- Home
- Domestic appliances
- Climate control
- Split-system air conditioners
- Mitsubishi Electric
- CC-Link IE Field Network
- Instruction manual
6. TROUBLESHOOTING. Mitsubishi Electric PUY-A-NHA3-BS, CC-Link IE Field Network
Add to my manuals164 Pages
advertisement
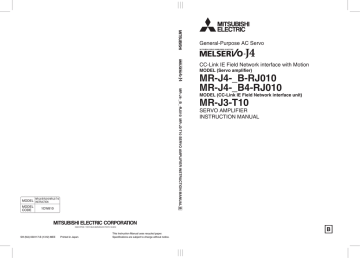
6. TROUBLESHOOTING
6. TROUBLESHOOTING
POINT
6.1 Alarm and warning list
Refer to "MELSERVO-J4 Servo Amplifier Instruction Manual (Troubleshooting)" for details of alarms and warnings.
As soon as an alarm occurs, make the Servo-off status and interrupt the main circuit power.
[AL. 37 Parameter error] and warnings are not recorded in the alarm history.
When an error occurs during operation, the corresponding alarm or warning is displayed. When the alarm or the warning occurs, refer to "MELSERVO-J4 Servo Amplifier Instruction Manual (Troubleshooting)" to remove the failure. When an alarm occurs, ALM will turn off.
After its cause has been removed, the alarm can be deactivated in any of the methods marked ○ in the alarm deactivation column in the following table. Warnings are automatically canceled after the cause of occurrence is removed.
For the alarms and warnings in which "SD" is written in the stop method column, the axis stops with the dynamic brake after forced stop deceleration. For the alarms and warnings in which "DB" or "EDB" is written in the stop method column, the axis stops with the dynamic brake without forced stop deceleration.
Alarm reset
Stop
No. Name
Detail
No.
Detail name method
(Note 3,
4)
10 Undervoltage
10.1 Voltage drop in the control circuit power
10.2 Voltage drop in the main circuit power
12.1 RAM error 1
12.2 RAM error 2
12 Memory error 1 (RAM) 12.3 RAM error 3
12.4 RAM error 4
12.5 RAM error 5
13 Clock
13.1 Clock error 1
13.2 Clock error 2
14.1 Control process error 1
14.2 Control process error 2
14
15
Control process error
Memory error 2
(EEP-ROM)
14.3 Control process error 3
14.4 Control process error 4
14.5 Control process error 5
14.6 Control process error 6
14.7 Control process error 7
14.8 Control process error 8
14.9 Control process error 9
14.A Control process error 10
15.1 EEP-ROM error at power on
15.2 EEP-ROM error during operation
DB
DB
DB
DB
DB
DB
DB
DB
DB
DB
DB
DB
DB
DB
DB
EDB
SD
DB
DB
DB
DB
6 - 1
6. TROUBLESHOOTING
No. Name
Detail
No.
Detail name
Alarm reset
Stop method
(Note 3,
4)
25 Absolute position erased
16.1
16.2
16.3
Encoder initial communication - Receive data error 1
Encoder initial communication - Receive data error 2
Encoder initial communication - Receive data error 3
16.6
16.D Encoder initial communication - Process error 4
16.E Encoder initial communication - Process error 5
16.F Encoder initial communication - Process error 6
17.1 Board error 1
17 Board 17.3 Board error 2
19
20
Memory error 3
(Flash-ROM)
1A
Servo motor combination error
1E
Encoder initial communication error 2
1F
Encoder initial communication error 3
16.A Encoder initial communication - Process error 1
16.B Encoder initial communication - Process error 2
16.C Encoder initial communication - Process error 3
17.4 Board error 3
19.1 Flash-ROM error 1
19.2 Flash-ROM error 2
1A.1 Servo motor combination error
1A.2 Servo motor control mode combination error
20.6
21
24 communication error 1 communication error 1
Encoder normal communication error 2
Main circuit error
20.A
Encoder normal communication - Receive data error 5
21.1 Encoder data error 1
21.2 Encoder data update error
21.3 Encoder data waveform error
21.5 Encoder hardware error 1
21.6 Encoder hardware error 2
21.9 Encoder data error 2
24.2
Ground fault detected by software detection function
25.1 Servo motor encoder - Absolute position erased
DB
DB
DB
DB
DB
DB
DB
DB
DB
DB
DB
DB
DB
DB
DB
DB
DB
DB
DB
DB
DB
EDB
EDB
EDB
EDB
EDB
EDB
EDB
EDB
EDB
EDB
EDB
EDB
EDB
EDB
DB
DB
DB
6 - 2
6. TROUBLESHOOTING
No. Name
Detail
No.
