- Home
- Domestic appliances
- Climate control
- Split-system air conditioners
- Mitsubishi Electric
- CC-Link IE Field Network
- Instruction manual
3. SIGNALS AND WIRING. Mitsubishi Electric PUY-A-NHA3-BS, CC-Link IE Field Network
Add to my manuals164 Pages
advertisement
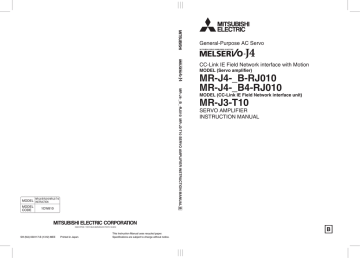
3. SIGNALS AND WIRING
3. SIGNALS AND WIRING
WARNING
Any person who is involved in wiring should be fully competent to do the work.
Before wiring, turn off the power and wait for 15 minutes or more until the charge lamp turns off. Then, confirm that the voltage between P+ and N- is safe with a voltage tester and others. Otherwise, an electric shock may occur. In addition, when confirming whether the charge lamp is off or not, always confirm it from the front of the servo amplifier.
Ground the servo amplifier and servo motor securely.
Do not attempt to wire the servo amplifier and servo motor until they have been installed. Otherwise, it may cause an electric shock.
The cables should not be damaged, stressed, loaded, or pinched. Otherwise, it may cause an electric shock.
To avoid an electric shock, insulate the connections of the power supply terminals.
CAUTION
Wire the equipment correctly and securely. Otherwise, the servo motor may operate unexpectedly, resulting in injury.
Connect cables to the correct terminals. Otherwise, a burst, damage, etc. may occur.
Ensure that polarity (+/-) is correct. Otherwise, a burst, damage, etc. may occur.
The surge absorbing diode installed to the DC relay for control output should be fitted in the specified direction. Otherwise, the emergency stop and other protective circuits may not operate.
Servo amplifier Servo amplifier
24 V DC 24 V DC
DOCOM DOCOM
Control output signal RA
Control output signal RA
For sink output interface For source output interface
Use a noise filter, etc. to minimize the influence of electromagnetic interference.
Electromagnetic interference may be given to the electronic equipment used near the servo amplifier.
Do not install a power capacitor, surge killer or radio noise filter (FR-BIF-(H) option) with the power line of the servo motor.
When using the regenerative resistor, switch power off with the alarm signal.
Otherwise, a transistor fault or the like may overheat the regenerative resistor, causing a fire.
Do not modify the equipment.
3 - 1
3. SIGNALS AND WIRING
CAUTION
Connect the servo amplifier power output (U, V, and W) to the servo motor power input (U, V, and W) directly. Do not let a magnetic contactor, etc. intervene.
Otherwise, it may cause a malfunction.
Servo amplifier
U
V
W
U
Servo motor
V
W
M
Servo amplifier
U
V
W
U
Servo motor
V
W
M
Connecting a servo motor for different axis to U, V, W, or CN2 of the servo amplifier may cause a malfunction.
The following item is the same as MR-J4-_B_ servo amplifiers. For details of the items, refer to each chapter/section of the detailed description field. "MR-J4-_B_" means "MR-J4-_B_(-RJ) Servo Amplifier
Instruction Manual".
Input power supply circuit
Explanation of power supply system
Connector and pin assignment
Signal (device) explanations
Forced stop deceleration function
Interface
Grounding
MR-J4-_B_ section 3.1
MR-J4-_B_ section 3.3
MR-J4-_B_ section 3.4
MR-J4-_B_ section 3.5
MR-J4-_B_ section 3.6
MR-J4-_B_ section 3.8
MR-J4-_B_ section 3.11
3 - 2
3. SIGNALS AND WIRING
3.1 I/O signal connection example
POINT
Be sure to mount a data line filter to the CC-Link IE Field Network cable.
