advertisement
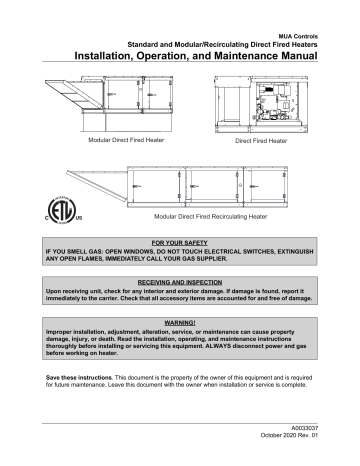
ELECTRICAL
WARNING!
Disconnect power before installing or servicing unit. High voltage electrical input is needed for this equipment. A qualified electrician should perform this work.
Before connecting power to the heater, read and understand the entire section of this document. As-built wiring diagrams are furnished with each unit by the factory. The diagrams are attached to the control module’s door or provided with paperwork packet.
National Electric Code, ANSI/NFPA 70. Verify the voltage and phase of the power supply, and the wire amperage capacity is in accordance with the unit nameplate. For additional safety information, refer to
AMCA publication 410-96, Recommended Safety Practices for Users and Installers of Industrial and
Commercial Fans.
1.
Always disconnect power before working on or near this equipment. Lock and tag the disconnect switch and/or breaker to prevent accidental power-up .
2. An electrical drop containing the line voltage power wiring is shipped with every unit. The electrical drop should be brought through one of the conduit openings located in the base of the unit (
Figure 3 on page 9 ), run through the curb, and connected to a junction box inside the building.
3. A dedicated branch circuit should supply the motor circuit with short circuit protection according to the
National Electric Code. This dedicated branch should run to the junction box.
4. Verify that the power source is compatible with the requirements of your equipment. The nameplate identifies the proper phase and voltage of the equipment.
5. Units shipped with a remote HMI will require a second drop through the base of the unit. It is important to route the motor wires in a separate conduit from the HMI wiring. Refer to
Figure 7 (Recirc) on page 11 .
6. Before connecting the unit to the building’s power source, verify that the power source wiring is deenergized. Refer to
“Fan to Building Wiring Connection” on page 16 .
7. Secure the power cable to prevent contact with sharp objects.
8. Do not kink power cable and never allow the cable to encounter oil, grease, hot surfaces, or chemicals.
9. Before powering up the unit, make sure that the fan rotates freely. Make sure that the interior of the unit is free of loose debris or shipping materials.
10. If any of the original wire supplied with the unit must be replaced, it must be replaced with type THHN wire or equivalent.
Table 6 - Copper Wire Ampacity
Wire Size AWG
3
2
6
4
1
14
12
10
8
Maximum Amps
65
85
100
115
130
15
20
30
50
15
Fan to Building Wiring Connection
Figure 11 - Wiring Connection Details
120V 1 PH.
1
Single Point Connection
208-240V 1 PH.
1
208-240/460/600V 3 PH.
1
2 2 2
3
4
BK WH GR
1. Disconnect Switch
2. Galflex Conduit (In Unit)
2
120V 1 PH.
1
3 3
4
BK
4
RD
WIRE COLOR
GR BK BK BK GR
BK - BLACK
RD - RED
WH - WHITE
GR - GREEN
3. Factory Wiring
4. Field Supplied Wiring - From building power or pre-wired control panel.
2
120V Optional
208-240V 1 PH.
1
208-240/460/600V 3 PH.
1
2
5
3
5
3
6
5
3
7
4 4
4
RD WH BK WH GR RD WH BK
1. Disconnect Switch
2. Galflex Conduit (In Unit)
3. Factory Wiring
4. Field Supplied Wiring - From building power or pre-wired control panel.
RD
WIRE COLOR
GR RD WH BK BK BK GR
BK - BLACK
RD - RED
WH - WHITE
GR - GREEN
5. 120V Single Phase Standing Power
6. 208-240 Single Phase
7. Three Phase
16
SL
SL
LLT
LLT
ICT
ICT
OCT
OCT
CDT
CDT
RT
OT
OT
DT
DT
ST
ST
IT
IT
RT
Make-up Air (MUA) Board Connectors
The Make-up Air (MUA) Board (
) is located in the main control cabinet.
