advertisement
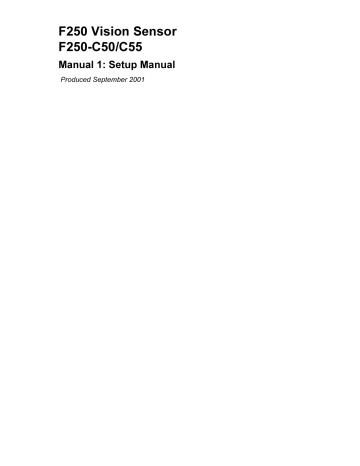
)9LVLRQ6HQVRU
)&&
0DQXDO6HWXS0DQXDO
3URGXFHG6HSWHPEHU
iv
Notice:
OMRON products are manufactured for use according to proper procedures by a qualified operator and only for the purposes described in this manual.
The following conventions are used to indicate and classify precautions in this manual. Always heed the information provided with them. Failure to heed precautions can result in injury to people or damage to property.
!DANGER
Indicates an imminently hazardous situation which, if not avoided, will result in death or serious injury.
!WARNING
Indicates a potentially hazardous situation which, if not avoided, could result in death or serious injury.
!Caution
Indicates a potentially hazardous situation which, if not avoided, may result in minor or moderate injury, or property damage.
OMRON Product References
All OMRON products are capitalized in this manual. The word “Unit” is also capitalized when it refers to an OMRON product, regardless of whether or not it appears in the proper name of the product.
Visual Aids
The following headings appear in the left column of the manual to help you locate different types of information.
Note Indicates information of particular interest for efficient and convenient operation of the product.
1,2,3...
,QGLFDWHVOLVWVRIRQHVRUWRUDQRWKHUVXFKDVSURFHGXUHVFKHFNOLVWVHWF
Precaution Indicates information required to take full advantage of the functions and performance of the product. Incorrect application methods may result in the loss of damage or damage to the product. Read and follow all precautionary information.
CHECK Indicates points that are important in using product functions or in application procedures.
TwoCamera Indicates information required when using a 2-camera system.
SeeAlso Indicates where to find related information.
HELP Indicates information helpful in operation, such as the definition of terms.
¸
OMRON, 2001
All rights reserved. No part of this publication may be reproduced, stored in a retrieval system, or transmitted, in any form, or by any means, mechanical, electronic, photocopying, recording, or otherwise, without the prior written permission of OMRON.
No patent liability is assumed with respect to the use of the information contained herein. Moreover, because OMRON is constantly striving to improve its high-quality products, the information contained in this manual is subject to change without notice. Every precaution has been taken in the preparation of this manual. Nevertheless, OMRON assumes no responsibility for errors or omissions. Neither is any liability assumed for damages resulting from the use of the information contained in this publication. v
TABLE OF CONTENTS
PRECAUTIONS . . . . . . . . . . . . . . . . . . . . . . . . . . . . . . . . . . . . . xi
1 Special or Critical Applications. . . . . . . . . . . . . . . . . . . . . . . . . . . . . . . . . . . . . xii
2
3
General Safety Precautions . . . . . . . . . . . . . . . . . . . . . . . . . . . . . . . . . . . . . . . . xii
Regulations and Standards. . . . . . . . . . . . . . . . . . . . . . . . . . . . . . . . . . . . . . . . . xiii
SECTION 1
Introduction. . . . . . . . . . . . . . . . . . . . . . . . . . . . . . . . . . . . . . . . . . 1
1-1 Installation Precautions . . . . . . . . . . . . . . . . . . . . . . . . . . . . . . . . . . . . . . . . . . . . 2
1-2 Confirming Package Contents . . . . . . . . . . . . . . . . . . . . . . . . . . . . . . . . . . . . . . . 6
1-3 Product Availability . . . . . . . . . . . . . . . . . . . . . . . . . . . . . . . . . . . . . . . . . . . . . . . 6
SECTION 2
Special Features, Installation, and Connections . . . . . . . . . . . . 7
2-1 Special Features . . . . . . . . . . . . . . . . . . . . . . . . . . . . . . . . . . . . . . . . . . . . . . . . . . 8
2-2 Basic System Configuration . . . . . . . . . . . . . . . . . . . . . . . . . . . . . . . . . . . . . . . 12
2-3 Component Names and Functions . . . . . . . . . . . . . . . . . . . . . . . . . . . . . . . . . . . 14
2-4 Mounting the Controller . . . . . . . . . . . . . . . . . . . . . . . . . . . . . . . . . . . . . . . . . . 15
2-5 Connecting Peripheral Devices . . . . . . . . . . . . . . . . . . . . . . . . . . . . . . . . . . . . . 17
2-6 Power Supply and Ground . . . . . . . . . . . . . . . . . . . . . . . . . . . . . . . . . . . . . . . . . 19
SECTION 3
Lenses, Lighting, and Memory Cards. . . . . . . . . . . . . . . . . . . . 21
3-1 CCTV Lenses. . . . . . . . . . . . . . . . . . . . . . . . . . . . . . . . . . . . . . . . . . . . . . . . . . . 22
3-2 Lighting . . . . . . . . . . . . . . . . . . . . . . . . . . . . . . . . . . . . . . . . . . . . . . . . . . . . . . . 25
3-3 Memory Cards . . . . . . . . . . . . . . . . . . . . . . . . . . . . . . . . . . . . . . . . . . . . . . . . . . 27
SECTION 4
Connecting External Devices . . . . . . . . . . . . . . . . . . . . . . . . . . . 29
4-1 Connecting through the Parallel Interface . . . . . . . . . . . . . . . . . . . . . . . . . . . . . 30
4-2 Connecting through the Serial Interface . . . . . . . . . . . . . . . . . . . . . . . . . . . . . . 37
SECTION 5
Troubleshooting and Maintenance . . . . . . . . . . . . . . . . . . . . . . 43
5-1 Troubleshooting . . . . . . . . . . . . . . . . . . . . . . . . . . . . . . . . . . . . . . . . . . . . . . . . . 44
5-2 Maintenance. . . . . . . . . . . . . . . . . . . . . . . . . . . . . . . . . . . . . . . . . . . . . . . . . . . . 46
5-3 Regular Inspections . . . . . . . . . . . . . . . . . . . . . . . . . . . . . . . . . . . . . . . . . . . . . . 49
5-4 Specifications. . . . . . . . . . . . . . . . . . . . . . . . . . . . . . . . . . . . . . . . . . . . . . . . . . . 50
5-5 F200/F300 Camera Parameters . . . . . . . . . . . . . . . . . . . . . . . . . . . . . . . . . . . . . 68
5-6 Connecting a Strobe Device . . . . . . . . . . . . . . . . . . . . . . . . . . . . . . . . . . . . . . . 70
Index. . . . . . . . . . . . . . . . . . . . . . . . . . . . . . . . . . . . . . . . . . . . . . . 71
Revision History . . . . . . . . . . . . . . . . . . . . . . . . . . . . . . . . . . . . . 73 vii
$ERXWWKLV0DQXDO
This manual describes the hardware for the F250 Vision Sensor and how to install the components, and it includes the sections described below. This is one of two manuals used to operate the F250. Refer to the following table for the contents of each manual.
Manual
1: Setup Manual
Contents
Provides information on system hardware and installation. Be sure to read this manual first.
2: Operation Manual
(on CD-ROM)
The Operation Manual CD-ROM is packed with the
F250-UME Application Software. This manual explains basic operations such as installing the Application Software, setting up inspection processes, and communicating with external devices.
Cat. No.
SCHB-736A
Z153-E1-01
Please read the above manuals carefully and be sure you understand the information provided before attempting to install or operate the F250.
Section 1 Introduction describes the precautions that must be taken when installing and operating the F250 Vision Sensor.
Section 2 Special Features, Installation, and Connections shows a basic F250 system configuration and explains how to install the F250 and connect it to a power supply and peripheral devices.
Section 3 Lenses, Lighting, and Memory Cards describes how to select and use these components most effectively.
Section 4 Connecting External Devices describes how to connect external devices through a parallel interface (the parallel connectors) or serial interface (the RS-232C/RS-
422 connector or Ethernet connector).
Section 5 Troubleshooting and Maintenance provides tables to help identify and correct hardware errors that may occur with the F250 as well as information on maintenance and periodic inspections.
!WARNING
Failure to read and understand the information provided in this manual may result in personal injury or death, damage to the product, or product failure. Please read each section in its entirety and be sure you understand the information provided in the section and related sections before attempting any of the procedures or operations given.
ix
PRECAUTIONS
This section provides general precautions for using the F250 Vision Sensor.
The information contained in this section is important for the safe and reliable application of the F250
Vision Sensor. You must read this section and understand the information contained before attempting to set up or operate an F250 Vision Sensor.
1
2
3
Special or Critical Applications. . . . . . . . . . . . . . . . . . . . . . . . . . . . . . . . . . . .
General Safety Precautions . . . . . . . . . . . . . . . . . . . . . . . . . . . . . . . . . . . . . . .
Regulations and Standards. . . . . . . . . . . . . . . . . . . . . . . . . . . . . . . . . . . . . . . .
xii xii xiii xi
Special or Critical Applications
1 Special or Critical Applications
1
When the F250 will be used in one of the conditions or applications listed below, allow extra safety margins in ratings and functions, add extra safety features such as fail-safe systems, and consult your OMRON representative.
• Operating conditions or environments which are not described in the manual
• Nuclear power control systems, railroad systems, aviation systems, vehicles, combustion systems, medical equipment, amusement equipment, or safety equipment
• Other systems, machines, and equipment that may have a serious influence on lives and property and require extra safety features
2 General Safety Precautions
Battery Precautions
!WARNING
Do not disassemble the F250, apply pressure to the F250 that would deform its shape, or incinerate the F250. A lithium battery is built into the F250 and it may combust, explode, or burn if not treated properly.
!WARNING
Do not short circuit, attempt to charge, disassemble, apply pressure that would deform, or incinerate the lithium battery. The lithium battery may start a fire, explode, or burn if not treated properly.
Installation Environment Precautions
!Caution
Do not use the F250 in environments with flammable or explosive gases.
!Caution
Install the F250 away from high-voltage devices and moving machinery to allow safe access during operation and maintenance.
!Caution
Install the F250 so that air can flow freely through its cooling vents. If the vents are blocked, heat will build up in the Controller and may cause burns.
Intake vent Exhaust vent
!Caution
Be sure to securely tighten the screws when mounting the F250.
Power Supply and Wiring Precautions
!Caution
Use the F250 with the power supply voltages specified in this manual.
!Caution
Use the wire and crimp terminals of the proper sizes as specified in this manual. Do not connect the power supply wires by just twisting stranded wire and connecting directly to the terminals.
!Caution
Use a DC power supply with countermeasures against high-voltage spikes
(safe extra low-voltage circuits on the secondary side).
xii
Regulations and Standards
Note 1.
Keep the power supply wires as short as possible (Max. 10 m).
2.
Ground the F250’s ground terminal to less than 100
W
.
3.
Use a grounding point as close as possible to the F250 and keep the ground line as short as possible.
4.
Wire the F250 to the ground with a separate ground wire. To avoid grounding problems, do not share the ground wiring with any other devices or ground the F250 to the building’s steel framing/plumbing.
3
Other Precautions
!Caution
Do not attempt to dismantle, repair, or modify the F250.
!Caution
Do not touch fluorescent or halogen lights while the power is ON or immediately after the power is turned OFF. These lights get very hot and can cause burns.
!Caution
If you suspect an error or malfunction, stop using the F250 immediately, turn
OFF the power supply, and consult your OMRON representative.
Note Dispose of the F250 as industrial waste.
3 Regulations and Standards
The F250 complies with the EC Directive and EN standard below.
1.
EC Directives
EMC Directive: No. 89/336/EEC
2.
EN Standards (European Standards)
EN 61326: 1997/Annex A+A1: 1998 (EMI: Class A) xiii
SECTION 1
Introduction
This section describes the precautions that must be taken when installing and operating the F250 Vision Sensor.
1-1 Installation Precautions. . . . . . . . . . . . . . . . . . . . . . . . . . . . . . . . . . . . . . . . . .
1-1-1 Controller Installation. . . . . . . . . . . . . . . . . . . . . . . . . . . . . . . . . . . .
