency Power Shutoff 5 Ingress/Egress Ladder 6 Hydraulic Oil Reservoir 7 Engine Air Cleaner 8 Front Bumper Work Lights 9 Field Lights 10 Taillights Sutter Buttes Manufacturing 4.1 Components 20 4.2 Daily Checklist Check daily, prior to each use. Task Make sure you have read and completely understand the Operator’s Manual before operating this equipment. Check for leaks. Hydraulic, radiator, engine, transmission, transfer case, axles, differentials, and hubs. Also check for leaks in the spray system. Check that all vehicle lights are functioning correctly. Check the mirrors are adjusted correctly, clean, and not damaged. Check the windows are clean and not damaged. Check tire conditions, are they cracked, separated, or damaged in any way? Check tire air pressure. Be sure all tires are evenly pressured. Inspect the overall unit for potential problems or damage. Do not operate vehicle if it needs repairs of any type. Check that the operating area is clear and fasten your seat belt before operating the vehicle. After starting the vehicle, perform a complete safety check of the brakes and air system. Check that the alternator is charging correctly, all gauges are working properly, the horn sounds, and the transmission shifts into forward and reverse. Owner Notes: AgTrk RS260 /300™ 21 5 Operating Instructions 5.1 Safety Do not drive this equipment in high range or on public roads with product in the bed or tank. Driving at high speeds with product in the bed/tank will overload the tires, causing tire failure and loss of control. Loss of control will cause death or severe injury. Read and Understand Manual To prevent personal injury or even death, be sure you read and understand all the instructions in this manual and other related OEM manuals. Entanglement Hazard Keep hands and clothing clear of moving parts. Pinch Point Hazard Do not place hands or fingers between moving and/or stationary parts. The weight of the unit will easily cause serious bodily injury. Crush Hazard (Rolling Over) When adjusting the unit or leaving the operator’s seat: Place the transmission in neutral, set the parking brake, shut off the engine, and remove the ignition key. Leaving the operator’s station while the engine is running could result in injury. If it is necessary to exit the operator’s station with the engine running, reduce engine RPM to low idle, place the transmission in neutral, and set the parking brake. The service brakes or the park brakes must be applied whenever the transmission is in neutral. Failure to do so could result in unexpected vehicle movement. Sutter Buttes Manufacturing Overturn Hazard Pick the most level route possible when transporting across fields. Avoid the edges of ditches, gullies, or steep hillsides. Safe Distance Keep all bystanders, pets, and livestock clear of the work area. Fire Hazard Do not pump flammable or explosive liquids or use the equipment near fire or in an explosive atmosphere. At least once per day, check for and remove any trash or debris from the unit, especially around hot components such as the engine, turbocharger, exhaust, batteries, and cooling system. 22 Tire Failure Hazard In the event a tire needs to be replaced, only tires with a 173D rating are acceptable. The owner/operator assumes all risk with using a tire with lesser ratings or if the tires are operated beyond the tire manufacturer’s specifications. 5.2 Cold Start Procedure The SBM AgTrk RS 260/300™ is equipped with an engine block heater and intake air heater for cold weather starting. The engine block heater plug is located on the right side of the engine, behind the alternator. Pre-heat the engine block for several hours prior to starting in cold weather. DO NOT use ether as a starting aid. Ether can cause an explosion if it contacts the intake air heater. 1. Turn the ignition key to the preheat position and the monitor will display “Wait to Start” while the intake heater warms the air in the intake manifold. 2. When the “Wait to Start” message disappears, crank the engine until it starts. a. The engine may misfire and run rough if operated at high throttle while cold. Idle will smooth out as the engine warms up. b. Cold hydraulic fluid may cavitate when pumped. This creates a whining noise and will stop as the oil circulates and warms up. Do not operate the truck above an idle with the hydraulic system cavitating. Do not crank the engine for more than 30 seconds at a time. Allow the starter motor to cool 2 minutes between cranking attempts 3. If the engine does not start, repeat the preheat process. 5.3 Transmission: Direction, Gear Control and Mode AgTrk RS260 /300™ 23 These instructions are intended to give the operator a quick overview of how to operate the transmission. This document does not replace the manual provided by Allison Transmissions. 1 2 3 4 Gear Direction Mode Selection Arrow Up / Down LCD Display Screen 1. Gear Direction The transmission monitor is used to select the travel direction by pressing “R” for Reverse, “N” for Neutral, and “D” for forward direction. 2. Mode Selection Access diagnostic screens and transmission settings 3. Arrow Up / Arrow Down Use the Arrow up and Arrow Down buttons to manually request a target gear. The current gear will be shown in the LCD screen on the shifter as well as on the monitoring console. 4. LCD Display Screen This shows the current gear the transmission is in, as well as any fault codes from the transmission. 5.4 High/Low Gearing The SBM AgTrk RS 260/300™ is equipped with a dual range transfer case, as well as the ability to shift from 2-wheel drive to 4-wheel drive. The Low/High Range switch, located on the right-hand console, allows the vehicle to operate in a gear range that is best suited for its current environment. 5.4.1 Switching between “Low Range” and “High Range” 1. Completely stop the unit, set the transmission to neutral. Sutter Buttes Manufacturing 2. Actuate the desired driving mode, using the “Low Range/High Range” switch on the right-hand console. 3. Listen for the audible gear engagement, place vehicle in desired gear and take off slowly. 5.4.2 Switching Between 2WD and 4WD 1. Completely stop the unit, set the transmission to neutral. 2. Actuate the desired driving mode, using the “2WD/4WD” switch on the right-hand console. 3. Listen for the audible gear engagement, place vehicle in desired gear and take off slowly. 24 5.5 Steer Mode Selection The SBM AgTrk RS 260/300™ has 3 different steer modes included with the vehicle: a standard 2wheel steer system, a 4-wheel steer, and crab steer. 4-wheel steer will turn the rear wheels in the opposite direction as the front, which will allow the vehicle to significantly decrease its turning radius. The crab steer will turn the rear wheels in the same direction as the front, which allows the vehicle to make lateral adjustments while remaining parallel to its direction of movement. 5.5.1 Engaging/Disengaging 4 Wheel Steer 1. 2. 3. 4. 4-wheel steer will have a significant effect on the turning radius of your vehicle. Do not operate the vehicle in 4-wheel steer or crab steer at a speed of over 10mph. Reduce travel speed to <10mph Leave transmission in current gear Engage 4-wheel steering using the “Engage 2WS/4WS” switch on the right-hand console Disengagement of 4-wheel steer is opposite of engagement 5.5.2 Engaging/Disengaging Crab Steer 1. Bring vehicle to a complete stop 2. Leave transmission in current gear 3. Engage Crab Steering using the locking “Engage Crab Steer” switch on the righthand console. Two-wheel steer MUST be engaged. 5.6 Parking Brake & Emergency Brake Operation The SBM AgTrk RS 260/300™ is equipped with a parking brake. The parking brake is to be used anytime the vehicle is stopped, and the operator intends on leaving the seat. The parking brake must be engaged anytime the operator is not in their seat. AgTrk RS260 /300™ 25 Never engage the parking brake when the vehicle is moving, as potential loss of control and brake system damage may occur. DEF is very corrosive to certain types of material. Care should be taken when handling DEF around equipment. 5.7 Refueling 1. Fill the fuel tank with diesel fuel only, from the left side of the vehicle. Replace the fuel cap and clean up any spills when finished refueling. 2. If the engine runs out of fuel, it will be necessary to bleed the fuel lines of air and recharge them with fuel. See the Cummins Operation & Maintenance manual, 4021531 for the proper procedure. 5.8 Diesel Exhaust Fluid (DEF) Diesel Exhaust Fluid (DEF) is a high purity solution urea in water which allows SCR (Selective Catalyst Reduction) engines to meet clean air standards. DEF is a clear liquid similar in appearance to water. DEF is safe to handle and use; it is not explosive, flammable, toxic, or subject to any hazardous product regulations. 