advertisement
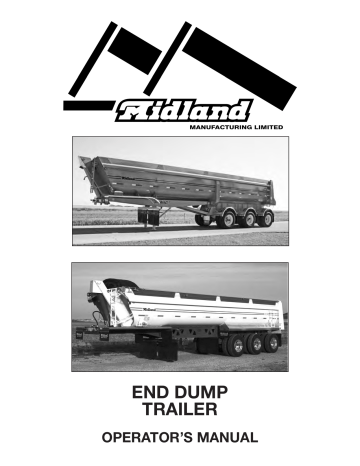
6 TROUBLE SHOOTING
A Midland End Dump Trailer uses a hydraulic cylinder on the front to raise the box for unloading. It is a simple and reliable system that requires minimal maintenance.
In the following section, we have listed problems, causes and solutions to the problems that you may encounter.
If you encounter a problem that is difficult to solve, even after having read through this trouble shooting section and through the specifically related components manufacturer's manuals. please call your local Midland dealer or distributor. Before you call, please have this Operator's Manual and the serial numbers from your trailer ready.
PROBLEM CAUSE SOLUTION
Trailer "Dog-Tracks"...
Trailer out of alignment.
Realign per procedure provided by the suspension manufacturer.
87
PROBLEM CAUSE
Tires
High or uneven tire wear.
Over or under inflation.
Loose wheel stud nuts or clamps.
Loose or tight wheel bearing.
Axle bent or out of alignment.
Tires not properly matched.
Improper acting brakes.
Rapid stopping.
Scuffed tires.
Wobbly tires.
Dog tracking.
High speed.
Over or under inflation.
Excessive speed on turns.
Tire wobble due to uneven rim clamping.
Worn or damaged wheel bearings.
Bent wheel or rim.
Bent axle.
Leaf spring broken.
Bent axle.
Frame or suspension (axles) out of alignment.
Loss of tire air pressure.
Puncture in tire.
Faulty valve or valve core.
Wheel or rim damage.
SOLUTION
Inflate to proper pressure.
Tighten wheel stud nuts or clamps.
Adjust bearings.
Straighten, align or replace axle.
Match tires.
Correct brakes as required.
Apply brakes slowly when approaching stops.
Reduce speed.
Inflate to proper pressure.
Reduce speed.
Torque tighten all rim clamps.
Replace bearings.
Replace wheel or rim.
Replace or straighten axle.
Replace leaf or complete spring.
Replace or straighten axle.
Straighten frame or align axles.
Repair or replace tire.
Replace valve assembly or core.
Replace wheel or rim.
88
PROBLEM CAUSE
Electrical
Lights flicker or do not come on.
Bad connection.
Frayed wires.
Lights flash improperly or appear to be crossed.
Battery on tractor not sufficiently charged.
Damaged or disconnected wire on ground cable.
Poor ground at sockets.
Complete loss of trailer lights.
Broken main harness.
Junction box failure.
Frayed wires.
Damaged or disconnected ground cable.
Loose or corroded connection in ground lead between tractor and trailer.
Internal short in junction box.
SOLUTION
Check electrical system circuits.
Repair as required.
Charge battery.
Repair or replace cable.
Repair as necessary.
Repair or replace.
Replace junction box.
Repair as required.
Repair or replace cable as required.
Repair or replace.
Replace junction box.
89
PROBLEM CAUSE
Air System
Excessive compressor cycling.
Air leak.
Trailer brakes slow and sluggish.
System or component failure.
SOLUTION
Check air line fittings and hose connections on service or supply line.
Check service chamber at clamp housing, push rod for damage.
Check service chamber diaphragm.
Check emergency chamber clamp and vent holes for leakage.
Repair or replace air chamber as required.
Check FFVII brake valve. Repair or replace as required.
Check slack adjuster and chamber/ spring brake push rod alignment for interference.
Assure slack adjuster and chamber/spring brake push rod angle 90° applied with proper adjustment.
Assure open lines - no kinks, bends, closed shut-off cocks, restrictions, excessive elbows.
Assure adequate tractor brake function.
Have authorized service center check for adequate pressure and timing balance relative to tractor/ trailer application.
90
PROBLEM CAUSE
Air System (cont'd)
Trailer brakes drag.
System or component failure
Trailer brakes won't apply
(service).
Park/emer brakes won't release.
System or component failure.
System or component failure.
SOLUTION
Assure emergency line maintains
120 psi pressure; check and maintain governor at max. cut-in.
Check slack adjuster and chamber/ spring brake push rod alignment for interference.
Assure slack adjuster and chamber/ spring brake push rod angle 90° applied with proper adjustment.
Assure open lines - no kinks, bends, closed shut-off cocks, restrictions, excessive elbows.
Check for trapped service air pressure at trailer service/ delivery hoses. If air pressure is noted, check for full release of all application valves (tractor/truck/ trailer).
Check air delivery to emergency system.
Check air delivery to service gladhand.
Check air delivery to air chamber or spring brake.
Check air delivery to all reservoirs at system working pressure.
Check slack adjuster and chamber/ spring brake push rod alignment for interference.
Check slack adjuster and chamber/ spring brake push rod angle 90° applied with proper adjustment.
Check air jumper hoses are not crossed between tractor and trailer.
Check air delivery to emergency gladhands exceeds 120 psi.
Check air delivery to FFV valve.
