Arc defined by three points (G09). Fagor CNC 8055 para otras aplicaciones, CNC 8055 para fresadoras, CNC 8055 for milling machines, CNC 8055 for other applications
Add to My manuals468 Pages
Fagor CNC 8055 for other applications is a powerful and versatile CNC that offers a wide range of features and capabilities. Some of the most important features of the CNC 8055 are listed below. With its advanced features and capabilities, the CNC 8055 is an ideal choice for a variety of applications, including milling, turning, drilling, and engraving.
advertisement
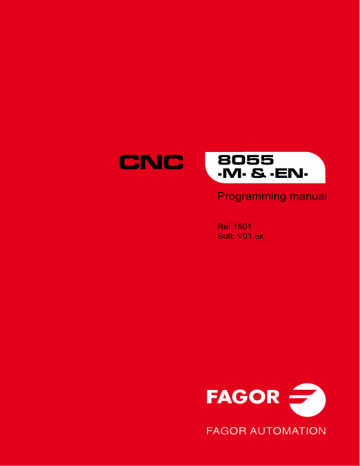
6.
Programming manual
6.6
Arc defined by three points (G09)
Through function G09 you can define an arc by programming the endpoint and an intermediate point
(the starting point of the arc is the starting point of the movement). In other words, instead of programming the coordinates of the center, you program any intermediate point.
The endpoint of the arc is defined in Cartesian or polar coordinates, and the intermediate point is always defined in Cartesian coordinates by the letters I,J, or K, each one being associated to the axes as follows:
Axes X, U, A
Axes Y, V, B
Axes Z, W, C
==>
==>
==>
I
J
K
In Cartesian coordinates:
G17 G09
Polar coordinates:
G17 G09
Example:
X±5.5
R±5.5
Y±5.5
Q±5.5
I±5.5
I±5.5
J±5.5
J±5.5
CNC 8055
CNC 8055i
·M· & ·EN· M ODELS
S OFT : V01.6
X
·90·
Being initial point X-50 Y0.
G09 X35 Y20 I-15 J25
Function G09 is not modal, so it should always be programmed if you wish to execute an arc defined by three points. Function G09 can be programmed as G9.
When G09 is programmed it is not necessary to program the direction of movement (G02 or G03).
Function G09 does not alter the history of the program. The same G01, G02 or G03 function stays active after finishing the block.
Function G09 may not be used to programmed a full circle because all three points must be different.
The CNC displays the corresponding error code.
advertisement
Key Features
- Advanced control algorithms for precise and smooth motion control
- Supports a wide range of machine configurations, including multi-axis machines
- User-friendly programming interface with graphical support
- On-board diagnostics for easy troubleshooting
- Remote monitoring and control capabilities
- Supports a variety of communication protocols
- Expandable I/O for flexible system integration
Related manuals
Frequently Answers and Questions
What is the maximum number of axes that the CNC 8055 can control?
What is the maximum feedrate that the CNC 8055 can achieve?
What is the maximum number of programs that can be stored in the CNC 8055?
