- No category
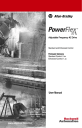
advertisement
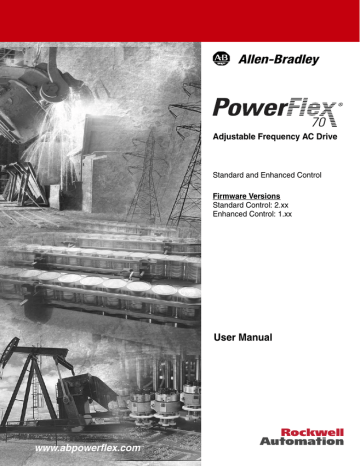
Programming and Parameters
3-23
No. Parameter Name and Description
137 [PI Error Meter]
Present value of the PI error.
138 [PI Output Meter]
Present value of the PI output.
460
461
462
463
E C
[PI Reference Hi]
Scales the upper value of [PI Reference
Sel] of the source.
E C
[PI Reference Lo]
Default:
Min/Max:
Units:
Default:
Scales the lower value of [PI Reference
Sel] of the source.
E C
[PI Feedback Hi]
Scales the upper value of [PI Feedback] of the source.
E C
[PI Feedback Lo]
Min/Max:
Units:
Default:
Min/Max:
Units:
Default:
Scales the lower value of [PI Feedback] of the source.
Min/Max:
Units:
Values
Default:
Min/Max:
Units:
Default:
Min/Max:
Units:
Read Only
–/+100.00%
0.01%
Read Only
–/+100.0 Hz
–/+800.0%
0.1 Hz
0.1%
E C
E C
100.0%
–/+100.0%
0.1%
–100.0%
–/+100.0%
0.1%
100.0%
–/+100.0%
0.1%
0.0%
–/+100.0%
0.1%
Dynamic Control File (File D)
thru
thru
No. Parameter Name and Description
140
141
[Accel Time 1]
[Accel Time 2]
Sets the rate of accel for all speed increases.
Max Speed
Accel Time
=
Accel Rate
142
143
[Decel Time 1]
[Decel Time 2]
Sets the rate of decel for all speed decreases.
Max Speed
Decel Time
=
Decel Rate
Values
Default:
Min/Max:
Units:
Default:
Min/Max:
Units:
146 [S Curve %] Default:
Sets the percentage of accel or decel time that is applied to the ramp as S Curve.
Time is added, 1/2 at the beginning and
1/2 at the end of the ramp.
Min/Max:
Units:
10.0 Secs
10.0 Secs
0.1/3600.0 Secs
0.1 Secs
10.0 Secs
10.0 Secs
0.1/3600.0 Secs
0.1 Secs
0.0%
0.0/100.0%
0.1%
thru
thru
thru
3-24
Programming and Parameters
No. Parameter Name and Description
147 [Current Lmt Sel]
Selects the source for the adjustment of current limit (i.e. parameter, analog input, etc.).
148 [Current Lmt Val]
Defines the current limit value when
[Current Lmt Sel] = “Cur Lim Val.”
Values
Default:
Options:
Default:
Min/Max:
Units:
Default: 149 [Current Lmt Gain]
Sets the responsiveness of the current limit.
150 [Drive OL Mode]
Min/Max:
Units:
Default:
Selects the drive’s response to increasing drive temperature.
Options:
0 “Cur Lim Val”
0
1
2
“Cur Lim Val”
“Analog In 1”
“Analog In 2”
[Rated Amps]
× 1.5
(Equation yields approximate default value.)
Drive Rating Based
0.1 Amps
250
0/5000
1
3 “Both–PWM 1st”
2
3
0
1
4 kHz
“Disabled”
“Reduce CLim”
“Reduce PWM”
“Both–PWM 1st”
2/10 kHz
2/12 kHz
1 kHz
E C
151 [PWM Frequency]
189
Default:
Sets the carrier frequency for the PWM output. Drive derating may occur at higher carrier frequencies. For derating information, refer to the PowerFlex
Reference Manual.
Min/Max:
Units:
E C
[Shear Pin Time]
Default:
145
Sets the time that the drive is at or above current limit before a fault occurs. Zero disables this feature.
E C
[DB While Stopped]
Enables/disables dynamic brake operation.
Min/Max:
Units:
Default:
Options:
155
156
Disabled = DB will only operate when drive is running.
Enable = DB operates whenever drive is energized.