30
31
Regenerative error
(Note 1)
Overspeed
Detail name
30.1 Regeneration heat error
30.2 Regeneration signal error
30.3 Regeneration feedback signal error
31.1 Abnormal motor speed
32 Overcurrent
32.4
Overcurrent detected at software detection function (during a stop)
33.1 Main circuit voltage error 33 Overvoltage
35 Command frequency error 35.1 Command frequency error
37 Parameter
37.1 Parameter setting range error
37.2 Parameter combination error
3E
45
46 circuit error
Operation mode error
Main circuit device overheat (Note 1)
Servo motor overheat
(Note 1)
3A.1 Inrush current suppression circuit error
3E.1 Operation mode error
45.1 Main circuit device overheat error
46.1
46.5
Abnormal temperature of servo motor 1
Abnormal temperature of servo motor 3
47 Cooling fan error
46.6 Abnormal temperature of servo motor 4
47.1 Cooling fan stop error
47.2 Cooling fan speed reduction error
50.1 Thermal overload error 1 during operation
50.2
50.3
Thermal overload error 2 during operation
Thermal overload error 4 during operation
50 Overload 1 (Note 1)
50.4 Thermal overload error 1 during a stop
50.5 Thermal overload error 2 during a stop
50.6 Thermal overload error 4 during a stop
51.1 Thermal overload error 3 during operation
51 Overload 2 (Note 1)
51.2 Thermal overload error 3 during a stop
52.1 Excess droop pulse 1
52 Error
52.3 Excess droop pulse 2
52.4 Error excessive during 0 torque limit
52.5 Excess droop pulse 3
56 Forced stop error
56.2 Over speed during forced stop
56.3 Estimated distance over during forced stop
74 Option card error 1
74.1
74.2
74.3
74.4
74.5
Option card error 1
Option card error 2
Option card error 3
Option card error 4
Option card error 5
Alarm reset
Stop method
(Note 3,
4)
DB
DB
DB
SD
(Note 1) (Note 1) (Note 1)
(Note 1) (Note 1) (Note 1)
(Note 1) (Note 1) (Note 1)
DB
DB
DB
DB
EDB
SD
DB
DB
EDB
DB
SD
SD
DB
DB
SD
SD
SD
SD
SD
SD
SD
SD
DB
DB
SD
SD
SD
EDB
EDB
EDB
EDB
(Note 1) (Note 1) (Note 1)
(Note 1) (Note 1) (Note 1)
(Note 1) (Note 1) (Note 1)
(Note 1) (Note 1) (Note 1)
(Note 1) (Note 1) (Note 1)
(Note 1) (Note 1) (Note 1)
(Note 1) (Note 1) (Note 1)
(Note 1) (Note 1) (Note 1)
(Note 1) (Note 1) (Note 1)
(Note 1) (Note 1) (Note 1)
(Note 1) (Note 1) (Note 1)
(Note 1) (Note 1) (Note 1)
DB
DB
DB
DB
DB
DB
6 - 3
6. TROUBLESHOOTING
No. Name
Detail
No.