Figure 12 - Make-up Air Board
J20 J21
Power Vent
Neutral
J19 J17
Power
Vent
Hot
Power
Vent
Hot
24V
DC
0-10
VIN
COM
COM
24V
DC
0-10
VIN
COM
COM
24V
AC
24V
AC
IN
COM
24V
AC
0-10
VIN
COM
COM
24V
AC
0-10
VIN
COM
COM
24V
AC
24V
AC
IN
COM
J39
PS1
1
CASLink BMS Slave
Pilot
Gas
Spark
Alarm
Blower
Burn
Hi
Temp
Aux
1 J11 8 1 J16 8 1 J25 3
R C DDC
C
HMI VFD Master
Y G BAS/STAT
17
Note: Some connections may not be used dependent on system configurations
RJ45 connectors.
Connector J1 and J2 are associated with BMS.
Connector J3 through J6 are interchangeable and may be used to connect to an HMI or VFD.
J1 - CASLink/Slave
J2 - CASLink/Slave
J3 - HMI/VFD/Master
J6
J4 - HMI/VFD/Master
J5 - HMI/VFD/Master
J6 - HMI/VFD/Master
J2
J5
J1
J4 J3
Connector J7 contains inputs and outputs for the
Flame Safety Controller (FSC)
9
18
Pin 1 - N/A
Pin 2 - 24VAC Pilot Valve
Pin 3 through Pin 8 - N/A
Pin 9 - 24VAC Common to Main/Pilot Gas Valve
Pin 10 through Pin 18 - N/A
1
10
Connector J8 contains inputs and outputs for the
Flame Safety Controller (FSC)
NOTE: Connector J8 only for Compact Models
9
18
Pin 1 - N/A
Pin 2 - 24VAC Pilot Valve
Pin 3 through Pin 8 - N/A
Pin 9 - 24VAC Common to Main/Pilot Gas Valve
Pin 10 through Pin 18 - N/A
1
10
Connector J9 contains 120V AC connections 1 8
Pin 1 - 120VAC Main Input
Pin 2 - 120VAC Input from Discharge Damper End
Switch
Pin 3 - 120VAC Input from Fire Micro-Switch
Pin 4 - 120VAC Output to Intake/Discharge Damper
Actuator
Pin 5 - 120VAC Input from Intake Damper End
Switch
Pin 6 - N/A
Pin 7 - 120VAC Output to Cabinet Heater
Pin 8 - 120VAC Neutral
18
Connector J10 contains 120V AC connections 1 8
Pin 1 - 120VAC Input from Evap Cooler Pressure
Switch
Pin 2 - 120VAC Input from Evap Cooler Float
Switch
Pin 3 - 120VAC Output to Evap Cooler Water
Solenoid
Pin 4 - 120VAC Output to Evap Cooler 3-way Drain
Valve
Pin 5 - 120VAC Input from Supply Overload
Pin 6 - 120VAC Output to Supply Starter Coil
Pin 7 - 120VAC Output to Exhaust Starter Coil
Pin 8 - 120VAC Input from Exhaust Overload
1 8
Connector J11 contains low voltage screw terminal connections
Pin 1
Pin 2
Pin 3
Pin 4
- 24VAC Auxiliary Input
- 24VAC Auxiliary Input
- 24VAC Auxiliary Input
- 24VAC Call for Heat Input
W Y G BAS/STAT
Pin 5 - 24VAC Call for Cooling Input
Pin 6 - 24VAC Call for Blower Input
Pin 7 - 24VAC Occupied Override Input
Pin 8 - 24VAC Isolated Common
1 8
Connector J12 contains low voltage screw terminal connections
Pin 1
Pin 2
Pin 3
Pin 4
- 24VAC Output to Smoke Detector
- 24VAC Output to Smoke Detector
- 24VAC Digital Input from Smoke Detector
- 24VAC Common to Smoke Detector
24V AC 24V AC
DI-1
24V AC
AI-1
Pin 5 - 24VAC Output to Air Quality Sensor
Pin 6 - 0-10V Analog Input from Air Quality Sensor
Pin 7 - 24VAC Common to Air Quality Sensor
Pin 8 - 24VAC Common to Air Quality Sensor
19
Connector J13 contains low voltage connections
7
14
1
10
Pin 1 - N/A
Pin 2 - PWM + Output for Supply ECM
Pin 3 - 24VAC Output for Low Gas Pressure Switch
Pin 4 - 24VAC Output for High Gas Pressure Switch
Pin 5 - 24VAC Output for Clogged Filter Switch
Pin 6 - 24VAC Output for Low Airflow
Pin 7 - 24VAC Input for Board Power
Pin 8 - N/A