5.8.1 Filling the DEF Tank Make sure the DEF nozzle and the fill port on the tank are clean and free of dust and dirt. Fill the DEF tank with ISO certified DEF from dedicated, sealed DEF containers. The DEF tank capacity is 15 gallons. Replace the cap and clean up any spilled DEF when finished. Never add DEF into the fuel tank. Never add diesel fuel into the DEF tank Do not use DEF that has been diluted or altered from manufacturer’s specification Fire Hazard Sutter Buttes Manufacturing • • • Diesel fuel presents a moderate fire hazard. Vapors may be ignited rapidly when exposed to heat, spark, open flame, or other source of ignition. When mixed with air and exposed to an ignition source, flammable vapors can burn in the open or explode in confined spaces. Being heavier than air, vapors may travel long distances to an ignition source and flashback. • • • Do not smoke when refueling the vehicle. Turn the engine OFF before refueling. Do not overfill the fuel tank. 26 5.8.2 Fill Locations AgTrk RS260 /300™ 27 1 2 3 Fuel Fill DEF Fill Hydraulic Oil Level Check 4 5 6 7 Hydraulic Oil Fill Engine Oil Fill Engine Oil Level Check Engine Coolant Fill Transmission Fluid Check and Fill Windshield Wiper Fluid NP NP Left side of chassis Left side of chassis, behind fuel tank Right side of chassis, mounted to hydraulic tank Right side of chassis Top of valve cover, near front Left side of motor On overflow tank, top of radiator Left side of transmission Behind left-rear access panel on cab 5.8.3 DEF Storage 1. Keep DEF storage containers tightly closed. 2. To avoid freezing, do not store at temperatures below 23°F (-5°C). Frozen DEF can be thawed and used without concerns of product degradation, however, damage to the container or equipment may occur. 3. Store only in approved containers. 4. Protect containers against physical damage. 5. To prevent decomposition and evaporation, prolonged storage above 77°F should be avoided. (See table below) Constant Ambient Storage Temperature (°F) ≤50 ≤77* ≤86 ≤95 >95 Minimum Shelf Life (Months) 36 18 12 6 ** *To prevent decomposition of DEF, prolonged transportation, or storage above 77° should be avoided **Significant loss of shelf life. Check every batch before use. 5.8.4 DEF Disposal Sutter Buttes Manufacturing For proper disposal of waste DEF, it should be solidified with stabilizing agents such as sand, flyash, or clay absorbent, so that no liquid remains before disposal in an industrial waste landfill. Always follow local rules and regulation when disposing waste. Fluid Check and Fill Locations 28 6. Cab Interior 6.1 Control Console The SBM AgTrk RS260/300™ is equipped with an Opus A8 engine monitoring console. Its interface has been designed to present relevant vehicle information in an intuitive layout for the operator. Please familiarize yourself with the gauge cluster as well as all the indicator and warning lights. 6.1.1 Gauge Cluster 2 1 13 5 0 4 3 11 0 9 AgTrk RS260 /300™ 29 1 2 3 4 5 6 7 8 9 10 11 12 13 7 6 8 DEF Gauge Transmission Gear Selector Fuel Gauge Tachometer Speedometer Coolant Temperature Gauge Hydraulic Oil Pressure Gauge Hydraulic Oil Temperature Gauge Throttle Engagement Gauge Voltmeter Pneumatic Pressure Gauge Fuel Economy Gauge Oil Pressure Gauge 10 0 12 0 6.1.2 Indicator Lights G F J H K L A B A B C D E F G H J K L M M E D Water in Fuel Exhaust Temperature Warning Parking Brake Engaged Check Engine Engine Preheat Low Fuel Engine Stop Transmission Malfunction Engine Brake High Gear Range Low Gear Range Hydraulic Temperature Warning Sutter Buttes Manufacturing C 30 6.2 Upper Control Panels 6.2.1 Cab Halo Left Switch Bank 1 2 3 4 5 6 Cab Lights Backlighting Hazard Lights Field Lights – Center Field Lights – Middle Field Lights – Outer 1 2 3 Fan Speed Off / On / Max AC Air Temperature 6.2.2 Cab Halo Center Switch Bank 6.2.3 Cab Halo Right Switch Bank AgTrk RS260 /300™ 31 1 2 3 4 5 6 Microphone Mirror or Auxiliary Lights Rear Work Lights Mirror Heater Windshield Wiper Windshield Wiper Fluid 6.3 Right Hand Console Blank Blank Center Rack Up/Down Left Boom Up/Down Right Boom Up/Down Spray Pump Engage PTO Blank Engage Crab Steering Engage 2WS/4WS Engage 4X4 Engage High/Low Range Bin Cover Up/Down Big Auger On/Off Vertical Auger On/Off 16 17 18 19 20 21 22 23 24 25 26 27 28 29 Unloading Auger In/Out Left Inner Boom Left Outer Boom Right Inner Boom Right Outer Boom Blank Blank Blank Engage Parking Brake Hand Throttle Push Button Shifter 12VDC Power Port Cup Holder 12V USB Power Port Sutter Buttes Manufacturing 1 2 3 4 5 6 7 8 9 10 11 12 13 14 15 32 6.4 Air Ride Seat Adjustments The SBM AgTrk RS260/300 is equipped standard with an adjustable air ride seat for maximum operator comfort during long operation hours. Never attempt to adjust the seat during operations. Always adjust the seat when the vehicle is stationary and park brake is set. AgTrk RS260 /300™ 33 1 2 3 4 5 6 7 8 9 10 11 12 Armrest Tilt Control Fore-Aft Isolation Lock-Out Adjustable Damper Control Height Adjustment Control Backrest Tilt Control Fore-Aft Slide Control (Seat Only) Fore-Aft Slide Control (Seat and Console) Seat Cushion Tilt Fore-Aft Control (Cushion Only) Lumbar Support Seat Venting/Heaters Seat Venting/Heaters High/Low 6.5 Buddy Seat The SBM AgTrk RS260/300™ is equipped with a buddy seat in all cabs. This allows for one person besides the operator to ride along in the cab. All passengers must wear their seat belt for safety. 6.6 Steering Column Adjustments Steering Wheel Height Adjustment 2 Steering Column Tilt 3 Steering Column Tilt (Top Half Only) 6.7 Remote Throttle Loosen hub and move steering wheel to desired height. Tighten hub. Press pedal with foot and move steering wheel to desired position. Press lever and move steering wheel to desired position. Sutter Buttes Manufacturing 1 The SBM AgTrk RS260/300™ comes standard with a hand throttle, located on the right-hand console. It is set up with the foot throttle as a “greater throttle wins” setup, meaning that whichever throttle is more engaged will be the throttle setting. Do not utilize the hand throttle with highway travel. Always use the foot throttle when on public roads. Runaway conditions may exist. 34 7. General Maintenance 7.1 Personal Safety To prevent serious injury or death, follow all guidelines outlined in this section before preforming any maintenance on the vehicle. Roll Over / Crush Hazard To prevent serious injury or death, before servicing, adjusting, repairing, or performing other work on the unit, always make sure that the transmission is placed in neutral, the parking brake is set, vehicle engine is stopped, and the ignition key is removed. Before repairing or removing any hydraulic, pneumatic, cooling system, or electrical parts be sure all pressure has been relieved in the hydraulic, pneumatic, and cooling systems. Also turn off the battery disconnect switch and hang a “DO NOT OPERATE” tag in the operator station, following proper lockout-tagout procedure. Securely support any machine elements that must be raised for service work. Always use the proper supports whenever the vehicle or its parts are raised. Be sure the support is rated for the load it is supporting and that it has no damage. Practice Safe Maintenance Understand service procedures before to starting any work. Keep work area clean and dry. Never lubricate, service, or adjust machine while it is still moving. Keep hands, feet, hair, and clothing away from power driven parts. Disengage all power and operate controls to relieve pressure. Stop the engine and remove the ignition key. Allow the engine to cool before removing the coolant filler cap. AgTrk RS260 /300™ 35 Contact with electrical power lines will result in serious injury or death. Check the surrounding area for power lines that could contact the unit. Maintain at least 20 feet of clearance between the unit and any power lines. Before making any adjustments on electrical systems or welding on the machine: o Disconnect the battery cables, negative cable first, and then the positive cable. o Disconnect the main harness at the Engine ECM, located on the left side of the engine, just above the dipstick. o Disconnect the transmission harness at the TCM, located at the right rear outside of the cab bolted to the harness bulkhead panel. Use Properly Rated Tools Use tools, jacks, and hoists that have the capacity for the job. Makeshift tools and procedures can create safety hazards. For loosening and tightening hardware, use the correct size tools. Crush Hazard Use support blocks or safety stands rated to support the load when changing tires or performing maintenance. Entanglement Hazard Keep hands, feet, clothing, jewelry, and long hair away from any moving parts to prevent them from getting caught. Engine exhaust fumes can cause sickness or death. If it is necessary to run the engine in an enclosed area, remove the exhaust fumes with an exhaust pipe extension to the outdoors. If you do not have an exhaust pipe extension, open the doors to get outside air flowing through the area. Use fans if necessary to remove fumes. Hazardous fumes can be generated when paint is heated by welding, soldering, or using a torch. Wear proper personal protective equipment (PPE) and ventilate the area. Handle Flammable Fluids Safely o Do not smoke or work near heaters or other fire hazards when handling flammable fluids. Make sure machine is clear of trash, grease, and debris. o Oily rags must be kept in fire resistant, OSHA compliant, covered containers; they can ignite and burn spontaneously. o Store and dispose of paint, solvents, and other hazardous fluids properly. Always store flammable fluids in an OSHA compliant flammable storage cabinet. Sutter Buttes Manufacturing o Prepare for Emergencies o Always keep a first aid kit and a fire extinguisher readily available and easily accessible. Be sure the fire extinguisher is fully charged, rated for the type of fire that might start, and large enough for the situation. o Keep a phone with you whenever operating the equipment so that emergency services can be contacted quickly if needed. 