Detail name
Alarm reset
Stop method
(Note 3,
4)
75 Option card error 2
75.3 Option card connection error
75.4 Option card disconnected
8A
USB communication timeout error
8A.1 USB communication time-out error
8D
CC-Link IE communication error
8D.1 CC-Link IE communication error 1
8D.2 CC-Link IE communication error 2
8D.3 Master station setting error 1
8D.5 Master station setting error 2
8D.6 CC-Link IE communication error 3
8D.7 CC-Link IE communication error 4
8D.8 CC-Link IE communication error 5
8D.9 Synchronization error 1
8D.A Synchronization error 2
8E.1 USB communication receive error
8E USB communication error
888 Watchdog
8E.2 USB communication checksum error
8E.3
8E.4
8E.5
USB communication character error
USB communication command error
USB communication data number error
88._ Watchdog
Note 1. Leave for about 30 minutes of cooling time after removing the cause of occurrence.
2. In some controller communication status, the alarm factor may not be removed.
EDB
DB
SD
SD
SD
DB
DB
SD
SD
SD
SD
SD
SD
SD
SD
SD
SD
DB
DB: Stops with dynamic brake. (Coasts for the servo amplifier without dynamic brake.)
EDB: Stop with electronic dynamic brake (enabled only with the specified servo motors)
Refer to the following table for the specified servo motors. The stop method for other than the specified servo motors will be DB.
Series
HG-KR
HG-MR
HG-SR
HG-KR053/HG-KR13/HG-KR23/HG-KR43
HG-MR053/HG-MR13/HG-MR23/HG-MR43
HG-SR51/HG-SR52
SD: Forced stop deceleration
4. This is applicable when [Pr. PA04] is set to the initial value. The stop system of SD can be changed to DB using [Pr. PA04].
6 - 4
6. TROUBLESHOOTING
No. Name
Detail
No.
Detail name
Stop method
(Note 2,
3)
91
92
Servo amplifier overheat warning (Note 1)
Battery cable disconnection warning
91.1
92.1
Main circuit device overheat warning
Encoder battery cable disconnection warning
95 STO
95.1 STO1 off detection
95.2 STO2 off detection warning
9D CC-Link IE warning 1
9E
9F
CC-Link IE warning 2
Battery warning
E0
Excessive regeneration warning (Note 1)
96.2
9D.1
9D.2
Command input warning at home positioning
Station number switch change warning
Master station setting warning
9D.3 Overlapping station number warning
9D.4 Mismatched station number warning
9E.1 CC-Link IE communication warning
9F.1 Low battery
E0.1 Excessive regeneration warning
E1
Overload warning 1
(Note 1)
E1.1 Thermal overload warning 1 during operation
E1.2 Thermal overload warning 2 during operation
E1.3 Thermal overload warning 3 during operation
E1.4 Thermal overload warning 4 during operation
E1.5 Thermal overload error 1 during a stop
E1.6 Thermal overload error 2 during a stop
E1.7 Thermal overload error 3 during a stop
E3
E4
Absolute position counter warning
Parameter warning
E6 Servo forced stop warning E6.1 Forced stop warning
E7
Controller forced stop warning
E7.1 Controller forced stop warning
E8
Cooling fan speed reduction warning
E8.1
E8.2
E9.1
Decreased cooling fan speed warning
Cooling fan stop
Servo-on signal on during main circuit off
E9
EC
ED
Main circuit off warning
Overload warning 2
(Note 1)
Output watt excess warning
F0
F2
Tough drive warning
Drive recorder - Miswriting warning
F3
Oscillation detection warning
E1.8 Thermal overload error 4 during a stop
E3.2 Absolute position counter warning
E3.5 Encoder absolute positioning counter warning
E4.1 Parameter setting range error warning
E9.2 Bus voltage drop during low speed operation
E9.3 Ready-on signal on during main circuit off
EC.1 Overload warning 2
ED.1 Output watt excess warning
F0.1 Instantaneous power failure tough drive warning
F0.3 Vibration tough drive warning
F2.1
F2.2
F3.1
Drive recorder - Area writing time-out warning
Drive recorder - Data miswriting warning
Oscillation detection warning
Note 1. Leave for about 30 minutes of cooling time after removing the cause of occurrence.