Pin 9 - PWM Output for Supply ECM
Pin 10 - 24VAC Input from Low Gas Pressure
Switch
Pin 11 - 24VAC Input from High Gas Pressure
Switch
Pin 12 - 24VAC Input from Clogged Filter Switch
Pin 13 - 24VAC Input from Low Air Pressure Switch
Pin 14 - 24VAC for Board Power
1 8
Connector J14 contains screw terminal connections
24V DC
AI-2
24V DC
AI-3
Pin 1 - 24VAC Output to Humidity Sensor
Pin 2 - 0-10VDC Analog Input from Humidity Sensor
Pin 3 - 24VAC Common to Humidity Sensor
Pin 4 - 24VAC Common to Humidity Sensor
Pin 5 - 24VAC Output to Humidity Sensor
Pin 6 - 0-10VDC Analog Input VFD/Humidity Sensor
Pin 7 - 24VAC Common VFD/Humidity Sensor
Pin 8 - 24VAC Common to Humidity Sensor
1 10
Connector J15 contains low voltage connections
Pin 1
Pin 2
Pin 3
Pin 4
Pin 5
- Intake Temperature Thermistor Input
- Intake Temperature Thermistor Input
- Return Temperature Thermistor Input
- Return Temperature Thermistor Input
- Outdoor Temperature Thermistor Input
THERMISTORS
Pin 6 - Outdoor Temperature Thermistor Input
Pin 7 - Discharge Temperature Thermistor Input
Pin 8 - Discharge Temperature Thermistor Input
Pin 9 - Space Temperature Thermistor Input
Pin 10 - Space Temperature Thermistor Input
20
1 8
Connector J16 contains low voltage screw terminal connections
BAS/STAT
Pin 1 - 0-10VDC Analog Input for Heat Modulation
Pin 2 - 4-20 mA Analog Input for Heat Modulation
Pin 3 - 24VAC Common
Pin 4 - 24VAC Common
Pin 5
Pin 6
Pin 7
Pin 8
- 24VAC Unit Interlock Input
- 24VAC Output (Stat)
- 24VAC Output (R)
- 24VAC Common
NOTE: Connector J17 is grouped with connectors J-19 through J-21
R C
Connector J18 contains low voltage connections
7
14
1
10
Pin 1 - 24VDC + Output
Pin 2 - 0-10VDC Analog Output for Mixing Box
Actuator
Pin 3 - 0-10VDC Analog Output for Bypass Damper
Pin 4 - 24VAC Output for DX Float Switch
Pin 5 - 24VAC Output for Door Interlock
Pin 6 - 24VAC Warm Liquid Bypass Output
Pin 7 - 24VAC for Damper Actuator
Pin 8 - 24VDC - Common
Pin 9 - Common for Mixing Box Actuator
Pin 10 - Common for Bypass Damper
Pin 11 - 24VAC Input from DX Float Switch
Pin 12 - 24VAC Input from Door Interlock
Pin 13 - 24VAC Warm Liquid Bypass Output
Common
Pin 14 - 24VAC for Damper Actuator
J20 J21
Connector J17 - N/A
Connector J19 - N/A
Connector J20 - N/A
Connector J21 - N/A
J19 J17
21
Connector J22 (Y1) Condenser 1
Connector J23 (Y2) Condenser 2
Connector J24 (Y3) Condenser 3
2 1
2 1
2 1
J22
J23
J24
J22 Pin 1 - 24VAC Output to Condenser 1
J22 Pin 2 - 24VAC Common to Condenser 1
J23 Pin 1 - 24VAC Output to Condenser 2
J23 Pin 2 - 24VAC Common to Condenser 2
J24 Pin 1 - 24VAC Output to Condenser 3
J24 Pin 2 - 24VAC Common to Condenser 3
1
Connector J25 contains low voltage screw terminal connections for DDC Communications Isolated
Pin 1 RS-485 +
Pin 2 RS-485 -
+ -
DDC
C
Pin 3 RS-485 Common
3
Connector J26 Programming Port
1
2
USB
Connector J27 USB Programming Port
1 8
Connector J28 contains low voltage screw terminal connections
Pin 1
Pin 2
Pin 3
Pin 4
- 24VAC Start Command for 3rd-Party VFD
- 24VAC Output
- 24VAC Trouble Input
- 24VAC Common for 3rd-Party VFD
24V AC 24V AC
DI-2
24V AC
AI-4
Pin 5 - 24VAC Constant Output
