5. SEQUENCE CHART OF PCB. Daewoo DWD-E6213, DWD-E1211W'S
Add to My manuals63 Pages
Daewoo DWD-E1211W'S is a modern washing machine with features that provide efficient and convenient laundry care. Its drum type design uses laundry falling energy, ensuring excellent washability without damage or entanglement. The NANO technology employed in the machine sterilizes up to 99.9%, promoting a hygienic wash. With a compact size, it offers a large capacity of 11 kg for both washing and drying, accommodating various laundry loads.
advertisement
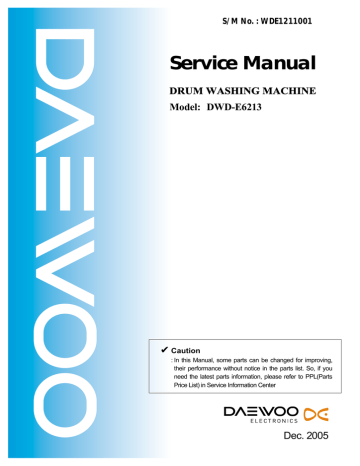
5. SEQUENCE CHART OF PCB
1. SEQUENCE CHART
Cotton Synthetic
Heavy
Stain
Whites ECO-White
Process Time
Small Middle Small Middle Small Middle Small Middle
Pre.
Wash i n g
W a s h s e
R i n
Sensing
Water Supply
Pre. Wash
Drain
Balancing Spin
Mid.Spin
Sensing
Water Supply
Washing1
(Heating)
Washing 2
Drain
Balancing Spin
Mid.Spin
Water Supply
Rinse 1
Drain
Balancing Spin
Mid.Spin
Water Supply
Rinse 2
Drain
Balancing Spin
Mid.Spin
Water Supply
20sec
2min
10min
8min
1min
1min
3min
20sec
2min
90min
80min
35min
30min
25min
25min
20min
15min
1min
2min
3min
1min
1min
3min
2min
1min
3min
2min
3min
1min
1min
3min
■
■
■
■
■
■
■
■
■
■
■
■
■
■
■
■
■
■
■
■
■
■
■
■
■
■
■
■
■
■
■
■
■
■
■
■
■
■
■
■
■
■
■
■
■
■
■
■
■
■
■
■
■
■
■
■
■
■
■
■
■
■
■
S p i n
Rinse 3
Drain
Balancing Spin
Main Spin
3min
1min
1min
7min
5min
3min
60sec Crease care
End
END
Remain Time Display
NOTE
10sec
■
■
■
■
■
■
1:27 1:32 1:27
■
■
1:55
1.Heavy Stain Course: Pre.Wash is Basic Default.
■
■
■
■
■
■
■
■
■
■
■
■
■
■
■
■
■
■
■
■
■
■
■
■
■
■
■
■
■
■
■
■
■
■
■
■
■
■
■
■
■
■
■
■
■
■
■
■
■
■
■
■
■
■
■
■
■
■
■
■
■
■
■
■
■
■
■
2:22 2:32 1:37 1:52
■
■
■
■
■
■
■
■
■
■
■
■
■
■
■
■
■
■
■
■
■
■
■
■
■
■
■
■
■
■
■
■
■
■
23
Wool Delicate Blanket Rapid
Process Time
Small Small Middle Middle
R i n s e
S p i n i n g
W a s h
Sensing
Water Supply
NOTE
"Wash 1
(Heating)"