For the branch of CC-Link IE Field Network by the switching hub, use DT135TX
(Mitsubishi Electric System & Service Co., Ltd.). For details of the switching hub, refer to "MELSEC-Q QD77GF Simple Motion Module User's Manual (Positioning
3.1.1 For sink I/O interface
Control)".
(Note 3, 4)
Forced stop 2
(Note 11)
FLS
RLS
DOG
(Note 5)
MR Configurator2
+
Personal computer
10 m or shorter
(Note 12)
Main circuit power supply
(Note 7) 24 V DC
EM2
DI1
DI2
DI3
DICOM
DICOM
USB cable
MR-J3USBCBL3M
(option)
Servo amplifier
(Note 9)
CN3
20
(Note 9)
CN3
3
10 m or shorter
DOCOM
(Note 7) 24 V DC
2
13 MBR
RA1
12 15 ALM
RA3
19
5
10
(Note 2)
CN5
6 LA
16 LAR
7 LB
17 LBR
8 LZ
18 LZR
11 LG
Electromagnetic brake interlock
Malfunction (Note 8)
Encoder A-phase pulse
(differential line driver)
Encoder B-phase pulse
(differential line driver)
Encoder Z-phase pulse
(differential line driver)
Control common
(Note 10)
(Note 13)
Short-circuit connector
(Packed with the servo amplifier)
CN8
4
1
14
MO1
LG
MO2
Plate SD
2 m or shorter
Analog monitor 1
±10 V DC
Analog monitor 2
±10 V DC
CC-Link IE Field Network
(Note 6) CN1A CN1B (Note 6)
CN7
MR-J3-T10
(Note 14)
CN10A CN10B
(Note 1)
Data line filter
ZCAT1730-0730 (TDK)
80 mm or shorter
CC-Link IE Field Network
Data line filter
ZCAT1730-0730 (TDK)
80 mm or shorter
3 - 3
3. SIGNALS AND WIRING
Note 1. To prevent an electric shock, always connect the protective earth (PE) terminal (marked ) of the servo amplifier to the protective earth (PE) of the cabinet.
2. Connect the diode in the correct direction. If it is connected reversely, the servo amplifier will malfunction and will not output signals, disabling EM2 (Forced stop 2) and other protective circuits.
3. If the controller does not have forced stop function, always install the forced stop 2 switch (normally closed contact).
4. When starting operation, always turn on EM2 (Forced stop 2). (Normally closed contact)
5. Use SW1DNC-MRC2-J. (Refer to "MR-J4-_B_(-RJ) Servo Amplifier Instruction Manual" section 11.7.)
6. CN1A and CN1B cannot be used. Be sure to cap CN1A and CN1B connector.
7. Supply 24 V DC ± 10% for interfaces from outside. Set the total current capacity to 300 mA. 300 mA is the value applicable when all I/O signals are used. The current capacity can be decreased by reducing the number of I/O points. Refer to section
3.8.2 (1) of "MR-J4-_B_(-RJ) Servo Amplifier Instruction Manual" that gives the current value necessary for the interface. The illustration of the 24 V DC power supply is divided between input signal and output signal for convenience. However, they can be configured by one.
8. ALM (Malfunction) turns on in normal alarm-free condition. (Normally closed contact)
9. The pins with the same signal name are connected in the servo amplifier.
10. You can change devices of these pins with [Pr. PD07], [Pr. PD08], and [Pr. PD09].
11. Devices can be assigned for these devices with controller setting. For devices that can be assigned, refer to the controller instruction manual. The following devices can be assigned for QD77GF_.
FLS: Upper stroke limit
RLS: Lower stroke limit
DOG: Proximity dog
12. Configure a circuit to turn off EM2 when the main circuit power is turned off to prevent an unexpected restart of the servo amplifier.
13. When not using the STO function, attach a short-circuit connector supplied with a servo amplifier.
14. Connector covers are mounted on the CN10A and the CN10B connectors when the product is shipped from the factory.
Remove those connector covers to connect the CC-Link IE Field Network cables.