36 Before starting a job: o o o o Clean the work area and machine. Make sure you have all the necessary tools to do your job. Have the right parts on hand. Read the instructions thoroughly. Do not attempt shortcuts. Dispose of Waste Properly Improperly disposing of waste can threaten the environment. Potentially harmful waste used with SBM equipment includes such items as oil, fuel, coolant, hydraulic fluid, filters, spray chemicals, and batteries. • Use leak proof containers when draining fluids. Do not use food or beverage containers that may mislead someone into drinking from them. Properly label all containers used to hold waste products with the waste product name and safety data sheet (SDS) required information. • Do not pour waste on the ground, down a drain, or into any other water source. • Air conditioning refrigerants escaping into the air can damage the atmosphere. Government regulations prohibit the release of refrigerants and may require a certified air conditioning service center to recover and recycle used air conditioning refrigerants. Contact your local environmental or recycling center for the proper way to recycle or dispose of waste. 7.2 Torque Values 7.2.1 Critical Torque Requirements AgTrk RS260 /300™ 37 PTO Mounting Bolts Piston Pump Bolts PTO flange Bell Housing Hot & Cold Charge Air Tube Clamps U-bolts Fuel Tank & Hydraulic Tank Strap Clamps Driveline Bolts (3/8”) Driveline Bolts (7/16”) Fan Bolts Air Governor Hose Clamps Ft-lbs. (Nm) 45 57 18.9 51-61 14 500 27 37 58 37.2 18 14 61 (77) (26) (69-83) (19) (678) (37) (50) (79) (50) (24) (19) 7.2.2 General Torque Chart (Imperial) Bolt Diameter 1/4” 5/16” 3/8” 7/16” 1/2" 9/16” 5/8” 3/4 7/8” 1” SAE Grade 5 Ft-lbs. 9 19 33 53 80 115 160 290 420 630 (Nm) (12) (25) (45) (72) (110) (155) (215) (390) (570) (850) SAE Grade 8 Ft-lbs. 12 27 45 75 115 165 220 400 650 970 (Nm) (17) (36) (63) (100) (155) (220) (305) (540) (880) (1320) 7.2.3 General Torque Chart (Metric) M6 M8 M10 M12 M14 M16 GRADE 8.8 Ft-lbs. 7.5 18 37 59 63 103 (Nm) (10) (25) (50) (80) (85) (140) GRADE 10.9 Ft-lbs. 11 26 55 83 97 151 Sutter Buttes Manufacturing Bolt Diameter (Nm) (15) (35) (75) (113) (130) (205) 38 7.3 Fluids and Filters 7.3.1 Fluid Requirements 2021 RS260 RS300 TYPE UNIT ENGINE OIL TRANSMISSION OIL TRANSFER CASE FUEL DEF COOLANT HYDRAULIC RESERVOIR AIR CONDITIONING FRONT DIFFERENTIAL (SISU) REAR DIFFERENTIAL (SISU) AXLE HUB (SISU) CAPACITY 15W-40 API CJ-4 or CK-4 Allison TES295 or TES389 Gear Oil, 80-90 to 85-140 (API GL-5) ASTM 2D ISO 22241-1 or DIN 70700 CES 14603 AW-42 R134A Gear Oil, 80-90 to 85-140 (API GL-5) Gear Oil, 80-90 to 85-140 (API GL-5) Gear Oil, 80-90 to 85-140 (API GL-5) 17.6 qts (16.7L) 26.5 qts (25L) 13.5 pts (6.4L) 48 gal US (191L) 15 gal US (57L) 14 gal US (53L) 48 gal US (191L) 3.9 lbs (1.77 kg) 40 pts (19L) 40 pts (19L) 2 pts (1L) *Fluid capacities are a guideline only. Proper fluid checks must be made to ensure there is correct fluid levels for operation. 7.3.2 Filter Requirements FUNCTION SBM PART # Engine Air Filter, Primary Engine Air Filter, Secondary Fuel Filter, Primary Fuel Filter, Secondary Engine Oil Filter Cab Air Filter (Standard) Cab Air Filter (Charcoal) Cab Air Filter (Recirculating) Hydraulic Oil Filter Transmission Filter 100047 100048 100049 100050 100051 100054 100055 100226 100052 100053 7.4 Lubrication AgTrk RS260 /300™ Grease all fittings using an SAE multipurpose high-temperature grease with extreme pressure (EP) performance. Wipe grease fittings with a clean cloth before greasing to avoid contamination. o o o o Apply grease until new grease can be seen coming out of each cap of the u-joint. Do not let excess grease collect on or around parts, particularly when working in sandy areas. Replace broken grease fittings immediately. If any grease fitting will not take grease, remove, and clean thoroughly. Also clean the lubricant passageway. Replace the hardware if necessary. 39 7.5 Engine Maintenance Always refer to the Cummins Operation & Maintenance manual, 4021531 for all engine maintenance procedures. 7.5.1 Engine Oil and Filter Check the engine oil level every 10 hours of operation. Change the engine oil and filter every 500 hours or 6 months, whichever comes first. To change the engine oil, use a container that can hold at least 24 quarts of oil. 1 Take all safety precautions to prevent the vehicle from moving unintentionally. Operate the engine until the coolant temperature reaches 140° F (60° C). 4 Remove the oil drain plug and drain the oil immediately to ensure that all suspended contaminants are removed with the oil. Wear the proper PPE to protect yourself from burns. Clean and check the drain plug threads and sealing surface. Re-install the oil pan drain plug. Remove the oil filter and clean the gasket surface on the engine filter head. 5 Lubricate the new oil filter gasket with clean engine oil. 6 Fill the new oil filter with the correct grade of clean engine oil. Pour the oil into the outer openings of the filter head, not the center opening. This will cause the oil to pass through the filter before entering the engine. 7 Install the new filter on the oil filter head. Tighten the filter until the gasket contacts the filter head surface. 8 Use the correct style oil filter wrench to tighten the filter an additional 1/2 to 3/4 of a turn. Follow the instructions included with the oil filter. 9 Fill the engine to the proper level with the correct grade of oil. 3 10 Start the engine and allow it to idle for two minutes. Sutter Buttes Manufacturing 2 If no oil pressure is noted within 15 seconds after the engine is started, shut down the engine to reduce the possibility of internal damage. 11 Shut off the engine. Wait approximately 10 minutes to let the oil drain from the upper parts of the engine. Check the oil level again. 12 Add oil as necessary to bring the oil level to the “H” (high) mark on the dipstick. 13 Dispose of the used oil and filter in accordance with local regulations. 40 7.5.2 Fuel System 1. Inspect the fuel cap for seal integrity and damage every time you add fuel. 2. Replace the primary fuel filter every 500 hours or 6 months, whichever comes first. 3. Take all safety precautions to prevent the vehicle from moving unintentionally. Shut off the engine and remove the key. 4. Remove the fuel filter using the correct tool. 5. Install a new fuel filter after applying a light film of engine oil to the gasket. DO NOT PRE-FILL THE FUEL FILTER. 6. Drain the water separator daily. Replace the secondary fuel filter every 500 hours or 6 months, whichever comes first. 7. Collect and dispose of used filters in accordance with local regulations. 7.5.3 DEF Filters 1. There are no serviceable parts within the DEF Dosing system. If you suspect the faulty components in the DEF dosing system, contact your dealer. 7.5.4 Cooling System 1. Check the coolant level every 10 operating hours. Add coolant as needed to maintain the proper level. Use the correct type of coolant. Do Not exceed a 50/50 mix. 2. Clean the radiator every 10 operating hours using water or compressed air, directing the flow of air or water from the engine side to the front of the radiator. Inspect the fan every ten operating hours for signs of damage or wear. Check the fan belt tension every 10 operating hours. 3. Every 6 months, 500 hours, or whenever coolant is added between filter changes, perform a SCA (supplemental coolant additive) check and check antifreeze concentration with a refractometer. Adjust the SCA and concentration of the coolant if necessary. Test coolant for replacement limits every 2000 hrs. or 2 years, whichever occurs first. Replace coolant only if replacement limits have been exceeded. Follow the guidelines in Cummins service bulletin 3666132. AgTrk RS260 /300™ 4. When adding coolant, always use a 50/50 mix of distilled water and antifreeze that meets Cummins CES 14603. Do not exceed a fill rate of 5 gallons per minute. 5. If the coolant must be drained for any reason, you must follow the refill procedure in the Cummins Operation & Maintenance manual 4021531. 7.5.5 Engine Air Intake 1. Inspect the air intake system for leaks or damaged components. Check the air filter restriction indicator every 10 operating hours. The indicator is located on the rear 41 side of the air cleaner cover. Replace the air filter when the restriction indicator shows the need. 2. Check the dust evacuator valve on the bottom of the air cleaner daily. Replace the valve if it is not closing and sealing properly. 7.6 Transmission Maintenance 7.6.1 Checking Transmission Fluid Level Check the transmission oil level every 10 operating hours. Always us OEM approved fluids. The transmission fluid level can be checked 2 ways. (COLD CHECK or HOT CHECK) 1. Using the dipstick method 2. Using the shift selector method to electronically check the Oil Level Sensor (OLS) located in the transmission control valve module. This method provides the most accurate readings. When the dipstick method must be used: a. The transmission fluid temperature is below 160° F (71° C) b. The oil level sensor (OLS) was not auto detected or is defective. DO NOT operate the transmission for extended periods of time until the proper fluid level has been determined. Transmission damage will result from extended operation with either high or low fluid levels. A COLD CHECK will verify the fluid level is adequate to start the engine A HOT CHECK will verify the proper fluid level for continued engine operation. 