1-1-2 Component Installation and Handling . . . . . . . . . . . . . . . . . . . . . . .
1-2 Confirming Package Contents . . . . . . . . . . . . . . . . . . . . . . . . . . . . . . . . . . . .
1-3 Product Availability . . . . . . . . . . . . . . . . . . . . . . . . . . . . . . . . . . . . . . . . . . . .
4
6
2
2
6
1
Installation Precautions Section 1-1
1-1 Installation Precautions
The F250 is highly reliable and resistant to most environmental factors. The following guidelines, however, must be followed to ensure reliability and optimum use of the F250.
!Caution
Read the Precautions section before proceeding with installation or operation.
1-1-1 Controller Installation
Installation Site
Do not install the F250 in locations subject to the following conditions:
1,2,3...
1.
Ambient temperatures outside of the 0 to 50
C (32 to 122
F) range
2.
Rapid temperature fluctuations (likely to cause condensation)
3.
Relative humidities outside of the 35% to 85% range
4.
Presence of corrosive or flammable gases
5.
Presence of dust, salt, or iron particles
6.
Direct vibration or shock
7.
Direct sunlight
8.
Water, oil, or chemical fumes or spray
Orientation of Controller
To improve heat dissipation, install the Controller in the following orientation only. For proper air flow, provide at least 20 mm of clearance above the Controller and at least 50 mm of clearance on both sides.
• Horizontal Installation
CORRECT
Do not install the Controller upside down as shown in the following diagram.
INCORRECT
2
Installation Precautions Section 1-1
• Vertical Installation
The Controller can be installed vertically with the air intake at the bottom and exhaust at the top. For proper air flow, provide at least 20 mm of clearance at the top of the Controller and at least 50 mm of clearance on both sides (the intake and exhaust sides).
CORRECT INCORRECT
Exhaust Intake
Intake Exhaust
Ambient Temperature
1,2,3...
1.
For proper air flow, maintain a minimum clearance of 20 mm at the top of the F250 and at least 50 mm of clearance at the sides where the cooling air intake and exhaust are located.
2.
Do not install the F250 immediately above significant heat sources, such as heaters, transformers, or large-capacity resistors.
3.
Do not let the ambient operating temperature exceed 50
C (122
F).
4.
Provide a forced-air fan cooling or air conditioning if the ambient temperature is near 50
C (122
F) so that the ambient temperature never exceeds
50 C (122 F).
Control panel
F250
Louver
3
Installation Precautions Section 1-1
Noise Resistance
Use the following measures to help increase noise resistance.
1,2,3...
1.
Do not install the F250 in a cabinet containing high-voltage equipment.
2.
Do not install the F250 within 200 mm of power cables.
Power lines
200 mm min.
200 mm min.
F250
1-1-2 Component Installation and Handling
OMRON Components
Use a Camera, Camera Cable, and Console designed specifically for the
F250.
Connecting Cables
Always turn OFF the F250’s power before connecting or disconnecting a camera or cable.
Handling the Camera
The Camera’s case is connected to the 0V line in the internal circuits. Observe the following precautions to prevent noise interference.
1,2,3...
1.
Do not ground the Camera.
2.
Do not remove the base attached to the Camera.
3.
Do not remove the ferrite core attached to the F150-VS or F160-VSR @@
Camera Cable.
Securing the Video Monitor (When Using the Recommended F150-M09)
Observe the following precautions to prevent noise interference, because the video monitor case is connected to the 0V line in the internal circuits.
1,2,3...
1.
Do not ground the video monitor.
2.
Do not ground the metallic part of the connector.
3.
Secure the video monitor with plastic screws if it is being mounted to a metallic surface.
Touching Signal Lines
To prevent damage from static electricity, use a wrist strap or another device for preventing electrostatic discharges when touching terminals or signal lines in connectors.
Handling the Memory Card
• To prevent damage from static electricity, do not touch the Memory Card directly while it is installed in the F250.
• To remove a Memory Card, turn OFF the power supply to the Card (using the menu command) or turn OFF the F250. Press the eject button to eject the Card. The Memory Card or the F250 itself may be damaged if a Memory Card is removed while power is being supplied.
Note F250-UME Precautions
It will not be possible to start the Setup Menu if you change the contents of the
Memory Card after installing it in a personal computer or other device. Never
4
Installation Precautions Section 1-1 change the contents of the Card with operations such as the following:
• Changing file names
• Moving or deleting files
• Overwriting data
• Formatting
Turning OFF the Power
Do not turn OFF the power while a message is being displayed indicating that processing is being performed. Data in memory will be corrupted, and the
F250 may not operate correctly the next time it is started.
0.Scn 0 MON ---- ---ms
Saving data.
Using the RESET Signal
Do not use the RESET input immediately after power is turned ON. When using the RESET input to synchronize startup timing, wait at least 1 second after the F250's power supply is turned ON before turning ON the RESET signal.
Replacing the Battery
The F250 is equipped with a battery that backs up the clock. When the battery is low, the message “BATTERY LOW” will be displayed on the monitor at startup. The battery must be replaced when this message is displayed. Return the
F250 to your OMRON dealer for service. (The battery is not user-serviceable.)
The battery will last approximately 7 years.
5
Confirming Package Contents Section 1-2
1-2 Confirming Package Contents
Check the contents of the package as soon as you receive the F250. It is extremely rare for components to be missing, but contact the nearest OMRON representative if any of the following items are missing.
1,2,3...
1.
F250 Vision Mate Controller Qty.: 1
2.
Ferrite core for F150-KP Console or F160-KP Console
Ferrite core for F150-VM Monitor Cable
Qty: 1
Qty: 1
3.
Setup Manual (this manual) Qty.: 1
CHECK The F250 Vision Sensor Manual 2: Operation Manual (on CD-ROM) is packed with the F250-UME Application Software.
1-3 Product Availability
Some of the products listed may not be available in some countries. Please contact your nearest OMRON sales office by referring to the addresses provided at the back of this manual.
6
SECTION 2
Special Features, Installation, and Connections
This section describes some of the special features of the F250, shows a basic F250 system configuration, and explains how to install and wire the F250.
2-1 Special Features . . . . . . . . . . . . . . . . . . . . . . . . . . . . . . . . . . . . . . . . . . . . . . .
2-1-1 Problems Solved with a New Algorithm . . . . . . . . . . . . . . . . . . . . .
2-1-2 Simple and Flexible Inspection Settings . . . . . . . . . . . . . . . . . . . . .
2-1-3 Smooth Switching between Processes . . . . . . . . . . . . . . . . . . . . . . .
2-2 Basic System Configuration . . . . . . . . . . . . . . . . . . . . . . . . . . . . . . . . . . . . . .
2-3 Component Names and Functions . . . . . . . . . . . . . . . . . . . . . . . . . . . . . . . . .
2-4 Mounting the Controller . . . . . . . . . . . . . . . . . . . . . . . . . . . . . . . . . . . . . . . . .
2-4-1 Horizontal Mounting . . . . . . . . . . . . . . . . . . . . . . . . . . . . . . . . . . . .
2-4-2 Vertical Mounting . . . . . . . . . . . . . . . . . . . . . . . . . . . . . . . . . . . . . . .
2-5 Connecting Peripheral Devices. . . . . . . . . . . . . . . . . . . . . . . . . . . . . . . . . . . .
2-5-1 Connecting a Console. . . . . . . . . . . . . . . . . . . . . . . . . . . . . . . . . . . .
2-5-2 Connecting a Monitor. . . . . . . . . . . . . . . . . . . . . . . . . . . . . . . . . . . .
2-5-3 Connecting a Camera . . . . . . . . . . . . . . . . . . . . . . . . . . . . . . . . . . . .
2-6 Power Supply and Ground . . . . . . . . . . . . . . . . . . . . . . . . . . . . . . . . . . . . . . .
2-6-1 Crimp Terminals and Cables . . . . . . . . . . . . . . . . . . . . . . . . . . . . . .
2-6-2 Ground (Earth) Wiring . . . . . . . . . . . . . . . . . . . . . . . . . . . . . . . . . . .
2-6-3 Wiring the Power Supply . . . . . . . . . . . . . . . . . . . . . . . . . . . . . . . . .
17
17
17
17
19
19
19
20
15
15
16
11
11
12
14
8
9
7
Special Features Section 2-1
2-1 Special Features
The F250 Vision Sensor uses a camera instead of the human eye to process images and inspect products. Visual inspections can be automated to perform complicated inspections quickly and accurately.
There were problematic cases in which Vision Sensors could not detect differences that could be detected by the human eye. The F250 is a high-performance Vision Sensor that solves many of these problems.
8
Special Features
2-1-1 Problems Solved with a New Algorithm
EC Defect Inspection
Detect minute damage, dirt, or deformation!
Good Chipped
Dirt on a deformed ring
Section 2-1
Quest Optical Character Verification
Verify expiration data and lot number!
Detect incorrect font size/ style as well as errors.
Good
01.01.28
It is possible to inspect for different font styles and sizes.
Size
Width
Interrupted
01.01.28
01.01.28
Italic
01.01.28
Blurred
Bold
01.01.28
01.01.28
01.01.28
9
Special Features
EC Positioning
Very precise positioning and positioning of lowcontrast objects.
Positioning mark Low contrast Internal defect
Section 2-1
Fine matching
Inspect for blurred characters or graphics!
Find differences from the model image.
Model image Measured image
Minute dirt Omission
The F250 has many other inspection processes in its line-up.
Dirt on design
Chip on edge
10
Special Features Section 2-1
2-1-2 Simple and Flexible Inspection Settings
First, install the required inspection processes from the Application Software
Memory Card.
F250-UME Application Software
Processes in the menu can be combined freely.
0.Scn 0=SET=
0.Camera image
1.EC pos. comp
2.Fine matching
3.Binary defect
4.DO data
5.
ENT:Set SFT+ESC:Edit
2-1-3 Smooth Switching between Processes
The scene function can be used to set up to 32 different inspections. When the inspection requirements change, the inspection process can be changed just by changing the scene. Up to 1,024 scenes can be stored on a 128-MB Memory Card.
11
Basic System Configuration Section 2-2
2-2 Basic System Configuration
The following diagram shows the basic F250 system configuration.
Precaution Some of the components shown in the configuration diagram are special
OMRON products that cannot be substituted with comparable devices. These items are indicated with an asterisk.
Monitor
Monitor with
S-VIDEO input
F150-M05L Color
LCD Monitor
F150-M09 Monochrome
CRT Video Monitor
(RCA plug input)
Use the Monitor to check images and display the condition-setting menus.
S-VIDEO Input Cable
(Use a standard cable.)
(BNC input)
BNC Jack
(Included with the
F150-VM Monitor
Cable.)
F150-VM Monitor
Cable (2 m)
Console
F160-KP
(2-m cable)
F150-KP
(2-m cable)
Controller
This is the F250 Controller itself.
The F250 performs the image processing specified by the user settings and outputs the measurement results.
Power
Supply
We recommend the
OMRON S82K-10024.
See page 20 for details.
*F150-VS Camera
Cable (3 m)
12
Basic System Configuration
The Camera captures images of the measurement objects. Up to 4 Cameras can be connected to one F250 Controller.
*Cameras
CHECK If F150@@@ or F160@@@ Cameras are being used, the connected
Cameras must belong to the same series, i.e., they must have the same model number prefix (F150 or F160).
Section 2-2
• Double-speed Cameras
Camera with Intelligent Lighting
F160-SLC20 (20-mm field of vision)
F160-SLC50 (50-mm field of vision)
Camera Only
F160-S1
Use the Camera by itself when the field of vision of the F160-SLC @ 0 does not match the size of the measurement object. A standard
CCTV lens and light source will be needed.
• F150 Cameras
Camera with Intelligent Lighting
F150-SLC20 (20-mm field of vision)
F150-SLC50 (50-mm field of vision)
Camera with Intelligent Lighting
F150-SL20A (20-mm field of vision)
F150-SL50A (50-mm field of vision)
Camera Only
F150-S1A
Use the Camera by itself when the field of vision of the F150-SLC @ 0 does not match the size of the measurement object. A standard
CCTV lens and light source will be needed.
CHECK F200-series and F300-series Cameras can also be connected. Up to four
Cameras can be connected, but they must all have the same model number.