3 - 4
3. SIGNALS AND WIRING
3.1.2 For source I/O interface
POINT
For notes, refer to section 3.1.1.
(Note 3, 4)
Forced stop 2
(Note 11)
FLS
RLS
10 m or shorter
(Note 12)
Main circuit power supply
EM2
DI1
DI2
Servo amplifier
(Note 9)
CN3
20
(Note 9)
CN3
3
10 m or shorter
DOCOM
(Note 7) 24 V DC
2
13 MBR
RA1
12 15 ALM
RA3
DOG DI3 (Note 2)
(Note 7) 24 V DC
DICOM
DICOM
19
5
10
(Note 5)
MR Configurator2
+
Personal computer USB cable
MR-J3USBCBL3M
(option)
CN5
6 LA
16 LAR
7 LB
17 LBR
8 LZ
18 LZR
11 LG
Electromagnetic brake interlock
Malfunction (Note 8)
Encoder A-phase pulse
(differential line driver)
Encoder B-phase pulse
(differential line driver)
Encoder Z-phase pulse
(differential line driver)
Control common
(Note 10)
(Note 13)
Short-circuit connector
(Packed with the servo amplifier)
CN8
4
1
14
MO1
LG
MO2
Plate SD
2 m or shorter
Analog monitor 1
±10 V DC
Analog monitor 2
±10 V DC
CC-Link IE Field Network
(Note 6) CN1A CN1B (Note 6)
CN7
MR-J3-T10
(Note 14)
CN10A CN10B
(Note 1)
Data line filter
ZCAT1730-0730 (TDK)
80 mm or shorter
CC-Link IE Field Network
Data line filter
ZCAT1730-0730 (TDK)
80 mm or shorter
3 - 5
3. SIGNALS AND WIRING
3.2 Servo motor with an electromagnetic brake
3.2.1 Safety precautions
Configure an electromagnetic brake circuit so that it is activated also by an external EMG stop switch.
Contacts must be opened when ALM
(Malfunction) or MBR (Electromagnetic brake interlock) turns off.
Contacts must be opened with the EMG stop switch.
Servo motor
RA
B 24 V DC
CAUTION
Electromagnetic brake
The electromagnetic brake is provided for holding purpose and must not be used for ordinary braking.
Before operating the servo motor, be sure to confirm that the electromagnetic brake operates properly.
Do not use the 24 V DC interface power supply for the electromagnetic brake.
Always use the power supply designed exclusively for the electromagnetic brake.
Otherwise, it may cause a malfunction.
POINT
Refer to "Servo Motor Instruction Manual (Vol. 3)" for specifications such as the power supply capacity and operation delay time of the electromagnetic brake.
Refer to "Servo Motor Instruction Manual (Vol. 3)" for the selection of a surge absorber for the electromagnetic brake.
Note the following when the servo motor with an electromagnetic brake is used.
1) The brake will operate when the power (24 V DC) turns off.
2) Turn off the servo-on command after the servo motor stopped.
(1) Connection diagram
Servo amplifier
(Note 2)
24 V DC
MBR
RA1
ALM
(Malfaunction) B1
Servo motor
DOCOM
MBR
RA1
24 V DC
(Note 1)
U
B
B2
Note 1. Create the circuit in order to shut off by interlocking with the emergency stop switch.
2. Do not use the 24 V DC interface power supply for the electromagnetic brake.
(2) Setting
In [Pr. PC02 Electromagnetic brake sequence output], set the time delay (Tb) from electromagnetic brake operation to base circuit shut-off at a servo-off as in the timing chart in section 3.2.2.
3 - 6
3. SIGNALS AND WIRING
3.2.2 Timing chart
(1) When you use the forced stop deceleration function
POINT
To enable the function, set "2 _ _ _ (initial value)" in [Pr. PA04].