7.6.1.1 Fluid Level Check Using Dipstick Method Sutter Buttes Manufacturing The dipstick, as shown, is marked with two temperature bands for a COLD and HOT fluid level check. Always check fluid level at least twice. Note the color of the fluid and check the fluid for contaminates. Typically, the most accurate COLD CHECK is with fluid temperatures from 61° to 120° F (16° to 49° C) The HOT CHECK is done with operating temperature of 160° to 200° F (71° to 93° C) which offer the best assurance of maintaining the correct fluid level. 42 To prevent damage to the transmission, the fluid level must be maintained above the COLD ADD mark and below the HOT FULL mark. The COLD ADD mark assures the fluid is above the charging pump suction port inside the transmission. This prevents charging pump cavitation which causes aeration of the fluid and erratic operation of the transmission. If the fluid is above the HOT FULL mark, it may contact the rotating parts of the transmission causing fluid aeration which results in erratic transmission operation, causing overheating and power loss. Rollover / Crush Hazard If the vehicle is left unattended while the engine is running, the vehicle can move unexpectedly, causing serious injury or death. Before leaving the vehicle while the engine is running: 1. Be sure the engine is at low idle. 2. Put the transmission in N, neutral. 3. Apply the parking brake. 4. Chock the wheels and take any other necessary steps to keep the vehicle from moving. The correct fluid level cannot be determined unless the transmission is in a level position. 1. Move the vehicle to a level surface, be sure the engine is at low idle, put the transmission in N (Neutral) and set the parking brake. 2. Idle the engine at low idle for about one minute. AgTrk RS260 /300™ a. COLD CHECK: With the brakes applied, shift to D (Drive) and then to R (Reverse) to clear trapped air from the hydraulic circuits. b. HOT CHECK: Continue to step 3. 3. Check the transmission fluid temperature. a. COLD CHECK: the transmission fluid temp. should be 61 to 120° F (16 to 49° C) b. HOT CHECK: the transmission fluid temp. should be 160 to 200° F (71 to 93° C) 4. Clean any dirt from around the end of the fill tube before removing the dipstick. 43 5. Remove the dipstick and wipe it clean. 6. Reinsert the dipstick into the fill tube, pushing down until it stops, but still in its loose and unscrewed position. 7. Remove the dipstick and observe the fluid level. a. COLD CHECK: If the fluid on the dipstick is within the COLD CHECK band, the level is satisfactory. If the fluid level is not within this band, add or remove fluid, as necessary. b. HOT CHECK: If the fluid on the dipstick is within the HOT CHECK band, the level is satisfactory. If the fluid level is not within this band, add or remove fluid, as necessary. 8. Check the fluid level more than once to confirm consistent readings. If the readings are not consistent, make sure the transmission breather is not dirty or clogged. 9. Adjust the fluid level accordingly. a. Do not overfill the transmission. Overheating can cause oil foam to clog the breather. A loss of power can also occur if the transmission is overfilled. b. DO NOT fill the transmission above the COLD CHECK band if the transmission fluid is below normal operating temperatures because the fluid level will rise as the fluid temperature increases. 10. If your fluid levels will not stay consistent, contact your dealer. 7.6.1.2 Fluid Level Check Using the Electronic Shift Selector Method The Oil Level Sensor (OLS) is a standard feature in the transmission and is designed to measure the transmission fluid level. This electronic sensor provides a fluid level check that is more accurate than the dipstick method, and thus is preferred. Sutter Buttes Manufacturing The OLS has a detection range of up to four quarts low (Lo 4) to three quarts high (Hi 3) which are displayed on the electronic shift selector. In the low-level condition, the actual oil needed may be greater than 4 quarts if the transmission is greater than 4 quarts low. In the high-level condition, the actual fluid volume to drain may be greater than 3 quarts if the transmission is greater than 3 quarts overfull. 1. Be sure the fluid has reached the correct operating temperature range of 104 to 219°F (40 to 104° C). 2. Park the vehicle on a level surface and set the engine to low idle. 3. Shift to N, neutral and apply the parking brake. 4. If the unit has been moved, wait for 2 minutes after placing it in neutral to allow the oil to drain back into the transmission. The TCM communicates status once fluid level request is indicated. 44 5. Press the ↑ (Upshift) and ↓ (Downshift) arrows simultaneously on the keypad of the shift selector. a. The display on the transmission shift selector should now indicate fluid level status by sequentially flashing the fluid level information two characters at a time to the select and monitor digital displays. b. A delayed fluid level check is indicated by a “—“ in each of the digital displays (Select and Monitor) followed by a numerical countdown. The countdown, from 8 to 1, indicated the time remaining in the two-minute waiting (Settling) period. c. Correct Fluid Level – “o, L” is displayed (represents Fluid (Oil) Level Check Mode), followed by “o, K”. The “o, K” display indicates the fluid is within the correct fluid level zone. The sensor display and the transmission dipstick may not agree exactly because the OLS compensates for fluid temperature. d. Low Fluid Level – “o, L” is displayed (represents Fluid (Oil) Level Check Mode), followed by “Lo” (represents low fluid level) and the number of quarts the transmission is low. For example: “2” indicates 2 additional quarts will bring the fluid level within the middle of the “o, K” zone. e. High Fluid Level – “o, L” is displayed (represents Fluid (Oil) Level Check Mode), followed by “HI” (represents High Oil Level) and the number of quarts the transmission is overfilled. For example: “1” indicates 1 quart of fluid above the full transmission level. f. Invalid For Display – “o, L” (represents Fluid (Oil) Level Check Mode), followed by “—” and an alphanumeric which is a fault code and indicates conditions are not acceptable to receive the fluid level information, or there is a system malfunction. g. Below are charts to help organize the Fluid Level Check diagnostics screen. Sequence 1st 2nd AgTrk RS260 /300™ 45 Sequence 1st 2nd 3rd Select o o Select o L o Monitor L K Monitor L o 1-4 Correct Fluid Level Description Fluid (oil) Level Check Mode Fluid (oil) is within the correct fluid level zone. Low Fluid Level Description Fluid (oil) Level Check Mode Low Fluid (oil) condition Indicates the number of quarts low High Fluid Level Sequence 1st 2nd 3rd Select o H 0 Monitor L I 1 Description Fluid (oil) Level Check Mode High Fluid (oil) Condition Indicates the number of quarts overfull Sequence 1st 2nd Select o -- Monitor L -- Invalid for Display Description Fluid (oil) Level Check Mode The dashes are followed by a numerical which is a fault code that indicates conditions that are not proper to receive the fluid level information or there is a system malfunction. 6. To exit Fluid Level Check Mode, press any range button on the push button shift selector. 7.7 Transfer Case Maintenance Check the oil level in the transfer case every 50 hours of operation. Fill as needed with the specified gear oil. Change the oil every 500 operating hours. To check the oil, remove plug at the left rear of the transfer case even with the output yoke. The oil should be at the bottom of the hole while cold. Do not overfill. Replace the plug and tighten it properly. To replace the oil, warm up the oil to operating temperature by driving the vehicle, remove the drain plug in the bottom of the case. When the oil is all drained out, replace the plug, and fill the transfer case at the oil check hole until oil runs out. Let the oil drain out the filler hole until it is at the bottom of the hole. Clean and replace the plug. Properly tighten both plugs. 7.8 Axles 7.8.1 King Pins Lubricate the upper and lower grease fittings on each of the front axle kingpins daily. Apply grease until you can see new grease coming out of the upper and lower bearing. Do not over-grease. 7.8.2 Tie Rod Grease the fittings on the tie rod ends daily. Apply grease until you can see new grease coming out of the joint. Do not over-grease. 