Only one Camera can be connected, however, when the F200-S Camera is used or when a camera with an internal sync mode is used.
Camera type Camera Cable Max. number of Cameras
F200-S F160-VSR3 1 (Connect to camera connector 0.)
F300-S
F300-S2R
F300-S3DR
F300-S4R
F160-VSR4
F160-VSR3
4
(The Cameras must have the same model number.)
SeeAlso Refer to page 68 for details on parameter settings.
13
Component Names and Functions Section 2-3
2-3 Component Names and Functions
The following diagram shows the F250 Controller’s major components.
14
1.
RS-232C/RS-422 Connector
Connects the F250 to an external device such as a personal computer or
PLC.
2.
Ethernet Connector (10BASE-T)
Connects the F250 to a personal computer. (Can be used with F250-UME
Application Software version 1.10 or higher.)
3.
Monitor Connector (S-VIDEO Output)
Connects to a monitor with an S-VIDEO input.
4.
Monitor Connector (Composite Video Output)
Connects to a monitor.
5.
Memory Card Slots 0 and 1
Memory Cards such as the Application Software Memory Card can be inserted in these slots.
6.
Memory Card Indicators 0 and 1
Lit when power is being supplied to the corresponding Memory Card. (The
Memory Card must not be inserted or removed when this indicator is lit.)
7.
Console Connector
Connects the F250 to a Console.
8.
ERROR Indicator
Lit when an error has occurred.
9.
RUN Indicator
Lit while the F250 is in Run Mode.
10. POWER Indicator
Lit while power is ON.
11. Parallel Connectors 0 and 1
Connect the F250 to external devices such as a sync sensor or PLC.
12. Camera Connectors 0 to 3
Connect to the Cameras.
13. Ground Terminal
Connects to the ground wire.
14. Power Supply Terminals
Connect to the DC power supply.
Mounting the Controller Section 2-4
2-4 Mounting the Controller
There are two ways to mount the Vision Mate Controller: horizontal mounting, or vertical mounting. (All dimensions are in mm.)
F250 Dimensions
270
115 min.
This screw hole cannot be used.
197
(25) 220
0.6
Four M4 taps
(for mounting)
Stopper
(40)
190
0.6
Panel thickness: T
The screw length L must be in the following range:
10+T < L < 13+T
10 to 13
CHECK Use the correct screw length. If the screw extends more than 13 mm past the panel, the stopper may bend and contact the
Controller’s internal PC board.
2-4-1 Horizontal Mounting
For proper air flow, provide at least 20 mm of clearance from the top of the
Controller and at least 50 mm of clearance from the sides (next to the intake and exhaust vents).
This screw hole cannot be used.
115 min.
20 min.
20 min.
50 min.
(Intake)
50 min.
(Exhaust)
8 mm
15
Mounting the Controller Section 2-4
2-4-2 Vertical Mounting
For proper air flow, provide at least 20 mm of clearance from the top of the
Controller and at least 50 mm of clearance from the sides (next to the intake and exhaust vents).
50 min.
(Exhaust) 115 min.
20 min.
20 min.
50 min.
(Intake)
Correct
View from bottom
Precaution The Controller must be installed with the air intake side down and the air exhaust side up.
Incorrect
Exhaust Intake
Intake Exhaust
16
Connecting Peripheral Devices Section 2-5
2-5 Connecting Peripheral Devices
This section shows how to connect peripheral devices to the F250.
Precaution Always turn OFF the power supply before connecting or disconnecting a peripheral device’s cable. The peripheral device may be damaged if it is connected while the power is ON.
The various connectors on the F250 are capped when the F250 is shipped.
When a connector is not being used, leave the cap in place or replace the cap to protect against dust, dirt, and static electricity.
2-5-1 Connecting a Console
Connect the Console to the F250’s CONSOLE connector. An F160-KP or
F150-KP Console can be connected. Install the provided ferrite core onto the cable, positioning the ferrite core about 10 mm from the F250-side connector.
ESC
SHIFT
ENT
TRIG
Approx. 10 mm
Ferrite core
CONSOLE
2-5-2 Connecting a Monitor
Connect the monitor cable to the F250’s MONITOR connector. Install the provided ferrite core onto the F150-VM Monitor Cable, positioning the ferrite core about 10 mm from the F250-side connector. The S-VIDEO and VIDEO outputs can be used simultaneously.
Ferrite core
POWER
SYNC
VIDEO
Approx. 10 mm
S-VIDEO
2-5-3 Connecting a Camera
Connect the camera cable to the F250's CAMERA connector.
CAMERA
Overview of Available Cameras
The F250 Camera with Light is a special Camera that has a special lens and light source already attached. The light source and lens are contained in a sin-
17
Connecting Peripheral Devices Section 2-5 gle unit, so installation is very simple. Just mount the Camera at the proper distance from the measurement object and it is ready to use.
Camera with Light
Item
Field of vision
Mounting distance
Relationship between Camera and object
F150-SL20A
20 mm
20 mm
61 to 71 mm
F150-SL50A
50 mm
50 mm
66 to 76 mm
Measurement object
Mounting distance
Field of vision
Lighting precautions None in particular
Camera with Intelligent Lighting
Item
Field of vision
Mounting distance
Relationship between Camera and object
F150-SLC20 or F160-SLC20
20 mm
20 mm
15 to 25 mm
F150-SLC50 or F160-SLC50
50 mm
50 mm
16.5 to 26.5 mm
Mounting distance
Measurement object
Field of vision
Lighting precautions Use with DIP switch pins 1 and 2 both set to
OFF.
Use with DIP switch pins 1 and 2 both set to
OFF.
O
F
F
1
2
Camera Only
Item
Field of vision and distance to object
F150-S1A or F160-S1
Determine the required field of vision based on the size of the measurement object and select an appropriate CCTV lens (C mount).
Lighting precautions Provide a light source appropriate for the measurement object.
CHECK Observe the following precautions when using a Camera with Light or Camera with Intelligent Lighting.
18
Power Supply and Ground Section 2-6
• The lens has a fixed focal point. The actual field of vision and focal point vary from lens to lens, so adjust the distance to the measurement object after replacing the lens or camera.
• The camera mounting distance listed in the following tables is an approximate value. Mount the Camera so that the distance to the measurement object can be adjusted easily.
If the object size and field of vision are incompatible, use a standard CCTV lens and light source.
SeeAlso page 22
2-6 Power Supply and Ground
Wire the power supply and the ground to their respective terminals. Tighten the screws to a torque of between 0.49 N
¼ m.
After wiring, confirm that the wiring is correct.
2-6-1 Crimp Terminals and Cables
The terminal block uses M3 terminal screws. Use appropriate crimp terminals for M3 screws, as shown below.
Forked Round
6.2 mm max.
6.2 mm max.
Applicable wire size: Insulated wire of 1.31 to 1.65 mm
2
(AWG16 to AWG15)
2-6-2 Ground (Earth) Wiring
Always connect a ground wire to the F250's ground terminal. To avoid grounding problems, do not share the ground wire with any other devices or wire the ground to the building's steel framing.
Use a grounding point that is as close as possible and keep the ground wire as short as possible.
Ground to 100
W
or less
19
Power Supply and Ground Section 2-6
2-6-3 Wiring the Power Supply
Wire the Power Supply Unit independently of other devices. In particular, keep the power supply wired separately from inductive loads. Also, keep the power supply wiring as short as possible (less than 10 m).
Use a power supply that meets the following specifications. We recommend using OMRON’s S82K-10024 Power Supply.
Item
Output current
Power supply voltage
Specification
3.7 A min.
24 VDC
+10%
/ -
15%
CHECK Use a DC power supply with countermeasures against high voltages (safe extra low-voltage circuits on the secondary side). If the system must meet UL standards, use a UL class II power supply.
+
−
24 VDC
!Caution
Keep the power supply line as short as possible (less than 10 m).
After wiring, replace the protective cover on the power supply terminals.
20
SECTION 3
Lenses, Lighting, and Memory Cards
This section provides additional information on CCTV lenses, lighting, and Memory Cards.
3-1 CCTV Lenses . . . . . . . . . . . . . . . . . . . . . . . . . . . . . . . . . . . . . . . . . . . . . . . . .
3-1-1 Optical Chart . . . . . . . . . . . . . . . . . . . . . . . . . . . . . . . . . . . . . . . . . .
3-1-2 Lenses and Lens Diameters . . . . . . . . . . . . . . . . . . . . . . . . . . . . . . .
3-1-3 Extension Tubes . . . . . . . . . . . . . . . . . . . . . . . . . . . . . . . . . . . . . . . .
3-2 Lighting. . . . . . . . . . . . . . . . . . . . . . . . . . . . . . . . . . . . . . . . . . . . . . . . . . . . . .
3-2-1 Lighting Methods . . . . . . . . . . . . . . . . . . . . . . . . . . . . . . . . . . . . . . .
3-3 Memory Cards . . . . . . . . . . . . . . . . . . . . . . . . . . . . . . . . . . . . . . . . . . . . . . . .
3-3-1 Installing a Memory Card. . . . . . . . . . . . . . . . . . . . . . . . . . . . . . . . .
3-3-2 Removing the Memory Card . . . . . . . . . . . . . . . . . . . . . . . . . . . . . .
3-3-3 Using Memory Cards in a Personal Computer. . . . . . . . . . . . . . . . .
25
27
27
27
28
22
22
23
24
25
21
CCTV Lenses Section 3-1
3-1 CCTV Lenses
When using a Camera without a light (F150-S1A or F160-S1), refer to the following graph to select the appropriate Lens and Extension Tube. The lens will differ depending on the size of the measurement object and the distance from the Camera.
3-1-1 Optical Chart
The values in the following chart are approximations, and the Camera must be adjusted after it is mounted.
Lens model: 3Z4S-LE
5,000
3,000
2,000
1,000
500
300
200 t: Extension Tube length
100
50
4 5 10 20 30 50 100 200 300 500
Field of vision L (mm)
The X axis of the graph shows field of vision L (mm), and the Y axis shows the camera distance A (mm). The curves on the graph show the relationship between the field of vision and camera distance for each CCTV lens. The values are significantly different for each lens, so double-check the model of the lens before using the graph. The “t” values indicate the lengths of the Extension Tubes. The value “t0” shows the case where an Extension Tube is not needed and the value “t5.0” shows the case where a 5-mm Extension Tube is used.
22
CCTV Lenses Section 3-1
Example
When a 3Z4S-LE C1614A CCTV Lens is being used and a field of vision of
40 mm is needed at the measurement object, a camera distance of 200 mm and 1-mm Extension Tube are required.
Camera
Extension Tube t @ (mm)
Lens
Camera distance A (mm)
Measurement object
Field of vision L (mm)
3-1-2 Lenses and Lens Diameters
Max. outer dia.
Unit: mm
1"-32UN
-2A
30 dia.
Lens
3Z4S-LE C418DX
3Z4S-LE B618CX-2
3Z4S-LE C815B
3Z4S-LE B1214D-2
3Z4S-LE C1614A
3Z4S-LE B2514D
3Z4S-LE B5014A
3Z4S-LE B7514C
Total length
4.8 mm
6.5 mm
8.5 mm
12.5 mm
16.0 mm
25.0 mm
50.0 mm
75.0 mm
Focal length
F1.4
F1.4
F1.4
F1.4
F1.4
Brightness
F1.8
F1.8
F1.5
Maximum outer diameter
40.5 mm dia.
48 mm dia.
42 mm dia.
42 mm dia.
30 mm dia.
30 mm dia.
48 mm dia.
62 mm dia.
Total length
35.5 mm
42 mm
40 mm
50 mm
33 mm
37.3 mm
48 mm
79 mm
---
Filter size
M40.5
P0.5
M27
P0.5
M46
P0.75
M58
P0.75
23
CCTV Lenses Section 3-1
3-1-3 Extension Tubes
One or more Extension Tubes can be inserted between the lens and the Camera to focus the Camera image. Use a combination of one or more of the six tubes to achieve the required length.
Extension Tube
Model Maximum outer diameter
3Z4S-LE EX-C6 31 dia.
Length
Set of 6 tubes
0.5 mm, 1 mm, 5 mm, 10 mm, 20 mm, and
40 mm
Length: 40 mm 20 mm 10 mm 5 mm 1.0 mm 0.5 mm
Precaution • Do not use the 0.5-mm and 1.0-mm Extension Tubes attached to each other. Since these Extension Tubes are placed over the threaded section of the Lens or other Extension Tube, the connection may loosen when more than one 0.5-mm or 1.0-mm Extension Tube are used together.