(a) At power-on to ready-off from the controller
Main circuit
Control circuit power supply
ON
OFF
Initialization
EM2 (Forced stop 2)
Controlword
(Controller → Servo amplifier)
Statusword
(Servo amplifier → Controller)
ON (disabled)
OFF (enabled)
Initial value
(A) Not ready to switch on
(2) Shutdown (3) Switch on
Ready-on command on
(4) Enable operation
Servo-on command on
(C) Ready to switch on
(D) Switched on (E) Operation enabled
(B) Switch on disabled
215 V
Bus voltage
Internal inrush relay
Dynamic brake
Base circuit
(Energy supply to the servo motor)
MBR
(Electromagnetic brake interlock)
Electromagnetic brake
0 V
ON
OFF
Release
Operation
ON
OFF
(Note 1)
ON
OFF
Release
Operation
100 ms
(Note 4)
Approx. 95 ms
Gate-on processing start Gate-on blocked
Release delay time and external relay, etc. (Note 2)
(8) Shutdown
(C) Ready to switch on
Operation delay time of the electromagnetic brake
Operation command
(Controller → Servo amplifier)
0 r/min
(Note 3)
Servo motor speed
0 r/min
Note 1. ON: Electromagnetic brake is not activated.
OFF: Electromagnetic brake is activated.
2. Electromagnetic brake is released after delaying for the release delay time of electromagnetic brake and operation time of external circuit relay. For the release delay time of electromagnetic brake, refer to "Servo Motor Instruction Manual (Vol. 3)".
3. To prevent the servo motor from rotating rapidly at servo-on, give a current position as a position command from the controller before servo-on.
4. It will be 200 ms for 5 kW and 7 kW servo amplifiers.
3 - 7
3. SIGNALS AND WIRING
(b) Servo-on command on/off
When servo-on command is turned off, the servo lock will be released after Tb [ms], and the servo motor will coast. If the electromagnetic brake is enabled during servo-lock, the brake life may be shorter. Therefore, set Tb about 1.5 times of the minimum delay time where the moving part will not drop down for a vertical axis system, etc.
Main circuit
Control circuit power supply
ON
OFF
EM2 (Forced stop 2)
ON (disabled)
OFF (enabled)
Controlword
(Controller → Servo amplifier)
(4) Enable operation
Servo-on command on
(5) Disable operation
Servo-on command off
Statusword
(Servo amplifier → Controller)
Dynamic brake
Base circuit
(Energy supply to the servo motor)
MBR
(Electromagnetic brake interlock)
Electromagnetic brake
Release
Operation
ON
OFF
(Note 1)
ON
OFF
Release
Operation
(E) Operation enabled (D) Switched on
(Note 2)
Tb
Coasting
Servo motor speed
Operation delay time of the electromagnetic brake
0 r/min
Note 1. ON: Electromagnetic brake is not activated.
OFF: Electromagnetic brake is activated.
2. Tb is a delay time from electromagnetic brake start to base circuit shut-off at servo-off. Set
Tb in [Pr. PC02].
3 - 8
3. SIGNALS AND WIRING
POINT
To enable the function, set "2 _ _ _ (initial value)" in [Pr. PA04].
(c) Forced stop 2 on/off
EM2 (Forced stop 2)
ON (disabled)
OFF (enabled)
Controlword
(Controller → Servo amplifier)
(4) Enable operation
Servo-on command on
Statusword
(Servo amplifier → Controller)
Base circuit
(Energy supply to the servo motor)
MBR
(Electromagnetic brake interlock)
ALM (Malfunction)
WNG (Warning)
Dynamic brake
ON
OFF
(Note 1)
ON
OFF
ON (No alarm)
OFF (alarm)
ON (No alarm)
OFF (alarm)
Release
Operation
(E) Operation enabled (F) Quick stop active (B) Switched on disabled
(Note 3)
Tb
(Note 2)
Model speed command = 0, and equal to or less than zero speed
Servo motor speed
0 r/min
Note 1. ON: Electromagnetic brake is not activated.