7.8.3 Planetary and Differential Sutter Buttes Manufacturing Check the oil level in each planetary and differential every 50 hours of operation. Change the oil every 500 hours of operation. Turn the hub until the oil check plug is at the 4 o-clock position. Remove the plug. The oil should be at the bottom of the hole when cold. Do not overfill. Replace the plug and tighten properly. Check the differential oil level after checking the hubs. Remove the filler plug on the rear of the axle housing. The oil should be at the bottom of the hole when cold. Replace the plug and tighten properly. Do not overfill. To replace the hub oil, warm up the oil to operating temperature by driving the vehicle, turn hub until the plug is at the bottom, remove the plug and drain the hub. Turn the hub to the 4 o-clock position and fill hub with the proper oil through the hole. When the oil runs out of the hole, stop filling it and let it drain until the oil is at the bottom of the hole. Replace the plug and tighten properly. To replace the differential oil, warm up the oil to operating temperature by driving the vehicle, remove the plug at the bottom of the axle housing, and drain the axle & differential. Replace the drain plug and tighten properly. Remove the fill plug at the rear of the 46 axle housing centered behind the differential. Fill the axle housing and differential with the proper oil through this hole. When the oil runs out of the hole, stop filling it and let it drain until the oil is at the bottom of the hole. Replace the plug and tighten properly. 7.9 Suspension Maintenance 1. Inspect suspension daily for weak or damaged springs, loose, or broken spring clamps, and worn U-bolts. Replace any of these items that are damaged or broken. 2. Clean leaf springs with wire brush and soap every 250 hours. Do not use a lubricating oil to clean leaf springs. Check the side of each leaf for hairline cracks. Replace any cracked leaf spring. 7.10 Steering System Maintenance Grease all lubrication points every 10 hours. Do not over-grease. Do not attempt to service the position sensors on the rear axle. These sensors can only be serviced by a qualified technician. 7.11 Pneumatic System The SBM AgTrk RS260/300 is equipped with an onboard air compressor, driven by the engine. It supplies compressed air to the brakes and automatic ladder. There are 2 tanks in the system, located on the right side of the vehicle, inside the frame. Each is fitted with a drain valve. Drain pneumatic system daily, or when servicing components. 1. Inspect the air compressor every 250 hours. 2. Repair all air leaks immediately. Do not operate the vehicle with air leaks. 7.12 AgTrk RS260 /300™ 47 Tires 7.12.1 Tire Replacement 1. Check tires for damage and wear, also check the air pressure every 10 operating hours. Maintain the tire pressure at the tire manufacturer’s recommended pressure. 2. Check the tightness of the wheel lug nuts every 10 operating hours. Tighten to the maximum torque specification using the procedure in “Wheel Torque Specifications” below. 7.12.2 Wheel Torque Specifications 1. Each wheel stud must be tightened to 450 ft-lbs. using the sequence listed below. 2. Tighten each wheel stud nut to 50 ft-lbs. following the pattern above. 3. Verify the alignment of the wheel on the hub. 4. Tighten to 250 ft-lbs. following the pattern above. 5. Tighten to 450 ft-lbs. following the pattern above. 7.13 Cab Maintenance Wipe interior of cab down with mild cleaning solution. Take extra precaution around switches and electrical components. Use leather conditioner on seat (if equipped with leather seat). 7.13.1 Cabin Air Filter The cab air recirculation filter is located on the right side of the seat support near the cab floor. This filter should be cleaned every 50 hours. Replace the filter every 250 hours. 1. Remove the two knobs and the cover. installing it. Sutter Buttes Manufacturing 2. Remove the foam filter element and wash with soap and water. Dish hand soap and water will work. Thoroughly rinse the filter and allow it to air dry completely before re- 3. Replace the filter and cover. Tighten the retainer knobs securely. 7.13.2 Cabin Pressurizer Air Filter The cab fresh air filter is located near the access panel at the left rear corner of the cab. The filter should be cleaned every 50 hours and replaced every 250 hours, or sooner if an odor is detected inside the cab. This filter is cleaning the outside air as it enters the cab. When spraying it is possible to saturate this filter with chemicals, from the spray, and it may need changed more often. 1. Remove the plastic knob and cover. 48 2. Remove the knob that holds the filter in place. 3. Replace with a new filter and re-install the retaining knob and filter shroud. 4. Replace the cover and secure with the retaining knob. Certain applications require specific pressurizer filters to meet safety requirements. Choose a filter that will work best with the usage of your vehicle. 7.13.3 Lights and Beacon Check the lights and rotating beacon for proper operation every 10 hours. 7.14 HVAC Maintenance Inspect the A/C compressor drive belt and condenser every 10 hours. Check the refrigerant hoses every 250 hours. Have a qualified service technician check the refrigerant levels, the compressor clutch, and belt tensioner every 1000 hours or annually, whichever comes first. The air conditioning system contains R134A refrigerant under pressure. It should only be serviced by a qualified technician with the proper equipment and training for recovery of R134A refrigerant. 7.15 Battery Maintenance Visually inspect the condition of the batteries every 10 operating hours. Check the cables for tightness, damage, and corrosion every 10 hours. Remove any corrosion present with a battery cleaner. Always wear the proper PPE when servicing batteries. 7.16 AgTrk RS260 /300™ 49 Hydraulic System Maintenance Check the hydraulic oil level at the sight gauge on the hydraulic tank and all hydraulic fittings and components for visible signs of leaks or wear every 10 hours of operation. If no oil is visible in the sight gage, add the correct type and weight hydraulic oil until it is in the center of the sight gage when the oil is cold, near the top of the sight gage when the oil is at operating temperature. Change the hydraulic oil filter every 500 operating hours. Replace the hydraulic oil every 1000 hours or annually, whichever comes first. NEVER, under any circumstance, should you use your bare hands to check for leaks in a high-pressure hydraulic system. Use a piece of cardboard or wood. 7.17 Powdercoat Finish Maintenance The recommended method for cleaning your powder-coated surface is to use warm water and mild soap. We do not recommend using chemical cleaners such as acetone, mineral spirits, or lacquer thinners. For difficult to clean areas, we recommend using a soft cloth, sponge, or soft bristled brush. Thoroughly rinse with water after cleaning the surface. Maintaining the finish of your powder-coated parts is essential to protecting your investment. Powder-coating is one of the most durable protective coatings available for metal surfaces, but proper care will help prolong the finish. Over time, a powder-coated finish exposed to the elements may show signs of weathering such as the following: reduction in gloss, chalking, and slight color loss. A consistent, scheduled cleaning of the surface will help remove dirt, grime, and other surface buildup that may be harmful to the powder coated finish. For a long-lasting aesthetically pleasing finish, a simple rule of thumb is to treat your powder-coated part as if it were a paint job on your automobile. 8. Transporting ALWAYS COMPLY WITH FEDERAL, STATE, AND LOCAL LAWS 8.1 Transporting Safety Loss of Control Do not drive this equipment in high range or on public roads with product in the bed of tank. Driving at high speeds with product in the bed or tank will overload the tires, causing tire failure and loss of control. Loss of control will cause serious death or injury. Sutter Buttes Manufacturing Tire Hazard Check the tires for tread wear, inflation pressure, and overall condition before transporting the unit. Do not exceed the operating limitations set by the tire manufacturer. Excessive Speed Hazard Do not operate this vehicle at more than 30 MPH at any time. Hazard Lights Make sure directional, brake, and running lights are connected and working properly. Bystander Warning Make sure the area is clear of children, animals, and any other obstacles before moving the unit. Towing Hazard 50 Do not use the vehicle for towing on a roadway. 8.2 Bystanders Stay Clear Beware of physical surroundings, especially bystanders, and children. Walk around the vehicle before entering the cab. Use a spotter to watch the area and make sure no one enters your blind spots. Use your hand-free phone to hear directions from your spotter. Before moving the unit sound the horn. With the high noise level and sound suppressed cab you may not be able to hear people shouting so be very cautious and move slowly while starting or ending any transport move. No Passengers Allowed Do not carry passengers. You may have one passenger if they are properly seated in the buddy seat with their seat belt fastened. 