advertisement
Table of contents
- 9 About the product
- 11 Declaration of conformity
- 13 Version history
- 15 Safety conditions
- 19 Warranty terms
- 21 Material returning terms
- 23 Additional remarks
- 25 Fagor documentation
- 28 Part programs
- 30 Considerations regarding the Ethernet connection
- 31 DNC connection
- 32 Communication protocol via DNC or peripheral device
- 34 Program structure at the CNC
- 34 Block header
- 35 Program block
- 36 End of block
- 38 Axis nomenclature
- 39 Axis selection
- 40 Plane selection (G16, G17, G18, G19)
- 42 Part dimensioning. Millimeters (G71) or inches (G70)
- 43 Absolute/incremental programming (G90, G91)
- 44 Coordinate programming
- 45 Cartesian coordinates
- 46 Polar coordinates
- 48 Cylindrical coordinates
- 49 Angle and Cartesian coordinate
- 50 Rotary axes
- 51 Work zones
- 51 Definition of the work zones
- 52 Using the work zones
- 53 Reference points
- 54 Machine reference (Home) search (G74)
- 55 Programming with respect to machine zero (G53)
- 56 Coordinate preset and zero offsets
- 57 Coordinate preset and S value limitation (G92)
- 58 Zero offsets (G54..G59 and G159)
- 60 Polar origin preset (G93)
- 62 Preparatory functions
- 65 Feedrate F
- 66 Feedrate in mm/min or inches/min (G94)
- 67 Feedrate in mm/rev.or inches/rev (G95)
- 68 Constant surface speed (G96)
- 69 Constant tool center speed (G97)
- 70 Spindle speed (S)
- 71 Spindle selection (G28, G29)
- 72 Synchronized spindles (G30, G77S, G78S)
- 73 Tool number (T) and tool offset (D)
- 74 Auxiliary function (M)
- 75 M00. Program stop
- 75 M01. Conditional program stop
- 75 M02. End of program
- 75 M30. End of program with return to the first block
- 75 M03, M4, M5. Spindle start and stop
- 77 M06. Tool change code
- 78 M19. Spindle orientation
- 79 M41, M42, M43, M44. Spindle gear change
- 80 M45. Auxiliary spindle / Live tool
- 81 Rapid traverse (G00)
- 82 Linear interpolation (G01)
- 83 Circular interpolation (G02, G03)
- 88 Circular interpolation with absolute arc center coordinates (G06)
- 89 Arc tangent to previous path (G08)
- 90 Arc defined by three points (G09)
- 91 Helical interpolation
- 92 Tangential entry at the beginning of a machining operation (G37)
- 93 Tangential exit at the end of a machining operator (G38)
- 94 Automatic radius blend (G36)
- 95 Chamfer (G39)
- 96 Threading (G33)
- 98 Variable pitch threads (G34)
- 99 Move to hardstop (G52)
- 100 Feedrate "F" as an inverted function of time (G32)
- 101 Tangential control (G45)
- 103 Considerations about the G45 function
- 104 G145. Temporary cancellation of tangential control
- 105 Interruption of block preparation (G04)
- 107 G04 K0: Block preparation interruption and coordinate update
- 108 Dwell (G04 K)
- 109 Working with square (G07) and round (G05,G50) corners
- 109 G07 (square corner)
- 110 G05 (round corner)
- 111 Controlled round corner (G50)
- 112 Look-ahead (G51)
- 114 Advanced look-ahead algorithm (integrating Fagor filters)
- 115 Look-ahead operation with Fagor filters active
- 116 Mirror image (G10, G11. G12, G13, G14)
- 117 Scaling factor (G72)
- 118 Scaling factor applied to all axes
- 119 Scaling factor applied to one or more axes
- 121 Pattern rotation (G73)
- 123 Electronic axis coupling/uncoupling
- 124 Electronic axis coupling, slaving, (G77)
- 125 Cancellation of the electronic axis coupling, slaving, (G78)
- 126 Axes toggle G28-G
- 128 Tool radius compensation (G40, G41, G42)
- 129 Beginning of tool radius compensation
- 132 Sections of tool radius compensation
- 133 Cancellation of tool radius compensation
- 139 Change of type of tool radius compensation while machining
- 140 Tool length compensation (G43, G44, G15)
- 142 Collision detection (G41 N, G42 N)
- 144 Canned cycle definition
- 145 Influence zone of a canned cycle
- 146 G79. Modification of the canned cycle parameters
- 148 Canned cycle cancellation
- 149 Some general points to consider
- 150 Machining canned cycles
- 153 G69. Drilling canned cycle with variable peck
- 155 Basic operation
- 158 G81. Drilling canned cycle
- 159 Basic operation
- 161 G82. Drilling canned cycle with dwell
- 162 Basic operation
- 164 G83. Deep-hole drilling canned cycle with constant peck
- 166 Basic operation
- 168 G84. Tapping canned cycle
- 170 Basic operation
- 173 G85. Reaming canned cycle
- 174 Basic operation
- 175 G86. Boring cycle with withdrawal in G
- 177 Basic operation
- 178 G87. Rectangular pocket canned cycle
- 181 Basic operation