[Stop Mode A]
[Stop Mode B]
Default:
Default:
Active stop mode. [Stop Mode A] is active unless [Stop Mode B] is selected by inputs.
(1)
When using options 1 or 2, refer to the
Attention statements at [DC Brake
Level].
Options:
2
3
0
1
1
0
0
0
1
0.0 Secs
0.0/30.0 Secs
0.1 Secs
“Disabled”
“Disabled”
“Enabled”
“Ramp”
“Coast”
“Coast”
“Ramp”
(1)
“Ramp to Hold”
(1)
“DC Brake”
!
ATTENTION: If a hazard of injury do to movement of equipment or material exists, an auxiliary mechanical braking device must be used.
Programming and Parameters
3-25
No. Parameter Name and Description
157 [DC Brake Lvl Sel]
Selects the source for [DC Brake Level].
Values
Default:
Options:
158 [DC Brake Level] Default:
Defines the DC brake current level injected into the motor when “DC Brake” is selected as a stop mode.
The DC braking voltage used in this function is created by a PWM algorithm and may not generate the smooth holding force needed for some applications. Refer to the PowerFlex Reference Manual.
Min/Max:
Units:
0 “DC Brake Lvl”
0
1
2
“DC Brake Lvl”
“Analog In 1”
“Analog In 2”
[Rated Amps]
0/[Rated Amps]
× 1.5
(Equation yields approximate maximum value.)
0.1 Amps
!
ATTENTION: If a hazard of injury due to movement of equipment or material exists, an auxiliary mechanical braking device must be used.
ATTENTION: This feature should not be used with synchronous or permanent magnet motors. Motors may be demagnetized during braking.
159 [DC Brake Time] Default:
Sets the amount of time DC brake current is “injected” into the motor.
Min/Max:
Units:
0.0 Secs
0.0/90.0 Secs
0.1 Secs
thru
160
Standard
E C
[Bus Reg Gain]
[Bus Reg Ki]
Sets the responsiveness of the bus regulator.
Default:
Min/Max:
Units:
450
0/5000
1
3-26
Programming and Parameters
No. Parameter Name and Description
161
162
[Bus Reg Mode A]
[Bus Reg Mode B]
Values
Default:
Sets the method and sequence of the DC bus regulator voltage. Choices are dynamic brake, frequency adjust or both.
Sequence is determined by programming or digital input to the terminal block.
Options:
Dynamic Brake Setup
If a dynamic brake resistor is connected to the drive, both these parameters must be set to either option 2, 3 or 4.
Refer to the Attention statement on page
for important information on bus regulation.
2
3
0
1
4
1
4
“Adjust Freq”
“Both-Frq 1st”
“Disabled”
“Adjust Freq”
“Dynamic Brak”
“Both-DB 1st”
“Both-Frq 1st”
!
ATTENTION: The drive does not offer protection for externally mounted brake resistors. A risk of fire exists if external braking resistors are not protected. External resistor packages must be self-protected from over temperature or the protective circuit shown
in Figure C.1 on page C-1 (or equivalent) must be supplied.
163 [DB Resistor Type] Default:
Selects whether the internal or an external DB resistor will be used.
If a dynamic brake resistor is connected to the drive, [Bus Reg Mode x], A, B or Both
(if used), must be set to either option 2, 3 or 4.
Options: 0
1
2
0
2
“Internal Res”
“None”
E C
“Internal Res”
“External Res”
“None”
!
ATTENTION: The drive does not offer protection for externally mounted brake resistors. A risk of fire exists if external braking resistors are not protected. External resistor packages must be self-protected from over temperature or the protective circuit shown
in Figure C.1 on page C-1 , or equivalent, must be supplied.
ATTENTION: Equipment damage may result if a drive mounted
(internal) resistor is installed and this parameter is set to “External
Res.” Thermal protection for the internal resistor will be disabled, resulting in possible device damage.
164
165
E C
[Bus Reg Kp]
Default:
Proportional gain for the bus regulator.
Used to adjust regulator response.
E C
[Bus Reg Kd]
Min/Max:
Units:
Default:
Derivative gain for the bus regulator. Used to control regulator overshoot.
Min/Max:
Units:
1500
0/10000
1
1000
0/10000
1
Programming and Parameters
3-27
No. Parameter Name and Description
167
E C
[Powerup Delay]
Values
Default:
Defines the programmed delay time, in seconds, before a start command is accepted after a power up.
168 [Start At PowerUp]
Min/Max:
Units:
Default:
Enables/disables a feature to issue a Start or Run command and automatically resume running at commanded speed after drive input power is restored.