Wash 2
Drain
Balancing Spin
Mid.Spin
Water Supply
Rinse 1
Drain
Balancing Spin
Mid.Spin
Water Supply
Rinse 2
Drain
Balancing Spin
Mid.Spin
Water Supply
Rinse 3
Drain
Balancing Spin
Mid.Spin
Crease care
D
R
Y
Dry
Cooling
END
Crease care
Crease care
End
END
Remain Time Display
3min
1min
1min
3min
2min
3min
1min
3min
2min
3min
1min
1min
3min
2min
20see
2min
60min
50min
35min
30min
15min
40min
20min
15min
1min
1min
1min
7min
5min
3min
60sec
15min
10min
5min
10sec
30min
60sec
10sec
■
■
■
■
■
■
■
■
■
■
■
■
■
■
■
■
■
46
■
■
■
■
■
■
■
■
■
■
■
■
■
■
■
■
■
46
■
■
■
■
■
■
■
■
■
■
■
■
■
■
■
■
■
■
■
■
1:07
■
■
■
■
■
■
■
■
■
■
■
■
■
■
■
■
■
■
■
■
1:10
1. In Rapid and Drum cleaning program, dry is default function.
2. This chart will be changed depend on market condition.
Drum cleaning
High
Memory
■
■
■
■
■
■
■
■
■
■
■
■
■
■
■
■
■
1:48
24
2. Main function of PCB program
2-1. LOAD SENSING
1) Deciding the water level
1 Cotton, Whites, ECO-White course will be followed by this process.
2 Check the water level with dry laundry at the starting wash.
3 Check the water level by using motor output data during 20 sec, 65 rpm.
2) Deciding Spin Starting Step.
1 Check after finishing washing step with wet laundry.
2 Checking by using motor output data during 20 sec, 65 rpm.
3 The decided data is different depending on loading condition.
2-2. BALANCE SPIN
1) Motor running during balance spin.
1 Spreading the laundry : Rotating the same 45 rpm with left and right direction alternatively.
2 Attaching stop : Attaching the laundry to drum inside with constant speed.
3 Unbalance checking point : First step, check the U.B at 95 rpm, 160 rpm.
Second step, check the U.B at 95 rpm, 350 rpm.
Third step, at 300 rpm. if the unbalance data is over the criterion,
This process will be repeated.
4 Drain step : Drain at water around 160 rpm.
5 After drain, check the unbalance data again. This is so-called balance spin step.
2) Property of balance spin.
1 Conducting 10 times maximum.
2 If the washer can not pass balance spin step during 10 times, then water will be supplied.
3 If the washer can not pass 20 times of balance spin, UE error mode will be displayed on PCB.
25
2-3. DOOR S/W
1) The working principle of Door S/W
1 Door Locking
Bimetal on ( 3 sec) --> solenoid (supply 20msec pulse 2 times)
2 Door Unlocking
Bimetal off --> solenoid (supply 20msec pulse, until unlock)
3 After door locking, all parts can work normally.
4 After pressing power button, if the temperature of wash thermistor is over 50°C or the water level is over the safety level, the door will be locked.
6 The door will be unlocked immediately after all processes are finished.
7 The door can be opened during processing if there is no problem to unlock.
26
2) DOOR OPEN SYSTEM
1If add the laundry during washing, press the door unlock button.
2Door open sequence at abnormal condition.
start / hold door unlock button, 2sec.ON
water level is less than safety level?
YES
Temperature is less than 50°C?
YES
Display <LOCK> off
NO
NO drain fan motor on/ cold water supply
Door open
27
2-4. Child Lock
1 Press the “TEMP”. and “DRY” button simultaneously during processing.
2 Under the Child Lock function, only power button is working.
3 During Child Lock function, CHL will be displayed on PCB.
4 In order to unlock Child Lock mode, press "TEMP" and "DRY" simultaneously.
2-5. The sequence of drain
1 If the checking time to reset point is below 1 min, the remaining drain time is 30 sec.
2 If the checking time to reset point is over 1 min, the remaining drain time is 2 min.
3 If the checking time to reset point is over 10 min, OE singal will be appeared on PCB.
4 If the temperature is over 50°C, the water will be supplied to high water level, then the drain will start.
28
3. Convenience service functions(test mode)
1. Testing Mode
PCB and other electronic parts will be tested without water supply whether they are normal or not.
1) Process : press power button --> press "SPIN" button 3 times with pressing "WASH" button --> 'L d' will be shown on LED --
> Whenever pressing "TEMP" button 1 time, below process will be occurred.
L C (Lock Closed) --> F ( Fan Motor) ---> H (Hot V/V) --> C (Cold V/V) ->
P (prewashing V/V) -> d ( dry V/V) -> bb (bubble) -> dr (drain motor) ->
L O(Lock S/W Open)
2) More details
1When turn on 'LOCK' singal, all process is conducting normaly.