- 184 G88. Circular pocket canned cycle
- 188 Basic operation
- 190 G89. Boring cycle with withdrawal at work feedrate (G01)
- 191 Basic operation
- 192 G210. Bore milling canned cycle
- 194 Basic operation
- 195 G211. Inside thread milling cycle
- 197 Basic operation
- 198 G212. Outside thread milling cycle
- 200 Basic operation
- 202 G60: Multiple machining in a straight line
- 203 Basic operation
- 204 G61: Multiple machining in a rectangular pattern
- 206 Basic operation
- 207 G62: Multiple machining in a grid pattern
- 209 Basic operation
- 210 G63: Multiple machining in a circular pattern
- 212 Basic operation
- 213 G64: Multiple machining in an arc
- 215 Basic operation
- 216 G65: Machining programmed with an arc-chord
- 217 Basic operation
- 221 2D pockets
- 224 Drilling operation
- 225 Roughing operation
- 228 Finishing operation
- 230 Profile programming syntax
- 231 Profile intersection
- 235 Profile programming syntax
- 237 Errors
- 239 Programming examples
- 242 3D pockets
- 246 Roughing operation
- 249 Semi-finishing operation
- 251 Finishing operation
- 254 Geometry of the contours or profiles
- 255 Profile programming syntax
- 260 Composite 3D profiles
- 263 Profile stacking
- 264 Profile programming syntax
- 266 Programming examples
- 278 Errors
- 282 Probing (G75, G76)
- 283 Probing canned cycles
- 284 PROBE 1. Tool length calibrating canned cycle
- 286 Calibrate the length or measure the length wear of a tool
- 289 Calibrate the radius or measure the radius wear of a tool
- 291 Measure or calibrate the tool radius wear and tool length wear
- 294 PROBE 2. Probe calibration canned cycle
- 296 Basic operation
- 298 PROBE 3. Surface measuring canned cycle
- 300 Basic operation
- 302 PROBE 4. Outside corner measuring canned cycle
- 303 Basic operation
- 305 PROBE 5. Inside corner measuring canned cycle
- 306 Basic operation
- 308 PROBE 6. Angle measuring canned cycle
- 309 Basic operation
- 311 PROBE 7. Corner and angle measuring canned cycle
- 312 Basic operation (measuring an outside corner)
- 314 Basic operation (measuring an inside corner)
- 316 PROBE 8. Hole measuring canned cycle
- 317 Basic operation
- 319 PROBE 9. Boss measuring canned cycle
- 320 Basic operation
- 322 PROBE 10. Rectangular part centering canned cycle
- 324 Basic operation
- 325 PROBE 11. Circular part centering canned cycle
- 327 Basic operation
- 328 PROBE 12. Tabletop probe calibration
- 333 Lexical description
- 335 Variables
- 336 General purpose parameters or variables
- 338 Variables associated with tools
- 341 Variables associated with zero offsets
- 342 Variables associated with function G
- 344 Variables associated with machine parameters
- 345 Variables associated with work zones
- 346 Variables associated with feedrates
- 348 Variables associated with coordinates
- 351 Variables associated with electronic handwheels
- 353 Variables associated with feedback
- 354 Variables associated with the main spindle
- 357 Variables associated with the second spindle
- 359 Variables associated with the live tool
- 360 PLC related variables
- 362 Variables associated with local parameters
- 363 Sercos variables
- 364 Software & hardware configuration variables
- 367 Variables associated with telediagnosis
- 370 Operating-mode related variables
- 374 Other variables
- 379 Constants
- 380 Operators
- 382 Expressions
- 382 Arithmetic expressions
- 383 Relational expressions
- 386 Assignment instructions
- 387 Display instructions
- 388 Enable-disable instructions
- 389 Flow control instructions
- 391 Subroutine instructions
- 395 Probe related instructions
- 396 Interruption-subroutine instructions
- 397 Program instructions
- 400 Kinematics related instructions
- 401 Screen customizing instructions
- 412 Movement in an inclined plane
- 413 Definition of the inclined plane (G49)
- 418 G49 in swinging spindles
- 419 G49 on Huron type spindles
- 420 Considerations about the G49 function
- 421 Variables associated with function G
- 422 Parameters associated with function G
- 423 Programming example
- 424 Movement according to the tool coordinate system (G47)
- 425 TCP Transformation (G48)
- 428 Considerations about the G48 function
- 433 Turning angular transformation on and off
- 434 Freezing the angular transformation
- 437 ISO code programming
- 439 Program control instructions
- 443 Summary of internal CNC variables
- 451 Key code
- 461 Programming assistance screens of the system
- 465 Maintenance