OFF: Electromagnetic brake is activated.
2. The model speed command is a speed command generated in the servo amplifier for forced stop deceleration of the servo motor.
3. Tb is a delay time from electromagnetic brake start to base circuit shut-off at servo-off. Set Tb in [Pr. PC02].
3 - 9
3. SIGNALS AND WIRING
(d) Alarm occurrence
1) When the forced stop deceleration function is enabled
Alarm occurrence
EM2 (Forced stop 2)
ON (disabled)
OFF (enabled)
Controlword
(Controller → Servo amplifier)
(4) Enable operation
Servo-on command on
Statusword
(Servo amplifier → Controller)
Base circuit
(Energy supply to the servo motor)
MBR
(Electromagnetic brake interlock)
ALM (Malfunction)
Dynamic brake
ON
OFF
(Note 1)
ON
OFF
ON (No alarm)
OFF (alarm)
Release
Operation
(E) Operation enabled
(G) Fault reaction active
Servo motor speed
0 r/min
Alarm reset
(B) Switched on disabled
(H) Fault
(15) Fault Reset
(4) Enable operation
Servo-on command on
(C) Ready to switch on
(D) Switched on
Approx. 210 ms
(Note 4)
(E) Operation enabled
(Note 3)
Tb
(Note 2)
Model speed command = 0, and equal to or less than zero speed
Controller command is ignored.
Servo amplifier display No alarm Alarm No.
No alarm
Note 1. ON: Electromagnetic brake is not activated.
OFF: Electromagnetic brake is activated.
2. The model speed command is a speed command generated in the servo amplifier for forced stop deceleration of the servo motor.
3. Tb is a delay time from electromagnetic brake start to base circuit shut-off at servo-off. Set Tb in [Pr. PC02].
4. Waiting time for relay-on + waiting time for servo-on
3 - 10
3. SIGNALS AND WIRING
2) When the forced stop deceleration function is disabled
Servo amplifier display
Alarm occurrence
EM2 (Forced stop 2)
ON (disabled)
OFF (enabled)
Controlword
(Controller → Servo amplifier)
Statusword
(Servo amplifier → Controller)
Base circuit
(Energy supply to the servo motor)
MBR
(Electromagnetic brake interlock)
(Note)
ALM (Malfunction)
Dynamic brake
ON
OFF
ON
OFF
ON (No alarm)
OFF (alarm)
Release
Operation
(4) Enable operation
Servo-on command on
(E) Operation enabled
(G) Fault reaction active
(H) Fault
Dynamic brake operation delay time
Approx. 10 ms
Dynamic brake
Dynamic brake + electromagnetic brake
Servo motor speed
0 r/min
Operation delay time of the electromagnetic brake
No alarm Alarm No.
Note. ON: Electromagnetic brake is not activated.
OFF: Electromagnetic brake is activated.
3 - 11
3. SIGNALS AND WIRING
3) When CC-Link IE Field communication brake occurred
Communication broke
(unexpected parallel off)
EM2 (Forced stop 2)
(Note 5)
ON (disabled)
OFF (enabled) (4) Enable operation
Servo-on command on
Controlword
(Controller → Servo amplifier)
Initial value
Statusword
(Servo amplifier → Controller)
Base circuit
(Energy supply to the servo motor)
MBR
(Electromagnetic brake interlock)
ALM (Malfunction)
Dynamic brake
ON
OFF
(Note 1)
ON
OFF
ON (No alarm)
OFF (alarm)
Release
Operation
(E) Operation enabled
(F) Quick stop active
Communication recovered
(parallel on)
(B) Switch on disabled
(A) Not ready to switch on
(4) Enable operation
Servo-on command on
(C) Ready to switch on
(D) Switched on
Approx. 210 ms
(Note 4)
(E) Operation enabled
(Note 3)
Tb
(Note 2)
Model speed command = 0, and equal to or less than zero speed
Servo motor speed
0 r/min
Servo amplifier display No alarm (d1 or E7) AA No alarm
Note 1. ON: Electromagnetic brake is not activated.