• Reinforcement may be required for combinations of Extension Tubes exceeding 30 mm if the Camera is subject to vibration.
24
Lighting Section 3-2
3-2 Lighting
A stable image must be obtained to ensure accurate inspection. Use appropriate lighting for the application and the measurement object if using a Camera without a light (F150-S1A or F160-S1).
3-2-1 Lighting Methods
Back Lighting
A stable, high-contrast image can be obtained using back lighting.
Applications: Inspection of exterior shape or positioning inspection
Camera
Measurement object
Light source
Reflected Lighting
Ring Lights
Light is shone uniformly on the measurement object.
Applications: Surface inspections
Camera
Light source
Measurement object
Oblique Lighting
Detection can be made utilizing the difference in regular and diffuse reflected light.
25
Lighting
Applications: Inspections for surface gloss
Section 3-2
Camera
Light source
Measurement object
Coaxial Lighting
A stable image can be obtained with few shadows from uneven surfaces on the measurement object.
Applications: Surface inspections, positioning, and hole inspections of comparatively small objects
Half mirror
Camera
Light source
Measurement object
26
Memory Cards Section 3-3
3-3 Memory Cards
Use a Memory Card to back up data such as settings and image data or increase the number of scenes when you are using the Scene Group function.
Data from the F250 can be backed up in the computer just by inserting the
Memory Card into the computer and copying the desired data. The following procedures also apply to the Memory Card containing the F250-UME Application Software.
We recommend the OMRON F160-N64S (64 MB).
CHECK The F250 is equipped with two Memory Card slots. Use these slots for the following functions.
Function Slot number
F250-UME Application Software installation Slot 0 (Use slot 0 only.)
Memory Cards for scene groups
Memory Cards for data backup
Slot 1 (Use slot 1 only.)
Either slot 0 or 1 can be used.
Precaution A filler card with no memory is inserted into the F250’s Memory Card slot before the F250 is shipped. Remove this filler card and install a Memory Card to use the Memory Card functions.
If Memory Cards are not being used, leave the filler card in place to prevent dust or dirt from entering the Memory Card slot.
3-3-1 Installing a Memory Card
1.
Insert the Memory Card into the Memory Card slot.
CHECK The eject button will pop out slightly when the Memory Card is inserted properly.
3-3-2 Removing the Memory Card
1.
Turn OFF the power supply to the Memory Card or turn OFF the F250.
SeeAlso Refer to Section 4 Additional Functions in the F250 Vision Sensor Manual
2: Operation Manual for details on turning OFF the power supply to the
Memory Card.
2.
Verify that the Memory Card indicator is not lit.
Memory card indicator
27
Memory Cards Section 3-3
Precaution Do not remove the Memory Card if the Memory Card indicator is lit. Doing so may damage the Memory Card or the F250 itself.
3.
Press the eject button to the right of the Memory Card slot. The Memory
Card will pop out slightly.
Precaution Do not remove the Memory Card without pressing the eject button. Doing so may damage the F250.
Memory card eject button
4.
Pull the Memory Card straight out from the slot.
3-3-3 Using Memory Cards in a Personal Computer
The F250’s Memory Cards can be used in a personal computer with a PC
Card drive (PCMCIA 2.0 or higher, type II compatible) or CompactFlash ™ drive.
The Memory Card must be inserted into a PC Card Adapter in order to be used in a PC Card drive. We recommend the OMRON HMC-AP001 PC Card
Adapter.
PC Card
Adapter
28
SECTION 4
Connecting External Devices
This section describes how to connect external devices through a parallel interface (a parallel connector) or serial interface (the RS-232C/RS-422 connector or Ethernet connector).
4-1 Connecting through the Parallel Interface . . . . . . . . . . . . . . . . . . . . . . . . . . .
4-1-1 Parallel Connection Methods . . . . . . . . . . . . . . . . . . . . . . . . . . . . . .
4-1-2 Parallel Connector Specifications. . . . . . . . . . . . . . . . . . . . . . . . . . .
4-1-3 I/O Specifications . . . . . . . . . . . . . . . . . . . . . . . . . . . . . . . . . . . . . . .
4-2 Connecting through the Serial Interface . . . . . . . . . . . . . . . . . . . . . . . . . . . . .
4-2-1 RS-232C/RS-422 Connections. . . . . . . . . . . . . . . . . . . . . . . . . . . . .
4-2-2 Ethernet Connection . . . . . . . . . . . . . . . . . . . . . . . . . . . . . . . . . . . . .
30
30
32
36
37
37
40
29
Connecting through the Parallel Interface Section 4-1
4-1 Connecting through the Parallel Interface
This section explains how to connect I/O to the F250 through its parallel interface to input signals such as measurement triggers or output signals such as measurement results.
When you want to use the parallel interface to input commands and output measurement results, prepare a parallel I/O cable and connect it to the parallel connector. A Terminal Block can also be used to connect external devices.
Refer to the F250 Vision Sensor Manual 2: Operation Manual for details on communications settings and I/O formats.
4-1-1 Parallel Connection Methods
Using a Parallel I/O Cable
Use an F160-VP Parallel I/O Cable (sold separately) to connect the F250 to external devices. Align the connectors and insert the cable’s connector straight into the F250’s parallel connector. Tighten the connector’s mounting screws to secure the connection.
Parallel
Connector 0
Parallel
Connector 1
30
Marks (1 to 4)
F160-VP Parallel
I/O Cable (2 m)
Wire color
FG terminals
Ground to 100
W
or less.
Precaution 1.
Turn OFF the power supply before connecting or disconnecting a Parallel
I/O Cable. Peripheral devices may be damaged if the cable is connected or disconnected ZLWKWKHSRZHU21
Connecting through the Parallel Interface Section 4-1
2.
The parallel connectors are capped with screw-on covers when the F250 is shipped. When a connector is not being used, leave the cover in place or replace the cover to protect against dust, dirt, and static electricity.
Using a Screw Terminal Block
Use a Screw Terminal Block and Special Cable to connect the F250 to external devices such as PLCs.
Parallel
Connector 0
Parallel
Connector 1
Special Cable
XW2Z-100B (1 m)
XW2Z-200B (2 m)
XW2Z-300B (3 m)
XW2Z-500B (5 m)
XW2B-40G5 Screw
Terminal Block
PLC or other device
31
Connecting through the Parallel Interface
4-1-2 Parallel Connector Specifications
Parallel Connector 0
A20 A1
Section 4-1
B20 B1
Each wire of the F160-VP Parallel I/O Cable has a unique wire-color/mark combination.
Pin
A1
$ ■
A4 DI2 Gray ■
A5
A6
A7
A8
DI4
DI6
(Open)
White ■
/WEURZQ ■ ■
<HOORZ ■ ■
STGOUT0 Green ■ ■
A20
Signal
5(6(7
67(3
A3 DI0
A9
A10
A11
$
A13
A14
A15
A16
A17
RUN
BUSY
OR
DO0
DO2
DO4
DO6
DO8
DO9
A18 DO11
A19 DO13
DO15
Color Mark
(Black)
/WEURZQ ■
<HOORZ
Green
Gray
White
/WEURZQ
<HOORZ
Green
■
■ ■
■ ■
■ ■ ■
■ ■ ■
■ ■ ■
Gray ■ ■ ■
White ■ ■ ■
/WEURZQ ■ ■ ■ ■
<HOORZ
Green
Gray
White
■ ■ ■ ■
■ ■ ■ ■
■ ■ ■ ■
■ ■ ■ ■
Function
5HVWDUWVWKH
)
0HDVXUHPHQW
WULJJHUVLJQDO
LQSXW
Command input
(Leave open.)
Strobe trigger 0 output (See note 1.)
ON while in
Run mode
ON during processing
Combined judgement result
Data output
Pin Signal Color
B1
&20,1 /WEURZQ ■
Mark
(Red)
Function
B
B3
'6$
DI1
<HOORZ
Green
■
■
Common for input signals
(See note 2.)
,QSXWVGDWD
VHQGUHTXHVW
VLJQDOV
Command input
B4 DI3 Gray ■
B5
B6
B7
B8
DI5
DI7
(Open)
STGOUT1
White ■
/WEURZQ ■ ■
<HOORZ ■ ■
Green ■ ■
(Leave open.)
Strobe trigger 1 output (See note 1.)
B9 ERROR Gray ■ ■ ON when there is an error.
B10 GATE White ■ ■ ON for the set output time
B11 COMOUT1
/WEURZQ ■ ■ ■ Common for control signals
B DO1 ■ ■ ■
(See note 3.)
Data output
B13
B14
DO3
DO5
<HOORZ
Green
Gray
■ ■ ■
■ ■ ■
B15 DO7 White ■ ■ ■
B16 COMOUT2
/WEURZQ ■ ■ ■ ■ Common for
DO0 to DO7
B17 DO10
<HOORZ ■ ■ ■ ■ Data output
B18 DO12 Green ■ ■ ■ ■
B19 DO14 Gray ■ ■ ■ ■
B20 COMOUT3 White ■ ■ ■ ■ Common for
DO8 to DO15
Precaution Do not input the RESET input immediately after turning ON the power. When using RESET input to synchronize startup timing, wait at least 1 s after turning
21WKH)VSRZHUVXSSO\EHIRUHWXUQLQJ21WKH5(6(7VLJQDO
CHECK Use a DC power supply with countermeasures against high voltages (safe extra low-voltage circuits on the secondary side) for the COMIN and COMOUT terminals. If the
V\VWHPPXVWPHHW8/VWDQGDUGVXVHD8/FODVV,,SRZHUVXS
SO\
32
Connecting through the Parallel Interface
Parallel Connector 1
A20 A1
Section 4-1
B20 B1
Each wire of the F160-VP Parallel I/O Cable has a unique wire-color/mark combination.
Pin
A1
$ 5HVHUYH
LQSXW
A3 DI8
■
A4 DI10
Green
Gray
■
■
A5
A6
A7
A8
DI12
DI14
(Open)
White ■
/WEURZQ ■ ■
<HOORZ
■ ■
STGOUT2 Green ■ ■
A9
A10
A11
$
A13
A14
A15
A16
A17
A18
A19
A20
Signal
(Open)
5HVHUYH
RXWSXWV
DO16
DO18
DO20
DO22
DO24
DO25
DO27
DO29
DO31
Color Mark
(Black)
/WEURZQ ■
<HOORZ
Gray
White
/WEURZQ
<HOORZ
Green
Gray ■ ■ ■
White ■ ■ ■
/WEURZQ ■ ■ ■ ■
<HOORZ
Green
Gray
White
■ ■
■ ■
■ ■ ■
■ ■ ■
■ ■ ■
■ ■ ■ ■
■ ■ ■ ■
■ ■ ■ ■
■ ■ ■ ■
Function
(Leave open.)
(Leave open.)
Command input
(Leave open.)
Strobe trigger 2 output
(See note 1.)
(Leave open.)
(Leave open.)
(Leave open.)
Data output
Pin
B1
Signal
&20,1
Color
/WEURZQ
Mark
(Red)
■
Function
Common for input signals
(See note 2.)
B
5HVHUYH
LQSXW
B3 DI9
<HOORZ
■ (Leave open.)
Green
Gray
■ Command input
B4 DI11 ■
B5
B6
B7
B8
DI13
DI15
(Open)
STGOUT3
White ■
/WEURZQ ■ ■
<HOORZ
■ ■
Green ■ ■
(Leave open.)
Strobe trigger 3 output
(See note 1.)
B9
5HVHUYH
RXWSXW
Gray ■ ■ (Leave open.)
B10 Reserve output
B11 COMOUT4
/WEURZQ ■ ■ ■ Common for control signals
(See note 3.)
B DO17
White
<HOORZ
■ ■
■ ■ ■
(Leave open.)
Data output
B13 DO19 Green ■ ■ ■
B14 DO21 Gray ■ ■ ■
B15 DO23 White ■ ■ ■
B16 COMOUT5
/WEURZQ ■ ■ ■ ■ Common for
DO16 to DO23
B17
B18
DO26
DO28
<HOORZ
Green
■ ■ ■ ■
■ ■ ■ ■
Data output
■ ■ ■ ■ B19 DO30 Gray
B20 COMOUT6 White ■ ■ ■ ■ Common for
DO24 to DO31
Note 1.