Pin 6 - 0-10VDC Analog Input VFD Speed
Reference
Pin 7 - 24VAC Common
Pin 8 - 24VAC Common
22
Connector J29 contains 120V AC connections
Pin 1 - 120VAC Blower Service Switch Input
Pin 2 - 120VAC Burner Service Switch Input
Pin 3 - 120VAC High Temp Limit Input
Pin 4 - 120VAC Output to FSC (6)
1
Pin 5 - 120VAC Output to FSC (7)
Pin 6 - N/A
Pin 7 - N/A
Pin 8 - 120VAC Neutral
8
Connector J30 contains 120V AC connections 1 8
Pin 1 - 120VAC Input from Pilot Gas FSC (3)
Pin 2 - 120VAC Pilot Gas Output - Connected to
J30-1
Pin 3 - 120VAC Input from Spark FSC (4)
Pin 4 - 120VAC Spark Output
Pin 5 - 120VAC Input from Main Gas FSC (5)
Pin 6 - 120VAC Main Gas Output - Connected to
J30-5
Pin 7 - 120VAC Alarm Input from FSC (A)
Pin 8 - 120VAC Alarm Output
Connector J31 - Contains inputs and outputs for components
9
18
1
10
Pin 1 - 24VDC + Output to Profile / Main Air Flow
Pressure Sensor
Pin 2 - 0-10VDC Analog Input from Profile / Main Air
Flow Pressure Sensor
Pin 3 - 24VDC/0-10VDC Common from Profile /
Main Air Flow Pressure Sensor
Pin 4 - N/A
Pin 5 - N/A
Pin 6 - N/A
Pin 7 - 24VDC + Output to Manifold Gas Pressure 1
Sensor
Pin 8 - 0-10VDC Analog Input from Manifold Gas
Pressure 1 Sensor
Pin 9 - 24VDC/0-10VDC Common from Manifold
Gas Pressure 1 Sensor
Pin 10 - 24VDC + output to Manifold Gas Pressure
2 Sensor
Pin 11 - 0-10VDC Analog Input from Manifold Gas
Pressure 2 Sensor
Pin 12 - 24VDC/0-10VDC Common from Manifold
Gas Pressure 2 Sensor
Pin 13 - 24VDC + output to Clogged Filter Pressure
Sensor
Pin 14 - 0-10VDC Analog Input from Clogged Filter
Pressure Sensor
Pin 15 - 24VDC/0-10VDC Common from Clogged
Filter Pressure Sensor
Pin 16 - 24VDC + Output for Analog or Static
Pressure Control for Blower/Damper
Pin 17 - 0-10VDC Analog Input for Analog or Static
Pressure Control for Blower/Damper
Pin 18 - 24VDC/0-10VDC Common for Analog or
Static Pressure Control for Blower/Damper
23
Connector J32 contains inputs and outputs for components
9
18
1
10
Pin 1 - N/A
Pin 2 - N/A
Pin 3 - 24VAC Output for Proof Of Closure
Pin 4 - N/A
Pin 5 - 24VAC Output To CO Alarm
Pin 6 - 0-24VDC + Analog Input from Flame Sensor
Pin 7 - 24VDC Powered PWM to Modulating Gas
Valve, Full Wave, 16 kHz
Pin 8 - 0-10VDC Out for VFD
Pin 9 - N/A
Pin 10 - N/A
Pin 11 - N/A
Pin 12 - 24VAC Input from Proof of Closure
Pin 13 - N/A
Pin 14 - 24VAC From CO Alarm
Pin 15 - 24VDC Common From Flame Sensor
Pin 16 - 24VDC Powered PWM to Modulating Gas
Valve, Full Wave, 16 kHz
Pin 17 - 0-10VDC Common for VFD
Pin 18 - N/A
Connector J33 contains inputs and outputs for components
Pin 1 through 8 - N/A
Pin 9 - 0-10VDC Analog Input for CFM
9
18
Pin 10 through 17 - N/A
Pin 18 - 0-10VDC Common for CFM
1
10
Connector J34 - N/A
2 1
4 3
1 10
Connector J35 N/A
THERMISTORS
24
Connector J36 N/A
9
18
Connector J37 N/A
2 1
4 3
MODBUS
C B A
Connector J38 Modbus
3
Pin 3 (C) Modbus Ground
1
Pin 1 (A) Modbus (-)
Pin 2 (B) Modbus (+)
ON
Dip Switch S1
1 2 3 4
Switch 1, 2, 3 always OFF. Switch 4 Always ON. If Switch 4 is OFF, BAS terminals disabled.
1
10
25
Dip Switch S2
Programming - Service Only
Dip Switch S3
End of line termination
Dip Switch S4
Programming - Service Only