OFF: Electromagnetic brake is activated.
2. The model speed command is a speed command generated in the servo amplifier for forced stop deceleration of the servo motor.
3. Tb is a delay time from electromagnetic brake start to base circuit shut-off at servo-off. Set Tb in [Pr. PC02].
4. Waiting time for relay-on + waiting time for servo-on
5. A delay time will be generated between communication brake occurrence and deceleration start due to processing time of parallel off. The dynamic brake will start depending on status of communication brake.
3 - 12
3. SIGNALS AND WIRING
(c) Both main and control circuit power supplies off
Main circuit
Control circuit power supply
EM2 (Forced stop 2)
Main circuit, Control circuit power off
ON
OFF
ON (disabled)
OFF (enabled) (4) Enable operation
Servo-on command on
Controlword
(Controller → Servo amplifier)
Statusword
(Servo amplifier → Controller)
Base circuit
(Energy supply to the servo motor)
MBR
(Electromagnetic brake interlock)
ALM (Malfunction)
[AL. 10.1 Undervoltage]
ON
OFF
(Note 1)
ON
OFF
ON (No alarm)
OFF (alarm)
(E) Operation enabled
Dynamic brake
Release
Operation
(Note 2)
Dynamic brake operation delay time
Approx. 10 ms
Dynamic brake
Dynamic brake + electromagnetic brake
Servo motor speed
0 r/min
Operation delay time of the electromagnetic brake
Note 1. ON: Electromagnetic brake is not activated.
OFF: Electromagnetic brake is activated.
2. Variable according to the operation status.
3 - 13
3. SIGNALS AND WIRING
(d) Main circuit power supply off during control circuit power supply on
Main circuit
Control circuit power supply
ON
OFF
EM2 (Forced stop 2)
ON (disabled)
OFF (enabled)
Controlword
(Controller
Statusword
(Servo amplifier
Base circuit
→ Servo amplifier)
(Energy supply to the servo motor)
MBR
(Electromagnetic brake interlock)
ALM (Malfunction)
[AL. 10.1 Undervoltage]
Dynamic brake
→ Controller)
ON
OFF
(Note 1)
ON
OFF
ON (No alarm)
OFF (alarm)
Release
Operation
(4) Enable operation
Servo-on command on
(E) Operation enabled
(G) Fault reaction active
(H) Fault
(Note 2)
Servo motor speed
The time until a bus voltage drop is detected.
Forced stop deceleration
Dynamic brake
Dynamic brake + electromagnetic brake
0 r/min
Approx. 10 ms
Dynamic brake operation delay time
Operation delay time of the electromagnetic brake
Note 1. ON: Electromagnetic brake is not activated.
OFF: Electromagnetic brake is activated.
2. Variable according to the operation status.
3 - 14
3. SIGNALS AND WIRING
(2) When you do not use the forced stop deceleration function
POINT
To disable the function, set "0 _ _ _" in [Pr. PA04].
(a) At power-on to ready-off from the controller
It is the same as (1) (a) of this section.
(b) Servo-on command on/off
It is the same as (1) (b) of this section.