2. The following shows two stop methods of DB and SD.
DB: Stops with dynamic brake. (Coasts for the servo amplifier without dynamic brake.)
SD: Decelerates to a stop
3. This is applicable when [Pr. PA04] is set to the initial value. The stop system of SD can be changed to DB using [Pr. PA04].
SD
SD
DB
DB
DB
DB
DB
6 - 5
6. TROUBLESHOOTING
6.2 Troubleshooting at power on
When an error occurs at the power supply of the controller or servo amplifier, improper boot of the servo amplifier might be the cause. Check the display of the servo amplifier, and take actions according to this section.
Display Description Cause Checkpoint Action
AA The power of the simple motion module was turned off.
The power of the simple motion module was turned off.
A CC-Link IE cable was disconnected.
Review the power of the simple motion module.
Turn on the power of the simple motion module.
Replace the CC-Link IE cable of the corresponding station.
Ab Initialization communication with the controller has not completed.
The setting of the station
No. is incorrect.
The station No. of the simple motion module is not matched.
A CC-Link IE cable was disconnected.
The power of the servo amplifier was turned on while the power of the simple motion module was off.
"AA" is displayed in the corresponding station and following stations.
Check if the connectors (CN10A,
CN10B) are unplugged.
Check that a device is not assigned to the same station No.
Check the settings and station
No. of the simple motion module.
"Ab" is displayed in the corresponding station and following stations.
Review the power of the simple motion module.
Connect it correctly.
Set it correctly.
Set it correctly.
Replace the CC-Link IE cable of the corresponding station.
Turn on the power of the simple motion module.
Ab. The initialization of the servo amplifier has not completed. malfunctioning.
The servo amplifier is malfunctioning.
The simple motion module is malfunctioning.
A CC-Link IE cable was disconnected.
The power of the servo amplifier was turned on while the power of the simple motion module was off.
"Ab" is displayed in the corresponding station and following stations.
"Ab" is displayed in the corresponding station and following stations.
Replace the simple motion module and check the repeatability.
"Ab." is displayed in the corresponding station and following stations.
Review the power of the simple motion module.
Replace the MR-J3-T10.
Replace the servo amplifier.
Replace the simple motion module.
Replace the CC-Link IE cable of the corresponding station.
Turn on the power of the simple motion module. malfunctioning.
The servo amplifier is malfunctioning.
The simple motion module is malfunctioning. does not match.
"Ab." is displayed in the corresponding station and following stations.
"Ab." is displayed in the corresponding station and following stations.
Replace the simple motion module and check the repeatability.
Check the communication cycle on the simple motion module side.
Number of using stations is 8 or less: 0.888 ms
Number of using stations is 16 or less: 1.777 ms
Replace the MR-J3-T10.
Replace the servo amplifier.
Replace the simple motion module.
Set it correctly.
6 - 6
6. TROUBLESHOOTING
Display Description Cause
MR-J3-T10 is malfunctioning. communications by specified cycle could not be made.
The servo amplifier is malfunctioning. b##.
C##. d##.
(Note)
The system has been in the test operation mode. off Operation mode for manufacturer setting is set.
The simple motion module is malfunctioning.
Test operation mode has been enabled.
"AC" is displayed in the corresponding station and following stations.
Replace the simple motion module and check the repeatability.
Test operation setting switch
(SW2-1) is turned on.
Operation mode for manufacturer setting is enabled.
Checkpoint
"AC" is displayed in the corresponding station and following stations.
Check that the test operation select switch (SW2-1) and manufacturer setting switch
(SW2-2) are not on.
Note. ## indicates axis No.
Action
Replace the MR-J3-T10.
Replace the servo amplifier.
Replace the simple motion module.
Turn off the test operation setting switch (SW2-1).
Set the auxiliary station number setting switches (SW2) correctly.
