- No category
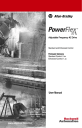
advertisement
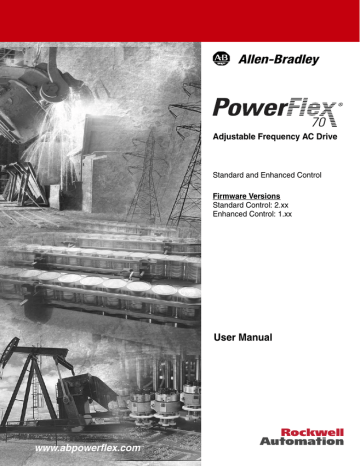
Overview
Drive Frame Sizes
Similar PowerFlex 70 drive sizes are grouped into frame sizes to simplify spare parts ordering, dimensioning, etc. A cross reference of drive catalog numbers and their respective frame size is provided in
.
General Precautions
P-3
!
!
!
!
!
!
ATTENTION: This drive contains ESD (Electrostatic Discharge) sensitive parts and assemblies. Static control precautions are required when installing, testing, servicing or repairing this assembly.
Component damage may result if ESD control procedures are not followed. If you are not familiar with static control procedures, reference A-B publication 8000-4.5.2, “Guarding Against Electrostatic
Damage” or any other applicable ESD protection handbook.
ATTENTION: An incorrectly applied or installed drive can result in component damage or a reduction in product life. Wiring or application errors, such as, undersizing the motor, incorrect or inadequate AC supply, or excessive ambient temperatures may result in malfunction of the system.
ATTENTION: Only qualified personnel familiar with adjustable frequency AC drives and associated machinery should plan or implement the installation, start-up and subsequent maintenance of the system. Failure to comply may result in personal injury and/or equipment damage.
ATTENTION: To avoid an electric shock hazard, verify that the voltage on the bus capacitors has discharged before performing any work on the drive. Measure the DC bus voltage at the +DC terminal of
the Power Terminal Block and the -DC test point (refer to Chapter 1
for locations). The voltage must be zero.
ATTENTION: Risk of injury or equipment damage exists. DPI or
SCANport host products must not be directly connected together via
1202 cables. Unpredictable behavior can result if two or more devices are connected in this manner.
ATTENTION: A risk of injury or equipment damage exists in firmware version 1.011 and earlier. When there is a combination of long shielded motor cables, high source impedance, low speed, light motor load and parameter 190 [Direction Mode] is set to “Unipolar” or
“Bipolar,” an unexpected change in motor direction may occur. If these conditions exist, choose one of the following corrective actions:
• Set parameter 190 to “Reverse Dis”
• Set parameters 161 and 162 to “Disabled”
• Install a properly sized Dynamic Brake resistor
P-4
Overview
!
!
ATTENTION: Nuisance tripping may occur in firmware version
1.011 and earlier due to unstable currents. When using a motor that is connected for a voltage that is different from the drive (e.g., using a
230V connected motor with a 460V drive) the following adjustment must be made to “Stability Gain” using DriveExplorer software and a personal computer.
Motor Nameplate Voltage
Drive Rated Voltage
×
128
Any adjustment made to “Stability Gain” must be manually restored if the drive is reset to defaults or is replaced.
If unstable currents are still present after making the adjustment, contact the factory for assistance.
ATTENTION: The “adjust freq” portion of the bus regulator function is extremely useful for preventing nuisance overvoltage faults resulting from aggressive decelerations, overhauling loads, and eccentric loads.
It forces the output frequency to be greater than commanded frequency while the drive’s bus voltage is increasing towards levels that would otherwise cause a fault; however, it can also cause either of the following two conditions to occur.
1. Fast positive changes in input voltage (more than a 10% increase within 6 minutes) can cause uncommanded positive speed changes; however an “OverSpeed Limit” fault will occur if the speed reaches
[Max Speed] + [Overspeed Limit]. If this condition is unacceptable, action should be taken to 1) limit supply voltages within the specification of the drive and, 2) limit fast positive input voltage changes to less than 10%. Without taking such actions, if this operation is unacceptable, the “adjust freq” portion of the bus regulator function must be disabled (see parameters 161 and 162).
2. Actual deceleration times can be longer than commanded deceleration times; however, a “Decel Inhibit” fault is generated if the drive stops decelerating altogether. If this condition is unacceptable, the
“adjust freq” portion of the bus regulator must be disabled (see parameters 161 and 162). In addition, installing a properly sized dynamic brake resistor will provide equal or better performance in most cases.
Note: These faults are not instantaneous and have shown test results that take between 2 and 12 seconds to occur.
advertisement
* Your assessment is very important for improving the workof artificial intelligence, which forms the content of this project
Related manuals
advertisement
Table of contents
- 7 Who Should Use this Manual?
- 7 What Is Not in this Manual
- 8 Reference Materials
- 8 Manual Conventions
- 9 Drive Frame Sizes
- 9 General Precautions
- 11 Catalog Number Explanation
- 13 Opening the Cover
- 14 Mounting Considerations
- 15 AC Supply Source Considerations
- 16 General Grounding Requirements
- 17 Fuses and Circuit Breakers
- 17 Power Wiring
- 21 IP66 (NEMA Type 4X/12) Installations
- 22 Using Input/Output Contactors
- 22 Disconnecting MOVs and Common Mode Capacitors
- 24 I/O Wiring
- 30 Speed Reference Control
- 31 Auto/Manual Examples
- 32 EMC Instructions
- 35 Prepare For Drive Start-Up
- 36 Status Indicators
- 37 Start-Up Routines
- 38 Running S.M.A.R.T. Start
- 38 Running an Assisted Start Up
- 39 About Parameters
- 41 How Parameters are Organized
- 49 Monitor File (File A)
- 51 Motor Control File (File B)
- 54 Speed Command File (File C)
- 61 Dynamic Control File (File D)
- 67 Utility File (File E)
- 75 Communication File (File H)
- 79 Inputs & Outputs File (File J)
- 85 Parameter Cross Reference - by Name
- 87 Faults and Alarms
- 88 Drive Status
- 89 Manually Clearing Faults
- 89 Fault Descriptions
- 93 Clearing Alarms
- 93 Alarm Descriptions
- 96 Testpoint Codes and Functions
- 96 Common Symptoms and Corrective Actions
- 99 Specifications
- 101 Communication Configurations
- 104 Dimensions
- 111 Output Devices
- 111 Drive, Fuse & Circuit Breaker Ratings
- 115 External and Internal Connections
- 116 LCD Display Elements
- 116 ALT Functions
- 116 Removing the HIM
- 117 Menu Structure
- 119 Viewing and Editing Parameters
- 121 External Brake Resistor
- 122 Skip Frequency
- 124 Stop Mode
- 126 Motor Overload
- 127 Start At PowerUp
- 128 Overspeed
- 129 Process PI for Standard Control
- 132 Voltage Tolerance