8.3 Roadway Travel AgTrk RS260 /300™ 51 o Check windshield for cracks and rearview mirrors for proper alignment. Remove anything that obstructs the view from inside the cab. o Check that all lighting is in proper working order. o Be sure all safety equipment, personal items, and tools are secured before proceeding. o If traveling on a roadway, be sure the application equipment is turned off. o Always drive at safe speeds for the road conditions and ensure that your speed is low enough for an emergency stop. Keep speed to a minimum. NEVER DRIVE OVER 30 MPH. o Reduce speeds prior to turns to avoid the risk of overturning. o Avoid sudden turns on steep slopes. o Always keep the vehicle in gear to provide engine braking when going downhill. DO NOT COAST. o When driving the equipment on the road or highway, use flashing amber warning lights where required. Display a Slow-Moving Vehicle (SMV) emblem. If operating at more than 25 MPH, display a SMV emblem and a Speed Indicator Symbol (SIS) sign. Some localities prohibit the use of flashing amber lights. Local laws should be checked for all highway lighting and marking requirements. o Be a safe and courteous driver. Always yield to oncoming traffic in all situations, including narrow bridges, inspections, etc. Plan your route ahead of time to avoid heavy traffic. o Be observant of bridge load restrictions. Do not cross bridges rated lower than the gross weight of your vehicle. o Watch for overhead obstructions and side clearances while transporting. o Always operate equipment in a manner that provides maximum visibility. Make allowances for increased length and weight of the equipment when making turns, stopping, etc. 8.4 Trailer Hauling 1. Be sure product bed/tank is empty. Do not transport with product in the bed or tank. 2. Load the chassis onto the trailer, place the transmission in neutral, and apply the parking brake. 3. Attach tie downs to the front and rear tie down loops. Make sure tie downs are rated for more than the weight of the load. Always cross-tie front and rear. 4. Remove the Slow-Moving Vehicle (SMV) emblem. Local authorities should be contacted regarding transporting an oversize load. Travel at a safe speed. Obey all traffic regulations. 5. Take special care when driving in early morning and evening. 6. All lighting, reflectors, and flags must be in place before transporting. 7. Use pilot cars front and/or rear as needed. When using pilot cars be always in radio contact with them. 9. Long-term Storage 9.1 Safety Store the unit in an area away from human activity. • Make sure the unit is stored in a dry and level area free of debris. Chock the wheels to prevent the unit from rolling. • Sutter Buttes Manufacturing Do not permit children to play on or around the stored unit at any time. If storing outside or in an area with rats, place rat traps around the vehicle. Rats can destroy a wiring harness in one winter. 52 9.2 Preparing For Storage The end of each operating season is a good time to replace and repair any components that are worn or not functioning properly. This will ensure that the unit will be ready to operate the next season and will save costly downtime. 1. Move the unit to a dry, level, indoor storage area, out of the weather. Touch up any paint scratches or nicks. 2. Run the engine and check for leaks of any kind. Repair any leaks found. Run the air conditioner for 3 minutes to lubricate the compressor seal. 3. Remove all dirt, fertilizers, chemicals, grease, fuel, DEF, and oil by washing thoroughly. Lubricate all grease points to remove trapped water. 4. Clean the radiator, condenser, and charge air cooler with water, compressed air, and a vacuum cleaner. Pressure wash the entire vehicle making sure the engine and transmission area are very clean. Don’t leave any grain, grass, or other agriculture product that would attract mice and rats. Lubricate all grease points to removed trapped water. 5. Clean the cab inside and out. Remove all food, wrappers, and trash from inside the cab. Close the cab door and lock it. Do NOT use gasoline for cleaning. Gasoline fumes can explode if they contact an ignition source. 6. Fill the diesel tank with diesel fuel to prevent condensation. 7. Clean the inside of the air cleaner and install new elements. 8. Change the engine oil and filter. Add 0.66 L (22 oz.) of corrosion inhibitor to the crankcase. Run the engine to circulate. AgTrk RS260 /300™ 53 9. Test the coolant with a refractometer. Test for additives with a test kit. Add antifreeze or replace coolant as necessary to prepare the cooling system for the temperatures expected. 10. Drain the water separator. 11. Fill the windshield washer reservoir with automotive, antifreeze rated, windshield washer fluid. Run washer until the antifreeze solution has filled the lines. Top off the washer reservoir. 12. Remove and clean the batteries. Store them in a cool dry place. Do not store them on concrete surfaces. Place them on wooden blocks and keep them charged with a trickle charger. 10. Component Identification & Reorder Information 10.1 Chassis Components Sutter Buttes Manufacturing Figure 10.1.1 Engine and Transmission Figure 10.1.2 Engine and Transmission 54 Figure 10.1.3 Engine Cooling and CAC Hoses AgTrk RS260 /300™ 55 Figure 10.1.4 Cooling Package Figure 10.1.6 Drivelines Sutter Buttes Manufacturing Figure 10.1.5 Transfer Case 56 Figure 10.1.7 Exhaust Assembly AgTrk RS260 /300™ Figure 10.1.8 Aftertreatment Shroud 57 Sutter Buttes Manufacturing Figure 10.1.9 Engine Air Intake Figure 10.1.10 Fuel Tank 58 Figure 10.1.11 Diesel Exhaust Fluid (DEF) Tank AgTrk RS260 /300™ 59 Figure 10.1.12 Battery Box 0 Figure 10.1.14 Hydraulic Tank Sutter Buttes Manufacturing Figure 10.1.13 Under-Cab Components 60 Figure 10.1.15 Pneumatic Tanks AgTrk RS260 /300™ 61 Figure 10.1.16 Cab HVAC Components Figure 10.1.18 Frame/Suspension Sutter Buttes Manufacturing Figure 10.1.17 Suspension Components 62 Figure 10.1.19 Platform AgTrk RS260 /300™ 63 Figure 10.1.20 Exterior Cab Components Figure 10.1.22 Exterior Cab Components Sutter Buttes Manufacturing Figure 10.1.21 Exterior Cab Components 64 Figure 10.1.23 Front Console/Steering Column AgTrk RS260 /300™ 65 Figure 10.1.24 Interior Cab Components See page 30 for detailed switch description. Sutter Buttes Manufacturing Figure 10.1.25 Control Console Figure 10.1.26 Cab Components - Headliner 66 Figure 10.1.27 Hood AgTrk RS260 /300™ 67 Figure 10.1.28 Toolbox 10.1 Chassis Components Drawing Key & Part List 10.1.1 Engine Item # A01 A02 A03 F03 A05 A06 A08 A09 A11 A12 A14 A15 A15 A15 A15 A17 A18 A19 A20 A21 A22 A23 A23 A24 A24 Description Diagram Engine, Complete (260HP) Engine, Complete (300HP) Starter Motor Lube Filter, Engine Motor Mount, Rear Isolator, Rear Motor Mount Fan Belt, Serpentine Cap, Engine Oil Fill Hand Throttle Assy. Mount, Hand Throttle Pedal, Foot Throttle Cap Screw, Motor Mount Nut, Motor Mount Washer, SAE Flat Washer, Isolator Rear Motor Mount Dipstick Tube, Engine Oil Dipstick, Engine Oil Belt Tensioner, Fan Crankshaft & Cam Position Sensor Tube, Charge Air Cooler Upper Tube, Charge Air Cooler Lower Hose, Charge Air Cooler Lower Clamp, CAC Lower Hose Hose, Charge Air Cooler Upper Clamp, CAC Upper Hose 10.1.1 10.1.1 10.1.2 10.1.2 10.1.2 10.1.2 10.1.1 10.1.1 10.1.25 10.1.25 10.1.23 10.1.2 10.1.2 10.1.2 10.1.2 10.1.1 10.1.1 10.1.2 10.1.1 10.1.3 10.1.3 10.1.3 10.1.3 10.1.3 10.1.3 SBM P/N 100612 100531 100876 100879 100416 100335 100880 101593 100438 101411 100476 ¾ x 4 USS gr5 ¾ USS gr5 ¾ 101412 101594 101596 101597 101598 101413 101414 101708 101681 100261 101681 10.1.2 Transmission B01 B02 B03 B04 B05 B06 Description Transmission, Complete Isolator, Transmission Mount Washer, Transmission Isolator Crossmember, Transmission Transmission Shift Selector Power Take-off 10.1.3 Transfer Case Item # C01 C02 Description Transfer Case Mount, Transfer Case Diagram Sutter Buttes Manufacturing Item # 10.1.1 10.1.2 10.1.2 10.1.2 10.1.25 10.1.2 Diagram 10.1.5 10.1.5 SBM P/N 100515 100334 101415 101416 101709 101079 SBM P/N 100622 100335 68 C03 C04 C05 C06 C07 Cradle, Transfer Case LH Cradle, Transfer Case RH Isolator, Transfer Case Lower Washer, Transfer Case Isolator Isolator, Transfer Case Upper 10.1.5 10.1.5 10.1.5 10.1.5 10.1.5 101417 101418 100335 101412 101678 10.1.4 Drivelines Item # D01 D02 D03 D05 D06 D07 Description Driveline Assy, Transfer Case to Rear Axle Driveline Assy, Transfer Case to Front axle Driveline Assy, Transmission to Transfer Case U-Joint, Driveline Front Axle Assy. Rear Axle Assy. Diagram 10.1.6 10.1.6 10.1.6 10.1.6 10.1.6 10.1.6 SBM P/N 100501 100502 100499 101044 101211 101169 10.1.5 Intake & Exhaust System Item # AgTrk RS260 /300™ 69 E01 E02 E03 E04 E05 E06 E07 E08 E09 E10 E11 E12 E13 E14 E15 E16 E17 E18 E19 E20 E21 E22 E23 E25 E26 Description Aftertreatment Assembly (260HP) Aftertreatment Assembly (300HP) Aftertreatment Shroud Cover Plate, Aftertreatment Shroud Cradle Mount, Aftertreatment Assy. (260HP) Cradle Mount, Aftertreatment Assy. (300HP) Strap, Aftertreatment Assy. (260HP) Strap, Aftertreatment Assy. (300HP) Exhaust Stack (260HP) Exhaust Stack (300HP) Bracket, Exhaust Stack Rubber Mount, Exhaust Stack Clamp, Exhaust 4” (260HP) Clamp, Exhaust 5” (300HP) Hanger Clip, Exhaust Exhaust Pipe (260HP) Exhaust Pipe (300HP) Air Cleaner Housing Mount, Air Cleaner Air Intake Guard Air Intake Tube Temperature Sensor, Air Intake Air Filter Restriction Indicator Air Filter Exit Elbow – 6”x 5” 90° Rubber Turbo Intake Elbow – 5” x 4” 90° Rubber Diagram 10.1.7 10.1.7 10.1.8 10.1.8 10.1.8 10.1.8 10.1.8 10.1.8 10.1.7 10.1.7 10.1.7 10.1.7 10.1.7 10.1.7 10.1.7 10.1.7 10.1.7 10.1.9 10.1.9 10.1.9 10.1.9 10.1.9 10.1.9 10.1.9 10.1.9 SBM P/N 101710 101711 101419 101420 101421 100459 101422 101599 101714 100361 101423 101243 101715 100361 101424 101425 101425 100494 101426 101427 101428 101716 100402 100417 100379 E27 E28 E29 E30 E31 E32 E33 E35 E36 E37 Clamp, V-Band 3-1/2” (260HP) Clamp, V-Band 4-1/2” (300HP) Hose Clamp, SS Tee 5-1/4” Hose Clamp, SS Tee 6-1/4” Exhaust Band Clamp, 4” (260HP) Exhaust Band Clamp 