6 - 7
6. TROUBLESHOOTING
MEMO
6 - 8
advertisement
* Your assessment is very important for improving the workof artificial intelligence, which forms the content of this project
Related manuals
advertisement
Table of contents
- 2 Safety Instructions
- 7 DISPOSAL OF WASTE
- 7 STO function of the servo amplifier
- 7 Compliance with global standards
- 8 About the manual
- 8 Cables used for wiring
- 8 U.S. customary units
- 10 CONTENTS
- 12 1. FUNCTIONS AND CONFIGURATION
- 12 1.1 Summary
- 13 1.2 Function block diagram
- 19 1.3 Standard specifications
- 19 1.3.1 Servo amplifier
- 21 1.3.2 MR-J3-T10 Field Network interface unit
- 21 1.4 Combinations of servo amplifiers and servo motors
- 23 1.5 Function list
- 24 1.6 Model designation
- 26 1.7 Structure
- 26 1.7.1 Parts identification
- 38 1.7.2 Parts identification of MR-J3-T10
- 39 1.8 Installation and removal of MR-J3-T10
- 43 1.9 Configuration including peripheral equipment
- 43 1.9.1 200 V class
- 49 1.9.2 400 V class
- 56 2. INSTALLATION
- 57 2.1 Installation direction and clearances
- 59 2.2 Keep out foreign materials
- 60 3. SIGNALS AND WIRING
- 62 3.1 I/O signal connection example
- 62 3.1.1 For sink I/O interface
- 64 3.1.2 For source I/O interface
- 65 3.2 Servo motor with an electromagnetic brake
- 65 3.2.1 Safety precautions
- 66 3.2.2 Timing chart
- 78 4. STARTUP
- 79 4.1 Switching power on for the first time
- 79 4.1.1 Startup procedure
- 80 4.1.2 Wiring check
- 83 4.1.3 Surrounding environment
- 83 4.2 Switch setting and display of the servo amplifier
- 83 4.2.1 Switches
- 86 4.2.2 Scrolling display
- 87 4.2.3 Status display of a station
- 89 4.3 Display of MR-J3-T10 CC-Link IE Field Network interface unit
- 90 5. PARAMETERS
- 90 5.1 Parameter list
- 91 5.1.1 Basic setting parameters ([Pr. PA_ _ ])
- 92 5.1.2 Gain/filter setting parameters ([Pr. PB_ _ ])
- 93 5.1.3 Extension setting parameters ([Pr. PC_ _ ])
- 94 5.1.4 I/O setting parameters ([Pr. PD_ _ ])
- 95 5.1.5 Extension setting 2 parameters ([Pr. PE_ _ ])
- 96 5.1.6 Extension setting 3 parameters ([Pr. PF_ _ ])
- 97 5.1.7 Option setting parameters ([Pr. Po_ _)
- 99 5.2 Detailed list of parameters
- 99 5.2.1 Basic setting parameters ([Pr. PA_ _ ])
- 106 5.2.2 Gain/filter setting parameters ([Pr. PB_ _ ])
- 115 5.2.3 Extension setting parameters ([Pr. PC_ _ ])
- 120 5.2.4 I/O setting parameters ([Pr. PD_ _ ])
- 122 5.2.5 Extension setting 2 parameters ([Pr. PE_ _ ])
- 123 5.2.6 Extension setting 3 parameters ([Pr. PF_ _ ])
- 125 5.2.7 Option setting parameters ([Pr. Po_ _)
- 126 6. TROUBLESHOOTING
- 126 6.1 Alarm and warning list
- 131 6.2 Troubleshooting at power on
- 134 7. DIMENSIONS
- 135 7.1 Servo amplifier
- 135 7.1.1 200 V class
- 144 7.1.2 400 V class
- 151 7.2 MR-J3-T10 CC-Link IE Field Network interface unit
- 152 8. OPTIONS AND PERIPHERAL EQUIPMENT
- 153 8.1 Combinations of cable/connector sets
- 155 8.2 Cable for CC-Link IE Field Network
- 156 APPENDIX
- 156 App. 1 Peripheral equipment manufacturer (for reference)
- 156 App. 2 Analog monitor
- 159 App. 3 Special specification
- 161 REVISIONS
- 162 Country/Region
- 163 Warranty