ON
26
HMI and Remote Room Sensor Installation
Remote HMI faceplates (
, remote room sensors (
), and smart controls may be ordered and shipped separately. These components measure temperature and assist in controlling the unit. These components should be installed in a safe location, free of influence from external heat sources.
Install sensors in areas indicative of the average room temperature, and away from heat-producing appliances. HMIs and remote room sensors can be installed directly to industry-standard junction boxes, either surface mounted or recessed mounted. HMIs have a built-in temperature/relative humidity (RH) sensor, which is typically used to help control the automatic function of the unit.
The HMI can also be configured to control the unit from a remote location manually. They can be configured not to use the internal temperature/relative humidity sensor. In this configuration, the sensor in the HMI is ignored in automatic operation. Multiple HMIs can be connected to one unit for temperature and
R/H averaging. All combination temperature/humidity HMIs will use a vented standoff. Mount the static pressure tube close to the HMI to obtain proper room conditions.
A max of 4 additional HMIs can be daisy-chained together. Place an End-of-Line (EOL) device in the last
HMI connected.
Figure 13 - HMI with Standoff
HMI Standoff
J-Box
Route static pressure tube close to the HMI in the space.
Static Pressure Tube
Connected to the High Pressure
Port on Pressure Sensor
5-1/2”
Cat 5 Connection
J1 on HMI-1 to J2 on HMI-2
HMI with Built-in
Temperature/Humidity
Sensor
5-1/2”
The room temperature sensor is a 10K ohm thermistor. The sensor provides constant room temperature to the controller.
It should be installed on a wall somewhere in the room, but not directly in the HVAC diffuser’s path or close to heatproducing appliances so that the reading is not affected by heat.
Room sensors are not required for proper control operation, but still can be configured as remote sensors or averaging sensors.
Do not install the room sensor on the ceiling .
Figure 14 - Remote Room Sensor
27
Temperature Control
Discharge Control : When used in discharge control, the MUA board receives a call to heat from the intake sensor. The MUA board will modulate the discharge temperature until the desired setpoint is reached. The user can choose whether discharge heating/cooling is activated based on intake temperature, space temperature, either, or both.
Space Control : When selected, an HMI with an internal temperature sensor or a temperature sensor wired to ST terminals on the MUA board can be used to sense space temperature. The user can choose whether the space heating/cooling is activated based on intake temperature, space temperature, either, or both.
Analog Control : If Analog Control is utilized, DIP switch #4 on the MUA board should be set On. Blower/
Heating/Cooling will be controlled by a 0-10V DC or 0-20mA signal based on input source.
Direct Digital Control (DDC) : A 0-10V DC or 0-20mA signal is sent to the MUA board from the building control system to regulate the blower/heating output of the unit.