5” (300HP) 3” Clamp on Exhaust Hanger Back Panel, Aftertreatment Primary Air Filter, Engine Secondary Air Filter, Engine 10.1.7 10.1.7 10.1.9 10.1.9 10.1.7 10.1.7 10.1.7 10.1.8 10.1.9 10.1.9 100995 101193 100275 101188 100283 100293 101717 101429 100047 100048 10.1.6 Fuel & DEF System Item # F01 F02 A04 F04 F05 F06 F10 F11 F11 F12 F13 F14 Description Diagram Fuel Tank Pickup Assembly, Fuel Tank Fuel Filter Fuel/Water Separator, Engine Fuel Sending Unit Cap, Fuel Tank DEF Pump DEF Tank Cap, DEF Tank Top Strap, DEF Tank Mount Front Strap, DEF Tank Mount Mount, DEF Tank 10.1.10 10.1.10 10.1.1 10.1.19 10.1.10 10.1.10 10.1.11 10.1.11 10.1.11 10.1.11 10.1.11 10.1.11 SBM P/N 101431 101432 100050 100050 101036 100369 101712 101048 101713 101433 101434 101435 10.1.7 Cooling System Description Cooling Tower, Complete Radiator Cap Side Mount, Cooling Tower LH Side Mount, Cooling Tower RH Isolator, Cooling Tower Left Rear Brace, Cooling Tower Right Rear Brace, Cooling Tower Crossmember, Cooling Tower/Front Motor Mount Hood Sealing Plate, Sides Hood Sealing Plate, Top Top Mount, Hood Limit Strap Hood Seal, Top Hood Seal, Sides Mounting Bracket, Hood Seal Isolator, Cooling Tower Side Clamp, Cooling Tower Side Isolator Radiator Hose, Upper Clamp, Upper Radiator Hose Radiator Hose, Lower Diagram Sutter Buttes Manufacturing Item # G01 G02 G03 G04 G05 G06 G07 G08 G09 G10 G11 G12 G13 G14 G15 G16 G17 G17 G18 10.1.3 10.1.3 10.1.4 10.1.4 10.1.4 10.1.4 10.1.4 10.1.4 10.1.4 10.1.4 10.1.4 10.1.4 10.1.4 10.1.4 10.1.4 10.1.4 10.1.3 10.1.3 10.1.3 SBM P/N 101718 101682 101437 101438 101719 101439 101440 101441 101442 101443 101444 100392 100312 101445 101446 101447 100385 101720 100631 70 G18 G19 G19 G20 Clamp Lower Radiator Hose Thermostat Thermostat Seal Water Pump Kit (includes seal) 10.1.3 Not Pictured Not Pictured 10.1.2 101720 101721 101722 101723 10.1.8 Electrical System Item # AgTrk RS260 /300™ H01 H02 H03 H04 H05 H06 H07 H08 H09 H10 H11 H12 H13 H14 H15 H16 H17 H18 H19 H20 H21 H22 H23 H24 H25 H26 H27 H28 H29 H30 H31 H32 H33 H35 NP Description Alternator Battery, 12V Battery Box Latch, Battery Box Battery Box Cover Fuse Box, Cummins Busbar Solenoid, Starter & Air Heater Battery Hold Down J-Bolt, Battery Hold Down w/ Wing Nut In Line Fuse, Alternator (250A) Battery Disconnect Switch, 500A Connecting Strap, Disconnect Switch Bulkhead Panel, Cab Exterior Bulkhead Panel, Cab Interior Mount Panel, Fuse/Relay J1 & J2 Radio Speaker, Radio Dome Light Switch Switch Blank Monitor, Engine Power Connector, Pillar Power Connector Cap Power Port, Console USB Port Backup Alarm Headlight Taillight Grommet, Taillight Front Work Light Bracket, Front Work Light Rear Work Light Power Port, Back Panel Rearview Camera 10.1.2 10.1.12 10.1.12 10.1.12 10.1.12 10.1.12 10.1.12 10.1.12 10.1.12 10.1.12 10.1.12 10.1.12 10.1.12 10.1.21 10.1.24 10.1.24 10.1.26 10.1.26 10.1.26 10.1.25 10.1.26 10.1.23 10.1.24 10.1.24 10.1.25 10.1.25 10.1.15 10.1.18 10.1.18 10.1.18 10.1.20 10.1.20 10.1.21 10.1.24 Not Pictured SBM P/N 101600 100451 101449 100291 101450 101724 100444 100405 100451 101201 100330 100440 101452 101453 101454 101455 101683 101684 101685 101725 100862 101726 101727 101727 100057 101114 100391 100875 100384 100252 101686 101687 101688 101689 101357 10.1.9 Hydraulic & Steering System Item # J01 J02 71 Diagram Description Hydraulic Pump Hydraulic Oil Cooler Diagram 10.1.2 10.1.13 SBM P/N 100513 100817 J03 J04 J05 J06 J07 J08 J09 J11 J12 J13 J14 J16 J17 J18 J28 J28 J29 J30 J31 J32 J33 Hydraulic Reservoir Filler Cap, Hydraulic Reservoir Filter, Hydraulic Hydraulic Reservoir Sight Gauge Hydraulic Valve Stack Mount, Hydraulic Valve Nipple 1 ¼” x 11 ½ Sch 40 Hydraulic Tube Support Bracket Temperature Sender, Hydraulic Steer Orbital Valve Steer Controller Mount, Steer Controller Steer Cylinder, without Position Sensor Steer Cylinder with Position Sensor Strap, Hydraulic Reservoir Cushion, Hydraulic Reservoir Strap Mount, Hydraulic Cooler Front Mount, Hydraulic Cooler Rear Tube Clamp, Hydraulic – 2 Lines Valve, Rear Steer Valve, Steer Mode 10.1.14 10.1.14 10.1.14 10.1.14 10.1.13 10.1.13 10.1.14 10.1.14 10.1.14 10.1.22 10.1.22 10.1.22 10.1.17 10.1.17 10.1.14 10.1.14 10.1.13 10.1.13 10.1.13 10.1.13 10.1.13 101456 100374 100469 100380 100520 101457 101149 101458 101729 100500 100043 101459 101266 101265 101436 101436 101462 101463 100256 100474 100471 10.1.10 Pneumatic and Braking System Description Air Compressor Tank, Compressed Air Air Governor Air Cylinder, Platform Step Rear Mount, Rear Air Tank Rear Mount, Front Air Tank Front Mount, Front Air Tank Front Mount, Rear Air Tank Brake Valve Treadle, Brake Valve Air Valve Manifold Assy, 3 Sections Mounting Plate, Air Valve Manifold Solenoid, Air Valve Muffler, Air Valve Quick Release Valve, Air Brake Air Brake Chamber, Dual Front axle Air Brake Chamber, Single Rear Axle 10.1.11 HVAC System Item # M01 M02 M03 Description Pressurizer Filter Knob, Pressurizer Filter Pressurizer Motor Assembly Diagram Sutter Buttes Manufacturing Item # K01 K02 K03 K04 K05 K06 K07 K08 K09 K10 K11 K12 K13 K14 K15 K16 K17 10.1.1 10.1.15 10.1.1 10.1.19 10.1.15 10.1.15 10.1.15 10.1.15 10.1.22 10.1.23 10.1.21 10.1.21 10.1.21 10.1.21 10.1.17 10.1.17 10.1.17 Diagram 10.1.16 10.1.21 10.1.16 SBM P/N 101728 100432 100371 100448 101464 101465 101466 101467 100428 100472 101087 101468 100460 100273 100314 100414 100366 SBM P/N 100055 101655 101656 72 M04 M05 M06 M07 M08 M09 M10 M11 M12 M13 M14 M15 M16 M17 M18 M19 M20 M21 Cabin Air Filter Cover, Cabin Air Filter Knob, Cabin Air Filter HVAC Control Panel HVAC Blower Motor AC Evaporator Heater Core AC Receiver Dryer HVAC Temperature Sensor Orifice Tube AC Clutch Switch AC Condenser AC Compressor Heater Bypass Valve Mount, Heater Bypass Valve Front Console HVAC Manifold Louver, HVAC (rectangular) Louver, HVAC (round) 10.1.24 10.1.24 10.1.24 10.1.26 10.1.16 10.1.16 10.1.16 Not Pictured 10.1.16 10.1.16 Not Pictured Not Pictured 10.1.2 10.1.13 10.1.13 10.1.23 10.1.23 10.1.23 100054 100688 101657 101658 101659 101660 101661 101662 101663 101664 101665 101666 101667 101668 101489 101670 101669 101671 10.1.13 Suspension Item # N05 N08 N09 N10 N11 N12 N13 N14 N14 N15 N16 N17 N18 Description Tie Rod Assembly Leaf Spring Assy, Front Axle Leaf Spring Assy, Rear Axle Shackle Mount, Rear Axle Spring Hanger, Rear Axle LH Spring Hanger, Rear Axle RH Shackle Shackle Bolt Shackle Nut Plate, Rear Axle Spring Hanger U-Bolt, Spring to Axle Nut, U-Bolt Top plate, Leaf Spring Diagram 10.1.17 10.1.17 10.1.17 10.1.18 10.1.18 10.1.18 10.1.18 10.1.18 10.1.18 10.1.18 10.1.17 10.1.17 10.1.17 SBM P/N 101730 100505 100511 101469 101470 101471 101472 100427 100427 101473 100395 100257 101474 10.1.14 Frame & Platform AgTrk RS260 /300™ 73 Item # P03 P04 P11 P12 P13 P14 P15 P16 P17 P18 Description Front Bumper Rear Bumper Handrail, Stairs to Platform Upper Stair Brace, Upper Stair Lower Stair Rear Cam Arm, Stair Front Cam Arm, Stair Shield, Below Cab LH Shield, Below Cab RH Diagram 10.1.18 10.1.18 10.1.19 10.1.19 10.1.19 10.1.19 10.1.19 10.1.19 10.1.13 10.1.13 SBM P/N 101481 101482 101488 101490 101491 101492 101493 101494 101495 101496 P19 P20 P21 P22 P23 P24 P25 P26 P27 Door Stop Gas Spring, Below Cab Door Latch, Below Cab Door Washer, Cab Riser Isolator Isolator, Cab Riser Hinge, Below Cab Door Bracket, Hood Rest LH Bracket, Hood Rest RH Hood Isolator Rest 10.1.19 10.1.13 10.1.13 10.1.19 10.1.19 10.1.13 10.1.19 10.1.19 10.1.19 101731 101732 101733 101412 100335 101734 101498 101499 101500 10.1.15 Cab Q01 Q02 Q03 Q04 Q05 Q06 Q07 Q08 Q09 Q10 Q11 Q12 Q13 Q14 Q15 Q16 Q17 Q18 Q19 Q25 Q26 Q27 Q28 Q29 Q30 Q31 Q32 Q34 Q35 Q36 Q37 Q38 Q39 Q40 Q41 Description Cab Windshield Rear Glass Right Glass Door Glass Door Hinge Assy, Upper Door Hinge Assy, Lower Latch Assembly, Cab door Cover, Cab Door Latch Assy. Seal, Cab Door Seal, Cab Door Side Windshield Wiper Blade Windshield Wiper Arm Windshield Wiper Motor Windshield Wiper Reservoir Cover, Cab Rear LH Cover, Cab Rear RH Knob, Cab Rear Cover Mirror Assy. Mounting Bracket, GPS Mounting Plate, GPS Antenna Seat Assembly Buddy Seat Assembly Storage Panel with Cupholder Emergency Hammer Right-Hand Console Assy. Right-Hand Console Cover Switch Panel 1, RH Console Console Switch Panel 2 Console Switch Panel 3 Console Switch Panel 4 Cup Holder LH Panel Cover RH Panel Cover Sunshade Diagram Sutter Buttes Manufacturing Item # 10.1.20 10.1.20 10.1.21 10.1.21 10.1.20 10.1.20 10.1.20 10.1.20 10.1.20 10.1.20 10.1.20 10.1.20 10.1.20 10.1.20 10.1.21 10.1.21 10.1.21 10.1.21 10.1.21 10.1.21 10.1.21 10.1.24 10.1.24 10.1.24 10.1.24 10.1.24 10.1.25 10.1.25 10.1.25 10.1.25 10.1.25 10.1.25 10.1.26 10.1.26 10.1.26 SBM P/N 100529 100884 101601 101602 100886 101603 101604 101605 101606 101607 101608 101035 101034 101033 101609 101610 101611 101612 101613 101737 101503 101614 101615 101616 101617 101504 101618 101505 101506 101507 101508 100222 101509 101619 101620 74 Q42 Q43 Q44 Q45 Q47 Floormat Handhold LH Handhold RH Horn, Electric Striker Assembly, Cab Door 10.1.23 10.1.24 10.1.24 10.1.22 10.1.20 101621 101622 101623 101624 101625 10.1.16 Hood Item # R01 R02 R03 R04 R05 R06 R07 R08 R09 Description Hood Hood Grill Handle, Hood Tilt Hinge, Hood Grill Latch, Hood Grill Hood Isolator Hinge, Hood LH Hinge, Hood RH Bushing, Hood Hinge Diagram 10.1.27 10.1.27 10.1.27 10.1.27 10.1.27 10.1.27 10.1.27 10.1.27 10.1.27 SBM