advertisement
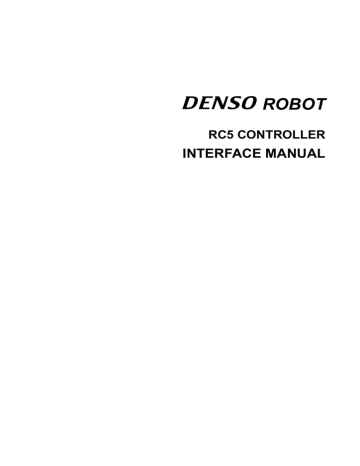
6.2 Robot Controller I/O Circuits (PNP type)
6.2.1 User-Input, System-Input and Hand-Input Circuits (PNP type)
The following two pages show examples of the user-input, system-input and hand-input circuit configurations and connections of the robot controller.
The maximum allowable capacity of the robot controller's internal power source is 1.3
A. Use the internal power source within this allowable range.
Caution Either an external power supply type or built-in power type Output card is available for the PLC. However, an external power supply type requires an additional power source (24V) to be installed. The power capacity is 15W or more.
When controlling two or more robots with a single PLC using the internal power source of the robot controller, set a PLC Output card for each robot.
Other than a PLC, a proximity switch, or a relay contact may be connected directly to the input terminal of the Robot Controller. In such a case, use the power input to pins 6 to 9 of the I/O power connector. A two-wire photoelectric switch or proximity switch can be connected if its leakage current is 1 mA or less.
Use a multi-core shielding cable for the purpose of protecting the robot controller from noise. Ground it to the robot controller.
144
(When the internal power source is used)
(When an external power source is used)
User-Input and System-Input Circuits (PNP type)
145
(When the internal power source is used)
(When an external power source is used)
Hand-Input Circuits (PNP type)
146
6.2.2 Robot Stop and Enable Auto Input Circuits
The Robot Stop and Enable Auto signals are important for safety. The input circuit for these signals must have contacts as shown below.
Use the INPUT CN8 (pins 1 and 3) of the robot controller for the power source, irrespective of whether the power source to be used for other I/O signals is the internal power source or an external power source.
(Note: For the “Dual emergency stop type”, refer to Subsection 6.2.4.2.)
Robot Stop and Enable Auto Input Circuits
TIP: The configuration sample of an emergency stop output circuitry is shown in
Subsection 6.2.4 "Emergency Stop Circuit."
147
6.2.3 User-Output, System-Output, and Hand-Output Circuits (PNP type)
The following two pages show an example of the configuration and connection of the
Robot Controller's user-input output, system-output and hand-output circuit.
Since the initial resistance of a lamp is small, the output circuit may be damaged by rush current that flows when the lamp lights.
When directly turning a lamp ON or OFF, use a lamp whose rating is 0.5W or less.
To reduce rush current, connect a resistor R that allows dark current 1/3 or less of the rated current to flow when the lamp goes OFF.
An example of connecting a lamp is shown on page 140.
(1) The User-Output, System-Output and Hand-Output Circuit are open collector output circuits.
(2) The maximum allowable sink current is 70 mA.
Keep the current consumption of a device to be connected to the Robot
Controller, such as a PLC and a relay coil, below the allowable current.
(3) Select an induction load, such as a relay coil, which has a built-in diode (for absorbing inverse electromotive force).
To use an induction load without a built-in diode, add a diode equivalent to the 1S1888 (Toshiba) in close vicinity to the coil.
Caution: When externally attaching a diode, connect it with correct polarity. Incorrect polarity may damage the Output circuit.
(4) Connecting a lamp requires a circuit through which dark current flows.
Caution: Since the initial resistance of a lamp is small, the output circuit may be damaged by rush current that flows when the lamp lights.
Refer to page 140.
(5) When using the internal power source, prepare a PLC input circuit unit that does not contain a power source.
Caution: Keep the total current capacity of the internal power source below 1.3A.
(6) Use a multi-core shielding cable for the purpose of protecting the devices from external noise. Ground it to the robot controller.
(7) 24V internal power source of the robot controller must not be grounded.
Caution: If the output terminal +24V of internal power source is grounded, there may be a case where the controller is damaged.
148
(When the internal power source is used)
(When an external power source is used)
User-Output and System-Output Circuits (PNP type)
149
(When the internal power source is used)
(When an external power source is used)
Hand-Output Circuits (PNP type)
150
Supplied from the II/O power connector when the internal power source is used
Lamp
Transistor array
Controller
Example of Circuit with Lamp (PNP type)
151
6.2.4 Emergency Stop Circuit
The following figures show the examples of configuration and connection of emergency stop circuit for the robot controller.