In all cases, the MUA board controls the amount of gas to the burner based on the signal from the temperature control components.
The operation of the modulating gas valve with regard to voltage is as follows: from 0 volts to approximately 5 volts, the modulating gas valve should be on bypass flow with the heater operating on low or minimum fire. From approximately 5 volts to 15 volts DC, the valve should be performing its modulating function, and the heater should be firing at a modulated flow rate between low and high fire, depending upon the voltage. Above approximately 15 volts DC, the valve should be delivering full flow to the heater and the unit should be on high fire.
control board.
Figure 15 - Temperature Sensor
ECM (Electronically Commutated Motor) Speed Control
EC motors with control allow accurate adjustment of fan speed. The benefit of EC motors is exceptional efficiency, performance, and motor life.
External PWM Signal
The fan unit will be shipped with power wiring and communication wiring fed to an internal junction box.
The fan is shipped with Shielded Twisted Pair (STP) wire, which is used for wiring to a remote PWM signal.
Red wire is used to go to the positive PWM signal, and black wire is used to go to the negative PWM signal.
Reference schematics for all wiring connections. STP is connected to the communication wiring of the motor using wire nuts in the junction box. If a preset length of STP is provided, it will be connected to the junction box from the factory. Run the STP through any available knockout in the fan base.
28
advertisement
Related manuals
advertisement
Table of contents
- 3 WARRANTY
- 3 Listings
- 3 Patents
- 4 INSTALLATION
- 4 Mechanical
- 7 Curb and Ductwork
- 9 Roof Mount Installation
- 9 Installation with Exhaust Fan
- 10 Duct Mount Installation
- 10 Indoor (Inline) Installation
- 11 Roof Mount Installation - Recirculation Unit
- 11 Indoor (Inline) Installation Recirculation Unit
- 12 Heat Module Add-On Installation
- 13 Gas
- 15 ELECTRICAL
- 16 Fan to Building Wiring Connection
- 17 Make-up Air (MUA) Board Connectors
- 27 HMI and Remote Room Sensor Installation
- 28 Temperature Control
- 28 ECM (Electronically Commutated Motor) Speed Control
- 28 External PWM Signal
- 29 OPERATION
- 29 Accessing Menu Configurations
- 29 Remote (HMI) Control Panel
- 29 HMI Notification Letters
- 30 HMI Configuration Menu
- 30 Communication
- 30 Advanced Options
- 30 Status
- 30 About
- 31 Scheduling
- 31 Fan Speed and Damper Position Presets
- 32 Unit Options
- 32 Building Signal Damper Control
- 32 Electric Cabinet Heater
- 32 Motorized Intake Damper
- 32 Mixing Box Control Unit Options
- 33 Menu Descriptions
- 41 Menu Tree
- 49 Variable Frequency Drive (VFD)
- 50 VFD Installation
- 50 Input AC Power
- 50 VFD Output Power
- 51 VFD Programming
- 52 ACTECH SMV VFD
- 53 START-UP OPERATION
- 53 Start-up Procedure
- 54 Pulley Adjustment
- 55 Pulley Alignment/Proper Belt Tension
- 56 Pulley Combination Chart
- 57 Air Flow Sensor
- 58 Modulating Gas System
- 58 High Temperature Limit
- 58 Pilot Adjustment
- 59 Main Burner Adjustment
- 60 Final Start-up Procedure
- 61 Sequence of Operation
- 61 Flame Safety Control
- 63 Components
- 64 Network
- 64 BACnet
- 65 LonWorks
- 66 Device Instance, MAC Address, Baud Rate
- 67 Changing the IP Address
- 68 DDC Control Points
- 72 DDC Fault List
- 73 Troubleshooting
- 74 Burner Troubleshooting
- 75 HMI Fault Codes
- 78 VFD Fault List
- 78 Resetting Unit
- 79 MAINTENANCE
- 79 General Maintenance
- 79 2 Weeks After Start-up
- 79 Every 3 Months
- 79 Yearly
- 80 Burner Maintenance
- 80 Unit Filters
- 81 Emergency Shutdown of Unit
- 81 Prolonged Shutdown of Unit
- 84 Start-Up Documentation