- No category
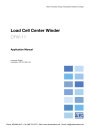
advertisement
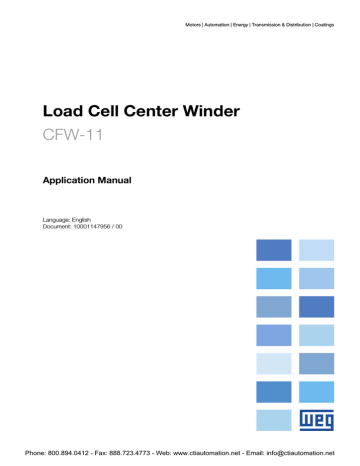
General Notes
10 GENERAL NOTES
Some points must be verified in order to assure a good performance of the considered winder. Some of these points are listed next.
Analog signals: The analog signals used in the applicative (web tension feedback via load cell, web tension setpoint, process line speed and roll diameter measurement) are of extreme importance for the winder good operation. It is important to examine how and where the analog signal cable passes until reaching the CFW-11 frequency inverter, verifying the grounding and cabling quality. Therefore, it is important to analyze the oscillation level of the signal and how much this oscillation interferes with the winder control. In order to evaluate this oscillation, there is the trend of the “Analog Inputs” in the trend variable dialogs, which contains the application analog input readings. Another factor that must not be forgotten is the resolution of the analog inputs; being 12 bits for AI1 and AI3, and 11 bits + sign for AI2 and AI4 (the AI4 of the IOA-01 expansion board has a 14 bit resolution). Observe also the precision of the equipments that are sending these signals to the CFW-11.
Another important analysis variable is the value of the low-pass first-order filter time constant. Ideal values are around 100 ms to 300 ms, because they act as signal filters and do not transmit delays to the control.
Regarding the web tension external feedback signals, it is important to observe their correct operation and the positioning of their components, because if they were not correctly installed, they will transmit false signals and this will have a negative effect on the winder control.
When using load cells it is recommended that:
■
The embracing angle be equal or bigger than 60 %;
■
They are not mounted in a place where the web position varies, because this would be perceived by the load cells as a variation in the tension;
■
Two load cells be used for the measurement, thus assuring that the force applied on the sensor roller be totally indicated, regardless of the point where the force is applied;
■
The surfaces for mounting the load cells be flat and parallel;
■
The value transmitted to the control never is the output with filter, because the signal transducers normally have two outputs, one with filter for display and another without filter to be used for the control.
CFW-11 Configuration: In order to get a good winder applicative performance, it is necessary first to evaluate the CFW-11 no load response, i.e., to observe its parameterization and the values estimated with the autotuning in the vector with encoder control mode. It is important to consider the motor overheating problem when operating at low speeds and beyond the nominal speed.
In order to evaluate the response in vector mode, in the trend variable dialogs, there is the “CFW-11 Regulators” trend that contains the motor speed reading in rpm, and the speed (Iq*) and flux (Id*) regulator outputs. Verify the response of these signals in several speeds and analyze them based on an acceptable average 2 % control oscillation. It is worthwhile to remind that in the Vector with Encoder mode, only the Iq* acts and Id* remains more stable. If bigger oscillations are present, it becomes necessary to adjust the speed regulator (Iq*) and flux regulator (Id*) parameters, according to their response, always beginning with the one that oscillates more.
NOTE!
Due to the load cell center winder control by using the variable motor torque calculated by the
Inverter CFW-11 and this depends on the rated motor current and its magnetization current, at times, when it requires a web tension setpoint for controlling below 10%, it is necessary to reduce the value of the magnetization current (P0410) in order that the speed regulator, which is responsible for the torque current, has more scope for control over the total motor current. This value can be 10 to 30% less than the value calculated by the CFW-11 inverter.
PID Controller: After the verification of the analog signals and the CFW-11 response in the winder control, it will be necessary to adjust the PID controller gains. This PID has the function of controlling the web tension, as has been seen previously in the description of each winder type. In the standard applicative, there are values that have been used in some applications. There are several factors, such as gearbox ratio, maximum line speed, winder inertia, type of wound web, among others, which influence the PID controller gain values. Due to this, there will be normally corrections in the values indicated in the standard applicative, where they must serve as starting values for the winder adjustment.
Load Cell Center Winder | 70
Phone: 800.894.0412 - Fax: 888.723.4773 - Web: www.ctiautomation.net - Email: [email protected]
General Notes
In order to monitor the PID control action, in the trend variable dialogs, there is the “PID Controller Settings” trend that contains the PID controller variable readings. In order to start the settings, the derivative gain must be set zero, so that it does not interfere in the process. Start increasing the proportional gain and monitoring the web tension feedback response, if it gets worse, reduce the gain and verify the improvement in the response.