Refer to page 70 for details if you want to connect a strobe device to the
F250.
Each Camera has its own strobe trigger output as shown in the following table.
33
Connecting through the Parallel Interface Section 4-1
Camera
Camera 0
Camera 1
Camera 2
Camera 3
Strobe trigger output signal
STGOUT0 (Pin A8 of parallel connector 0)
STGOUT1 (Pin B8 of parallel connector 0)
STGOUT2 (Pin A8 of parallel connector 1)
STGOUT3 (Pin B8 of parallel connector 1)
2.
COMIN1 is the common for A1 to A6 and B2 to B6 on connector 0.
COMIN2 is the common for A3 to A6 and B3 to B6 on connector 1.
3.
COMOUT1 is the common for A8 to A11 and B8 to B10 on connector 0.
COMOUT4 is the common for A8 and B8 on connector 1.
Wiring Connector-Terminal Block Conversion Units
Connector-Terminal Block Conversion Unit
Manufacturer
OMRON
Model
XW2B-40G5
Connecting Cables
Manufacturer
OMRON
Model
XW2Z-100B (1 m)
XW2Z-200B (2 m)
XW2Z-300B (3 m)
XW2Z-500B (5 m)
34
1
Connecting through the Parallel Interface
Connecting to the F250
Parallel connector 0
Parallel connector 1
39
Section 4-1
Connecting to Parallel Connector 0
35
37
39
27
29
31
33
19
21
23
25
11
13
15
17
5
7
9
1
3
Conversion
Unit Terminal
DO4
DO6
DO8
DO9
DO11
DO13
DO15
Signal
RESET
STEP
DI0
DI2
DI4
DI6
Not used.
12
14
STGOUT0 16
RUN 18
BUSY
OR
DO0
DO2
20
22
24
26
6
8
10
2
4
Conversion
Unit Terminal
36
38
40
28
30
32
34
Signal
COMIN1
DSA
DI1
DI3
DI5
DI7
Not used.
STGOUT1
ERROR
GATE
COMOUT1
DO1
DO3
DO5
DO7
COMOUT2
DO10
DO12
DO14
COMOUT3
2
Connector-Terminal Block
Conversion Unit
40
Connecting to Parallel Connector 1
5
7
9
11
13
15
17
31
33
35
37
23
25
27
29
39
Conversion
Unit Terminal
1
3
19
21
DO16
DO18
DO20
DO22
DO24
DO25
DO27
DO29
DO31
Signal
Not used.
Reserve input
DI8
DI10
6
8
DI12
DI14
10
12
Not used.
14
STGOUT2 16
18 Reserve output
Reserve output
Reserve output
20
22
Conversion
Unit Terminal
2
4
24
26
28
30
32
34
36
38
40
Signal
COMIN2
Reserve input
DI9
DI11
DI13
DI15
Not used.
STGOUT3
Reserve output
Reserve output
COMOUT4
DO17
DO19
DO21
DO23
COMOUT5
DO26
DO28
DO30
COMOUT6
SeeAlso Refer to the beginning of
3DUDOOHO &RQQHFWRU 6SHFLILFDWLRQV
for signal definitions.l
35
Connecting through the Parallel Interface Section 4-1
Making a Parallel I/O Cable
A parallel I/O cable can be assembled using the following connector and cover or equivalent components. Keep the cable length less than P
Component
Connector
Cover
Manufacturer
Fujitsu
Fujitsu
Model number
)&1-$8
)&1&%
CHECK Double-check the connector wiring for mistakes before turning ON the power
VXSSO\IRUWKHILUVWWLPH
4-1-3 I/O Specifications
Input Specifications
Item
Model
Input voltage
ON current
ON voltage
OFF current
OFF voltage
ON delay
OFF delay
F250-C50 (NPN mode)
12 to 24 VDC
10%
5 to 15 mA
8.8 V max.
0.1 mA max.
4.5 V min.
RESET input: 10 ms max.
Other inputs: 0.5 ms max.
RESET input: 15 ms max.
Other inputs: 0.7 ms max.
Internal circuits
COM IN
+
Specification
F250-C55 (PNP mode)
Input terminal
Input terminal
COM IN
Output Specifications
Item
Model
Output voltage
Load current
ON residual voltage
OFF leakage current
Internal circuits
F250-C50 (NPN mode)
12 to 24 VDC
10%
45 mA max.
2 V max.
0.1 mA max.
Specification
F250-C55 (PNP mode)
Output terminal
Load
+
COM OUT
COM OUT
Load
Output terminal
Precaution Do not exceed the maximum load current specified for the F250. The F250 will be damaged if an output is short-circuited.
36
Connecting through the Serial Interface Section 4-2
4-2 Connecting through the Serial Interface
The F250’s serial interface (RS-232C/RS-422 connector or Ethernet connector) can be used to input signals such as measurement triggers or output signals such as measurement results. Additionally, data that has been set in the
F250 can be backed up in a personal computer.
Refer to Section 6 Communicating with External Devices in the F250 Vision
Sensor Manual 2: Operation Manual for details on communications settings and I/O formats.
4-2-1 RS-232C/RS-422 Connections
Connection Examples
1:1 Connection (Normal, Menu Operation)
RS-232C cable
F250
Computer
Multi-drop Connection (Normal)
Communications between one computer and several F250s is possible using
Link Adapters.
31 Units max.
RS-422 cable
Link Adapter
OMRON
3G2A9-AL004-E recommended
RS-232C cable
RS-422 cable
Computer
Link Adapter
RS-422 cable
Link Adapter Link Adapter
OMRON
B500-AL001 recommended
F250 F250 F250
CHECK When 3G2A9-AL004-E Link Adapters are being used, termination must be set to ON in the last node in the line and the node must be terminated as follows:
• Connect 220
W
(1/2 W min.) between RDA(
-
) and RDB(+).
• Connect 220 W (1/2 W min.) between SDA(
-
) and SDB(+).
37
Connecting through the Serial Interface
1:1 Connection (Host Link)
Connector
Section 4-2
RS-232C cable
F250
PLC
The F250’s RS-232C/RS-422 Connector is a 9-pin D-SUB female connector.
The pin allocation is shown below.
1 2 3 4 5
7
8
9
1
2
3
4
5
6
6 7
Pin
8 9
Signal
FG
SD
RD
NC
RDB(+)
RDA(
-
)
SDB(+)
SDA(
-
)
GND
Name
Protective frame ground
For RS-232C
Not connected
For RS-422
Signal ground
The following plug and hood are recommended and are available from
OMRON.
Plug
Hood
Model Model No.
XM2A-0901
XM2S-0911
Wiring
RS-232C Wiring
The maximum cable length is 15 m for RS-232C or RS-422
Signal
SD
RD
GND
F250
Pin
2
3
9
External device
Pin
✽
✽
✽
Signal
SD
RD
GND
RS/CS control cannot be used.
Use only shielded cable.
38
Connecting through the Serial Interface
RS-422 Wiring
F250
Signal
RDB (+)
RDA (
−
)
SDB (+)
SDA (
−
)
GND
7
8
9
Pin
5
6
Pin
✽
✽
✽
✽
✽
External device
Signal
RDB (+)
RDA (
−
)
SDB (+)
SDA (
−
)
GND
Section 4-2
Connection
Use only shielded cable.
Note Pin numbers on the external device will depend on the device being connected. Refer to the manual for the personal computer or PLC being connected.
Align the connector with the socket and press the connector straight into place. Tighten the two mounting screws to secure the connector.
Precaution Always turn OFF the power supply before connecting or disconnecting cables.
The peripheral device may be damaged if connected or disconnected with the power supply turned ON.
Note The connector is capped when the F250 is shipped. When not using the serial interface, leave the cap in place to protect against dust, dirt, and static electricity.
39
Connecting through the Serial Interface
4-2-2 Ethernet Connection
Section 4-2
Connection Examples
■ 1:1 Connection
Use a Shielded (STP) 10 Base-T Crossover Cable to make the 1:1 connection.
The cable length must be less than 30 m.
10 Base-T Crossover Cable (STP)
(Less than 30 m)
F250
Computer
■ 1:N Connection
A Hub can be used to communicate with two or more F250s from a single computer. Use Shielded (STP) 10 Base-T Straight-through Cables to make the
1:N connections. The cable length between the F250s and the Hub must be less than 30 m.
F250
10 Base-T
Straight-through
Cable (STP)
(Less than 30 m)
Computer
10 Base-T Straightthrough Cable (STP)
HUB
10 Base-T
Straight-through
Cable (STP)
(Less than 30 m)
10 Base-T
Straight-through
Cable (STP)
(Less than 30 m)
F250 F250
40
Connecting through the Serial Interface
Connection
Section 4-2
Align the connector with the socket and press the connector straight into place.
Precaution 1.
Always turn OFF the power supply before connecting or disconnecting cables. The peripheral device may be damaged if connected or disconnected with the power supply turned ON.
2.
The Ethernet connector is capped when the F250 is shipped. When the
Ethernet interface isn’t being used, leave the cap in place or replace the cap to protect against dust, dirt, and static electricity.
CHECK Refer to Section 6 Communicating with External Devices in the F250 Vision
Sensor Manual 2: Operation Manual for details on setting the F250’s IP
Address and Subnet Mask.
41
SECTION 5
Troubleshooting and Maintenance
This section provides tables to help identify and correct hardware errors that may occur with the F250 as well as information on maintenance and periodic inspections.
5-1 Troubleshooting . . . . . . . . . . . . . . . . . . . . . . . . . . . . . . . . . . . . . . . . . . . . . . .
5-1-1 Connection Errors. . . . . . . . . . . . . . . . . . . . . . . . . . . . . . . . . . . . . . .
5-1-2 Menu Operation Errors. . . . . . . . . . . . . . . . . . . . . . . . . . . . . . . . . . .
5-1-3 Parallel Interface Errors . . . . . . . . . . . . . . . . . . . . . . . . . . . . . . . . . .
5-1-4 Serial Interface (RS-232C/RS-422) Errors. . . . . . . . . . . . . . . . . . . .
5-1-5 Cameras . . . . . . . . . . . . . . . . . . . . . . . . . . . . . . . . . . . . . . . . . . . . . .
5-1-6 Memory Cards . . . . . . . . . . . . . . . . . . . . . . . . . . . . . . . . . . . . . . . . .
5-1-7 Serial Interface (Ethernet) Errors . . . . . . . . . . . . . . . . . . . . . . . . . . .
5-1-8 Cabling Errors . . . . . . . . . . . . . . . . . . . . . . . . . . . . . . . . . . . . . . . . .
5-2 Maintenance . . . . . . . . . . . . . . . . . . . . . . . . . . . . . . . . . . . . . . . . . . . . . . . . . .
5-2-1 Replacing the Light . . . . . . . . . . . . . . . . . . . . . . . . . . . . . . . . . . . . .
5-3 Regular Inspections. . . . . . . . . . . . . . . . . . . . . . . . . . . . . . . . . . . . . . . . . . . . .
5-4 Specifications . . . . . . . . . . . . . . . . . . . . . . . . . . . . . . . . . . . . . . . . . . . . . . . . .
5-5 F200/F300 Camera Parameters. . . . . . . . . . . . . . . . . . . . . . . . . . . . . . . . . . . .
5-6 Connecting a Strobe Device . . . . . . . . . . . . . . . . . . . . . . . . . . . . . . . . . . . . . .
44
44
45
46
46
44
44
45
45
46
46
49
50
68
70
43
Troubleshooting Section 5-1
5-1 Troubleshooting
This section lists probable corrections for common hardware problems. Please check all of the following items before requesting repairs.
5-1-1 Connection Errors
Problem
The POWER indicator is not lit.
The Video Monitor is blank.
The Video Monitor image is not clear.
Cannot make key inputs from the
Console.
Camera images do not appear on the screen (for Cameras with Light
Source).
Camera images do not appear on the screen (when a standard CCTV lens and lighting are used).
The indicators do not turn ON (for
Cameras with Light Source).
Probable cause
The Power Supply is not connected properly.
The supply voltage is not 24 VDC
+10%
/
-15%
.