Requires a digital input configured for Run or Start and a valid start contact.
Options:
0
0
1
0.0 Secs
0.0/30.0 Secs
0.1 Secs
“Disabled”
“Disabled”
“Enabled”
!
ATTENTION: Equipment damage and/or personal injury may result if this parameter is used in an inappropriate application. Do not use this function without considering applicable local, national and international codes, standards, regulations or industry guidelines.
169 [Flying Start En]
Enables/disables the function which reconnects to a spinning motor at actual
RPM when a start command is issued.
170 [Flying StartGain]
Default:
Options:
Default:
Sets the response of the flying start function.
Min/Max:
Units:
Default: 174 [Auto Rstrt Tries]
Sets the maximum number of times the drive attempts to reset a fault and restart.
Min/Max:
Units:
0
0
1
“Disabled”
“Disabled”
“Enabled”
4000
20/32767
1
0
0/9
1
!
ATTENTION: Equipment damage and/or personal injury may result if this parameter is used in an inappropriate application. Do not use this function without considering applicable local, national and international codes, standards, regulations or industry guidelines.
175 [Auto Rstrt Delay]
Sets the time between restart attempts when [Auto Rstrt Tries] is set to a value other than zero.
Default:
Min/Max:
Units:
1.0 Secs
0.5/30.0 Secs
0.1 Secs
3-28
Programming and Parameters
No. Parameter Name and Description
184 [Power Loss Mode]
Values
Default:
Sets the reaction to a loss of input power.
Power loss is recognized when:
• DC bus voltage is ð 73% of [DC Bus
Memory] and [Power Loss Mode] is set to “Coast”.
• DC bus voltage is ð 82% of [DC Bus
Memory] and [Power Loss Mode] is set to “Decel”.
Options:
185 [Power Loss Time] Default:
Sets the time that the drive will remain in power loss mode before a fault is issued.
Min/Max:
Units:
0
0
1
2
“Coast”
“Coast”
“Decel”
“Continue”
0.5 Secs
0.0/60.0 Secs
0.1 Secs
E C
advertisement
* Your assessment is very important for improving the workof artificial intelligence, which forms the content of this project
Related manuals
advertisement
Table of contents
- 7 Who Should Use this Manual?
- 7 What Is Not in this Manual
- 8 Reference Materials
- 8 Manual Conventions
- 9 Drive Frame Sizes
- 9 General Precautions
- 11 Catalog Number Explanation
- 13 Opening the Cover
- 14 Mounting Considerations
- 15 AC Supply Source Considerations
- 16 General Grounding Requirements
- 17 Fuses and Circuit Breakers
- 17 Power Wiring
- 21 IP66 (NEMA Type 4X/12) Installations
- 22 Using Input/Output Contactors
- 22 Disconnecting MOVs and Common Mode Capacitors
- 24 I/O Wiring
- 30 Speed Reference Control
- 31 Auto/Manual Examples
- 32 EMC Instructions
- 35 Prepare For Drive Start-Up
- 36 Status Indicators
- 37 Start-Up Routines
- 38 Running S.M.A.R.T. Start
- 38 Running an Assisted Start Up
- 39 About Parameters
- 41 How Parameters are Organized
- 49 Monitor File (File A)
- 51 Motor Control File (File B)
- 54 Speed Command File (File C)
- 61 Dynamic Control File (File D)
- 67 Utility File (File E)
- 75 Communication File (File H)
- 79 Inputs & Outputs File (File J)
- 85 Parameter Cross Reference - by Name
- 87 Faults and Alarms
- 88 Drive Status
- 89 Manually Clearing Faults
- 89 Fault Descriptions
- 93 Clearing Alarms
- 93 Alarm Descriptions
- 96 Testpoint Codes and Functions
- 96 Common Symptoms and Corrective Actions
- 99 Specifications
- 101 Communication Configurations
- 104 Dimensions
- 111 Output Devices
- 111 Drive, Fuse & Circuit Breaker Ratings
- 115 External and Internal Connections
- 116 LCD Display Elements
- 116 ALT Functions
- 116 Removing the HIM
- 117 Menu Structure
- 119 Viewing and Editing Parameters
- 121 External Brake Resistor
- 122 Skip Frequency
- 124 Stop Mode
- 126 Motor Overload
- 127 Start At PowerUp
- 128 Overspeed
- 129 Process PI for Standard Control
- 132 Voltage Tolerance