After finding the value where the response does not improve nor deteriorate any longer, proceed with the integral gain in the same way as for the proportional. If after this there are still undesirable oscillations or a response delay during accelerations and decelerations, then adjust the default value for the derivative gain, always starting with small values (0,010) to avoid oscillations in the system. For the derivative gain, proceed in the same way as for the other gains. After this, it may be necessary to redo some small adjustments in the gains.
Another important factor for the PID adjustment is its sampling time. This value is introduced by the parameter directly in the PID block of the WLP applicative and it must always be longer than the program scan cycle that can be visualized in P1002.
CANopen Network: A center winder is normally not alone in a machine or application. For instance, in a plastic web extruder we have the motors for the extruder screws, the pull roller, the pre drag and the center winders.
In order to control the entire application process, we can use the CFW-11 frequency inverter optional board
PLC-11, because it allows interconnecting all the drives through a CANopen communication network. This board will be assembled on one of the CFW-11 frequency inverters, thus enabling it to be the CANopen network master.
The WLP programming software allows the user to implement the control and interlocking logics necessary for the application control; and the WSCAN configuration and programming software makes the configuration and operation of the equipments in the CANopen network possible.
See below the CANopen network configuration executed via WSCAN with the inverters used in the application example mentioned above, where the PLC11 board was fitted on the pull roller. A remote unit for the acquisition of digital and analog points was also included.
Figure 10.1 – Example of CANopen network configuration on the software WSCAN
NOTE!
Refer to the help topics in the WLP and WSCAN programming software for more information.
NOTE!
In the application example mentioned above, we can also interconnect the inverter DC link, obtaining with this a reduction of energy consumption of the machine due to the regeneration process from the unwinder, and also only use a braking resistor for the entire application, and be installed on this unwinding, which is usually the highest power inverter drive.
Load Cell Center Winder | 71
Phone: 800.894.0412 - Fax: 888.723.4773 - Web: www.ctiautomation.net - Email: [email protected]
advertisement
* Your assessment is very important for improving the workof artificial intelligence, which forms the content of this project
Related manuals
advertisement
Table of contents
- 6 ABOUT THE MANUAL
- 6 ABBREVIATIONS AND DEFINITIONS
- 6 NUMERICAL REPRESENTATION
- 7 1. INTRODUCTION TO CENTER WINDERS
- 7 1.1 WINDING
- 7 1.2 CENTER WINDER CONCEPT
- 8 1.3 TERMS USED IN CENTER WINDERS
- 11 1.4 GENERAL CHARACTERISTICS OF THE CENTER WINDER APPLICATIVE
- 12 2 LOAD CELL CENTER WINDER
- 12 2.1 TORQUE LIMIT MODE
- 15 2.2 TORQUE MODE
- 18 2.3 SPEED MODE
- 21 3 WLP APPLICATIVE CONFIGURATION
- 33 4 WLP APPLICATIVE DOWNLOAD
- 34 5 PARAMETERS DESCRIPTION
- 34 5.1 CENTER WINDER CHARACTERISTICS
- 34 5.2 ORIGIN OF THE COMMANDS
- 35 5.3 RAMPS
- 35 5.4 SPEED LIMITS
- 36 5.5 DYNAMIC BRAKING
- 36 5.6 WINDER CONTROL CONFIGURATION
- 37 5.7 PID CONTROLLER
- 39 5.8 MOTOR TORQUE CURRENT REFERENCE
- 40 5.9 CONTROL WORD
- 41 5.10 DIGITAL INPUTS
- 45 5.11 DIGITAL OUTPUTS
- 46 5.12 ANALOG INPUTS
- 52 5.13 WEB TENSION VIA LOAD CELL
- 52 5.14 WEB TENSION SETPOINT
- 53 5.15 LINE SPEED
- 54 5.16 ROLL DIAMETER
- 58 5.17 TAPER FUNCTION
- 58 5.18 STALL MODE
- 59 5.19 WEB PRESENCE DETECTION IN WINDER
- 60 5.20 READING PARAMETERS
- 62 6 FAULT AND ALARM MESSAGES
- 63 7 MONITORING DIALOGS
- 67 8 TREND VARIABLES DIALOGS
- 69 9 PARAMETER VALUE DIALOGS
- 70 10 GENERAL NOTES