The power to the Video Monitor is not ON.
The Monitor Cable is not connected properly.
The Video Monitor is malfunctioning.
When using an LCD Monitor, the power supply capacity is insufficient.
There is electrical noise entering from the power supply or cables.
The Monitor Cable is not correctly connected.
The Console Cable is not correctly connected.
The Camera Cable is not correctly connected.
The lighting cable is not properly connected to the Camera.
The lens cap has not been removed.
The Camera Cable is not properly connected.
The lens iris is opened or closed too far.
The shutter speed is not suitable.
The lighting method is not suitable.
The lighting cable is not correctly connected to the Camera.
Power is not being supplied to the F250.
When using a Camera with Intelligent Lighting, the DIP switch pins are not set to 0.
5-1-2 Menu Operation Errors
Problem
The measurement results are not displayed on the Video Monitor.
Probable cause
The F250 is not in Monitor or Run mode.
5-1-3 Parallel Interface Errors
Problem
Trigger signals (input signals) are not received.
Probable cause
The cables are not correctly wired.
The signal line is disconnected.
The status of communications can be checked with the I/O monitor.
The F250 is not in Monitor or Run mode.
Signals cannot be output externally.
The trigger signal has not been input.
The cables are not correctly wired.
The signal line is disconnected.
The status of communications can be checked with the I/O monitor.
The F250 is not in Run mode.
44
Troubleshooting
5-1-4 Serial Interface (RS-232C/RS-422) Errors
Section 5-1
Problem
No communications are possible.
Probable cause
The cables are not correctly wired.
The F250’s communications specifications do not match those of the external device.
The communications mode was not selected under System settings/
Communication/Serial.
Select Normal, Host link, or Menu in the Communications (Serial) menu. (Normal is no-protocol.)
The status of communications can be checked with the I/O monitor.
The reception buffer on the external device (e.g., computer) is full. Check that settings allow the data to be properly received.
The Unit operates well initially, but after a while there is no response from the F250.
Cannot perform menu operations from the computer.
Data cannot be saved
The communications mode was not set to Menu in the System settings/
Communication/Serial settings.
• Are the same communications conditions set for both the external device and the F250?
• Is flow control turned OFF under System settings/communication/
Normal? Refer to the F250 Operation Manual.
5-1-5 Cameras
Problem
Are the shutter trigger pulses synchronized when more than one camera is connected?
Probable cause
The shutter trigger pulses are not synchronized for the F160-S1 and
F150-S1. The timing is offset so that light from other Cameras does not enter. The offset depends on the model of Camera that is used.
Model tD
F160-S1 F150-S1
Approx. 500 m s Approx. 1 ms
Camera 0
Camera 1
If a strobe is used, the strobe trigger signals are also offset in the same way as the shutter trigger pulses.
Camera 2
Camera 3 tD
Shutter trigger pulses ON
Can more than one internally synchronized Cameras be connected?
Can the F150-LT10A Light be connected to the F160-S1 Camera?
The shutter trigger pulses are synchronized for other Cameras, i.e., there is no offset.
No. Only one F200-S Camera (internal sync) can be connected, and it must be connected to Camera connector 0.
Yes, it can be connected and the following Lenses are available.
• Lens with 20-mm field of vision: F150-LE20
• Lens with 50-mm field of vision: F150-LE50
5-1-6 Memory Cards
Problem
Can either of the Memory Card slots be used?
Probable cause
Only the following two functions have restrictions in the slot that can be used.
• Starting the Setup Menu: Slot 0 only
• Switching scene groups: Slot 1 only
Either slot can be used for all other functions (outputting results to a Memory Card, saving scene data, etc.).
45
Maintenance
5-1-7 Serial Interface (Ethernet) Errors
Section 5-2
Problem
No communications are possible.
Probable cause
A 10 Base-T Crossover Cable is not being used for a 1:1 connection.
10 Base-T Straight-through Cables are not being used for the 1:N connections.
Power is not being supplied to the HUB, the settings are incorrect, or the connections are incorrect.
The personal computer’s IP Address and Subnet Mask settings are not correct or the settings are duplicated in another device.
The F250’s IP Address and Subnet Mask settings are not correct or the settings are duplicated in another device.
The IP Address set for the F250 in the computer’s communications software is incorrect.
The communications mode was set to Normal or Menu in the System
settings/Communication/Serial window.
The status of communications can be checked with the I/O monitor.
The F250 is being accessed by another computer.
Communications are being affected by a noise source (such as a power line) that is too close to the F250 or communications cables.
Communications are not set for a TELNET connection (TCP/IP, port 23) in the computer’s communications software.
The reception buffer on the external device (e.g., computer) is full. Check that settings allow the data to be properly received.
The Unit operates well initially, but after a while there is no response from the F250.
The response from the F250 is slow.
(It takes too long to transfer data and errors occur.)
Cannot perform menu operations from the computer.
The IP Address of the F250 or computer is duplicated in another device.
Communications are being affected by a noise source (such as a power line) that is too close to the F250 or communications cables.
The network’s communications load is too heavy.
The computer’s processing load is too heavy. (A program that requires a lot of processing capacity is being run simultaneously.)
The communications mode was not set to Menu in the System settings/
Communication/Serial settings.
5-1-8 Cabling Errors
Problem
A recommended OMRON RS-232C cable is not being used.
Can a commercially available cable be used instead of the R150-VM
Monitor Cable?
Probable cause
One of the following OMRON cables can be used. Select a cable that works with the device being connected.
Connecting to a PC/AT or compatible computer (9-pin connector)
• XW2Z-200S-V (2 m)
• XW2Z-500S-V (5 m)
Connecting to a SYSMAC device (9-pin connector)
• XW2Z-200T (2 m)
• XW2Z-500T (5 m)
Yes, as long as it’s a pin jack cable (with a yellow connector) for video signal connection.
5-2 Maintenance
5-2-1 Replacing the Light
• The Light will gradually lose brightness over time (about 20% loss after
1,500 hours of use). Replace the Light after about 1,500 hours of use.
46
Maintenance Section 5-2
• Replace the Light if it is damaged or not fully functional.
F150-SL20A/SL50A
Use the following procedure to replace a Light with the F150-LT10A Light.
(The F150-LT10A cannot be connected to the older F150-S1 Camera.)
Removing the Light
Camera base
2
3
1
Hold this part when removing the Cable.
4
Precaution
Installing the Light
Light
Lighting connector
Camera cable connector
1.
Disconnect the light cable from the light connector on the back of the Camera.
2.
Remove the light cable from the slot in the camera base.
3.
Remove the two screws securing the Light.
4.
Remove the Light from the Camera.
Do not disassemble the Lens. Disassembly can damage the Lens.
Camera base
3
2
4
1
Light
Lighting connector Camera cable connector
1.
Mount the Light on the Camera.
2.
Screw in the two screws that secure the Light.
3.
Place the light cable in the slot in the camera base.
4.
Connect the light cable to the light connector on the back of the Camera.
47
Maintenance Section 5-2
F150-SLC20/SLC50 or F160-SLC20/SLC50
Use the following procedure to replace a Light with an F150-LTC20 (20-mm field of vision) or F150-LTC50 (50-mm field of vision) Light.
Removing the Light
5
3
Precaution
CHECK
Camera base
2
Light
4
1
Hold this part when removing the Cable.
1.
Disconnect the light cable from the light connector on the back of the Camera.
2.
Remove the light cable from the slot in the camera base.
3.
Remove the two screws securing the Light at the top.
4.
Remove the two screws securing the Light at the bottom.
5.
Remove the Light from the Camera.
Do not disassemble the Lens. Disassembly can damage the Lens.
When you want to use the Camera alone without connecting an Intelligent
Lighting, use M2 3 screws in the bottom of the Camera instead of the long screws removed in step 4. The screws removed in step 3 are not needed.
Installing the Light
1
3
Camera base
4
Light
2
5
1.
Mount the Light on the Camera.
2.
Screw in the two screws that secure the Light at the bottom.
3.
Screw in the two screws that secure the Light at the top.
48
Regular Inspections Section 5-3
4.
Place the light cable in the slot in the camera base.
5.
Connect the light cable to the light connector on the back of the Camera.
5-3 Regular Inspections
To maintain the F250 in the best condition, perform the following regularly.
• Clean the Lens and LED indicators with a lens-cleaning wipe or blow off dust with an aerosol air sprayer.
• Lightly wipe off dirt with a soft cloth.
Inspection point Details
Power supply The voltage measured at the power supply terminals must be 24 VDC
+10%
/
-15%
.
Ambient temperature
The operating ambient temperature inside the cabinet must be between 0 and 50
C.
Ambient humidity The operating ambient humidity inside the cabinet must be between 35% and 85%.
Installation Each component must be firmly secured.
Each cable connector must be correctly inserted and locked.
The Cameras must be firmly secured.
The camera lens mounts must be firmly secured.
Indicators All indicators must light when the power is turned ON.
Verify that a through-image is displayed.
When using an Intelligent Lighting, verify that the light level settings are set to their maximum values.
Tools required
Circuit tester
Thermometer
Hygrometer
Phillips screwdriver
---
Precaution • Turn OFF the power and take safety precautions before conducting inspections. Electrical shock can result from attempting safety inspections with the power turned ON.
• Do not use thinners or benzene to clean the F250. They will damage
F250 components.
49
Specifications Section 5-4
5-4 Specifications
This section provides the specifications and dimensions of the F250 and its peripheral devices. (All dimensions are in mm unless otherwise noted.)
F250-C50/C55 Vision Mate Controller
270
115 min.
(25)
220
0.6
Four M4 taps
(for mounting)
197
This screw hole cannot be used.
Stopper
10 to 13
Panel thickness:
T
(40) 190
0.6
Screw length L:
10+T < L < 13+T
Model
Item
F250-C50
Specification
F250-C55
Input/Output type
Supply voltage
NPN
20.4 to 26.4 VDC
PNP
Current consumption 3.0 A max.
Insulation resistance 20 M
W
min. between all DC external terminals and GR terminal (100 VDC Megger, with internal surge absorber removed)
Dielectric strength
Leakage current
1,000 VAC, 50/60 Hz between all DC external terminals and GR terminal (with internal surge absorber removed)
10 mA max.
Noise resistance 2,000 V; pulse width: 50 ns; rise time: 5 ns (pulse)
Burst continuation time: 15 ms; Period: 300 ms
Vibration resistance
10 to 150 Hz; half-amplitude: 0.1 mm; maximum acceleration: 15 m/s
2
, 10 times for 8 minutes each in 3 directions.
Shock resistance
150 m/s
2
, 3 times each in 6 directions
Ambient temperature Operating: 0 to 50
C (with no condensation)
Storage:
-
25 to 65
C (with no condensation)
Ambient humidity Operating and storage: 35% to 85% (with no condensation)
Ambient environment No corrosive gases
Ground Class 1 (Ground resistance 100
W
max.)
Degree of protection IEC60529 IP20 (in-panel)
Case material SECC-T
50
Specifications
Item
Battery life
Weight
Specification
Approximately 7 years when used 24 hours/day.
Approx. 3.1 kg (Controller only)
F150 Cameras
Cameras with Light
■ F150-SL20A/SL50A
39
27
67 (70.5)
Section 5-4
Unit: mm
F150-LT10A Light
(50.25) (16.75)
Two M4 taps, Depth 8
(40.25) 20 ± 0.1
1/4-20UNC tap, Depth 8
(6.75)
51
Specifications
Cameras with Intelligent Lighting
■ F150-SLC20
70
12 12
F150-LTC20 Light
73 40
Section 5-4
Unit: mm
(85)
(10) 25
12
31
40
12
(96.25)
(86.25)
30.5
(16.75)
Two M4 taps, Depth 10
1/4-20UNC tap,Depth 10
20
±
0.3
(6.75)
52
Specifications
16
90
■ F150-SLC50
16
F150-LTC50 Light
80 40
Section 5-4
Unit: mm
(85)
(10) 25
16
31
60
16
(103.25)
30.5
(16.75)
Two M4 taps, Depth 10
(93.25) 20 ± 0.3
(6.75)
1/4-20UNC tap, Depth 10
53
Specifications
Camera Only
■ F150-S1A
(15.5)
8
48
(40) (6)
Section 5-4
(6.2)
Unit: mm
(6.2)
Light Connector
(8.8 dia.)