The red mushroom-shaped switch provided on the robot controller front panel, on the teach pendant, or on the operating panel can be used as a switch for stopping the equipment in case of emergency.
6.2.4.1 Standard type
Robot controller
Internal 24V
F1
Fuse (1.3A)
CN7
Internal 0V
F9
Fuse (0.3A)
Fuse (1.3A)
F2
Emergency
Stop +
CN10
Emergency
Stop +
Internal
24V F8
Fuse (1.3A)
Output
CN8
Emergency stop switch on the front panel of the controller
Input
Emergency stop circuit
(prepared by customers)
Robot stop switch circuit
(prepared by customers)
CN5
Teach pendant
Emergency stop switch on teach pendant
Internal 0V
(When the internal power source is used)
Robot controller
F9
Fuse (0.3A)
Emergency
Stop +
CN10
Emergency stop circuit
(prepared by customers)
External 24V
Emergency
Stop -
Internal
24V F8
Fuse (1.3A)
Output
CN8
External 0V
Robot stop switch circuit
(prepared by customers)
Emergency stop switch on the front panel of the controller
Input
CN5
Teach pendant
Emergency stop switch on teach pendant
Internal 0V
(When an external power source is used)
Emergency Stop Circuit (Standard type)
152
6.2.4.2 Dual emergency stop type
Emergency Stop Circuit (“Dual emergency stop type”)
153
6.2.5 I/O Power Connector (PNP type)
For the power source to communicate signals between the robot controller and the external device, the internal power source of the robot controller or an external power source is used.
The figure below shows an example of connecting I/O power connectors when the internal power source is used, and the figure on the next page shows an example of connecting I/O power connectors when an external power source is used.
I/O Power Connection Sample (When the internal power source is used) (PNP type)
Caution: To use the internal power source of the robot controller, connect the wiring so that the internal power source will be separate from the external power source. Improper wiring may damage the internal circuit.
The +24V internal power source of the robot controller must not be grounded.
154
I/O Power Connection Sample (When an external power source is used) (PNP type)
Caution: Use a cable of 0.5 mm controller.
2 or more in size for the wiring between the external power source and the I/O power input connectors of the robot
155
advertisement
* Your assessment is very important for improving the workof artificial intelligence, which forms the content of this project
Related manuals
advertisement
Table of contents
- 3 Preface
- 4 How the documentation set is organized
- 5 How this book is organized
- 7 SAFETY PRECAUTIONS
- 17 Contents
- 21 Chapter 1 General Information about RC5 Controller
- 21 1.1 Controller Model Name on Nameplate
- 24 1.2 Names of the Robot Controller Components
- 27 1.3 Robot Controller Specifications
- 31 1.4 Controller System Configuration
- 31 1.4.1 Internal Circuits of the Controller (Typical configuration)
- 32 1.4.2 Typical Robot System Configurations
- 34 Chapter 2 General Information about the Interface
- 34 2.1 Standard Mode and Compatible Mode
- 34 2.2 Switching between Modes
- 42 2.3 Types and General Information about I/O Signals
- 42 2.3.1 Standard Mode
- 43 2.3.2 Compatible Mode
- 44 2.4 Using User I/O Signals (common to both modes)
- 44 2.4.1 I/O Type Variable Declaration
- 44 2.4.2 I/O Type Global Variables
- 44 2.4.3 I/O Type Local Variables
- 44 2.4.4 User Input Commands
- 45 2.4.5 User Output Commands
- 45 2.4.6 Note When Using Input Signals
- 46 Chapter 3 System I/O Signals Standard Mode
- 46 3.1 Types and Functions of System Output Signals (Standard Mode)
- 47 3.2 Usage of System Output Signals (Standard Mode)
- 47 3.2.1 Robot Initialization Complete (Output)
- 48 3.2.2 Auto Mode (Output)
- 49 3.2.3 External Mode (Output)
- 50 3.2.4 Servo ON (Output)
- 51 3.2.5 Robot-in-operation (Output)
- 52 3.2.6 Normal CPU (Output)
- 53 3.2.7 Robot Failure (Output)