(c) Off/on of the forced stop command or Forced stop 1
Main circuit
Control circuit power supply
ON
OFF
Forced stop command
(Controller → Servo amplifier) or
EM1 (Forced stop 1)
Controlword
(Controller → Servo amplifier)
ON (disabled)
OFF (enabled)
(4) Enable operation
Servo-on command on
(F) Quick stop active
Statusword
(Servo amplifier → Controller)
(E) Operation enabled
(B) Switched on disabled
Base circuit
(Energy supply to the servo motor)
MBR
(Electromagnetic brake interlock)
Dynamic brake
ON
OFF
(Note 1)
ON
OFF
Release
Operation
Servo motor speed
Dynamic brake operation delay time
Approx. 10 ms
Dynamic brake
Dynamic brake + electromagnetic brake
(C) Ready to switch on
(D) Switched on
Approx. 210 ms (Note 2) (E) Operation enabled
Electromagnetic brake release
0 r/min
Operation delay time of the electromagnetic brake
Note 1. ON: Electromagnetic brake is not activated.
OFF: Electromagnetic brake is activated.
2. Waiting time for relay-on + waiting time for servo-on
(d) Alarm occurrence
1) At alarm occurrence
The servo motor driving during an alarm is the same as (1) (d) 2) of this section.
3 - 15
3. SIGNALS AND WIRING
2) When CC-Link IE Field communication brake occurred
Communication broke
(unexpected parallel off)
(Note 3)
EM2 (Forced stop 2)
ON (disabled)
OFF (enabled)
Controlword
(Controller → Servo amplifier)
(4) Enable operation
Servo-on command on
Communication recovered
(parallel on)
Initial value
(F) Quick stop active (B) Switch on disabled
(A) Not ready to switch on
(4) Enable operation
Servo-on command on
(C) Ready to switch on
(D) Switched on
Approx. 210 ms
(Note 2)
(E) Operation enabled
Statusword
(Servo amplifier → Controller)
Base circuit
(Energy supply to the servo motor)
MBR
(Electromagnetic brake interlock)
ALM (Malfunction)
Dynamic brake
ON
OFF
(Note 1)
ON
OFF
ON (No alarm)
OFF (alarm)
Release
Operation
(E) Operation enabled
Dynamic brake operation delay time
Approx. 10 ms
Dynamic brake
Dynamic brake + electromagnetic brake
Servo motor speed
0 r/min
Servo amplifier display No alarm (d1 or E7)
Operation delay time of the electromagnetic brake
AA No alarm
Note 1. ON: Electromagnetic brake is not activated.
OFF: Electromagnetic brake is activated.
2. Waiting time for relay-on + waiting time for servo-on
3. A delay time will be generated between communication brake occurrence and deceleration start due to processing time of parallel off.
(e) Both main and control circuit power supplies off
It is the same as (1) (c) of this section.
3 - 16
3. SIGNALS AND WIRING
(f) Main circuit power supply off during control circuit power supply on
Main circuit power supply
ON
OFF
Forced stop command
(Controller → Servo amplifier) or
EM2 (Forced stop 2)
Controlword
(Controller → Servo amplifier)
ON (disabled)
OFF (enabled)
(4) Enable operation
Servo-on command on
(G) Fault reaction active
Statusword
(Servo amplifier → Controller)
(E) Operation enabled
(H) Fault
(Note 2)
Base circuit
(Energy supply to the servo motor)
MBR
(Electromagnetic brake interlock)
ON
OFF
(Note 1)
ON
OFF
ALM (Malfunction)
[AL. 10.1 Undervoltage]
ON (No alarm)
OFF (alarm)
Dynamic brake
Release
Operation
Dynamic brake operation delay time
Approx. 10 ms
Dynamic brake
Dynamic brake + electromagnetic brake
Servo motor speed
0 r/min
Operation delay time of the electromagnetic brake
Note 1. ON: Electromagnetic brake is not activated.
OFF: Electromagnetic brake is activated.