Check air delivery to all reservoirs at system working pressure.
91
PROBLEM CAUSE
Air System (cont'd)
Park/emer brakes won't release (cont'd).
System or component failure
(cont'd).
SOLUTION
Park/emer brakes won't hold.
Air reservoir leaks or loose mounting.
Semi-trailer "Runs-Up" on tractor.
Poor braking performance.
System or component failure.
System or component failure.
Check brake linkage.
Uneven brakes.
Check open lines - no kinks, bends, closed shut-off cocks, restrictions, excessive elbows.
Check that brake shoes are not frozen to drums.
Check slack adjuster and chamber/ spring brake push rod alignment for interference.
Assure slack adjuster and chamber/ spring brake push rod angle 90° applied with proper adjustment.
Replace/use rubber grommets with integral brackets.
Assure slack adjuster and chamber/spring brake push rod angle 90° applied with proper adjustment.
Check gladhand connection.
Assure open lines - no kinks, bends, closed shut-off cocks, restrictions, excessive elbows.
Have authorized service center check for adequate pressure and timing balance relative to tractor/ trailer application.
Check slack adjuster and chamber/ spring brake push rod angle 90° applied with proper adjustment.
Check slack adjuster and chamber/ spring brake push rod angle 90° applied with proper adjustment.
Check open lines - no kinks, bends, closed shut-off cocks, restrictions, excessive elbows.
Check a leak free system by applying service brake and inspecting.
92
PROBLEM CAUSE
Air System (cont'd)
Poor braking performance
(cont'd).
Trailer brake lining wear excessive.
Trailer brakes slow to apply.
Trailer service brakes slow to release.
Slack adjuster not autoadjusting.
Cracked housing.
Worn clevis pin bushing.
SOLUTION
Have authorized service center check for adequate pressure and timing balance relative to tractor/ trailer application.
Proceed per problem "trailer brakes drag."
Check slack adjuster and chamber/ spring brake push rod angle 90° applied with proper adjustment.
Check air delivery to all reservoirs at system working pressure.
Check open lines - no kinks, bends, closed shut-off cocks, restrictions, excessive elbows.
Have authorized use of "jumper hose analyser" and duplex gauge to pin-point brake imbalance.
Check functional return spring in service chamber or spring brake.
Check open lines - no kinks, bends, closed shut-off cocks, restrictions, excessive elbows.
Have authorized use of "jumper hose analyser" and duplex gauge to pin-point brake imbalance.
Check for damaged actuator rod.
Replace as required.
Slack adjuster internal components seized. Replace.
Replace slack adjuster.
Replace bushing
93
PROBLEM CAUSE
Air System (cont'd)
Poor braking performance
(cont'd).
Full function valve (FFV) leaks at exhaust port with all brakes released.
Full function valve (FFV) leaks at exhaust port with service brakes applied.
Spring parking brake (service only service chamber side of spring brake) drags or won't release.
Spring parking brake (service only service chamber side of spring brake) leaks when pressurized for park brake release.
SOLUTION
Replace FFV valve.
Replace FFV valve.
Check for:
- Improper adjustment, restriction or broken line.
- Diaphragm failure.
- System pressure too low (120 psi min).
- Improper manual release.
- Broken return spring (spring side).
- Broken power spring.
- Replace entire unit or piggy-back emergency section.
Check for:
- Ruptured spring side diaphragm.
- Hose leaks.
94
advertisement
Related manuals
advertisement
Table of contents
- 13 1 Introduction
- 14 Safety
- 15 General Safety
- 16 Operating Safety
- 16 Maintenance Safety
- 17 Unloading Safety
- 17 Travel Safety
- 18 Loading Safety
- 18 Tire Safety
- 18 Safety Signs/Decals
- 19 Sign-Off Form
- 20 Safety Sign (Decal) Locations
- 24 Operation Guidelines
- 24 To the New Operator or Owner
- 25 Terminology
- 26 Break-In
- 28 Controls
- 32 Pre-Operation Vehicle Inspection Procedure
- 35 Hooking Up/Unhooking
- 35 Hooking Up
- 37 Unhooking
- 38 End Gate
- 39 Lift Cylinder
- 40 Air System
- 40 Gate Latch Control System
- 41 Tanks
- 42 Loading/Unloading
- 47 Transporting
- 47 Operating Instructions
- 48 Braking Guidelines
- 49 Tires
- 50 Optional Equipment
- 51 Service and Maintenance
- 51 5.1 Service
- 51 Fluids and Lubricants
- 51 Greasing
- 53 Servicing Intervals
- 65 Service Record Summary (Lubrication)
- 66 Periodic Maintenance and Adjustments
- 66 Torque Specification Summary
- 68 Kingpin and Anchor Frame
- 69 Axle Alignment
- 71 Wheel Hubs/Bearings
- 75 Wheels
- 77 Tires
- 79 Brakes
- 82 Slack Adjusters
- 82 Automatic Slack Adjuster
- 83 Automatic Slack Adjuster Maintenance
- 89 Air Chamber/Spring Brake
- 90 Trailer ABS
- 91 Suspension System
- 91 Air Ride Suspension
- 95 Spring Ride Suspension
- 97 Air System
- 97 Air System Inspection
- 97 Air System Functional
- 98 Electrical System
- 99 Trouble Shooting
- 107 Bolt Torque