2When working starts, the PCB displys all the sensor conditions.
3In this case, BLDC Motor is not tested. In order to test it, select spin or rinse.
2. Continous testing mode
1) Process : after pressing "WASH", "RINSE", "SPIN" button simultaniously, press "POWER" button.
ALL LED On/Off 1 time --> L C (Lock Closed) ---> R (Motor right) --> L (Motor Left) --> F ( Fan Motor) ---> H
(Hot V/V) --> C (Cold V/V) --> b (pre-wash V/V)
--> d ( dry V/V) --> bb (bubble) --> h1 (HEATER WASH)--> h2(HEATER DRY) --> dr (DRAIN MOTOR On) --
>L O(Lock S/W Open)
2) More tails
1LED test can be done with all LED On.
2All sensor conditions will be shown on PCB during processing.
29
4. ERROR DISPLAY
ERROR
SINGAL
IE
OE
UE
LE
E2
E3
E9
E5
E6
E7
E8
H1
H2
H3
H4
H6
H7
H8
PEF
ERROR CAUSE
WATER
INLET ERROR
DRAIN
ERROR 3 pressure switch disorder
4 PCB can not check water level
UNBALANCE ERROR 1 laundry unbalance
DOOR
1 door opened during processing
2 LOCK S/W broken
OPEN ERROR
1 inlet valve broken
2 drain motor working during water supply
3 pressure switch disorder
4 PCB can not check water level
1 drain motor out of order
2 inlet valve working during drain
Overflow
3 PCB can not check door lock
1 continuous water supply
2 drain motor can not work
FAN MOTOR disorder
3 pressure switch disorder
1 fan motor cannot work
2 PCB cannot control fan motor
SENSOR PRESSURE
1 abnormal water level
ERROR
HIGH VOLTAGE
ERROR
EMG ERROR
Direction Error
1 huge noise
2 spining with jamming clothes between gasket
3 PCB broken
1 huge noise
2 spining with jamming clothes between gasket
3 motor broken
4 PCB broken
1 move opposite direction
2 motor Hall IC broken motor disorder sensor temp. dry disorder
1 connector problem
2 abnormal loading condition
1 sensor temp broken
2 connector problem
1 sensor temp. of washing broken sensor temp.
wash disorder overheating dry heater
2 connector problem
1 fan motor cannot move
2 sensor temp. of dry broken overheating wash heater
1 heater working with no water supply
2 sensor temp. of wash broken abnormal of washing heater 1 washing heater cannot work abnormal of drying heater 1 dry heater cannot work abnormal of sensor temp. of washing
1 heater working with no water supply
Pump Filter 1 The drain filter is clogged.
30
COUNTERPLAN
Change the Inlet-Valve
Change the Drain Motor
Change the Sensor Pressure
Change the PCB
Change the Drain Motor
Change the Inlet-Valve
Change the Sensor Pressure
Change the PCB rearrange the laundry
Clode the Door
Change the LOCK SW
Change the PCB
Change the Inlet-Valve
Change the Drain Motor
Change the Sensor Pressure
Change the Fan-Motor
The contact of the Connector or Change the PCB
Change the Sensor Pressure re-installation rearrange the laundry
Change the PCB re-installation rearrange the laundry
Change the Motor
Change the PCB check the connector and change
The contact of the Connector check the loading condition and change
Change the Sensor Temp.
The contact of the Connector
Change the Sensor Temp.
The contact of the Connector
Change the Fan Motor
Change the Sensor Temp.
check water level
Change the Sensor Temp.
Change the Heater Wash
Change the Heater Dry check the water level and washing heater
Clean the drain filter
advertisement
Key Features
- Large capacity: 11kg washing, 6.5kg drying
- Powerful motor: 1250W~2400W washing, 1100W~2400W drying (optional)
- Advanced technology: Digital condensing dry system
- Gentle and efficient washing: Direct drive system
- Consistent water temperature: Built-in heater
- Easy to use: Digital display, intuitive controls
- Stylish design: Modern and sleek
- Quiet operation: Minimized noise and vibration
- Energy-efficient: Low water and energy consumption
- Durable construction: Stainless steel drum, tempered glass door