P/N 100634 101361 100290 100288 100401 100375 101362 101363 100277 10.1.17 Accessories Item # T01 T02 T03 T04 T05 T06 T07 AgTrk RS260 /300™ 75 Description Toolbox Toolbox Lid Latch, Toolbox Hinge, Toolbox Ram Mount® Flange-Mount Ball Ram Mount® Double-Socket Arm Console Base Plate Diagram 10.1.28 10.1.28 10.1.28 10.1.28 10.1.23 10.1.23 10.1.23 SBM P/N 101364 101365 101735 101736 101360 101147 101366 10.2 Grain Bin Components Sutter Buttes Manufacturing Figure 10.2.1 Grain Bin Figure 10.2.2 Bin Auger 76 Figure 10.2.3 Lower Auger AgTrk RS260 /300™ Figure 10.2.4 Upper Auger 77 10.2.1 Grain Bin Item # A01 A02 A03 A04 A05 A05 A06 A07 A08 NP A10 A11 A12 A13 Description Diagram Grain Bin Crossmember, Bin Diverter Valve Mounting Bracket, Diverter Valve Isolator, Bin Mount Lower Isolator, Bin Mount Upper Washer, Bin Mount Isolator Clamp, 1” Hydraulic Tube - Dual Clamp, 3/8” Hydraulic Tube - Dual Clamp, 3/8” Hydraulic Tube - Single Hydraulic Tube Assy, 3/8” Hydraulic Tube Assy, 3/8” Hydraulic Tube Assy, 1” Work Light 10.2.1 10.2.1 10.2.1 10.2.1 10.2.1 10.2.1 10.2.1 10.2.1 10.2.1 Not Pictured 10.2.1 10.2.1 10.2.1 10.2.1 SBM P/N 101367 101368 101738 101369 100335 101680 101370 101739 100299 100299 101371 101372 101373 100247 10.2.2 Bin Auger Item # Description 10.2.3 Lower Auger Item # C01 C02 C03 C04 C05 C06 C07 C08 C09 Diagram Bin Floor Auger Cover, Bin Floor Auger Position Rod, Bin Floor Auger Cover Bearing Cover Bearing, Bin Floor Auger Hydraulic Motor, Bin Floor Auger Motor Mount 1, Floor Auger Motor Mount 2, Floor Auger Shaft Coupler End Plate, Bin Floor Auger Alignment Plate, Bin Floor Auger Cylinder, Floor Cover Guard, Floor Cover Cylinder Mount, Floor Cover Cylinder Description Load Auger, Lower Housing, Lower Load Auger Upper Support, Lower Load Auger Top Access Panel, Lower Load Auger Bottom Access Panel, Lower Load Auger Seal, Load Auger Housing Upper Bearing Mount, Lower Load Auger Upper Bearing, Lower Load Auger Drive Collar, Lower Load Auger 10.2.2 10.2.2 10.2.2 10.2.2 10.2.2 10.2.2 10.2.2 10.2.2 10.2.2 10.2.2 10.2.2 10.2.2 10.2.2 10.2.2 Sutter Buttes Manufacturing B01 B02 B03 B04 B05 B06 B07 B08 B09 B10 B11 B12 B13 B14 Diagram 10.2.3 10.2.3 10.2.3 10.2.3 10.2.3 10.2.3 10.2.3 10.2.3 10.2.3 SBM P/N 101374 101375 101376 101377 101740 101741 101378 101379 100475 101380 101381 101742 101382 101383 SBM P/N 101384 101385 101386 101387 101388 100559 100610 100539 100535 78 C10 C11 C12 C13 C14 C15 Locator Pin Lower Bearing, Lower Load Auger Motor Mount 1, Load Auger Motor Mount 2, Load Auger Shaft Coupler Hydraulic Motor, Load Auger 10.2.3 10.2.3 10.2.3 10.2.3 10.2.3 10.2.3 100403 100042 101378 101379 100475 100562 Diagram SBM P/N 10.2.4 Upper Auger Item # D01 D02 D03 D04 D05 D06 D07 D08 AgTrk RS260 /300™ 79 Description Load Auger, Upper Housing, Upper Load Auger Fold Cylinder, Load Auger Fold Pin, Load Auger Locator Socket Mount, Top Bearing Auger End Plate Bearing, 10.2.4 10.2.4 10.2.4 10.2.4 10.2.4 10.2.4 10.2.4 10.2.4 101389 101390 100300 101391 100368 101392 101393 100544 10.3 Sprayer Components Sutter Buttes Manufacturing Figure 10.3.1 Sprayer Components Figure 10.3.2 Tank Components 80 Figure 10.3.3 Pump Components AgTrk RS260 /300™ Figure 10.3.4 Four-Link Boom Mount 81 V-Wheels Item # A01 A02 Description Diagram V-Wheel Wear Plate, V-Wheel 10.3.1 10.3.1 SBM P/N 101672 101673 Spray Tank Skid Item # B01 B02 B03 B04 B05 B06 B07 Description Diagram Tank Skid, 500 Gallon Tank Skid, 750 Gallon Tank Strap, 500 Gallon Tank Strap, 750 Gallon Lower Isolator, Skid Mount Washer, Skid Mount Handle, Tank Drain 10.3.2 10.3.2 10.3.2 10.3.2 10.3.1 10.3.1 10.3.3 SBM P/N 101674 101676 101675 101677 100335 101680 101693 Spray Boom 4-Link Item # C01 C02 C03 C04 C05 C06 C07 C08 C09 Description Diagram Boom Frame Chassis Mount 4-Link Frame Mount Upper 4-Link Frame Lower 4-Link Frame Bushing, ½ x 3-1/4 Bushing, ½ x ¾ Cylinder, 4-Link Lift Lock. 4-Link Cylinder Clevis Pin, 4-Link Lock 10.3.4 10.3.4 10.3.4 10.3.4 10.3.4 10.3.4 10.3.4 10.3.4 10.3.4 SBM P/N 101394 101395 101396 101397 101694 101695 101568 101398 101696 10.3.4 Fluid Routing D01 D02 D03 D04 D05 D06 D07 D08 D09 D10 D11 D12 D13 D14 D15 Description Tank, 500 Gallon Tank, 750 Gallon Bracket, Front Fill Support, Front Fill At Air Cleaner Support, Front Fill To Frame Manifold Valve Mount Front Fill Hose & Clamps Tank-To-Pump Hose & Clamps Pump-To-Manifold Hose & Clamps Manifold-To-Tank Hose & Clamps Manifold-To-Sprayer Hose & Clamps Pump Vent Hose & Clamps U-Bolt, 2-1/2” U-Bolt, 4” Sprayer Pump Diagram Sutter Buttes Manufacturing Item # 10.3.2 10.3.2 10.3.1 10.3.1 10.3.1 10.3.3 10.3.1 10.3.3 10.3.3 10.3.3 10.3.3 10.3.3 10.3.3 10.3.1 10.3.3 SBM P/N 100037 100007 101399 101400 101401 101402 101403 101404 101405 101406 101407 101408 101691 101692 100028 82 D16 D17 D18 D19 D20 D21 NP D23 D24 D25 D26 D27 D28 D29 D30 D31 D32 D33 D34 D35 D36 D37 D38 D39 D40 D41 D42 D43 D44 D45 AgTrk RS260 /300™ 83 Nipple, 1/8 x 2 Adapter, ¼ FPT x 1/8 FPT Adapter, ¼ MPT x ¼ Hose Barb - 90 ° Bulkhead, ¼” FPT, Plastic Valve, 2” Clamp, 2” Valve, 3” Stubby Valve, 3” Male Adapter x 3” Manifold Flange Valve, 2” 3-Way Manifold Drain, 2” Standard Port Elbow, 2” x 2” Flange 90 ° Strainer, 50 Mesh Elbow, 2” Flange x 2” Hose Barb 45° Bulkhead, 2 X 2 FPT Bushing, 2 MPT X ¾ FPT Adapter, 3” Flange x 3” Hose Barb Bulkhead, 3 X 3 FPT Clamp, 3” Flange Adapter, 2” Flange X 2” Hose Barb 90° Adapter, 2” Flange X 2” Hose Barb Adapter, 2” Flange X 2” Hose Barb 45° Valve, 2” Adapter, 2 x 2 Flange, 90 Degree Drain, 2” Full Port Tank Agitator Nozzle 1/8” Nozzle Body Pressure Gauge Clamp, 2” Flange Adapter, 2” Flange X 2” Hose Barb Cap, 3” Cam Lever 10.3.3 10.3.3 10.3.3 10.3.3 10.3.2 10.3.2 Not Pictured 10.3.1 10.3.3 10.3.2 10.3.2 10.3.3 10.3.3 10.3.2 10.3.2 10.3.1 10.3.2 10.3.2 10.3.3 10.3.3 10.3.2 10.3.2 10.3.2 10.3.2 10.3.2 10.3.3 10.3.3 10.3.2 10.3.3 10.3.1 101628 101629 101630 101631 101632 101633 101634 101635 101636 101637 101638 101639 101640 101641 101642 101643 101644 101645 101646 101647 101648 101632 100014 101649 101650 101651 101652 101653 101654 100013 10.4 Stomper Components Figure 10.4.2 Stomper Trailer Sutter Buttes Manufacturing Figure 10.4.1 Stomper, Complete 84 Figure 10.4.3 Tow Hitch Assembly Stomper Wheels Item # A01 A02 Description Stomper Wheel, Left Stomper Wheel, Right Diagram 10.4.1 10.4.1 SBM P/N 101358 101359 Stomper Trailer Item # AgTrk RS260 /300™ 85 B01 B02 B03 B04 B05 B06 B07 B08 B09 B10 B11 Description Trailer Frame Stomper Wheel Hub Bearing, Stomper Hub Transport Tire, 380/85 R24 Wheel, Transport Tire Wheel Adapter, Transport Tire Hub, Transport Tire Hydraulic Line Support Trailer Jack Hitch Receiver SBM P/N 10.4.2 10.4.2 10.4.2 10.4.2 10.4.2 10.4.2 10.4.2 10.4.2 10.4.2 10.4.2 10.4.2 101344 101345 101346 101313 100576 101348 101347 100576 101349 100601 100573 Stomper Trailer Tow Hitch Item # NP C02 C03 C04 C05 C06 C07 C08 C09 Description SBM P/N Tow Hitch Assy. Tow Bumper Tow Hitch Upper Clevis, Tow Hitch Tow Brace, Upper Left Tow Brace, Lower Left Tow Brace, Upper Right Town Brace, Lower Right Hitch Pin Not Pictured 10.4.3 10.4.3 10.4.3 10.4.3 10.4.3 10.4.3 10.4.3 10.4.3 101356 101350 101351 101707 101352 101353 101354 101355 100604 10.4.3 Stomper Trailer Hydraulics D01 D02 D03 NP D05 D06 NP NP NP NP NP NP NP Description SBM P/N Cylinder, Transport Wheel Raise - Lower Lock, Transport Wheel Cylinder Clevis Pin, Lock Clamp, Dual Line Cross Port Muffler Hose, Cross Port to Cylinder Hose, Cylinder to Cross Port Hose, Supply to Cross Port Hose, Cross Port to Return Hose, Chassis to Supply Hose, Return to Chassis Cross Port to Sun Valve 10.4.2 10.4.2 10.4.2 Not Pictured 10.4.2 10.4.2 Not Pictured Not Pictured Not Pictured Not Pictured Not Pictured Not Pictured Not Pictured 100590 101697 101698 101699 101700 101701 101702 101703 101704 101704 101705 101705 101706 Sutter Buttes Manufacturing Item # 86 11. Warranty Please note the serial and model number of your vehicle and write the information down in the space provided. This information is critical for us to provide you with the best service throughout the life of your product. Model Number: _______________ Serial Number: _______________ Dealer: _____________________ Sutter Buttes Manufacturing warrants all products manufactured and sold by it against defects in material. This warranty being expressly limited to replacement at the factory of such parts or products as will appear to be defective after inspection. This warranty does not obligate the company to bear cost of labor in replacement of parts. It is the policy of the company to make improvements without incurring obligations to add them to any unit already sold. No warranty is made or authorized to be made, other than herein set forth. This warranty is in effect for one year after purchase. It is the responsibility of the user to read the operator's manual and comply with the safe and correct operating procedure and to lubricate and maintain the product according to the maintenance schedule in the operator's manual. The user is responsible for inspecting his machine and for having parts repaired or replaced when continued use of the product would cause damage or excessive wear on other parts. It is the user's responsibility to deliver his machine to an authorized dealer for service or replacement of defective parts that are covered by the warranty. AgTrk RS260 /300™ 87
advertisement