1"-32UN-2A
(C mount)
30.5
31.25
±
2 (16.75)
1.5
Two M4 taps, Depth 8
31
Camera Cable
Connector
(11.8 dia.)
21.25
±
2 20 ± 0.1
1/4-20UNC tap, Depth 8
(6.75)
54
Specifications
F160 Cameras
Cameras with Intelligent Lighting
■ F160-SLC20
70
12 12
F150-LTC20 Light
73 46.5
Section 5-4
Unit: mm
(85)
(10) 25
12
31
40
12
(96.25)
30.5
8
(23.25)
1/4-20UNC tap, Depth 10
(86.25) 20 ± 0.3
(13.25)
Two M4 taps, Depth 10
55
Specifications
16
90
■ F160-SLC50
16
F150-LTC50 Light
80 46.5
Section 5-4
Unit: mm
(85)
(10) 25
16
31
60
16
(103.25)
30.5
(23.25)
8
1/4-20UNC tap, Depth 10
Camera Only
■ F160-S1
(15.5)
8
54.5
(46.5)
(93.25) 20 ± 0.3
(13.25)
Two M4 taps, Depth 10
(6)
(6.2)
Unit: mm
(6.2)
Light Connector
(8.8 dia.)
1"-32UN-2A
(C mount)
31.25
±
2
21.25
± 2
30.5
(23.25)
8 31
Two M4 taps, Depth 8
Camera Cable
Connector
(11.8 dia.)
20
±
0.1
(13.25)
1/4-20UNC tap, Depth 8
56
Specifications Section 5-4
Camera Specifications
General Specifications
Item
Supply voltage F150-series: 12 VDC
F160-series: 13 VDC
Current consumption F150-S1A: 100 mA max.
F150-SL20A/SL50A: 110 mA max.
F150-SLC20/SLC50: 200 mA max.
F160-S1: 130 mA max.
F160-SLC20: 260 mA max.
F160-SLC50: 310 mA max.
Vibration resistance
Specification
10 to 150 Hz; half-amplitude: 0.35 mm; maximum acceleration: 50 m/s
2
, 10 times for 8 minutes each in 3 directions
Shock resistance
150 m/s
2
, 3 times each in 6 directions
Ambient temperature Operating: 0 to 50
C (with no condensation)
Storage:
-
25 to 65
C (with no condensation)
Ambient humidity Operating and storage: 35% to 85% (with no condensation)
Ambient environment No corrosive gases
Camera materials Cover: Galvanized steel sheet metal
Case: Die-cast aluminum alloy
Camera mounting base: Fiber-reinforced plastic (black)
Light materials
(Cameras with Lights)
Weight
Case: ABS
Transparent cover: PC
F150-S1A: Approx. 80 g
F150-SL20A/SL50A: Approx. 135 g
F150-SLC20: Approx. 280 g
F150-SLC50: Approx. 370 g
F160-S1: Approx. 85 g
F160-SLC20: Approx. 285 g
F160-SLC50: Approx. 375 g
Characteristics
Item
Picture element
Effective pixels
Synchronization
Shutter speed
(Electronic shutter)
Lens mounting
■ Camera Characteristics
Specification
1/3" Interline CCD (reading all pixels)
659
494 (H
V)
External sync. via horizontal sync signal
F150-series: 1/100 s, 1/500 s, 1/2000 s, 1/10000 s
F160-series: 1/120 s, 1/200 s, 1/500 s, 1/1000 s, 1/2000 s, 1/4000 s, 1/8000 s,
1/20000 s
C mount
Item
Lens model
Method
■ Lens Characteristics (Cameras with Lights only)
Specification
F150-SL20A: F150-LE20
F150-SL50A:F150-LE50
F150-SLC20:F150-LE20
F150-SLC50:F150-LE50
F160-SLC20:F150-LE20
F160-SLC50:F150-LE50
Fixed focal point, fixed iris
57
Specifications
Item
Brightness
Focal point distance
F2.8
F150-SL20A: 13 mm
F150-SL50A: 6.1 mm
F150-SLC20:13 mm
F150-SLC50: 6.1 mm
F160-SLC20:13 mm
F160-SLC50: 6.1 mm
Specification
■ Light Characteristics (Cameras with Lights only)
Item Specification
Light model
Light source
F150-SL20A/SL50A: F150-LT10A
F150-SLC20:F150-LTC20
F150-SLC50:F150-LTC50
F160-SLC20:F150-LTC20
F160-SLC50:F150-LTC50
F150-SL20A/SL50A:
Red LED (Peak emission wavelength: 680 nm)
F150-SLC20/SLC50 and F160-SLC20/SLC50:
Red and green LED combination
(Peak emission wavelengths: 660 nm and 570 nm)
Light emission method Pulse emission (synchronized with the camera shutter)
Item
Mounting distance
Field of vision
■ Other Characteristics
Specification
F150-S1A: Depends on lens being used.
F150-SL20A: 61 to 71 mm
F150-SL50A: 66 to 76 mm
F150-SLC20: 15 to 25 mm
F150-SLC50: 16.5 to 26.5 mm
F160-S1: Depends on lens being used.
F160-SLC20: 15 to 25 mm
F160-SLC50: 16.5 to 26.5 mm
F150-S1A: Depends on lens being used.
F150-SL20A: 20 mm
20 mm
F150-SL50A: 50 mm
50 mm
F150-SLC20: 20 mm
20 mm
F150-SLC50: 50 mm
50 mm
F160-S1: Depends on lens being used.
F160-SLC20: 20 mm
20 mm
F160-SLC50: 50 mm
50 mm
Section 5-4
58
Specifications
Consoles
■ F150-KP Console
50
ESC TRIG ENT
Section 5-4
1.5
Unit: mm
13
40
34
SHIFT
CONSOLE
2000 23 5 10
Item
Vibration resistance
Minimum bending radius
Materials
Specification
10 to 150 Hz; half-amplitude: 0.15 mm; 4 times for 8 minutes each in 3 directions
Shock resistance
196 m/s
2
; 3 times each in 6 directions
Ambient temperature Operating: 0 to 50
C (with no condensation)
Storage:
-
25 to 65
C (with no condensation)
Ambient humidity 35% to 85% (with no condensation)
Ambient environment No corrosive gases
Degree of protection IEC60529 IP20 (in-panel)
75 mm
Weight
Body: ABS
Cable sheathing: Heat-resistant chlorinated vinyl
Connector: PC and PBT
Approx. 135 g
59
Specifications
■ F160-KP Console
48
ESC
SHIFT
ENT
TRIG
F1
F4
F7
F2
F5
F3
F6
F9
F8
29.7
20
Unit: mm
Section 5-4
4.8 dia.
12 dia.
Item
Degree of protection
Minimum bending radius
Materials
Specification
Current consumption Approx. 10 mA
Vibration resistance
10 to 150 Hz; half-amplitude: 0.35 mm; maximum acceleration: 50 m/s minutes each in 3 directions
2
,10 times for 8
Shock resistance
150 m/s
2
; 3 times each in 6 directions
Ambient temperature Operating: 0 to 50
C (with no condensation)
Storage:
-
25 to 65
C (with no condensation)
Ambient humidity 35% to 85% (with no condensation)
Ambient environment No corrosive gases
IEC60529 IP20 (in-panel)
75 mm
Weight
Body: ABS
Cable sheathing: Heat-resistant chlorinated vinyl
Connector: PC and PBT
Approx. 160 g
60
Specifications Section 5-4
CHECK The switch on the back of the F160-KP must be set to “ENABLE”.
SHIFT
ENT
ESC TRIG
F1
F4
F7
F2
F5
F8
F3
F6
F9
These keys will be disabled if the switch is set to "DISABLE".
ENABLE
ENABLE DISABLEE
Cables
Camera Cables
■ Camera Cable Specifications
The F150-VS, F160-VSR3, and F160-VSR4 Camera Cables have different dimensions and wiring, but they share the same specifications.
Item
Vibration resistance
Specification
10 to 150 Hz; half-amplitude: 0.15 mm, 4 times for 8 minutes each in 3 directions
Shock resistance
196 m/s
2
, 3 times each in 6 directions
Ambient temperature Operating: 0 to 50
C (with no condensation)
Storage:
-
25 to 65
C (with no condensation)
Ambient humidity 35% to 85% (with no condensation)
Ambient environment No corrosive gases
Materials Cable sheathing: Heat-resistant chlorinated vinyl
Connector: Fiberglass-reinforced PC and PBT
75 mm Minimum bending radius
Weight Approx. 170 g
61
Specifications Section 5-4
■ F150-VS Camera Cable (For F150-S @ , F160-S @ Cameras)
3000
Unit: mm
36
51
(30)
43
F250 Connector
Signal Pin
Power
GND
GND
VIDEO GND
1
2
3
4
VD
ESCNT1
VIDEO
HD
5
6
7
8
9 SCAN
ESCNT2
INDEX
TRG
Shell
10
11
12
Connector model:
Hirose RP17A-13PA-12PC
6
7
8
9
4
5
Pin
1
2
3
10
11
12
Camera Connector
Signal
GND
Power
GND
VIDEO
VIDEO GND
HD
Not used.
ESCNT1
ESCNT2
INDEX
TRG
SCAN
Shell
Connector model:
Hirose HR10A-10P-12S
62
Specifications Section 5-4
■ F160-VSR3 Camera Cable (For F300-S2R/S3DR/S4R and F200-S @
Cameras)
3000
Unit: mm
(120)
46
43
F250 Connector
Signal Pin
Power
GND
1
2
GND
VIDEO GND
VD
3
4
5
6 ESCNT1
VIDEO
HD
SCAN
7
8
9
10 ESCNT2
INDEX
TRG
Shell
11
12
Connector model:
Hirose RP17A-13P-12PC
Camera Connector
7
8
9
10
11
12
Pin
1
2
3
4
5
6
Signal
GND
Power
VIDEO GND
VIDEO
HD GND
HD
VD
GND
−
INDEX(SI)
TRG
VD GND
Shell
Connector model:
Hirose HR10A-10P-12S
63
Specifications
■ F160-VSR4 Camera Cable (For F300-S Cameras)
3000
(120)
46
Section 5-4
Unit: mm
43
F250 Connector
Signal Pin
Power
GND
GND
VIDEO GND
1
2
3
4
VD
ESCNT1
VIDEO
HD
5
6
7
8
SCAN
ESCNT2
INDEX
TRG
Shell
9
10
11
12
Connector model:
Hirose RP17A-13P-12PC
F150-VM Monitor Cable
2000
6
7
8
4
5
Pin
1
2
3
9
10
11
12
Camera Connector
Signal
GND
Power
VIDEO GND
VIDEO
HD GND
HD
VD
GND
−
INDEX(SI)
Power
VD GND
Shell
Connector model:
Hirose HR10A-10P-12S
Unit: mm
46.7
46.7
Item
Vibration resistance
Specification
10 to 150 Hz; half-amplitude: 0.15 mm, 4 times for 8 minutes each in 3 directions
Shock resistance
196 m/s
2
, 3 times each in 6 directions
Ambient temperature Operating: 0 to 50
C (with no condensation)
Storage:
-
25 to 65
C (with no condensation)
Ambient humidity 35% to 85% (with no condensation)
Ambient environment No corrosive gases
Materials Cable sheathing: Heat-resistant chlorinated vinyl
Connector: PVC
64
Specifications
Minimum bending radius
Weight
Item
Accessories
50 mm
Approx. 40 g
BNC Jack Adapter
F160-VP Parallel I/O Cable
40 40
20 200
Specification
20
40
Section 5-4
Unit: mm
200
2000
200
Item
Vibration resistance
Shock resistance
196 m/s
2
, 3 times each in 6 directions
Ambient temperature Operating: 0 to 50
C (with no condensation)
Storage:
-
25 to 65
C (with no condensation)
Ambient humidity 35% to 85% (with no condensation)
Ambient environment No corrosive gases
Materials
Specification
10 to 150 Hz; half-amplitude: 0.15 mm, 4 times for 8 minutes each in 3 directions
Cable sheathing: Heat-resistant PVC
Connector: Polyester resin
120 mm Minimum bending radius
Weight Approx. 340 g
50
65
Specifications
F150-M05L LCD Color Monitor
Section 5-4
Unit: mm
Mounting plate thickness: 1.6 to 4.8
(46 max.)