- 54 3.2.8 Robot Warning (Output)
- 55 3.2.9 Dead Battery Warning (Output)
- 56 3.2.10 Continue Start Permitted (Output)
- 56 3.2.11 SS mode (Output)
- 57 3.2.12 Emergency Stop (Output from a contact)
- 58 3.3 Types and Functions of System Input Signals (Standard Mode)
- 59 3.4 Usage of System Input Signals (Standard Mode)
- 59 3.4.1 Enable Auto (Input)
- 60 3.4.2 Robot Stop (Input)
- 61 3.4.3 Step Stop (All Tasks) (Input)
- 62 3.4.4 Instantaneous Stop (All Tasks) (Input)
- 63 3.4.5 Interrupt Skip (Input)
- 65 3.5 Command Execution I/O Signals Dedicated to Standard Mode
- 65 3.5.1 General Information about Commands
- 66 3.5.2 Processing I/O Commands
- 72 3.5.3 I/O Commands Details
- 85 3.6 Example of Using System I/O Signals in Standard Mode
- 89 Chapter 4 System I/O Signals Compatible Mode
- 89 4.1 Types and Functions of System Output Signals (Compatible Mode)
- 90 4.2 Usage of System Output Signals in the Compatible Mode
- 90 4.2.1 Robot Power ON Complete
- 91 4.2.2 Auto Mode (Output)
- 92 4.2.3 Servo ON (Output)
- 93 4.2.4 CAL Complete (Output)
- 94 4.2.5 External Mode (Output)
- 95 4.2.6 Teaching (Output)
- 96 4.2.7 Program Start Reset (Output)
- 97 4.2.8 Robot-in-operation (Output)
- 98 4.2.9 Single-Cycle End (Output)
- 99 4.2.10 Normal CPU (Output)
- 100 4.2.11 Robot Failure (Output)
- 101 4.2.12 Robot Warning (Output)
- 102 4.2.13 Dead Battery Warning (Output)
- 103 4.2.14 Error No. (Output)
- 104 4.2.15 Continue Start Permitted (Output)
- 104 4.2.16 SS mode (Output)
- 105 4.2.17 Emergency Stop (Output from a contact)
- 106 4.3 Types and Functions of System Input Signals (Compatible Mode)
- 107 4.4 Usage of System Input Signals in Compatible Mode
- 107 4.4.1 Enable Auto (Input)
- 108 4.4.2 Operation Preparation Start (Input)
- 110 4.4.3 Program No. Select (Input)
- 112 4.4.4 Program Start (Input)
- 118 4.4.5 Program Reset (Input)
- 120 4.4.6 Robot Stop (Input)
- 121 4.4.7 Step Stop (All Tasks) (Input)
- 122 4.4.8 Instantaneous Stop (All Tasks) (Input)
- 123 4.4.9 Clear Robot Failure (Input)
- 124 4.4.10 Interrupt Skip (Input)
- 125 4.4.11 Continue Start (Input)
- 126 4.5 Example of Using System I/O Signals in Compatible Mode
- 130 4.6 Selectable I/O Mode [Ver 1.95 or later]
- 130 4.6.1 What is a selectable I/O mode?
- 131 4.6.2 Setting up the selectable I/O mode
- 133 4.6.3 System input signal lines that can serve as user I/O signal lines
- 135 4.6.4 System output signal lines that can serve as user I/O signal lines
- 137 4.6.5 Sample usage of selectable I/O mode
- 138 Chapter 5 Connector Pin Assignment and I/O Circuits (NPN type)
- 138 5.1 Connector Pin Assignment (NPN type)
- 138 5.1.1 Connector Pin Assignment Common to Both Modes (NPN type)
- 140 5.1.2 Connector Pin Assignment in Standard Mode
- 144 5.2 Robot Controller I/O Circuits (NPN type)
- 144 5.2.1 User-Input, System-Input and Hand-Input Circuits (NPN type)
- 147 5.2.2 Robot Stop and Enable Auto Input Circuits
- 148 5.2.3 User-Output, System-Output, and Hand-Output Circuits (NPN type)
- 152 5.2.4 Emergency Stop Circuit
- 154 5.2.5 I/O Power Connector (NPN type)
- 156 5.3 Wiring Notes for Robot Controller I/O Connectors (NPN type)
- 158 Chapter 6 Connector Pin Assignment and I/O Circuits (PNP type)
- 158 6.1 Connector Pin Assignment (PNP type)
- 158 6.1.1 Connector Pin Assignment Common to Both Modes (PNP type)
- 164 6.2 Robot Controller I/O Circuits (PNP type)
- 164 6.2.1 User-Input, System-Input and Hand-Input Circuits (PNP type)
- 167 6.2.2 Robot Stop and Enable Auto Input Circuits
- 168 6.2.3 User-Output, System-Output, and Hand-Output Circuits (PNP type)
- 172 6.2.4 Emergency Stop Circuit
- 174 6.2.5 I/O Power Connector (PNP type)
- 176 6.3 Wiring Notes for Robot Controller I/O Connectors (PNP type)
- 178 Chapter 7 I/O Wiring
- 178 7.1 Multi-core Cables with Connectors
- 180 7.2 Wiring of Primary Power Source