2. Waiting time for relay-on + waiting time for servo-on
3 - 17
3. SIGNALS AND WIRING
MEMO
3 - 18
advertisement
* Your assessment is very important for improving the workof artificial intelligence, which forms the content of this project
Related manuals
advertisement
Table of contents
- 2 Safety Instructions
- 7 DISPOSAL OF WASTE
- 7 STO function of the servo amplifier
- 7 Compliance with global standards
- 8 About the manual
- 8 Cables used for wiring
- 8 U.S. customary units
- 10 CONTENTS
- 12 1. FUNCTIONS AND CONFIGURATION
- 12 1.1 Summary
- 13 1.2 Function block diagram
- 19 1.3 Standard specifications
- 19 1.3.1 Servo amplifier
- 21 1.3.2 MR-J3-T10 Field Network interface unit
- 21 1.4 Combinations of servo amplifiers and servo motors
- 23 1.5 Function list
- 24 1.6 Model designation
- 26 1.7 Structure
- 26 1.7.1 Parts identification
- 38 1.7.2 Parts identification of MR-J3-T10
- 39 1.8 Installation and removal of MR-J3-T10
- 43 1.9 Configuration including peripheral equipment
- 43 1.9.1 200 V class
- 49 1.9.2 400 V class
- 56 2. INSTALLATION
- 57 2.1 Installation direction and clearances
- 59 2.2 Keep out foreign materials
- 60 3. SIGNALS AND WIRING
- 62 3.1 I/O signal connection example
- 62 3.1.1 For sink I/O interface
- 64 3.1.2 For source I/O interface
- 65 3.2 Servo motor with an electromagnetic brake
- 65 3.2.1 Safety precautions
- 66 3.2.2 Timing chart
- 78 4. STARTUP
- 79 4.1 Switching power on for the first time
- 79 4.1.1 Startup procedure
- 80 4.1.2 Wiring check
- 83 4.1.3 Surrounding environment
- 83 4.2 Switch setting and display of the servo amplifier
- 83 4.2.1 Switches
- 86 4.2.2 Scrolling display
- 87 4.2.3 Status display of a station
- 89 4.3 Display of MR-J3-T10 CC-Link IE Field Network interface unit
- 90 5. PARAMETERS
- 90 5.1 Parameter list
- 91 5.1.1 Basic setting parameters ([Pr. PA_ _ ])
- 92 5.1.2 Gain/filter setting parameters ([Pr. PB_ _ ])
- 93 5.1.3 Extension setting parameters ([Pr. PC_ _ ])
- 94 5.1.4 I/O setting parameters ([Pr. PD_ _ ])
- 95 5.1.5 Extension setting 2 parameters ([Pr. PE_ _ ])
- 96 5.1.6 Extension setting 3 parameters ([Pr. PF_ _ ])
- 97 5.1.7 Option setting parameters ([Pr. Po_ _)
- 99 5.2 Detailed list of parameters
- 99 5.2.1 Basic setting parameters ([Pr. PA_ _ ])
- 106 5.2.2 Gain/filter setting parameters ([Pr. PB_ _ ])
- 115 5.2.3 Extension setting parameters ([Pr. PC_ _ ])
- 120 5.2.4 I/O setting parameters ([Pr. PD_ _ ])
- 122 5.2.5 Extension setting 2 parameters ([Pr. PE_ _ ])
- 123 5.2.6 Extension setting 3 parameters ([Pr. PF_ _ ])
- 125 5.2.7 Option setting parameters ([Pr. Po_ _)
- 126 6. TROUBLESHOOTING
- 126 6.1 Alarm and warning list
- 131 6.2 Troubleshooting at power on
- 134 7. DIMENSIONS
- 135 7.1 Servo amplifier
- 135 7.1.1 200 V class
- 144 7.1.2 400 V class
- 151 7.2 MR-J3-T10 CC-Link IE Field Network interface unit
- 152 8. OPTIONS AND PERIPHERAL EQUIPMENT
- 153 8.1 Combinations of cable/connector sets
- 155 8.2 Cable for CC-Link IE Field Network
- 156 APPENDIX
- 156 App. 1 Peripheral equipment manufacturer (for reference)
- 156 App. 2 Analog monitor
- 159 App. 3 Special specification
- 161 REVISIONS
- 162 Country/Region
- 163 Warranty