Mounting bracket
POWER
SYNC
Panel opening dimensions
(100)
185
174
(5.5)
F150-VM Monitor Cable
•
Tolerance:
±
1 mm
The dimensions in parentheses are provided for reference.
133.5
+0.5 mm
0
175.5
+0.5 mm
0
Item
Supply voltage 20.4 to 26.4 VDC
Specification
Current consumption 700 mA max.
Vibration resistance
10 to 150 Hz; half-amplitude: 0.1 mm; maximum acceleration: 15 m/s minutes each in 3 directions
2
, 10 times for 8
Shock resistance
150 m/s
2
, 3 times each in 6 directions
Ambient temperature Operating: 0 to 50
C (with no condensation)
Storage:
-
25 to 65
C (with no condensation)
Ambient humidity 35% to 85% (with no condensation)
Ambient environment No corrosive gases
Degree of protection
Materials
Panel size
Panel type
Resolution
Image pitch
Contrast
Viewable angle
Luminance
Backlight
Response speed
Input signal
IEC60529 IP20 (in-panel)
Case: ABS/PC
Display surface: PMMA (Acrylic)
5.5 inches (111.36
83.52 mm (H
V))
TFT color liquid crystal
320
240 dots
0.348
0.348 mm (H
V)
85:1 (typical)
25
up/down and 50
left/right (with a contrast ratio > 10)
250 cd/m
2
(typical)
Cold cathode fluorescent light
60 ms max.
NTSC composite video (1.0 V/75
W
termination)
66
Specifications
Item
Weight
Accessories
Approx. 1 kg
Four mounting brackets
F150-M09 Video Monitor
222
Specification
Unit: mm
250
Section 5-4
190 50 160
22
Item
Supply voltage 85 to 264 VAC, 50/60 Hz
Current consumption 20 W max.
Specification
Vibration resistance
5 to 100 Hz; 0.16-mm full-amplitude or acceleration of 7.35 m/s
2
(whichever is smaller),
6 times for 10 minutes each in 3 directions
Ambient temperature Operating:
-
10 to 50
C (with no condensation)
Storage:
-
20 to 65
C (with no condensation)
Ambient humidity 10% to 90% (with no condensation)
Ambient environment No corrosive gases
Materials
CRT size
CRT type
Front: ABS plastic
Metal part: SECC (galvanized steel sheet)
9 inch (164
123 mm (H
V))
Monochrome CRT
Resolution
System
800 TV lines min. (at center)
Number of scanning lines: 600
Horizontal frequency: 15.75 kHz
I/O impedance
Field frequency: 60 Hz
75
W
, high impedance (selectable)
I/O level and polarity Composite image signal: 1 V (peak to peak)
Input signal
Weight
Image: 0.7 V (peak to peak), positive
Synchronization: 0.3 V (peak to peak), negative
NTSC composite video (1.0 V/75
W
termination)
Approx. 4.5 kg
67
F200/F300 Camera Parameters
Memory Cards
F160-N64S
42.8
3.3
Unit: mm
Section 5-5
Item Specification
Ambient temperature Operating: 0 to 60
C (with no condensation)
Storage:
-
25 to 85
C (with no condensation)
Ambient humidity 8% to 95% (with no condensation)
Ambient environment No corrosive gases
Life expectancy 300,000 overwrite operations
Number of pins
Weight
50 pins
Approx. 15 g
Application Software
F250-UME
42.8
Units: mm
3.3
Item Specification
Ambient temperature Operating: 0 to 60
C (with no condensation)
Storage:
-
25 to 85
C (with no condensation)
Ambient humidity 8% to 95% (with no condensation)
Ambient environment No corrosive gases
Life expectancy 300,000 overwrite operations
Number of pins
Weight
50 pins
Approx. 15 g
5-5 F200/F300 Camera Parameters
Detailed parameter settings are required when a Camera other than an F150-
S1A or F160-S1 is connected. Make the following settings when using an
F200/F300 Camera. The Camera settings window is displayed at startup and
68
F200/F300 Camera Parameters Section 5-5 can be displayed at other times by selecting Camera settings from the System Menu.
Camera settings
Camera : Others
Intelligent Lighting 0:
Out of use
Intelligent Lighting 1:
Out of use
Intelligent Lighting 2:
Out of use
Intelligent Lighting 3:
Out of use
End
Set the Camera model to "Others" and select
"End".
Camera settings(Detail)
Camera Speed :
Shutter : SYNC RESET
Synchronization : External
Strobe disable, start
Strobe disable, end
Clamp pulse timing
Clamp pulse width :
:
:
:
Normal
[ 0]H
[ 0]H
[ 90]CLK
[ 25]CLK
Shutter trigger width : [ 3]H
End
Camera
Camera speed
F200-
S
F300-
S
F300-
S2R
Standard
Standard
Standard
F300-
S3DR
Standard
F300-
S4R
Standard
Shutter
OFF
OFF
SYNC
NON
RESET
SYNC
NON
RESET
SYNC
NON
RESET
Synchronization
Strobe disable
Start End
Internal
External
External
10
6
External
External
17
8
(None)
(None)
-
8
-
2
-
2
-
2
-
0
0
0
6
-
10
-
8
-
2 0
3 5
1/1,000
1/2,000
1/4,000
1/10,000
1/1,000
1/2,000
1/4,000
5 7 1/10,000
-
5
-
3
-
3
-
2
-
16
-
14 1/1,000
-
11
-
9 1/1,500
-
8
-
6
-
-
6
4
1/2,000
1/3,000
-
3
-
1
-
1
1/4,000
1/6,000
1/8,000
0 1/10,000
-
2
-
2
0
0
1/30,000
1/50,000
Shutter speed
1
Clamp pulse
Timing
60
90
90
25
25
Shutter trigger pulse
Width Width Polarity
20 (Note
2)
(Note
2)
7
Positive
Positive
Negative
External
VD
Sync
3
OFF ---
OFF ---
OFF ---
Image read Y timing
3
90
90
25
25
7
7
Negative
OFF ---
Negative
OFF ---
Note 1.
The shutter speed is set in the Camera itself.
2.
Set the shutter trigger pulse width to match the strobe’s specifications only when a strobe is being used.
3.
These settings (indicated by ---) are ignored.
69
Connecting a Strobe Device Section 5-6
5-6 Connecting a Strobe Device
Use the camera’s corresponding strobe trigger output signal (STGOUT0 to
STGOUT3) to control the strobe flash timing.
SeeAlso Refer to page 32 for details on the pins allocated to these signals.
Check the strobe device's specifications and set the appropriate “Shutter trigger polarity” and “Shutter trigger width” in the Camera settings (Detail) Menu.
The Camera settings (Detail) window is displayed at startup and can be displayed at other times by selecting Camera settings from the System Menu.
Shutter trigger width Strobe specifications Shutter trigger polarity
Positive When the flash is synchronized to the OFFto-ON transition of the strobe trigger signal
W
STGOUT0 to 3
OFF
ON
When the flash is synchronized to the ON-to-
OFF transition of the strobe trigger signal
Negative
W
STGOUT0 to 3
OFF
ON
The “shutter trigger width” setting determines the pulse width W.
When using a Double-speed Camera:
W = Shutter trigger width setting (H)
32 m s
(1H = 32 m s)
When using a Camera other than a Doublespeed Camera:
W = Shutter trigger width setting (H)
63 m s
(1H = 63 m s)
Note: Depending upon the timing, W may have an error of up to
1H.
Combining an OMRON Camera and Strobe
The following table shows the timing polarity. Use a strobe that is compatible with this timing.
Camera
F150-S1A
F160-S1
F200-S
F300-S
F300-S2R
F300-S3DR
F300-S4R
Shutter trigger polarity
Positive
Positive
Positive
Negative
Shutter trigger width
3H (1H = 63 m s)
3H (1H = 32 m s)
Can be set to match the strobe's specifications.
7H (1H = 63 m s)
Note The window used to change the shutter trigger polarity and shutter trigger pulse will not be displayed when an F150-S1A or F160-S1 Camera is connected, but the STGOUT0 to STGOUT3 signals will be output with the polarity and width shown in the table above.
70
A
ambient temperature
, 3
B
battery
BATTERY LOW message
, 5 replacing
,
5
C
cables
,
4
Camera Cable specifications
, 61
Camera Only
, 18
Camera with Intelligent Lighting
,
18
Camera with Light
, 18
Cameras
, 4 characteristics
,
57 connecting
, 17 overview
, 17 parameters
,
68 specifications
, 57
CCTV lenses
,
22 communications connector
, 38 wiring
, 38 components
, 4 installation
, 4 names and functions
, 14 computers using Memory Cards
, 28 connector
,
38
Consoles connecting
, 17 specifications and dimensions
, 59 crimp terminals
,
19
D
dimensions
,
50
E
Ethernet
,
40
Extension Tubes
, 24 external devices connecting
, 29
Index
F
F150 Cameras dimensions
, 51
F150-KP
, 59
F150-M05L
, 66
F150-M09
,
67
F150-S1A
, 54
F150-SL20A/SL50A
, 47 , 51
F150-SLC20
, 52
F150-SLC20/SLC50
,
48
F150-SLC50
,
53
F150-VS
, 62
F160 Cameras dimensions
, 55
F160-KP
, 60
F160-N64S
,
68
F160-S1
,
56
F160-SLC20
, 55
F160-SLC20/SLC50
, 48
F160-SLC50
,
56
F160-VP
, 65
F160-VSR3
, 63
F160-VSR4
, 64
F250-C50/C55
,
50 field of vision
, 58
G
ground
, 19
I
I/O specifications
, 36 inspections
,
49 installation components
, 4 precautions
, 2 site
,
2
L
LCD Monitor
, 66 lenses
, 22 characteristics
,
57 diameters
, 23 light
71
72 characteristics
, 58 replacing
,
46 lighting
, 25
M
maintenance
, 46 manuals
, ix
Memory Cards
, 27 in personal computers
,
28 removing
, 4 specifications
,
68
Monitor specifications
,
66
Monitors connecting
, 17 mounting
,
15 distance
, 58
N
noise resistance
,
4
O
optical chart
, 22 orientation
, 2
P
package contents confirming
, 6 parallel interface connecting external devices
, 30 peripheral devices connecting
,
17 power supply
, 19 turning OFF
, 5 wiring
, 20 precautions
, xi applications
, xii battery
, xii general safety
, xii installation
, 2 installation environment
, xii power supply and wiring
, xii products availability
, 6
Index
R
RESET signal precaution
,
5
RS-232C
,
38
RS-422
, 38
S
Screw Terminal Blocks
, 31 serial interface connecting external devices
, 37 signal lines
,
4 specifications
,
50 general
, 50
I/O
, 36
Parallel Connectors
,
32 strobe combining with Camera
, 70 connecting
, 70 system configuration
, 12
T
temperature ambient
, 3 troubleshooting
,
44 cables
, 46 connection errors
,
44 menus
, 44 parallel interface
, 44 serial interface
,
45
V
Video Monitor
,
4
,
67
W
wiring communications
,
38
Revision History
A manual revision code appears as a suffix to the catalog number on the front cover of the manual.
Cat. No. SCHB-736A
Revision code
The following table outlines the changes made to the manual during each revision. Page numbers refer to the previous version.
Revision code
A
Date
September 2001 Original production
Revised content
73
advertisement
Related manuals
advertisement
Table of contents
- 13 Introduction
- 14 Installation Precautions
- 18 Confirming Package Contents
- 18 Product Availability
- 19 Special Features, Installation, and Connections
- 20 Special Features
- 24 Basic System Configuration
- 26 Component Names and Functions
- 27 Mounting the Controller
- 29 Connecting Peripheral Devices
- 31 Power Supply and Ground
- 33 Lenses, Lighting, and Memory Cards
- 34 CCTV Lenses
- 37 Lighting
- 39 Memory Cards
- 41 Connecting External Devices
- 42 Connecting through the Parallel Interface
- 49 Connecting through the Serial Interface
- 55 Troubleshooting and Maintenance
- 56 Troubleshooting
- 58 Maintenance
- 61 Regular Inspections
- 62 Specifications
- 80 F200/F300 Camera Parameters
- 82 Connecting a Strobe Device
- 83 Index
- 85 Revision History